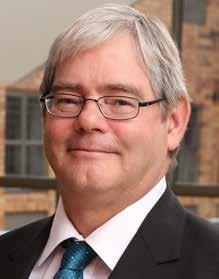
5 minute read
Tailings management aims to progress despite headwinds
Tailings storage facilities (TSFs) are great achievements of civil engineering and have tested some of the best brains in the mining sector. Now, despite current headwinds related to the Covid-19 pandemic, the industry is planning to raise the bar even further by advancing its best practice in a concerted fashion over the next decade.
The impetus for this, according to Adriaan Meintjes, partner and principal civil geotechnical engineer at SRK Consulting, has been a series of TSF accidents in the past few years. The most recent – and dramatic – was the failure of the TSF at Vale’s Córrego do Feijão iron ore mine in Minas Gerais, Brazil. The event, which took place on 25 January 2019, killed over 250 people.
Advertisement
“This led to an industry-wide response from a range of organisations – which could be compared in some ways to the response of the security community to the New York terror attacks in 2001,” says Meintjes. “Needless to say, consultancies like SRK have been kept very busy, as mining companies assess their fiduciary risk connected with TSFs.”
He highlighted the difficulties in TSF engineering, stemming mainly from the dynamic nature of the infrastructure – which is subject to the facility’s growing capacity. The contents of the TSF shift constantly, with chemical and structural changes in the tailings themselves as the orebody and mineral processing parameters alter.
“The changes in and interactions of all these factors – often over a lifespan of decades – complicate the planning, construction, operations, decommissioning and closure of these facilities,” he said. “If errors occur during any of these stages, failure can result.”
New lessons The Feijão accident surprised experts for various reasons. An important one was how quickly and completely the integrity of the TSF failed. The front wall was inspected in the days before the failure and deemed to be stable, but it collapsed completely in less than one minute. This mode of rapid failure is a brittle failure,
Adriaan Meintjes, principal civil geotechnical engineer, SRK Consulting
similar to glass breaking. It is normally expected that early signs of failure are ductile and gradual, and can be picked up and addressed long before a total collapse.
It was also troubling that the facility was in a mature stage of its life, and was in fact in the process of decommissioning;

Vibrating wire with transmitter installation on a TSF
it had not received any tailings for more than a year.
“The prevailing view is that TSFs are most vulnerable as they approach the end of their lives – and while they are still actively being fed with tailings,” he said. “This accident shows that TSF failure can occur at any time, if adverse site conditions combine.”
Monitoring At the centre of managing the risk of TSFs is the ability to monitor accurately and frequently, says Meintjes. Unfortunately, this is probably where there is the most variation in best practice within the industry. So, it is fitting that TSF monitoring is an important focus of global efforts by various stakeholders to improve standards.
“The instrumentation that is traditionally deployed on TSFs usually has to be manually read, at intervals that vary from days to months,” he says. “The shortcomings of these systems include human error and other inconsistencies – as well as the obvious time lapses before results are available for decision-makers.”
Advances in electronic instrumentation and remote sensing systems, such as satellite deformation modelling, however, have opened the door to real-time performance monitoring. The sophistication of the equipment, combined with the power of remote sensing, makes it much easier and quicker for mines to conduct detailed field sampling – even testing the properties of tailings.
“Certain modern instruments – many of which are smaller and cheaper to install – can now be hosted in the tailings material, and can send data relating to deposition parameters,” Meintjes adds.
He notes that the improved readings can be leveraged by better data acquisition systems; data transmission systems can centralise the collection of data, which can also then be shared across mine networks.
“New industry standards will demand that these systems are integrated. Better monitoring means that potential failures can be detected earlier, and interventions can be put in place. In many instances, we have been doing this for decades – but it needs more consistent application across the whole sector,” Meintjes says.
Modelling will also be a valuable field of technological advance. Fed by the data from modern sensors, modelling software will help engineers to compare the TSF’s actual behaviour with its original design expectations.
“This will allow us to understand more clearly what is taking place at different stages in the TSF life cycle. We can then further improve best practice as it relates to each phase – from design through to closure – and incrementally learn from the information gained as to the next steps to be taken,” he says.
Safety first Meintjes is sober about the timeframe that such a process will involve, indicating that it may easily take 10 or more years of diligent perseverance. Indeed, he warns that attempts to rush such an important review would not be advisable – as key

An example output from a vibrating wire data logger

observations and insights would then be missed.
“To achieve the necessary innovations that we seek, we will obviously have to run the manual legacy system alongside the high-tech options that we want to test,” he says. “This approach is the responsible route, which ensures that safety is always at the heart of our efforts.”
But he is upbeat about the commitment demonstrated by all stakeholders, including mining company executives. The sector’s global body, the International Council on Mining and Metals, is undertaking a comprehensive review of tailings management – in conjunction with the United Nations Environment Programme and the Principles for Responsible Investment, as well as the International Commission on Large Dams and a number of other related and interested organisations. He also emphasises the need to convince all stakeholders that the process is moving constructively and efficiently.
“Our work to date in both field sampling and testing is already delivering better results,” he says. “We expect a continued improvement, and look forward to taking significant steps in TSF safety through scientific and applied endeavour.”
He acknowledges that Covid-19 lockdowns are indeed slowing the pace of this good work.
“The economic disruption from lockdowns, with the loss of income in local and global economies, is certainly focusing minds on survival,” says Meintjes. “However, addressing these demanding conditions goes alongside the need to constantly pursue and improve industry best practice.”