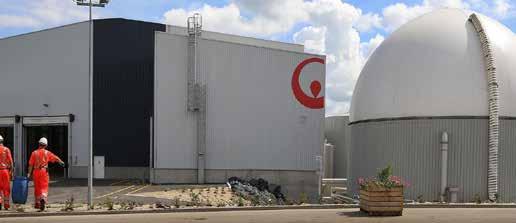
5 minute read
From appalling to appealing – wastewater sludge beneficiation
Managing wastewater sludge represents a significant portion of total wastewater treatment plant (WWTP) costs. To reduce this expense, the volume of sludge can be reduced or alternatively beneficiated into biogas or a saleable product. WASA asks Chris Braybrooke, GM: Marketing at Veolia Services Southern Africa, about the treatment of wastewater sludge.
In 2020, Veolia produced nearly 43 million megawatt hours of energy and treated 47 million tonnes of waste
Advertisement
How is sewage sludge locally managed? Conventional practices related to wastewater sludge management include land disposal, waste piling, landfill disposal and, to a lesser degree, use in agricultural practices. These are becoming less viable, with a ban on liquids to landfill and the plan to reduce solid organic waste to landfill. Furthermore, transport costs and landfilling fees keep increasing. With sludge production increasing daily, the current practices are unsustainable.
Unfortunately, on-site land disposal and waste stockpiling have become the standard options for many WWTPs in South Africa. Some of these sludges also find their way into water resources and contaminate them.
Bold steps must be taken to ensure that these volumes are reduced, made safe and valorised where possible. This would include looking at fertiliser production, materials of construction, and biosolids used to produce energy or heat.
Innovative solutions are available to reduce wastewater sludge and turn it into a resource.
How can wastewater sludge create biogas? Anaerobic digestion (which forms part of the secondary step of sludge treatment) is one of the oldest and most used processes for sludge stabilisation and biogas production. This is where microbes feed on the organic matter, transforming it into methane gas and carbon dioxide when digested.
It is possible to increase biogas production by adding co-fermentation agents like grease, untreated (and highly concentrated) sewage and additional bio-waste to the digesters. Typical gas production for sewage sludges ranges from approximately 400-450 m3 per tonne.
The biogas is removed from the digested sludge by air stripping in the gas removal unit before the sludge is fed further to the intermediate storage. Digester biogas would normally contain small amounts of water and hydrogen sulfide (< 0.01 %). This could cause corrosion
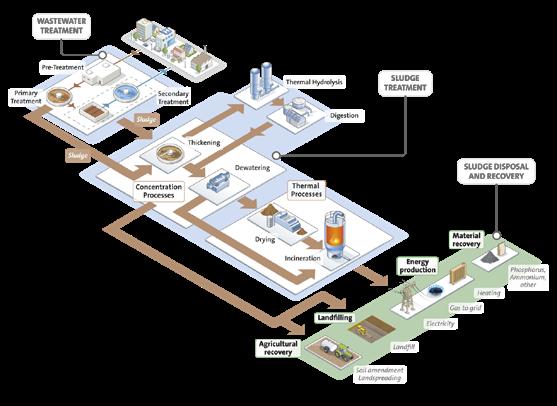
Chris Braybrooke, GM: Marketing, Veolia Services Southern Africa
Exelys™ increases biogas production and lowers sludge volumes considerably, while simultaneously pasteurising the recovered sludge. It is also proven to help sewage works reduce CO2 emissions by between 10% and 30%
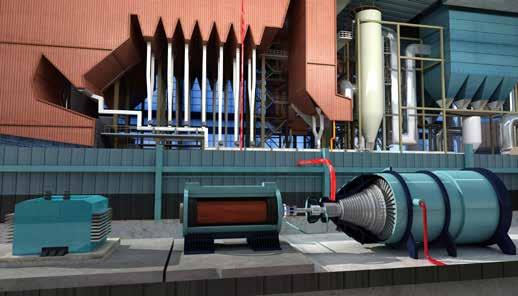
in CHP (combined heat and power), tube and gas storage systems. The removal of sulfur is recommended. The treatment gas is then pumped into a storage tank.
What biogas management systems are offered by Veolia? Veolia has optimised a process known as thermal hydrolysis, which uses temperatures between 150°C and 190°C, as well as pressures of between 6 bar and 15 bar, to crack the long-chain molecules found in municipal sludge. This increases the reaction rate, making more bio-active carbon available than previously possible.
Known as Exelys™, it has been utilised in Veolia-built and -operated plants across the EU and USA. It helps to turn 1.2 Mℓ of sewage into enough energy to supply a single average home for one month. This dehydrated sludge can then be utilised as compost in fields to facilitate agriculture.
Exelys™ is the most effective energy enhancement methodology available to the market, because it increases biogas production and lowers sludge volumes considerably, while simultaneously pasteurising the recovered sludge. It is also proven to help sewage works reduce CO2 emissions by between 10% and 30%.
Biogas production from wastewater sludge requires optimal temperatures, ranging between 30°C and 40°C for the digestion process to function. In areas where this is a problem, Veolia applies some of its technologies to utilise biogas production to heat up the digestion process.
Furthermore, Veolia’s Struvia technology has been developed to facilitate the recovery, valorisation and reuse of phosphorus contained in wastewater and concentrated industrial water. Phosphorus is a key ingredient in fertilisers used in agriculture and for animal feed. It is primarily produced by mining, and no synthetic substitute currently exists. Struvia allows for the recovery of phosphorus from effluents produced by industrial, agricultural and municipal activities, as struvite crystals (a mineral substance composed of magnesium ammonium phosphate). This opens the way for a local reuse of phosphorus, especially in agriculture.
An example of Veolia solutions can be found in T-Park, Hong Kong. Designed by Veolia, this is the world’s largest sludge treatment and recovery plant that is self-sufficient in water and energy and complies with the increasingly stringent environmental standards required by Hong Kong.
Incinerating the sludge reduces its volume by 90% and T-Park has the capacity to generate up to 14 MW of electricity during the treatment process. Electricity generated that exceeds T-Park’s energy needs is fed into the public grid. No wastewater is discharged into the sea, as all of it is treated and recycled through the plant. Fully energyautonomous, it is also water self-sufficient.
What are some barriers to biogas production? One of the barriers of biogas production could be the lack of secondary treatment works where digesters are utilised. In smaller treatment plants, these process steps are not included, which means there is no method of capturing biogas, so it boils down to the initial planning of a wastewater works and the capex associated with such a plant. For smaller plants, it is important to manage sludge disposal in a responsible way.
In addition to the regulations and specifications regarding the disposal and utilisation of wastewater sludge, the Water Research Commission (WRC) has also published five volumes of guidelines. It is of utmost importance that wastewater sludge is handled responsibly.
Many WWTPs already have anaerobic digesters (ADs), but these are in various states of disrepair. Also, where biogas (methane) is produced, it is simply flared (or just released into the atmosphere). The opportunity to utilise this biogas by-product to offset the energy requirements of the WWTPs requires the implementation of CHP technology, as well as the refurbishment of the existing ADs in many cases.
Veolia offers operation and maintenance contracts for WWTPs where processes are improved, future upgrades (if necessary) are designed, and the overall sustainability of the plant is increased.
Conclusion In 2020, the Veolia group supplied 95 million people with drinking water and 62 million people with wastewater services, produced nearly 43 million megawatt hours of energy, and treated 47 million tonnes of waste. Veolia is committed to ecological transformation.