
28 minute read
Director for Loramendi & Aurrenak
our industry into the future, ” says Küpper as the core content of his presidency.
Background: Clemens Küpper learned the profession of foundry mechanic and completed studies in Duisburg and Bielefeld as a foundry engineer (Dipl.Ing.) and industrial engineer (Dipl.-Wirt.-Ing.). He is the spokesman for the management of the Baumgarte iron foundry in Bielefeld-Brackwede. Clemens Küpper was born in 1967, born in Bielefeld, married and has three children. ■ BDG秘书长Max Schumacher密切合作,竭尽全力引领 我们的行业走向未来”。 背景:Clemens Küpper学习铸造机械专业,并在 杜伊斯堡和比勒费尔德完成了铸造工程师(Dipl.-Ing.) 和工业工程师(Dipl.-Wirt.-Ing.)的学习。他是比勒 费尔德-布拉克韦德Baumgarte铸铁厂管理层的发言 人。Clemens Küpper1967年出生于比勒费尔德,已 婚并育有三个孩子。 ■
Advertisement
35 Years Loramendi Germany and New Managing Director for Loramendi & Aurrenak 罗拉门迪(德国)公司成立35周年并迎来新任总经理
The Year 2020 Was A Very Special Year For Loramendi, Especially In Germany.
In one of our most important markets, we were able to celebrate our 35th anniversary after the foundation of Loramendi Germany in 1985. Since the very first day, we have attached great importance to the best possible customer orientation and the development of long-term partnership relationships with our customers and suppliers.
In order to further improve this customer service and to expand our market position, we were able to win Dr. Oliver Vogt as a new managing director for our company. He took over the management of our Loramendi Vertriebs GmbH team with effect from 01.02.2020. In this function, he is responsible for 2020年对于罗拉门迪公司来说是非常特殊的一 年,尤其是其德国公司。 罗拉门迪德国公司于1985年成立,我们能够在我 们最重要的市场庆祝公司成立35周年。因为从成立第 一天起,我们就非常重视以客户为导向,并且与我们 的客户和供应商建立长期合作伙伴关系。 为了进一步改善客户服务并扩大我们的市场地 位,我们成功邀请Oliver Vogt博士作为公司的新任 董事总经理。从2020年2月1日起,他接管了Loramendi Vertriebs公司。他负责罗拉门迪公司在德国
the areas of core production, vertical molding and 3D printing for Loramendi in Germany & Central Europe.
In addition, he has been assigned responsibility for our complete Aurrenak activities for this region.
With Dr. Vogt, we have been able to gain a manager with both technical and commercial experience for Loramendi and Aurrenak. He has been working successfully in the foundry industry for 20 years in leading positions in development, production and sales. In addition to his most recent position as sales manager of an aluminium foundry, he was responsible for the overall commercial management of a machining site for cast components.
In addition to his strong customer orientation, he brings with him many years of management experience as well as well-founded industry expertise and has a correspondingly broad network.
In addition to the further optimisation of our customer relationships, one of our common goals is to exploit the advantages of the synergies of Loramendi & Aurrenak Group for our customers in the best possible way. Loramendi and Aurrenak, both headquartered in Vitoria, Basque Country, are part of the Mondragón Group, a cooperative organisation, and have been global leaders in the foundry world for 50 years. Through the synergies of the Group, the know-how of core production and tooling technology is combined in a way that is unique in the market, to the benefit of our customers.
Other very future-oriented fields of work are the expansion of our product portfolio, in areas like electrification, as well as the systematic implementation and expansion of 3D core printing technology for large-scale industrial applications. In the first mentioned field of work, we are pleased to report that further orders for electric motor components have been won, and significant progress has been made also in the industrial 3D printing of cores together with our partners Voxeljet and ASK. Not to forget in addition the impressive improvements in industry 4.0 assuring our customers having the best profit out of our equipment.
Based on these positive developments, both organisationally and technically, as well as the many years of very trusting cooperation with almost all OEMs and many well-known foundries in the global environment, Loramendi & Aurrenak sees itself very well equipped for the future. ■ 和中欧的制芯生产、垂直 造型线和3D打印业务。 此外,他还负责AK模 具公司在该地区的所有 业务。 在Vogt博士的带领 下,公司为罗拉门迪和 AK模具公司找到了一位 技术和商业经验兼具的 经理。他在铸造行业工 作了20年,在研发、生 产和销售方面有丰富的 经验。除了担任一家铝 铸造厂的销售经理外,他还负责铸件的机加工厂 的综合管理。 他不仅具有强烈的客户导向意识,还带来了多年 的管理经验以及扎实的行业专业知识,并拥有相对 广泛的关系网络。 除进一步优化我们的客户关系外,我们的共同目 标之一是以尽可能最好的方式使我们的客户充分利 用罗拉门迪和AK模具集团的协同优势。总部位于 巴斯克地区维多利亚的罗拉门迪公司和AK模具是 Mondragón集团的一部分,并且50年来一直是铸 造领域的全球领导者。通过集团公司的协同效应, 制芯生产和模具技术的专业知识相结合,在行业中 是独一无二的,使我们的客户受益。 其他面向未来的工作领域包括在电气化等领域 的产品组合的扩展,以及用于大规模工业应用的 3D 砂芯打印技术的系统实施和扩展。在提到的第 一个领域,我们骄傲地宣布,公司已经赢得了更多 的电机组件订单,并且与合作伙伴 Voxeljet和ASK 在工业3D打印砂芯方面也取得了重大进展。此外, 工业4.0的发展显著,将确保我们的客户从公司设备 中获得最大利润。 基于公司组织和技术方面的积极进展,以及多年 来与全球范围内几乎所有原始设备制造商和很多知 名铸造厂的互信合作,罗拉门迪和AK模具公司已为 未来做好了充分的准备。 ■
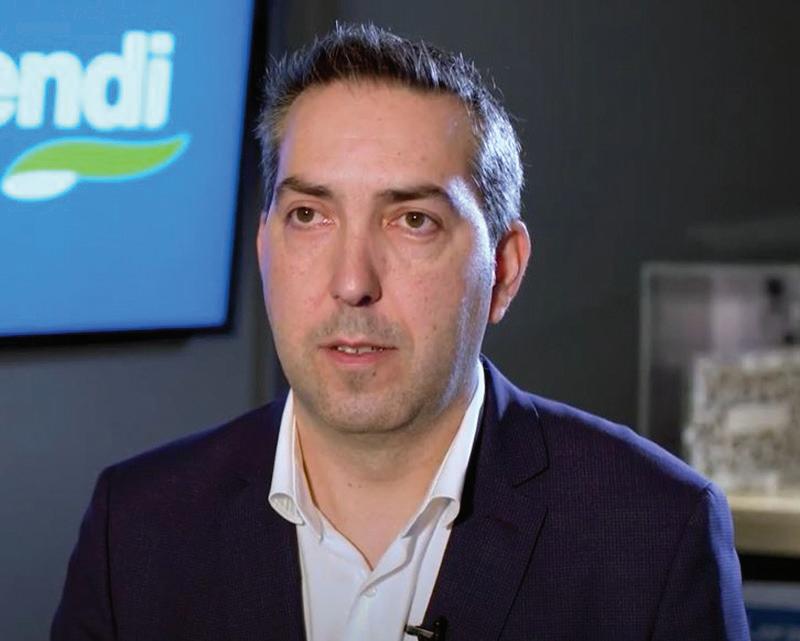
Cast Magnesium Foam for Energy Absorption and Bone Regrowth
Low-cost cast magnesium foam could open new markets in biomedical applications as well as transportation systems.
hannah ullberg, kaustubh rane, amir kordijazi, and pradeep rohatgi, university of wisconsin – milwaukee
用于吸能和骨骼再生的铸造泡沫镁
低成本的铸造泡沫镁可以在生物医学应用和运输行业开辟新的市场。
威斯康辛大学密尔沃基分校 HannaH Ullberg, KaUstUbH rane, amir Kordijazi和 PradeeP roHatgi
Engineers and research scientists have been exploring lightweight energy absorbing materials for applications in vehicles to reduce injuries sustained in crashes. Aluminum foams have been used in several automobiles so far, but the lower density of magnesium makes it attractive as a potential material for foam casting, as well. In a recent study by researchers at the University of Wisconsin-Milwaukee (UWM), a pressure infiltration process was used to synthesize magnesium alloy closed cell syntactic foams incorporating silicon carbide and alumina microballoons. According to the experimental results, when these syntactic foams are deformed above a certain stress, the hollow microballoons incorporated in the matrix of alloys start to collapse and a plateau in stress is observed until very large strains occur—leading to high energy absorption in these syntactic foams.
In addition, the novel process was used to further examine
为
了减轻事故中的伤害,工程师和技术人员一 直在寻找应用于汽车轻量化的吸能材料。到 目前为止,已经有几款汽车在使用泡沫铝,
但镁的密度更低,使其作为潜在的铸造泡沫材料也很有 吸引力。威斯康辛大学密尔沃基分校(UWM)的技术人 员在最近的一项研究中,利用压力渗透工艺合成了含有 碳化硅和氧化铝空心微珠的镁合金闭孔聚合泡沫。根据 实验结果,当应力达到一定水平,这些合成泡沫开始变 形时,合金基质中的空心微珠开始坍塌,在非常大的应 变发生之前,可以观察到应力的平台期——这就是这些 合成泡沫可以吸收高能量的原因。 另外,这个新工艺还被进一步研究泡沫镁在生物医学
Fig 1. Cross-section morphologies of the LAMed ZK61 are depicted.
图1:描述了LAMed ZK61的 横截面形态。
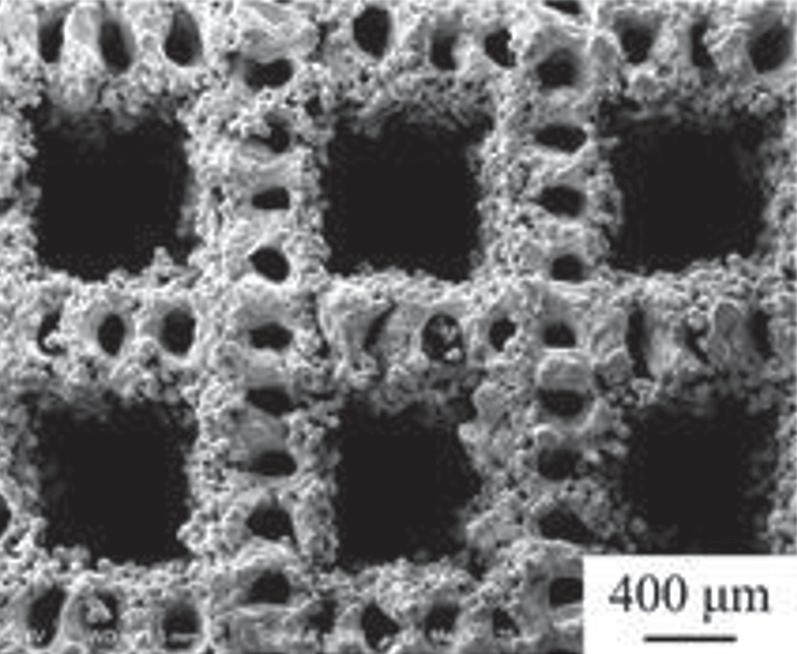
Fig 2: Foam Design 2 (left) was designed with cuboid pores and Design 4 (right) was designed with cylindrical pores.
Fig 3. Pictured is the CAD model of new ceramic mold shape. Red is the foam shape, green is the basin for the magnesium, and orange is the holder for the foam, basin, and liquid plaster.
图2:泡沫设计2(左)采用方孔 设计,设计4(右)采用圆柱孔 设计。
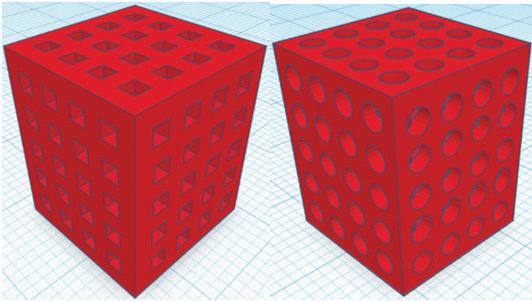
图3:新型陶瓷模具形状的CAD模 型。红色是泡沫的形状,绿色是镁 的盆,橙色是泡沫、盆和液体石膏 的支架。
magnesium foams’ applicability for biomedical applications, such as scaffolds for bone regrowth.
Based on the case study, magnesium foams appear to be very promising for resolvable scaffolds, and casting the foams appears to be a promising route for making these scaffolds. Additionally, pressure infiltration of plaster molds with a polymer-invested pattern has been used to synthesize magnesium with open porosity suitable for bone growth scaffolds.
Healing Segmental Bone Defects
A bone break that is too large to be healed naturally is called a segmental bone defect. These defects are healed using techniques beyond natural bone regrowth. One method involves a bone graft, which takes nonessential bone tissue from one body part to be used at the bone break site. This method has many limitations, such as infection risk, accessibility of donor bone, mismatch of shape between the donor bone and break site, and the surgeon’s ability to shape the donor bone as necessary. Other methods involve man-made materials such as bioceramics or polymers as implants. These materials were created with porosity to promote bone cell growth in the matrix but the porous shapes did not provide the strength requirements necessary to mimic bone strength as it undergoes daily loading and unloading conditions. Additionally, some were not able to maintain the nutrient transportation, had high degradation rates, or released toxins in a biological environment. 应用中的适用性,如骨再生的支架。 基于相关案例研究,用泡沫镁做支架似乎是非常 有前途的解决方案,而铸造泡沫似乎是制造这些支 架的很有前景的方法。此外,石膏型压力渗流法已 被用于合成适合骨生长支架的具有开放的孔隙度的 泡沫镁。
节段性骨缺损的愈合
创口太大而不能自然愈合的骨断裂被称为节段性 骨缺损。类似这样缺损的愈合所应用的技术,超越 了自然的骨再生。一种方法是骨移植,它从身体某 个部位提取非必要的骨组织,用于骨断裂部位。这 种方法有许多局限性,如感染风险、供体骨的可及 性、供体骨和断裂部位之间的形状不匹配,以及外 科医生在必要时塑造供体骨的能力。其他方法包括 人工材料,如生物陶瓷或聚合物作为植入物。这些 材料具有孔隙率,以促进骨细胞在基质中的生长, 但多孔形状没有提供模拟骨强度所需的强度要求, 因为它经历了日常的加载和卸载条件。此外,一些
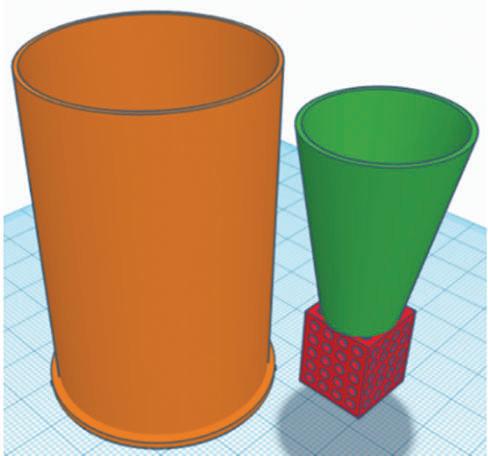
Fig 4. Pictured is the pre-cast magnesium billet inside the designed basin of the ceramic mold.
图4:陶瓷模具设计盆内的预铸镁坯。
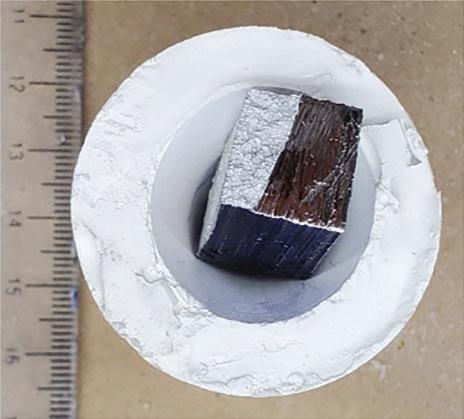
As an alternative to ceramics or polymers, metals are preferred in load bearing applications due to their strength, ductility, resistance to failure and biocompatibility. Biocompatibility is a main factor in the material selection process, as rejection of the implant by the body can cause a multitude of problems with the patient’s recovery. Permanent bone implants are widely used to repair large injuries. However, drawbacks include permanent irritation, stress shielding, possible secondary surgery requirement, and the inability to adapt to growth.
Biodegradable implants allow for regrowth of tissue, allow for vascularization of the area, reduce need for secondary surgery by dissolving completely as the implant area regrows bone, and reduce stress shielding. Stress shielding happens when the bone matter around an implant experiences lower proportion of loading due to the higher strength of the implant. It then loses density and therefore strength. A bone implant must exhibit mechanical properties similar to bone tissue to avoid this phenomenon. The strength requirement for optimal bone implants was found to be 100150MPa along the axis.
Many materials are used as bone implants, such as titanium, zinc, stainless steel or cobalt-chromium. These, however, may introduce toxins into the body, cause inflammation, and mismatch the elastic modulus of bone. Magnesium presents the most compatible physical and mechanical properties, which reduces stress shielding and increases the probability of a successful implantation. This metal has been researched in labs as a bone scaffold but is not commercially available. The main drawback of magnesium in the environ材料无法维持营养物质的运输,降解率高,或在生 物环境中释放毒素。 作为陶瓷或聚合物的替代品,金属由于其强度、延 展性、耐失效和生物相容性而在承载应用中是首选。 生物相容性是材料选择过程中的主要因素,因为如果 身体拒绝植入物,会在患者的恢复过程中引发许多问 题。永久性骨植入被广泛用于修复大型损伤。然而, 缺点包括永久性刺激、应力屏蔽、可能的二次手术以 及无法适应生长。 可生物降解的植入物能够让组织再生,能够使作 用区域血管化,通过植入物在骨再生时完全溶解,减 少二次手术的环节,并减少应力屏蔽。当植入物周围 的骨物质由于植入物的强度较高时,就会发生应力屏 蔽。然后,因此失去了密度和强度。骨植入物必须表 现出与骨组织相似的力学性能,以避免这种现象。最 佳骨植入物的强度要求沿轴线为100-150mpa。 许多材料被用作骨植入物,如钛、锌、不锈钢或 钴铬。然而,这些物质可能会将毒素带入体内,引起 炎症,并导致骨骼的弹性模量不匹配。镁具有最兼容 的物理和力学性能,减少了应力屏蔽,增加了成功植 入的概率。这种金属作为骨骼支架在实验室进行了研
Table 1. Comparison of foam trial dimensions
Foam Design
Number Length (mm) Width (mm) Height (mm)
Pore Shape 1 17 17 17 Rectangular 2 13.5 13.5 16.5 Rectangular 3 14 14 18 Rectangular Pore Size (mm) 1
1.5
2
4 13 13 16 Circular 2
Fig 5. Shown is the setup of steel tube with steel cab for near vacuum infiltration.
Fig 6. Pictured is (a) the as-cast magnesium foam with ceramic remaining in pores and (b) a completed foam made by N. Kirkland.
图5:钢管与钢驾驶室接近真空 的渗透设置。
图6:(a)现铸镁泡沫和陶瓷残留在孔隙和 (b)N.Kirkland制造的完整泡沫。
ment of the human body is a high rate of corrosion leading to large amounts of hydrogen bubble accumulation due to the cathodic reaction of magnesium with water during corrosion. New techniques to understand this corrosion in vivo remain under development. The rapid corrosion can be slowed by changing the elemental composition such as adding rare earth metals or also by coating the magnesium with other materials. Despite rapid corrosion, scientists have measured the occurrence of an osteoblastic response as magnesium degrades in a biological environment. Future work on the biocompatibility of foams would include slowing corrosion rate and exactly matching mechanical properties.
For the application of a dissolvable insert to promote bone regrowth, a porous shape would provide the needed strength as well as increase the sites for bone cell growth. These scaffolds should also provide possibilities for nutrient transport. A porous bone scaffold was found to have porosity values ranging from 60%–90% for optimal bone regrowth 究,但还没有推向市场。镁在人体环境中的主要缺点 是在腐蚀过程中镁与水发生阴极反应,导致大量的氢 气泡积累。了解这种体内腐蚀的新技术仍在开发中。 通过改变元素组成,如添加稀土金属或用其他材料涂 覆镁,也可以减缓快速腐蚀。尽管腐蚀迅速,科学家 们已经测量了在生物环境中镁降解时成骨细胞反应的 发生。未来关于泡沫生物相容性的工作将包括减缓腐 蚀速率和完全匹配的力学性能。 为了应用可降解的植入物来促进骨再生,需要多孔 形状的支架提供所需的强度,并增加骨细胞生长的部 位。这些支架也应该为营养输送提供可能性。多孔骨 支架的孔隙率为60%-90%,以获得最佳的骨再生, 孔径平均大于150-μm。如果设计正确,开放式的泡
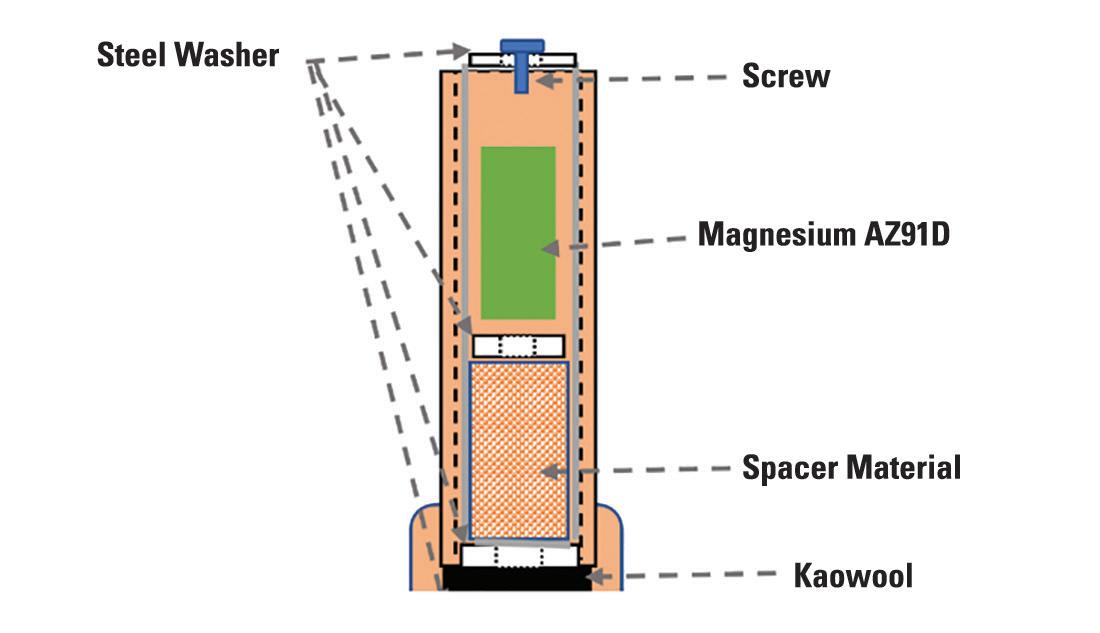
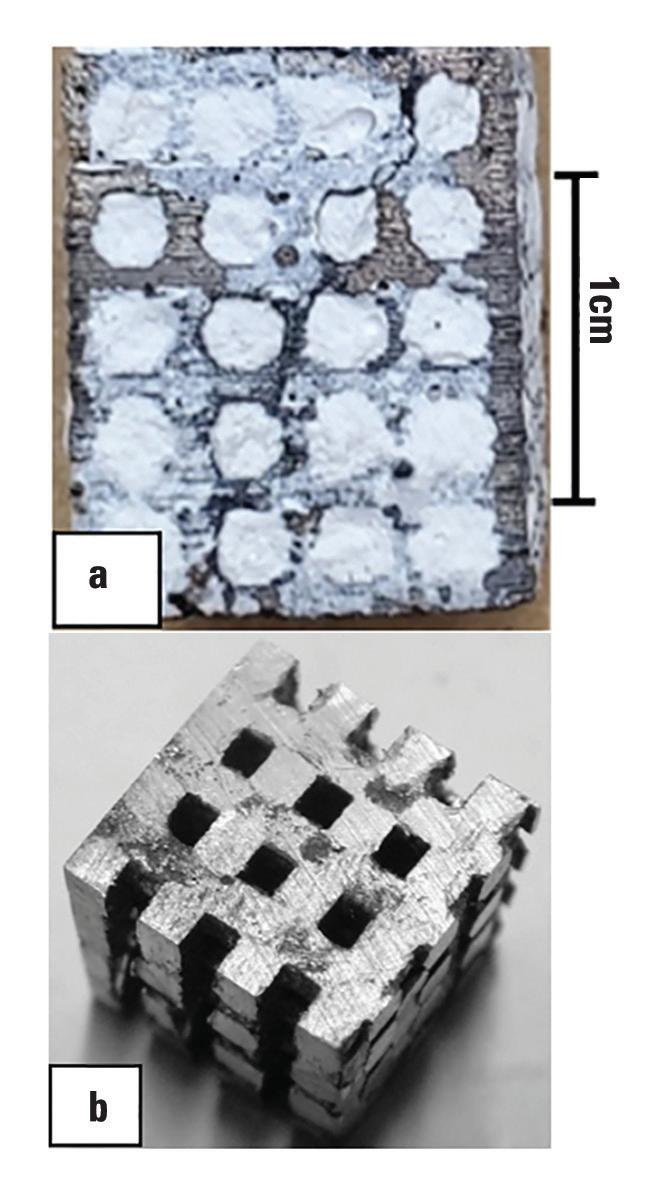
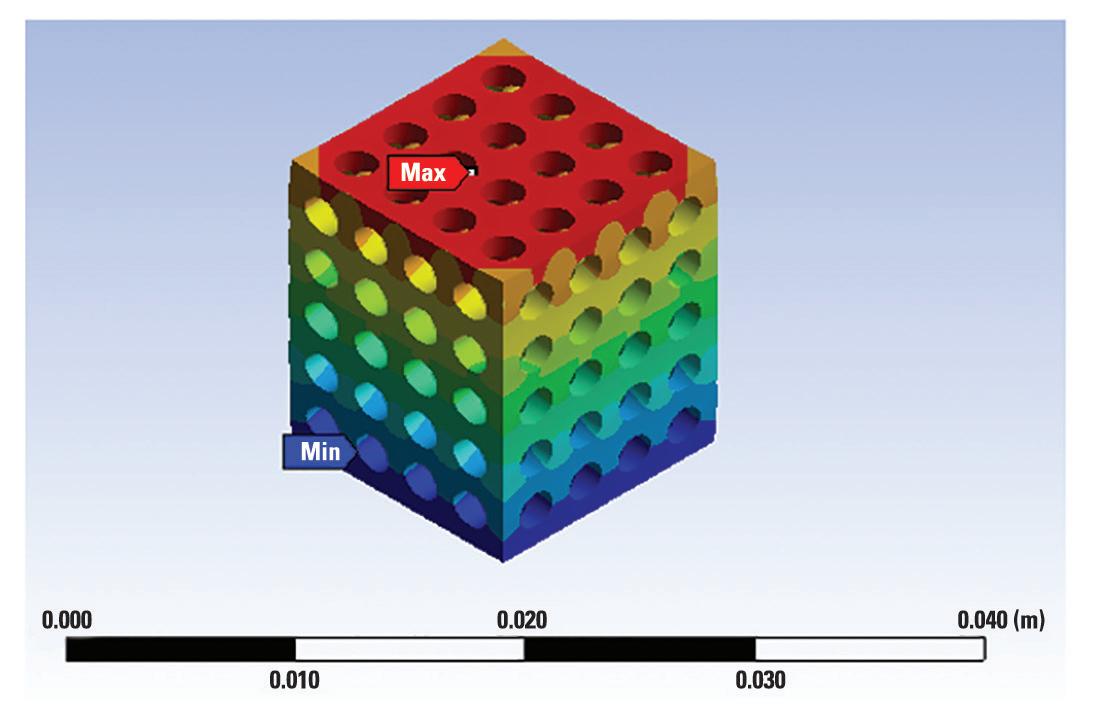
Fig.7. Shown is the maximum deformation of the simulated Design 4 foam at 150MPa applied from the top. Red denotes areas of maximum deformation ranging to blue, which denotes the least deformation.
图7:所示为模拟设计4泡沫在150MPa处的最大变形。红 色表示最大变形区域,蓝色表示变形最小。
with the pore size averaging larger than 150-μm. An open cell magnesium foam could meet these conditions if correctly designed. CAD programs are becoming popular to design and simulate scaffold structures to optimize the shape before physical samples are made.
Magnesium Foam Production Methods
Many magnesium foam production methods have been investigated. For example, laser additive manufacturing (LAM) has been used to produce porous magnesium alloy WE43 and Mg-Zn-Zr ZK61 alloys (Fig. 1). LAM consists primarily of laser melting deposition (LMD) and selective laser melting (SLM). Since the cooling rate can be as high as 103–104 K/s during the LAM process, small grains of metal parts result, which can improve the mechanical properties of the materials. LAM can produce complex parts with high precision and purity. Additionally, the production cycle is short, and no post-processing is needed. The adjustment of the laser processing parameters allows the control of the pore size. However, this process is likely to be costly compared to casting, and the production rate will be low; plus, reproducibility will need to be established.
Other methods include powder metallurgy, spacer casting, pressure foaming, and 3D printing of foams. In this study at UWM, a pressure infiltration using a ceramic mold as a spacer was designed and trialed. The novel pressure infiltration technique infiltrates magnesium alloy melts into a plaster mold made by pouring liquid plaster around a 3D printed PLA open cell foam, which is evaporated upon heating, leaving a porous plaster mold. The porous plaster mold is placed in pressure infiltration equipment where AZ91D magnesium alloy is melted and pressure-infiltrated into the porous plaster 沫镁可以满足这些条件。CAD程序非常适合设计和模 拟支架结构,以优化形状。
泡沫镁制备方法
泡沫镁有许多种制备方法。例如,激光增材制造 (LAM)已被用于生产多孔镁合金WE43和Mg-Zn-Zr ZK61合金(图1)。LAM主要由激光熔化沉积(LMD)和 选择性激光熔化(SLM)组成。由于在模拟过程中,冷 却速率可高达103-104k/s,从而细化金属部件的晶 粒,可以提高材料的力学性能。LAM可以生产高精 度、高纯度的复杂零件。另外,生产周期较短,不需 要后处理。激光处理参数的调整能够控制孔隙率和孔 径。然而,与铸造相比,这种工艺成本高昂,而且产 量很低,此外,还需要建立重现性。 其他方法包括粉末冶金、脉冲电流铸造、压力发泡 和3D打印泡沫。本研究在威斯康辛大学密尔沃基分 校设计并试验了以陶瓷模具为间隔的压力渗透技术。 新的压力渗透技术渗透镁合金熔入一个石膏型,将液 体石膏倒在3D打印的开放细胞泡沫周围,加热后蒸 发,留下多孔石膏模型。将多孔灰模放置在压力渗透 设备中,将AZ91D镁合金熔化并将压力渗透到多孔灰 模中。熔融的镁凝固形成泡沫镁。将石膏从铸件中移 除,留下泡沫镁。
mold. The molten magnesium solidifies to form the magnesium foam. The plaster is removed from the casting, leaving the magnesium foam.
Open Cell Magnesium Alloy Foam Using Pressure Infiltration
In the UWM pressure infiltration study, foam shapes were designed using CAD software. Four blocks, with dimensions shown in Table 1, were virtually designed. The shapes were created with interconnected holes, or pores. Foam Designs 1, 2 and 3 were designed with cuboid pores while Foam Design 4 was designed with cylindrical pores (Fig. 2).
Previous trials exhibited a difficult extraction process of the cast sample from the furnace equipment. The problem arose from molten magnesium spilling between the ceramic mold and the furnace equipment. To combat this, a new shape of ceramic shell was designed using the same CAD software as the foams. This new design allowed for a basin in which the molten magnesium could remain until pressure was applied. Shown in Figure 3, the green cone basin and red foam fit inside the orange cylinder holder and the ceramic would take the negative shape. Figure 4 exemplifies how the magnesium fits into the cone basin.
All foam designs and new ceramic shell shapes were 3D printed using PLA material. The pore size of foam Design 3 was too large for accurate 3D printing and could not be used for the subsequent experimental procedures.
Powdered calcium sulfate, (Plaster of Paris) was used as the ceramic mold material. The mixture, prepared as per container instructions, was poured into the shell shape, which included the basin area and foam shape. Immediately following this, all parts were placed in a sonicating machine to ensure complete distribution of ceramic slurry through the entire foam matrix. Each sonicated mold was then allowed to set for 24 hours.
Next, the molds were sintered in a furnace with a programmed ramp burn-out cycle intended to first remove any remaining water, then melt and burn the PLA, and finally to sinter the ceramic. Each mold was placed upside down onto a casting filter to allow melted PLA material space to run out of the ceramic mold, ensuring little ash buildup inside the mold.
Pressure infiltration of preforms with molten magnesium alloy was executed. This method forms near-net-shaped castings of the mold shape as shown in Figure 5. The sintered molds had small billets of magnesium placed into the basin. The mold was then placed into the furnace, which was then sealed and evacuated of air for 10 minutes. Air evacuation continued as the furnace was heated to 650C and held at this temperature for 10, 20, or 30 minutes as melting time was considered a variable. The air evacuation was halted, and argon gas was slowly released into the chamber, until a pressure of 150 psi was reached. This pressure was held for 10 minutes. Finally, the furnace was turned off, allowed to cool naturally, then vented of pressure, in this order, to ensure the molten magnesium did not burn.
After removal of the sample from the ceramic mold,
采用压力浸渗方式制备开孔镁合金泡沫
在威斯康辛大学密尔沃基分校的压力渗透研究 中,使用CAD软件设计泡沫形状。实际上设计了四 个方块,尺寸如表1所示。这些形状是由相互连接的 孔洞或孔隙形成的。泡沫设计1、2和3采用长方体 孔,泡沫设计4采用圆柱形孔。(图2) 先前的试验表明,从炉体装置中取出铸造样品的 过程很困难。这个问题是由于熔融的镁在陶瓷型和 熔炉设备之间溢出而引起的。为了应对这一问题, 我们使用与泡沫相同的CAD软件设计了一种新形状 的陶瓷外壳。这种新设计使熔融的镁合金保持在熔 池中,直到施加压力。如图3所示,绿色圆筒熔池和 红色泡沫适合橙色圆柱支架,陶瓷呈负形状。图4举 例说明了镁是如何融入锥形熔池的。 所有的泡沫设计和新的陶瓷外壳形状都使用PLA 材料进行了3D打印。泡沫设计3的孔径太大,无法 精确打印,不能用于后续的实验程序。 采用硫酸钙粉(巴黎石膏)作为陶瓷型壳材料。 根据容器说明制备的混合物,倒入壳形状,包括熔 池面积和泡沫形状。随后,所有零件被放置在超声 设备中,以确保陶瓷浆料通过整个泡沫基质完全分 布。然后让每个经过超声处理的型壳静置24小时。 接下来,铸型在炉内烧结,并有编程的斜坡燃 烧循环,旨在首先去除任何剩余的水,然后熔化和 燃烧,最后烧结陶瓷。每个铸型都被倒置在一个铸 造过滤器上,以使熔化的PLA材料尽可能流出陶瓷 型,确保型内很少有灰烬堆积。 用熔融的镁合金对预成型物进行了压力渗透。该 方法形成如图5所示的近网状铸件,烧结的镁坯。 然后将模具放入炉子中,然后密封,排出空气10分 钟。当炉被加热到650度,并在这个温度下保持10 、20或30分钟,因为熔化时间被认为是一个变量。 空气疏散被停止,氩气被慢慢地释放到腔室中,直 到达到150psi的压力。这个压力保持了10分钟。最 后,关闭炉子,自然冷却,然后按这个顺序排出压 力,以确保熔融的镁不会燃烧。 从陶瓷模具中去除样品后,模具材料留在泡沫基 质的孔中,如图6所示。虽然用精细工具手工刮取 很容易去除,但这将很耗时。我们尝试进行了一种
material of the mold remained in the pores of the foam matrix, as seen in Figure 6. Though this could have easily been removed by scraping by hand with fine tools, this would be time consuming. A chemical removal process was attempted. Sodium bicarbonate was found to degrade the ceramic mold material without degrading the magnesium structure. However, the sodium bicarbonate needed to be in solution or suspension to evenly degrade the ceramic material on all surfaces. Water degrades magnesium; therefore, isopropyl alcohol was initially tested as a carrier for the sodium bicarbonate suspension. The isopropyl alcohol, sodium bicarbonate and foam structure were placed onto a magnetic stirring machine for one hour. The foam was then removed and placed into a fresh suspension and allowed to mix for another hour. A solution of water and sodium bicarbonate was tested for effectiveness in the same way.
Case Study Results on Open Cell Foam Made at UWM
Foam structures were successfully designed and 3D printed with controllable porosities ranging from 42%–57%.
The new mold design allowed the furnace equipment to be consistently reusable as well as allowed for cracked molds to be used. These aspects lower the cost of the production process. As mentioned previously, harsh chemicals are difficult to work with and expensive. This technique does not use harsh chemicals and is therefore safer and more cost effective than other methods of creating a porous foam structure. The two different trials to remove the excess ceramic from the foam pores yielded no results. The excess ceramic was not able to be removed by these methods in the timeframe stated.
Finite element analysis was performed on a model magnesium foam structure of foam Design 4. Compression tests were performed to understand how the foam would reach under loading conditions sustained by human bone. Simulations were run with a force of 150MPa at a slow rate. Results showed a maximum deformation of 0.23 mm of the foam structure in the direction of the force (Fig. 7). This low value is promising as small deformation values are ideal for this foam structure under compression to accurately simulate human bone. Stress concentration points were analyzed as well. The circular pores aided in load distribution and minimizing stress concentrating areas. This minimizes the risk of foam failure under stress due to foam shape design.
Foam designs were created using a CAD program with controllable porosities up to 57%. The mold shape was optimized to enable furnace equipment reuse. Successful investment casting and melt introduction to the mold created a low-cost magnesium foam. Simulated compression tests show the magnesium foam mimics bone tissue properties as minimal deformation occurs. ■ This article is based on the paper “Cast Magnesium Foam for Energy Absorption and Bone Regrowth,” (Paper 21-052) originally presented at the 2021 Metalcasting Congress. 化学去除过程。发现碳酸氢钠可以降解陶瓷模具 材料而不降解镁结构。然而,碳酸氢钠需要放在 溶液或悬浮液中,才能均匀地降解所有表面的陶 瓷材料。水降解镁;因此,异丙醇最初作为碳酸 氢钠悬浮液的载体进行了测试。将异丙醇、碳酸 氢钠和泡沫结构放置在磁性搅拌机上1小时。然后 将泡沫移除,放入新鲜的悬浮液中,再混合一个 小时。用同样的方法测试了水的碳酸氢钠溶液和 碳酸氢钠溶液的有效性。
在威斯康辛大学密尔沃基分校开孔泡沫制备的 研究结果
泡沫结构设计成功,3D打印,孔隙率可控在 42%-57%之间。 新的铸型设计使熔炉设备可以重复使用,甚 至允许使用开裂的铸型。在这些方面降低了生产的 成本。如前所述,苛刻的化学物质很难使用,而且 也很昂贵。这种技术不使用苛刻的化学物质,因此 比其他创建多孔泡沫结构的方法更安全、更具成本 效益。从泡沫孔中去除多余陶瓷的两种不同试验没 有得到任何结果。在规定的时间框架内,这些方法 无法去除多余的陶瓷。 对泡沫设计的镁泡沫结构模型进行了有限元分 析4。进行了压缩试验,以了解泡沫在人骨承受的 加载条件下如何达到。模拟以150英里的慢速度运 行。结果表明,泡沫结构在力方向上的最大变形为 0.23mm(图7)。这种低值是有希望的,因为小变 形值是理想的这种泡沫结构在压缩下,以准确模拟 人骨。对应力浓度点也进行了分析。圆形孔隙有助 于负荷分布和最小化应力集中区域。这使泡沫形状 设计降低了泡沫形状设计在应力下失效的风险。 泡沫设计是使用CAD程序创建的,可控孔隙率 高达57%。对模具形状进行了优化,使炉膛设备能 够重复使用。成功的投资铸造和熔体引入的模具创 造了一个低成本的镁泡沫。模拟压缩试验表明,镁 泡沫模拟骨组织性能。 ■
本文基于最初发表在2021年美国金属铸造大会上的论 文“铸造泡沫镁进行能量吸收和骨再生”(论文21052)。
METAL CHINA 2021: Full Recovery, Boost Confidence, Face the Future
全面复苏、提振信心、面向未来——METAL CHINA 2021 Report
From May 26-28, 2021, the 19th China International Foundry Expo (METAL CHINA), the 15th China International Die Casting Industry Exhibition (DIECASTING CHINA) & the 15th International Nonferrous and Special Casting Exhibition has been successfully held at National Exhibition and Convention Center (Shanghai).
During the three-day exhibition period, the 78,000 square meters gathered more than 860 well-known domestic and foreign companies. The on-site visits reached 96,186 and the online visits reached 223,448. The quality of trade visitors has been further improved.
The event included several highlights, exhibiting of smart, green, and environmentally friendly products, the integration of information technology and traditional technique; the 1,850t diecasting machine, which is the highest record exhibited at the show, and a series of supporting programs, such as signing ceremonies of a 9,000t diecasting machine, interpretation of the latest policies, theme forums covering various product technologies; display of 3D printing, innovative technology, squeeze casting, low-pressure casting, local exhibition groups and foundry culture and other special exhibition areas.
Green technology leads industry innovation progress
In response to climate change, China has proposed that carbon dioxide emissions will reach a peak by 2030 and realize the carbon neutral by 2060. Foundry companies’ attention to green and environmental protection has increased to a new level. Aiming at the urgent need for sustainable development in the current metal industry market, many exhibitors have brought green, low-carbon and environmentally friendly products, focusing more on materials, processes, technology and quality, with the goal of improving efficiency and reducing pollution, focusing on benefits and applications, and attracting more visitors to negotiate.
Feature exhibition areas focus on industry hotspots
To further focus on the needs of enterprises and industry hotspots, the exhibition set up nine major exhibition areas, including intelligent manufacturing and robot exhibition area, casting innovation experience area, testing instrument exhibition area, safety and environmental protection 2021年5月28日,为期3天的第十九届中国国际 铸造博览会、第十五届中国国际压铸工业展览 会&第十五届国际有色及特种铸造展览会在国 家会展中心(上海)完美收官。 3天的展期内,78000平米的展出面积,聚集了 860余家中外知名企业,实际到场观众达96186人 次,线上观众达223448人次,专业观众质量较以往有 了进一步提升。 从智能、绿色、环保的亮眼产品,到信息技术与传 统铸造的融合应用;从1850吨压铸机实体展出的最高 纪录,到以9000吨压铸机现场签约等系列活动;从解 读最新政策信息,到覆盖产品技术的主题论坛;从3D 打印、创新体验、挤压铸造、低压铸造的集中展示, 到各地方展团和铸造文化等多个特色展区,展会亮点 多多,精彩纷呈。
绿色引领 创新前行
为应对气候变化,中国提出,二氧化碳排放力争 2030年前达到峰值,力争2060年前实现碳中和。铸 造企业对绿色、环保的关注提升到了新的高度,众多 展商带来了绿色、低碳、环保产品,瞄准当下金属市 场对可持续发展的迫切需求,更多地在材料、工艺、 技术和品质上下功夫,以提高效率、减少污染为目 标,注重效益和应用,吸引许多客商驻足交流。
特色展区聚焦行业热点
为进一步聚焦企业需求和行业热点,展会设立了智 能制造与机器人展区、铸造创新体验区、检测仪器展 区、安全与环保展区、 管网系统铸件展区、产 业集群展区、铸造文化 展区、大专院校与科研 院所等九大展区,重点 展示、发布和推广本领 域在转型升级中的改革 成果和发展成就,为参 展企业和专业买家搭建 起更为精准的对接平
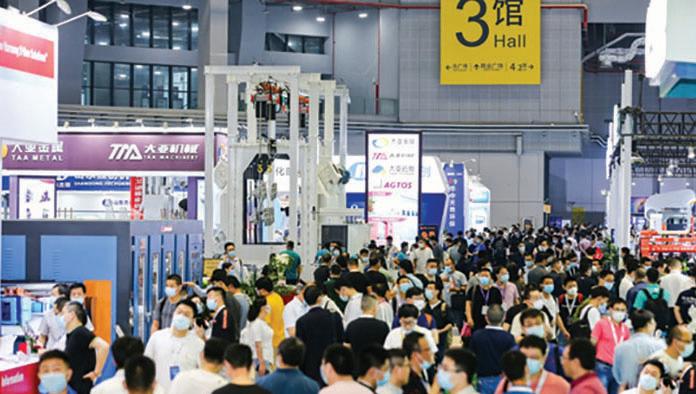
exhibition area, pipe casting network exhibition area, industrial cluster exhibition area, casting culture exhibition area, colleges, universities and scientific research institutes area. They focus on displaying, publishing and promoting the reform and development achievements of transformation and upgrading of the industry, and building a more targeted matchmaking platform for exhibitors and buyers.
Local pavilions with characteristics
As representatives of the local foundry industry and the main force of the industry, Hong Kong Pavilion, Suzhou Pavilion, Chongqing Pavilion, Guangdong Pavilion, Shandong Pavilion, Shanxi Pavilion, Zhejiang Pavilion, Anhui Pavilion, Henan Pavilion, and Liaoning Pavilion and other industrial cluster pavilions represented by Jiahe and Zhangwu give full play to the advantages of the local industry clusters, display the most representative enterprises and products, and demonstrate characteristic and sustainable development trends of the industry.
New products and equipments
During the exhibition, there were a lot of new products release ceremonies. Wheelabrator’s new CT continuous shot blasting machine series, which perfectly realize full automation and flexible anti-rolling parts cleaning; DISA’s DISAMATICD5 vertical molding line, DISA TAG digital solutions have made its debut; Wanfeng Technology’s intelligent aluminum alloy casting production line (low-pressure, gravity) showcases the latest achievements and strength of the brand; new products from MAGMA’s MAGMASOFT® 5.5 is newly presented, which can help customers create more values in casting design, mold manufacturing and casting production.
The releases of series of new products and new applications once again confirms the vigorous development of the foundry industry, and high-end casting featured with intelligent and green, has become hotspots for foundry enterprises.
地方展团特色亮相
作为地方产业代表和 行业发展的主力军,以 香港展团、苏州展团、 重庆展团、广东展团、 山东展团、山西展团、 浙江展团、安徽展团、 河南展团、辽宁展团, 嘉禾、彰武等产业集群 展团为代表的各地方展团,充分发挥地方铸造产业集 聚区的优势,集中展示最具代表性的企业和产品,为 行业演绎出特色发展、可持续发展的行业态势。
新品首发频频
展会期间,各展台新品发布不断:维尔贝莱特的全 新CT连续通过式抛丸机系列,完美实现了全自动化 和灵活的防翻滚零件清理能力;迪砂DISAMATICD5 垂直造型线、DISA TAG数字化解决方案等先后绚丽 登场;万丰科技的铝合金智能化(低压、重力)铸造 生产线,展示出企业在热加工领域全线设备研发、软 件开发、系统集成等方面的最新成果和品牌实力;迈 格码新产品MAGMASOFT® 5.5全新呈现,可帮助 客户在铸造设计、模具制造和铸造生产中创造更多价 值…… 新产品、新应用的逐一揭晓,再次印证了铸造产 业整体业态蓬勃发展,智能化、绿色化等高端铸造成 为了铸造企业的关注热点。
商贸收效颇丰
展期内,专业观众川流不息,参展企业应接不暇, 现场成交频现,商贸氛围十分浓厚,展馆内“设备已 售出”的庆贺条幅随处可见……
多彩活动传递前沿理念
展会期间,行业发展趋势及铸件、装备需求研讨 会、新品发布会、签约 仪式、压铸技术论坛、 中欧铸造业交流论坛以 及数十场洽谈会、技术 交流会精彩纷呈,为铸 造行业探讨创新发展、 绿色发展、经贸对接、
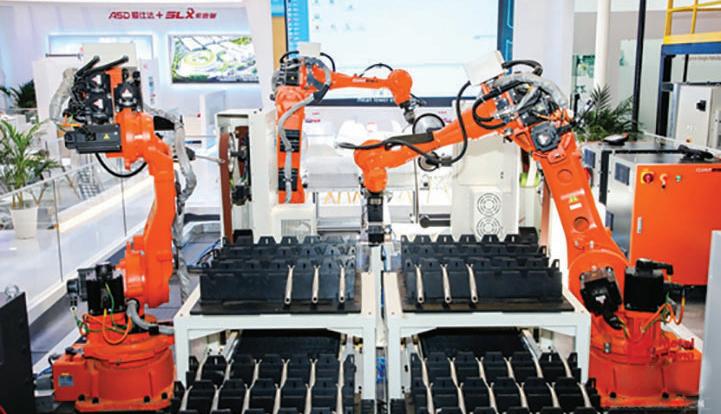
Positive trade atmosphere
During the exhibition period, there was a very positive business atmosphere that the halls were brimming with negotiations and transactions.
Colorful activities
Dozens of supporting programs were held during the show, such as industry trend release, seminars, new product launch conferences, signing ceremonies, die-casting technology forum, China-Europe foundry industry forum, at which innovation and
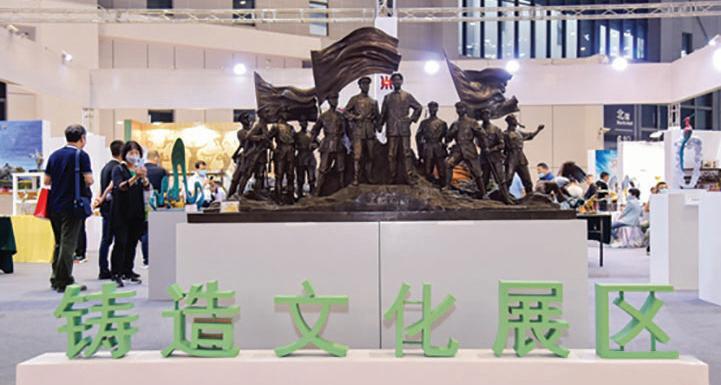
development were thoroughly discussed, economic and trade information was exchanged, and international cooperation stage has been provided.
Foundry is an important part in the development of the equipment manufacturing industry, as well as an important support for the development of OEMs and major technical equipment. During the 14th Five-Year period, China’s foundry industry will improve its own industrial chain coordination, deepen the adjustment of industrial structure, transform the development mode of the industry and accelerate the progress towards high-quality development.
METAL CHINA and DIECASTING CHINA 2022 will be held at the National Exhibition and Convention Center (Shanghai) from May 18-21, 2022. Looking forward to a wonderful 2022, and looking forward to seeing you again in Shanghai! ■ 国际合作传递了信息、 提供了舞台。 铸造是装备制造业发 展的重要环节,也是众 多主机和重大技术装备 发展的重要支撑,十四 五时期,铸造产业将加 快补齐产业发展短板, 完善自身产业链协同水 平,深化产业结构调整,转变行业发展方式,加速迈 向高质量发展。 2022年铸博会、压铸展将于2022年5月18-21日在 国家会展中心(上海)举办。期待美好的2022,期 待在上海再相见! ■
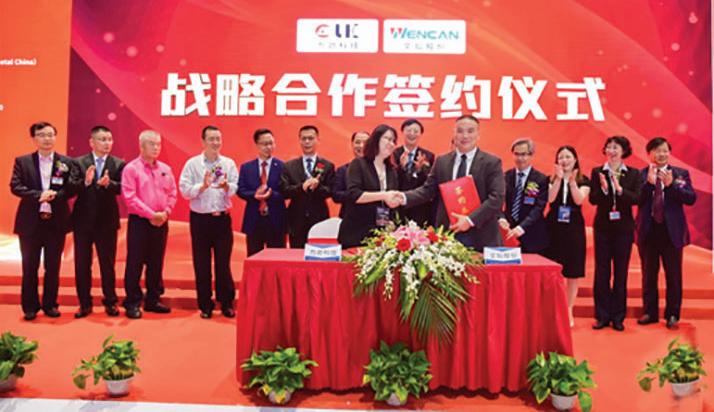
Chinese Foundry Industry Data Released 2020年度中国铸造行业数据发布
2020 was an extraordinary year—with normal control of the COVID-19 virus and resumption of work and production, the restoration of the economy has been sped up. At the same time, a number of favorable business policies such as fee and tax reduction have been issued. At the end of 2020, some of China’s economic indicators have returned to pre-epidemic levels, and the machinery industry has also recovered rapidly. Driven by the OEM industry, the total casting output will reach 51.95 million tons in 2020, a year-on-year increase of 6.6%.
From the perspective of changes in downstream industry demand:
• 1. In 2020, automobile production and sales are 25.225 million and 25.311 million, down 2.0% and 1.9% year-on-year respectively. Among them, the annual production and sales of passenger vehicles dropped significantly, with a decline of 6.5% and 6% year-on-year; driven by factors such as the elimination of National III vehicles, stricter regulations, and infrastructure investment, the production and sales of commercial vehicles in 2020 show a substantial increase, becoming an important driving force for the recovery of the auto market this year; driven by the substantial growth of commercial vehicles, the output of auto castings in 2020 increased by 5.6%. • 2. Due to the growth of large and medium tractors and other agricultural machinery, commercial vehicles, and construction machinery, the output of agricultural machinery and internal combustion engine castings increased by 4.9% in 2020; construction machinery continues to maintain a strong growth momentum in recent years, with castings increasing by 11.4%; power generation equipment castings (mainly in wind power equipment) have increased by 19.1%. • 3. Mining and metallurgical heavy machinery castings, machine tool castings, and casting pipes and pipe fittings maintain a certain degree of positive growth, 2.2%, 0.9% and 2.8% respectively; rail transit and ships remain stable, general machinery products and strategic emerging industries (such as robots) in 2020 have relative strong growth, and it has also driven the growth of castings. 2020年是不平凡的一年,在常态下疫情管控和复工复产 加快恢复经济秩序的同时,国家各部委陆续出台了如减费降 税等多项惠企政策。2020年年底,中国部分经济指标已经恢 复到疫情前的水平,机械工业也得到快速恢复。受下游主机 行业的带动,2020年我国铸件总产量达到5195万吨,同比 增长6.6%。
从下游行业需求变化来看:
1、2020年,汽车产销2522.5万辆和2531.1万辆,同比下 降2.0%和1.9%。其中乘用车年度产销同比下降较大,降 幅达到6.5%和6%;受国Ⅲ汽车淘汰、治超加严以及基建 投资等因素的拉动,商用车2020年全年产销呈现大幅增 长,成为2020年车市恢复的重要动力;受商用车大幅增 长的拉动,2020年汽车铸件产量增长5.6%。 2、由于2020年大中型拖拉机等农机及商用车、工程机械的 增长,农机和内燃机铸件产量增长4.9%;工程机械继续保 持近年来强劲的增长势头,铸件增长11.4%;发电设备铸 件(主要集中在风力发电设备)增长19.1%。 3、矿冶重机铸件、机床工具铸件和铸管及管件保持一定幅度 的正增长,分别为2.2%、0.9%和2.8%;轨道交通和船舶 保持平稳,2020年通用机械产品和战略新兴产业铸件( 如机器人等)增长较为强劲,也带动了铸件的增长。
从材质来看:
1、2020年商用车、工程机械和内燃机等的增长,带动 了灰铸铁的增长,灰铸铁产量占比为41.9%。
In 2020, all kinds of castings reach 51.95 million tons, a year-on-year increase of 6.6%.
2020年各类铸 件总产量5,195 万t,同比增长 6.6%。
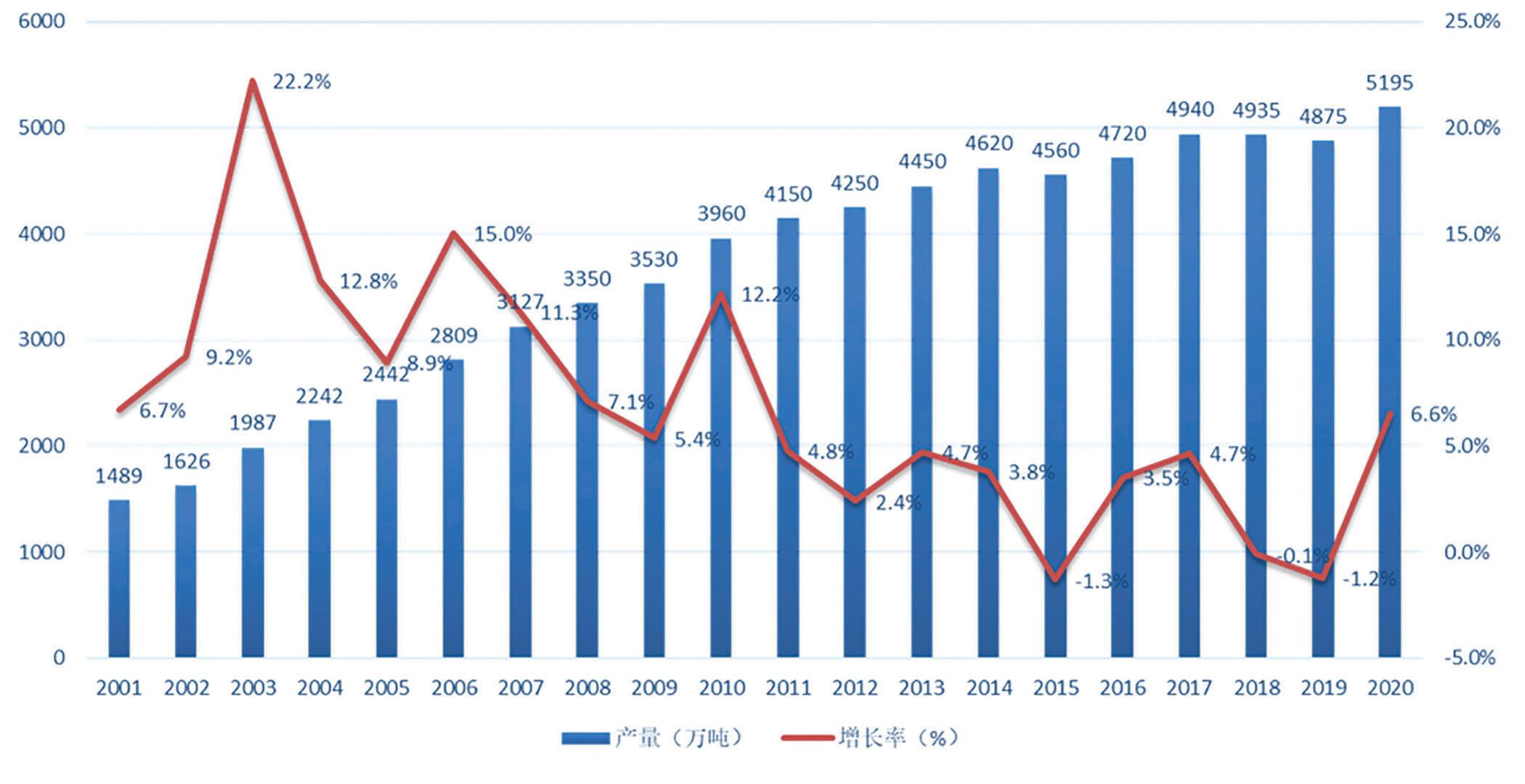
From the perspective of materials:
• 1. In 2020, the growth of commercial vehicles, construction machinery and internal combustion engines drove the growth of gray cast iron, which accounts for 41.9% of the output. • 2. Due to the increase in internal combustion engines, agricultural machinery, wind power castings, and cast pipes and pipe fittings, the output of ductile iron (including vermicular graphite cast iron) increased from 13.95 million tons in 2019 to 15.3 million tons in 2020, an increase of 9.7%. The production accounts for 29.5%. • 3. In 2020, the mining and metallurgical heavy machinery, construction machinery and power generation equipment industries grew, and the output of steel castings increased to 6.35 million tons, accounting for 12.2% of the output. • 4. In 2020, new energy vehicles, 5G and motorcycles drove the growth of aluminum alloys. However, due to the combined impact of the decline in passenger car production and the sharp decline in exports of aluminum wheels, aluminum (magnesium) alloy castings fell in 2020, with an output of 6.8 million tons. The proportion of production is lowered to 13.1%. • 5. Malleable cast iron and copper alloys increase slightly and overall output remain relatively stable.
Demand ratio of castings in downstream industries
Castings for power generation equipment and power industry, general machinery and emerging industries have increased their market shares.
The automobile industry is the largest user of castings.
In 2020, the proportion of automobile castings reached 28.9%. Because of the driving force of commercial vehicles, the output of castings increased by 5.63% compared with 2019.
Proportion of castings of various materials
• 1. The output of steel castings continued to grow, and the proportion in 2020 rose to 12.2% (11.7% in 2018; 12.1% in 2019). • 2. The proportion of aluminum (magnesium) alloy castings output was reduced to 13.1% (14.5% in 2018; 2019) 14.1% in the year). • 3. The output of ductile iron castings increased to 29.5% (27.7% in 2018; 28.6% in 2019). ■ 2、受内燃机、农机、风电铸件和铸管及管件增加等 的叠加影响,球墨铸铁(包括蠕墨铸铁)产量由 2019年1395万吨增长至2020年1530万吨,增长 9.7%,产量占比29.5%。 3、2020年矿冶重机、工程机械和发电设备等行业增 长,铸钢件产量增至635万吨,产量占比12.2%。 4、2020年新能源汽车、5G和摩托车带动了铝合金的 增长,但受乘用车产量下滑、铝制车轮出口大幅下 降的叠加影响,2020年铝(镁)合金铸件下降, 产量680万吨,产量占比下调至13.1%。 5、可锻铸铁和铜合金略有增长,产量总体保持相对 平稳。
下游行业铸件需求比例
铸件市场需求占比:发电设备及电力行业铸件和通用 机械及新兴产业等市场占比提升较大,铸件占比上升; 汽车工业是铸件最大需求用户,2020年汽车铸件占比为 28.9%,由于商用车的拉动作用,铸件产量较2019年增长 5.63%。
各类材质铸件占比
1. 铸钢件产量保持增长,2020年占比上升至12.2% (2018年为11.7%;2019年为12.1%); 2. 铝(镁)合金铸件产量占比下调至13.1%(2018年 为14.5%;2019年为14.1%); 3. 球墨铸铁件产量上升为29.5%(2018年为 27.7%;2019年为28.6%)。 ■
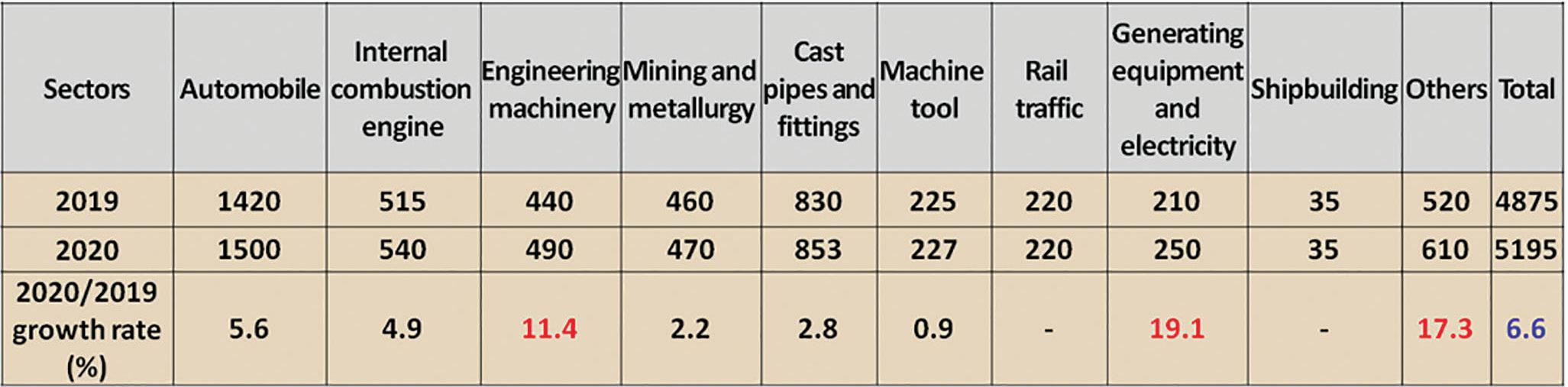
Product News Table of Contents 产品新闻目录
MOLD, CORE & SAND PREPARATION
Clutch & Brake Xchange Keeps California’s Ag Industry Moving With the Help of ESPRIT 33 Clutch & Brake Xchange在ESPRIT 的 帮助下保障加州的农业发展 Italpresse HPDC TF1850 Exhibited at DIECASTING CHINA 2021 1850吨压铸机惊艳亮相压铸及有色展览会 37
Global Foundry Group Grows Business With Sand 3D Printing Innovation 37 木村铸造集团通过砂型3D打印技术发展业务
MELTING, POURING & HEAT TREATMENT
Weijing Degating Hammer Used Worldwide 36 微晶气冲锤为何值得拥有?
Auto Heinen Recommends Latest Dosing Furnace Innovation From Strikowestofen 40 AUTO HEINEN向您推荐来自史杰克西的 最新定量炉创新技术
SOFTWARE KURTZ Powerboard in Production 38 KURTZ POWERBOARD投入应用
Stockton, California’s Clutch & Brake Xchange is a family-owned shop that provides the construction, agriculture, and other industries with the heavy-duty parts they need to stay in motion.
As a factory-authorized Permco Build Center, Clutch & Brake Xchange has the capacity to machine bare castings with three standards of SAE hydraulic ports. This special partnership enables the team to build and assemble nearly any combination of hydraulic gear pump the same day a customer places an order; rather than the six to eight-week turnaround time from the factory.
California’s Central Valley is an agricultural powerhouse, responsible for one-quarter of the food produced in the United States. Naturally, the region runs on tractors, trucks, and fluid power—and Clutch & Brake Xchange is one of the region’s most trusted suppliers for the vital parts this industry demands.
John Hitchcock joined his family’s business as an apprentice machinist three years ago. “I was a chef for 30 years but had to quit due to the extreme pressure. Joining the business was my brother’s idea—I had no clue what CAM was, so I just ran with it.”
John credits ESPRIT’s renowned customer support with making his career transition as seamless as possible. “We piloted three software programs and determined that ESPRIT CAM’s support was superior to that of any other company. We have not been disappointed in the product, support, or service.”
On the shop floor, John and the rest of the Clutch & Brake Xchange team work their magic on a Mazak Quick Turn 350MY, a Mazak VC-500C vertical machining center, a Mazak VCN-570 vertical mill, and a Haas TL3. Working primarily with aluminum, steel, and cast iron, John and his team use ESPRIT to replicate obsolete parts, like S-cams, that are vital to the heavy-haul industry.
An S-cam is a required part of a vehicle’s braking system, most commonly trucks and other heavy-duty machinery. An S-cam has a shaft that can be up to 25” long and an S-shaped cam on one end. As the 加利福尼亚州斯托克顿的 Clutch & Brake Xchange 公司是一家家族企业,为建筑、农业和其他行业提供保 持运转所需的大型零件。 作为工厂授权的泊姆克液压制造中心,Clutch & Brake Xchange有能力加工符合3个SAE标准的毛坯铸件 的液压端口。这种特殊的合作关系使团队能够在客户下 订单的同一天构建和组装几乎任何液压齿轮泵组合,而 不需要在工厂进行6-8周的周转。 加利福尼亚州的中央山谷是一个农业基地,美国约 四分之一的粮食产自这里。自然,该地区需要用到拖拉 机、卡车和流体机械,而Clutch & Brake Xchange是该 地区最值得信赖的供应商之一,可提供该行业所需的重 要零部件。 三年前,约翰•希区柯克作为学徒机械师加入了他的 家族企业。“我做了 30 年的厨师,但由于压力太大不 得不辞职。后来加入公司是我哥哥的主意,刚开始我并 不知道CAM是什么,所以我就跟着学。” 约翰将他的无缝职业转换归功于客户ESPRIT的支持。“ 我们试用了三个软件程序,并确定 ESPRIT CAM优于其他 公司。ESPRIT的产品、支持或服务没有让我们失望。” 在车间,约翰及Clutch & Brake Xchange团队的其 他成员在 Mazak Quick Turn 350MY、Mazak VC500C 立式加工中心、Mazak VCN-570 立式铣床和 Haas TL3 上展示了奇效。约翰和他的团队使用 ESPRIT 的技术复制旧零件,如 S 凸轮,主要材质为铝合金、钢 和铸铁,对重型运输行业至关重要。 S 形凸轮是车辆制动系统的必需部件,最常见的是 用于卡车和其他重型机 械。S形凸轮的轴最长可 达 25 英寸,一端有一 个 S 形凸轮。当轴转动 时,它将制动钳与制动 鼓连接起来以产生摩擦 并使车辆减速。 “重型起吊机有时 需要一种老式的S形凸 轮,”约翰说,“我父
John Hitchcock simulates a machining operation with ESPRIT 约翰•希区柯克使用 ESPRIT 模拟机加工操作。
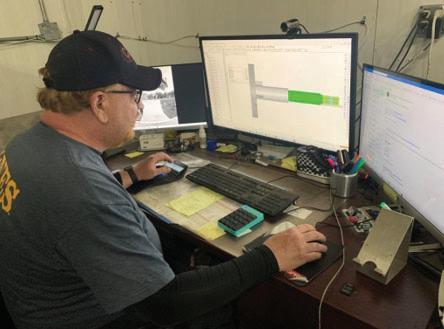
The Clutch & Brake Xchange team is a family-owned operation that makes durable parts for California's booming agriculture industry.
John Hitchcock, Apprentice Machinist, Clutch & Brake Xchange
In the photo above, the castings are semifinished. Says John, “I port according to the Permco code book and what the callout is.” Note: “Porting” refers to optimizing the shape of the ports through machining. “Callouts” are annotations that clarify vital machining information such as tolerances. Clutch & Brake Xchange 团队是家族企业,为加州 蓬勃发展的农业提供耐用 零件。
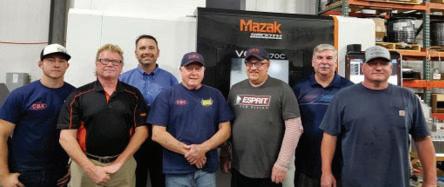
约翰•希区柯克是Clutch & Brake Xchange公 司的一名机械师学徒。
图中的铸件是半成品。约翰说:“我根据 泊姆克代码手册和标注内容进行端口操 作。”注:“端口操作”是指通过机械加 工优化端口的形状。“标注”是重要加工 信息(例如公差)的注释。
shaft turns, it connects the brake shoe with the drum to create friction and slow down the vehicle.
“Heavy-duty haulers were in need of an obsolete type of S-cam,” says John. “My father, who began his career as a truck driver and heavy-duty mechanic, recognized that there was a need for an S-cam. Without it, trucks would either need to retrofit their brake systems or convert the braking system altogether, which is a major expense. These trailers, many valued at more than $1 million, were essentially inoperable due to the strict safety guidelines outlined by DOT and state agencies. This S-cam was necessary to keep these trailers on the road without costly retrofitting expenses. “I was tasked with developing the program for this essential part. I faced challenges and enlisted the help and expertise of [ESPRIT application engineer] Spencer Hallin. I got to meet Spencer at ESPRIT World, and since then he’s been my mentor and friend. His support is spot-on and invaluable,” says John.
Spencer is more than happy to help. “John is an extremely receptive learner who constantly strives to increase his skills in programming and in manufacturing. He is a pleasure to work with, and I really look forward to seeing what he can accomplish.”
John is grateful for ESPRIT’s versatility when it comes to effectively serving his cus亲的职业生涯始于卡车司机和重型机械师,他意识到需 要S形凸轮。如果没有它,卡车要么需要改造他们的制 动系统,要么需要完全转换制动系统,这是一笔很大的 开支。由于DOT和州政府制定的严格安全准则,很多拖 车的价值超过100万美元,基本上无法运行。这个S形凸 轮是必要的,可以让这些拖车在路上行驶,而无需昂贵 的改装费用。” “我的任务是为这个重要部分开发程序。我直面挑 战并通过ESPRIT应用工程师斯宾塞寻求帮助和专业知 识。我在ESPRIT World认识了斯宾塞,从那时起他就 成了我的导师和朋友。他的支持是及时且无价的,”约 翰说。 斯宾塞非常乐意提供帮助。“约翰是一个非常容易接 受的学习者,他不断努力提高自己在编程和制造方面的 技能。和他一起工作很愉快,我真的很期待他取得更大 的成就。” 约翰感谢ESPRIT在有效地为客户提供 服务方面的灵活性。“通过与ESPRIT工 程师的咨询,我了解到这些部件非常复 杂,”约翰说,“这项工作没有蓝图。 我必须根据规格对每个S-cam CAD 和 CAM与工程师进行沟通。我永远不知道
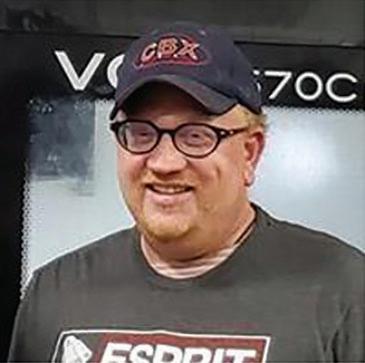
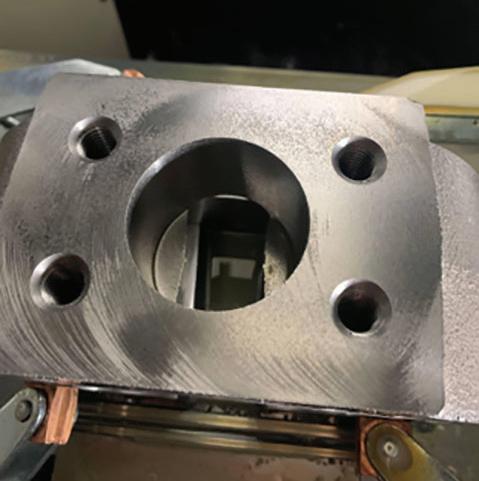