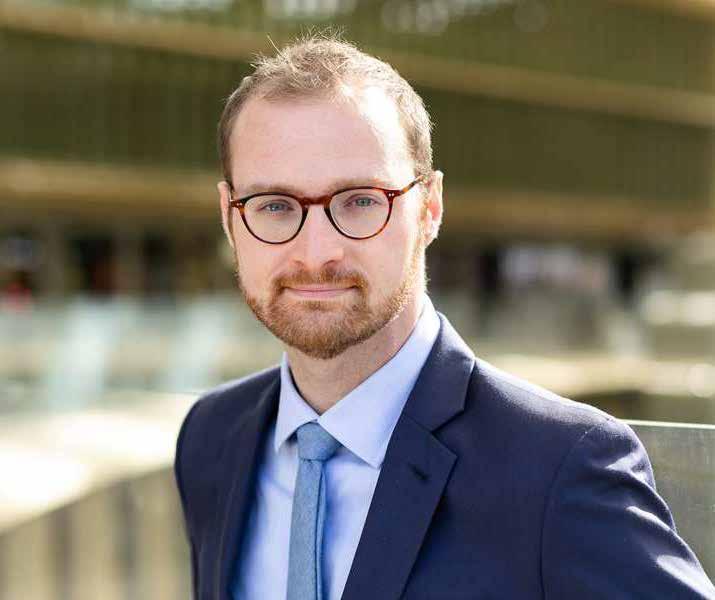
10 minute read
Savoye
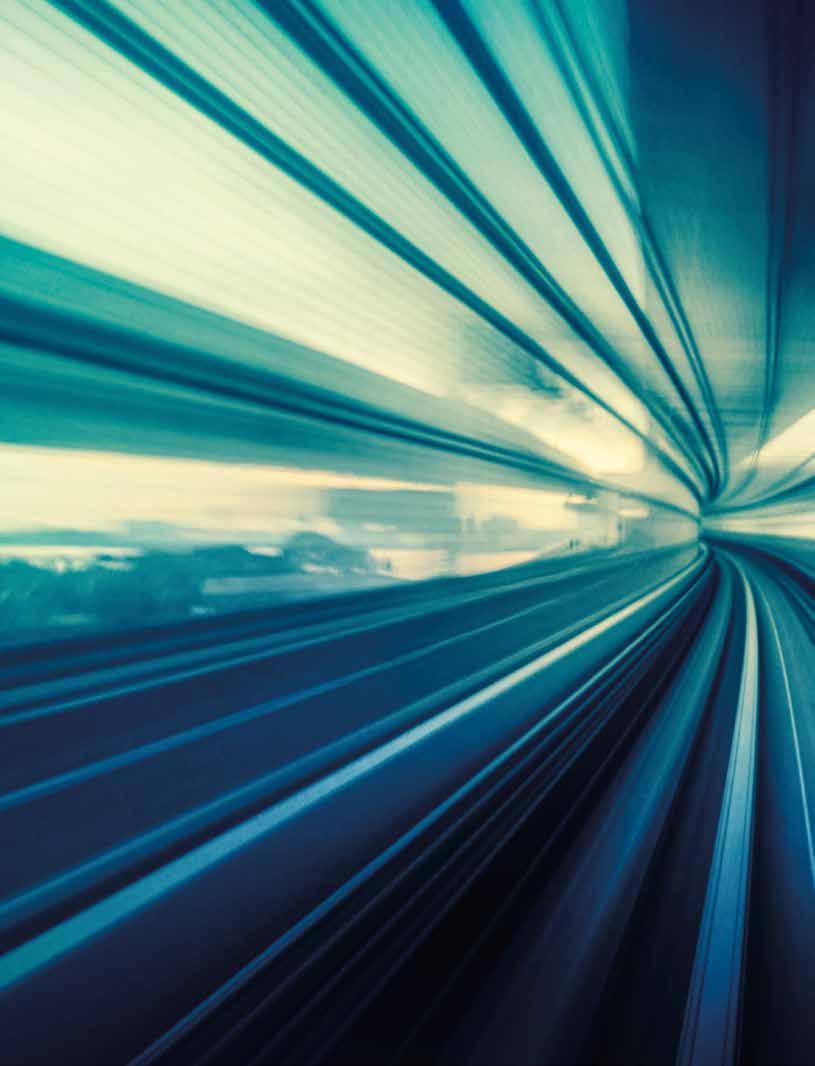
dynamic pricing and overbooking forecast are typical areas where we offer things others do not.
Fourthly, in connectivity. All our architecture is API-centric, which means every single data point belongs to a dedicated API. This allows to connect to any system more efficiently than in the past.
GSC: How will airlines, freight forwarders and other stakeholders benefit from the adoption of this mechanism?
NDT: I believe that working with a modern CMS is set to become a competitive advantage for airlines. They gain efficiency, and most importantly they become easier to work with.
I believe that in the future, if you do not have a CMS that offers such advantages as those I described earlier, you will gradually lose market share. Of course, that is not to say that success relies solely on a good CMS. However, as the cornerstone system of Air Cargo operations, it certainly is a strong asset for airlines to achieve their targets.
GSC: How well has the product been received since its launch? What feedback have you received?
NDT: We have just launched the first version of CargoStack, which we unveiled at Air Cargo India in Mumbai. The response we are getting is encouraging, and we got some useful feedback as well as to how we can further improve the solution moving forward.
GSC: Has any Middle Eastern Airline adopted or implemented this product suite thus far?
NDT: As I was stating, we just launched the product. At this time, we have already established multi-pronged relationships with airlines, and we are confident we can secure contracts soon.
GSC: What prospects do you foresee for CargoStack in the Middle East?
NDT: The Middle East is a region that is important for us: it is very dynamic and home to some of the biggest airlines in our industry, and we have customers in that region.
In addition, we have already identified leads in the area, that we believe could be great fits for CargoStack, so we will work hard in convincing them to partner with us.
GSC: How has the Wiremind Group performed in this fiscal year and what is the outlook for the remainder of the year?
NDT: The Wiremind Group has had a double-digit growth in revenue every year since its inception, and this fiscal year was no exception. Wiremind Cargo is somewhat of a specific case, given the fact we are investing to launch new products, so our focus right now is on delivery.
GSC: What are the challenges confronting CargoStack in its rollout?
NDT: The biggest one is definitely prioritization. We are aiming at making CargoStack the best system in the industry, so that comes with hard work, a lot of features to deploy and a very ambitious roadmap.
It also means you have to find the balance between contradicting factors: keeping a fast pace while taking the time to regularly ask feedback from your partners and customers, covering a large scope of capabilities while making sure you keep your focus on the aspects that create more value for the customers.
If you want to find that balance, you must apply fierce prioritization – a difficult but crucial process.
GSC: Is CargoStack an upgrade or will it entail the replacement of legacy systems?
NDT: CargoStack targets three types of clients: First, airlines that do not have any reservation system, and are looking to implement one. We provide consulting services for them as well. Second, airlines who do have a legacy system and are looking to transition to a modern SaaS system. Third, airlines who have a CMS but want to implement CargoStack modules, which can be acquired independently and plugged to any CMS. This is the case for example of our Revenue Management tool or our SkyPallet system.
An agreement was signed between Etihad Rail and Spain’s CAF for supplying, and maintaining passenger trains in the Sakamkam area, where the first passenger train station will be built in the heart of Fujairah city.

Sheikh Theyab Bin Mohamed bin Zayed Al Nahyan, Chairman of Abu Dhabi Crown Prince’s Court and Chairman of Etihad Rail, visited the final package of Stage Two of the UAE National Rail Network, which extends for 145km from Sharjah to Fujairah Port and Ras Al Khaimah, to review the progress of rail construction works in these Emirates.
During the visit, which started in Al Suyoh area in Sharjah and concluded in Sakamkam, the Chairman inspected key landmarks on the project’s route in the final package of Stage Two of the network starting with the rail bridge in Al Suyoh area in Sharjah, followed by a stop in Al Bithnah area in Fujairah to visit Al Bithnah bridge, then headed to visit a number of tunnels where he witnessed tracklaying works across the tunnels in Al Hajar Mountains in Fujairah.
Accompanied by HE Suhail Mohamed Faraj Al Mazrouei, Minister of Energy and Infrastructure, the Chairman witnessed the signing of an agreement between Etihad Rail and Spain’s CAF company, one of the world leaders in the railway sector, for designing, manufacturing, supplying, and maintaining passenger trains for the Etihad Rail project valued at US$ 326.7mn (AED 1.2bn)
The agreement, which emerged as a result of Etihad Rail’s success at the Middle East Rail 2022, was signed by Shadi Malak, CEO, Etihad Rail, and Josu Imaz, CEO, Rolling Stock, CAF, in the presence of HE Inigo de Palacio, Ambassador of Spain to the UAE, and officials from both sides. The agreement was signed in Sakamkam area, where the first passenger train station will be built in the heart of Fujairah city.
Chairman Theyab Bin Mohamed Bin Zayed oversees progress of Etihad Rail project
Etihad Rail Chairman witnessed the signing of agreement for manufacturing passenger trains valued at US$ 326.7mn
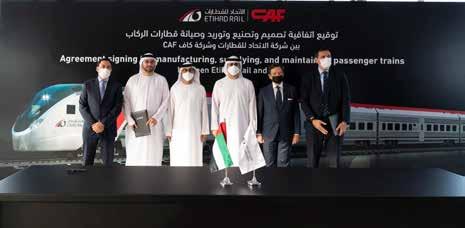
Etihad Rail Passenger Trains
The passenger train will connect eleven cities and regions in the UAE from Al Sila to Fujairah, including Al Ruwais, Al Mirfa, Dubai, Sharjah, Al Dhaid, and Abu Dhabi. Passenger services will allow travellers to plan their journeys between the Emirates and cities of the UAE more efficiently, from booking their tickets until they reach their final destination.
They will reduce commute time by 30-40% compared to other modes of transport, where travelling from Abu Dhabi to Dubai, and from Dubai to Fujairah, will take only 50 minutes only, travelling from Abu Dhabi to Al Ruwais will take 70 minutes only, while travelling from Abu Dhabi to Fujairah will take 100 minutes only.
The National Railway Network Stage Two
The National Rail Network’s route in the final package of Stage Two extends for 145km, connecting the borders of Dubai and Sharjah, going through Fujairah all the way to Ras Al Khaimah. It comprises 54 bridges and 20 wildlife crossing points.
It also has nine tunnels which extend for 6.9km through Al Hajar Mountains, including the largest heavy freight railway tunnel in the Arab Gulf which runs for 1.8km. The route is known for its distinct geographic location, being surrounded by mountains on all sides.
BITO experiences a resurgence with 2021 billed the most successful year thus far

Manufacturer upbeat about sales prospects and future potential
In a strong recognition of its products credentials, BITO was awarded the climate-neutral certificate. Furthermore, an extension and strengthening of the BITO Group Management, extension signals and reaffirms 2021 as the strongest year in company history with a turnover of EUR 303mn (US$ 318.25mn).
The past two years have been very challenging for logistics companies and providers of logistics services.
Border closures and supply chain disruptions because of the pandemic have shown how fragile supply networks can get from one moment to the next. Delivery delays have resulted in production stops or disruptions in trade chains.
Change of mindset
“We have noticed that the circumstances have led to a change of mindset in many companies. After the market had recovered from the initial shock, both internationally and nationally, the trend was clearly towards more stockpiling to cope with times like those caused by the pandemic. Companies were expanding their storage capacities, many new coordination centres have been established,” affirmed Winfried Schmuck, CEO, BITO-Lagertechnik.
In addition, some sectors, such as the online business, which has been booming for years anyway, continue to see enormous growth. This is a challenge that the companies concerned must cope with, especially in their organization. As a result, the demand for BITO storage and organization solutions has also increased significantly.
“We had the highest order intake since the company was founded, with full capacity utilisation in all areas. Tonnages were moved through the production halls that would have been unimaginable a few years ago. A great success that we were only able to achieve together in a well-functioning team,” added Schmuck.
BITO awarded the climate-neutral certificate
In addition to the turnover figures, there has also been a positive development in implementing even more sustainable practices. In 2021, BITO-Lagertechnik was certified as a climate-neutral company.
Winfried Schmuck “Sustainability has always been a priority for us. We are proud of our quality products which were designed to last. To name just a few aspects: BITO multi-trip bins and containers help to avoid tons of packaging waste. When selecting our raw materials and auxiliaries, we always opt for materials that are not harmful to health and that allow environmentally friendly processing,” asserted Schmuck.
“Our production process is based on a commitment to sustainability and a resource-saving, energy-efficient approach in order to minimise the impact on our environment while saving raw materials. We have been operating a plastic bin recycling process in our own facility for many years. Acting with economic, environmental, and social responsibility should not be viewed as an obligation. We see sustainability as a great opportunity for all of us,’’ he observed.
The BITO Group Management team extended
Meanwhile, BITO-Lagertechnik has also undergone some organisational changes in 2021 when the management team has been extended with the induction of two senior officials into key roles.
With Dominik Freyland-Mahling (COO) appointed for the production division and Uwe Sponheimer (CSO) appointed for the sales division, CEO Winfried Schmuck CEO will now be assisted by two long-standing executives from within the company to further professionalise the tasks and responsibilities of the three divisions.
“The extension of the management team enables us to focus even more closely on customer requirements,” assured Schmuck.
Eco-friendly plastic bins and containers support sustainable storage and handling
For many years, the concept of sustainability has been put into practice at BITO-Lagertechnik, supported by innovative technologies and state-of-the art machinery. Sustainable development requires a new mindset that affects the entire supply chain. In 2021, BITOLagertechnik was verified as climate-
neutral by TÜV Rheinland Group Carbon Services.
Energy-efficient manufacturing and ecological alternatives to virgin plastics
Users are more aware now than ever of the environmental impact of goods and services. In the field of storage, order picking and transport, as well as in production environments such as Kanban processes, reusable, sturdy, and reliable transport equipment have always been in demand in order to avoid packaging waste. Whereas the focus was on reducing costs in the past, the idea of sustainability is moving into the focus today.
Recycling and upcycling in BITO-owned facility
As a manufacturer, it is equally important for BITO-Lagertechnik to offer ecological alternatives to virgin plastic. Apart from reducing the environmental impact, using regranulated plastics increases energy efficiency in production. Every ton of polypropylene that is not produced saves 1.7 tons of carbon dioxide
Customisable divider systems and inlays with a perfect fit
Practical bin inserts, inlays and subdivisions also contribute to saving packaging waste. Therefore, BITO also focusses on developing new solutions in this field. Perfectly fitting divider systems such as lengthwise and crosswise dividers, push-fit accessories and insert boxes make sure that goods do not shift and get damaged during transport.
As a result, no additional disposable packaging, filling material or other protective materials are needed. There is now an ecological alternative to disposable packaging which not only provides optimum product protection during storage and transport, but also allows to place goods in a space-saving way.
Bins made from sunflower compound
A clever alternative to conventional polypropylene (PP) is Sunflower Compound (SFC), an environmentally friendly material which has been used since 2018 to manufacture BITO C-item bins. No food must be used to obtain sunflower seed shells, nor are additional cultivation areas required, as the shells are a by-product of sunflower seed production.
This new material is a mixture of PP and sunflower seed shell fibres, a food industry waste product. Making a product from sunflower compound produces significantly fewer emissions than making a product from 100% polypropylene, since the compound is processed at lower temperatures than PP. By buying a sunflower compound product, customers will help to reduce their carbon footprint.
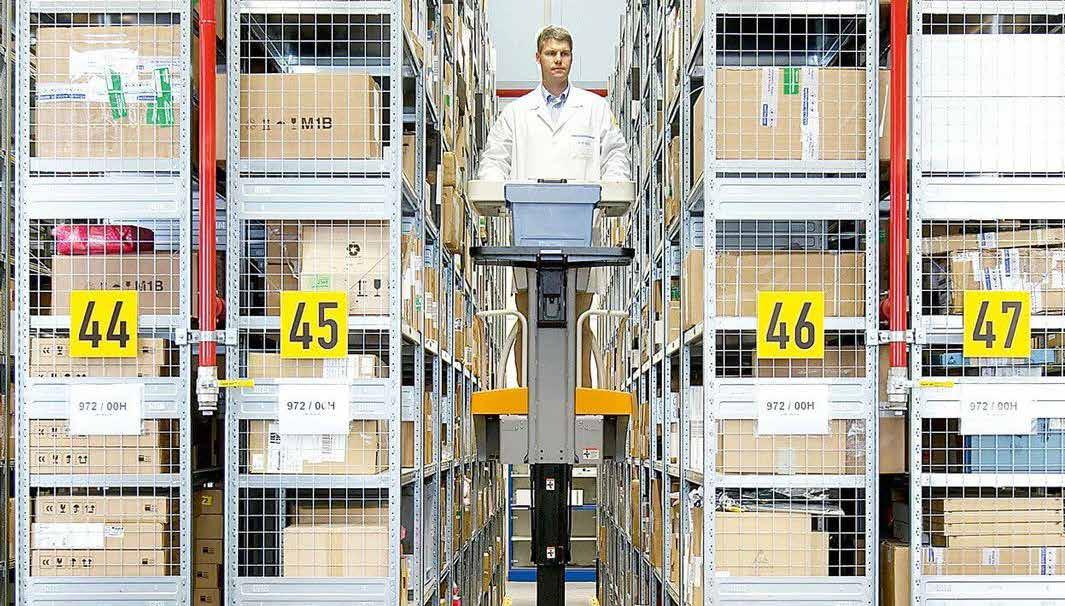