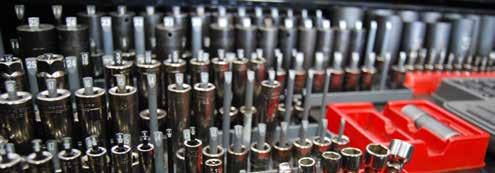
14 minute read
Are print consumables consuming your profits?
The keys to success are proactive press maintenance, understanding the overall value of consumables in your offset production processes, and managing costs while maintaining print quality.
You’ve likely heard the cliché “if it isn't broken, don't fix it.” This might be the norm in other industries, but in offset printing, it’s a recipe for future disaster. Today’s offset presses are masterpieces of complex technology that have genuinely earned the characterization “workhorses.” Your press might be running just fine today, but unless you perform regular, proactive maintenance checks, it could cost you thousands of dollars in downtime tomorrow. Proactive maintenance checks are pre-emptive strategies designed to eliminate every possible repair that might adversely affect print quality, reduce press speed, increase waste and makeready times, require additional staffing, and so on. If these issues remain unchecked as you meet your hectic day-to-day deadlines, then you’re courting disaster. Maintenance and repairs
Advertisement
Most successful printers have established a proactive, preventative maintenance program – and they stick to it. Some even train pressroom employees in all aspects of hardware maintenance, establish an on-site spare parts and consumables inventory, institute procedures where repairs are identified quickly, and develop a daily maintenance log of jobs in progress. This log should contain not just production analytics like counts, waste and makeready times, but also alerts on delaying factors such as web breaks, press breakdowns and slowdowns. Art Andrews, owner of Arcade Printing in Toronto, whose main press is an RMGT offset from Ryobi, echoed those comments – but added that press operators should also be involved in the buying decisions of consumables. “I leave many of the purchasing decisions regarding consumables, including inks and plate sourcing, to my experienced frontline press operators who’ve had decades of experience with different products and suppliers. They know what works best on-press. For us, repairs are still the most costly issues. So involving press operators in decision-making and relying on their expertise has kept those costs low. Another strategy that has been successful for us is the management of waste. For example, we’ve been selling endof-life printing plates for scrap for over 40 years. Even small day-to-day costsaving strategies like that certainly add up at the end of the year,” he added. Here’s a brief update on pressroom consumables and issues that affect production and profits.
Pressroom chemicals
“Preventative and scheduled maintenance are the key to achieving the maximum benefits from your fountain solution system especially when it comes to having well maintained water tank(s), water lines, water pans and rollers by deglazing them on a regular basis,” said Mike Thibault, Vice President of Technical Services at Unigraph International, Canada’s leading pressroom chemical manufacturer. “These can affect ink/water balance, drying times, colour consistency and the ability to have repeatable, predictable results on press. Regular preventative maintenance can be integrated into a weekly schedule without affecting production deadlines. The costs are small compared to the enormous gains in productivity,” he added. Daily monitoring of the pH, conductivity and Brix are essential to understanding how well your press chemistry is performing. Always start with a fresh mix and take those values. As the days and week go on, it’s normal to have a rise in all three. As you do this on a consistent basis, the press operator will be able to determine how well the chemistry is working and take action accordingly. Understanding how certain inks and stocks affect the chemistry is essential in order to have the most stability on press. Pressroom chemicals are essential to the efficient running of an offset press. These can include fountain solutions and additives, alcohol replacements, press wash-up products (including roller and blanket washes) silicones (for heatset web presses) and specialty products such as roller deglazers, plate cleaners, chrome roller cleaners/desensitizers and more. This brings us to our next and often overlooked factor – cost per printed page. “If you buy everything on up-front price without a guarantee of on-press performance, you’re playing a risky game,” Thibault pointed out. “For example, in some cases just changing to a premium fountain solution and alcohol replacement can lower a printer’s ink bill by 5% to 10%, while also reducing paper waste. As well, significant savings on filters for the water system can result. Our products reduce cost per page, improve print quality and provide greater stability on press.
They can remedy common problems such as calcium carbonate build-up and contamination, drying issues, picture framing, dirty water system/back cylinders, blankets and metering rollers. “We are always following market trends and developing new products to complement process-free plates, HUV and LED inks,” said John Thibault, President at Unigraph International. “Our R&D department is continuously working with our production department to develop, test and bring new innovations to the pressroom. We are always looking to add quality products to our portfolio to increase productivity and reduce costs in the pressroom. We’ve been doing this since 1982 – and our focus has never changed,” he added.
Plates
A common error here is confusing the cost of individual plates with the overall cost of plate production. It can be deceiving because it’s the overall cost of use that actually affects profitability, not just the individual plate price. Printers may also needlessly pay thousands more each year on chemistry consumption and labour. For example, if a processing system is cleaned every 4,000 m2 but is being
High-Performance Printing Chemicals
replaced by a system that must be changed every 1,000 m2, cleaning, labour, filling costs and downtime increase by 300%. Also, expensive effluent treatment and removal should be considered. A second common error is failing to plan a transition for your pressroom. All plates are not equal. Each plate has different emulsion and plate-graining characteristics. These affect ink/water balance, tone reproduction, dot gain, run life, handling, paper waste and overall print performance. Plan a complete print comparison test and learn the differences between what you currently use and any new plate products. When choosing a plate supplier, ensure that they can install, service and support your current processing line, are located in Canada, carry a full range of spare parts here, can respond quickly to your needs, and fully understands all aspects of prepress and pressroomrelated support – including on-press troubleshooting. Next, the use of process-free plates, especially from the industry’s leading players – Agfa, Kodak and Fujifilm – continues to impress. Why? For starters, chemical and disposal purchases are no longer necessary, plus the cost of buying film and the equipment to develop it, are no longer needed. Eliminating the use of chemicals also reduces employee health risks. These plates offer longer run lengths, usually from
As we struggle through these challenging times together, our technical team is at the ready. 50,000 to 250,000 impressions. Chemistryfree plates also provide
Rest assured we will always be here higher sensitivity and to support now and in your pressroom needs, a post-pandemic world. throughput per hour. Shops switching from Words alone cannot express our gratitude conventional CTP systo our dedicated dealers and printers, tems to chemistry-free for their loyalty and their business. can also use their existing
We’ve been proudly serving the plate processors for Canadian printing community since 1982, plate heating and gumand we promise to continue that tradition. ming after imaging.
So from our family to yours, The chemistry is simply please be well, stay safe and stay positive. removed from the pro-
Better days are on the horizon. cessor. Watch for more about chemistry-free plates in our April printed issue. Blankets

The most important advance in recent years has been the rollout of Landa Nanographic printing presses. Their use of specially-treated blankets utilizes breakthrough technology to ensure an optimal image – including the full image transfer to the paper, the prevention of any ink residues, and a smooth and stable blanket motion. Their design enables the transfer of NanoInk ink drops to the various substrates without leaving a trace on the blanket. This ensures that the full image is transferred without any distortions and, most importantly, that the blanket remains completely clean and ready to receive the next image. The estimated life of these blankets, at last count, was about 500,000 sheets. One Canadian company active in this sector is Vancouver-based Enviro Image Solutions (EIS). For the past several years, through its blanket-rejuvenation program, EIS has helped printers reuse blankets up to 12 times. The company has some helpful advice. First, reduce blanket usage by ensuring that your mechanical blanket washer device is regularly maintained and free of dry, abrasive ink contaminants. Next, go back to the basics of a dry substrate run without impressions when moving over to new sheet sizes. Most substrate-related blanket smashes occur at the beginning of the run, so this saves production time as well as blankets. Lastly, after a mechanical blanket wash, inspect your first few blankets for build-up around the outside edges of the substrate area known as a paper line, that, when left on the blanket, could score and even cut it!
Substrates
Commercial printers today continue to look for guarantees when it comes to a substrate’s runability, printability, shade, smoothness – anything that might affect production, overall workflow and image quality. Ergo, leading press manufacturers have gone to great lengths to certify or recommend certain substrates for maximum on-press performance. And there are literally thousands of choices out there, especially for inkjet. We’ve also seen an
increase in the use of synthetic substrates. These papers are often lightweight with high opacity, and can play an especially unique role in packaging. In general, synthetic papers combine the versatility of traditional paper with the durability of plastic, which makes them ideal for outdoor applications. They can be environmentally friendly, waterproof, more durable than traditional papers, flexible, foldable and can even hold colours well, regardless of the printing process used. For printers who deal in smaller runs, specialty substrates are becoming increasingly popular because they can differentiate print customers from their competitors via sensory and aesthetic appeal. Some papers, such as Neenah’s Elevate Your Brand media for premium packaging, are quite stunning – and are aimed at designers as much as commercial printers. Bottom line: the growing demand for specialty substrates that can change a customer’s interaction with the printed piece – in other words a material that’s more than just regular paper – adds enormous value for the end user.
One recent development of note is the Substrate Bank, a new online tool to source printing substrates launched in January in the Netherlands. The platform brings together print-media manufacturers and their products on a B2B industry platform, making the sourcing and specifying of substrates easy, fast and transparent. The Substrate Bank takes into account the intended use to find and source products digitally. Users of the platform can easily source substrates via industry-specific search criteria. After registration, they can even connect with manufacturers directly – to request samples, ask for directions to the nearest distributor, learn about print settings and receive technical datasheets, etc. As we all know, substrates (especially paper) represent a major expense. So always buy your paper from a merchant who offers you a guarantee regarding runability, printability, smoothness and so on. This way you’re sure of getting the right paper cut from the master rolls of the same shade and production lot. Also, remember that each lot likely has a shade variation, though minor. Also, some papers might be converted locally and may contain more dust that will affect productivity in the long run, and might result in more blanket changes. Finally, don’t open skids unless you’re going to use the paper immediately, to ensure uniform moisture consumption. Paper, especially board, can curl from the edges. This could affect your ability to print at the required speed, which in turn impacts productivity.

Inks
Generally speaking, ink formulation depends on the printing technology, namely the application technique to the substrate (offset, flexography, gravure, inkjet) and the drying mechanism of the solvent (evaporation, absorption into the substrate, oxidative drying, or curing by irradiating energy such as UV light or an electron beam). For example, an ink to be UV-cured may consist of monomers and pre-polymers such as acrylates, pigments, photo-initiators and additives (i.e. surfaceactive substances, waxes, silicones and curing inhibitors). What does all this mean for the average print provider? If you’re in doubt in any way, always seek advice first from your ink manufacturer, and second from your OEM. For commercial printers, two emerging trends here are an increase in flexographic printing inks and the continuing shift towards environmentally-friendly inks demanded by the end user – such as waterbased products which have fewer toxic effects when compared to conventional printing inks. Also, as more sophisticated presses emerge, inks are becoming more specialized, especially for wideformat inkjet and textile printing. Equally important in this space is technology that controls the amount of ink used for any given print project. Common devices that reduce ink waste and costs are ink dispensers, ink levelers and ink agitators. In the end, it’s all about cutting costs by reducing consumable and substrate waste while maintaining print quality. Even software can play a part. For example, Agfa’s InkTune allows for better control over printing resources and standards. The software can optimize print performance, reduce production costs and lower total cost of ownership. This intelligent tool is part of Agfa’s ECO³ platform that gives printers more control – from ink use to compliance with ISO, G7 and client-specific standards – while reducing production costs. The OEM’s focus on Ecology, Economy and Extra Convenience (ECO³) make prepress and printing operations cleaner, more costeffective and easier to manage and maintain. This isn’t surprising, given that Agfa-Gevaert has a long tradition of lowink laydown technology built in to its ‘workhorse’ wide-format printers.
Tony Curcio Editor, Graphic Arts Magazine tony@graphicartsmag.com
Flash Reproductions installs first Valiani Omnia in North America from Sydney Stone
Print-finishing leader Sydney Stone (Mississauga, ON), Canada’s exclusive Valiani Omnia dealer, has announced the first North American installation at Flash Reproductions (Etobicoke, ON). The Valiani Omnia (VO) flatbed die cutter automatically feeds and contours cut media. The operator can load material up to 60 cm x 80 cm. Omnia will feed media to the cutting arm using a suction system that lifts media from the feeder and drags it onto the conveyor. The feeder holds up to 500 sheets, depending on media thickness. Once in position, the camera will detect crop marks and execute the cut file for the pre-printed graphics. The completed sheets drop into the catch tray. A wide array of tools handles many applications and substrates – including bevel cut 40 or 45 degree, embossing/debossing, creasing, kiss cuts, and style pens in three different sizes. “Our purchase of the Valiani Omnia die cutter stemmed from the equipment’s multiple industry-leading attributes,” said Rich Pauptit, President of Flash Reproductions. “Topping our list is the near-infinite flexibility of contour cuts that cover a wide range of substrates – from text-weight paper grades to heavy-gauge corrugated board. Its cutting flexibility with a highly adaptable media gamut paves the way for Flash to expand our range of signage and POP offerings. Compatibility with our existing KM1 digital press is optimal in terms of maximum sheet size (60 cm x 80 cm), allowing us to press the limits of this formidable combination of technologies. Lastly, VO’s Auto Load capability frees up our operator, allowing for increased productivity.” The software can control multiple workflows – including cut files from various graphic design software, QR code mode and non-printed material. Omnia is ideal for die cutting cardstock projects including packaging, business cards and kiss-cut. It can also process heavy materials such as corrugated cardboard, chipboard or thin plastic sheets.
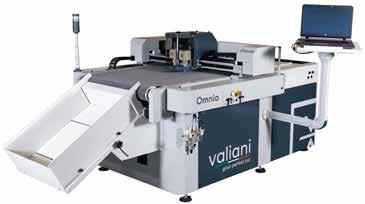
Valiani Omnia automated flatbed die cutter
Alain Deschamp, owner of Albion Screen Printing, beside his new Esko Kongsberg C24 Digital Cutter from Agfa Canada.
AGFA and Esko install Esko Kongsberg C24 finishing solution at Albion Screen Printing
Albion Screen Printing (Gatineau, Quebec) has invested in a new Esko Kongsberg C24 Digital Cutting solution from Agfa Canada. This investment has allowed Albion to considerably increase the productivity in its finishing operations. “The added value of the Kongsberg table lies in the service and the robustness of the equipment,” said Alain Deschamp, owner of Albion Screen Printing. “The 3 kW motor in the router allows us to cut materials like acrylic, much faster.” Albion specializes in a huge array of wide-format products – including banners, posters, signage, fleet graphics, window / wall decorations and POP/POS displays, as well as decals, promotional products and nameplates and tags. Albion also provides a wide range of client services – from screen and digital printing, die cutting, installations, distribution packaging and more, to rapid and accurate estimating, on-time shipments and reliable installations.
The carbon fibre traverse of 3.2 m makes the Kongsberg C Series of digital cutters uniquely equipped for high speeds. Its rigid quality makes it possible to maintain consistent accuracy on all materials. It also minimizes deflection when carrying heavy tooling or creasing with high down force. The series is the only super-wide finisher with a powerful 3 kW continuous-duty, high-performance milling unit. It can be configured for milling applications ranging from sporadic, light-duty routing, to lengthy jobs working with dense materials – all while boosting exceptional productivity. Its heavy-duty Tool Unit offers 500N (110 lbs) of down force, sufficient to crease even the most challenging materials at large diameter creasing dimensions (150 mm). The Kongsberg C series can also be outfitted with a wide-format roll feeder to support heavy-duty rolls of materials such as textiles and vinyls up to 3,330 mm (131”) wide.
