
5 minute read
Paper mill leads water stewardship
By: Lisa Bauer-Lotto, M.S., Corporate Director, Environment & Sustainability, Green Bay Packaging Inc.
For strategic growth, Green Bay Packaging Inc. (GBP) constructed a new 100% recycled paper mill in Green Bay that uses recycled old corrugated containers (OCC) and mixed office paper to produce paper used to make packaging and boxes. The new mill was a substantial investment, not just in the productive capacity of the mill and quality of our products, but importantly in the company’s sustainability efforts. It reflects fidelity to GBP’s deep heritage of environmental stewardship and its commitment to an environmentally sustainable future.
We are seeing a shift in customer and stakeholder interest toward increased sustainability attributes of their products and their desire to align with likeminded sustainable supply chain partners, like GBP. In a visible example of this interest, we have seen a blossom of tours by customers, other paper mills, supply partners, community and education stakeholders that wish to see first-hand the technology and advanced sustainability performance of the next level for papermaking at our Green Bay mill.
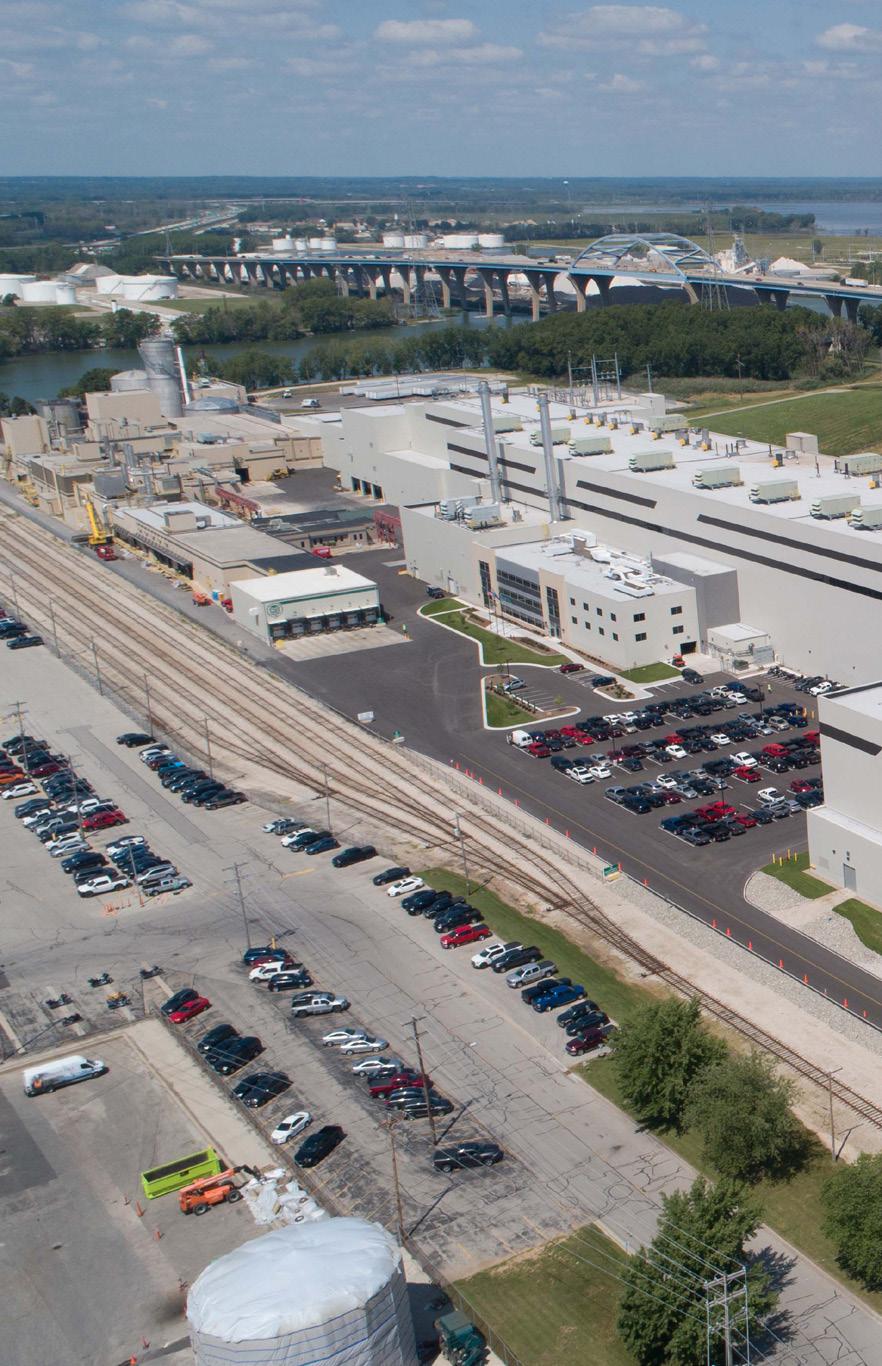
One of these industry leading advancements drawing attention is the mill’s use of “reclaimed” water and its circular water system, where municipal wastewater is recovered and treated by GBP for further reuse. A portion of the Green Bay mill make-up process water is piped from the municipal wastewater discharge (NEW Water) with additional treatment for continued use in our papermaking. The reclaimed wastewater replaces water volume that otherwise would be city’s freshwater (tap water) supply. A water system that fully counterbalances its freshwater demand through the use (and reuse) of reclaimed water is known as a “net zero” water system. The GBP Green Bay mill is the first in the world to achieve third-party validation as a net zero water operation, by United Laboratories (UL). In 2022 alone, the water saving innovation of the circular reclaimed water system and advanced technology reduced use of water from Lake Michigan by more than 200 million gallons. It resulted in 30% less water use per ton of paper production.
Paper mills are water intensive and highly reliant on water sourcing which, makes net zero water use in a papermill setting a seminal achievement. Water as the lifeblood of papermaking, transports the paper fiber through the papermaking process, with the paper starting as 99% water and 1% fiber and the final product consisting of approximately 8% moisture. GBP chose to be more water resilient with reclaimed water use and avoid the need for any direct intake or discharge to the adjacent Fox River. In addition to the efficiency gains and the importance of water stewardship to the company, it was a key decision for the longterm strategy of the mill sustainable water program to incorporate reclaimed water due to the increasing regulatory uncertainty in this area. Attributed to water treatment removal efficiencies, our reclaimed water system has resulted in 64% less BOD and 73% less TSS per ton of paper production. Using an alternative (reclaimed) water supply also benefits the shared local water resource, protecting water quality.
Paper is a sustainable product of nature sourced from responsibly managed forests. The trees are grown and nurtured like a crop in tree farms. Paper is renewable, recyclable and wood fiber regenerative. The forests have sustainable green attributes during the years of growth absorbing the greenhouse gas carbon dioxide (carbon sequestration) and in final products (carbon storage). For the corrugated packaging industry to remain sustainable we rely on virgin wood fiber inputs; without virgin fiber from trees recycled fiber (paper) would not exist. Boxes can be recycled about seven times– seven lives!
Advancing water stewardship of paper mill water systems pays homage to the Kress family’s vision, starting with its founder George Kress. The Green Bay mill was the first in the world to have a closed process-water-loop in the early 1990s and was featured in a National Geographic article on The Magic of Paper, March 1997. In 2022, the GBP Green Bay mill was recognized for sustainable circularity and water stewardship on many levels to include the Wisconsin Sustainable Business Council’s 2022 Sustainable Product of the Year, Clean Water Action Council award to Will Kress as Environmental Citizen of the Year and American Forest and Paper Association peer industry award for Leadership in Sustainability.

The success of any good sustainability investment for change should be measured not in awards received but in gallons, energy, and waste. The overall sustainability performance of the mill investment has reduced impacts by 25% less greenhouse gas, 12% less energy, 30% less water and 33% less waste per ton paper production. These reductions are assurance of GBP’s sustainability commitment on transformative manufacturing through product innovation, technology and pioneering ‘out-of-the box’ advancements into our products.
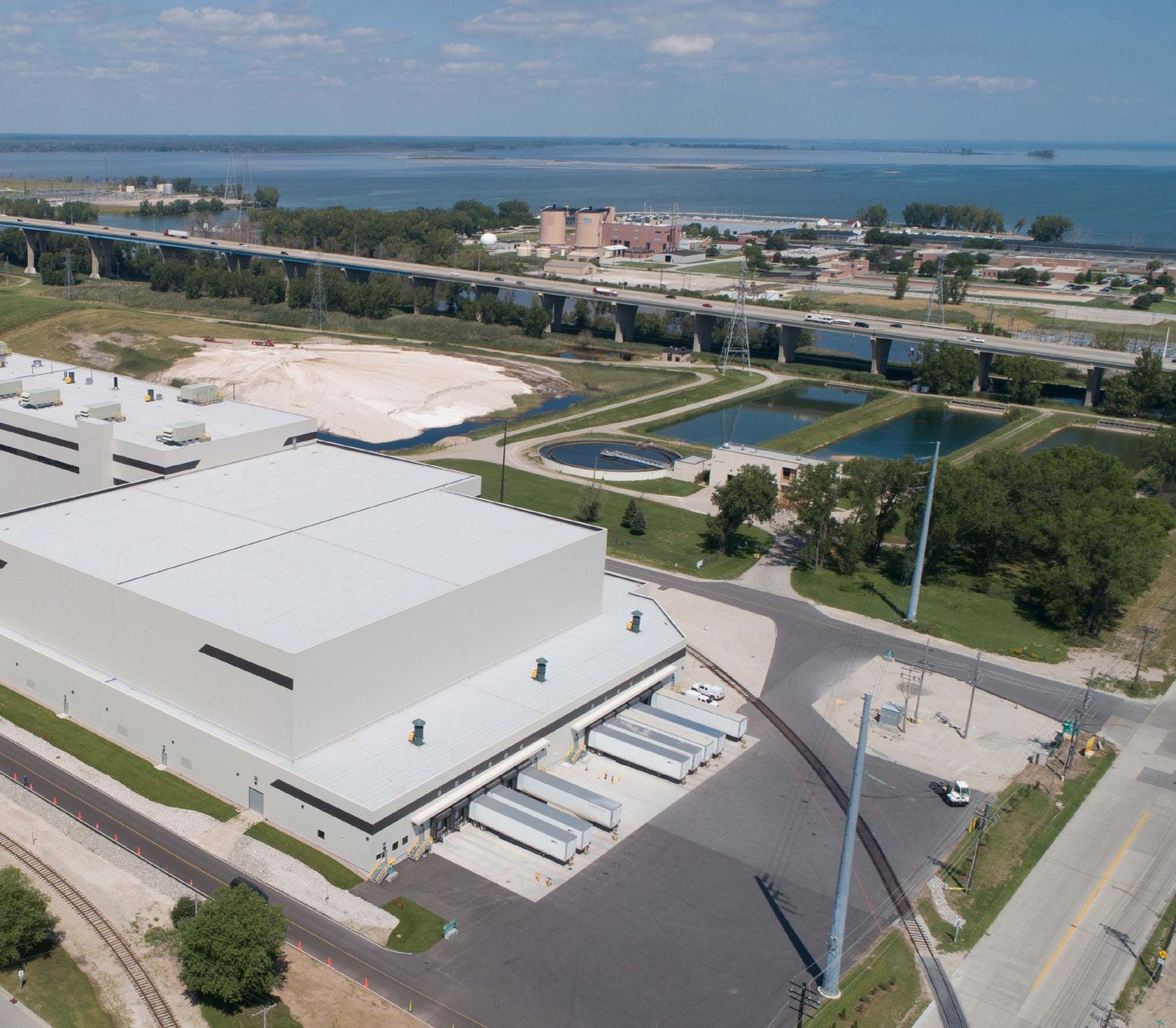
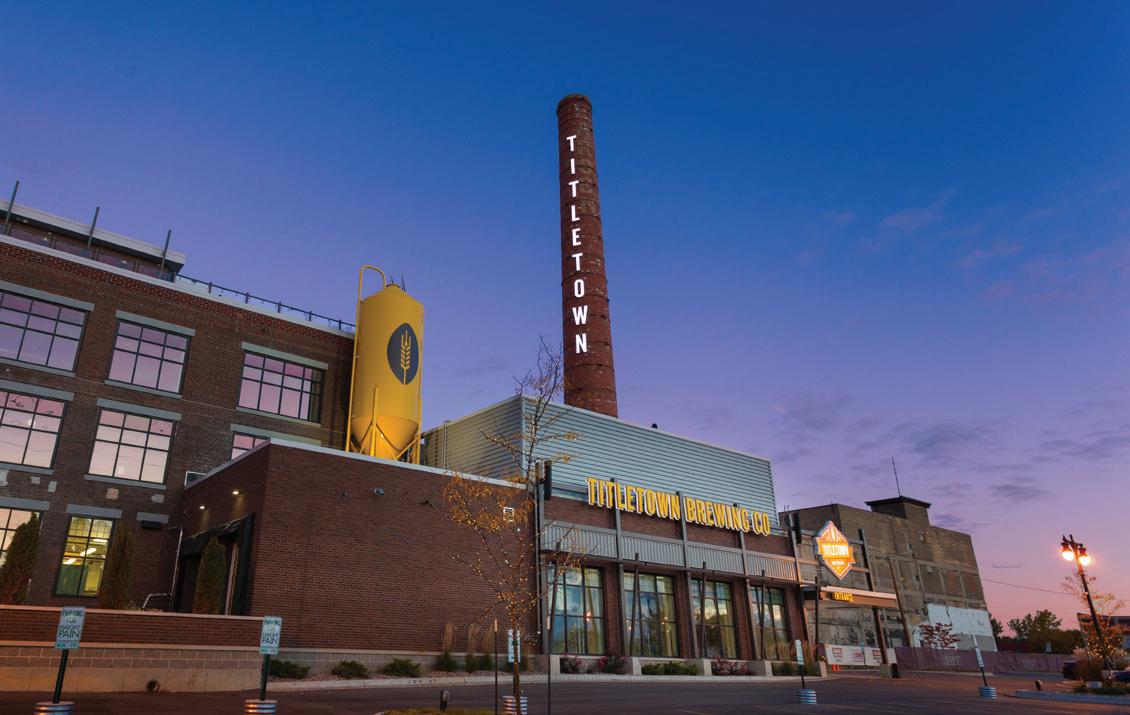
At Miron Construction, our project teams leverage a deep bench of experience to live out our commitment to excellence in everything we do. Engaging multiple stakeholders, partners, technology suppliers, and skilled craftspeople, we rally together and work as a team to get the job done. In the end, what means the most to us is celebrating our successes together, sharing in the sense of accomplishment and comradery we have built along the way.
Together, we are Building Excellence.

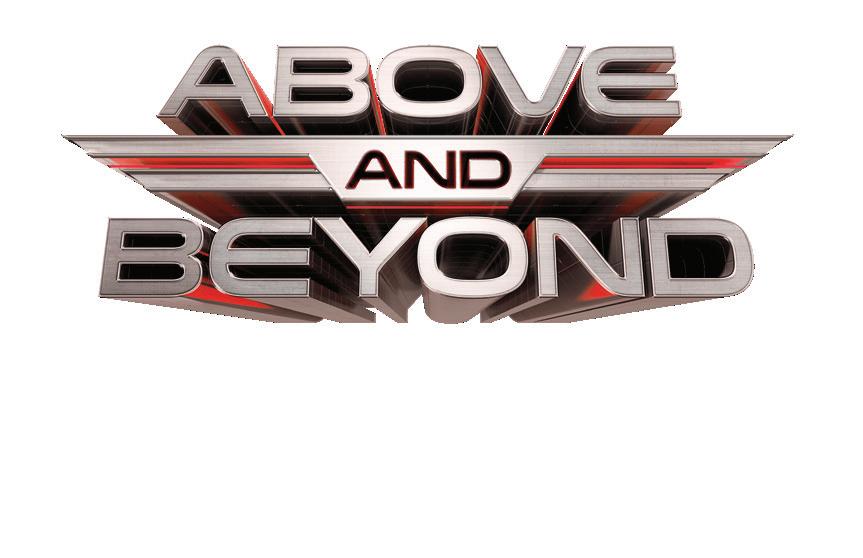
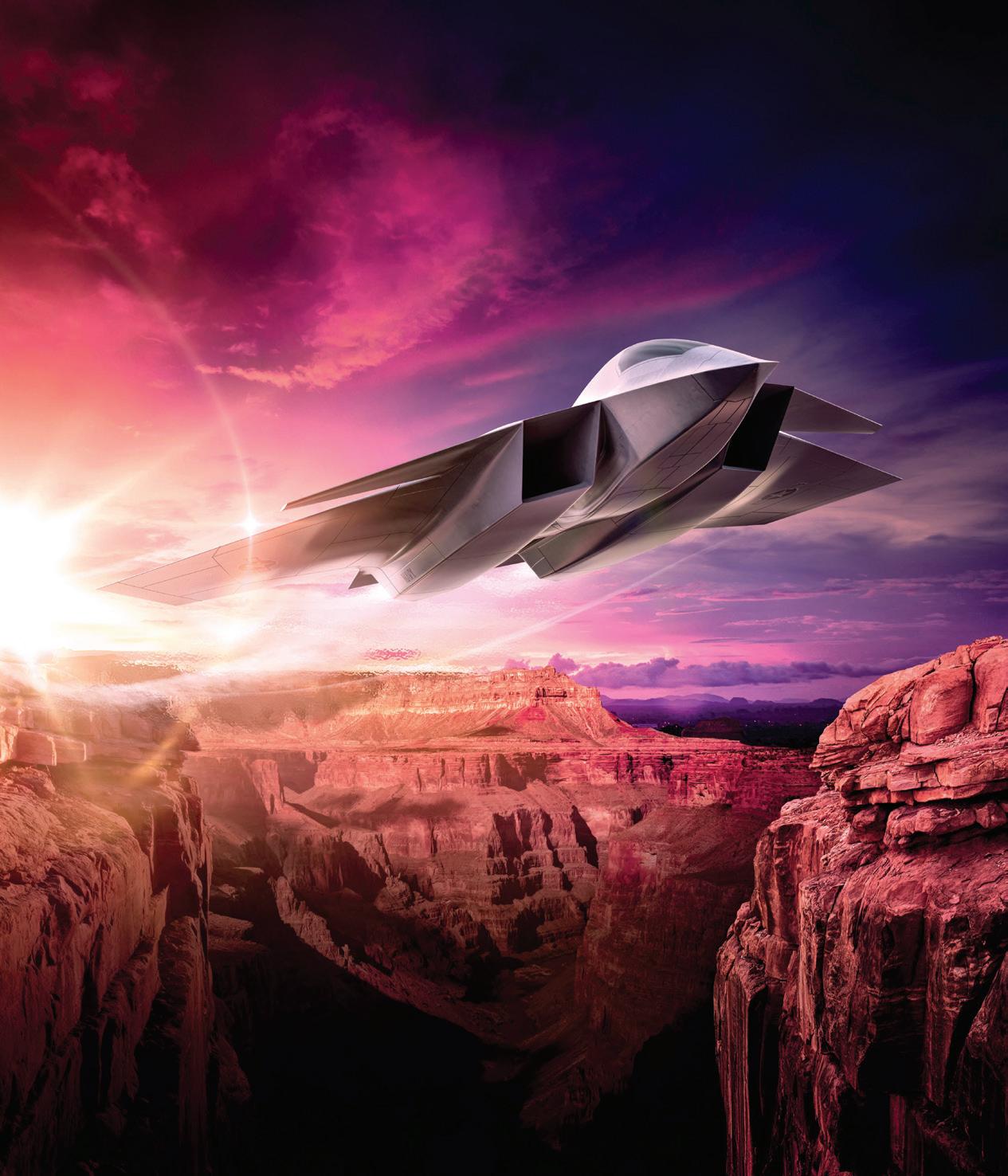
Sanimax and the original recycling industry
By: Donn Johnson, Vice President U.S. Manufacturing, Sanimax
As a business that specializes in rendering, Sanimax has played a key role in the food supply chain since becoming a member of the Green Bay community in 1881.
Rendering is known as the original recycling industry. Every day Sanimax transports millions of pounds of agri-food by-products representing the roughly 50% of the animal that is considered inedible by U.S. standards. At the Green Bay facility, the by-products are transformed into two main products: proteins that are used to create livestock feed, and fat that is used to make a variety of everyday items including renewable fuel. On an annual basis, Sanimax-Green Bay transforms enough material to fill semitrucks stretching from Green Bay to Orlando, Florida. In the U.S., renderers collect 56 billion pounds of by-products annually. Without the rendering industry, landfills across the U.S. would be filled in approximately four years.
Sanimax is dedicated to reducing the environmental footprint, constantly looking for new ways to make rendering more sustainable. This led Sanimax to finding alternatives to reusing water, which helped reduce water consumption by more than 8.25 million gallons per year. In the U.S. annually, 3.7 billion gallons of water are reclaimed during the rendering process and returned to natural resources.
As Sanimax continues looking for ways to find environmental efficiencies, a process was implemented to preheat water going to the boiler. The preheated water reduced natural gas consumption. As a result, the amount of natural gas saved is the same as heating 1,500 residential homes for an entire year.

The fat produced during the rendering process is used by companies to make everyday items like tires, wax crayons, lubricants, and more. However, the most prevalent use of rendered fat is to create renewable diesel. In fact, almost 20% of the material used to make these biofuels comes from fats and oils supplied by the rendering industry. Sanimax-Green Bay produces in excess of 75,000 tons of fat annually, which can be converted into renewable diesel. In the U.S. over 778,000 tons of animal fat contributes to the production of renewable diesel. Cleaner-burning renewable diesel reduces greenhouse gas emissions over 80% compared to fossil fuel-based diesel, which is the equivalent to removing 5.4 million cars from America’s roads.
From creating valuable ingredients from resources that would otherwise be sent to landfills to finding ways to reduce the company’s environmental footprint, Sanimax has a positive environmental impact that plays an integral part in global sustainability and the food supply chain.