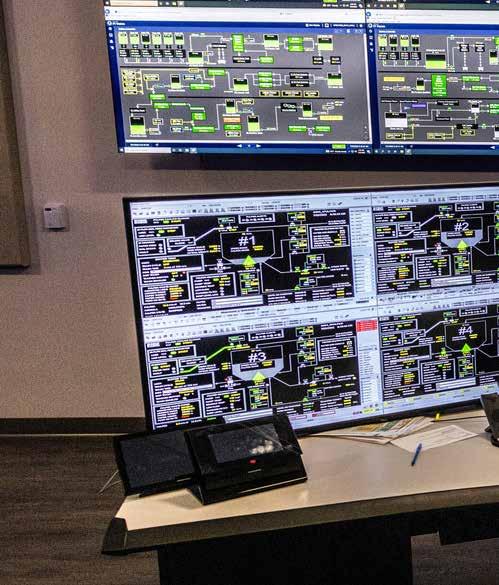
2 minute read
Not Your Father’s Paper Mill Anymore
Written by: Chris Brennan, Public Affairs Manager for Georgia-Pacific’s Green Bay Operations
Historically, paper manufacturing was a series of very manual processes –employees hand-packing products into cartons, manually interacting with machine controls, loading raw materials by hand or manually changing paper rolls. Georgia-Pacific (GP) continues to replace these practices across its Green Bay operations. Instead, the company is focused on employees learning and maintaining upto-date technology and automation that helps them move materials throughout the facilities and reduce close interactions with equipment. This keeps employees safer and creates a more efficient, productive and attractive work environment.
Over the next three years, Georgia-Pacific is investing more than $600 million in its Green Bay-based operations (including the new Brawny® paper towel addition at
1919 S. Broadway Street) on high-tech equipment and technology. This includes the latest in automation, laser-guided vehicles (LGVs), artificial intelligence (AI) and robust data analytics.
Automation is Key for
the Future Reducing manual “touches” will be a critical part of the production process of the new Brawny® paper machine, the associated converting equipment and the overall infrastructure. With the entire production process being nearly 85% automated, the 120 technology-focused jobs as part of this project will manage high levels of automation across the entire product system. Automation improvements are also underway at other parts of the Broadway Mill including the addition of more than 100 LGVs that will continue to ensure that paper rolls and other materials are moving through the facility with limited manual interaction by employees.
AI Ensures Quality Products and Packaging
To help ensure package quality and limited defects, Georgia-Pacific engineers used AI to help create a package inspection system for one of its film-bundled toilet paper packages. Defective package end seals on a film-bundled product can cause package failures, so the need for zero defective end seals is critical. The system executes 100% of the inspection on the packaging using AI technology that “learns” what a good quality image is and assigns a quality score. If a package does not meet the target “score,” it is rejected. Additionally, through special cameras and lighting, product quality itself is also being evaluated and measured at the same time as the packaging seals.
Using Technology to Consolidate Operations
Many of the operational areas at GeorgiaPacific’s Broadway Mill site (including Fiber, Power, Wastewater Treatment Plant, Paper Machines and Logistics) had their own separate control rooms. There was a clear opportunity to use technology and remote monitoring capabilities to eliminate some redundancy in processes. The mill’s Daily Operations Center (DOC), which went online in 2020, combines the controls for these operational areas into one central location and enables a workforce transformation shift for employees from “operate, inspect and maintain” to “monitor, analyze, predict and maintain.” When needed, the DOC also provides remote monitoring support for process areas at other select GP facilities in the United States.
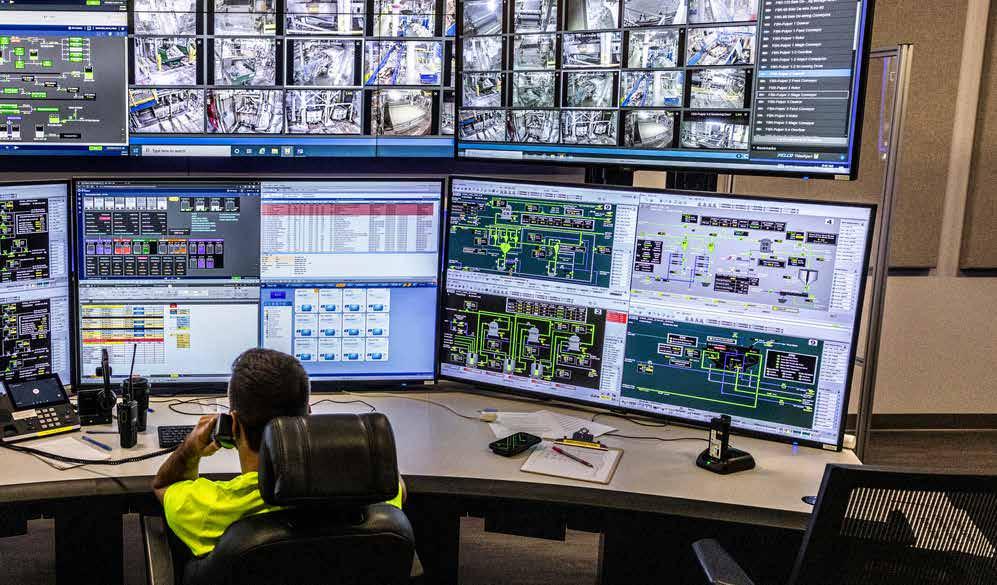
With a focus on continuing to transform its operations through innovative technology and automation, and recruiting and developing a world-class workforce to lead this transformation, GeorgiaPacific is excited about its future and ongoing evolution of “your father’s paper mill” into something uniquely different, state-of-the-art and attractable to the workforce of the future.
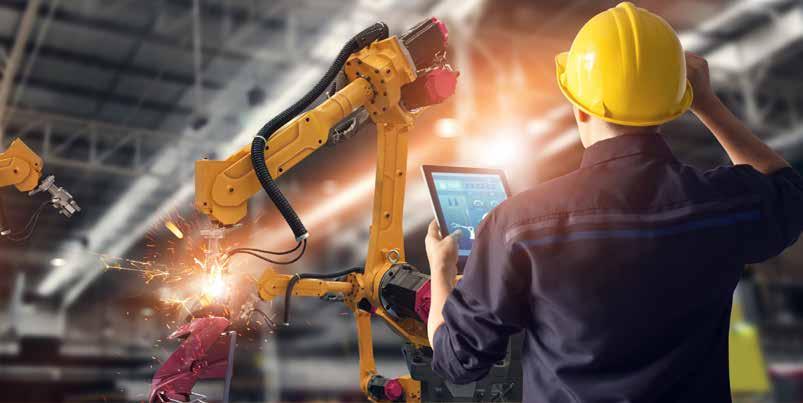