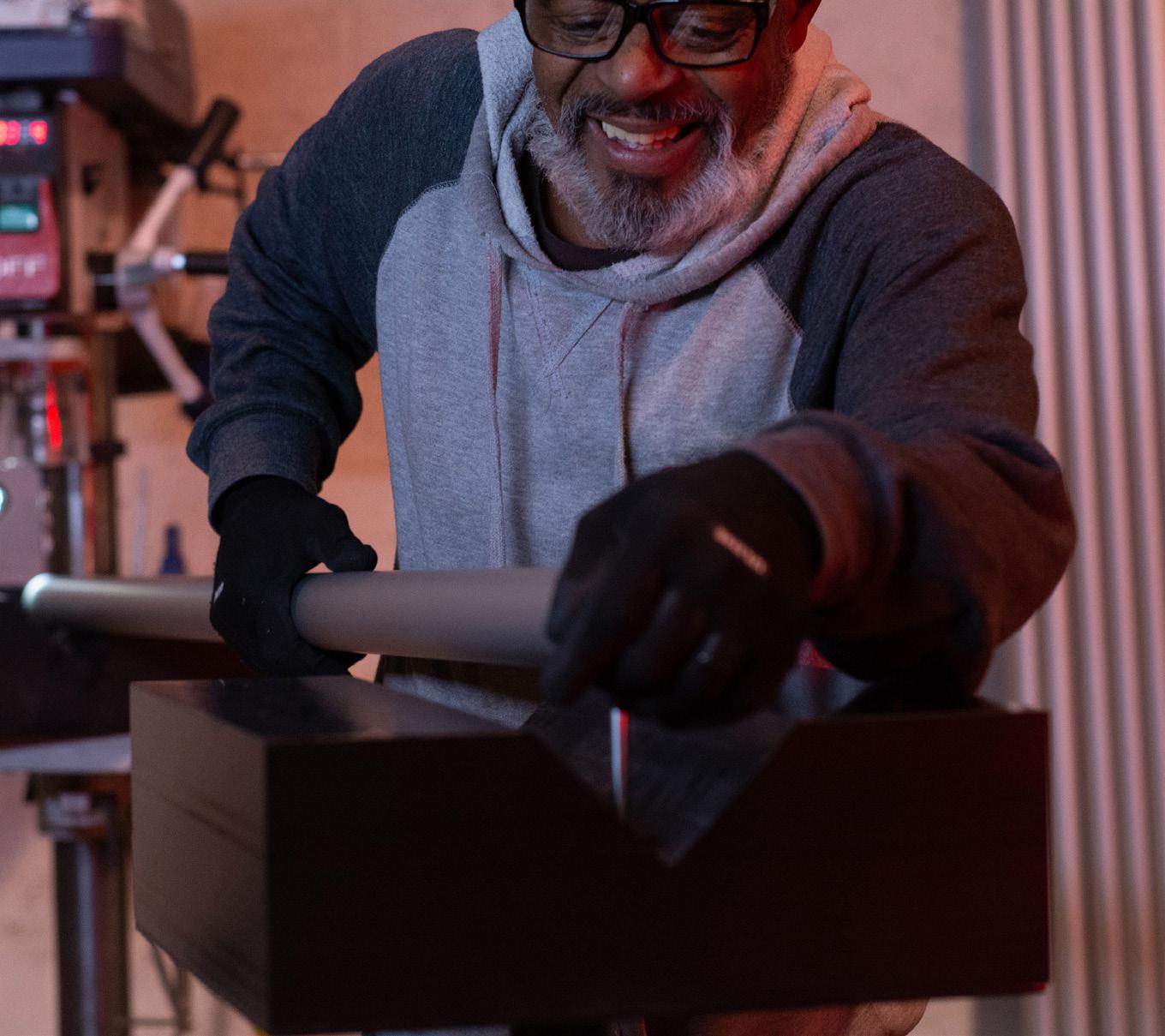
9 minute read
Celebrating Manufacturing Month

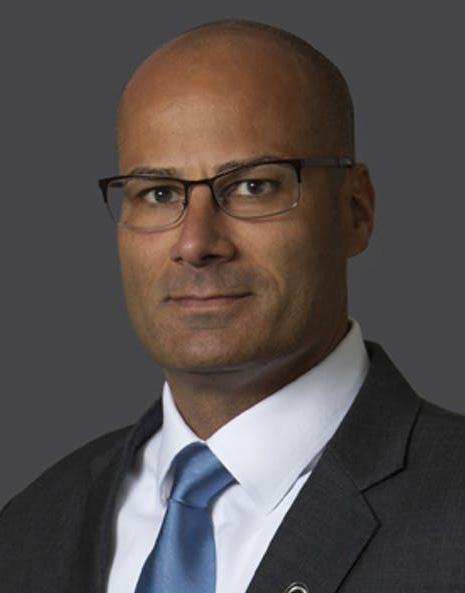
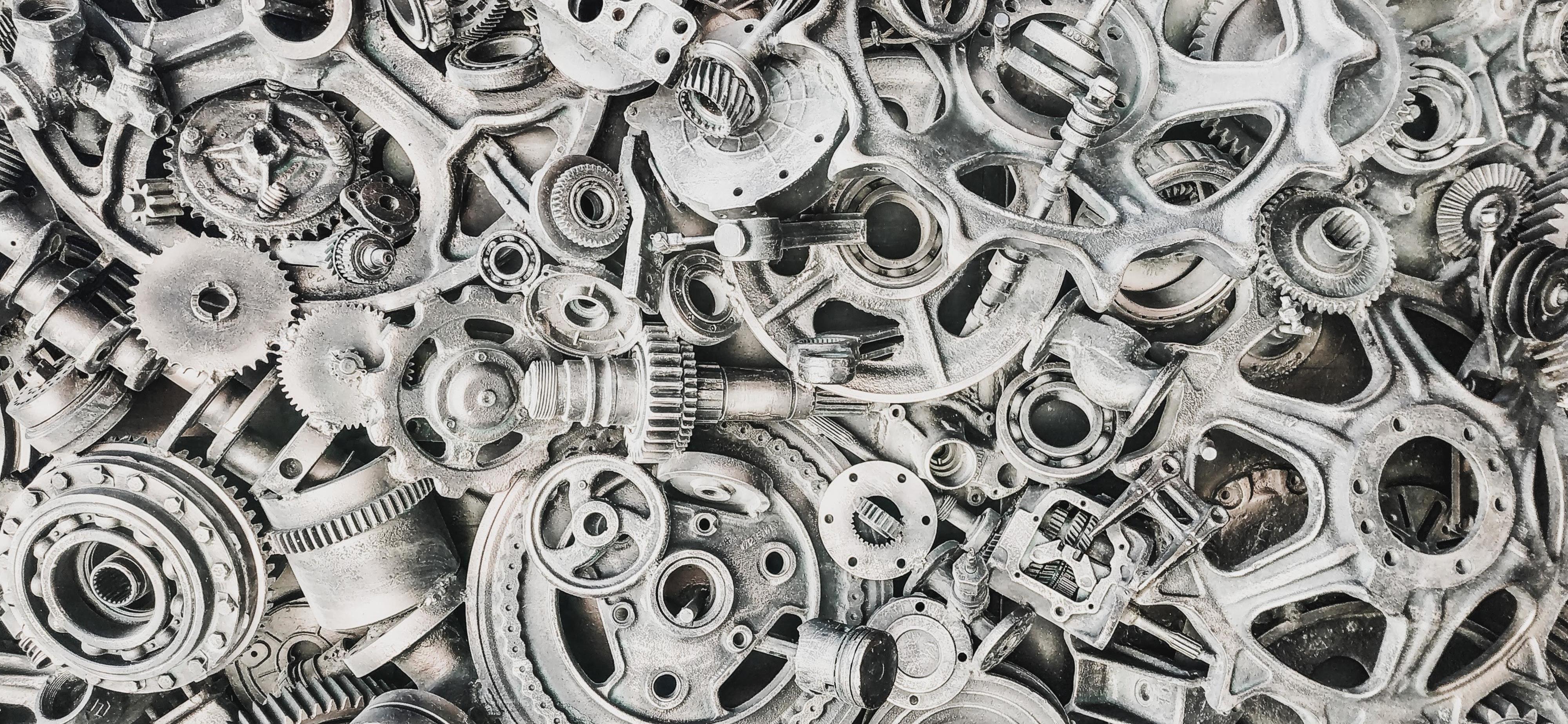
By: Greg Sofra, audit partner, Baker Tilly
Ever wonder if having manufacturing within your local community is valuable? Significant research has been performed regarding the economic benefit of manufacturing and it has shown that manufacturing is the driver of a healthy, vibrant community that significantly impacts both local and regional economies. For every dollar of manufacturing value created in the United States, $3.60 in additional economic activity is generated. Another study shows that every manufacturing job created in the U.S. leads to approximately 3.4 non- manufacturing jobs to take the product from start to finish.
I’m Greg Sofra with the advisory, tax and assurance firm Baker Tilly. At Baker Tilly, we are proud to partner with the Greater Green Bay Chamber in celebrating Manufacturing Month. We in Northeast Wisconsin are fortunate that so many great manufacturers have chosen our area to build, develop and make the products we all use and rely on each and every day.
Manufacturing is an economic activity. Every economic activity stimulates another economic activity. Evidence clearly shows that manufacturing has a strong “multiplier effect” that impacts our economy in many unique ways. For example, manufacturing stimulates the need for semi-trucks, cargo ships and freight trains to move goods to market. The movement of these goods and the demand for them in the marketplace, in turn, stimulates manufacturing production, provides retail outlets with things to sell and provides other industries the parts and machinery needed to make unique products. Manufacturing truly is the backbone of our economy.
So, during October, if you are stopped in traffic by a freight train or feel semi-trucks slowing your daily commute, pause for a moment and realize that manufacturing is good for the long-term health and development of our community and perhaps that minor traffic inconvenience is really a positive thing after all. On behalf of Baker Tilly, the Greater Green Bay Chamber and all of us in Northeast Wisconsin, thank you for your perseverance, ingenuity and innovation.
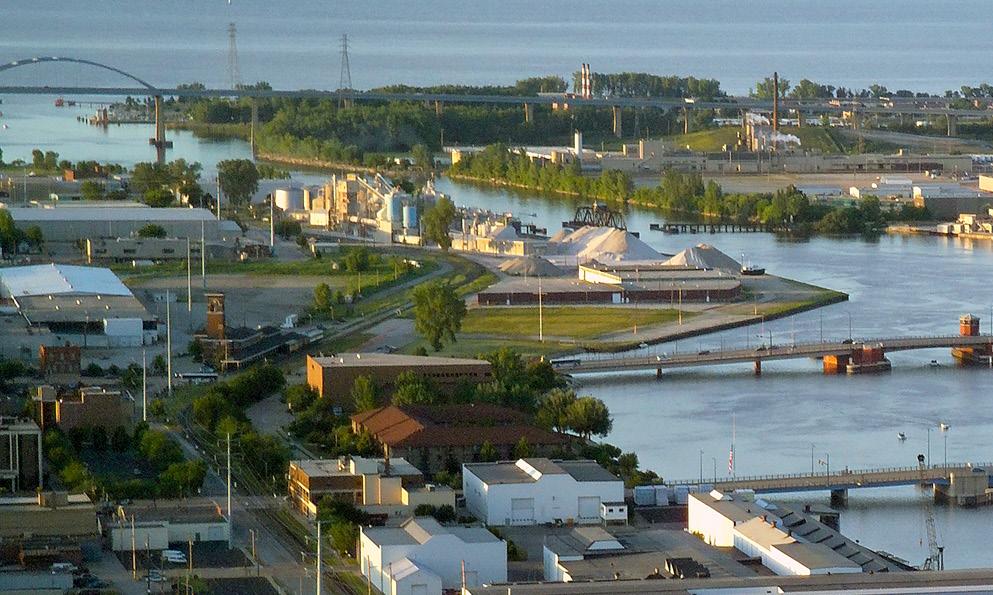
Reevaluating your supply chain with nearshoring
By: Jeff Jorge, principal, and Erich Bergen, director, Baker Tilly
COVID-19 shined a harsh spotlight on many business facets in the US, especially supply chains. From product shortages to capacity constraints, the pandemic has impacted supply chains continuously, brought certain industries to a standstill and proved to be a rude awakening for American companies that have offshored production to countries in the Far East.
Logistical risks, rising labor costs in the Far East and heightened shipping costs make being far away from your base less appealing. Plus, around the world, social, political and geo-economic influences—such as the tariff war between the U.S. and China—are happening more frequently and with greater effect, having a big impact on businesses.
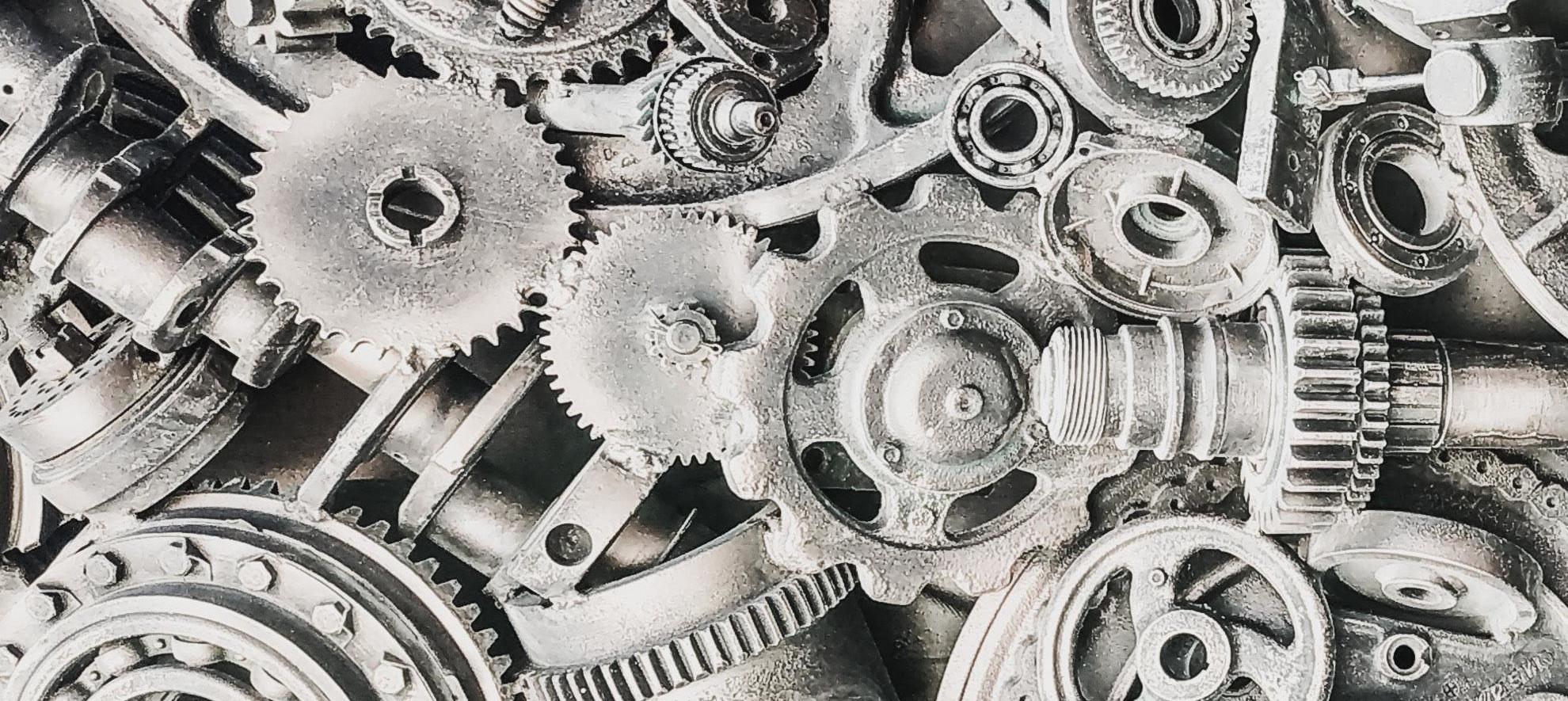
To combat the changing business landscape, companies are considering nearshoring—the act of bringing your production closer to the end destination point—their operations to minimize risk and help their business grow.
Let data drive decision-making
When considering nearshoring, it’s important to start with the question: Is nearshoring right for you? Evaluate whether making a change to your supply chain is a good fit for your company. Nearshoring offers a higher return on investment and focuses on providing value to the client but most of the risks of nearshoring have to do with poor planning or lack of proper due diligence. Understanding your data and having a confident model is key in deciding what to do.
Consider geo-politics
It’s also important to evaluate potential site locations history and anticipated future global impact as it relates to trade and tariffs, as well as its overall relationship with the U.S. Considering these factors will prevent you from creating more problems down the road.
The benefits and challenges of nearshoring
The benefits of moving operations closer to home include working in the same time zone, fewer cultural differences, greater cost- effectiveness, proximity allowing face-to-face meetings, faster communication and more timely decision-making and problem solving–all of which can contribute to higher productivity and morale.
Nearshoring also faces several obstacles, such as a fear of the new, change or taking aggressive action. For others, they feel they are the experts on their business and can analyze and assess the pros and cons of nearshoring on their own. The problem is that most middle-market manufacturers are already resource constrained: Their team already has full-time jobs that draw on all their energy and talents and while they feel they can do the analysis and modeling on their own, most companies lack the human resources and talent to do so. They get suboptimal results when attempting to understand if they should nearshore because the people asked to do the work are often already overworked. This results in the quality
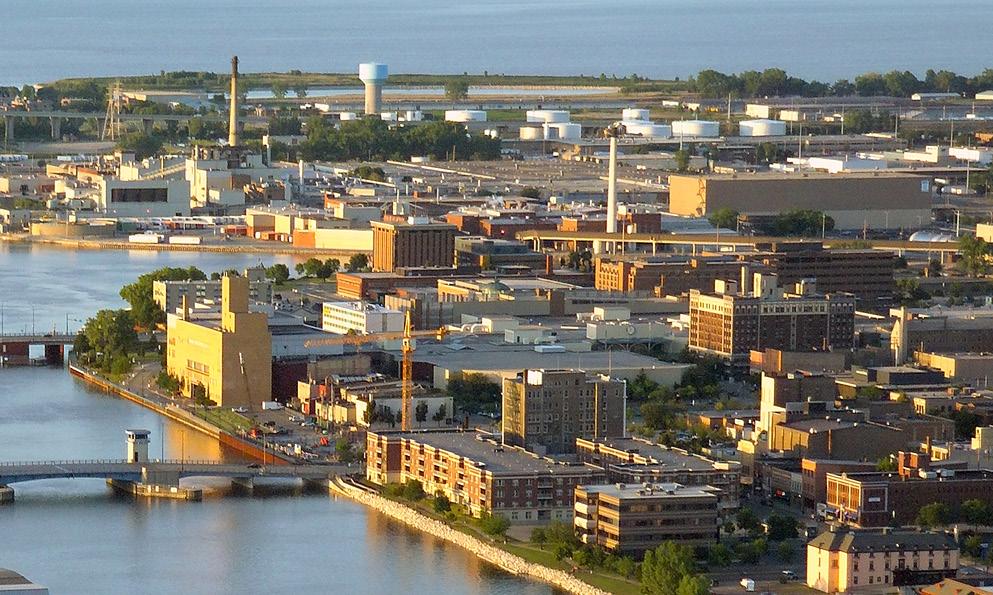
of the analysis rarely allowing them to make a confident, educated decision.
The future of supply chains
Supply chain disruptions have been evident since the beginning of the COVID-19 pandemic. A semiconductor chip shortage slowed car manufacturing, constraints in steel production led to higher prices and COVID-19- related absences created bottlenecks globally. As COVID-19 continues to confound the global economy, supply chain disruptions will continue to evolve. As a result, companies are using new methods to create a resilient supply chain, including nearshoring.

Your supply chain can be either your basis of strength or your greatest weakness. Nearshoring brings your products closer to markets, providing you with greater control over operations and allowing you to de-risk the supply chain to position your business for accelerated profitability. Baker Tilly professionals are prepared to help your business explore if nearshoring is right for your business.
About Baker Tilly
Baker Tilly U.S., LLP (Baker Tilly) is a leading advisory CPA firm, providing clients with a genuine coast-to-coast and global advantage in major regions of the U.S. and in many of the world’s leading financial centers–New York, London, San Francisco, Los Angeles and Chicago. Baker Tilly is an independent member of Baker Tilly International, a worldwide network of independent accounting and business advisory firms in 148 territories, with 36,000 professionals and a combined worldwide revenue of $4 billion. Visit bakertilly.com or join the conversation on LinkedIn, Facebook and Twitter.
Baker Tilly US, LLP, trading as Baker Tilly, is an independent member of Baker Tilly International. Baker Tilly International Limited is an English company. Baker Tilly International provides no professional services to clients. Each member firm is a separate and independent legal entity, and each describes itself as such. Baker Tilly US, LLP is not Baker Tilly International’s agent and does not have the authority to bind Baker Tilly International or act on Baker Tilly International’s behalf. None of Baker Tilly International, Baker Tilly US, LLP nor any of the other member firms of Baker Tilly International has any liability for each other’s acts or omissions. The name Baker Tilly and its associated logo is used under license from Baker Tilly International Limited.
The information provided here is of a general nature and is not intended to address the specific circumstances of any individual or entity. In specific circumstances, the services of a professional should be sought. © 2021 Baker Tilly US, LLP.
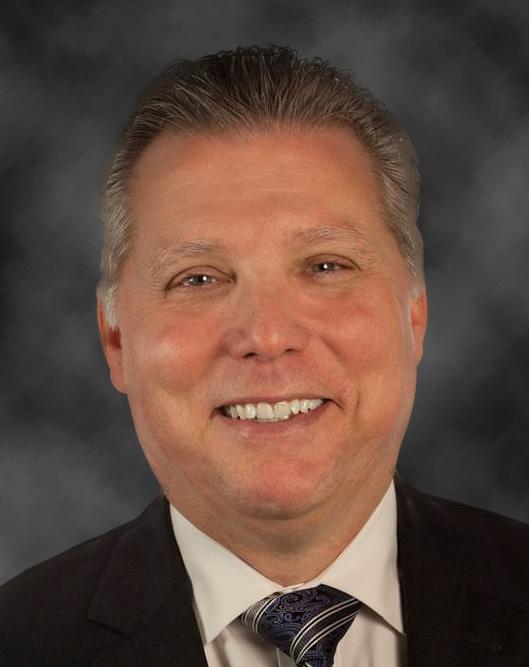
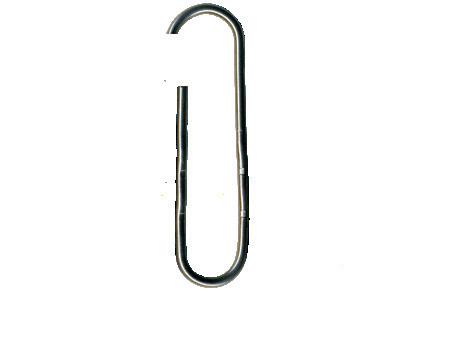
Developing your workplace culture
Mark Kaiser, owner/president of Lindquist Machine Corporation
The need for qualified workers has become more evident as the pandemic economy continues. There are many reasons that job openings continue to outpace the number of available workers. Unfortunately, some workers have chosen to retire early. Still others may be taking their health or the health of a family member into consideration before returning to work.
Eventually, those employees will return to work. In the era of the great resignation, it’s important for manufacturers (and all businesses) to consider its company culture to ensure employees stay, believe in the mission and understand their vital contributions to moving the business forward and delivering high quality products to customers around the state and country.
It’s been great to see the Greater Green Bay Chamber Book Club form and offer up-and- coming leaders the opportunity to develop their skill sets. One book I’d recommend is Crucial Conversations: Tools For Talking When Stakes Are High by Joseph Grenny, et al. This book has been pivotal for Lindquist Machine Corporation and helping transform the culture, assist in cultivating more trust between the shop employees and the office personnel, and produce a collaborative environment for employees to solve the technical problems that manufacturers encounter.
Even though the temptation in the pandemic economy is to hire quickly and fill those openings, it is equally important to remember to recruit and hire the employee that will fit the culture. A business can always train the right employee with the skills they need to be successful but it’s much more difficult to retain a employee that does not “buy into the vision” of the company.
As the head of the company, it’s important for the president or owner to drive the process in developing the culture, realize that patience and repetition of the vision are required, seek regular feedback from employees as the new processes are implemented and treat culture as an investment in the business. The return on investment just may be a business that is not only growing and creating new jobs but also growing and developing the next generation of leaders.
Ahlstrom-Munksjö and its Wisconsin operations dedicated to creating fiberbased solutions through their ‘ƒrom Plastic to Purpose’ campaign
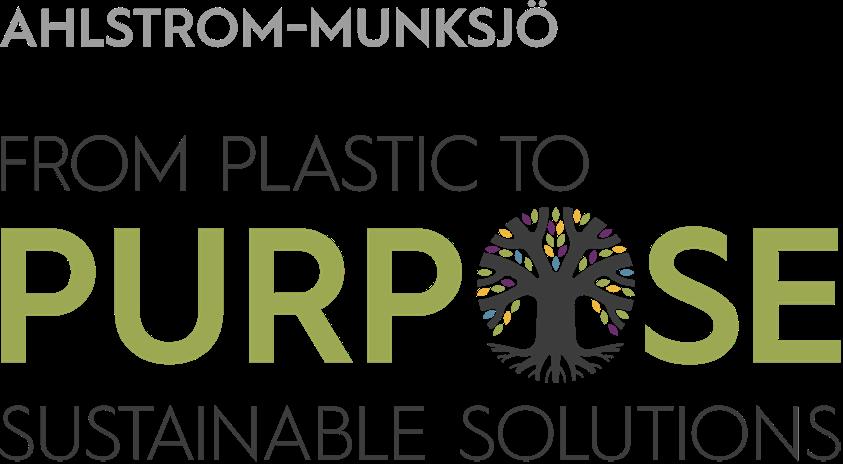
As part of its continued focus on global sustainability leadership, the team at Ahlstrom-Munksjö launched its ‘ƒrom Plastic to Purpose’ campaign this past year. Ahlstrom-Munksjö has four plants in Wisconsin and employs directionally 1,800 employees.
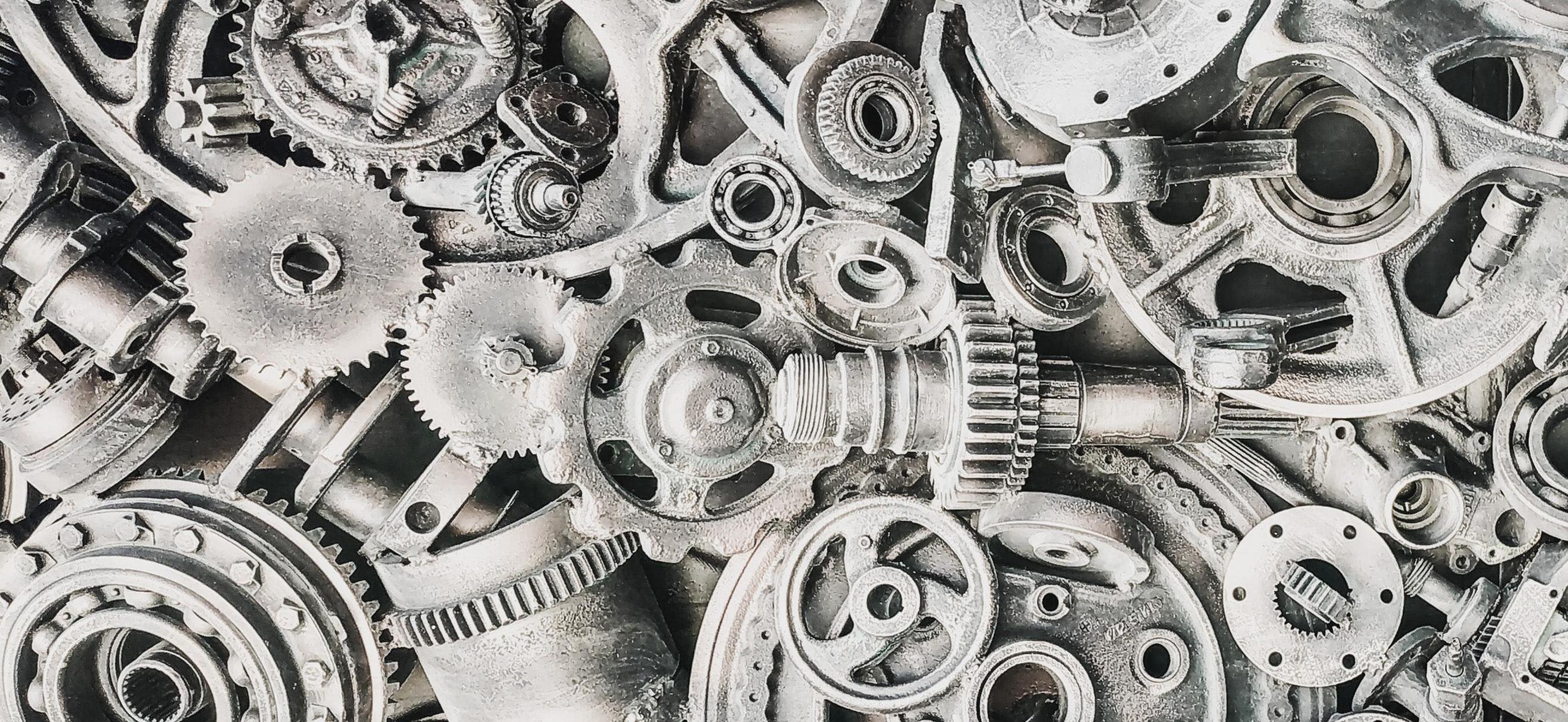
“Our ‘ƒrom Plastic to Purpose’ campaign aims at raising awareness around the world regarding the possibilities of fiber-based solutions as a renewable option,” said Addie Teeters, head of marketing communications & public affairs for Ahlstrom-Munksjö. “Many industries are demanding more sustainable solutions that reduce their impact on the environment and also have a positive end-of-life story – anywhere from compostability and biodegradation to recyclability. By educating the marketplace on the possibilities related to ‘ƒrom Plastic to Purpose’ we are encouraging industry stakeholders globally to consider fiber and paper-based alternatives where plastic and non-renewable materials are used today.”
As part of the campaign, three webinars were organized to provide more insight on how to transition from non-renewables to fiber-based packaging. These educational seminars featured parchment technology, highly technical applications and the food packaging arena.
Visit Ahlstrom-Munksjö’s ‘ƒrom Plastic to Purpose’ hub which includes more information about the philosophy and guiding principles as well as partnerships, the latest products in the news and the on-demand playback of the three webinars!
View the campaign page:
Thank you to our Manufacturing Month sponsors
PRESENTING SPONSOR
GOLD SPONSORS IN-KIND SPONSOR
With disruption all around us, standing still is not an option.
Baker Tilly is honored to support the Greater Green Bay Chamber of Commerce in celebrating manufacturers in Northeast Wisconsin.
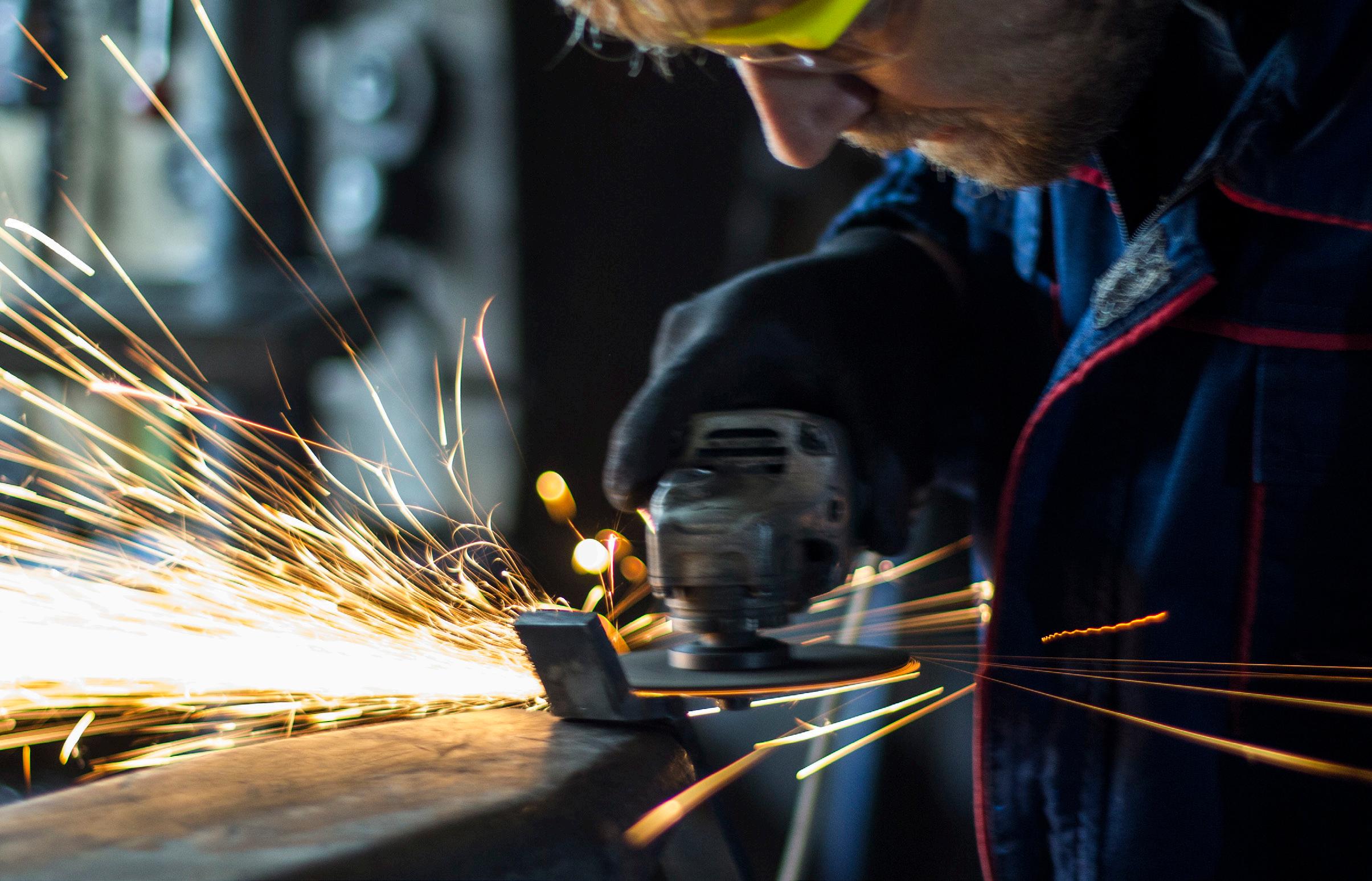
advisory. tax. assurance. | bakertilly.com Greg Sofra, CPA

Wisconsin Manufacturing and Distribution Practice Leader +1 (920) 739 3368 greg.sofra@bakertilly.com