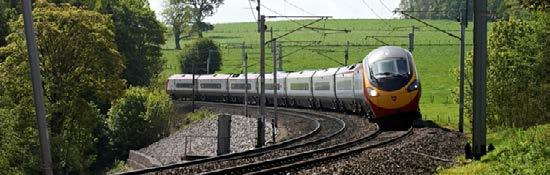
4 minute read
HP335 comes of Age
British Steel has been enjoying a double celebration this year - two big milestones for their High-Performance rail, HP335. Not only has this premium rail turned a decade old, but the company has now sold more than 100,000 tonnes of it – enough to build a direct track from where it’s made in Scunthorpe straight to Oslo in Norway!
The first HP335 rail, or HPrail® as it was then known, was installed in Bessy Gill, UK, back in August 2010. British Steel had been working closely with Network Rail to develop a rail that would combat the issues of rolling contact fatigue and wear. When this new microstructurally engineered rail with uniform through-hardness proved favourable in laboratory tests, it was installed on a number of trial sites across the UK.
Advertisement
Key Account Manager John Austin said: “Its performance in-track demonstrated longer rail life and lower life cycle costs due to reduced grinding frequency – in some cases of up to 60% – when compared to standard grade rails, and this led to Network Rail’s full product approval of HP335 in 2012. Since then, it’s been installed in light rail, mainline and heavy haul applications throughout the UK and Ireland. HP335’s high performance continues to delight our customers with extended rail life and fewer track maintenance requirements and is now the premium rail of choice in the UK mainline network. Happy birthday HP335 – here’s to the next 10 years!”
What is different about this Rail?
This non-heat-treated rail is designed for curved track and other high duty areas, where it has proved to improve wear resistance, cut life cycle costs, reduce grinding frequency and extend rail life. Suited to a wide range of applications, HP335 (also known as HPrail®) was approved for use by Network Rail in 2012 and is now the premium rail of choice in the UK mainline network. Several light rail operators have also adopted HP335 as their premium rail solution for reducing wear, corrugation and grinding requirements to maximise rail life whilst reducing life cycle costs.
Reduced Life Cycle Costs
HP335 delivers low wear rates (comparable with R350HT rails) without the need for heat treatment. It also delivers greatly improved rolling contact fatigue (RCF) performance above other 'as-rolled' rails. This reduces the need for rail grinding to control RCF by typically 66%, thereby increasing
Lindsey and Brindusa from our Rail Technologies team surveying track at Drax power station
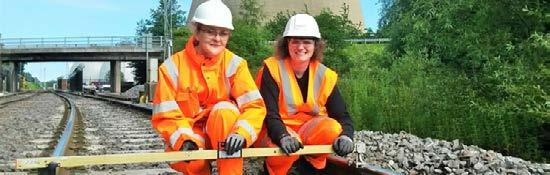
rail life, increasing track availability and reducing maintenance costs.
A 4-year test of HP335 rail in a heavy haul application at Drax power station has delivered a £92,000 cost saving on just one curve. The as rolled hypereutectoid rail - HP335 / HPrail® - has been installed and monitored over a period of 4 years following the recommendations of the Rail Technologies team.
Drax is the largest power station in the UK providing ~6% of the country’s electricity. Two thirds of the power station have been converted to use sustainable wood pellets instead of coal, with plans to switch the remaining two coal generating units to high efficiency gas. The solid fuels for power generation are brought to site by rail using freight wagons with the maximum permissible axle load on UK national railways of 25 tonnes. Historic performance of standard R260 grade rails had been poor under arduous conditions with a life of ~2 years being typical in the freight arrivals curve. The rails suffered both from excessive plastic flow and also rolling contact fatigue and spalling of the rail surface.
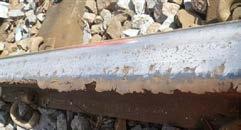
Plastic flow of the rail steel under high loads has led to lipping and spalling of the R260 rail surface
The spalling damage to the rail surface progresses and eventually makes ultrasonic testing of the rail un-testable necessitating its replacement. British Steel was asked for advice on how to improve the performance of this track and the first HP335 rails were installed in October 2014. Working in partnership with Drax engineers to assess the performance improvements, the improvements made have led to all subsequent renewals being completed using HP335 rails on this site.
High rail rolling contact fatigue damage was also greatly reduced.
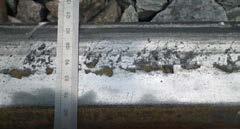
R260 Low rail showing spalling and rolling contact fatigue damage after ~35MGT of traffic HP335 Low rail showing significant improvements in performance at 38MGT of traffic.
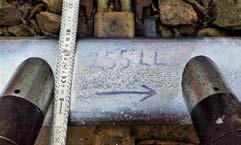

R260 rail ~35MGT

HP335 rail at 35MGT
One of the main performance benefits demonstrated was the elimination of gross plastic flow to the rail profile combined with greatly reduced levels of wear.
When combined with a suitable maintenance regime, the expected lifespan of the HP335 rail is