
9 minute read
Steve Masters
Steve Masters MEng
Chief Mechanical Engineer East Somerset Railway & Dartmouth Steam Railway
Advertisement
History of the Collett Designed GWR 5100 Class 2-6-2T No 4110
Built at Swindon in 1936, 4110 was initially allocated in October of that year to Severn Tunnel Junction to undertake tunnel banking duties. Two months later it was moved to the Wolverhampton district where it stayed for most of the next 26 years.
It operated on the intensive local passenger services from Birmingham Snow Hill and Moor Street stations to Leamington Spa, Stratford upon Avon and Warwickshire in general.
In March 1942 until April 1943 it was based at Birkenhead before returning to the Birmingham area.
Whilst at Taunton in 1962, 4110 was deployed on the branch line to Minehead which is now the West Somerset Railway and at Neath in 1963 it worked the Vale of Neath line to Pontypool Road on its last day of passenger services in June 1964.
It was withdrawn in June 1965 during the conversion from steam to diesel haulage, having run over 730,000 miles in mainline service.
It was sold for scrap to Woodham Brothers at Barry and entered the scrapyard in August 1965. It remained there until May 1979 following its purchase for preservation by the Great Western Preservation Group at Southall Railway Centre. It was the 100th locomotive to leave the Barry scrapyard. 4110 then moved to the Birmingham Railway Museum at Tyseley for contract restoration. Only a partial amount of restoration was completed before the owners decided to put the engine up for sale in order to release funds for the completion of work on 5700 class engine 9682.
The West Somerset Railway put in a competitive tender and bought 4110 in 2015 and the locomotive was then moved to Minehead in June 2015. In 2016 it was estimated that it would take three to five years once the funds and resources to undertake the work is available. It was then owned by WSR plc who planned to have it in traffic in 2022.
With no work having been done on the locomotive by May 2018 consideration was being given by the West Somerset Railway to a possible sale of the locomotive. Any sale would be conditional on the locomotive being hired back to the WSR once it was restored.
Towards the end of 2018 a group (GWR 4110 Ltd) was set up to buy the locomotive. At the same time the West Somerset Railway Association announced that they had agreed to accept ownership of the locomotive and future stewardship.
It was later announced that the locomotive was had been sold to the Paignton and Dartmouth Railway as this was the best bid and the WSR needed the funds. The locomotive will run at a WSR gala at no cost as part of the deal.
The locomotive was moved to the Dartmouth Steam Railway in February 2019. In September 2019 the East Somerset Railway announced that they were close to completing a deal with the Dartmouth Steam Railway to restore. the locomotive. As part of the arrangement 4110 will operate on the East Somerset Railway for three years following its restoration. The locomotive moved to Cranmore on the East Somerset Railway in January 2020 and restoration work was planned to start straight away.

Restoration Finally Begins after 40 Years!
The boiler was lifted off the frames in February 2020 following the removal of the tanks, cab and bunker.The restoration work reached a milestone in October 2020 when the frames were re-wheeled at the East Somerset Railway. In January 2021 it was reported that the work on the locomotive was on schedule to have it in steam in 2023. 4110 arrived here at Cranmore in February 2020 and after a rapid start stripping and dismantling what was left of the loco, progress was hit hard by the introduction of the first Covid lockdown! Fortunately there were still tasks we could complete
Great Western Star Summer 2021
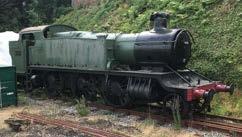
1. 4110 at Dartmouth prior to moving to Cranmore for overhaul. The poor condition of the tanks can clearly be seen here.
2. A 3D CAD model of the cylinders and cladding
3. A 3D CAD model of the tanks, boiler cladding and ashpan. 4. The horn grinding in progress.
5. The optical telescope set up in the LH cylinder.


away from the workshop including many machining jobs in some of our volunteers home workshops and also a lot of time was spent creating the 3D CAD models for the boiler cladding, cylinder cladding, tanks, bunker, ashpan and many other items which enable us to buy laser cut profiles ensuring great accuracy as well as huge time savings.
Reatoring the Frames
The frames were lifted off the wheels and all components were stripped, cleaned and inspected. The frames were cleaned back and tested for cracks. As soon as any welding or riveting work was complete, the frames were sat on stands and were weighed and shimmed to ensure that each stand carried the correct proportion of weight. This meant that the frames were sat naturally and were not sagging at any point and so had the least stress.
Once set up in this way, we set about using our horn grinder which is of our own design. The grinder and it’s accessories are set up using optical alignment gear running down the centre of the cylinders. This ensures that the horns are ground perfectly square to the centreline of the frames and are upright. Due to the way the horn grinder works, the finished surfaces are flat and parallel to within 0.002”.
Once the horn grinding was complete, the optical gear was again set up to enable us to take very accurate measurements of where the horn faces were relative to one another as well as from the cylinders. By entering all these measurements together with the design clearances etc into our spreadsheet, a set of dimensions are generated for each axlebox to be machined to give the precise location of the axle and position the axles in a straight line. This ensures that the axle centres are correct and that there is equal side to side travel each way for each axle as required.
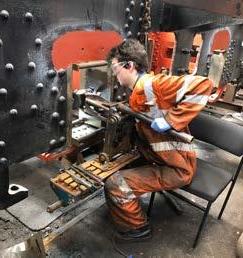

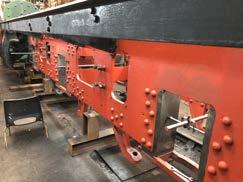
6. The dummy axles set up in each horn way. Used in conjunction with the optical gear gives very accurate results.
7. The frames being rewheeled with the use of two road cranes.
8. The newly completed bunker fully riveted externally but welded on the inside and on the base.
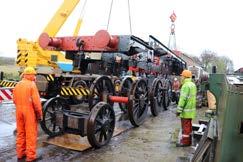
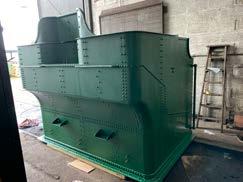
With all this work complete, the frames were painted before being rewheeled.
All of the valve gear was inspected and measured and in most cases, new bushes made and fitted as well as new motion pins being made, hardened and ground. The brake gear was done in the same way.
The cylinders were inspected and measured. The cylinder and valve bores were badly pitted from its

9.The new side tanks in progress being built in situ.

10. All new crown stays fitted to the top of the firebox.
time exposed at Barry. The valve liners were bored up a size and have plenty of life left in them. The cylinder bores did not quite clean up at max size and so are awaiting the fitting of new liners taking them down to the original start size again.
Tanks and Bunker
The original tanks and bunker were in a very sorry state and needed replacing. The new tanks and bunker were supplied to us as folded, laser cut sections meaning that they simply needed assembling, riveting and welding together as required. The bunker is now finished and is in position on the loco and the two tanks are well advanced being built in position on the frames. This has several advantages to us. Firstly the frames provide the perfect level base to build them, we know that they will fit when finished and most importantly, they don’t occupy too much space in our workshop!
The boiler has also made very good progress since being lifted from the frames. The first task was to shotblast all of the steel surfaces in preparation for a full NDT (crack detection) survey. This confirmed that the boiler was in relatively good health with only really the lower sections of the throat plate,
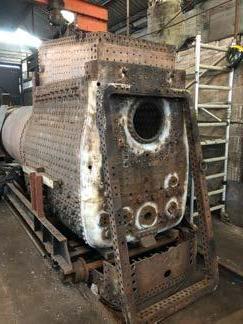
11. The boiler upside down with the lower (now upper!) sections cut away and the foundation ring removed. 12. New doorplate section formed and offered up to the original plate work and foundation ring.
doorplate and side sheets needing replacing due to excessive wastage and being too thin. In all four of these plates, the wastage was external rather than internal and so is likely to be the result of the long term storage outside since being scrapped rather than due to stress corrosion on the inside when in service.
The Firebox
The general condition of the firebox was very good and can not have been too old when the loco was withdrawn as all of the stays were at the start size. Even the smokebox has enough thickness to do another 10 years of service quite happily and so is being left in place.
All of the steel side stays and the crown stays were badly corroded and so needed replacing. Many of the side stays had already been burnt out of the copper side already but they all needed drilling from the steel outside.
With the boiler sat up the right way, the crown stays and side stays were all removed, the holes reamed and tapped and new stays fitted. Once complete, the boiler was turned upside down onto a purpose made boiler trolley. This then allowed us to cut away the wasted steel platework and remove the foundation ring.
New sections of boiler plate were then cut and bent around our formers in house before carefully grinding the weld preps to give an equal gap for a coded welder to weld up in the near future.
As soon as the welder has been, we will be able to finish off this bottom end of the boiler by riveting up the foundation ring and fitting the last few hundred side stays.
The boiler will then be turned back up the right way for us to fit the flues and tubes.
We are hopeful to have the loco complete some time next year in 2022 where it will run at the East Somerset Railway for 3 years before then returning to the Dartmouth Steam Railway.

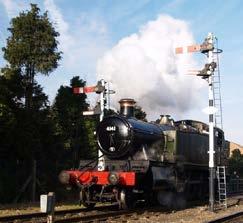