SVALBARD: DESIGN FOR A VULNERABLE CLIMATE +
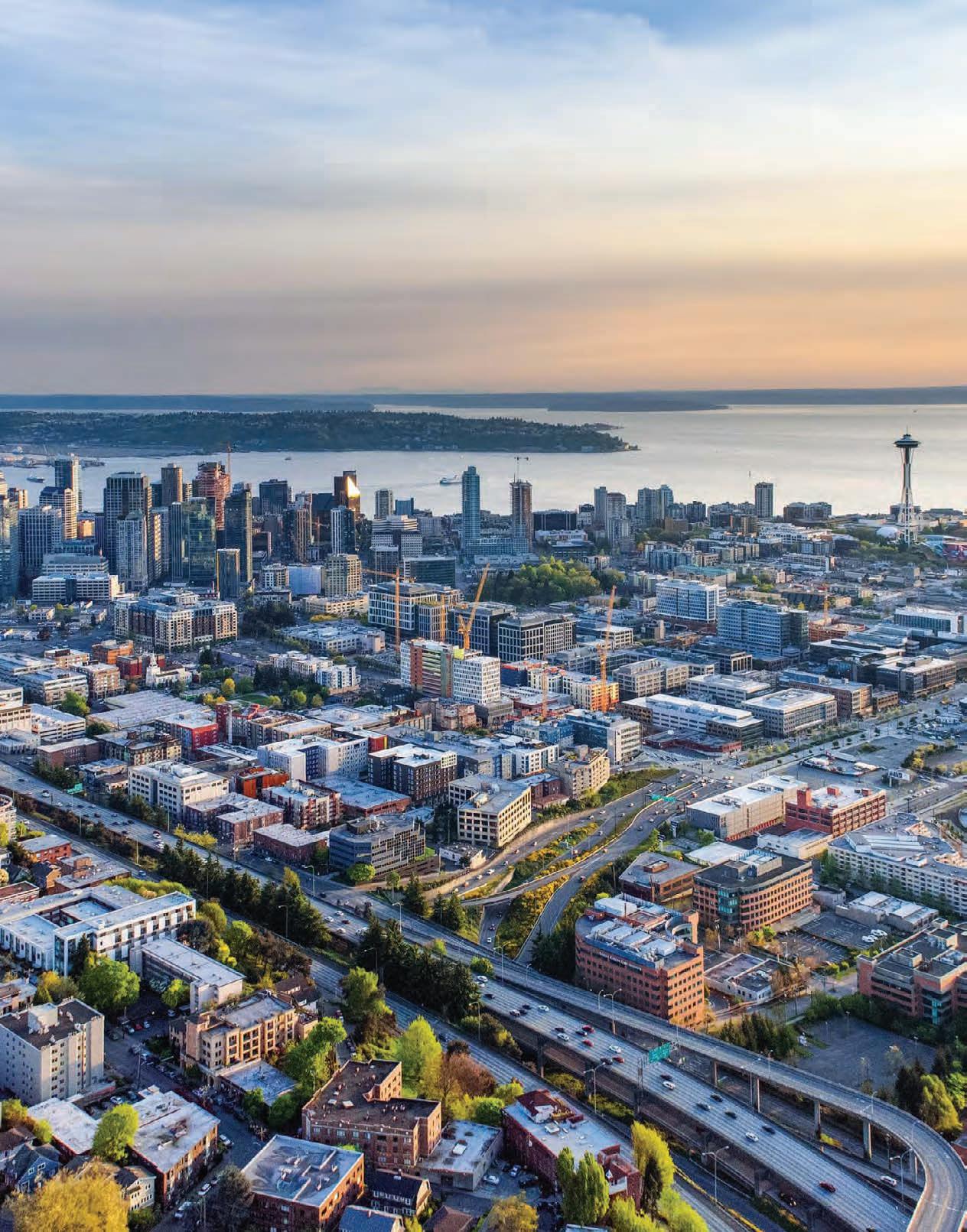
SUSTAINABLE DESIGN STRATEGIES FOR A BETTER TOMORROW SEATTLE, PG. 266
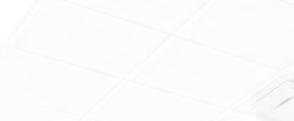
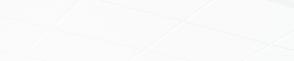
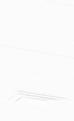

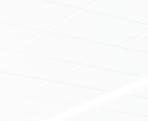
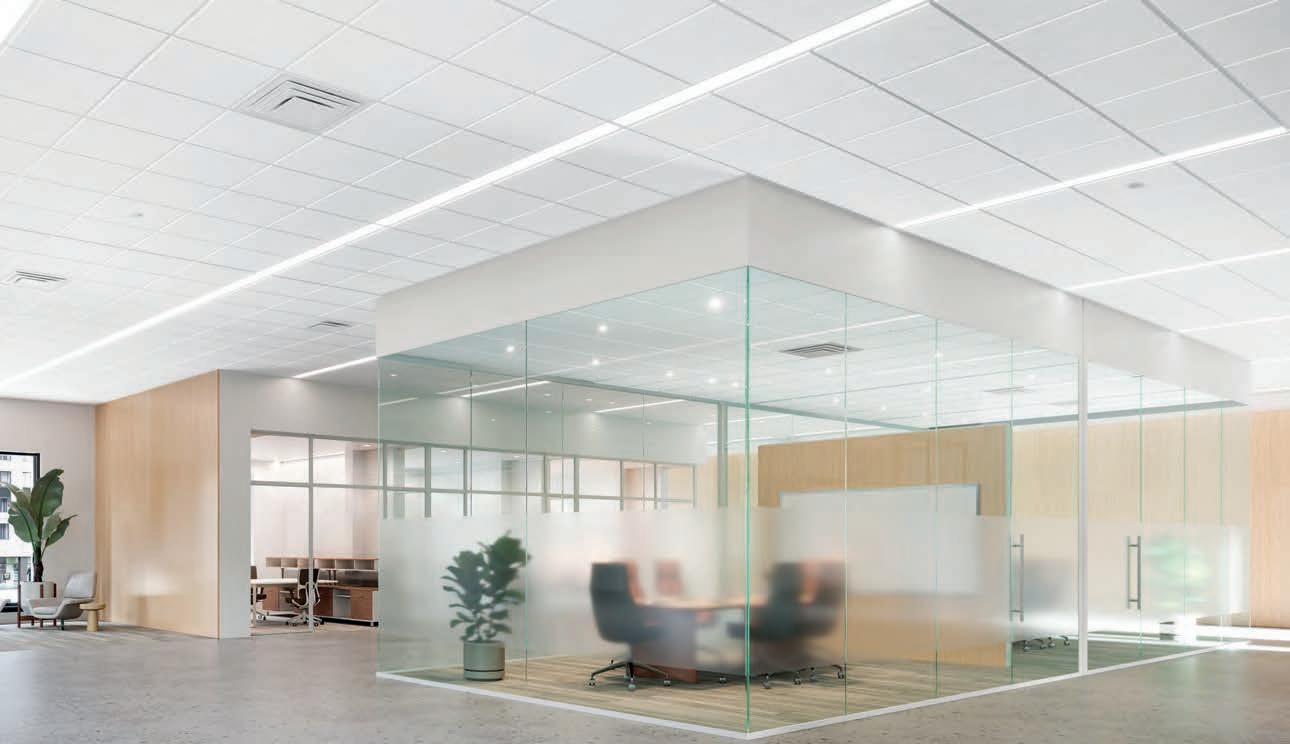

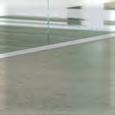
SVALBARD: DESIGN FOR A VULNERABLE CLIMATE +
SUSTAINABLE DESIGN STRATEGIES FOR A BETTER TOMORROW SEATTLE, PG. 266
Saves up to 15% energy
Aids in carbon reduction
Templok® Energy Saving Ceilings can reduce building HVAC energy costs and consumption up to 15%* and enhance thermal comfort for occupants using advanced Phase Change Material (PCM) technology. Create resilient, sustainable spaces at armstrongceilings.com/energysavingceilings
PG 94
Beyond Carbon Neutral
The journey to “nature-positive” with innovative manufacturing and design
PG 108
Strong Design
Reconsidering how health care environments can stand up to storms and more
PG 116
A Safer Path
Bird-friendly glass, energy efficiency, and more combine in the latest innovations.
PG 124
Think Zinc
Historic zinc is rediscovered as a sustainable solution that checks all the right boxes.
PG 132
Maximizing Curb Appeal
Exciting exteriors to consider on residential projects
PG 138
The Evolution of Precast Concrete
Addressing everything from logistics and performance to aesthetics and reusability
PG 144
Exterior Building Systems
Setting the stage for high performance
PG 158
IAQ Meets Energy Efficiency
Inside a dedicated clean air system with real-time sensing
PG 164
Illuminating the Future
Daylighting for the modern designer
PG 172
Design of Doors Options for more light, privacy, and flexibility than ever before
PG 180
The Circularity
Disparity
The journey to identifying and reclaiming materials
PG 314
Future-Proofing Airports
Airport design is evolving to make some of the world’s busiest places more adaptable.
PG 330
The Modern Commercial Washroom
How expectations of restrooms are changing—and how designers can adjust
Create dual-tone designs as bold or subtle as you are with the latest addition to the Autex Acoustics® Groove range: Groove Duet.
With Groove Duet, you can combine any two colors in our range to create one precision-cut grooved panel–one guaranteed carbon neutral and made with at least 80% post-consumer recycled materials.
www.autexacoustics.com
PG 188
Contemporary Office Design
Flexible office spaces are evolving but continue to be in high demand.
PG 298
All Eyes on Svalbard
Designing for vulnerable climates is needed now more than ever.
PG 302
Top of the World
The paradox of sustainable tourism in vulnerable places
PG 322
A Whole New Ball Game
Designing for varied spectator experiences
PG 338
Designing Year-Round
Outdoor Spaces
Gensler on the growing demand and connection between indoors and out
ON THE COVER
Sustainable building is booming in Seattle.
Photo by Tim Durkan
PG 19
Editor’s Picks Designs and materials inspired by wood
PG 24
Intumescent Coatings
Sustainability, health, and design benefits
PG 30
Fighting Food Waste
InSinkErator innovates to help families and companies be more sustainable.
PG 35
Waterproofing
Beachfront Properties
Balancing aesthetics and functionality to combat coastal challenges
PG 44
Considering
Stained Concrete
How concrete stains offer design flexibility and more
PG 52
Designing with Thermal Breaks
How to seal the building envelope against energy loss
PG 60
Clear Vision
How innovative glass solutions are exceeding designers’ expectations
PG 192
Making Moves
The role of movable wall solutions
PG 204
Wellness Everywhere
A new HED office in Detroit offers an improved experience for all who enter.
PG 212
Adaptable Offices
Flexible office design for employee well-being
PG 218
Inspiring Acoustics
No longer an afterthought, sound solutions that are functional and flexible are in demand.
PG 226
Historic Preservation, Modern Innovation
Studio Gang’s adaptive reuse of the Gray Design Building at UK
PG 232
Giving Shape to Scientific Research
ZGF Architects designs a home for the San Diego-based genomic research giant Illumina
PG 242
A Net-Zero
Teaching Tool HGA designs an energy-efficient early learning center where kids thrive.
PG 250
A Treehouse Above the Dunes
Wheeler Kearns Architects designed a lakeside retreat for years of outdoor adventure.
PG 258
Sensitive and Modern
A bucolic England landscape inspired this minimalistic home on a historic estate.
PG 266
The Emerald City Perspective Seattle’s commitment to sustainability goes beyond green buildings to a green economy.
PG 268
A Century of Memories
The Fairmont Olympic Hotel in downtown Seattle is a gem in preservation.
PG 274
A Mixed-Use Treehouse
Graphite Design Group’s playground for Amazon employees and their neighbors in downtown Seattle
PG 288
A New Project Takes Flight Biophilic design is central to an expansion at this major airport.
PG 290
The Greenest Port
Exciting developments as the Port of Seattle aims to become the most energy-efficient port in North America
PG 361
In Conversation KFA Architecture’s Lise Bornstein on placemaking in LA
PG 366
Large-Scale
Affordable Housing Susan King on new apartments in Chicago
PG 370
Educational Designs
How RAMSA’s studentcentric projects teach sustainable behaviors
PG 374
Designed to Heal Reimagining America’s jails
PG 378
Architect to Watch KTGY’s Megan Valentine on designing for flexibility and adaptability
PG 382
Designer to Watch David Michael designs for connection in San Diego’s first “agrihood.”
Editor-in-Chief
Christopher Howe
Associate Publisher
Laura Howe
Managing Editor
Laura Rote
Art Director
Victoria Norman
Designer Madison Wisse
Content Marketing Director
Julie Veternick
Content Marketing Manager
Colette Conway
Contributors
Lark Breen, Rachel Coon, Sophia Conforti, Christina Dean, Will Gridley, Kate Griffith, Pauline Hammerbeck, Elyse Hauser, Brittany Howard, Lauren Jones, Megy Karydes, Ravail Khan, Susan King, Russ Klettke, Emma Loewe, Marcy Marro, David Miller, Ian P. Murphy, Mikenna Pierotti, Mike Thomas, Matt Watson, Lisa White
ONLINE gbdmagazine.com gbdmagazine.com/digital-edition
SUBSCRIPTIONS
Online shop.gbdmagazine.com
Email service@gbdmagazine.com
gb&dPRO
Online gbdmagazine.com/ gbdpro
Email info@gbdmagazine.com
Green Building & Design 47 W Polk Street, Ste 100-285 Chicago, IL 60605
Printed in the USA. © 2024 by Green Advocacy Partners, LLC. All rights reserved.
Green Building & Design (gb&d) is printed in the United States using only soy-based inks. Please recycle this magazine.
The contents of this publication may not be reproduced in whole or in part without the consent of the publisher. The publisher is not responsible for product claims and representations.
The Green Building & Design logo is a registered trademark of Green Advocacy Partners, LLC.
EMMA LOEWE
(“Design of Doors,” pg. 172; “Flexible Office Design,” pg. 212) is a writer, editor, and design lover based in New York City. Her writing explores the intersection of nature, climate, and human health. She is the author of Return to Nature: The New Science of How Natural Landscapes Restore Us (HarperCollins 2022) and the co-author of The Spirit Almanac: A Modern Guide To Ancient Self Care (Penguin Random House 2018). Her work has appeared in Grist, National Geographic, and Bloomberg, among others. emmaloewe.com
ELYSE HAUSER
(“Building Community through Placemaking,” pg. 361) is a writer from the Seattle area with an MFA from the University of New Orleans. Through journalism and creative writing she focuses on environmental issues and solutions. Elyse has learned from organizations including Bergen’s Center for Investigative Journalism, Seattle’s Jack Straw Cultural Center, and the Bread Loaf Environmental Writers’ Conference. elysehauser.com
MIKE THOMAS
(“Designed to Heal,” pg. 374) is a Chicago-based writer whose work appears regularly in Chicago magazine and gb&d, among others. He also spent nearly 15 years at the Chicago Sun-Times and is the author of two books. He has written about a wide range of subjects—from movie stars and bestselling authors to famous musicians and business leaders.
1
Minimalist no more. Corporate offices have historically had stark, streamlined designs. ZGF Architects’ James Woolum predicts this will change to meet employees’ desire for workspaces that are extensions of home following years of remote work. “If you look around your home, it’s not one color. It’s not one pattern or one texture,” he says. “The way we live our lives outside of the office is so much more nuanced than a lot of corporate design.” Flexible Office Design For Employee Well-Being, pg. 212
2
Strategic density is an architectural solution that solves multiple challenges. It provides more housing on less land, which frees up room for green spaces. Density can help people access health care, grocery stores, and schools. “I love to talk about equity in architecture,” says Lise Bornstein, partner at KFA Architecture in Los Angeles. “Density is a big equity piece as well, because it helps to normalize and strengthen our communities, especially in
areas where there are food deserts, and it just gives more people a chance to have the California dream and to participate in access to education.” Building Community through Placemaking, pg. 361
3
As regulations across the country roll out in metropolitan areas around all-electric buildings, some building owners are preparing for a future that’s increasingly electric. “You really want to start thinking about the next five, 10 years,” says Blake Petty, commercial specification lead at Bromic Heating. “Start thinking about what your outdoor space is going to look like, what those needs are, and plan ahead … Make sure the building has a proper infrastructure to be able to power those types of electric infrared heaters.” Stay Awhile, pg. 342
4
Lampwick Quay marks the final chapter in a decades-long effort to revitalize New Islington, a post-industrial area of Manchester, England. The project is rooted in the quirky unconventional vision of architect Will Alsop, whose original master plan drew inspiration from the creative energy of cities like Rotterdam and aimed to give the community a sense of fun and engagement. The architects behind Lampwick Quay honored this intent with bold colors and by reimagining a large, warehouse-inspired structure into smaller components—positioning Lampwick Quay as a key component in the plan to give this once-forgotten community a new life. Think Zinc, pg. 124
5
In Chicago the 167 Green Street project, designed by Gensler and developed by Shapack and Focus, offers remarkable amenity space. Gold-paneled elevator doors open at the level 17 amenities floor. To the south is an informal game room and kitchenette. At the east end, with views of the skyline, an NBA size basketball court has double-height laminated glazing on three sides—250 feet above the street. For large events the hoops can be folded up to the ceiling, and the space can be transformed. To the north, the space opens onto a large terrace. The Class A spec office spaces use a VRF system, separating outside air from each tenant. Designing Year-Round Outdoor Spaces, pg. 338
Cooling strategies were emphasized as part of the design of this Guadalajara International airport terminal.
Arcadis’ free web-based tool revolutionizes low carbon, climate-friendly design.
BY PABLO LA ROCHE, ARCADIS
Understanding climate and developing an appropriate architectural response is the foundation of sustainable design. With climate change affecting every region of the world, it has become of the utmost importance for architects and designers to adopt practices that mitigate environmental impact, reduce GHG emissions, and aid in creating structures that respond to the specific conditions of their location.
At Arcadis we have developed and shared CLIMATESCOUT—a free web-based tool designed to assist architects, designers, and urban planners in creating buildings that are more responsive to their surrounding climate and biome. CLIMATESCOUT aims to promote carbon-free buildings by connecting climate data with architecture. It serves as a resource for sustainable design advice that considers both a site’s environmental factors and the architectural strategies needed to create a more harmonious relationship between buildings and nature.
A core feature is its use of the Köppen-Geiger climate classification system, which divides the world into distinct climate zones
based on temperature and precipitation patterns. By incorporating this system CLIMATESCOUT provides users with climate-specific design strategies from Architecture 2030. This tool allows architects to create buildings that meet the needs of the people inhabiting them while also responding appropriately to the environmental challenges presented by their respective locations. Our team uses CLIMATESCOUT early in the design process to understand what strategies are appropriate for each specific project.
The app is interactive and intuitive, featuring diagrams that allow users to see how architectural responses can change based on the climate. This connection between sustainable design strategies and specific climate conditions in real-time is a crucial aspect of CLIMATESCOUT. It enables users to better understand how to adjust their building designs based on the surrounding environment, supplementing both functionality and sustainability. By providing design guidance tailored to each site’s unique conditions, architects can create efficient and ecologically harmonious buildings.
Ultra-low conductance polyurethane foam for superior strength, durability, and unrivaled U-factors.
Buildings are currently responsible for 39% of global energy-related carbon emissions—28% of that comes from operational emissions, from the energy needed to heat, cool, and power them, and the remaining 11% from the materials and construction, according to the World Green Building Council.
V2 incorporates operational carbon data, or the carbon emissions associated with energy use during a building’s lifespan. To address this CLIMATESCOUT V2 includes a grid carbon intensity map, providing users with data on the carbon intensity of energy grids in countries worldwide. This feature allows architects and designers to evaluate, based on a target Energy Use Intensity (EUI), how their buildings’ energy consumption will contribute to carbon emissions, enabling them to make informed, data-driven design decisions.
Users can assess the carbon impact of their building based on location, EUI, and grid carbon intensity, and adjust their designs accordingly to minimize their carbon footprint. The grid carbon intensity map also includes annual averages and historical data, making it easier for users to analyze the impact of the energy grid on operational carbon intensity for specific regions. This data is updated annually.
Energy Star’s Target Finder can be used to determine the median EUI for the property type and size in the selected location. Using the information from Target Finder, the carbon calculator will estimate the carbon intensity (kgCO2e/m2yr) and the total carbon emitted per year (kgCO2e/yr), assuming the building is all electric. Different targets can be selected and calculated. The app is currently being used in professional practice and academia worldwide.
CLIMATESCOUT’s ability to connect climate data, operational carbon, and architectural design makes it a crucial tool for the global design community. As cities and countries advance legislation mandating net-zero carbon emissions for new buildings— particularly high-energy-use structures like laboratories, hospitals, and manufacturing facilities—tools like CLIMATESCOUT are essential for achieving these ambitious sustainability goals.
Design of the San Antonio Military Medical Center is seen above. Developed by Arcadis, the CLIMATESCOUT App helps design teams create more sustainable buildings.
Combine varied panel depths, sizes and colors to create your artistic vision. This incredibly versatile metal cladding system will inspire you. Acheive unique sculptural façades using PAC-CLAD’s extensive PVDF color palette including brilliant metallics, warm wood grains and elegant ore finishes. Spell words, form logos, shapes or images with perforation. Explore the possibilities.
1 3/8” to 3” Depths
Autex Acoustics Pg. 4, 94 autexacoustics.com 424.203.1813
DuPont Performance Building Solutions Pg. 144 armorwall.dupont.com 1833.338.7668
The Belden Brick Company Pg. 103, 108 beldenbrick.com 330.456.0031
Bradley Company Pg. 72, 330 bradleycorp.com 800.BRADLEY
Bromic Heating Pg. 342 bromic.com 800.301.1293
Ecore International Pg. 18, 180 ecoreintl.com 717.295.3400
Gate Precast Pg. 138 gateprecast.com 904.813.6525
Hunter Douglas Architectural Pg. 164 hunterdouglasarchitectural.com 800.727.8953
Hussey Seating Company Pg. 322 husseyseating.com 207.676.2271
InSinkErator Pg. 30 insinkerator.com 800.558.5700
GCP Pg. 85 gcpat.com 866.333.3726
Coronet LED Pg. TK coronetled.com 973.345.7660
GPS Air Pg. TK gpsair.com 980.279.5622
Nawkaw Pg. 44 nawkaw.com 866.462.9529a
ODL Pg. 172 odl.com 800.253.3900
Primacoustic Pg. 218 primacoustic.com 604.942.1001
LP Building Solutions Pg. 132 lpcorp.com 615.986.5600
MDC Interior Solutions Pg. TK mdcwall.com 847.437.4000
Sherwin-Williams Pg. 24 sherwin-williams.com/protective 800.524.5979 Schöck North
Schöck North America Pg. 52 schoeck.com 855.5724625
Concrete design isn’t just gray – in fact, it’s any color and finish you can imagine.
Textured concrete molds create the canvas on which we craft the look you’ve always envisioned. Through Nawkaw, you can embrace the looks of stunning & unique natural materials without sourcing, extracting & depleting those resources from the environment. All rendered in highly-durable, energy efficient concrete facades & long-lasting stain with low or zero-VOC content.
Nawkaw isn’t a just a product manufacturer or an application service. It’s a proprietary custom color solution backed by an in-house team of scientists. It’s a personalized color consultation and expert application service available in North America, Australia, and beyond that’s proven to last decades, not years.
Give us a call – and discover why architects, designers & producers around the world have worked with Nawkaw for over thirty years.
By choosing Ecore’s performance surfaces, you’re not only investing in high-quality flooring but also contributing to environmental sustainability by repurposing rubber that would otherwise end up in landfills. These innovative surfaces are designed with recycled materials, aligning with eco-friendly practices that help reduce waste and conserve resources.
ecoreintl.com
This deep-seating furniture, designed by Tuuci founder Dougan Clarke, combines luxury, durability, and craftsmanship (more on pg. 354). The innovative Aluma-Weave technique from Tuuci enhances each frame, while the Aluma-Forge joints use cold-weld technology for superior structural resilience
and artisan quality. The collection is accented by the Meritage Bezel, adding a fine jewelry detail that elevates its sophistication. Choose from six Aluma-TEAK finishes for the timeless look of wood without the upkeep. There is also the option to blend with eight powder coat colors.
TUUCI.COM
TUUCI’S LUMA COLLECTION HAS A SCULPTURAL AESTHETIC FEATURING THE ALUMA-WEAVE DESIGN DETAIL, FUSING ARTISTRY WITH MASTERFUL CRAFTSMANSHIP.
Is it wood? Is it metal? The new PAC-CLAD Timber Series wood grain finishes from Petersen include a range of colors from rich browns to shades of gray and white. The simulated PVDF finishes can be applied to all PAC-CLAD soffit and wall panel systems and feature a consistent wood grain pattern that may make observers pleasantly pause when they realize the appearance of wood is actually metal. The five finishes combine the beauty of wood with the durability of metal. The Waterford Bay project in St. Paul, Minnesota was designed by BKV Architects using multiple PAC-CLAD profiles in weathered zinc, matte black, a custom rustic amber, and a custom classic II bronze.
The Waterford Bay project is a partial-wrap residential concept with a parking structure at its center and dwelling units surrounding it on three sides. PAC-CLAD.COM
Inspired by nature with all of the benefits of tile, the RIVA Wood Tile Collection features porcelain tiles in seven colors—pearl, cotton, crystal, sand, smoke, earth, and amber. Measuring 10-by-60 inches, the tiles are designed to match the color and width of RIVA MAX natural wood flooring, which is sourced sustainably from European forests. Tiles have a sleek, knot-free appearance, designed to look like wood with the durability and cleanability benefits of tile.
The large-format tiles coordinate with wood collections, allowing for seamless designs from interior wood to match tiles in high-moisture areas. RIVA Wood Tiles are water-resistant, slip-resistant, and easy to clean, offering a feeling of elegance and timelessness in any space.
The fourth-generation family business with roots in Spain uses rectified porcelain tiles sourced from reputable factories in the country through established relationships the brand has made over the years. RIVASPAIN.COM
Pursuing better.
We pioneered the first PVC-free wall protection. Now, we’re aiming for every 4x8 sheet of Acrovyn to recycle 130 plastic bottles—give or take a bottle. Not only are we protecting walls, but we’re also doing our part to help protect the planet. Acrovyn sheets with recycled content are available in Woodgrains, Strata, and Brushed Metal finishes. Learn more about our solutions and how we’re pursuing better at c-sgroup.com.
San Francisco–based sustainable design and build company Fyrn recently unveiled its new Keyhole Collection. The collection gets its name from the proprietary brackets seen through “keyholes” in the solid-wood tops of the table and bench. Made in the USA of high-quality, North American Hardwoods, each solid wood piece is one-of-a-kind, celebrating the unique natural characteristics of the material. Table lengths can be customized between 66 and 144 inches (bench lengths from 39 to 92 inches).
Fyrn was created by a fourth generation woodworker with furniture design rooted in circularity. The company prioritizes minimal raw material waste, maximum durability, and easy repair or refurbishment for a long life for its pieces. Shipping, too, is considered, as the pieces are built to flatpack, ensuring efficiency. FYRN.COM
This project in Helsinki’s iconic Market Square ushers in a new generation of Finnish large-scale wood architecture. Anttinen Oiva Architects designed the building entirely of mass timber elements. The four-story project now houses the head office of Finnish forestry company Stora Enso and a 164-room hotel, all made from Finnish and Swedish timber. For the facade, a special two-layer solution was developed.
“A double skin was the best solution given the architecturally and technically challenging maritime context,” says Selina Anttinen, architect and partner at Anttinen Oiva Architects. “The outer protective layer integrates with its stonebuilt surroundings and is made of glass with vertical white metal lamellas and natural stone. The building’s appearance transforms in different times of the day and lighting conditions and fits the various scales and motifs of the surrounding buildings from the different historical eras.”
Promoting wood construction is key to achieving Finland’s carbon neutrality goals. Inside, wood continues to tell the story of strong Nordic nature. AOA.FI
Intumescent fire protection solutions were used on the interior and exterior of the Brunel Building in London.
The sustainability, health, and design benefits
BY RUSS KLETTKE
Architects design from outside in or inside out. And now they can give thought to the inside of the inside early in the process.
Stories of star architects sketching out the contours of great buildings on a napkin over dinner with the client are legendary. Reportedly that’s the origin of the Sydney Opera House (Jørn Utzon), Guggenheim Museum New York (Frank Lloyd Wright), Walt Disney Concert Hall (Frank Gehry),
and Denver International Airport (Curtis Fentress, see pg. 314). It’s the grand inspiration of the project that prompts clients to commit to building it.
But the vast majority of the built environment, addressing important but perhaps less-glamorous needs, comes about in more pragmatic ways. Most working architects start with the program, designing structures that serve their purposes. It’s
what ultimately makes the building work for the people who will occupy it. What’s adding a layer of complexity to this are the urgent needs of sustainability and healthy buildings. The LEED certification pro gram, among other sustainability-driven certifications, and the WELL building standard require architects to think through carbon footprints and healthy indoor air quality. No less import-
SHERWIN-WILLIAMS MANUFACTURES INTUMESCENT FIRE RESISTIVE PRODUCTS DESIGNED FOR ONSITE AND OFFSITE APPLICATION TO PROVIDE FIRE PROTECTION OF STEEL.
ant is maintaining structural integrity in the case of a fire, arguably a sustainability measure. When such needs are addressed early in the design process a lot more can go right in later phases.
Since the 1970s the use of intumescent coatings has replaced concrete as a means to protect structural steel in buildings. It works—as fires burn, the coatings react to heat by forming a thick, carbonaceous, insulating char layer to protect structural elements from the fire. Things still heat up, of course, but it gives sprinkler systems and fire departments more time to bring down the flames and save the building. And replacing all that concrete reduces the carbon inputs on the buildings and enables greater design latitude for architects.
Intumescent coatings currently supplied by Sherwin-Williams go beyond the initial version of the product. First, contemporary buildings are often designed with exposed structural elements as part of the aesthetic—and the design might call for something other than an institutional gray or off-white.
“This is important to architects,” says George Guanci, fire protection market segment manager for Sherwin-Williams. “If an architect requires a color, for example in a hotel lobby, we can provide a topcoat for that color.” He says the product also has no dusting or flaking that might otherwise challenge its appearance.
Sherwin-Williams tests topcoats used with its intumescent fire resistive products. The International Building Code requires that either UL-263 or ASTM E119 be the standard for intumescent fireproofing. Varying thickness requirements for intumescent fireproofing is required depending on the mass of steel, the required hourly rating, and whether the steel is used as a beam or column.
Intumescent coatings were once solvent-based with high VOCs, Guanci says. But Sherwin-Williams also provides water-based products with a much lower VOC level.
This matters, as more building owners and their occupants demand healthy interior environments. The WELL standard has specific requirements for VOC reduction in paints, coatings, adhesives, and sealants used in buildings. This looks at not just the content of the coating but emissions from them over time.
To satisfy LEED and other green building standards—as well as anyone concerned about climate change—Sherwin-Williams also addresses the carbon footprint of its products. It provides data in product EPDs (Environmental Product Declarations), a “cradle-to-gate” data point. But it also goes several steps beyond that with cradle-tograve EPD data.
Architectural coatings are assessed according to Product Category Rules, or PCRs. These consider the likely lifespan of a building and when paints and coatings need to be reapplied, which is typically at around 60 years.
Hearkening back to the architectural design process, these are important but complex calculations to make while matters of form, function, massing, economics,
context, and traffic flow are high priorities. But there is a tool that make it possible.
Guanci shares how Sherwin-Williams’ third-party verified design and estimation software, called the Fire Design Estimator, can calculate accurate quantities and thicknesses of intumescent products that will be needed in the projects. The tool looks at the precise quantity of materials, which vary in quantity and thicknesses, and factor for the carbon equivalences. With speed and efficiency the FDE can help optimize the amount of intumescent material to be used as well as how it can factor into green building credit systems.
The FDE might not be a part of those high-level napkin conversations. But once the project moves ahead to the actual architectural design phase, it’s a valuable tool for making a project greener. All while the product ensures that design and wellness goals are met. g
WHY INTUMESCENT FIREPROOFING IS IMPORTANT
• WHEN STEEL REMAINS UNPROTECTED AND IS EXPOSED TO TEMPERATURES NEARING 1,000ºF, IT UNDERGOES A REDUCTION OF APPROXIMATELY 50% IN ITS LOAD-BEARING CAPACITY.
• FIREPROOFING IS MEANT TO INHIBIT STEEL FROM SURPASSING THIS CRITICAL TEMPERATURE THRESHOLD.
• INTUMESCENT COATINGS ARE MADE WITH PIGMENTS THAT INITIATE A REACTION WHEN THE STEEL CORE TEMPERATURE REACHES APPROXIMATELY 300°F. THIS PROMPTS THE FIREPROOFING TO EXPAND AND GENERATE A CHAR, WHICH PROVIDES FIRE-RETARDANT PROPERTIES TO THE STEEL.
Sherwin-Williams tests topcoats used with its intumescent fire resistive products. The International Building Code requires that either UL-263 or ASTM E119 be the standard for intumescent fireproofing.
At MDC Interior Solutions, we’re committed to delivering sustainable, innovative design solutions like Zintra. Red-List Free and certified by Declare, GREENGUARD, and HPD, Zintra is thoughtfully crafted from 95% recycled content and is fully recyclable.
This eco-conscious product not only enhances acoustics but also promotes sustainability in corporate spaces. Available in versatile options such as
solid panels, ba es, and drop-in ceiling tiles, Zintra seamlessly adapts to any environment, creating productive and environmentally responsible workspaces.
Our commitment to you goes beyond products. With custom design capabilities through our digital studio, we tailor solutions that meet your unique needs. From PVC-Free wallcoverings to tackable surfaces, dry erase solutions, and architectural
panels, we provide the tools to elevate your o ce’s performance and aesthetics.
Plus, our nationwide team of personal account executives is here to support you every step of the way, ensuring on-the-ground service wherever your project takes you. Let MDC Interior Solutions help you shape healthier, more sustainable spaces.
Discover more at mdcwall.com.
WASTE REDUCTION
InSinkErator innovates to help families and companies be more sustainable.
BY LISA WHITE
As landfills become oversaturated, technology is being developed to sustainably divert food waste. This couldn’t come too soon, as more than 20% of the approximately four-and-a-half pounds of trash that the average American generates per day is food, according to the EPA. Only about onethird of that is recycled or composted.
After the USDA and EPA released the US 2030 Food Loss and Waste Reduction Goal in September 2015, the White House, along with the EPA, USDA, and FDA, launched
the National Strategy for Reducing Food Loss and Waste and Recycling Organics in June 2024. The effort lays out a path for the US to meet its national goal of reducing food loss and waste by 50% by 2030. The strategy aims to reduce greenhouse gas emissions, save households and businesses money, and build cleaner communities by reducing food loss and waste.
“According to the latest numbers by the EPA in 2019, an estimated 66 million tons of food is going to waste in the US, not includ-
ing industrial waste,” says Casey Furlong, environmental specialist at InSinkErator.
“Approximately 60% of this is coming from commercial, and 40% from residential.”
The good news is that wastewater treatment plants can convert disposal waste into renewable energy and beneficial fertilizer. Using
IN 2019 AN ESTIMATED 66 MILLION TONS OF FOOD WENT TO WASTE IN THE US.
FOOD WASTE, WHEN LANDFILLED, PRODUCES METHANE, WHICH IS 28 TIMES MORE P O TENT THAN CARBON DIOXIDE.
a garbage disposal in conjunction with wastewater treatment without anaerobic digestion can lower Global Warming Potential (GWP) by at least 50% compared to landfills, according to the Life Cycle Assessment report by PE Americas. And if the community uses an advanced wastewater treatment plant, GWP is lowered by at least 90% compared to landfills.
“The federal government is looking to divert food waste from landfills and repurpose it,” Furlong says. “We can recover water in food and, with anaerobic digestion, we can recover natural gas. We also can utilize bio solids from food waste to create fertilizer.”
According to four international Life Cycle Assessment (LCA) studies, using a disposer with anaerobic digestion can be comparable to composting from a GWP reduction. Installing a disposer as part of a new build earns a one point green building credit through the National Green Building Standard, according to the ICC.
To help with the government’s food waste initiative, the InSinkErator brand has made significant investments in its garbage disposal lines over the last three years. “There are major areas where we are innovating,” says Drew Carmichael, director of product development, strategy, and innovation. “First is the quality of the grind and what can be put in the disposal. We’re always finding new ways to make food waste into a slurry that can be transported to wastewater treatment plants.”
InSinkErator garbage disposals are inherently green tech. Using a garbage disposal in conjunction with wastewater treatment with anaerobic digestion, food waste can be converted into energy, thereby lowering GWP by at least 90% compared to landfills.
InSinkErator has launched multiple product lines that address various types of end users and their needs. “Core to that strategy is incorporating multiple levels of grind with our MultiGrind® Technology to grind food waste into finer particles,” Carmichael says.
InSinkErator brand’s Badger series disposers have one stage of grind. The Power series offers additional horsepower, along with a second stage of grind. Finally, the Advanced Series adds even more horsepower for up to four stages of MultiGrind Technology.
InSinkErator is also launching products in 2024 that support digestion of septic solids. InSinkErator Boost™ Septic Guard is scientifically proven to break down food waste
to support septic systems, providing added assurance to homes on a properly maintained septic system. “The new product can break down pipe buildup and helps reduce sink odors,” Carmichael says.
On the commercial side InSinkErator is also helping businesses, stores, restaurants, hospitals, and universities meet their sustainability goals. The Grind2Energy® food waste recycling system was developed for large generators of food waste. It’s currently being used at Ohio State University, Notre Dame University, Gillette Stadium, and Whole Foods Markets. “It provides a more sustainable solution to dispose of large amounts and all types of food waste, including grease and oils,” Carmichael says.
The Grind2Energy system is the only full-circle, closed-loop food waste recycling system of its kind. “Food is put in a large disposal and ground onsite, then pumped
into a holding tank before being trucked to an anaerobic digester,” Furlong says.
Once at the anaerobic digestion facility, methane is removed from the energy-rich slurry and turned into renewable energy. The remaining biosolids are turned into nutrient-rich fertilizer to help grow more food. “To date Grind2Energy has helped divert more than 112 million pounds of food waste from landfills,” Furlong says. “The fugitive methane resulting from landfilled food waste is 28 times more potent than carbon dioxide’s contribution to climate change, according to the EPA.”
On the residential side InSinkErator conducted a study in five cities to measure food waste. It found that about 30% of household food waste was diverted from landfills using disposals. “If disposals were not yet invented, this is the perfect time for them,” Furlong says. g
BY DAVID MILLER
When it comes to dealing with decks and walkways, properties near the ocean present a unique set of challenges. High humidity can cause materials to swell, warp, or develop mold and mildew, UV exposure can break down coatings, and temperature fluctuations between night and day may cause decks and walkways to expand and contract. As such, selecting the right waterproofing system is vital to maintaining the health of a beachfront property.
“Oceanfront properties have a different set of problems. Things like rusting rebar
Did You Know?
COASTAL PROPERTIES FACE HEIGHTENED RISKS DUE TO HIGH HUMIDITY, UV EXPOSURE, AND TEMPERATURE FLUCTUATIONS, BUT WATERPROOFING SYSTEMS CAN HELP.
that’s two inches below the surface of the concrete with concrete that is crumbling and falling apart, or you may have structural issues—items breaking down underneath top deck area,” says Marc Di Zinno, regional sales manager at Westcoat. “It is a different set of challenges. We are always concerned with the amount of moisture, and there’s the marine layer that comes in almost every day of the year on the coast of California. These types of environments with moisture making contact with these decks can completely destroy certain types of metals very quickly.”
Consider Surfsong HOA, a beachside condominium community in Solana Beach, California. When Di Zinno visited the site, he found that the coating had expired and there were a number of issues with the details of the previous deck systems’ construction. Copper flashings underneath the thresholds had been broken through and were touching galvanized steel flashings. When two dissimilar metals touch each other without some kind of go-between, it can lead to a process called galvanic corrosion, Di Zinno says. This occurs because some metals are more reactive than others. When moisture is present, the more reactive metal starts to break down or corrode faster. As one metal corrodes it can weaken the surrounding materials. In the case of Surfsong, this issue with the initial construction was leading to water infiltration that was eroding the pre-existing coating. Before Westcoat’s involvement, repairs were being conducted twice a year to fix areas with problems. “They just kept putting a Band-Aid on it, but they never really dug into what the source of the problem was,” Di Zinno says.
For this particular project, the applicator General Coatings Corporation was able to remove the worn-out solution from a competitor on the original concrete surfaces before preparing the concrete surfaces for an application of Westcoat’s MACoat—a fiberlath reinforced deck system installed with a series of waterproof acrylic applications and sealed with a clear sealer.
Di Zinno stresses that it’s issues like those uncovered in Surfsong’s previous deck system that make it so important to get things right from the start. To that end, he recommends strong oversight by construction management when tackling complex projects.
“What often happens is a sheet metal company comes in and does its work, and they might be very good at cutting, bending, and fastening sheet metal, but then you have a separate contractor who is going to do a waterproof deck coating application. He may also be very good at what he does, but he knows he didn’t get paid at all to have anything to do with the flashing, so he says to himself, ‘Oh, I assume that the flashing works and the pillars, drains, and rails are done because it’s none of my concern’,” Di Zinno says. “He’ll then install a waterproof deck coating system per specification, but because the trades weren’t talking to each other, there may be problems.”
He says construction management can avoid situations like this emerging in the first place. By making sure the trades communicate with each other and appropriately coordinate their work, a more effective overall installation can be ensured.
Effective waterproofing doesn’t have to come at the expense of aesthetic appeal, either. Often clients seeking a less commercial finish will opt to install tile over their
waterproofing system for decorative purposes. However, even with an appropriate waterproofing membrane that allows the tile to be safely applied, it may be difficult to identify water intrusion should it occur, Di Zinno says.
To solve this problem Westcoat offers a variety of systems that allow for a shapeable cement-based layer to be applied on top of a waterproofing membrane. Scoring can then be used to create grooves or joints that give the surface the appearance of tile. Finally, color stains and finishes can be ap-
plied to emulate the look of natural stone and other common aesthetics. Westcoat’s Texture-Crete system is also one of a few different options that allow for a more decorative surface.
“The beauty of this is that it gives people the aesthetic qualities that they are after, but the priority is still the waterproofing,” Di Zinno says. “People often want things to look very nice, and so the priority tends to become the aesthetics. However, it really needs to be the waterproofing integrity because if there’s a leak all bets are off.” g
Leveraging the science of adhesion to redefine the way we think about architectural drainage
STAINING MASONRY AND CONCRETE ADDRESSES MANY OF THE FLAWS OF TRADITIONAL PAINTS. METALLIC FINISH WORK BY NAWKAW IS SEEN HERE.
BY MATT WATSON
Concrete is the most common building material on earth. It’s durable, versatile, and affordable, yet few architects or designers would say it’s at the top of their list of visually appealing materials to work with. While some solutions make it more aesthetically pleasing, painting concrete can lead to its deterioration when moisture gets trapped under the coating. As a result, concrete and masonry stains are rising in popularity, as they form penetrative mechanical bonds, chemical bonds, or both with the substrate they are applied to, increasing durability and lifespan.
“Architects and designers are always keen to look toward the full life cycle of their designs,” says Kasia Purzycka, president of Nawkaw, a leading manufacturer and installer of architectural finishes, including concrete stains. “They’re considering upkeep costs and carbon emissions throughout the first five, 10, 15 years of a building’s maintenance and operations.”
The versatility of stains opens up nearly limitless design opportunities. “Concrete staining really allows you to leverage the materials that are already there and allows you to get more of an elevated finish on a base product,” says Charles Kimmel, architect at Perkins Eastman.
For architects and project teams looking to craft unique designs with masonry and concrete, stains offer a far broader range of opportunity than traditional paint solutions and allow designers to bring new life to these traditional materials.
“Stains give you a range in the color palette that you can’t get with paint pigments, where you can get into the darker colors and match the masonry with the style of the architecture,” Kimmel says.
Nawkaw’s suite of stain solutions include translucent finishes, metallic and glossy finishes, and pearlescent looks. Their technicians have applied their products onto formlined concrete surfaces to replicate the look of wood, stonework, metal paneling, leather, and cork, among other natural textures.
The exact details of their process are a proprietary secret, but how Nawkaw’s technicians can so closely replicate natural materials is all about the application. Replicating the look of wood on concrete, for example, involves applying a base coat and then using a sponge to add accents that mimic the look of wood grain.
“Limitations on what you can do with stains often fall to the imagination of the designer or architect,” Purzycka says.
Nawkaw’s precast stain work is seen here.
“As we move deeper into the decade, the white and black look is slowly giving way to new and beautiful shades of natural greens, warm neutrals, and blues.”
The versatility of stains allows designers to be far more adventurous with concrete and masonry structures than before. Perkins Eastman, for example, turned to concrete stains for the design of a new residence hall at Frostburg State University in Maryland.
“To get the dark black that we wanted on the exterior precast concrete of the building, stain was the only way to get there,” Kimmel says.
The bold design of the six-story, 125,000-square-foot residence hall put the finishing touches on a previously underused residential quad on campus.
In terms of aesthetic appeal and color, experts point to a high demand currently for clean, modern finishes.
“Monochromatic looks are highly popular,” Purzycka says. “As we move deeper into the decade, the white and black look is slowly giving way to new and beautiful shades of natural greens, warm neutrals, and blues.”
The trend of replicating various materials using color and formlined concrete is growing and shows little signs of abating. This approach increases durability and reduces costs as well as the delays often associated with sourcing materials like metal paneling or natural wood.
“Those looks and more traditional looks such as brick and mortar can each be replicated utilizing high-quality stains paired with textured or even smooth concrete surfaces,” Purzycka says.
With elevated material and labor costs and some supply chain issues never fully recovered from the pandemic, many customers are searching for a high-performance color solution they won’t need to worry about in the decades to come.
Many others also demand their products be sustainable.
“It’s a real cultural shift and sea change we’re seeing from younger generations, and rightfully so,” Purzycka says. “It is a moral imperative we all need to strive for.”
“
I think it’s critical we stay clear-eyed about the impact construction has on our environment. No matter how you look at it, concrete production makes up an outsized amount of annual carbon emissions.”
Perkins Eastman used concrete stains on a new residence hall at Frostburg State University in Maryland to get the shade they wanted on the exterior precast concrete of the building.
All sectors of the building industry have seen a major shift recently toward historical preservation work and existing building retrofits, driven in part by federal, state, and local incentives that aim to combat greenhouse gas emissions from the built environment. “Oftentimes the most sustainable building is the one that is already built,” Purzycka says.
Concrete and masonry stains are regularly used to support projects that restore legacy buildings to their original design and colors. “In smaller communities especially, this work is preserving iconic elements of a town’s culture for future generations.”
This work extends to historical landmarks in major cities as well. Built in 1878, the Cincinnati Music Hall had well over a century of exposure to the elements when its owners embarked on a major renovation that included extensive improvements to the building’s interior and exterior.
Years of tuckpointing, wall replacement, and infill work on the music hall’s facade left the brick exterior uneven and visually disjointed. Nawkaw’s team used the firm’s color-matching stain solutions to create a cohesive look across the facade while masking repair and infill work.
“We were able to blend the color of
mismatched bricks and mortar work and return the facade to its former glory,” Purzycka says. “It’s incredibly and deeply rewarding work to return a building this old to its original form.”
While concrete is prolific in the built environment, it is also considered one of the least sustainable materials to create and transport. And given that truly sustainable concrete solutions are still being scaled for mass production, current efforts must also focus on increasing the longevity of existing concrete structures—and stains can add decades to the life of the material.
“I think it’s critical we stay clear-eyed about the impact construction has on our environment. No matter how you look at it, concrete production makes up an outsized amount of annual carbon emissions. We have a fiscal, ethical, and moral imperative to lead the way when it comes to sustainability,” Purzycka says.
Because of the high durability of concrete and masonry stains, these finishes will last for decades with proper maintenance and can improve the durability and lifespan of
the materials they envelop, too. “That’s far simpler, more cost effective, and more sustainable than maintaining even a premium paint coating on a similar substrate,” Purzycka says.
Unlike traditional paints, stains penetrate the substrates they are applied to and form strong mechanical bonds, chemical bonds, or both—serving as a densifier to concrete and masonry, she says. Stains are also more permeable, allowing moisture from rain and snow to evaporate more efficiently than it is absorbed into the facade.
“Why is that good? Because the stain won’t peel; it’s a permanent bond,” Purzycka says. “You won’t experience the problem of facade deterioration.”
Even high-quality paints, including premium acrylic and epoxy-based coatings, can seal off the natural voids and channels in concrete, entrapping moisture, she says. “Good stain products have a permeability of 25 perms. Our products show around 80 perms for a single coat, and we’re happy with that.”
Trapped moisture can also contribute to carbonation of concrete and cut short its lifespan. Similarly, moisture trapped in a brick facade can cause deterioration and spalling of the bricks. gb&d
BY IAN P. MURPHY
Buildings exist to protect their inhabitants from the harsh extremes of the climate outside. But no building is hermetically sealed; despite advancements in insulation and fenestration, they continue to allow the transfer of heat and energy.
“Energy is going to find the path of least resistance,” says Nate Lambrecht, regional sales manager for Schöck North America. “It’s like in a cartoon where someone sticks their finger into a leak to stop it and a new leak springs up. Even if you plug all of the holes, whatever is on the other side is going to try to get through.”
Junctions in the building envelope may be the final frontier in lessening the effects of energy transfer or thermal bridging, particularly when the outside air is colder than the conditioned environment inside.
“Walls are already doing a really good job at mitigating heat loss,” says Cody Belton, passive house specialist and building enclosure consultant with Stantec, the global engineering, architecture, and environmental consulting firm. “It’s the transition details that are the problem. [We recommend] trying to mitigate thermal bridging at any transition in the building envelope.”
That’s where thermal breaks come in. Low-conducting structural elements used to separate building components and stem the transfer of heat and condensation, they are catching on throughout North America as building codes become more environmentally conscious.
“Some municipalities are already pushing thermal breaks from a code standard,” Lambrecht says. “But you’re also seeing the design community say, ‘We want to put forth a good product,’ so this type of thing is coming into a lot more conversations.”
Company founder and civil engineer Eberhard Schöck was vacationing at a Swiss ski lodge in the 1970s when he noticed moisture and mildew growth on the ceiling of his room. Cold from the exterior balcony slab in the unit above was penetrating the concrete and reinforcing steel, cooling the surface to a temperature below the dewpoint of the interior air.
“Whenever you have a surface that’s below the dewpoint of the humidified interior air you are going to get condensation,” Lambrecht says. “This is a durability problem
and a health concern. If you’re going to build a building to the best possible standard, you’re going to use a thermal break to not only minimize heat loss but also eliminate the risk of condensation.”
Schöck’s Isokorb® portfolio of structural thermal breaks includes products designed for concrete construction, steel construction, floor slabs, and other applications. But the company is perhaps best known for the concrete-to-concrete thermal breaks used on the cantilevered floor slabs that form balconies.
The Stantec Tower in Edmonton, Alberta demanded thermal breaks to head off the potential of considerable energy transfer. The tallest skyscraper in Western Canada at 66 stories, the LEED-certified building houses the company’s headquarters and 36 floors of condominiums—17 of which have expansive balconies overlooking the city and windswept prairie beyond.
Architects specified load-bearing, concrete-to-concrete thermal breaks—1,590 in all—to create an insulated barrier between the balconies outside the building and the floor slab inside. Most are Isokorb assemblies, which feature a graphite-enhanced block of expanded polystyrene insulation
and stainless steel rebar for tension and shear resistance.
Depending on conditions, Isokorb thermal breaks can eliminate up to 95% of energy transfer through a concrete connection, according to Schöck. Thermal modeling indicated that the temperature of the Stantec Tower’s interior slabs would be up 6 to 7°C warmer with thermal breaks, eliminating the need for baseboard heating, preventing condensation from forming on adjacent surfaces, and reducing energy consumption for heating 7.3% compared to constructing the building with uninsulated balcony slabs.
Designing for thermal breaks has a few minor challenges. Primarily architects and engineers need to think beyond the uninterrupted slab to forecast the building envelope’s performance and structural integrity.
“It isn’t difficult to integrate thermal breaks into a typical project,” Lambrecht says. “There can be occasions where the loading is outside of what would typically be possible, but if considered early enough in the design process there is usually a solution.”
What’s more, thermal breaks are only part of the answer to an energy-efficient and sustainable building. “If you interrupt
a high-performance wall assembly with a highly transferable assembly of concrete and steel, you instantly reduce the benefit from the wall itself,” Lambrecht says. “And if you bought the cheapest window system, adding a thermal break is not going to solve your energy issues.”
The cost/benefit analysis of incorporating thermal breaks should consider their effect on the overall performance of the building envelope. The energy savings delivered has allowed some projects to downgrade from triple-glazed window systems to double-glazed systems, offsetting costs while still meeting operational and environmental goals.
“When you can mitigate heat loss and conserve more energy, you can significantly downsize mechanical systems,” Belton says. “Instead of putting a lot of money into oversized mechanical systems for heating or cooling, you can transfer that initial capital investment into a high-performance building enclosure.”
In abating moisture and condensation, thermal breaks can also head off costly maintenance. “A lot of people overlook the durability aspect,” Lambrecht says. “Beyond the energy performance, you’re looking at reduced overall maintenance and upkeep costs.”
Users benefit from an engineered and tested assembly. “We provide a nice, clean pass-
through to simplify the geometry and still provide continuity to the building envelope,” Lambrecht says. “We can build to a higher standard without massive increases to cost if we plan it well.”
While some building codes still ignore the problem of thermal bridging and require only added insulation, others are embracing thermal breaks as a step toward net-zero energy or net-zero carbon goals.
“We’re getting much more sophisticated with our building envelope design,” Lambrecht says. “Major municipalities are updating building codes, and they’re pushing thermal breaks to be more of the norm as opposed to the exception. It’s part of a more holistic approach of saying, ‘OK, how do we make the tightest building envelope possible?’”
Architects, engineers, and developers seeking to decrease energy transfer and preserve building integrity are also waking up to the benefits, particularly in settings where consistent interior temperatures are desired. Several museums (including the Statue of Liberty Museum), the under-construction Obama Presidential Center in Chicago, and a hospital above the Arctic Circle have Isokorb breaks specified to guard against energy transfer.
“Higher performance energy targets are changing the way we design buildings for
Stantec Tower in Edmonton, Alberta stands at 69 stories and required thermal breaks to head off the potential of considerable energy transfer.
the better,” Belton says. “We definitely need solutions such as Isokorb—anything that’s going to mitigate thermal bridging.”
In a post-construction research study led by Belton, Morrison Hershfield (now Stantec) applied the lessons learned from 825 Pacific to develop a market-ready, high-performance window connection for wall assemblies that use exterior insulation. The Akira Window Connection is a window and door dead load support system with intermittent brackets fastened to the backup wall structure and continuous angle supported by the brackets. The continuous angle is decoupled from the backup wall to reduce heat transfer and simplify air and moisture barrier detailing.
This connection method results in nearly thermal bridge–free linear transmittance values at window-to-wall transitions, improving whole-building thermal energy performance. On an affordable housing project in North Vancouver, for example, the company found that incorporating Akira Window Connections cut the 10 inches of exterior insulation needed to satisfy thermal energy demand intensity (TEDI) targets in half.
Armed with a Building Excellence Research & Education Grant from BC Housing, Stantec’s goal is to provide open-source thermal bridging data on the new system’s performance for any project team to use. “Adding insulation is kind of the go-to solution to address energy loss,” Belton says. With the Akira Window Connection system, “we can make facades more cost-effective by decreasing exterior insulation costs. That thins the external walls and has the potential to create more interior floor area.” gb&d
BY RACHEL COON
Building aesthetics often follow lifestyle trends—and as more people seek the comfort and simplicity of nature, homeowners also look for ways to bring the benefits of the natural world indoors. A desire for daylight and unobstructed views leads to one obvious solution: more glass.
“In our single-family residential projects, we work extensively with window companies to find creative solutions to complex problems,” says Ray Calabro, a principal in the Seattle studio of Bohlin Cywinski Jackson (BCJ).
“We use glass in innovative and often unexpected ways—creating more meaningful connections between people and environments, enhancing building efficiency and performance, and contributing to the overall architectural expression of a project,” Calabro says.
It’s that demand for unexpected solutions that has driven Cardinal Glass Industries for more than 60 years. The largest producer of insulated glass (IG) units in North America, Cardinal delivers glass products with endless possibilities.
“We are always looking to lead the industry in performance and durability,” says Pete Whaley, project manager of product integration and stakeholder experience at Cardinal Glass. “It’s one thing to have the ideas; it’s another to execute and bring those dreams into the real world.”
Historically new glass products have been driven by thermal performance requirements. As building codes have slowly progressed, glass production has, too. Most modern homes have some version of insulated glass in their exterior windows and doors. But where many glass companies miss the
mark on longevity, Cardinal has led in IG durability, performance, and technology with a remarkably low 0.1% claim rate on its 20-year warranty, Whaley says.
Cardinal’s various LoĒ (low emissivity) coating options improve thermal efficiency, lower solar heat gain, and meet stringent performance standards. “Though Low-E coatings are not new, our technology has progressed,” says Ben Zurn, vice president of IG technology at Cardinal. “EPA’s Energy Star 7 came out last year, pushing performance levels higher. As smart home technology has become real, that has transferred into the glass and window market as well, so it’s not just thermal performance that matters, but also more user value.”
BCJ integrates solutions like Low-E glass and triple-glazed windows in many of its residential designs. “These solutions allow for energy efficiency and indoor thermal comfort without sacrificing the desired connection to the outdoors,” Calabro says.
Top architects point to modern home design leaning contemporary, with clean, minimalistic lines—a trend that lends itself to bigger and better glass solutions. “Our residential clients are interested in feeling connected to a particular place and/or view,” Calabro says. “We are interested in pushing the limits of size for both fixed and operable units to help our clients feel immersed within their surroundings.”
Designers are also looking for alternatives to anything that obstructs the view or infringes on design goals. “They want that view,” Whaley says. “And to draw that exterior light in and expand the feel of the home,” Zurn adds.
That feeling of being enveloped is exactly what BCJ’s clients were looking for at Henry Island Guesthouse in the San Juan Islands. “We wanted the guesthouse to immerse visitors in the extraordinary island landscape while providing a comfortable and efficient environment for year-round stays,” Calabro says.
The guesthouse overlooks a meadow on one side with expansive forest views and glimpses of the bay on the other. The project has a high-performance building envelope, including thermally broken wood windows and doors with insulated glass units.
“The central common space opens completely to the landscape,” Calabro says. “By incorporating two layers of enclosure—glazed lift and slide doors and insect screens—guests have the option to control how much of the outdoors they wish to experience. And with deep roof overhangs and operable windows in all spaces, daylighting and natural ventilation further enhance this connection to place.”
That increased desire for natural light combined with a continuing need for thermal protection and privacy led to Cardinal’s development of CLiC switchable privacy glass. “One of the more advanced subsystems in the smart home realm is lighting control. With products like CLiC you’re controlling not only the light you’re creating inside your house but also the light coming in from outside,” Whaley says.
Zurn says CLiC gives designers that clean, minimalist aesthetic while maintaining privacy. “You don’t have to blow up your building design in order to get that desired clean look.”
Traditional privacy glass consists of layers of glass, film, liquid crystal, and polymer. “It has multiple pieces that create a hazy milkiness that the industry just couldn’t engineer out, which is why it was never quite clear enough for residential products,” Whaley says.
For years Cardinal researched the advantages of existing products and evaluated many different material sets before ultimately finding a chemistry that allows them to make CLiC switchable privacy glass that is clear at all viewing angles. “We developed our own formulation of a liquid crystal that gets applied directly to the glass with no film in between—just a piece of glass, the liquid crystal, and then another piece of glass,” Whaley says. “It’s much clearer than
ABOVE The project has a high-performance building envelope, including thermally broken wood windows and doors with insulated glass units.
RIGHT The Henry Island Residence is a year-round gathering place. On arrival visitors step onto a staggered boardwalk and into an open foyer overlooking the bay.
any other switchable glass on the market.”
When an electrical signal is applied to a CLiC window, the crystals align to a completely straight grid, creating complete transparency. When there’s no power applied, the liquid crystals are randomized and scattered, providing privacy. “We didn’t want our customers to worry about the complexity of wires and electrical connections, so we built our own electronics and made them universal,” Whaley says. “CLiC is not complicated. Most experts in the field can install CLiC with their eyes closed.”
With CLiC IG units, designers get multiple benefits that standard IG units don’t offer, including privacy, acoustical control, storm protection, thermal performance, light filtering, forced entry protection, and comfort. Historically those were individual things a consumer or designer migh t want, but CLiC offers them all in one, Zurn says.
He says CLiC is the modern version of antiquated venetian blinds. “It’s the iPhone 27 instead of the Fred Flintstone flip phone.”
The building industry has seen an increased demand for glass across markets— from luxury residential projects to offices, retail, and health care.
BCJ clients are often surprised by the amount of flexibility and customizable options they have in residential. “Flexibility in operable units, in particular, helps give our clients a great deal of control over their environment in all areas of the home while helping circulate natural air throughout the day and strengthening biophilic connections to the outdoors,” Calabro says. gb&d
Elevating efficiency, airports are evolving to meet the demands of a tech-driven future. With Tate's innovative raised access floors, airports gain the flexibility to adapt seamlessly to changing technology and passenger needs. Our flooring solutions simplify infrastructure upgrades, reduce disruptions, and ensure quick, cost-effective modifications. Whether it's upgrading security checkpoints or integrating new data systems, Tate solutions help future-proof airports, enabling efficient power and data management underfoot. Experience unmatched versatility and sustainability with Tate—designed to move with the future.
Phone number: 410-799-4200
email: info@tateinc.com
FRANKLIN TOWER IN PHILADELPHIA, REIMAGINED AS RESIDENTIAL BY GENSLER WITH PMC PROPERTY GROUP, USED TO BE A VACANT AND OUTDATED OFFICE BUILDING.
from a top architect on pushing the industry forward
WORDS BY MEGY KARYDES
As the world grapples with the realities of climate change, the built environment is finding ways to reduce its carbon footprint. Even small changes can make a large impact, considering the buildings and construction sector is the largest emitter of greenhouse gases, accounting for a staggering 37% of global emissions, according to a 2023 report from the UN.
Gensler is among those designing the path forward, with a goal of achieving carbon neutrality on all of its projects by 2030.
As the building and construction sector is responsible for more than one-third of global emissions, finding ways to lower or eliminate the carbon footprint is necessary to impact the effects of climate change.
For a company like Gensler, the largest architecture firm in the world, reaching carbon neutrality is not just an abstract goal; it’s a responsibility. But the journey toward carbon neutrality is complex, particularly when it comes to the selection and use of building materials. Gensler launched its Gensler Cities Climate Challenge (GC3) with the specific goal of achieving carbon neutrality, according to Vince Flickinger, principal and design director at Gensler’s Houston office and global practice area leader for energy.
As part of the GC3 efforts, Gensler says architects first have to be able to measure their impact in order to improve outcomes and reach carbon neutral goals. “To do that we must establish a universal and uniform method for measuring the operational and embodied carbon across all our projects. We are streamlining our data collection from consultants to wrap our arms around our operational carbon. To understand our embodied carbon output, we’re identifying accurate material quantities and assigning embodied carbon values to them,” they announced.
Often Flickinger and the Gensler team also have to ask themselves: How do we move toward carbon neutrality in a world that isn’t carbon neutral? They are turning their attention to materials. Strategies for reducing embodied carbon include right-sizing, selecting lowand zero-impact materials, reusing buildings instead of engaging in new construction, and offsetting impact through net-positive production and/or increases in carbon sequestration (captured through absorption), according to GC3.
To streamline the selection of materials that contribute to carbon neutrality, Gensler also recently developed the Gensler Product Sustainability (GPS) Standards (more on pg. 80). This initiative involves rigorous vetting of products based on their environmental impact, ensuring they meet or exceed specific standards.
“We look at all the documentation based on a standard, and this filter allows us to look at a list of products that we know have been vetted, that either meet or exceed [specific standards],” Flickinger says.
Gensler’s Morphable Office concept builds out a hypothetical office building in Baltimore to emphasize nature.
WORDS BY MEGY KARYDES
Proper lighting shapes how we experience spaces and plays a significant role in reducing the environmental impact of a building over its lifetime. “The right lighting and ambience can change people’s worlds,” says JR Krauza, vice president of product for Coronet LED, an architectural lighting manufacturer that designs and builds sustainable lighting solutions in the US.
Krauza says carbon neutrality in lighting can be divided into two primary phases: the production phase (cradle-to-gate) and the use phase (gate-to-end-of-life). The production phase involves the carbon emissions associated with manufacturing the lighting fixtures, including the sourcing of materials and the energy consumed during production. The use phase considers the carbon emissions generated by powering these lights throughout their operational life.
The pursuit of carbon neutrality has spurred innovation in design in many areas, and that includes lighting. Energy-efficient lighting continues to be in high demand from top architects, including those at Gensler. While the world’s largest architecture firm prioritizes natural light where possible, every other lighting element they choose must be super sustainable.
BIALEK HEADQUARTERS
This Bialek headquarters project designed by Gensler uses Magneto with linear and pucks.
“We try to use as little artificial light as possible, but when we do need it, it needs to be the most energy-efficient lighting fixture we can find,” says Stephen Katz, a principal and technical director in Gensler’s Chicago office. “Does it use the least amount of material and last a long time before needing repair or replacement? What is the recycled content of the materials? Those questions are just as critical as ‘Does it look good?’”
Coronet, itself a CarbonNeutral® company, is focused on designing energy-efficient fixtures that provide the best quality light to meet the needs of companies and designers who want to reduce their carbon footprint.
Coronet’s updated LS Series luminaires, including the LS Curve, achieve up to 135 lumens per watt at greater than 90 CRI. The Declare-listed products are available with optional Red List–free construction. When a designer chooses a product with a Declare label, they have full transparency with regard to the ingredients.
Coronet is also leading efforts within the lighting industry to standardize Environmental Product Declarations, or EPDs. “The idea behind EPDs is to collect all the information about the embodied carbon in your product,” Krauza says.
Unlike concrete, which has a handful of ingredients, lighting products involve complex components like aluminum, steel, wiring, LEDs, and PCBs—making EPD data collection challenging, Krauza says. Coronet participated in the LCA (Life Cycle Assessment) incubator project alongside approximately 30 manufacturers to develop industry-standard EPDs by contributing data for some of its products, including linear and pendant fixtures.
Gensler hopes more companies will work to find ways to build toward a carbon neutral world. “If they’re already using materials that have a very good carbon rating right now, why not just be aware and use more of them and find out what the other ones are?” says Vince Flickinger, principal and design director at Gensler’s Houston office and global practice area leader for energy. “At some point we’re trying to make this ubiquitous.” gb&d
The right lighting and ambience can change people’s worlds.
Designing with glass elevates aesthetics and enriches human experience. But birds have trouble distinguishing glass from their environment, leading to billions of tragic collisions each year.* How can we create beautiful buildings where both people and birds can live and thrive? Guardian bird-friendly glass helps make it possible. Gain choice and control with a range of glass options that balance beauty, performance and bird protection.
Guardian Bird1st UV
A UV stripe coating is transparent in most viewing conditions and helps signal a barrier to birds, ensuring safety without compromising views.**
Guardian Bird1st Etch
Four translucent patterns in large sizes combine diverse aesthetics with essential bird safety.
Watch our new videos to debunk common myths about birdfriendly glass and get inspired.
* Klem, Daniel, et al., “Evidence, Consequences, and Angle of Strike of Bird–Window Collisions,” The Wilson Journal of Ornithology, vol. 136, no. 1, 2024, pp. 113–119, https://doi.org 10.1676/23-00045.
** The UV stripes are more pronounced when the glass is wet or when condensation forms. Surface residue can also make the stripes more visible.
How architects are using the Gensler Product Sustainability (GPS) Standards to reconsider materials
When architects at Gensler see a void in the industry, they don’t waste time; they work to fill it. “We’re tool-friendly at Gensler. We like to develop not only the industry’s latest and greatest tools, but if we see a need for something, we’ll develop it,” says Stephen Katz, a technical director in Gensler’s Chicago office. “We’re basically trying to have as big of an impact as we can on the market.” Part of that, he says, is developing tools and promoting the ones they feel are most effective.
To streamline the selection of materials that contribute to carbon neutrality, Gensler recently developed the Gensler Product Sustainability (GPS) Standards. The initiative involves rigorous vetting of products based on their environmental impact, ensuring they meet or exceed specific standards. “Getting the right products and materials into a project that can move the needle is really, really challenging,” Katz says.
Gensler released the new material standards, which anyone can access, in early 2024, starting with the most common, high impact product categories—from acoustic ceiling panels and carpet tiles to gypsum board, resilient flooring, and task chairs. “We’re eventually going to roll that out to even more specifications and products as time goes on,” Katz says. “We’re trying to really change the reporting structure that goes into how we specify and then track all this data. The data can be a little overwhelming, but we think this is a great way to get in front of the market and really have an impact. There are targets, and then there are what you receive for the actual product. We’re trying to establish those targets as early as possible and then monitor them in the later phases.”
At Gensler the work begins with setting up embodied carbon targets in their specifications. These could be for building systems like structural steel or concrete. Then they require embodied carbon EPDs to be submitted for select building materials. “We feel that’s the biggest way we can have an impact on the industry—to essentially lead by example,” Katz says.
Considering buildings are responsible for 40% of greenhouse gas emissions globally, every choice made on a project can make a difference, Katz says. Significant advances also continue to be made in reducing the operational carbon footprint, for example, by moving from fossil fuel sources to all electric.
Repurposing as much as possible—buildings and furnishings—is another approach. “I worked with the Old Chicago Post Office and The Mart in Chicago. These are huge buildings,” Katz says. “If you think of the amount of embodied carbon that went into making those struc-
The
tures, it’s enormous. Instead of those buildings being torn down and built anew, the owners were able to leverage the embodied carbon already there and simply renovate and repurpose the building.”
Katz has worked with Gensler for 26 years and says he’s seen a lot of positive growth in that time. “The firm has a really deep social conscience, and that’s driven by the leadership,” he says. “It’s been really wonderful to be a part of that over the years. I think of the opportunities I’ve had to work and grow within the firm, and I think of those conversations about sustainability and how that’s changing. There’s a lot of excitement from our younger staff, too, who really understand that mission statement. They don’t have to be sold on it, and that’s the kind of joy we see having an impact on the market.”
At 200 Park Avenue Gensler worked with client Jay Paul Company to design a fully electric, 19-story office tower in an underdeveloped corner of downtown San Jose, California. Katz was part of the project team that emphasized sustainable materials at every turn, as the tech-oriented office tower brought the energy and identity of Silicon Valley to downtown San Jose’s urban core. Gensler calls the project bold and optimistic, with an eye toward the future. “Solar canyons” redefine the
cityscape and change the way people experience their workspace, while natural light, open spaces, and incredible views are a breath of fresh air. The building features outdoor terraces at every level, coupled with wellness-oriented amenities that allow occupants to balance work and self-care. “It turned out amazing,” Katz says. “It’s got a really dynamic facade.”
To control solar heat gain, the team adjusted the window-wall ratio based on each elevation’s solar exposure. The south and west facades, receiving the most sunlight, feature more insulated opaque panels and less vision glass. The glass is also angled away from the sun’s intensity.
Going all-electric was one of Gensler’s first ambitious sustainability goals at 200 Park Avenue. By committing to the all-electric mechanical system, they achieved a 73% reduction in greenhouse gas emissions compared to traditional gas boilers. This also ensured the building could be fully powered by renewable energy as the grid becomes greener.
“It’s definitely going to take a big effort in terms of understanding how to get from point A to point B,” Katz says of the journey to greener building. “There’s an old saying that if you can measure it, you can manage it, so we really want to understand how we measure the targets and how we measure what we’re seeing and actually being built.” gb&d
- Acoustic Ceiling Panels, Tiles, and Suspension Grids
- Batt Insulation
- Board Insulation
- Carpet Tile
- Decorative Glass
- Glass Demountable Partitions
- Gypsum Board
- Interior Latex Paint
- Non-Structural Metal Framing
- Resilient Flooring and Base
- Systems Furniture Workstations
- Task Chairs
“Getting the right products and materials into a project that can move the needle is really, really challenging,” says Gensler’s Stephen Katz. 200 Park Avenue is a 19-story office tower in an underdeveloped corner of downtown San Jose, California, that emphasized sustainable materials at every turn.
Companies like GCP, a Saint-Gobain company, have long been committed to innovating with new solutions for more sustainable construction.
WORDS BY LAURA ROTE
Big or small, the choices architecture and design teams make every day add up to whether a project contributes to a more sustainable world or not.
“It’s incredibly important. We want to work with manufacturers and suppliers who share our passion for advancing sustainable solutions and making the most progress,” says Stephen Katz, a technical director in Gensler’s Chicago office. “Manufacturers have a really deep understanding of their process and where they get their materials. Some of the solutions that are out there are really going to come from the manufacturing and fabrication side.”
Companies like GCP, a Saint-Gobain company, have long been committed to innovating with new solutions for more sustainable construction. Areas like waterproofing, fireproofing, and weatherproofing are among their top products aiming to make projects more energy-efficient while reducing carbon footprint in the manufacturing and build process.
The fireproofing industry is ahead of the game, according to John Dalton, GCP’s fire protection technical service manager. “We have gone well beyond what most architects are requiring now in terms of environmental or sustainability attributes.”
GCP continues to look at new technologies to enhance the performance and sustainability characteristics of its solutions, including MONOKOTE® Fireproofing—a product that has been around in one form or another since 1938. “We have been at the forefront of
that development for almost a century, and we are keen to be around for the next one,” Dalton says. “I am excited about what the next five to 10 years will bring in terms of our formulations and product characteristics.”
Solutions like MONOKOTE have about half the GWP compared to competitors’ products, with 70% of materials made from a hydro-powered plant. MONOKOTE also has third-party verified Environmental Product Declaration to back up its attributes.
MONOKOTE is designed to reduce the rate of temperature rise in steel or concrete in the event of a fire. This prolongs the structural integrity of the elements, which allows more people to leave a building in an emergency situation and gives first responders time to save the building. It’s been used in some of the world’s biggest projects—from the MGM City Center in Las Vegas to New York City’s Freedom Tower and Canary Wharf in London.
Contractor-friendly, MONOKOTE is typically spray-applied and can be pumped easily into the upper floors of
tall buildings. It is less abrasive and less challenging to pump, so users can choose to inject it to reduce set time and increase yield of the material if they prefer.
“MONOKOTE Fireproofing is considered a cementitious product, and it has a long track record of being robust and that it will remain in place for the life cycle of the building,” Dalton says. “Cementitious fireproofing is mixed with water and pumped as a slurry, and there is a competing fiber-based dry-mix technology that has a reputation for being less robust, but it is inexpensive. We regularly get updates from contractors with photos of 50-year-old MONOKOTE in the same condition as it was in when it was first applied. A solution is only cheap if you don’t have to repair or replace it.”
He says MONOKOTE is like getting two for one—you pay for the durability, and the low GWP is a bonus. “We feel that is the case with the use of cementitious. Most architects and specifications now require it in lieu
Areas like waterproofing, fireproofing, and weatherproofing are among GCP’s top products aiming to make projects more energy-efficient while reducing carbon footprint in the manufacturing and build process.
of the other technology. The other technology has an eye-wateringly high GWP, too—almost two times that of MONOKOTE.”
Still, he says the architectural industry has been slow in using sustainability as a selection metric for fireproofing, as it’s such a small part of a building’s embodied carbon. That said, the past five years have been promising, as more teams look to earn LEED points, considering any solutions that help to lower GWP add up. “The pending release of LEED V5 and its heavy focus on embodied carbon has sharpened people’s minds on this, and we expect it to be more of a ‘thing’ in the future,” Dalton says. “We have seen several recent specifications where GWP is a metric, used as you would with any other performance characteristic like bond strength or abrasion resistance. It has been heartening to see it being a deciding factor in several recent project awards in the Midwest.”
As understanding of materials evolves, the movement toward choosing building materials with low embodied carbon grows. “Fireproofing can be as much as 2% of the embodied carbon in a building. While not huge like, say, steel or concrete, it’s big enough to make a measurable difference—like the recycling of your single soda can. Certainly more than carpet,” Dalton says.
More sustainable waterproofing strategies are being adopted now than before, too, according to Iltaz Alam, senior building envelope product manager at GCP who oversees commercial waterproofing. GCP has always worked to develop durable, innovative products that are long-lasting and sustainable, Alam says.
Recently the company launched its latest Preprufe Liquid Flashing, which reduces the need for additional materials and multiple product logistics to complete a waterproof pre-applied penetration detailing. Based on a typical pipe penetration detail, it reduces up to 20% of global warming potential when compared to traditional detailing. “It’s durable, and it keeps groundwater away from the structure. That’s a big environmental plus right there,” Alam says.
This innovative product reduces installation time as well as the amount of material used to complete pre-applied detail, he says. “Previously you would need to use some kind of liquid membrane, some sheets, and some construction tape. Now GCP has come up with a material that avoids the need of all those additional materials like tape or other types of liquid membrane. It’s just liquid flashing.”
The user applies the liquid flashing, and it will bond to the concrete continuously, he says—the same way GCP’s current Preprufe membrane bonds.
Alam says the team is always pushing for more sustainable sources in its products, too. The more these types of solutions are available, the more accessible and affordable they will become, he says, while further reducing installation timeline and total carbon footprint.
Katz says areas like fireproofing and waterproofing can make a big difference on projects. He points to an abovegrade wall with waterproofing as an example. “If that waterproofing product fails, there can be a cascade of other
issues, which in turn affects the amount of operational carbon the project requires,” he says. “Or maybe the building doesn’t last as long, which leads to a hit on embodied carbon for replacement value. We really want to understand the nature of the waterproofing product as well as whether the source materials or production methods are heavy in embodied carbon.”
Katz says architects at Gensler look at the whole picture when considering a project’s sustainability, especially as the firm works to declare all of its work completely carbon neutral in 2030. “Are they produced far from the project site? Can the manufacturers report the reliable embodied carbon data? All those factors go into that se -
“It’s big enough to make a measurable difference.”
lection process,” he says.
When it comes to something like fireproofing a steel building, for example, he says that project typically has a spray-on cementitious-based fireproofing. “The Portland cement in that product has a big embodied carbon hit usually. How can we use as little as possible of that, and use it really efficiently, so it still meets a fire rating at a building? Ideally we’re able to specify a low carbon, cementitious fireproofing. We want to meet the code requirement but not use more than we need to.”
Dalton says GCP has been excited to explore this, too. “Where we see potential is the removal of Portland cement from our products. Portland cement is typically a pretty bad actor when it comes to embodied carbon. That has been a focus for us over the past several years. We’ve finally completed a series of tests with UL, and we have replaced the Portland cement with Portland Limestone Cement to allow us to significantly reduce the embodied carbon of our products.”
GCP is also looking at Alternative Cementitious Materials, or ACMs. “That has been a big focus for us from a sustainability point of view. That is where the industry is going, and we’re happy to be a part of it,” Dalton says.
GCP’s latest PERM-A-BARRIER® ULTRA™ wall membrane and flashing is yet another innovation. Alam says the new impermeable sheet membrane pushes into the envelope to provide a more durable solution when it comes to very high temperatures—for example, a south-facing building in the southern part of the US. There a building’s wall cavity or parapet temperature can go up more than 170 or 180 degrees Fahrenheit with reflections from another building due to radiation and convection, he says.
“In those situations you need a flashing solution that is stable for a longer period of time, for the duration of the building in such demanding climatic conditions,” he says, adding that a flashing solution that is not durable could bleed through and impact the long-term durability of the tie-ins.
He says ULTRA is stable up to 300 degrees Fahrenheit. The same material can also be used on the roofing parapet. “With climate change we are seeing that every year average temperature is only increasing and not decreasing. For example, Texas this year is facing the warmest weather in a long time. Climate change is happening, and we need to be prepared and think about how the building materials we are innovating are suitable for the future.”
GCP also recently acquired International Cellulose, with more low carbon, high-performance products in the area of insulation that are designed to last the life of a building. Solutions like K-13 Thermal Insulation can help in terms of light reflectance, too, as well as improve acoustical performance and overall sustainability of a project.
Many more innovations are likely on the way. “We have to be willing to push the envelope and offer better solutions,” Dalton says. As manufacturers it’s our responsibility, he says—both to innovate but also to use less raw materials. Then the industry will be forced to follow suit.
Specification is key, Alam says. “Once architects make the decision to use more sustainable products, everyone will be encouraged to contribute and innovate because no one will want to be left behind.” gb&d Fireproofing
GCP’s MONOKOTE is designed to reduce the rate of temperature rise in steel or concrete in the event of a fire.
Can manufacturers report reliable embodied carbon data? All those factors go into that selection process.
May 4 – 8, 2025
Las Vegas, Nevada USA
Join thousands of lighting professionals at LightFair 2025 to discover the latest technologies and trends. With over 100 CEU-eligible sessions, it’s a great opportunity to sharpen your skills and connect with industry leaders shaping the future of lighting.
WORDS BY LAURA ROTE
orget carbon neutral. Autex Acoustics wants to be “nature-positive.” “The purpose of Autex is to care for people, and to do that we have to make sure the world we live in and the resources we use are looked after and valued because they’re finite,” says Jonathan Mountfort, creative director at Autex Industries, based in New Zealand. Mountfort oversees product development and new product design as well as sustainability and compliance.
Autex aims to become a nature-positive company by 2036, emphasizing regenerative processes and paying close attention to ecological outputs. Since its start in New Zealand in 1967 the company has pushed the envelope for what non-woven architectural textiles and modern acoustic solutions can be. The third-generation family-run manufacturer has solidified itself as an award-winning global design practice that innovates to transform spaces. The company has expanded to ser ve more than 18 markets, plus manufacturing and finishing networks in Australia, the UK, and the US. In 2024 they brought their pelletization technology, which aids in rec ycling Autex products, to the US.
Currently Autex Acoustics is looking to scale up work like what they are doing in the US. “The pelletization process was developed in New Zealand and trialed and then taken to the States and implemented there, albeit at a very small scale,” Mountfort says.
Autex innovated the world’s first pelletizer on its journey to circular manufacturing when it couldn’t find a simple effective process already out there. “The thought behind the project was, if this textile has come from a solid material, then a truly circular product should be able to return to a solid material,” Mountfort says.
In California Autex takes its offcuts and finds other uses for them. “There’s a partner less than 20 miles away from our Riverside, California, facility where our pelletizing machine is that we’re already talking to to start doing it for America.” Now they want to scale up and make pelletization available to even more people.
“There is potential for a company to make product that makes the world better and therefore usher in a life of abundance,” Mountfort says. “And we don’t have to do that in a way that’s ridiculously restricted, because if we get all the technologies right and the material selection correct, we can live in partnership with nature, as opposed to on top of nature. I fully believe it’s possible.”
Pelletization provides a tangible way to manufacture products in a circular way. Collecting used products or material offcuts is one thing, but transforming them into a useful product extends the material life cycle and actively reduces waste in the landfill, Mountfort says. Because the product entering the Autex Pelletizer is made of Autex material already, solutions like the company’s SpinFix adhesive-free mounting kits or Frontier End Caps (accessories made from pelletized PET) can be recycled with Autex products or through standard curbside recycling processes globally.
“Now that we have rolled this technology out to each of the countries we operate in, we want to ensure we continue to improve, increase, and partner with other businesses in the industry to scale the capacity. Eventually we can build out an industry solely fueled by reclaimed materials that are re-manufactured into high-value long-lasting products,” Mountfort says.
He says the scaling up and continuing to evolve the technology is one of the most important things that could be done in the industry today. “It’s acoustics agnostic. It’ll work for fashion. It’ll work for building products. It’ll work for other textile product streams. It will give a pathway to a whole host of material out there that doesn’t, at present, have a solid pathway, and it will increase the value of that material through it.”
Already some recycling companies take material and recycle it “in a really sort of blunt form,” Mountfort says. He points to the example of mining cities and says the possibilities for new material—even right from our landfills—is tremendous. “There’s phenomenal opportunity for a company to become a modern Industrial Revolution version of a mining company, where they mine cities and take minerals and raw product from feedstock that we would now consider waste. There’s massive op-
Pelletization provides a tangible way to manufacture products in a circular way. In 2024 Autex Acoustics brought their pelletization technology, which aids in recycling Autex products, to the US.
away, and it ends up in a pile of junk. “It’s insane. If you actually value the material, put the value not on the product; put the value on the material. Then all of a sudden that’s got value through the whole chain, and therefore the concept of waste is removed. It’s a simple shift, but complex to implement.”
Autex already works with many sustainable leaders in the industry, including architecture giant Gensler. The firm itself is well on its way to carbon neutrality in all of its work by 2030.
“We’re making progress on our goal, which would be described as a zero carbon impact portfolio in 2030, and that’s a big investment,” says Stephen Katz, a technical director in Gensler’s Chicago office. “It’s a big leadership moment for us.”
Katz says the next step toward zero carbon requires better data collection and tools for tracking embodied carbon from the built environment. That’s part of why Gensler released its new material standards in early 2024. Starting with the most common, high impact product categories, the GPS, or Gensler Product Sustainability Standards (page TK), program is a way to establish sustainability performance criteria. It all starts with managing the data so you can better understand it and plan for a greener future, he says.
Reuse is one area where Katz sees room for improvement in the built environment. “It’s a really interesting challenge, how to reuse existing materials and furnishings,” he says. “It’s going to take some outside the box thinking in terms of the construction procurement process.”
portunity for landfill mining, for city mining, and taking usable materials and adding processes to turn those into feedstocks for other industries.” Conversations around turning what was once considered waste into something useful in a low or zero carbon manufacturing way are happening now.
All of Autex’s products are carbon neutral already, and the company established a zero-waste product line back in 1990, before most manufacturers took the concept of zero waste seriously. But what’s next?
The research and development Autex is known for reaches far beyond acoustic solutions, as the built environment at large can benefit from its circular design strategies. “Acoustics are just our vehicle,” Mountfort says.
“If we dial in and focus on acoustics, that’s part of a building that’s not really focused on at the moment, it’s not really taken into account across the world and building code and all that’s required to make a building habitable for people, but we feel it’s so important. The ability to hear and be heard—that’s a fundamental component of what it is to be human.”
The concept of waste doesn’t exist in the natural world, Mountfort says. “Everything has a pathway back into another form.” And yet, we as humans take a material, make a product, use the product, throw it
He says this new approach in the industry would have enormous carbon savings. “For us we find that has a lot of potential, and we’re really excited about that.”
Having the right partners and a seat at the table is important when it comes to making big moves in the industry. Autex is already part of Gensler’s standard product library as a carbon neutral solution, but at a higher level they’re in discussion about a carbon negative product, too, Mountfort says. “I’m really keen for the uptake of this type of thinking to be connected to the material and the product, shifting away from credits and offsets and connecting the environmental measurement to the material,” he says. “We’ve got a carbon neutral company here producing carbon neutral products.”
When it comes to specifying recyclables, though, Mountfort urges attention to detail. “Just because it is recyclable doesn’t mean it gets recycled. It’s on our architects and the people going into fitouts to consciously work through their demolition plan, because when a new company moves in, they’ll walk in with their architect and they’ll go, ‘What can we do here? We need to make it look like x, y, z.’”
What if, instead, they walked in and asked, “What can we reuse?” he says. “That would massively reduce the global warming potential and the environmental load that construction and fitout has on our planet.”
“If
we get all the technologies right and the material selection correct, we can live in partnership with nature, as opposed to on top of nature.”
Manufacturers like Autex Acoustics seek to move beyond carbon neutral with pelletization.
And while recycling has been around for decades, we’re only now living in an age when people expect things to actually be recycled, Mountfort says. “It takes that long for a technology to be taken up. Initially people resist it.”
He says the next phase of technology is reliance, and that’s where he expects society to move in the next five to 10 years, as the world begins to rely on the recycled product stream working. Still, Mountfort says massive education is needed across the industry. Not everyone knows plasterboard can be recycled, for example, he says. “It’s a really useful material. All of that has to be thought about.”
“All of this is a massive opportunity to create new industry and more than economically viable businesses being made out of mining our cities and mining rubbish,” Mountfort says. “Focus on it. Get the investments going, and don’t try and tackle the whole thing by yourself. Everybody has a part to play. Look at that pathway, and start filling gaps.” gb&d
A PATIENT TOWER AT CAPE COD HOSPITAL INCLUDED SIGNIFICANT INFRASTRUCTURE CHANGES FOR RESILIENCY.
Reconsidering how health care environments can stand up to storms and more
WORDS BY LAURA ROTE
Address aging infrastructure, evaluate your systems, and understand the conditions that can’t be designed for and make emergency plans accordingly—these are among the directives SmithGroup shares in a recent post by Greg Heppner, senior principal, called “Building a Climate-Resilient Healthcare System: What is Your Plan?”
The leading architecture firm with 20 offices and more than 1,400 employees is increasingly prioritizing strong, sustainable building materials as they rebuild and renovate health care and other projects in the face of increasing storms with high winds, hail, and flooding, to name a few issues.
“Climate change is something we’ve known about for a long time, and the design community and regulatory community is finally beginning to get around to effectively considering it and addressing it,” Heppner says. “We have clients who are beginning to require it as part of their project RFPs. Regulatory agencies, building departments, and zoning departments are beginning to incorporate it in their building regulations. It’s something the design community has to deal with.”
In summer 2024 SmithGroup was working on multiple health care projects to address the impacts of climate change. This included a new four-story patient tower with a cancer center and two floors of patient rooms at Cape Cod Hospital, a facility less than 500 feet from where the harbor connects to Lewis Bay and feeds into the Atlantic Ocean. “Any hurricane coming up the East Coast and slamming into the southern coast of Cape Cod will have a direct effect on this campus and specifically our new buildings,” Heppner says.
The project was designed to address sea-level rise, wind-borne projectiles, and provide hurricane storm-surge mitigation up to a Category 4. The team isolated all of the emergency generators above the anticipated flood level and elevated the site to keep the first floor of the building out of the 500-year flood zone.
“Significant infrastructure changes were made to this specific building to keep it re-
silient,” Heppner says, adding that they also chose not to have a basement, where health care facilities often put their mechanical, electrical, and plumbing systems to keep them out of sight. “Those tend to turn into swimming pools when a site gets flooded, and that puts critical infrastructure directly in harm’s way.”
Another project SmithGroup is working on currently, the Myrah Keating Smith Health Center on St. John in the US Virgin Islands, was put out of service in 2017 after Hurricane Maria ripped out the corroded base attachments of the rooftop equipment, causing those units to fail. The metal boxes were blown across the roof, ripping the EPDM membrane to shreds with their sharp edges and flooding the interior. The largest health care facility on the island was permanently closed when it was needed most.
“Something as simple as just using stainless steel attachments where they face the environment—and if you’re in a salt air marine environment using stainless steel almost has to be a given because even galvanized steel with a sacrificial coating will give way so much earlier than stainless steel,” Heppner says. “I won’t say anything is perfect as a material. Maintenance of material, constant inspection, and upkeep is essential to maintain the resilience of your facility.” gb&d
Given its close proximity to Lewis Bay and the Atlantic Ocean, the new cancer center and patient tower at Cape Cod Hospital is designed to address sea-level rise and wind-borne projectiles and provide hurricane storm-surge mitigation up to a Category 4.
In Petoskey, Michigan, SmithGroup created a more modern front door for the campus at McLaren Northern Michigan using brick to help integrate the South Tower addition with the existing buildings. The project was part of a $1 billion facilities upgrade for the health care system.
A timeless material provides security and aesthetics.
WORDS BY LAURA ROTE
Brian Belden has long been surrounded by brick. He started working for The Belden Brick Company in 1997 and is now its executive chairman and vice president of sales and marketing. The family-run business has been dedicated to the art of brickmaking since 1885.
Like anyone in the built environment, brick manufacturers have seen their fair share of ups and downs—from an economic boom in the early 2000s to the housing crisis and recession in 2008 to a growing demand for new products today. Currently Belden Brick sells to more than 230 independent distributors across the US and Canada.
While brick has long been a go-to material for teams designing for durability, brick is experiencing a resurgence and seeing new uses in some perhaps less than expected markets, including health care.
“Architects perceive brick as a value product because of its longevity and its versatility,” Belden says. He says the company’s many colors, styles, and sizes of brick make it a natural fit for areas like health care and schools.
Thin brick products are in demand all over the US, but particularly in the Midwest, Mid-Atlantic, New England, and West. “It’s becoming more commonly recognized in the industry as a quality product that will perform,” Belden says.
Thin brick is also popular for its ease of installation, as you don’t typically need a mason to install it, Belden says. And it’s not a stacked product that needs a foundation or a brick ledge to be used. “You can use it as a material that’s applied vertically to the wall and is maybe a little bit easier for some contractors to use.” It’s especially popular for apartment and high-rise exteriors for its aesthetics, he says.
“Once you build a brick building you’re not going to have to do much to it. It’s go-
ing to be there a long time,” Belden says, assuming, of course, that the project was completed correctly.
With the exception perhaps of natural stone, there’s no greater life cycle than brick. “The brick will last the life of the building without a whole lot of extended maintenance. And if you look at the energy that’s used to create a brick versus other products over the life of the product itself, it really stands out as a good value,” Belden says.
Greg Heppner, a senior principal at SmithGroup architecture firm, says brick may not be immediately thought of for some projects because some may think of the brick of old—considering it perhaps a dated material from the 1950s or ’60s—but SmithGroup considers it widely for many new uses and styles.
“A designer has to look at two things— the context of a project, not only for the campus but also what’s the neighborhood, what’s the region, and what are the primary external factors that the design will have to address? In conjunction with that, when you begin to design the project, how does it integrate into the resiliency of the overall campus?” he says.
Heppner says one approach to resiliency is to design higher quality buildings in both construction and design, trusting that those will be better maintained over their life. “If brick is a component of that design and contributes to that quality then it could be an advantageous material to use,” he says. “A
The ZGF-designed Cincinnati Children’s Critical Care Building expansion included a custom blend using 8521, 8522, and 8523 Course Velour brick in modular, norman, and special sizes from The Belden Brick Company.
lot of the challenges health care facilities face with climate change is deferred maintenance with a lot of their facilities and infrastructures. That makes components of their campus and their operations susceptible to the impact of climate change.”
Brick is clearly timeless, even as various colors or styles come and go. While new colors, textures, and lengths are exciting, the industry isn’t expected to change drastically, Belden says. It’s dependable that way. “It hasn’t changed a whole lot. We’ve been in this business for 140 years.”
Oversized bricks are now in demand and may help reduce costs on large projects while also making a building or space feel more approachable. Longer, linear style bricks are also in vogue, Belden says, and allow teams to use one brick instead of two in places. For example, Belden Brick’s Am-
bassador style is 15-and-five-eighths inches long, compared to a traditional modular brick of seven-and-five-eighths inches long. “It provides a different aesthetic. Some people like that more linear appearance.”
The possibilities seem endless, as you can create shapes with Belden Brick to make an arch over a window or provide a grand detail along the foundation. “There are lots of different things you can do in manufacturing that allows for not just a traditional 90-degree corner or typical ledge underneath the windowsill.”
Belden Brick has also increased its glazed bricks over the past few years as demand continues for exteriors as well as interiors. “We’re always working on new colors and textures,” Belden says.
The company’s top two colors currently continue to be a black brick and a white brick, but gray also remains popular. “We’re starting to see a bit of that trend
slow and go toward more earthy colors recently, but black and white are still at the top of the list this year for us.”
People are also more interested in various textures as opposed to monolithic flat finishes. “We’re doing a more rustic look on a lot of our products now,” Belden says, adding that texture can help make commercial or clinical spaces feel more inviting. “We’re seeing it more on the interior now than we used to in the past. People want to transition from exterior to interior, trying to keep the theme, and know a brick product is not going to get hurt by a wheelchair or a bed bumping into the wall.”
The Belden Brick Company is making significant capital investments in their facilities to continue to improve efficiencies and reduce manufacturing time, too. “I think that’s the trend in the industry—to be able to get the brick manufactured in a shorter amount of time using less energy.” gb&d
“We’re seeing it more on the interior now than we used to in the past.”
Bird-friendly glass, energy efficiency, and more combine in the latest top innovations.
WORDS BY LAURA ROTE
“Nobody is intentionally designing buildings to harm birds, but it does take some foresight to design a building that helps not to,” says Heidi Trudell, bird-friendly specialist and regional technical advisor with Guardian Glass.
Trudell is the first ornithologist to work at the major manufacturer—one of the many signs of their commitment to stewardship and its environmental aspect. Guardian continues to conduct research and work to develop innovative solutions for buildings while also placing a large emphasis on educating the architectural and construction communities on how different bird-friendly glass technologies can be incorporated within their projects.
In North America bird populations are down roughly 30% since the 1970s, with current estimates pointing to at least 2 billion birds killed per year from colliding into buildings, Trudell says. The American Bird Conservancy (ABC), the National Audubon Society, Cornell University, and all major bird research organizations cite glass as having the highest human-caused risk to birds, aside from outdoor cats—but there is a solution to the problem.
While many in the industry were initially in denial that collisions were an issue, that has changed. Now birds are a common part of many design considerations. “I’m most excited about how normal it is now; the bird-friendly conversation used to be a real niche,” says Dan Piselli, director of sustainability and a principal at FXCollaborative. “Now it’s something everybody has to deal with. That’s particularly good for me because I’m interested in all sustainability issues, and I see the bird collision issue as one manifestation of the negative human impact on our climate and our environment.” Climate change is abstract, he says, manifesting in greater storm intensity or wildfires that can be hard to directly con -
nect. Hundreds of birds hitting the same facade, though, shows a clear correlation.
Piselli says the topic is more prevalent in part because there are now more products on the market to address it. “It’s about specifying something now. There’s less mystery. Back when I was first introduced to the issue the experts were not sure what the successful strategies were going to be. Now after many years and examples, it’s better.”
Because there are more products available—many of them with little aesthetic impact—and a stronger understanding of the issue, designers can do the right thing with little effort, Piselli says. “I hope greater awareness of human impact on the environment and climate change is driving more sustainability-focused design generally,” he says. “Obviously everybody is preoccupied with operational energy and human health, or lately embodied energy, and that’s all right, but part of a comprehensive approach also includes addressing ecology issues like reducing bird collisions or promoting pollinators with landscapes that help them thrive.”
Trudell says reducing pressure on birds is critical because those populations can recover if changes are made. She says voluntary bird-friendly standards are gaining traction, and while building code requirements, bylaws, and incentivization are happening largely in Canada, the US is catching up. Codes now exist in Europe and Korea as well. Approximately 50 municipalities in Canada have requirements on the books and roughly 40 in the US have active or pending codes, she says. Cities like Portland, Maine have acted, and Austin, Boulder, Denver, and Nashville could be next, she says.
The new FXCollaborative-designed Park Point project in Brooklyn features bird-friendly glass and a curved design.
“We are now asking glass to do more than we ever have before, especially for the exterior envelope,” says Alan Kinder, director of commercial segment at Guardian Glass. “We see a continued tightening of industry standards that are challenging us to develop new coatings that meet more stringent U-value and SHGC requirements. We see Jumbo glass capabilities and the request for oversized glazing units grow at an increased rate.”
Enhanced acoustics, improved safety and security, and impact protection are product-specific variables Guardian discusses as part of the glazing unit configuration, Kinder says. Embodied carbon and stewardship initiatives also influence specifications and material selections, and adding the much needed component of bird-friendly solutions is pushing the industry and Guardian in particular to continue to provide innovative technologies that solve many challenges. “Beyond the product and material development, we also are having to ensure effective
transfer of knowledge and the ability to provide project-specific custom content to help architects, building owners, and consultants make the proper material selections that check all the boxes,” Kinder says.
Guardian Bird1st UV is among the latest innovations. Bird1st UV helps to prevent bird collisions with buildings using a UV coating with a striped pattern that’s nearly invisible to humans but visible to birds. The alternating UV reflecting stripes on the outside surface of the glass with a UV absorbing laminate material really makes the UV contrast pop, Trudell says.
FXCollaborative uses a variety of strategies depending on project needs, including Bird1st on multiple projects recently. Guardian’s Bird1st UV requires a #1 surface placement to increase the efficacy to mitigate bird collisions. Different lighting and viewing conditions can impact the visibility level of all deterrents. Even with the worst case of bright reflected sky on the exterior, the visibility of Bird 1st UV to humans is
low. “It’s still subtle,” Piselli says.
Guardian also offers Bird1st Etch, a surface 1 acid etch in patterns that meet ABC’s 2-by-2-inch spacing requirements (not to be confused with abrasive etch or laser etch). Trudell says the pattern spacing is critical because birds know their own dimensions and what they can or can’t fly between.
Beyond the benefits to birds, though, Trudell says these products may also offer benefits to building occupants, including outstanding thermal performance, lower maintenance costs (nobody has to clean up after collisions, and pests are not attracted to the site), as well as increased mental, emotional, occupational productivity (no one is witnessing collisions or having their meetings disturbed by them).
Kinder says Guardian is on the leading edge with research and innovation, especially with product test methodologies and comparative metrics. “We are continuing to innovate to develop a suite of products that provide the best range of coverage to
meet performance and aesthetic demands while also ensuring an efficient supply of material,” he says. Guardian Glass plans to launch Jumbo Bird1st UV in 2025, increasing availability for this patterned coating to a 130-by-204-inch glass lite.
Guardian already had a couple of bird-friendly products at the time Trudell joined, and those offerings have only grown after she and the R&D team did field trips to explore how birds act in the environment. “One of the reasons I am working for Guardian is that they do their homework,” she says. “They have solicited not only input from biologists, but also all of these products get assigned a Material Threat Factor score through the American Bird Conservancy. Guardian also asks, ‘What can we learn or improve from all the other testing methodologies that are available?’”
This is important, she says, because the collisions research field is just starting to refine its understanding of the many variables that impact a solution’s performance and how context-specific they can be. “Right now it’s still a little bit of the Wild West because architects are working under the assumption that every solution is going to work equally well in every installation. This is not accurate. Every deterrent technology ever made works differently in different visual environments,” she says. “For example, a black frit color might work great as a deterrent against a bright background but have significantly less efficacy against a dark background. The collisions world is still in the early years of discovering all of these relationships, and future embodiments of testing and regulations will likely be more sophisticated than the ones we have today.”
Even within a technology category, similar sounding solutions might not work the same. There are material differences between different types of etch that impact the visual contrast for birds, so acid etch versus laser etch versus abrasive etch will not have the same efficacy as each other, for example.
“If you look at the field of UV in general this is especially true because every manufacturer has a completely different approach to UV,” Trudell says. Guardian takes the time to push the limits of UV deterrent technology in a good way. “You’ve got the increased contrast between the super high UV reflective coating (~75%) and total UV absorber (>99%). That boost in contrast is only possible if the UV reflector is on surface 1 with the absorber on surface 2, and Guardian makes sure all of their IGU makeups have that proprietary boost.”
Trudell says best practices are changing rapidly to keep up with evolving technology. “I have to update all of my product information and reference materials every four to
six months.” While concrete and steel have been understood for centuries, float glass wasn’t really a thing until 1960. “Not only was float glass a very new technology, but understanding that birds hitting it was even a problem was a very new thing as well.”
She says architects have an obligation to tell their clients about the environmental impact of their buildings according to the AIA 2018 code of ethics. Collisions are part of that broader concept, but architects often don’t know the information, and Guardian can help them understand and improve their designs for birds. “When people ask me about a design, the first thing I do is look at a geographic location and take into consideration what species move through the area. We have to look at a landscape level very immediately as well as in terms of what the habitat is around the building. No building is exempt,” she says. “You have to toddler-proof your building from the outside, and your toddlers are hummingbirds. Certain variables can make your building more high-risk, but really nothing is low-risk unless you intentionally design it to be low-risk using products that are bird-friendly.”
An Architect’s Perspective
Piselli has been with FXCollaborative for 19 years, working first on the Center for Global Conservation at the Bronx Zoo—an experiment in designing a bird-safe building.
“That building ended up being a test case for certain strategies,” he says. “It was a great learning opportunity.” They learned, for example, that overhangs or awnings were in fact not good collision mitigation strategies.
The 2013 renovation of Manhattan’s Jacob K. Javits Center, however, was a huge success. It was the first time a major New York City building was retrofitted with bird-friendly glass, according to the NYC Bird Alliance. The renovation by FXCollaborative and Epstein in consultation with NYC Bird Alliance resulted in a drop in bird-building collisions at the site of more than 90%.
“We replaced all the glass at the Javits Center with a kind of glass that had a frit pattern on it,” Piselli says, adding that the pattern provided several benefits. It was bird-safe, and it reduced the solar heat gain to minimize energy use for air conditioning. The frit also allowed for a non-tinted glass, which Piselli says is much clearer even with the frit, so you can see in and out of the building much better. “The frit also reduced glare, so there were a number of co-benefits of that fritting strategy, which included but were not limited to being bird-friendly.”
Since the Javits Center project FXCollaborative has had a number of projects complete similar objectives, often pairing solar heat gain reduction through fritting as an added benefit of collision mitigation. While bird-friendly solutions were relegated
Bird1st UV’s alternating UV-reflecting stripes on the outside surface of the glass with a UV-absorbing laminate material make the UV contrast pop, preventing bird collisions. Guardian Glass plans to launch Jumbo Bird1st UV in 2025, increasing availability for this patterned coating to a 130-by-204-inch glass lite.
The 204 Fourth Avenue project in New York City is a 13-story building that uses Bird1st UV.
Nothing is low risk unless you intentionally design it to be low risk using products that are bird-friendly.
to commercial and institutional clients for some time, that changed when NYC Local law 15 of 2020 got passed. At first Piselli says residential clients worried people wouldn’t want to lease apartments with frit. “Now we have a whole crop of residential buildings that have bird-friendly glass on them. Different clients have used different solutions, and we’ve been able to see what’s working well.”
Piselli has been involved with the BirdSafe Buildings Alliance for more than a decade, helping to create the bird-friendly guidelines from its first iteration in 2007. The biggest challenges today, he says, are cost and aesthetics, but improvements continue to be made. “Aesthetics is a real challenge because a lot of it comes down to personal preference,” he says. “Some people don’t mind seeing horizontal lines, and some people hate that and like dots instead. Some people like dots in a rectangular pattern. We did a custom pattern that was essentially in the form of dotted lines at the Statue of Liberty Museum, and that’s successful because we were very deliberate with the view, creating a vertical dot line pattern that was going to blend in better with the surroundings than other patterns.” Today that project sees maybe one collision a year, he says.
Recent research shows bird deaths from col-
lisions far surpass previous estimates—more than one billion annually in the US alone— highlighting an urgent need for bird-safe glass retrofits and artificial light reduction measures, according to ABC.
The findings revealed only 40% of birds with injuries from collisions survive, even with the highest standards of wildlife rehabilitator care, suggesting current mortality estimates based solely on birds found dead at collision sites vastly undercount the true toll. “Birds generally cannot see or recognize glass. When they see vegetation or the sky reflected in windows, they perceive it as habitat and do not know there’s a barrier in the way that they cannot fly through,” says senior author Kaitlyn Parkins of ABC. “The good news is people can help. For existing buildings and homes the easiest fix is to add inexpensive, commercially available bird-safe window treatments such as those tested by ABC.”
Piselli hopes the continued visibility of the issue will push people to make change, as people get interested in issues when they’re up close. A nature lover himself, he recalls various bird collisions close to him that were unsettling. They began to add up, even just from his own experience. “The scale of this issue has become apparent, and once you realize you can do something about it and it can have co-benefits with other sustainability strategies, and it can look good, it’s like, why not?” gb&d
Historic zinc is rediscovered as a sustainable solution that checks all the right boxes.
WORDS BY PAULINE HAMMERBECK
The opening ceremony of this summer’s Paris Olympics featured a striking moment: a masked torchbearer leaping across the city’s iconic zinc rooftops. This vivid scene wasn’t just a celebration of architectural heritage; it subtly underscored why zinc is rapidly gaining favor in green building.
Built to Last
Zinc has a long history, especially in European architecture, where its durability is legendary. Parisian rooftops, some more than a century old, exemplify that longevity. “There are not many roofs you can put up that you can say will last over 100 years,” says Mike LeRoy, general manager for VMZINC North America.
Viewed through a modern lens of sustainability, zinc’s resilience is seen as a way to contribute to lower life cycle costs, reduced waste, and decreased energy use in mining and transportation.
Protective Patina
Zinc’s longevity largely stems from its natural patina—a layer of zinc carbonate that forms as the material reacts with the environment. This protective layer enhances corrosion resistance but also has a self-healing quality that fills in scratches and imperfections, reducing maintenance needs over time.
It also results in a gradual color transformation, transitioning from a shiny metallic to a soft matte gray.
“It has quite a warm feeling, which sounds strange to say … that a metal feels warm,” says Matt Pickering, associate principal at Arcadis in Manchester, England.
Natural and Recyclable
As the 23rd most abundant element in the Earth’s crust, zinc is widely available. But for architectural applications, pure zinc is too
soft and brittle, so it’s often alloyed with titanium and copper for modern building needs.
One standout feature is its 100% recyclability. “You can recycle zinc at any point in its lifetime,” LeRoy says. “We often recycle it at the pre-consumer stage in the plants, with scraps that accumulate.”
Post-consumer recycling is also common, he says. “Old stock can be shipped back to our facilities, melted down, and added to new zinc.”
This closed-loop cycle reduces the need to mine new ore, conserving resources and energy.
That’s why zinc seems to be increasingly favored over other metals like aluminum, copper, and steel. Its sustainability benefits make it a compelling alternative, especially in institutional and high-end residential markets where durability and long-term savings are priorities.
“The demand is widespread,” LeRoy says. “We see it with a lot of institutional work— schools, churches, colleges, and universities. And then there’s the high-end residential market, which is really liking zinc as well.”
While zinc’s upfront costs can be higher than materials like steel or aluminum, its longevity and low maintenance can make it a cost-effective choice over time. “It’s going to last longer than aluminum or steel,” LeRoy says.
Additionally, zinc production is more energy-efficient, requiring half the energy of copper and a fifth of what it takes to produce aluminum, LeRoy says.
“It gives the building a real identity of its own.”
A project in New York uses QUARTZZINC, a prepatinated zinc that closely imitates what nature does to natural zinc.
Arcadis’ Pickering says end-user demand is another factor. “Institutional investors are very aware that a tenant will now choose an environmentally sustainable building over a non-sustainable one,” he says. And that is driving material choices like zinc.
In terms of aesthetics, zinc’s malleability allows for various design applications. Historically used for roofing, zinc is now popular in cladding, rainwater systems, and even interior applications like perforated panels and bar tops. “Zinc can be used just about anywhere on a building,” LeRoy says.
One notable example is the Lampwick Quay project in Manchester. Designed by Arcadis, this multi-family apartment development employs multiple zinc techniques to convey a sense of evolving scale.
The building prominently features traditional standing seam panels in gold, which
serves as its focal point. Behind this, lighter gray interlocking planks add texture and depth. Further back, larger panels create a more expansive and simplified look.
The design achieves a detailed, residential scale at street level, transitioning to a more substantial, warehouse-inspired look as you move back. “It gives the building a real identity of its own,” Pickering says.
One of the chief goals of the project was to ensure favorable operational running costs. That was achieved in part through large mineral wool panels behind the zinc for insulation. “The use of zinc was great for our thermal envelope and in keeping the running costs down,” Pickering says.
Maximizing sustainability through design often involves optimizing the form and orientation of the building. But LeRoy emphasizes the importance of optimizing the zinc
as well. “The more you optimize the panel sizes, the more of the zinc you’re using, and the less waste you produce,” he says.
Integrating renewable energy technologies like photovoltaics in a standing seam roof can further boost sustainability.
Despite its many benefits, zinc also faces challenges.
Initial costs can be higher than some traditional materials, though long-term savings in maintenance and energy efficiency often offset this. And, as Alex Pittman, technical manager for VMZINC, points out, perceptions of zinc costs may differ from reality.
“When zinc first entered the North American market, the higher cost was due to a lack of familiarity among installers. They didn’t know how to work with zinc, which inflated prices,” he says. “Now, two decades later, with many great projects
and experienced installers, the cost has come down.”
Certain environments can also pose challenges for zinc, particularly coastal areas with saltwater exposure. But proper detailing can mitigate these issues, Pittman says, allowing zinc to develop a protective patina even in harsh conditions.
Understanding zinc’s compatibility with certain materials, like copper and certain high pH timbers, is also important to prevent staining and corrosion, Pittman says, noting that it’s important to work early in the process to ensure the zinc is set up for optimal performance.
The need to educate clients is also important, particularly in areas dominated by traditional materials. “In the UK the majority of building stock is red brick and slate tiles, and moving away from that can be met with resistance,” Pickering says. “Educating clients about the benefits of zinc, both aesthetically and in terms of sustainability, is crucial.”
Clients may also need reassurance about performance, especially with newer zinc products, Pickering says, but having a successful project to point to can make all the difference.
Where the industry can really help, Pickering says, is with a better focus on post-occupancy evaluations. “There’s a need for stronger assessments of how buildings perform after completion,” he says. “We can look at manufacturer data, but we also need to learn from end users about how these buildings are operating in [real-world conditions].”
This feedback is crucial for refining future designs and ensuring that zinc maintains its position as an invaluable sustainable ally—because the outlook is bright. “It’s really about how big the design world’s imagination is,” Pickering says. gb&d
Zinc is fully recyclable and more energyefficient to produce than most metals. The material’s malleability enables a range of innovative architectural uses.
WORDS BY MARCY MARRO
Over the past few years the home renovation industry has reached new heights. Driven by the pandemic, when many homeowners began doing more renovations inside and out, the home remodeling market saw a high of nearly $500 billion in 2021 and reached an estimated $567 billion in 2022, according to Harvard University’s Joint Center for Housing Studies’ Leading Indicator of Remodeling Activity (LIRA).
While high interest rates and inflation have pointed to a slowdown in sales at some major retailers, spending on home improvements may pick up next year, partially due to the aging US housing stock, according to Home Depot. The number of single-family homes in the 20- to 39-yearold range, the prime years for remodeling, is expected to increase 16% by 2026.
When it comes to exterior renovations, updating siding can be an inexpensive way to change a home’s appearance and increase its value, with reports of as much as an 80% ROI, according to many manufacturers.
While kitchen and bath remodels are among the most common home renovation projects, replacing siding ranks as one of the top four remodeling projects for ROI from 2023, according to Home Depot.
Replacement projects like roofing, siding, windows, and doors continue to dominate the $331 billion homeowner market in 2021, making up 48% of expenditures, according to the Joint Center for Housing Studies of Harvard University’s Improving America’s Housing 2023 report.
These days exterior siding comes in all sorts of materials, styles, and colors.
A subset of composite siding, engineered wood siding is an innovative solution that offers the look of wood while being lighter and more durable. LP SmartSide is built off of the company’s proprietary oriented strand board (OSB) technology. Utilizing wood substrates, LP SmartSide is a combination of Aspen wood laid onto a mat after being coated with resins and waxes, impregnated with zinc borate, and pressed into the siding with a paper overlay, creating a highly durable siding product that resists moisture, fungal decay, and insects. Every strand in the board is wrapped in a 360-degree covering to protect the engineered wood substrate.
“What this allows us to do is create a highly durable product that looks amazing,” says Derek Blank, senior director of marketing at LP Building Solutions. “It looks and works just like wood so you can use typical woodworking saws and tools. There are no special tools needed to cut and work with the siding.”
Blank says many people choose engineered wood siding over vinyl or stone to improve a home’s curb appeal while enjoying other
Brushed Smooth Lap Siding and Trim in Abyss Black can give residential projects a sleek, stylized look that stands out.
LP Building Solutions’ products are durable enough to withstand tough conditions.
benefits. LP SmartSide is a hardboard siding that is a premium relative of vinyl and an alternative to brick that still looks great. “LP SmartSide is cheaper to install than brick and a little more expensive than vinyl, but it gives you that premium look homeowners are looking for.”
Last year LP Building Solutions launched a brushed smooth texture to complement its cedar grain texture. While the brushed smooth texture has a modern and timeless feel, the cedar texture more closely resembles the look of real wood.
“Many modern homes are desiring a smooth texture, and we have a texture that meets those needs,” Blank says. “If you’re in a region or an area where the preferred texture is cedar, we have that as well. Those are the two most desired textures.”
LP SmartSide’s ExpertFinish comes in 16 prefinished colors for even more design flexibility—from Snowscape White to Abyss Black. ExpertFinish is also available
in brushed smooth and cedar textures and comes with a 15-year paint warranty. “ExpertFinish provides a factory-finished paint that goes on and maintains the durability of the product as well as or better than field paint,” Blank says.
Depending on the need, LP SmartSide runs the gamut of siding styles, including lap, nickel gap, shakes, panel, and vertical.
LP Building Solutions recently launched nickel gap to give homeowners a flat siding look with a 1-inch reveal. Styles like nickel gap can be installed horizontally or vertically. LP SmartSide also has matching trim, fascia, and soffit.
Siding is important in part because it protects buildings from the elements. Choosing nontoxic building materials and safe building materials add up to long-lasting, sustainable projects. Carbon-negative LP SmartSide is engineered to provide strength and pow-
erful resistance; it’s made to resist hail up to 1.75 inches in diameter.
LP SmartSide’s limited 50-year warranty backs up its claims. “It’s an exceptional warranty for long life, making sure the product will hold up over the course of time on the side of the home, looking beautiful for years to come,” Blank says.
“We offer a good level of durability due to the waxes and resins in the product but also the orientation of the strand to make them more durable,” says Isaac Ojeda, construction service associate at LP Building Solutions. “During manufacturing the strands are arranged in cross-directional layers to help improve the resilience of the product.”
High wind and freeze-thaw are other concerns LP Building Solutions has designed for. “High-wind zones are mapped from Maine to South Texas,” Ojeda says. “LP SmartSide lap and panel siding can withstand high winds and has earned APA Product Approval.”
Major retailers like Lowe’s and Home Depot are also committed to sustainability and continue to carry engineered wood siding solutions. Lowe’s recently announced its own 2050 science-based, net zero target across more than 1,000 stores.
The addition of products like brushed smooth panels have allowed LP Building Solutions to double its business in the Northeast, Blank says, while across the US the company continues to see growing interest in its SmartSide products. “A lot of that demand is a trade up from vinyl and traditional lumber such as cedar lap or shakes,” he says. “We provide great options for that trade up as well as competition to other existing premium hardboard siding.” gb&d
The right landscaping can combine with sustainable siding and trim to enhance the final look of residential projects.
“We offer a good level of durability due to the waxes and resins in the product.”
Rapids Blue ExpertFinish Siding and Snowscape White ExpertFinish Trim are a compelling combination.
How the solution addresses everything from logistics and performance to
WORDS BY RAVAIL KHAN
Globally the architecture and construction industries are responsible for approximately 50% of greenhouse gas emissions and nearly 45% of global resource consumption. While much progress is yet to be made, practitioners are increasingly recognizing the built environment’s potential as a key driver for change in the push toward greener practices.
Historically efforts of the building sectors have largely targeted reducing operational carbon emissions. In recent years methods have shifted to a more holistic approach that begins planning with considerations of embodied carbon across a building’s entire life cycle.
As industries grapple with evolving demands for sustainability and efficiency, precast concrete has proven to be a viable solution addressing several challenges—from logistics and performance to aesthetics and reusability—while accounting for many innovative construction solutions. While precast concrete has its benefits throughout the life cycle of a building, it is during the use stage when these systems truly shine. By prioritizing sustainability from a life cycle perspective in the design phase rather than focusing on first cost, architects, builders, and owners can make a positive impact on the environment and contribute to a more sustainable built environment.
The understanding of sustainability gained new focus in the building industry in the early 2000s, in part accelerated by the expansion of the USGBC’s environmental ini-
tiatives and regulations. Around this time global architecture firm Corgan began questioning how buildings could be designed in a way that they are no longer a detriment to the environment, but rather active contributors to restoring ecological balance.
Corgan’s Botanical Research Institute of Texas (BRIT) integrates various innovative (and unconventional for their time) sustainability measures—including the implementation of both structural and aesthetic concrete components. The decision was initially driven by cost restrictions and the need for construction efficiency in developing the LEED Platinum facility. “The concrete becomes both your envelope and your structure, meaning you don’t have duplicative columns or foundations,” says Matt McDonald, commercial sector leader and principal at Corgan.
The use of precast at BRIT was also an aesthetic choice, affording a cleaner, more uniform facade design. The undulating panels were fabricated offsite, allowing for a degree of precision and quality control that would have been difficult to achieve with traditional onsite methods. How the precast panels were colored and treated with a natural
The Corgan-designed Botanical Research Institute of Texas (BRIT) project includes both structural and aesthetic concrete components.
This courthouse was designed to LEED Gold BD+C standards and showcases concrete’s sustainability, inherent durability, and low maintenance requirements.
finish eliminated the need for exterior paint, simplifying the building envelope while significantly reducing maintenance concerns like peeling and weathering.
A blade connection for scaffolding was specially fabricated to ensure the bracing system did not interfere with the exterior appearance of the panels, according to Regina Stamatiou, project manager and vice president at Corgan. Developed by US-based building products manufacturer Gate Precast, this element keeps aesthetic intent intact while removing the need for additional patchwork in the future, minimizing interventions and resources for repairs. In July 2024 Gate Precast joined Wells, expanding to a national footprint.
Architectural precast allows for various aesthetic expressions and more design flexibility than ever—with virtually unlimited shapes, textures, and finishes that can be
adapted to suit different design requirements and ensure long-term sustainability, says Brian Griffis, Gate Precast’s vice president of sales. “By emulating materials like natural stone through our GateStone finish, we also reduce the need to quarry additional materials.”
Beyond aesthetics, precast concrete’s inherent durability and low maintenance requirements are pivotal in reducing the environmental footprint over a building’s life cycle. “It’s a timeless material that doesn’t weather. It holds up to the elements and is very sustainable in its fabrication and longevity,” McDonald says.
Broadly, precast concrete can contribute to a reduction of up to 40% of embodied carbon compared to traditional cast-inplace methods, according to UKGBC. Griffis
PHOTO BY GABE FORD
“It gives the building a real identity of its own.”
LEFT The Printing House Hotel, part of the Tapestry Collection by Hilton, in Nashville, uses Gate Precast’s unitized precast solutions.
says innovations in precast concrete—like GateLite, with thinner, fully insulated panels—further reduce embodied carbon while maintaining high-performance standards, exponentially aligning with the industry’s sustainability initiatives. “You’re also getting that continuous insulation and encouraging industry advancements such as admixtures, cement substitutes, and Type 1L cement to lower cement content,” he says.
As impacts upon and demands of the building industry continue to evolve, so too does the impact of precast concrete. Notably industries like data centers, health care, and cultural institutions are embracing its advantages, some even seeking to adopt total precast systems for their unparalleled benefits. Griffis says “clients are looking for cost control, speed to market, improved quality, and minimal project risk.” Gate Precast has been increasingly working with more lightweight, unitized precast solutions prefabricated offsite with glass and insulation that allow for faster installation, minimized onsite labor, and higher quality.
Applications are diverse and also site-specific, integrating means for resiliency, including hurricane-resistant designs in the Gulf and wind load-resistant panels for tornados in the Midwest. “A lot of it is designed around the need for 100-year buildings,” he says.
Thirteen years on from the completion of BRIT, Corgan, too, continues its commitment to sustainable construction as it seeks to achieve carbon neutrality by 2025. Their ongoing project is a net-positive corporate campus for Wells Fargo in Irving, Texas, employing a faceted precast concrete facade that speaks to the growing demands to meet environmental goals within the industry. gb&d
WORDS BY SOPHIA CONFORTI
In the built environment the success of a building is determined by its performance. Yes, aesthetics are important, but if a structure doesn’t live up to the building intent, then it has failed.
In the past “building performance” has been a generic phrase used throughout the built environment for how well each element of a building works together. But in today’s data-driven world, building performance is evolving, transforming how we construct and design buildings along with it—especially when it comes to efficiency.
“The whole building industry is advancing, which means that every design and operations element needs to be considered for overall performance and energy efficiency,” says Elsa Mullin, sustainability director at Skanska. “We’re no longer just looking at operational energy or operational carbon anymore. We’re also looking at embodied carbon and things that otherwise are harmful to human and environmental health.”
For exterior walls, in particular, a multitude of considerations must be carefully considered to achieve optimal building and energy performance. And they go far beyond the traditional codes and measures the industry typically thinks of.
“We have to go above just the typical MEP systems, standard R-value, and thermal performance,” Mullin says. “Now we have even more attention and focus on how important air tightness is and also making sure we’re not over-insulating or under-insulating a wall. Designing for resilience is extremely important, too.”
To meet modern standards for building performance, Mullin says building disci-
plines must come together ready to collaborate as early as possible on a project. “With all of these considerations now, you need a holistic approach really early on,” she says. “It really takes a team willing to dig in early and vet different design solutions and different materials to get there.”
Needless to say, there is a lot of pressure on the building envelope to make buildings efficient, resilient, and safe for occupants. The team at DuPont is working to find the balance between meeting—and exceeding—those requirements and innovating solutions that ease installation, reduce costs, and, ultimately, create better, high-performing buildings.
“Given the growth of continuous exterior insulation, architects face a real challenge when it comes to exterior wall design,” says Chip Bisignaro, national account manager at DuPont. “They’ve got to balance energy needs and are required to provide a system that is not only energy-efficient but at its core is fire-resistant and meets code. It can get very complicated.”
Exterior building systems in particular include many considerations that must be carefully thought through for optimal building and energy performance.
“The whole building industry is advancing, which means that every design and operations element needs to be considered.”
“Given the
exterior insulation, architects face a real challenge when it comes to exterior wall design,” says Chip Bisignaro, national account manager at DuPont.
Of the many fruits of DuPont’s labors, the DuPont™ ArmorWall™ System is a standout. The system consolidates five traditional building enclosure elements into one: structural sheathing for direct cladding attachment, fire resistance, air barrier, water-resistive barrier, and continuous insulation.
“It’s a five-in-one solution. It takes applications on the exterior wall—as far as solutions that provide insulation, air and water barriers, and structural sheathing— and combines them into a single product,” says Casey Sincavage, DuPont North America ArmorWall growth manager. “It can be installed quicker than doing each layer individually, as is done in a traditional wall assembly, while also adding the value of being able to attach cladding directly to the ArmorWall System. It’s about building more efficiently with a single solution that achieves more.”
In a way ArmorWall works as a blank canvas, Bisignaro says. “Architects may
want to use a certain cladding product or products, but it adds cost because of the complicated structural design needed for the cladding installation. With a product like ArmorWall, you’re essentially creating a canvas that you can directly attach these cladding systems to.”
Of course, essential building elements like cladding attachment, air barriers, water-resistive barriers, and insulation are not new. But DuPont’s holistic view on creating a solution that puts these individual elements at work together is innovative. ArmorWall is perhaps a prime example of how manufacturers are putting Mullin’s whole-building approach to building performance into practice, finding ways to work together early and efficiently before breaking ground.
“The materials themselves have been around for a long time, but the idea of combining them into a multi-layer material serving multiple purposes to speed up the construction process is relatively new,” Bisignaro says. New—and an offering that
“By consolidating products to be installed separately, you reduce labor and reduce costs.”
can bring efficiency and performance to the construction process itself.
“Years ago continuous exterior insulation, or ci, was not a major part of commercial wall designs. Architects are now adding ci regularly to their designs to meet growing energy code requirements, so that’s another contractor and another schedule for general contractors to account for. Not only that, but you need to install sub-girt assemblies to span the depth of that insulation to handle your cladding loads, which adds another whole step to the construction process,” Bisignaro says. “What we at DuPont try to do is say, despite having all these requirements, a multi-layered performing material like ArmorWall can help eliminate steps without sacrificing quality. There are less subcontractors and less construction
schedules for a GC to manage.” And he says owners can begin generating revenue earlier because buildings can be built faster.
Sincavage agrees. “By consolidating products to be installed separately, you reduce labor and reduce costs. It’s about reducing labor and requiring less materials from different manufacturers to achieve the same thing or more, because we’re adding the capability of direct cladding attachments without fastening back to studs. Before it would take maybe four trades to install the exterior wall detail. Now you may only need one to two with this wall system,” he says.
From a sustainability standpoint ArmorWall offers a reduction of onsite waste generation since weather-resistive barriers and insulation, for instance, are now installed together. It’s also GreenCircle Certified and
eligible for LEED credits. The ArmorWall System is ideal for incorporation into advanced energy enclosure designs—like passive design, stretch codes, and LEED—due to the limited thermal bridging of the system significantly increasing the effective thermal resistance when considering the impact of fastener and cladding attachments. When it comes to performance—because it does always come down to performance— the insulation layer of the ArmorWall System has a high R-value of 6.5 per inch.
Manufacturers like DuPont are strategizing how to sustainably innovate solutions that push the built environment further, not only to make architects’ and contractors’ jobs easier but to help ensure the buildings we live, work, relax, and play in are working in our—and the environment’s—favor. gb&d
HDR DESIGNED THE JUMP BUSINESS
CENTER NEAR SEATTLE AS A “WORKPLACE IN THE WOODS” WITH VIEWS TO NATURE.
WORDS BY LAURA ROTE
PHOTOS
BY
JOSH PARTEE
People today are more widely concerned about their IAQ, whether they work in the architecture or design industry or not, says Danielle Masucci, HDR’s workplace design director. There is a strong desire for a higher volume of outside air, while also maintaining interior temperature and humidity setpoints. “How can we be creative to provide a mixed mode of ventilation?” she says. And how do you alleviate outside pollutants while also keeping energy use low?
The trend across many HDR projects today is decoupling ventilation from thermal needs, according to HDR’s Tom Knittel, sustainable design director. “Water is 782 times denser than air and is therefore a better medium to heat or cool our buildings,” Knittel says. “Delivering the right amount of air for the activities and quantity of occupants is critical to maintaining healthy and productive spaces. Using hydronic-based systems like all-electric air-to-water heat pumps that eliminate onsite fossil fuel combustion is an important part of achieving healthy, low carbon buildings, set up for net-zero ready adaptability.”
That includes the new HDR-designed Jump Business Center, just 30 minutes outside of Seattle. For this project Bristol Myers Squibb (BMS) needed a facility that mirrored its precise work while respecting nature and thereby improving occupant well-being.
The Jump project is a two-story facility centered around a light-filled atrium and referred to by some as “the workplace in the woods” for its views to and respect of nature. In this design two simple bars allowed for core functions to be closer to workplace neighborhoods with a clear distinction between work and collaboration areas. Health and wellness were prioritized throughout,
with an open, unassigned, active workplace. A rooftop area is designed to support future photovoltaic power for net zero to support the company’s 2040 climate action goals.
Mixed-mode ventilation is enabled by the central atrium, providing free ventilation for approximately one-quarter of the year. The feasibility design initially considered had elevators in the middle of the building—as many buildings do—but HDR chose a more sustainable strategy. For more than a quarter of the year they bring in outside air through ductwork. “It is pulled through buoyancy through that central atrium, and it’s filtered because we have, in some cases in Seattle and other places, wildfires and other instances of poor air quality,” Knittel says.
Heat recovery ventilation and Dedicated Outside Air Systems (DOAS) will continue to be critical to sustainable designs, Knittel says. “We do that at a building scale.”
HDR often uses heat recovery on DOAS, but at the Jump project they used air-towater heat pumps to provide heating and cooling directly to the DOAS for optimized efficiency. “The air-to-water heat pump moves energy from a heat source to a heat sink, such as moving heat from inside the building to the outside in the cooling season or extracting heat from outside and
HDR designed the two-story Jump Business Center around a light-filled atrium. Wood is used extensively on the interior and exterior to emphasize connections to nature. The central staircase is made from a tree that was located onsite.
moving it indoors in the winter, basically like a refrigerator but at a larger scale. It is circulating water through the building in a closed loop, then the building distributes that water to heat or cool as needed. With that we got ourselves down to a very low energy use intensity of 26 kBTU per square foot,” he says.
By leveraging natural ventilation systems and stratification (i.e. heat naturally rises) and removing all the mechanical equipment off the roof, the roof is structurally and electrically adaptable for future photovoltaics, too. “We did all that without any additional cost,” he says.
The team was very interested in reducing embodied carbon as much as they could as part of this project—and within budget, Knittel says. Estimates of embodied carbon reductions throughout the facility equal 400 years of carbon sequestration of the trees that once occupied the building’s footprint. This was achieved by substituting rock columns in lieu of concrete piers, and substantial reductions in the quantity of beams and columns over the baseline design.
“Instead of using deep concrete piers, we used rock columns, which are basically rock that’s pounded into place. I know it sounds kind of Fred Flintstone, but it’s actually really cool. Then we picked the lowest embodied carbon envelope for the building, which was metal, but we designed it in the spirit of wood,” Knittel says.
The Jump project is inspired by nature at every turn, with beautiful wood finishes
inside and views to nature out. “The thing about Seattle is, like people in Japan or in Scandinavia, they do this thing called forest bathing where they go out into the forest for health reasons. Science is showing that those terpenes—the VOCs pine trees give off—are really good for us, and they have NK (natural killer) cells that fight cancer,” Masucci says. She says conversations with a researcher at the University of Oregon were interesting, as they told HDR, “Architects think all VOCs are bad. VOCs are everywhere, and there are good VOCs, and there are bad ones.” She says, “Having our workplace in the woods we think is a positive health benefit.”
Masucci says the team was also able to afford all of the building occupants equal opportunities for daylight and views throughout the space. Providing opportunities for physical movement, encouraging people to use stairs versus elevators, was also key to the project’s sustainability. “We’re encouraging our staff to use those stairs, and we do that by elevating the visual experience.”
HDR partnered with an arborist to identify existing trees to be repurposed for the stair in the center of the atrium. “It was a beautiful thing, but also a special piece to the sustainable story that encouraged movement throughout the space,” Masucci says.
Generally speaking, Knittel says “short path ventilation,” or where ventilation quite literally travels a relatively short path, is preferred on projects. This is because the longer
it takes air to travel through ductwork or anything else that’s moving it, the more likely it will accumulate dust and microbes. HDR mitigates this occurrence with optimized filter design and “path of least resistance” duct design. Research at the University of Oregon also looked at hospitals with vertical air handling units on the roof going through multiple levels of hospitals over time. “That’s creating diverse microbiomes within buildings that are not necessarily healthy,” Knittel says.
Research like this informs architects that the structural configuration of a building and how we think about creating short path air delivery systems is worth considering. In the case of the Bristol Myers project, it was a two-story building, so they were all short paths working their way toward the atrium. “You could say, why not just scale that up if the building were twice as big, do two of those if you had space to do it? That’s to me one of the biggest things I try to think about when we’re delivering a new building: How can we design a system that, if the ductwork goes down, the embodied carbon goes down?”
In complex projects like laboratories, where even molecular air filters will clean the air, you can substantially reduce the amount of ductwork and provide a healthier interior, Knittel says. “There’s a lot of technology that, when you look at it holistically, you might say, ‘Oh, it costs more upfront,’ but that’s why we are increasingly using life cycle assessments to really prove out the real value of these decisions over time.” gb&d
Both
harvest daylight, turn lights off at night, and dim illumination levels during the day.
HDR says the Jump Business Center’s innovative, net-zero ready, holistic design supports both the well-being of the people who use it and that of the surrounding environment.
WORDS BY LAURA ROTE
Updated indoor air quality procedures from ASHRAE (Standards 62.1 & 62.2) is making it easier to have good, clean air and reduce risk, cost, and energy, according to GPS Air, a top IAQ solutions provider.
ASHRAE’s 2030 vision hopes for a built environment that provides resilient, livable, and beautiful places to live, work, shop, and commune with people. Transforming new and existing building stock is necessary to ensure a decarbonized future, according to GPS Air, who is focused on reducing the energy burden of conditioning air while improving indoor air quality.
“Years ago energy efficiency and indoor air quality were diametrically opposed,” says Tracy Stoner, special project manager at GPS Air. “You couldn’t have good indoor air quality without paying a premium for it with larger equipment and higher operating costs.”
Today that’s simply not the case—and there’s no excuse not to have both.
Implementing the new Indoor Air Quality Procedure might be the single largest equipment and energy-saving opportunity not being widely considered, Stoner says. When applied to education, office, and multi-use spaces, the procedure reduces required outdoor air by as much as 60%, according to GPS Air. It can also simplify HVAC equipment and reduce cost on both new designs and adaptive reuse projects, saving up to $2 per square foot on annual energy costs, according to GPS Air. In fact ASHRAE’s own 62.1-2019 user manual describes the procedure in this way: The IAQP
may allow for a more cost-effective solution to providing good air quality.
“The new standard allows designers to leverage design elements in a very meaningful way so you can both produce a good indoor environment for building occupants as well as do it in an energy-efficient manner. This has only been in the last year or so as the standard has evolved,” she says. “Conversations now are more open and amenable to the two of those working in a symbiotic way.”
Where you used to have to bring in large quantities of air, cool or heat it, and increase equipment size or building infrastructure to support it, today’s carbon footprint can be much smaller and the whole process can be a lot simpler, Stoner says. This is where an innovation launched in late 2024—the smartIAQ™ Dedicated Clean Air System™ —comes in.
GPS Air’s new smartIAQ Dedicated Clean Air System is an autonomous, demand-driven air cleaner for the design compounds, or contaminants, ASHRAE lists in 62.1. “It is a device that does one thing; it cleans your air, on demand, responsive to the onboard air quality sensors to determine when it’s time to work and how much air it needs to clean,” says GPS Air CEO Audey Cash. A revolution in sensors in the last five years allows the new system to measure air quality and react in real time. But you don’t have to interpret the data yourself; the system does it for you.
smartIAQ quietly operates based on advanced sensing trained to recognize build-
New from ASHRAE, Standard 62.1 specifies minimum ventilation rates and other measures intended to provide IAQ that’s acceptable to human occupants and that minimizes adverse health effects.
A new solution from GPS Air launching in December 2024 recognizes building and occupant air quality patterns, sensing when contaminants of concern, such as VOCs and fine particles, are introduced—automatically responding to clean the air.
ing and occupant patterns, accelerating air cleaning when needed and idling when unoccupied, thereby extending filter life and lowering maintenance. Onboard filtration offsets outdoor ventilation, ensuring occupants breathe clean air with minimal sound and maintenance. Thoroughly designed for easy installation and deployment, smartIAQ is compatible with inspace supply and return diffusing systems to seamlessly fit into any design. Because smartIAQ recognizes patterns and air quality risks, it only operates when needed, remaining virtually silent most of the time, and operating quickly and quietly when its advanced sensors detect contaminants of concern, for example. “It’s quiet, and it’s out of sight, out of mind,” Cash says.
With plans to begin shipping in December 2024, the system is an evolution of thinking—instead of large dedicated outdoor air systems (DOAS) for massive ventilation, balance smaller outdoor air approaches with a dedicated clean air system that targets contaminants to ensure indoor air quality is met with comfortable HVAC operation. “All of this at a fraction of the first cost,” Cash says.
“I liken it to daylight harvesting. In lighting if there’s enough outdoor sunlight, that’s free energy, that’s free illumination. You can shut your indoor lights off. Same idea here— if you don’t have enough contaminants that it’s a concern, you don’t have to run the unit as hard. It’s a fully variable system.”
It addresses a longstanding issue in the industry, Cash says, where most projects take a ventilation approach: They bring in a large amount of outdoor air to ventilate a space. “That approach works fairly well, but it overshoots that target more than 90% of the time. Building systems basically over-ventilate. There are conditions when all of that air is needed if you do not address
the contaminant at the source. And that is what makes IAQP so effective; by capturing the contaminant sources in the breathing zone instead of waiting for outdoor air to dilute, you can find a much better balance— just the right amount of conditioned outdoor air along with effective air cleaning when the occupant conditions demand it.”
Stoner says the new smartIAQ product allows a designer to use the latest ASHRAE standards and take a performance-based approach in control of contaminants— whether it’s too many people in a space, an environmental contaminant, or general building-generated off-gassing. “You’re addressing it at the source and you’re not having to increase the size of the equipment on the roof compared to traditional HVAC system design.”
Indoor air quality is top of mind in most designs these days, and that’s true of projects by HDR (pg. 154), too. HDR is a global professional services firm specializing in architecture, engineering, environmental, and construction services.
“I think a lot about the VOCs and the products we’re selecting and how that contributes to the quality of space,” says Danielle Masucci, HDR’s workplace design director. “In general there’s a greater awareness of it. We talk about it a lot more with our clients because they’re aware of that sensitivity and the quality of the air in the space.”
How a design addresses indoor air quality makes a big difference to the approach of the building overall, Masucci says, adding that the conversation really begins at a conceptual level.
“Making commitments to how you’re going to ventilate and condition the interior environment and how that can elevate
the air quality is really important because the method you move forward with as you design that new building impacts so many things,” she says. “It impacts the floor height; it impacts the roof construction, it impacts the equipment selections and whether you have air handlers or pumps. How do you design to support those building selections, which ultimately impact the energy efficiency in the building?”
Cash came into the IAQ game after years in the construction industry working with lighting and controls. He likens what’s happening in IAQ today to conversations about lighting 20 years ago.
“If you think about automated lighting, daylight harvesting, occupancy sensing, all those things really came to the forefront in lighting 20 years ago,” he says. “And then LEDs made them so much easier and more cost-effective. I see that opportunity emerging here.”
Stoner, who’s been in the industry for 30 years (including in mechanical and electrical systems design), says thinking about lighting is a great way to get introduced to energy efficiency and controls and consider the possibilities. “What we’re seeing with indoor air now is that it’s the next energy efficiency opportunity.”
Cash says the change that’s happening now is dramatic. “The single largest energy user in your building is your HVAC sys-
tem. Think about how you manage the load through variable speed systems to be more responsive to what the space needs versus relying on large amounts of outdoor air,” he says. “I watched lighting go from twoby-four light fixtures consuming more than 100 watts of energy reduced to 18 watts today with the same amount of light—arguably better quality of light—and certainly lower maintenance. The energy savings is massive. The customer experience to not have to change lightbulbs ever again is also astounding. HVAC is next.”
In IAQ, while they can’t eradicate air filters altogether, they can extend the time between changing filters as well as reduce the HVAC watts per square foot on a project by as much as 15 to 30%, since ventilation is such a big part of the conditioning load. “You now have a much more efficient building per square foot, and then by being on demand we don’t exhaust filters very quickly. We get one- to two-year filter cycles, so you get a much lower maintenance proposition than you would normally expect out of an air cleaner,” Cash says.
He says LEED version 5, which is expected to go into effect in 2025, is even taking note, as it accepts the indoor air quality procedure and provides extra points for sensing and response. “You can see this shift occurring. That’s a huge deal to us.”
And while existing buildings lose their per-
formance over time, installing an air cleaner and having variable airflow allows the building to adapt and the system to adequately clean the air in the space. “It is a much more sustainable approach, and that air quality is as good on day 1,000 as day 1,” Cash says. He says the problem with traditional ventilation is that the issue is never fully resolved. “You need to handle the source. The source for most of the contaminants in a building are either the furnishings or the people. Targeting the source of the problem by cleaning either the source itself, the VOCs in the air, or the formaldehyde that gets emitted from the furnishings—by taking that out of the air, you get better indoor air.” And that, he says, leads to healthier buildings.
“ASHRAE designed the standard around occupant comfort along the lines of air quality and what it means to have clean air. You target the problem at the source, treat it, and deliver better, cleaner, healthier air.” gb&d
WORDS BY MIKENNA PIEROTTI
You know it when you step into a room. You feel it—on your skin, behind your eyelids, in the deep rhythms of your unconscious. Lighting, especially daylight, is essential for creating a healthy, productive interior space.
Nick Inman, senior project manager at Hunter Douglas Architectural, an industry-defining manufacturer of window coverings and architectural products for more than a century, spends a lot of time thinking about this fact. Ask him for examples, and he’ll pull up photos like an 850-year-old, gold-splashed cathedral ceiling in Palermo, Sicily. “This is daylighting,” he says. “The reason they painted the whole upper half in gold—real gold—was because it was the most reflective material they had at the time.”
He’ll also mention the genius of industrial-era factory design, where north-facing clerestory windows and sawtooth roofs were no accident. They were designed to direct as much light as possible onto the factory floor.
Inman says these historical, cross-cultural truths often surface in his work today. Designers are relearning the art and technology of controlling daylight in our spaces—not only for its potential to save energy but also for its role in productivity, creativity, and health.
A range of concerns comes into play when designing a customized daylighting plan for a modern building, Inman says. But no matter when a team like his joins the process—whether during the ideation stage, just before breaking ground, or long after
the building has opened—they can find solutions that balance the power of the sun with human needs by asking a few key questions.
“Our first question is: What does the building look like? We examine the building plan, the orientation, and the location.”
A project in northern Alberta, Canada won’t have the same challenges and opportunities as one in sunny California. In one case Inman may recommend directing light and heat onto a slab floor to reduce heating costs in winter, while in the other he’d likely explore how to reduce glare with exterior shades.
Purpose also matters: What is the space used for? Is it an art gallery or office space? Should daylight be minimized to protect sensitive objects, or leveraged to keep workers productive and comfortable even on the hottest, brightest days?
How can the space be made as sustainable and healthy as possible for the people who use, maintain, or are impacted by it?
“In hospital settings, for example, facilities workers have much bigger concerns than maintaining the shades,” Inman says. Only by taking all these factors into account can designers and manufacturers create a customized system that stands the test of time.
For modern designers like Shivani Langer, director of regenerative design and senior project architect at Perkins&Will, creating healthy spaces is a calling. Twenty years ago c onversations around daylight focused primarily on energy savings, with an emphasis on harvesting natural light to minimize artificial lighting. But that has
Top-down and bottom-up tension shades allow for more light control
Controlling light and glare is crucial in an art setting such as
BY ROLAND BISHOP
evolved with the rise of LEDs and stricter building codes.
“Turning off the lights no longer saves as much electricity as it used to,” Langer says. Now the bigger question is how to control the light that enters a space to maximize comfort and usability—and how to do so sustainably, often to meet and exceed benchmarks like LEED or the WELL Building Standard.
“Early versions of LEED only asked us about how much daylight was getting into the space. That was a minimum standard,” she says. Today certifications require a balance between daylight and occupant comfort. “All rating systems are realizing it’s not enough to bring in minimum daylight; we also need to stop glare that leads to discomfort.”
To achieve this balance modern designers have an array of solutions at their disposal, including healthy window coverings made from PVC-free fabrics or recycled ocean plastic, and innovations like solar control fabrics that reflect solar energy, absorb minimal heat, and still allow in diffused light.
Sustainability, both in materials and processes, is a growing focus for modern de-
signers and their clients. Organizations like Hunter Douglas Architectural strive to meet high green building standards with many products, including venetian blinds made from recycled aluminum, being Cradle to Cradle–certified, and having both GREENGUARD and OEKO-TEX certifications.
Technologies like animeo and Solarai automate natural light management based on the sun’s position in the sky and facade orientation. Powered by partners Somfy and Embedia, the intelligent systems elevate these materials to a new level by intuiting a building’s daylighting needs, even when occupants aren’t present. However, Langer warns that choosing the right level of automation is critical in our AI-driven world. “Automation is great, but surveys show that people are less satisfied with their spaces if they don’t have control. It is good to provide automation with manual overrides.”
Controlling daylight will only become more nuanced as new challenges emerge. Privacy and security are becoming key concerns for designers, especially in educational
settings, Langer says. Likewise, extreme weather and tighter building regulations will require new solutions. Designers and manufacturers must collaborate, using both advanced technologies and time-tested knowledge, to meet these hurdles.
Inman points to the east-facing windows in his Los Angeles office as a prime example—durable venetian blinds outside, soft natural twill shades inside. “One of the best fabrics we have for glare control, outward visibility, and occupant comfort is a twill weave. Twills have been around for thousands of years,” he says. “But if I only had that fabric roller shade, I’d need a very tight weave or the sun’s corona would burn a hole in the side of my head. It wouldn’t be great for working. Instead we have a more open weave to handle glare, and an exterior venetian blind to block the morning sunlight. Now it’s afternoon, and the sun is in the south. I have my shade down for glare control because there are shiny cars in the parking lot reflecting light, but I can still see. I’m interacting with nature. I can see people,” he says. “This isn’t a new concept, even in the simplest architecture.” gb&d
The American Airlines headquarters in Fort Worth was designed to include sloped wire-guided shades from Hunter Douglas Architectural.
BY
“People are less satisfied with their spaces if they don’t have control. It is good to provide automation with manual overrides.”
Doors are evolving to provide more light, privacy, and flexibility than ever before.
WORDS
BY EMMA LOEWE
Doors have long served as sites of connection and retreat, bridging one realm to the next for thousands of years.
From robust Sycamore Fig slabs that enclosed the tombs of ancient Egyptian elites to iron-locked passageways that defended the barrier walls of Medieval Rome, doors tell the story of humanity. They also broadcast cultural and religious beliefs, with mezuzahs marking the doorposts of Jewish homes and red doors warding off evil spirits in Chinese tradition.
Over time door designs have ranged from the practical (automatic doors to help waiters carry plates inside; revolving doors to keep wind and snowfall out) to the ceremonial (certain Holy Doors are sealed from the inside, only to be open during religious holidays). They’ve spanned from Gothic to Georgian, Romanesque to Renaissance, and every style in between.
Nowadays designers and manufacturers are adjusting entryways to fit the needs of the modern consumer—and they’re leaving no door unopened in the process.
In a residential context doors have always acted as barriers between a home and its environment. Now more homeowners are looking to bring the outside in.
“Historically there was a lot of decorative glass on doors. You got a little bit of light from the glass, but it was really for style purposes,” says Denise Quinnette, executive vice president of engineering and product management at ODL Doors. But as people become increasingly aware of the benefits of natural sunlight, she’s noticed an uptick in doors with large-format glass and very thin frames.
For homeowners looking for natural light and clean lines, ODL offers flush-glazed glass doors in many styles. These embed glass directly into doors and streamline framing,
making the glass a more prominent part of the overall design.
“Some of the other flush-glazed doors on the market don’t have the clean, sharp lines we have,” Quinnette says. “It’s a more seamless construction that elevates the home aesthetic.”
In addition to flooding home entrances with light, large-format glass doors serve an important design purpose: They are more legible on homes with natural, unfinished siding.
Many architects are turning to doors with more glass for this very reason. For the Red Creek Road Residence, architects used glass to ensure the front door was immediately visible among the exterior cedar. “It reads as a gap in the wall that signifies the entrance rather than the door itself,” says Magnus Westergren, an associate at Marvel Designs, who designed the home.
Safety, Privacy, and Energy Efficiency
“Doors impact not only the aesthetics but also very much the functionality of the home,” Quinnette says. As more manufacturers embrace glass, they will also need to consider safety and security.
Older adults in the US are staying in their homes for longer, which means more doors will need to be ADA-compliant and easy to maneuver for those with limited mobility. Privacy will also be key, as some homeowners may feel more comfortable with textured glass that obscures the view to the inside while still allowing in plenty of light.
In a rapidly changing climate, glass will also need to be able to stand up to extreme storms while leaving behind a light impact. Research shows that triple-paned glass can be upwards of 40% more energy-efficient than double-paned, and it can be retrofitted with inert gas for additional insulation. As certification bodies like ENERGY STAR look to tighten their standards for residential and
Modern doors need to balance homeowner’s desire for sunlight with their need for privacy.
commercial properties in the future, these highly insulated materials will likely be in higher demand.
“As you put more glass in, how do you make sure you don’t lose energy efficiency in the doors? How do you make sure you have the structural integrity that you need?” Quinnette predicts these questions will influence door design for years to come.
Natural Look
The front door is the first opportunity for people to engage with a space, and it’s often the part of the building that guests get the closest to. “The fact that doors have a tactile element means that they become a lot more memorable than other parts of the facade,” says Marvel Architects’ Westergren.
Since doors are where first impressions are made, their materials and hardware are essential. Most residential doors are made
out of wood, fiberglass, or steel, and each materials comes with its own set of pros and cons.
While natural wood has a beautiful grain, color, and weight, it tends to be more expensive and prone to warping. Over time it may not form as tight of a seal with its frame, impacting the energy use and thermal comfort of a home. Quinnette estimates that only 5 to 10% of new doors are made from wood for these reasons.
But when one door closes, another opens. Quinnette has seen the market increasingly move toward fiberglass options, which are durable and well-insulated. “Every year we see fiberglass doors taking over more of the market share,” she says.
Fiberglass can be treated to resemble solid wood for a sliver of the price tag. ODL went to great lengths to emulate the warmth and texture of wood with its fiberglass Rift
Cut line and even created a wooden door model to ensure the texture and staining were just right. “From a curb perspective it’s really indistinguishable whether you have a fiberglass door or a wood door,” Quinnette says.
One downside is that fiberglass is more difficult to reuse or recycle than wood or steel. The composite material must be manually broken down into its constituent parts that can be used for lower-value applications (like planks for decking or material for park benches). As fiberglass becomes more popular ODL and other manufacturers are looking to minimize its construction waste and find innovative ways to give it a second life.
When asked to imagine the door of the future, experts in both manufacturing and architecture predict some high-tech elements.
For the Red Creek Road
Residence Marvel Architects used glass to ensure the front door was immediately visible among the exterior cedar.
“The fact that doors have a tactile element means that they become a lot more memorable than other parts of the facade.”
“Some of the buying power is moving away from the baby boomers to the younger generations—and they’re very tech-savvy,” Quinnette says.
Smart security features like facial recognition software, doorbells that detect motion and record video, and voice control locks are posed to gain popularity among a new generation of homeowners.
ODL is also working on giving door glass the smart treatment, with technologies that automatically shade the glass from within on sunny days as well as obscure the view from the outside for privacy. “Right now those are two different technologies, but we’ll be looking to see how we could accomplish both of those with the same tech,” Quinnette says.
The industry will also need to figure out the most efficient way to power these smart upgrades—be it by installing a battery into the door itself or running wires through its hinging or frame. Solar energy could help provide a clean source of juice, as long as doors have contingency plans for rainy or overcast days.
Even as these technologies go mainstream, Westergren hopes that homeowners still hang onto old-school door vestiges like keys. “They’ve been around for thousands of years,” he says. “They should stick around for longer.”
The front door can pull together a commercial or residential project, keep interiors safe from the elements, and serve as a gateway into the world of a building. Choosing the right one also opens up new design possibilities, helping to break up a building’s exterior or fill its interior with light. “If you’re spending a bit of money on a project, it’s worth it to spend it on doors,” Westergren says.
As we unlock the doors of tomorrow, we’ll likely find them equipped with smart security systems, innovative weatherproofing, and adaptable designs that provide privacy, storm protection, and sustainability benefits. Talk about a grand entrance. gb&d
The Red Creek Road Residence is a 5,000-square-foot weekend residence located on the Great Peconic Bay in South Hampton, New York.
WORDS BY SOPHIA CONFORTI
They say cats have nine lives. In the built environment, materials are lucky if they get just one.
“We know that we have a circularity problem,” says Candon Murphy, firmwide materials resource manager at HOK. “We know we need to prioritize materials that can have a second, third, fourth, and fifth life.”
But in the industry shift to circular design, the problem is not necessarily in specifying circular products. The larger issue, Murphy says, is identifying those materials that can be reclaimed and repurposed.
“What I’ve seen throughout my career is that there is a lost link in being able to identify the materials upon demo. The contractor who’s working on the demo is generally not the same contractor that built the space. So how would they know what these items are?” she says. “The legacy information about a design gets lost. How do construction drawings, purchasing documents, and our knowledge as an architecture and design firm get translated through the life of that built environment and then handed off to the person who’s taking it down in the end?”
In countries throughout the European Union, that kind of legacy information is readily available. But in the US, when a tenant vacates a space, they often leave it asis. When the new tenant comes along, there is no information beyond the visual cues of the space—and that previous tenant, and all of the material knowledge with them, is long gone.
At HOK the team has developed a materials tracking framework to increase transparency and make material information more accessible. Rooted in the AIA Materials Pledge and Common Materials Framework (CMF) from mindful MATERIALS, HOK’s ma-
terial tracking system is built on data from third party certifications and manufacturers to help decode some of the highly technical language around materials.
Everyone in the firm, from the most junior members all the way to the top, is responsible for contributing to the framework. And since they started tracking data in 2020, Murphy says the team has found some holes in the market, where certain product categories have a lot of information missing.
“It’s been helpful for us to see where we need to do internal education but also where we need to do external advocacy,” she says. “Circularity is a really interesting conversation because it’s something we’re learning how to do pretty recently in the built environment. Reclaiming materials— that’s actually a pretty difficult conversation because as designers we don’t really have the power of what happens at the end of the life of our project. We’re starting to talk about that now and trying to get help from manufacturers to figure out how to make that happen.”
Ecore is betting it all on circularity. The company started in 1871 as a cork manufacturer before experimenting with rubber in 1965—its primary focus today. And while rubber—and cork, for that matter—are both sustainable materials, merely using them hasn’t been enough for Ecore. Ecore is pio-
Ecore Athletic flooring supports a variety of workouts with its durable, shock-absorbing surface—ensuring safety and performance for athletes of all levels.
neering, in its own words, the “rubber waste revolution”—reclaiming discarded rubber and reusing it endlessly.
Ecore diverts 430 million pounds of commercial tires—the equivalent of 8.5 billion water bottles—from landfills annually, avoiding 9.5 million pounds of carbon dioxide emissions. It boasts more than 1,500 product variations made from reclaimed rubber.
“Over the course of my nearly 30 years in the industry I have seen the evolution from when people didn’t want recycled material because of the misperception of lower quality to the green building movement in the early 2000s to now where people are saying, ‘We don’t just want recycled content. We want transparency to the manufacturing process and to what happens at the end of a product’s life,” says Rich Willett, president of flooring and industrial at Ecore. “This aligns with Ecore’s belief that the most sustainable materials are the ones that already exist. For us there’s no end of life. Material goes right back into the cycle and becomes circular.”
It all starts with reclamation. Ecore has partners across industries—the built environment, tire maintenance, trucking, distribution fleets, and more—to identify and collect discarded rubber materials, including rubber tires, flooring, playgrounds, and more.
Then they transform it, cleaning and grinding the rubber waste to remove impurities and create new high-performance products. From commercial flooring to sports and play surfacing, industrial components to transportation and agricultural products, “there are so many different products that lead to so many different design possibilities,” Willett says.
When Ecore’s rubber products do reach end of life, the TRUcircularity take-back program allows Ecore to reclaim those materials and repurpose them again and again.
Through it all the rubber never loses its inherent benefits—of which there are many. Rubber is naturally sound absorbent, leading to better acoustics and quieter spaces. It’s better for our bodies physically, with
Ecore’s cutting-edge athletic flooring at the UNLV Football Facility supports athlete safety, performance, and team spirit with a bold design and high-performance features.
comfort underfoot that helps reduce strain on our backs, legs, and feet. Rubber is also slip-resistant, making it safer to walk on, and the material is resilient and easy to maintain.
And then, of course, there is the sustainability factor. The circularity of Ecore’s rubber products keeps rubber waste out of landfills and gives it new life. But its manufacturing processes, too, are helping the environment. Ecore’s facility in York, Pennsylvania, earned UL Platinum Zero Waste to Landfill certification, the highest designation that is awarded to plants that consistently achieve a landfill waste diversion rate of 100%. And because Ecore manufactures in the US, the company reduces the carbon emissions and energy usage that comes with transporting products across far distances.
Beyond rubber and how it’s manufactured, perhaps the biggest indication of Ecore’s commitment to circularity is in its recent hiring of Shweta Srikanth, the company’s first chief circularity officer. With
Srikanth on board, Ecore is one of the first companies to add a dedicated circularity executive to its leadership team. And Srikanth is ready as ever to join Ecore’s rubber waste revolution and change the way the built environment—and all industries—look at circular design.
“What Ecore is trying to do, being 100% circular on rubber, is not something any other company has done before. It’s exciting to be at the forefront of rubber circularity and paving the way for more companies to think about what circularity looks like,” she says.
That includes developing circularity criteria and conducting life cycle analyses to really understand the impact of materials— even circular ones—on the environment and where we as an industry can continue to innovate.
It’s this innovation that has driven Ecore to this point in its 153-year history. Society has evolved, and Ecore has moved with it. “We were a flooring company,” Willett says. “But now we’re a rubber circularity company.” gb&d
Used tires travel along the conveyor belt at the beginning of their transformation into sustainable, highperformance flooring materials for Ecore.
Ecore’s recycled rubber rolls, seen here in bulk, are ready to convert into sustainable flooring products, embodying the company’s commitment to circularity and environmental impact.
Ecore’s flooring is often specified in hotel spaces for its safety, ergonomic, and acoustic benefits.
COLOR AND PATTERN ADD TO THE LIVELINESS INSIDE OF THE NEW LINKEDIN OFFICE IN TORONTO, DESIGNED BY CANNONDESIGN.
Flexible office spaces continue to be in high demand.
WORDS BY MATT WATSON
The increase in remote work opportunities coupled with the rapid advancement of workplace technology over the past few years has significantly altered how architects, developers, and employers conceive of contemporary office design.
“It has been proven that most work can happen anywhere,” says Peter McCarthy, principal and commercial leader at CannonDesign, a top architecture firm with nearly 1,300 employees across 18 offices. “This means workplaces are now competing against the comforts of home or an employee’s local coffee shop.”
These trends in office design have placed a greater emphasis on the overall experience that a workplace offers to employees. Workers now have far greater choice of where they can operate, and organizations are responding by creating new reasons for their workforce to return to the office.
You won’t find many single workstations at LinkedIn’s Toronto office. Instead, “desksharing neighborhoods” are set up for tapered schedules, balanced with enclosed rooms and pods for quiet meetings with clients as well as more social seating options.
The flexibility and adaptability of a workplace is key to accomplishing this. Office designs now include spaces for individual workstations as well as private meeting rooms, flexible conference and team collaboration spaces, as well as central common areas like cafes that can spark cross-team interactivity.
“The goal is not to have people come in, put their headphones on, and work independently,” McCarthy says. “Companies are creating spaces so that when people do come in, they can have town hall meetings, team collaboration, greater virtual connectivity—it’s about fueling work opportunities that cannot be realized from home.”
LinkedIn’s new office in Toronto offers an instructive case study of these trends. CannonDesign was awarded the project in 2019, but the onset of the Covid pandemic paused the project and led to a broader discussion between the design team and client about the future of the workplace. A new phased construction approach allowed the team to test different layouts, furniture and
technology solutions, and the square footage of various spaces, and apply the best results.
“The idea behind the project was to create an ecosystem of connections,” McCarthy says. “The workplace is designed to be exceptionally adaptable and nimble to empower all different teams, technologies, and work styles into the future.”
There are few singular workstations at LinkedIn’s Toronto office, which features “desk-sharing neighborhoods” for tapered schedules balanced with enclosed rooms and pods for quiet meetings with clients. Visual elements were also incorporated, such as an environmental graphics program designed by Toronto illustrator Jeannie Phan that depicts a natural wonder of Canada on each of the company’s three floors.
“By creating that array of spaces, you give employees choices and companies flexibility to change and pivot spaces dayto-day and season-to-season as needed,” McCarthy says. “These efforts will also help instill deeper pride for employees in their organization.” gb&d
“THE IDEA BEHIND THE PROJECT WAS TO CREATE AN ECOSYSTEM OF CONNECTIONS.”
WORDS BY MATT WATSON
Designers and their clients are employing a number of unique strategies and tools to address the changing dynamics in contemporary office design in the “work-from-wherever” era. Bryan Welch, president of Modernfold—a leader in movable wall partitions— agrees that flexibility and adaptability are critical in today’s office market.
“I feel like flexibility is becoming more and more of an expectation, rather than an add-on, from an office design standpoint,” Welch says. “We make operable partitions, but what we are really selling is flexible space.”
Movable partitions can facilitate a more adaptable work environment by giving tenants the freedom to quickly reconfigure their spaces to meet their needs at any given time. And while architects once viewed movable walls simply as utilitarian tools to address this particular need, recent innovations in the market have resulted in a wide array of products that can create both beautiful and functional spaces.
“If an organization can evolve conference spaces into amenity spaces or flex the number of workstations they need month-to-month, then they are inherently more ready for the future,” says Peter McCarthy, principal and commercial leader at CannonDesign, a top architecture firm with nearly 1,300 employees across 18 offices.
Yet encouraging employees to return to the office requires more than building out an adaptable space. At a time when office footprints are shrinking and the same number of employees are expected to productively share a smaller space, privacy and comfort are factoring into design decisions more than ever.
“The office needs to be a space that feels good to go to. It has to be a productive environment; you have to feel efficient, like you’re getting something done,” Welch says. “You made the commute, and when you get there it needs to be some place that you want to be and accomplish something that you would have difficulty doing remotely.”
As hybrid work becomes the new normal and companies large and small adjust their spaces accordingly, movable walls have moved up on architects’ radars as a necessary feature of their designs.
When Lifeway, a nonprofit provider of ministry resources based in Nashville, set out to create a new home for their hybrid workforce, the space needed to be flexible and adaptable to accommodate private workstations, small team meeting rooms, multimedia production spaces, and gathering areas for up to 300 people to host produced launches and larger events.
To accomplish this, the design team worked with Modernfold to incorporate the firm’s Acousti-Clear® Glass Wall Systems into the concept. In a space that would serve a diverse array of uses and needs, Acousti-Clear’s combination of sleek, modern aesthetics and high acoustical control made it the ideal solution.
The 4-inch dual paned glass wall system was customized with a satin black powder coat frame to match the frontage window design of the building, and its 51 STC rating—a measure of the number of decibels of sound it can block out—meant that the operations in the organization’s video, podcast, and photography studios would not disturb employees who needed a quiet place to work.
“The Lifeway project addresses the return-to-work revamps that are quite common these days as companies look to maximize their footprint with a partially remote workforce and simultaneously create an inviting space that employees want to go into the office to enjoy,” Welch says.
As office footprints shrink employee comfort and privacy are more important than ever, as crowded open spaces cause distractions that lower overall productivity.
Even when separated by a partition, a series of adjacent meeting rooms will not provide comfortable, productive spaces for their occupants if acoustical control has not been considered in the design phase.
That’s why Acousti-Clear has been engineered with a higher STC rating than traditional glass wall partitions. “I can’t give away the exact secret sauce, but our engineers were able to find the right formula that allows it to stop more sound without adding to the weight of it or making the panels thicker,” Welch says.
The comfort of a workspace extends beyond acoustics, and hybrid workers have become accustomed to the health and wellness ben-
Movable partitions can facilitate an adaptable work environment by giving tenants the freedom to quickly reconfigure their spaces to meet their needs at any given time, as seen here at Lifeway.
“SUSTAINABILITY CONTINUES TO BE MORE AND MORE IMPORTANT WITH DECISION-MAKERS,” WELCH SAYS. “WHAT’S CONSIDERED A HIGHLY SUSTAINABLE PRODUCT TODAY MIGHT BE AVERAGE IN THE NEXT FEW YEARS.”
Buchalter upgraded its entrance and conference space for more flexible work environments with a movable wall system.
efits of natural daylight. That’s one of the reasons glass walls have become increasingly popular in interior design, as they allow everyone in a workplace to experience daylight—not simply the executives with corner offices.
“More and more there’s pressure to open office spaces up on the interior and push light deeper and deeper into the building, and our glass wall portfolio can help with that,” Welch says.
This was a key consideration when national law firm Buchalter began renovating portions of its Portland office, including the conference spaces. The firm’s office offers sweeping views of the Port -
land skyline, and the goal was to ensure these views could make their way into the entirety of their space.
Buchalter engaged Modernfold to explore solutions that would maximize views and daylight while also offering sound control for their conference rooms. The firm landed on Modernfold’s Pureview® Plus horizontal rail system, which features a slimmer, single-paned glass system that employees can easily operate themselves with a 37 STC rating, and was able to create a bright, transparent space with appropriate acoustical control.
“What are architects looking for today? They want a product that integrates well
with their design,” Welch says. “They want something that is as simple as possible, looks good when it’s deployed, and fills the needs of the space.”
Movable partitions like Modernfold’s suite of products can also be used to achieve sustainability goals and support LEED points for energy as well as indoor air quality. Offering health product declarations (HPDs), environmental product declarations (EPDs), environmental impact reports, California Department of Public Health certifications, and GBCI-certified continuing education, Modernfold is focused on being the sustainability partner in the operable wall market. “Sustainability continues to be more and more important with decision-makers,” Welch says. “What’s considered a highly sustainable product today might be average in the next few years.”
Movable walls help facilitate zoned HVAC systems by partitioning off unused sections of the office, where the HVAC system can be shut off until the space is used. “This helps lower your CO2 load because now you have a smaller space to heat or cool more efficiently,” Welch says.
The daylight that glass walls bring into a space further reduces energy use for lighting and provides occupants with greater access and visibility to a natural, outdoor environment, improving overall occupant well-being.
Few can predict with certainty what the future of offices will look like, but according to Welch, technological features like automation will only continue to grow in popularity.
“What we see is that automation is the way of the future. If you go back and look at car windows, manual operation was standard and automation costs extra. Today customers expect automation to be the standard,” he says.
Modernfold’s ComfortDrive® offering is an automated self-driving panel system that allows its glass panels to be moved to pre-programmed positions with the touch of a button. The system works on programmable trolleys with a home position, a deployed position, and two additional custom configurations.
This feature ensures consistency while removing the need for workers to manually move partitions between meetings. This is especially beneficial in spaces that turn over multiple times each day for different needs.
“Automation is going to support that need for flexibility because the space is going to be transformed so quickly,” Welch says. gb&d
20 Brattle Street gives young professionals an office environment that’s flexible and sustainable.
WORDS BY IAN P. MURPHY
PHOTOS BY CHRIS ROGERS
It takes more than good colleagues and an attractive salary to get young workers into an office. A Zoom call can’t always foster creativity, spontaneity, and camaraderie, though, so workplaces are being reconceived post-pandemic to give the best and the brightest the kinds of spaces where they can thrive.
Completed in December 2023, 20 Brattle Street is at the forefront of trends in workplace design. Emphasizing flexible workspaces and hybrid work, Dyer Brown & Associates outfitted the space to suit the preferred work styles of Generation Z—the demographic cohort that will be reshaping the professional workforce in the decades to come.
Christened The Abbot by developer Regency Centers, the 16,000-square-foot space spans the upper floors of three adjacent buildings—two historic—at the center of Harvard Square in Cambridge, Massachusetts. Designed to attract young talent and startups to its sustainably designed coworking suites, it’s almost an extension of the Harvard and MIT campuses.
The design “supports the culture and workflow of the kinds of forward-thinking organizations members of Generation Z overwhelmingly say they want to work for,” says Sara Ross, who led the 20 Brattle Street project as principal and director of Enterprise Services at Dyer Brown. “It’s built to collaborate.”
A glowing circadian orb above the conversation pit at the point of the building makes it look like a shadowbox after dark.
PROJECT: The Abbot
LOCATION: Cambridge, MA
ARCHITECT: Dyer Brown & Associates
Size: 16,000 square feet
Completion: 2023
Developer: Regency Centers
Dyer Brown launched its work on the project with a strategy session, asking local students, entrepreneurs, and other likely users to weigh in on the amenities they want in an office space. “We conducted a bunch of surveys to get feedback on what was going to go in the building and why,” Ross says.
Young workers are looking for professional development and growth and prefer a flexible work environment that encourages interaction. “People—and in particular, Gen Zers—are looking for a variety of places to work in the office and communicate and be seen and see other people,” Ross says.
The Abbot offers spaces that can be configured quickly to meet a variety of workplace needs. There are private offices, shared offices, formal conference rooms, and informal huddle spaces. There are phone booths for calls, pits for open collaboration, and a fully soundproofed podcast studio.
“There’s a wide range of space types that can be used wherever your day takes you,” Ross says. “If you want to have a one-onone mentoring, you can do that in one of the smaller rooms. But if you’re having a huddle with your peer group or team, you can go to a room that holds five, six, seven, or eight people.”
Rooms offer seating options including desks, chairs, lounges, and even beanbag chairs to allow employees to choose what’s most comfortable for them and the task at hand. Most offer flexible configurations and height-adjustable surfaces. Webcams, monitors, and whiteboards support scheduled meetings and spontaneous breakouts alike.
“20 Brattle Street really is meant for you to get out your marker and start putting a quadratic equation on the board or figuring out the next best thing someone’s going to invent,” Ross says. “Having that capability anywhere you go was really important when we were building out the space and design.”
Survey respondents also expressed a desire for a workplace that protects health and wellness. Dyer Brown specified enhancements to the interior environment such as far ultraviolet air sanitizing technology. “The amount of filtration is almost like having a constant breeze in your space,” Ross says.
Ceilings and walls limit noise with acoustic panels and sound-dampening construction. Undulating acoustic baffles of recycled PET plastic from Turf run throughout the common areas, further squelching echoes. And an appreciation for neurodi-
vergent workers led Dyer Brown to include dedicated quiet spaces.
A Japanese-inspired reception area invites visitors to remove their shoes, minimizing ambient noise and adding to the calm. A living wall of moss and potted plants sets off a multipurpose café/event space that features reclaimed-wood accents.
Materials meet a near-vegan and ethically sourced standard. Most wood surfaces are crafted from reclaimed wood. The concrete countertop in the kitchenette incorporates recycled glass. And Dyer Brown opted for wool upholstery over leather or vinyl. “Everything is sustainable and rapidly renewable,” Ross says. “Sheep need haircuts, too.”
Circadian lighting gradually dims after business hours, providing enough “tuned” light to continue working, but preventing late-night brainstorming sessions from interfering with sleep schedules. “The building is telling you that maybe you should get some rest,” Ross says.
The design aims to “spark wonder” with bright, unexpected color combinations and natural textures. It’s like a high-end spa crossed with a Nickelodeon set—a place industrious young disruptors can enjoy creating.
“We wanted to make sure there were lots of nods to nature,” says Samantha Worth,
The space features a variety of flexible seating options, including traditional office chairs, lounges, and beanbag chairs.
interior designer. “Little pops of color that are found in nature are the key elements. We have these pockets of hot pink that are a nod to flowers in the environment—a really hot magenta or a millennial pink.”
Biophilic elements can make traversing 20 Brattle’s urban interiors seem like a walk in the woods, Ross adds. “You’re kind of experiencing being in nature,” she says. “The undulation of the felt panels is really meant to encapsulate you—pull you in so you feel almost like a nature hug.”
Since it unites three adjacent buildings, 20 Brattle Street required Dyer Brown to work closely with project engineers and developers to address emerging technical issues on a tight schedule.
“There were some really low ceiling height conditions,” Ross says. “In the middle section I think the floor-to-deck measurement is only about 13 feet. That may sound like a lot, but when you add redun-
dant systems for airflow and air quality, it leaves a lot of the ceiling open or exposed.”
Floor heights also vary; the middle segment required the installation of an ADA lift to ensure accessibility. “It’s challenging, but it makes our projects unique,” Ross says. “It makes for a nice user experience, because it’s not a traditional high-rise office building due to its idiosyncrasies. A lot of little nooks and crannies makes it more like a campus building.”
While sustainable, 20 Brattle Street’s real innovation is how it accommodates its end users. “We’re trying focus more on the people occupying the space, because standard practice for Dyer Brown is to use sustainable materials,” Ross says. “That’s what we live and breathe.
“We’ve been talking about the quote-unquote ‘future of work’ for almost five years now,” she adds. “Offering variety, flexibility, and different ways to work—I don’t think that’s going away. You have to create the space for all types of people.” gb&d
ABOVE A living wall of moss and potted plants sets off a multipurpose café/event space that features reclaimedwood accents from Oregon–based TerraMai.
LEFT Offices and conference rooms are easily reconfigured with adjustable height desks and movable partitions.
HED used its move to a new office to embrace community and a hybrid programming style.
WORDS BY RACHEL COON
For years HED was a small tenant in a large building in a sea of parking. Like many companies, the architectural design and engineering firm in Detroit seemed to prioritize the clients’ front-door arrival experience over, say, the staff’s happiness and workability. When the time came for HED to decide whether to move, their 100-person team made clear they wanted to stay—on one condition. “Everyone voted for a walkable city where they could feel connected to something bigger than the firm itself, where they could be part of a community with different benefits and amenities,” says Tim Gawel, HED associate principal. So the company packed up and moved to Royal Oak, a midscale urban arts community on the outskirts of Detroit also known as a core retail district.
Now on the second floor of a multi-tenant building, HED’s Detroit office boasts 20,000 square feet overlooking Main Street and the railroad tracks—a vital artery in the city. “We’re in this rich urban environment, swept up in the momentum of watching people walking by on the streets below, and you feel connected to something bigger than just HED,” Gawel says.
Like many companies in recent years, HED recognized a necessary shift from traditional offices with assigned desking and physical project settings to multi-faceted workspaces catering to undulating employee schedules and virtual collaborations across markets and time zones. “It gave us the chance to consider why people come together, which really came down to programming in a different way,” Gawel says. “We used to program by headcount; you had so many people or you needed so much of this or so much of that. Our new office design is really about being hybrid. Every setting has a multitude of ways the space can be used.”
After riding a bike to work or finding parking at street level, staff and clients enter HED’s new Detroit office the same way— through the studio, a park-like setting with ample natural lighting, grand outdoor views, comfortable benches, and various workspaces. “We created a space intended to bring you back to nature, mixing real plant materials with billboards featuring landscapes instead of architecture. The billboards are more of a psychological symbol of being in green, and having the green illustrated in such a fun, artsy way roots the company in what the Royal Oak community is all about while also understanding, from a human behavior standpoint, that green matters,” Gawel says. HED continued with its varied program-
ming by designing workspaces based on railcars and cabins, two themes that reflect the company’s new location—both on the tracks in the heart of the city and also within reach of the quieter solitude of cabins up north. “We have railcars where the team can jump in from both sides, where people want to work together without interrupting others around them,” Gawel says.
From the beginning HED was dedicated to pursuing the high standards required of WELL buildings. “A lot of what might be celebrated as sustainable moves are just a course of action for HED,” he says. “We chose to pursue WELL certification because it required us to be more consistent over time, making a significant commitment to staying on track.”
WELL certification is a performance-based system for measuring, certifying, and monitoring features of the built environment that impact human health and well-being through seven core areas—air, water, nourishment, light, fitness, comfort, and mind.
Gawel says the worlds of sustainability and wellness are merging. “On the one hand you have materials and systems, while on the other hand you have human behavior, and we know so much more now about how these pieces fit together,” he says. “Wellness is everywhere. Wellness is not disconnected from sustainability; they’re rooted together.”
In Detroit’s Royal Oak arts community, HED created interior billboards featuring landscapes instead of architecture to bring its team members back to nature. The art is more of a psychological symbol, illustrating green in a vibrant way that roots the company in its new community.
HED’s new office space in Detroit shows clients how programming can be done differently.
“Clients right now are struggling with how to create flexibility,” says HED associate principal Tim Gawel. “We’re showing them how a space that might look like it’s designed for 35 people can be used for 85.”
PROJECT: HED Detroit Office
LOCATION: Royal Oak, MI
ARCHITECT: HED
Size: 19,700 square feet
Completion: 2023
General Contractor: PCI Dailey
Lighting Design: Gasser Bush Associates
Certifications: Pursuing WELL
A shift from permanent project settings and assigned desking to virtual collaboration and flexible programming allowed HED to create more of a park-like work environment specifically designed for socializing. “People come together to enjoy what’s around them and be part of something,” Gawel says. “But in the new office staff and guests can still work on their own thing, observing the people around them without necessarily having to work elbow to elbow.”
“WE CREATED A SPACE INTENDED TO BRING YOU BACK TO NATURE.”
HED worked to find value in the new building’s existing constructs, opting not to throw away things that could be reconsidered or repurposed. “Why put more metal studs and drywall into the landfills?” They focused on what was salvageable and what could be reinvented, including carrying over furniture from the old office instead of selecting new styles.
While some decisions challenged the budget, the team was able to adjust to stay on target. Better lighting solutions and controls were implemented in-house by HED lighting designers, including fixtures that stabilize human circadian rhythms. “Gasser Bush Associates was an important partner in enabling us to manage the lighting on our own,” Gawel says.
The company also added VRF to the build-
ing’s existing HVAC system—a super-efficient upgraded mechanical system that provides cooling and heating to individual zones, allowing for better temperature control and user adjustability. This zoning capability helps optimize energy consumption and reduce waste. The company also concentrated on using low-VOC materials when possible and focused on AIA 2030, a set of standards and goals for reaching net zero emissions in the built environment.
“Wellness is powerful,” Gawel says, and it’s at every turn at the new office—from bike storage to acoustics to facilities for mothers. “It’s why we pursued WELL certification. It’s why we’re guiding our clients through sustainable projects, because it matters to us. We had an opportunity to lead by example, and we took it.” gb&d
Better lighting solutions and controls, combined with plentiful natural light, were implemented in-house by HED lighting designers, including fixtures that stabilize human circadian rhythms.
LEFT HED Detroit’s previous office setup was antiquated, and when employees were asked about the new design, technology was a must. “People expect everything to work when they come in,” Gawel says. “Staff wanted ease of use with a user-focused technology platform.”
Here’s how adaptable offices are coming to life.
WORDS BY EMMA LOEWE
Would you take a job without seeing the office?
When 1,000 workers in the US and UK were asked the question, half of them said they wouldn’t accept the offer, and roughly 36% admitted to declining jobs due to an unattractive office space—a testament to the importance of workplace design in recruiting and retention.
Once employees are in the door, research shows that a well-designed work environment can also help improve their performance and motivation and enhance their resilience and ability to cope with stress.
Over the last few decades office design has toggled between two extremes: the isolated cubicles of the ’80s and ’90s and the open-plan offices of the turn of the century. These days designers and employers are largely in agreement that the best spaces for worker well-being land somewhere in the middle.
“Covid accelerated the conversations around giving people the freedom to work in different ways,” says James Woolum of ZGF Architects. In a post-pandemic era he’s noticed many employees crave a return to the office—but they want it to happen on their own terms.
This is where flexible design comes in. By creating adaptable offices employers can appeal to top talent and foster a more collaborative, motivating work environment.
But what does flexible office design actually look like in 2024? Here are a few ways to design adaptive spaces that will grow with employees for years to come.
Create Areas to Be Alone, Together, or “Alone Together”
Today’s office workers are increasingly looking for a mix of public areas to chat with coworkers and private spaces to do focused work.
“We need to design space for people who are less extroverted and get work done better in a quiet environment, or those who are just not having a great day and need a little bit of space,” Woolum says.
One way to do this is by using seating arrangements, wall treatments, and architectural panels to send subtle clues about how different spaces are best utilized. Tucking a tempting chair behind a movable panel can signal focused solo work, for example, while placing a table in an open space within 10 feet of another table will invite more buzzy and collaborative uses.
“You could put the same table in a smaller space that has darker walls and some acoustical treatment on the walls to send the signal: ‘This is a room you can be in with a group, but you’re probably going to keep it down,’” Woolum says. He predicts that cozy, communal spaces like these will be in higher demand as Gen Z trickles into the workforce.
“There’s a lot of data to show that people who were in school during the pandemic are now conditioned to want to communicate with others in a non-verbal way,” he says, increasing the need for “alone together” spaces that let people feel connected to others without saying a word.
Acoustic treatments can help carve out mi-
“COVID ACCELERATED THE CONVERSATIONS AROUND GIVING PEOPLE
FREEDOM TO WORK IN DIFFERENT WAYS.”
cro-environments in flexible offices—and they’re especially useful as employees continue to return to the workplace.
Dan Brandt, the vice president of product and marketing at MDC Interior Solutions, says trends over the past decade have introduced more hard surfaces into many office buildings. These surfaces are easy to clean and disinfect, but they reflect sound and can contribute to a noisy, distracting environment that negatively impacts employee well-being.
Brandt has seen an uptick in demand for MDC’s core product, Zintra Acoustic Panels, to buffer these sounds. The 100% recycled polyester panels are configured into dimensional designs that makes them easy to install around existing fixtures like lighting or HVAC systems.
The panels can be fabricated into an unlimited array of cuts, colors, and forms that can either blend in or stand out depending on the needs of the space. Brandt recalls one project in the Kickernick Building, a commercial workspace in downtown Minneapolis, where the client was looking to place a conference table in a bustling open-floorplan lobby.
To balance the need for noise abatement and the desire for an attractive showpiece in a highly trafficked area, MDC partnered with a local design firm, Studio BV, to create a custom design that cut lightly colored acoustic panels into five slightly different shapes and layered them into a massive 13foot tall display.
“As you move left to right, the context of the space and the shadowing moves with you. It becomes a public art piece,” he says—and a functional one at that. Every additional angle absorbs sound waves a bit differently, so this piece provides impressive noise mitigation.
Brandt finds that employees tend to naturally flock to softer, more muted soundscapes like the ones these panels create, even if they don’t consciously realize it. “That’s always a win when you don’t have to explain to anybody what the benefit is,” he says.
The office of the future won’t just allow for more flexible work; it will inspire a more flexible life, says Woolum. He predicts that the most successful offices will be those that offer amenities that let employees exercise, socialize, and play on the job. This could look like having fewer dedicated desks and private offices and filling the newfound open space with workout gear, kitchen equipment, or games.
“In all the major office markets the real estate that is being leased is generally in buildings that have amenities. I think this speaks to people’s growing desire to have things close,” he says. This, too, could be a response to the work-from-home era when we grew accustomed to using one space for a variety of purposes.
Offices are now poised to catch up to other categories such as health care buildings, which already bring everything a visitor needs (blood pressure machines, scales, vaccines, etc.) directly to them. “We’ve had interesting discussions with a range of clients about how we can think about that model for [non-health care settings],” Woolum says. “I’ll be curious to see how that begins to factor more into the workplace.”
Flexible design is also timeless design. As styles change and trends come and go, it remains relevant and modern. Woolum and Brandt both say nature-inspired, biophilic touches can help shape transcendent spaces like these.
When designing an office Woolum often considers natural light first, using it to help dictate the placement of desks and communal workspaces. “There’s a lot of peer-reviewed scientific data that people who have access to natural daylight and views are more productive,” he says. “I always start there: ‘How can I get the most people as close to natural light and views as possible?’”
He’ll also choose paint colors and finishes that feel aligned with the world outside the office window, gravitating toward
woods and other materials that evoke natural landscapes.
ZGF’s May Lee State Office Complex—the largest all-electric, zero-carbon workplace campus in the US—is a prime example of timeless biophilic design. The thousands of California state workers who pass through the building are greeted by colors, patterns, and textures that evoke the neighboring Sacramento River Basin.
Across the country in Arlington, Virginia, ZGF’s design for Amazon HQ2 Metropolitan Park reflects a very different type of landscape. The 2.1 million-square-foot project (the largest LEED Platinum new construction building in the world when it was completed in 2023) contains 3,000 operable windows across two buildings. Virginian humidity can be stifling, but Woolum says having operable windows ticks multiple flexibility and sustainability boxes: It gives workers a sense of control over their space, brings nature into the design, and allows for energy savings.
left, MDC Interior Solutions’ Zintra custom pattern panels are seen on a sliding track. The pattern matches the historic vent design throughout the building at this Zizzo Group in Milwaukee.
RIGHT ZGF designed the May Lee State Office Complex to include a rich amenities program curated to occupants’ needs, as well as a lush landscaping program.
It’s important to acknowledge that office design touches that work well for one group of people can be totally ill-suited for another.
As journalist Emily Anthes writes in her book, The Great Indoors: The Surprising Science of How Buildings Shape Our Behavior, Health, and Happiness, “Many features of the built environment can pose challenges for people with certain cognitive disabilities, mental illnesses, and neurological conditions. For instance, people with post-traumatic stress disorder (PTSD) can become anxious when they’re forced to navigate narrow passageways or blind corners, while autism, epilepsy, migraines, and traumatic brain injuries can all make people exquisitely sensitive to certain sensory stimuli like light and sound.”
This makes it essential to consult office workers during the design process—and to do so equitably to address their specific needs. In this way employers would be wise to treat their building design more like a business: Only as successful as the people it brings to the table. gb&d
Acoustics are no longer an afterthought, as design teams seek sound solutions that are functional, flexible, and environmentally friendly.
WORDS BY RACHEL COON
We’ve all been there—in the office on an important call, desperately trying to drown out the workspace cacophony so we can hear the person on the other end.
“People don’t necessarily understand the physics behind acoustics because you can’t see them, but everyone knows bad acoustics,” says Rob Cooke, managing director of Primacoustic, a top acoustic solutions company for more than 20 years.
While acoustics have not always been at the forefront of design conversations, modern spaces are considering sound in innovative ways.
Today expectations are high—acoustic solutions must perform well, fit modern aesthetics, and ideally be environmentally friendly. Wood has long been a popular material for its warmth and apparent absorptive properties, but alternatives like PET (polyethylene terephthalate) plastic have proven to be the better option.
That’s what Primacoustic realized when it tested PET and discovered it worked quite well acoustically. The company created EcoScapes—a collection of wall panels, ceiling clouds, and slat walls made from PET plastic that comes from recycled water and soda bottles. EcoScapes panels don’t compromise on sound absorption performance and are also highly customizable; they can be cut into nearly any shape and size and printed with colors, prints, patterns, and logos with custom manufacturing in Colorado.
“PET lends itself very nicely to print—any pattern that can be done in nature can be duplicated,” Cooke says, calling to mind the most popular natural elements being incorporated in modern designs—marble, granite, concrete, and of course, wood.
Brands are striving to meet market needs with acoustic products using recycled con-
tent and bio-based materials, low-carbon options, recycled PET panels, wood pulp panels, paper pulp panels, and mycelium-based acoustic panels. “We’re seeing a trend in terms of acoustics and how far you can push innovation, and sustainability is a huge element. These brands are helping designers achieve certain sustainability criteria,” says Emanuela Caffrey, a senior interior designer at Perkins&Will in Dublin.
Caffrey says there’s been a lot of change in workplace design, and it’s all very exciting. “The pandemic reiterated how we cannot get too comfortable, that we have to constantly develop and evolve our solutions and embrace the fact that the nature of work is forever changing. There will never be a onesize-fits-all solution.”
Whether retrofitting existing buildings, renovating expanding businesses, or working on new projects, sound experts have had to pay attention to marketplace trends and user expectations, too.
But while more and more companies seek social, collaborative, and open office designs, many of those designs also boast aesthetic finishes in granite, marble, concrete, and glass. While beautiful, these layouts often create noise. And all those shiny modern finishes exacerbate—rather than absorb—sound reverberations.
“Open plan workspaces offer so many benefits, not just for collaboration, but for people’s well-being, for driving innovation and productivity, for driving work culture and social interactions—those water cooler moments,” Caffrey says. But issues like noise and distractions, privacy, and sound transmission continue to be common concerns.
Taking sound into consideration as a measure of building wellness is a recent revelation—acoustics weren’t even included in WELL’s original core standards. But the people spoke. Employees couldn’t stand being in workspaces because of the noise. People were realizing the effect noise has— on chronic stress, on productivity, on end users’ overall mental health and well-being. Companies were suddenly competing for employees based on how comfortable the workspace was.
“Sound is important—and acoustics always matter,” Cooke says. “It’s our mission to educate the experts charged with designing spaces so that they understand sound and can make sure it’s considered in every design. All we need is a few people to understand acoustics for everyone to benefit—so nobody has to put up with bad acoustics.”
It’s a highly complex process to incorporate proper acoustic solutions into building designs when every wall, ceiling, piece of furniture, fixture, and even services can be taken into consideration for sound treatment.
“Our key consideration is understanding our clients—the various end user groups and how they’ll work differently from each other—then designing holistic spaces that
ABOVE Perkins&Will designed a global FinTech headquarters in Dublin to include an array of acoustic products, including wall panels for sound absorption and aesthetics.
support the various activities. We take an activity-based planning approach,” Caffrey says of Perkins&Will.
Caffrey and her team found themselves drawing on an array of acoustic products and solutions in their recent completion of a global FinTech headquarters in Dublin. Within this open office project, a number of acoustic wall panels achieve sound absorption and serve as an aesthetic feature within the space, creating visual interest with pops of color and pattern. Semi-open slatted screens, rather than fully enclosed dividing partitions or walls, created a break in the open space to interrupt reverberation and sound transmission.
“Even though it may not seem like an acoustic solution at first glance, the more surfaces you have breaking up a wide, open plan space, the better it is for breaking up sound. It’s also a visual block to create a sense of privacy and serves as an aesthetic focal point as well,” Caffrey says.
Perkins&Will designed support spaces in such a way that they were broken up by cellular spaces that reduced the extent of sound travel and each of those blocks had private offices, phone booths, and quiet rooms where people could take calls or focus uninterrupted. Locally made acoustic rafts above desk banks and acoustic panels and ceiling baffles were utilized to address absorption.
In the canteen, glazed folding walls allowed for multi-function utilization, connecting wider social spaces or allowing an area to be enclosed to create acoustic privacy.
Acoustic pendants in certain open collaboration zones were yet another feature that added a focal point, provided lighting, and helped absorb sound.
“An acoustic finish can have so many functions and different elements. It can address privacy, it can bring biophilia and sustainability, it can address wellness. Some of the products and innovations we’re seeing address that multi-need very well,” Caffrey says. gb&d
“SOUND IS IMPORTANT—AND ACOUSTICS ALWAYS MATTER. IT’S OUR MISSION TO EDUCATE THE EXPERTS CHARGED WITH DESIGNING SPACES SO THAT THEY UNDERSTAND SOUND AND CAN MAKE SURE IT’S CONSIDERED IN EVERY DESIGN.”
FROM THE FIRST LEVEL LOOKING UP, THE OPEN DESIGN AND SLEEK MODERN FINISHES OF THE BUILDING FOSTER A DYNAMIC ATMOSPHERE, ENCOURAGING COLLABORATION AND CONNECTIVITY ACROSS DEPARTMENTS IN THIS REIMAGINED SPACE.
Studio Gang’s adaptive reuse of the Gray Design Building at UK
WORDS BY BRITTANY HOWARD
PHOTOS BY TOM HARRIS
As you approach the Gray Design Building at the University of Kentucky, the boundary between interior and exterior begins to blur. The 20th century tobacco warehouse—now a cutting-edge academic facility—breathes with the landscape. Expansive windows reflect the sky while weathered brick tells of the building’s past.
Students move between indoor studios and outdoor workspaces, embodying the seamless transition Juliane Wolf, design principal and partner at Studio Gang, envisioned for this adaptive reuse project. “We were able to reuse most of the existing building’s structural components, which greatly reduced the project’s embodied carbon,” Wolf says, referring to the structure, foundation, skin, and roof.
Limiting the need for new materials, the team focused on upgrading the envelope with a new roof membrane, interior insulation, tuck-pointed brick, and operable windows for improved ventilation.
Sustainability also extends beyond the building’s shell. A geothermal well system in the adjacent parking lot provides 100% of the heating and cooling. The southwest-facing facade and main entry feature a new, large canopy and native trees, creating shade and
a comfortable microclimate. Transparent panels allow daylight to filter through, while carefully designed gaps promote air circulation. Wolf says it’s all part of a design approach to reinvent the building in a contemporary way while maintaining a relationship with the historic structure.
This indoor-outdoor connection is also realized in the building’s layout. Wolf’s team made the bold decision to place the workshop adjacent to the main entry—an unusual choice for a design school. “Typically the shops are tucked away in the back of the basement,” she says. “But here it’s right in the front.” This placement allows for easy movement of large prototypes or pieces between the indoor workshop and outdoor spaces, facilitating a more fluid creative process.
Inside the Gray Design Building, visitors are transported from a world of industrial past to a vibrant center of architectural innovation. The space that once housed heavy, wet tobacco has been transformed into a place of creative inspiration.
At the heart of this transformation lies a central staircase, strategically placed to create what Wolf calls “a hub of energy right in the middle of the building.” This isn’t just a
The revitalized facade of the Gray Design Building—where historic brick meets modern glass—exemplifies the seamless blend of past and future in Studio Gang’s adaptive reuse project.
Preserved timber columns and reinterpreted steel supports showcase the thoughtful dialogue between old and new, central to the building’s design philosophy.
SITE DIAGRAM
PROJECT: Gray Design Building
DESIGN ARCHITECT: Studio Gang
LOCATION: Lexington, KY
Completion: September 2024
Size: 132,000 square feet
Architect of Record: K Norman Berry Associates Architects
Structural Engineer: Brown + Kubican
General Contractor: Turner Construction
MEP/FP Engineer, AV/IT & Security: CMTA
Landscape Architect & Civil Engineer: CARMAN
Lighting Designer: PritchardPeck Lighting
Quantity Surveyor: Robert Pass & Associates
3D Laser Scanning: Ayoroa Simmons
Surveyor: Endris Engineering
Acoustics Consultant: Harvey Marshall Berling Associates
means of vertical circulation; it’s the pulsing core of the entire structure.
Surrounding the staircase are carefully planned openings in the floors, creating a visual connectivity that spans two levels. This design choice allows for views across different floors, fostering a sense of community and shared purpose among students and faculty.
This center of activity is juxtaposed with quieter faculty spaces at both ends of the building, creating a balanced ecosystem that caters to different needs and work styles. The result is a space that’s alive with the energy of learning and creation.
The building’s transformation from a tobacco warehouse to an educational space is more than just functional; it’s deeply symbolic. “The opportunity to take something with an unhealthy association and transform it into a positive and optimistic space for future makers was an exciting aspect of this project,” Wolf says. This builds on Studio Gang’s ongoing work to reimagine older structures—a practice that’s as much about sustainability as it is about design innovation.
The building’s history presented unique challenges and opportunities. The lower level, designed to support wet tobacco’s immense weight, featured tightly spaced timber columns. In contrast the top level was light and open. Wolf’s team embraced these constraints, using them to create a
In the fabrication shop students bring their ideas to life surrounded by the historic and modern elements of the Gray Design Building—a space that not only inspires creativity but also prepares future architects for the challenges of sustainable design.
dialogue between old and new.
This dialogue is most evident in the central staircase columns. “At the top of the timber columns horizontal members support and spread the load of the truss,” Wolf says. “We wanted to highlight this central gathering space of the building so we made a similar detail out of steel for the new main staircase, creating that dialogue between the old and new where it’s not replicated, it’s just reinterpreted.”
Details like this extend to every aspect of the building, preserving and adapting existing materials wherever possible.
The Gray Design Building stands as a testament to the power of adaptive reuse in creating sustainable, inspiring learning spaces. It demonstrates how thoughtful design can transform not just a building’s physical structure, but its essence—from a space of production to one of innovation, from a relic of the past to a beacon for the future of sustainable architecture.
A transformation from tobacco warehouse to design school represents the power of architecture to change narratives, create positive spaces, and shape a sustainable future. For the architects of tomorrow studying within its walls, the Gray Design Building is not just a place of learning—it’s a constant source of inspiration and a tangible example of the principles they aspire to embody in their own future works. g
Color and science
saturate a storageturned-hospitality space designed by ZGF Architects for the San Diego-based genomic research giant Illumina.
ZGF and Illumina worked closely together throughout the build.
“The leadership team was figuring out in real time how they were going to use and activate the space. Ultimately this is not about people coming in
to work every day; it’s about bringing in outside partners and visitors. You need to think about how to program and activate beyond the architecture,” says James Woolum, partner at ZGF.
When biotech company Illumina, which makes advanced gene sequencing machines, sought to transform an awkward storage building bordering the main quad of its campus in San Diego, ZGF Architects were eager to design a high-tech hospitality space that would welcome visitors, present products, and build partnerships.
The Illumina Executive Briefing Center was imagined as a touchpoint for the company, embodying the Illumina mission (“to improve human health by unlocking the power of the genome”) with tangible branded elements, clever programming, and guaranteed comfort for occupants.
“I think this kind of project sets a really good example for how you think about a brick-and-mortar experience for a brand or a concept that’s pretty elusive,” says James Woolum, partner at ZGF. “It offers a journey of learning, connecting, innovating. It’s about celebrating what the people at Illumina are doing.”
ZGF won the design competition with a concept that preserved as much of the existing building as possible, linking four highly programmed stories with a helical spiral staircase the recalls the structure of DNA. In the final build the stairway links the first three floors for a seamless experience.
A focal point of the building, the staircase draws people into the space with color and intrigue in the form of an art installation by Ray King. The installation, “IllumaLens,” covers the wall of the stairway atrium with more than 5,000 pieces of dichroic glass that shift in color throughout the day. “It was literally inspired by the flow cells inside Illumina’s gene sequencing machines,” Woolum says, describing the work as a physical amplification of the mind-blowing scientific work at Illumina.
Beyond the staircase on the first floor is an audio-visual exhibition space where curving screens showcase the capabilities of Illumina technology. Upstairs, the second floor encourages gathering with a dining room, an expansive events terrace, a flex theater space, and lounge seating. The meeting spaces get increasingly intimate on the top floors. The third floor offers cafes, conference rooms, and meeting spaces while the fourth floor executive suite includes collaboration spaces, staff workstations, and a boardroom.
To continue the spatial flow introduced by the spiral staircase, a ceiling treatment of triangulating, layered wood slats builds the dialogue between the floors. The design creates an illusion of expansiveness within the narrow plan. “We could have just put one ceiling in and let it go all the way to the edges, but we subdivided it and used
PROJECT: Illumina Executive
Briefing Center
ARCHITECT: ZGF
LOCATION: San Diego
Completion: November 2023
Size: 30,000 square feet
MEP: Infrastructure Factor
Contractor: BNBuilders
Interior Designer: ZGF
Environmental Graphics: ZGF
Landscape Architect: The Office of James Burnett
Illumina’s primary brand color is orange—“a little goes a long way,” Woolum says. “We decided to think more about the spectrum of color in their brand guidelines, the depth of what they do.” Tangerine pops appear subtly in furnishings and finishes throughout.
multiple materials. That’s a result of letting our minds completely wander in the competition design process,” Woolum says.
Transforming the existing site required a rational kind of innovation. The building was once an undefinable storage space wedged between Illumina’s main quad and a parking garage. “It was almost like the building was built specifically to be an edge for the quad; it never had a program,” Woolum says. Determining the building plan while preserving the original structure and as much of its embodied energy as possible was the first—and biggest—challenge.
“Our approach is always to ask: How do you do the absolute minimum to the existing architecture to achieve a new result? How do you save the embodied carbon and everything that’s already gone into the building that we received?” Woolum says.
The ZGF team focused on useful adaptive reuse solutions that preserve the building’s place within the larger campus while adding function, beauty, and cohesiveness to its interior. For example, on the second floor an existing curtain wall was opened up and outfitted with floor-to-ceiling accordion doors. “It spills out onto this new events terrace overlooking the quad. It’s a perfect way to take advantage of the environment,” Woolum says.
The biggest structural changes came in the form of safety measures. To transform storage space to hospitality space, egress was a particular consideration. With assembly spaces on the second floor, the building needed a second stairway.
“Every material and every piece of furniture was reviewed by the client because they wanted it to be a place that was comfortable and welcoming to people,” Woolum says.
Illumina’s San Diego campus integrates beautifully with the landscape, and employees spend a lot of time in the quad enjoying Southern
California’s famously nice weather. Integrating the outdoor and indoor space was crucial to the Executive Briefing Center’s success.
From the beginning ZGF and Illumina wanted an immersive exhibition space with big screens. “But we didn’t know what the content would be. As the storytelling aspects evolved we had many “aha” moments: Here’s where we’re right on track, and here’s where we need to pivot the architecture in order to get the experience that we want,” Woolum says. ZGF worked with design agency Hyperquake to realize the exhibition space.
Other solutions are a bit sneakier. The executive boardroom on the top floor offers space to meet and entertain guests with a beautiful view and ample seating thanks to a banquette seat on one wall. “It’s perfect because it gives Illumina five, six, or seven more places for people to sit. It looks beautiful, and you’d never know, but it’s concealing structural fasteners to the curtain wall,” Woolum says.
The center achieves a 25% energy savings and 15% reduction in light power density compared to the baseline for similar hospitality spaces. “We’re signatories to The 2030 Challenge and are tracking energy on every
project,” Woolum says. The reductions are largely thanks to the installation of efficient fixtures in Illumina’s lighting-centric, hightech space—which still feels airy, welcoming, and comfortable for occupants.
“At the end of the day you can make the most wonderful, super high-performance building, but if people hate being there, is it really sustainable? One of the great things about this space is that it creates enriching human experiences,” Woolum says. Occupants are always close to refreshments and accessible bathrooms, and the narrow floor plate means natural light reaches every corner. The integration of art, color, and textures also offers a sense of beauty and humanity in the space. g
HGA uses playful shapes and advanced technology to create an energyefficient early learning center where kids thrive.
The Blake School Early Learning Center provides students with strong indooroutdoor connections and natural light.
Not all clients are enthusiastic about every effort to make a project earth-friendly. But when HGA was asked to design a new early learning center at the Blake School in the Minneapolis suburb of Hopkins, it was encouraged to go beyond designing an efficient educational building to demonstrate the client’s commitment to climate and conservation.
“A lot of people were excited about the project as an opportunity to demonstrate Blake’s values,” says Nat Madson, design principal at HGA. “It was important that the building make strong connections to nature for the earliest learners and that the building be a sort of teaching tool.”
HGA engaged with client and user groups to figure out how the private college preparatory school wanted to present its brand in its second 100 years. Following
the Reggio Emilia teaching philosophy, the Blake School encourages children to learn through observation and exploration as part of a supportive community.
“What’s so cool about Reggio is the spatial implications of these ideas,” Madson says. “This was a huge opportunity to explore and develop that.”
The ELC’s compact site down the hill from the original school building didn’t offer the room needed for a single-level structure, and HGA wanted to prevent the community disconnects that might occur in a more traditional two-story structure. “By nestling the building into the hillside, we were able to make a kind of split-level,” Madson says. Using shapes suggested by Froebel, a venerable children’s building-block set, HGA de-
PROJECT: Blake School Early Learning Center
ARCHITECT & INTERIOR DESIGNER: HGA
LOCATION: Hopkins, MN
Completion: 2023
Size: 32,000 square feet
Contractor: Mortenson
signed a building that looks like a collection of boxes. “This kind of simple assembly was a driving idea throughout the project,” Madson says. “You zoom out and see five or six blocks nested together.”
Observing Reggio’s mandate to create community, the building is organized around a common indoor/outdoor plaza or town square where multiple activities can take place. The school’s cafeteria and library overlap, and classrooms orbit the common spaces. “As an architect that’s exciting because you don’t have to think in a compartmentalized way,” Madson says.
HGA strives to lower embodied and operational carbon on all projects and is a signatory on multiple materials pledges. Using Revit’s Tally application to assess global warming potential, the firm compared several construction options.
HGA had recently completed a mass timber project in Maine and was hoping to repeat its success with the Blake Early Learning
Center using glulam columns, glulam beams, and cross-laminated timber decking. Decking costs proved prohibitive, however, and the firm chose a hybrid strategy: glulam frame and beams with steel composite decking. The structural decision influenced the building’s appearance inside and out. Leaving the glulam columns and beams exposed, HGA was able to eliminate the carbon emissions associated with the wraps and wallboards used to hide a typical steelframed structure, achieving an embodied carbon savings of approximately 500,000 kilograms of carbon dioxide.
Glulam timbers were sourced from the Eastern US and Canada, supporting regional industry while further limiting the carbon needed for transport. Glulam beams also cut through the facade, tying interior and exterior together.
Stakeholders were thrilled with the look. “The decision to go with wood and expose it was about doing a lower-carbon structure,” Madson says. “But the client and user groups were excited about the idea of the
structure being expressed and exposed. You can see how the building is assembled, and it was a real driving idea.”
The lowest level of the building (Field) houses a pre-K classroom and the building commons. About nine feet up and connected by a staircase and slide is the kindergarten (Forest) level; four feet further is the first grade (Treetop) level. Classrooms open to the south, east, and west toward Blake ELC’s certified teaching forest, and all offer direct outdoor access.
While building mechanicals are mostly hidden, the building features three light monitors that help daylight the school commons, in line with Reggio guidance that young learners experience different kinds of light. Each is oriented to catch light at different times of day and direct it to the interior, more like clerestory windows than skylights.
Glulam beams extend beyond the façade to form canopies that dapple the natural light in every classroom. “It creates this kind of threshold condition between the outside and inside,” Madson says. “Reggio calls those filter spaces.”
The site has an actual filter space for rainwater. Basins planted with hardy grasses retain 90% of all rainfall with no discharge to the Minnehaha Creek watershed, and a “Stormwater Scramble” invites children to learn about groundwater and the planet through play. “One of the things we heard early and often was that kids love playing with water,” Madson says.
LEED Gold certification helped frame the project’s environmental goals. Internal modeling helped determine how to lower energy usage long before breaking ground, and third-party modeling helped achieve targeted goals.
“Ultimately our predicted EU was right in line with what we were trying to
achieve,” says Ben Pielhop, senior mechanical engineer at HGA.
A geothermal field under the parking lot and a variable refrigerant flow system contribute to a 41% reduction in energy costs compared to the ASHRAE 90.1 2016 baseline. Radiant hydronic floors heat the building, providing warmth and comfort for children.
“We’re using the earth as a heat sink to naturally heat and cool the building,” Madson says. “The simplest way to describe it is that we run pipes underneath the parking lot, and every so often we run a pipe hundreds of feet down in the earth.”
Completed in fall 2023, Blake ELC became the first fossil fuel-free, non-collegiate education building in Minnesota. Natural gas is relatively inexpensive in the Upper Midwest, Pielhop notes, so going all-electric wasn’t an obvious choice. He says having a more renewable grid is going to help the sustainability effort in the long term, as being connected to a cleaner grid gets them closer to decarbonization.
“Each year we’re finding new ways we can push the limits of sustainability through early analysis and new technology,” Pielhop says. g
Wheeler Kearns Architects designed Sawyer Retreat to nestle into the lakeside ravine like a treehouse and serve its occupants for countless years of outdoor adventure.
The architects removed invasive species from the site and replaced them with native plants to enhance the local dune landscape and eliminate irrigation needs.
“We didn’t want to turn our back to the neighbors, but at the same time this is an entry point, which works from an architectural idea of compression. Once you pass through the threshold you see the views; from the backside we maximized transparency, but it is very private because of the way the house is sited,” says Wheeler Kearns Project Architect Michael Kendall.
Just off the shores of Lake Michigan, a modern holiday home seems to float in the trees above lakeside sand dunes. A swing dangles invitingly over the expansive, boardwalk-style deck and wide windows offer a peek inside, where the lake’s blues, greens, and sandy shades are reflected in the home’s finishes. Designed by Wheeler Kearns Architects, Sawyer Retreat mirrors the natural landscape that nestles around it, offering a cozy home base for all manner of outdoor adventure.
“The clients wanted something that captures the essence of the site—two beautiful acres at the end of a narrow lane. They didn’t want the house to compete with its surroundings,” says Wheeler Kearns Project Architect Michael Kendall.
In the Trees
The program was strict: five bedrooms, three baths, and a big living space with views to-
ward the lake. The project’s location on a steep ravine was at once a constraint and inspiration as the design came about. There was little leeway as far as where the bulk of the house could be situated thanks to structural limitations and zoning restrictions.
The Wheeler Kearns team seized the idea of making the retreat feel truly a part of its wooded surroundings, like a treehouse consisting of two rectangular masses. “As the site sloped away we had an opportunity to build something fairly modest at the front that then could open up and sort of float out into the ravine,” Kendall says. From the unassuming front entrance reached via footbridge, the home expands generously to the back of the property for large living spaces and sweeping views.
Achieving the treehouse effect was no small feat. The architects knew they would use concrete to anchor to the site and manage the practical aspects of building, allow-
ing them to build up into the trees. However, they soon found the existing sand of the dune below was too light and powdery to bear the load of the house. The architects replaced some of this beachy sand with a coarser grain, increased the width of the foundations to boost the bearing capacity, and used concrete piles to support the deck.
“Luckily that didn’t necessarily change the footprint or the end design. We had to respect the landscape. Dunes are ever moving and undulating. We were thinking of this house as a light element that sits gracefully on the site,” Kendall says. The airy design stands in contrast to many of its more ostentatious neighbors. It’s nothing like the house the clients have in the suburbs; it’s a true place of respite.
Approaching the retreat visitors first catch a glimpse of the entry bridge, a design solution
that allowed the architects to start building from the highest point on the site. “It solves a practical issue, but then it further adds to that treehouse effect and the lightness of the building hovering above the ground plane,” Kendall says.
Beyond the treehouse-like plan, the architects utilized specific materials to enrich the optical illusion of the house hovering in the trees. Charred shou sugi ban siding allows the home to recede into its context like a natural part of the landscape. Inside, the material palette mirrors Lake Michigan with blues, greens, and warm sandy tones.
Such aesthetic references meet practicality and durability. Concrete floors on the main level are ready for dirty hiking gear and sandy feet. “All of the materials were geared around the idea that they are from nature, require minimal maintenance, and can stand the test of time. We’re hoping that this is a 100-years-plus home,” Kendall says. It’s the
perfect home base to return to for hot chocolate after a paddle on the lake.
The shores of Lake Michigan are, famously, very cold in winter, and so is the lakeside community of Sawyer, Michigan. It was especially important for Kendall and his team to ensure a tight building envelope for occupant comfort and energy efficiency.
The concrete floors on both levels of the house have radiant heat to provide optimal comfort as the cold winter winds blow off Lake Michigan. The homeowners wanted a fireplace to gather around, so Kendall and the team convinced them to get a high-performing, closed wood stove, which produces a lot of heat without losing much to airflow, rather than a low-performing fireplace.
“We went above and beyond as far as detailing, using the latest and greatest products,” Kendall says. Triple-paned Marvin
LED lighting is used throughout the home, and all exterior lights comply with DarkSky requirements. An electric charger allows the homeowners to juice up their EV for the commute to and from their primary residence.
The multipurpose building was engineered to survive catastrophic events like storms and earthquakes.
SITE MAP
PROJECT: Sawyer Retreat
ARCHITECT: Wheeler Kearns Architects
LOCATION: Sawyer, MI
Completion: May 2024
Size: 3,150 square feet
Construction Manager: Scott Christopher Homes
Structural Engineer: Enspect Engineering Consultants
Landscape Architect: McKay Landscape Architects
Interior Designer: Kathryn Murphy Interiors
windows, wood frames, and spray-foam insulation on the walls and ceiling all help the thermal performance and, by extension, reduce energy consumption on the property.
“In that area the electric grid is somewhat reliable but not great. We didn’t want to use a generator, so why not try solar with a battery backup system?” Kendall says. The team installed 16 LG Electronics solar panels on the roof, and two Enphase Encharge 10 batteries occupy the basement. Since moving in the homeowners have found a rhythm using the batteries to run the home at night and allowing them to recharge during the day.
Before construction even started the homeowner proposed a rope swing off the back deck as a playful place to relax and take in the lakeshore and dunes. They had to wait more than two years to enjoy it, as labor shortages during and post-Covid slowed construction drastically.
But as the home’s design came together, zoning and massing questions were resolved, the treehouse idea took shape, and the architects extended the boardwalk-style deck, creating the perfect swinging spot. Now that the house is fully, finally complete, the swing has become a favorite place to appreciate the dunes—though with the home’s expansive windows and ample living space, it’s got plenty of competition. g
The bucolic England landscape inspired this minimalistic home on a historic estate.
For MailenDesign and Peter Bradford Architects, a residential project in Kent, England was an opportunity to collaborate with inspired, innovative, site-specific design. When their clients purchased the verdant two-acre plot they were eager to move from their central London townhouse to a place where they could reconnect with nature and host family and friends. Their vision was an unimposing, low-energy home that would not only nod to the local agricultural vernacular but be a peaceful retreat with cinematic views. They had a clear aesthetic in mind, presenting the design team with a scrapbook filled with Japanese minimalist and bespoke New Zealand beach homes in a simple palette of glass, steel, concrete, and wood.
While a design had already been approved by the planning commission, the condensed three-story footprint felt “too large, too bold,” says Ben Mailen, project director and founder at MailenDesign. “We weren’t trying to make the building look like a house. We wanted it to feel like a barn.” Instead they opted for a more conscious approach to the build, one that would seamlessly blend in with the neighboring barns, historic brick farmhouse, and black-clad Grade II-listed barn, all within an L-shaped form.
The new home replaced a series of black barns, likely once used for storage. “There’s something interesting in picking up a few elements from the site to respond to,” Mailen says. Rather than stand out, the project blends in with a pitched zinc roof, concealed rain gutter, and timber cladding with boards of varying depth for natural texture and warmth.
The true challenge was designing a house that engaged with its landscape while maintaining privacy and a feeling of intimacy, especially given its closeness to surrounding plots. “As you come down the lane it’s hard to tell that it’s a domestic house,” Mailen says.
Its front facade is intentionally closed off and gives brief glances of the airy interiors through full-height niches and a corridor. Once inside, the connection to the meadow beyond can be fully appreciated. In the
PROJECT: Weald House
ARCHITECTS: MailenDesign & Peter Bradford Architects
LOCATION: Staplehurst, Kent
Completion: December 2023
Size: 4,100 square feet
Structural Engineer: SD Structures
Contractor: Syntheto Construction
Interior Designer: MailenDesign
Fireplace Specifier: Victoria Stone
The low-lying L-shaped home blends into the site and includes passive ventilation, rainwater collection systems, and solar panels.
The main entrance leads to an open living area, including the kitchen and living room with black paneled walls and a concrete fireplace as well as an oak staircase and mezzanine. Three skylights reflect the canopy of trees overhead.
The lot’s sense of tranquility is amplified through carefully placed windows that frame the views.
south-facing kitchen an 82-foot glass wall allows for panoramic views of the countryside, while a paved terrace and deep eaves make for sheltered spaces that can be enjoyed year-round.
The architects arrived at the plan quickly, sketching layout options derived from previously approved plans and the location of the old barns, all which lead to the L-shaped form “creating a bookend corner to the rest of the site,” Mailen says.
Plentiful natural light reaches the main spaces, while other rooms yield perfectly framed views. “It was important to place picture windows to make it look like a beautiful British landscape photo,” Mailen says.
The palette was also key to making the home feel peaceful, with white walls, a matte black kitchen, and light gray porcelain tiles. “There’s something magical about the way the sun creates beams of light in the house, especially when it hits the roof light. It brings the space to life,” Mailen says. Strategically placed roof lights and full-height windows give way to an ever-changing dynamic between light and shadow.
Sustainability was a top priority for both the architects and the homeowners. The home is able to function largely off-grid, with 45 solar panels and two air source heat pumps, while the roofline, which extends over the front and rear sides of the home, helps regulate temperatures while also providing shade. Rainwater is captured through a subterranean collection system.
The location of the walls and windows themselves also served the home’s sustainability mission. “We didn’t want too much glazing,” Mailen says. “The closed and insulated elevations provide environmental protections and help regulate the home’s internal temperature.”
The project was also the chance to lean into one of the homeowner’s Sicilian roots and embrace his passion for cooking, gardening, and entertaining. He’s already planted an orchard with plans to produce his own wine and cider. “He’s a man of the land. Every time we visit he’s planting something new,” Mailen says. “He’s really in his element there.” g
Seattle’s commitment to sustainability goes beyond green buildings to a green economy.
WORDS BY KATE GRIFFITH
In a hyperpolarized era Seattle’s commitment to climate response continues to inspire the Emerald City—long a bastion of sustainability and environmental innovation. “Climate is one of those things that people across the city, across sectors, have a lot of civic engagement for,” says Jessyn Farrell, director of the Office of Sustainability & Environment (OSE) for the City of Seattle and a former state legislator for the North Seattle area. “Perhaps not unity, but definitely a sense of purpose.”
Ferrell’s work at OSE is to bring people and sectors together around big ideas. She leads a mayoral office built to drive climate strategy across city departments, coordinate innovation, pilot new programs, and scale those ideas to bigger city programs across transportation, energy, environment, and, of course, buildings sectors. But in Seattle the drive to combat climate change isn’t limited to technocratic innovation and the latest in emissions reduction; it’s about people.
“Our core services go deep into climate justice and how we can cater to people in our community bearing the brunt of the climate crisis,” Farrell says. “Within that we’re reducing emissions from buildings and transportation as fast as we can as well as supporting our communities by ensuring ample tree canopy and working on food systems.”
Buildings make up more than 30% of Seattle’s overall emissions. The passage of Seattle’s Building Emissions Performance Standard codifies the city’s steps toward carbon neutrality by requiring nonresidential and multi-family buildings, new and old, that are more than 20,000 square feet to reach net zero by 2050. The standard requires progressive decarbonization over five-year intervals starting in 2030 and addresses the tension between standardizing a predictable regulatory environment with the fact that every building is different by creating various compliance pathways based on the specifics of the building at hand. “We’ve allowed for lots of flexibility, but we’re also requiring more information from building owners,” Farrell says. The city estimates the policy will reduce Seattle’s emissions by 27% by 2050.
Even as Seattle drives policy standards to support green design in the cities’ largest buildings, Seattle is also on a path to decarbonize residential homes currently heated by oil by 2030. Next steps in residential decarbonization are to move beyond transitioning from oil heating to electrifying homes heated by natural gas (a heat source long considered a “bridge fuel” in the fight against climate change, and now on the chopping block as more information about fuel’s contribution to climate emissions comes to light).
The city’s work on its building emissions standard is a point of pride in Farrell’s work. “In the midst of a challenging downtown recovery post-pandemic, we got building owners into a space that they were willing to work with us,” she says. “There’s a civic culture in Seattle that really cares about climate change and climate issues, and being able to lean into that really matters.”
She credits success to her office staff’s deep listening skills, political leadership from the mayor’s office, and good old-fashioned negotiating skills and creativity. “When things are polarized, sometimes inventing a new way of thinking of things helps us all achieve our goals.”
get closer to net zero.
What’s next? Farrell wants to scale green building trends—use of materials like engineered wood products and low carbon cement as well as green roof requirements. “There’s a whole world of materials the city doesn’t do a bunch with yet, but private developers are working with them; the city needs to figure out how to support and expand those efforts.” One example has been Seattle’s Living Building Pilot program, which provides incentives to developers to reach for the Living Building Challenge, a green building certification program managed by the International Living Future Institute.
To support her office’s work Farrell looks in part to opportunities for state and federal funds. Washington’s leading Climate Commitment Act, which requires Washington cities and the state’s largest emitters to reduce climate pollution at the source or purchase allowances at auction reinvests funds into projects like those OSE is working on. Meanwhile the federal Inflation Reduction Act also provides funding to the city’s buildings program. “Building owners need help to do this. It’s expensive, challenging, and difficult. So we’re hustling to go after grants.”
Seattle’s biggest challenge, she says, will be getting a handle on transportation emissions, especially after the pandemic. “We’re just not commuting how we were before,” she says. “Our bus systems and trip reduction programs have to be realigned. Transportation electrification will be a place building owners can assist and be forward-thinking.” Part of that will be reimagining how the city interacts with its electrical grid. As Seattle electrifies buildings and transportation, new stressors will be placed on the grid. “Energy efficiency is a key part,” she says. “Making sure the grid can handle this massive transition is important. Car charging, delivery charging, zero emissions delivery writ large, bike delivery—what do we need to do in the built environment to make sure those things are easy to engage with?”
The future looks bright for Seattle, and more spacious, as the city embarks on not just a greening of its buildings and transportation sector, but also a reimagining and revitalization of its waterfront just a few years after an elevated double-decker highway that cut the city off from Elliott Bay was moved underground. “What is it about Seattle that creates a propensity for civic action? It’s in part this beautiful natural environment we live in,” Farrell says.
Standing on First Avenue looking west toward the water, you can sense a new quiet. View corridors that were formerly blocked are restored. Residents delight in new shoreline and places to connect with the water, while a sea wall rebuild project fosters habitat for the many creatures that live in Puget Sound. Amenities like access to Pike Place or to the state ferry system are that much closer. “It is transformative,” Farrell says. We are just starting to feel that.” g
The Fairmont Olympic Hotel in downtown Seattle is a gem in preservation.
The Fairmont Olympic Hotel in downtown Seattle was built in 1924.
The Ramones played there, dignitaries dined there, and locals came in for afternoon tea for 75 cents. The Fairmont Olympic Hotel in downtown Seattle celebrates 100 years in December 2024 with the $25 million renovation of its lobby, bar, restaurant, and meeting spaces under the vision of Spanish design studio Lázaro Rosa-Violán (LRV) with local architecture firm MG2, completed in 2021.
While we can neither confirm nor deny whether Rod Stewart ever swung from a chandelier, the excitement and elegance of the historic Fairmont property lives on while leaving no one out. And that’s on purpose. From the moment you enter the hotel lobby, you feel welcome. “The lobby is the heart and soul of the hotel,” says Sunny Joseph, general manager of the Fairmont Olympic Hotel in Seattle.
“The task given was how do we ensure we respect the past but look ahead to the future as well? How do we ensure whatever design we select is going to incorporate the best of both worlds? That we will talk to the audience of the past plus the audience and the guests of our future?”
The team wanted to move away from what was formerly a very traditional lobby, carpeted, with soft seating and little else. The design of the building itself is interesting, as the main floor is split into three levels, and it beckoned some of the world’s best designers with opportunity. The hotel team chose LRV to bring their vision to life. “They are known for renovating a lot of the castles in Europe, and they have done amazing renovation in some hotels as well,” Joseph says.
While in the past there was no real bar to speak of in the lobby (you could order a soda or a beer, but no real incentive to hang out, Joseph says), the new lobby is home to the Olympic Bar—a focal point and a hotbed of activity on any given night. “Our prime focus was: How can we do this renovation in a way where it becomes a place for the community to hang out? And that’s exactly what we did.”
During a visit in June the hotel was a hub for Pride Month, quite literally on the parade route with a flag flying high outside, while people of all ages buzzed about surrounding the Olympic Bar dressed in styles from the Roaring ’20s, cocktails in hand. “We try to activate as much as possible for everything,” Joseph says. “A lot of that energy is brought by our guests. People know they can come to our place without being judged and be who they are and have amazing times. Our mission is turning moments into special memories, and that’s what we strive to do every single day.”
Atop the Olympic Bar guests will find a sprawling, nautical-themed art piece inspired by the hotel’s original sailing ship logo. “In 1924 when the hotel was built you could see the water from it. There weren’t that many buildings,” Joseph says.
The design team darkened the wood throughout the lobby and made the meeting spaces and restaurant
PROJECT: Fairmont Olympic Hotel
DESIGN ARCHITECT: Lázaro Rosa-Violán
LOCATION: Seattle
Completion: 2024
Cost: $25 million
Local Architect: MG2
New restaurant, American brasserie
The George, is known for its standout lavish design and locally sourced dishes.
The color pink was popular in the 1920s, when the hotel opened. “The greens and the pinks really spoke to the original building,” says Sunny Joseph, general manager at the Fairmont Olympic Hotel.
around it ADA-compliant, while equipment throughout the hotel is now much more efficient, including energy-efficient LED lights.
Hidden behind a bookcase just off of the main lobby area, guests will find the new Founders Club—a dark, intimate, spirit drinker’s getaway that’s now one of the top bars in the country. The speakeasy bar seats 30 guests and is defined by deep, rich wood tones and the soft glow of polished brass. “It’s not a place where you are going to just have a beer. It’s an experience,” Joseph says.
Beyond the hotel’s main lobby space, a few steps up, the historic Georgian Room was transformed into The George and an outside entrance was added to connect more easily with the community. The new American brasserie is known for its lavish design and locally sourced dishes. The design incorporates the pinks and greens popular in the 1920s.
the Details
In the midst of renovation the team ordered new carpet for many of the staircases, but as the workers were
removing the old carpet they discovered the original flooring from 1924 laid by Spanish artists and Italian skills people. “We said forget the carpet. We are going to restore it,” Joseph says. “All the beautiful staircases have restored terrazzo from 1924.”
Wood details throughout the hotel are original, with darkened tones in some places. “The beautiful woodwork, the carvings, they are all original,” Joseph says.
The team also took the 300-pound crystal chandeliers from 1924 that were in pieces in storage in the basement and put them back together to hang in the foyer of the Spanish Ballroom.
The original white-cloth restaurant is still upscale but approachable, with comfortable pink and green seats or floral, leather booths and beautiful vintage lighting details. “Now it is a very lively restaurant with lots of light.” Walls are decorated with Puget Sound chart maps and a nod to the city’s nautical history.
“The George is just fantastic—the chandeliers, the art deco glasswork behind the bar. It is just amazing,” Joseph says. “I’m proud to show off the entire renovation. Not one area is left behind.” g
A central challenge for Graphite was identifying Amazon’s key ideas and ethos and finding ways to implement those ideas in the building: What does problem-solving and creativity mean to people, and how do you prompt people to be in that mental space?
Seattle is often touted as a city of neighborhoods. Each urban oasis has a character of its own, surrounding a small commercial core. From Capitol Hill to Queen Anne to Columbia City, these eclectic dens make up greater Seattle. Their personalities have been established for decades, though the growth of the city has heralded change within all of them. But in Seattle’s commercial downtown, Graphite Design Group has been quietly building a new neighborhood focused on tech, connection, and density, all for Amazon.
The Frontier Building, Graphite’s latest LEED Gold addition to Seattle’s Denny Triangle neighborhood and Amazon’s Regrade Campus, fully opened its doors to Amazon employees in summer 2023. The campus sits in a five-and-a-half city block mixed-use district that Graphite helped to master plan and where they also developed six other buildings.
“Halfway through the design of Nitro, another building on the campus, Amazon approached us about property across the street, which became Frontier,” says Graphite Founding Principal Peter Krech. “They told us ‘We
Fifteen years ago the area known as the Denny Regrade featured parking lots, two unoccupied hotels, and a smattering of underutilized spaces. Amazon partnered with Graphite and other firms to transform the neighborhood into a 24/7 community that would attract places to live, shop, eat, socialize, and find childcare.
PROJECT: Amazon Frontier
LOCATION: 2205 7th Ave
ARCHITECT: Graphite Design Group
Completion: 2023
Building Size: 540,000 square feet
Structural Engineer: Magnusson Klemencic Associates
Mechanical Engineer/Energy Design: WSP
Electrical Engineer: Stantec
Contractor: Sellen Construction
Interior Designer: Graphite Design Group
Civil Engineer: Coughlin Porter Lundeen
Landscape Architect: SiteWorkshop
Development Manager: The Seneca Group
Lighting: Oculus Light Studio
learned a lot from Graphite. Help us find what makes this block unique and special. How does it contribute to what we’ve created already in the surrounding neighborhood?’ What a dream challenge for the client to give to you.”
At the request of Amazon, Krech and his team put extensive effort into building community both around the building and within it. “It’s hard to build connections,” he says. “This is often why technology and other connective employers look to create horizontal buildings.”
Though the Frontier site constituted only half a city block, Krech’s team worked with Amazon to break down vertical barriers; moving people between floors was their biggest challenge. “It’s not intended to be a cube farm,” Krech says. “It’s meant to inspire the exploration Amazon wants from their workforce. They pride themselves on a creative environment and creative problem-solving, so our challenge was figuring out how their spaces can support that culture.”
An Urban Treehouse
Architects went all out on a single gesture—a staircase that connects all floors of the building and dubbed the Treehouse Stair. It’s now the building’s signature mark and sits just inside the facade of the building overlooking an open park and the surrounding community.
Tree houses and tree forts are spaces invented by children who take the notion of a home, room, or space and reinterpret them to suit their own imagination. They’re a collection of spaces, made of found objects and ad hoc materials, usually perched high in a tree. Creativity is the name of the game. “We quickly thought that this is a nice metaphor. How would we scale this up and manifest in a building that’s 3,000 feet tall?” Krech says.
In the case of the Frontier building, the centralized stair becomes the ladder to climb through and around the structure of the building. Throughout the building the steel structure is visible, allowing occupants to tune in naturally to how the space works. “Treehouses are in natural environments, and in the Pacific Northwest connection to the natural environment is part of who we are. Weaving those material choices into the building is part of the treehouse theme.”
Some conference rooms feel like sitting around a campfire; some mimic sitting under a tent; others mimic a walk in the woods thanks to lighting and ceiling treatment. Graphite worked closely with Amazon’s horticulture team to create living forest spaces throughout the building. Contractors and furniture suppliers sourced deadfall old growth trees to create benches resembling fallen logs. Meanwhile, misters come on sporadically, creating a small-scale replication of the famed Amazon Spheres— Jeff Bezos’ interpretation of a greenhouse—inside.
Seven outdoor terrace spaces, including a large one with a dog park on the 17th floor that offers unsurpassed views of the Olympic Mountains, are outfitted with hospitality furniture and soft seating to provide supplemental
meeting and collaborative spaces. All of this is connected by Frontier’s central staircase, an atypical arrangement spatially and one that required close coordination with city and fire officials to meet safety requirements and ensure a responsible design. “Those very subtle things combined create a very unique environment,” Krech says. “People tell us it’s one of the more desirable office spaces to return to as Amazon returns to the office.”
A building’s sustainability wins are largely conceived in the pre-planning stages, says Graphite’s Director of Sustainability Ryan DiRaimo. “Immediately choosing to be a mixed-use building or to be situated in a mixed-use
“TREEHOUSES ARE IN NATURAL ENVIRONMENTS, AND IN THE PACIFIC NORTHWEST CONNECTION TO THE NATURAL ENVIRONMENT IS PART OF WHO WE ARE.”
The project has seven outdoor terrace spaces, including a large one with a dog park on the 17th floor that offers views of the Olympic Mountains.
Graphite worked closely with Amazon’s horticulture team to develop curated planting areas featuring
neighborhood is the biggest sustainability choice you can make. If a green building needs a car to get to it, you’ve already lost all of your building’s gains with ancillary car emissions.”
Beyond the restaurants and the clothing stores, the surrounding Amazon Campus boasts retail, childcare, small grocers, art, and entertainment. “Our buildings have been inhabited by a wide range of retail uses. All the neighborhood is thriving, invested in the success of mixed use—economic success, environmental success, and social success.”
Frontier sits in both a mixed-use neighborhood as well as a walkable, bikeable neighborhood allowing occupants and neighbors to get their needs met within a short distance. The building is also LEED Gold, featuring highlights like concrete walls with recycled content, FSC-certified wood throughout, a high-performance envelope, and the ability to tap into a hot water loop that circulates excess heat from a nearby data center to offset on-site heating needs.
Structural elements are used as final finish elements, meaning fewer materials and a smaller life cycle energy cost for the building. Commuters benefit from nearby transit options, bike lanes, and commuter shower facilities, which may also come in handy for the building occupants taking advantage of the central staircase to get their steps in.
“We’re always proud when our projects meet our clients goals, and we feel we did that here. We created something that was unique from other campus buildings but feels connected to the others,” Krech says. “It’s a real positive contribution to the community.” g
Structural elements are used as final finish elements, meaning fewer materials and a smaller life cycle energy cost for the building.
This Seattle arena was designed with the future in mind.
Rainwater is collected from the arena’s roof, prefiltered to remove any debris before entering a large underground cistern, and then released when needed into a smaller tank
at the arena’s event level. There the water goes through a reverse osmosis purification system before being pumped into the electric Zambonis used for ice resurfacing.
There is a major arena in downtown Seattle that is like none other. Designed by global architecture firm Populous, Climate Pledge Arena is the first arena in the world to achieve Zero Carbon Certification from the International Living Future Institute.
The 17,000 capacity arena opened in 2021 but continues to be an example of the possibilities when it comes to arena and other spectator spaces (read more about designing for spectators on pg. 322). Living walls, rainwater harvesting, and the elimination of single use plastics are just some of the many sustainable strategies on display in and around the Climate Pledge Arena.
“We were very intentional about the ways we thought about sustainable design with Climate Pledge,” says Geoff Cheong, a senior principal at Populous, who specializes in multipurpose entertainment venues.
He points to the example of rainwater harvesting used in the project. “That strategy only works if a number of things come into perfect alignment. If you need that water at a time of year when it doesn’t exist, it doesn’t make any sense to explore a strategy like that.” But in a place like Seattle where, during fall and winter you get the majority of rainfall, that happens to align perfectly with the NHL hockey season.
Cheong says the biggest sustainability success is the reuse of the historic roof.
“Purely from a building reuse standpoint, embodied carbon associated with that historic structure, preserving it was monumental.”
A “rain-to-rink” system collects water from the historic roof—it dates back to the 1962 World’s Fair—into a 15,000-gallon cistern that sits under the west plaza of the arena and is then brought into the facility all the way down to the event level, or about 50 feet below the street. It’s then purified and pumped into the electric Zamboni and used to resurface the ice—the greenest ice in the NHL. “It’s a really incredible story and strategy, and we’re always excited to share about it,” Cheong says.
Water is conserved in several other ways at Climate Pledge Arena, too. All concourse restrooms utilize waterless urinals, for one. The site design also includes onsite stormwater retention for landscaping, and native plant species that require less watering and maintenance are used extensively throughout the project.
“Saving the roof was the result of incredible collaboration between Populous and Thornton Tomasetti, the project structural engineer,” Cheong says.
He says the team designed a temporary shoring system to suspend the roof in a floating state while the original foundations were demolished. While suspended, nearly a million tons of earth was excavated and removed from the site to make room for the new arena’s expanded subterranean footprint, which extends well beyond the dripline of the historic roof. “New concrete foundations were then poured, and permanent support columns extended upward almost 50 feet so they could be reconnected to the 44-million-pound roof—a true architectural and engineering feat.”
He says creative and sustainable engineering resulted in the repurposing of elements of the temporary shoring system to build another temporary support system later in construction—one that supported the 270-foot-long press box bridge that spans over the arena’s west upper deck seating.
Zero waste initiatives, touchless technology, and LED lighting are more sustainable strategies seen throughout the arena. The venue is also home to a 200-foot living wall with greenery hanging overhead—an Amazon vision Populous brought to life. Amazon is the arena’s naming rights partner, and the Climate Pledge was the name of the mega retailer’s goal to reach net-zero carbon emissions by 2040—a goal they achieved seven years early.
The best sustainable designs, including this one, often inspire awe, and designing for a dramatic first impression was also always part of the goal, Cheong says. “As guests enter Climate Pledge Arena through the Alaska Airlines Atrium, they’re presented with an 8,500-square-foot immersive, high-definition digital backdrop adorning the atrium’s walls, ceiling, and vertical structure. Alongside our client (Oak View Group), we imagined the arena’s entry as a canvas for immersive digital art that transforms night-to-night and allows visitors to have a unique and tailored experience from one event to the next.”
Like at many venues, the design for Climate Pledge also embraces highly efficient self-serve and touchless technologies for food and beverage experiences. “It drastically reduces queue lines and elevates the customer experience and impression of the venue by allowing guests to be away from their seat for less time,” Cheong says. g
WORDS BY LAURA ROTE
Along the waterfront in Seattle’s historic Pioneer Square neighborhood, The Jack respects the past while looking to the future. Designed by Olson Kundig and developed by Urban Visions, the project is defined by street-level retail with seven floors of creative office space, a rooftop amenity, and one level of below-grade parking.
“The most exciting part about The Jack’s completion is seeing how the building interacts with the neighborhood in a quiet, contextual way,” says Tom Kundig, principal, owner, and founder at Olson Kundig. “It’s a testament to the level of attention and care that went
into its subtle detailing and proportions. What’s really exciting, though, is the positive feedback we’ve received from our neighbors and members of the community; a lot of people didn’t even realize it was built—which, in a way, was the goal all along.”
The Jack is a modern heritage building whose design is sensitive both to the past and the future—especially important in Seattle’s oldest neighborhood. It harmonizes with surrounding buildings in materiality and scale, while its flexible design has future uses in mind.
“The Jack is an intentionally quiet building in a neighborhood that is important to us not only because of its rich history, but because it’s our neighborhood— our offices have been located in Pioneer Square for over five decades,” Kundig says.
Taking advantage of the alley space was key to the design. “The building core was intentionally pushed back toward the alley to provide a big, flexible floor plate that can accommodate numerous functions. Because the building’s alley-side is typically less preferred, this strategy also shifts the building toward the water to really maximize those views,” Kundig says.
The Jack’s location on the waterfront is directly adjacent to the Alaskan Way Viaduct, which was demolished during the design process—offering new, unobstructed views of Elliott Bay. “It was important for us to maximize
The Jack’s 16,000-squarefoot rooftop deck is arranged into multiple glass pavilions focused around the central green roof.
Olson Kundig designed The Jack to be a modern heritage building whose design is sensitive both to the past and the future, building on the cultural and architectural history of Pioneer Square, Seattle’s oldest neighborhood.
the panoramic views, pulling back the roof elements to really prioritize those sightlines from the terrace. Inside we incorporated a lot of transparent warehouse windows and floor-to-ceiling windows to continue the visual connection to the larger landscape outside.”
The building was designed with low-iron, low-E, high-performance glass, chosen both for function and composition. Multiple window types can be found on the facade, including warehouse windows and punch windows. “From the exterior different window styles and textures work to break down the scale to match the surrounding buildings, while inside they delineate the functionality of each space,” Kundig says. “At the base of the building we intentionally kept it very open and transparent for future retail and storefronts.”
The design team referenced the rich architectural character of the neighborhood in part with brick facades inspired by the colors and textures of the historic buildings defining the neighborhood. “On the main facade facing the waterfront the brick massing is extruded into two distinct parts with different window treatments, weaving the building into its context by
PROJECT: The Jack
LOCATION: 74 S Jackson St.
DESIGN ARCHITECT: Olson Kundig
Completion: 2023
Contractor: JTM Construction
Certifications: Salmon-Safe, Targeting LEED Gold
appearing as separate masses. Between the two masses recessed glazing delineates the building entrances with steel windows that draw on the surrounding historic industrial buildings.”
Kundig says the building’s brick facade is a subtle way to evoke history without reproducing it. “We wanted to mimic the historical buildings in the neighborhood, which typically have more refined brick at the base, transitioning into smooth brick above, with rough brick in the alley. Our strategy was to interpret that language by using three different types of brick. At the base of the building the transition from smooth to textured brick aligns with the adjacent buildings instead of the floor, drawing a line to reference how the historical buildings were added onto and evolved over time.”
The project’s commitment to sustainability is clear— from its solar panels to the green roof system. The rooftop is arranged into multiple glass pavilions focused around the central green roof, including an occupied terrace that offers expansive views across the water.
The green roof reduces the heat island effect and provides a biophilic habitat for people to enjoy, planted with structural trees and Mexican feathergrass selected for its resilience to windy environments. Together the plantings are meant to blow in the wind and mimic the movement of the water beyond—creating a connection between the built and natural environment that is punctuated by the rooftop’s transparent pavilions, Kundig says.
The project also incorporates sustainable design strategies that comply with its LEED and Salmon-Safe certifications.
“I’ve always thought of this project as less revolutionary and more evolutionary,” Kundig says. “Pioneer Square will continue to evolve and change; the goal is for The Jack to be appropriate to the historical context of the neighborhood and an authentic response to our time.” g
Biophilic design is central to an expansion at this major airport.
Work is ongoing on the C Concourse Expansion, or CCE, at Seattle-Tacoma International Airport. The project is expected to be complete in May 2026—before the World Cup comes to Seattle in June. The start of structural steel delivery, to add four new floors to the existing three-story building, began in fall.
The design by Miller Hull and Woods Bagot is inspired by the beauty of the Pacific Northwest and will elevate the passenger experience. The project will create a new passenger gathering and amenity hub at the base of the concourse.
“The CCE will provide 10 new dining and retail venues, six new retail kiosks, airline office space, and a two-story airline lounge,” says Rich Whealan, principal at Miller Hull. Amenities will also include an interfaith prayer and meditation room, sensory room, nursing suite, and an outdoor deck area to overlook airside activities.
The Port of Seattle, which owns and operates the airport, is working to be the greenest and most energy-efficient port in North America. CCE is the first project to apply the Port of Seattle’s new Sustainable Project Framework and sets the precedent for all future capital projects. Sustainable features include rooftop photovoltaics, fossil fuel–free systems for heating and hot water, electrochromic glazing for windows, dishwashing capabilities for vendors reducing the need for disposal dishware, embodied carbon reduction strategies, low-flow water fixtures, and biophilic design principles.
Whealan is perhaps most excited about the dynamic glass tinting of the folded facade. “The folded facade is a series of vertical ribbons of glass that alternate between south-facing and west-facing exposures and provide controlled daylight to the building interior,” he says. “Creating this folded pattern allows for more daylight to enter the building and be optimized during the day. On sunny mornings just the south-facing glass ribbons will
The C Concourse Expansion will bring much-needed light and air to one of the busiest crossroads in the terminal.
tint while west-facing glass ribbons can remain clear. This will shift throughout the day and reverse during late afternoon and evening hours when the west-facing glass will be tinted and south-facing glass will be clear. On overcast days when solar glare isn’t a concern, and during the evening hours, all glass panels of the folded facade can be clear, creating the highest level of transparency and connection between inside and outside.”
Whealan says airports are largely becoming more sustainable. “Sometimes this is driven by agency goals, like the Port of Seattle’s Century Agenda, or by limitations to infrastructure capacities. In either case we’re seeing clients wanting to explore options and rewarding creative innovation.”
The project itself promises plenty of activity and excitement when complete. A public lookout on the third floor is a secure outdoor space that connects passengers with the sights and sounds of an active airside environment, while the Grand Stair seating area overlooks a live performance venue.
Wood and natural stone terrazzo are among the sustainable building materials used in the project. Miller Hull has collaborated with Woods Bagot on the architectural design of the CCE project, and Woods Bagot has led the development of the wood features inside the building. “The use of wood provides a warmth and character emblematic of the Pacific Northwest and welcomes passengers to enter and linger within this active hub,” Whealan says.
There is no natural gas piping to the building. Instead the building is heated through the use of dedicated air source heat pumps on the roof. A 500kVA rooftop photovoltaic array will provide up to 11% of the building’s annual energy demand. The project is targeting LEED Gold. g
PROJECT: C Concourse Expansion at SEA LOCATION: Seattle
ARCHITECTS: The Miller Hull Partnership & Woods Bagot
Completion: Anticipated May 2026
Size: 226,000 gross square feet
Cost: $250 million construction cost
Structural & Civil Engineer: Magnusson Klemencic Associates
MEP Engineers: PAE
Electrical Engineer: ARUP
Contractor: Turner Construction
Lighting Design: Dark Light Design
The Miller Hull Partnership is helping the Port of Seattle on their mission to become the most energy-efficient port in North America.
The Port of Seattle has committed to growing Seattle’s maritime technology sector with the Maritime Innovation District at Fishermen’s Terminal, comprised of the Maritime Innovation Center for
seeding small startups and the Gateway Maritime Technology Incubator—a complex of flexible energyefficient and welldaylit industrial workspaces for more established maritime enterprises.
In May 2024 the Port of Seattle broke ground on the new Maritime Innovation Center at Fishermen’s Terminal. The project centers around the adaptive reuse of the terminal’s oldest remaining structure (circa 1918) reimagined by The Miller Hull Partnership.
Expected to be completed in 2025 with tenant improvements continuing into spring 2026, the Maritime Innovation Center will support and drive innovation in the maritime sector through collaborative research and development facilities.
The Port of Seattle made a huge commitment when they set out to be the greenest port in North America, according to Mike Jobes, design lead on the project and a principal at Miller Hull.
“It’s a huge statement project,” Jobes says of the twophase endeavor. “We’re taking the oldest remaining building in their portfolio, right on the waterfront at the Fisherman’s Terminal site. It’s a building you can see from the Ballard Bridge—a really important thoroughfare in town. A lot of people will see this project.”
In alignment with the mission to become the greenest and most energy-efficient port in North America, the building is seeking full Living Building Challenge certification, with innovative and sustainable strategies, serving
The original timber structure is retained and exposed to highlight the impressive volume of the existing space, while a new steel structure delicately needles through.
PROJECT: Maritime Innovation Center
LOCATION: Fisherman’s Terminal
ARCHITECT: The Miller Hull Partnership
Completion: Expected 2025
Size: 26 acres
Structural & Civil Engineer: PND Engineers
Mechanical & Plumbing: The Greenbusch Group
Electrical Engineer: Elcon Associates
Environmental: Herrera Environmental Consultants
Biophilic Design: LENS Strategy | Shepley Bulfinch
Indigenous Interpretive Program: Headwater People
Landscape: Hough Beck & Baird
Signage: Mayer Reed
Polycarbonate Wall System: Kingspan UniQuad
Triple Pane Exterior Glazing System: Arcadia
Blackwater Treatment System: Orenco
Certifications: Pursuing Living Building Challenge Certification
as a model for other ports to follow. Once completed the Maritime Innovation Center will be Miller Hull’s seventh Living Building, joining the firm’s portfolio alongside the Bullitt Center, The Kendeda Building for Innovative Sustainable Design, and Loom House.
Reintroducing Fisherman’s Terminal
Jobes says many people don’t realize Fisherman’s Terminal is operated by the Port of Seattle. It’s a crucial site, including for the major Alaska fishing fleet, he says. “It’s a pretty important site of the whole fishery, and so it’s a perfect place to make a big statement and go for a high-visibility project where they’re also heralding their commitment to driving the ’blue economy’ in Seattle,” Jobes says. The blue economy, or “blue tech,” has been described as an emerging focus area for sustainable development in many countries, according to World Bank Water Data, with a range of development opportunities in sustainable fisheries and aquaculture as well as opportunities to address marine pollution and rethink oceanic sectors.
The new project is designed to truly be a hub of innovation. “If a fisher comes in off of a boat after being out for months and has an idea for how to make things better or an idea for a new product or a new way of fishing, they can come into the Maritime Innovation Center with its big welcoming door right there facing the water. They could come in there and hopefully find someone to help them innovate,” Jobes says.
The building’s anchor tenant, Washington Maritime Blue, is committed to the development of maritime business, technology, and practices that promote a more sustainable future. They will ultimately operate the facility when it opens. “They couldn’t be more perfectly aligned with the Port’s goal. They’re bringing together maritime innovation from around the globe—businesses that are innovating and electrifying fleets and sustainable measures in all aspects in the maritime industry. They’re growing that economy.”
The project’s location along the water with helpful signage and wayfinding throughout the site is meant to encourage the public to explore, too. The area around Fisherman’s Terminal has long been a bustling, central area where people go to shop, dine, and take photos.
“This building is in a hardworking part of the terminal. It’s safely bringing people down to the water’s edge with signage to encourage them to check it out,” Jobes says. A large gathering space on the ground floor of the center with a huge bifold door is also designed to be a place for public events and outreach. It’s an opportunity to get people aware of what’s happening at the port, the innovation that’s possible, and potentially inspire younger people to consider a future career in the field. Tulalip Coast Salish Artist Ty Juvinel as well as local artist Shogo Ota are also working on murals for the site to further engage the public.
Education is one tenet of the Living Building Challenge (LBC), according to Chris Hellstern, Living Building Challenge services director and senior architect at The Miller Hull Partnership. “We hope it’s an inspiration for the fishers who use this but also other people who can see working waterfront buildings and port buildings and be able to emulate this level of building performance,” he says.
The Maritime Technology Incubator co-locates innovative maritime startups within the complex, where chance encounters are maximized to spur further innovation. Located at the primary entrance gateway to the Terminal, the daily activity within the complex is on display to visitors, increasing awareness of Seattle’s important maritime history as well as its innovative future.
Miller Hull has achieved LBC certifications across many different building types with many different needs. “In terms of this building it’s really just protecting the historic nature of the building—making sure we’re honoring the architecture there and the existing, somewhat delicate parts of the structure,” Hellstern says.
The design saves the building’s original heavy timber frame and is currently working to solve some unique challenges, Jobes says. “The building sits on really poor soil, so we’re having to drive all new piles below it,” he said in fall 2024. “The building has been lifted up, moved over on wheels, and they’re driving piles right now and then have to pull the building back on top of it.”
He says the exterior cladding and envelope of the existing building was deteriorated, with no real insulation value. It had long served as a storage area and was cobbled together over many years with corrugated sheet metal and plaster on top of it. “Everything’s discontinuous and there’s no good shear value to it. It has no seismic value in the current seismic code. So it’s this beautiful, old, patinated timber frame that is being saved, and then we are putting a whole new jacket on it,” Jobes says.
New will blend seamlessly with old as all materials are being selected within the palette of the industrial materials used elsewhere in the port. “We’re not making it fancy; we’re just making it really well daylit and really well insulated with a high-performance envelope and simple detailing that fits in with the rest of the project,” Jobes says. “It’s a great daylight and performance envelope we’re sliding down over top of that old structure.”
Inside, to meet current seismic code, they will work in a secondary structure to supplement the existing frame while honoring the existing frame. When visitors walk into the completed project they will be able to appreciate the old and new and see the whole operation within the historic frame, with dramatic daylight pouring in through the skylight. “They have a large atrium space in the middle—a double-height space where you walk in and look up and you can see all the existing historic trusses,” Jobes says. Translucent polycarbonate panels will further drive daylight into the main space, while a huge bifold lift door allows for large equipment to be loaded in and people to easily walk in and out.
Jobes is also excited about reusing a series of big, heavy timber columns and beams that were inside the building—elements thought to be the armature for a gantry
Fishermen’s Terminal serves as the home port for Seattle’s commercial fishing fleet and is poised to become the hub for the region’s growing “blue tech” economy.
crane that picked up the boats to pull them in. “They were just there to hold up a gantry that no longer existed, so we were able to salvage those. I think they’re 24-by-24 inch columns, huge old growth timbers, and we’re reclaiming them as big benches where people can sit and exchange ideas or hear about the last time they went out on the boat,” Jobes says. “We’re trying to make a lot of spaces for people to sit and be together.”
Inside people will find another couple of benches on the ground floor made from the existing historic beams.
Beyond the reuse of material and its inherent embodied carbon savings, much effort has also gone into ensuring material selections are Red List–free and indoor air quality is improved. “We want to take an industry that certainly is based on nature, but then that often gets some noxious fumes and contaminants that these
“WE HAVE THE ENGINEERING
FOR THESE THINGS NOW. THIS IS NOT OUT OF THE ORDINARY ANYMORE.”
folks work in, and have a place for them to almost have a respite from that and have a much healthier indoor air quality space to work in,” Hellstern says.
He says natural ventilation is a major function of the project as well as sustainable filtration strategies with the building’s mechanical systems, bringing in dedicated outside air.
The project’s commitment to stormwater treatment is also inspiring, Jobes says. “Fisherman’s Terminal is a pretty asphalt-heavy area, and in order to meet Living Building levels of stormwater treatment for site runoff we’re introducing a bioswale garden at the far south end of the site across from a small parking area,” he says.
The area will serve both as a point of relief in a heavy industrial area, planted with trees and serious bioswales before the water goes back into Salmon Bay “nice and clean for the fish,” Jobes says. “It’s going to be this really cool area of respite on the site.” Cleaner coastal waters directly impact fishers’ livelihood, he says, demonstrating how sustainable design can strengthen the connection between the built environment and natural ecosystems.
Hellstern likes to make sure people understand just how possible these types of projects are. “A lot of different owners and organizations can have these same ideas about being the greenest; they may not know how to get there, but there are those of us in the design industry who can help,” he says. “We have the engineering solutions for these things now. This is not out of the ordinary anymore. It just takes a commitment, and we’re really excited to be able to support and to be able to see this expand. We hope many other ports around the world follow suit.” g
The Arctic archipelago of Svalbard offers an up close look at the real and devastating effects of climate change.
BY LAURA ROTE
The people
The Norwegian islands near the North Pole are home to roughly 2,500 people—most of them living in a vibrant settlement called Longyearbyen in the valley. But with unprecedented climate disasters—including two devastating avalanches in 2015 and 2017—there is cause for worry.
“A lot of my friends who lived here during those avalanches, they just moved out because it was too scary for them to live here with their family. Some of them were digging the snow out of the houses, and to them the trauma was too big to stay here,” says Ingvild Sæbu Vatn, an architect who relocated to Svalbard from mainland Norway in 2011, in part to open the Longyearbyen office of LPO, an Oslo-based architecture firm.
The week before Christmas 2015 a strong storm triggered an avalanche, killing two people, including one child, and caused many injuries and destroyed 11 houses, according to an article from ScienceDirect. More than 200 people were evacuated. The region has repeatedly been called the most climate-sensitive in the world.
Another avalanche occurred under similar conditions in February 2017, striking apartments near those destroyed in 2015. Since then more measures—like snow fences—have been put into place and homes have been moved, but some say more needs to be done to protect both the people and the land.
“We’ve put up a lot of fences. In a way it’s a physical manifestation of the threat,” Vatn says. “Now we have triple fencing, triple security.” One fence is meant to collect any snow that barrels down the hill, while another aims to keep the snow in the hill. Both help prevent an avalanche from reaching the town’s third layer of protection—a large wall at the bottom of the mountain. While it’s added security, Vatn says these changes also reduce the available living area in an already small place. The historic settlement is located in a narrow river valley with beautiful views and incredible access to nature, but there is very little place for building. “The town is not allowed to expand on unbuilt land outside the existing footprint,” she says.
But it’s not just the avalanche risk that has increased since Vatn moved less than 15 years ago. She’s also seen receding glaciers and a decrease in animal population, as she and her partner can’t find as many seals to feed their dog-sledding dogs, a common practice on Svalbard. That’s also a problem for the polar bears. Different fish, though, have also shown up as the water warms.
We recently traveled to this northern land of fjords and glaciers—about 60% of Svalbard’s land is currently covered by glaciers—to learn just how quickly things are changing.
Insider insight and an architect’s look at saving Svalbard
Unprecedented beauty, unprecedented ice melt, unprecedented rain, unprecedented pain. It’s a word I heard—and probably said myself—a lot during my brief time on Svalbard. Unprecedented pronunciations, too, for some people; for weeks when I mentioned my upcoming trip people asked me to repeat myself. “Can you spell it?” They asked. “Small bar?” I eventually just showed them on Google Maps.
While some people were unfamiliar, or even confused, others called it a trip of a lifetime. The latter is almost certainly true. I’ve long been enchanted by the stark landscapes of the glacier-laden places of the globe—Svalbard literally and figuratively high among them. It was a place I wanted to see before it was, well, possibly too late.
Widespread studies, including research from a professor at Uppsala University who’s been studying the arctic ice since 1997, show Svalbard and the Barents Sea are the fastest warming region on the globe.
People living on Svalbard face a number of challenges. Architects especially are tasked with getting creative if they want to preserve this rare place that so many, like LPO architect Ingvild Sæbu Vatn, love. Vatn’s own identity became intertwined with the island quickly after she made it her permanent home in 2011. She tried living in other places—Trondheim, Oslo. “I don’t know who I am if I’m not on Svalbard,” she says.
Vatn says a lack of local materials and the effects of very fast global warming— including the melting of permafrost on Svalbard, erosion, avalanches, and the destabilization of building foundations—are troubling for the community. Plus, those who want to live more sustainably are at odds with the prevailing practices, and she says a legal framework makes it difficult to reuse materials and whole buildings.
Architects at LPO led a feasibility study called Right Place - Right Form to look at buildings as a local resource and consider material banks in a future-oriented development of Longyearbyen (the main settlement on Svalbard). Since 2019 they have shepherded reuse projects in collaboration with several other actors and grants from DOGA, which administers the Ministry of Foreign Affairs grant program for architecture and design in Norway. The program
FOSSIL seeks to preserve and bring new life to a former power station that closed in the 1980s. LPO and others are working to make it an artistic attraction and cultural arena.
aims to move people toward a more circular construction industry.
“Right Place - Right Form was a project trying to reuse as much as possible of the buildings and materials in an immediate approach to the development of the city. It didn’t matter what kind of a building or function; we tried to make a project where we could move buildings from Svea to Longyearbyen to reuse them here for new purpose or also move buildings within Longyearbyen. The project was not only about physical projects but also about creating awareness and local ownership within the community and showcase for a more sustainable building practice,” Vatn says.
While reusing materials is nothing new, she says some laws and regulations make it difficult in Longyearbyen and mainland Norway. LPO is looking at how they and others can limit the amount of resources both produced and transported back and forth to the island, especially as 40% of the world’s greenhouse gas emissions come from the built environment, and transport of machines and materials to construction sites accounts for 25% of heavy transport in Norway, according to LPO.
Vatn says reusing Svalbard’s own materials and buildings is also important to the region’s storytelling and identity. “There are histories in these materials and buildings.”
LPO initiated an effort to reimagine an old coal-fired power plant in Longyearbyen as an industrial monument, opening it up as an accessible, artistic attraction and cultural arena for the public on Svalbard. The FOSSIL project seeks to preserve and bring a new and different life to the power station, which has stood virtually untouched since its closure in the early 1980s. The project is a collaboration
between LPO, the local council in Longyearbyen, Riksantikvaren (the directorate of cultural heritage), and others, including those working in tourism. “We wanted to show what kind of activities and cultural things and beautiful spaces we could use this building for,” Vatn says.
Longyearbyen has a long history as a coal mining town, dating back to 1906 when John Munro Longyear—the settlement’s namesake—started the industry. All but one mine in remote Svalbard has ceased operations, and Gruve (mine) 7 was set to cease production by summer 2025 as part of area’s ongoing effort to reduce carbon dioxide emissions.
“It’s very difficult,” Vatn says. “The coal we have been using until now produces a high percentage of CO2. We were like the dirtiest people in the whole of Norway because our CO2 is so large per person. But the coal is here in Longyearbyen, so the coal extraction is already taking place.” While she describes its removal on Svalbard as “wounds in the landscape” she recognizes it both as a local resource and for its cultural significance. And compared to global CO2 emissions, what’s experienced on Svalbard she says is very small.
Still, she says the community must commit to finding more sustainable systems, though the challenges are significant. Vatn says windmills can harm the birds (a solution near Isfjord Radio Adventure Hotel, a 55-mile boat ride away, is being considered that is lower to the ground), and some view them as an eyesore, while solar panels can be difficult to work with in a place of sometimes total darkness.
LPO recently designed an inspiring new administration building for Telenor, completed in 2022, in Longyearbyen. The Nor-
LPO designed a nearly zeroenergy building for Norwegian telecommunications company Telenor, who is committed to reducing its climate footprint on Svalbard.
“There are histories in these materials and buildings.”
wegian telecommunications company aims to become carbon neutral by 2030 and was committed to reducing its climate footprint on Svalbard. Today it’s almost a zero-energy building, with solar cells on the roof and heat recovery from the data center.
Material reuse was also a large focus of this project. The building’s wind bracing includes reused steel plates from a decommissioned mining operation elsewhere on Svalbard. Steel beams from the old building were transformed into footbridges, and parts of the external cladding were reused as siding in the gables of the new building. “The building balances Telenor’s need for an energy-efficient and high-tech office building in the historically important building environment at Skjæringa (Longyearbyen’s oldest quarter) and is an important example for the future development of Longyearbyen,” Vatn says.
Architects have a critical role in helping to save vulnerable places where people live, she says. Many houses on Svalbard will ultimately have to be rebuilt as many stand on wooden piles driven 20 or 30 feet into the permafrost—and that permafrost is melting. For homes on sloped terrain, that can be an even bigger problem, with rain and rotting piles.
“To make new foundations for the housing is quite expensive, so it is most cost-effi-
cient just to tear the house down,” Vatn says, adding that there’s no use fitting it for the storms with extra insulation or new windows if the foundations are moving.
Heating is another problem, as cold air blows straight through many of the old buildings, Vatn says. “As long as we’ve had the coal power plant, which has a lot of extra heat energy, it hasn’t been a big problem. We can have houses with thin walls and wind blowing through them because we have the central heating system with a lot of the heat energy. But when we’re going over to new sources of energy, we’re probably not going to have that excess heat. We have to do something about insulation.”
Architects are uniquely positioned to help, Vatn says. “I think we have an understanding of the connections between people and built environment, people and landscape, and an ability to zoom in and out, abstract and conceptualize, that definitely can be used in the processes of developing, changing, and restoring places in vulnerable and harsh nature.”
LPO continues to look to circular strategies to help the community have a safer, more sustainable future. Strategies based on local needs and resources will also make
the community less dependent on transporting goods from the mainland, less vulnerable for hostile actions on infrastructure, and less vulnerable to high prices on necessities while further bringing the community together, according to Vatn.
“We can develop circular solutions in Longyearbyen that can also benefit so many other small settlements and local societies in the world. We have huge human resources and knowledge in our international and transient little town.”
LPO considers Svalbard the perfect test case for exploring circular solutions because of its small size. Take food waste, for example, that ultimately ends up in the sewer system, which goes into the fjord. That waste carries with it a lot of potential resources.
“We could first take the water out, and the water could be cleaned and used, if not as drinking water then as the water that goes into the toilet or other kinds of water. And you could use all that dry stuff you get out of it and make it into either biocoal or biogas (see how the local brewery is doing something similar at gbdmagazine.com). You could use it as a fertilizer, or you could use it to make heat or electricity,” Vatn says. “It’s quite a lot of resources we just put straight into the ocean. These kinds of circular systems would be so interesting to try to make work in this very small scale community.” gb&d
Longyearbyen is already pedestrian-friendly, and improvements continue to be made in the settlement.
Travel company Svalbard Adventures offers excursions like boat trips and snowmobile tours.
Inside the paradox of sustainable tourism in vulnerable places
Svalbard is a beautiful, strange, perhaps calamitous contradiction; I both desperately want to see it, to be on an open-air boat on the way to its glaciers, but I also want to keep it secret. Not because I want to keep it to myself, but because I’m afraid for it. The effects of climate change have been clearer there than perhaps anywhere else. This group of Norwegian islands about halfway between the northern coast of Norway and the North Pole is home to Longyearbyen—the northernmost town in the world. But it’s the fastest warming place in the world, too.
“In the Arctic we can see the effects of climate change firsthand, year after year. We’re witnessing significant changes in weather patterns, vegetation, glaciers, and wildlife,” says Benedicte Klyve, marketing manager at Svalbard Adventures, an ecotourism company on Svalbard that offers everything from boat trips and hiking excursions to dog sledding and snowmobiling—all through an educational lens.
On a boat tour in September, one Svalbard Adventures guide recounts how she’s seen the glaciers change right before her eyes. She says surging glaciers are usually due to pressure, as so much snow falls on top of them. “But now they’re finding that there’s a new type of surging glacier, and it’s most likely linked to climate change,” says Taygen Hughes, a seasonal employee from New Zealand.
Summers and winters alike in Svalbard are warmer and rainier than usual for this “Arctic desert.” With more sun hitting the glaciers, there is also more calving—when large chunks of ice break off the end of a glacier, sending a big splash and sound echoing across the ocean.
A glaciologist recently told Hughes that if all of Svalbard’s glaciers suddenly melted, global sea level would rise a couple of centimeters. Not too bad, she says, but Svalbard is tiny compared to neighboring Greenland, whose own ice melt would cause a lot of trouble. As for Antarctica’s rapidly melting glaciers, that’s a major fear for many. “Obviously that isn’t going to happen overnight, but it is pretty alarming if you look at the rates that all of the glaciers are melting up here in the Arctic,” Hughes says just moments after the Sveabreen glacier calved in front of us. “It is melting a lot faster here on Svalbard. A lot of other Arctic regions are looking to Svalbard to see what’s coming for them.”
Another tour company, Basecamp Explorer, offers similar excursions, including a
journey to Isfjord Radio Adventure Hotel—a remote outpost accessible only by boat in summer and dog sled or snowmobile by winter (more on pg. 306). “From year to year it’s really remarkable. I can tell the glaciers have moved two, three, four meters,” says Cecilie Feen, sales and marketing manager at Basecamp Explorer.
There’s no hiding climate change when you’re out in nature. Feen says the signs are everywhere. “That’s something we want to tell our guests—what you’re doing at home has an impact in the Arctic.”
People of all backgrounds from all over the world (50 different countries at last count) live in Longyearbyen today. Many come from mainland Norway, having fallen in love with the otherworldly nature, the wildlife, the Northern Lights, even the snowmobiling—but many also arrive from Thailand, Russia, Ukraine, and elsewhere for work or to try another way of living. Anyone can live and work in Svalbard regardless of where they’re from; no one is required to have a visa or residence permit.
“The community in Svalbard has a deep love for this place we call home, and visitors often come to share that same affection,” Klyve says. “By fostering this connection we hope it inspires our guests to reflect on how their environmental choices back home have an impact, not only in Svalbard but on the rest of the planet. Climate change is most visible in polar regions, making this connection important.”
Ronny Brunvoll, CEO of Visit Svalbard, has seen tourism evolve over the past 10 years and says it’s a delicate balance. “There’s been a major development in volume,” he says, noting that the settlement managed to increase volume without increasing the number of beds more than 20%. They did so by doubling the amount of visitors to create nearly year-round tourism. “Now we’ve got a full season from February to September, where it previously was March and April, then nothing, then half of June to half of August, and then more or less closed for four to six months.”
Limiting the number of visitors on Svalbard is important both to protect the integrity of the land as well as preserve the feeling of being somewhere special. Tourists mingle with seasonal workers at the bar, while photographers strike up conversation with locals along walking paths. It’s both peaceful and bustling in September when I’m there. You can get a seat at most restaurants easily, and strangers don’t stay that
way long, as people seem eager to share what brought them there. There’s a feeling of connectedness.
“We’ve gradually grown what sustainability means—not only caretaking of nature and cultural heritage, but also caretaking and coexistence with the local society. The tourism sector shares it with the locals; locals have the priority obviously, but we have to find a good balance,” Brunvoll says.
The number of visitors, length of stay, where they stay, and what they do all have a direct impact on Svalbard. The number of people coming in by cruise ship was a huge issue until recently, when strict cruise rules were set to limit the number of people coming in for a short amount of time—sometimes as short as a day. Brunvoll and others in the industry are working to emphasize extended stays. “That is the only efficient way,” he says, adding that the average guest stays 4.5 days. “How do we increase that to 6 or 7?”
Beginning Jan. 1, 2025, ships will be limited to a maximum of 200 passengers in all protected areas on Svalbard. The number of cruise passengers allowed onshore at any single time at select sites is no more than 39, with one guide for every 12 passengers required.
“Climate change together with increased activity has resulted in a great pressure on the vulnerable arctic wildlife and nature in Svalbard. We are now tightening the environmental regulations in Svalbard to strengthen the protection of flora and fauna,” the Norwegian minister of climate and environment, Andreas Bjelland Eriksen, told authorities and media.
Many say it’s a move in the right direction. “The biggest footprint is from the flight—getting here—or from the cruise ship,” Brunvoll says. Of course, working in tourism, he still wants people to visit, and he sees great value in people exploring other places—both socially, to understand one another, and economically. “The consequences for the world will be disastrous if people stop traveling,” he says.
Tourism is admittedly part of what makes the place special, according to Hege Giske, COO of Svalbard Brewery (more on the brewery at gbdmagazine.com). She moved from mainland Norway to Svalbard in 2018. “If we didn’t have tourism, we wouldn’t have such great culinary offerings,” she says. On the contrary, visitors and locals alike can enjoy a number of fine
“We hope to inspire others by showing that even small actions can create meaningful change.”
BY LAURA
or casual dining experiences, cocktail bars, the brewery, and frequent special events— from the annual blues festival to a literature festival to food events and even the world’s northernmost Pride.
A special kind of determination is required of people who live on Svalbard, Giske says. She remembers when she quit her job on the mainland and decided to make the move after her husband got a job and was settled in Longyearbyen. “I thought, ‘OK. I’m going to do it. I’m going to do something crazy and get some special experience before I get too old,’” she says. “The people who live here are so willing to participate, so willing to be a part of the society.”
What is learned from living in such a remote place is very much centered around community and not giving up, Giske says. “When you live with this kind of nature you can’t say, ‘Stop. I can’t do it.’ You just have to keep going. You may get your snowmobile stuck and you can’t call anyone; you just have to keep moving,” she says. “You have to take one step at a time to get where you want to go, and that does something with the whole society.”
Brunvoll recalls the avalanche that claimed two lives in 2015 (pg. 297). The community rose to the occasion to help. They dug people and homes out of the snow, they comforted one other, they made coffee. They had to. “When things happen up here we have to resolve it ourselves because it takes a while to get help,” he says. “It was a shock to everybody.”
There’s neighborliness on a settlement scale, and it’s a model other places could follow, Klyve says. Though Longyearbyen is small, it’s committed to being a good and healthy place to live, and it’s committed to protecting itself for the future. “From shutting down coal mines to transitioning to renewable energy, we work on both
Longyearbyen is an official Sustainable Destination, as owned and recognized by Innovation Norway. The designation has been an important tool for Visit Svalbard, as they and others work to improve sustainability in the local tourism industry.
large-scale changes and smaller community-driven efforts,” Klyve says. “The key is that everyone is involved, and every step matters. While we’re fortunate in Norway to have the resources for this, we hope to inspire others by showing that even small actions can create meaningful change.”
Brunvoll says there’s a certain grit people either already have or seem to develop living on Svalbard that’s not common in most places. “Even though there are a lot of challenges when it comes to nationality, geopolitics, the security situation, climate change, whatever, people still want to live here and want to make this a good place to live,” he says. And it quite simply doesn’t matter where they’re from. “What defines us is that we have chosen to live in this outpost.” gb&d
How Isfjord Radio is on a mission for clean energy at the edge of the world
ˮPlease note that Isfjord Radio is a wilderness hotel and to move outside you need a guide with rifle for polar bear protection.” Wait, what?
I clearly hadn’t thought this through. I hadn’t even considered polar bears when I booked the flight. Now I was on a boat from Longyearbyen, the main settlement on Svalbard in the Arctic, to a remote lodge 55 miles away, crossing the fjord to learn about a historic property’s sustainability efforts and, well, maybe see a polar bear? Two were spotted near the property earlier that week. I asked for the address so I could tell my loved ones where I’d be. “There is no address,” I was told. “It’s the wilderness.” OK then. Let’s go.
First we met at Basecamp Hotel in Longyearbyen. The modern-day take on a trapper’s lodge is decked out in driftwood and sealskin
An impressive solar park at Isfjord Radio hopes to be an example for properties in other vulnerable places. Guests at the hotel learn how to make more sustainable choices while out enjoying the wilderness.
with maps and photos of adventure at every turn. I sipped tea and waited for the van to pick us up and take us to the 12-passenger boat. It ended up being a surprisingly calm day out on the water. It was so calm my seatmate was knitting a sweater on the ride. The roughly two-hour journey took us past old mining towns, including Grumont—a former Soviet company town established in 1912 and abandoned in 1965. So many Arctic terns and puffins passed by that I lost count.
They weren’t joking about the rifles. As soon as we stepped off the boat, smiling guides with weapons casually slung over their shoulders were waiting to give us the rundown and a quick tour once settled. Fortunately we never got too close to any polar bears (we did see one through binoculars on the beach), but reindeer we saw everywhere.
Initially a radio station, the property opened in 1933 as a crucial connection from Svalbard to the outside world. The station was destroyed by both sides during World War II and rebuilt in 1946 (you can still see craters from the war onsite). The central buildings at Isfjord Radio were built in the 1950s, with additional structures added later.
Today Basecamp Explorer runs the Isfjord Radio Adventure Hotel. While it may look rustic from the outside, inside has all the comforts of any modern hotel, including a warm dinner with optional wine pairings. Just steps from the hotel, a sauna overlooking the water is an added bonus—guests just have to remember to take a guide carrying a rifle with them when they go.
Today the property is also home to a pilot program for renewable energy. The solar project was completed in early September 2024 and produced energy through late October.
“Many remote Arctic communities are looking into how to reduce their diesel consumption, and the learnings from this project could be valuable for those communities,” says Mons Ole Sellevold, project manager for the energy project. He’s been involved since phase one construction began in May 2021. The pilot project aims to be replicable for other remote communities dependent on fossil fuel.
“Many remote Arctic communities are looking into how to reduce their diesel consumption.”
From the end of October to the middle of February Svalbard experiences total darkness, when little energy can be obtained from the system. But when the midnight sun shines 24 hours a day from April to August, an extensive battery pack in the basement at Isfjord Radio can be fully charged for later use.
“From the two solar facilities at Isfjord Radio—the ground-mounted and the rooftop-mounted—we expect to produce about 230,000 kWh in a normal year, accounting for about 40% of the total annual energy needs at Isfjord Radio of 575,000 kWh,” Sellevold says.
The project at Isfjord Radio has reduced overall diesel consumption by approximately 70%. “We are very happy about this, but there is potential to reduce it even further by introducing more renewable energy production,” Sellevold says. “We are looking into wind power to be able to also deliver renewable energy production during the polar night and the winter months.”
Norwegian mining company Store Norske owns the facility at Isfjord Radio and started looking into alternatives early on. The exploration into wind is being carefully considered given that a bird sanctuary sits next to the station. “We have been looking into a project, including installing two smaller wind turbines of about 25 kW each,” Sellevold says. “They are about 18 meters (59 feet) tall. We think this turbine size would be suitable for the local conditions and energy needs at Isfjord Radio and also more bird-friendly than larger wind turbines.”
Currently during polar nights the property runs largely on its existing diesel gen-
erators. Sellevold says going for 100% diesel reduction would most likely be difficult and may result in over-investment in renewable production capacity, but the team would be very pleased to achieve 90% diesel reduction. “Diesel generators will most likely be needed as a backup and peak load capacity for a long time anyway. It’s all just about using it as little as possible,” he says.
Sellevold says he’s most excited about the opportunity to combine different types of energy technologies across production, storage, and consumption—making them all work together to reduce diesel consumption.
The project is working toward using 90% renewable energy in 2025. The battery pack
and thermal storage also includes 12,000 liters of hot water.
While Isfjord Radio attracts visitors from all over for everything from midnight sun to wilderness hikes to see walruses, it’s also a popular spot for students and researchers studying meteorology, glaciology, wildlife, and more.
“It is a unique pilot project for Arctic hybrid energy systems, and it’s under continuous development and improvements,” Sellevold says. “There is a lot that needs to be developed and learned along the way, and we are happy to cooperate and share our findings with other actors and with research and education institutions.” gb&d
The solar project at Isfjord Radio has reduced overall diesel consumption by approximately 70%.
High in the Arctic and tucked more than 300 feet into the side of a mountain in Svalbard, the Global Seed Vault held more than 1.3 million seed varieties from almost every country in the world as of May 2024. Affectionately referred to by some as the “doomsday vault,” the Seed Vault is insurance against destruction—at least of crops.
“Conserving plant genetic resources and making them available for plant breeding and research has always been important. Climate change and a growing population have made the resources even more crucial,” says Åsmund Asdal, Global Seed Vault coordinator. “Troubled times and increasing levels of conflicts in the world have probably made more people, including politicians and gene banks, more aware of the need for extra security.”
From unique varieties of major African and Asian food staples like maize and sorghum to European and South American varieties of eggplant and potato, the Seed Vault holds the most diverse collection of food crop seeds in the world. Seeds are stored under “black-box conditions,” meaning the depositors are the only ones who can withdraw their own seeds.
Asdal travels to Svalbard from his office at a research station in southern Norway three to four times a year, when gene banks ship their seeds. He coordinates and handles the seed deposits and communicates with the banks. More than 1,700 gene banks hold food crops for safekeeping all over the world, but many are vulnerable to natural disasters and war, according to the Crop Trust, an international nonprofit dedicated to conserving and making crop diversity available globally. The Seed Vault is owned and administered by the Ministry of Agriculture and Food on behalf of the Kingdom of Norway and is established as a service to the world community.
The original Seed Vault building in Svalbard opened in 2008. Over the years, and with temperatures warming, water started to intrude in the entrance tunnel and had to be pumped out. “The need for rehabilitation became clear as climate conditions shifted more rapidly than anticipated, leading to water infiltration challenges,” says Hans Martin Frostad Halleraker, a senior architect at Snøhetta’s Oslo studio. “Additionally, the original design did not fully account for the evolving environmental factors that arose in the years follow-
ing the vault’s construction. In 2017 Snøhetta, together with engineers Dr. Techn. Olav Olsen, was brought in to address these issues and strengthen the facility’s resilience.”
Investigations with the engineers pointed to a need for a new tunnel to prevent future water infiltration and ensure the facility could cope with changing environmental conditions. The highly technical tunnel project required close collaboration between architects and engineers to address the water ingress and permafrost issues. By 2019 the new, watertight entrance tunnel was constructed.
A new service building was also added for more technical installations, as well as offices and facilities for seed-handling operations. This part of the project faced its own complex challenges. “The building had to withstand the movement of the permafrost, which behaves like a slow-moving glacier,” Halleraker says. “Since the service building is located on a slope, this continuous movement puts pressure on any structure in its path. To handle this we designed the building with a steel structure connected to solid ground, elevated on minimal touchpoints to adapt to the
The Global Seed Vault in Svalbard holds the most diverse collection of food crop seeds in the world. Seeds range from unique varieties of major African and Asian food staples such as maize, rice, wheat, cowpea, and sorghum to European and South American varieties of eggplant, lettuce, barley, and potato.
shifting permafrost while minimizing its impact on the surrounding landscape.”
Halleraker says the facade of the service building also played an important role in its durability and adaptability. “We chose raw steel plates with a thickness of 8 millimeters, designed to rust naturally over time. The rusting process allows the steel to weather, creating a natural protective membrane that can withstand the rough Arctic environment. The facade was designed to rust approximately 2 mm from each side, forming a barrier that protects the core of the structure while also blending with the stark, rugged landscape of Svalbard.”
Using durable, low-maintenance materials was critical to ensure the building will last for a long time—even in extreme conditions. “The choice of materials and the building’s overall design reflect a careful balance between functionality, resilience, and environmental sensitivity. By minimizing the building’s footprint and using materials that age naturally in response to the environment, we ensured that the structure could withstand the unique challenges of its location while preserving the fragile
landscape around it,” Halleraker says.
Potential reuse was another consideration.
“The building materials were selected and components were designed in formats that can be easily disassembled and repurposed in other structures, making the project become part of a future regenerative ecosystem of buildings in Longyearbyen,” Halleraker says.
A temperature of −18°C is required for optimal storage of the seeds, and the permafrost and thick rock in this location ensure seed samples will remain frozen even without power. It’s part of why Svalbard was chosen for the Global Seed Vault in the first place, according to the Crop Trust. It’s also the farthest north a person can fly on a scheduled flight—so it's remote but still accessible.
Halleraker says the design principles used on the most recent project—like elevating the structure on steel poles and minimizing contact with the ground—could benefit designs in other vulnerable climates, including environments with unstable ground, flooding risks, or other climate-related challenges. “Anchoring buildings to solid ground while allowing flexibility for environmental shifts helps ensure long-term resilience without
damaging the surrounding ecosystem.”
Using robust materials like raw steel, which he says naturally weathers into a protective layer, also offers a low-maintenance solution for extreme environments. “This approach, combined with resilient engineering, is ideal for remote areas where regular maintenance is difficult. The strategies developed for the Seed Vault demonstrate how thoughtful engineering and material selection can create buildings that are both resilient and environmentally adaptable.”
Beyond the ongoing permafrost challenges that were addressed during the rehabilitation project, Halleraker says no significant impacts on the structures have been seen since. “However, on a global scale, the existence of the Seed Vault is increasingly critical,” he says. “As climate change accelerates and disrupts ecosystems, the need to safeguard the world’s agricultural diversity becomes ever more urgent. The facility plays a vital role in protecting seeds in a secure environment, ensuring that future generations have access to the resources necessary to restore and sustain crops in the face of environmental challenges.” gb&d
“It’s a really exciting structure that won a lot of architectural awards,” says Fentress Architects founder Curtis Fentress of the LAX project. “It was the largest LEED Gold building at that time in the aviation industry throughout the world.”
Airport design is evolving to make some of the world’s busiest places more adaptable.
WORDS BY LAURA ROTE
Plentiful natural light, palm trees, and a wide open boulevard fill the new International Terminal C at Orlando International Airport (MCO). While daylighting and designing for a sense of place are key to everything Fentress Architects does, some surprising and exciting trends are happening in airport design, too, says Curtis Fentress, who founded the firm in 1980.
“Currently there is a massive amount of money available for infrastructure—and airports fall into that category,” Fentress says.
MCO’s extensive overhang and 15-degree canted glazing reduce bird strikes by breaking up the reflectivity of the main glass facade.
Many airports are in the process of upgrading their facilities, adding buildings or new gates or modernizing overall. “It seems like all the airports in the US are trying to upgrade their facilities. It’s an exciting time in the aviation industry,” he says.
Of course, not all firms are experienced in aviation design, so the demand for the expert team at Fentress is high. They’ve been designing sustainable airports, starting with the inspiring Denver International Airport (DEN) in 1995, long before sustainability
was a buzzword. Fentress became internationally recognized for their work after the DEN project, known for its unique roof and streamlined “curbside to airside” design. DEN is consistently recognized as one for the most sustainable, efficient, and significant airports worldwide. The design set a new standard, from relocation of the building’s mechanical system from the roof to underground and, at the time, innovative automatic bathroom sinks that only ran water when your hands were beneath the faucet.
“At the time we designed the terminal, we took many risks,” Fentress previously said. “A lot of creative decisions we made had not been done before on such a massive scale. To all the young architects, don’t be afraid to push the limits to create great architecture.”
Fentress also designed Incheon International Airport in Seoul, another “world’s best airport” serving millions of international travelers every year. In 2008 the firm was chosen to modernize the Tom Bradley International Terminal at Los Angeles Inter-
The boulevard inside Orlando International Airport Terminal C is characterized by its continuous skylight of varying blue frits. The expansive, daylit passenger thoroughfare is arriving and departing passengers’ first and last taste of the Orlando experience.
national Airport (LAX)—the fifth busiest airport in the world.
More than 650 million passengers travel through aviation facilities designed by Fentress each year; that’s more than 84 million square feet of projects, from the LEED Gold LAX project to South Terminal C at MCO.
Making the most efficient designs is paramount—from getting passengers comfortably through airports to reducing energy bills to being able to upgrade facilities to keep up with technology and other needs with minimal disruption, Fentress says.
Raised access flooring is one solution that helps minimize possible disruption. The relatively new adoption for US airports is used more widely internationally; Fentress was excited when the team behind the Orlando project came on board to use a large amount of raised floor.
“We made the entire area where you go through TSA all on raised floor,” he says. “We had proposed that on many airport projects previously because we saw that changes were in the pipeline for the industry—and many more to come, of course,
with advances in technology. They agreed to it in Orlando, and so it was much, much easier to do the first installation.”
With raised access floor, as things need to be altered, it is much easier to make changes, Fentress says, getting beneath the floor to install new technology or wiring systems if needed, for example. “Protocols are going to continue to change in the area of security,” he says, citing a need for raised access flooring.
Raised access floors provide flexibility and adaptability so the airport can evolve with changing needs by allowing point-ofservice terminals and kiosks to be added or moved anywhere on the floor plate without core drilling or trenching the building slab.
Raised flooring began showing up in airport security areas about 10 years ago, according to Mark Johnson, sales director at Tate Access Floors, but he’s seen an increase in demand as of late. The Orlando Terminal C is the biggest airport application Tate has completed as of 2024.
“It provides you a lot more flexibility to move your services and, specific to airports,
the power and data that are sitting under a raised floor. I think Orlando was a six-inch high raised floor, which leads to about a four-and-a-half-inch space under the raised floor to run power and data.”
That area of raised access floor then extends over to an electrical closet with electrical panels. The Orlando airport project includes raised access floor from the checkpoints to ticketing kiosk areas, with power and data coming from beneath the floor. Johnson says the project covered about 80,000 square feet.
The decision to use raised flooring needs to happen early in the design process because it affects the structure of the building and a lot of other decisions, Johnson says. “In terms of the installation, raised floor makes all of the other components easier to install. It accelerates the construction, shortens the construction schedule, and allows people to move in quicker.”
Walking into the new MCO terminal, you’d likely not realize you’re standing on raised flooring. While the access flooring of years past—often in data centers—was lightweight and may have felt creaky, the flooring in airport projects like these is far
superior, Johnson says. With a terrazzo finish on the raised floor panel, what’s under your feet in Orlando looks like a beautiful new terrazzo-style floor.
“When we installed the raised floor we installed the terrazzo finish at the same time. That’s huge because doing poured in place terrazzo takes weeks,” Johnson says. “We offer a lot of high-end finishes with the raised floor. And when it comes pre-finished, it’s a lower cost than doing that same finish in the field.”
The biggest benefit, though, continues to be that flexibility—being able to get back into a project and run different technology or make changes if needed. Without raised flooring, teams would have to take all of that power and data from its central location and run it horizontally in the ceilings below the floor above.
“Then wherever you need it up above you core drill the slab; it could be 8 inches of concrete and terrazzo finish; you pull your power data up, you put the electrical device that you plug into right there, and you stick a kiosk over it. You keep drilling holes and obviously that’s very expensive. It’s very disruptive. It’s not fast, as com -
pared to if the power and data is under a raised floor,” Johnson says.
With raised floor you simply pick up a panel, pull cable, plug in, and put the panel back. “You can move them around. It’s way less cost of change, and, because nobody knows exactly what the future is going to call for, you’re future-proofing that design.”
Johnson says Tate is starting to see more raised floor at airport gates, too—another area dominated by technology as people scan their tickets and board planes. He’s also heard talk of a future in which passengers go directly from their parking spot to their gate.
“At some point in time we’re going to pull into the parking garage, walk right through the airport and onto the plane,” he says. “All that technology that continues to evolve needs to be easily adapted and updated and changed, and that ties back to raised floor.”
Internationally Tate has seen raised floors incorporated across whole airports, in part because, even if there isn’t a lot of technology under the floor, tenants still come and go
across food, beverage, retail, and more. “It needs to be flexible and adaptable.”
More airports are rethinking how they entertain passengers while also generating revenue, too. “Airports are now being designed or renovated to have added food, beverage, and shopping everywhere,” Johnson says.
Abundant seating at the gate is largely being removed to encourage people to shop and dine instead. “They want you to sit across the hallway at the bar, the restaurant, or shopping. You are within eyesight of where you need to be to get on the plane, but you’re spending money.”
Beyond being able to quickly make changes, Fentress designs airports to feel their place. In Orlando, for example, you can feel a buzz of excitement as many people are on their way to or from vacation. Palm Court, located airside, was designed as a vibrant location with ample opportunity to shop, dine, or socialize in bright, garden-like settings.
Of course, light looks different in various places, whether you’re in Seattle or Orlando, for example, and it continues to be a top
LEFT: Denver
International Airport’s iconic roof is a Tefloncoated fabric, stretched into a fluid and symbolic form that captures the West’s pioneering spirit, culture, and ecology. The translucent roof material reflects up to 90% of solar heat gain while allowing 10% of sunlight to pass through for natural daylighting.
“We build lots of scale models and test how the light is coming in and try to make it a unique place.”
consideration in Fentress designs. “We try to capture that as well and use it to our advantage in terms of making these buildings special. It’s part of our craft as architects,” Fentress says. “We build lots of scale models and test how the light is coming in and try to make it a unique place.”
In Orlando Fentress designed a large, lightfilled boulevard that goes from the train station all the way into the building, the ticketing hall, the security checkpoint, and onward into a large dining and shopping concourse.
“Airports are trying to find every way possible to conserve energy and to bring daylighting into the building if possible. We’ve been using daylight to guide people through the building since DEN in 1995. South Terminal C in Orlando is a recent example,” Fentress says.
He likes to ask teams, “How can you think smarter?” How can you recycle air, for instance? How can you use high-speed, low-volume fans? How can you recycle waste?
“Recycling waste is something we do in all of our buildings—certainly during construction but also within the building. About 90% of the construction waste was recycled for Orlando’s South Terminal C.” The team also strives to pick materials that are low in carbon.
Designing buildings to have more efficient mechanical and electrical systems continues to be key. The Fentress team set out to reduce their energy cost by at least 29% in Orlando. “Reducing the amount of electricity helps with that, and the glass we used in the building is more performance-related; it cuts the rays of the sun coming in. Then we had about a 45% reduction in the energy cost for water. These things are a crucial part of the design.” gb&d
Inside LAX, wood floors and ceiling soffits are consistent design elements that unify the 100,000 square feet of retail space. Indoor plants add to the biophilic design.
WORDS BY LAURA ROTE
Forget popcorn and peanuts and Cracker Jacks; spectators today require a whole lot more of their outings. Today’s spectator experiences—from sports to concerts—are more social than ever, with plentiful other activities to choose from while you’re onsite as well as the ever-growing option to upgrade, upgrade, upgrade.
“Traditionally on the lower level you had the general admission seating, then the club suite, and then upper level general admission. That was the standard for most outdoor stadiums,” says Sean O’Leary, vice president of sales and marketing for Hussey Seating, a top manufacturer of seating across sports and entertainment venues.
“Similarly with indoor arenas you had three seating differentiations—general admission, club, and suite. Now we’re seeing numerous seating areas, seating zones, different chair styles, different price points, and a really differentiated experience for fans.”
College games are feeling more like pro games, and the opportunities for shopping, dining, and socializing in areas around pro stadiums are expanding, too. “Almost all these new venues are adding an entertainment district around it to generate more revenue on off-game days,” O’Leary says.
Designing Excitement
Architect Jason Michael Ford has worked
with Populous since 1996, helping to shape experiences everywhere from Phillies games to countless minor league parks and more. “Thirty years ago everyone was talking about capacity—the number of seats and the number of suites. That was the focus of a lot of projects early on. If you look back at buildings from the ’90s and 2000s, people thought the number of seats in general transcended to revenue.”
Today’s designs are focused more on providing a variety of social experiences, Ford says, adding that some are so special people will pay more for them. “We’re seeing a lot more social areas—so less fixed seating and more flexible seating—and open stand-
ing room areas where people can be with their friends. People want their experience in a venue to be different when they’re with their family, when they’re with their friends, when they’re with their coworkers. These facilities have to have price points and seating areas that cater to those different experiences. Take a Major League Baseball game, for example. If you’re going to 40 of the 81 home games, you don’t want to have 40 of the same experiences; you want to have different experiences.”
Populous’ Geoff Cheong has been focused largely on the arena market for the last decade, with projects like T-Mobile Arena in Las Vegas and Climate Pledge Arena in Seat-
tle (pg. 282). “There is a focus around creating these incredible experiences within our venues,” Cheong says. “One of the trends we’re seeing a lot in arenas is so much focus on experiences throughout the building other than the game or the concert or the main event you’ve paid for. People want to be able to explore the venue and experience these different activation zones and sponsor zones.” When designed well, these additional, tangible moments stick with patrons long after they leave, too. “It’s really driving additional revenue for our clients and operators as well.”
Cheong says Populous has put a lot of attention on evolving the actual in-seat experience in its arena designs, too. “We spend a lot of time creating a variety of seating experiences because, again, like Jason de-
scribed, a lot of folks are looking to come to a venue time and time again and not wanting to do the same thing. They want to feel like they’ve had a different experience. They want to see the game or the action from a different vantage point, and they honestly want to even sit in a different type of chair. A standard folding arena chair is just one of the many different types of ways you can consume the event. We’re doing everything from individual, comfortable lounge chairs with arm tables or side tables to banquette seatings or even sofas or couches that are very unique ways to witness an event.”
Modern arenas and stadiums are being designed to be so much more than a place to watch a concert or game. Many are designed
to be able to host various types of events. That’s where options like telescopic seating comes in, as it allows for maximum flexibility of floor plans.
“We go in and custom design the telescopic platforms to fit the allowable space, and we spend a ton of time upfront with the architect, designer, and the operators when available to really understand their needs,” O’Leary says. “Then we design the product to be able to not only accommodate those events but everything else they throw in, from rodeo to concerts to mixed martial arts, you name it. We really try to do more listening upfront around how the facility is going to look given every different scenario. With the telescopic retractable seating they can really change the seating capacity and the setup based on the events.”
Cheong says the industry has been challenged for many decades by how to maximize utilization in large-scale sports and entertainment venues. “The ultimate goal we constantly strive to design around is how do you as a client, as an operator, have more event days than non-event days? And how do you achieve that degree of flexibility and adaptability for a wide array of events?”
In addition to retractable telescopic platforms Hussey offers a broad range of fixed-seating options—from basic to super high-end. Designers have a seemingly infinite array of chairs to choose from in the categories of fixed, beam, and telescopic depending on what style, fabric, seatback, and even color is desired. The company recently acquired Camatic Seating, too, further adding to their portfolio of options for a one-stop shop with beam-mounted seating as well.
An increasing number of designers are also looking to specify more comfortable, upholstered seating on retractable platforms—something you couldn’t do 10 years ago but can today. Climate Pledge Arena included Camatic seating and was a highly competitive bid, O’Leary says. “The design team of Populous, Oakview Group, and Icon really put all of the players under the microscope,” he says, adding that the chosen Camatic chair was part of the arena’s overall sleek design. “It was the same chair that was on the retractable telescopic platforms as in the fixed seating bowl behind, and then different chairs used for suites in their upgraded areas. It’s a really good look, and it was a lengthy selection process and a great win for Camatic.”
The main difference between installing a fixed stadium chair versus a beam mount stadium chair is that on a Hussey fixed stadium chair, where there is an armrest between each chair it’s also attached below to the concrete, O’Leary says. “If the chair was a 20-inch wide chair, you’d have two anchor bolts every 20 inches. With beam you only have to anchor it on average every 40 to 48 inches, depending on the layout of the facility. You’ve got half the anchor bolts, so your installation time is much less.”
The flexibility of beam mounted chairs leads to a longer life, too. For example, O’Leary says the Seattle Seahawks Camatic installation is more than 20 years old and going strong. Beam mounted also means an older stadium, say like the Chicago Bears’ stadium, could upgrade its seats or add drink tables without having to touch the beam, he says. “The beam is probably 40% of the installation cost.”
Hussey takes care of its customers long after installation, too, with a full service and parts department. They’ll continue to help with maintenance if needed and even help solve problems with a competitor’s products. That said, O’Leary says you get what you pay for. “It can be very competitive out there, and if a GC wants the lowest price that doesn’t necessarily serve the operator well for the next 8 or even 20-year lifespan, then that early savings didn’t turn out to be a savings.”
The Populous-designed Atrium Health Ball-
ABOVE Atrium Health Ballpark opened in 2020, 35 minutes outside of Charlotte, North Carolina.
RIGHT The Minor League ballpark is a great example of plentiful options, with a family seating area, box seating, elevated sky lounge, and even suite banquet space that can be rented on non-game days.
“There is a focus around creating these incredible experiences within our venues.”
park opened in 2020, 35 minutes outside of Charlotte, North Carolina, and includes Hussey Seating with a capacity around 5,000 seats. The Minor League ballpark is a great example of the trends happening today, O’Leary says, with a family seating area, box seating, elevated sky lounge, and even suite banquet space that can be rented on non-game days.
Outside of the seating area are even more designed experiences, like kids zones with a splash pad and walking trails around the stadium. “It’s all about getting people there not just to watch a ball game, but when you come to watch a ball game, you’ve also got multiple choices of how to do that.”
The site placement of that park is another win, Ford says, as the ballpark acts as an anchor bringing people downtown. Atrium is highly accessible to the public. “What’s probably most unique about this ballpark is it truly is a park,” he says. The concourse is open every day, and people walk it on non-game days, too. “We’re really proud of that ballpark.”
Atrium was named 2022 Ballpark of the Year by Ballpark Digest, in part for its beautiful grass berms, home run porch, and other amenities open to the community yearround. Its right field acts as an extension of
the main street development, and the park is open from dawn to dusk daily for use as a public amenity.
Designing for spectators must not just be inviting and exciting, though; it must truly be accessible, and the idea of inclusive design is evolving, Cheong says. “If you are a person with a disability, how do we make a really positive experience for you within not only the venue but the seating bowl and where you’re watching that from. If you’re with young children, same thing. In the arena it’s a very important focus of ours right now, especially with renovations. We’re spending a lot of time in the world of renovations for buildings that were built before the early ’90s, when ADA code came into play. A lot of expertise and focus is required to make older venues really comfortable, accessible, and meaningful for that user group.”
He says accessible, inclusive design is what sustainability was like 20 years ago. “It’s going to be the next wave of focus and conversation in the sports and live entertainment industry,” Cheong says. “The saying is that there are two types of people in this world—people with disabilities and those of us who haven’t discovered ours yet.” gb&d
How expectations of restrooms are changing—and how designers can adjust
WORDS BY SOPHIA CONFORTI
For travelers the airport is the gateway to a new city—a launching pad to adventure, relaxation, or business. But current research suggests that the design and cleanliness of an airport is also reflective of the destination itself.
One major point of impact: the bathroom.
The bathroom is a universal experience at airports and commercial buildings all over the world. About 92% of people surveyed say they expect high-quality bathrooms in high-quality businesses, according to research from Bradley Company, a leading manufacturer of commercial plumbing fix-
tures and washroom accessories. Yet almost 70% say they have had a negative bathroom experience. And in commercial buildings, a dirty or poorly perceived bathroom can cost you business.
It’s true—34% of respondents said they will leave without doing business if they don’t like the restroom. Compare that to 62% who would frequent a business knowing they have a nice restroom and 59% who said they would spend more money at a business they know has clean restrooms.
“We all use restrooms, and so when we walk into a space that’s really nice, we
remember it. And if we walk into a space that’s really bad, we also remember it. The restroom is a direct reflection of the business,” says Yang Clark, senior business development manager at Bradley. “If you’re not paying as much attention to the restroom as you are making the lobby look nice, you are ultimately impacting your business’ profit and revenue.”
Features of a Well-Designed Washroom “Bathrooms are very important to the overall guest experience. At the heart of what we do as designers, we try to be good
hosts—and help our clients be good hosts in their own facilities,” says Wesley Crosby, senior principal and interior design director for the Americas at Populous.
But despite consumers’ desire for well-designed, clean bathrooms, in many cases their expectations remain low. “Traditionally people see restrooms as dirty, dark, and sometimes not safe. Most people avoid it if they can,” Clark says of some commercial restrooms.
So, how do you design a washroom where people can feel safe, comfortable, and actually enjoy the space? “People want
restrooms that have a nicer look and nicer feel. Aesthetics can easily elevate commercial spaces, but then you also have to consider sustainability, whether it’s easy to maintain so it can continue to look nice, and if it’s accessible to all people,” Clark says. “A well-designed restroom has to have all of these things. As a supplier we try to develop solutions to help businesses achieve that.”
From the consumer perspective three other bathroom elements are also important:
1. Privacy
70% of Americans want more private washrooms. And it’s not just a preference—it’s a safety issue.
“The international market has always been much more private than the US. A lot of times when you walk into a commercial restroom, you can see people through a big gap. You can see their legs. It’s not very protected,” Clark says.
Floor-to-ceiling privacy walls like Bradley’s Euro Style Partitions are becoming more common to offer a private restroom experience, ease user discomfort, and increase washroom safety.
“Some people are anxious about going to the restroom. People are much more relaxed when they feel safe, and privacy walls offer that,” she says.
2. Touchless Technology
Coming out of the pandemic, no one wants to touch anything in the restroom, Clark says. In fact, the survey found that 86% of Americans believe it’s important for public restrooms to have touches fixtures. But in traditional restroom design you often have to touch everything—opening and closing doors, flushing toilets, turning on and off faucets, pumping soap dispensers, hitting buttons or turning knobs on hand dryers and paper towel machines.
The push for touchless makes washrooms more hygienic, yes, but it also ushers in an era of smart bathroom technology that improves cleanliness and facility operations.
Many commercial washrooms are high-traffic areas. With an influx of patrons, people washing their hands may get water on the sink or floor while shaking their hands to dry. That water buildup can cause accidents, which puts the onus on maintenance teams to clean more frequently.
“About 75% of restroom complaints are about general untidiness,” Clark says. “The smart restroom uses technology to help reduce maintenance and keep washrooms safer from spills, slips, and falls.”
It’s one reason why Bradley was driven to create WashBar®—a touch-free water, soap, and hand dryer solution that combines all three functions into one product. WashBar keeps water to the sink basin because users
don’t have to walk from sink to soap and hand drying stations. It’s all in one right in front of them—which comes with the added bonus of improved bathroom flow.
“Traffic flow and hands-free fixtures can create fewer contact points and reduce opportunities for transmission of germs,” Crosby says. “Eliminating doors where possible can also speed people’s movement in and out of the space while minimizing transfer of germs.”
However, in a major reversal of traditional bathroom design, no longer are bathrooms merely meant to serve one function and be do-your-business-and-get-out spaces. Many are designed as comfortable, even luxurious destinations in and of themselves.
“In the old days when we traveled, for example, we would go to the airport, and your vacation began when you got to your destination. The younger generation now, they start from the minute they leave their home. They want to enjoy everything from the moment they leave the house to when they arrive,” Clark says. “It’s the same for sports, for all commercial buildings. People want the whole experience. So a lot of these facilities now need to provide that
enhanced user experience so they can be a whole experience.”
Crosby agrees. “Bathrooms have an ability to enhance or detract from the overall experience. Design has been democratized and there’s a higher level of expectation from everyone—a spectacular bathroom can be the cherry on top of a memorable experience,” he says.
For designers this new vision of a restroom means reimagining what a bathroom can be—both in terms of function and artistic expression—and more creative freedom. Biophilic design, lighting, color—all of these elements can create a more comfortable, modern washroom experience.
Bradley’s Elvari™ washroom accessories collection, for instance, brings minimalist, functional luxury and design cohesion to the bathroom experience across the collection’s 650 individual products—including grab bars, paper and soap dispensers, waste receptacles, LED mirrors, hooks, shelves, and more.
The point is: It’s all in the details. “Restrooms can be multipurpose and can look and feel like a modern experience when designed with intent,” Clark says. “When you go into a nice restroom, it’s a surprise. It’s uplifting rather than depressing.” gb&d
Bradley’s new suite of Elvari washroom accessories creates a cohesive and modern look to take commercial washroom designs to the next level.
“They want to enjoy everything from the moment they leave the house to when they arrive.”
THE GENSLERDESIGNED 167 GREEN STREET IN CHICAGO WAS DEVELOPED BY SHAPACK AND FOCUS WITH ABUNDANT OUTDOOR AMENITIES.
The line between indoors and out continues to blur with inspiring designs.
BY LAURA ROTE
Buildings today are like ecosystems. They no longer stand alone, disconnected from their surroundings, serving one purpose. They do so much more. At least, that’s how Brian Vitale, co-managing director of Gensler Chicago, thinks of them.
“They are much more extroverted in that they’re always reaching out beyond their walls, right? The buildings are more porous—and not from a water standpoint.”
There’s no longer one way to enter, one exit, but there are multiple points of entry and egress and much more activity in modern commercial, higher ed, and even hospitality projects. “People love that connection between the interior and the exterior; that’s getting blurry. And that blurring is really important because people want to have that freedom.”
That persists year-round, too, even in places with four distinct seasons like Chicago. Take the 167 Green Street building in the hip West Loop/Fulton Market area in Chicago, for example. Designed by Gensler and developed by Shapack and Focus, the project pushes outdoor views and access to the next level, from the incredible roof deck to pockets of green space and connection to community— complete with a large outdoor space that hosts everything from food trucks to concerts. A firepit and comfortable outdoor furniture invite people to hang out, and there’s a feeling of liveliness, including art, at every turn. “There are little places for everyone to be,” Vitale says. “It’s so inviting, and you start to blur the line between indoors and outdoors because you can see everything.”
The most successful outdoor spaces are truly flexible, Vitale says. “You have to keep them almost purposely ambiguous because you want to be able to do a lot with them. You can’t just say, ‘This is where you sit, and this is where you eat.’”
Vitale says one area outside 167 Green has taken on a life of its own, and the possibilities are endless. “It’s no longer you go outside and you’re just outside. You can go out there and work. There’s Wi-Fi out there, there’s music, there’s food. It’s about extending these buildings outward.”
The LEED Gold 167 project is 750,000 square feet—13 floors of office space above two partial levels of parking and ground- and second-floor retail. The project is defined by a pedestrian-only thoroughfare that cuts through the building and connects to other streets bustling with dining and retail. On the roof deck with views of downtown Chicago an NBA size basketball court opens onto a large terrace with prairie plants.
He says that while blurring interior and exterior space is important and creating space that is flexible will make it more useful, defining boundaries also ensures the space will succeed.
“These boundaries can be defined by the building, hardscape, furniture, or landscape, all providing a sense of space and dis-
tance, not just vast openness. People want to understand their boundaries and feel the embrace of space,” he says.
When he thinks about successful outdoor designs, he looks to Mies van Der Rohe’s Barcelona Pavilion. Completed in 1929 the project seamlessly connects space and blurs the line between interior and exterior.
“The two become symbiotic and invite users to meander between them. This is what makes engaging exterior spaces— when they are treated as part of the design, not as leftover space,” Vitale says. “Some of these spaces may be designed with a specific function, but we see the most usable space being designed to be flexible, allowing for many types of uses and programs.”
Recent educational projects have also found success in designing flexible outdoor space, as many universities look to design environments that set students up for success after graduation. Many have taken inspiration from the design of modern commercial projects. “It’s a much easier transition for students to go into the workforce if they’re used to these types of spaces,” Vitale says, noting both the demand for exterior spaces and an emphasis on amenities.
Gensler recently completed a number of education projects that all heavily feature outdoor amenities, including work at the Wichita State University Barton School of Business, which includes a prominent bridge feature that doubles as a metaphor for a student’s academic journey. “The buildings in higher ed used to be very inwardly focused. It was all about focusing on the teacher. Now it is much more holistic; they want you to be engaged with what’s going on in your surroundings.”
But it doesn’t just stop at the building site, he says. The considerations continue, from what neighborhood a project is in to whether there is a great coffee shop nearby. What about a park? “That’s what I mean when I say these buildings are much more extroverted. They have to connect to their surroundings in a much different way than they used to, where we would just design pretty buildings and they would be their own thing.”
Collaboration starts early and includes partnering with landscape designers, he says, to ensure transitional spaces are just as thoughtfully considered. Gone are the days of simply walking from sidewalk to door to elevator. “We try to make that a much more experiential moment. You
have this in-between moment,” Vitale says. “It’s like a porch on a house; you’re not part of the street, but you’re not inside the house. It’s working with the landscape designers to create not only the landscape but to create spaces so the building extends beyond its own four walls.”
At Wichita State University Woolsey Hall the pedestrian bridge is all about meandering. “You can see it’s not a point A to point B bridge; rather it takes you in a much more experiential way around so you’re getting multiple views,” Vitale says. “When we’re thinking about outdoor spaces we’re not thinking about just creating this formal thing but about how do people experience it? This bridge takes them on a sort of curved journey so they’re seeing different points of the building and the landscape.”
There’s also a place where people can get off the circulation path but still be on the bridge to study, eat lunch, or just hang out. “The students will start to take these elements and make them their own. These things just happen naturally,” Vitale says, adding that it’s since become the top spot on campus for graduation photos.
The design team aims to create vistas that, yes, ultimately guide you or invite you to a place that’s welcoming, but also provide beautiful views and places to relax. Vitale likes to say not all architecture has windows and doors.
School designs like this Gensler project at Wichita State University are focusing more on preparing students for what’s next—including life in a potential bustling workplace.
As people crave more time outside and even some classrooms move outdoors, he expects these conversations will continue to evolve. Architects and designers will keep looking for ways to make more flexible, inviting spaces—whether it’s for outdoor yoga or a safe place to protest.
“We’re not necessarily designing the building, but we’re designing the experiences,” Vitale says. g
Comfortable, efficient outdoor spaces people really want to use
BY LAURA ROTE
As more and more people want to be outside for all types of activities in all kinds of spaces across four seasons, it’s important to design so people feel comfortable staying awhile, according to Brian Vitale, co-managing director of Gensler Chicago. He and his team often ask: How do you design outdoor experiences that are comfortable and inviting?
“We know from research that just having a view of nature and the outdoors improves people’s well-being, their capacity to think and be productive, and improves their overall mood. Being able to access outdoor space—a function that is one of the highest-ranking amenities a building can offer—increases these outcomes exponentially, even in cold weather climates, and thus makes properties more desirable and thus easier to lease, higher rents, and better performance,” Vitale says. “If you
are a part of a campus, a variety of large and small spaces is typically easy to achieve and expected, but in an urban context, any outdoor space, even the smallest of areas, will improve the well-being of its users and see heavy use.”
Bromic’s infrared outdoor heaters (seen at left) are one solution helping to make spaces comfortable year-round.
Vitale says comfort and security are major factors in designing successful outdoor spaces. From providing shade in the summer to allowing enough sun to wash over a space in the winter, the right placements make a space more usable year-round. “You must also build a variety of seating options, not unlike a workspace, into the design of outdoor space. Areas for groups to gather to eat lunch together or hold a meeting are paired with places where people can be alone to recharge or just people-watch,” he says. “We also focus on the outdoor ‘ceiling’ or the variety of datum lines that compress and expand outdoor space. This is achieved with different types of tree canopy heights (where one might circulate versus where one would sit to have a meal), outdoor structures, and even, of course, lighting canopies. This variety makes the outdoor space more comfortable for the users and enhances their experience.”
Vitale says outdoor spaces are increasingly having the comforts of indoors, from highly functionable furniture that make it easy for people to work or socialize to outdoor kitchens and technology like video screens. “Large spaces to gather with a crowd to watch a game together, easy access to food and beverage, and flexible seating are becoming the norm even in colder winter climates,” he says. “We have the capabilities through different heating strategies to keep people comfortable, making this strategy applicable 365 days a year.”
As the line between indoors and out continues to blur, manufacturers have seen the need for solutions to make more comfortable spaces year-round, too. “Demand’s at an all-time high.
“ People want to be comfortable, and they want to be able to use those spaces year-round .”
Demand for year-round outdoor spaces is at an all-time high across hospitality and residential.
Restaurants, hotels, and high-end luxury residential properties traditionally have always wanted this solution, but now we’re seeing new spaces we’ve never seen before,” says Blake Petty, commercial specification lead at Bromic Heating. “People are trying to heat outdoor workspaces because—especially now with technology, you’re not stuck in a cubicle in your office. You can take that meeting or call outside.”
Even in Chicago Vitale says people are committed to being outside as much as possible. They just dress for it and go where they know will be comfortable. “There really has been no pushback in this climate to outdoor space. There’s no one who says, ‘Why do we need outdoor space? Just give me a sealed up building, and I’ll be fine.’ They all want to have access to the outdoors.”
Both Vitale and Petty have seen universities increasingly demand outdoor spaces that act as year-round community spots to gather. Multifamily projects, too, want not just the ability to heat communal spaces but individual patios. “People who can’t necessarily afford to buy the house with the yard still want a private outdoor space, and they want to be able to use that year-round. Now with technology and multiple manufacturers investing in this space, there are solutions that didn’t necessarily exist for them 10 or 15 years ago,” Petty says.
Bromic’s infrared outdoor heaters in gas, electric, and portable models are one solution helping to make spaces comfortable year-round—and more efficiently, with the capability of zone heating.
The outdoor heaters balance heat output, light output, and energy extended, and intelligent design lets you direct heat exactly where needed. Consider a restaurant, where in the past you may have had 15 propane-powered mushroom heaters on a patio. “You had to turn them all on to start the shift and wait for people to show up. Now you’re heating this entire patio and you’re burning fossil fuels. With zone controlling and electric infrared, at the flip of the switch the heater’s on and it’s at full power within 30 seconds,” Petty says.
Heating and cooling indoor spaces at all times, even when not in use, can be extremely wasteful. Outdoor spaces with
Bromic offers an opportunity to heat spaces more efficiently, too, with the capability of zone heating.
added outdoor heating solutions can be separated into zones so heaters will only be turned on in areas where people are, contrary to indoor commercial spaces that often have just a single HVAC system constantly running.
Zone heating, scheduling, and timers as well as dimmability make for much more efficient heating. And now you don’t have to depend on people remembering to turn heat off or on at all. “We are focusing the heat where it’s intended,” Petty says. “With a traditional convection heating system you’re heating the entire building regardless of who’s in it, when, and where. With infrared heating it’s spot heating.” Petty likens Bromic’s infrared heating, which uses parabolic reflectors to direct the heat on to a target, to a flashlight; you point the light where it needs to go. “It’s a much more efficiently designed product so maybe you don’t use nearly as many
heaters and you can directionally focus where it’s needed.”
In October Bromic unveiled its new line of controls, which includes the ability to turn heaters on/off remotely, dim heaters, set timers, schedule functioning hours, create heating zones, and more. The appbased control gives people even more flexibility and comfort. “It has a control modular or box that the heater is wired into and then from your phone or smart device there’s a Bromic app. You have complete control of all your heaters—from scene setting to timing to dimmable control with electrical heaters.”
It’s a huge perk in commercial or rental properties, as you can turn off heaters when no one is there. “We are the only manufacturer to have our own app-based controls. Some of the others rely on a third party and you have to buy another accessory to have those communicate.”
It integrates seamlessly with other building or home automation systems, too.
While Covid drove people outside, Vitale says much of the demand for outdoor spaces was already happening. The pandemic just heightened the need. “Although we were doing this before, it made it much more commonplace—and not only commonplace, but people were starting to really request it so we had to have outdoor spaces.”
Petty agrees that the pandemic, while terrible, opened up a whole new world, and the demand for outdoor spaces is here to stay. “Outdoor spaces are no longer an afterthought. You can no longer just stick some pergola structure on the side of a building,” he says.
The line between indoors and out will continue to blur, too, he says. “People want to be comfortable, and they want to be able to use those spaces year-round. Start thinking about how you properly cool them in the summertime and how you can properly heat them in the wintertime.” g
Bromic’s infrared heating uses parabolic reflectors to direct the heat on to a target so you can focus where it’s needed.
BY LAURA ROTE
There’s no denying it; more of everything is happening outside. It’s not just dining al fresco. Many people are also aiming to work, study, and socialize outdoors as much as possible—and year-round.
“People are doing more things outside. Now we even have classrooms outside,” says Brian Vitale, a co-managing director at Gensler based in the Chicago office. “It’s no longer, ‘Here’s some outdoor space. Do with it what you want,’ but rather how can we tune these spaces so they can be programmable?”
From outdoor yoga at college campuses to workspaces where people meet and want to stay awhile, more people are demanding dedicated space beyond a bench outside. “Things have been magnified really since Covid,” Vitale says. “How do you design these spaces so they’re comfortable and inviting?”
Gensler knows lighting is a big part of the conversation. It can often make or break an environment. “It’s incredible what the right type of lighting does for these spaces. When you talk about technology, that might be the biggest leap we have made—the ability to light spaces properly with new technology, where people feel much more comfortable using them after hours. We talk about winter being cold, but it’s also short days, right? We want to make sure people feel safe in these spaces, and lighting is key to all of that.”
A good lighting designer can make lighting seamless, too, Vitale says, if that’s the goal. “When LED lights first came out they were really bright white; your kitchen looked like you could operate in it. The technology has come so far now it can be softer and feel much more flexible. In certain conditions you do want the bright light, but it’s much more flexible. The fact that you can gently illuminate a space and make people feel comfortable is incredibly important.”
WAC Lighting’s new Colorscaping system includes tunable white light as well as color changing illumination for landscaping.
WAC Lighting knows firsthand the capabilities of lighting, having been in the industry for 40 years and watching it evolve up close as part of their own R&D efforts. For example, WAC Lighting developed human-centric tunable white fixtures that replicate the natural light of the sun, which benefits people’s health and well-being.
Most recently WAC unveiled its Colorscaping lighting system, which includes tunable white light as well as color changing illumination for landscaping. It’s the latest in a long line of indoor and outdoor lighting, smart ceiling fans, and more from WAC as well as its brand Modern Forms.
The new Colorscaping system takes lighting to the next level, says Todd Goers, an expert on landscape and outdoor lighting who works with WAC Lighting. In the past it was a big deal if a homeowner didn’t like the look of their lighting once installed; a contractor might have to go high up into a tree to change a fixture. With the Colorscaping system and app, homeowners or installers can adjust lighting from their phones or tablets. “Once those fixtures were installed in the past that’s what you had. It was a big deal for a homeowner to say, ‘I don’t like the look of this,” Goers says. “It took a lot of work to go back and make a change. Now with the introduction of Colorscaping it’s as easy as clicking a few buttons then saying, ‘How do you like it now?’”
Colorscaping also makes the whole moonlighting process safer (less climbing), quicker, and more affordable, as time is money, he says. “This product has really given us a lot of flexibility and
control, which really was not there before we brought this product to the market,” Goers says.
The person with the app has more control—whether it’s a residential project or a commercial building owner. “Everybody can control lighting color schemes or light intensity when doing outdoor lighting,” says Tom Lillie, executive director for specification lighting for WAC Lighting. “Especially when you look at our Colorscaping product—it is like a blank canvas someone is painting. With color tunability we can make your landscape pop with white light ranging from warm 2700K to cool 6500 Kelvin. In addition, you can choose from over 16 million colors with our virtually unlimited color palette. You really can make the environment beautiful.”
The technology can be used in virtually any setting, from entertaining at home to setting school colors for an event at a university or making wedding colors feel even more special. “It’s something not everyone is going to have, so maybe it’s a little bit of vanity, too,” Goers says. “Like, ‘Hey, look what I can do with my lighting system.’”
While the colors are seemingly infinite, Goers imagines most of the time the Colorscaping line will be used in variations of white when at home. “I know there are a lot of contractors who are buying this product from us today who have no intention of moving the lights to color; they just want the tunable light aspect, which is interesting, being able to change that,” he says. “You can change every fixture to a different color temperature using the same app, or you can group them to have certain sets of fixtures doing the same thing. The possibilities are endless, and that makes it fun. You could dedicate your life to playing around with your lighting system.”
As many people continue to work at least some of the time at home, solutions like these as well as Modern Forms’ outdoor-rated ceiling fans make working outside a more comfortable option. “The people I’m talking to are sitting on their patios under the pergola, enjoying their home office,” Lillie says.
Home-like environments and natural materials are expected to continue to be in demand, too. People are blurring the line between indoors and out, Lillie says. WAC Lighting offers the full gamut of outdoor decorative and functional lighting to
complement their indoor offerings, too, from sconces to bollards to post lights and more. Both inside and out people are looking for more organic materials in their designs—like wood, stone, and even crystal, Lillie says. WAC is developing new outdoor products, including concrete sconces, to meet this demand and add to their already existing line of biophilic-inspired offerings like wood sconces.
WAC Lighting is also committed to using sustainable materials in its designs with no waste at its dedicated factories.
When WAC Lighting first entered the landscape space nearly a decade ago and revealed its adjustable, tunable products,
WAC Lighting offers a full range of outdoor solutions, from its new Colorscaping system (complete with app) to wall, outdoor ceiling, step and wall lights, LED tape, post lights, landscape lighting, and more.
they were unique compared to anything else on the market, Goers says. He remembers showing people how they could adjust the beam angle and the brightness right at the fixture with a screwdriver; people loved it, but their first questions were often about cost.
“I think higher cost is one thing people think about our product line that is not true,” he says. “Our products are made at our dedicated factories, which only produce WAC’s products. A lot of people
in the landscape lighting space do not have this luxury. They are going overseas and finding somebody to make products to their specifications, then paying that markup, which then gets another markup when sold to distributors.”
Lillie says many other lighting manufacturers buy product and private label it from the same factory so it goes out one door as company X and comes in another door as company Y. “Not only is price a big issue, but quality, control, and consistency when
somebody is going overseas and buying product from who knows what company.”
WAC offers consistency, he says, as they use the same chips to make the same product each time. It’s the same light, with the same finish, and the same caliber, Lillie says. “We have control over the quality, and it is top-notch. I’ve been to the factory, and they really go that extra step. And if someone calls up with any issue, we have the support to handle it. We know our product because we’ve developed our product.” g
BY LAURA ROTE
Now more than ever people want to live, work, play, and socialize outdoors. We’re drawn to more natural surroundings,” says David Schutte, president at Tuuci, a global leader in sustainable, luxury outdoor shade solutions.
Schutte says it’s an energizing time in outdoor design, as more and more people continue to rethink what it means to embrace the outdoors. “Exterior design is no longer an afterthought. It’s an integral part of the planning process.”
Architects are seeing this demand for outdoor spaces from the beginning of project conversations, too. Brian Vitale, co-managing director of Gensler Chicago, has worked with Gensler for 18 years and says choices like the right shade, lighting, heating, and even plant life are crucial to ensuring outdoor spaces are used and loved.
“Shading is so critical. People design all these outdoor spaces, and if you don’t focus
on people’s comfort, they’re not going to get used,” Vitale says. Where some outdoor designs used to simply include trees and little more, he now sees more landscape furniture, beautiful canopies, and clever, inviting solutions that make people want to stay and hang out. “People are much more in tune to the sustainable aspects of this,” he says. “Native plantings that are not just formal and beautiful, but thinking about how does this work with our climate? People pay much more attention to that.” It makes places much more welcoming, too, he says.
Tuuci furniture leverages more than 25 years of leadership in the outdoor world to create a versatile, nautically engineered set of collections that enhance indoor and outdoor living.
More than 25 years ago Tuuci was born out of a need for something great. That was when now-CEO, founder, and chief product designer Dougan Clarke was casually selling outdoor commercial furniture—including umbrellas he considered subpar. Clarke was born and raised in South Florida; he loved to tinker almost as much as he loved the water. He was working in the back of a friend’s boatyard when he started experimenting with his own product and formed what would ultimately become Tuuci—or The Ultimate Umbrella Company Incorporated. “His idea was to create umbrellas that last—that didn’t just become garbage,” Schutte says.
Now, instead of throwing a parasol away after one bad rainstorm, people can choose Tuuci solutions; they last so long people are ordering to replace damaged parts many years later and keep them even longer. “The best sustainability is always in the products that endure, that don’t have to get rec ycled, and don’t go into a dumpster,” Schutte says. “This is not fast furnishings.”
Schutte says Clarke created a company culture based on curiosity, creativity, and exploration, his eyes always on the future. “He created products no one even knew they needed; that’s the brilliance of a creative thinker.”
Today Tuuci works with clients to create bespoke projects, too, including customizing for projects to feel like a series of rooms outdoors. Designing and defining an outdoor room can be
challenging, as there is a lack of natural definition provided by walls and ceilings. Tuuci has products to help create outdoor destinations and define spaces, whether designers choose a couple of soft-sided cabanas, a louvered, marine-grade aluminum cabana complete with power outlets, or a mix of solutions.
Design teams are looking for flexibility, Schutte says, whether it’s a corporate environment, higher ed space, or hospitality. “We’re thinking about utilization rates of the spaces you’re creating, and if you’re in hospitality, how are you monetizing that space?” he says. “The goal for many people, and it’s clear in the lessons we’ve learned over the decades, is creating magnet spaces for groups that attract and welcome users. How do you create spaces that people want to be in?”
Today there is a growing push for a seamless transition from indoor to outdoor, from the look and feel of wood to connecting to nature at every turn. It’s creating spaces that are thought of holistically. “Tuuci’s mission is to help people live their best lives outdoors. It’s simple, but it’s hugely profound,” Schutte says.
Having spent a lot of his own career in office meeting rooms, Schutte can testify to the desire to get outside. “Nobody wants to be in a conference room,” he says. “Good planning creates compelling spaces that are also highly functional and highly utilized.”
As more people work, meet, study, or simply relax outside, Schutte says the standard shade umbrella of old won’t do. “You can’t all be huddled where half the
people are under an umbrella and half are baking in the Scottsdale sun.” Tuuci’s cantilevered umbrellas omit the center post, allowing for more flexibility and more coverage, for example. “People are looking for larger, more agile spaces,” he says.
Tuuci’s MEGA MAX parasols span up to 24-by-24 feet. “That’s the size of a studio apartment. It’s almost 600 square feet,” Schutte says.
In November Tuuci introduced its Ocean Master Max Solanox cabanas, which can be used to design a lounge space, dining room, or any number of configurations of spaces. “That’s going to provide up to 14-square-foot spaces uninterrupted by columns. That’s a pretty big room,” Schutte says. It’s also engineered to withstand high sustained winds of up to 45 miles per hour and gusts up to 75 miles per hour.
This “little architecture” supports the larger architecture of space when done correctly, Schutte says. “If you think about hierarchy of space and sight lines and creating topography outside, particularly when people are planning rooftop or other areas that are just inherently flat, how do you create a natural topography? Cabanas provide different sight lines.”
Gensler is always thinking about sight lines and how to draw people in, including with their Wichita State University Barton School of Business project (pg. 340). “How do you design these experiences so they’re comfortable and inviting?” Vitale says.
Gensler designs outside to create vistas with a purpose. “This is taking you directly to the business school,” he says, pointing to a popular pedestrian bridge and seating area outside the business school. “We can control what you see. We don’t want people to think about that, but they’re experiencing it. They get these beautiful views, and there’s some of that outdoor furniture. It’s architecture itself, but it doesn’t have doors and windows.”
From palm trees to cabanas to umbrellas and chaises, outdoor spaces can be designed to hold visual interest with different dimensions. With Tuuci designers can choose various iterations of open or closed roofs or walls with louvers, various trellises or curtains, and mix hard and soft elements and more for flexibility in enclosure and opacity. Add to that elements like sustainable lighting, ceiling fans, and TVs, and many people won’t want to leave.
Weatherproofing begins with shade, as that’s one quick way to reduce how hot a person feels, says Schutte, pointing to a recent article published in The Atlantic called “Shade Will Make or Break American Cities.” “Blocking the sun can lower how hot a person feels by 36 to 72 degrees,” he says, referring to the article. “Shade is significant in terms of how to keep a space as relevant at 3 in the afternoon as it is at 7 at night.”
Outdoor structures with roofs can make a space viable for longer, both with protection from sun as well as rain or other elements. Add lighting and study sessions and hangouts can last well after dark, too. He says heaters help a lot, too, in cooler months. “How do we help architects create spaces that can be optimized over the greatest period of time?”
There’s a reason many hotels, resorts, and restaurants are seeking luxury shade solutions with all of these benefits, Schutte says, and that’s because the stakes are high.
“If their outdoor space is not functional and it doesn’t work for their clientele, it literally doesn’t work. It renders spaces unable to properly be used,” he says. “It goes back to how to maximize the utilization rate of spaces you’re creating. If there’s not proper shade or protection, if you suddenly don’t have shade for 30 people at the pool or a restaurant that doesn’t have shade for protection, all of a sudden that outdoor space doesn’t work and they can’t monetize it.”
Anyone living in Chicago or Seattle knows, for example, when it’s a nice day, people want to dine outside. “People go where there is outside seating,” Schutte says. While some people may consider Tuuci expensive, Schutte says it’s an investment that’s going to have a long life. “These are investment pieces that stand the test of time; they are not disposable. If something breaks we can replace that particular part. It’s something you want to use well beyond one season.”
Inspired by Nature Marine-grade engineering and construction is evident across Tuuci’s offerings, from Aluma-TEAK—a high-performing
replication of wood f inishes—to the high-performing MEGA MAX that stands up to tough storms.
Schutte points to Aluma-TEAK as yet another example of indoors moving outdoors, too. “It has that compelling visual and sets a more residential tone people like in commercial environments,” he says. While it looks like wood, this finish is maintenance-free and available in six weather-resistant wood looks—Java, Natural, Driftwood, Weathered, Cypress, and Aspen White.
Schutte says materials and finishes like these are designed to withstand the harshest conditions while meeting a range of aesthetic needs. “People like the look and the warmth of wood, but they don’t like the care, particularly in commercial environments, because there’s no one to care for it. Aluma-TEAK provides the look of wood without the hassle, and it does not fade or scratch over time.”
Tuuci also launched an extensive furniture range in October 2024, including four deep seating collections: Luma, Sail, Horizon, and Sola, supported by multiple sun lounges, tables, and benches. Each collection is designed with flexibility and customization in mind. Sola comes in one-
foot increments so designers can attach as many or as few units as they want to form a sectional or have standalone pieces. “That can be reconfigured on the fly,” Schutte says. “Everything we do is thinking about flexibility and how it’s really going to be used.”
The Luma, Sail, and Horizon Collections, Marquesa Sun Lounges, and Meritage Tables offer the ability to combine the rich textures of Aluma-TEAK, the sleek tones of premium powder coat finishes, and the refined accent of various Meritage Bezel jewelry-like finishes to create furniture for any vision. Design teams can go
subtle or bold to create combinations that feel truly personal.
The meticulous marine engineering Clarke founded the company with continues, as Tuuci uses the materials seen in boating—like aluminum fasteners that hold up under the harshest marine conditions day after day—and incorporates them across collections. “In the form following function of marine design, everything on a boat is there for a purpose—no more, no less than is necessary. It’s taut, thoughtful design, and that is the guiding principle for everything we do at Tuuci,” Schutte says. g
In the Sola Collection pieces are designed for ultimate modularity, as each piece may be used individually or combined to form various sectional configurations.
THE WEST LA VA CAMPUS MASTER PLAN, INCLUDING BUILDING 207 DESIGNED BY KFA, IS AT THE FOREFRONT OF A SIGNIFICANT EFFORT TO SUPPORT AT-RISK VETERANS.
KFA Architecture’s Lise Bornstein on sustainable designs that offer home and healing in LA
BY ELYSE HAUSER
What does placemaking mean to you?
Placemaking begins with listening—listening at all levels. Listening to the neighborhood, to context, to clients, to future residents—and really distilling down what home means to them, and how our building or project will become a good neighbor within the community, and how we can create community within the building. To me it’s like a nesting doll. There are so many different layers to a project and how a place becomes a place, and it always centers back on people and context.
Awell-designed building isn’t just where experiences happen—it also plays an active role in shaping those experiences. Architecture creates community through experience when it fosters engagement, familiarity, and well-being. This is placemaking: design that shows love to the people who use it.
Lise Bornstein’s approach to placemaking emerged through finding her place at KFA, where she’s now a partner. She recalls circling three newspaper ads, one of which was for a job at KFA, when she was a new architect in Los Angeles. “It seemed like a wonderful place where you could be yourself,” she says. “And so where I have ended up has been a function of the environment in which I found myself.”
Bornstein is the partner in-charge for a portfolio that includes projects like campus developments and permanent supportive housing. Through these projects she’s discovered her passion for creating community, using architecture that puts people first. “That is where I found myself—with amazing colleagues and clients who have a shared vision to create home for people from all walks of life in a city we love,” she says.
Bornstein demonstrates this vision in recent projects like Building 207, which provides affordable housing to veterans, and SP7, which provides permanent housing to people facing homelessness. She fuses elements of nature and art, crafting spaces that offer holistic well-being and connection. Bornstein recently sat down with gb&d to share how her latest projects embody placemaking for people, and what’s on the horizon.
ORIGINALLY A MISSION REVIVALSTYLE STRUCTURE FROM 1940, BUILDING 207 HAS BEEN TRANSFORMED TO PROVIDE 59 RESIDENTIAL UNITS.
A lot of what I look at through placemaking is how we can create architecture that not just welcomes but loves the people who live there, and through that becomes place. Placemaking can be as big as the building’s place or the project’s place within the larger regional community or even neighborhood. But I think it can be something as small as the place where you meet your neighbor when you’re waiting for the elevator or outside your unit door. Placemaking has multiple different scales and purposes in terms of community.
What makes your recent project, Building 207 on the West LA VA Campus, special?
I’m going to broaden it out to the larger campus because we’re doing multiple projects on the VA Campus. We’ve had a hand in the master planning as well.
The placemaking and home there is really seen as what the client likes to call “collective impact.” It’s looking toward creating different ways communities can come together and services are actually brought to people. I like to think of it as holistic wellness. That comes in so many different ways. It’s mental. It’s physical. It’s biophilic. When we talk about sustainability, a lot of the sustainability measures we’re talking about are energy conservancy and efficiency. But it’s also access to air and light. That seems so simple, but having people feel at home and comfortable, with access to greenery and actual real dirt and open spaces. And a place to, especially as former veterans, have respite and quiet solitude, as well as community. A place to heal. Those places are so incredibly impactful in not just the healing process but community-building as well.
There’s a lot of shared experience that happens on the campus. Having those spaces where people can meet at different scales and variety is critical to creating those groups and comfort zones for people to feel at home. The campus itself also has services. So when we talk about collective impact and wellness, it goes beyond the unit—which is super important—but it goes into those other spaces that become so valuable in creating that sort of expanded architectural embrace. There are community spaces: community gathering rooms and amenity spaces and lounges. But then there are also larger amenities for the campus, where there’s going to be arts and vocational training and all of those services that bring familiarity and expansion to the residents. It’s a lot about engagement and interactiveness and camaraderie. It’s creating all of these layers on the campus, from the smallest scale of the unit all the way out to big town square spaces and outdoor movie spaces.
There are so many ways people can feel part of the community, and the idea is to try to give them access to as many as we can, as well as health care. The campus has health care embodied within it. There’s the large VA Medical Center campus to the south, but then there’s also clinics and more one-on-one spaces on the North Campus, which is where Building 207 lives.
Building 207 itself is part of the collective whole. It’s one of several buildings along the street. And then that street has its own character and community-building space. A street is a space. The plaza to the north is a space. All of these connected open spaces throughout the campus really create that network of landscape and connective places, where people can find their home.
SP7 is such a contrast to the VA Campus. The VA campus is this huge, bucolic, 388-acre site with mature trees and tons of gophers. Then
you look at SP7, which is in the center of Skid Row, and it’s a very different landscape. It’s a very urban landscape.
SP7 was really meant to address how people feel at home within this urban landscape. We opened the corner of the building—it became a raised deck, and you can see through it. We brought light and air into the inner courtyard, and we made the ground floor transparent so there was separation from the street, but it was transparent and inviting.
One of the things that’s part of the homeless experience is feeling invisible. We wanted to take that idea of feeling invisible and flip it on its head. People who are residents at SP7 can look out into their neighborhood from the second floor deck and the top floor deck. They can be in the downstairs lobby and lounge and inner courtyard and have this transparency and openness to their neighborhood and to their community, so they’re not invisible. That was a really big part of SP7’s genesis.
And then layering in places, again, for respite. The lower deck is really much more connected to the neighborhood because it’s only a story up. But the upper deck is meant much more for a quiet place. You get the vista. So people who are experiencing a different sort of trauma can have a place to breathe and feel calm in those spaces.
How is architectural design connected to wellness and health?
We call it social impact in our design. Wellness comes in so many different layers, and architecture creates the places where things happen.
That is so important to thinking about community. I think about the apartment buildings I’ve lived in. The ones with the central courtyards and the open corridors are where I know all of my neighbors, and I form really strong bonds and friendships with my neighbors. The building I’m in now doesn’t have that, and I don’t know anybody.
That’s an architectural move we can make as designers, to invite connection. It’s something we should be thinking about as we look at a holistic approach to wellness through architecture: light and air. We talk about it a lot, but really making sure that happens, making sure windows are open and inviting, operable. Simple things like that where people can feel connected to the outside.
We talked about scales of connecting places: places for one-on-one interactions. There’s a sort of passive interaction where you maybe meet your neighbor when you’re going to the mail or the elevator. But then there’s a space where you can have a conversation—smaller spaces, one on one, maybe a little widened corridor. We like to recess our entries at our unit doors so people feel like there’s a place to pause within the architecture and not just continue and move, move, move.
Then, of course, courtyards and porches. Porches are huge, especially in senior housing. You need to feel safe where you are, but isolation is huge with senior housing. So how do you get people into the front of the building, but in a safe place where they can look outside and watch the family walk by with the kid and the dog and have that connection?
These are all parts of wellness that are part of the shared human experience and so important to our humanness within architecture.
Can you talk about how your work reflects your love of art? I’m a painter. It is my world. Honestly architecture, to me, is a lot about the void. When I think about art it’s what you don’t include that’s as important as what you include. How you edit in art down to the most important piece, whether it’s a feeling or an image, is very aligned with how architecture evolves in our design process. What is most important? We always call it the sword you would fall on, or the hill that you would die on. But it’s distilling down to those most important moments and pieces that, I believe, is very parallel when you look at art and architecture.
Can you tell us about the Avenue 34 affordable housing development coming up?
It’s a big project—lots of units. It’s right next to transit, next to the Gold Line, and it has two really big courtyards. A lot of care was put into the characters of the courtyards in terms of identifying different spaces—passive and active.
A lot was put into the community, too. We have what we call “the boulevard” inside that connects all three buildings. That’s an outdoor boulevard that penetrates through the buildings and continues on through all three. We thought it was a fun space. It was a way to connect the site and give the site an internal character as well as its external view out into the neighborhood, which has a park and shared retail space out-front.
We’re really excited about that project because it’s going to be a really big impact in that neighborhood. It’s a lovely neighborhood, and we’re excited to be there.
What else does the future hold for your community and design work?
Sustainability is part of our future world in architecture and design. In LA specifically we look a lot toward how LA is growing, and growing pains, and how density can sometimes be a bad word. But I think it’s actually part of the solution to housing, to community—and also wellness and sustainability in terms of being good stewards and efficient in our land use. Using the boulevards for what they’re really planned to be, which is these beautiful wide lanes, connectors in our city. I’m thinking about how we can take density and use it toward fulfilling so many different roles.
Sustainability’s super important. There are places in Culver City where they use parking spaces as porous pavement, which is great. On your boulevard you’re getting transit, but then you’re also getting permeability and recharging our aquifers. And then along the boulevard you have wide sidewalks; they’re 100 to 120 feet wide. That’s light and air, and we can plant along there and have beautiful trees. And then putting housing along there creates critical density along the paths of our city where we need it most. It creates a critical mass to get transit to be more effective. It’s a way to build our city that doesn’t impact the California dream, which is the single-family house—which people will protect, and that’s where a lot of the NIMBYism comes from. But if we can use what we have in a smarter way and do smart density, I think our city can continue to grow in a beautiful way. g
THE AVENUE 34 PROJECT WILL COMBINE NATURE WITH AFFORDABLE HOUSING.
BY SUSAN KING
No one likes to be a test pilot. However, when HED was enlisted by Interfaith Housing Development Corporation (IHDC) to design the Conservatory Apartments, we were rewarded for stepping into uncharted terrain. By leaning into the challenge of navigating the city’s changing building codes, as well as the state’s new green building incentives, we discovered that aggressive green building could be successful in a large-scale affordable housing context.
In October 2024 the project became the first affordable housing project of its size to achieve Phius certification in Chicago. The 43-unit proj-
ect near Garfield Park Conservatory demonstrates that sustainability can—and should—be part of the affordable housing definition.
Like most cities across the country, Chicago grapples with increasing housing shortages and barriers to affordability. Traditionally the financial mechanisms in place to create affordable housing focus on construction costs only, ignoring the long-term operating expenses. Low Income Housing Tax Credits (LIHTC) are the most common tool, and the 9% programs are extremely competitive because they use a scoring system to select funded projects.
While Illinois requires a minimum sustainability standard, slightly above code, in funded projects, higher levels of sustainability from Third Party certifications (i.e. LEED Platinum or Phius) are offered through an optional scoring package in the Illinois Qualified Action Plan (QAP). This is a great step toward addressing long-term affordability, but there have been issues with the points offered not being enough to appeal to developers.
In 2020 I was part of a task force that worked with the Illinois Housing Development Authority to help shift the state incentives toward more advanced green building certifications by offering 10 points for pursuing them. In turn it made competitive sense for developers like IHDC to pursue a higher level of performance certification like Phius. At the same time the city of Chicago issued a new building code and a ventilation reduction pathway to accommodate the stringent Phius energy efficiency guidelines. Ultimately we were able to demonstrate that raising the bar in terms of aggressive green building can work for a large-scale affordable housing project despite being situated in a challenging four-season climate like Chicago.
The focus of Phius certification is an extremely tight building envelope that is closely integrated with the mechanical and ventilation systems. Even though the guidelines are also an excellent path to net zero, efficiency is the primary goal. As a result the Conservatory Apartments’ Phius-related features include complying with ComEd’s energy guidelines, 14 kw photovoltaic systems, Energy Star appliances, LED lighting, and water-saving plumbing fixtures (projected to reduce water use by 25%). The building’s transit-oriented location (just 1,320 feet from the nearest Chicago public transit Green Line Conservatory stop) also contributes to the project’s sustainability.
It’s a great-looking, boxy (in the best sense of the word) building that allows for simplicity in terms of efficient infrastructure, such as continuous insulation installation. The new 2020 Chicago building code allowed us to substitute wood frame for the former code’s masonry/precast requirements. Despite the high costs of building supplies during the height of the Covid pandemic, the savings on superstructure materials opened funding avenues for attaining Phius standards, such as incorporating high-performance windows and HVAC systems. We were also nudged by the city to substitute a durable and beautiful slate rainscreen as exterior insulation in lieu of standard an EIFS (Exterior Insulation Finish System).
Finding the sweet spot between excellent energy efficiency and superb air quality proved to be a tricky balance. Ultimately we worked through stringent ventilation requirements, finding ways to comply with code that allowed us to maintain an energy-efficient building in a Midwestern climate as well as healthy air quality. While we were driven by Phius guidelines, IHDC and HED never lost sight of the importance of human and environmental health in the process of building the project.
Connection to nature is vital for everyone. As the biophilic design HED
Incorporating a Biophilic Strategy
Susan F. King is a principal with HED. As a studio leader for housing and mixed use in the Midwest, she advocates for both attainable housing and green market transformation of the building industry; she is routinely invited to speak on these topics. As a principal she leads multi-disciplinary teams toward achieving aesthetically appealing sustainable solutions in a collaborative integrated design setting. She was recognized by gb&d magazine with a Women in Sustainability Leadership Award in 2016. Most recently she has been an active participant with Living Future Affordable Housing Pilot Cohort 3.
trend has bloomed in recent years, various studies have attributed improved well-being, increased productivity, and an array of health benefits to the presence of natural features in homes, offices, and all types of indoor environments. Given that most Americans spend 90% of their time indoors, that connection to nature isn’t a given.
The Conservatory Apartments’ site on a tree-filled boulevard, just north of its namesake, naturally lends itself to biophilia. Due to the project’s selection as part of the Living Building Challenge Pilot Program for Affordable Housing, we were also given the opportunity to bring natural elements inside the building. But in my opinion, the apartments’ coolest biophilic feature is the lobby’s signature, low-maintenance moss wall.
We’ve also simulated natural forms via light fixtures and patterned glass. Four photographic murals—each depicting different
images of the nearby Garfield Park Conservatory—lend a sense of place and a dose of nature to each elevator lobby. With another nod to the great outdoors and energy efficiency (and as a resiliency strategy), we also prioritized daylighting, both inside the studio units and in the building’s hallways.
Building a Sustainable Home Energy efficiency and creating connections to nature contribute significantly to the sustainability puzzle when it comes to pioneering a new standard for affordable housing. After all, the core goal of this kind of project is to provide good, safe, healthy housing for unhoused people. Thirty-four of the Conservatory apartments will accommodate chronically homeless individuals and people with disabilities. The remaining nine units will be allocated to people through the Illinois State Referral Network with support services via nonprofits, Deborah’s Place and Trilogy Behavioral Healthcare.
Being the first is worth it as long as we’re not the last. Building livable and sustainable housing means creating a space that is fiscally and environmentally healthy well into the future. Although pricing for green building features and materials are rarely the cheapest option, the Conservatory Apartments are proof that resisting the short-sighted tendency to cut these upfront costs will pay off in the long run. Adhering to green certifications saves money over time. In the affordable housing equation, that matters. g
THE CONSERVATORY APARTMENTS INCLUDE 14 KW PHOTOVOLTAIC SYSTEMS, ENERGY STAR APPLIANCES, LED LIGHTING, AND WATER-SAVING PLUMBING FIXTURES.
BY WILL GRIDLEY
n the world of architecture, the design and planning of student housing stands out. Not only are universities among the most ambitious clients when it comes to sustainable performance, but the precipice between adolescence and young adulthood is a formative time in one’s life. It’s when many of us form the foundations of our lifelong worldviews, values, lifestyles, and habits.
For architects, student residences have never been simply a passive container for life; such buildings are an important tool for teaching young adults about how to become healthy, happy, and self-sufficient adults. Shared dorm rooms, for example, have taught countless students (sometimes frustrating) lessons about compromise and collaboration.
Inevitably the lessons that a building aspires to teach its inhabitants change over time. Over the past decades this mandate has broadened for many architects to more fully encompass environmental responsibility. A well-designed student residence can help teach sustainable behaviors by shaping a person’s awareness of what and how they consume.
At RAMSA we have designed and planned student residences and residential complexes totaling some 20,000 beds on campuses nationally and abroad. Our approach continues to evolve, and yet much of our contemporary sustainability practice stems from the lessons we learned more than a decade ago when designing the Kohler Environmental Center at Choate Rosemary Hall, a day and boarding school in Wallingford, Connecticut.
Completed in 2012, the Kohler Environmental Center is a 31,325-square-foot academic and residential facility built of stone and cedar and sited gently in a small clearing of second-growth forest. The building houses up to 20 students at a time for a yearlong immersive living and learning experience. Students eat, sleep, and learn within the complex’s 14 dorm rooms, classrooms, labs, and greenhouse.
The ambitions of Choate Rosemary Hall’s administration and its benefactor, the late Herb Kohler, made the project a dream commission for any sustainability-minded architect. The LEED Platinum- and Net-Zero–certified building’s list of sustainable features is long: a grid-connected photovoltaic array and roof-mounted solar array supply more than 100% of the building’s annual energy needs; thick exterior walls and insulated roof panels along create an efficient, high-performing envelope; electric lighting is rarely required throughout the day due to the building’s narrow floorplate and expansive glazing; heating and cooling loads are mitigated by the building’s orientation, eave overhangs, solar shading; and dual underground earth ducts that temper outdoor air before it enters the building. Even a tower, which springs from the building’s roofline, acts as a solar chimney.
What makes the Kohler Environmental Center so special, however, is not simply that it performs at the highest level, but its mandate. The building was designed to teach students about living responsibly. It offers students control of their surroundings. They decide how to use many of the building’s features and its monitoring system, which is displayed in shared spaces and on students’ devices and provides them real-time feedback on their energy and water usage. Students learn about how their behaviors translate into consumption in the process—a relationship that often goes unseen elsewhere in day-to-day life.
STUDENTS ARE IMMERSED IN LEARNING AT KOHLER ENVIRONMENTAL CENTER’S CHOATE ROSEMARY HALL. AT GEORGETOWN, 55 H STREET IS A NEW, LEED PLATINUM GRADUATE RESIDENCE (BOTTOM, LEFT). NEW HOUSING PLANNED FOR THE UNIVERSITY OF MICHIGAN IS BEING DESIGNED TO ACHIEVE LEED PLATINUM.
A culture of collective responsibility has sprung up within the Kohler Environmental Center. During the school year student cohorts regularly meet to discuss how to best use the building’s features and to coordinate their plans. These conversations often revolve around seemingly minor details, such as the impact of opening a window for cross ventilation. Incoming students receive a summary of their predecessors’ performance, and a sense of friendly competition, perhaps unsurprisingly, has arisen in the building’s halls.
In 2016 four years after the Kohler Environmental Center was first occupied, we learned something remarkable: The building’s energy consumption was 48% less than anticipated. Year over year the building’s energy usage has continued to decrease. Today the Kohler Environmental Center consumes 24% less than energy than it produces.
The lessons of the Kohler Environmental Center continue to shape our sustainability practice. Designing an efficient and successful building in the 21st century isn’t solely about high-performing systems but also engaging inhabitants. When students at the Kohler Environmental Center were offered a sense of own-
Will Gridley is an associate partner with Robert A.M. Stern Architects (RAMSA), specializing in higher education building projects. Gridley has played an integral role in various campus-transforming projects, including the Harvard Kennedy School Pavilions Project, the Southern Methodist University Cox School of Business Expansion, and the McCourt School of Public Policy’s new home in Washington, DC. From initial feasibility studies through construction, Gridley’s work employs a variety of housing product types, delivery methods, and construction techniques. Recently he co-led the University of Michigan Central Campus Housing Project in collaboration with American Campus Communities. It is the largest singlephase student housing project in the nation’s history.
ership over their surroundings and agency over their behaviors, they have proven to be exceptionally conscientious, discerning, and responsible inhabitants. This combination of high-performing systems with considered human behavior has produced a building that has exceeded our own expectations significantly.
55 H Street, Georgetown University & Jane Pinchin and Burke Halls, Colgate University
When designing 55 H Street—a new 476-bed graduate residence at Georgetown University’s downtown campus and the university’s first to be LEED Platinum–certified—with our partners at American Campus Communities and Elkus Manfredi Architects, the Kohler Environmental Center was top of mind.
Not only is 55 H Street all-electric powered, fossil fuel-free, and home to an expansive rooftop solar array, the building aims to similarly educate its residents on its own sustainable features and positively shape residents’ behaviors in turn. Inside 55 H Street’s lobby, monitors display the energy and water usage of each floor.
A similar approach has proved successful at Colgate University with the Jane Pinchin and Burke Halls, completed in 2019. Built of locally quarried bluestone, the pair of five-story residential halls are contextually attuned to Colgate’s historic architectural vocabulary, yet they also establish a new standard for future growth as the university pursues carbon neutrality. Both projects offer students the opportunity to understand the building’s sustainability features and offer insights into their collective consumption.
Recently our team at RAMSA embarked on a major student housing development at the University of Michigan. Designed and developed again with American Campus Communities and Elkus Manfredi Architects, the South Fifth community will bring five student residences totaling 2,300 beds and a 900-seat dining hall to the Ann Arbor campus when completed in 2026. (Notably, it’s the first student residence built for first-year students at the university since the 1960s, and it will help alleviate the housing challenges faced by the university and city of Ann Arbor.) Designed to achieve LEED Platinum, the complex will feature high-performing envelopes and solar arrays. The dining hall will be fully electric, with its heating and cooling needs completely supported by a geothermal field.
Excitingly, the South Fifth dining hall will translate many of the lessons we’ve learned designing student housing into dining. Consistent with the building’s sustainable performance, it will serve healthy, sustainably sourced foods. Our ambition is for a building that will not only tread lightly, but positively impact students’ well-being by establishing healthy eating habits while also imparting an appreciation for sustainable foods.
Our expectations for such a project are high, and yet perhaps they will be exceeded when it becomes inhabited by students. Universities today are full of environmentally conscientious young adults. Their spaces should not only be fitted with the requisite high-performing systems but offer insights into their own individual and collective consumption, and the opportunity to live accordingly. g
RAMSA’s Graham S. Wyatt, partner, contributed to this article.
BY MIKE THOMAS
Even in the most thoughtfully designed and humane jails, like the ones Ricci has worked on for many decades now, he says, “That’s pretty serious stuff. The fact that I’m slightly claustrophobic didn’t help.”
Seeing is Believing
Well before his fleeting stint behind bars, Ricci’s eyes-and-ears-opening introduction to the US jail system began back in the 1960s, when he visited New York City’s Rikers Island while writing his senior thesis at the Brooklyn-based Pratt Institute’s School of Architecture (Ricci would eventually design Rikers’s youth correctional center).
Spanning 413 acres in the East River, Rikers has long been known as one of the country’s least hospitable lockups. It is currently being dismantled to make way for a “smaller network of safer modern jails,” but Ricci saw the notorious complex at its worst—when inmates (now commonly referred to as “occupants”) were considered little more than bodies to be warehoused. As at so many other US jails (which differ from prisons in that they house people pre-trial vs. post-adjudication), their physical and psychological well-being—and that of the guards, now “officers,” who supervised them—was an afterthought at most.
“It was loud. It smelled. It was scary,” Ricci remembers. “It’s not a place you’d want to stay overnight. And I thought, ‘Why can’t it be better?’”
His mentor Donald Goff—a highly regarded figure in the New Jersey and New York corrections sectors—thought likewise, encouraging and supporting his protégé. Before long, at age 27, Ricci founded his own New York-based architecture firm (with Goff as his first client) and began making a name for himself in a society that was gradually being primed for a kinder incarnation of incarceration.
rchitect and advocate Ken Ricci has never done time. He has, however, been locked in a jail cell. It was only briefly, while touring a detention facility years ago. But that momentary—and, it should be noted, voluntary—loss of freedom had a lasting impact.
“Americans value our freedom,” says Ricci, vice president and business development leader in the civic and justice division of NELSON Worldwide. “When that door slams behind you, you realize you’re powerless to exit that room unless someone lets you out.”
NELSON WORLDWIDE IS DESIGNING THIS NEW JERSEY JUVENILE JUSTICE PROTOTYPE FACILITY TO ENHANCE THE SAFETY OF STAFF AND YOUTH AND PROVIDE THERAPEUTIC SERVICES IN A SAFE ENVIRONMENT.
Since then jails across the country have adopted his vision, including Ricci-designed facilities in Poughkeepsie, Denver, and Maricopa County, Arizona. In the name of convenience and more expedient justice, they’re each all-encompassing complexes wherein occupants (or potential occupants) are screened and then diverted to the appropriate area. If they have mental health issues they’re assigned to a mental health professional. If their violation is low-level, they can see a magistrate in an onsite courtroom and quickly get released on recognizance or bail—no waiting around for days until an outside judge can hear their case. If they’re in for an extended stay, Ricci’s design elements both enhance their safety and affirm their humanity.
“There are some philosophers who’ve said that beautiful buildings make people better,” Ricci says. “I like to say environment cues behavior.”
He has built a career on that premise—and on the idea that the daily operations of any given facility should drive design while hewing to an overarching vision of humanity, efficiency, and safety. “Before you design,” goes one of his mantras, “you must define.”
That’s exactly what Ricci did in Dutchess County, New York, where he worked with New York Congressman Marc Molinaro, County Executive William O’Neil, and Commissioner of Public Works Robert Balkind to design and build a state-of-the-art Justice and Transition Center. It opened in 2021 after seven years of planning and construction that occurred in three phases: validation, community involvement, and project definition.
Novel features include direct supervision housing pods, ample sunlight in all dayrooms (which bleeds into the individual cells—a pioneering technique known as “borrowed light”), an open waiting area for people in custody, a so-called “R.E.S.T.A.R.T.” center that facilitates a softer transition for occupants who’ll soon be released. In addition to dormitory-style sleeping areas, it sports colorful murals as well as immediate access to program spaces for treatment
six days per week. During the early planning stages capacity was reduced from 580 to 328, preventing overcrowding, saving millions of dollars, and significantly reducing its footprint both literally and ecologically.
“There was an altruism to Ken’s philosophy that he imparted to our whole design team,” Balkind says. “It’s this sense of humanity and treating people in a dignified manner. That’s the core of who he is. But there was another purpose to that philosophy from our perspective at the county. We were interested in creating not just a physical facility, but one that had programs within and without. The idea was to curb recidivism and not just detain somebody because they were charged and convicted, then simply release them back out into the street where they would eventually reoffend.
“There was this notion of dignified incarceration—providing a space where people could avail themselves of all kinds of programs: drug and alcohol, restorative justice, education, spiritual enlightenment. We want to give people an opportunity not only to reflect on and repent for what they’d done, but also give them skills so that when they get out of jail, they aren’t prone to reoffend because they have other coping methods. Ken brought a lot of that to the initial parts of our project.”
These days, Ricci says, mental health issues are far more serious than overcrowding. Along with mental health specialists, the physical environment can have an outsize impact on occupants’ frame (and peace) of mind. In the absence of mitigating features, he explains, cortisol and adrenaline levels remain higher than they should be, promoting a “fight or flight” mentality.
Ricci offered some examples of elements he incorporates into his jail designs, along with explanations of how each can positively impact the physical and psychological well-being of those who live and work in a facility.
Air conditioning: We don’t call it air-conditioning. We just say we’ll install a system that keeps the temperature at 72 degrees Fahrenheit all year round.”
Good sightlines: “Sightlines are important for maintaining safety and security. That means wide corridors and no blind corners. If officers have eyes on everybody, there’s less of a tendency to join a gang or make a weapon. In jail housing units, which can have anywhere from eight to 24 occupants, officers work inside the unit. When occupants know that someone is in charge, they feel safer.”
Open views to the outdoors: A view of the horizon and green land are crucial. So are windows that allow in direct sunlight (as opposed to the diffused sunlight that enters through skylights) to hit the common day room, which in turns keeps occupants “connected to the [outside] environment” and makes them more “optimistic about tomorrow.”
Improved acoustics: “We use soft materials for the ceilings and have acoustic paneling on the ceilings and walls,” Ricci says. “We even put carpet in one jail. We also use so-called ‘normative materials.’” Chairs, for instance, are very soft and colorful while also being heavy and hard to move. Wooden doors are common, too. Besides enhancing the environment, they reduce costs (steel bars are expensive).
Being a Good, and Green, Neighbor Ricci is practiced at wading through the red tape that inevitably comes with designing municipal structures. His biggest challenge, he says, is finding sites to build on. Some communities, like Denver. (whose downtown detention center Ricci worked on), eventually subscribed to his vision of synergy between a jail and its external environment—but only after years of consensus-building. Others are reluctant to house those who’ve been accused of crimes among residences and businesses. But such areas, Ricci says, are closer to the courts. Very often they’re also more accessible to the family members of occupants and to legal professionals via public transportation, which makes visiting and commuting to work much easier—not to mention greener.
Sustainability is also built into Ricci’s designs. While his jails are made to be as efficient as possible when it comes to water and energy use, he takes more of a systems view that involves right-sizing a facility before it is built—as in the case, for instance, in Dutchess County.
“You have to think not only of the individuals who are incarcerated, but also the staff that works at a jail,” Ricci says. “What’s it going to take to make it safer and more secure? And then we think of the building itself: What does it need to accomplish? Does it cast a long shadow across the street? How can it become a good neighbor?”
The best modern jails are a world apart from their predecessors, but Ricci thinks there’s plenty of progress to be made. Invoking another longtime mantra, he says the potential exists to make jails even “smaller, smarter, greener, and kinder.”
Because rather than merely being punitive housing facilities, they should instead be “a place to heal.” g
BY CHRISTINA DEAN
Megan Valentine, director of sustainability for KTGY, a national design firm based in California, has made it one of her career goals to expand people’s definition of resilience. While the term in the design and construction industry conjures images of buildings withstanding severe weather events or natural disasters and remaining operational afterward, modern society requires all aspects of societal adaptability and flexibility to be part of the resiliency conversation because we’re all connected.
“Resilient design is not just about weather events,” she says. “It’s also about any
foreseen or unforeseen changes—designing places that are inherently flexible to pandemic response, technological advancements, economic shifts. At its essence resilience is designing for adaptability.”
The US has experienced nearly 400 weather and climate disasters since 1980, according to the National Oceanic and Atmospheric Administration in August 2024. The costs of overall damages exceed $2.755 trillion. As of July 9, 2024, the nation had incurred 15 weather events that each surpassed $1 billion in damages.
As it becomes more difficult to ignore these extreme weather events, members of the design and construction industry are talking more about resilient buildings. Although codes are leaning more toward resilience in some parts of the country (like California’s seismic retrofitting requirements), the codes still aren’t stringent enough to protect buildings from these erratic events. Valentine thinks architects should take the lead in making buildings more resilient in their practices in part by educating clients and project teams about the benefits of resilience.
“We do think about these resilience topics in every one of our projects,” she says. “Most of it is part of our design standards because most of our work is in California. If you think about the climate events and natural disaster events like earthquakes and the fact that Silicon Valley is located here, our building code expectations are much higher.”
California’s leadership in resilience recalls the state’s early strides in the green building movement years ago, though Valentine doesn’t believe resilience will have the same broad market acceptance sustainability has. “The unfortunate part of the conversation around resilience goes to the gut of how we respond to things as humans,” she says. “Resilience is about being adaptable to change, and humans are not very adaptable beings. Resilience requires us to design proactively for something we haven’t experienced yet but we may experience, and that’s a really hard thing for a client—and his/her budget—to get behind. And it’s a hard thing for our design teams to push for if they haven’t seen the direct impacts.”
Unlike sustainability, which can show proof of payback in lower energy bills, resilience is difficult to measure unless a building is the only one operating after a natural disaster, for example.
“Resilience is a really forward-thinking approach, which makes it a more difficult conversation than sustainability,” Valentine says. “There are so many aspects of sustainability where you can see ROI quickly. Resilience doesn’t have that going for it.”
KTGY’s internal conversations about resilience extend to its R&D department, which tests innovative ideas to demonstrate to clients how the firm can assist clients with problems they are experiencing in the built environment. For example, after the pandemic changed driving habits, parking structures throughout major cities were underutilized. KTGY found a way to adapt parking structures into much-needed housing via its Park House 1.0 and 2.0 projects.
KTGY DESIGNED SHAWOOD AT SOMMERS BEND IN TEMECULA, CALIFORNIA, WITH SUSTAINABILITY, RESILIENCE, AND ADAPTABILITY IN MIND. THE PARK HOUSE PROJECT CREATIVELY REPURPOSES PARKING INTO HOUSING.
“Park House takes the average parking structure and considers how we can adapt it for housing without removing the structural integrity,” Valentine says. “The really cool thing about that—aside from the fact that they are reusing the structure—is they can transition part of the structure to housing and continue incrementally. This is resilience in that it’s allowing the structure to remain relevant for a long time.”
In the real world KTGY was the architect on Shawood at Sommers Bend in Temecula, California. The housing development boasts
homes designed with sustainability, resilience, and adaptability in mind. The developer, Woodside Homes, a subsidiary of Sekisui House, which has provided more than 2.6 million homes in Japan and globally, is committed to creating healthy homes with less construction waste that are durable and adaptable.
The Shawood at Sommers Bend homes’ framing system is a very old Japanese building practice. The nail-free system requires precisely cut wood pieces to be nested together. When designers ask how to create something that’s super sustainable and resilient, she tells them it’s about keeping it as simple as possible. “The less material we use, the less complicated joints are, the less waste we have, and the less reliant we are on different things that may fail,” Valentine says. “At Shawood the sticks are all pre-cut before they get to the site, so it’s like putting Legos together. That modularity reduces construction waste and makes things faster onsite.”
Buyers at Shawood at Sommers Bend have the option of installing solar before the home is purchased or buying a solar-ready house. Each solar-power system has battery backup that ensures the home can remain operational during a blackout. “Solar with battery backup is an option on quite a few of the homes we design,” Valentine says. “A lot of our codes are requiring that, but the idea that these homes can operate off-grid is really thinking about resilience.”
Shawood at Sommers Bend homes range in size from approximately 3,000 to 5,000 square feet. The benefit to that, Valentine says, is there are spaces that can be adapted for a homeowner’s current and future needs.
“There are some fairly private spaces in these homes that are pretty adaptable,” she says. “For example, they have wellness rooms in them, but nothing is built-in, so the room can be used as a home office or gym. Having separate spaces that are blank canvases allows people to use these spaces in any way that makes sense for them.”
Valentine says the homes at Shawood are resilient in almost any climate. “When we talk about resilience, we talk about being specific to different areas of the country, but we now are hearing about crazy weather events we’d never expect to happen in a certain area of the country. Who knows what’s going to be affecting this area in 50 years when your building is still operating? I think having this holistic view that we need to design for worst-case and hope for the best everywhere needs to happen.”
Shawood at Sommers Bend is the second development KTGY has worked on with Woodside Homes (the first community is in Las Vegas). Despite challenges with approvals for the framing system, Woodside Homes is proving its business model can work. “They’re thinking outside the box and the market is demanding it,” Valentine says. “They charge a premium for their product and are creating really resilient sustainable, healthy spaces people are buying.”
THE SHAWOOD AT SOMMERS BEND HOMES’ FRAMING SYSTEM IS A VERY OLD JAPANESE BUILDING PRACTICE. THE NAIL-FREE SYSTEM REQUIRES PRECISELY CUT WOOD PIECES TO BE NESTED TOGETHER.
KTGY follows these third-party certification systems:
• LEED
• Enterprise Green Communities
• Green Globes
• National Green Building Standard
• US DOE Zero Energy Ready Home
• EPA Indoor AirPlus
• EPA WaterSense
• Wellness Within Your Walls
• ENERGY STAR
• GreenPoint Rated
• Build It Green
• Local “Reach” Codes
KTGY does not follow any universal benchmarks when it comes to resilient design, but the firm’s staff has conversations about how to maintain a baseline level of resilience, health and wellness, and sustainability in all its projects. “We are considering implementing a sort of internal check on ourselves to make sure we are achieving the goals we have,” Valentine says.
In five to 10 years Valentine expects resilience will be part of every design and construction conversation. “I would say every architecture firm will have resilience top of mind and integrated in some way just because of codes, but whether it’s a priority on every project, I’m not sure,” she says. “We need to shift the way we think about resilience and how, as a culture, we’re not proactive. Let’s be proactive thinkers and take our roles as designers really seriously because resilience is not going to be integrated unless we’re leading that conversation and making these nudges.” g
Designing for connection and sustainability in San Diego’s first “agrihood”
BY PAULINE HAMMERBECK
In the coastal hub of Encinitas, California, a new project aims to redefine sustainable living. Just a mile from the Pacific, Fox Point Farms emerges as San Diego’s first “agrihood”—a mixed-use development blending a three-acre farm with residential and commercial spaces. Here agriculture isn’t just a feature; it’s designed as the community’s lifeblood.
At the helm is a dynamic team of architects, builders, and designers, including David Michael, cofounder of Tecture—the design and fabrication studio tasked with creating a mix of hospitality, retail, and communal spaces to offer a fresh take on modern living.
As lead designers for these key components, Tecture has played a pivotal role in shaping the project’s identity.
Though a young firm, Tecture’s origin story speaks to the innovation driving Fox Point Farms. Michael and two classmates from San Diego’s New School of Architecture & Design banded together to create their own studio after graduation in 2012, in the shadow of the Great Recession. With established firms struggling to stay afloat, the trio embraced the challenge, working out of a garage to forge their own path.
“We started building fun projects with whatever we could find,” Michael recalls. Early projects, like repurposing tires into flooring or fashioning pallets into tables, showcased the team’s resourcefulness, though Michael admits some methods wouldn’t make the cut today.
Their ingenuity didn’t go unnoticed, though. Former professors took note, offering the team real-world projects that laid the foundation for a string of restaurant build-outs and other commercial ventures. These projects put Tecture on the map, leading to major clients across San Diego and beyond.
That success paved the way for Tecture’s involvement in Fox Point Farms. About five years ago, Brian Grover, the developer behind Nolen Communities, approached Michael with a vision that fused natural preservation with a community-centric design. Michael was instantly drawn to the concept. “We loved the whole premise,” he says.
Tecture’s team of younger designers, artists, and builders was uniquely positioned for the concept, Michael says. “The preservation of farmland, the reuse of material, the simplicity of design ... it was all within our wheelhouse,” he says. “We were excited to help drive this project.”
They collaborated with architect Steinberg Hart and landscape architect Schmidt Design Group. And with their in-house fabrication studio Tecture had the ability to craft elements directly, customize materials, and develop the environments with precision.
Tecture was granted considerable creative freedom to do so, which allowed the team to design spaces that created what Michael describes as an “unspoken dialogue” between visitors and the structures at Fox Point Farms.
The designs and their very orientation guide people through a series of visual and spatial experiences that continually reconnect them with the surrounding farmland. “It’s a series of moments that tells the story,” Michael says. “It becomes an almost educational point of view.”
The project’s 8,000-square-foot retail and dining structure is a prime example of this. Blending a traditional California-style barn with a contemporary-style greenhouse, the Western red cedar–clad building houses a market and cafe on the first floor and a zero-waste restaurant on the second. Large glass panels flood the space with natural light and create a visual link to the farmland outside.
TECTURE’S USE OF LOCAL, RECLAIMED MATERIALS AND PASSIVE DESIGN FOSTERS AN INDOOROUTDOOR EXPERIENCE AT FOX POINT FARMS.
As guests ascend to the second-story restaurant, sweeping views reinforce the connection between the food on their plates and the fields it came from. Communal spaces like the event venue with another greenhouse-like atmosphere seamlessly blend indoor and outdoor environments, further connecting visitors with the land.
This connection to the environment extends beyond the orientation and layout of the buildings. Throughout the project Tecture emphasizes reclaimed wood (reclaimed teak in the interiors), locally sourced stone, and natural elements like boulders, grounding the development in its surroundings. Michael believes “designs should speak to their context,” and Fox Point Farms reflects that ethos.
One such example is a eucalyptus tree, originally slated for removal in a nearby community, that was transplanted to a play area within Fox Point Farms. It’s a symbolic gesture that speaks to the project’s emphasis on sustainability and deep sense of place. Even the tabletops at the restaurant feature herb-infused resin, bringing the farm-to-table concept to life.
Building on the seamless integration with nature, Michael champions natural ventilation techniques that not only reduce the need for mechanical cooling but also lower operational costs.
Expansive steel-and-glass sliding doors offer the flexibility to welcome in Southern California’s temperate climate and flood the interiors with fresh air and natural light.
While Michael acknowledges this approach isn’t feasible for every project, he’s a passionate advocate for it in his region, where the climate makes it possible to prioritize sustainable solutions without compromising comfort.
Like many ambitious projects Fox Point Farms encountered some challenges, particularly with construction overlapping the pandemic. The intricate design of the main structure—a barn-andgreenhouse hybrid with seemingly more windows than walls— only added to the complexity of the initiative. Despite these hurdles Michael credits the developer’s persistence and highlights the collaborative spirit of the entire team, whose unified approach helped them overcome each obstacle.
“There’s always a way to make things happen,” Michael says. “Money often helps, of course, but if you’re committed, you can always find a way to get it done.”
Looking ahead Michael sees Fox Point Farms as just the beginning of a broader shift in development. He’s inspired by a new wave of professionals challenging conventional practices and pushing the boundaries of sustainability.
And he credits his own success to his ability to connect with visionary leaders who share this forward-thinking mindset. “You attract what you put out there,” Michael says. “When you’re aligned with that kind of energy, it’s only natural that innovation follows.” Fox Point Farms, for him, is more than a project. It’s a model for the future. g
Project: Fox Point Farms
Location: Fox Point Farms
Completion: 2024
Size: 21 acres
Architect: Steinberg Hart
Residential Construction: Shea Homes
Design & Fabrication: Tecture
Landscape Architect: Schmidt Design Group
FOX
A WORKING FARM WITH RESIDENTIAL AND COMMERCIAL SPACES TO RETHINK SUSTAINABLE LIVING.
A once-in-a-century renovation brought new life and beauty to the 115-year-old Sydney Central Station in 2024. Delivered by Laing O’Rourke and designed by Woods Bagot in collaboration with John McAslan Partners, the project was more than five years in the making.
The original Walter Vernon–designed Central Station serves 96% of Sydney’s train services, and the upgrade can accommodate 40,000 metro passengers every hour—a 60% increase on current capacity. New open spac-
es improved circulation while a Central Walk in the underground concourse was designed to ease congestion and improve pedestrian flow. The walkway connects Chalmers Street and the Sydney Light Rail directly to the new metro platforms as well as provides easier access to many platforms.
“The elemental and material choices for Central are anchored by a deep nostalgia for Sydney’s history,” says Domenic Alvaro, Woods Bagot’s global design director. “The seamless commuter experience made possible by peo-
ple-centric design rivals iconic train stations in major cities around the world.”
The new North-South Concourse and refurbished Northern Concourse unify the upgrade. Dark pedestrian tunnels are replaced with a light-filled public room in the tradition of the world’s great train halls.
The new Central Station Metro achieved a 6-Star Green Star Design and As Built rating certification. The refurbished station above has achieved a Leading Infrastructure Sustainability (IS) rating. Read more at gbdmagazine.com.
From how much post consumer waste is used in Creating products, to low-emitting materials, ARCAT green reports can help.
ARCAT provides thousands of reports from building product manufacturers on how their products can help you make the right choice.
Find manufacturers, their products and other LEED contributing credits with ARCAT green reports.
Just look leaf icon.