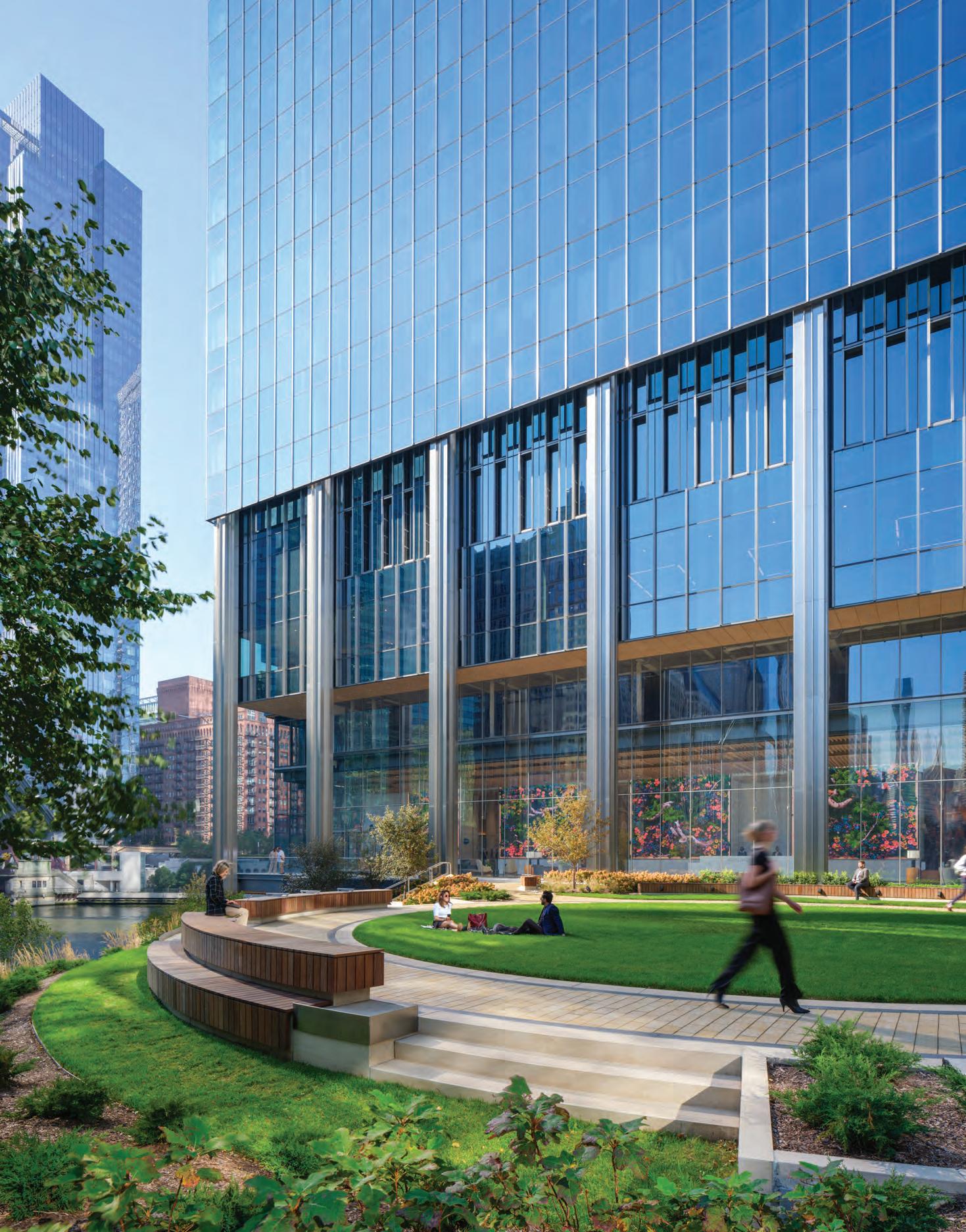
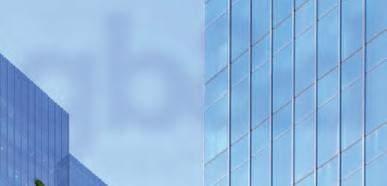

ARCHITECTS DESIGNING
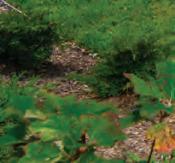
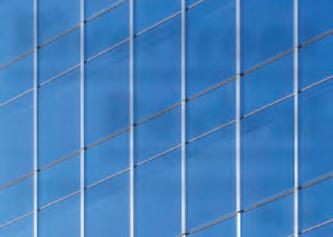
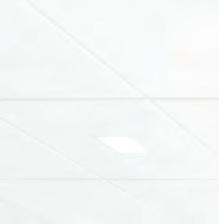


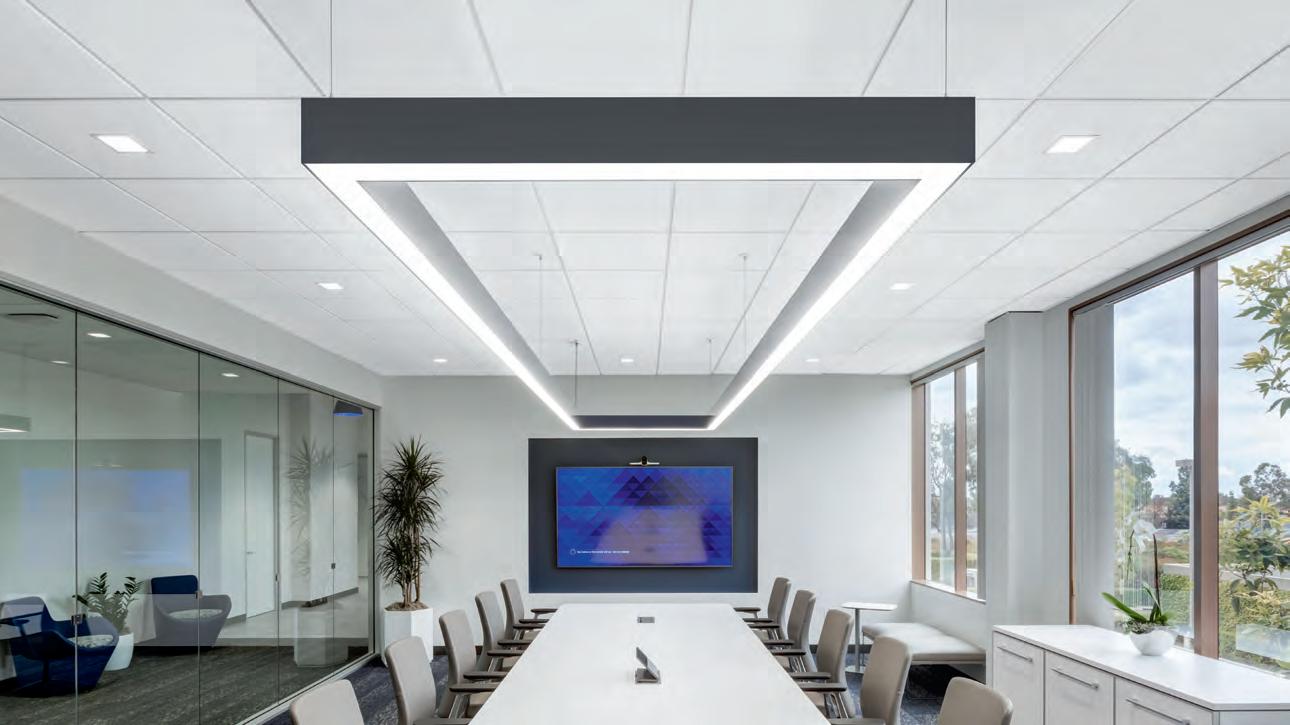
ARCHITECTS DESIGNING
Saves up to 15% energy
Aids in carbon reduction
Templok® ceiling panels can reduce building HVAC energy costs and consumption up to 15%* and enhance thermal comfort for occupants using advanced Phase Change Material (PCM) technology. Start saving today at armstrongceilings.com/energysavingceilings
PG 136
Net Neutrality
Keilhauer is on a journey to make all of its contract furniture carbon neutral.
PG 144
Collaboration Made Easy
How technology like VR Enscape brings projects to life
PG 152
The Sound of Well-Being Form and function merge with today’s top acoustic solutions.
PG 168
Modern Classrooms
As student needs evolve, the spaces where they learn must offer more flexibility.
PG 180
The Future is Circular REGUPOL on pushing the industry forward with smarter solutions
PG 186
Total Transparency
Kimberly-Clark Professional offers a road map to decarbonization.
PG 204
Safeguarded Against Extremes Climate change is expanding the need for resiliency and sustainability in buildings.
PG 212
The Future of Safety Exploring the evolution of access control
PG 229
Healing Places Experts at the Cleveland Clinic and beyond share insights on evolving health care design—including care for caregivers.
PG 238
Comfort Under Foot
Sustainable flooring from American Biltrite makes a difference.
PG 244
Storytelling with Metal How modern cladding is designed to last
PG 252
Move Air, Create Comfort
Innovative HVLS fans support air movement that is effective, comfortable, and energy-efficient.
PG 258
Sight and Sound
Acoustic lighting tiptoes into the spotlight.
PG 264
Manufacturing for a Better World
Insulated metal panels are pushing the green building industry forward.
PG 42
Welcome to Chicago From sustainable skyscrapers to grassroots endeavors, the city on the lake is committed to all things green.
PG 160
The Path to Net Zero How Skanska is working to reach ambitious goals
PG 174
Preserving History with Natural Stone Gensler restored the Old Chicago Post Office with Indiana Limestone from Polycor.
PG 192
Committed to Greatness How companies like Aquafil and Patagonia are pushing the industry forward
PG 198
Building Resiliency Modern exterior product solutions should be designed to adapt to unpredictable weather patterns.
PG 220
Stacking the Deck
Creating flexible outdoor living spaces that flow seamlessly from the home
PG 270
10 Architects
Conversations with top and up-and-coming architects changing what it means to design for equity
ON THE COVER Salesforce Tower Chicago, designed by
with Nfuse® technology
ABPURE® In nity, a Carbon Neutral ooring collection respectful of mother nature
ABPURE® Infinity is a Carbon Neutral rubber sheet flooring collection featuring an elegant tone-on-tone visual in 20 earth-centric colors. It is produced with renewable natural gas from 100% organic waste that reduces greenhouse gases at the source. It is a no-wax, easy-to-maintain flooring, featuring PURE colors that last and contributes to the reduction of the embodied and operational carbon footprint of buildings.
Watch the video:
www.american-biltrite.com
PG 17
Editor’s Picks
The latest in lighting we love
PG 28
A World of Coatings
A wide portfolio of applications continues to meet industry needs.
PG 32
Comfort Flooring
Inside the highperformance flooring segment at Sherwin-Williams
PG 36
Secure Doors
Exploring low-carbon security systems with SALTO Systems
PG 46
A Different Kind of Office ark
The design of Salesforce Tower Chicago celebrates its riverfront location.
PG 52
Flexible Skyscrapers
How SOM is approaching 400 Lake Shore, the former site of the failed Chicago Spire
PG 56
Life Sciences Design
The first major project to open at Lincoln Yards is designed by Gensler and makes a sustainable statement.
PG 64
Salt Shed Pub
Goose Island Beer Co. brings life to an old building on the historic Morton Salt site.
PG 68
Maxwells Trading
Behind the scenes at a rooftop farming experiment, restaurant, and more
PG 74
The Wild Mile
From industrial riverfront to inviting habitat for all
PG 80
Hotel in the Sky
Designing the new St. Regis as part of the city’s third largest skyscraper
PG 85
Bringing in Light Stantec reimagined a UC Davis Health admin building to meet ambitious carbon neutrality goals.
PG 90
Training Greatness
ZGF designed the San Antonio Spurs’ new world-class practice facility.
PG 100
Tiny Grocer
A 1960s post office becomes a specialty grocer and restaurant.
PG 108
Design for Mixed-Use
Perkins&Will designed 799 Broadway in Greenwich Village.
PG 116
Modern Ranch Life
The Skylab-designed Cascade Bungalows at Brasada Ranch combine luxury with care for the environment.
PG 122
Mass Timber Living
An architect uses a dilapidated 1870s carriage house in Brooklyn to test mass timber methods.
PG 130
Forest Lake House
A home in the Berkshires is designed to make as little impact on the landscape as possible.
PG 301
Grid-Aware Architecture
EskewDumezRipple takes a holistic approach to decarbonization.
PG 306
Terminal in a Garden SOM designed this airport terminal in India to connect travelers to nature in a big way.
PG 310
Demanding Biodiversity McCullough Landscape Architecture shares important considerations for designing for climate change.
PG 314
Protecting Roofs
How a coating corrects years of weather damage and degradation
PG 318
Design for Interaction
Site-specific installation
Tidal Shift brought new life to this area in New York City.
Large scale quality illumination that feels like outside
Editor-in-Chief
Christopher Howe
Associate Publisher
Laura Howe
Managing Editor
Laura Rote
Art Director
Madison Wisse
Content Marketing Director
Julie Veternick
Content Marketing Manager
Colette Conway
Contributors
Lark Breen, Andy Carlo, Sophia Conforti, Rachel Coon, Will Crooks, Dave Hanna, Russ Klettke, Peter Lefkovits, Zeek Magallanes, Rachel Mullis, Ian P. Murphy, Sean O’Keefe, Jim Schneider, Myah Taylor, Ryan Brooke Thomas, Kris Vire, Matt Watson, Yuyan Zhang, Jessica Zuniga
ONLINE gbdmagazine.com gbdmagazine.com/digital-edition
SUBSCRIPTIONS
Online shop.gbdmagazine.com Email service@gbdmagazine.com
gb&dPRO
Online gbdmagazine.com/ gbdpro Email info@gbdmagazine.com
Green Building & Design 47 W Polk Street, Ste 100-285 Chicago, IL 60605
Printed in the USA. © 2024 by Green Advocacy Partners, LLC. All rights reserved.
Green Building & Design (gb&d) is printed in the United States using only soy-based inks. Please recycle this magazine.
The contents of this publication may not be reproduced in whole or in part without the consent of the publisher. The publisher is not responsible for product claims and representations.
The Green Building & Design logo is a registered trademark of Green Advocacy Partners, LLC.
RACHEL MULLIS
(“Sight and Sound,” pg. 158) is a freelance writer and journalist based in Vermont. She covers sustainability-focused topics for the state’s independent weekly newspaper, Seven Days, and several national and global organizations, including USAID and EnergyHub. She holds a BA in English from UC Berkeley and an MFA in Fiction Writing from Vermont College of Fine Arts and is hopelessly addicted to green tea. rachelmullis.com
IAN P. MURPHY
(“Mass Appeal,” pg. 122, “Net Neutrality,” pg. 136, and “Safeguarded Against Extremes,” pg. 198) is a freelance writer and editor based in Chicago. Over three decades in journalism he has covered a range of topics, including architecture, travel, and education. He speaks enough French to order a meal confidently and enjoys exploring urban environments, cycling, live music, and the company of a good dog. Murphy grew up in a ’60s modern, attended college on a Brutalist campus, and lives in a Craftsman cottage.
KRIS VIRE
(“Design for Equity,” pg. 270) is a Chicago-based writer, editor, and pub quiz enthusiast. Currently the arts and culture editor for Chicago magazine, he’s also written for the Chicago Sun-Times, The New York Times, American Theatre, and Curbed, among other publications. krisvire.com
NEED A UNIQUE AND INDIVIDUAL SOLUTION?
Customized IP Video Door Stations only with DoorBird.
DoorBird combines exclusive design with the most innovative IP technology in the field of door communication.
It’s important to take a multi-sensory approach to design, according to Rune Veslegard, an architect at Snøhetta. “We are trying to address all the different senses in the way you perceive the space within the architecture—the light and the sensory input from touching the surfaces in the spaces and even how you perceive the space. If you’re blind, for instance, acoustics is a really important component to a threedimensional space without being able to see it with your eyes.” Sight and Sound, pg. 258
2
Non-potable gray water is captured from bathrooms and air-handling condensation, treated, and used for landscape irrigation. Safeguarded Against Extremes, pg. 198
3
It’s important to know how making a product affects people. “One of the most recent examples in the news is the silicosis from quartzite countertops,” says Lindsey Wikstrom, founder of Mattaforma. “It’s tricky because technically if you look at only the carbon footprint of quartzite, it has been described as being sustainable.” Quartz surface imports to the US increased approximately 800% from 2010 to 2018. The CDC says cutting, grinding, polishing, and drilling can release hazardous levels of silica dust. Inhalation of that dust can lead to silicosis—a progressive, debilitating, and sometimes fatal disease. Design for Equity, pg. 270
4
WRNS Studio’s Lilian Asperin has been reflecting on her career lately, having been invited to speak to students recently at her alma mater UC Berkeley, where she graduated in 1993. It dawned on her that 30 years had passed since she was a student. She thought, “What have I learned since then?” She’s been committed to sustainability and equity throughout her career, but she says it was time to double down. “In this third decade of my career, I call it ownership. I literally am an owner in this firm, and I have this incredible sense of responsibility to own these ways of working. I can’t just dream about them.” Design for Equity, pg. 270
5
A passionate group of ecologists, entrepreneurs, and public servants make up Urban Rivers. The nonprofit organization works with the City of Chicago’s Department of Planning and Development, community groups, corporations, and local businesses to ensure thoughtful planning and acceptance of a project called the Wild Mile, so it can be a long-term and cherished asset on the riverfront. The Wild Mile is a public park with ADA accessible boardwalk, and the project is ongoing. The Wild Mile, pg. 74 1
Engineered by Buro Happold, the Santa Monica City Hall East building is one of the most sustainable in the world thanks in part to three water strategies that meet all site needs. Water captured from the roof is stored in a 40,000-gallon cistern beneath the building and treated onsite with cartridge filters and granulated filters—a first in California.
The nonprofit works to decarbonize the built environment with high-performance passive building.
Two passive building organizations exist in the world—Passivhaus Institute in Germany and Phius in North America. Around 2012 Phius was searching for a way to improve the performance of buildings for North America’s numerous climate zones. This led them to move away from using the standards originally based on Germany’s climate.
Phius worked with Building Science Corporation (under a grant from the US Department of Energy) to write the Climate Specific Passive Building Standard. This standard, available for jurisdictions to use as a model for building codes, has been incorporated into code in Massachusetts, Colorado, New York, and more.
Today Phius continues to train and certify professionals while maintaining and updating the Phius climate-specific passive building standard and conducting research to advance high-performance building.
PHIUS DEFINES THE PRINCIPLES OF PASSIVE BUILDING AS:
1 Using continuous insulation throughout the building envelope to minimize or eliminate thermal bridging.
2 Creating an extremely airtight building envelope, preventing infiltration of outside air and loss of conditioned air.
3 Employing high-performance windows and doors. Solar gain is managed to exploit the sun’s energy for heating purposes in the heating season and to minimize overheating during the cooling season.
4 Using some form of balanced heat- and moisture-recovery ventilation to significantly enhance indoor air quality.
5 Using a minimal space conditioning system.
LAKESIDE NET ZERO PASSIVE HOUSE IS A PHIUS-CERTIFIED PROJECT IN SOUTHWEST MICHIGAN DESIGNED BY MARK MILLER ARCHITECTURE.
Saying “passive house” does not indicate an official certification organization or entity. Passive house is a set of principles that can be used and applied in various ways. Phius aims to make passive building principles climate-specific and cost-efficient. The Phius standard is customized to fit each project’s unique climate in an effort to make a comfortable, healthy, and resilient building.
Phius experts say the nonprofit’s work builds upon the standards of LEED and various other green building certifications with passive-specific requirements like airtightness and thermal comfort. Airtightness is a cornerstone to passive building design for both the durability of the enclosure as well as energy savings achieved by minimizing infiltration of outside air and loss of conditioned air.
Phius-certified buildings maintain internal temperatures for longer periods of time, even without heating and cooling. They are designed and built for resilience, habitability, and passive survivability during power outages, extreme storms, fires, and other climate-driven events— without reliance on strained power grids.
Phius-certified projects are reported to use 40 to 60% less total energy use than codebuilt buildings at minimal to no upfront cost premium. By drastically reducing energy use from the get-go with passive strategies like having an airtight envelope, high-quality fenestration, and balanced ventilation, Phius buildings are uniquely equipped to reach net zero.
Carbon neutrality is one of the prime directives at Phius. With its climate-appropriate energy targets and electrification requirements, constructing a building to Phius standards goes a long way in reducing a person or organization’s carbon footprint.
Create designs as subtle or as bold as you you are by adding an Autex Acoustics® Solid Color finish to your next project. With CMYK, RGB, and PANTONE® matching available, your designs can be as colorful or toned down as you need. Available across the Autex Acoustics® range of high-performance acoustic treatments, your customization options are endless.
Roppe flooring, stair treads, wall base and accessories offer durability and peak performance, plus they are environmentally friendly.
Our resilient products are especially well suited to biophilic design, with such features as underfoot comfort, sound-absorbing acoustics and sustainable formulations.
And our updated palette offers a plethora of natural colors and textures, many of which were nature-inspired, and provide design versatility.
THE DUNE TABLE LAMP WORKS INSIDE AND OUT, WITH A DIMTO-WARM LED, A DECORATIVE DIMMER, AND A RECHARGEABLE 10-HOUR BATTERY.
Set upon the table, mounted on the wall, or at your fingertips, this is the latest in eco-friendly lighting.
Brooklyn-based lighting design studio In Common With launched its new indooroutdoor lighting collection, Dune, earlier this year. This function-forward design comes in energetic colors and three styles—the Dune Table Lamp, the Ripple Sconce, and the Ridge Surface Mount. Named for the natural sand formations that shape-shift and migrate with the wind, each fixture brings a touch of whimsy to the ritual of gathering. In Common With is a design studio built on collaboration between artists, materials, environments, and the community at large. Founders Felicia Hung and Nick Ozemba are longtime friends whose path into business began with a shared goal—to create welldesigned items that combined meticulous, made-to-order craftsmanship with scalable manufacturing. In Common With launched in 2018. INCOMMONWITH.COM
hollis+morris has been committed to sustainable sourcing and manufacturing since its founding in 2014, and their latest lighting collection—featuring the Berm Orb, Berm Sconce, and Oyster Sconce—is no different. All light fixtures are assembled in the company’s Toronto-based, LEED Platinum–certified manufacturing facility. All raw lumber used for products that hollis+morris constructs in-house is FSC-certified, and the wood species used are native to the Toronto area to minimize the material footprint.
hollis+morris fixtures are built with LED technology to provide a more energyefficient, longer-lasting lighting solution with lower carbon emissions. Integrated LED ensures that the products can adapt to using even more efficient technology as it becomes available. HOLLISANDMORRIS.COM
HIGH-PERFORMANCE
Fabric, rubber, and rigid models designed for industry, food, parking, retail automotive, EMS and more (BIM objects + specification available).
COMMERCIAL
Backed by decades of engineering excellence, with trend-setting features and options only available from Hörmann.
RESIDENTIAL
Offering value builder to the highest-end luxury designs, and crafted with the quality you’d expect from a company with over 80 years of experience.
Lutron showed off its new Luxury Experience App at KBIS in February 2024 as part of Tiny Home Experience that also featured some of the brand’s latest and most popular offerings. The app allows homeowners and designers alike to take control of the mood and ambience of a space with assets that evoke natural light and more.
Demonstrations showed off a wide range of Lutron and Ketra smart home offerings to reveal how light can shape our perception of any space. “The industry is beginning to realize that the life that we’ve inhabited for the past 10 years has not met the standards of what we’ve previously had with incandescent lights or sunlight alone,” says Cecilia Ramos, senior director – architectural market at Lutron. “There is a thirst and hunger for something that’s dynamic, that’s natural feeling, that’s sustainable as well because it’s low energy.”
The new app features allow users to visualize Lutron products within projects, seamlessly blending digital elements with reality to improve decision-making and the overall customer experience.
Ramos, who studied architecture, says what people demand of their interior lighting today is changing. “For me it’s a shift in mindset where people are like, ‘I deserve better than this.’” LUTRON.COM
Acoustic lighting leader Luxxbox recently launched illi Bon—a beautiful, functional, more compact version of the brand’s award-winning illi acoustic pendant, crafted from recycled PET material and coupled with a high-output LED.
The illi Bon offers sound absorption and direct illumination in a compact form, ideal for smaller commercial and residential spaces. Like its larger sibling, it boasts a captivating array of soft PET outer gills that significantly enhance noise absorption. The mini pendant is available in two sizes and 15 vibrant colors, offering design flexibility while seamlessly blending into existing aesthetics.
Beyond its minimalist design and impressive sound absorption, illi Bon champions sustainability and efficiency. Its high-performance LED uses just 25 watts of power, delivering bright illumination while minimizing environmental impact. LUXXBOX.COM
Swedish startup Enkei transforms building waste into beautiful, functional design pieces. Their debut product, the Reminder (001) lamp, incorporates a movable textile shade and is made mainly from repurposed waste—including from high-end fashion deadstock, discarded ventilation pipes, fossil-free steel, and their own newly developed material, ReCeramix.
ReCeramix is a new material innovation and substitute for concrete. Instead of conventional sand, Enkei opts for ceramic waste from construction sites, tackling the issues associated with both sand mining and improper ceramic waste disposal. This circular approach not only decreases environmental impact but also helps prevent potential soil and groundwater contamination, offering a comprehensive solution to waste reduction and landfill overflow.
“Our mission is to inspire conscious choices, believing in the possibility of another world that challenges today’s linear systems and unsustainable consumption patterns,” says Lovisa Sunnerholm, cofounder and CEO at Enkei. ENKEI.WORLD
Fi™ Interiors’ Acusti•fi™ PET felt combines sound absorption with visual versatility. Select from 21 distinct colors or you can even choose to print natural textures or the artwork of your choice to create acoustic décor that fosters comfort and connection for interior spaces.
Visit us at NeoCon on the 7th floor, space # 5078 for a firsthand experience.
Westcoat’s surface coat category includes the 11-10 System to protect and transform existing concrete or previously coated substrates, yielding a pigmented and easy to clean finish, in addition to the Nano Stain Grind and Seal System, which features no caustic ingredients and can be sealed with highquality clear waterbased coatings.
Application type, texture, color—an ever-expanding portfolio of building coatings exists today for architects, designers, and end users.
How a wide portfolio of applications continues to meet industry needsBY ANDY CARLO
Today’s professionals can choose between cementitious or cement-based coatings or resinous coatings like epoxies, polyurethanes, polyaspartics, urethane cements, and waterproofing coatings—and those are just some of the options. There seems to be a coating solution for almost every application—interior or exterior, new construction or reconstruction, floors or walls.
“Coatings as a whole make up a huge family of chemistries and technologies,” says Todd Cook, product manager at Westcoat, a leader in the field, manufacturing coatings for more than 30 years with systems installed all over North America. “There is a vast array of materials and solutions that fall under the umbrella term of coatings.”
Seamless in nature, the right coating can excel over traditional flooring like tile, brick, or carpet. Coatings also offer greater cleanability without the need for maintaining grout.
Westcoat’s Cove application, for example, can be used with resinous flooring to provide even more ease of maintenance, Cook says. Other specifically formulated coatings also feature anti-microbial additives, ideal for hospitals, veterinary offices, and food and beverage manufacturing. Other features that can assist designers include chemical, impact, and abrasion resistance; fire resistance; waterproofing; flexibility; sound dampening; UV resistance; slip resistance; and safety striping, among other options.
• ALX PRO, WATERPROOFING FOR PLYWOOD SUBSTRATES
• MACOAT, WATERPROOFING FOR CONCRETE SUBSTRATES
• TEMPER-CRETE URETHANE CEMENT
• TIDALSTONE
• DUBRO QUARTZ, 100% SOLID EPOXY FLOORING COATING
“Coatings have really evolved from the standard gray and tan options of the past,” Cook says. “There are unlimited decorative options available for an architect, designer, or owner to choose from.”
Westcoat offers various solid color finishes, including safety or advisory colors, along with custom colors to meet any designer’s palette.
Clear protective coatings like Westcoat’s EC-11 Water-Based Epoxy or SC-65 Water-Based Polyurethane can be used over concrete to protect and enhance the natural beauty of the concrete substrate, while semi-transparent stains can be used with clear coatings to offer the stained concrete look with a durable clear topcoat.
Westcoat metallic coatings, including Liquid Dazzle, can be used to offer even more vibrant and unique finishes. Various decorative aggregates like the TC-60 Color Chips, TC-62 Tidalstone Aggregates Blends, or TC-65 Quartz Sand can be broadcasted or mixed into the coating to provide variegated finishes.
Westcoat also recently released its Tidalstone system—a thin film, high build system. The multi-layered resinous flooring system features the TC-62 Tidalstone aggregate blend and produces a finish that is similar to the look of polished concrete or terrazzo flooring, with a natural flat finish, while providing all the benefits of a resinous flooring, like chemical and abrasion resistance.
The company also recently extended its Temper-Crete line with urethane cement technology. Urethane cements have been proven to outperform previous resinous materials in spaces like food and beverage manufacturing due to their thermal shock resistance, moisture tolerance, and function as well as versatile underlayment for various finishes.
“Emerging technologies are always occurring in this industry,” Cook says, citing the demand of architects, designers, and facility managers working to better serve the industry. “We also see greater education and exposure of the coating industry, which pushes further demand. And we see regulatory changes occurring that focus on certain materials, VOC limitations, and goals regarding better sustainability.”
Westcoat continues to respond to the demand for more options. Innovation requires various customer touchpoints—job walks, lunch and learns, and keeping up with new rules and regulations. “Our team works to be proactive and not reactive. This allows us to stay ahead of trends or updated regulations.”
Westcoat has an extensive team of technical and architectural reps helping customers through the design and product selection process while soliciting feedback about product performance and needs. Fresh solutions are then brought to life by Westcoat’s dedicated team of chemists, formulators, and application specialists. As a result Westcoat is continually expanding its offerings.
For example, Westcoat previously observed food and beverage manufacturing where existing flooring technologies— tile or epoxy—were installed but did not properly meet the facility’s needs. The result was a shorter service life for the product, poor performance, and damage to the facility’s concrete. Westcoat saw how its urethane cement technology, like Temper-Crete, could support the harsh demands of this environment.
Cook says product users trust manufacturers to have the right solutions to help properly address design needs. “Some coatings aren’t a single solution that can be applied across the board, and what may have worked on a previous project may not be appropriate for the next project,” he says. “It’s important to have open communication with the coating manufacturer, to outline the use and demand of the space so the correct solution can be provided.” g
Resinous flooring is “forever.” It is one of the longest life cycle options, and that’s a good thing, says Phillip C. Smith, market segment manager at Sherwin-Williams. Smith is on the leadership team for the High Performance Flooring segment at Sherwin-Williams. He’s been in the resinous flooring industry for more than 20 years, with 10 years in design and construction before that, and he’s seen major changes in the industry. He’s passionate about product.
“Of all the choices for flooring, this is the one that stays with the building,” he says. “It penetrates the surface, bonding to the concrete, almost becoming part of the slab. If you want to do something different in the future you don’t have to tear this out and put it in a landfill. You can build on top of it, which is potentially a more sustainable option, and that’s important.”
The Sherwin-Williams SofTop Comfort Systems is relatively new to the US, but it’s
been successful in Europe for years. It’s among the top resinous flooring options today, and Smith says it is easier on the feet, easier on the eyes, and easier on the earth.
SofTop Comfort is poured, fluid-applied, decorative, elastomeric, seamless flooring that feels soft underfoot. It has acoustic, ergonomic,
SOFTOP IS FORMULATED WITH UP TO 25% RENEWABLE PLANT OILS.
A COMMON MISCONCEPTION IS THAT RESINOUS FLOORING IS EXPENSIVE, BUT WHEN COMPARING LIFE CYCLE MAINTENANCE COST, RESINOUS FLOORING CAN BE MORE COST EFFECTIVE THAN MANY OTHER TYPES OF FLOOR FINISHES.
and hygienic benefits that make it a great fit across health care, education, and other commercial and institutional facilities.
In addition to being ergonomic and soft underfoot, SofTop is tough; it contains industrial grade resins that help protect against abuse. At the same time it offers various design options. It’s a pretty floor, Smith says.
SofTop Comfort SL is a quarter-inch decorative elastomeric flooring system, while SofTop SL is a one-eighth-inch system. Options include 12 standard colors as well as custom color matching, plus aesthetic finishes to complement design themes.
Installation is contractor-friendly. “These are poured, fluid-applied systems that are spread with a squeegee and roller, allowing for large areas to be installed efficiently,” Smith says.
That ease of installation in large part can mean lower cost. “This new generation of SofTop Comfort Systems has an attractive price point and offers the owner excellent value.”
Resinous flooring also requires no waxing. “That’s a big deal,” Smith says. “Many of the traditional options are materials like vinyl, which tend to require waxing. When you look at that type of floor, a lot of folks don’t consider the maintenance life cycle cost. The waxing maintenance cycle involves frequent stripping, reapplying, and buffing through-
SofTop resinous flooring is a great solution for high pedestrian traffic areas.
WHY CONSIDER SOFTOP COMFORT RESINOUS FLOORING?
• FORMULATED WITH UP TO 25% NATURAL PLANT OILS FOR LOWER ENVIRONMENTAL IMPACT RELATIVE TO NON-BIOBASED ALTERNATIVES
• SOUND DAMPENING BENEFITS FOR A BETTER INDOOR EXPERIENCE
• SEAMLESS, SANITARY, AND EASY TO CLEAN AND MAINTAIN
• IMPACT RESISTANT AND STANDS UP TO HEAVY FOOT TRAFFIC AND CARTS
• EFFICIENT INSTALLATION AND FAST RETURN TO SERVICE
out the life of the surface throughout the life cycle. That’s a lot of cost not considered on the front end.”
SofTop is also resistant to chemicals and staining. Its slip-inhibiting surface is seamless, sanitary, and easy to clean. “This is a great fit for health care,” Smith says.
The system is ideal for sensitive, high occupancy, high-traffic environments like hospitals and nursing homes, schools and universities, hospitality and entertainment venues, offices, and retail stores. In a setting like a hospital, medical staff are on their feet all day and need soft flooring as well as surfaces that are easy to clean and that stand up to harsh chemicals. “This is going to provide all of that,” Smith says.
Seamless resinous flooring can be a more sanitary option compared to vinyl flooring, Smith says, which typically comes in squares or sheets with glued or welded seams. When seams or welds break down, dirt and chemicals can penetrate and bacteria and other microbes can grow. “That’s a big deal in today’s world.” SofTop is seamless and sanitary.
In a stadium environment, where you may have tens of thousands of people making noise, you also need flooring that is sound
dampening. “SofTop helps reduce the decibels of sound within the space,” Smith says.
In addition to being hygienic and potentially staying out of landfills, SofTop is low-VOC and formulated with up to 25% renewable plant oils to reduce the environmental impacts relative to non-biobased alternatives. Smith says the industry continues to provide more environmentally friendly options. He says more people want sustainable flooring with a quick turnaround and a long life cycle with flexible design options. Efficiency across all areas counts, and speed of installation matters, too. “Resinous flooring is typically applied over concrete, which normally has to cure 28 days. We have trended toward products that can be applied over what we call green concrete. These new resinous flooring products can be installed on the concrete after five to seven days,” Smith says. “Time is money in the construction industry.” SofTop offers quick turnaround options and a long life cycle. g
SALTO uses 100% renewable energy in its Spain manufacturing and administrative headquarters, thanks to an array of solar PV panels plus offsite renewable energy sourcing.
ACCESS CONTROLS
Low-carbon security systems are the future of door locks.
BY RUSS KLETTKEIt may surprise some that in the conversation about controlled access—that is, how buildings and occupant security are managed by locks and keys—sustainability is a priority. What do the small devices we barely see have to do with carbon, pollution, or climate change?
It helps to consider first what’s new in locks and security. Modern secured access has redefined what locks and keys look like, how they function, and how
they are made. Brass keys that turn a cartridge have been fading from doors for a generation. Fobs and card keys in hotels and corporate settings are common. But moving into the more advanced realm are SALTO Systems, which use wireless, electronic technologies that manage access to multiple sites from a single, flexible platform. From sourcing to manufacturing to product operations, SALTO pursues the greenest methods possible.
The company designed its first data-on-card technology and an advanced battery-operated wireless electronic smart door lock range in 2001. With about a quarter of corporate staff dedicated to research and development, the company’s products have continued to evolve since.
These sophisticated systems run on elec-
THE NUMBER OF CYCLES PER BATTERY OF CURRENT SALTO MODELS
Did You Know?
tricity, but even with the considerable degree of resources SALTO uses in R&D, the company has minimized electricity consumption while eliminating the waste that disposable plastic cards, fobs, and brass keys would generate.
“Our goal was ultra-low power consumptions,” says Colin DePree, who oversees North American sales strategies at SALTO. Most of the company’s locks are powered by simple alkaline batteries—no power-source wiring required at installation—so the goal is to maximize the length of time the locks can operate before a battery change is required. “We measure battery use in cycles or unlocks. The earlier products would get 40,000 to 60,000 cycles per battery. The current models now get 160,000 to 210,000 cycles.” In the near future some locking solutions may not require batteries at all, but will operate instead by harvesting power wirelessly from a user’s cell phone battery.
Multiply those kinds of results over the number of SALTO’s more than 40,000 projects in operation globally. These encompass 5 million equipped access points and 40 million daily users—transforming controlled access on a large scale while providing distinct sustainability benefits to customers.
SALTO SYSTEMS OFFERS
A
For example, Princeton University, with 1,000 faculty, 7,500 students, and 3,200 doors, needed to improve upon its brasskey locks. A working group of more than two-dozen people spent more than a year searching for a better system for their security when they found the smart-card SALTO system. It was installed with minimal disruption to the campus dorms and academic and administration buildings—taking on-campus security and sustainability to a new level.
A multifamily residential development in Calgary is another example. Across nine properties with more than 2,300 residents and 1,400 doors, a better solution was needed for doors that range from glass to aluminum and standard apartment front doors, including on gyms, parking areas, and external entry doors that face temperatures as low as -50ºF in winter. The developers, who are also long-term owners of the facilities, chose a SALTO system for its ongoing support as well as its commitment to sustainability. The specific technologies used are wire-free, operating on a smart-locking platform with web-based software.
In these and other installations the owners and users of the secured access systems have reduced use of power and other resources, generating almost no waste with a smart system that enhances security across the board. They also get the benefit of far lower embodied carbon in the instruments due to
the sustainability measures taken in SALTO’s sourcing and manufacturing process.
That mission of sustainability includes SALTO’s use of 100% renewable energy in its own Oiartzun, Spain manufacturing and administrative headquarters. They accomplish this with an array of solar photovoltaic panels plus offsite renewable energy sourcing, achieving 100% carbon neutrality in line with its ISO 14001 certification.
At SALTO, raw materials are sourced as close to the facility as possible, ideally within 100 kilometers. The 650 employees at their Spain facility are incentivized to carpool, travel by public transportation, or bike. (Fun fact: the Tour de France rolled directly by the company’s Basque region facility in July 2023.)
This ethos extends to every facet and function of the company. “The team responsible for new product launches has been trained on eco-design and the circular economy in order to integrate these into the launch process,” according to the company’s 2022 Sustainability Report.
Why so green in a product category that is perhaps less scrutinized than many other industries? “The original founders are from
SALTO Systems use wireless, electronic technologies that manage access to multiple sites from a single, flexible platform.
Oiartzun,” DePree says. “This is a beautiful place. They are oriented to the local economy and environment.”
The company is privately held by those same people, perhaps giving them a leg up on making decisions that look at the longer-range impact of their work. Environmentalism is embedded in the company’s published core values, written to help meet the United Nation’s 2030 Agenda for Sustainable Development.
Company leadership layers those environmental concerns with the pragmatic realities of what their customers need. For example, in complex buildings and campuses the types of doors and functions behind those doors often require different types of security. That means different locking systems are necessary within the same development. SALTO Systems can accommodate that.
And as actual building construction and real estate design evolves, SALTO develops systems to accommodate such things as well. DePree describes a trend toward modular construction, often built offsite, where walls and layouts are designed to be moved according to changing occupant needs. “We design it so the locks do not need to be changed,” he says. “Space has to be flexible to changing businesses and changing functions. There should be no need to replace a locking system.”
The company leadership studies all new trends in how buildings are built and used, including in student housing and co-working facilities. “We work to complete the circle,” DePree says, referring the cradle-to-cradle philosophy. “This is a focus on longevity, including about the speed of technological advances and making software ‘backward compatible.’”
By this he means using future software with existing locks, negating the need for new physical components. The company also incentivizes customers to recycle old locks and has a research foundation that looks for ways to reuse more than recycle those materials.
To the uninitiated, door locks and latches might seem like a small part of the reduce-reuse-recycle equation. But to users of SALTO Systems secured access systems, it’s a much bigger deal with meaningful impact. g
Controlled access to buildings of all types continues to evolve from brass key and disposable card systems.
How Chicago continues to push for innovative green building
An enormous public park system with plentiful green space, a great lake, vast public transit—there’s a lot you might consider green about the country’s third largest city. The city is especially known around the world for its architecture.
Chicago was an early adopter in the green building movement, says Brian Imus, executive director at the Illinois Green Alliance. “I give a lot of credit to the AEC industry that’s based here in Chicago. They had a lot of interest in green building,” he says. “They did a lot of experimentation early on on how to advance a lot of the new technologies and design best practices. As a result, not only did it have an impact on what was built in Chicago, the architecture community here got a reputation for understanding how to design and build green buildings around the world.” He says Illinois gets recognized as one of the states with the most LEED-certified square footage every year.
The city’s evolving commitment to sustainability continues to be seen in what companies choose to headquarter here, too, Imus says, noting businesses like Salesforce and Google, both of which are pursuing or have pursued all-electric projects in Chicago. “The new Salesforce Tower (page 46) is all-electric. The new Google renovation of the Thompson Center is going to be all-electric. I can’t speak to why, other than I think for corporations like Google and Salesforce, it reflects their corporate values around the environment.”
Imus hopes the lessons of projects like the Chicago Salesforce Tower, which opened in 2023, can be translated into other buildings in the city, too. “How can we translate those successes so they can be easily adopted by other building professionals, by other building types? How do you start taking what we’ve learned and be able to translate that to our schools, to housing?” Imus asks. “I think there’s a huge potential and a huge opportunity to do that, particularly because there’s more and more financing and funding available for decarbonization projects and all building types, which will have a huge impact.”
Chicago has always taken its architecture seriously, says Kimberly Dowdell, current AIA president, who lives part-time in Chicago. “Architecture is such an important identity of the city, it’s prioritized,” she says.
Dowdell credits the city’s leadership over the years for not letting many buildings go into disrepair, which can have a very draining effect on people as well as hurt property values. “It can have a chain reaction, and I appreciate that Chicago has been really protective of its built
environment. My hope is that other cities can take that more seriously,” she says.
While she thinks Chicago does a fairly good job when it comes to sustainable development, she’d love to see a more hyper-focused leadership role in city government with regard to reporting on sustainability efforts. That’s a great opportunity for a chief architect, she says, referring to a program she’s championing as part of her AIA presidency (page 270). “The chief architect role would depend on what the city needs, but I think at the very least championing climate action and looking at affordable housing should be at the top of the list, so I would advocate for that in Chicago.”
From sustainable skyscrapers to community projects like the riverfront Wild Mile, green development efforts in Chicago continue. In April 2024 Chicago City Council debated the Clean and Affordable Buildings Ordinance, which includes support from the Illinois Green Alliance and many others. The ordinance would eliminate natural gas emissions by setting an indoor emissions limit— effectively requiring all new construction to switch to clean power sources like electric or other high efficiency systems.
In particular sustainable development has been a hot topic in the city of Chicago recently. In the last couple of years the city released its climate action plan with a huge focus on addressing carbon pollution from the building sector, Imus says.
“They recognized that 70% of carbon pollution in the city of Chicago is coming from our buildings. The city also released a building decarbonization policy working group that provided 26 different recommendations around how the city can support and advance building decarbonization. The city is starting to act on those recommendations,” he says.
Chicago’s Energy Transformation Code, which was an update to the energy code, was also passed last year, which Imus says is a step in the right direction. “And then the mayor introduced the Clean and Affordable Buildings ordinance this January that the city council is considering right now (in spring 2024).” The Clean and Affordable Buildings Ordinance would eliminate harmful natural gas emissions by setting an indoor emissions limit banning the combustion of fuels that emit more than 25 kg/btu—effectively requiring all new construction to switch to clean power sources like electric or other high efficiency systems. The proposed ordinance would provide exceptions to specific systems, including for commercial cooking and emergency backups.
The state of Illinois’ Climate Bank provides education and financing tools for sustainable projects, which Imus expects to have a huge impact. The Greenhouse Gas Reduction Fund includes $7 billion for competitive grants to enable low-income and disadvantaged communities to deploy or benefit from zero-emission technologies, including distributed technologies on residential rooftops. It also includes $8 billion for competitive grants to eligible entities to provide financial and technical assistance to projects that reduce or avoid greenhouse gas emissions in low-income and disadvantaged communities.
Illinois Green Alliance also offers resources like the new Building Energy Resource Hub, a project to help owners, developers, and others in the industry understand the policy and financing trends around building decarbonization.
In general, conversations about green building are no longer LEED-centric, Imus says. They’re about so much more.
“It’s not just about third party certifications. It’s about truly getting to a place where all buildings are net zero. How do we get there? That’ll take making sure there’s adoption of the technologies we know work. It will take a lot of lessons learned from the early adopters who have done net zero projects in Illinois. I think that’s really exciting.” g
Green space, kayaking, and biking are all accessible from the new Salesforce Tower in Chicago.
“This is a skyscraper on a very specific site in downtown Chicago, which promotes density. We feel cities are more sustainable than suburban sprawl,” says Darin Cook, partner at Pelli Clarke & Partners.
They wanted it to feel like a park. Salesforce Tower Chicago is a modern landmark on a historic site—at the confluence of the Chicago River’s three branches downtown, surrounded by green space with access to the city’s bustling Riverwalk. “It’s really this unique site,” says Darin Cook, partner at Pelli Clarke & Partners and the lead architect for the Chicago Salesforce project.
The new tower anchors Wolf Point, the extraordinary mixed-use development that includes three buildings. Pelli Clarke & Partners started on the project in 2010. “The Salesforce Tower is sort of the crown jewel in the completion of this project,” Cook says. The other two buildings are residential.
With the river and plentiful green space, Cook says this project is not your typical office tower on a city street—and that aligned with the vision of Salesforce, who Pelli Clarke & Partners also worked with for their San Francisco Tower. The project was designed to include bike storage and safe entry so employees can come directly in from the Riverwalk or the lower driveway. “People can ride their bikes into the building right into the bike storage below the building,” he says. “It’s very
PROJECT: Salesforce Tower
DESIGN ARCHITECT: Pelli Clarke & Partners
LOCATION: 333 W Wolf Point Plaza
Architect of Record: HKS Architects
Completion: 2023
Size: 1,450,000 square feet
Structural Engineer: Magnusson
Klemencic Associates
MEP: Alvine Engineering
Certifications: LEED Gold
much this physically active, outdoor-focused environment that supports the youthful spirit of Salesforce.” Amenities like a fitness center with showers, coffee bar, conference center and lounge, and underground parking (hidden from sight) are also highlights. There’s even storage for kayaks.
“It’s not just a multi-building project. It’s really a mixed-use, live-work-play community,” Cook says. Neighbors can interact while relaxing on the green space or Riverwalk, and the project is a short walk to the Merchandise Mart and multiple modes of public transit. “We have great access to everything on the river. It’s really expanding the local community.”
Many office projects today emphasize outdoor connection, be it through roof terraces or other outdoor spaces on the ground. Salesforce Tower has both, not to mention those river views and access. “People want to get out and have fresh air. They want to get a sense of the seasons, the time of day. They want to exercise,” Cook says. The Salesforce team also wanted a large folding glass wall high on the tower that they could open on nice days to let the breeze in.
The entire building is clad with floor-to-ceiling glass. The architects used Viracon [VRE 1-59] insulating glass to reduce the amount of solar energy. “It has a 38% solar energy reflectance, throwing off nearly 40% of the heat that would be cast into the building,” Cook says, with 53% visible light transmittance. “At the same time we’re really trying to spill daylight into the inside of the building, minimizing the amount of electrical lighting we have to provide when it’s nice and sunny. It’s simple, elegant architecture that is still very high-performance.”
The team was also very conscious of where materials came from. Viracon is based in Minnesota, so the glass didn’t have to travel far, and the curtain wall enclosure was fabricated by Harmon, based in Cincin-
The municipal symbol of Chicago is seen throughout the project. The “y” within a circle represents the three branches of the Chicago River. That’s also the representation of Wolf Point, etched into handrails
and in the outdoor space. “That’s really celebrating the intersection of the river, which was essentially the site of the first settlement of Chicago,” Cook says. From the top floor looking out, you feel like you’re sitting in the river, he says.
“Our lobby is right up against this outdoor garden park filled with couches and lounge chairs. People come in and they hang out in the lobby. They don’t just rush off to their office space. It’s trying to be a very warm and inviting, living, casual hangout environment. It’s very much part of the spirit of both Salesforce as well as the trends we’re seeing in office development.”
“In the very beginning of the project we recognized the unique aspect of this site, and we said, ‘This is going to be a park. We’re putting all the parking below-grade and expanding the green space wherever we can,’” Cook says. The team committed to a minimal footprint and to touch the ground lightly.
nati. Both locations are within 500 miles of the project site—a critical measure for LEED certification.
The project also aimed to bring feelings of nature and warmth into the building, with wood details and art. In the lobby a large, rotating art installation cycles through different scenes throughout the day—ranging from a woodland setting from Salesforce’s home base of California to abstract biophilic-inspired digital works, so that feeling of being outside continues.
At the end wall of each elevator lobby are vertical, rolling strips of eucalyptus wood inspired by the river. “It also looks like water rivulets are running through it,” Cook says. Part of that was about bringing in as much wood as possible—not just because that’s what Salesforce wanted, but it’s what many companies want to see in their spaces today. Cook says many of their office tower projects now have lobby spaces that feel like living rooms. “They’re comfortable gathering spaces. They’re not the sort of cold, formal, empty space where you go and check in at a security desk.”
Salesforce Tower Chicago just so happens to be the first building in Chicago to require and measure environmental product declarations, Cook says, so the carbon footprint of materials used across the project
was tracked diligently. Many building professionals have moved on from LEED to net zero, Cook says. “Now everyone’s on a path to net zero. How do we get to net zero carbon emissions? To do that you have to start measuring things.”
The project reported a 19% reduction in carbon emissions for concrete and steel production, with a 27% reduction in the production of concrete used and a 9% reduction in the production of steel used, compared to the industry standard. That equates to saving 7,800 tons of CO2, or getting 1,500 cars off the road a year, Cook says.
Beyond the data, though, a truly sustainable building is one that’s used and loved for a long time, Cook says. This project was especially meaningful to him knowing the site’s history. When Daniel Burnham came up with the 1909 “Plan of Chicago,” it included this site as significant, as he envisioned a building icon right where the Salesforce Tower stands today. “We got to build on this long tradition and history of urban planning and growth in Chicago,” Cook says. “It was a fantastic opportunity and honor to bring this vision that’s been floating around for 100-plus years finally to life. We’ve created a great new landmark and icon for the city.” g
400 Lake Shore, formerly the site of the Chicago Spire, is finally on its way to the Chicago skyline.
WORDS BY LAURA ROTE RENDERINGS COURTESY OF SOM, RELATED MIDWEST
400 Lake Shore, designed by SOM and developed by Related Midwest, is finally under way in Chicago.
What was once a giant hole in the ground in the middle of the Chicago skyline is now on its way to becoming something real—and while not as tall as what was originally planned for that site, the final design may be more momentous because it’s meant to last.
“We inherited an amazing project and site. There was a lot of pressure, just given the history. It was a beautiful building that Santiago Calatrava designed, and it would have been fantastic, but it didn’t pencil out,” says Scott Duncan, partner at Skidmore, Owings & Merrill (SOM), who is designing 400 Lake Shore, developed by Related Midwest, on the former site of the Chicago Spire. “Related took over the site and, through a process, engaged with us. We quickly came to the conclusion that two buildings were better than one—and not quite as tall.”
SOM’s 72-story, 841-foot building—one of two buildings drawn up for the site—is set to house more than 500 residential units, more than 100 of them affordable housing. The first bit of concrete was finally poured in spring 2024—eight years after SOM started working on 400 Lake Shore. It was the first project SOM took on when Duncan moved from New York to Chicago. “It was hugely exciting for me,” he says.
The Chicago Spire was planned to be 2,000 feet tall and was partially built in 2007 and 2008 before construction was canceled; it was simply inefficient. 400 Lake Shore
PROJECT: 400 Lake Shore DESIGN ARCHITECT: SOM
Completion: Anticipated 2027 (Tower 1)
Net Site Area: 95,000 square feet
Architect of Record: Stantec
Interior Design: MAWD
Developer: Related Midwest
Structural Engineer: SOM
Civil Engineer: Spaceco
MEP & Fire Protection: Salas O’Brien Engineers
is planned to be less than 900 feet. “This neighborhood of 800-ish feet is a sweet spot for structural efficiency,” Duncan says. “That’s one of the reasons you see a lot of buildings hover around that height.”
Ultimately a big gaping hole was left behind by the Spire and, years later, SOM was tasked to fill it. “We had to position and design the footprint of the tower so that it sat on what was a pretty crazy circular foundation—the hole you may have seen down there. It was quite literally a square-shaped peg in a round hole.”
At the confluence of Lake Michigan and the Chicago River, 400 Lake Shore will be an example of flexible design, as the two towers are not designed in such a way that they have to be perfect mirror images. “They are like sister buildings, not twins,” Duncan says. “We’re building the first one now, and the sister building will come later.”
This design allows for more flexibility in many ways, continuing inside the building, as the walls can essentially go anywhere. “In our design, because of the bay window facade design and because of this grid we’ve created, we laid out all of the units in a way that was flexible but still had an alignment between the architectural expression, the structure, and these interior partitions,” Duncan says.
The project’s apparent curved profile is actually a strategic stepping of that column grid, Duncan says. “Every time you see a step it’s where the column grid has changed or has a natural break in it. It’s a very structurally efficient and cost-efficient way to achieve what I think is a pretty dynamic form, as opposed to curving the building and making every single unit layout unique, which creates a lot of headaches for construction, leasing, and so on. This is on a module.”
He says some have joked, S-O-M means stay on module. “This could suggest that we’re overly rigid, but I think
what it speaks to is the desire to achieve a deep understanding of the systems we’re working with and then working within that system.”
Its stepped profile also makes the building friendlier to birds, something that’s personally important to Duncan and a hot topic in Chicago lately. “We need to prevent the interruption of bird migration paths. We see what happens if we don’t,” says Duncan, who adds that SOM consulted an ornithologist during the design process. “Because the facade at 400 has a stepped profile, it’s almost like a corduroy fabric or some kind of articulated surface. There aren’t broad expanses of glass that confuse birds.”
The idea of pushing the structure into the glassy exterior wall plane also means there are enough elements in the facade so the birds can orient themselves properly while flying. The project reimagines the classic “Chicago bay window”—a design that is a hallmark of the city’s historic architecture—as a shallow bay of floor-to-ceiling glass, with ornamental metal detailing inspired by the rippling surface of Lake Michigan. The design also creates a better insulated facade than a normal glass facade.
While the narrower east and west sides of the building are more glassy, the north and south have a mix of solid and glazed elements. “That has a huge benefit on opacity in the building and energy performance in the building,” Duncan says. “It’s about a 40% improvement over an allglass facade. It’s like the difference between wearing a windbreaker and a puffer jacket.”
Ultimately a plaza between the two towers will also feature in-demand amenities like public art and spaces for residents and guests within a two-story podium. 400 Lake Shore will connect to the north edge of Chicago’s Riverwalk, with open spaces and pedestrian routes connecting to the planned DuSable Park. g
The project reimagines the classic “Chicago window”—a hallmark of the city’s historic architecture—as a shallow bay of floor-to-ceiling glass, with metal detailing inspired by Lake Michigan. Rendering courtesy of SOM, Related Midwest
Lincoln Yards’ first major project, 1229 W Concord, opens on the Chicago River.
A special frit on the glass that helps prevent bird collisions is also part of the design at 1229 W Concord.
An eight-story-building overlooking the recently revitalized Chicago River sets the tone for Lincoln Yards—Sterling Bay’s new 53-acre mixed-use community in a once heavy industrial area of Chicago. The project at 1229 W Concord encompasses 285,000 square feet and is leasing for life sciences companies.
The building’s relationship to the river was critical to its design, according to Gensler Principal Michael Townsend. “This project is the first picture of what this area could look like in the future and the community’s connection to the river,” he says.
As a life science building, he says it emphasizes Chicago’s commitment to the industry. “It’s saying, ‘Hey, we want to make an investment in life science. We see a lot of great potential for life science in Chicago, and we think a lot of that could happen at Lincoln Yards.”
To be clear, this is not your average life science building. For starters, while its exterior is dominated by glass, that glass is bird-friendly. Access to nature and a sense of
PROJECT: 1229 W Concord
ARCHITECT: Gensler
Completion: 2023
Size: 285,000 square feet
Developer: Sterling Bay
General Contractor: Power Construction
Carpet: Tarkett
Terrazzo: Menconi Terrazzo
Lighting: Anne Kustner
The Genslerdesigned 1229 W Concord life science building in Chicago is a nod to the health and well-being principles established in early 20th century modernism, brought about by the tuberculosis pandemic—natural light, openness, and access to the outdoors.
openness abound, as balconies give people up-close access to the outdoors while city views are abundant. Inside, the interiors are inviting. A warm, neutral color palette draws you in, and public spaces are designed with cozy furniture, wood detailing, lamps, plants, rugs, and other aspects to make public spaces feel more like home.
It’s all inspired by the nature around the building, says Lori Mukoyama, the design principal at Gensler who led the project’s interior design. She and Townsend both have a hospitality background and said part of this building’s mission was to think differently about what people need—especially post-Covid.
A wood wall in the interior is a perfect example of doing things differently. Rather than a perhaps more expected glass wall—giving the feeling of airport security—Gensler thought, why not design something that feels more at home in hospitality? “I don’t want to go to work feeling like I’m going through a terminal every day,” Mukoyama says. “So we created a wood screen that has beautiful DNA. If you look at it from the side, it looks like it has a helix going through it, and then a bookshelf as well.” It offers security and separation, but it’s also aesthetically pleasing and multipurpose.
The design team wanted the interiors to feel like a continuation from outdoors—from water and nature to wood and glass. An enormous white circular staircase conjures the wind as it carries people to the second floor. The color palette reflects the greens and ombre tones of foliage, rugs are layered to provide a feeling of warmth, and woods are pulled from native species. “We’re trying to bring that whole experience inside the space,” Mukoyama says.
Much of the design was informed, perhaps surprisingly, by the sanatoriums of the 1800s and 1900s. While there may have been no cure for tuberculosis, the experts of the time knew access to fresh air and daylight made people feel better. “At the time buildings and architecture were not providing those things. It was a full building movement and the bones of what we think of as modern architecture today,” Townsend says. “If you look back at some of the sanatoriums of the time, you’ll see the direct inspiration we took from those in this building— with these long horizontal balconies and ample levels of daylight in the space, floor to ceiling glass, color palettes, and things like that.”
Those principles of light, air, and openness drove much of the project’s design, as those elements were top of mind when this project started and the design team was largely working from home. “We were all talking about the value of fresh air and access to outdoors and daylight. Those are the principles for a great building and environment for the people inside,” Townsend says.
Mukoyama says the lighting strategy was especially important, as it wasn’t all direct. When you think of a lab you may think of harsh lighting, and the team took great care to ensure that wasn’t the case here. “We wanted to take advantage of the architecture and the glass, taking advantage of full height space. Michael and his team were really conscious to carve out a tall lobby space. Everyone has access to that lobby, so then you give everybody the opportunity to have that nature and that closeness to natural daylighting.”
Gensler’s Lori Mukoyama says the interior design is a true mix and match, including bespoke furniture. “We’re definitely having more fun with it,” she says.
The interior design of 1229 W Concord feels warm and inviting—more hotel or living room than life sciences building.
In the middle of the stairway—itself a work of art in the corner of the lobby—a stunning light fixture hangs, furthering the idea of the helix and adding more soft lighting. “We have a lot of soft cove lighting and indirect lighting. There’s a really beautiful glow. You feel very warm and comfortable, and it’s also very peaceful,” Mukoyama says.
A lot of the design centered on pairing the unexpected— combining the comforts of home with the sterileness of life sciences. In the ceiling, a metal panel has acoustical benefits and provides beauty and a feeling of calm comfort, while the white and wooden staircase brings people together.
“It appears as a visually continuous ceiling, but it also
helps absorb sound. Then, when you go up the stairs, you suddenly have an exposed ceiling. That’s so different because it slides right into this really beautiful, perforated, off-white ceiling panel,” Mukoyama says.
Wood stairs carry you up the stark white staircase. “That ribbon of wood on the inside of the stair becomes the foundation of flooring, to the second level of the amenity area, which is where we have smaller breakout conference rooms and communal tables. That encourages people to have those opening meetings and still to gather and congregate together in a different way,” she says.
From the beginning the design team and Sterling Bay wanted to set the expectation that people who work in
“IT’S A REALLY BEAUTIFUL ART PIECE AND A NOD TO THE INGENUITY AND THE THINKING BEHIND LIFE SCIENCES.”
this building want to take part in an outdoor lifestyle. They want to be connected to a broader Riverwalk experience that will ultimately travel through Lincoln Yards. “Putting the amenities on the ground level and the main conferencing space on level two with outdoor terraces was very intentional,” Townsend says.
Mukoyama says the design continues to reveal people’s desire for outdoor space as part of their daily work lifestyle. People demand access to nature, and they want spaces that feel more like home. You’ll find a beautiful fitness center on the ground floor, and the staircase is highly visible, encouraging people to walk to and from building amenities. “That already changes your mentality of what you’re walking up to.”
The stair itself is prefabricated in three steel sections, designed and engineered to be self-supported. “It’s a real-
A high-performing facade, low-VOC materials, terrazzo flooring, and recycled materials round out the building’s design. “Everything we’re seeing architecturally is also a beautiful mix of sustainable materials,” Mukoyama says.
A dramatic spiral stair connects the first and second floors and is a nod to the DNA helix.
ly beautiful art piece and a nod to the ingenuity and the thinking behind life sciences,” Mukoyama says.
Plants, too, are unexpected in a life sciences building, as such spaces are required to be more sterile due to contaminant concerns. “Since we created such a generous amenity and community space on the ground floor and on the second, we wanted to bring that to light.” They used the public area as an opportunity for biophilic design. “In the actual lab area you wouldn’t be able to do that, but in a lobby environment you can, so you get both experiences in this building.”
The building’s position along a migratory path meant considering serious bird-friendly strategies, too. Ultimately several levels of the building’s exterior glazing were outfitted with a subtle stencil pattern to avert bird collisions, protecting hundreds of species annually. It’s an expectation of all buildings at Lincoln Yards now, Townsend says.
“Chicago’s one of the most heavily trafficked migratory paths on Earth, particularly in the United States. We have a particular problem here in Chicago with this. This building has a number of ways that it is helping to minimize those collisions,” he says.
The typical glazing in the tower is an insulated glass unit with the Solarban 90 low-e coating and a 0.23 solar heat gain coefficient. A silkscreened quarter-inch dot spaced two-by-four inches helps make the glass more visible to birds. The exterior reflectance of the unit is also only 12%, which Townsend says is very low compared to many modern buildings in Chicago. “This helps limit the reflectance of the sky in the glass, which can also disorient birds.”
Lighting can also interfere with birds’ navigation systems. “That’s one of the reasons many buildings in Chicago turn off their lights after a certain period of time,” Townsend says.
As part of Sterling Bay’s efforts to further establish the life sciences community in Chicago, 1229 W Concord plays a key role in this first phase of developing the heart of Lincoln Yards. While the state-of-the-art building is designed to be a home for innovation, it also sets a precedent for design that is both science- and people-friendly, as the project takes cues from hospitality at every turn.
“It was a very purposeful blending of maybe what you would expect in a more warm, hospitable environment, almost like your living room or a hotel or any other hospitality-based environment,” Townsend says. “Scientists are people, too. All the things we think are so valuable to the human experience are also valuable in a lab environment.” g
Bright, airy, and open spaces were key to the design of the interiors. Hospitalityinspired amenities like a fitness center and café are at home on the lower levels with access to the river and public green spaces.
Goose Island brings life to another old building on the historic Morton Salt site.
The Salt Shed Pub, a new Goose Island brewpub and adaptive reuse project, opened in May 2024.
What used to be a garage outside of the old Morton Salt Shed in a previously industrial area of Chicago is now open to beer and music lovers alike outside the popular riverfront music venue.
Similar to the 3,600-capacity indoor performance hall in the main historic building next door, this smaller building long sat vacant when the historic Morton Salt Company Warehouse Complex (circa 1929) closed.
“I’m assuming for quite a while it was used as a repair shop for their vehicles and their machinery. Then it was all walled in and beat up and left for dead,” says Craig Golden, founder of Blue Star Properties, the contractor on this and all projects at the Salt Shed site. Now it’s home to the Salt Shed Pub, a new Goose Island brewpub opened in May 2024, complete with a skyline-backed riverfront patio. Inside, sunlight pours through new skylights as patrons enjoy a rotating selection of Goose Island brews and great eats. Woman-owned, Chicago-based architecture firm AltusWorks, known for their work in preservation and adaptive reuse, designed the project.
“The most sustainable building is one that you reuse, one that doesn’t get torn down, so that already was a big start,” Golden says. The team was able to reuse virtually everything that remained at the site—from the old fire doors to the bow barrel truss roof. “We restored that and repaired the truss. They used the existing footprint, so it worked out really well. It was a nice way to reestablish that building on a new path.”
Chicago-based architecture firm AltusWorks, known for their work in preservation and adaptive reuse, designed the project, working alongside contractor Blue Star Properties and Goose Island.
It’s the first business on the site that will be open seven days a week, which excites Golden, who wants the area to continue to be a place where people gather—music or not. Golden wants the whole community to enjoy the property. “Food shows, art shows, anything that engages the community more—that’s who we are,” he says. “That’s what keeps people coming back, too. Post-pandemic we’re all looking for things that are real. And we want to get back to doing what we love and taking care of each other.” The Salt Shed Pub is open to patrons of drinking age regardless of whether they have a ticket to a Salt Shed show.
“Music has always played a huge role in the identity of Goose Island, from our 312 Block Party to partnerships with music festivals and more. So to be able to move our home brewpub next to a space that’s not only one of Chicago’s most-talked about new music venues but also a refurbed historical landmark site is an exciting way to further cement ourselves as Chicago’s beer and be a part of the city’s next chapter,” says T.J. Annerino, senior director of marketing at Goose Island Beer Co.
Goose Island opened its first brewpub on Clybourn Avenue in Chicago in 1988. Open for 35 years until December 2023, the Clybourn brewpub was the birthplace of the now beloved brews. “Goose is a company we worked with for many years in the past in our music venues, so we were very excited that they wanted to move their operation there,” Golden says.
Golden is also the cofounder of hospitality group 16 on Center, known for its work in restoring and running music venues like Thalia Hall and the Promontory in Chicago and, now, The Salt Shed. Most recently they also welcomed Reverb to the Salt Shed site. The store for new and used musical equipment announced plans to take much of the second floor of the main building for offices. Another beverage outfit, likely in the property’s original boiler room, may also be on the horizon. “The goal is to have things going on all the time,” Golden says. g
Building and celebrating community, from floor to rooftop
Vintage lighting inside Maxwells Trading was sourced to feel appropriate to the 1928 period the original building is believed to date back to.
There is so much life inside Maxwells Trading. More than a restaurant, this building that used to be a manufacturing warehouse near Chicago’s West Town is now three lively entities that celebrate all things made with care.
Maxwells Trading is part of a larger collective of food, design, and sustainability-centric businesses. The project spun off from The Roof Crop Farm, founded by Tracy Boychuk. The building on Carroll Avenue reopened after sitting vacant for awhile when The Roof Crop became the anchor tenant, launching in 2015 with the installation of its first commercial farm. “It was very rough, like someone had tried to renovate it but never used it. It was empty I think for quite a while,” Boychuk says. The building was a single-story, open warehouse, believed to date back to 1928, that they eventually added on to.
In addition to the restaurant and The Roof Crop (TRC), the building is now home to an apothecary and design store called Third Season, also founded by Boychuk, and Flashpoint Innovation, a food and beverage
PROJECT: Maxwells Trading ARCHITECT: Bureau Gemmell LOCATION: 1516 W Carroll Ave
SIZE: 4,300 square feet
INTERIOR DESIGN: Meg McMorrow Design, WDA Design GREENHOUSES: Wisconsin Greenhouse
The bar top features concrete and wood, using reclaimed live edge walnut slabs and burying the live edge with concrete.
“Instead of being a live edge, it’s a live middle. It was definitely challenging,” Boychuk says.
Third Season is The Roof Crop’s retail, coffee, and apothecary shop featuring items and ingredients that come from the roof as well as locally grown flowers.
consultancy with its own high-end kitchen upstairs where clients test menus and more.
Most people will likely initially interact with the building via the main floor restaurant, Maxwells Trading—an open kitchen concept from Underscore Hospitality, led by Chef Partner Erling Wu-Bower and Executive Chef Chris Jung. Many ingredients for the dishes and cocktails served are sourced onsite from one of the three greenhouses or plentiful gardens on the roof. Even the honey comes from TRC beehives. It’s an evolving example of what TRC can do, as they build farms, design products, and develop experiences to engage clients in a shared mission of sustainability all over the city.
Walking up to Maxwells Trading on a summer day, windows are open and light pours in. A cohesive, considered design carries across the three businesses and embraces the building’s industrial history, from concrete floors to some of the original brickwork. The dining room ceiling features a series of warm wooden slats that evoke broken shutters and provide visual balance against the concrete floors, while a double arch designed by Bureau Gemmell founder Lynsey Sorrell separates the restaurant from the Third Season retail space. The double arch also provides a beautiful focal point and can be closed with an oversized linen curtain for private events.
“We reused everything we could, and we maintained the integrity of the building as much as we could,” Boychuk says. In the instance when something did have to be new, they let the building’s original aesthetics guide the way. “There was sort of this mantra in the project about how to stay true to what the building’s foundation was,” she says. They kept the original color scheme and repurposed wood from another project where possible.
Much of the design throughout the building was brought to life by Boychuk and Sorrell as well as Meg McMorrow Design and WDA Design. WDA’s Warren Afthai designed many of the benches and stools. Leather on the barstools were sourced from the neighborhood, up the street from Tannery Row, and a local millworker made the ceiling’s wooden slats, which hide the acoustic treatments.
On the other side of the double arch, Third Season sells everything from the honey made onsite to Ikebana vases from a local maker down the street. The shop keeps regular daytime hours, but restaurant patrons can also pop in anytime they’re dining if they want to add a special item to their bill or pick up a fresh bunch of TRC flowers.
Just beyond the store is the Third Season design studio, where a team works on floral designs and dries flowers. The large space also hosts flower-arranging and dye classes or can be reserved for events. Boychuk’s husband is an avid vintage book collector, and finely curated book collections can be found on both floors, many of them for purchase.
“We also had the opportunity to return the window and door expressions to something that felt more old-period appropriate,” Boychuk says. The design team wanted everything to feel open and warm but also industrial and true to its beginnings. In TRC’s upstairs office space, they chose a modern version of glass block, completely clear, with darker grout. It’s both true to what would have been in the neighborhood originally and allows for great light.
Maxwells Trading is part of a business collective consisting of The Roof Crop headquarters, a retail space called Third Season, and a food and beverage innovation hub formed in partnership between The Roof Crop and Flashpoint Innovation.
On the roof in late April the TRC team was experimenting with different kinds of drip irrigation. “We can now quickly plug and play as we need,” Boychuk says with excitement. “We’re not locked into it always being this kind of crop in that bed. I can put drip tape down here and do one crop, and then I can pull the drip tape up and put on that sprinkler head and do a different crop. Right now we’ve got arugula and herbs growing.” The tomatoes were due to be planted soon.
TRC worked with a soil scientist to develop an effective, more lightweight mixing soil they’re now using on the roof. “It’s more tillable. It’s more farmable. It can be more productive,” Boychuk says. “Really what we do is productive landscaping. It’s like what any other green
roof company or any other landscaper would do, except that most landscapers are green roof people—they put their green roof on and then they’re done, or they maintain it and they’re done. You have a relationship with us past just the landscaping.”
The combination of business types is part of what the team hopes will keep people interested in supporting all of these companies for the long haul. The engagement piece makes it easy for people to invest in, Boychuk says, but that’s where many developers get stuck. “People are actually simpler than you think. They like nature; they want to do the right thing. At the buildings we’re farming or doing these productive landscapes on, it’s a big draw for them that it’s not
The Roof Crop (TRC) is a design-focused, urban agriculture initiative that values and promotes sustainability, ecology, and community engagement.
“YOU HAVE A RELATIONSHIP WITH US PAST JUST THE LANDSCAPING.”
just a sedum green roof on there. Even if they don’t ever see it, they love the idea that there’s something more than that, that it’s contributing to pollinators, for example,” she says. “When you have that engagement, they start to talk about sustainability, and then they start to value sustainability.”
The combination of partners with related but varied interests is a win-win, too, she says.
“When you put partners together like this who have these different audiences, you get to create a Venn diagram where they cross over. That’s where there are exciting opportunities that maybe none of us would have thought of. And that’s when you see success.” g
TRC maintains a number of beehives around the city, including on the roof at Maxwells Trading. You can also buy their honey at Third Season.
From industrial riverfront to inviting habitat for all
Urban Rivers, SOM, and others are creatively adapting what was an unsightly relic of Chicago’s industrial past into a thriving natural habitat for plants, animals, and people.
Icould not have been less prepared for a muskrat to pop its head up from a hole amid new plant life on a floating habitat in what was once a very industrial area. In fact, I didn’t even know if it was a muskrat. I had to look it up to confirm. It looked so happy.
“Yes, they should look so happy; we provide them with so many easy meals in the form of our native plants, but they are helping eat invasive mussels as well, so that’s something,” says Phil Nicodemus, research director with Urban Rivers, who studies and maintains the Wild Mile project.
This previously unlikely spot behind an REI and Off Color Brewing in Chicago is now home to the start of the Wild Mile—a floating eco park and public green space that is bringing life back to the Chicago River.
“The water quality has improved. The number of fish species has increased in a very short time. The nutrient levels in the river are starting to return,” says Doug Voigt, a partner at Skidmore, Owings, and Merrill (SOM). Voi-
gt leads urban design at SOM and has been heavily involved in the riverfront project since its early stages. “There’s a lot of great evidence now that this first phase has been completed; you can really see the value and the importance of a project like this around green infrastructure.”
The Wild Mile is a planned mile-long, interactive river restoration project that originated as part of a larger framework plan with the City of Chicago, Urban Rivers, and SOM. This plan outlines potential development and green space expansion opportunities along the north branch of the river. The first phase of the project was completed in 2021, and phase two was scheduled to begin in summer 2024, as the Urban Rivers team planned to install the second 300 to 400 feet of floating wetlands and walkways with continued support from SOM in coordination, planning, and advocacy.
Already Voigt likes to walk down by the Wild Mile in all seasons. “Like a lot of Midwestern landscapes, it’s beautiful at all times of the year, if you have an appreciation for places like Chicago,” he muses.
As life returned to the area in spring, Voigt was taken not just by the greenery but also the many colorful plantings popping up. When I was there in April a pair of geese seemed to be protecting their eggs in the far corner of the park, honking furiously when gulls flew overhead. “When you’re down there it’s this immersive experience walking on this very intimate boardwalk. Being able to sit in nature and look back down the Chicago River to the skyline is a really unique experience,” Voigt says. Site furniture from Vestre, a Norway-based furniture company committed to sustainable manufacturing, dots the boardwalk.
This focus on the Chicago River dates back 20 years or more, and SOM has long been involved in helping not only provide public access but also to restore natural edge conditions. It all started when Urban Rivers, a grassroots organization, began to experiment with the floating wetlands concept. Voigt says it was low-tech at first—milk crates with soil and tomato plants to test the concept. Then they started to raise funds to develop the first floating habitat.
Voigt says those ideas took root in many different ways over the years, including a city plan in 2003 that was updated in 2008, showing illustrations of the initiative on the east side of Goose Island in Chicago. “It was not called the Wild Mile then, but the idea of creating additional park space, public access, and naturalizing the edges of the Chicago River outside of the core of the city were all part of that.”
When complete, the Wild Mile is designed to be a 17-acre floating eco-park.
Before the project got off the ground its advocates argued that the area’s channelized edges prevented native flora from establishing and were barriers for fauna, while surface runoff and combined sewer overflows contributed to poor water quality. Urban Rivers wanted to convert under-utilized industrial spaces like this one, use plants to improve water quality in the river, and become a local garden. It’s now well on its way as both a source of food and life for native plants and animals and a point of social connection for the area. Its location near businesses like REI and Whole Foods, too, have been beneficial as sources of corporate sponsorship.
“It’s an incredibly diverse group of collaborators who have worked on this project over many years,” Voigt says. “We had early workshops with scientists from
will transform the area into an oasis of floating gardens, forests with public walkways, kayak docks, and other amenities.
the Shedd Museum and from Northwestern University. Then you have community groups like NeighborSpace and Friends of the River as well. It’s pretty incredible.”
The project faced challenges in that the majority of the land around the Wild Mile is privately owned, and the river is managed by the US Army Corps of Engineers. It required much effort to get all private parties to see the value of investing in the health of the river, then they had to get approvals from the federal government. “To do anything in that corridor you need not only support from the Army Corps of Engineers but to deauthorize a navigable channel requires an act of Congress,” Voigt says.
Through community-based planning work Urban Rivers and SOM found a way to add wetlands and public access within the first 20 feet of the retaining walls, working with the Army Corps. “In some ways it’s a park system developed on found land that doesn’t belong to the city, and it doesn’t belong to a private property owner. It’s an interesting set of solutions from a policy and overall approach of implementing green infrastructure
in the public realm,” Voigt says.
The team leveraged existing infrastructure like the sheet pile along most of the channels to anchor the floating docks and garden beds. “We attached to that at certain points to bring access down to the water level, but the actual rafts are secured very carefully because this portion of the river, like most of the river, was industrialized. There are a lot of pollutants in the sediment at the floor of the river. There was a very careful anchoring and set of weights placed to minimize the amount of disruption to the sediment, which would then put pollutants back in the water. That was all very carefully considered and intentional in the design but also during the install.”
The continued work is inspiring other cities to look to Chicago for guidance. “Projects like the Wild Mile are a really great example of the creativity and innovation that’s happening throughout the city. Chicago is putting water innovation front and center,” Voigt says.
Cities of all sizes all over the globe have already
“IN MANY WAYS WE’RE NOT ONLY PRESERVING BUT GROWING AND STRENGTHENING HABITAT FOR ALL FORMS OF LIFE.”
reached out to see what they can learn from the project. “We get inquiries all the time—people wanting to learn from the Wild Mile and see how those lessons can be applied in their own community. In many ways we’re not only preserving but growing and strengthening habitat for all forms of life,” Voigt says.
He champions the Wild Mile as not simply solving a single problem. The project is also investing significantly in the community and has the potential to benefit people, plants, animals, and even the business community around it.
“We constantly look at these types of projects at multiple scales—from the benefits of the individual to the community to restoring habitat and biodiversity to its connection and place within the city and even the entire ecosystem,” Voigt says. “Projects like the Wild Mile highlight the importance of these nature-based solutions in moving beyond single-purpose solutions. These investments have the ability to bring transformative change in many different ways to the surrounding community.” g
The St. Regis Chicago is an enormous undertaking and a beautiful success.
The architecture of the Studio Gang–designed St. Regis Chicago (Vista Tower) is heavily influenced by water and sky.
Towering at 101 stories, The St. Regis Hotel and Residences is hard to miss in the Chicago skyline. It’s the third tallest building in the city, and it includes beautiful new five-star lodging.
As the Architect of Record for the entire project, bKL oversaw and managed a team of more than 25 consultants, including seven other architectural and interior design firms. “We coordinated and managed a pretty enormous team of consultants,” says Charles Hasbrouck, director of bKL. The exterior form and material selections were designed by Jeanne Gang of Studio Gang Architects.
Hasbrouck says bKL approaches every project with sustainability in mind, and the St. Regis was no different. Strategies like rainwater retention were implemented for irrigation, and the building’s dense, urban location includes great proximity to public transportation.
Scott Farbman, design engineer and LEED consultant on the project, says LEED can help to push a project’s sustainability goals forward, even if it’s just a starting point. “When we are thinking about sustainable outcomes, goals, and strategies, we do let LEED often drive the process, but there are things that happen outside of the LEED framework, which can be limited in scope. At a high level following the credits and protocols of LEED really helps us better select things like materials and finishes, the products used within the building, lighting,
PROJECT: St. Regis Chicago
DESIGN ARCHITECT: Studio Gang
LOCATION: 401 E Wacker Dr
Architect of Record: bKL Architecture
Completion: Summer 2023
Size: 1,982,846 square feet
Design Engineer & LEED consultant: dbHMS
Structural Engineer: Magnusson Klemencic Associates
Wind Engineer: RWDI
Contractor: McHugh Construction
Interior Design: KTGY + Simeone Deary
Design Group, Gensler
Acoustics: Shiner Acoustics
Hotel Lighting: CD+M, Reveal Design Group
Landscape Architect: OLIN
The St. Regis hotel project included low-emitting adhesives, sealants, paints, and coatings to improve the quality of indoor air for occupants.
Lighting and thermal controls promote productivity, comfort, and well-being of the occupants in the building.
the HVAC systems—pretty much everything comes with a certain performance requirement attached to it that really helps promote and drive sustainability and also occupant health and wellness,” he says. “When you put all that together, you get something like the St. Regis, and the hotel specifically.
On the exterior, Studio Gang used high-performing glazing as a primary sustainability strategy. A gradient on the hotel’s exterior is tailored to channel solar heat and keep interior temperatures comfortable throughout. In construction, rebar, aluminum component window wall assembly, post tension strand cable, gypsum board, metal framing stud, steel pipe casing, concrete, and other materials with significant recycled content reduced impacts resulting from extraction and processing of virgin materials. The project also diverted more than 75% of construction waste to redirect recyclable material back to the manufacturing process.
Inside, sustainable accents can be seen throughout the property, including curated art featuring reclaimed materials behind the front desk.
“Focusing on the complexities of a building like St. Regis, it makes it very challenging to do something that is quote-unquote as simple as LEED,” Farbman says. “LEED can be fairly easily implemented into many building types and project types, but when you scale it up to a project of the size and caliber of St. Regis, it becomes inherently more complicated and complex.”
He says the number of entities involved and the time it takes to get a project this large completed can be challenging. “You need someone to manage and champion the sustainability process, and that person needs to be there for 10 years or so. It’s a very big undertaking, and I would applaud the success of a project like St. Regis.”
The project is expected to achieve LEED Silver. g
THE PROJECT SUCCESSFULLY MET THE UNIVERSITY OF CALIFORNIA’S CARBON NEUTRALITY INITIATIVE’S GOAL, AND THE BUILDING ACHIEVED LEED GOLD. THE DESIGN WAS 31% MORE EFFICIENT THAN A STANDARD ASHRAE BASELINE BUILDING.
How Stantec transformed a former call center into a bright administration building for UC Davis Health
WORDS BY LAURA ROTE PHOTOS BY KAT ALVESYou’ve seen it all before. The 1990s era building, the large and boring box, outdated in every way, and ultimately torn down. But the former call center turned UC Davis Health Admin Building really didn’t need to be torn down, as it offered a wealth of opportunity. The design team at Stantec saw those opportunities and seized them.
Before the new office building opened the organization’s administrative departments were spread across the region, requiring new staff to visit more than one location for IT, HR, and other support functions. To streamline access for staff, Stantec’s design team set out to create a modern workspace that combined services under one roof while giving employees a much more inviting, light-filled environment.
The development team chose an existing two-story, 194,000-square-foot office building originally constructed in the 1990s. The outdated space was not without its challenges. Each level was isolated from the other, with limited natural light and few opportunities for staff to gather. Stantec’s design updated and unified the building, taking a minimal approach with fresh, light colors throughout the project and extensive native landscaping and solar sails outside for a new, engaging place to gather outdoors.
Sustainability was at the forefront of all decisions, as the design team aimed to meet
the requirements of the University of California Carbon Neutrality Initiative. Reusing an existing building rather than designing a new one resulted in a 58% reduction in embodied carbon.
“It would take 27 years for an equivalent new energy-efficient building to offset the embodied carbon savings of this project through its operations,” says Brian Crilly, design principal at Stantec. Crilly oversaw the sustainability strategies along with Stantec’s Carbon Impact team for the UC Davis Admin Building. “The amount of CO2 removed is equivalent to 700-something cars driven for one year—or almost 400 homes’ energy use for one year by reusing the building here.”
The team was committed to using the very best they could get their hands on for this project—from Red List-free materials to FSC-certified woods, PVC-free products and resilient flooring. A wood veneer by Koroseal (FSC-certified) was used instead of wood or plastic paneling, and carbon neutral carpet and low-VOC paints add to the project’s clear commitment to sustainability.
The UC Davis project was designed in large part to increase access to daylight, both for the aesthetic and mental health benefits, as access to light improves circadian health. New light wells now bring daylight to the darkest reaches of the vast floor plates, and more greenery promotes wellness and a sense of calm throughout the project.
Lobby fins not only serve to block solar heat gain from the west facing window wall, but also function as radiant panels and create a pleasant lobby experience.
Communal spaces include a mix of patterns but also are often white, bright, clean, and engaging. Crilly says whites can sometimes be off-putting, especially if there’s so much it’s overstimulating alongside too much light. “What worked for us is that we used the whites sparingly in places,” he says.
The team broke up an expansive floor plate with a center boulevard between staircases, interrupted by three large skywell openings. Those areas also have more high-quality, tactile material choices and less white—with warmer champagne colors and wood-looking textures, Crilly says. “Sometimes it can be difficult with an open office; it becomes a sea of workstations. We succeeded in yes, there are a lot of workstations, but they all have access to either views to the exterior or views internally to shared spaces at the center, where it’s not just white colors and added daylight.”
A focal wall in a lobby area was one creative solution responding to too much light. “Behind that wall is a two-story window wall that faces directly southwest; it’s the worst exposure you can have for a two-story glass wall in our region.”
The design team wanted to have some solar control at that wall, but with minimal work to the building envelope at the exterior other than paint and tile work. They provided a series of fins as a focal element that wraps over the ceiling. “These fins gesture in that direction. It provided a really nice play with daylighting and now also lighting, but they’re also used in the heating and cooling of the building as well. These are radiant panels.”
The building is now all-electric power, and radiant panels heat and cool the entire proj-
Right: Incorporating greenery, daylight, and many chances to connect creates a sense of well-being and calm. Light and bright finishes allow natural light to bounce deep into the space.
ect. “There are zero ducts except one room that is essentially for a data center for the building,” Crilly says. It’s an added benefit, as that gave the team additional free space and removed the usual visual clutter. It also reduces recirculated air and the potential for distribution of allergens.
The design also includes plentiful plants and living art in the forms of hanging circles with greenery, plus access to the outdoors, but the design also works with the nature that’s already there, Crilly says.
Generally speaking, much of the year is nice in the Sacramento area, Crilly says, so outdoor access was a must. After the pandemic there has continued to be a far greater outcry for high-quality outdoor spaces as well as views to nature at every turn.
“This building is surrounded on three sides by mature trees. While this is more of a suburban setting, you can see from the cafeteria, we allow for views to this greenery. That’s very important from the standpoint of human health, and that gets back to the textures and colors we’re using as well—a little bit more natural and not just white everywhere.”
A variation in the color of tiles and more champagne colors provide a timeless feel, too. “We’re not designing based on fad. It’s a variation of patterns and textures, it’s access to daylight, and it’s the celebration of shadows. You get the dappled shadows or lighting from the tree canopy. These are things you cannot recreate exactly with building materials,” Crilly says. “It’s timeless in the sense that it’s based in nature.” g
PROJECT: UC Davis Health Admin Building
ARCHITECT: Stantec
LOCATION: Rancho Cordova, CA
COMPLETION: October 2022
SIZE: 194,000 square feet
CERTIFICATIONS: LEED Gold
Balance—between public and private spaces, mental and physical well-being, the use of shadow and light—is constantly at play in the design of the new San Antonio Spurs’ facility.
Intentionality and duality were constantly at play in the design of the Victory Capital Performance Center. The building needed a heroic public facade and a variety of interior programs that allowed the team’s staff functionality while also giving the players a more intimate space to recover and reconnect.
Jetting across time zones. Unpredictable schedules. Transitioning from professional basketball arenas to airplanes to parking lots and back to training facilities. The San Antonio Spurs’ athletes spend an unusual amount of time indoors, constantly making demands on their minds and bodies. So when the leaders of the Spurs organization began developing plans for the new Victory Capital Performance Center, considering the players’ holistic well-being was essential.
It took a decade of traveling, touring, and research along with consultations with the architectural leaders at ZGF to land on a future-proof biophilic design that would give the Spurs an edge in professional sports while providing a restorative space for the players to feel grounded and reconnected with nature.
“We knew this building had to be of its place, connected to the community and its fan base but also rooted in the land from which they rise,” says Kathy Berg, ZGF’s lead design architect. “You know you’re in San Antonio when you’re there. The historic missions that glow this intense
yellow-orange in the early morning light; they’re beautiful and were a huge inspiration for us.”
Built seamlessly into the limestone landscape at the foot of the Texas Hill Country, the Victory Capital Performance Center is 138,000 square feet of practice courts, locker rooms, training areas, strength and conditioning spaces, recovery spaces with hydrotherapy pools, a sauna, float tanks, kitchen, meeting spaces, an outdoor training area, and more. The training center anchors a multi-building, 45-acre campus focused on the advancement of human performance and boasts a grand three-story facade facing a public plaza that tapers into more intimate, residential interiors with landscaped outdoor oases tucked away from public view.
Connecting the players to nature even when they are indoors was a driving force in the decision to use mass timber construction, as was the fact that mass timber has proven to significantly reduce a building’s embodied carbon.
The natural aesthetic of timber was further incorporated with cross-laminated timber panels provided by SmartLam and a practice court with Robbins Sports Surfaces’ maple hardwood flooring system, installed and painted by Covington.
Once wood was determined as the key element in the center’s biophilic design, Texas-based Timberlyne became an essential player in the engineering, fabrication, and erection of the mass timber structure, which included wooden columns and 150foot long beams—the largest on the market at the time—from American Laminators and Duco-Lam.
“Mass timber offered a huge benefit in terms of carbon sequestration and the biophilic feel. So much of the timber is exposed, and it just feels really good,” Berg says. “We also loved that mass timber harkened back to how early structures were built with stone walls and timber roofs, which was a good expression of the local region.”
Mass timber also allowed ZGF to eliminate a second level of materials, since the exposed beams and columns served as the finish.
To further ensure building materials reflected the area, ZGF explored the city’s famed Riverwalk and historic Pearl district, drawing inspiration from the water and concrete structures that help to sustain cooler temperatures in San Antonio’s extreme climate. “Even if it was 106 degrees, you could walk inside these concrete structures and feel the temperature drop,” Berg says. “We had equally amazing moments ascending up and down the Riverwalk. It could be an immensely hot day, but you’d get down to the river and it immediately felt cooler.” ZGF drew on these elements, bringing them into the design with colonnades, courtyards, and the use of water.
Daylight in all of the interior spaces was another way ZGF worked to reduce electric energy used for lighting the building. “It was the players’ unexpected schedules that drove the idea that every occupied space in this building should be daylit, that every space should allow you to look outside and see the environment you’re in, ground yourself, and know what time of day it is,” Berg says.
Ensuring
Riverwalk
The one-level building also provided ample roof area and sky access for a massive PV array. A rainwater capture and storage system serves some of the onsite irrigation, an important feature in San Antonio where water is a precious resource. And best practice mechanical elements installed by Arup make the project even more sustainable.
Considering how the building would be used was just as crucial as how it would be built. The Spurs’ referred to their original practice facility as a “fortress of solitude,” and the organization wanted to carry that ethos forward, creating a new center that balanced a fortress-like public front with a private and restorative interior, ensuring players had a safe space to train and focus on their job.
For 55 years innovation has been at the heart of the Spurs organization. ZGF and Spurs leaders toured many two- and three-story facilities, even spaces with no windows, as part of their research. Many of the places they visited were very bespoke—it was going to be challenging for the buildings to evolve with advances in technology and equipment. “The Spurs were constantly asking: How can we future-proof this facility? How can we provide something that will shift and change as technology changes?” Berg recalls.
The Spurs’ analytics team continually focuses on deep-level analysis of the players’ performance and well-being—referencing studies on circadian rhythms, how being exposed to light affects athletes, how players perform when traveling west to east versus east to west. “We spent a lot of time with the organization thinking about how—as technology continues to change—they could integrate that into the facility and not disrupt its functions,” Berg says. “There was
a constant intentionality about how people would move through this facility that drove the overall layout.”
It was essential that the entire organization had spaces to collaborate and hold meetings, that anyone could engage publicly or navigate their way through the building in less public ways, that the players could practice and “pound the rock,” as the Spurs players like to say, but also that everyone inside the building would always have a place to reconnect with nature.
Design conversations also consistently revolved around the question of how to give the building a monumental shell while still offering those intimate and biophilic interiors. This impactful public facade was created with board-formed concrete and glass fiber reinforced concrete piers that form a colonnade that utilizes the play of angles and light to convey an image of power and strength or, depending on the time of day, the sense of a light being left on at home.
“On a clear day in that strong San Antonio sunlight, you see the center’s hard exterior shell, the black windows, that give this sense that, ‘Yeah, we’re here. This is a great place to be. But we’re doing work inside,’” Berg says. But then at night as daylight fades, the center shines. “You see the double-lit mass timber beams, the championship banners, and you get that glow of wood in the three-story entry lobby. You get that duality of what happens in the building during the day versus at night.” g
A long corridor is a perfect example of the building’s functionality and balance, allowing people to meet in a more public arena at the front office or taking them back to a more private social interaction area.
“I love the play of light and shadows,” says Kathy Berg, ZGF’s lead design architect.
PROJECT: San Antonio Spurs Victory Capital
ARCHITECT & INTERIOR DESIGN: ZGF Architects
LOCATION: San Antonio
Completion: 2023
Size: 138,000 square feet
Local Architect: RVK Architecture
Developer: Lincoln Property Company
Structural & MEP Engineer, Lighting Design: Arup
Civil Engineer: Pape-Dawson Engineers
General Contractor: Joeris General Contractors, Sabinal Group
Energy Modeling: Arup
Mass Timber Installer: Timberlyne
Facades: Curtainwall Design Consulting
Landscape Architect: Rialto Studio
Ultra-low conductance polyurethane foam for superior strength, durability, and unrivaled U-factors.
Material thermal conductivity – Btu-in/(hr-oF2-ft)
Architect Side Angle Side and entrepreneur Steph Steele bring a second Tiny Grocer to life in Austin.
A 1960s-era post office is turned into a specialty grocer and French bistro. The new space, along with a large outdoor seating area, serves as a hub for the community, and people love dining on offerings from Chef Jo Chan.
Even in bustling cities, each neighborhood needs an anchor—a hub where the community can congregate around a shared space, the doors are open to all, and chance meetings can take place.
Recreating this concept of a community hub was a critical piece of the vision behind the second iteration of Tiny Grocer, which in September 2023 opened in a rehabilitated mid-century post office in the Hyde Park neighborhood of Austin, Texas.
“The beauty of reusing a post office is the central location post offices have historically taken within neighborhoods,” says Annie-Laurie Grabiel, who co-owns and operates the architecture firm Side Angle Side with her husband Arthur Furman. “This neighborhood has so many people walking and riding their bikes that the space became a natural community center.”
Tiny Grocer is a small-format market that carries curated specialty items alongside a full cafe and deli as well as a wine and coffee bar. The new location—which, while still tiny, is considerably larger than the original—also includes a full-service restaurant, Bureau de Poste, which serves modern French cuisine by celebrity chef Jo Chan.
The concept is the brainchild of entrepreneur Steph Steele, who commissioned Side Angle Side for the project after Grabiel and Furman designed her home. Rather than create a new vision from scratch, the original Tiny Grocer offered the architects a successful template to build off of while integrating their own touches.
“In a way our assignment was to take that success and grow it,” Furman says. “When a client has such strong ideas and a strong vision, it’s our job to listen and make sure we can bring that concept to life.”
Furman and Grabiel approached the project’s design with an understanding that there would be three focal points to the space. The first—and foremost, from a commercial perspective—were the products themselves. “We had to ensure the merchandise was highlighted front-and-center,” Grabiel says.
To accomplish this the team defined the grocery aisles with custom white oak cabinets that complemented the character of the merchandise without stealing the spotlight. “The quality of the millwork indicates that these are premium, highly considered products,” Furman says.
The architect duo designed the display shelves to span the large steel windows in the front of the market so potential customers could catch a glimpse of the products from the sidewalk outside, enticing them to enter the store.
The second focal point Furman and Grabiel worked with was the Tiny Grocer coffee and wine bar. Located at the center of the indoor space, the bar needed to be open and inviting so customers could easily navigate around what was expected to be a high-traffic area.
“We knew there was going to be a lot of activity here throughout the day, so we
On the street-facing side of the lot the team added a concrete wall with a banquette and trellis to give the space a courtyard feel. Integrating a long, steel planter on the adjacent side of the lot created another edge for the space and protects from any disturbance from cars in the parking lot.
The outdoor dining space was once a loading zone for the former post office; now customers can enjoy fine French cuisine in a courtyard setting reminiscent of the Riviera. Tables by Portofino and chairs by Isimar provide plenty of space beyond the limited indoor seating.
wanted to make sure it was visually accessible and that the flow worked well,” Grabiel says. Like much of the rest of the space, the coffee and wine bar are light, open, and airy. Even the countertops are a sparkling white and gray quartz.
The third and final focal point of the rehabbed space—the 1,500-square-foot outdoor dining area—came into conception later in the project timeline. “The full-service restaurant wasn’t part of the original scope,” Furman says. “We were almost ready to submit the permit for the interior renovation for the store and cafe.”
The post office’s loading area had originally presented Furman and Grabiel with perhaps their biggest challenge. “It was a street-facing facade that everyone could see and was sort of a blight on the neighborhood,” Grabiel says.
Around the time when the design team was considering whether and how to activate the outdoor space, Steele began discussing the idea of potentially incorporating a full-service restaurant into the project with Chan.
Given that the indoor cafe seating area was limited, the design team knew they would need to add outdoor seating to ac-
commodate a busy dinner rush. “We thought about adding some picnic tables outside, but as our discussions became more serious and the idea of the restaurant moved forward, we knew we would have to be more intentional,” Grabiel says.
If the former delivery zone was to become the restaurant and cafe’s main dining area, Grabiel and Furman wanted to ensure diners felt casual and comfortable. They therefore conceived of the space as an outdoor room— enclosed yet open. “We wanted to make you feel that you were in a space, not just out on the street,” Furman says.
On the street-facing side of the lot the architects added a concrete wall with a banquette and trellis to give the space a courtyard feel. Integrating a long, steel planter on the adjacent side of the lot created another edge for the space. “This not only covers any disturbance from the cars in the parking lot, but also allows customers to peek past the planter into this intriguing space,” Grabiel says.
Aside from adding more seating, the patio space also presented an opportunity to incorporate more bathrooms and back-of-house space for the restaurant, like busser and wait staff stations.
For architects historic preservation and
rehabilitation projects offer more than a vintage canvas to work off of; they are also far more sustainable than building from scratch. The notion of using recycled materials to reduce the burden on current resources is central to Side Angle Side’s philosophy on green design.
“We think the most sustainable thing an architect can do is to reuse an existing building and give it another life,” Furman says. “When designing new construction, designing for long life and loose fit allows for our work to be reused in the future.”
The original building structure itself was the single biggest reused material of the project, but Side Angle Side incorporated other reclaimed materials as well, including the quartz countertops and the brick pavers adorning the patio.
“I think it’s important to make the distinction that not adding in new materials to a project is very sustainable,” Grabiel adds. The decision to leave the original concrete slab uncovered and the ceiling rafters open, rather than sheathe both with new materials, was not only a design choice but a conscious effort to reduce the project’s carbon emissions.
If there are lessons for other designers in this project, Furman says it’s that “if you can remodel or reuse a building, don’t knock it down and start over.” g
PROJECT: Tiny Grocery & Bureau de Poste
ARCHITECT: Side Angle Side
LOCATION: Austin, TX
Completion: September 2023
Size: 5,000 square feet
MEP Engineer: ATS Engineers
Structural Engineer: Creative Engineering
Builder: Archive Properties
Building Shell: Thought Barn Studio
Landscape Design: Side Angle Side & Wild Heart Dirt
The new space, along with a large outdoor seating area, serves as a hub for the community. Reused materials and an eye toward minimalist design help reduce the project’s carbon footprint.
Expanding beyond the premier Durable® Series of healthcare recliners, the broad and varied lines of sleep products crafted by the design team at Knú® Healthcare have made it their fastest growing category, enhancing the patient room with a comfortable seat and sleep space for loved ones to find welcome relief.
Outside of the patient room, several collections of public area seating round out the offering. Visitor and lounge seating, hip chairs, modular lounge, and others bring trusted comfort to the masses, without sacrificing performance and durability.
799 Broadway further diversifies a mixed-use neighborhood.
When the New York studio of Perkins&Will was selected to lead the design of a boutique office project in Greenwich Village, it presented a unique opportunity for the design firm to reimagine what the future of workspaces looks like within a distinct neighborhood context.
“Even though people think of the Village as this small-scale, informal, brownstone neighborhood, the next generation of office workers and tenants are looking for a much more loft-like, fluid, and flexible environment,” says Robert Goodwin, design principal at Perkins&Will New York.
Though the firm has a global reach with more than 20 offices across multiple continents, their expertise lies outside of commercial office design, Goodwin says. “We realized that landing the project was a bit of an uphill climb for us.”
To ensure their brief stood out from competing bids, Goodwin’s team designed their proposal in the format of a tenant lifestyle magazine, which featured a series of articles about the site’s zoning, possible tenant amenities, and potential occupants.
“It was a very unique proposal,” Goodwin says. “The client told us afterward that our focus on the tenant experience and the needs of the users of the building is really what galvanized them to work with us.”
Completed in 2022, 799 Broadway offers 182,000 square feet of next-generation commercial space across 12 floors. The interior office layouts are open and airy, with 15-foot exposed ceilings and floor-to-ceiling windows
bringing natural light and the vibrancy of the cityscape into the workplace. The design also places a greater emphasis on equity by breaking down traditional hierarchies.
“Our design is a reversal from the traditional Midtown Manhattan office, where senior-level folks get the window offices and everyone else is on the interior,” Goodwin says. “This building creates an environment where everyone gets to be a part of the perimeter, and it doesn’t feel like a traditional hierarchy-driven workplace.”
Sustainability was top of mind for both the design team and the client. Solar orientation and daylight were studied during the design phase to help inform the massing and envelope of the building, which primarily faces east and north.
“Solar heat gain on the eastern face was minimal and did not require an external shading system,” Goodwin says, and limited south-facing glass allowed for a 10% reduction in the cooling tower load.
Meanwhile the building’s narrow floor plates, high ceilings, and open format provide an abundance of natural light that limits the need for artificial lighting and lowers energy usage. And with six different subway lines converging three blocks away at Union Square, the building has no need for onsite parking—substantially reducing its overall carbon footprint. These features and others helped 799 Broadway achieve LEED Gold.
“You don’t separate design and sustain-
ability; they are one in the same,” Goodwin says. “We always need to be considering energy efficiency, resiliency, regeneration, and occupant wellness. True sustainability requires a comprehensive approach.”
In a dense city like New York “the zoning parameters for the massing of buildings is all about how you get daylight to the street,” Goodwin says. There are two ways to accomplish this: the “wedding cake” approach, where the designers progressively terrace the building back from the street at higher intervals; and the “tower” approach, “where you make the building skinny so light can go around it,” though the latter requires adding height to achieve the same floor area.
Given the local character of traditional mid-rise buildings in the Village, Goodwin and his team adopted the terraced approach with setbacks at every other level. They were aided by the distinct nature of the site itself, with Broadway starting to curve at 11th Street, creating an angular context that provided opportunities for additional terraces.
“There’s this unique moment in the New York City urban character that we had a chance to recognize and celebrate,” Goodwin says.
The site also sits across from the historic Grace Church, a renowned French Gothic Revival built in 1847 that features a secluded courtyard filled with trees and greenery.
“The white limestone of Grace Church gave us a theme to work with,” Goodwin says, serving as an inspiration for the white architectural paneling that trims the exterior angles of 799 Broadway.
The integration of metal panels also helped solve one of the key challenges for the design team: balancing the needs of contemporary office tenants with a respect for preserving the feel of the surrounding neighborhood.
“As you can imagine tenants want to see the view, which means they want to have a lot of glass,” Goodwin says. “We wanted to design something that was not all glass.” They wanted to respect the local character of Greenwich Village. The white panels break up the facade of glass windows while ensuring the building stands out from the typical “glass box” typology.
At the same time, Grace Church’s lush courtyard inspired Goodwin and his team to incorporate more natural elements into their design.
Fifteen-foot ceilings and floorlength windows help bring natural light into the space, giving the interiors an open and transparent feel while lowering energy costs.
“We were really struck by this notion that an office building should embrace and engage nature,” he says. “One of our core questions was: How do we recognize that and take this moment of nature and bring it into the building itself?”
Natural materials were integrated into the interior and exterior design, including a faceted wood ceiling and stone panels in the double-height lobby.
On top of that, the tapered design framework of 799 Broadway allowed the architects to incorporate outdoor terraces on nearly level, “with the idea of understanding the potential to bring nature inside and extend the workplace outdoors,” Goodwin says.
They also added their own outdoor courtyard in the rear of the ground-floor space that houses additional tenant amenities, including a fitness area and bike storage. The building offers a total of 17,000 square feet of outdoor space—a rarity among New York City office buildings.
Leveraging natural materials and outdoor space was only one aspect of the building’s health-focused design. Given that it was conceived during the uncertainty of the pandemic, the architect and developer placed an even greater focus on features that promote the well-being of the building’s occupants.
To improve indoor air quality, the team incorporated MERV-8 and MERV-13 air filtration systems along with a bipolar ionization system that affects the molecular protein structures of viruses and pathogens, making them less infectious. “Each floor experiences five to seven fresh air exchanges per hour, and tenants can monitor indoor air quality in real time,” Goodwin says.
Touchless access is also utilized throughout the building, including in entryways and all amenities areas. All of these features contributed to the building achieving WELL Certification and a Fitwel 2-star rating. g
PROJECT: 799 Broadway
ARCHITECT: Perkins&Will
LOCATION: New York City
Completion: 2022
Size: 182,000 square feet
Structural Engineer: DeSimone
Contractor: Consigli Construction
Civil Engineer: Bohler Engineering
MEP/FG: Cosentini
Certifications: LEED Gold
The palette of the bungalows reflects the high desert outside. “We purposefully wanted nature to be invited to come into this space with a certain neutrality.”
“For a moment nothing happened. Then after a second or so, nothing continued to happen.” This idea of “nothing happening” forms the backbone of a luxurious western retreat at Brasada Ranch’s Cascade Bungalows in Bend, Oregon.
“We liked this idea because ranch life is an opportunity to slow down, to connect with the land, and be present as a human in this place,” says Nita Posada, project director and Skylab Architecture principal. In the bungalows local artisanry and regional themes frame moments of observation and peace with sustainable style.
The Brasada Ranch owners tasked Skylab to build 32 adults-only guest retreats with three main priorities—a boutique resort experience, integrated hospitality, and ranch life. Posada says the first 16 bungalows have been almost fully booked since their opening in August 2023. She expects that if spring and summer see the same popularity, the second set of 16 will follow soon.
To invite ranch life, each bungalow is set into the high desert landscape with a perfect view of the Cascade Mountains. “The view is doing a lot of work for us. It’s one of the main design elements,” Posada says.
The bungalows offer guest rooms with a sunken living area and cozy fireplace. Each bathroom has a private patio with a hot tub and outdoor shower. Big windows frame the mountainside and maximize daylighting; overhangs and screens diffuse the desert
sun and offer some privacy from the resort’s nearby adult pool and tennis courts.
“Finding the balance between privacy and an incredible view set the stage for how we oriented and placed the bungalows on the campus,” Posada says. Originally the plan consisted of four rectangular buildings of four suites each. After analyzing the site’s topography, the units were separated and slightly staggered, offset for privacy from the other units and nearby amenities.
The architects were able to work within the topography to maintain much of the original landscape and trees. Plus they minimized asphalt on the property; to integrate further with quiet ranch life, the bungalows are designed for golf cart access.
“It gets really hot down there. The more planting and less paving you can have the less heat island effect you get in that area. Plus we wanted to encourage people to walk around the site for a combination of benefits: sustainability, people moving their bodies, and reduced emissions from cars,” Posada says. The electric golf carts—or as Brasada calls them “Ranch Rovers”—allow for relative quiet in the bungalows.
Building with the topography, utilizing daylighting, and encouraging guests to travel via golf cart isn’t going to earn anyone a LEED certification alone, but Brasada Ranch’s main buildings did achieve Gold,
The bungalows offer a taste of ranch life in a boutique resort experience.
The Skylab team ethically and sustainably sourced building materials, furniture, and more by collaborating with local firms and artisans.
“We love the idea that in the summertime when it’s hot, people could have the windows open and the fans going and that it’s still very comfortable. It’s a very magical place.”
PROJECT: Cascade Bungalows at Brasada Ranch
DESIGN ARCHITECT: Skylab Architecture
LOCATION: Bend, OR
Completion: August 2023
Size: 14,816 square feet
Contractor & Architect of Record: Sun Forest Construction
Interior Design: Skylab Architecture
while the owners opted not to pursue certification for the bungalows.
“But it was important to keep in mind that this is a very sustainable property. We wanted to make good choices and build with integrity on the site,” Posada says. All the wood finishes are FSC-certified, and some of the casework was completed using scraps from other parts of the project.
One of the biggest challenges to construction was that the units are right in the heart of occupied spaces, which stayed operational throughout. Thoughtful phasing allowed guests to continue to enjoy the resort and reduced the impact on the environment during construction.
Some of that phasing also considered how to avoid trucks of furniture and supplies driving back and forth to Portland every day. “We wanted to keep the carbon footprint low on this project.”
The team’s most intentional sustainability-focused, carbon-footprint-minimizing endeavor is the regional sourcing of materials, objects, and artworks. The team conducted a full review of all specified products to make sure they met Greenguard Gold Certification and Red List–free requirements and were ethically sourced.
“We worked with the vendors and the subcontractors to switch things out whenever possible,” Posada says. The team was able to swap in local tile, custom fabrications, and casework as well as much of the art and objects in the bungalows. “We wanted the communities in Bend, Redmond, and the surrounding communities to have a hand in shaping the next generation of the ranch.”
The Skylab team even helped with the small hospitality details, sourcing local soaps, coffee, cocktails, wine, and the custom breakfast baskets delivered to the suites each morning. “I’d never been asked to support the process of what soap goes in the shower, but it was nice to be able to do that. It was such a seamless integration between the contractor, the owner and Skylab. Everyone feels ownership.” g
The idea of heritage was crucial to the design decisions in the bungalows, aiming to link old and new and
allow guests to truly disconnect, going back in time while having very comfortable amenities.
In 2023, 79 solar PV panel installations around the world generated 35.4 GWh of clean energy.
Kingspan’s Global Planet Passionate program strives to add solar PV systems to all our wholly owned facilities and achieve 60% direct renewable energy use by 2030.
Our 10-year global sustainability program set ambitious targets across four focus areas: carbon, energy, circularity and water. Learn more at planetpassionate.kingspan.com.
*U.S. EPA Greenhouse Gas Equivalencies calculator. 14,758 metric tons of CO2 equivalent.
An architect makes his future home a test case for mass timber construction.
The project restored the carriage house’s original redbrick facades using a variety of local fabricators.
Aaron Schiller—founder and lead designer of the New York City-based architectural design firm Schiller Projects and a former carpenter—was looking for a residential project that would allow him to try his hand at mass timber construction.
“We were looking for clients who were interested in pushing the envelope on sustainability,” Schiller says. “We identified a need for a better quality of housing in terms of carbon footprint. It’s critical to the future of the country.”
Engineered for high strength, mass timber is lighter than steel or concrete and can replace both in load-bearing floors and walls. It’s also much lower in environmental impact than such carbon-intensive materials when constructed of sustainable lumber from managed forests.
Schiller eventually found the perfect project—an 1870s carriage house in Clinton Hill badly in need of renovation and primed for residential conversion—and the perfect clients: himself and his partner. “We bought it ourselves to design as a tentpole of what’s possible,” he says.
The building had seen better days. Formerly a limousine garage, the property’s front and rear facades were marred by previous renovations that bricked up windows and installed rollup doors. “It could have been mistaken for a meth lab,” Schiller says.
But the building didn’t share its sturdy, load-bearing masonry walls with any adjacent buildings—a rarity in the high-density, historic neighborhood. A gut rehab would present “a unique opportunity to add to an older structure,” Schiller says.
Long-range sustainability was central to the project. While commercial clients like to see LEED and other certifications, “that really is only half the point,” Schiller says. “You aren’t talking about the carbon footprint of the building and its construction. What drove us was the capacity to minimize the carbon footprint of the materials we were putting into the building.”
Since mass timber construction is relatively new to the United States, Schiller scoured the East Coast to find a larger project his
future home might piggyback onto. A New England university was set to start construction on a mass timber dorm building, and he convinced the supplier to load a few extra engineered panels on its trucks.
“We called the manufacturer and said, ‘Hey, you’re already shipping all this timber to the Northeast. What if you added 5,000 more feet?’ Schiller says. “We showed up with a U-Haul truck, turned around, and delivered the raw material to our fabricator.”
Brooklyn-based Tri-Lox milled the lightweight, fire-resistant panels to specifications, fabricating them to within a sixteenth of an inch tolerance and transferring them from the factory floor to the job site. Material costs were a fraction of what Schiller would have paid for a standalone order.
Much of the home’s lighting was integrated into the mass timbers in manufacturing, creating the world’s first electrified laminated timber (ELT) installation. Schiller partnered with Stickbulb, a New York Citybased sustainable lighting company, on the patent-pending system.
“When you make lighting integrated at the building level, you lose the pounds of aluminum in the fixture,” Schiller says. “It’s just LEDs and wire, so you’re able to get more control on the materials that come in and out of your site and limit its carbon footprint.”
Structural mass timbers were installed from flatbed trucks in just six days, marrying the new construction to walls that had settled and bowed since the 1870s. “We had to put something completely perfect coming out of a modern factory on top of this built structure from 150 years ago,” Schiller says. “There were some challenges.”
The studio also recycled components of the original structure, including the massive structural beams of old-growth North American timber that had sustained smoke and water damage over the years. “The old struc-
A stairway of gluelaminated Douglas fir descends through the center of the house, lit by a large skylight that forms part of a rooftop terrace.
ture of the building is now the flooring of the completed building,” Schiller says. “We recycled the building inside the building.”
New components are designed to last 100 years or more without degradation. “We approached the project with the lifetime of the home in mind,” Schiller says. “Should the house need to be replaced at some point, the materials used can be repurposed without producing waste.”
The building’s facades now satisfy Landmarks Preservation Commission guidelines, showcasing redbrick construction, arched windows, and dark accents. The windows were fabricated a few blocks away, reducing the environmental impact of elements like a 15-foot wall of glass on the new thirdfloor master suite and terrace.
A striking three-story staircase made of glue-laminated Douglas fir ascends through the center of the house, illuminated by large skylight. At the bottom, the building’s former coal ash pit has been repurposed as an indoor garden. “There’s a Japanese maple growing in the middle of the house, which has the additional benefit of cleaning the air,” Schiller says.
The home’s HVAC maximizes energy efficiency and adds to air quality. Schiller estimates that 45% of the square footage
would have required drywall if he hadn’t used mass timber. “You’re creating a more organic and health-conscious environment,” he says. “If there are less VOCs in the atmosphere, the whole house is healthier—and the wood smells really good.
“The thing with this project is that it’s so constrained,” Schiller adds. “You’re in the middle of Brooklyn. You have a very well-defined lot. And then you have the opportunity to do something on the interior that defines it. The big moves we made— bringing in the timber, doing the stair, introducing the skylight—have all been richly rewarding.”
Permitting caused a few delays because the house was only the third mass timber structure in New York City and the first residential property. “We had to educate people in the planning and fire departments about mass timber’s capacities versus its risks,” Schiller says. “A lot of people in this city aren’t used to working with this material.”
But the community “showed up” for the project to keep its construction impacts and carbon emissions low, he says. “The challenge of doing something new is that you have to bring a lot of folks with you. Fortunately the mission around climate impact gets a lot of people to the table, so people’s ears perk up and they say, ‘OK, this is different. We want to participate in this.’” g
PROJECT: Brooklyn Mass Timber House
ARCHITECTS: Schiller Projects, Acheson Doyle Architects
LOCATION: Brooklyn
Completion: 2023
Size: 3,050 square feet
Builder: Schiller Projects
Structural Engineer: Silman Associates
MEP/FP Engineer: PA Collins
Timber Fabricator: Bensonwood
Lighting Design: Stickbulb, Schiller
Projects & Loop Lighting
Interior Designer: Schiller Projects
Flooring: Tri-Lox
Landscape Architect: Brook Landscape
Schiller added a rooftop master suite and terrace to the carriage house in converting it to a singlefamily residence.
The Forest Lake House was designed to have the smallest environmental impact as possible.
The black Accoya treated siding underscores the architects’ goal to diminish the visual impact of the home, allowing the structure to slip into shadow and age beautifully with minimal maintenance.
“You could always go back and re-stain it if you wanted to, but the idea is to let it age and grow with its location,” says Pedro Pachano, of Pachano & Vollert.
PROJECT: Forest Lake House
ARCHITECT: Pachano + Vollert
LOCATION: Lee, MA
Completion: May 2021
Size: 6,000 square feet
Contractor: 377 Builders
MEP Engineer: Baukraft
Structural Engineer: Berkshire Engineering
Lighting Designer: Pachano & Vollert
Stone Supplier: BAS Stone
Windows: Yaro
Plumbing Fixtures: Dornbracht
The flooring is a natural wide plank oak provided by a local supplier.
Tucked among the trees, a house emerges like a shadow in the Berkshires. Architects Amparo Vollert and Pedro Pachano, co-principals of the New York-based firm Pachano & Vollert, wanted the home to camouflage with its surroundings, making as little impact on the landscape as possible—visually, but also in terms of its physical and environmental footprint.
“It’s always our strategy to try to integrate whatever structure we design into the landscape,” Vollert says. Gazing from a paddleboard on the lake edging the backyard, she says the house is difficult to spot.
The clients, two artistically inclined retired lawyers, wanted a calming retreat in the forest for their family of eight. They were involved at every stage of developing the house.
“The client now knows the wall system as well as we do,” Vollert jokes. “It was fun to have engaged conversations, to propose an idea from our perspective, then have it become theirs. It is like a woven tapestry we created together.” Together they designed
custom pieces like the staircase handrail and dining table, and selected pieces from Egg Collective, Dmitriy & Co, Kalon, Allied Maker, and B&B Italia as well as fabrics from Maharam and Schumacher.
From the front it is impossible to perceive the totality of the house. Nestled into the foliage and the topography of the site it appears to be just one-and-a-half story. As you move around the house, the full three stories come into view.
To accomplish this the architects maximized the potential of the half-acre site— which is very tight for a 6,000-square-foot house. The previous structure was much smaller, leaving most of the site full of natural foliage. The architects aimed to preserve as much of it as possible.
An 80- to 100-year-old maple caught their focus as one to preserve. “We liked the idea of framing that beautiful tree from different perspectives of the house,” Vollert says. As the building plan took shape the architects decided to separate the living areas from the
“It’s a project that we feel very honored to have worked with these clients and to have had all the stars align, when the clients, the builder, all the consultants and us are working together in a very fluid, open way, but with that boundary of sustainability.
Having that as our lighthouse, everything really fell into place quite smoothly in this project,” Vollert says.
bedrooms so two main volumes emerged—a private wing and a living wing pivot around the maple to offer views of the tree from trunk to canopy.
“Part of our strategy is to put together a team—owner, us, builders, engineers—that all work toward the same goals, so when you start to implement the project, everything is relatively smooth,” Pachano says. Saving the maple tree and achieving their sustainability goals required commitment from everyone working on the project to ensure construction waste was disposed of responsibly and the impact of the building process was minimized. Their first big test took place when excavation revealed a mass of sandstone underneath the southern end of the site. The immediate inclination was to blast the rock away, but Pachano hit pause. “This is a huge stone embedded in the ground there. Why can’t we just pin to it? A good portion of that half of the building now is pinned into
the rock. We actually use the ground to anchor the house.”
Beneath the home’s shadowy black Accoya siding lies perhaps the architects’ greatest trick: Gutex wood fiberboard exterior insulation. “We decided to use exterior insulation outside of the main weather barrier and the secondary air barrier because of some volumetric negotiations that we had to do with the zoning. We were able to get more floor area if we put half of the insulation on the exterior,” Pachano says.
INTELLO membranes serve as the primary air barrier in the home and, along with SOLITEX MENTO barriers, allow the project to exceed rigorous Passive House standards. While Passive House requires no more than 0.6 air changes per hour at 50 Pascals pressure, the Forest Lake House measured between .35 and .53 ACH/50Pa in three blower door tests. Pachano says the walls achieve an impressive thermal performance rating of
R-62 while the ceilings measure in at R-90. The efficiency reduces the electrical load for the heat pumps, perfectly calibrated by electrical engineers and Passive House experts from Baukraft.
The architects establish the space as a lakeside respite, the experience inside the home an echo of the natural landscape outside. Materials, especially light oak throughout the home and stones with a honed finish and depth of color, also play a big role in helping create a sense of calm.
The windows are intentionally placed for natural light and solar gain during the winter months but also to reveal views of the lake and trees. “As you move through the house, windows frame that movement of the body,” Vollert says. “When people talk about bringing the outside in, it doesn’t have to be just about large expanses of glass. It can be how you very consciously frame certain moments.” g
The lake reflects light into the building late in the day, particularly in spring, summer, and fall, through the dining room window and on the level immediately below.
“That’s an atmospheric part of the house that I think is really fun and interesting. We knew it was going to happen, but we didn’t exactly know how. When we go over there and you see the shimmering up on the ceilings from the direct reflection of the lake, it’s just wonderful,” Vollert says.
The powder room’s immersive use of Tanzania Onyx Stone from BAS Stone creates a calm but extraordinary atmosphere.
“It feels like you’re being
transported to another planet. The stone is a beautiful, strange color with a terrain type of landscape feeling,” Vollert says.
Keilhauer plans to make all of its contract furniture carbon neutral.
By Ian P. MurphyTerms like carbon-neutral and sustainable get tossed around a lot in resource-intensive industries like design and construction. But one contract furniture company is taking a cradle-to-grave approach to the design and manufacture of its products to reduce its environmental impact—and that of its products.
The North American contract furniture manufacturer Keilhauer introduced Swurve— what may be the world’s first carbon-neutral office chair line—in 2020. The company followed up with Melete, a collection of side chairs and stools, in February 2023, and the industry’s first certified carbon-neutral ottomans, Vagabond and Dally, in March 2023. In June they’ll debut four new carbon-neutral lounge chairs at Chicago’s NeoCon.
The demand for sustainable products has grown apace with the growing awareness of the built environment’s impacts on climate. “Sustainability has become a leading indicator of the success of an organization, as well as a valued attribute of a product,” says Josh Belczyk, sustainability officer for Keilhauer. “In the eyes of many investors it’s no longer enough for companies to simply focus on short-term profit, and in the eyes of many customers it’s no longer enough for products to simply compete on cost.”
When it comes to sustainability in the built environment, Belczyk says architects and interior designers are at the tip of the spear. “There are valuable statements for the clients, builders, and eventual owners to be able to make about a new project. The sustainability attributes of products is one of the most promoted, advertised, and salient differentiators. It’s become quite an arms race.”
Product Manager Maggie Keilhauer says
the company watched as trends in the market moved in that direction. “Since the company started we have worked on growing our sustainability practices and staying ahead of trends. It has always been important for us to do what is right, well before these metrics were in the spotlight,” she says. “With the conversation about carbon neutrality starting to take off, we decided we would launch an office chair that was very organic feeling to test the waters. Making all of our products carbon-neutral is the goal.”
Making a chair or ottoman 100% carbon-neutral requires careful sourcing and consideration of the totality of the product’s environmental impacts, including transportation and disposal. But it’s an ongoing challenge to control every aspect of carbon neutrality.
“We have control over the evaluation and selection of suppliers with whom we work and the source materials,” Belczyk says. “We can control how we consider the proximity of those suppliers to try to reduce transportation costs. And we have control over our own operations and over the design of the product itself.”
The process begins with a cradle-to-grave life cycle assessment of the product and its components. Keilhauer streamlines design and manufacturing to minimize waste, choosing materials that include recycled content and finding additional ways to reduce a product’s carbon footprint.
It can take just three months to add a product to an existing line if Keilhauer has already performed most of the legwork on the sustainability of suppliers and components, or up to nine months for a completely new product with a new supply chain.
Front-end work gets into details like what
Melete’s minimalist silhouette elevates the office. The carbon neutral chair is available as a side or stacking chair, in counter or barstool height.
FSC-certified
Keilhauer has long been attentive to its environmental impacts. It hired its first sustainability officer in 2003 and has offset 100% of its electricity consumption with certified renewable energy credits since 2006.
kind of glue or foam is used in manufacture. “You know—all of the little nitty-gritty things that go into a product,” Keilhauer says. “We align on that early because it allows the engineering team to develop a product that has as little impact as possible, then you offset what you inevitably can’t design for.”
Looks and longevity are important factors in the carbon-neutral equation. An aesthetically pleasing, high-quality design that lasts has a smaller carbon footprint and produces less waste, so the company prides itself on creating timeless designs. “If you make a beautiful product and it’s sustainable, people will buy it and keep it in use for a longer life,” Keilhauer says.
“We look at what people are looking for regardless of sustainability,” she adds. “You don’t want to make a product no one wants— that just becomes waste. We look at what other people in other industries are doing and try to figure out what new and interesting materials we can use.”
More architects and interior designers are looking for an organic feel, bringing the outdoors in with inviting green spaces and soothing shapes and textures. The sweeping lines of Swurve meet the trend, incorporating a sustainably sourced and manufactured mesh that requires less gluing and less material.
With work-from-home and hybrid environments now commonplace, there’s also a call for more flexible seating in offices. Inspired by the shape of an orange pip and created by award-winning designer Andrew Jones, the Vagabond is named for its portability. It features a reinforced black leather handle and can be used to stage impromptu sit-downs or grouped in a communal area.
“As the shape of hybrid work continues to evolve, we think collaboration is the key,” Keilhauer says. “Collaboration is the reason you go to the office—to have those one-off conversations you would never have otherwise. We focus on making those conversations happen comfortably.”
Keilhauer backs up product claims with certifications to build buyer trust. For example, all carbon neutral lines are certified carbon-free by ClimeCo and carry BIFMA Level 2 and Indoor Advantage Gold SCS Global Services certifications. They also partner with suppliers who source certified Forest Stewardship Council wood to reduce climate impact and ensure proper support of Indigenous communities.
Keilhauer presents clients with an Environmental Product Declaration (EPD) that summarizes the technical content that goes into its life cycle assessment while protecting suppliers’ proprietary information.
The information supports LEED and WELL certifications, including information on how products affect indoor air quality. Some Keilhauer lines include an extended manufacturer responsibility program that asks owners to return retired items for disassembly and recycling.
Checkpoints throughout development ensure the end-product is both salable and sustainable. “Sustainability is often described as ‘the ultimate team sport’ in the corporate world because we have to work cross-functionally with all departments— from accounting and finance to engineering, procurement, and operations and eventually to product development, marketing, and communications,” Belczyk says.
“There are internal and external aspects of transparency in carbon neutrality,” he adds. “Internally the challenging aspects are quantifying things that have never been quantified before; it’s a difficult technical project to calculate a carbon footprint. That’s true for both the organization and for any given product.”
While it’s difficult to reengineer an existing product, Keilhauer is working on getting all of its offerings—even it legacy lines—to achieve carbon neutrality going forward. “Making products people will use and making them as sustainable as possible is what we’re focusing on right now,” Keilhauer says.
“We’re leading in a lot of ways because we’ve been doing it for so long,” she adds. “We really care about the environment and try to be as sustainable as we can. It’s part of who we are as the Keilhauer corporate family—and it’s a team effort that includes every employee at every level. g
Virtual reality and real-time renderings are making collaboration across architecture and design easier and more fun. By
LAURA ROTEBy offering realtime visualization capabilities, Enscape empowers architects to ideate effectively, make fast design decisions, and streamline the design process.
Lipan’s role is focused largely on delivering new and improved functionalities for Enscape a few times each year. Her background in architecture and technology plus her passion for virtual reality (VR) keeps her interested in the evolution of this tech.
“With the integration of VR Enscape has democratized the perception of space—once a skill requiring extensive training in geometry and sketching. Now accessible instantly through a VR headset, individuals can perceive architectural designs with the acuity of an architect,” she says.
The AEC industry has seen significant transformation in the last 10 years—largely due to technological advancements in real-time visualization that revolutionized the design process along the way. “This innovation enables AEC professionals to explore ideas rapidly, create lifelike visualizations instantly, and conduct immersive virtual reality walkthroughs,” Lipan says. “Architectural firms worldwide now engage in design and communication more intuitively, creatively, and collaboratively, thanks to the seamless integration of real-time visualization software with 3D modeling applications.”
Arcadis—which recently combined with CallisonRTKL and IBI Group to form a multidisciplinary firm with 36,000 employees—uses technology like this every day for its sustainable design, engineering, and consultancy solutions.
“As a culture we’ve all gotten so much more visual with things like Instagram and TikTok. Our attention spans are shorter, and being able to showcase projects quickly and give people an overview, you can really share the story so much quicker without having to walk people through a potentially dense presentation or show them a series of plans that may be hard for the average person to interpret,” says Caoimhe Loftus, digital lead at Arcadis.
Loftus points to the Station Hill South project in Reading in the UK, in which the first of three phases has been completed and residents moved in. The project could ultimately deliver up to 1,300 new homes in Reading when complete. “It’s this huge, multiphase project,” Loftus says. “The visuals were so important to really sell and share the vision that was created. That was a collaborative effort between ourselves, Gensler, and Lincoln MGT really coming together to unlock that proposal and make that project happen on a site that had been derelict for quite a long time.”
The visuals for the Station Hill project came to life through a combination of Revit, SketchUp, and Enscape. Loftus says she and the team often use technology like Enscape alongside SketchUp or Revit to get real-time renderings. It’s something she simply couldn’t get at the start of her career, she says. “You needed slightly more elaborate rendering programs, whereas this is, at least at the basic level, more of a click-of-the-button solution that can be refined, and that’s great. You can export pan-
“Enscape’s VR is a game-changer in the design process, as it offers architects, designers, and clients a profound understanding of scale, proportion, and spatial relationships within the built environment,” says Andreea Lipan. It’s also easy to onboard. “Enscape is seamlessly integrated into the tools they are already using.”
“This immersive experience empowers the design team to conduct design evaluation and iteration with unprecedented intuition and depth. Through real-time interaction with their designs, they can identify flaws, assess design decisions, and implement adjustments while experiencing the space firsthand,” Lipan says.
oramas. I’ve even loaded this onto headsets to immerse myself in the scene to see what the project feels like.”
While that kind of immersion simply wasn’t available 10 years ago, the cost of this type of tech has fallen, and the power of computers has improved—and so has access. Loftus says these tools very clearly improve projects. Not only are teams able to collaborate more easily, but the different tech programs work together seamlessly, too. For architects already using design applications like Revit, SketchUp, Rhino, ArchiCAD, or Vectorworks to model buildings, Enscape is a very easy-to-learn plugin, Lipan says.
Enscape’s variety of export modalities and sharing options make collaboration easy, facilitating seamless communication among design teams. Architects and designers can quickly iterate on designs and receive instant feedback.
Enscape is the only real-time plug-in solution with 100% direct integration. Architects and designers leverage the bi-directional data exchange between the 3D model and the renderer to enhance their day-to-day design decision operations. “Any changes made in the rendering window are synced back to the 3D model and vice-versa, maintaining one single source of truth and having one project. Because of this, Enscape has evolved rapidly into a mission-critical workflow solution,” Lipan says.
Before Enscape, visualization was a separate workflow from the design process; the design process needed to stop for 3D artists to create a visualization. Now designers no longer need to export and import different file formats. “It also eliminates the need for adjusting complex rendering settings to get high-end outputs, making the design process faster and more efficient than ever,” Lipan says.
Fulton Trotter Architects also used Enscape’s real-time renderings while working remotely during Covid. It saved them time and improved communication around a North Sydney Public School project in Australia. “Being able to show the clients high-quality images to sell our design to them was really critical as part of that process,” the architecture firm told Enscape.
Lipan says Enscape helps architecture firms reach design decisions more quickly and easily. “It’s easy to use, and it’s very cost-effective. Architects don’t have to learn a new tool, so it’s easy to onboard them,” she says. “They model the building and instantly get visualization. They get a 3D walkthrough. They get videos of the project they are working on.”
Enscape’s Light View mode provides architects with valuable insight into how much natural light is hitting various surfaces, shown as a heat map, allowing for informed decisions on daylighting strategies. Enscape also enables the creation of solar studies by adjusting the position and angle of the sun while considering geolocation and time of year settings from the design application. Architects can quickly visualize and analyze the impact of solar angles and rotations on their designs, helping to maximize passive and cooling opportunities while reducing reliance on artificial lighting and heating sources.
In 2023 Enscape began a new journey of expansion and innovation, introducing a range
of new functionalities to enhance its already robust feature set. Among the notable additions were adjustable assets and scanned people, enriching the user experience with greater customization and lifelike realism. “These enhancements allow users to fine-tune elements within their designs and populate scenes with realistic human figures, adding depth and authenticity to architectural visualizations,” Lipan says.
She says Enscape also made significant strides in rendering quality with new advances in Global Illumination technology. “This improvement elevates the realism of rendered scenes, enhancing indirect lighting accuracy and overall visual fidelity to create more realistic environments.”
There is also new support for macOS, widening accessibility for a broader user base.
Enscape’s VR capabilities alleviate confusion and enhance understanding of projects, Lipan says. “By immersing themselves in the virtual environment, clients can explore proposed projects comprehensively and use real-time feedback to make informed decisions about design elements, materials, and spatial configurations. This eliminates misunderstandings that often arise from 2D documentation or static images, allowing clients to visualize projects effectively and participate actively in the design process.”
Lipan expects improved realism and enhanced interactivity as more people adopt cloud-based solutions and hardware capabilities advance. This is already happening to an extent with Chaos Vantage, which can deliver photorealistic visuals in real-time, but Lipan imagines new technology could create even more exciting and dynamic workflows.
“Cloud-based rendering will democratize access to high-quality rendering, while AI integration optimizes workflows and enhances image quality. Cross-platform compatibility will facilitate seamless transitions between devices, and real-time collaboration tools will revolutionize teamwork and communication among distributed teams,” she says. g
“AS A CULTURE WE’VE ALL GOTTEN SO MUCH MORE VISUAL.”
Form and function merge with today’s top acoustic solutions.
By Matt WatsonTo entice workers back into the office, building owners, operators, and tenants are placing a greater emphasis on amenities than ever before—with lifestyle perks like fitness centers, game rooms, and outdoor terraces receiving much of the media attention.
Yet there is a growing recognition in the industry that employee well-being, satisfaction, and productivity can benefit from simpler but more fundamental improvements to a workspace—with acoustic considerations now featuring prominently in interior design discussions.
“Acoustical solutions truly are one of the quintessential amenities,” says Arjav Shah, associate principal of corporate interiors at Perkins&Will. “They help us perform and function; they reduce sensory overload and enhance communication, especially in a work setting. Nobody wants to work in a noisy office.”
The need for interior acoustic performance extends beyond the office typology. Designers of restaurants, retail, education, and health care spaces are increasingly incorporating acoustic decor into their plans as awareness of their benefits rises.
“The industry is really in this learning phase right now,” says Marco Alvarez, vice president of Fabric Images, one of the top manufacturers of design-centric architectural acoustic solutions. “A few years ago we were mainly seeing these included in a space when someone was doing a retrofit. Now designers are making it part of the environment from the beginning.”
Acoustic decor addresses three main pain points in office settings. The first is the sound transfer between offices and conference rooms through walls. Another is the echo and reverberation that occurs in any enclosed space.
“That is especially important with the rise of hybrid meetings,” Shah says. “Video conferencing requires extremely clear sound so anyone who’s not in the room can understand what is being said.”
And third, the popular open office format presents its own challenges, where a conver-
sation at a neighboring desk can interfere with your focus and cause distractions. “If employers want to improve the overall longterm productivity and well-being of their employees, investing in acoustics is required for any workplace.”
The same could be said for commercial settings. A cacophonous retail experience will likely drive customers away and hurt sales. Restaurants in particular aim to create a comfortable ambience that fosters conversation and leisure.
That was part of the consideration when Fi Interiors, a studio of Fabric Images, was approached to support the design of a new celebrity chef’s restaurant at Chicago’s Navy Pier. The vision was one of a homestyle aesthetic—comfortable, casual, and warm.
One of the key elements tying the space together was the treatment of the ceiling. The project designers wanted the look of natural wood but understood that the sound reverberation off of a hard surface would disrupt the restaurant’s atmosphere.
The Fi Interiors team introduced the designers and contractor to Acusti-fi—their brand-approved acoustic PET felt—which they printed with an authentic wood grain. One of the challenges was avoiding the use of repeated textures or patterns, which would not occur in natural wood and would be noticeable from below.
To avoid this, the graphics team utilized a broad range of wood tones that could be mixed throughout the space to avoid repetition, making each panel look one-of-a-kind.
“Even professionals who work with the material daily can’t tell it’s not real wood,” Alvarez says. Two months after the restaurant’s opening, the client reported back on the positive impact the material has had on the sound quality of the space—as well as
the number of compliments they receive on the look of the ceiling.
Ultimately everyone is affected differently by noise. “When thinking about neurodiversity as designers, it’s important to understand that people have different tolerances to noise,” Shah says. “Designing accordingly is one way a workplace can be made more inclusive.”
As demand rises manufacturers of acoustic products are developing innovative ways of increasing acoustic comfort while leveraging materials to create captivating interior spaces, seamlessly blending form and function. Though simple fabric wall mounts are still common, more designers are stepping outside the box to build jaw-dropping architectural installations. “With the integration of this material into the space, an architect and designer can truly control the experience that much more,” Alvarez says. “As a partner to designers we’re constantly looking at architecture, at fashion, at the tech space, and nature. It’s almost limitless what can be created.”
Foam and cork are among the more common acoustic dampening materials. Fi Interiors’ solutions are made from PET felt—a porous material that absorbs sound energy—reducing what would otherwise reflect off hard surfaces like ceilings, walls, and floors.
PET felt is highly versatile and customizable, presenting designers with essentially a blank canvas that can be cut and molded into just about any shape or configuration. Beyond the physical form, Fi Interiors’ ability to print on the material without sacrificing sound absorption adds another level of personalization and expands the designer’s palette to include a
wide array of bright, vivid imagery.
The versatility of today’s acoustic solutions is on full display at a high-end boutique perfumery that recently launched a flagship store in Huntington Beach, California. The design theme centered around the feel of a contemporary beach cottage and aimed to replicate “the energy of the sea.”
The space’s concrete floors, large windows, and high ceilings presented a challenge for the designers, knowing the resulting echo would harm the retail experience. The Fi Interiors team was commissioned to create a ceiling system that utilized the firm’s acoustic baffles and beams to absorb sound while seamlessly integrating the boutique’s branding into the experience.
The result is a uniquely molded suspended sculpture featuring undulating baffles printed in a smooth gradient of light blues that mimics the waves of the ocean, adding a finishing design touch to the bright and airy space. “This definitely helped create this relaxing, zen-like feeling that not only represented the brand well, but helped create an acoustic environment that is soothing,” Alvarez says.
Fi Interiors also offers Blaze Illuminated Art—a product collection that can serve as an artistic complement to any architectural acoustic solution. These work well in spaces that require a specific emphasis on artwork, branding, or messaging.
“Whether mounted to a wall or used as a spatial divider, these products draw attention and provide added ambient light,” Alvarez says. “When you incorporate the illumination products with the felt, it looks absolutely stunning.”
Not all acoustic decor needs to be the highlight of a space’s design; in fact, some of the most effective solutions go unnoticed by those who experience them daily. “As a designer I’m often interested in designing acoustical solutions that almost disappear,”
“We’re constantly looking at architecture, at fashion, at the tech space, and nature. It’s almost limitless what can be created.”
Shah says. “That’s much easier than it once was. The industry has come a long way, and there is a lot of product now that is very sophisticated.”
Shah recently designed a workplace for a financial services firm that wanted to line the walls of a boardroom with wood. To avoid acoustical challenges, the solution was to insert micro-perforations in the wood veneer, which was also backed with a one-inch sound absorbing substrate. “Those micro-perforations aren’t visible from a distance, so we were able to create a space that offered the warmth and character of wood, but with great acoustics,” Shah says.
“PET felt repurposes material that would otherwise end up in landfills or oceans, helping to reduce the environmental impact of plastic pollution,” Alvarez says. The material is also known for its durability, offering a long service life and reducing the need for frequent replacements.
“I think we can do more to repurpose waste and turn it into acoustical solutions, which can ultimately help achieve LEED and other similar sustainability certifications,” Shah says. g
Though there is growing recognition in the design community that acoustic solutions improve interior spaces in terms of both performance and aesthetics, some environmentally conscious designers may be skeptical of utilizing additional materials on a project if it’s not completely necessary. Many of today’s acoustic solutions are highly sustainable—and the industry is only improving. Bamboo and cork, known as rapidly renewable materials, are highly effective for acoustic wall treatments. And the PET felt Fi Interiors uses is a minimum of 60% post-consumer content.
Perkins&Will designed the Mintz office to accommodate the firm’s continued growth in New York as well as the changing needs of the workplace.
Builders, architects, and manufacturers alike are redefining “green” building.
BY LAURA ROTEThe Eight in Bellevue, near Seattle, is a 26-story, 541,000-squarefoot office tower built by Skanska that embraces native landscapes and activates the plaza along NE 8th street with 11,000 square feet of retail, including a 1,900-square-foot standalone pavilion. The Living Room is connected to the lobby and is an indoor/outdoor casual space also connected to retail.
“Uponor is working to produce 90% of its product portfolio with
Environmental Product Declarations.”
Uponor has also long been committed to green building, including using renewable raw materials; they even piloted and produced circular PEX pipes from their own PEX production waste in Europe, with plans to implement this process in North America in the future.
With federal commitments to reduce net greenhouse gas (GHG) emissions by 50% in 2030 and reach net zero by 2050, many industries are carving new paths to sustainability. All eyes are largely on the architecture, engineering, and construction industries, as buildings account for more than 40% of annual global CO2 emissions.
One of the largest construction and development companies in the US, Skanska, has even more ambitious goals, with a climate plan for net-zero by 2045. They’re also working to reach a 70% reduction in Scope 1 and 2 emissions by 2030, and in 2022 they achieved a 55% reduction. Part of how they accomplish that is by working with equally committed partners. “The building material supply chain is hugely important, and getting that supply chain decarbonized,” says Heidi Creighton, former national head of sustainability for Skanska USA Commercial Development, now principal of Creighton Sustainability Advisors. “We really need all of those pieces to fall in place so we can all get to our zero commitments.”
Creighton, who recently joined USGBC California as a senior advisor for decarbonization, says people can sometimes be confused about what net zero means, as different definitions exist. “The Federal Government is working on a definition so the whole industry can get around it,” she says. “Because when somebody makes a claim like that, you really need to drill in and understand. Educating the market is hugely important, and understanding what Scope 1, Scope 2, and Scope 3 are is also important.”
The EPA defines Scope 1 emissions as direct GHG emissions that occur from sources controlled or owned by an organization (in other words, emissions associated with fuel combustion in boilers, furnaces, vehicles). Scope 2 emissions are indirect GHG emissions associated with the purchase of electricity, steam, heat, or cooling. While Scope 2 emissions physically occur at the facility where they are generated, they are accounted for in an organization’s GHG inventory because they are a result of the organization’s energy use, the EPA says. Scope 3 emissions include all sources not within an organization’s scope 1 and 2 boundary.
“Education within our industry and also outside of our industry and to our customers is super important,” Creighton says. “I think when people don’t understand something they’re not as engaged, or maybe they feel like it’s a little bit too abstract or like what they’re doing wouldn’t impact the end result, but that’s not true at all. We all need to band together and work toward these goals for a healthy, sustainable, regenerative built environment.”
Skanska works to set aggressive sustainability goals early in each project. “We set a target for all of our projects and do everything we can to indicate to the market that this is a key priority for us—and that we’re going to focus on low carbon materials because I think it’s so important for the supply chain to see those signals that the large buyers really want this.”
And that is true of every Skanska project. “We need everybody to be doing this, and we are able to say that 100% of our commercial development portfolio in the US is LEED-certified or pursuing certification. LEED Gold is the minimum target—and we get to Gold or Platinum on all of our projects. We love our third-party certifications,” Creighton says, pointing also to WELL, Fitwel, Salmon-Safe, and others.
Skanska also considers aspects like water usage, stormwater collection, and heating and cooling as part of its efforts to reach net zero. “Carbon is super important, but we also can’t lose sight of other really important aspects around sustainability. For example, water scarcity is becoming more and more important,” Creighton says. “And storms are becoming more frequent and more intense.”
Some manufacturers, too, have been focused on developing greener solutions since before it became trendy. “Sustainability is a part of Uponor culture. It’s really been a part of what we do for a long time,” says Chrissie Walsh, sustainability manager at Uponor, a global leader in plumbing innovations.
Uponor is now shining a light on their work and sharing data from what they’ve learned with the industry, helping customers to reach their own sustainability goals. Solutions like their AquaPort are one way Uponor is making projects more sustainable, as it decentralizes domestic hot water in commercial settings. The AquaPort is a new technology focused on generating domestic hot water that is both more hygienic and delivered more efficiently. It’s an ideal solution for owner-occupied spaces with high unit density, says Hailey Mick, business development manager for engineering services at Uponor. She points to patient towers in health care, student housing and higher education, and high-end hotel rooms as great examples.
“It’s a self-contained unit that uses the energy from a building’s hydronic HVAC heating system to create domestic water locally on demand in the unit,” Mick says. “By doing that, we’re eliminating the central domestic hot water system, which results in a 40% reduction in the piping in the building. So every pipe is basically a heat exchanger.” That also means a 50% reduction in the volume of domestic hot water in the plant.
Installing AquaPorts gives design teams more designable space, delivers hot water faster, and requires less chemicals. “We can lower the amount of water in the plant, and we can lower the energy it takes to deliver hot water to the faucet,” Mick says. “It’s a huge savings for both energy and water, and then look at the elimination of all the additional piping you would need.”
She says it’s sometimes difficult for owners to choose high-efficiency solutions if the payback is 10 years or more, but the AquaPort aims to address domestic hot water issues without driving up the initial cost for the building owner.
“We at Uponor may not be a huge part of the volume of your total build, but we can have a substantial impact on how you’re going to approach building better and how you’re going to start the conversation around decarbonization,” Walsh says.
A new Uponor program called Kitting Services is all about speeding up installation and reducing labor, material costs, and jobsite waste, making the entire construction project smoother from start to finish. “Because at the same time that we’re trying to create these super-efficient buildings and use all this new technology, we’re also dealing with a shortage on both the engineering side of the business and the contractor side. Having solutions that are more efficient and easier and faster to install is going to be critical to the success of projects,” Mick says.
Uponor’s core product, the total polymer solution, is also important to the whole life of a building, Mick says. “A traditional metallic piping system needs to be re-piped every seven to 10 years. With a total polymer solution, we’re looking at 50-plus years.”
Piping is a bigger piece of the whole puzzle than some may think. “It’s not just going to last longer, it’s less likely to become more energy intensive to run water through a polymer pipe than a metallic
pipe over time because it’s less prone to corrosion and buildup, which ultimately affects the pressure drop and how much energy it takes to get the water through the pipes. It really is more important than people think. They just never had to look at all of the components at such a granular level.”
Mick has been in commercial construction for almost two decades and has watched what she calls a very welcome shift to working smarter and more collaboratively. “It’s great because when people are willing to share their experience, it can really accelerate technology in this space.”
Uponor is a leader in energy-efficient underfloor heating and cooling and offers reliable, hygienic plumbing and infrastructure solutions that are lightweight and easy to install.
Walsh agrees and says they’re seeing not just more collaboration across the industry but also a shift to a more systems-based thinking and approach to sustainability. “Every facet of the industry is easing into and simultaneously accelerating the understanding and acceptance that sustainability needs to be a part of how we’re going to build better,” she says. “It’s an exciting time to be working in sustainability and seeing these conversations really move forward in tangible ways. It’s no longer a legitimate thing to say sustainability costs too much.”
In fact, she says that’s no longer true in many cases, as it often costs less over the course of a building’s lifetime. “It’s going to cost you less in maintenance. It’s going to cost you less to operate over the lifetime of the project. And with evolving legislation and investment funding being put in place to scale technologies, a lot of what used to seem unrealistic is becoming cost-neutral or, at least, competitive.”
Radiant heating and cooling will be critical to helping both commercial and residential projects reach net zero, Mick says. “Radiant heating and cooling are going to provide that energy efficiency profile you need to integrate into that solution. There’s more and more discussion across industry boundaries—it’s brand agnostic—and we’re starting to see more stakeholders sit down and talk to each other in a way that is meaningful and impactful.”
While more people are considering radiant than in years past, some misconceptions do persist. “People see it as a luxury item,” Mick says. “They think it’s going to cost more, but modeling is key to getting the right data in front of the decision-makers. When you model a building and you account for thermally active surfaces, then you can really see that a radiant system is going to require so much less energy. It’s going to be smaller-capacity equipment that you’re installing.”
Because water has the capacity to trans-
The design of 1550 on the Green in Houston incorporates plentiful indents, allowing for more corner offices. Skanska’s Heidi Creighton points to the project’s beautiful metal framing and aluminum fins. “We’ve been pretty focused on steel and concrete to date, but I think the facades are also going to be an important focus. We can make some great strides there.”
“The building material supply chain is hugely important, and getting that supply chain decarbonized.”
port energy 3,500 times greater than air, hydronic radiant is an effective way to lower energy demand and gain energy efficiency while providing more designable space to architects. Radiant can be installed in renovations, too. “Everyone thinks you have to have a new build for radiant. It’s ideal for a new build, but there are solutions out there; you just have to think outside the box.”
Plus, renovations are critical to the overall sustainability story, Mick says. “We want to talk about renovation because there’s a huge stock of existing buildings that will need to be addressed for efficiency gains and decarbonization strategies. It’s really important we talk to everyone involved in the construction process. We can’t just talk to one stakeholder in a silo; we have to make sure owners, engineers, architects, contractors, and so on are comfortable installing these technologies and know how it works because each has an influential voice in the build process. If they don’t know these solutions exist or that they can be applied in a renovation, they’re certainly not going to advocate for it, and they might even advocate against it.”
Skanska has been doing sustainability reporting since the mid-90s and continues to look for partners who push the envelope to help them achieve more energy-efficient buildings.
“We want to do the right thing and also attract best-in-class tenants and investors,” Creighton says. “We want to future-proof these buildings and show those investors that we see decarbonization regulations coming and we’ve already designed the building to meet those future regulations, so you don’t have to do really expensive retrofits.”
For example, Skanska is heavily invested in doing all electric buildings ahead of regulations. “We want to keep that forward-thinking lens and really work with our tenants to help them meet their goals and help educate them on how the built environment is part of their Scope 1, 2, and 3 emissions and the goals they set for themselves.”
Skanska worked on the recently opened 1550 on the Green in Houston, designed by Bjarke Ingels Group. The 375,000-squarefoot, 28-story office building is on Discovery Green—a beautiful park in the central business district. “It’s a stunning project with outdoor roof terraces on three levels and beautiful views,” Creighton says. “That indoor-outdoor experience and views are becoming increasingly important for projects as tenants want to attract people back to the office.”
The team was able to reduce the embodied carbon by 45% over the baseline for the Houston project, in part thanks to choices
Radiant is an effective way to lower energy demand and gain energy efficiency while providing more designable space to architects, as the panel and equipment in radiant is substantially smaller.
like low-carbon concrete, metal framing, aluminum fins, gypsum boards, glazing, and the acoustic ceiling, she says.
The Eight in Bellevue, just outside of Seattle, is another successful Skanska project, with tenants set to occupy the building in January 2025. Creighton says it’s the largest single office transaction in the company’s history and one of the largest leases in the Puget Sound area in the last few years, at more than half-a-million square feet and 25 stories, with an emphasis on native plants and mass timber.
Material choices are easier with the free, open-source EC3 Tool, co-created by Skanska with industry partners. “When you’re procuring materials, it helps you make the best decisions around embodied carbon,” Creighton says. Input your project address and material quantities, and it will search more than 100,000 Environmental Product Declarations to deliver your options, showing the best low-carbon choices and offering a comparison with other materials.
“It was a really exciting commitment in Skanska because we could have just made a tool to use internally, but it’s grown immensely because it’s a free and impactful tool for the industry to use. We’ve committed to using that tool since 2020 on all of our projects,” Creighton says.
Setting sustainable goals clearly and early is more important than ever, she says, and Skanska will continue to invest in low-carbon strategies. “Business as usual isn’t going to continue to work. We need to continue to transform ourselves and innovate and invest in new strategies and technologies.”
Creighton says, “I don’t think anyone should feel like they’re alone in this. All those collaborators and all those partners are super excited to push the envelope, too. I believe our architecture and engineering teams truly enjoy working with us because we are really leading the way, and they get to be an important part of that.” g
As student needs e volve, the spaces where they learn must offer more flexibility.
By MYAH TAYLORFor decades students sat in rows of desks lined up in front of their teachers. Open concept designs promoted direct instruction, but that uniformity did not keep all students engaged.
Today’s students face new challenges every day—from evolving technology to feeling comfortable in the classroom. Modern learning spaces are breaking out of the four walls of the traditional classroom to allow for greater student exploration, self-discovery, and wellness.
“The best way to address students’ needs is by involving their voices in every project,” says Paola Moore, vice president of marketing for MooreCo, a leader in innovative furniture solutions. “Being aware of the students not only as elements that will occupy the building during a few hours a day, but rather as human beings who are developing their identity and formation, with ambitions and struggles, who are affected by so many things that occur outside the building yet they carry with them every day when they walk through those doors— that’s crucial.”
To thrive in the 21st century, students need more than traditional academic learning, Rutgers psychology professor Maurice J. Elias said in a 2021 webinar organized by MooreCo. They must be adept at collaboration, communication, and problem-solving, which are some of the skills developed through social and emotional learning, he said, citing an earlier World Economic Forum report on education.
Coupled with mastery of traditional skills, social and emotional proficiency will equip students to succeed in the swiftly evolving digital economy, Elias wrote.
Supporting the social and emotional wellness of students has long been part of global architecture and design firm DLR Group’s mission in designing schools. “A
lot of time school is that safe space,” says Ian Kilpatrick, principal K-12 education design leader for DLR Group. “It’s where students are getting fed. It’s where they feel safe because their home environment may not be.”
Fifty years from now classroom design will undoubtedly look different, and already some of those changes are being seen, with more collaborative spaces and various types of seating and tables in the same classroom. Kilpatrick anticipates more shared spaces in the future. “Kind of a suite of spaces where you might have a maker lab or a technology lab,” he says. “Instead of designing five of the same space and furnishing them all the same, designing spaces to facilitate different activities.”
Manufacturer MooreCo’s innovative furniture designs are driven by a philosophy they call Thrive, which explores how the conscious design of environments can impact human happiness and health.
MooreCo aims to foster environments that inspire and support growth as part of Thrive’s six stages of development—social-emotional, intellectual, moral, psychological, physical, and spiritual. Students develop important life skills like collaboration, communication, and problem-solving through social and emotional learning, for example. “We understand not all students learn the same way,” Moore says. “We identify those needs—physical and social-emotional—and develop products for students to be able to engage and learn in an inclusive way.”
The company considers students’ wide-ranging needs when developing new products, with the aim of helping them engage and learn in more inclusive ways. Their designs are also flexible.
MooreCo’s Porcelain Steel Hierarchy Shapes Desk comes with a porcelain steel dry-erase top students can use in a variety of ways. This easy-to-assemble desk is designed to last longer than alternatives, while the porcelain steel whiteboard offers space for drawing, note-taking, or brain-
MooreCo’s Hierarchy Creator Desk system accommodates different abilities and needs with ADA-compliant desks. Design teams can choose from square, triangle, rectangle, and half-round shapes.
storming. It also fosters group work and collaboration—key components to the modern classroom. “In general a markerboard desk is a good idea for students to use in classes,” says Molly Cox, design team manager for MooreCo. “Having one that lasts longer than a few months is much nicer.”
Cox says the adjustable desk is superior to laminate whiteboard desks from both a durability perspective and a use perspective. It also has less glare and is low maintenance. “A lot of times with the laminate you’ll see it’s scratched easily and markerboard particles will get down in there,” Cox says. “That’s not going to happen. With the porcelain steel top, when it erases, it erases. You don’t have to worry about still seeing the lettering on the desk afterward.”
MooreCo’s options vary to meet the needs of users of all ages and activities. Moore knows some students learn better standing, while others learn better sitting; allowing those students to work together with the same product is key. That kind of flexibility is emphasized throughout MooreCo designs. Products can double as tables or mobile whiteboard easels, depending on classroom needs. “Being able to take one piece of furniture and use it in multiple ways without taking up three different spaces to do that in a classroom is cool but also really important to the students and teachers trying to use that space,” Cox says.
“The best way to address students’ needs is by involving their voices in every project.”
The Thrive philosophy centers on addressing the various styles of teaching and learning. This includes project-based, experiential leaning, differentiation, online/hybrid, and collaborative/active teaching styles. Learning styles encompass visual, aural/musical, physical, verbal/linguistic/social, color learners, and natural/ nature learners. These styles all add up to an increasing need for flexible design.
Much of MooreCo’s recent research has centered on how Gen Z learns, for example, and the impact of Covid-19. According to a MooreCo CEU presentation in 2023, the average student lost more than half a school year of learning in math and nearly a quarter of a school year due to Covid.
The company is also working to share the results of other research—such as how auditory/linguistic learners benefit from collaborative setups, while naturalists connect more with outdoor environments. Solitary learners need quiet spaces, while verbal learners thrive with writing desks or surfaces. Colorful spaces create more engagement, while flexible furniture promotes movement.
Architects at DLR Group agree flexible learning environments are key to successful learning spaces. “Having that choice— soft seating, high-top desks, tables. All of that mixed in a classroom environment gives the autonomy to learn where you learn best or engage the best,” Kilpatrick says. “At the end of the day we’ll see 12 to 15 different pieces of furniture in a lot of our classroom environments, and that helps a lot.”
Flexible seating means offering several options in height, motion, and texture, too. Some students engage with rhythmic motion, like rocking chairs (see the Hierarchy Rocker Chair from MooreCo) or wobble stools (Grow Stool). Other students need to relax their entire body to engage. The Elevate Wind Quartile Chair can be configured in multiple arrangements, while the Akt 5-Star Chair was designed with a beveled edge to help posture. All of MooreCo’s products consider the people who will use the furniture, Moore says.
“It’s not just the ergonomics behind the product or how it supports the back, or how a beveled angle of the chair will support leg circulation,” she says. “It’s also the physical aspect that stimulates your mind.” g
BY
THE OLD CHICAGO POST OFFICE WAS A LOST CAUSE. THAT’S HOW IT FELT, AT LEAST, FOR NEARLY TWO DECADES AS THE ART DECO BEHEMOTH ON THE CHICAGO
“The biggest challenge was probably getting the project off the ground,” says Gensler’s Ashley Rogow, project architect for The Post Office and an adaptive reuse leader at the global architecture firm.
The building—clad in incredible Indiana Limestone—had been abandoned since the late ’90s, increasingly giving developers, investors, and even the city of Chicago a bad impression, Rogow says. Much was written in the news about the massive empty building—2.8 million square feet, to be exact— and much of it was not nice. “It had this reputation that nothing would ever happen to it,” Rogow says.
The old building, circa 1921, was designed by Graham, Anderson, Probst & White. When Gensler got involved nearly 100 years later to save the giant, she says there was a lot of “eyebrow raising,” like, “Is this really going to happen?” It was Rogow’s first project with Gensler, working as an architectural designer primarily on the core and shell as well as some of the interior spaces and public spaces on the first floor from the beginning conceptual design. The project was completed in 2020 and ultimately achieved LEED Gold. It’s now home to some high-profile tenants, including Uber.
The building’s facade is made out of Indiana limestone, a classic for this style of architecture, Rogow says, but some of the pieces were starting to fall off after so many years. “When we were looking at restoring it, it was very important to us to replace as little as possible so we could try to preserve the natural stone and materials that were already within the project,” she says.
Gensler began replacing broken pieces and got to work cleaning the stone, and they were careful to make sure any new stone matched, getting sample after sample of dif-
ferent limestone colors. They worked with Regal Stone, a local fabricator in Chicago, which Polycor supplied the raw material to. Based in Canada, Polycor has quarries across North America and Europe.
“One of the benefits of the Indiana limestone that was on that project is that when you have to do these renovations decades later, Indiana limestone is such a consistent material that the stone that comes out of the ground today will basically look like the stone that came out of the ground 100 years ago,” says Stephen DiRaffaele, an Indiana limestone expert who focuses largely on building cladding. DiRaffaele is a LEED Green Associate and architectural sales representative for Polycor. “You can get a very consistent look of material. Really nothing compares to that specific species of natural stone when it comes to its consistency.”
Rogow says natural stone is also great for high traffic interiors because it’s so resilient. Plus, it’s more environmentally friendly than many alternatives. “I love it as a material in a vacuum. It’s an incredibly sustainable material,” she says. “It’s going to last longer than concrete or glass. It doesn’t corrode like metals. It’s recyclable and low maintenance. It doesn’t release VOCs, and it takes a lot less water to produce.”
One important thing to note, though, is where it’s coming from. Gensler always aims to source from as near as possible. “If you have to bring it in from very far away, all of that goodwill can go out the window because now you’ve used a lot of resources to move a very heavy material a long distance. When we’re talking about sustainable stone, we’re really looking for stone that’s maybe within 500 miles of the site,” she says.
She says some people think a lot of natural stone has to come from Europe, but
More design teams are also incorporating natural stone in their interiors in part because it’s environmentally friendly.
it simply doesn’t. “We have a lot of really beautiful natural stone in the United States and North America. You can find great stone that is local, in which case it becomes a very, very sustainable material.”
DiRaffaele says today’s stone quarries follow very responsible sourcing practices, too, to minimize the ecological impact to the earth. “It’s a very simple process; you just need brute strength. It’s ready-made, and it’s also recyclable. It comes from the earth, and it goes back to the earth. Unlike strip mining you’re not damaging the environment. A lot of quarries are reclaimed after their usefulness has expired and natural water fills them; they become lakes.”
You can also finish natural stone in ways that can extend the life of the material, Rogow says. “You can make it more weather-resistant or resistant to wear and tear. You can make it very non-slip to use outside.”
Today Gensler considers natural stone most often for interiors. Even inside the Old Chicago Post Office you’ll find plentiful marble and granite—including a pink granite that the Gensler design team spent a lot of time matching.
Rogow says natural stone can make a big impact with color. “One of the really nice things about stone is all the varieties of ways it can be finished,” she says. “There’s this
thinking that natural stone has to look very heavy. You can use it to make spaces that are dark and moody and look very stately, but you can also find stone that’s very playful in color. It can create spaces that feel very light.”
The diverse range of colors and patterns mean seemingly limitless design potential. Natural stone can even be used as a feature wall or backsplash. Gensler has used it for both, including recently as a wall in a restroom. “The design impact is huge. It makes the space feel very luxurious,” Rogow says.
DiRaffaele says more design teams are also incorporating natural stone in their interiors in part because it’s environmentally friendly. “It doesn’t emit any VOCs. We see natural stone in the interior environment all the time.” Beyond feature walls, it’s also showing up in fireplaces, swimming pools, and office desks.
On the exterior some architecture teams are turning to options like Ultra-Thin Natural Stone Slabs or honeycomb panel systems to reduce the weight of natural stone by up to 80%, DiRaffaele says.
He says natural stone is held in a very high regard for good cause, as it’s a premier building material. “It really reflects the unique character or grandeur of a project. The variations in natural stone are so broad in range of color and pattern and texture that it’s visually interesting, and it really is impossible to replicate. When an architect is looking to put their mark on a building nothing comes close to natural stone. It’s a very versatile material.” g
“ONE OF THE REALLY NICE THINGS ABOUT STONE IS ALL THE VARIETIES OF WAYS IT CAN BE FINISHED.”
Building facades are one of most prevalent areas where natural stone is used in modern architecture, whether it’s Indiana limestone or granite for a timeless look.
The time is now for smarter solutions in the built environment.
BY LAURA ROTE“LET’S CHANGE” IS THE MOTTO BEHIND REGUPOL’S SUSTAINABILITY STRATEGY.
“We see it as a call for all of us to take new paths, gear our actions toward conserving our environment and resources, and contribute to shaping market changes. We can no longer afford to wait and see. We have to change things now,” says Niels Pöppel, CEO of REGUPOL Germany. “We are more than happy to be miserly with our resources, because we have no other choice if future generations want to inherit a world worth living in. As a family enterprise, that’s the way we’ve been operating for seven decades.”
When REGUPOL started to process recycled materials from furniture production 70 years ago and used them to make judo mats, for example, many people didn’t talk about recycling or what happens to waste, says John Aten, vice president of sales and marketing REGUPOL America. Aten has been with REGUPOL Group for more than 30 years, and the industry has come a long way since those early days.
“We have contributed to a significant change in the way the circular economy is viewed today. It is now seen as the economic model of the future,” Aten says. “We see ourselves as a driver of the circular economy and are living up to our claim of being a quality and service leader.”
Over seven decades REGUPOL has continued to innovate—especially in the realm of commercial flooring. Their products are now supplied to more than 130 countries. “Over the past few years we have not only developed new countries for our REGUPOL products, we have also greatly expanded our product ranges. Acoustics, sports, building protection, commercial flooring, and load securing now contribute to an extremely broad spectrum,” Aten says. “These product range expansions have taken place gradually, which has contributed to very healthy growth for the company as a whole. The majority of our products now have a recycled content of 75%, and the highest percentage is actually 95%.”
REGUPOL is one of the world’s leading processors of recycled elastomers, which are used to create the company’s high-performance sports and safety flooring, commercial resilient sheet and tile products, anti-slip mats for load securing, products for impact sound insulation and vibration isolation, and protective and separating layers for use in construction projects. Worldwide they recycle more than 90,000 tons of elastomers.
REGUPOL is a member of Initiative New Life in Germany, a collective of companies committed to recycling and the circular economy. Together the members work to demonstrate the benefits of products made from recycled tires at the end of their useful lives and encourage others to make similar sustainable commitments. This effort goes hand-in-hand with a 2020 forum launched for waste tire recycling called AZuR. AZuR was launched and is funded by the Federal Ministry for Education and Research of Germany.
“This rapidly growing network currently comprises some 60 partners—including companies, associations, colleges, universities, and environmental organizations,” Aten says of AZuR. “We at REGUPOL have been part of the innovation forum from the outset. AZuR aims to find ways and solutions for economically and ecologically feasible tire recycling.”
Many architects, too, are looking for ways to design better—from the products they specify in their projects to the overall life of a building they design. It’s not just about what happens to a chair when no one wants it, though that’s important, too, says Kimberly Dowdell, 2024 AIA President and architect at HOK. “Zooming out, the circular economy also can relate to the actual container—the building itself. That’s something that’s really tied into our sustainability ethos at HOK. How do we take what’s existing and help it to have a new life, whether it’s the scale of a chair or the scale of an entire building?”
REGUPOL’s products are made of up to 95% recycled content, either from shredded and cleaned SBR tire rubber (100% post-consumer waste) or a combination of SBR tire rubber and vibrant EPDM color granules (post-industrial waste). “If you want to build a sustainable building or live and work in a
When it comes to acoustic products, REGUPOL manufactures sustainable solutions like impact sound insulation underlays. In construction or building storage, they offer building protection products, roof and sidewalk tiles, or decking.
“If you want to build a sustainable building or live and work in a sustainable building, you should use sustainable building materials.”
“We subject our products to extensive tests, we receive test reports from neutral testers, and we carry out very close internal tests ourselves. All for the benefit of our customers and for safe and sustainable products,” Aten says.
sustainable building, you should use sustainable building materials,” Aten says.
REGUPOL also looks beyond raw materials—to product impact. “For example, we reduce impact sound and vibration noise in cities and urban environments to help create a more sustainable and healthier living space,” he says. “Our sports flooring and resilient commercial flooring products add shock absorption and energy return to the athlete as well as ergonomics for the customers and employees standing on the flooring.”
In January 2024 REGUPOL America launched REGUPOL upscale recycled rubber commercial flooring—the first of its kind micro-bevel plank and tile. REGUPOL upscale is available in 12 standard color combinations and features either a square or micro-bevel edge. Square-edged floors fit together flush, resulting in a sleek and seamless-looking transition. In contrast, the micro-bevel edge brings subtle texture and dimension to an interior space in an elegant way. The addition of a sealed finish can be applied at the factory or in the field, strengthening the tile’s defense against dirt and spills.
Upscale’s combination of design capability and performance benefits make it uniquely suited for education, corporate, retail, hospitality, and health care environments, Aten says. It is anti-slip and comfortable, with high acoustic performance and simple maintenance. The densely patterned tones can also help to mask scuffs and soil in busy commercial spaces.
EPDs and HPDs continue to be an important element for backing up a company’s sustainability claims, as they detail products’ environmental and health impacts based on an ISO compliant life cycle assessment.
“REGUPOL is committed to product transparency, and EPDs and HPDs are the best way for us to effectively communicate the environmental impact of our products across product categories,” Aten says. “We are using these tools to drive innovation and product development and to reduce our Global Warming Potential throughout the full product life cycle. We also are using these tools to evaluate our recycled product architecture versus other non-recycled products and their overall global environmental impact.”
The company is also Cradle to Cradle Certified Bronze and has been recognized in the “Efficient Product” category as part of the NRW Environmental Economy awards. Every two years the Efficiency Agency NRW in Germany honors resource-efficient products and services of German-based companies. REGUPOL continues to focus on sustainability during its product development process, always striving to improve processes that reduce waste and energy consumption for our production.
The work is not done. “We have not yet reached the end of our journey,” Aten says. “Every day we work with our teams around the world to become better or to develop new products with our customers.” g
“Every day we work with our teams around the world to become better or to develop new products with our customers.”
Kimberly-Clark Professional offers a road map on what successful knowledge transfer looks like.
BY SOPHIA CONFORTIInitiatives that focus on greater energy efficiency are decarbonization strategies that offer environmental and economic benefits.
In the built environment—and all over the world—we’re feeling the effects of climate change. As extreme weather events increase, people and buildings alike are left bracing for impact. The aftermath is often devastating.
To remain standing, buildings and the spaces inside must be designed for resiliency. And for the betterment of the planet, architects and designers must embrace decarbonization strategies.
“In the history of design and buildings, way back in the day before modern times, the idea of adaptive reuse and building buildings to last was part of the baseline process. But somehow in modern times, we look at buildings and think of a short life cycle, maybe 30 years,” says Lisa Adams, sustainable design leader at HKS Architects and director of CitizenHKS.
“We are at a moment in time where we are reconsidering, looking back at what buildings have meant as a society, trying to bring us back to that point beyond focusing on a project’s immediate requirements,” she says. “In the world we’re living in now with global warming, the impact of the decisions we make as designers is probably the most impact-
ful of any profession on the planet.”
For manufacturers, the weight of those design decisions comes down to transparency about the processes and products they create. How can architects and designers be expected to successfully design for durability and decarbonization without it?
Kimberly-Clark Professional, a leading manufacturer of hygiene solutions for workplaces, isn’t afraid to show what’s going on behind the curtain. In fact, Kimberly-Clark is ranked #2 on Barron’s list of the most sustainable companies in the US and is a nine-time honoree on Ethisphere’s list of World’s Most Ethical Companies. For its customers, Kimberly-Clark Professional makes information about carbon footprint and other sustainability metrics accessible as a point of business integrity.
“Our customers expect we will always do what’s right,” says Cristine Schulz, global sustainability manager at Kimberly-Clark Professional.
“Everything we share is based on data and science to reassure our customers we’re doing everything we can, in the most effective manner, to continue to innovate and reduce their carbon footprint. This helps customers meet their own sustainability goals and commitments to their employees and guests.”
For example, based on progress against existing goals, Kimberly-Clark is setting a new ambition to be 100% Natural Forest Free across its product portfolio. The company expects to be more than halfway to this goal by 2030.
In 2022 Kimberly-Clark achieved an absolute reduction of greenhouse gas emissions of 42%—a reduction of 65,000 metric tons of carbon dioxide equivalent from the previous year.
“It’s not just about our direct carbon emissions. It’s about getting carbon emission data from up and down our supply chain,” says Lena Heidel, sustainability manager at Kimberly-Clark Professional.
“Carbon emissions from the manufacturing of the raw materials and all the way through to the finished goods disposal at end-of-life have an impact to our climate.”
Taking the entire supply chain into account is a necessary step. And yet this is where decarbonization gets complicated. “We’re not simply going out and buying offsets. We’re exploring partnerships and emerging technologies to help get to zero waste and reduce carbon emissions,” Heidel says. “We’re going to do it the right way.”
For facility designers and managers, smart, internet-connected restrooms are playing a larger role in healthy commercial buildings. Onvation is an example of a connected software solution for smart restroom servicing by Kimberly-Clark Professional that tracks use and immediately deploys cleaners when and where they are needed to reduce waste and ensure restrooms meet enhanced cleanliness expectations.
The team is also rethinking product end-of-life programs. These initiatives take eligible Kimberly-Clark Professional products and recycle them for use in new consumer
goods like outdoor furniture. These programs are highly traceable, too— another layer of transparency.
Encouraging transparency and making information accessible is one thing; the credibility behind the data is another. Kimberly-Clark Professional invests in third-party certifications. In fact, the company was the first in its industry to certify tissue products to be Forest Stewardship Council-compliant in 2008.
Add on requirements from other certifications like UL ECOLOGO, which certifies products and services have reduced environmental and health impact, and there’s no doubt that the investments for third-party certification are significant. But they are essential in a world of misinformation.
“Third-party certification gives our customers confidence that when they’re buying our products, or when they’re working with our suppliers, we’re doing the right thing. We are verifying the recycled content that’s put into our products, buying from responsible sources of virgin material, and reducing our plastic and water footprints,” Heidel says. “It gives
customers confidence that they can buy from Kimberly-Clark Professional and do good.”
The alternatives are not manufacturing in an environmentally responsible way, not providing transparency, and not giving architects and designers the tools they need to specify materials that aid in decarbonization and building resiliency. What kind of future does that create for the planet and those of us who call it home?
“When discussing sustainable design with clients, initial concerns can revolve around costs. However, decarbonization emerges as the hero in this narrative,” Adams says. “Materials like mass timber, acting as carbon sinks, can significantly expedite project schedules, while prefab solutions can streamline the overall project timeline, leading to faster completion. Decarbonization strategies bring value when designing for change, reduce the burden of cost, and provide economic benefit to clients.”
And that’s nothing to say about the environmental benefits of decarbonization, which are certainly appealing to the built environment’s biggest client: the Earth. g
“Decarbonization strategies bring value when designing for change, reduce the burden of cost, and provide economic benefit to clients.”
How companies like Aquafil Group are committed to greatness
By Lark BreenIIN TODAY’S WORLD many enterprises are genuinely doing their part to support the future of our planet, while many others get by on empty promises and implied environmentalism. “Greenwashing” is not news to the world of sustainable building, and it rears its ugly head in countless consumer-facing industries. In fashion, a UN report found that 60% of sustainability claims by European fashion giants are “unsubstantiated” and “misleading.”
There are, of course, companies genuinely doing the work—and consumers who pay attention to who’s making real progress and who is encouraging further innovation. Two of those companies driving change are Aquafil, the Italian fiber engineering group prioritizing innovation for a more conscious future, and Patagonia, the famously anti-consumerist outdoor clothing and lifestyle brand.
Sustainability via Transparency
Sustainability is ingrained in Aquafil Group. Its champion product, ECONYL® regenerated nylon, is made entirely from waste, can be recycled an infinite number of times, and maintains the same quality as standard nylon made from oil but with a much lower environmental impact.
Aquafil collects carpet waste through its US carpet recycling facilities, collects industrial waste from partners around the world, and collaborates with the aquaculture industry to recover fishing nets. As of today ECONYL regenerated nylon has supported more than 1,700 partnering brands, including Patagonia, in their journey toward sustainability.
The ECONYL brand makes leaps toward larger, industry-wide change that Aquafil intends to manifest with its partnerships and advance through education and transparency. By talking about initiatives that impact the environment, Aquafil engages greenwashing’s most formidable enemies: education and transparency.
“Education is a powerful tool, so part of our brand mission is to raise awareness of sustainability issues and help both brands and consumers make more informed decisions about their consumption and lifestyles,” says Aquafil’s CEO Giulio Bonazzi.
Meanwhile, transparency drives Aquafil’s governing bodies, its goal-setting initiatives, and its relationships with its equally-as-dedicated partners across industries—from carpet manufacturers to fashion innovators like Patagonia—at every step.
The clothing and lifestyle brand shares the priority of transparency. “We’ve found that being open about our success—and failures—has helped the company and, in some cases, other businesses, too. The more you can share about what you’ve learned, the more chances you have to inspire industry-wide shifts toward more responsible environmental and social practices,” says Patagonia’s Gin Ando.
Making a Commitment
“More and more companies around the world are focusing on Environmental, Social and Governance (ESG)
themes and touting their achievements, but very few of them really make sustainability part of who they are. We do not want this to be the case for Aquafil,” Bonazzi says.
Instead Aquafil has encoded sustainability into its mission. Developed in 2008, Aquafil’s ECO PLEDGE consists of five principles that inspire all of Aquafil’s activities and guide its operations. These principles are: rethinking products in a circular perspective; protecting the environment; sharing responsibilities throughout the value chains; caring for the well-being of individuals; and supporting the local communities.
The ECO PLEDGE principles were not chosen at random. “Each one aligns with the UN Sustainable Development Goals (SDGs) to ensure consistency with overarching international agendas and to achieve transparent, effective, and long-lasting responsible growth,” Bonazzi says.
Aquafil selects SDGs to target in a bottom-up approach beginning with evaluating each goal’s impact, then grouping them into macro-themes. A customized software platform collects data among all the Aquafil production plants to track both social and environmental KPIs. With this system Aquafil is able to actively target 11 concrete SDGs through its projects.
Bonazzi points to the EU Commission’s Strategy for Sustainable & Circular Textiles in 2022 as a guiding initiative for the textile industry and proof that Aquafil is on track with its efforts. The initiative defines a set of concrete actions to ensure that by 2030 textile products are long-lived, recycled and recyclable, free of hazardous substances, and produced ethically and sustainably.
Aquafil is 20 years ahead of the curve on this one and is thrilled to see governing bodies and textile industry peers following suit. The group voluntarily pursues certifications that back up adherence to the highest environmental, social, and quality standards and has launched numerous initiatives aimed at key EU priorities including eco-design and greenwashing.
“Education is a powerful tool, so part of our brand mission is to raise awareness of sustainability issues and help both brands and consumers make more informed decisions about their consumption and lifestyles.”
Transparency in business offers companies, including sustainability leaders Aquafil and Patagonia, the opportunity to inspire industry-wide shifts toward more responsible environmental and social practices.
“In the last year alone we have spent €10.7 million on R&D activities to develop cutting-edge technologies and circular materials that reduce the industry’s negative impact on the planet,” Bonazzi says. “Our objective for 2025 is to generate 60% of our fibers revenues from ECONYL nylon and other regenerated fibers. We aim to do this by increasing waste recovery, strengthening take-back programs, and educating and communicating our vision to clients.”
The Born Regenerated to Be Regenerable, or “Born R2R,” program is one of Aquafil’s most successful recent initiatives. The project engages manufacturers to co-design carpets that are created to be recycled instead of ending up in landfills at the end of their life. These carpets of the future are made with ECONYL nylon and can be fully recycled and repurposed into something new.
Born R2R targets the first three pillars of the ECO PLEDGE. Meanwhile Aquafil is also reducing scope 1, 2, and 3 emissions, uses 100% renewable electricity, and is recovering more than 90% of waste created in production—clear steps toward lessening its impact on the environment.
The ECO PLEDGE principles focused on social change are also seeing progress, as Aquafil contributes to charitable organizations like Alba Chiara APS, a domestic violence protection group, and invests in the future of design by partnering with university programs like New York City’s Parsons School of Design and Burg Giebichenstein University of Art and Design Halle in Germany.
Aquafil’s strategic partnerships involve stakeholders across the value chain, including suppliers, manufacturers, designers, and even customers. The key, Bonazzi has told gb&d, is finding partners who integrate sustainability into their business models and are ready to pursue SDGs hand in hand.
Patagonia certainly fits the bill, as the company continues to be dedicated to combating climate change with dozens of social, environmental, and material programs that promise to lessen their impact on the world. Plus the company relies heavily on nylon—light, quick-drying, and durable—for many of its products.
“Using ECONYL recycled nylon is a way to prove to other manufacturers the material can stand up to the high-quality standards we demand in whatever we design and build,” Ando says. Of course, it also makes a marked impact on the sustainability of the brand as a whole.
Ando reports that in Patagonia’s latest line, the use of recycled nylon reduced CO2 emissions by more than 6.6 million pounds compared to non-recycled nylon, according to the Higg Materials Sustainability Index.
Partnerships like that of Aquafil and Patagonia allow companies to share their successes—with each other, with customers who wear and love the clothing, and with anyone who cares about sustainable innovations, whether or not they wear Patagonia. They can all see the value of a product and process that can achieve everlasting life through concentrated eco-design for the circular economy. g
Climate change is expanding the need for resiliency and sustainability in buildings.
By Ian P. MurphySSince the dawn of civilization architecture has helped people cope with extremes like heat, moisture, and seismic activity. But with climate change making such extremes more punishing, buildings must withstand stronger storms, higher temperatures, and more devastating floods to protect their occupants.
“Architecture is coming from extremes,” said Kathleen Hetrick, sustainability engineer for Buro Happold, a global sustainability engineering consultancy. “Every aspect of the built environment is protecting people from extremes.”
While some areas might feel relatively safe from the most disruptive effects of climate change, the industry is realizing no one is immune—and more RFPs are including resilience in their sustainability goals as a result. Projects must anticipate and meet climate challenges to retain value. And ideally they need to accomplish this without contributing to the factors producing climate change.
Architect Frederick Fisher + Partners’ Santa Monica City Hall East, which Buro Happold also worked on, employed advanced architectural, engineering, and construction practices to confront the challenges of climate change. Built to the Living Building standard and one of the “greenest” buildings in the world, it makes positive contributions to its environment rather than merely lessening its negative impact.
Santa Monica City Hall East has automated windows and air quality monitoring to deal with the threat of California wildfire smoke. The building collects and treats rainwater to make it potable, and it features the largest composting toilet installation on the West Coast. The project “really focuses on passive design—having the building work as hard as it can to keep it comfortable,” Hetrick says.
Designing for climate change is an exercise in risk management, Hetrick says, though some risks may be more obvious than others. “It’s hard for humans to think about the future. You deliver on time and under budget, and then X, Y, and Z happens, and you didn’t design for those possibilities. Do yourself a favor: Model for every contingency.”
A holistic approach to designing for climate change should extend throughout a building’s life cycle, from supply chain to upkeep. “You have to layer the systems, which is going to cost a little bit more upfront,” Hetrick says. “You’re thinking about all the situations that could come. Even the maintenance is important.”
For example, “When you’re making decisions about finishes, you know that toxic chemicals come cheap, and those materials are manufactured in Texas or Louisiana,” she says. “When a big hurricane comes through, those factories can flood and spread a lot of pollution. Do you want your brand associated with that?”
energy, and net-zero water project. Buro Happold provided integrated engineering and sustainability consulting services.
“It’s hard for humans to think about the future. You deliver on time and under budget, and then X, Y, and Z happen, and you didn’t design for those possibilities. Do yourself a favor: Model for every contingency.”
“Every aspect of the built environment is protecting people from extremes.”
Any project that prioritizes resiliency represents progress in meeting the challenges of climate change. “These are complex problems,” Hetrick says. “Just because you can’t claim zero carbon doesn’t mean you aren’t making a difference. Take an activist approach: Push contractors in the right direction, and push clients in the right direction.
“This is what people want to see, and it also protects your investment,” she continues. “Climate change is happening everywhere all at once. You want to minimize risk. You also want to maximize opportunity. If you’re spending millions of dollars on a project, it’s a huge investment. Do you want to risk that?”
Weather is harsh on building finishes, and climate change is making the wearing effects of UV light, wind, and water stronger. But advancements in coating technologies can protect a variety of substrates used in construction against the elements for longer periods, and often head off the need for significant repairs or replacement.
Founded in 1878, Ohio-based APV Engineered Coatings custom formulates and manufactures industrial coatings and advanced chemical products. Chief among them is NeverFade®—a premium line of low-VOC, water-based exterior architectural coatings formulated with Kynar Aquatec® PVDF, a resin that is unprecedented in the industry for lengthening the life of building facades.
NeverFade can be used on the entire building envelope, including metal roofs, concrete, walls, and stucco surfaces. While a typical building facade requires recoating every four to six years, the product is warrantied to protect surfaces for at least 15. “It’s not going to break down,” says Ernie Porco, product application engineer at APV. “It’s protecting that substrate for the entire time.”
Beachfront properties are particularly vulnerable to the elements, being exposed to sunlight, high humidity, salt spray, and sand. When the builder-applied acrylic coatings on the stucco exterior of the 41-story Trump Hollywood condo building in Hollywood Beach, Florida
started to get chalky and dull, Capital Contractor Services opted for NeverFade.
“Trump Hollywood’s prestige, size, unique shape, and location, coupled with the fact that it was occupied by residents who didn’t want to be inconvenienced during the facade restoration process, made it imperative for us to work deliberately, safely, and with a high level of quality,” says Alex Forjan, executive vice president of Capital’s Exterior Division.
Another building in Rockwood, New York recently underwent a complete facade restoration using NeverFade. The coating on the 40,000 square feet of aluminum panels had previously been field-applied with an acrylic polyurethane that had degraded significantly due to UV exposure and precipitation.
Both restorations were accomplished with minimal disturbance to building occupants. Unlike most high-performance coatings, NeverFade is low-odor and water-based, Porco says. “We’re doing fully occupied buildings and not receiving any complaints.”
Maintenance and upkeep are expensive, but recoating can often help building owners avoid costlier repairs. “Most of the time buildings will just rip the substrate off and replace it,” Porco says. “We can get another 15 years and keep those materials out of a landfill. And if we can get people to paint the building the first time with it, it works even longer.”
Other APV products include BLOCKSEAL™, a liquid flashing that is AAMA 714-22 verified, low-VOC, fast-drying acrylic adhesive that keeps moisture from penetrating door and window openings beneath a structure’s exterior facade. Another superior product is KAPGUARD®, a line of factory-applied finishes custom-formulated with Kynar polyvinylidene fluoride resin, a tough thermoplastic polymer, in both water and solvent-borne chemistries.
NeverFade often comes in at a higher price point, but this premium coating line offers no-fuss application and ready-to-use formulations. “Building owners see the price tag and shudder a little bit,” Porco says. “But then they realize they’re not going to have to put up swing stages and do all the labor again for 15-plus years.”
“A field-applied product that can be air-dried and have the same performance as a baked-on coating is huge,” Porco says. “Some of the architects we meet ask, ‘Why didn’t we learn about this sooner?’ It’s a next step in the coatings world, especially with VOC requirements.” g
Modern exterior product solutions should be designed to adapt to unpredictable weather patterns.
By Laura RoteHHOW DO YOU DESIGN AND BUILD FOR THE FUTURE IN A WORLD THAT’S UNPREDICTABLE?
Climate change has led to an increased number of severe storms, and building codes are changing rapidly to ensure modern projects stand a better chance to weather the storm.
Expansion joints may be niche, but they’re a crucial part of the resiliency conversation when it comes to the building envelope, says Matthew Fisher, senior product design manager at Inpro’s Engineered Metal Division. And he’s not just saying that because he designed the latest in Inpro’s 650 Series. The former architect and construction manager has been a LEED AP since the inception of the sustainable certification program in the early 2000s, and he’s passionate about designing better buildings. “It’s always been a topic I’ve been sensitive to,” he says. “I will always try to lean toward the smarter, more durable solution, ensuring we’re using something that is responsibly resourced.”
Fisher says expansion joints have to withstand daily, seasonal, and seismic movement patterns. “There is driving rain trying to push moisture into every crack, and high temperature differentials from interior to exterior create tough HVAC loads. The covers and their accessories also need to resist hurricane force winds, fires, insects, et cetera—all while being adaptable to the multitude of building veneers that architects design with.”
Architects are reporting a growing need for wider expansion joints in projects than they used to encounter. Take a New York tremor that occurred in early April 2024, registering at 4.8 magnitude, or indications in Texas of increased joint width requirements on new buildings even though no fault lines exist in that state. Fracking is thought to be creating unusual soil displacement resulting in tremors; the number of encounters has doubled to 201 events in 2021 alone, according to the Bureau of Economic Geology at University of Texas in Austin. And Miami-Dade County in Florida is infamous for encountering hurricane level events so often their ultra-stringent wind resistance code is being adopted in other regions experiencing similar high wind events, including projects in Oregon along the West coast.
“If you don’t plan for proper expansion joints, Mother Nature will install one free of charge, and it will likely not be a nice straight line,” Fisher says. He says expansion joints are a necessary evil that architects and structural engineers must plan for, and that while many architects and designers don’t love them, modern solutions from Inpro will surprise them.
“Architects think expansion joints all leak, and they’re all ugly. That’s not the case,” he says. “I can make it be a chameleon in the background. I can make sure it’s waterproof, that it addresses your thermal needs, and I can even make them acoustically dampening.” He says few people like these functional joints, as they interrupt the aesthetics and complicate the cohesive skins on the project, but Inpro offers solutions to meet these challenges that are also designed to a higher durability than code currently requires.
“Elongating the product’s lifespan while allowing for adaptability to changing conditions is always a goal I strive to achieve when we begin a new endeavor. I first start
with a responsible material—in this case aluminum. Then I ensure we have a modular-based design that is easily customizable and adaptable. I then ensure the cover is able to camouflage itself in its environment while balancing safety with durability, all the while not losing sight of the core function of addressing dynamic structural movement,” Fisher says.
While the purpose of expansion joints is to break up the structure into individual sub-structures, the role of the architectural joint covers is to mask that break and give the appearance of a seamless, large building, Fisher says. Projects with the most common application of expansion joint solutions include but are not limited to mass transit (railway and airports), educational campuses, stadiums, civic centers, and mixed use developments employing parking with featured plazas above them.
“The key to a successful expansion joint solution is proper product selection specific to the unique project challenges,” Fisher says. “Coordination with surrounding substrates and waterproofing measures is key, then tight trade sequencing is required
through the multiple stages for success.”
Unlike most building products, he says expansion joints reach across nearly every building material—concrete, steel studs, fireproofing, waterproofing, wall, floor, and plaza finishes. “These needs continue all the way up the roof. This presents a unique challenge versus most other products you will specify.”
When expansion joint conditions fail, the threat of water intrusion increases the opportunity for mold to grow, Fisher says. “If that occurs, accessing these often tough conditions is the first problem, followed by removal and disposal of many finishes, degradation of the structural integrity, and downtime for operations in those affected finished spaces,” he says. “If thermal considerations are not implemented on joints, air drafts, loss of heating and cooling efficiency, and potential reduction of the life safety accessories behind the covers can also result.”
The LEED-certified Owensboro Health Medical Center project emphasized flexible design that accommodates streamlined processes, advanced technology, and future growth.
“THOSE TRANSITION POINTS ARE CRITICAL, AS THAT’S WHERE 90% OF LEAKS ARE FOUND.”
Inpro’s 650 series was tested and developed to anticipate even more stringent codes of the future.
The 650 Series is a complete building envelope solution in one product, and it’s the first of its kind in the industry, Fisher says. Unlike competitors’ roof and wall systems, 650 was designed to work together—from roof to wall. It’s designed to handle complex transitions seamlessly. “I’ve designed the first cohesive system that addresses the wall, the roof, and every change in direction with the same system,” Fisher says, adding that those transition points are critical, as that’s where 90% of leaks are found. “You start letting in water or letting out heat or cold, and that’s not a good sustainable life cycle for that building to undergo.”
The 650 allows for full 100% three-dimensional movement along with full lateral shear capabilities. Inpro’s panels are factory preassembled to minimize onsite installation labor costs. The installation for the walls is similar to and as simple as hanging a prefinished door on its hinges within your home, Fisher says. The roof system locks down tight but can open and close like the hood of a car, allowing for ease of annual inspections of the waterproofing membrane under it. The systems’ modular design allows for project-specific customization without the cost and complexity typically associated with this approach. Inpro engineering teams also designed and tested every component to endure hurricane level winds, particularly on the roof’s leading edge, where the most uplift forces culminate.
“These are designed to survive a seismic event. Most earthquakes last about 45 seconds. Buildings are moving and swaying violently in that time. This system is designed to survive all of that swaying without getting damaged, so the expansion joints can be reused.”
Small things are important, especially to the overall sustainability of a project, says Brian Crilly, a senior associate and designer at Stantec.
“When you get down to the heart of the matter, a different architect or designer might give you a little bit of a different answer, but from the standpoint of Stantec, we’re absolutely committed to the environment and also preserving what we’re creating,” he says. “Our lives are changing because of what we’ve done to the climate, and we’ve got to do something about it.”
Stantec is very much concerned with building projects that last with durable materials, and in the instances where a building is being torn down, looking at how that can be done more sustainably, too. Material choice, he says, is of utmost importance.
Architects can design a beautiful, flexible space a client loves, but that client may not always be there. Hopefully the next client loves the space, too, but that’s not always the case, Crilly says. The next tenant may make significant changes to the building, and some buildings are even torn down.
“Let’s not use materials that when thrown away are harmful toward the environment,” he says. “It’s about identifying materials or promoting ideas where there is a longer life to what we’re doing. And if there’s not, making sure that if something is removed, that it’s not harming us when it’s thrown away or recycled. It gets down to the basic tenets of resiliency really.” g
“With climate changes intensifying, ensuring structural resilience has become paramount,” says Inpro’s Matthew Fisher. “That’s where solutions like our 650 Series come in. We’ve engineered it not just to meet current codes but to anticipate future requirements, particularly regarding wind resistance.”
Innovative technology in access control
BY LAURA ROTEAcrisp and clear microphone, HDTV video, a friendly chime, and even night vision— access control has come a long way from a knock on the door and a glance through a peephole. Today’s technology gives people almost instant information about who’s at their door, as well as a remote way to let them in if they so choose.
Access control is a key component of how Stantec designs safe buildings, according to Scott McChesney, senior project manager, technology, for Stantec. Cameras and how people enter a building are conversations that are had early on in the design process today, he says. “It’s one of the very first conversations that are had—because not only does access control control the building, but access control is changing and becoming more integral with smart buildings,” he says.
It’s important for architects to fully understand a door’s design needs early, for example, so they can also bring in a door hardware consultant early to get the proper hardware, says Misty Ryan-Gonzales, a project manager at Stantec. “Doors are super complicated,” she says.
Specialty locks are another consideration, McChesney says, including things like access control on exit routes and duress buttons at a hospital or school. Card credentials continue to get more secure, too, to protect against scams, and some video features take a timestamp so you know when someone enters and leaves a building. Delivery services can also be accommodated with temporary pins that expire after use. Features like mobile credentials on cell phones and video that pops up so you know who is at the door make people feel safer, McChesney says.
The biggest change in access control in the last 25 years, though, is probably the reader itself. Designs today are much more beautiful and often fit seamlessly into projects. “There’s been a tremendous change in the aesthetics,” McChesney says. “I remember 10 or 15 years ago, they looked like somebody put a brick wall on the wall. That’s not so much the case anymore.”
Now there are stainless steel options and customizable covers, easily integrated for project consistency. Ryan-Gonzales remembers when Stantec worked on a wedding venue a few years ago that didn’t want cameras or security functions visible in the background of photos.
“They wanted all of these different aspects of security to blend into the background,” she says. “That’s the part that’s really important to architects. They want the feeling of safety without seeing it.”
In previous years aesthetics may have been an afterthought in design, but not so anymore. “Security obviously is always necessary, but what’s happening now is individuals are starting to realize that it is necessary and there’s a lot you can do from an architectural perspective,” says Justin Clark, head of sales in the Americas, Australia, and New Zealand for DoorBird, who manufactures IP-based video door intercoms, access control devices, indoor stations, and accessories. DoorBird started in 2015 in San Francisco and is based in Germany; the brand was acquired by ASSA ABLOY, a global leader in access solutions, in 2022.
“Typically something that’s very high tech and very secure doesn’t always match the aesthetic desire of the developer, the architect, or the building owner,” Clark says. w“Design is becoming more focused when it comes to security products that hit the market. Specifically for what we do, that’s always been a focus—technology meets design. We believe firmly that we can create something that is technologically advanced and at the same time looks elegant and is consistent with the architecture of the building.”
Design conversations are increasingly including access control from the start. DoorBird offers a 3D configurator so design teams can imagine and customize their designs. “We have a configurator that allows you to create custom units, providing real-time pricing so you know what to expect, with more than 50 finishes, real bronze, burnished brass, and more colors. You can get it right and make sure it’s consistent with the other things you’re designing,” Clark says. “We’ve always had unique colors and finishes, but we really went full throttle in the design element about two to three years ago with the configurator.”
When someone comes to a DoorBird door station, they hit a call button or search the directory for a name and dial the corresponding buttons. That user then receives a notification on their smartphone or at an indoor station, or, if in a commercial setting, potentially on an IP-based phone. The user can screen the person and decide if they want to speak to them or let them inside the building. The setup can be installed anywhere from an apartment building to a single-family home to hospitality or schools.
Since the technology is now network or IP-based, it can be installed anywhere. “You only need two wires to turn our product on,” Clark says. It’s also helpful in a retrofit scenario, as that means DoorBird can leverage existing wiring, as long as there are two wires, and get the device online and connected to the internet and users’ smartphones quickly. Of course, for folks who may not want smartphone access or who just also want an indoor station, too, that also continues to be an option. “Having an actual intercom device on the wall inside the apartment or a separate unit is still necessary in a lot of different applications. For instance, in a senior citizen type of living situation, having an indoor station is critical,” Clark says.
DoorBird’s indoor stations connect back to the door station through the cloud, making installation and even retrofits easy. “It also saves time and money,” Clark says.
McChesney says modern access control is a breath of fresh air. “It used to be that we were hampered by having one station in the field that had to have a direct connection back to, say, an office phone, so we were limited,” he says. “Now with mobile creden-
tials they can log onto any computer on the network and interact with the intercom and buzz people in and out of the door. That’s another driving factor behind seeing intercoms being used on doors more than we used to.”
Security needs are ever-evolving, so what happens when technology needs to be updated? “With DoorBird it doesn’t mean we have to upgrade the whole unit. It just means we have to get inside the unit, get inside the cavity, and swap the internal module out. That’s way less expensive, with way less material that we have to replace time and again. That makes us quite unique in this space,” he says. “What we’re creating is not something you’re going to be replacing every season as soon as a newer product comes out.”
Instead of having to switch the intercom or the access control peripheral on the entrance, DoorBird can switch out modules with the latest technology while maintaining the existing hardware, whether that’s installed in stone cladding or set in a specific finish—things that are expensive to change. “That ability to create a true fixture definitely looks better, but then it’s also way more sustainable than switching something out every season.”
Features like mobile credentials on cell phones and video that pops up so you know who is at the door make people feel safer.
From a sustainability standpoint, design teams can also choose stainless steel, a highly recyclable material, for their covers, and, of course, when a module is designed to last, replacement materials are kept out of the landfill. “That’s going to be an enduring product on the building,” Clark says. “We’re really creating a fixture that stays on the building. Just as you might, for instance, find a certain sconce or lighting fixture on the outside that’s always going to be there; you just change out bulbs.”
Today DoorBird also reduces waste by sending only what is needed to customers, as opposed to sending power transformer options to meet various countries’ needs
and letting teams choose; they send only what is necessary to reduce costs and waste. The need for security certainly isn’t going anywhere, but access control should continue to become more user-friendly, Clark says. “People want to feel safe. Whether you’re at home or at work, you want to feel safe. It needs to become more user-friendly, and it needs to fit in with the world we see and how we want to see it. That design element is a factor there because it should look nice when you’re walking up to an entrance. It should blend in with everything else that’s going on. I think the more this becomes a status quo standard, the more we’ll find creative ways to make it fit with the world we want to see.” g
“The more this becomes a status quo standard, the more we’ll find creative ways to make it fit with the world we want to see.”
Preferences for outdoor living spaces that transition seamlessly from interiors are driving innovation in design.
Outdoor living is getting a lot more integrated into the everyday as the same level of attention around interior design is moving into outdoor spaces. Homeowners are finding new ways to get their outdoor spaces to flow almost seamlessly from their homes, opening their residences to the surrounding landscape while taking advantage of flexible, useful space.
Even in cold climates homeowners like to spend time outdoors, says Ray Calabro, a principal in the Seattle studio of Bohlin Cywinski Jackson (BCJ). “There’s a desire for fresh air,” he says. “There’s a desire to feel immersed a little more in the weather. And I think there’s a desire for people to want to gather together outdoors in spaces that feel comfortable.”
Depending on the client that might mean adding amenities like heat and ventilation, an outdoor shower, hot tub, grill, or bar to a deck or patio. Whatever shape the outdoor space takes, people are looking for the flexibility to entertain guests, read, dine, exercise, and relax just steps from their interiors.
“Spaces might have something like a firepit or a built-in cocktail bar—something that allows them to enjoy the view or the place a little bit more,” Calabro says. “Maybe it’s a fireplace, maybe the deck is covered but open to the view. Maybe there’s a heated floor or heaters in the soffits. You can do any number of things to mitigate some of the extremes and make places more comfortable for people.”
While outdoor living has never gone out of style, pandemic lockdowns encouraged people to reassess their spaces, expanding the concept of home to fresh air settings. “The outdoors was seen as the only safe way to connect,” Calabro says. “People decided to use their outdoor spaces in different ways. That was a huge leap forward.”
Serving residential clients in locations of natural beauty, Calabro and BCJ strive to design spaces that present minimal visual barriers to the surrounding landscape. “We’re trying to kind of dissolve the envelope of the house a little bit,” he says. “A trend seems to be spaces that blur the boundary between indoors and out. The materials used on the exterior and on the interior draw your eye out with as little interruption as possible.”
A guesthouse Calabro designed in the San Juan Islands, for example, features a central living room/kitchenette that opens to the outdoors on two sides. Depending
on the weather, the occupants can keep the wide glass pocket doors closed, leave only screens in place, or open the home completely. “We’re trying to make a place that feels calm and static-free.”
What makes a great outdoor space? “For me it’s a sense of calm,” Calabro says. “Immersion in the outdoors is about trying to become a little more connected to your surroundings. It gives you a feeling that you are given a perch or a view that maybe no one else has.”
Natural woods aren’t always up to the task when it comes to temperature extremes or high-humidity applications, however. Calabro specified thermally modified woods for a pool deck in one high-end home and says many West Coast clients are asking about fire-resistant composites for their home exteriors.
Even in relatively predictable climates, wood decking requires considerable maintenance and upkeep as well as periodic replacement. Architects and homeowners familiar with early versions of recycled composite decking materials may remember them looking, well, not so beautiful, but that’s not how they are now.
“The aesthetics have come a long way,” says Amanda Cimaglia, vice president of corporate communications and ESG for TimberTech, part of parent company The AZEK Company, a building products manufacturer headquartered in Chicago with operations across the US. “TimberTech’s decking materials are almost indistinguishable from real wood.”
So far only about one-quarter of decks in the US are made from composites, she says, but residential projects are increasingly turning to the manufactured alternatives. TimberTech is building awareness by tapping influencers like HGTV’s Married to Real Estate hosts Egypt Sherrod and Mike Jackson.
“Homeowners, architects, and designers don’t have to trade off on aesthetics to get performance and durability,” Cimaglia says. “That’s what’s helping us convert the market away from traditional wood applications that require a lot of maintenance and are less sustainable.”
TimberTech offers two decking lines that mimic the look and feel of real wood, albeit without the knots, splinters, and loose
“A trend seems to be spaces that blur the boundary between indoors and out.”
Indoor areas transition seamlessly to an expansive outdoor terrace protected by a dramatic roof overhang at the Highbank Residence, designed by Bohlin Cywinski Jackson (BCJ).
This BCJ-designed home in Alberta, Canada takes advantage of panoramic mountain and valley views.
screws. Durable and sustainable, they “allow homeowners to live their best lives outdoors,” Cimaglia says.
TimberTech Composite Decking by AZEK contains approximately 85% recycled material, a combination of high-density polyethylene (think laundry detergent bottles) and low-density polyethylene (the typical grocery store bag). These are shredded and combined with reclaimed wood flour, then encased in a protective layer of virgin polyethylene.
TimberTech Advanced PVC Decking by AZEK incorporates about 60% rigid recycled PVC from castoff flooring, siding, and piping products. Together the lines offer 35 colors and multiple textures, mimicking everything from elm to oak to walnut.
Homeowners looking for that seamless indoor/outdoor flow have options. “If they have light, airy oak floors on the interior of the home, they want to transition that aesthetic to their outdoor living space,” Cimaglia says. “If they’ve got darker rich walnuts inside, they want to be able to carry that to their outdoor living spaces as well.”
Weathered looks are currently popular, but preferences vary. “From a design perspective it’s unique to the homeowner,” Cimaglia says. “What I might like in my home might be different from what you might like in your home. But the great thing is the breadth and depth of our portfolio matches any design desire or aesthetic.”
For TimberTech the aesthetics are more crucial than ever. While older composites often had an exaggerated, almost cartoonish wood grain look with one or two base colors and a repeated faux grain, TimberTech delivers a more nuanced product that looks as elegant as real wood.
For nearly a decade TimberTech has designed its composite and PVC decking lines to mimic specific woods like stained ipe, mahogany, and reclaimed wood. Pigments are blended to deliver the rich spectrum of coloration seen in natural wood, and capstock finishes are refined to eliminate repeated patterns in the grain; like real wood, no two boards are identical.
As a result architects and designers no longer need to worry that composite decking materials won’t meet the aesthetic demands of high-end homes. TimberTech’s decking is almost indistinguishable from real wood—but with better performance and longevity.
TimberTech’s R&D has successfully increased the amount of recycled material used in its products without impacting their design profile, diverting more than 2.1 billion pounds of waste and scrap from landfills in the last few years since 2019. “We have a goal of using 1 billion pounds of recycled material annually to manufacture our products,” Cimaglia says.
Every pound of recycled plastic used in lieu of new plastic represents a 75% reduction in TimberTech’s carbon footprint, Cimaglia says, and it’s more than just reusing scrap. TimberTech sources postconsumer vinyl siding, plastic bottles, bags, and other plastic wastes to recycle into its products.
The company has made itself the largest vertically integrated PVC recycler in the US, creating a fully sustainable, circular life cycle for PVC that would otherwise take up to 500 years to break down in a landfill.
The company doesn’t yet have a lot of decking material that has reached the end of its 30- to 50-year warranty (depending on the product line), but it does have a
recycling program to collect TimberTech cuttings and scrap and turn it into new decking. “There’s so much waste in the built environment,” Cimaglia says. “We want to make sure we’re doing our part to recapture those products at the end of their useful life.
“Low-maintenance decking means less frequent cleanings, no harsh chemicals needed, and less water used. Additionally, because of the long-lived nature of our decking products and high amount of recycled content, TimberTech actually has lower embodied carbon and a lower lifecycle carbon footprint than traditional applications,” she says. “People are often surprised to hear that something that is made of synthetic material is more sustainable than wood.”
Cimaglia says that there’s no limit for TimberTech decking products once people discover their aesthetic and environmental advantages. “New generations of architects and homeowners care about sustainability,” she says. “We all want our homes to be more sustainable, but we still want them to look good.” g
June 10–12
Comfort
For more than 100 years Cleveland Clinic has been setting the standard for patient care in clinical settings.
THE NONPROFIT ACADEMIC MEDICAL CENTER has grown from a small outpatient clinic to nearly 300 locations with over 80,000 caregivers worldwide, adding up to 15 million patient visits per year.
Travis Tyson has been with Cleveland Clinic for more than 17 years. He started as an architect in the planning and design department and now works as the director of planning and design. His team—more than a dozen employees—oversees all of the programming, planning, and design for the entire enterprise internationally. “Primarily we are here in Cleveland, but we oversee all 39 million square feet of our portfolio,” he says. “We are really proud of the work we do and the coordination between the clinicians, patients, and design team to create these built environments. It’s pretty exciting.”
The team is working on more than 1,200 active projects at any given time. A new Neurological Institute (NI) building is just one example; it’s currently being built on the main campus in Cleveland. “It’s one of the largest projects we’ve ever done. It’s just over a million square feet. That project itself is going to allow us to consolidate all of our NI services into one building on campus. Right now we’re spread out in about nine locations where patients may have to go.”
The project will dramatically expand the physical infrastructure dedicated to neurological care on the campus while consolidating inpatient and outpatient neurological care services. The design aims to maximize open spaces and natural light for ease of movement for patients. The NI project is scheduled to open in late 2026. It’s partly
the result of feedback from Cleveland Clinic’s clinical users and physicians as well as patient focus groups. Cleveland Clinic also has an Office of Patient Experience and Office of Caregiver Experience that help inform design across facilities.
Across projects the Cleveland Clinic team is big on daylighting, Tyson says, especially as he says Cleveland is not exactly known for being sunny. “It’s important for our patients’ healing and even the mood of our caregivers.” The clinic’s new Mentor Hospital opened in 2023 makes great use of skylights, for example. “It really demonstrates how you can get natural light into a facility.”
The right LED lighting is an important supplement, too. Cleveland Clinic recently replaced all of its overhead lighting with LEDs. LED lighting in patient rooms can also have varying shades and brightness— giving control back to the patients. “Patients can change the color to help calm and relax them,” Tyson says.
Tyson says that while health care design has centered mainly on the patient for many years up until as recently as a decade ago, a high level of care and attention is now paid to every person who enters the building. Cleveland Clinic focuses on what’s best for patients, their families, and caregivers, too. “That’s just as important as the patients themselves because we want to make sure we take care of caregivers so they can give proper care to our patients,” he says.
Places where staff can rest, relax, and even emotionally heal after a traumatic event are a growing emphasis. More caregiver spaces are being rolled out across Cleve-
land Clinic inpatient facilities currently as part of a phased rollout. “We’re creating more respite spaces and ‘lavender lounges’ for caregivers.”
The clinic also continues to find ways to give patients back a feeling of control, Tyson says. “We ask: What do they want to control, and what would make them heal faster and better within their spaces? We have patient panel focus groups we talk to to get feedback, whether it’s their lighting controls, HVAC controls, or what they can order for food and how they order it,” he says.
Comfort and control are also top concerns for another leader in the industry—La-Z-Boy Healthcare | Knú Comfort, whose designs include a growing series of patient room recliners and sleep sofas to make overnight stays for guests more comfortable when wanting to be near loved ones.
“Comfort is more than just a physical feeling of the occupant,” says Adam Stemle, vice president of sales and marketing at La-Z-Boy Healthcare | Knú Comfort. Stemle has been in the industry for more than 20 years and seen the evolution firsthand. “For us the physical comfort of the occupant or patient is a main driver, but we consider all aspects of comfort when designing our products. The comfort of the caregiver or nurse or doctor is an equally important driver on how and why we design specific products and features of the products.”
For example, seat height can be specified based on specific needs, providing added physical comfort to palliative patients to get into and out of a chair, as well as when it’s a higher seat height, the caregivers don’t have to bend down as much or endure physical strain while lifting or transferring patients from chair to bed or bed to chair. “Another aspect is the way our motion products are intuitive and don’t rely on a multi-page in-
struction or use guide on how to use these products,” Stemle says.
Comfort can be financial as well, he says, not only considering the competitive cost of these products in the market, but also how La-Z-Boy Healthcare | Knú Comfort designs products to last a long time and have field replaceable components and parts if something should happen. “When something happens to an infusion chair or oncology chair, that chair can be repaired onsite and back in service quick.”
The Durable Series is La-Z-Boy Healthcare | Knú Comfort’s flagship, including the Durable 550, 650, 750, Durable Power, and Exam Lift solutions. This lineup includes the world’s first zero gravity recliners designed for health care applications, Stemle says, combining the company’s 50-plus years of recliner mastery with the latest technology to create the unexpected—a fully adjustable power recliner.
“That whole product line was designed to really provide a solution that took comfort to the next level, took intuitiveness to the next level. It took the recline handle and
back recline pull off the chair, and it put all the chair’s function and motion into the patient’s or caregiver’s hand. That really revolutionized how that chair works,” Stemle says. “Now you’re not relying on physical action to open and push a chair back and do all of these functions. Now you have all of that control in the power of a wand.”
While he says there have been other power recline products in the marketplace, the Durable Power Series is the only one to offer multiple motors working together. “We’ve got three and four motors inside these chairs that are programmed to work together to provide positions like zero gravity, sleep, Trendelenburg, and home position on a preset. A zero gravity position is best achieved by taking as many presser points off of your body by evenly distributing your weight and body angles with leg rest, seat angle, and back angle adjustments to eliminate pressure points during long-term sitting or treatment applications.”
The trusted aesthetics and comfort of La-Z-Boy remain with their health care furniture, and the chairs themselves are in-
“Now you have all of that control in the power of a wand.”
tuitive, Stemle says, adding that they fill a void where durability is a must. “Most of the power products and recliner mechanisms in health care today are off-the-shelf mechanical products that some manufacturers will try to beef up in different ways to make them more durable or sustainable for the health care environment.”
The La-Z-Boy Healthcare | Knú Comfort offerings are built to take the daily abuse common in a health care environment, and new offerings also include lift assist and exam lift functions to raise the chair off the ground. “That’s really focused on caregivers not having to lift the patient out of the chair. Caregivers are asked to do so much in the facilities, and we are trying to bring products to address caregiver safety in addition to all the functionality that is needed in today’s health care environment,” Stemle says.
All Durable Series recliners feature a quick removable back that can come off for cleaning in seconds. Zero entrapment areas and the lift-up seat allow fast sanitization on every shift, too.
In spring 2024 La-Z-Boy Healthcare | Knú Comfort launched its new Kenzley Sleep Sofa, an evolution of their other lines that makes keeping rooms and furniture clean even easier. Stemle says it’s important to have a product that doesn’t require you to put your hands anywhere you can’t see when you’re cleaning—especially considering there could be fluids or even sharp objects.
“We’re trying to integrate a lot of those cleanouts, a lot of that functionality, but the whole goal with everything, going back to the late ’90s, is to make it less institutional.” Modern furniture solutions should make patients feel as comfortable as possible and make for more inviting healing environments, Stemle says. La-Z-Boy Healthcare | Knú Comfort offers sleep sofas, sleep benches, pullout sleep sofas, and customizable options as part of a vast array of solutions that fit well in a variety of patient rooms, including labor and delivery and pediatric spaces.
“There are a lot of products being designed and developed in the last few years that are more than just a couch and a bed. You might have a couch with a table in the
center of it that raises up so you can work or dine off of it or use it as a game table, but it’s still in that same footprint of sleep sofa so you’re maximizing your real estate in a patient room.”
Maximizing real estate is a key goal at Cleveland Clinic. Given that the institution dates back more than a century, they’ve had to figure out how to grow from their original main campus over the decades. “Our footprint is fairly large on our main campus, but we don’t have a lot of other space to grow, so we have to think about: How do you best utilize your existing space, what’s the function of those spaces, and how do you use space in the most efficient way? One of the trends we’re seeing is converting administrative space or other types of space into clinical spaces to minimize the footprint of our administrative space,” Tyson says. Tyson says planning and design is often centered around the idea of doing more in less space and with less money. “How can we convert or utilize our spaces differently in the future using technology?” he asks. What used to be considered futuristic is near, he thinks. “It could be integrating technology on the wall so it’s monitoring you as you come into a building and telling you where to go and removing all waiting rooms. It’s using your spaces differently so patients know exactly where to go. We talk about the future, but how do we implement ideas like that to change the footprint and change the layouts and designs of our spaces? I don’t know where we’re going to land, but I hear lots of conversation about all this cool stuff. We want to make sure we get it right before things are rolled out because of course we are dealing with people, but I think in the next few years things are going to change quite a bit.” g
How sustainable flooring and more makes a difference in health care
The need for sustainable, people-friendly, easy to clean products in health care settings is great, especially as the built environment is responsible for roughly 40% of global carbon dioxide emissions.
NEARLY 5% OF THOSE GREENHOUSE GAS emissions are reported to come from the world’s health care sector, according to the Commonwealth Fund. The US health sector is responsible for an estimated 8.5% of national carbon emissions.
Experts point to a growing need to make health care systems greener, recommending renewable energy integration, natural lighting, sustainable materials, green roofs, and smart building management systems as part of overall design, according to the National Institutes of Health.
Health care facilities nationwide have largely taken note of this need. In 2007 Cleveland Clinic committed to LEED for all of its new major construction projects. “Our guidelines on all of our projects are to meet those criteria,” says Travis Tyson, director of planning and design at Cleveland Clinic.
Cleveland Clinic has an Office for a Healthy Environment that oversees sustainability across facilities—not just the buildings and mechanical systems but a lot of different programs, Tyson says. The health care system is constantly considering ways to reduce energy and water usage as well as consider each material that’s used in its designs.
“We take a hard look at all of our suppliers and what our materials are made from. We want to make sure they aren’t hazardous to the health of our caregivers or our patients. When we specify something we always ask for that detailed information so we can review it and make sure it’s something we want to put into our buildings.”
Every year the Cleveland Clinic team re-
views its many spaces—from waiting areas to patient rooms—to see if there are any design needs, especially in highly trafficked areas. “The same products might not last the same amount of time because of wear and tear from patients and such,” Tyson says.
The clinic uses its own system to evaluate flooring, furniture, and even the walls, but they strive to use materials and furniture that are highly durable. “We try to get the right quality materials because we don’t want to go in there every two years and keep replacing things.”
Designing products to last is a key part of the mission at American Biltrite, a more
ABPURE Infinity is occupancy-ready, with no initial set-up needed.
than century-old manufacturer innovating in commercial flooring and performance sheet rubber products. Take their ABPURE Infinity Collection, for example, which launched in 2023. The cradle-to-gate, carbon neutral rubber sheet flooring is made with renewable natural gas (RNG) from 100% organic waste. “It’s an occupancy-ready rubber floor. A lot of rubber floor needs to be finished after installation, but not in our case,” says Catherine del Vecchio, vice president of marketing at American Biltrite.
The Red List–free rubber flooring is low maintenance, easy to clean and disinfect, and you never have to wax it, thanks to its innovative Nfuse technology. The patented product treatment technology doesn’t just coat the product but penetrates and seals the rubber flooring, extending its life with supe-
ABPURE Infinity is 3-millimeter rubber sheet flooring with tone-on-tone chip visual. The Infinity palette features foundational base colors from light to dark within hue families to create harmonious tonal combinations. The line has a large selection of foundational grays and beiges, environmental blues and greens, and uplifting accent colors.
“We take a hard look at all of our suppliers and what our materials are made from.”
rior resistance to rolling loads and eliminating the need for stripping, sealing, or waxing after installation and beyond. It’s also highly flexible and easy to weld and cove to the walls, as it will not whiten, crack, or break.
ABPURE also won’t experience any tarnishing effect when you clean it—a result of extensive R&D during the pandemic, when American Biltrite applied the ASTM F925 testing method, using various disinfectants on different types of rubber flooring. The patented ABPURE Nfuse was the only rubber flooring that did not show signs of loss of luster nor tarnishing, while other SBR rubber floors did. “This exercise proved to us that our ABPURE rubber floors are different than others. It is much easier to clean and disinfect,” Del Vecchio says. “We now know why some SBR rubber floors seem to be hard to clean; it’s because of a reaction from the most commonly used disinfecting agent on SBR rubber floors. ABPURE patented rubber formula provides unique properties, pure colors that last, and is easy to clean and disinfect.”
ABPURE Infinity is manufactured with renewable natural gas derived from organic waste from industrial, commercial, agricultural, and even residential activities. The new energy source is produced locally by collecting this waste and, instead of letting it go to a landfill where it would release greenhouse gas, it is transported to biomethanation farms, where it’s fermented and purified to generate renewable natural gas. “We use the full amount of RNG made from 100% organic waste to offset ABPURE’s cradle-to-gate carbon footprint, as measured in our Environmental Product Declaration.”
Acoustics and ergonomics are added benefits of this and American Biltrite’s other rubber flooring solutions, as rubber flooring both controls sound and is more comfortable for staff on their feet all day. “You want the least amount of disruption for the patient, so having a line that has all the ergonomic properties of rubber flooring is really beneficial for a facility and for the pa-
The flooring has a nature-influenced color palette.
tient,” Del Vecchio says. Not having to wax it also reduces the amount of disruption in a health care facility.
The colors for the Infinity collection were inspired by nature—from the clear blue lake feeling of Expanse Blue to the mossy hue of the Eco Greens. Designers can choose from an intentional, biophilic color palette that sits nicely alongside classic neutrals—all part of 20 total colors. “These colors are very natural looking. They’re soothing,” says Lora Di Fabio, American Biltrite’s product designer and Color Marketing Group board member. She says blue is becoming even more popular in design in recent years, surpassing the much beloved greens. “I met with some designers a couple of weeks ago, and they are all specifying blue for some reason,” she says.
Beyond foundational colors like grays, whites, and beiges, design teams can also choose from chromatic colors—or what American Biltrite calls their “new neutrals” and organic-feeling accent colors. A bright trio of colors called Jovial are another great option and a good fit for pediatrics or therapeutic areas. No matter the color, the choic-
es come across as comforting, Di Fabio says.
American Biltrite also has an in-house color lab to create custom colors for customers. “The minimum requirement for custom colors is only 2,500 square feet, so a big part of my time is working with our color lab on custom colors for projects,” she says.
While SBR-based rubber flooring may fade over time, perhaps impacting the overall look of a space, that doesn’t happen with the patented ABPURE, Di Fabio says. “That’s a huge advantage of our ABPURE. The colors will last.” ABPURE Infinity comes with a 10year color fastness warranty.
American Biltrite, too, isn’t going anywhere anytime soon. “We’ve manufactured rubber since 1903, and we’re here in North America,” Del Vecchio says, noting that much of the rubber sheet used in health care systems is imported from Europe. “We manufacture here, and we hold more patents than the other players.” Even during the pandemic, considering supply chain issues all over the globe, American Biltrite was able to stay in operations in North America.
“People could really count on us. We’ve been through the Spanish flu, two world wars, and some difficult economic times, and we keep going. We’re just a phone call or truckload away.” g
When a hurricane hit Mississippi a few years ago, all the homes in one area were flattened except the Blue House with its blue metal roof. It’s a testament to the durability of their products, says Kenneth Holler of Petersen, manufacturer of PACCLAD architectural metals.
Holler says some architects are primarily concerned with performance, while others are all about aesthetics, but the right metal cladding accomplishes both. “What has become common is the uncommon,” he says.
Modern clients want buildings with unique facades. That’s why Petersen’s PAC-CLAD product line includes an extensive offering of wall and roof cladding systems, perimeter and edge products, and custom fabrication services. Their wall panels alone come in more than 45 standard colors, multiple wood grains, and custom finishes.
Part of Holler’s job is to work with designers, structural engineers, and contractors to help them choose the right cladding for their project. For example, when the Perkins Eastman team was designing the International Magnet School for Global Citizenship in South Windsor, Connecticut, metal roofs were the obvious choice from the beginning. “There are a lot of barns in the area, and many of them have standing seam metal roofs, and zoning requirements stipulated that any portion of the building that faced a major street must have a pitched roof,” says Joseph Culotta, project architect at Perkins Eastman.
In that design, four adjoining structures were laid out in a “village” configuration, with a circular media center acting as the hub of the school. Aluminum Snap-Clad panels were segmented to create the roof of the media center and each of the other four structures. The design team chose Hartford Green and Dark Bronze finishes to reference the local area and complement the brick and concrete masonry facade.
Perkins Eastman often turns to metal panels to help make projects more sustainable. They also designed the John Lewis Elementary School in Washington, D.C.; it’s reported to be the world’s first net-zero, LEED Platinum, and WELL-certified public school. “Material selection was based on delivering the highest performance space for the kids,” says Nicholas Leahy, co-CEO and executive director at Perkins Eastman.
Light color metal panels were used on the facade of this project to blend in with the surrounding residential neighborhood. The insulated metal panels also eliminated the need for an air barrier system.
Truly efficient buildings often have strong exterior insulation, according to Holler. “The building envelope has evolved, and we’ve been evolving along with that envelope,” he says. “Metal has become a very popular cladding product because of that evolution.”
Holler continues, “We’re now moving insulation to the outside of the building. The wall panel becomes part of the whole rainscreen system. We’re using it to get better efficiency, better sustainability, and better energy performance.” It can also reduce the risk of mold growth.
Above: The International Magnet School for Global Citizenship in Connecticut was designed by Perkins Eastman and roofed with Petersen Aluminum’s 16-inch SnapClad metal panels, segmented to create the radius.
Left: The design of the Altgeld Gardens public housing complex in Chicago included metal wall panels in a custom Dynamic Blue finish.
The John Lewis Elementary School was designed for net-zero energy and “netpositive”education.
is often chosen by architects for its longevity and cost efficiency.
Leahy says technology is changing the way the industry works with metal. With the introduction of Boolean geometry to computer programs like Rhino, architects can create any form, and with the advancement of technology like CNC machines, manufacturers can customize far beyond the more expected standard offerings.
Perkins Eastman recently worked on a very expressive design themed around a “moonrise” for a Symphony Hall in China. The roof was first sculpted using software, and then Rhino and parametric modeling were used to determine the panelization and connections. Zinc panels were chosen for their longevity and sustainability. The panels were overlaid to look like reptile skin, a nod to the dragon in Chinese culture.
Petersen also takes advantage of technological advancements to create more custom solutions for clients. Play was at the center of the KOO Architecture–designed Altgeld Family Resource Center, for example. Located in Altgeld Gardens, a Chicago public housing complex that was once a dumping ground for toxic waste, the new resource center includes a library, childcare center, and community meeting rooms.
In contrast to the mostly boxy buildings of its surroundings, the resource center is a continuous curved ribbon, with no distinct front or back. The outside facade is made with masonry to echo the brick used in the development, but KOO opted to use blue metal wall panels for the interior courtyard.
With its compelling curves and angles and custom cutouts, installers from Progressive Dynamics handmade many of the panels from PAC-CLAD coil. The blue wall panels contribute to creating a separate protected space in the courtyard, where children are free to play. Part of the blue metal walls and roof peak above the masonry, for bits of whimsy seen from the outside.
Holler says no matter how trends evolve, beauty and performance are always top priorities for Petersen. “Our products contribute to beautiful buildings that are functional and sustainable because beautiful buildings get maintained.” g
Below: Millennium High School uses metal wall panels for its exterior facades to capture the school spirit.
Innovative HVLS fans support air movement that is effective, comfortable, and energy-efficient.
By Jim SchneiderIIn the quest to combat climate change, the building industry has increasingly put a great deal of focus on things like energy, building performance, resource conservation, and embodied carbon. But often design demands can distract from what’s perhaps most important— the people inside the buildings.
“Now more than ever, as we continue to weather and learn from conjoined public health, economic, social justice, and environmental crises, it has become increasingly apparent that we need to acknowledge the interrelationships between the wellness of people and the wellness of our planet,” says Heather Jauregui, director of sustainability and associate principal at Perkins Eastman in Pittsburgh. “Each of these has been influenced by the others, and the impact of climate change on all these crises cannot be overlooked. We cannot tackle these crises individually. We need to address all of them.”
It’s estimated that people spend about 90% of their lives indoors, and indoor air pollution is responsible for approximately 3.8 million deaths each year, according to the World Health Organization. Better airflow has a number of benefits. “Numerous studies have shown that improved air movement and circulation contribute to better indoor air quality and occupant wellness,” says Dan Tolles, HVLS product manager at Wisconsin-based Greenheck, a manufacturer of air movement, air control, air
conditioning, and air distribution equipment. The company’s products are used in many types of buildings—including hospitals, office buildings, hotels, shopping malls, restaurants, schools, and industrial facilities.
“Research also indicates that occupant perception of indoor air quality and building comfort are heavily influenced by air movement. People tend to correlate increased airflow with better indoor air quality, and they generally report higher satisfaction with environmental comfort when they can feel air moving. In other words, humans tend to associate a breeze with fresh, outside air,” Tolles says. “How occupants perceive the comfort of an indoor environment can often be overlooked, but it’s another critical piece of high-performance building design.”
Perception and performance are both essential goals. Air needs to move and be kept fresh in a manner that both preserves energy and offers comfort and assurance to occupants. An effective way to create optimum air movement is by using high-volume, low-speed (HVLS) fans. These are large-diameter, ceiling mounted axial fans that are meticulously designed to move large volumes of air at low speeds, utilizing minimal energy. Ideal in large, open spaces and originally designed for places like barns, warehouses, and manufacturing facilities, HVLS fans today are proving to be a powerful tool in many building types.
Overhead HVLS fans provide energy-efficient air circulation and evaporative cooling in commercial and industrial spaces.
Below: DS-3 is a powerful, lightweight, budget-friendly overhead fan designed to boost air comfort with less noise.
Numerous studies have shown that improved air movement and circulation contribute to better indoor air quality and occupant wellness.
“Over the last 10 to 15 years we’ve seen a pretty dramatic increase in design professionals utilizing HVLS fans for commercial and institutional applications,” Tolles says. “Fans are being incorporated in a variety of building types like schools, retail stores, and fitness facilities because they’re an efficient way to provide elevated comfort in large spaces.”
Large, open indoor areas are traditionally very energy-intensive to heat and cool by utilizing standard HVAC and air movement methods alone. Adding an HVLS fan to the mix not only helps keep air moving in a healthy and comfortable manner, it can also contribute to significant energy savings.
“HVLS fans can counteract thermal stratification to both save on heating/ cooling demands and create more comfortable environments through air movement,” Jauregui says. “By helping shift heat down to the occupant level during the winter and creating a light breeze in the summer to shift the perceived comfort zone, these fans can significantly save on energy demand for heating and cooling needs, particularly in larger spaces like gymnasiums.”
Utilizing little energy themselves, HVLS fans supplement building ventilation, so those systems don’t have to work as hard and expend as much energy. From blades to motors, the fans are thoughtfully designed for efficiency and airflow far superior to standard ceiling fans.
“To put it in perspective, most traditional ceiling fans provide airflow between 3,000 and 6,000 CFM. A single HVLS fan can provide airflow up to 250,000 CFM,” Tolles says. “Combine that level of air movement with high efficiency motor technology and the end result is an extremely efficient and effective product. For example, Greenheck uses a direct drive motor platform on our HVLS fans that consumes less than $1 per day in energy on average.”
In a truly holistic sustainable design, designers try to achieve multiple goals simultaneously. “It’s about wellness of people and wellness of the planet,” Jauregui says. “We like to zoom into design strategies that impact both sides of that equation. We focus on daylight, thermal comfort, acoustics, and air quality in our design process. Some of those are easy. For example, with daylighting, the better the natural light the less need you have for electric lighting, so the more energy you save. Others are more challenging. Better air quality can require increased ventilation as a strategy, which can increase energy. It’s about finding the right balance to get the best indoor air quality as efficiently as possible.”
Energy efficiency, building performance, health, and comfort may at times seem like opposing goals, but there are ways to bring them all together. HVLS fans may be one of them, as Greenheck says they’re an effective, low-energy way to support multiple objectives in a sustainable project.
“There is a misconception of HVLS fans being exclusively an agricultural or industrial product, but we believe every building on Earth could realize a benefit from using them,” Tolles says. “It’s not a one-size-fits-all technology, and there are different variations of fans for different purposes. Whether a building requires increased airflow to improve comfort or a means to reduce energy consumption, there’s an HVLS product to suit that need. At the end of the day, HVLS fans are designed to augment the rest of an HVAC system to deliver better building performance.” g
Acoustic lighting tiptoes into the spotlight.
By Rachel MullisWWalking into the King Abdulaziz Center for World Culture exhibition hall in Saudi Arabia is more like being outside on a starry night—if the sky were made of copper. The lustrous paneling rises organically from the room’s edges to a crest of 13 meters, studded with thousands of tiny holes that let light gleam through.
The panels envelop a vast, open room that features world-class exhibitions like Leonardo da Vinci’s manuscripts and Edvard Munch’s paintings. However, designing the space posed a particular challenge for Snøhetta, a global architectural firm based in Norway.
While other buildings in the center include structural elements like stairs and balconies, the exhibition hall is bare, and its surfaces are hard and smooth. Without acoustic insulation, voices would reverberate around the hall as echoes, causing an unpleasant auditory experience.
To ensure the hall’s acoustic aesthetics matched its stunning visuals, Snøhetta concealed lighting and sound-absorbing insulation materials behind the copper panels. The innovation was an early example of acoustic lighting, a growing trend in the design industry that integrates illumination, acoustic performance, and aesthetics in one cohesive design.
Traditionally designers and engineers purchased acoustic panels and lighting fixtures separately, hiding acoustics behind ceiling tiles and wall partitions. But as more buildings embrace open floor plans, the mixture of acoustic baffles and lighting fixtures in ceilings can look mismatched and cluttered.
In other cases designers compromise lighting quality or acoustic performance. The result is unhappy occupants. “We’re trending toward open landscapes, and with that comes a lot more sound and noise,” says Bjørg Aabø, a senior interior architect at Snøhetta who worked on the King Abdulaziz Center project. “So we need different means to reduce the noise impact.”
As the trend takes off, Canadian company Cooledge Lighting has unveiled a line of acoustic lighting solutions that combines lighting and acoustic performance in the same product. The company sees huge potential in deploying the technology in open offices and other large spaces.
“If you look at studies of complaints about offices and public spaces, lighting and noise are usually in the top five, if not the top three,” says Grant Harlow, the company’s vice president of marketing and communications.
The need for solutions that address poor lighting and noise control issues has grown post-pandemic, especially for companies seeking to attract workers back to the office. The design industry is increasingly focused on designing public spaces and offices for wellness.
Acoustic lighting reduces ambient noise, allowing small groups of people to hear each other more clearly and feel like their conversations are more private even in a large open space. Meanwhile, the space is well-lit and the overall visual aesthetic remains bright and modern.
This 65,000-square-foot library in Saudia
part of the impressive King
Center for World
features 134 illuminated panels of various sizes used to highlight the bookshelves.
Harlow says the shift toward wellness means lighting and noise control designs are ripe for new approaches and technologies. Cooledge’s large-scale acoustic lighting luminaires and stretch ceilings incorporate a clean design with plenty of lighting surface area to absorb sound. The technology is a step up from acoustic lighting products that simply wrap pendants in felt or other sound-absorbing materials. While these solutions may work for small dining rooms or offices, they won’t do much in a large, noisy space.
But that doesn’t mean designers should shy away from using more robust acoustic lighting solutions in smaller spaces. Aabø says Snøhetta recently incorporated another acoustic lighting project to redesign the Oslo Opera House’s tiny gift shop. They strove to maintain the visual language they’d used in the overall building design, opting for a sound-absorbing stretch ceiling used in other spaces, but this time with a back-lit function. The effect is bright but tranquil. “It’s not a big shop,” she says. “But it’s an excellent way of keeping the noise down while taking care of the lighting and making the little space feel more intimate.”
To set the stage for optimal sound performance in any space, Harlow says designers should pay attention to sabin values, which evaluate a luminaire’s sound absorption (measured by its noise reduction coefficient, or NRC) against its size. To explain the value of sabin, he likes to use the analogy of paper towels. “No matter how good your paper towel is, you can only soak up so much water with one,” he says. “If you have a whole roll of paper towels, you can soak up much more.”
In other words, designers and engineers should account for the total surface area of acoustic lighting rather than individual fixtures’ NRC value. In most cases they should also aim to target acoustic frequencies in the range of human speech—about 100Hz to 4000Hz.
The benefits of acoustic lighting go beyond aesthetics and performance. In many cases the technology can also yield cost savings. After all, buying one product that does two things eliminates the need to buy two separate products.
Aabø agrees. “When the design has more than one function, it’s always a great thing.” g
“When the design has more than one function, it’s always a great thing.”
How insulated metal panels are pushing the green building industry forward
BY ANDY CARLOKingspan’s primary customers are in the industrial sector—think mammoth warehouses, distribution centers, and production facilities.
SSustainability has long been the focus of Kingspan Insulated Panels, a leading manufacturer of insulated metal panels and innovative facade solutions. “Given that we are an insulation manufacturer, energy efficiency has always been a driver for us,” says Brent Trenga, director of sustainability for Kingspan Insulated Panels, North America.
Kingspan Insulated Panels is part of the larger Kingspan global business, which also includes Insulation; Data + Flooring; Light, Air + Water; and Roofing + Waterproofing. As part of Kingspan’s Planet Passionate sustainability initiative, the building products producer aims to achieve net-zero carbon in its manufacturing operations and is committed to a 90% reduction in scope 1 and 2 greenhouse gas (GHG) emissions by 2030. The program is a massive undertaking when considering the size of Kingspan, which operates across 80 countries with more than 22,500 employees.
The company reduced emissions of its Ireland headquarters by 40% in 2023 compared to the previous year. Kingspan’s forklift fleet is 40% electric, and last year the company invested nearly $62 million in research and development—to name just a few of the visible examples of its commitment to sustainability. “It’s about us leaving the people and planet a better place than we found it,” Trenga says.
Trenga says infrastructure construction continues to drive sales at Kingspan, which is also a second generation family-run business. This includes massive data centers, automotive plants, and auto electric battery manufacturing facilities. Kingspan’s insulated panel customers include some of the biggest companies out there—like Tesla, Ford, General Motors, Google, and LG.
CannonDesign has worked with Kingspan on a number of projects, including data cen-
ters and industrial buildings. “Then we realized these systems can be used for all types of buildings,” says Eric Corey Freed, director of sustainability at CannonDesign.
The architecture firm with offices all over the US has also worked with Kingspan on institutional, commercial, health care, and university projects. “It’s a higher performing envelope and gives us a pathway toward net zero energy for a high-performance building,” Freed says.
Insulated metal panels, or IMPs, helped a medical center renovation at the University of Cincinnati go more quickly when CannonDesign chose them as the building envelope for the expansion. The project was completed in December 2022. Quick installation of IMPs provided a weathertight envelope in reduced time, drying in the emergency room faster and allowing for inside finish work to begin
sooner, according to Kingspan. “Creating a nice tight envelope—insulated metal panels give me an opportunity to do that,” Freed says.
In general he says working with clients like these—from Kingspan to the University of Cincinnati—is exciting. “We get to use work with the most amazing clients who are looking to solve emission problems in health care, education, and science.”
He says continued innovations in the industry have also improved with regard to the life cycle cost of buildings and more durable solutions, as most see the value of building projects that won’t soon be torn down. “What we are really building are 100-year buildings.” Kingspan’s IMPs offer another step toward building better, longer-lasting projects. And that’s important, considering about half of carbon emissions come from the design and construction of the building.
Planet Passionate is a 10-year sustainable program focused on climate change, circularity, and protecting the natural world. Kingspan is committed to reducing its manufacturing carbon emissions to as close to zero as technically possible, together with halving carbon intensity in their primary supply chain.
Kingspan’s Planet Passionate initiative means accelerating net zero emissions. The company formally set sustainability targets in 2011, achieved its initial net zero goals, and then released the Planet Passionate plan in 2020.
“We have made incredible progress against every target we have set,” Trenga says. “We knew it was a challenge, and we are excited about the challenge and the opportunity.”
Kingspan’s insulated panels continue to help the company achieve its Planet Passionate goals. Manufactured offsite, the panels are a single component providing cost savings and thermal value while being produced with high recycled content. Because they are constructed in a controlled environment, IMPs are produced with little waste. Ease of installation on the job site also cuts down on time and provides labor savings.
Trenga says both the foam and steel used in the panels are low carbon materials that can be taken back and recycled for end-of-life solutions. “The panels are manufactured with a target of zero waste heading to a landfill.”
When it comes to the building envelope, the panels provide the proper air, thermal, water, and vapor barriers for structures, Trenga says. IMPs are available as wall systems, roof systems, and cladding accessories and components. And Kingspan’s QuadCore ® Technology offers one of the most thermally efficient insulation cores on the market. This next generation of self-blended hybrid insulation has cores available in a range of thickness widths, with superior fire protection, health and wellness certifications, and a 30-year thermal warranty. “We continue to improve the products we manufacture and bring to market,” Trenga says.
Kingspan’s BENCHMARK Architectural Wall Panels also provide superior thermal properties as well as offer up a wealth of aesthetic capabilities with more styles and colors for creative freedom. These architectural insulated wall panels are exterior wall panels with steel skins and feature an insulating foam core.
Kingspan has set the bar high with its own facilities, too. Ultimately they not only measure the performance and targets of their own products and operations but also what each product is made with, how materials are sourced, and what happens after production. Many of its plants use renewable power onsite, and every site has a “zero waste to landfill” goal. Trenga says they hold themselves accountable while continuing to push others in the industry. “It’s not just about construction products. It’s how everyone runs their business.” g
How 10 architects across North America are redefining justice in the built environment
ILLUSTRATION BY MADISON WISSE
SHE DOESN’T LIKE TO SAY IT, BUT TECHNICALLY IT’S true. She’s been a leader for more than 30 years. She laughs because, well, she’s 40. But even as a kid her peers turned to her when someone needed to step up. They’d say, “Kim, you should be the leader.”
“My first presidency was when I was 7. I was president of the Youth Usher Board at my church.” Big changes were made almost immediately. “I didn’t like the uniforms,” she laughs. “I worked closely with my grandmother and others to get that done. It was an early win to prove they made the right decision.”
But in all seriousness, Kimberly Dowdell has been making tremendous strides in an effort to make the world a better place since the start of her career or earlier. Today she serves as president of the American Institute of Architects (AIA) while continuing her busy role as the director of strategic relationships at HOK, a global design firm. She’s also past president of the National Organization of Minority Architects (NOMA)—essentially a six year-commitment that ended in 2022.
She remembers when her mentor suggested the NOMA role, driving from Chicago to meet her in Detroit (she splits time between the two cities as much as possible) to float the idea at a restaurant. “We order our food, and he’s like, ‘Kim, it’s time for you to be NOMA’s president.’” She was taken aback. She was 33 at the time, but she’d been involved with the organization since she was a student, including working as a university liaison.
It was a fulfilling experience, though challenging. She was considering taking a break from such active leadership roles when then she got a call from a past AIA president with a similar message—that she should run for president.
“I was so exhausted from these past six years, part of which was the pandemic, but I was really proud of the work I did with NOMA. We nearly tripled our membership from 900 to nearly 3,000 in a two-year window and created or enhanced a lot of impactful programs. We raised over $1 million to fund our programs and hire full-time staff for the first time. Because of the momentum that had been built with NOMA, I felt some level of confidence that I could be successful in the AIA election and continue some of the efforts I began with NOMA, specifically around racial, ethnic, and gender equity. Granted, AIA is a much larger organization, but I still felt like I had something unique to contribute there.”
Today she serves as AIA’s first Black, woman president and the organization’s 100th elected leader; it’s a one-year team she hopes shows movement to a more inclusive and equitable profession. “AIA was founded in 1857, and we know that probably wasn’t a great year to be a Black person, or a woman, and certainly not a Black woman,” she says. “We
“ I FEEL LIKE I’M DOING WHAT I’M SUPPOSED TO DO .
are hoping to secure a stronger future for everyone in the profession of architecture, no matter what they look like.”
Dowdell’s mantra for her AIA presidency has been “more in ’24” and is divided into three pillars—more money, more members, more mission. “I want architects to make more money because we provide a tremendous amount of value that isn’t necessarily seen,” she says.
Architects often come out of school with debt, while starting salaries tend to be in the $50 to $60,000 range. “Because of that we lose a lot of young talent,” Dowdell says. “We’re really trying to think about talent, attraction, and retention. We have to make sure young people are seeing this as a viable profession. It is very rewarding in a lot of ways, but we have to make sure the financial piece is there. If we want to have a more equitable profession, we also have to make sure you’re not just coming from a background of privilege.” It takes many in the profession five to seven years of education to pursue licensure. On average it is reported to take more than 13 years to become a licensed architect, factoring in education, required work experience, and examinations. That’s a lot of time that could be spent making money in other roles, for example, like working for construction companies or as project managers in an engineering company. “Almost all the other companies in the built environment are more profitable,” she says.
Dowdell says she is lucky to come from very humble beginnings in Detroit because it allowed her to get a lot of scholarships. “I was a smart, articulate little kid who was like, ‘I want to be an architect to save the world.’” Between scholarships, financial
From top: The firm is also committed to designing transit projects for equity, like this rendering showing 9th Street in Brooklyn. The Hamad International Airport in Doha was one of the first HOK projects worked on. The Cortex Innovation Center in St. Louis is a recent example of adaptive reuse by HOK that Dowdell is proud of.
“ARCHITECTS
BUT WE’RE NOT OFTEN UTILIZED IN THAT WAY.”
aid, and church assistance, she came out of school with no loans. “But I also started out with $0,” she says.
The middle class doesn’t have the same support, she says, in terms of scholarship and financial assistance, as many people expect them to be able to “pay something” and “figure it out.” And school today is even more expensive, from tuition to supplies to the simple cost of living. “You have to come from a background of privilege or be very lucky. Most people are not in that spot,” she says.
Until about age 11 Dowdell thought she wanted to be a doctor when she grew up. She had a change of heart when, as a kid in the ’90s in Detroit, she was fascinated by the old Hudson’s department store downtown. “It closed the year I was born.” The place where her family used to go for photos with Santa sat empty. “It took up a full city block, but when I experienced it—never on the inside— it was psychologically draining.”
At the time Detroit was experiencing a lot of disinvestment as people moved out of the city and more buildings became vacant, leading to more crime and just an overall not great situation, she says. “In a middle school art class I learned about what an architect did, and I somehow made this connection between architecture, buildings, and the health of the city,” she recalls. The 11-year-old Dowdell thought, “If I become an architect I can fix this building, and then that could heal the community.”
While she grew up to learn that’s not quite how things work, it also contributed to her love of green building and adaptive reuse. “The most sustainable building is the one that already exists,” she says. Sadly that building from her childhood was demolished, but the site will soon be home to Hudson’s Detroit—a 1.5-million-square-foot mixeduse development that is expected to house offices, retail, a hotel, rooftop bar, condos, and more. General Motors recently named the site as its new global headquarters. The project is designed by SHoP with many local design contributors.
One of Dowdell’s earliest successes was the SEED Network, an idea she and fellow architects, designers, and leaders developed in 2005. Dowdell created the initial idea while sitting at her desk at the US General Services Administration in the Office of the Chief Architect, where she was an intern. Her supervisor and mentor Steve Lewis soon shared the idea at a program hosted by Harvard Graduate School of Design, which resulted in a larger movement toward a network of like-minded professionals. “LEED was becoming popular, and I was like, ‘That’s great, but we need something for the social issues.’” The community-based design network has a mission to advance the right of every person to live in a socially, economically, and environmentally healthy community.
Considering the impact on people as part of every project is part of the HOK ethos. “We design the places that make cities work,” Dowdell says, echoing Peter Ruggiero, design principal for HOK’s Chicago studio. “We’re probably most known for our sports stadiums and airports, and those are part of the inner workings of the city, but we’re also preserving existing buildings. Our work is driven by what our clients ask us to do, but we’re excited to really support the mission of our clients in service to the broader communities we serve.”
One reason she joined HOK initially, back in 2008 when she worked in their New York office, was because it felt like a place where she could grow. “I really appreciated their approach to sustainable design, which at that point wasn’t yet a buzzword. I have on my bookshelf the HOK Guidebook to Sustainable Design, published in 2000. That signaled to me that the firm was doing things that maybe other firms were not.”
But in thinking about designing for equity, it’s not just about what a project gives a person or community, but it’s also considering what might be lost. “You have to find ways to minimize those impacts, and you have to have conversations to understand what those potentially negative impacts are,” Dowdell says. “A big component of design for equity is actually listening to the communities that are impacted by work and really taking stakeholder engagement seriously, thinking critically about who those stakeholders are, and how this project, whatever size or scale it is, impacts their work, their lives, how they play, their health outcomes, everything. That’s important.”
With the year flying by, Dowdell zeroed in early on what she hoped would be part of her legacy at AIA. It’s called the Chief Architect Initiative, or the idea of cities having chief architects.
“Architects are the civic problem solvers. We have all of this high-level training and technical expertise and the ability to leverage design thinking to solve complex problems, but we’re not often utilized in that way,” she says. “Let’s think about the city as a client. Having a chief architect in place to be a key advisor to mayors on issues around climate action, affordable housing, adaptive reuse, or blight—these are some of the things many cities deal with that having that unique perspective to weigh in on could be really valuable.”
She envisions a network of architects that not only support their individual cities but also work together to compare what they’re seeing and share resources. “I’d love to find a philanthropic source to fund and maybe pilot a few cities to fund a chief architect for a number of years. I think that would be a huge success.” g
“PIP” LEWIS GREW UP IN DETROIT, AND between his home city, visits to relatives in Chicago, and weekend trips to Toronto, by junior high he’d developed a strong interest in the built environment.
“We went to Expo 67, and I saw the fantastic pavilions that were there—the Russian pavilion, Moshe Safdie’s Habitat,” Lewis says. “I got really excited about architecture and design.” At Detroit’s Cass Technical High School, he took advantage of the school’s architecture curriculum, taking classes in drafting and construction.
After completing his master’s degree at MIT in 1981, Lewis was hired as “a junior drafter” at Cambridge’s HMFH Architects. He’s now a principal at the firm, where he’s spent his entire 42-year career. “It’s a very good, comfortable, family-like organization to be in,” he says. “That’s why myself and actually a lot of people have been there for a number of years.”
Part of what makes HMFH’s practice rewarding for Lewis is its focus on designing public and charter schools around New England. “I’ve always said I’m so glad I do schools, rather than luxury condominiums or shopping centers or something like that,” he says. “You always have to go and engage with the community you’re going to build a project in. And it’s so nice engaging with the community to build a school, because in general the communities want the school. It’s not like when they’re out to stop the strip mall that’s going to get built.”
With many stakeholders, not to mention the vagaries of local politics, school projects can take years to come to fruition. One of HMFH’s latest projects is the Josiah Quincy Upper School in Boston’s Chinatown neighborhood. It’s the first permanent home for the school, which was established as a pilot program in 1997 and serves a diverse population. “The school is something like 94% minority,” says Lewis, who’s been attached to the project since 2011; it’s on track to open for the 2024–25 school year.
“We went through four mayors and something like six superintendents of schools to get this project up and running,” Lewis says. Massachusetts’ complicated funding formulas for school construction were a factor, but finding the right site was also a challenge. “We looked at 40 different sites over the years. We had three different false starts where we did a whole schematic design package: traffic studies, zoning issues, hundreds of pages of documents,” only to fall through for various reasons.
“I saw it as an injustice going on, that this minority school was promised something years ago and wasn’t really getting it,” Lewis says. “You found you really had to be an advocate for the school. You had to push.”
The eventual location for the new JQUS facility is on “a tiny site” surrounded by of-
On a limited 0.9acre lot less than a mile from Boston City Hall, the new Josiah Quincy Upper School design responds to its urban site constraints with a dynamic rooftop designed as an accessible outdoor space for learning, gathering, and activity.
fice towers. “It’s less than an acre, an impossibly small site to build a high school on.” It’s also right next to the Massachusetts Turnpike. “Communities of color are always located in the areas that have the worst air quality, and this was no exception.”
By building up seven stories, Lewis and his colleagues were able to incorporate amenities JQUS had previously been missing—including a library, science labs, and a full-size gymnasium—while also addressing environmental challenges. “We’re going to bring fresh air in from as far away from the traffic as we could,” Lewis says. “All the classroom spaces in the building get their air from above the rooftop, facing away from the source of the pollutants,” before passing through MERV 14 filters.
While the school’s small footprint left no room for ground-level outdoor space, HMFH advocated for an 18,000-square-foot openair garden on the building’s rooftop. “It’s an educational space, an informal socializing space, and also a therapeutic space when kids are in crisis,” Lewis says.
For the JQUS project, one of Lewis’s most anticipated moments will come when the school opens this fall: seeing students encounter “this wonderful new environment, and just seeing the joy and awe in their faces— that’s always been the most rewarding thing.”
“I SAW IT AS AN INJUSTICE GOING ON, THAT THIS MINORITY SCHOOL WAS PROMISED SOMETHING YEARS AGO AND WASN’T REALLY GETTING IT.”
LINDSEY WIKSTROM HAS TAUGHT AT COLUMBIA AND Yale, worked with Studio Gang, written an acclaimed book about mass timber, and founded her own firm, Mattaforma, in the midst of a pandemic.
“One of the best pieces of advice I got was if I don’t bet on myself how can I expect other people to bet on me?” she says, recalling conversations with friends and colleagues further along in their careers. In 2021 she took the leap. At the time Wikstrom was working with one of her mentors, David Benjamin, after he recruited her from Studio Gang to be the project architect for a new engine factory for Airbus in Hamburg. But when Covid hit, talk of innovations in the airline industry faded, and she decided it was time to try something new.
Wikstrom continues to be inspired by the mentors in her life—people like Benjamin, whose work largely focuses on biogenic materials; he founded The Living, a design studio and experiment in living architecture; and Hilary Sample, cofounder of Mos Architects; and Mabel Wilson, who co-directs the Global Africa Lab. “She’s leading the charge when it comes to understanding who built the built environment today. It’s mostly on the backs of enslaved peoples.”
These multi-talented influences have in part led her to focus her own work on materials, equity, and, she says hesitantly, sustainability. “Recently I’ve been trying to steer people away from that word and using more specific language, like enhancing biodiversity or improving the health of workers—being clear about what we’re working on. It’s always been about this sense of resources and thinking about who gets access to those resources,” she says.
While teaching architecture at Yale Wikstrom asked students to consider where materials come from. She says it’s critical for people in the industry to understand the materials used in everyday situations and not just accept “the norm.” “Many modern materials are unhealthy for you and others,” she says.
Mattaforma recently designed a classroom inside a public school for young adults on the autism spectrum in Queens. In that project the design team helped the client move away from luxury vinyl tile (LVT) to a vinyl flooring material that is Greenguard-certified with extremely low VOC emissions as well as being commercial grade. But it took some convincing, as some assumed LVT is a common practice in schools because of its durability and cost effectiveness. That may be true, but she says that doesn’t mean it’s not dangerous. “We need to constantly question the status quo when we’re designing, for example, with luxury vinyl tile or quartzite. If we say, ‘LVT is the typical material in schools, and we don’t vet that assumption, that’s on us. We would be contributing to the dam-
BY LAURA ROTE“It takes a level of care to question the status quo. That’s not intuitive for everyone,” says Lindsey Wikstrom, founder of Mattaforma.
aging of bodies for years to come, especially young and vulnerable people as well as the folks who manufacture materials, and the environment.”
LVT is known to emit toxins called phthalates, which are known to be cancer-causing and can lead to developmental delays and other issues, Wikstrom says. “Phthalates are released largely in the manufacturing process but also offgas after installation, which is why they are prohibited in children’s toys, but somehow they’re still used in the flooring of children’s schools. Ideally schools integrate natural material alternatives into their design guidelines, like flooring made from bio-polyurethane composites or vegetable oils, which are just as durable, but also safer.” As for quartzite, she says it is harmful to those cutting, grinding, and polishing it. “Natural stone is a better alternative because when it’s cut during the manufacturing process, it doesn’t release resin dust into the air and lungs of people nearby.”
In spring 2024 Mattaforma was completing their neurodivergent classroom, where students will learn skills like laundry and dishes as part of a class called Adapted Daily Living. The principal wanted an apartment unit in the school so students could immerse in the learning. The finished project has a full ADA kitchen, bedroom setup, and more so students can practice apartment living. “Each wall is painted a different color so it feels like you’re in a different room, and the materials are meant to be domestic, but they are also really durable,” Wikstrom says.
In general Wikstrom hopes for a future with more careful consideration of both individual needs and individual materials. “I think architects can do a better job of listening to the public. We have this habit of being very insular,” she says. “I’ve found the most enjoyable conversations are with people who really care about where their food comes from, for example. Those people, and most of our clients, really identify with this concept of material sourcing not because they’re interested in architecture and materials, but because they care what goes in their body. It’s not an elite architectural theory; it’s very human, and I find that to be so life-giving.”
Mattaforma designed a public classroom in a school for young adults on the autism spectrum.
Below: In the early days Wikstrom’s Mattaforma projects were largely word of mouth. Soon after she started the office she began work on a residential project for a friend of a friend. The Edgewater project was a small renovation and addition with environmentally friendly materials and attention to detail, like a white oak screen in the kitchen handmade by a local millworker.
TATIANA BILBAO DREAMS OF SLEEPING IN A HAMMOCK, in a home where Western ideas of “bathroom” and “bedroom” are turned on their heads. “I really would love to have a bathroom the size of my bedroom and a bedroom the size of my bathroom,” she says. “I’m not kidding; I would like to sleep in like a monk cell—really small—and I would love to have a bathroom so big I could spend hours there.”
The Western notion of the bedroom is so specific, Bilbao says. “That’s a place with a bed. What is a bed? A standard piece of furniture that the West invented for sleeping. There are many people in the world who cannot and do not sleep on these things, you know?” she says. “For example in the Yucatan Penninsula, it’s super humid there, so they sleep in hammocks, which is very practical because you swing at the same time; you get fresh air; and it’s harder for bugs or scorpions or snakes to reach you.”
Bilbao and her namesake studio and team of 55 are based in Mexico City, where she’s been working since founding her practice in 2004. Much of her work focuses on rethinking the way we live, work, and interact, from affordable housing strategies to city planning to large-scale parks, a research center and aquarium, and other public projects. When it comes to equity, she pushes people to think differently.
“How can we create architecture that becomes a platform for anyone to create their own way of living in it?” As it stands, she says every decision an architect or designer makes about a space determines how it can or cannot be used.
Bilbao says modern technologies make it easier than ever to open up the idea of rooms, though. Consider a person who doesn’t want a kitchen. Maybe they are rarely home, they’re single, or they just don’t want a kitchen. “How can you occupy that space that is very valuable today for other uses?” Then, there’s the living room, much explored and reconsidered during the pandemic. “How can we allow more flexibility? We do it by not labeling spaces.”
Currently Bilbao and her team are working on a 150-unit domestic building in Monterrey, Mexico called Roble 700, expected to be complete in 2025. The client emphasized a desire for community, saying that equated to 150 units plus amenities. “We’re like, ‘No, that will not create a community. Booking your hour in the pool or in the yoga room will not create a community,” Bilbao says. “Instead of amenities there are many open spaces around the building to be programmed. There are spaces that can be a living room or a yoga room or a place for children. There’s a terrace with a barbecue. There’s communal kitchen space.” There’s even a guest room occupants can reserve. “If your parents come to visit you don’t need to put them in the living room on the couch. You could put them in this room.”
BY LAURA ROTETHE LIMITING LANGUAGE OF LABELS IN SPACES
All of the common spaces connect to the apartments, and many flexible rooms open up a world of possibility. The complex itself opens to the city via a clustered patio in the center that connects the interior of the building with the urban environment.
Design, again, should be flexible. She goes back to the bed in a room example. That may be how she lives now, having grown up in the Western world, but so often we do things without even thinking about them. “I really don’t understand who decided I needed to share a bed with a person. I really don’t get it, but any built space I can find around me has a double room. How can we understand that not one single person in this world lives the same? And how can architecture allow every single person to live the way they decide to live and not become part of the system that discriminates against those who are not in the standard way of living?”
While it is abundantly clear that people are different, that we inhabit the world differently and have diverse wants and needs on any given day, most buildings are designed for a specific “type” of per -
When it comes to equity, Tatiana Bilbao pushes people to think differently.
“How can we create architecture that becomes a platform for anyone to create their own way of living in it?”
“I BELIEVE ARCHITECTURE PROVIDES A PRIMARY FORM OF CARE TO OUR BODIES. WITHOUT IT WE CANNOT EXIST ON THE PLANET.”
son. “The domestic built environment is designed in the majority of countries today—and the industry supports this, the policy supports this, the code supports this or restricts other forms—for a form of living as a couple with two kids. The majority of the built environment is built for these social configurations,” she says. One room is larger than the others, then depending on a family’s economic situation, there are other rooms. There’s a kitchen, there’s a bathroom, there’s a living space. “But guess what? If you decide to live this way, as a heteronormative couple with two kids, you exist only in that condition for, what, 15 years?” Even with kids, she says, that setup changes, and she should know. She not only leads a busy architecture and design office and travels the world for work; she also has five children. “The children become teenagers, and even though they live with you, that’s a totally different story in terms of space,” she says.
Bilbao hopes architects will continue to open up the ideas of spaces to more possibilities and more types of people. “We don’t as humans inhabit the space the same way every day.”
Thinking of the living unit as the starting point where different social configurations could exist, Tatiana Bilbao Estudio designed Roble 700 not to be divided by its floors and corridors, but instead thought of as a series of spaces that foster the possibility of different types of relationships between neighbors.
“I COULDN’T PUT MY FINGER ON IT, BUT
I KNEW I wanted to see my neighborhood become better,” says Nicolia Robinson. “I wanted it to be a better place; I wanted things to look better, feel better. I wanted our grocery store to come back, all the stuff that disappeared.”
Robinson now lives in the Atlanta area, where she’s the director of urban planning and design at the firm Cooper Carry. But she’s describing growing up in South Florida, where she felt that nagging sense of her neighborhood becoming less livable.
“My first job, I walked from my house to the little pharmacy I worked at; this was in the late ’80s, early ’90s,” Robinson says. “It was very suburban, and it was still difficult to do that, but I could, right? But I saw things changing, and not necessarily for the better.”
Later, while studying architecture at the University of Florida, Robinson took a course in urban design that caught her imagination. “I thought, ‘Whoa, this is really more in line with what I think I’m going to do,’” she says. “Architecture trained our brains to think creatively about finding a solution to a challenge: How do we accommodate people, how do we shelter them? But I became more interested in what really makes a community work.”
One big contributor in Robinson’s estimation is the now-familiar concept of the “third place,” or “the space where you go to be that isn’t work or home, where you feel like you belong.”
That sense of belonging is key: Simply designating a third place doesn’t make it so. “I love when clients are like, ‘Let’s build a third place!’ Like, we can build a great space, but we can’t guarantee it will become your community’s third place,” Robinson says. “I truly believe, in order for it to become that, you have to have a certain level of engagement with the community— they will tell you what they want it to be.”
That approach informed Cooper Carry’s recent renovation of Atlanta’s Fulton County Central Library. The 1980 building, a brutalist design by Marcel Breuer, had a lot of architectural significance, Robinson says. But through a series of listening sessions with library patrons, staff, and other stakeholders, it became clear that “for the library to be better utilized, it needed to be more welcoming.”
That meant opening up the ground floor, allowing in more natural light, and “making the front more of a plaza that’s more connected to Peachtree Street,” along with reorienting interior spaces to match evolving expectations of a library’s purpose—serving not just as a repository for books but as an inviting community hub.
Community input was perhaps even more central to Cooper Carry’s planning work for Legacy Park, a 77-acre development in Decatur,
BY KRIS VIREGeorgia. “We always start the story by saying on a rainy Sunday afternoon, more than 500 people came out to lend their voice,” Robinson says of the initial community meeting, which kicked off a yearlong series of workshops to create a master plan.
Significantly, part of that master plan was empowering the community to implement new features in the park as Decatur’s needs evolve, Robinson says. “We gave them the framework and the tools to let some of it be grassroots.”
In Robinson’s eyes, that thread of self-determination is essential to equitable urban planning. “I have a special fondness for communities that look a little bit like where I grew up, because a lot of the disinvestment that happened was in minority communities,” she says. “And so how could I professionally work to make that young girl walking to work happy again? That’s what gets me going every day.”
Cooper Carry recently renovated Atlanta’s
Community meetings were a vital part of planning for Legacy Park, a 77acre development in Decatur, Georgia.
Fulton County Central Library—a 1980 building with brutalist design by Marcel Breuer.NEW YORK-BASED MARVEL ARCHITECTS BOASTS a diverse portfolio that includes its fair share of commercial projects. But the firm can’t deny that it’s drawn to ventures of a civic nature, says partner Annya RamírezJiménez, who’s been at Marvel since 2016.
“We don’t say no to anything. Architects, we’re always trying to find the opportunity in everything—small, big, what’s the potential?” Ramírez-Jiménez says. “But our civic work has created some self-selection; the type of work that comes through our door, it starts to become that nature. And while there’s always a few market-rate projects on the boards here, we always try to find, what is it that ties back to more of our civic space?”
Marvel’s more explicitly civic-oriented recent projects have included a revamped public park in Philadelphia, a new home for a nonprofit theater in Arkansas, and a renovated visitors’ center for a national forest in Puerto Rico, where Marvel has an office in Ramírez-Jiménez’s hometown of San Juan.
“I moved to New York City to do my master’s at Columbia University; I was going to stick around for a year or two and then go back home. That’s a very familiar story, right?” says Ramírez-Jiménez, who’s now lived in NYC for more than 20 years. Marvel, she says, offered “a great opportunity for me to cement that relationship I’ve always had between New York and San Juan, and just to see how I could weave those two existences together. This was obviously the perfect venue for it.”
Two of Ramírez-Jiménez’s latest “babies”—“I don’t have kids, so I have buildings”—are public-oriented projects in the Bronx.
The Walter Gladwin Recreation Center, situated in one of the borough’s oldest public parks, is on track to be among the first public buildings in New York City made entirely from mass timber. “It really depends on the procurement process and the construction timeline if we get to make that mark,” Ramírez-Jiménez says of the center, which is scheduled to be completed in 2027. “If it’s not the first one, it will be one of the first ones, and that is a big, big, big win because New York City is still working through the legal aspects of mass timber. We want to show everyone that even with those challenges, you can still do mass timber here.”
The advantages of the building medium include meeting the parks department’s goals for carbon neutrality and Marvel’s own metrics for energy performance. Timber also fit naturally into the challenging topography of the site, with a three-volume design that maintains a feeling of openness to the outside from every facade. The result is an inviting, accessible facility that not only brings valuable amenities to park patrons, but acts as “a beacon in the park,” Ramírez-Jiménez says, “to provide a sense
BY KRIS VIREHOW DO YOU DESIGN FOR EVERYONE WITHOUT FEELING GENERIC ?
of security and sort of extend the safe hours of the park.”
Similarly, Marvel’s revamp of the Bronx Museum’s facade, starting construction this summer for a 2025 target, aims to open the building up to its surroundings, making the museum feel more responsive to the immediate neighborhood.
“There’s this very fun party on the street along Grand Concourse, Boogie on the Boulevard—an annual festival on the main thoroughfare of this part of the neighborhood,” Ramírez-Jiménez says. “When you see pictures of it, you see this backdrop of the museum that feels like it’s not part of that—just closed off, not participating in this celebration of the community.”
Marvel saw its “homework,” as RamírezJiménez puts it, as making the museum’s south wing into “the Bronx’s living room.” That meant making the space accessible, visible, and welcoming—counteracting the perception that institutions like museums “tend to be elitist.”
The principles that animate Marvel’s civic works, Ramírez-Jiménez says, ultimately improve everything they do. “How can you design for everyone without creating something generic? You need to find a way that’s flexible, and adaptable, and that is going to eventually outlive you. That’s really the testament of when something was successful— not the initial moment, but how it evolves after many years.”
The Walter Gladwin Recreation Center is expected to be among NYC’s first public buildings made entirely from mass timber. Marvel’s revamp of the Bronx Museum’s facade aims to open the building to its surroundings, making the museum feel more like it’s part of the immediate neighborhood.
“DESIGN IS SPIRITUAL.” IT’S SPELLED OUT ON Rachael Grochowski’s sweater as we sit down for breakfast at the annual Biophilic Leadership Summit, which took place this year at Serenbe, a neighborhood itself designed to focus on well-being, just outside of Atlanta. But the sweater is not just a stylish statement; Grochowski means it. It’s part of why she’s speaking at the event.
For Grochowski, the idea that design is spiritual dates back to her graduate school thesis. In that project she aimed to design a wellness center using elements that existed in structures from nature that she had experienced and found to be meaningful in some way—be it for its sense of place or feelings of intimacy or safety, for example. “They were elements that really resonated with me. As I was designing that project and leaning into ways I could create this space where people could heal, I started to pull those pieces together,” she says.
She began to see and explore more around design’s ability to bring people into the present. “When you start to look at it through that lens, it starts to affect your ability to connect to gratitude—to your own self and to those around you. On a spiritual level I believe design has this ability to bring us back together.”
She points to design as a true representation of connections between people. One person can’t bring a building to life on their own, for example. “You realize the number of people whose sweat, love, and commitment went toward creating a structure and the dependency on each other to do each one’s job—because I can’t do my job if this person doesn’t do their job. It’s a web of commitment.”
In today’s world most people don’t often consider who physically makes the things they love or even who provides much needed services. “Who collects the trash?” she asks. “We forget that we should be grateful for that, but it’s an important job, frankly. And we forget that people’s hands go to create our homes, too.”
Now based in Montclair, New Jersey, Grochowski started her own firm, RHG A+D, in 2004, after years of working for other firms and working on luxury hospitality projects. “I loved it because there was a lot of craft in it, but I didn’t love that it wasn’t accessible to everyone, and the firms I was working for at that point didn’t have the balance of like, ‘We’re also going to do this project.’”
At some point she decided she didn’t want to work for vanity alone anymore, and she began to reconsider where her skills might be used best. “I’ve always believed that design is for everyone,” she says. “As I grew into my career there was a real moment of, ‘What am I doing? Is this really contributing to the whole? Is it contributing to the well-being of everyone? As a yogi and someone committed
BY LAURA ROTEto social justice and equity, something didn’t feel right. At that point in time there were other firms doing more equitable work, but what I was doing was not. I loved what I was doing, but it was not for everyone.”
When she started her own office she made a commitment to hire diverse architects, and she talked to the team (now 15 people) about how quality design should be for everyone. “When you experience quality design it changes your life. We started doing projects that were more for everyone,” she says.
From volunteer or discounted projects for community groups to specifying materials that aren’t toxic, she wanted every element of a project to show a commitment to the service of mindful design. Today, while her projects include high-end residential work, she emphasizes that it’s not about creating the most expensive space. It’s more about helping families lead happier lives. “We’ve had a couple residential clients who’ve said things like, ‘The way you designed our kitchen, our family sits together now every night, and we talk more than we ever have.’ That’s equity in a different way. It’s equity of time and relational equity.”
Grochowski and her firm continue to give of their own time to various nonprofits, too, like The Clairidge, a nonprofit theater that dates back to 1922 that now operates under the Montclair Film umbrella. RHG A+D renovated the theater in 2021. Montclair Film was cofounded by Evie Colbert, Stephen Colbert’s wife, and Bob Feinberg, a titan in the public media sphere. What started as a film fest developed into an educational program that went far beyond interesting films into growing a community around the arts. The film program now includes summer programs that invite out of state high school students to apply for scholarships for hands-on filmmaking workshops. “For some of those students it’s a pathway to college they didn’t know they had.”
The Clairidge is a nonprofit theater that dates back to 1922. RHG A+D completed renovations of the formerly abandoned theater, which is now run by Montclair Film and intended to provide film at affordable pricing as well as serve as a community hub.
WHEN LILIAN ASPERIN, PARTNER AT WRNS STUDIO, sits at the table in an early project meeting, she wants to hear from more people—to really hear from them. “In managing projects I feel like we can’t rush the earlier phases as much as people might have assumed. We have to pause and listen and invite more conversation,” she says.
It’s no longer enough to do a few things or follow a LEED checklist, Asperin says. Architects and designers need to dig in to uncover things they didn’t even know were needed. The result can make for truly great projects with long-lasting impacts—not just for the built environment, but for building occupants, too.
The Dennis & Janice Caprara Community Center in Gonzales, California is a project with a lot of lessons to share already. The WRNS team visited Gonzales—a city of about 8,500 residents, mostly Hispanic and Latinx with a large demographic of residents under 19—to find out what they needed from the project early on. Asperin says where some architects might have simply talked to community leaders about the project, WRNS wanted face time with those who’d actually use the community center—the youth.
First the team considered how to engage in a way that made the young people feel they could really share their thoughts. “Who’s going to be involved in this community? Gray hairs don’t have all the answers, and they’re not living the kinds of lives the youths are living right now,” Asperin says. “In this community in particular the youth are really active. They have a youth council, and they consider themselves ambassadors. They have this sense of responsibility.”
WRNS went to their high school at lunch to learn more about their priorities. They designed all of their questions in Spanish and English, and Lilian and her colleague Raul Garduño, also a partner at WRNS, could talk with students in both languages, too. They engaged in various formats to encourage more participation.
Asperin says considering who is invited to a design conversation and how they’re engaged is critical to getting helpful feedback. “Invite others and engage in ways that are welcoming. Speak a language they feel comfortable with,” she says. “There was no shortage of opinions once we asked. I could see it in their faces, like, ‘No one’s really asked us, and no one’s bothered to ask us in a way that makes us feel like we can speak broadly in a safe space about things we really care about.’”
The conversation just so happened to build upon community surveys students did during the pandemic around anxiety, health and well-being, and feelings of isolation. They decided these should be priorities, as well as quiet spaces with access to
BY LAURA ROTEHOW TO DESIGN SO PEOPLE FEEL SEEN
nature and flexible space where they could do yoga one day or work on college applications together the next. “They wanted this room that could flex according to the things that could potentially be stressors for them, to create community around them,” Asperin says. “It was interesting because they were still churning on what they discovered about themselves and their needs during the pandemic and how to make that more of a mainstream event. We all need a place to be, to relax. We all feel better when we can look at green and see daylight. They’ve internalized wellness into physical spaces. They were telling us, ‘Please make it as flexible as possible so we can have a range of opportunities that all feel good to us.’” The project broke ground in spring 2024.
Having people on the ground that the students could relate to was also key. Asperin says the students wanted to hear more about how she and her colleagues found themselves in these careers. “They wanted us to tell our life stories—where we were born and how we made decisions about college and how that’s translating
A planned community center in Gonzales, California considered a lot of input from young people in the community.
At center, the Palm Springs Development Project will be a student-centric and community-rich regional center of innovation distinguished by its multifaceted program in the Coachella Valley.
into working,” she says. “In some ways designing for equity is like designing for my people. We’ve never really been a majority. We’ve never really been asked questions. I am really compelled to ask, ‘Who else is not here that we should be hearing from to feel like everybody’s represented?’”
In engaging the students they also shared with them what it’s like to be an architect, as well as what it’s like to partner with a builder who is from Monterey, the next town over, for example, and the importance of creating such opportunities. “We wanted to show them you can have a career and a profession that is around design and construction. They wanted to know more about us because it’s rare that a lot of people have these career pathways or aspirations.”
Asperin herself was born and raised in Puerto Rico. “Licensed architects are mostly white, frankly. Hispanic women architects make up 1% of the population of licensed professionals. As a Latinx person, I am part of the 1%. There were not too many of us women going through architecture,” she says.
A big part of equity is about opportunity, and Asperin says the AEC industry has the power to really make a difference. “Committing to equity is not just designing. It’s designing a sort of infinite loop of opportunity. And yes, we’ll design and build it, but how does it enable more opportunities that are broader in reach for longer?” she asks. “That to me is equity— having things in place that are really supportive, restorative, inspiring, and, in the best of worlds, really life-changing. How do you design places where people feel like they belong and they’re supported, and they’re not an exception? They’re seen in their full selves.”
“WE ALL NEED A PLACE TO BE, TO RELAX. WE
“A LOT OF PEOPLE IN THE BAY AREA HAVE BEEN focused on equity in design for a very long time, without the umbrellas of DEI or social justice that have become banner terms,” says Hafsa Burt, the founder and design director of hb+a Architects.
That includes Burt herself, who cites the influence of the late architect Harry Overstreet of Oakland’s Gerson/Overstreet Architects, where Burt worked for some time before establishing hb+a in 2006. “He was working on pretty remarkable projects all over the Bay Area and in Southern California,” Burt says. “And besides being an architect, he was a big civil rights activist. I was fortunate to have known him for a very long time before he passed away in 2019.”
One particularly meaningful project is the West Oakland Youth Center, a collaboration between Gerson/Overstreet and hb+a. A renovation and expansion of a former church building, the center was completed in 2013 and includes amenities like computer labs, a fully equipped commercial kitchen for culinary training, and a 200-seat auditorium.
The project involved extensive consultation with the community—particularly with its target audience of neighborhood youth. “The kids were so involved,” Burt says. “All the stakeholders, the whole local community; everybody was pretty excited about it.”
Burt took on responsibility for the sustainability aspect of the venture, “which was a big thing because the city of Oakland had just passed its green building ordinance, and they had higher aspirations for it,” she says. “And Harry had aspirational goals, too, so it has a rainwater harvesting system; we had higher standards for indoor air quality when that conversation was just starting.”
Burt has made indoor air quality a focus of her own work, regularly presenting on the topic to industry audiences over the past 15 years. She was also an early adopter and proponent of the 2030 Challenge (the initiative to make all new developments carbon-neutral by the year 2030) and is currently co-authoring a white paper for the Urban Land Institute on “how land-use decisions can actually affect public health in terms of access to health care, access to nature, access to clean air—which I see as basic human rights,” she says.
“There’s a history of land-use practices in the US being racially motivated, and those practices can actually contribute to [disparities in] the mental and physical health of community members,” Burt adds. She and her co-authors aim to lay out their findings for “how land use and development has been historically, where it is now, and what we think should be the future—as a moral obligation of design professionals” to re-examine those practices,
YOU CAN BELIEVE INBY KRIS VIRE
she says. “We can make an impact if we think from that perspective, regardless of the ZIP code.”
Burt also points to the efficacy of renovation versus new construction—not just for sustainability purposes, but for maintaining a community’s sense of ownership. An example is the Marin Health and Wellness Center, a revamp of a 1960s-era clinic in the historically Black San Francisco neighborhood of Bayview.
The building had a landmark designation from the city that meant its exterior could be restored but not altered. “My job was—how can I restore this gem that is so important to the community but that had code problems, access problems, and make it possible to have a functioning, state-ofthe-art clinic inside? My general approach to projects might be more avant-garde if they were, you know, ground-up,” Burt says. “But there’s a huge opportunity in bringing existing building stock to its highest use and making it a place of pride for the community.”
In 1960 Arthur H. Coleman opened a clinic in San Francisco’s Bay View neighborhood to provide equitable access to health care. hb+a worked on two facilities for this nonprofit in San Francisco and Marin. Facilities like these, grown from grassroots efforts, are remarkable examples of the work that hb+a architects does. The exterior of the Class A culturally historic building was renovated in kind and includes the original lighting fixture from 1960s.
“THERE’S A HUGE OPPORTUNITY IN BRINGING EXISTING BUILDING STOCK TO ITS HIGHEST USE AND MAKING IT A PLACE OF PRIDE FOR THE COMMUNITY.”
MICHAEL ALLEN ALWAYS LIKED TO DRAW. GROWING up he loved to sketch and tinker and learn new things. He went to the library and read books about architecture for fun. “I was always a learner. I still am,” he says.
Allen went on to study architecture at Clemson University, where he also played football, before deciding to test his true passion. He worked for a few firms, soaking up real-world knowledge and learning what he liked and didn’t like about the industry before realizing it was time to make a name for himself. “I kept having this itch to do it on my own,” he says. In 2019 he started MOA Architecture, and in 2021 he received the Social Justice Award from the South Carolina Chapter of AIA.
Now 47, the architect is partly immersed in working on the Echo Theater in Laurens, South Carolina (population less than 10,000). It’s such an important project that, at first, he and the Greenville-based firm volunteered design services to help get things moving. The Echo Project aims to build a museum and center for racial healing at the site of a former white supremacist headquarters. The building was first a segregated movie theater and then a place called the Redneck Shop, a known gathering place for the Ku Klux Klan and other hate groups until as recently as 2012.
Allen remembers when he first talked to the leaders of the Echo Project—people like Reverend David E. Kennedy, who grew up in Laurens in the midst of the Civil Rights Movement. Kennedy currently serves as president of the project. “I sat and talked with Reverend Kennedy, his wife, and the board members to hear the stories surrounding the theater, and it really impacted me emotionally,” he says. “As an architect—one of the few Black registered architects and one of the only Black-owned firms in the state of South Carolina—I thought it would be a strong representation to come in and be the lead architect of record on a project like this. We want to transform a building from a symbol of hate into something positive for the community and the state.”
Allen was born and raised in Conway, South Carolina, and his alma mater Clemson is just over an hour away from the site, though he had no idea it was there—or its history. “This is the state I was born and raised in, and I have so much passion for this. We’re not finished with some of these stories. Race in America is an ongoing issue. The history of this theater is an example of how hate for another race of people can change lives forever. This hate continues today in many communities. This type of project is a step forward in helping to correct misdirected hate,” he says. “Also the Reverend and board have some huge ideas about teaching restoration and teaching overcoming pain and understanding. There is so much that’s going
BY LAURA ROTE PHOTOS BY WILLIAM CROOKSto come from this project. I have to help this vision come to life.”
The project so far has included a lot of interior demolition and removing racist paraphernalia, but a 20-foot swastika has proven challenging to cover up as it bled through the paint. The design team is considering incorporating it as an educational element. The symbol of hate was painted inside the building when the KKK moved in and began having active meetings for hate groups.
“The idea is to use that as a portion of the overall design. Although painful to see, it’s very symbolic. It’s where the screen for the theater was,” Allen says. “Blacks went up this skinny, dark stairwell and a separate door to get to the balcony to watch a movie. You come in and experience the racial divide of the theater. We want people to emotionally connect with the community and the history of the theater.”
MASS Design Group is also expected to work alongside MOA to design the project’s experiential elements. The museum and experience center will be major aspects of the project, including a history of Laurens
and a place for speeches on diversity and inclusion. An outdoor amphitheater is also in the works.
Architecturally Allen says the biggest challenge is recreating the space to reflect its history as a segregated theater while also designing a feeling of hope. “You don’t want to rip up the history, but you also want to create a space that feels like a fresh new start.”
While Charleston has a strong history of museums in the state, including the new International African American Museum, the Echo Project is an opportunity to build on that storytelling. “I don’t think people realize how big this is for the state,” Allen says. “This is part of South Carolina history that people are still learning. It’s a story and a building that is something physical; you can actually visit it and see it and have your emotions wrapped into understanding how hate has gotten transformed into something new.”
Allen continues to have high hopes for the project, which is in the fundraising stage. He says some in the community have mixed feelings about the project overall. “It’s still the South. It’s a small town. I know there are people who are for the project, and there are people against the project. As far as the tension, I know from speaking with Reverend Kennedy, they’re still fighting the good fight to get this project going.” g
Standard and custom colors available to complement building aesthetics
Multiple models and styles to meet performance requirements
Reduces HVAC operating costs up to 30% annually
Greenheck overhead HVLS fans supply energy-efficient air circulation that balances temperature and humidity, improving occupant well-being and safety in any environment. Whether the goal is to blend in or stand out, Greenheck overhead HVLS fans quietly deliver comfort you can truly feel.
View the case study and video
Colorful metal panels mimic signature sculpture
Parc Haven features industrial-style PAC-CLAD Highline B2 metal cladding that references the adjoining train tracks. A punch of colorful Flush panel highlights nod to Symphony Park’s Pipe Dream sculpture sited directly across the street.
THE DALNEY IS A 54,500-SQUAREFOOT OFFICE BUILDING AT GEORGIA TECH WITH SURPRISING DESIGN.
EskewDumezRipple helps move the needle on decarbonization.
BY SEAN O’KEEFEadults, asking not just what the environment can do for them, but what they can do for the environment.”
Smith says autonomous buildings, where the entire sphere of public architecture is disconnected from the grid, is more of a survivalist vision than a likely reality. “The big opportunity is for buildings to have enough onsite equipment to be active, grid-aware participants in infrastructure as network citizens.”
We recently sat down with Smith to learn more about EDR’s efforts to help clients decarbonize.
In 2015 EDR responded to a design competition by the Georgia Institute of Technology (Georgia Tech) to develop the first building in the southeastern United States to earn a Living Building Challenge (LBC) certification. Along with two other teams, EDR’s team was chosen from more than a dozen international teams to explore what a Living Building could be in this climate. The competition helped EDR raise our sights on integrated design, where designers, social scientists, and specialists work parallel rather than sequentially. This allowed us to develop some radical ideas about what a building could be.
Using energy more efficiently will provide better environments , improve mental health, and increase human and building productivity as much as it will impact climate change, if not more, says Z Smith, principal at New Orleans-based EskewDumezRipple (EDR), a national practice with deep roots in the South.
As a signatory to the AIA 2030 Commitment—the actionable climate strategy aimed at reaching net zero emissions in the built environment—EDR takes sustainability seriously. Smith, who came to architecture through a career in physics and engineering, says long-term sustainability must be holistic, and buildings must become contributors.
“My work at EDR is focused on shaping buildings to be much better on energy use in pursuit of better environments for people,” Smith says, adding that buildings can be a lot like infants with constant demands.
“‘Feed me,’ ‘Clean up my waste.’ We’re trying to make buildings more like responsible
ESKEWDUMEZRIPPLE (EDR) AND GEORGIA TECH ARE WORKING ON TECH SQUARE 3—A 400,000-SQUAREFOOT ACADEMIC TOWER IN MIDTOWN ATLANTA.
EDR’s big idea was to put the building’s wastewater treatment plant front and center for all to see when they walked in. If you want people to appreciate their impact, they must be made aware of where the things we produce go when we’re done with them. Ultimately another team was awarded the Living Building Challenge project, but we learned a lot, and this changed the nature of what Georgia Tech asked for in its subsequent projects.
The following RFP for a new construction building issued by Georgia Tech called for a public-facing wastewater treatment plant as a critical component of a mixed-use office building. EDR won that project and designed The Dalney Building—a 54,500-square-foot office building designed to host a blackwater reclamation system on the first level. EDR not only finished The Dalney Building before the Living Building competition project but also believes they achieved much of competition building’s overall performance at half the cost.
It is essential to understand that it is not just about low-carbon construction or zero-carbon operation; it’s about designing a building tuned to pull from the grid when carbon intensity is lowest.
For example, EDR and Georgia Tech are working on Tech Square 3—a 400,000-square-foot academic tower in Midtown Atlanta. This building will be grid-aware, meaning this all-electric building can shift demand to lower its overall carbon intensity. This building’s Energy Use Intensity, or EUI, is projected to be under 25 compared to 90 for a typical office tower in Midtown. This is being achieved at a cost-per-square-foot comparable to a conventionally designed building, essentially at no extra first cost.
Roughly 30 years ago, long before EDR’s involvement, Georgia Tech (GT) embarked on a visionary plan to revitalize the campus experience in the heart of Atlanta as a performative landscape of intertwined uses and purposes. Project by project they have implemented this vision, which they call the “Eco-Commons,” to become a green necklace weaving its way through campus.
As an extension of the relationship established on The Dalney Building and Tech Square 3, EDR was asked to join GT as an advisor on their emerging Climate Action Plan (CAP). Beginning in 2022 almost 100 campus stakeholders convened across nine subject matter working groups to develop climate mitigation and resiliency strategies to cut net emissions in half by 2030 and achieve net-zero emissions by 2050, while leveraging the GT’s academic and research strengths.
Most of GT’s immediately reducible emissions are Scope 2, or those driven by the generation of the electricity it uses. But its
Scope 1 emissions, driven mostly by its campus steam loop (where steam generated by central boilers is piped to campus buildings), are not negligible.
Nearly a century old, Georgia Tech considered replacing the steam loop with like-for-like until CAP analysis revealed that replacing it with a thoroughly modern warm-water loop that harvests wasted heat from campus cooling towers could be accomplished for less money upfront and would cost less to operate; fed by clean, renewable electricity, this can help eliminate Scope 1 emissions.
The CAP aims to act as a bridge between climate planning and land use planning. In considering the positive impact of providing more student housing, the CAP seeks to minimize the carbon footprint on campus and reduce that associated with commuting students, faculty, and staff. During planning it came to be appreciated that while Georgia Tech has enough sites to double the existing real estate portfolio, the emissions caused by building that much space would be greater than current Scope 1 emissions campus-wide.
Rather than trying to meet future needs entirely by adding buildings, GT’s plan highlights the importance of using existing assets far more space-efficiently first. For example, the average academic office is typically occupied only a few hours a week. Finding ways to provide all the privacy people need when they need it, but not building offices that stand empty most of the time, will be key. The plan prioritizes as-needed offices and classrooms, accelerated virtual learning programs to limit the need for to-campus travel, and more consistent building metering.
On many university campuses not all buildings are fully metered, and so it can be difficult to know which assets are most badly in need of improvement. Though it might be easy to imagine that the oldest buildings would perform the worst on energy due to age and older building methodologies, that doesn’t prove to be the case. For instance, buildings built in the 1920s were designed for daylight and cross ventilation, making them inherently easier to illuminate and cool. However, buildings constructed during the ’60s, ’70s, and ’80s seemed to have turned away from the physics of nature to their detriment. Transforming the existing building stock—especially the often under-loved buildings constructed 30 to 50 years ago, is going to be key to achieving their environmental goals—with the added benefit of providing better places for learning, which is, after all, the mission of a great university. g
TECH SQUARE 3 IS PLANNED TO BE GRIDAWARE, MEANING THE ALL-ELECTRIC BUILDING CAN SHIFT DEMAND TO LOWER ITS OVERALL CARBON INTENSITY.
THE 54,500-SQUAREFOOT DALNEY BUILDING COMBINES A PARKING STRUCTURE, AN OFFICE BUILDING, AND A BIOLOGICAL WASTEWATER RECLAMATION FACILITY AT GEORGIA TECH.
Designed as a “terminal in a garden,” Terminal 2 (T2) at Kempegowda International Airport in India is inspired by the city of Bengaluru’s “garden city” heritage. We wanted to radically reimagine the travel experience by connecting passengers to nature along each step of their journey. From check-in to boarding, passengers experience a sequence of distinctive spaces, each integrated with a variety of sensory landscape features.
Upon check-in passengers are immersed in hanging gardens, after security passengers can find peace among soothing sounds of water and verdant plants, and before boarding passengers can enjoy a meal beside stepped gardens. If time allows, passengers can traverse a network of bridges and outdoor walkways en route to their gate.
We wanted to create a calming oasis within the hustle and bustle of an international airport. What unfolded was a series of landscaped experiences that create a tranquil environment as well as moments of delight. We proposed an architecture that would be more subtle to complement these landscaping experiences. We explored the use of rich, locally sourced materials that are not typically found in airports. We used natural stone, rattan, brick, and engineered bamboo. This was our first time utilizing engineered bamboo, which proved to be a highly renewable and sustainable material that complemented the garden concept.
We worked closely with our landscape architect, Grant Associates, and our lighting designers, BPI, to balance daylighting requirements of the plants and the energy loads of the building. We wanted our landscaping to feel complete today as well as thrive in a future environment. We tuned the skylights to provide the perfect amount of filtered natural daylight to the interior spaces.
irports vary from country to country , even region to region. What airports have in common is their notion of connectivity—they are a significant point of departure or arrival in a traveler’s journey. Our approach to designing terminals around the globe is rooted in a sense of responsibility to deliver designs that truly reflect the identity, culture, and needs of the communities they serve. The challenge is how to design this environment in such a way that is flexible, sustainable, and fosters a memorable experience for passengers. As architects we welcomed this challenge, and together with our collaborative team set off to invert expectations of how an airport should look and feel.
SOM WORKED CLOSELY WITH LANDSCAPE ARCHITECTS AT GRANT ASSOCIATES AND LIGHTING DESIGNERS AT BPI TO BALANCE THE DAYLIGHTING REQUIREMENTS OF THE PLANTS AND THE ENERGY LOADS OF THE TERMINAL 2 PROJECT AT KEMPEGOWDA INTERNATIONAL AIRPORT IN INDIA.
Airport terminals are also fairly complex buildings that integrate a wide range of movement systems—including aircrafts, passenger boarding bridges, baggage handling systems, airside and landside vehicles, and passengers. They must function as efficiently and smoothly as possible. From the size and characteristics of aircraft to security screening and passenger processing technology, airports are constantly evolving. It takes years to design and build a terminal, and some technologies that exist at the start of the project may be obsolete by the time the terminal opens. Another challenge is designing built-in flexibility to afford terminal operators the ability to adapt to future needs and opportunities that we may not even know about yet.
All the gates at T2 are set up on a two-for-one basis. That is, each can serve either a single wide-body (two-aisle, like the old B747) or two narrow-body aircraft (single-aisle, like the B737). In addition, we designed the piers (concourses) in such a way that the gates can “swing” between domestic and international use. In India and most of the world, departing international and domestic passengers must be segregated from each other. The gate areas of the Bengaluru piers can be opened or closed to one or the other sector of operation, depending on the need or time of day. By getting double use out of all gates we avoided overdesigning the terminal.
We also carefully considered how the airport connects to other modes of transportation today, and in the future. We designed a multi-modal transit hub that connects passengers to buses, cars, and eventually a metro, in a safe and efficient way. The T-shaped, two-level space is situated at the center of the airport and makes the airport entirely walkable.
As large buildings airports are culprits in intensive energy and resource use. As architects it’s our responsibility to design an economical building that still delivers on experience. We implemented a series of sophisticated sustainability strategies to allow the terminal to run entirely on renewable energy. These strategies include
Peter Lefkovits, design principal at Skidmore, Owings & Merrill (SOM) is a designer in SOM’s New York studio with significant experience leading projects throughout the US and Asia.
Lefkovits’ expertise in the aviation sector has led the design and implementation of several of SOM’s awardwinning airport terminals, from the new terminal at Kansas City International Airport to Terminal 2 at Kempegowda International Airport in Bengaluru.
PROJECT Terminal 2 (T2) at Kempegowda International Airport
LOCATION India
ARCHITECT
SOM
COMPLETION YEAR 2023
SIZE
380,000 square meters
LANDSCAPE ARCHITECT: Grant Associates
LIGHTING DESIGN: BPI
CERTIFICATIONS
LEED Gold
extensive solar sharing and intelligent building systems as well as the use of renewable materials. The abundant vegetation is irrigated with rainwater harvested onsite, and the retail area’s waterfalls cool the inside temperature. For the majority of the operating daytime hours the terminal relies on natural daylight, which significantly reduces the energy consumption of the building and fosters a natural interior environment for passengers. We also focused our engineering on reduced embodied carbon and designing a structure that maximizes the use of locally sourced materials. We designed a small structural grid (only 18 meters by 18 meters) that supports the program spaces needed for 25 million annual passengers. Our smaller grid reduces the material needed and creates a lightness in the structure. The terminal’s roof is made entirely out of domestically produced materials and built with local construction technology.
Our goal for T2 was also to balance the requirements of bustling international travel with a need to create a building with a human scale and an uplifting experience. We often engage artists and designers to develop a deeper and more meaningful understanding of a place. Integral to the design of the new terminal was the idea of creating a passenger experience that captured the spirit of Bengaluru and the culture of Karnataka. We collaborated with celebrated fashion designers Abu Jani and Sandeep Khosla (AJSK) to study the local landscape, traditional dance, art, and architecture. These insights inspired the materials, forms, and installations in the new terminal. We are excited for passengers to experience our design for many years to come. g
Derek A.R. Moore, design principal at Skidmore, Owings & Merrill, also contributed to the story.
ronmental challenges facing the global community at a micro-scale using a sustainable approach to design.
According to the World Economic Forum, a staggering 80% of global wastewater is released back into the environment without proper treatment, leading to contamination of rivers, lakes, and oceans. We also experience a global loss of more than 16 million acres of forests annually—affecting biodiversity, carbon sequestration, and climate regulation, according to the World Wildlife Fund. Facts like these illustrate the necessity of landscape architects to act as environmental stewards responsible for embedding the principles of sustainability in every facet of their work.
With these facts in mind sustainability should not become a superficial buzzword, but an essential commitment that every landscape architecture project strives for to preserve our planet and its natural resources for future generations. By adopting a critical approach to sustainable practices, we stand to make an immediate and lasting impact on the reduction of pollution and protection of habitats to ensure a healthy balance between environmental, economic, and social needs.
McCullough was invited to join multidisciplinary firm HGA as part of the renovation of the Don Powell Theatre and addition of a new Second Stage performance building for students at San Diego State University (SDSU). The outdoor spaces surrounding the theater were designed with a focus on biodiversity and four important areas of sustainable development: reducing urban heat island effects, increasing carbon storage, conserving water, and beautifying green infrastructure, also known as low-impact development (LID).
climate-conscious approach to locally adapted landscape design , alongside thoughtful spatial organization of outdoor spaces, are effective means shown to mitigate the negative effects of climate change, helping to protect commercial, entertainment, and educational spaces while demonstrating the power of sustainable design. At San Diego State University’s Don Powell Theatre renovation, McCullough, working in tandem with HGA Architects, created an opportunity to address many of the envi-
MCCULLOUGH
LANDSCAPE
ARCHITECTURE
COLLABORATED WITH HGA ARCHITECTS ON A UNIVERSITY
THEATER RENOVATION IN SAN DIEGO.
Reducing urban heat island effects can help lower ambient temperatures, which in turn reduces the demand for electricity and lowers greenhouse gas emissions from power generation. Trees, green spaces, and living vegetation all play a pivotal role in shading surfaces, deflecting radiation, and releasing moisture into the atmosphere, improving overall environmental well-being.
Both SDSU projects made use of large canopy tree species, including Tipuana Tipu and Chinese Elms, to help ensure vegetation protected buildings and pavement areas from direct solar exposure. Recreational lawn and large areas of drought-tolerant plants like sages, deer grass, and yarrow were also used to minimize hardscape that would contribute to the absorption and radiation of excess heat.
Increasing carbon storage helps to sequester excessive carbon dioxide emissions. To support this process McCullough’s design ensured a dense layer of mulch was used to provide organic material that, upon decomposition, would feed the soil microbiome and “grow” soil to increase its carbon sequestration capabilities. By storing carbon dioxide the SDSU project helped to localize stabilization practices that assist in further reducing the harmful effects of carbon release. Additionally, we intentionally opted for peat-free amendments, as peatlands store more carbon than all other vegetation types in the world combined. By leaving peatlands alone they can continue to perform their essential function of storing carbon, which is lost as soon as they are harvested.
Often called our most precious resource, water conservation is a mandatory consideration for any effective sustainability plan. Water conservation plays a critical role in supporting groundwater preservation that is vital for plants, animals, and people. Ground-
Zeek Magallanes is the studio team leader at McCullough Landscape Architecture. He studied landscape design at Cuyamaca College and has worked for the Cuyamaca College Plant Nursery, Armstrong Garden Centers, and the City of San Diego’s Water Conservation Program. He earned his master’s in landscape architecture and urbanism from the University of Southern California. He is passionate about empowering others by sharing his knowledge of the intersection of urbanism, social and environmental resiliency, and the business of design.
PROJECT
Don Powell Theatre
+ Second Stage
Renovation at San Diego State University
LOCATION
San Diego
ARCHITECT & INTERIOR DESIGN
HGA
LANDSCAPE
ARCHITECT
McCullough
Landscape Architecture
GENERAL
CONTRACTOR
Rudolph and Sletten
CIVIL ENGINEER
Michael Baker International
STRUCTURAL ENGINEER
Degenkolb Engineers
MECHANICAL ENGINEER
ME Engineers
LIGHTING
HLB Lighting
ACOUSTICAL
McKay Conant
Hoover
water is often the sole source of tap water for daily use in some communities and foundational to many industries, including manufacturing, agriculture, and technology—not to mention the reliance of diverse ecological systems like rivers, lakes, and streams.
To minimize waste and amplify the amount of direct water plants received, the SDSU Don Powell Renovation and Second Stage project made use of low-flow drip irrigation systems, prioritizing high-efficiency spray heads to maximize water distribution efficiency while minimizing water usage, reducing overall run time by up to 35%.
Green infrastructure, also known as low-impact development (LID), plays a decisive role in mitigating the adverse effects of urbanization and climate change by restoring or supporting pre-development hydrological functions. Simply put, LID ensures natural factors and pathways are allowed to continue playing their part in protecting the natural ecosystem of an area, even after a commercial development has disrupted the native hydrological flows of a region. Distributing stormwater control and natural features that form the basis of urban stormwater management helps to minimize pollution, enhance water quality, and improves the overall well-being of local ecological systems.
The SDSU project was able to beautify the stormwater detention basins with attractive plant material, calling attention to and highlighting them as educational tools to demonstrate the attractive efficacy of LID. McCullough carefully selected plant species such as Muhly Grass and Cape Rushes that thrive in both dry and wet conditions, look beautiful year-round, and provide reliable structures to support local insects, birds, and butterflies.
Climate change continues to have a very real impact, putting sustainability at the forefront of key concerns for current and future designers who stand to make a direct difference in their line of work. The World Economic Forum estimates of a potential loss of $360 billion annually to the global economy in climate-related damages, demanding collaboration and partnerships across industries to shape the future.
Alongside HGA, we endeavored to provide an inspiring and eye-catching design committed to addressing the critical challenges of reducing urban heat island effects, increasing carbon storage, water conservation, and green infrastructure in a sustainable way. The longterm global impact remains to be seen, but landscape architects are in a prime position to impart well-considered, attractive designs that serve a greater purpose—encouraging others to make small but meaningful changes toward a world that balances our human needs with those of the planet we call home. g
to the point where we were concerned that the exposed metal panels could rust and create opportunities for leaks.”
Eager to avoid the expense and disruption of replacing the roof, Draughn reached out to the plant operations division of the North Carolina Department of Public Instruction for advice. The division’s engineers inspected the roof and recommended recoating it with a fluoropolymer-based roof coating—a strategy that had been used successfully in other school districts in the state.
The engineers invited several coatings manufacturers to visit the school and provide recommendations for remediation. APV Engineered Coatings, maker of NeverFade® Exterior Coatings, was one of only two coatings suppliers to take them up on the offer. The company sent Product Application Engineer Ernie Porco to inspect the roof and evaluate the condition of the existing coating.
“We conducted a visual inspection as well as mil thickness readings and scratch testing,” Porco says. “In many areas you could easily scrape off the degraded coating with your finger.”
As the scope of the project revealed itself, it became apparent that all the existing coating would need to be removed—a process that involved more than just simple power washing. Custom Coatings was selected to manage the entire job—from removal of the existing coating to recoating with NeverFade. “We reached out to a couple of other contractors, but due to the complexity of the coating removal process, they wouldn’t touch the job,” Porco says. “Custom Coatings was ideally suited for the task.”
Custom Coatings is known for providing a range of commercial services throughout the southeastern United States, including expert sealing, restoration, and high-tech coatings for the entire structure, from roof to basement.
The damage started to become apparent during a roof inspection in the spring of 2015. After 25 years of service life, the metal roof on Central Middle School in Dobson, North Carolina was showing its age. Backto-back winters with heavier-than-average amounts of snow and ice caused the blue, factory-applied coating on the standing seam roof to flake and peel off, exposing large sections of gray primer and the underlying steel roof panels to the elements.
“As snow and ice slid off the roof, they took chunks of paint with them,” says Robert Draughn, director of Construction, Planning & Design for Surry County Schools. “The coating failure got worse and worse,
AFTER
“We had successfully completed a prior roof coating removal and replacement project for the Department of Public Instruction, so there was a level of trust that we would also be successful with this job as well,” says Joe Brindle, president of Custom Coatings.
Draughn praised the project team’s dynamic, noting that everyone communicated well, worked well together, and responded quickly to concerns or issues throughout the project. “I couldn’t have asked for a better relationship, from start to finish,” he says.
Brindle says proper removal of existing coatings is crucial for the ability of a new coating to perform as intended. Without it the new primer and topcoat will fail. During the company’s 30-plus years of experience, it has developed advanced coating removal methods—including the use of a proprietary paint stripping material—that are both effective and cleaner than other methods. The stripping material works quickly; during an initial test it completely removed a patch of existing coating down to bare metal in under 15 minutes.
“I discussed options for removing the existing coating with our engineering team and asked each bidding contractor how they would address it,” Draughn says. “The chemical stripping recommended by Custom Coatings won out over options like bead blasting for the cleanest, most efficient, and environmentally safe way to remove the paint with minimal impact on students and staff.”
As part of its standard waste disposal policy, the Custom Coatings team took care throughout the removal process to keep the stripping chemical and coating residue from contaminating the environment—a special concern because a farm with a pond was located adjacent to the school property. They set up a series of drainage pipes and collection bins across the 125,000-foot roof to capture the chemical and solid waste so it would not get into the storm drain system and groundwater. Once captured, all the waste was placed in a dumpster and disposed of according to local waste disposal regulations.
After stripping the old paint from the roof, the Custom Coatings team thoroughly pressure-washed the entire surface to ensure no paint remover or residual materials remained. Then they sprayed a coat of APV’s W-1650 Bonding Primer at a thickness of 1.5 to 2.0 mils. The primer is designed to adhere to tough surfaces, including metal and pre-coated metal. Its water-based, low-VOC chemistry provides early water resistance, protects against corrosion, and applies with a smooth, uniform finish for optimum aesthetics.
Next they spray-applied two 2.5 to 3.0 mil layers of NeverFade Metal Restoration Topcoat in a custom-tinted blue color to perfectly match the roof panels’ original factory finish. Engineered for coated or uncoated ferrous and non-ferrous metal surfaces, the topcoat resists the harmful effects of UV degradation like fading, erosion, and chalking. It safeguards against salt spray and corrosion, protects against a wide range of abrasions, and has exceptional resistance to algae, mold and fungal growth, dirt pickup, and stains. It also is water-based and low in VOCs, meeting SCAQMD Rule 1113.
NeverFade Coatings contain Kynar Aquatec®, a polyvinylidene fluoride (PVDF) resin with super-strong carbon-fluorine bonds that do not break down under exposure to the elements, thus resisting the film erosion common with exterior-grade, acrylic-based latex coatings. When exposed to UV energy and environmental stressors, the additives, pigment, and resin in latex coatings break down, creating a chalky residue. Eventually the chalked coating wears away from the substrate—or is washed away by rain, wind, pressure washing or cleaning—until the coating film is gone and no longer protects the substrate. In addition, the chalky residue changes the coating’s surface energy and serves as a food source for mold and
mildew growth, which further degrades a building’s appearance and creates cleaning and maintenance problems.
Kynar Aquatec also resists fading. It has a 20-plus year demonstrated record of performance in extreme conditions, allowing APV to offer a 15-year product-and-labor guarantee that the coating will not fade by a Delta E of five or higher. Transferable to future building owners, the guarantee is unique to the architectural coatings industry.
“For decades architects have trusted the long-term, fade-resistant performance of Kynar 500® solvent-based finishes, which are baked onto metal surfaces of exterior building products like aluminum doors and window frames at the factory,” Porco says. “Today Kynar Aquatec allows specifiers to get similar performance in a water-based resin formulated for field applications.”
Quality assurance was top of mind throughout the four-month project, which took place primarily during the school’s unoccupied summer months. Even before the job started the APV/Custom Coatings team conducted multiple installation mockups to test coating adhesion. During installation the team did adhesion testing and x-cut tests after each coating layer was applied. At the end of installation they inspected the coated roof, checking mil thickness to ensure the job complied with the terms of APV’s guarantee. Because the paint removal process caused some sealant degradation, the Custom Coatings team also replaced those sealants, re-waterproofing the entire roof, then coated over the sealant.
The project was Custom Coatings’ first time using NeverFade Coatings, and the company has since become a NeverFade Certified Applicator. The certification process includes special training to learn about the chemistry behind the product, details around pre-job testing, color matching, application mockups, on-the-job troubleshooting, and post-installation quality assurance—all steps that give customers the confidence that NeverFade will perform throughout its guaranteed life cycle.
“We’ve worked with other fluoropolymer coatings before, but NeverFade is by far the best,” Brindle says. “It’s easy to use, easy to spray, and has a phenomenal finish that looks just like a new, factory-coated metal roof.”
THE SCHOOL HAS A FRESH, NEW LOOK AFTER THE ROOF COATING PROJECT WAS COMPLETED.
Draughn adds that between the performance of NeverFade and the skills of the Custom Coatings team, the roof coating project met the goals set out at the start. “We’re very pleased with the results. The coverage is impeccable, and it looks great all around.” g
utdoor urban spaces within the public realm can often land at opposing ends of the spectrum in terms of the experiences they provide—feeling either boisterous, large-scale, and overwhelming or empty, under-stimulating, and generic. Whether due to over-standardized design guidelines or a lack of emphasis on diversifying social use at the human scale, public spaces like plazas or streetscapes are not always as welcoming or engaging as they could be. Tidal Shift demonstrates an approach to design in the public realm using a different lens. This site-specific installation was developed for The Shed, a nonprofit institution for art and culture in New York City,
and was designed to activate their public plaza for summertime programming. The design proposal was developed by the WIP Collaborative, a shared practice and platform that enables independent design professionals and their respective practices to combine their varied expertise and perspectives to realize broader impact through collaboration and non-hierarchical modes of working.
Tidal Shift aimed to introduce sculptural forms and vibrant materials to the site that respond to the angular geometry of The Shed while offering a striking contrast to the monumental towers and wide open public spaces of Hudson Yards. Alternatively, the installation aimed to support and emphasize the scale of human bodies—both individually and in congregation—through inclined planes and stepped surfaces that invite play, rest, and social connection.
Conceived as a family of interrelated shapes, the platforms were configured in formal dialogue with one another, each developed to accommodate sitting, lounging, performing, and gathering, not only through their respective forms as separate objects but also via their composition together with the negative spaces in between them. This configuration was intended to be both dispersed and coherent as a collective zone of gathering, with the platforms oriented to support a sense of togetherness while also remaining open and connected to the surrounding plaza and pedestrian areas. The scale of the platform elements was uniquely determined to mediate the open plaza’s expansive space with a more approachable scale of communal furniture.
Symbolically the blue-green colors and undulating forms celebrate movement and action. They were also expressions of solidarity with the “green wave” of feminist activism that gained global momentum with recent hard-fought victories for women’s health care rights in Latin America at the time of the project’s opening in summer 2022. Through its forms, colors, and responses to context, the project called for a tidal shift in the liberation and care for diverse embodied experiences.
On a more local, site-specific level, the installation’s material palette and textures incorporated an additional layer of vibrancy, warmth, and soft tactility to complement the sleeker and more monochromatic backdrop around it.
After installation there was a noticeable shift in the patterns of movement through the plaza as well as an uptick in the diversity and range of spontaneous modes of social interaction—whether through everyday gathering and relaxing or communal assembly and group interaction for specific music performances, dance parties, and other events hosted by The Shed. From cartwheels and synchronized dance ensembles to lunchtime meetings and naps in the sun, the variety of social activities displayed and the personalization of use reflected the expressive character of civic life that emerges when people are given the possibility of more choice and engagement in public spaces.
TIDAL SHIFT
WAS A SITE-SPECIFIC INSTALLATION DEVELOPED BY WIP COLLABORATIVE FOR THE SHED IN NEW YORK CITY.
The Tidal Shift project allowed us to test and explore a number of recurring questions from my independent practice, Kalos Eidos, as well as work in architecture more broadly. How can qualities of interiority and urbanism hybridize to yield a sense of belonging and coherence while allowing a wide range of activities to co-exist? How can form and materiality be calibrated to prompt a range of possibilities for social engagement without being overly prescriptive, staying multi-faceted and open to interpretation? How can spaces be radically transformed through an economy of means, synthesizing inputs from the material and spatial to the programmatic and cultural?
As a designer working across an array of project types and contexts that often span across human, architectural, and urban
scales, it’s been important to understand project sites as dynamic, multi-scalar, and materially layered environments. Whether designing a building interior or a public plaza in a domestic or civic domain, the framework for shaping a project’s identity always entails a mix of space, surfaces, objects, textures, colors, and other dynamic forces acting together to support various modes of interaction and experience. In combining, overlaying, and developing them with enough coherence to be meaningful, each of these facets of an environment can contribute as critical ingredients for crafting and cultivating the identity and performative capacity of design interventions. When that balance of components also allows openness to and anticipation of the unplanned nature of social interaction and use, it activates the potential for design outcomes to invite, surprise, welcome, and embrace adaptability. g
Ryan Brook Thomas is principal of Kalos Eidos and a founding member of WIP Collaborative. The founding members of WIP Collaborative and project collaborators also include Abby Coover (Overlay Office), Bryony Roberts (Bryony Roberts Studio), Elsa Ponce (Studio Elsa Ponce), Lindsay Harkema (WIP), Sera Ghadaki (SERA GHADAKI), and Sonya Gimon (3fwild).
TIDAL SHIFT
AIMED TO INTRODUCE SCULPTURAL FORMS AND VIBRANT MATERIALS TO THE SITE THAT RESPOND TO THE ANGULAR GEOMETRY OF THE SHED WHILE OFFERING A STRIKING CONTRAST TO THE MONUMENTAL TOWERS AND WIDE OPEN PUBLIC SPACES OF HUDSON YARDS.
This summer some travelers will get a very green night’s sleep at Populus—the first carbon positive hotel in the US. In downtown Denver, the project is Studio Gang’s first freestanding hotel, and nature can be seen at every turn in the design. Studio Gang was inspired by the patterns on Colorado’s native Aspen tree, for which the hotel is named.
Biophilic design strategies continue in the interiors, designed by Wildman Chalmers Design, with a palette of warm browns and wood that conjures
up the forest. A thoughtful art collection curated by artist and environmentalist Katherine Homes adds to the mission.
Populus was built with an innovative ECOPact low-carbon concrete mix developed by Holcim, which offers a minimum of 30% lower CO2 emissions compared to standard concrete. “The uniqueness of ECOPact lies in its optimized blend of performance, durability, and sustainability,” Michael LeMonds, chief sustainability officer for Holcim US, previously told gb&d. The new
material launched in 2020.
The hotel is part of the Urban Villages Aparium Hotel Group. “For Urban Villages it was crucial that we pair Populus’ stunning architectural design—destined to forever change Denver’s skyline—with remarkable interior design that could seamlessly marry the building’s sculptural form with warm, welcoming interiors while extending its nature-inspired ethos,” says Jon Buerge, president and partner at Urban Villages. —Laura Rote
Salto delivers the most advanced, flexible, and secure access control solutions for all building and facility types.
Our global commitment to responsible materials sourcing and manufacturing practices sets us apart. It is our promise to our partners, customers, and the planet that we will lead our industry towards a greener, more sustainable future for generations to come. salto.us
ARCAT provides thousands of reports from building product manufacturers on how their products can help you make the right choice.
With ARCATgreenTM reports, you can find out how much post consumer waste is used in creating products, to lowemitting materials and other LEED contributing credits. You can find this information and more with ARCATgreen reports.