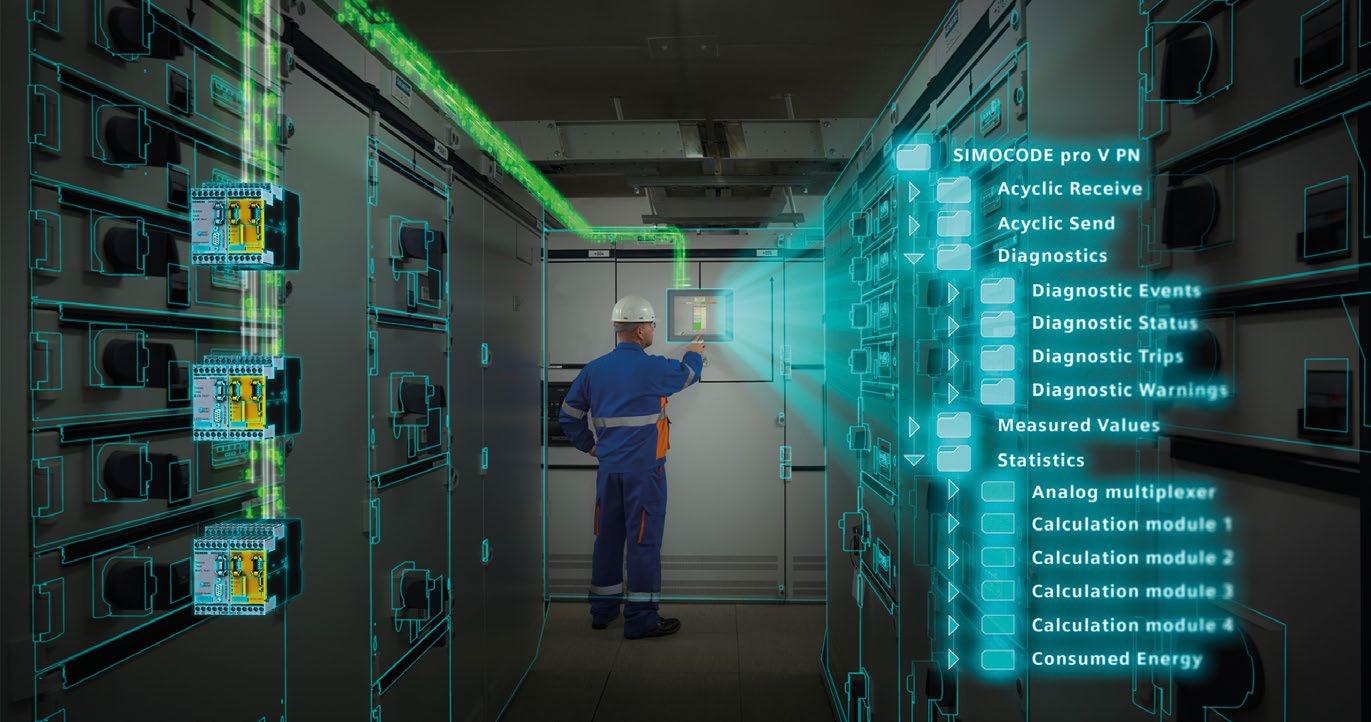
29 minute read
El camino hacia la gestión energética en plantas industriales
Soluciones para distintos niveles El camino hacia la gestión energética en plantas industriales
La eficiencia energética juega un papel fundamental en la industria. El cumplimiento de las leyes como el Real Decreto 56/2016, la creciente presión por los objetivos y la cada vez mayor concienciación en la protección del medio ambiente, con las restricciones en las emisiones de CO 2 asociadas, son factores básicos para reducir los costes energéticos y utilizar un sistema de gestión de energía conforme a las directrices que marca la ISO 50001.
n SIMOCODE - Pro permite la total transparencia de los datos operacionales, de servicio y diagnóstico en las instalaciones.
La gestión energética (GE) permite a una empresa determinar, mejorar y analizar de forma sistemática y continua su consumo de energía. Dentro de este proceso de optimización se han de considerar aspectos económicos, técnicos y legales. Dicho cometido se ha de integrar en el nivel de gestión y consta de medidas organizacionales y de inversión.
A la hora de abordar la eficiencia energética de nuestra planta deberemos actuar en algunos o varios de los siguientes apartados: Eficiencia energética productos / sistemas: Reducción de pérdidas de energía usando sistemas y tecnologías altamente eficientes (p. ej. motores de ahorro energético). Eficiencia energé tica significa reducir el consumo sin tener que disminuir el uso de plantas y equipos que consumen energía.
Sistema de gestión energética (SGE): Desarrollo e integración de un sistema para recogida, análisis, documentación y visualización de datos energéticos, así como regulación y control del consumo energético en plantas y edificios. Servicios energéticos: Servicios para optimización a lo largo de toda la cadena de valor de producción energética, p. ej. optimización del proceso de ingeniería o gestión de carga, así como consultoría y contratación.
En el caso de los sistemas de gestión energética se configuran típicamente de tres niveles para la integración de los datos: � Nivel de adquisición. � Nivel de pre-procesado y monitorización. � Nivel de gestión.
En el primer nivel, el de adquisición, existen en el mercado multitud de equipos que facilitan datos energéticos (p. ej. intensidades, tensiones, potencia…), y los comunican al nivel superior de preprocesamiento y monitorización. En este nivel cada día están tomando mayor importancia equipos de doble propósito como el Simocode Pro-V, que nos permiten el control del motor y a la vez nos brinda transparencia energética al tener disponible toda la información relevante como si de un medidor energético se tratase y que estudiaremos más en profundidad a continuación.
Simocode es un sistema de gestión de motores flexible y modular para motores con velocidades constantes en el rango de rendimiento de baja tensión. Optimiza la conexión entre la ingeniería de control y los motores, aumenta la disponibilidad de planta y mejora la puesta en marcha, operación y mantenimiento de los sistemas. Existen distintas versiones de producto, pero en este caso tendremos en cuenta la versión Simocode Pro-V con comunicación abierta a través de Profinet y OPC UA.
Cabe destacar que los dispositivos Simocode pro admiten la función de redundancia del sistema Profinet, y por tanto, pueden conectarse directamente a sistemas de alta disponibilidad con dos controladores sin necesidad de hardware adicional. Esto es especialmente importante en tareas complejas de automatización en la industria de procesos, donde el foco está en la disponibilidad y redundancia del sistema de control. Entre sus ventajas destaca: � Disponibilidad del sistema claramente mejorada. � Reducción de los cortes de producción, y por lo tanto, alta productividad. � Datos operacionales, de servicio y de diagnóstico detallados. � Diagnóstico web.
En línea con el futuro, la industria 4.0 y gracias a la comunicación abierta que ofrece Simocode Pro-V, una de las últimas funcionalidades que incorpora es la conexión con soluciones cloud de alto nivel como Siemens MindSphere, donde ya existe una aplicación desarrollada para estos equipos: Sirius Asset Monitor, que se explicará ampliamente al final de este artículo.
El siguiente nivel, el de preprocesado y monitorización, es el encargado de recopilar toda la información de los equipos de campo vía diferentes buses de comunicación y en su caso tratarla (totalizadores, contadores...) para su archivado y monitorización en sistemas HMI/SCADA. En este apartado los PLCs de la gama S7- 1500 con la opción Simatic Energy Suite permiten vincular la gestión energética con la automatización e implementar la gestión de cargas activa y, en consecuencia, control de los consumos energéticos además de obtener transparencia energética en la producción y las infraestructuras.
El esfuerzo de configuración se reduce de forma notable mediante una configuración sencilla de componentes mediante librerías de dispositivos para la medición energética, así como del control de los actuadores de conmutación para la gestión de cargas.
Las siguientes propiedades caracterizan al Simatic Energy Suite: � Integrado en la automatización.
� Transparencia energética a través de la recogida de los datos de energía. � Configuración de consumos eléctricos y no eléctricos (p. ej. kWh, m3, kg, unidad). � Archivo e informes básicos en los registros de datos de WinCC Professional. � Consumo flexible a través de la gestión de carga. � Gestión de carga basada en prioridades para los consumidores y productores energéticos. � La integración en el PLC asegura una alta flexibilidad y una elevada fiabilidad. � Configuración sencilla e intuitiva en vez de la compleja programación manual. � Generación automática del programa de energía del PLC para controladores S7-1500. � Generación de las pantallas para el HMI/SCADA de forma automática.
Por último, en el nivel de gestión nos encontramos herramientas como Simatic Energy Manager Pro, solución escalable, desde una estación única hasta una arquitectura distribuida. El objetivo es hacer que todos los datos relacionados con la energía y la producción estén disponibles en un único sistema. Esto requiere un sistema de gestión de energía que acepte datos de fuentes heterogéneas. Estos datos se

almacenan en una base de datos central (MS SQL Server). Los datos que ya están disponibles de forma electrónica son adquiridos e importados automáticamente de los sistemas existentes. Los que no están disponibles en forma electrónica, tales como datos de instrumentos de medición no automatizados o datos de producción, se transfieren manualmente al sistema de gestión de energía Energy Manager Pro. Los clientes Web permiten el acceso a los informes y la introducción manual de valores. Los clientes instalados también permiten la entrada a la configuración del sistema y de los informes.
Además, los usuarios pueden definir nuevos indicadores de rendimiento KPIs sin conocimientos de programación y son capaces de producirlos en forma de informes o cuadros de mando, así como realizar el seguimiento de las medias de mejora y el cálculo de líneas de base y "forecast" de consumos. Todo esto se realiza adaptando la visualización de los datos a un grupo de usuarios específico.
El estado del arte de la utilización de esta herramienta de gestión energética es el que se ha implementado en la planta de Pikolin en Zaragoza, gracias al cual se ha conseguido una reducción de un 40% de consumo de gas e incrementado un 30% la capacidad de producción. (Para más información sobre esta referencia: https://new.siemens. com/es/es/productos/automatizacion/referencias/pikolin.html).
n Dashboard de una App de eficiencia energética.

Por último, es interesante comentar que cada día las aplicaciones en la nube están tomando mayor relevancia, y la eficiencia energética es un buen ejemplo del aprovechamiento de estas herramientas en casos de usos reales. En función de nuestras necesidades podremos subir datos a la nube desde cualquiera de los niveles antes comentados y explotarlos en aplicaciones como App Simatic Energy Manager o la App Sirius Asset Monitor, ambas aplicaciones para MindSphere, la solución en la nube de Siemens.
Sirius Asset Monitor para MindSphere La aplicación para la obtención de datos de forma transparente de motores de baja tensión.

Gracias a Simocode Pro-V, y el desarrollo de la App para MindSphe re Sirius Asset Monitor, Siemens ofrece una aplicación con la que se pueden obtener datos de motores de baja tensión de manera transparente en plantas, máquinas o aplicaciones. Simocode Pro-V proporciona información detallada que contribuye a la operación óptima en planta, la planificación eficiente del mantenimiento y la monitorización de la energía. La aplicación permite el acceso al sistema de gestión del motor en cualquier momento y en cualquier lugar. Proporciona al usuario información detallada sobre el estado del equipo, así como mensajes de error y alertas.
La App Sirius Asset Monitor ofrece a los usuarios una visualización de valores como el consumo de energía, la potencia activa o la potencia aparente, pudiendo hacer una gestión de los datos enfocada al ahorro energético, lo que va a permitir gestionar y hacer un uso eficiente de la energía. La aplicación también presenta una imagen clara de los eventos que conducen a fallos y errores, lo que permite la optimización a largo plazo de la operación y el mantenimiento, facilitando al usuario adelantarse a posibles problemas.
n Gracias a Energy Manager Pro, Pikolín ahorra hasta un 40% en consumo de gas en su planta de Zaragoza. Según el tipo de aplicación, el activo se creará en la jerarquía MindSphere Un activo es una representación digital de una máquina o sistema
de automatización con una o más unidades de automatización (p. ej, Simocode con motor) que están conectadas a MindSphere.
La recopilación y provisión de datos de MindSphere se basa en lo que se refiere a un Activo (virtual). Puede ser una bomba, un motor, un PLC, una máquina herramienta completa, una línea de producción, un automóvil o un molino de viento. Los datos de un activo se recopilan y se envían a MindSphere para que estén disponibles para su posterior procesamiento y análisis. Los datos proporcionados por los activos a la App contienen información útil en tiempo real sobre el estado actual de operación y esto ayudará a detectar anomalías en los datos del proceso, lo que permitirá actuar en consecuencia adelantándonos a futuros problemas.
¿Qué funciones ofrece Sirius Asset Monitor? Sirius Asset Monitor puede usarse para monitorizar bombas y otras aplicaciones donde el sistema de administración de motores Simocode Pro-V protege, monitoriza o controla un motor de velocidad fija. Los datos de Simocode Pro-V se almacenan a largo plazo y se procesan sin trabajo de parametrización adicional para proporcionar diagnósticos claramente estructurados del estado actual y los análisis del histórico. La aplicación proporciona funciones y visualización para la parte de diagnóstico, mantenimiento, monitorización de energía y protección de funcionamiento en seco de las bombas. A continuación, se verán más en detalle algunas de las funcionalidades de la aplicación:
Dashboard Es el lugar donde se pueden recopilar y visualizar los diferentes estados de los activos utilizando los widgets disponibles. Los paneles de control proporcionan funciones diversificadas de varios activos y algunos de ellos se enumeran a continuación: � Vista completa del estado de los diferentes activos.
n Vista general del Dashboard de Sirius Asset Monitor.

� Datos centralizados de diferentes activos instalados en las diferentes aplicaciones. � Visión general del rendimiento de los activos a la jerarquía de usuarios.
� Planificar / modificar los períodos de mantenimiento. � Analizar los datos de carga variable. � Planificar las estrategias de gestión de carga.
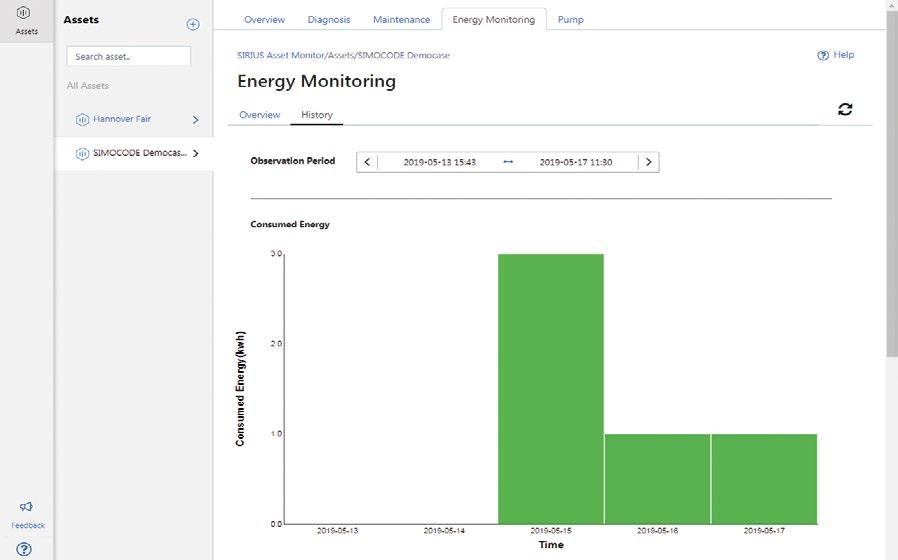
n Paneles de monitorización de la energía.
Monitorización de energía (Energy Monitoring) La pestaña de monitorización de energía proporciona las medidas sobre la energía consumida y valores de las potencias. Se puede controlar el consumo de energía durante el período de tiempo establecido, así como visualizar en tiempo real y también hacer el seguimiento de los datos históricos. Según la potencia activa y los datos de potencia aparente disponibles, puede realizar algunas de las siguientes operaciones:
� Encontrar motores sobrecargados y poder gestionarlos de manera eficiente. � Aumentar la eficiencia energética mediante el uso óptimo de la potencia.
Estefanía Benavente López Product Manager Control y Protección Industrial de Siemens España Diego Muñoz López Product Manager SIMATIC Software de Siemens España www.siemens.es
De la industria 4.0 a la 5.0, centrada en el elemento humano Tendencias 2020 para el sector industrial: persiguiendo la eficiencia
El sector industrial se encuentra ante un contexto repleto de oportunidades que van desde la mejora operativa a los cambios completos de modelo de negocio. Estas oportunidades se han dado en diferentes momentos y sectores, pero actualmente es el sector industrial el que, dadas sus características intrínsecas, puede aprovechar al máximo estas oportunidades.
Las oportunidades para el sector industrial vendrán en su mayor parte dadas por las diferentes disrupciones tecnológicas y por la convergencia del mundo IT y OT, es decir, lo que tradicionalmente se ha entendido como entorno informático con el mundo de las operaciones en fábrica. Esto se dará gracias a tecnologías como el machine learning o el blockchain, la hiperconectividad, el despliegue del 5G o la total implantación de las plataformas cloud. Y
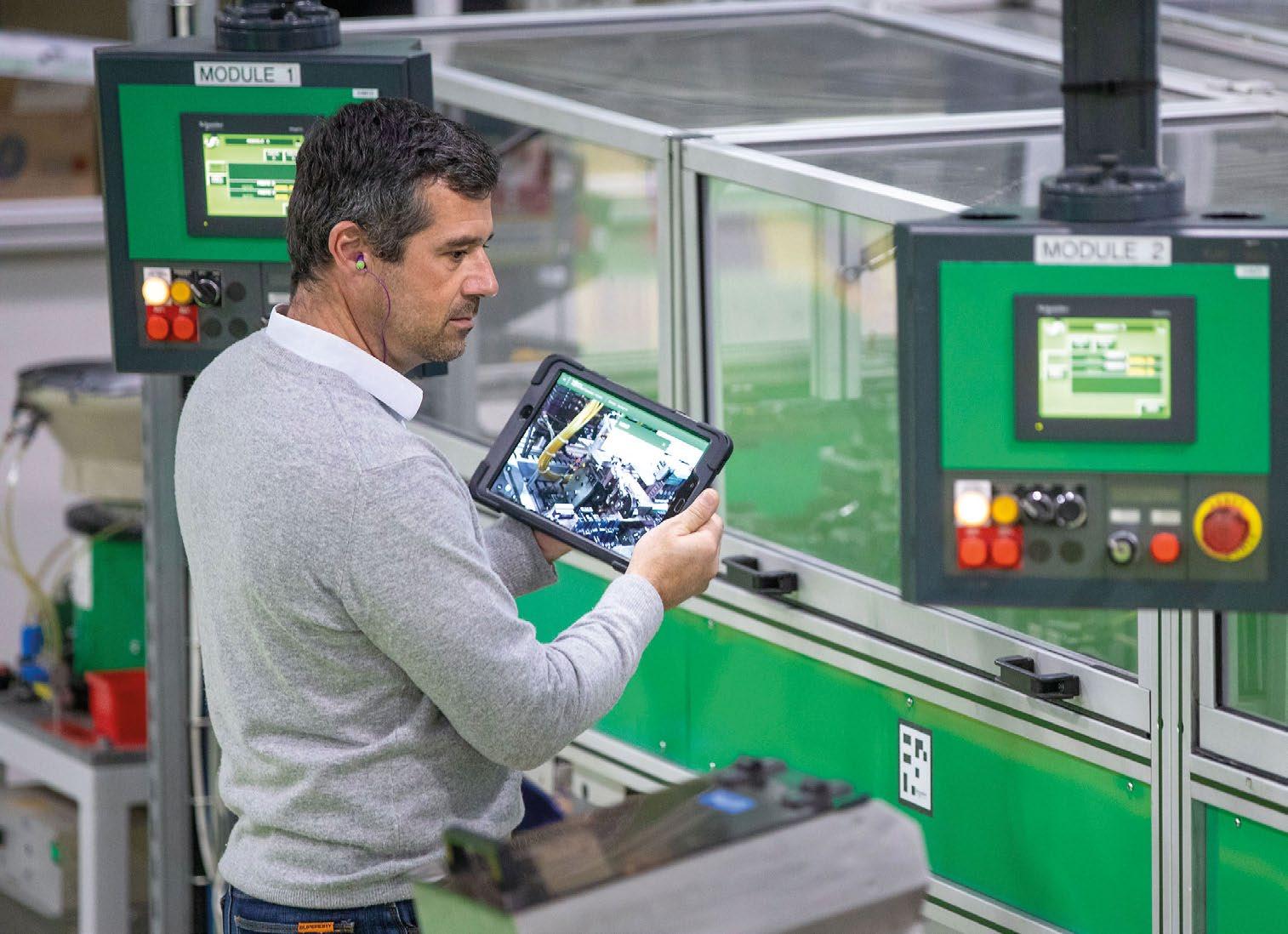
para poder aprovechar y optimizar los beneficios de estas tecnologías, la industria debe poner como prioridad la digitalización.
La irrupción de la tecnología inteligente en las plantas ya está suponiendo toda una revolución
para el sector industrial. Las fábricas inteligentes han llegado para quedarse y entidades como el Digital Transformation Institute de Capgemini prevé que, en los próximos cinco años, estas instalaciones puedan llegar a aportar hasta 1,5 billones de dólares al sector industrial, reforzando los objetivos de crecimiento del sector. En este artículo se destacarán algunas de las tecnologías y estrategias que marcarán la industria este año.
Productividad, ahorro y un mantenimiento más eficiente La realidad aumentada es una de las tecnologías que más está impactando actualmente en el sector industrial. Y se prevé que siga haciéndolo en el futuro. Así, si actualmente el volumen de mercado a nivel global está valorado en 11

mil millones de dólares, se prevé que en 2023 esta cifra ascienda hasta los 60 mil millones.
Esta tecnología ya permite hoy ampliar la visibilidad tanto de máquinas como de procesos, de manera que provoca claras eficiencias y el aumento en la seguridad de máquinas, y más importante aún, de los operarios. En el pasado, cuando surgía un problema en una máquina era necesario apagarla, abrir el armario, localizar la incidencia y buscar la solución en el manual de servicio. Esto suponía períodos de inactividad y pérdidas de producción y rendimiento. Ahora, la realidad aumentada simplifica los pasos y hace que el mantenimiento sea más eficiente y más seguro.
Existen soluciones en el mercado que permiten que el smartphone o tablet del operario reconozcan la máquina y muestran automáticamente en la pantalla los puntos de interés fusionando entorno físico y objetos virtuales. Además, el usuario tiene acceso a datos en tiempo real, diagramas, instrucciones…, con un simple toque. El resultado es una reducción muy significativa de los tiempos necesarios para llevar a cabo las labores de mantenimiento. Abriendo, además, la puerta al mantenimiento preventivo y predictivo, que aún suma más eficiencias.
Maximizar el retorno de la inversión Relacionado también con los activos, este año tomarán protagonismos las estrategias y herramientas relacionadas con la gestión del rendimiento de activos. Esto se debe principalmente a dos motivos. Por un lado, aproximadamente el 70% del capital invertido en una nueva planta es para los activos de producción y su rendimiento es clave para controlar el CAPEX (inversiones en bienes de capital). Por otro, los períodos de inactividad no planeados pueden llegar a suponer hasta un 5% de pérdidas de productividad. Un mantenimiento preventivo será clave para controlar estas pérdidas. Se trata de una disciplina clave para obtener el máximo retorno del capital empleado y puede ayudar a cualquier compañía a alcanzar sus objetivos de negocio, ya que, no solo permite reducir el riesgo, sino que puede darle la vuelta para conseguir mayores retornos.
Sin embargo, contar con un programa de gestión del rendimiento de activos efectivo y orientado a los resultados, pasa por desarrollar una estrategia bien pensada que satisfaga los imperativos generales del negocio. Esta estrategia debe combinar información y datos, con personas, procesos y tecnología y puede hacer necesaria la intervención de analistas y consultores externos que analicen y evalúen el estado actual de la compañía.
En este caso, es importante que los expertos tengan conocimiento de temas críticos para la gestión del rendimiento de activos – estrategias de APM (Asset Performance Management), Objetivos de Rendimiento de Activos, Gestión del Flujo de Trabajo, Inventario y Adquisiciones, etc. – y que entiendan cómo estos aúnan esfuerzos para equilibrar la disponibilidad, el coste, la capacidad, la calidad y el riesgo.
Hoy en día, existen en el mercado soluciones APM completas que permiten conectar todos los activos de la planta – también a la nube, si es necesario. Estas herramientas disponen de analíticas que pueden buscar patrones en los datos y generar conocimiento, lo que permite acercarse al mantenimiento prescriptivo, reducir los costes de mantenimiento en un 50% o ahorrar, de media, un 30% de los costes de energía.
Liderando la eficiencia Por último, deben destacarse las significativas mejoras que cada vez más negocios consiguen gracias a la tecnología inteligente. En este sentido, el Foro Económico Mundial ha destacado a nueve fábricas inteligentes de todo el mundo nombrándolas como claros ejemplos de la cuarta revolución
n Le Vaudreuil cuenta con microcentros de datos que almacenan de forma local los datos críticos de la instalación, permitiendo una mayor accesibilidad y control de la seguridad.
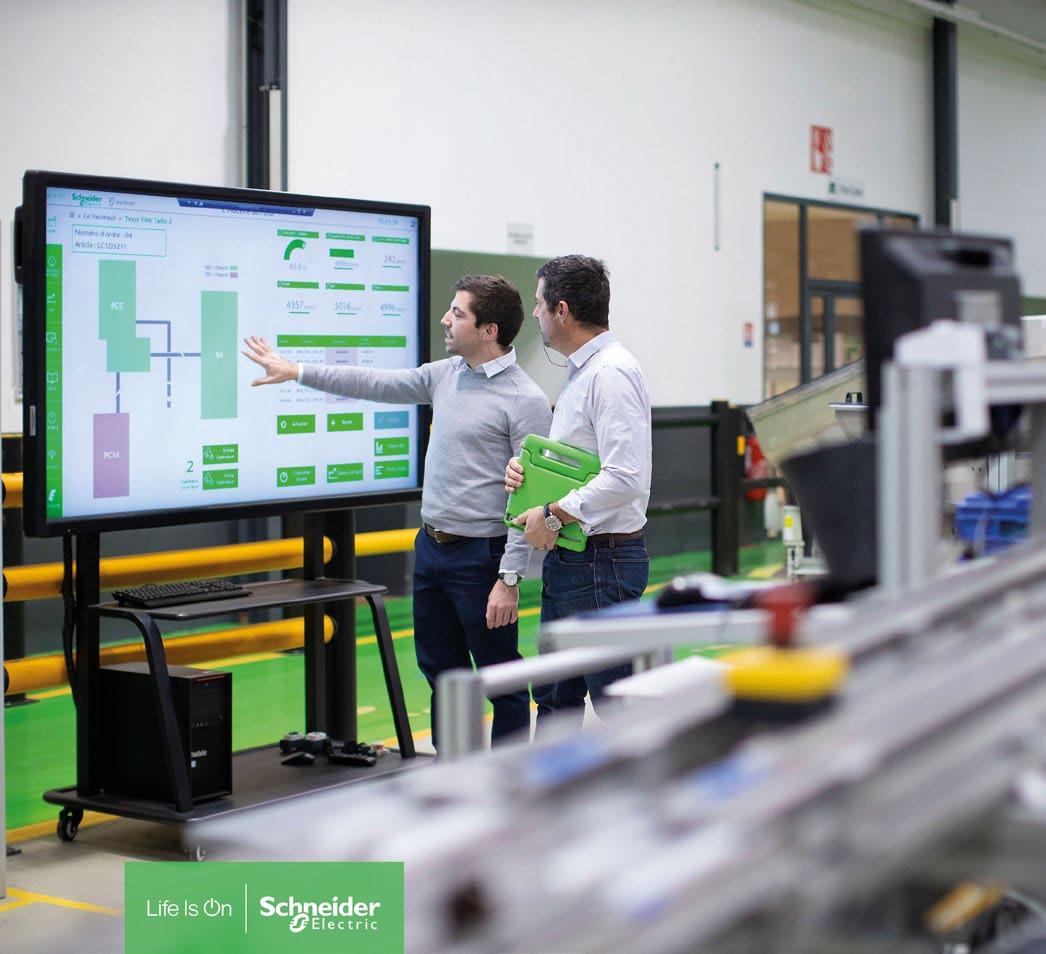
industrial. Se trata de plantas que han desplegado totalmente las tecnologías inteligentes, al tiempo que mantienen a personas y sostenibilidad en el centro de la innovación.
Uno de estos casos es la fábrica Le Vaudreuil de Schneider Electric. Situada en Francia, constituye un ejemplo perfecto de convergencia y automatización. La planta utiliza la arquitectura y plataforma IoT EcoStruxure de Schneider Electric – que conecta tecnologías operativas y las últimas tecnologías de la información – para mejorar y controlar las operaciones. Así, Le Vaudreuil cuenta con microcentros de datos que almacenan de forma local los datos críticos de la instalación, permitiendo una mayor accesibilidad y control de la seguridad. Además, dispone de sensores que monitorizan la maquinaria para predecir las necesidades de mantenimiento y realidad aumentada para acelerar las operaciones y el mantenimiento. Todo ello se traduce en ganancias de productividad del 7% y en ahorros del 30%. El productor de materiales de alto rendimiento Saint-Gobain es otro caso de éxito de maximización de las eficiencias a través de la tecnología inteligente. La compañía utiliza el software basado en la nube para tener una visibilidad total de los datos de energía y sostenibilidad y generar conocimientos que le permitan ahorrar. El objetivo final es, además de ahorrar energía, reducir sus emisiones de CO 2 en un 20% en 2025. En resumen, los beneficios para las empresas asociados a la digitalización ya son una realidad y nadie pone en duda que las innovaciones tecnológicas seguirán marcando el futuro del sector industrial.
De la industria 4.0, que conecta a máquinas y sistemas, estamos a punto de pasar a la industria 5.0, que se centrará en el elemento humano. Veremos cómo los roles de humanos y máquinas se mezclan, refuerzan mutuamente y complementan. La fábrica inteligente, lejos de reemplazarnos, nos empoderará, ya que la contribución humana seguirá siendo esencial para la dirección y el control, así como para la recolección, comparación, análisis y aplicación de los datos. Y no podemos obviar la llegada del 5G. Latencias más bajas harán que las descargas y las respuestas de las aplicaciones sean más rápidas, haciendo que los sensores se expandan todavía más y que las compañías sean capaces de reaccionar en tiempo real. En el sector industrial, el 5G tendrá un impacto especial, ya que facilitará aplicaciones como el mantenimiento preventivo y el control remoto de las máquinas.
Son muchas las tecnologías que aportan beneficios y definen la estrategia del sector industrial, tecnologías que marcan el efecto multiplicador de la convergencia IT y OT. Pero no debemos olvidar que, aunque la tecnología es un habilitador, lo verdaderamente importante es conseguir que la industria sea más eficiente operacionalmente, más eficiente energéticamente y que pueda evolucionar su modelo de negocio hacia uno que aproveche al máximo todas las ventajas que le aporta la digitalización.

Xavier Armengol, Vicepresidente del Negocio de Industria de Schneider Electric en la zona Ibérica
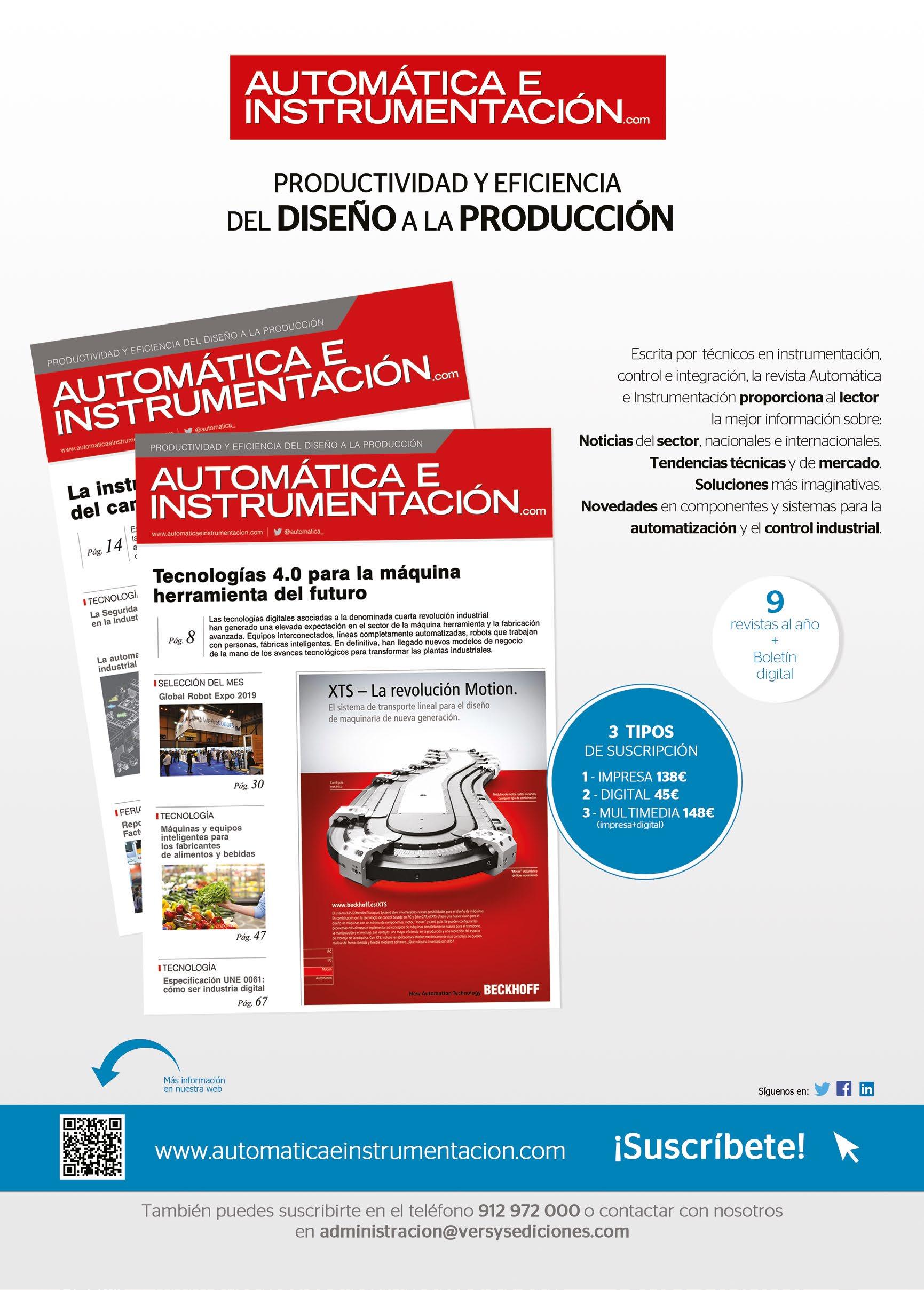
Cabeza fría, corazón caliente
Sostenibilidad. Es indudable que el cambio climático ocupa cada vez más espacio en los programas políticos. Y, ¿es suficiente? No necesariamente: “La necesidad de proteger el medio ambiente está fuera de duda, pero la cuestión es cómo hacerlo”. Así de sincero se muestra Nicola Salandini, director de la planta de Rittal en Italia, sobre lo que se ha convertido en un acalorado debate a nivel global.
n Nicola Salandini, director de la planta de Rittal en Italia, en la Via degli Imprenditori en Valeggio sul Mincio, al norte del país.

Nicola Salandini resume la situación de una forma increíblemente sencilla. Necesitamos sentido común: las circunstancias son demasiado dispares y el debate en los medios de comunicación está sometido a una gran tensión. Con Fridays for Future acercándose al radicalismo, los responsables de la toma de decisiones tácticas adoptando una posición más visionaria y los tecnócratas escondiéndose detrás de pautas y directivas, parece que actualmente solo hay una cosa clara: alguien debería mantener la cabeza fría. Y eso es exactamente lo que están haciendo Salandini y sus 430 colegas en la planta situada en la Via degli Imprenditori en Valeggio sul Mincio, al norte de Italia. La plantilla de la planta de Rittal situada al sur del lago de Garda tiene su propia respuesta al problema climático global: unas soluciones probadas en la industria que están reduciendo el consumo de energía y las emisiones de CO 2 en un 75%. Blue e+, la última generación de unidades de refrigeración se fabrica en Valeggio sul Mincio desde 2015: “Con la serie Blue e+, Rittal ha conseguido crear la clásica situación en la que todos ganan”, explica Marco Villa, director general de Rittal Italia: “Los usuarios se benefician de ventajas a nivel económico y medioambiental y, a su vez, Rittal puede situarse a la vanguardia como fabricante de tecnología de refrigeración ecológica”.
Respetuoso con las futuras generaciones y eficiente En el caso de los refrigeradores Blue e+ de Rittal (sistemas de refrigeración de 1-6 kW) que también se fabrican en Vallegio sul Mincio, la tecnología inverter de
CC es el verdadero punto de inflexión en cuanto a las tan conocidas “diferencias irreconciliables” en el debate sobre el clima. Dado que las velocidades son infinitamente regulables y una válvula de expansión electrónica regula automáticamente la potencia de refrigeración para que coincida con el perfil de carga de la aplicación, solo se genera la potencia que se necesita. Además, el intercambiador de calor de microcanal utiliza un 55% menos de refrigerante; otro avance muy necesario.
Durante décadas, Rittal ha estado comprometido con las medidas que tienen un rápido impacto en lugar de limitarse a hacer declaraciones de intenciones. Marco Villa añade: “Deberíamos recordar que Rittal fue uno de los primeros en pasarse a los refrigerantes sin CFC ya en 1992, con la iniciativa ProOzone. E incluso los equipos con más de 20 años de Rittal cumplen con la nueva normativa sobre gases fluorados de efecto invernadero que entrará en vigor en toda la UE en 2020. De modo que los productos respetuosos con el medioambiente también son válidos desde el punto de vista económico.
La maratón de la industria 4.0 Villa cree que las regiones que realmente están en auge en Italia están al norte de la capital, como la Lombardía, Emilia Romagna, Venecia y la Toscana. Los fabricantes de cuadros eléctricos en estas regiones quieren unos armarios perfectos y unas soluciones de refrigeración eficientes para un uso industrial en la ingeniería mecánica y de plantas, los sectores del petróleo y el gas, y las aplicaciones en el sector de alimentación y bebidas. La industria 4.0 y el futuro no son meras palabras de moda en la planta de Rittal en Valeggio, sino que se están poniendo en práctica de forma muy específica. “Pongamos por ejemplo los refrigeradores Blue e+”, explica Salandini: “Lo más importante, es decir, la opción de conectarse por redes TI con otras máquinas, es ya una realidad gracias a sus interfaces inteligentes. Ya se ha incorporado la tecnología del sensor de control integrado, que resulta esencial para el mantenimiento predictivo”. Desde 2011, cada rincón de la planta de Valeggio sul Mincio se ha convertido en una muestra de la implementación progresiva de la industria 4.0 en las propias actividades de producción de la empresa. El sistema para almacén pick-to-light, que ahora ya es estándar, los vehículos de transporte automatizado en la producción, el control de calidad completamente automático en una de las seis estaciones de ensayo y el empaquetado semiautomático de los refrigeradores son solo algunos ejemplos. Inicialmente todo dependía del factor humano. “Hemos cambiado

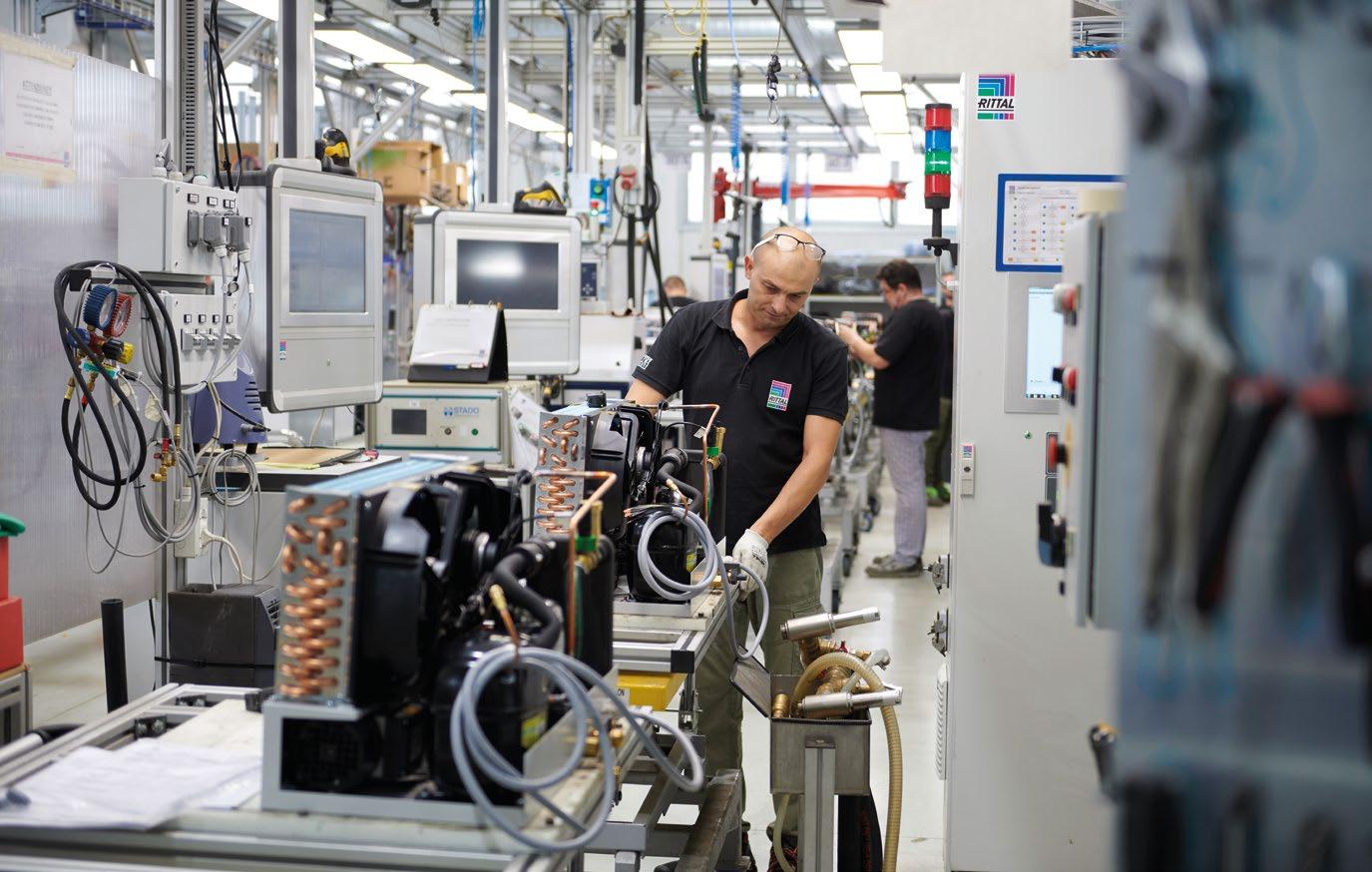
n La plantilla de la planta de Rittal situada al sur del lago de Garda tiene su propia respuesta al problema climático global: unas soluciones probadas en la industria que están reduciendo el consumo de energía y las emisiones de CO 2 en un 75%.
la mentalidad hacia procesos más eficientes”, explica Salandini. “Ha sido como correr una maratón, pero ya hemos conseguido la máxima transparencia y estamos aprovechando al máximo los flujos de trabajo estandarizados”. Salandini debe saberlo más que nadie. Probablemente conoce mejor la planta que la palma de su mano. Como parte de la empresa desde 1993, este licenciado en Administración y Dirección de Empresas de 47 años comenzó en producción antes de pasar a diseño y, posteriormente, asumió la responsabilidad del Departamento Técnico. En 2011 se convirtió en el jefe de operaciones y, finalmente, en director de planta en 2014.
Cuando las máquinas sirven a los humanos La integración en la red internacional de Rittal sigue fascinándole: “Prácticamente cada uno de los pasos del montaje se determina en estrecha colaboración con el Departamento de Ingeniería de Fabricación en la sede de Rittal en Herborn”. Aquí también se tomó la decisión de lanzar un sistema de producción modular para que las nuevas cadenas de montaje se pudieran configurar rápidamente para nuevas series. “Este trabajo en grupo semiautónomo también ha demostrado ser un gran éxito”, afirma Salandini. “Nuestros equipos especializados supervisan las unidades de refrigeración desde el principio del montaje hasta su finalización”, añade. En consecuencia, el acto de entregar unidades semiacabadas a otros empleados, así como la responsabilidad, es ya cosa del pasado.
De hecho, la capacidad de producción se ha triplicado en los últimos ocho años. Salandini está realmente orgulloso de la digitalización sistemática de la producción. “Estamos construyendo una línea de producción física y digital de forma paralela al montaje de las unidades Blue e+”. A nivel práctico, unas grandes pantallas táctiles guían al personal a través del trabajo de montaje. Por ejemplo, en este caso se utiliza Eplan Smart Wiring, una solución de software de la empresa Eplan, asociada a Rittal. Este software muestra el cableado, con todo el trazado de los cables y los pasos de montaje. En cuanto se conecta una conexión correctamente, se enciende de color verde según el sistema de semáforo. La pantalla digital en el Eplan Smart Wiring hace referencia al diseño en 3D del modelo virtual en Eplan Pro Panel (software de ingeniería para los diseños en 3D de armarios de control, conmutadores de alta tensión y sistemas de distribución de potencia), que permite comparar continuamente el objetivo con la realidad.
El resultado final es que la visión de los pioneros de la industria 4.0 por fin está llegando a buen puerto. Mientras que antes los humanos servían a las máquinas, la relación se ha invertido: ahora son las máquinas las que sirven a los humanos.

En la compañía Nestelberger de Perg (Alta Austria)
Yaskawa automatiza una fábrica de procesamiento de cereales
Mucho antes de que el grano se convierta en harina para hacer pan y pasteles, debe pasar por una serie de pasos y estaciones de trabajo entre el campo y la panadería. Visitamos la fábrica de descascarillado y almacenamiento de Nestelberger en Perg (Alta Austria) para analizar más de cerca su solución de automatización basada en componentes Yaskawa.
n Fábrica de descascarillado y almacenaje a la que Yaskawa ha aportado una solución completa de automatización.
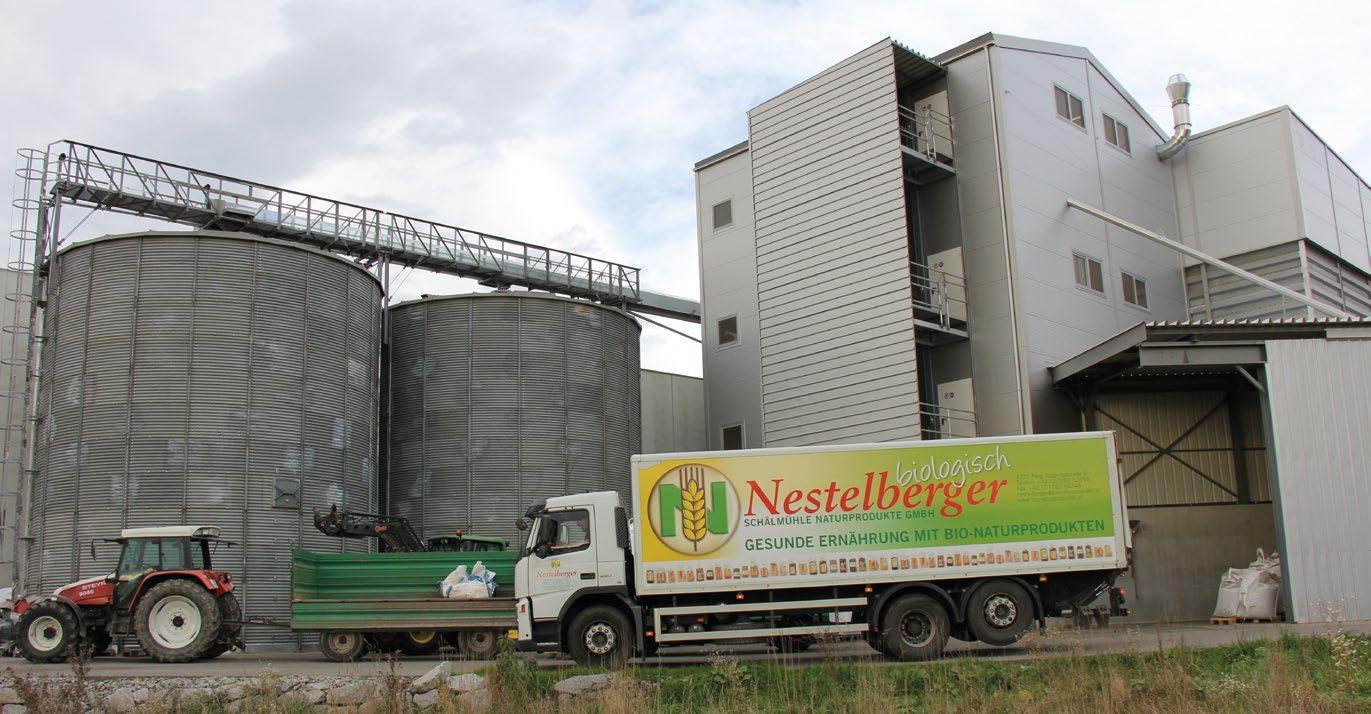
Después de cada cosecha, las instalaciones de almacenamiento de la fábrica de descascarillado de Nestelberger están completamente llenas de cereales orgánicos. “Tenemos alrededor de 2.500 toneladas de espelta, trigo, cebada, avena..., almacenadas en 24 contenedores”, explica Peter Pilsl, gerente de producción de la fábrica de descascarillado Nestelberger.
Pero antes de llegar a esa etapa, los granos se someten a una serie de pasos de procesamiento: el grano entregado se introduce en el molino, se limpia (se eliminan piedras, malezas y cualquier otra cosa que se haya podido acumular durante el proceso de cosecha) y se pesa. Durante los procesos de limpieza y pesaje, el grano vuelve a caer donde se descascarilla y/o transporta para almacenarlo en los silos correspondientes.
Comprender el proceso completamente es crucial para poder implementar un sistema de automatización óptimo en una planta de producción de este tamaño. Andreas Stingeder, de la empresa de instalaciones eléctricas Mesta, fue el responsable de todo. Desde la planificación, la construcción del gabinete de control, el cableado y la programación hasta la visualización y la puesta en marcha. Durante las etapas de construcción y puesta en marcha, Stingeder también participó en la gestión de la fábrica de descascarillado para “sumergirse completamente en la vida de la planta de producción”. Ahora el operador del molino puede ajustar todos los parámetros relevantes utilizando el sistema de visualización del software “zenon” de Copa Data. Primero, se selecciona el tipo de grano y luego, el proceso deseado (descascarillado, almacenamiento o relleno) se puede especificar de manera fácil e intuitiva con solo unos pocos clics. Una vez que se ha establecido la secuencia deseada para el grano, el operador inicia el proceso con el botón “Inicio” y el molino comienza a funcionar. La persona responsable del molino ahora tiene una tarea considerablemente más fácil y puede operar el molino con una sola mano, ya que está totalmente automatizado.
Implementación El hecho de que un sistema tan complejo pueda funcionar de una manera tan simple se debe en gran medida a los componentes de automatización utilizados. “Este fue el primer proyecto que implementamos conjuntamente con Vipa Elektronik-Systeme GmbH, un histórico socio de distribución de Viena. Para mí, las soluciones proporcionadas por Yaskawa fueron la opción más lógica y se adaptaron a nuestros proyectos desde el principio. No hubo problemas con estos componentes en ningún momento”, apunta Andreas Stingeder.
“Sin embargo, con el tiempo los componentes requeridos se volvieron más complejos. Inicialmente, solo consideramos un controlador. Pero, tras debatirlo, nos dimos cuenta de que había interfaces adicionales que podríamos desarrollar conjuntamente”, agrega Martin Zöchling, director y gerente del socio de distribución de Yaskawa Vipa Elektronik-Systeme.
Esto se debe al hecho de que el cliente no tenía claros sus requisitos de automatización al comienzo del proyecto. “Con el tiempo, el alcance de la automatización se hizo evidente. Ahora confiamos en Vipa Elektronik-Systeme para todos nuestros componentes Yaskawa, desde controladores hasta tecnología de accionamiento. La ventaja es que todo proviene de una sola fuente. Lo principal que impresionó al cliente fue el servicio de Vipa Elektronik-Systeme con sus socios de contacto competentes y tiempos de entrega rápidos”, dice Stingeder. Los detalles más precisos El molino de descascarillado Nestelberger se divide principalmente en dos áreas. En primer lugar, la planta de silos para el almacenamiento del grano y, en segundo lugar, la planta de descascarillado. Ambas secciones de la planta están controladas por una “CPU Vipa SLIO 015” con expansión de memoria. El controlador es, por lo tanto, responsable de todos los motores de transporte, tanto verticales como horizontales, así como de transportadores de tornillo, válvulas de dosificación, controladores de nivel de llenado y detectores de contacto en las válvulas de compuerta. El controlador también está equipado con una conexión Ethernet para visualización mediante zenon.
“La comunicación se transmite generalmente a través de Profibus, aunque los variadores de frecuencia Yaskawa son compatibles con todos los sistemas de bus comunes”, explica Zöchling. Se utilizan un total de tres unidades de variadores Yaskawa de la serie V1000 para controlar las unidades. Los variadores de frecuencia de esta serie no solo impresionan por su tamaño compacto, sino también por su electrónica extremadamente robusta y su potente rendimiento. “Estos variadores son extremadamente robustos. No hay ningún problema con los cortes de energía o el desprendimiento de carga después de una parada de emergencia. He visto muchos otros variadores que no pudieron soportar tales presiones “, dice Stingeder.
“La robustez de estos variadores es directamente atribuible a las generosas dimensiones de las unidades de potencia y sus vastas reservas; esto significa que pueden resistir mucho”, agrega Zöchling.
Stingeder ha incorporado mensajes de error basados en texto en el sistema de visualización zenon para cualquier problema que pueda ocurrir durante la operación del sistema. Esto muestra inmediatamente dónde se produjo el error y alerta al operador de la planta. Solución completa “Los productos Yaskawa fueron la solución ideal para este proyecto. Ciertamente volveré a usar estos productos en el futuro, por el momento no puedo imaginar usar otros. Pero no solo los componentes son impresionantes, si tengo alguna pregunta, puedo llamar a Vipa Elektronik-Systeme y obtener respuestas inmediatas y sugerencias de soluciones por personas de contacto competentes”, resume Stingeder.
El molino de descascarillado completa su configuración técnica con una solución de mantenimiento remoto equipada con un “Enrutador de Teleservicio Vipa TM-C”. Esto permite a los gerentes de la fábrica de cascos Nestelberger consultar todos los datos de producción y los estados de las plantas a través de Internet o dispositivos móviles. Yaskawa www.yaskawa.es n Se utilizan un total de tres unidades de variadores YASKAWA de la serie V1000 para controlar las unidades.
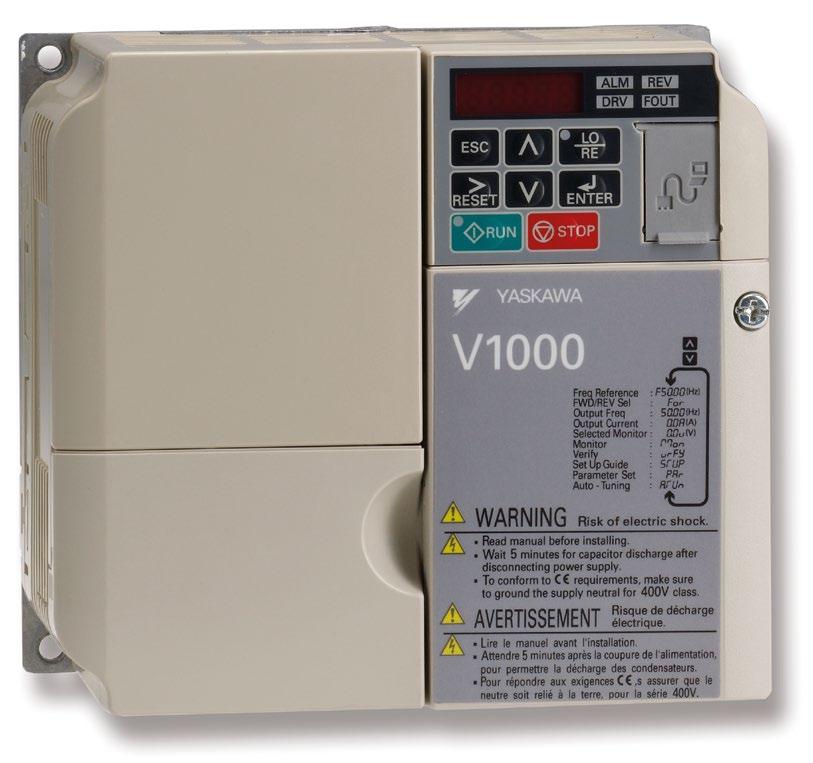