Material Guide
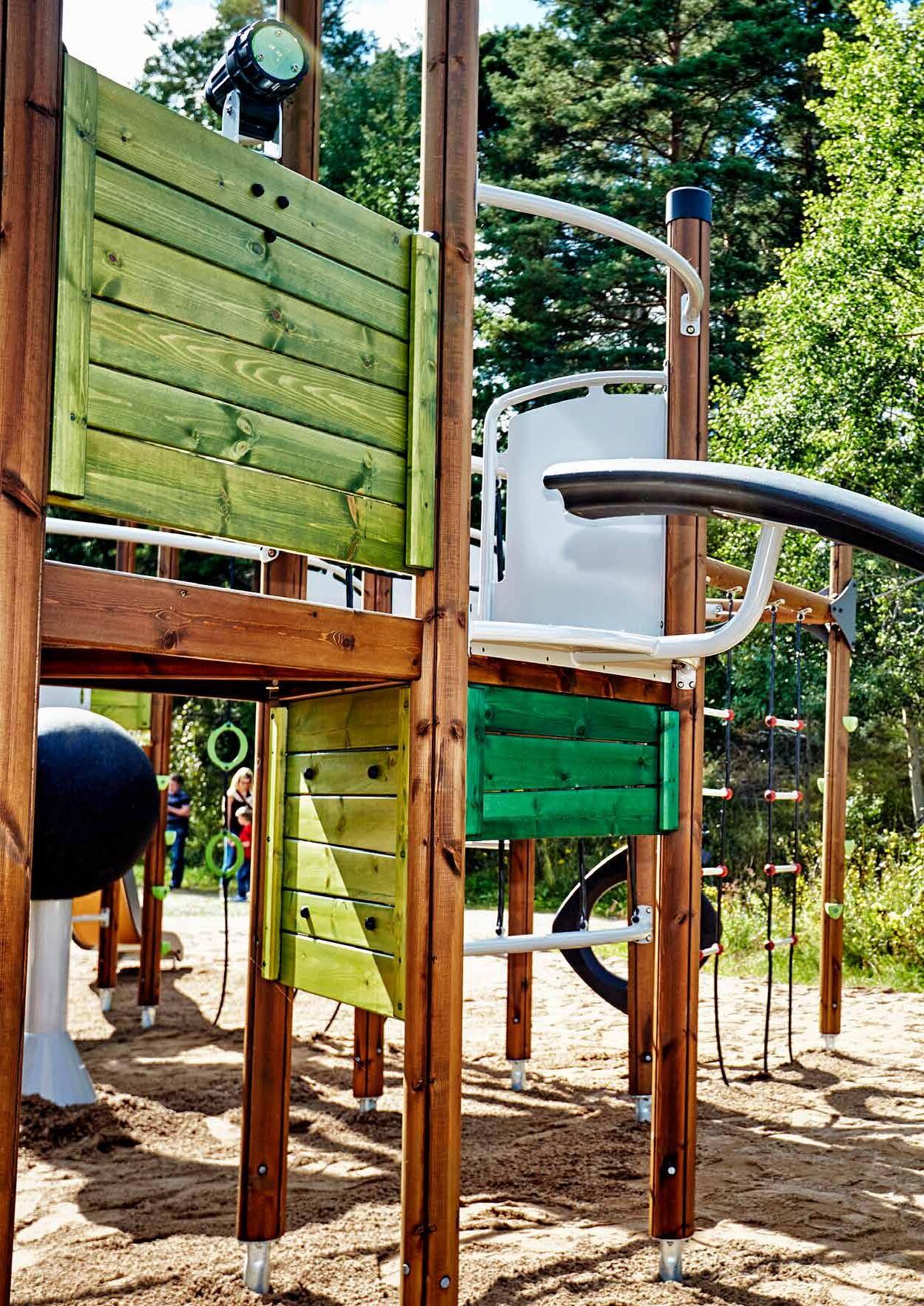
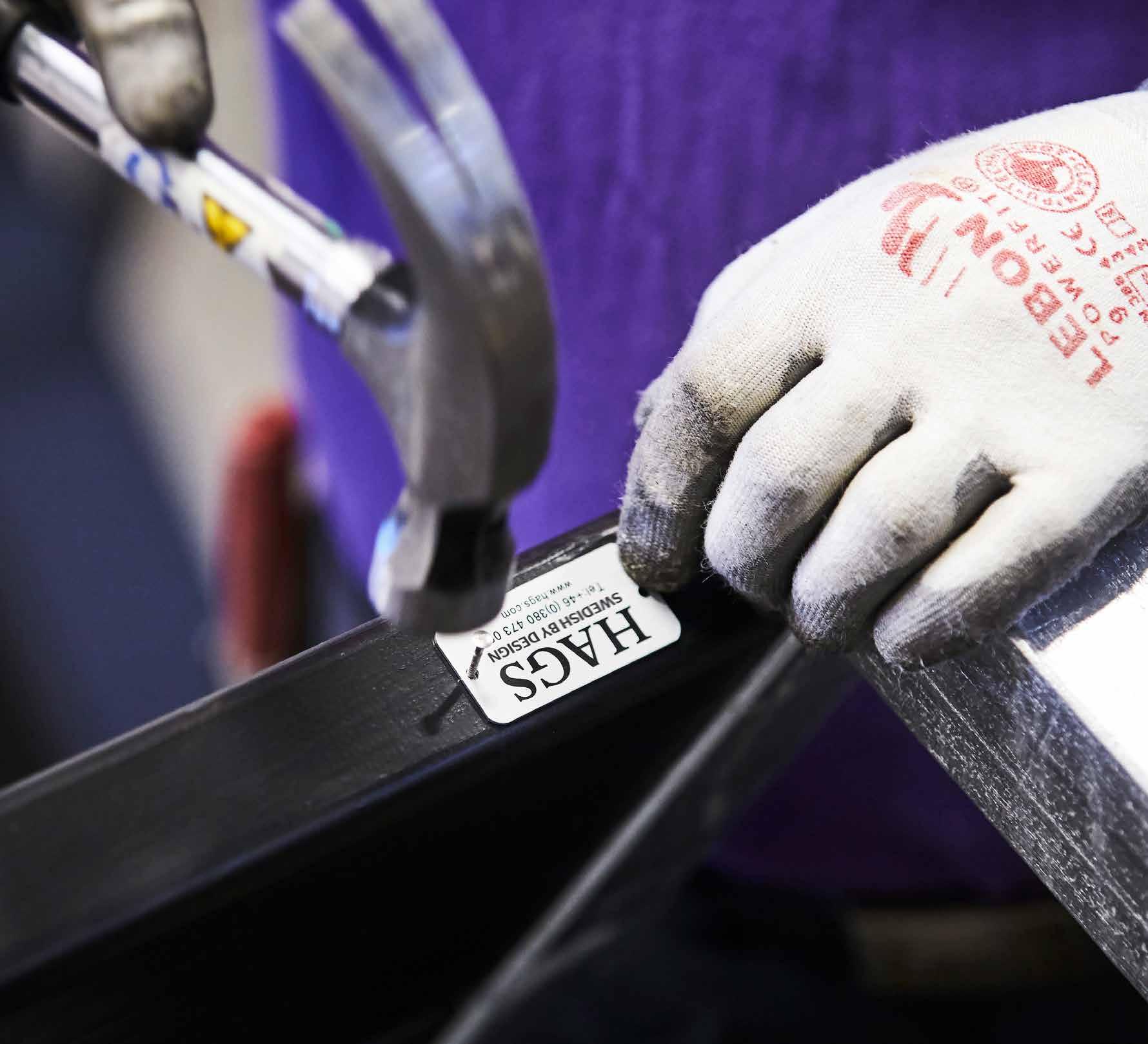
Introduction
HAGS design and manufacture commercial play, sports, fitness, and furniture products to enable our customers to develop inspirational indoor and outdoor spaces that people want to use. We develop solutions for municipalities, schools, housing, retail, hospitality and infrastructure along with many other market segments where high quality and attractive equipment is an important criteria.
As our products are installed globally in public areas and in a wide variety of climates, we take time to choose materials that are robust and long-lasting, while trying to reduce our environmental impact with the choices we make.
Within this document, we highlight some of the key materials we use, the properties that they have and the processes they undergo to ensure a high-quality finish.
Quality matters
Since HAGS started in 1948, quality has been a key principle in our company culture. We strive to provide a quality service as well as quality products. We are a certified company according to ISO 9001 and ISO 14001.
Our playground equipment is third-party certified by TŰV, in accordance with the European standard for “Play equipment and surfacing”, EN 1176. Our outdoor Fitness products are certified according to EN 16630, Multisport Arenas are certified to EN 15321, and Parkour according to EN 16899.
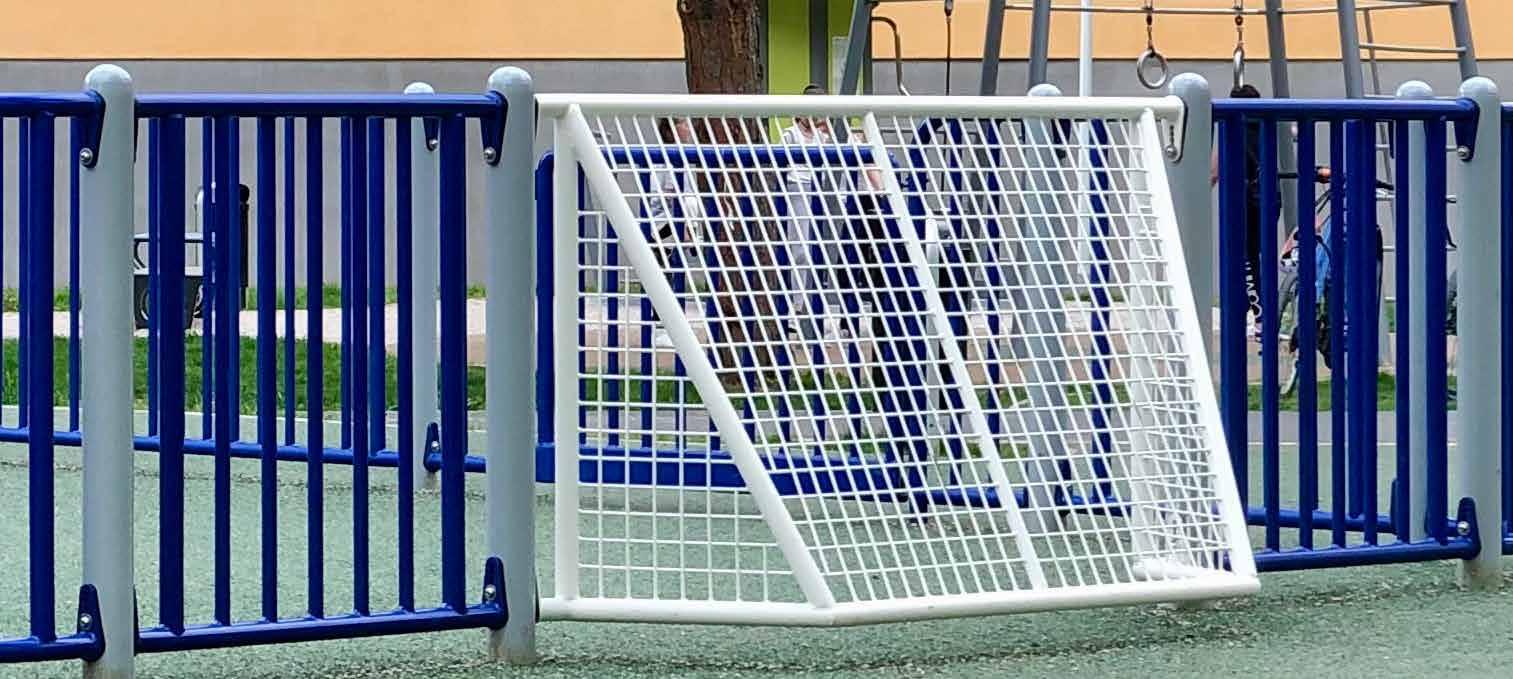
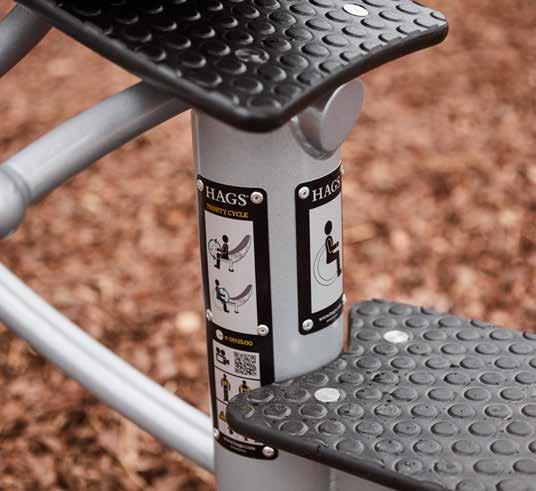
We work closely with our suppliers to ensure that all materials meet current legislations, such as REACH and other EU regulations, as well as being in line with our own environmental and sustainability goals. We always strive to choose materials with a low environmental impact, and we use plastics that are 100% phthalate free.
For information on recycling materials, please see the document "Inspection and maintenance Guidelines for HAGS playground equipment" on our website.
hags.com

Wood
We use a variety of high-quality wood in our equipment depending on the product and requirements. The largest proportion of wood that we use is Scandinavian dense pine due to its natural resistance to rot and fungal attack. Its composition also makes it a great building material and has been successfully used in our UniPlay and UniMini play systems for over 50 years.
Our wood-cutting process is entirely computerised and reduces the amount of waste.
Our triple laminated timber poles are composed of three sections joined together, a method that increases strength and reduces cracking.
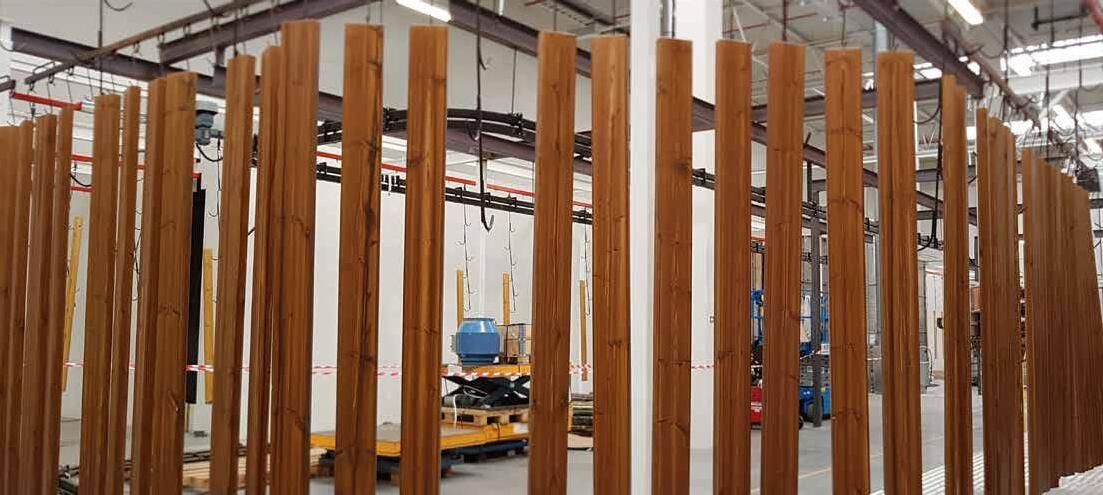
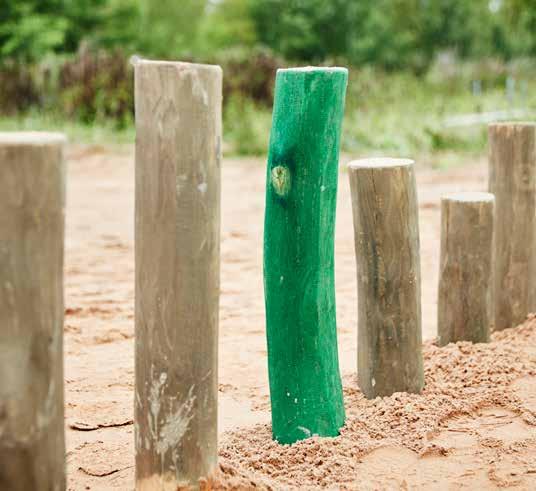

The timber is then treated with preservative, wood stain coatings to provide additional protective layers and a smooth finish. We only use water-based biodegradable coating materials, which don’t have a negative impact on the environment.

Wood is a naturally renewable material; therefore, it has a low environmental impact. Cracks and some deformation in the wood is expected as the material adjusts to different environmental conditions.
The other types of wood which are present in some of our products are mentioned below:
Jatoba and Bilinga are tropical hardwoods that also have great durability and are only used on very few of our components to meet particular customer requirements.
Accoya, a fast-growing sustainable wood, is also used in a number of our products. Accoya has some excellent properties, including high rot resistance and the ability to maintain stability with change of temperature.
Robinia, also known as false acacia, is a sustainable hardwood that grows in plantations; it's predominantly used in our Nature Play product line.
All our supplied wood is certified according to FSC or PEFC. HAGS is continually reviewing its wood species and supply chain to ensure we continue to use the most sustainable reserves.
Surface treatment wood
All our Scandinavian pine wood components are treated with one layer of wood preservative (In accordance with EU Regulation 528/2012); this not only gives it a nice finish but also protects against rot and mould infestation, and increases the lifespan of the product. This is used throughout our portfolio.
At HAGS, we use different processes depending on the product and treatment type required.
These are all based on 3 steps;
Step 1 – Preservative (According to EU legislation)
Step 2 – Basic Glaze (In some cases a cover glaze)
Step 3 – Top Glaze (Up to 2 layers depending on area of application)
The components are hung on a conveyer which transports them through different spray booths (as per the steps mentioned previously) and sprayed with the respective treatment, being quality controlled, to ensure the final coating provides the required preservative and durability efficacy.
For each process we use water-based liquids containing biodegradable enzymes.
Products made of hardwood (such as Bilinga) are delivered either untreated or treated with a finishing oil.
The environmentally friendly processes that we have in place means that all wood from HAGS can be reclaimed for recycling or energy recover.
HPL and wood-based board
According to EN 438-6, high pressure laminate (HPL) is a sheet of material made up of about 60% cellulosic fibre (paper) and about 40% phenolic resin (thermosetting plastic) which is compressed under high pressure and heat. As well as meeting this regulation, our HPL material also meets the formaldehyde emission standard E1.
This tough and dimensionally stable material has very good strength properties. Furthermore, HPL is moisture resistant, resilient to scratches and other deformations, needs very little maintenance, is easy to clean, and has a long lifespan, even in the outdoors.
The top layer consists of melamine (thermosetting plastic) plus a transparent UV protective film to minimize colour change during outdoor exposure. The surface can also have an embossed texture either for decorative or safety reasons, such as to reduce the risk of slipping.
All our HPL can be reused, recycled or used as energy recovery.
Plywood
Plywood is a board of layered wood made up of several veneers that are laid alternately across the direction of the grain and glued together with a phenolformaldehyde glue that provides strength, durability and protects against moisture.
We use a multilayer birch plywood which can sometimes have a layer of phenol (thermosetting plastic) to further protect the board from moisture penetration, impact and wear. In some cases, the surface may also have an embossed texture to control the risk of slipping.
When the plywood has no extra surface layer, and when milled edges are found on the product, the entire plywood is painted, to prevent moisture penetration.
Our plywood components are currently being phased out and replaced with HPL as this material has far greater durability.
All our plywood can be reused, recycled or used as energy recovery.
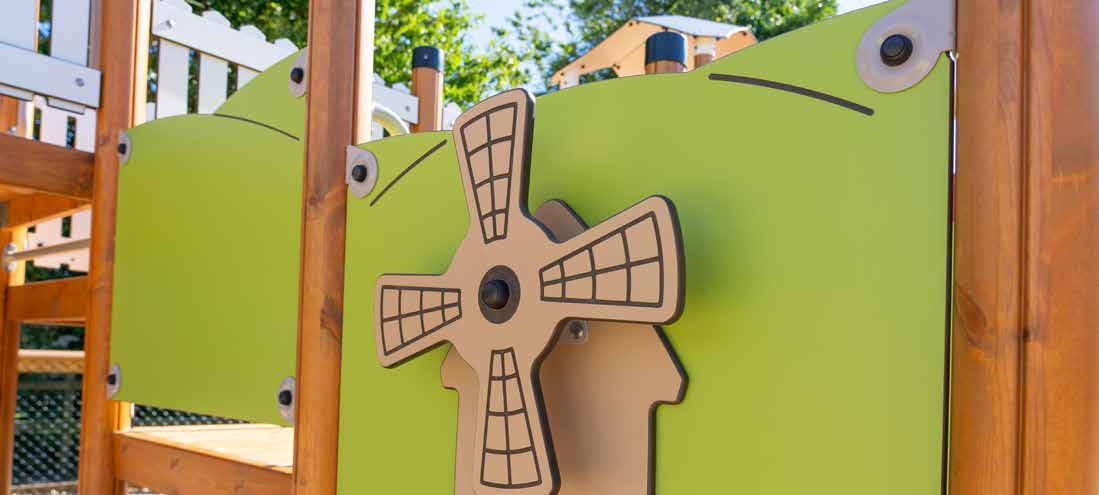
Steel
Steel contains a high percentage of recycled material, which means that the environmental impact is relatively low. It’s also a material that has established recycling systems in most countries.
Stainless steel
We mostly use stainless steel of EN1-4301 (304) quality. A pattern-rolled sheet is used for some sections of playground slides as the pattern helps provide additional strength to the sheet and allows a thinner section to be used.
Steel
There are two processes used for shaping steel, hot-rolled and cold-rolled. Hot-rolled steel gets its final shape in a hot (glowing) state. This means that the steel has a so-called scale on the surface. Any scale can be removed by blasting or pickling.
In contrast, cold-rolled steel gets its final shape once it’s cold and the scale has been removed. This gives the material high strength, good formability, and a smooth surface.
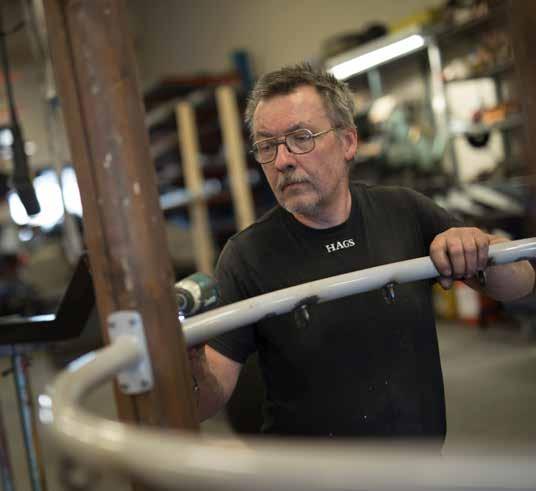
We select the most appropriate type of steel depending on the size and strength properties needed for the product.
HAGS uses steel with a yield strength of 220 - 600N / mm2 and carefully selects the right quality for each application. We only use steel with excellent weldability to ensure that our products have the required strength and durability.
We also ensure that the content of silicon and phosphorus is controlled in order to achieve the desired appearance and thickness.
Cast iron and cast steel
Cast iron or cast steel is used when it’s suitable from a production and functional point of view. We carefully select the right material grade depending on its purpose, and we also use Gray iron, ductile iron and cast stainless steel where appropriate.
Other metals
Aluminium
Aluminium can be found in many of HAGS’ products, such as ladder rungs and sliding poles. In extruded profiles, we use material with an EN AW6060 T6 quality. The most common surface treatment is natural anodizing 20μm. Powder-coated goods and anodizing are used as surface treatments on die-cast goods.
Aluminium contains a high proportion of recycled material, and most countries have an established recycling system for this material. This, plus the fact that it has a high recycling efficiency rate as it can be recycled many times, results in aluminium having a low environmental impact.
Surface treatment steel
Protecting steel products from moisture and oxygen and thus preventing the risk of rust, or in more technical terms, corrosion, is important for function, safety and appearance.

Therefore, using well-proven methods of surface treatment on our products is key. The best process is selected depending on the product to achieve the optimum balance, between appearance, corrosion resistance and abrasion resistance. Here, we highlight the treatments that we use.
Hot dip galvanizing
In hot-dip galvanizing, the entire steel part, which is to be protected in molten zinc, is dipped at approx. 460°C. This means that both external and internal surfaces will be coated with a 35 - 300μm thick layer of zinc that is metallically connected to the steel.
The thickness of the layer is primarily determined by the type of steel base chosen. The zinc that we use is of high quality (special high grade), and the whole process complies with EN-ISO 1461 and 14713-1.
We classify hot-dip galvanized surfaces into three categories: A, B, and C. Class A is the highest and it’s used for clearly visible surfaces, such as on HAGS’ furniture. Class C is used on steel that is under ground, it's not visible but needs good rust protection to fulfil its function for a long period of time.
Electrolytic zinc nickel coating
HAGS uses zinc nickel with a thickness of at least 8μm which has a rust protection ability that is about 4-5 times better than ordinary electric galvanizing of the same thickness.
The product is dipped in a tank and, with the help of electricity, the metal is bound to the steel, creating an outside layer that provides protection against corrosion.
Smaller parts, such as fasteners, are placed in a rotating barrel and follow the same process. The colour of our zinc nickel coating is usually shiny silver to matt grey, although some parts can also be black.
Powder coating
We have a state of the art powder coating plant where we can handle a large number of different colours. The process includes both automatic and manual controls, and tests that ensure a high and consistent quality.
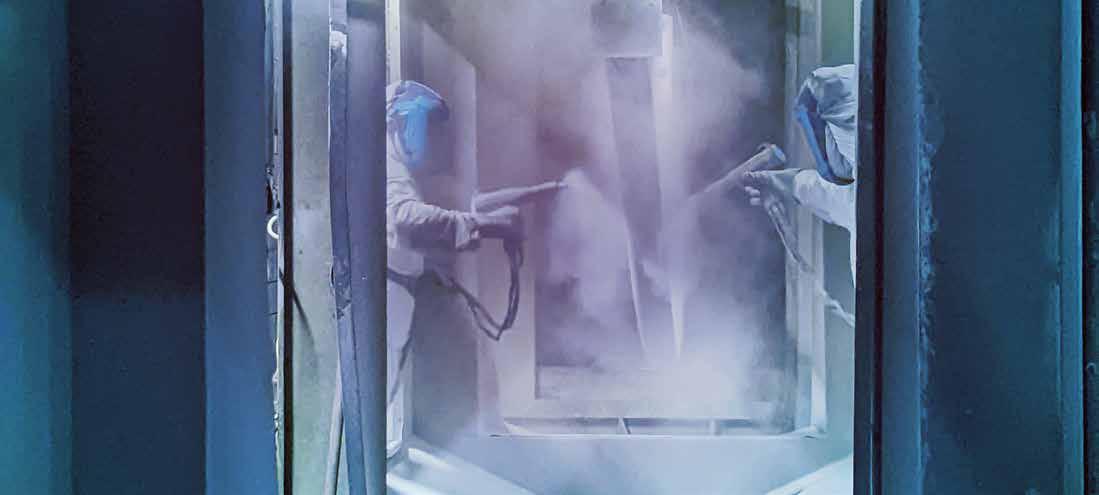
We work with a specialist global supplier of different powder coating systems and are audited as an ‘Approved Applicator’. With their support we can also offer some additional options on certain products, such as an anti-microbial top coat or a ‘Triplex’ layer system. The triplex layer can help support durablity of products in harsher environments such as coastal locations.
The five-step process described below is for our standard coating system.
Step 1 – Blasting
All items go through what’s known as a shot blaster, where all external surfaces get the right surface texture and are free from contaminants. This prepares the metal to ensure maximum adhesion on the subsequent steps.
Step 2 – Application of primer
The parts are coated with an epoxy-based primer with a minimum thickness of 60μm. The primer is electrically charged and then applied to the steel parts with 10 automatic guns. In addition to this, there are two manual booths that are used to paint folds and welds that may need extra protection, or where the automatic booths find difficult to access.
Step 3 – Curing
The primer (powder) is melted in an oven at 185°C.
Step 4 – Application of top colour coat
This polyester-based top colour coat is applied in powder form with a minimum thickness of 70μm. We use an outdoor quality powder that provides resistance to UV radiation.
Step 5 – Curing
The products are cured at 210°C to give the coating its final finish. A colour change takes about 8-10 minutes, and our operatives make about 5 colour changes per day. The conveyor is 185m long, has 64 beams and can handle items measuring 4000 x 1600 x 700 mm.
It takes about 3 hours for a product to go through the whole process. The final coating system provides the optimum combination of an aesthetically appealing colour as well as excellent corrosion and abrasion resistance.
EcoArmor
On some specialist products, HAGS also uses an EcoArmor coating which has a greater thickness to provide increased mechanical and anti-slip resistance.
Fasteners
Fasteners are the collective name for all types of bolts, nuts and rivets available from HAGS. Our fasteners always have an important function to fulfil in our products, so we place great emphasis on having the right type and high-quality fasteners.
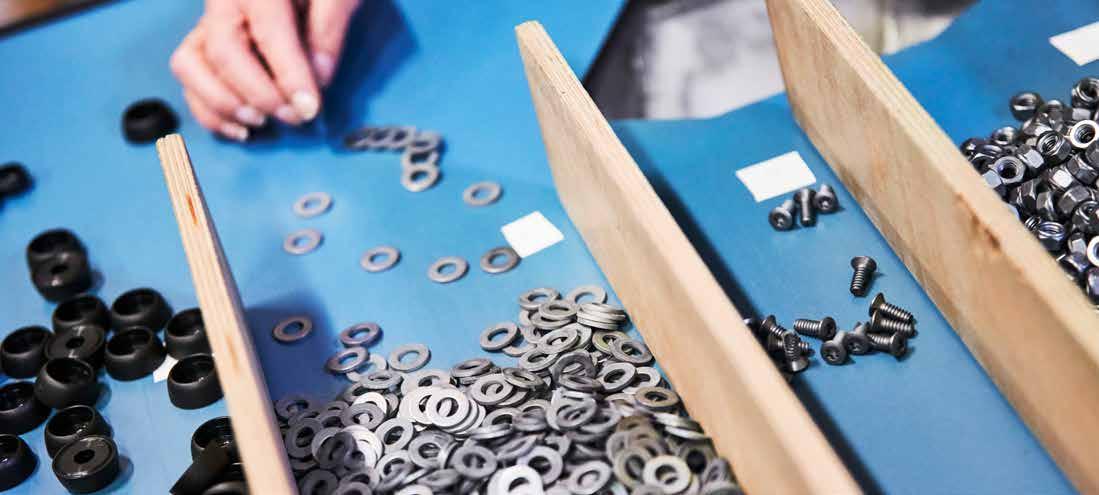
Machine threaded bolts
We use a variety of steel bolts with different grades of strength, which are carefully chosen depending on their purpose. If steel is specified, then they are surface-treated electrolytically with zinc or nickel (thickness layer of at least 8μm), giving them excellent anti-corrosion properties.
On some nuts, there is metal locking or locking fluid. In some cases, there is also a barbed washer to prevent it from loosening accidentally. Our range also includes stainless steel bolts and nuts of grade A2.
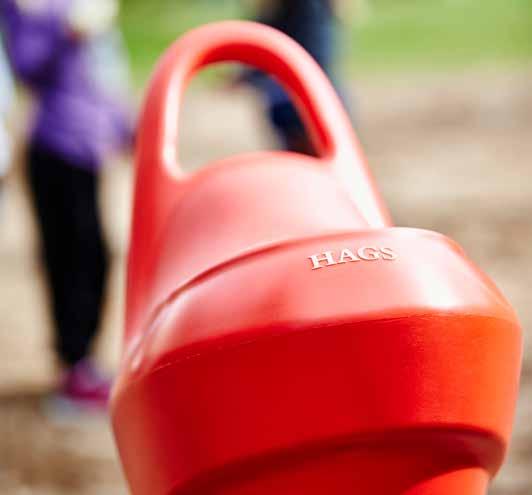
Furthermore, to prevent tampering of fasteners and to avoid the risk of vandalism, in many cases cover caps are provided on bolts and nuts.
Flat washers
HAGS primarily uses steel washers with a hardness of 2-300HV that comply with ISO 7089 and ISO 7092. These are surface-treated electrolytically with zinc or nickel (thickness layer of at least 8μm), giving them excellent corrosion-protective properties.
The strength of the washer is important in order to give the entire joint the same high durability and quality. Our range also includes stainless steel washers.
Rivet (blind rivet), Blind rivet nut
We use blind rivets in either stainless steel or aluminium. Our blind rivet nuts are made of galvanized steel.
Wood screws
These are made of SAE 1022 SAE 1018 quality material which has been surface hardened to get a tough core and a hard surface. All our wood screws have a zinc or nickel surface treatment layer for a high quality and longer lasting finish.
Plastic
Plastic is available in many different variants, as highlighted below. To extend our products' life, all our plastics have UV protection against colour fading and embrittlement, due to the sun's rays. Some plastics have also been modified to increase strength and counteract squeaks.
Polyethylene, PE
Polyethylene is the most common type of plastic in our society and there are established national recycling systems in place. At HAGS, we have broadly divided this plastic into three graded categories: high density (HD), medium density (MD) and low density (LD). LD and MD are generally used in HAGS’ rotationally moulded parts, while HD is generally used in injection moulded parts and board materials.
Polyamide, PA
Polyamide, or commonly known by the trade name Nylon, is a tougher plastic that is often used in areas with a mechanical stressed construction. It is available both with and without reinforcement. The reinforcement can be things like fiberglass or Teflon. Examples of where it can be found are in HAGS’ cover caps, fastening details and in certain bearings.
Polypropylene, PP
This material often offers a good compromise between price, producibility and durability. It is available both with and without reinforcement, which can be fiberglass. Polypropylene has good weather resistant properties and is great against pressure, so it’s often used for hinges. This material can be found in HAGS’ injection moulded covers and some boards.
Polyurethane, PUR (solid)
Polyurethane is a two-component plastic that is also called an elastomer. It is a very durable and flexible material, and it’s therefore used in places that are subjected to a lot of stress, with high wear and tear. This material can be found in components intended to dampen the stress from moving parts or where flexibility and high abrasion occur.
Polyurethane, PUR (foamed)
This multi-component plastic undergoes fermentation during the manufacturing process to form air bubbles inside the material; giving it a porous core and a smooth surface. This material is very suitable for parts that need an impact-absorbing function, so it can often be found in HAGS’ seats and handles.
Thermoplastic elastomer, TPE
This is a rubber-like plastic that can be injection-moulded and sometimes also used together with a harder PP type plastic. TPE has very good abrasion properties as well as being flexible, so it can be used for applications requiring shock absorption.
Recycled plastic
‘EcoGrip’ is an example of recycled plastic used at HAGS. This environmentally friendly material consists of 89% recycled polyethylene with a 2mm thick layer on one side. Furthermore, we also use recycled polyethylene slats for some of our furniture range. Plastic-based components can be sorted and sent to recycling.
Rubber
Available as both synthetic rubbers (EPDM or SBR), and natural rubber. Rubber is very good at absorbing vibrations and dampening movements, therefore it is commonly used as impact dampers where a flexible material is required.
Some of HAGS’ swing seats are made of recycled car tyres, which in turn are made of both natural rubber and synthetic rubber. Our use of recycled tyres provide an opportunity to give them a second life.
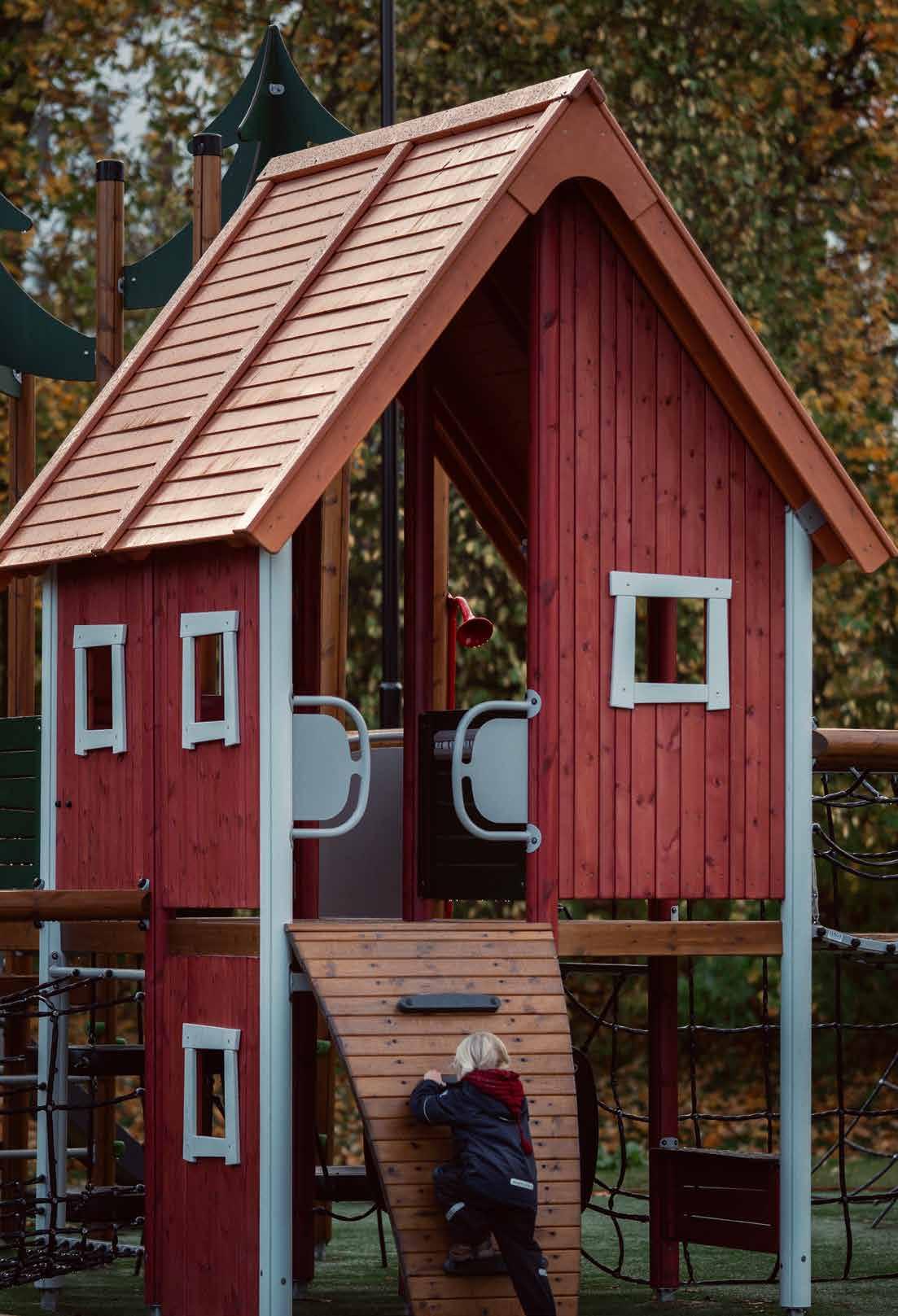

To make sure our products are safe and of high quality, we only select tyres which were originally manufactured after January 2010 to ensure they comply with REACH requirements.
Concrete
The concrete parts we supply are standard precast concrete. In some larger products, as well as in products with higher requirements for strength, the concrete is reinforced. Concrete is supplied in precast ground foundations, where these are available as an option.
In cases where concrete is to be cast on site by the customer, there are instructions provided, stating the required volume and quality. At the end of its life, concrete can be crushed and reused in the construction industry eg, for building temporary roads.
For further information about our warranties, materials, colours, inspection & maintenence or more details about our products please visit: hags.com