
9 minute read
Why Hemp is set to revolutionize Plastic in consumer Products
Artikel auf Deutsch: www.hanf-magazin.com/vc6
Vincent Cavalier | trifilon
Why hemp is set to revolutionize plastic in consumer products
It’s not the first place you’d expect to find industrial hemp: a plastic suitcase. But it’s only one product that the Swedish company Trifilon helps make with a high-tech biocomposite, which uses hemp fibers as a reinforcing agent. The largescale possibilities of its technology helped the startup win the award for the 2018 Hemp Product Innovation of the year at the 16th European Industrial Hemp Association hosted by the Nova Institut. Hemp fibers may soon help make air conditioners, vacuums, light fixtures, vehicles, toys, mops, buckets, hangers, beach chairs….
It’s not the first place you’d expect to find industrial hemp: a plastic suitcase. But it’s only one product that the Swedish company Trifilon helps make with a high-tech biocomposite, which uses hemp fibers as a reinforcing agent. The large-scale possibilities of its technology helped the startup win the award for the 2018 Hemp Product Innovation of the year at the 16th European Industrial Hemp Association hosted by the Nova Institut. Hemp fibers may soon help make air conditioners, vacuums, light fixtures, vehicles, toys, mops, buckets, hangers, beach chairs….
New questions about materials
To understand why you would consider putting hemp into plastic products, you should understand a problem that manufacturers sometimes face. Say that you want to design and sell plastic suitcases. You decide to test two models: One suitcase has a thin plastic shell. The second suitcase has a thick one. To test these models you place a Parisian pastry in each bag and ask a traveler to bring them to his grandmother. With the first model, the pastry is smooshed because the thin shell bends too easily during the journey. Model two, the thick version, protects the pastry. But the traveler's arms are too tired to give grandma a firm hug. The bag’s too heavy.
The ideal suitcase design would have the weight of the thin-shell model and the hardness of the thick-shell model. What to do?
This problem simplifies complex negotiations that material engineers face when choosing how to make things. One reason it’s a simplification is that there are many sorts of plastics with many more nuanced material qualities than “light” or “hard.” Another reason is that we haven’t mentioned the most important variable – cost. But the logic here helps illuminate why you might consider plastic reinforcement, the addition of an ingredient to change the qualities of primary material. By reinforcing plastic we can keep its benefits – it can be molded easily to specific shapes and is relatively cheap and durable, for example. But the reinforcing ingredient changes its material performance in a certain product. In our example with a reinforced thin plastic shell, the bag would be stiff but light. Grandma gets a pastry and a hug.
Reinforcement is no new thing. You have probably heard about two famous classes of reinforcement technology. “Fiberglass” and “carbon fiber” typically refer to using glass fibers and carbon fibers mixed with polymers to form things that should be relatively rigid but relatively lightweight. Fiberglass, for example, forms canoes and municipal recycling bins. Carbon fiber, which is even stronger and more lightweight, is used for aerospace and automotive applications. Or expensive canoes.

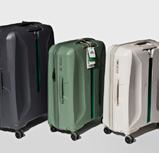
Manufacturers do their best to puzzle out optimal ways to mix and use materials with given constraints. How should the product perform so that customers want to buy it? How much can the product cost make? How easy is it to get the materials? How should the product look?
Another constraint is growing in importance and allows a company like Trifilon, whose business is “greener plastics,” to exist. That constraint is sustainability. How do product ingredients affect the planet? Where have they come from? How much energy did it take to make them? Are they toxic when used? Are they toxic when they are thrown away? For reasons that a reader of this magazine may already know about, this newest manufacturing constraint – sustainability – makes hemp an interesting material to consider.
Plants with promise and problems
In 2006 two researchers at Linköping University in Sweden tried to answer a question: How do you make a stiff and lightweight material, like carbon fiber, that’s easier to produce and recycle? While we implied that carbon fiber has exceptional mechanical properties, it currently requires a lot of energy to make and is difficult to reuse.
Martin Lidstrand, CEO of Trifilon

The researchers found an answer in hemp fibers some of the toughest plant material we know about. Hemp grows tall and thin (not fat like trees) and so has selected for bast fibers that are strong along their length but flexible ensuring the thin stalks don’t snap in the wind. Because hemp fibers can be thin but still strong, they are ideal for polymer reinforcement.
If it were as simple as just sprinkling some hemp fibers in a vat of melted plastic then you might think the researchers didn’t discover much. Of course, it’s not that simple. We mentioned glass and carbon fibers. Those are artificial products in which variables and inputs can be controlled. But bonding fibers from a living organism with polymers for manufacturing presents a number of chemical and logistical challenges. Time and place of harvest, the length and method of retting, and storage all affect the small fibers that you would introduce to a plastic suitcase. And one batch of suitcases should look and behave just like the next.
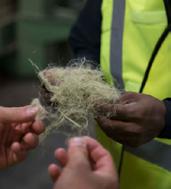
“Biocomposite” is loosely defined as the combination of something biological – like sawdust – with something artificial – like plastics that you can melt and reform. The technology to combine plant matter with plastics has been around for decades. But in manufacturing the plants are typically only used because they lower the costs of production. One example is for decking material made of wood-plastic composites (WPCs). Performance-wise, decking needs simply to be stood upon, to bear weight. Sawdust or wood fibers wouldn’t necessarily improve that performance. But if a lumberyard has lots of excess sawdust then it makes sense to find a new profitable purpose for it, instead of throwing it out.
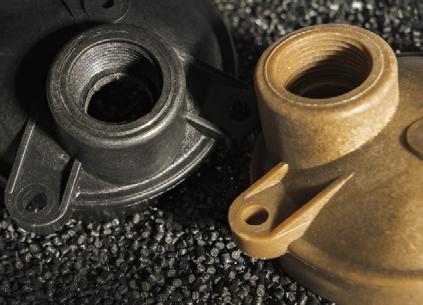
The technology behind Trifilon’s biocomposite represents something different and new. Remember, the researchers only looked at hemp to solve a performance problem while improving sustainability merits, in effect to enhance the performance qualities of the end material for a given application. That requires understanding the variables by which the living organism cannabis sativa produced fibers. And it meant understanding how best to prepare the fibers for their bonding with the plastic molecules. Many things can be achieved in research laboratories that are unfeasible in business. But the co-founders of Trifilon, Martin Lidstrand and Jeremiah Dutton, saw the potential to develop manufacturing processes that made consistently high-performance biocomposites. Through trial and error they found a way to source, receive, treat and prepare the hemp for inclusion in production processes. And that competence is something new for manufacturing because it enhances polymers and improves sustainability. So Trifilon’s interest in hemp isn’t born of any romance with cannabis sativa and not either a financial obligation to it (Trifilon does not own a hemp farm). Hemp simply solves a material problem given certain constraints.
From cars to suitcases
Because the technology was originally considered an alternative to carbon fiber, the co-founders began courting automotive businesses. But as Lidstrand and Dutton met with people in the business of plastics – product designers, materials engineers, marketers, and mold operators – they saw that their technology had applications beyond automotive. They heard that many European consumers (especially in the Nordics) wanted “eco” choices for any and every sort of product. But they wouldn’t accept sacrifices of performance. So a performance biocomposite seemed like a good solution for many applications.
But the co-founders of Trifilon also heard something unexpected. They heard that many individuals in businesses that used pure plastics personally wanted to develop greener products, not in superficial ways, but in deep and permanent ones that could be measured like reducing CO2 footprint. So Trifilon’s biocomposites were not only interesting because of greener reinforcement technology. Not only could they replace glass and carbon fiber plastics. They also provided a substitute for pure plastics. The partners raised investment money and opened a commercial plant in Nyköping in 2018. Their first customer, EPIC Travelgear, produced the world’s first hemp-fiber biocomposite suitcase.
Hemp, plastics, and the future
We haven’t mentioned the elephant in the room. Plastics are on the main stage of environmental debate these days. And it’s true, the ways we produce, use, and discard of plastics are inefficient, unsustainable, sometimes toxic, and possibly reckless in the sense that we don’t know what effects they’ll have on future generations. It’s a complex and ongoing debate, which you can and should read about elsewhere. But one main problem: The ways most (but not all) plastics are made is by chemical processes linked to fossil fuel production. So your computers, toys, shampoo bottles, and toasters have production roots in fossil fuel extraction. And so some people ask, why don’t we think up a world without plastics?
But it is difficult to imagine our present world without automobiles, coffee makers, mobile phones, water pipes, and baby highchairs just to name a few items. Most western lifestyles currently require manufacturers to create products that solve problems for people. Plastics are durable, malleable, and cheap. They solve many problems for manufacturers who are solving problems for people. So some types in that diverse family of materials are likely here to stay.
But there are efforts to improve things underway. Using agricultural fibers like hemp in a material ingredient mix does not involve chemical processes as you might have to produce glass fiber, for example. And using hemp lowers the CO2 footprint of the manufactured product. Much of that comes from sequestration, the action of hemp storing carbon in its plant cells while it grows. And because hemp grows so quickly, it’s quite good at capturing carbon. Fields of hemp, while they aren’t better than forests, are better than paved lots for glass-fiber factories.

Hemp crops are hardy and versatile meaning they can grow nearer to production sites. And they don’t compete with food crops. In fact, some dual-purpose strains can produce both fibers and seeds to make nutritional products, cosmetics and oils. So while the material problems that led Trifilon to hemp might change in 20 years, it still feels like a worthy agricultural industry to have supported.
And how do we get to the Promised Land? How do we make a suitcase 100% derived from renewable resources, 100% high-performance, and 100% reused or discarded efficiently? Hemp might not be all of the solutions, but it’s a good start.