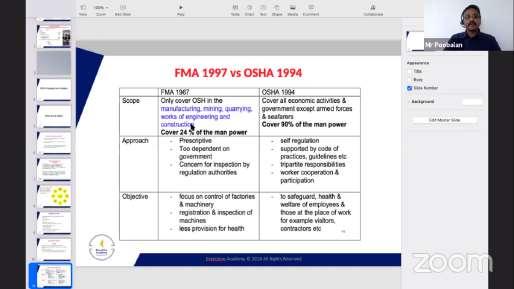
4 minute read
BASIC UNDERSTANDING & IMPLEMENTATION ON ENVIRONMENTAL, HEALTH & SAFETY (EHS)
Poobalan Gopalakrishnan walked MIIP members through the basic understanding of EHS for ID works, interior fit-out, manufacturing and suppliers.
Tong S L, President of MIIP welcomed the attendees to the session and introduced the speaker. Poobalan has more than 26 years’ experience in the health and safety industry, and is currently a Director of Evershinex EC Sdn Bhd. The company specialises in occupational health and safety as well as handles tower crane operations, scaffolding works, HSSEQ Consultancy and manpower supply.
Speaking about the Occupational Health and Safety (OSH) Management System, Poobalan explained that first it is important to understand the Factory & Machinery Act (FMA) and OSH Act (OSHA). He explains that in the year 1967, the FMA was approved by Parliament. In 1970, the eight regulations under FMA were enforced. This Act was legislated to overcome weaknesses in the Machinery Ordinance 1953, and those working in an environment with no machinery were not protected under this Act.
He continues that OSHA was established in 1994 to promote and encourage OSH awareness among workers and to create organisations with effective safety and health measures. OSHA covers various industries in Malaysia but uniform units such as the police and army are not covered under this Act. OSHA is also not applicable onboard ships governed by the merchant because shipping is covered under the Merchant Shipping Ordinance 1960 of Sabah and Sarawak. Poobalan also explained the differences between FMA and OSHA Acts. FMA covers only 24 percent of manpower, while OSHA covers 90 percent of manpower.
Expounding on the objectives of OSHA 1994, Poobalan says the Act is aimed at securing the safety, health and welfare of persons working against risks; protecting persons at a place of work other than persons at work against risks; and, promoting an occupational environment for persons at work which is adapted to their physiological and psychological needs. The purpose of the act is also to provide the means whereby the OSH legislations may be progressively replaced by a system of regulations and approved industry codes of practice operating in combination with the provisions of this Act designed to maintain or improve the standards of safety and health.
He adds that the utmost priority of OSHA is accident prevention, followed by inculcating co-operation between management and workers, ensuring that top management take the lead in OSH, defining OSH policies, obtaining resources to achieve the policy and encouraging the use of best practices.
Employers must have OSH policies in place, establish an OSH committee, appoint a Safety Officer and carry out reporting of accidents, Poobalan advises. There are 34 guidelines under OSHA that employers are required to adhere.
He explained that there are several general duties of employers and self-employed persons under Section 15, 16, 17, and 18 of the Act. The topmost priority is to ensure safety, health and welfare of employees at work. Other duties include providing and maintaining a safe working environment; maintaining of plant and system of work; ensuring safety during operation, handling storage and transport; providing information, instruction, training and supervision; and, providing and maintaining safe outlet for entering and leaving.
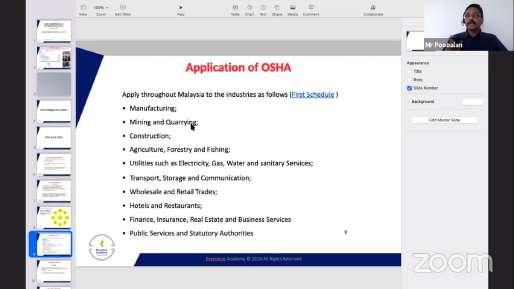
Poobalan explains that under the Act, OSH policies are required for any organisation that has more than five workers, failing which there will be a fine imposed. The company also has to ensure other persons are not exposed to risk from activities at the workplace; and, to disseminate information on aspects of work activities that could affect the safety and health of others. Contravening Sections 15, 16, 17 and 18 is liable to a fine of RM50,000 or 2 years of imprisonment, or both. He also explained that the general duties of designers, manufacturers and suppliers which is also to ensure health and safety involved in the works carried out. He highlights that medical surveillance has to be carried out to ensure that no injury or death occurs in the workplace.
Organisations can either opt to have a full-time safety officer or a visiting officer to ensure that all regulations under the Act are complied to. Organisations with more than 40 or more employees are required to have a safety committee. Penalty for contravening this requirement is a fine not exceeding RM5,000 or imprisonment for a term not more than six months or both. The committee needs to review incidences, as well as come up with improved safety measures and SOPs. Employers also need to ensure that the company has in place a Health, Safety and Environment (HSE) policy. Policies must be created to suit the company’s business, environment and work processes.
Key to HSE implementation and awareness is conducting regular monitoring and inspections, conducting monthly safety programmes to raise awareness, conducting toolbox meetings, organising trainings and seminars to ensure a safe workplace, and conducting safety induction for all employees.
The foundations of health and safety revolve around HIRARC (Hazard Identification, Risk Assessment and Risk Control), explains Poobalan. He adds that the types of hazards include physical, chemical, ergonomical, biological, psychological and environment. Meanwhile, risk control involves, elimination control, substitution control, engineering control, administrative control, and personal protective equipment. HIRARC planning and implementation requires feedback and complaints, inspections and audit, ERP, training, safety committee, policy, internal audit, SOPs, legal and accident as well as near misses reports. He advises that in achieving ISO14001, HIRARC is a key document that the authorities will require from the company.
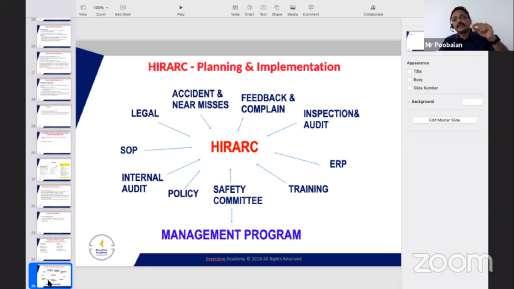
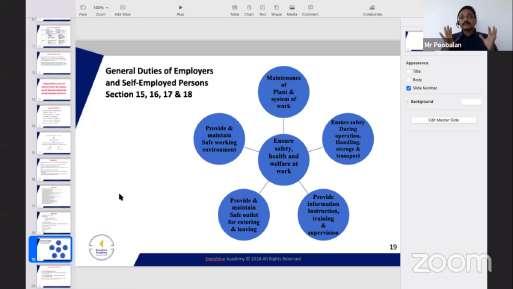
He highlights that HSE implementation and awareness calls for a safe system of work. Also addressed during the talk were hazards, bad practices and work site conditions, personal protective equipment, noise control, dust control, maintenance schedules, emergencies plans, as well as COVID-19 SOPs, among others. Poobalan reminds business owners to ensure that work site housekeeping is carried out effectively to avoid and prevent accidents. Good housekeeping that can improve workplace safety include maintenance, dust, spills and waste.
There is a checklist on housekeeping under OSHA. In order to ensure EHS in the workplace, there needs to be a stringent but practical EHS management system. He advises to set KPIs for contractors and sub-contractors to ensure compliance to OSHA. He cautions not to compromise on safety just to cut costs as accidents can cause huge monetary losses.
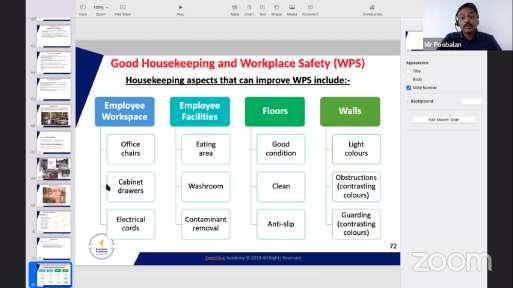
