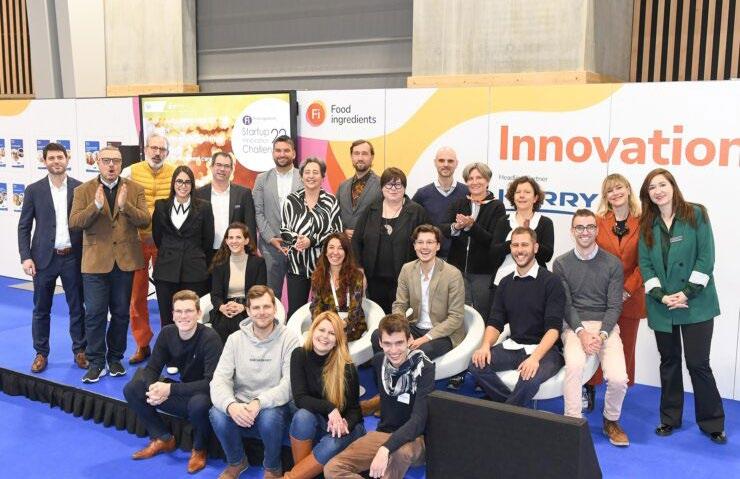
11 minute read
Startups Stand Up and Take the Challenge
The food and beverage ingredient industry’s most celebrated startup awards return to Fi Europe in 2023
Entries are now live for the 2023 Fi Europe Startup Innovation Challenge, giving innovators a rare opportunity to take their concepts to the next level. Now in its eighth edition, the awards programme champions innovation in food and beverage ingredients and technology. Taking place at the Innovation Hub during Fi Europe, it provides a unique platform for young companies to gain exposure to a global audience, attract investment and showcase their products and ideas to influential industry players.
Startups that are less than five years old are invited to submit entries for one or more of the following categories:
• Most Innovative Food & Beverage Ingredient
• Most Innovative Plant-Based or Alternative Ingredient
• Most Innovative Processing Technology or Technology Platform
• Most Innovative Service or AI Solution Supporting the F&B Industry
As it has become requisite for any new venture or ingredient to demonstrate inherently strong sustainability credentials, there will also be a Jury’s Choice award for the Most Innovative Sustainable Solution. Companies cannot apply directly for this category – the winner will be chosen from the finalists across all categories by the expert judging panel.
As well as benefitting from the kudos and publicity that go hand in hand with clinching a prestigious 2023 Startup Innovation Challenge accolade, category winners can choose from a selection of high-value business support packages as prizes. These include a free stand at a future Fi Europe, a comprehensive digital marketing package delivered in conjunction with Ingredients Network, and mentoring services from investors and incubators.
But in these awards, winning isn’t everything. Simply by entering, applicants benefit from the experience of pitching their business case on paper to the Fi Europe Startup Innovation Challenge jury board.
All shortlisted startups are then invited to introduce their innovations to an expert judging panel for 2023 made up of industry luminaries such as Michael Dovbish (executive director, Nutrition Capital Network), Kevin Camphuis (co-founder, ShakeUpFactory), and Giulia Crastolla (investor relations manager, StartLife).
Shortlisted companies also have the opportunity to present their solutions on stage to a global audience via the Innovation Hub on 28 November at Fi Global’s flagship European show. Given that Fi Europe attracts over 25,000 attendees from all over the world, this represents a highly efficient route to reaching a vast yet targeted cross-section of the food and beverage industry population.
In addition, organiser Informa has created an onsite Startup Lounge for exclusive use by shortlisted entrants. This gives startups access to a private space on the show floor to hold meetings with potential partners, customers, and investors.
Yannick Verry, Brand Manager, Food Ingredients Europe and Americas, says: “Fi Europe is all about promoting, sharing and celebrating ingredient innovation. Every breakthrough ingredient or disruptive technology starts as an idea and we are proud of our role in helping to nurture and bring on startups. With the Startup Innovation Challenge, we have created a programme that rewards entrepreneurial spirit and helps young businesses to make the connections they need to scale up and grow – essentially it provides a springboard into a vast sea of opportunity.”
Entries are open at bit.ly/SUIC2023_apply from 3 July to 1 September 2023.
Finalists will be announced on 13 October, and final judging will take place on 27 November in Frankfurt, Germany.
Minebea Intec, one of the world’s leading industrial weighing and inspection technology manufacturers, is expanding its existing load cell portfolio with the single point load cells PR 53, PR 54 and PR 57, and the bending beam load cell PR 77. These high-quality stainless-steel load cells provide a reliable solution for demanding weighing processes in industrial environments. These products and other selected weighing components are available immediately from the online shop (shop.minebea-intec.com). Customers can quickly access product information and order the products directly from here.
Single point and bending beam load cells are the best-selling load cells on the market. They are crucial in various applications, whether in bench and floor platforms or integrated into machines. The new load cells PR 53, PR 54, PR 57 and PR 77 cover a wide load range from 7.5 kg to 750 kg, making it possible to realize any application, from small bench or floor scales to vessel weighing.
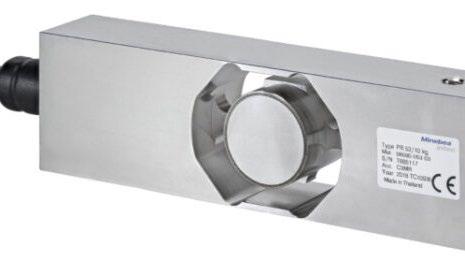
A vital strength of the new load cells is that they are certified to international standards. The load cells PR 53, PR 54, PR 57 and PR 77 are certified to OIML, NTEP, ATEX and IECEx, which means that they can be used in a wide range of industrial environments worldwide.
Load cells developed in collaboration with MinebeaMitsumi
Minebea Intec worked closely with its parent company MinebeaMitsumi on developing and producing the PR 53, PR 54, PR 57 and PR 77 load cells. The MinebeaMitsumi Group is a publicly listed Japanese group with over 85,000 employees worldwide and its head office in Tokyo. The company operates in various industries and manufactures high-precision production parts such as ball bearings and engines. Working together on this project allowed the companies to make optimal use of their shared expertise, and the partnership helped to guarantee the high quality and reliability of the load cells. “We are proud to join forces with MinebeaMitsumi to offer high-quality load cells that meet our clients’ requirements,” says Yannick Salzmann, Product Manager Process & Weighing Products.
The exceptional quality of the advice and service that customers receive from Minebea Intec allows them to take advantage of individual load cell applications, e.g. for vessels or silo weighing, or alternatively to order the load cells for integration into a checkweigher or platform scale. “We support our customers throughout the entire process, from the moment goods arrive at customers’ premises to the moment they leave,” says Yannick Salzmann. “Introducing these new load cells helps us to widen our portfolio in order to meet the increasingly demanding requirements for weighing processes in industrial environments.”
Potential customers can find more information about the new single point load cells from Minebea Intec in the How-To Guide ‘Single point load cells: Key features, advantages and benefits’ from Minebea Intec.
Yili Innovation Center Europe, the Institute for Manufacturing and StartLife in the Netherlands jointly hold the Open Innovation Forum
From July 5 to 6, 2023, the Open Innovation Forum was held on the campus of Wageningen University and Research (WUR), one of the world’s top higher education institutions focusing on agricultural studies in the Netherlands.
Organised by the Open Innovation (OI) Forum at the Institute for Manufacturing at the University of Cambridge, the event was hosted by StartLife, a specialised investment organisation based in the Netherlands, and Yili Innovation Center Europe under the theme of “Disruptive Food Production Technologies.” The forum aimed to advance the upgrading and innovative application of global health food technologies, providing consumers with more comprehensive health solutions.
During the forum, Mr Dominic Oughton, Industrial Associate & Leader of OI Forum at the IfM, University of Cambridge, Dr Maurits Burgering, Program Director at WUR, Ms Annelies Schenk, Head of Innovation &
Partnerships at StartLife, Mr Hittjo Homan, Manager of Dairy Technology at Yili Innovation Center Europe, and Dr Matthias Eisner, Senior Product & Process Technology Scientist at Yili Innovation Center Europe participated in discussions with other esteemed experts, as well as representatives from technological innovation enterprises on a series of cuttingedge technologies.
Regarding this forum, Dr. Lin Zhu, Open Innovation Manager at Yili Innovation Center Europe, said: “The forum will further promote the high-quality development of the industry, and in turn, provide consumers with healthier, more comprehensive and more nutritious solutions.”
During the open discussion session on innovation practices under the theme of “Innovation in a Cross-cultural Context,” Dr Maurits Burgering noted that Yili not only focused on a considerable number of innovative projects with WUR but also actively supported students and start-ups as part of its contributions to a better future.
The Yili Innovation Center Europe has now become a bridge for Yili to connect China with innovative endeavours in Europe and the world. Mr Dominic Oughton said, “Yili has achieved cutting-edge innovation in the process of connecting the world and bringing the power and innovation of its brand to Europe. This is the best case study of how universities, start-ups and large companies can work together across different regions to achieve open innovation.”
“Yili works closely with start-ups that are part of StartLife, through providing them with constructive feedback and guidance regarding innovation and entrepreneurship. Yili’s support has helped them in their journey to becoming larger and more impactful businesses. We are grateful for Yili’s dedication to supporting start-ups around the world,” said Ms Annelies Schenk.
In June 2021, Yili signed a cooperation agreement with StartLife in food and agricultural technology and became a member of the OI Forum. The OI Forum at the IfM, University of Cambridge is a structured programme for members to share best practices, explore ‘hot topics’ and accelerate open innovation collaborations along the Food, Drink & FMCG value chain.
IFFCO Group Strengthens Production Capabilities with Sidel’s Cutting-Edge PET Lines in the Middle East
The multinational IFFCO Group, headquartered in the United Arab Emirates, is expanding its condiments production capacity by installing Sidel’s complete PET lines in the UAE and a new facility in Iraq.
Throughout the entire project, IFFCO Group has entrusted Sidel to oversee the entire turnkey line project and ensure optimal efficiency. Sidel, renowned for providing end-to-end solutions, has tailored the complete lines around their best-selling equipment, strategically placed at each crucial stage of the packaging process.
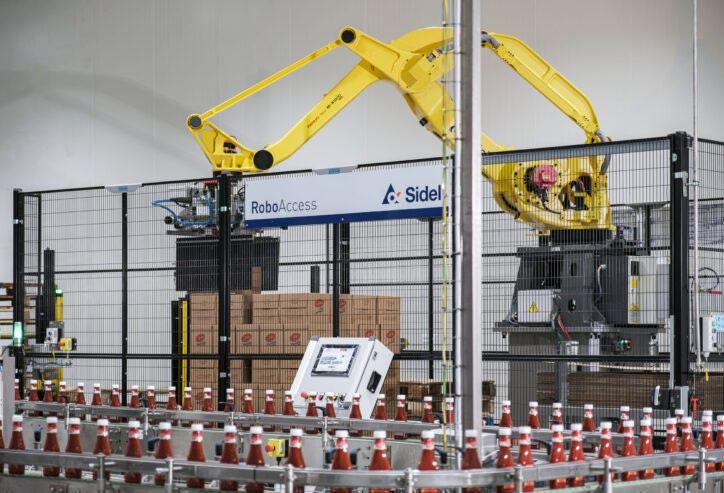
With a wide range of leading FMCG brands and an array of industry solutions and services, IFFCO Group enriches the lives of millions of consumers and customers globally. Operating in over 100 countries, reaching customers through 80+ brands, and employing more than 15,000 persons across 49 countries, IFFCO Group has established itself as a leader known for innovation, convenience, and sustainability.
Recognizing the growing demands of consumers in Iraq, IFFCO Group embraced local production and inaugurated their first factory in Baghdad, dedicated to producing top-quality condiments.
Sidel’s involvement has been instrumental in providing a comprehensive and top-tier solution for both the site in Iraq and IFFCO’s group factory in Al-Ain, United Arab Emirates, to increase production capacity across the region. These lines boast an impressive capacity of up to 9,000 bottles per hour (bph) and the flexibility to handle three unique bottle designs, two cap options, and three label variations. By incorporating Sidel’s cutting-edge equipment and through the optimal utilization of individual assets, enhanced overall efficiency has been achieved.
The upstream part of the line benefits from the compact blow/fill/cap Combi solution, which integrates Serac’s accurate weight filler. The Combi’s blowing part also benefits from preferential heating technology, which optimises PET distribution while allowing the asymmetrical stretching needed to blow flat and shaped containers.
Down the line, the AQFlex® smooth contactless accumulation and conveying system contributes to bottle integrity during the transfer from the Combi to the labeller, ensuring the container quality remains optimal when reaching the retailer’s shelves. For secondary packaging, the Cermex WB46 case packer is unique for its ability to ensure perfect case squaring and hot melt sealing, despite the limited counterpressure provided as a result of the shaped bottles inside the wrap-around outer packaging. End-of-line efficiency is later delivered through the affordable RoboAccess robotic palletiser, which comprises an exclusive gripping tool capable of handling cases, interlayers, and pallets.
Sidel and IFFCO Group share common values and market positions as organizations. The two companies are committed to delivering exceptional quality products and adopting a comprehensive and efficient approach to serving diverse industries such as sauces and dressings, edible oil, food, and personal care. A key focus for both entities lies in promoting sustainability throughout their operations.
Andrey Dribny, CEO of IFFCO Group – Culinary, said: “The project management was commendable, and our collaboration proved effective in overcoming challenges. By partnering with Sidel, we benefit from their impeccable service, consistent reliability, and exceptional quality, which are vital for our daily operations. Sidel’s remarkable capacity allows them to meet IFFCO’s requirements seamlessly, regardless of location, circumstances or market segment.” With convenience and sustainability as sizable trends for condiments packaging, Sidel has also supported IFFCO Group in redesigning their current bottle range, keeping the essence and maintaining the legacy of their renowned design, but with a view of contemporising it. Easy to hold and visually pleasing to consumers, the three iconic new bottle designs have been developed with material saving and a reduction in environmental impact in mind. Additional lightweighting steps are now in place, and opportunities available through the utilisation of r-PET have also been discussed.
Mr. Dribny, concludes: “We are committed to embracing sustainability and moving beyond light-weighting efforts. Recognizing the potential of r-PET as the future, we are confident in Sidel’s pioneering position in this field. Therefore, we will rely on their technological support, knowledge, and expertise to navigate our path forward.”
INEOS Styrolution partners with EGN and Tomra to develop food-contact polystyrene
• Process enables closed-loop circularity for polystyrene (PS) at food contact quality levels.
• First large-scale mechanical recycling facility for processing recycled PS suitable for food packaging.
• Start-up expected by mid-2025.
INEOS Styrolution, the global leader in styrenics; Tomra, the world leader in waste transformation; and EGN Entsorgungsgesellschaft Niederrhein, a leading recycling company, have announced a ground-breaking project to convert post-consumer polystyrene (PS) waste into recycled polystyrene for food packaging applications.
EGN, a subsidiary of SWK AG, will build a green field stateof-the-art advanced mechanical recycling facility processing with a capacity to process 40kt of post-consumer polystyrene (PS) waste per year. It is expected to be the first large-scale facility of its kind. EGN will manage sorting and washing, while INEOS Styrolution will be responsible for the “super-cleaning” purification process to comply with the European Food Safety Authority (EFSA) requirements for food contact applications.
The new facility will be located in Krefeld, Germany. It is expected to start up in mid-2025, allowing INEOS Styrolution to start serving customers at a commercial scale.
An agreement with Tomra to provide sorting technology and feedstock completes the project. Tomra Feedstock will collect postconsumer polystyrene waste from disposed food packaging and deliver it to the new site in Krefeld, Germany.
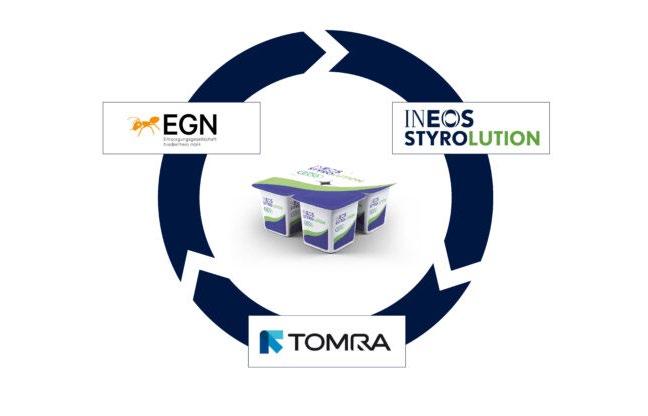
Pierre Vincent, Managing Director EGN, says: “We share INEOS Styrolution’s vision of closing the loop for food-contact quality polystyrene. I expect the dairy industry to especially benefit from this new offering by allowing them to mechanically recycle from yoghurt pot to yoghurt pot creating a true circular economy for this material.”
Jürgen Priesters, Managing Director Tomra Feedstock, comments: “We are proud to contribute to this first commercialscale polystyrene mechanical recycling facility for food contact applications. Polystyrene has the right composition to be recycled mechanically for food applications.
The mission of Tomra Feedstock is to keep PS in true circularity.”
Steve Harrington, CEO, INEOS Styrolution, adds: “This is an exciting step forward for our industry. Our three companies bring complementary expertise to this project, and because of this unique collaboration, we will be able to provide customers high-performing circular polystyrene produced at a significantly lower carbon footprint. Already, we are seeing high interest from customers and brand owners to secure long term contracts.”
Key facts about recycling of polystyrene
The advanced mechanical recycling process benefits from the inherent properties of polystyrene making it the material of choice for real circularity.
PS is proven to be one of the best sortable plastics in the waste stream and is one of only two polymers that can achieve foodcontact qualities with mechanical recycling. The material offers infinite recyclability, retaining its property profile after many mechanical recycling cycles at virgin quality levels. Due to its properties, PS offers very low contamination uptake in the waste stream.
It is expected that a significant percentage of recycled food packaging material will be realised in a very short timeframe. Investment in commercial scaling of PS recycling will lead to a growing market share and a reduction in packaging taxes and licensing fees in countries where such frameworks are in place.