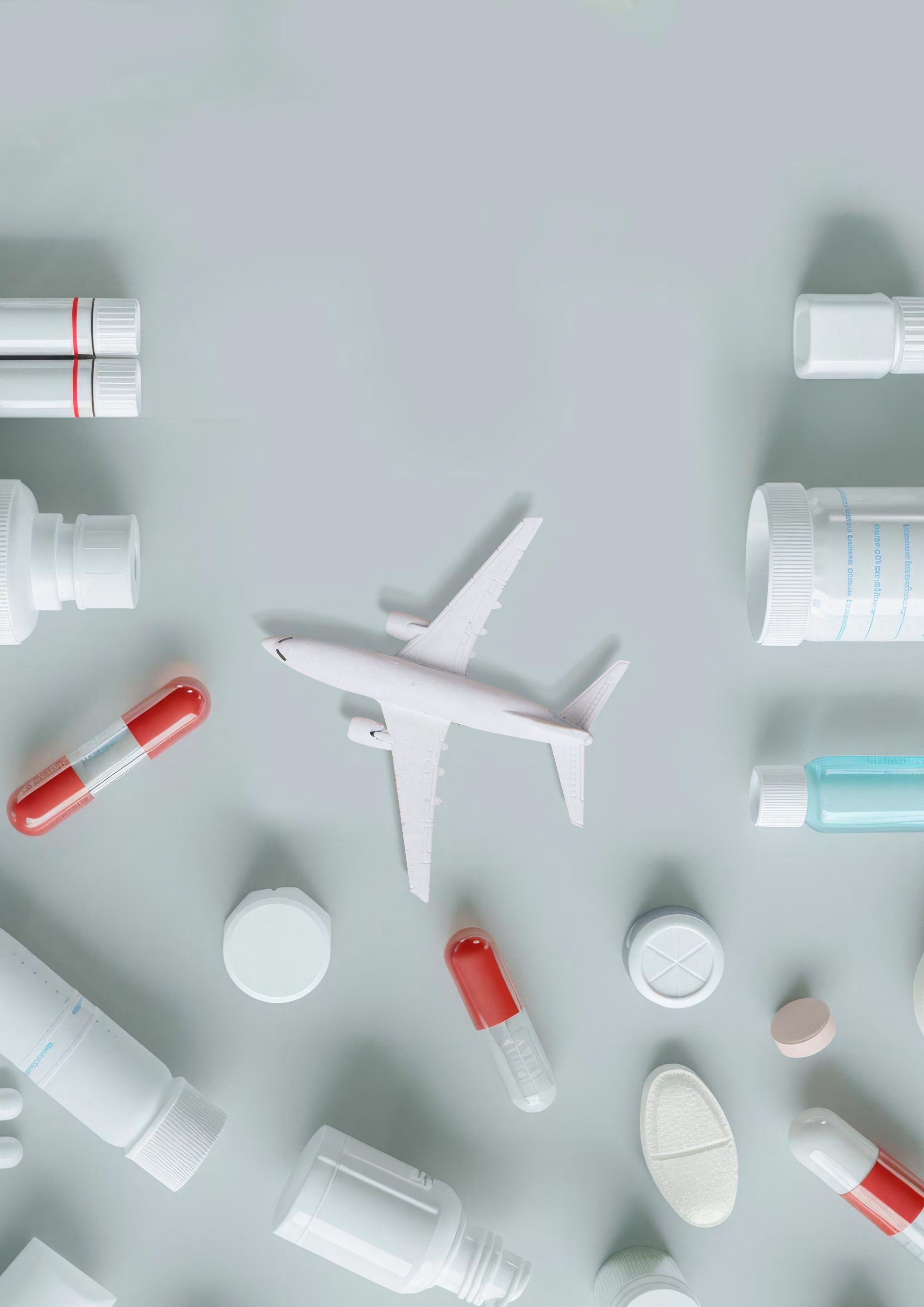
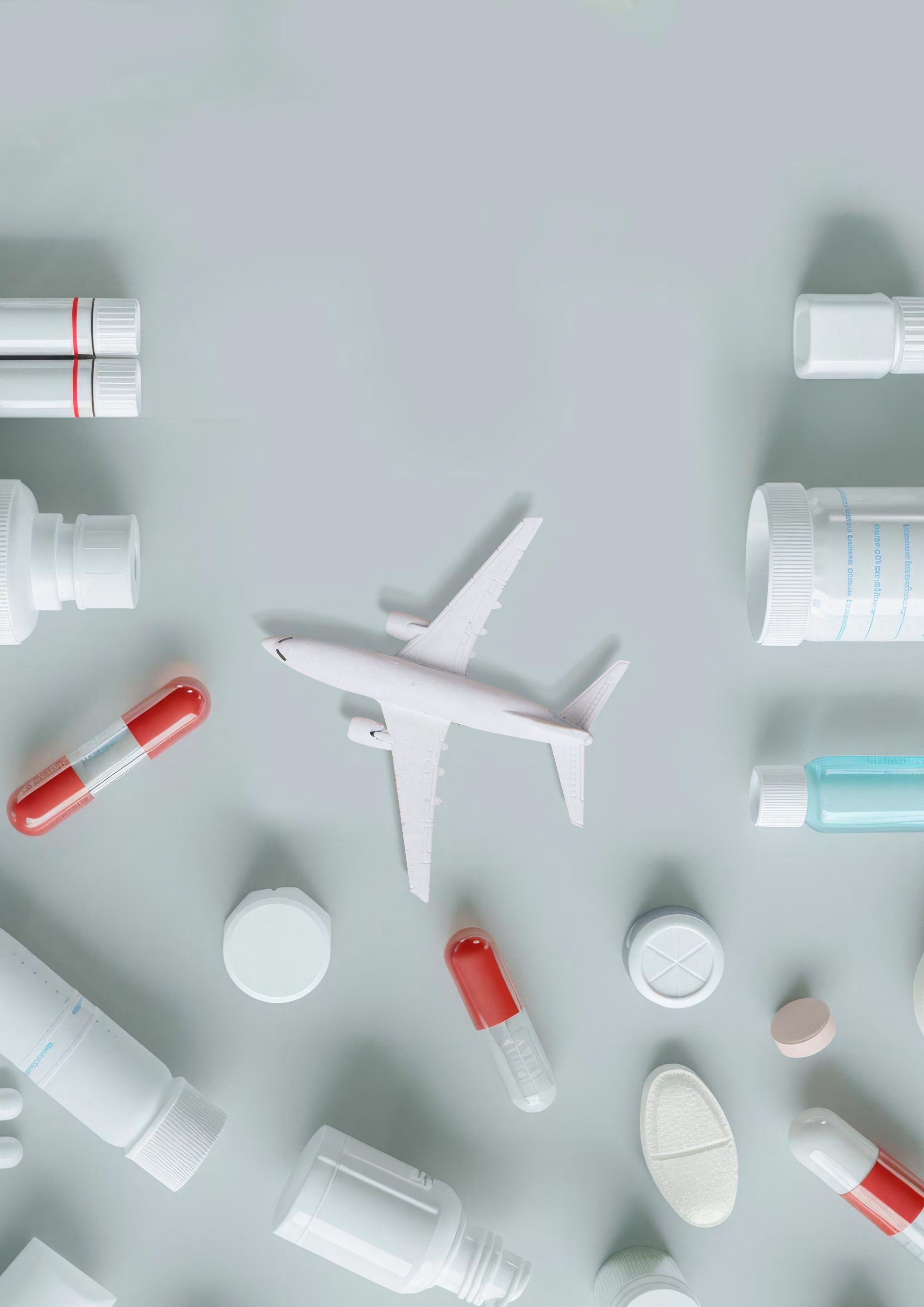
DANGEROUS GOODS AND PHARMACEUTICALS
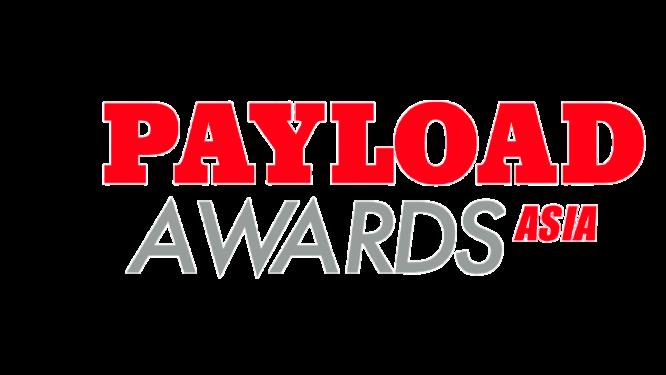

https://payloadasia.com/payload-asia-awards-2024/

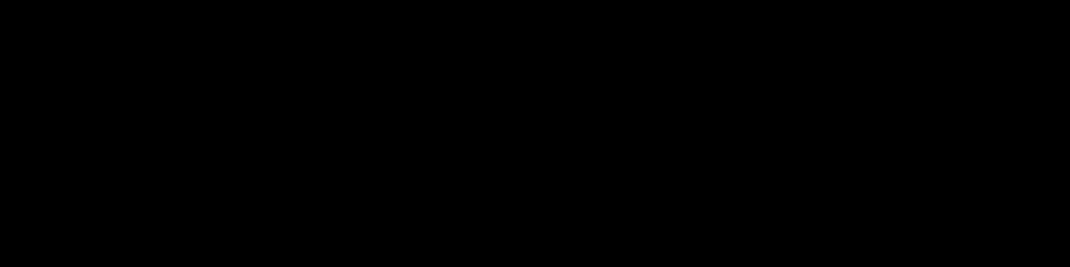
EDITOR’S NOTE

Welcome to the latest issue of Payload Asia, where we delve into the critical realm of dangerous goods and pharmaceuticals.
Our cover story, “Safeguarding dangerous goods and pharmaceuticals in global logistics,” features exclusive insights from WestJet Cargo and IATA, highlighting the industry’s cutting-edge approach to safety and compliance. We explore how technological advancements and stringent protocols are revolutionising the transport of volatile materials and sensitive medical cargo, ensuring unprecedented precision and responsibility in this high-stakes sector.
This edition also showcases three groundbreaking developments in specialised air cargo: Cathay Cargo’s innovative dangerous goods handling system, which sets new benchmarks for pharmaceutical and high-risk shipments; Corex Logistics’ CEO, Steve Healy, sharing state-of-the-art strategies for navigating the complex supply chains of life sciences products; and Japan Airlines’ digitisation initiatives that are transforming pharmaceutical air freight, complemented by Hong Kong International Airport’s collaborative approach to cementing its position as a
These stories offer a comprehensive look at the trends and innovations reshaping air cargo operations for dangerous goods and pharmaceuticals. We’re grateful for your readership and excited to continue bringing you expert coverage of this crucial industry niche in future issues.
Turkish Cargo achieves LEED V4.1 operations certification for SMARTIST Facility at Instanbul Airport
Challenge Airlines BE celebrates five years of success in the air cargo industry
Rotate’s Sales Cockpit selected by Air Canada Cargo
Americas GSA announced strategic partnership with JetBlue Cargo
Korean Air selects Air Incheon as preferred bidder for Asiana Airlines’ freighter business
Etihad Cargo expands European freighter network with launch of Madrid
Lufthansa Cargo launches freighter operations from Munich WFS and Singapore Airlines extend cargo handling partnership for launch of new flights to London Gatwick Airport
Silk Way West Airlines forest strategic partnership with China Henan Aviation Group
Suparna Airlines and WorldACD Market Data sign MOU for strategic data partnership
Skytanking commissions two custom-made fully electrical hydrant fuel dispensers at Brussels Airport
Liege Airport sees an increase in cargo movement, rise in tonnage for the first half of 2024
Swiss WorldCargo commences 3-year cargo handling contract with WFS in Milan Malpensa Airport
Incentive programme to encourage more flights at HKIA
Miami-Dade officials greenlight $400M major cargo expansion at MIA
Changi Airport reports robust growth in Q2 2024 operating indicators
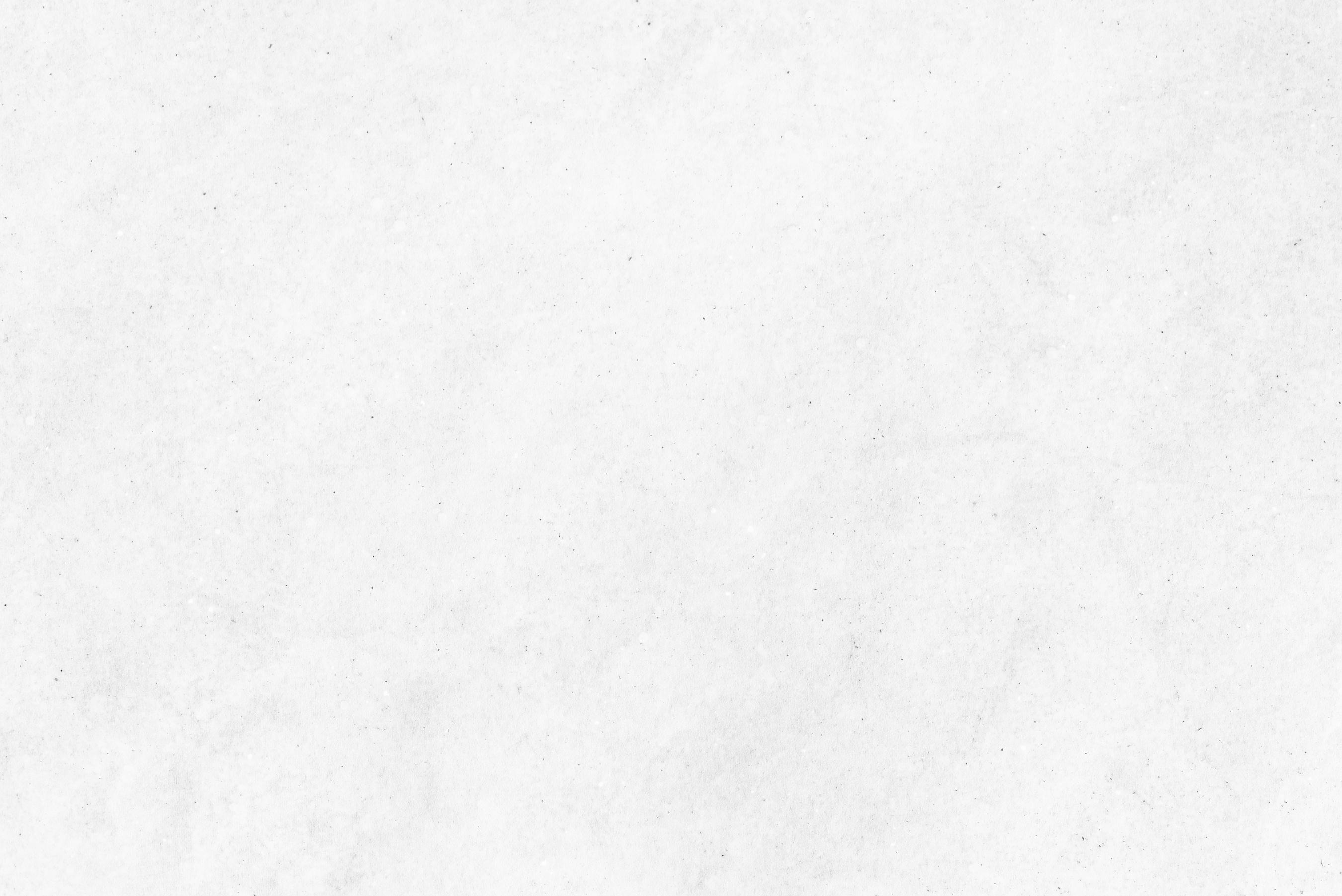
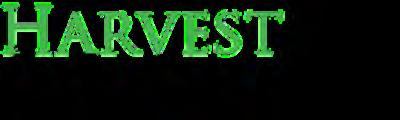
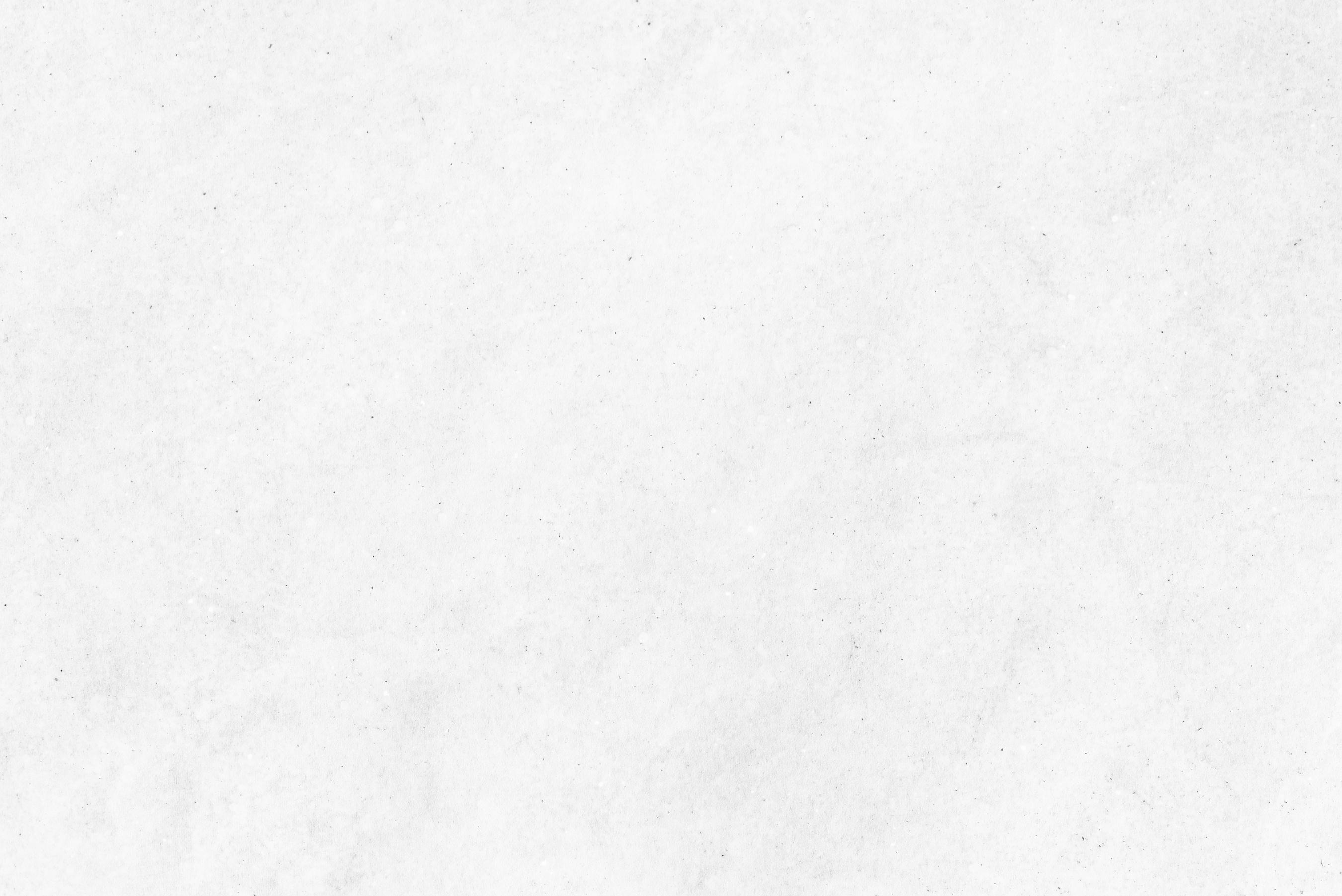
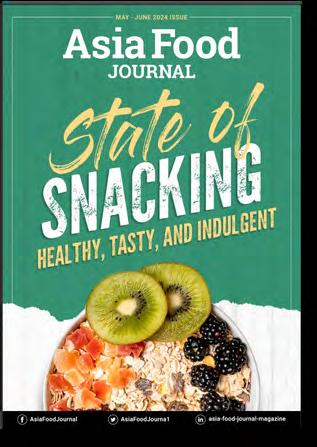
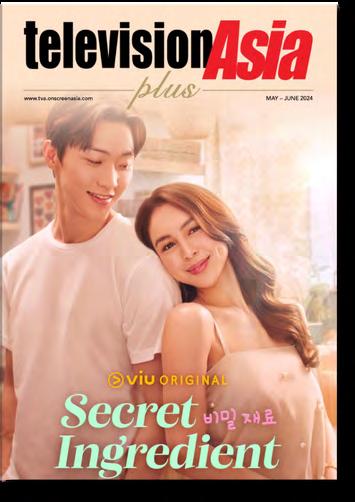
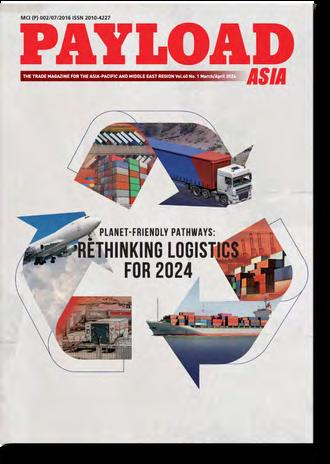
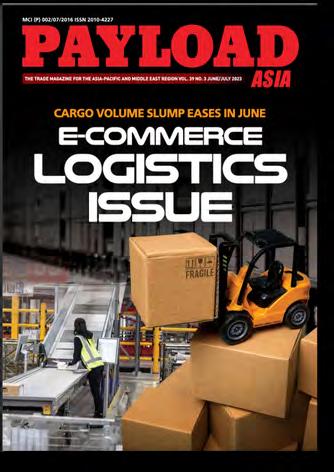
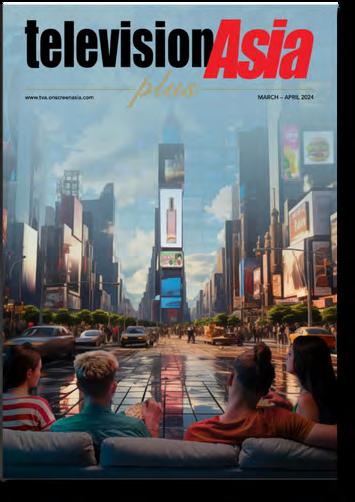

Turkish Cargo achieves LEED V4.1 operations certification for SMARTIST Facility at Instanbul Airport
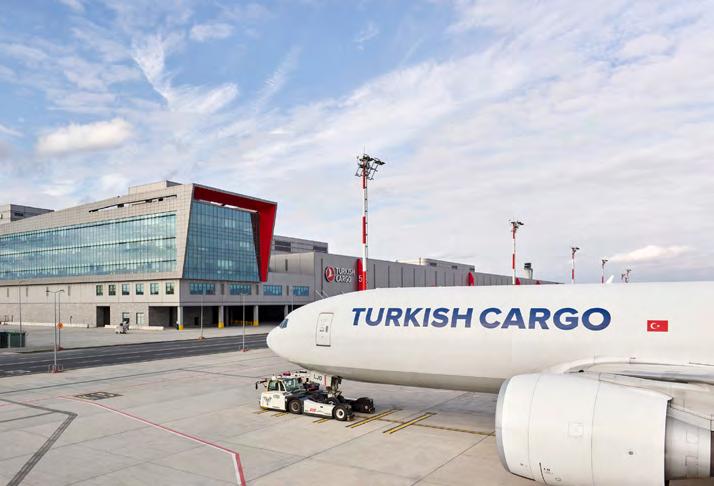
Turkish Cargo pursues its human- and nature-conscious approach based on the activities it carries out in energy efficiency. The global brand has been carrying out to obtaining the LEED (Leadership in Energy
and Environmental Design) v4.1 O+M: EB Operations Certification to enhance its service quality and solidify the leading position it holds in the industry. The carrier became entitled to obtain the platinum operations certification for its SMARTIST cargo facility following the verification and review process.
At SMARTIST, one of the state-of-the-art facilities in the world, cargo is stored and transferred using a computer-controlled Automated Storage and Retrieval System (ASRS) without requiring an operator or forklift. Additionally, ULD storage processes are automated through the ULD Storage System. This smart storage management system not only
Challenge Airlines BE celebrates five years of success in the air cargo industry

Challenge Airlines BE, one of the three airlines part of the Challenge Group, has marked its fifth anniversary.
Rotate’s Sales Cockpit selected by Air Canada Cargo
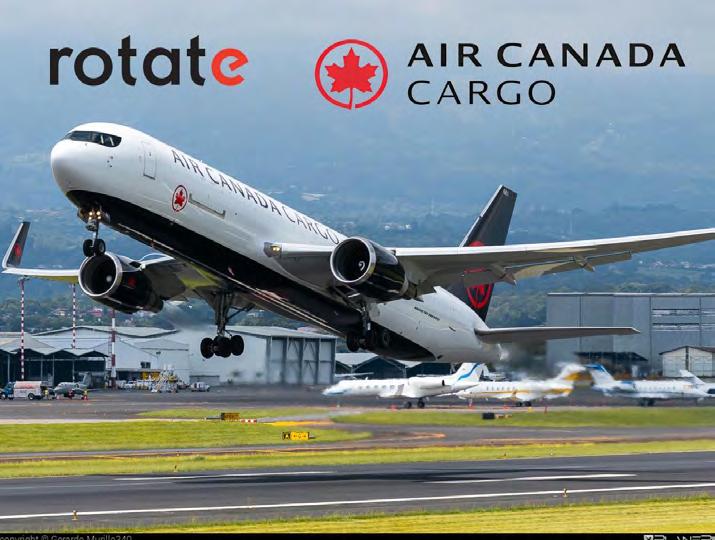
Established in 2018 as ACE Belgium Freighter and rebranded in 2020, Challenge Airlines BE has shown remarkable growth and resilience. Starting with two B747F aircraft, the airline expanded its fleet by adding a third aircraft in 2022. Over the past five years, it has operated over 6,300 flights, managed more than half a million tons of cargo, and served around 20 destinations.
Specializing as ACMI provider to the Challenge Group, Challenge Airlines BE has significantly supported the group’s diverse portfolio of clients and operations.
With a Belgian Air Operator Certificate
Rotate has been selected by Air Canada Cargo to implement the Sales Cockpit, a strategic move that significantly advances the carrier’s global digitalisation efforts.
The Sales Cockpit is web-based software that continually scans the airline’s data to automatically identify specific opportunities with customers. Integrating this with existing systems allows Air Canada Cargo to automatically open sales opportunities in its CRM, and better monitor agreements to track performance against customer expectations. This integration ensures sales teams have timely and relevant information to improve discussions and serve customers more effectively.
expedites the operational processes, it also minimises any unfavourable circumstance which may arise and is cost-efficient.
LEED v4.1 O+M: EB Platinum Operations Certification, which has been obtained for the SMARTIST Terminal, is designed to enhance the energy, water, material and interior quality and reduce their environmental impacts on a continuous basis. Enhancement of energy and water efficiency and interior quality enables the accomplishment of sustainable goals while reducing the operating costs of the SMARTIST facility.
(AOC) and a range of operational certifications, including CCAR-129 for Chinese Operations, US Operations Specifications, and numerous ACC3 certificates for security licenses worldwide, Challenge Airlines BE has cemented its reputation as a trusted and reliable air cargo carrier. As a European airline, it benefits from extensive traffic rights and is a proud member of both the European Aviation Safety Agency (EASA) and the International Air Transport Association (IATA).
To commemorate this milestone, Challenge Group founder and top management organized a celebratory event on Thursday, May 30th, at Liege Airport. The event brought together key stakeholders to reflect on the airline’s achievements and contributions to the air cargo industry.
The implementation of the Sales Cockpit is part of Air Canada Cargo’s broader digitalisation strategy, aimed at enhancing the overall customer experience. By automating the identification and management of sales opportunities, the Sales Cockpit helps ensure that no opportunity is missed, and that customer interactions are more informed and responsive.
Following successful implementations with Air Canada and Etihad, Rotate plans to further extend this CargoTech solution to other airlines, aligning with its mission to help the air cargo industry make better commercial decisions.

Americas GSA announced strategic partnership with JetBlue Cargo
ECS Group subsidiary Americas GSA announced a strategic partnership with JetBlue Cargo. This collaboration marks a significant milestone, enhancing its services on domestic routes out of Florida. The contract commenced in February 2023 for Florida State and on June 1, 2024, for Puerto Rico.
Under this new agreement, Americas
Korean Air selects Air Incheon as preferred bidder for Asiana Airlines’ freighter business
Korean Air has selected Air Incheon as the preferred bidder for the sale of Asiana Airlines’ global cargo freighter business. The decision was made at the Board of Directors meeting held on June 17.
Korean Air selected Air Incheon as the preferred bidder based on several key criteria: the certainty of completing the transaction, the ability to maintain and enhance long-term competitiveness of the air cargo business, and the capability to mobilise funds through a competent consortium.
Founded in 2012, Air Incheon is Korea’s only all-cargo airline, with operations focused in Asia. Air Incheon is expected to strengthen its competitiveness by
GSA will leverage the capabilities of ECS Group’s Augmented GSSA to support JetBlue’s network, enhancing its domestic and international cargo operations. This model provides a bespoke, à la carte service that includes supports, services, and solutions not typically offered by traditional GSAs. While the current focus is on traditional GSA services, this partnership paves the way for expanding
JetBlue’s operations through interline agreements and the management of new commodities.
The collaboration highlights Americas GSA’s strategic vision to enhance its presence in Florida’s cargo market. By integrating with JetBlue’s operations, Americas GSA will provide tailored solutions through its Augmented GSSA model, facilitating the airline’s growth and expanding its cargo network, thereby opening new business opportunities and potentially expanding JetBlue’s cargo operations internationally.
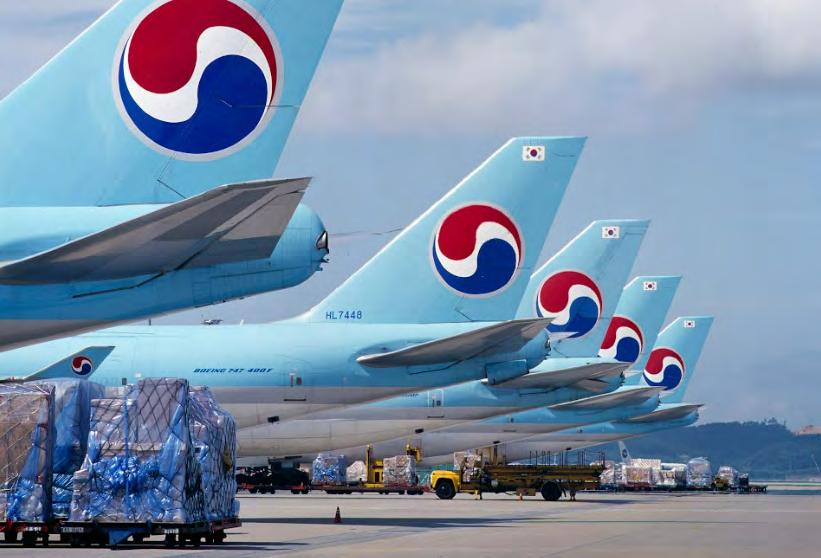
Asiana Airlines’ long-haul network to the Americas and Europe, and a fleet of larger cargo aircraft.
Korean Air plans to sign a framework
Lufthansa Cargo launches freighter operations from Munich
Lufthansa Cargo will expand its operations at the southern German hub and will be operating freighters from the hub for the first time from 6 July 2024. An A321 freighter will connect Munich with Istanbul Airport twice a week, complementing the existing belly network from Munich. The new freighter connection is planned every Saturday and Sunday with flight numbers LH8350 / LH8351 and LH8346 / LH8347. Lufthansa Cargo customers can book their shipments on the new route with immediate effect.
Lufthansa Cargo operates its hub in Munich on a total area of 38,000 m². Among other things, the state-of-the-art CEIV-certified Pharma Hub MUC, in which temperature-sensitive pharmaceutical products can be stored and handled under optimal conditions, is integrated into the premises. This means that the carrier can also transport almost all product and goods groups via Munich. Until now, these have mainly been transported from the Bavarian capital to destinations all over the world via the belly capacities of Lufthansa, Brussels Airlines,

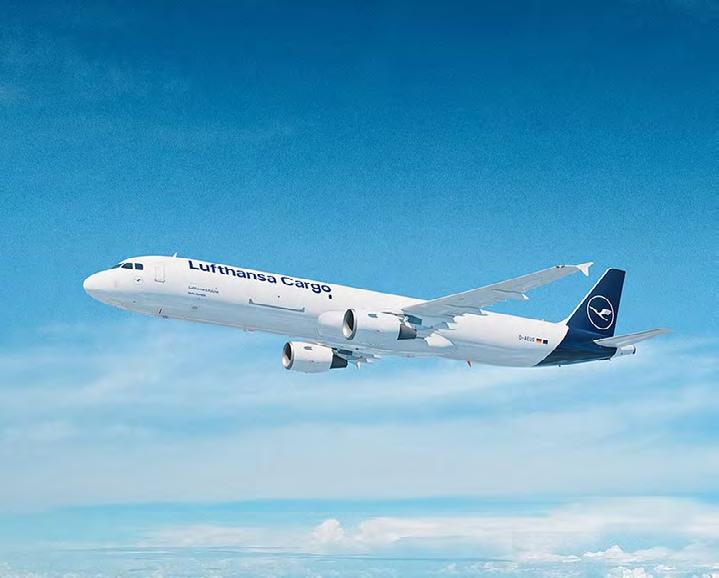
Discover Airlines, Austrian Airlines and SunExpress passenger aircraft. The hub is also connected to a dense RFS network, which enables smooth transportation by road.
utilising
agreement with Air Incheon in July after agreeing on the contract conditions. The agreement is subject to review by the European Commission.
NEWS - CARRIERS
Etihad Cargo expands European freighter network with launch of Madrid
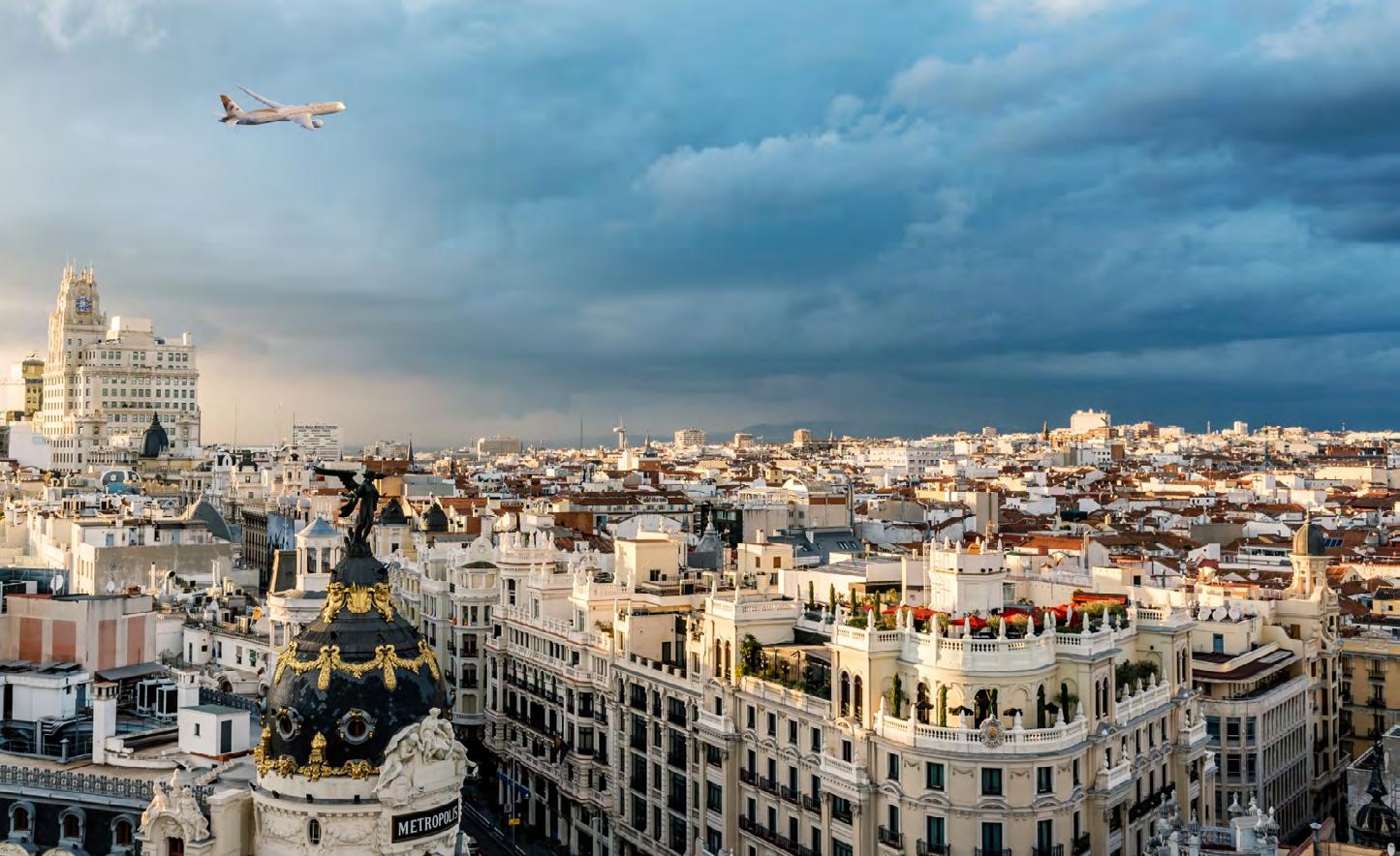
Etihad Cargo, the cargo and logistics arm of Etihad Airways, expands its freighter network with a new route to Madrid. Starting 15 July 2024, Etihad Cargo will operate two weekly Boeing 777 freighter flights between Abu Dhabi and Madrid, adding over 200 tonnes of cargo capacity for Europe.
The launch of a twice-weekly freighter
service between Abu Dhabi and Madrid will increase the total number of flights to Spain to 25 per week. Etihad Cargo provides belly capacity via 10 passenger flights to Madrid, 10 to Barcelona and three seasonal flights to Malaga launched as part of the airline’s summer schedule. This expansion highlights the strategic importance of these destinations, particularly Madrid as a key
European fashion hub, and aims to boost e-commerce connectivity from Asia to Europe via Etihad Cargo’s Abu Dhabi hub.
This new route complements Etihad Cargo’s existing European freighter network, which includes six weekly flights to Amsterdam and three weekly flights to Frankfurt. With the addition of Madrid to the network, the total number of Etihad Cargo’s freighter flights to Europe will increase to 11 per week. Customers will also benefit from additional belly hold capacity offered as part of the carrier’s summer schedule, which includes the launch of two weekly seasonal flights to Nice. Flights to Athens will increase to 14 per week, with two operating via seasonal destination Mykonos and two via Santorini. A new route to Antalya will operate with three weekly flights, and flights to Istanbul will increase from ten to 14 per week starting 22 July 2024. Additionally, Dublin will see three more flights from 23 July 2024, totalling ten per week.
Etihad Cargo’s hub in Abu Dhabi serves as a crucial link between East and West, providing efficient and reliable cargo services to meet the specific needs of the fashion industry and other sectors dependent on timely e-commerce deliveries.
WFS and Singapore Airlines extend cargo handling partnership for launch of new flights to London Gatwick Airport
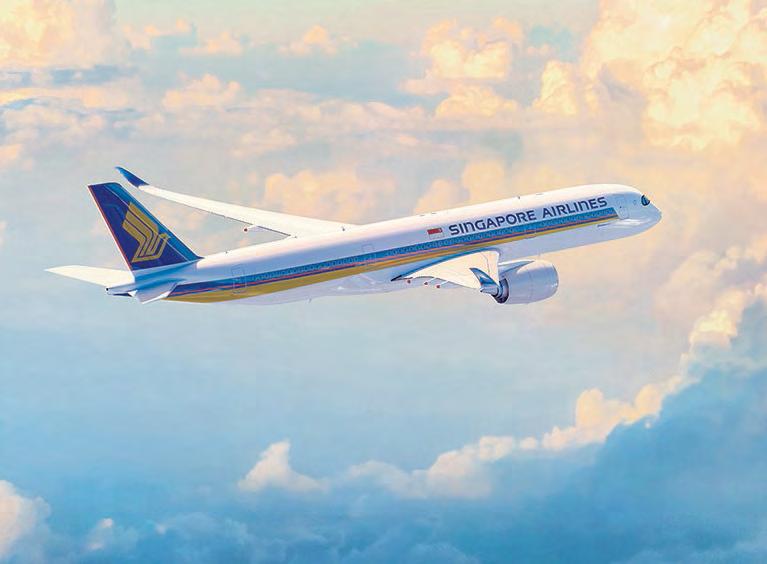
Worldwide Flight Services (WFS), a member of the SATS Group, has been awarded three-year cargo handling contract extensions with Singapore Airlines in the United Kingdom, France, and Belgium.
In the UK, in addition to renewing its cargo handling and UK domestic road feeder services with WFS at London Heathrow and Manchester airports, Singapore’s national carrier is also partnering with WFS for cargo handling at London Gatwick Airport for the June launch of five Airbus A350-900 direct flights a week connecting to Singapore Changi Airport.
In Paris, the new 3-year contract will extend WFS’ service to Singapore Airlines in France for over 40 years, having commenced in 1986 at Paris Charles de Gaulle Airport. Singapore Airlines is also renewing its commitment to WFS in Brussels, where the two companies have worked together since 2021.

Silk Way West Airlines forest strategic partnership with China Henan Aviation Group
Silk Way West Airlines, the leading cargo airline in the Caspian and Central Asian region, has signed a Memorandum of Understanding (MOU) with China Henan Aviation Group during Air Cargo China 2024 in Shanghai. This strategic partnership aims to enhance air cargo connectivity and efficiency between Zhengzhou and Baku to build a robust dual-hub cooperation model that spans the Asia-Pacific region and connects Europe, America, and Africa.
This year marks Silk Way West Airlines’ inaugural participation at Air Cargo China 2024, showcasing the airline’s dedication to expanding its global footprint and exploring new business opportunities. By joining this prestigious event, Silk Way West Airlines aims to strengthen its presence in the Asian market and foster new partnerships within the international air cargo industry.
Silk Way West Airlines has been successfully operating in the Chinese market for over ten years, continuously expanding its services and strengthening its network. The MOU with China Henan Aviation Group represents a significant milestone in the airline’s journey, promising enhanced connectivity and
new growth opportunities.
The collaboration will leverage the respective strengths of both parties, including strategic locations, extensive route networks and diverse valuable resources. By joining forces, Silk Way West Airlines and China Henan Aviation
Group aim to significantly increase the frequency of all-cargo routes between Zhengzhou and Baku. This initiative will position Zhengzhou as a key hub for the Asia-Pacific region and Baku as a central hub for Europe, America, Africa, and other regions
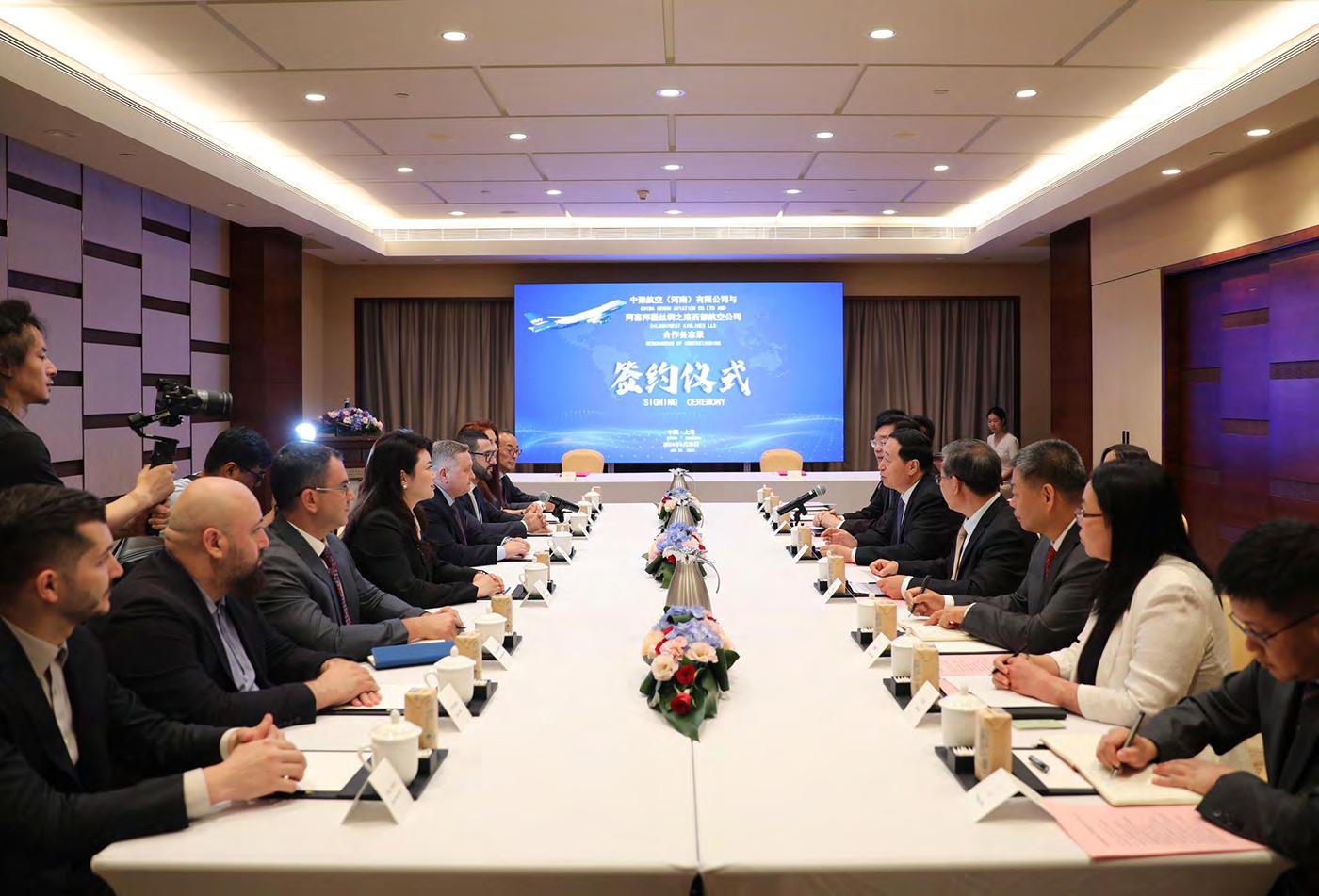
Suparna Airlines and WorldACD Market Data sign MOU for strategic data partnership
WorldACD Market Data, a provider of air cargo market data and insights, announced the signing of a memorandum of understanding (MoU) with Suparna Airlines, a prominent player in the Chinese air cargo industry. This strategic partnership enhances Suparna Airlines’ understanding of the air cargo market dynamics and will further expand WorldACD’s comprehensive air cargo database.
WorldACD will provide Suparna Airlines with in-depth air cargo data and analytics to support the airline’s commercial decision-making processes and strategic initiatives. This cooperation will enable Suparna Airlines to gain a deeper insight into market size & share and rates, trends, customer opportunities, competitive dynamics, thereby optimising the commercial performance and enhancing its market position.
The partnership between WorldACD
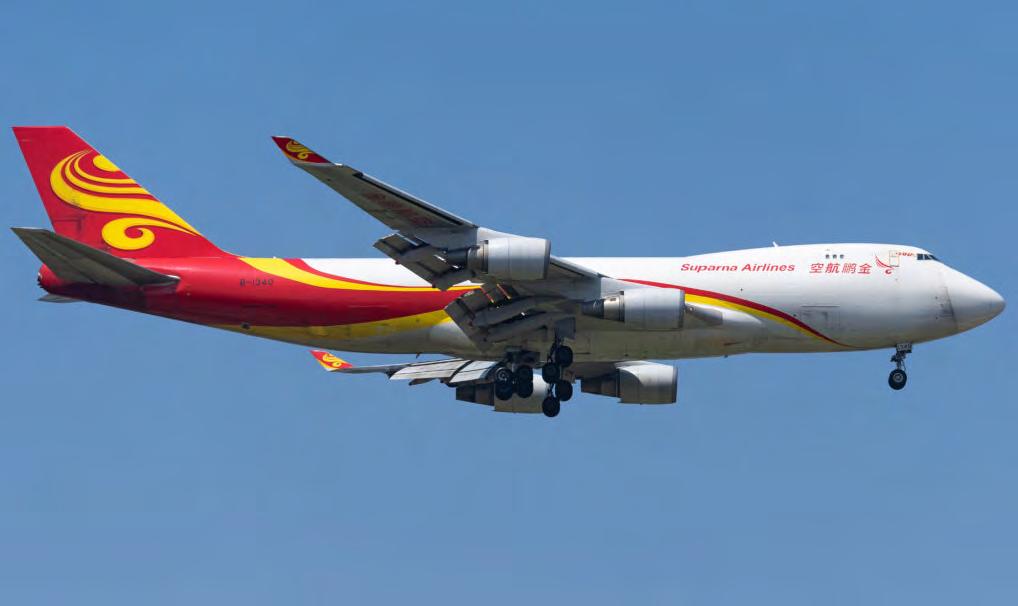
Market Data and Suparna Airlines underscores the importance of datadriven decision-making in the competitive
air cargo market. Both organisations look forward to a long-term partnership.

Skytanking commissions two custom-made fully electrical hydrant fuel dispensers at Brussels Airport
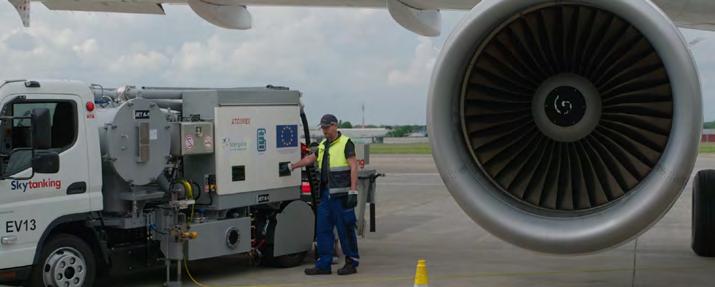
for the local environment in terms of noise and exhaust gases.
The Stargate project, an EU Green Deal project led by Brussels Airport to implement innovative solutions to green the airport industry, is continuously researching new ways to further decarbonise ground handling activities. In 2022, Stargate-partner Skytanking started an intensive test period with two full electric hydrant fuel dispensers at Brussels Airport. These converted diesel to electrically driven, made-to-measure vehicles of Turkish Fuel Services were of Belgian design and were being tested to gain the necessary insights into the
energy consumption in the function of the aircraft model, average distance per movement at the airport, and weather conditions.
After these successful tests at Brussels Airport, Skytanking developed, in cooperation with Atcomex BV and Fuso, the 100% electric hydrant fuel dispensers. These are built on an original electric chassis to allow for easy reproducibility on an international level while assuring the highest level of safety.
Skytanking is the first to operate this first generation of industrial lithium battery hydrant dispensers, able to handle high flow rates and made using a standard industrial chassis, on a European airport of this size. The aim is to deploy the dispensers to fuel 15 to 25 aircraft a day with one single charge per vehicle.
Liege Airport sees an increase in cargo movement, rise in tonnage for the first half of 2024
Skytanking is operating its custom-built electric high-flow hydrant fuel dispensers for fuelling operations at Brussels Airport. These electric dispensers, with a firstgeneration standard high-performance electrical chassis, were delivered on April 26 and are used to deliver aviation fuel from the underground hydrant system into the aircraft. These new electric fuel dispensers are a significant improvement (12,987 vs. 11,604). Tonnage grew at a more sustained pace, up 15% (566,117 tonnes vs. 492,295 tonnes) over the first 6 months of 2024, again compared with the first 6 months of 2023, reflecting a strong improvement in the average aircraft load factor.
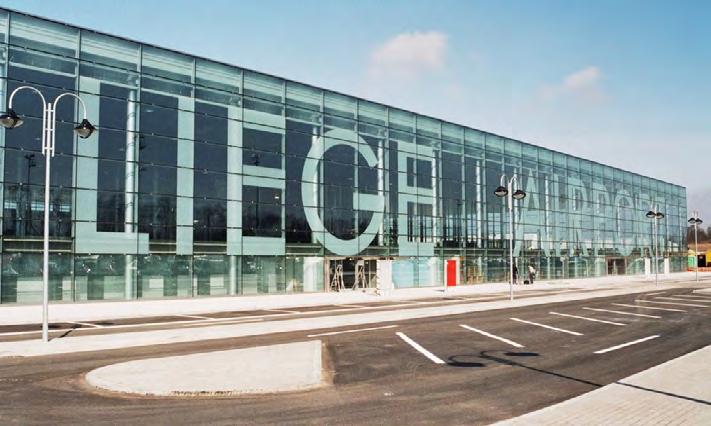
At the halfway mark of 2024, Liege Airport is soaring ahead, with total aircraft movements and tonnage up sharply, marking a strong performance in the first six months of the year.
From January to the end of June, the number of cargo aircraft movements was up 12% on the same period in 2023
In June 2024 alone, the number of cargo aircraft movements was up 9% on June 2023 (2,157 vs. 1,977). And tonnage rose from 78,786 tonnes in June 2023 to 95,514 tonnes in June 2024, a spectacular 21% increase!
This volume growth at Liege Airport exceeds the global trend for freight transport, as noted in the latest analysis published by Xeneta: “Demand in June
was +13% year-on-year, continuing the upward trend seen throughout the first half of 2024.
The e-commerce boom, disruptions in ocean freight due to conflict in the Red Sea, and general improvements in global manufacturers’ activities were the three main pillars driving up global air cargo in June.”
It is also important to emphasize that the airport’s growth has been virtuous, with the share of night flights reduced from 33.23% of total flights in 2023 to 31.45% in 2024, and the number of flights operated by aircraft with poorer acoustic performance, the B747-400 and B747200, reduced by 3% compared to 2023.
Swiss WorldCargo commences 3-year cargo handling contract with WFS in Milan Malpensa Airport

Worldwide Flight Services (WFS), a member of the SATS Group, has commenced a new three-year cargo handling contract with Swiss WorldCargo at Milan Malpensa Airport in Italy.
WFS expects to handle annually 2,000 tonnes of cargo in Milan Malpensa for the airfreight division of SWISS, which serves the Italian city with 28 weekly flights using narrowbody Airbus A320/321 and Embraer aircraft. Additionally, Swiss WorldCargo’s customers will continue to benefit from road feeder services connecting Milan and the Swiss city of Zurich six days a week.
Swiss WorldCargo has been a longstanding customer of WFS across its
global network. At present, WFS provides cargo handling services for the airline’s airfreight division at key airport stations in North & South America, Europe and the Asia Pacific region. Its decision to appoint WFS as its air cargo ground handling partner in Milan Malpensa was based on WFS’ modern cargo handling facilities, the size of its operation, and its ability to provide dedicated solutions for Swiss WorldCargo’s specialised high-value, care-intensive and temperature-sensitive shipments.

Incentive programme to encourage more flights at HKIA
Airport Authority Hong Kong (AAHK) has introduced a new programme to provide incentives for airlines to open more routes and increase frequency of flights connecting to Hong Kong, with a view to further strengthening the position of Hong Kong International Airport (HKIA) as an international aviation hub.
Following the Early Bird Guaranteed Landing Charge Rebate Scheme which ended in March this year, AAHK launched
the new Airport Network Development Programme (the Programme) in June 2024 after consultation with local and foreign airlines’ representatives. The Programme includes two schemes, namely the New Route Scheme and the Strategic Development Scheme.
Under the New Route Scheme, all passenger and cargo airlines that launch new destinations connecting to HKIA with a defined continuity will be eligible to receive financial incentives for two years. Both airlines now operating at HKIA and airlines that are new to HKIA are eligible to receive incentives from the Programme, which is open for applications from 1 June 2024 to 31 December 2027.
Miami-Dade officials greenlight $400M major cargo expansion at MIA
Miami-Dade County Mayor Daniella Levine Cava and County Commissioner Raquel Regalado, District 7, announced that the Miami-Dade Board of County Commissioners has approved to invest a minimum of $400 million in constructing a four-story cargo facility at Miami International Airport that will be the first of its kind in the Western Hemisphere and when completed, will increase the airport’s total cargo capacity by at least 50% or potentially up to two million tons annually. Scheduled for completion in 2029, the new facility will bring MIA’s total capacity to a minimum of 4.5 million tons of cargo and potentially 5 million tons, future-proofing America’s busiest international freight airport until 2041.
The future Vertically Integrated Cargo Community (VICC) at MIA, a nearly 800,000-square-foot facility on 11 acres
of airport land, will have a massive local economic impact as well: 8,500 new temporary jobs earning a total of $500 million in wages during five years of design and construction; 2,500 new permanent jobs earning $100 million post-construction; and a minimum of $512 million in rent and business revenue to Miami-Dade County’s Aviation Department over the 40 years of the agreement. Without the VICC, MIA would begin to reach capacity at three million tons of cargo annually. The airport is on pace for 2.9 million tons of cargo in 2024.
The Board of County Commissioners approved a lease agreement with a private developer that will require at least 60% of the design and construction firms to be headquartered in MiamiDade County, and for those firms to hire registered small businesses during all
Changi Airport reports robust growth in Q2 2024 operating indicators
Singapore Changi Airport handled 16.5 million passenger movements from April to June 2024, an increase of 13.4% compared to a year ago. This was 98.2% of passenger movements for the same period in 2019. Aircraft movements, including landings and take-offs, totalled 89,300 for the quarter, up 9.7% year-onyear, and was 94.5% compared to the second quarter of 2019.
Changi Airport’s top five markets for the second quarter of 2024 were Indonesia, China, Malaysia, Australia and India. China saw the highest growth among
Changi’s top markets, with traffic doubling compared to the same period last year, and surpassing pre-Covid numbers. For the period, North Asia was the fastest growing region, registering a 40.8% increase year-on-year, and also exceeding pre-Covid levels.
From April to June 2024, Changi Airport registered 486,000 tonnes of airfreight throughput, surpassing the same period last year by 16%. Growth was registered across all cargo flows – exports, imports and transhipments, led by strong cargo flows between Singapore and China, as

The Strategic Development Scheme encourages airlines to operate routes aligned with AAHK’s strategy. Any passenger and cargo airlines that launch new routes and/or increase frequencies to AAHK’s targeted regions or countries will be granted financial incentives for three years. In addition, to encourage airlines to utilise the HKIA Dongguan Logistics Park (HKIALP) for air cargo operation, the same offer will also be applicable to any incremental cargo flights provided that all cargoes on board are accepted at HKIALP in Dongguan.
In addition, AAHK has been sponsoring airlines in their promotional activities for launching new routes at HKIA

project phases.
In addition to its enormous impact on job creation and local business revenue, the VICC will be a sustainable, environmentally friendly facility with a silver Leadership in Energy and Environmental Design (LEED) certification and a silver certification from Global Infrastructure Basel under SuRe standards for sustainability and resiliency.
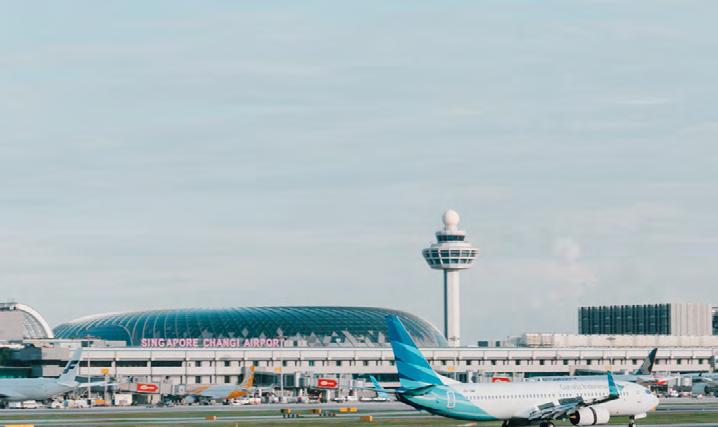
well as the United States of America. For this period, Changi’s top five air cargo markets were Australia, China, Hong Kong, India and United States of America.
As of 1 July, 94 airlines operate over 6,900 weekly scheduled flights at Changi Airport, connecting Singapore to 158 cities in 50 countries and territories worldwide.
NEWS - GROUND HANDLING
American Airlines awards WFS cargo handling contract in Europe to mark Copenhagen launch
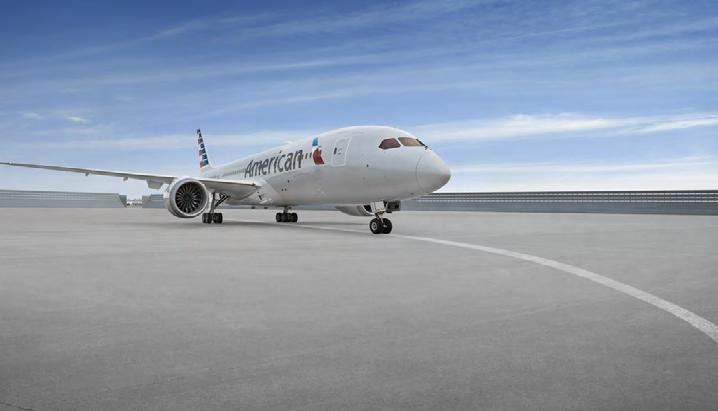
Worldwide Flight Services (WFS), a member of the SATS Group, has extended its partnership with American Airlines in Europe with a new cargo handling contract in Copenhagen to support
the launch of the airline’s daily Boeing 787 flights between Denmark and its transatlantic hub in Philadelphia.
In Europe, WFS is already handling American Airlines’ growing cargo volumes in France, Germany, Ireland, Italy, the Netherlands, Spain, and the United Kingdom. The new contract in Denmark will be supported by WFS’ continued investments in its cargo and premium products handling infrastructure at Copenhagen Airport.
At the end of 2022, WFS opened its third
Swissport Basel inaugurates new cool chain terminal ‘Cool+Connect’

Swissport Basel inaugurated its new “cool+connect” terminal on 27 June 2024. The new infrastructure seamlessly ensures the integrity of pharmaceutical and temperature-sensitive goods (28°C) throughout the loading process. By consolidating shipments from the
same suppliers in a single truck instead of several as before, CO2 emissions and handling time are reduced by around 70% (from 4.5 to 1.5 hours), as transportation outside the airport is no longer necessary.
Swissport plans to introduce the “cool+connect” infrastructure worldwide. Additionally, the company is committed to expanding its network of IATA CEIV Pharma-certified cargo warehouses for pharmaceutical logistics. Swissport aims to achieve CEIV certification across its network, with Geneva, Switzerland, and Hamburg, Germany, already in the planning stages. In the United States,
new cargo terminal at the airport, adding a further 3,700 square metres of capacity. Copenhagen is also one of the more than 25 global airports in WFS’ network with a dedicated GDP-certified pharmaceutical handling facility to support customers working with pharma and life science business community located in Medicon Valley in Greater Copenhagen.
The addition to direct flights from Copenhagen is also positive news for American Airlines’ customers in Sweden which will now enjoy faster cargo connections with the U.S.
WFS now handles some 100,000 tonnes annually in Copenhagen for more than 20 online airline customers and a further +150 offline carriers
Swissport is actively pursuing certification for major pharmaceutical centres at Miami International Airport and Chicago O’Hare International Airport, reinforcing its dedication to providing world-class handling of pharmaceutical goods.
The modern cargo warehouse at EuroAirport Basel includes an IATA CEIVcertified Swissport Pharma Center, which offers optimum conditions for handling temperature-sensitive goods, mainly from the pharmaceutical industry. Swissport plays a key role in the temperaturesensitive air cargo supply chain and its cargo infrastructure is renowned for its expertise in handling pharmaceutical products. In 2023, Swissport Cargo in Basel handled 43,000 tons of freight for 1,875 flights and employed 105 staff.
SATS and SF Group sign MoU to expand supply chain optimisation, drive global expansion

Singapore-headquartered SATS Ltd, the world’s largest provider of air cargo handling services and Asia’s pre-eminent provider of food solutions has signed a Memorandum of Understanding (MoU) with SF Group, the leading express delivery and logistics service provider in China and globally, to expand their
strategic collaboration and supply chain optimisation into a global footprint.
The partnership agreement between the market leaders was formally signed at SF Group’s headquarters in Shenzhen by Zhang Ji, Vice President of SF Group, and Bob Chi, CEO of Gateway Services AsiaPacific at SATS. Bob Chi will also jointly lead the Steering Committee overseeing regional or country-level Working Groups conducting the Strategic Projects under this agreement.
SATS and SF Group will combine their respective areas of expertise and service offerings as well as those of their affiliate companies, including Worldwide Flight Services (WFS), a member of the SATS
Group, and SF Airlines, the Chinese cargo airline owned by SF Group.
The partners will initially look to expand the successful collaboration of the existing hub operations in Singapore and eCommerce handling in Liege, Belgium, to other global hubs. These include the hub operations in Kuala Lumpur, Malaysia, and exploring Proof of Concepts (“PoCs”) for eCommerce handling in Beijing, and at New York’s JFK International Airport. The partners will also identify and build other network solutions or specialised services from more than 200 locations where SATS is present with SF Group’s extensive demand channels, which is currently the world’s 4th largest integrated logistic provider, and is based in China.

Menzies Aviation and KLM renew long-running partnership at Amsterdam Airport Schiphol
Menzies Aviation, the leading service partner to the world’s airports and airlines, announced the renewal of a major cargo and ground handling contract with the Dutch flag carrier, KLM Royal Dutch Airlines, at Amsterdam Airport Schiphol (AMS).
Menzies will provide cargo warehouse and ramp handling services for all KLM/ Martinair freighter operations at AMS for the next five years, with this renewed contract representing the company’s
largest contract at the main international airport in the Netherlands. The extension will see teams at the airport manage approximately 600 aircraft turns and handle almost 100,000 tonnes of cargo every year.
The renewal was announced at an official signing ceremony today at Menzies’ cargo facility at AMS where Miguel Gomez, EVP Europe and Dave Beekman, SVP Benelux from Menzies were joined by KLM Cargo’s Koen Bolster, Vice President
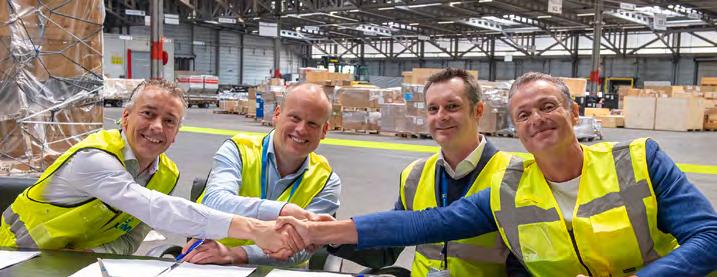
Worldwide Operations and Paul van der Wardt, General Manager Martinair Cargo to celebrate the successful partnership. This announcement underscores the relationship between KLM and Menzies Aviation, which stretches back decades. Menzies currently works with the airline at more than ten locations across the world, spanning Europe, Africa, India and Latin America.
DoKaSch temperature solutions expands global reach with new Opticooler® stations in Miami and Dublin
DoKaSch Temperature Solutions, a specialist in temperature-controlled active packaging, has opened new Opticooler® stations in Miami, USA, and Dublin, Ireland. These strategic locations enhance DoKaSch TS’s reach and provide better access to our reliable packaging solutions in the Americas and Europe, supporting the global supply of life-saving medicines.
Located near Miami International Airport (MIA), this new station will increase the availability of Opticooler® in the southern US and offer more flexibility to customers in the region as well as Latin America. The station has an initial capacity of 30 containers and is to be expanded further. Miami International Airport, the tenth busiest in the US, is a major hub for air traffic between the Americas and Latin America. The airport handles over 451,000 square feet of specialised facilities for temperature-sensitive goods, making it an ideal location for pharmaceutical distribution. In 2023 alone, $3.9 billion worth of medical products were managed at MIA.
The Dublin station, with a starting capacity of 40 containers, highlights Ireland’s growing importance in the life sciences sector. Ireland is home to manufacturing facilities for the world’s top ten pharmaceutical and biopharma companies and is the fifth-largest exporter of pharmaceutical products, according to the OECD.
The new Opticooler® stations in Miami and Dublin align perfectly with DoKaSch Temperature Solutions’ comprehensive Free Delivery Areas. This service ensures that the Opticooler® RAP and RKN containers are delivered directly to the loading point, with DoKaSch handling the organisation and coordination. Large Free Delivery Areas are available in Europe and the United States, with smaller regions covered in Asia, offering significant transport cost savings. The goal is to deliver the Opticooler® the evening before the rental period starts, ensuring the container is fully conditioned and ready for use. Even outside the Free Delivery Zones, DoKaSch provides worldwide delivery, ensuring clients benefit from cost savings, enhanced
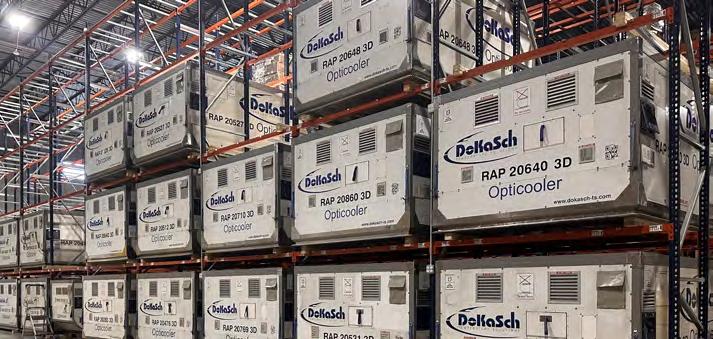
efficiency, and improved flexibility. With the opening of the new stations, these benefits are now more accessible, enhancing their global network and connectivity.
DoKaSch’s Opticooler® is known for its exceptional reliability and thermal stability in transporting sensitive pharmaceutical products. The containers feature advanced batteries and technology to maintain constant temperatures, ensuring product quality and eliminating the need for reloading and intermediate storage.
With these expansions, DoKaSch TS continues to strengthen its global network, ensuring the safe and efficient distribution of pharmaceutical products across key markets.
China Airlines’ new contract extends its partnership with Frankfurt Cargo Services beyond 25 years
Frankfurt Cargo Services (FCS) has earned a new multi-year cargo handling contract with China Airlines, extending their partnership at Frankfurt Airport, Germany’s biggest air cargo gateway, to over 25 years.
China Airlines signed its first cargo handling agreement in 2000 with FCS, a subsidiary of Worldwide Flight Services
(WFS), part of the SATS Group. Today, it is the most longstanding airline customer of FCS, transporting some 25,000 tons of cargo annually on its Boeing 777 flights connecting Frankfurt and Taipei.
The new contract commenced in August 2024. It also further extends China Airlines’ partnership with WFS, which provides cargo handling for the airline


in Belgium, Denmark, France, Germany, Ireland, Spain, and the United Kingdom as well as in India, Thailand, and North America.
NEWS - LOGISTICS
C.H. Robinson expands presence in Southeast Asia with new office in the Philippines
C.H. Robinson expands its presence in the Asia-Pacific region with the opening of its Filipino office. The strategic move bolsters support for the burgeoning logistics and transportation sectors in the country, aligning with C.H. Robinson’s commitment to providing unparalleled, tailored services in key markets worldwide.
As one of the most vibrant economies in Southeast Asia with a forecasted economic growth of 6 percent in 2024, the Philippines’ demand for freight and logistics services is quickly escalating due to higher levels of international trade and export. In particular, the country’s logistics industry contributes 4 to 6% to
its overall gross domestic product (GDP) and is expected to reach a market size of P1.160 trillion by 2027.
“C.H. Robinson has long held a presence in the Philippines via our partners’ logistics network. The opening of an office here elevates our commitment to the country and the region, and further facilitates our customers’ access to our expansive global network. Looking ahead, the office will provide customers in the country with global scale and connectivity to key trading partners, such as the United States, Singapore, South Korea, Germany, and China (including Hong Kong SAR),” said Andrew Coldrey, vice president, APAC, C.H. Robinson.
In addition, existing and potential customers can tap into C.H. Robinson’s vast North American trucking network to offer seamless delivery for end customers. The new office, located in Manila, will be led by Bobo Yang in her new role as General Manager. Bobo will be responsible for developing the Filipino business as well as securing opportunities for regional and global sales.
C.H. Robinson’s multimodal transportation management system and specialised expertise will also cater to major manufacturing industries in the Philippines, with a particular focus on automotive and high-tech sectors such as semiconductors and integrated circuits. By delivering tailor-made solutions, C.H. Robinson aims to play a pivotal role in fostering sustained growth and efficiency within the Philippine logistics industry.
International Cargo Logistics doubles cold storage facility at Heathrow to meet boom in demand

Global forwarder, International Cargo Logistics (ICL), has nearly doubled the size of its cold storage facility at Heathrow Airport, from 153 square metres to 300 square metres, to meet rapidly growing
customer demand.
ICL Site Unit 13 now consists of five chambers with varying temperature regimes, as well as X-ray and external temporary storage facilities (ESTF), and temperature-controlled vehicles to transport goods across the UK.
In addition, the facility boasts inspection areas for the Department for Environment, Food & Rural Affairs (DEFRA) and a control point for Customs checks and clearances,
further streamlining operations.
Earlier this year, ICL expanded its temperature-controlled airfreight capabilities in the UK when it launched a partnership with FreshLinc, collaborating on final-mile delivery. ICL also opened a new office in Rotterdam, the Netherlands, as part of an ongoing growth strategy focused on expanding its perishables operations across Europe and beyond. ICL will further extend its global reach this year and plans to expand into Southeast Asia, starting with a new office in Vietnam.
Navia Freight deploys Raft AI, streaming operations, and delivers a new class of performance insights
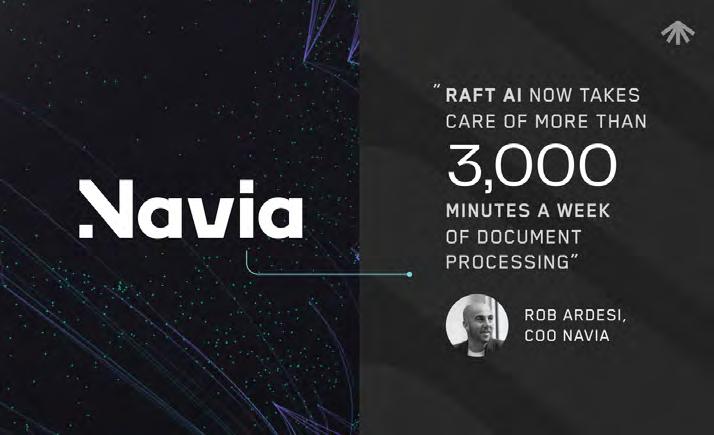
Raft announced that Navia, an integrated global freight and logistics company, has successfully rolled out its AI-automated logistics finance capability to process high volumes of AP invoices.
Every month, Navia finance teams receive thousands of invoices from the partners they work with to keep their customer’s freight moving. With Raft, AI now handles the bulk of that processing, including
not just document processing and data extraction, but also validation against existing data. This allows Navia teams to focus on providing services and value to their customers.
Navia is a vertically integrated supply chain partner that provides solutions in purchase order and vendor management, freight forwarding, customs brokerage, and third-party logistics for B2B and e-commerce applications. Experienced staff with deep-level expertise leverage proprietary and partner technology to move hundreds of thousands of containers a year across nine offices globally, with over 100,000 items dispatched for some of the world’s leading retail and industrial machinery companies.
AI is helping Navia overcome the
hurdles of manual financial operations with zero-touch invoice processing, automated approval workflows, and centralised dashboards. Today, 35% of invoices received don’t need any human intervention to process successfully, and another 40% require just one touch. At scale, these were workloads that previously consumed a significant amount of work by the Navia finance teams.
Raft is the world’s largest AI-powered logistics platform, used by more than 50 logistics providers – companies that together help run 80% of the Global 1000 supply chains. Each year, more than 10,000 users manage over 5 million shipments on the platform, representing every commodity, transit mode, and trade lane.

Kuehne+Nagel and Mercedes-Benz boost sustainable air freight with aviation fuel innovation
As a long-standing airfreight partner of Mercedes-Benz, Kuehne+Nagel has also been supporting Mercedes-Benz’s logistics chains to the USA since 2019, for example for the plant in Alabama. For over a year, sustainable fuels have been used in this strategic partnership in transport logistics. Sustainable aviation fuel is used for the vehicle manufacturer’s air freight transport, thus, actively supporting Mercedes-Benz in decarbonising their supply chain.
Thanks to the use of SAF, Mercedes-Benz has reduced around 11,000 tonnes of CO2 emissions in the past twelve months,
in comparison to only using conventional fuels. SAF was used on charter flights with Kuehne+Nagel’s own Boeing 7478F cargo aircraft ‘Inspire’ on the route from Stuttgart (Germany) to Birmingham (Alabama, USA).
Mercedes-Benz and Kuehne+Nagel have set themselves the goal of avoiding and actively reducing emissions in transport logistics. “Transport logistics is a key part of the automotive value chain. By using sustainable aviation fuel for air freight transport, we can reduce emissions along our value chain and take an important step towards net carbon neutrality. We
Dachser completes acquisition of Brummer
The German-Austrian Brummer Group is now wholly owned by Dachser and has become a part of Dachser’s European network for the transport and storage of temperature-controlled food. This marks the beginning of Brummer’s full integration into the Dachser network. Customers will benefit from uniform quality standards.
In April, to expand its own European food logistics network to cover Austria and neighbouring countries, Dachser announced its intention to acquire Brummer, one of Central Europe’s leading food logistics companies. Following the green light from the German and Austrian competition authorities, the acquisition has now been completed and work can begin on integrating Brummer into Dachser’s network. Dachser has acquired Brummer Logistik GmbH in Germany and Brummer Logistic Solutions GmbH & Co KG in Austria—in other words, the entirety of the Brummer Group’s
are delighted to reach another milestone in sustainable logistics together with our partner Kuehne+Nagel,” says Jörg Burzer, Member of the Board of Management of Mercedes-Benz Group AG, Production, Quality and Supply Chain Management.
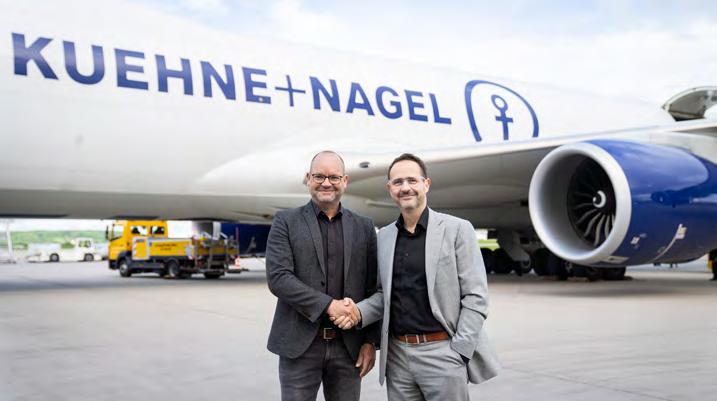

operational logistics business.
As an effective full-service logistics provider, Brummer has specialized in transport, warehousing, and contract logistics services for food, including frozen foods below −18 degrees Celsius, in the region of southern Germany and Austria.
Brummer was one of the founding partners of the European Food Network in 2013, which spans 34 European countries under Dachser’s system leadership. This network offers manufacturers,
suppliers, and retailers in the food market access to unparalleled network coverage for groupage transports within Europe. Brummer’s operational logistics business comprises more than 300 of its refrigerated trucks, some 85,000 m2 of storage space, and an e-commerce fulfilment centre in Sankt Marienkirchen. In 2023, Brummer generated revenue of around EUR 128 million. As part of the transaction, almost all the roughly 950 employees at the two locations close to the border in Neuburg am Inn, Germany, and Sankt Marienkirchen, near Schärding, Austria, have transferred to Dachser.
Teleport opts for Wiremind’s SKYPALLET solution
Teleport, the logistics venture of Capital A Berhad is the first Southeast Asian logistics provider to implement Wiremind’s SKYPALLET product and is also lined up as one of the first customers of upcoming SKYPALLET Version 2.
Southeast Asia’s number one integrated logistics provider, Teleport, and Wiremind signed the SKYPALLET implementation contract on 01 June 2024, following a successful Proof of Concept trial. The stepwise roll-out of the original SKYPALLET software version is now
underway, with a subsequent SKYPALLET Version 2 deployment phase planned as soon as the product is launched later this year.
Initial cooperation talks began at the end of last year when Teleport sought to find the perfect digital fit to advance its capacity steering and load planning processes. Having established Teleport’s requirements, Wiremind arranged an accompanied trial period enabling the carrier to test the full range of SKYPALLET’s functionalities. In particular,

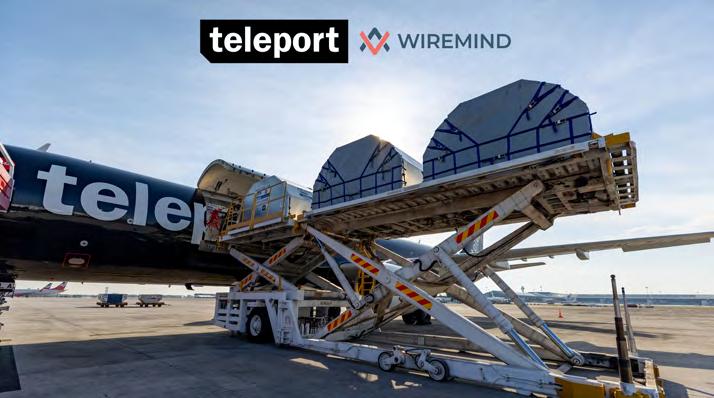
SKYPALLET’s advanced algorithmic logic and the software’s extensive integration options convinced Teleport to begin implementation.
MASkargo and CargoAi revolutionises airfreight transactions with CargoWALLET

CargoAi announced a strategic partnership with MASkargo, the cargo airline and subsidiary of Malaysia Aviation Group. This collaboration aims to revolutionise airfreight booking and payment processes across nearly 100 countries worldwide through CargoWALLET, CargoAi’s innovative payment solution.
This partnership integrates MASkargo’s
extensive airfreight services into CargoAi’s ecosystem, arming freight forwarders with the ability to book and pay for shipments directly through CargoWALLET.
From its hub in Kuala Lumpur, MASkargo is significantly accelerating the digitalisation of air cargo in the APAC region by offering all its worldwide cargo capacity, belly, and freighters on CargoAi. The new synergy between CargoAi and MASkargo will
open up a more extensive network to all forwarding agents worldwide.
CargoWALLET’s advanced capabilities include instant payment processing, eliminating the need for bank guarantees, and offering a variety of preferred payment methods, such as local transfers and credit card payments. This not only removes the reliance on cash payments but also ensures secure and efficient financial transactions.
Moreover, the reconciliation process is automated within CargoWALLET, reducing administrative burdens, and enhancing operational efficiency for freight forwarders. Importantly, freight forwarders using CargoMART do not need to provide a bank guarantee or pay yearly subscriptions to access CargoWALLET, simplifying their financial processes and reducing overhead costs.
This partnership with MASkargo demonstrates CargoAi’s dedication to driving innovation and delivering unparalleled value to its customers. By leveraging CargoWALLET, freight forwarders can now enjoy a more streamlined, cost-effective, and efficient booking and payment experience.
Royal Air Maroc Cargo kick-starts its first digital bookings with cargo.one
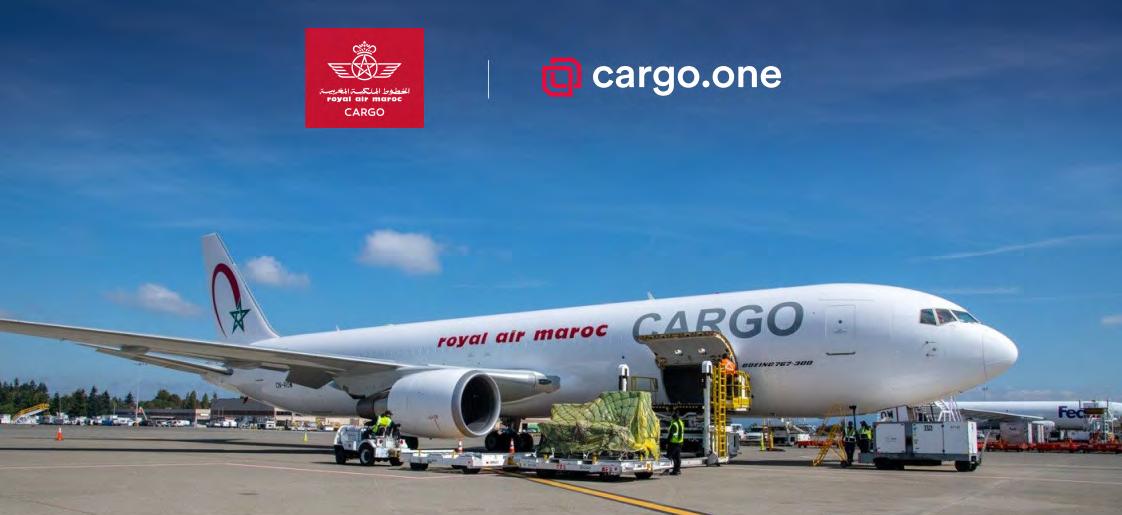
Royal Air Maroc Cargo and cargo.one unveiled a global partnership that brings the Moroccan national carrier’s cargo capacity to the leading platform for digital air cargo bookings. Providing its first digital sales channel, cargo.one now delivers its user-friendly and efficient booking platform for Royal Air Maroc Cargo offers. The airline partnered with cargo.one based on its ability to deliver a world-class digital booking experience and visibility across cargo.one’s vast
global footprint of customer markets. Freight forwarders using cargo.one now has instant digital access to valuable connectivity from Royal Air Maroc Cargo. Offering both belly and dedicated freighter capacity, Royal Air Maroc Cargo is developing fast. With a flexible fleet and its main hub in Casablanca, the carrier benefits from a geostrategic location at the crossroads of international air cargo lanes linking the Americas, Europe, Africa
and the Middle-East. Royal Air Maroc Cargo offers a broad range of cargo services catering to many industries and sectors.
cargo.one delivers forwarders the goto choice for instantly scanning the global market and quoting and booking confirmed shipments at speed. The launch of Royal Air Maroc Cargo services further enriches cargo.one’s acclaimed diversity of global supply options. Subject to route availability, Royal Air Maroc Cargo customers can now book digitally for General Cargo shipments up to 1000kg (wide body) and 500kg (narrow body), and perishable shipments in the coming weeks, with all bookings benefiting from cargo.one standards for usability, control and competitive rates.
Freight forwarders using cargo.one can now book Royal Air Maroc Cargo capacity for General Cargo from selected EMEA markets, with many additional markets including North America, and the Middle East being added in the coming weeks.

Scan Global Logistics expands its worldwide transport network by opening its first offices in Saudi Arabia
Global freight forwarder Scan Global Logistics (SGL) added a new country to its global network by establishing new locations in Riyadh and Jeddah. This gives the company an immediate footprint in the economic Central and West Provinces of Saudi Arabia as part of its strategic expansion plan. With one additional office planned for 2024 in Dammam in the East province, this emphasises a market in which the company sees great potential.
Establishing a local presence in Saudi Arabia provides access to one of the fastest-growing economies globally. This expansion is driven by Saudi Arabia’s strategic location as a central gateway to the Gulf Cooperation Council (GCC) countries, Europe, Asia, and Africa, which makes the country an ideal distribution hub for these regions.
The country is heavily investing in infrastructure projects to diversify its economy and thereby minimise its dependence on oil. Furthermore, Saudi

Arabia’s growing buying demand requires more logistics. The country’s wellestablished transportation infrastructure, including air, ocean, and road networks,
makes trade and commerce seamless and efficient, facilitating businesses’ ability to reach regional and international markets easily.
CargoAi launches Shipper Quotation Module on CargoMART
CargoAi, the industry’s fastest-growing digital enabler, announced the launch of its newest innovative feature, the Shipper Quotation Module, on CargoMART. This latest addition provides small, medium, and large freight forwarders with a powerful tool to create and customise real-time quotations for their customers, significantly reducing the back-and-forth routine between procurement and sales teams.
In an industry where efficiency and accuracy are critical, CargoAi’s Shipper Quotation Module revolutionizes the way freight forwarders generate and manage quotations with their clients.
The feature allows users to create detailed, real-time quotes tailored to their customers’ specific needs, streamlining the sales process and enhancing customer satisfaction. By integrating this module into CargoMART, CargoAi continues to demonstrate its commitment to providing comprehensive digital solutions that drive operational efficiency and business growth
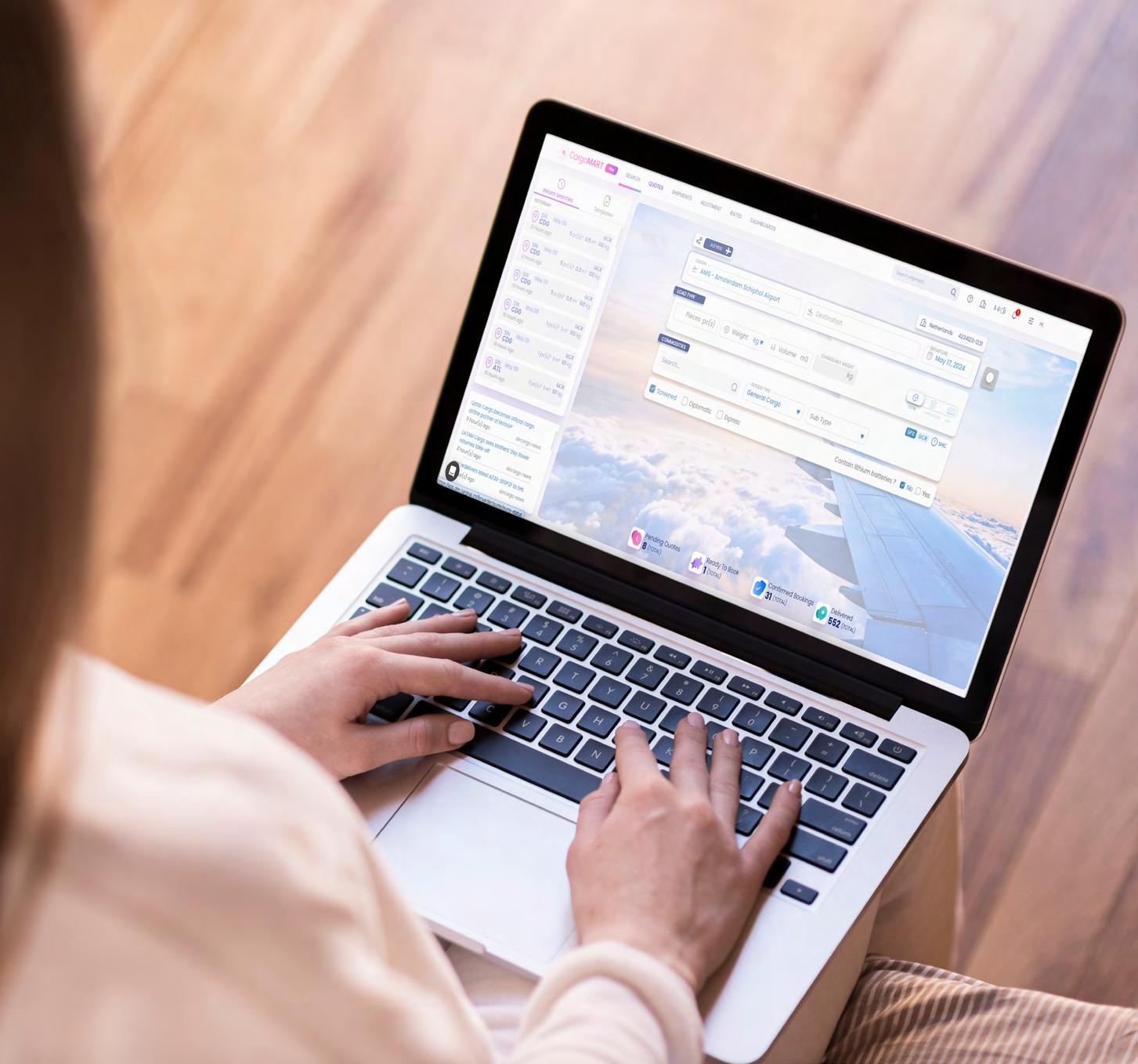

- EXPRESS
FedEx signs agreement to expand Philippine gateway in Clark
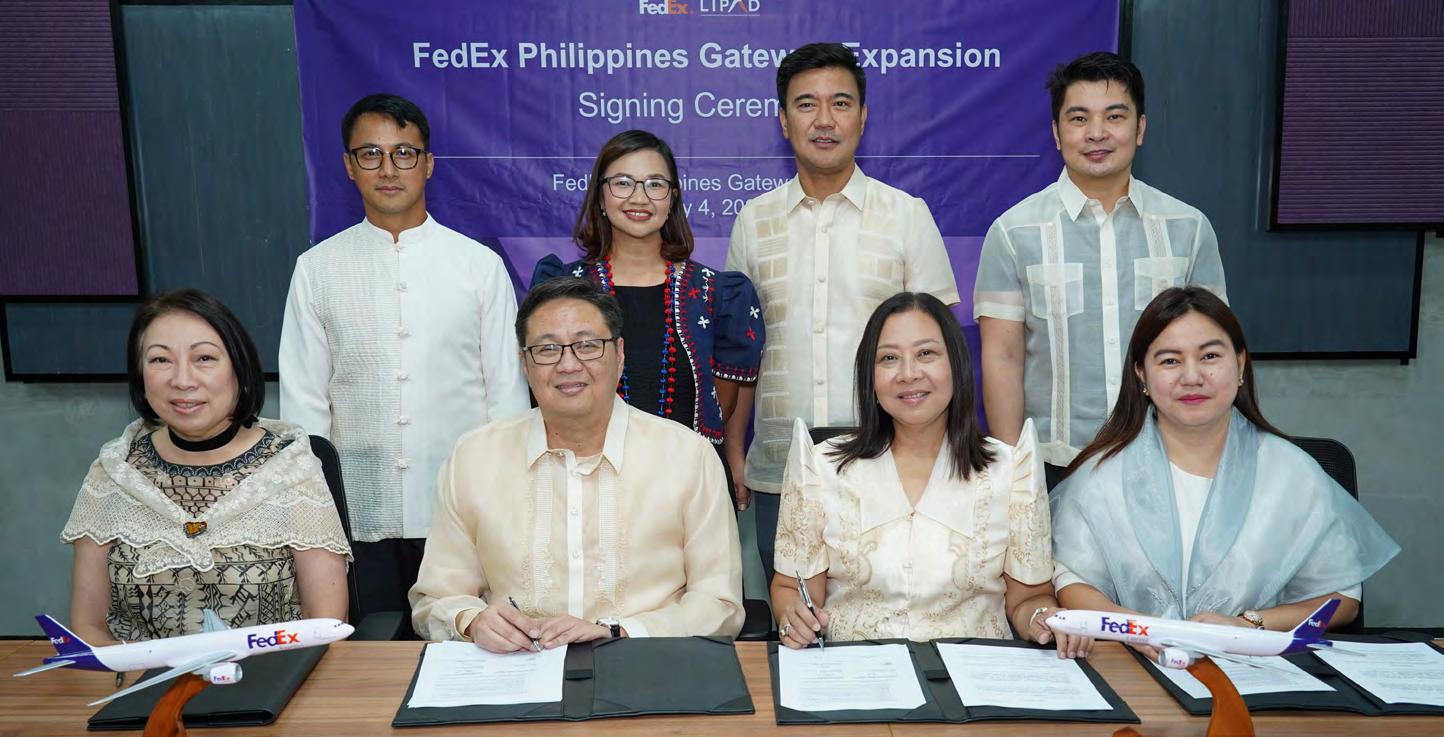
Federal Express Corporation signed an agreement with Luzon International Premiere Airport Development (LIPAD), operator and manager of Clark International Airport, to expand and upgrade the company’s gateway in Clark, Pampanga. The new facility is set to offer enhanced capabilities that benefit local businesses looking to amplify their presence in international markets and support the growing demand for e-commerce, freight, and cold-chain shipments across the Asia Pacific region.
To demonstrate their support for the expansion, Joshua Bingcang, President and Chief Executive Officer, Bases Conversion and Development Authority
Arrey Perez, President, Clark International Airport Corporation (CIAC), and Noelle Meneses, Vice President for Business Development and Business Enhancement, Clark Development Corporation (CDC) attended the signing ceremony at the FedEx Gateway.
Upon completion, the new FedEx facility will be more than double the size of its current facility. The gateway will further boost support for importers and exporters including small and medium enterprises (SMEs) and heavy-weight freight shippers with greater and more reliable access to and from international markets.
Australia Post opens multi-million-dollar Parcel Facility on the Gold Coast

Australia Post officially opened its new $12 million Parcel Facility on the Gold Coast, cementing its long-term investment in the region.
Built to accommodate increased parcel growth, the modern 15,087m2 facility will improve turnaround times and help process up to 6,000 parcels per hour,
75,000 parcels a day and up to 90,000 during peak periods like Christmas. Minister for Communications, the Hon Michelle Rowland MP and Australia Post Executive General Manager Network Operations Rod Barnes were onsite to unveil the facility.
The new state-of-the-art facility integrates cutting-edge sortation technology, enabling increased visibility of customer parcels moving throughout the network and seamlessly integrating Australia Post’s suite of services including Express Post, Parcel Post, StarTrack Premium and its newest next-day delivery service, Australia Post Metro, to provide a better experience for customers.
In a first for Australia Post, the facility
This strategic expansion aligns with the vision of BCDA, CDC, and LIPAD to transform Clark International Airport (CRK) into a premier global civil aviation logistics hub for international cargo. The planned establishment of additional facilities, such as aprons and taxiways will facilitate FedEx operations, enabling better handling of cargo and fostering growth in the logistics sector. These developments are expected to bring economic benefits to the northern Luzon region, providing job opportunities for the local community and serving as an economic stimulus in the region.
In October 2021, FedEx first unveiled its gateway in Clark to boost support for local businesses and e-commerce growth. Equipped with state-of-the-art technology, the 17,000-square-meter facility can sort up to 9,000 parcels per hour and enables FedEx to provide customers with reliable service more efficiently. The facility’s dedicated freighthandling area spans 630 square meters.
As FedEx celebrates its 40th anniversary in the Philippines, the company continues to offer products and services that provide convenience for customers. In October 2023, FedEx launched a new flight service between Vietnam and the Philippines with improved transit time, supporting the growth in trade volumes between both markets. The continuous introduction of an enhanced and differentiated portfolio of solutions from FedEx will enable Philippine businesses to capture more import and export opportunities.
has achieved an accredited 5-star Green Star rating, featuring a 99kW solar system capable of powering up to 30% of the total load for the facility, to reduce carbon emissions.
The opening also commemorates 50 years of StarTrack, with the new facility enabling StarTrack to collect from over 250 customers daily and servicing an average of 25,000 delivery points within the Premium network.
The new facility will accommodate over 300 team members in the region and recruitment for Australia Post’s peak period in the lead-up to Christmas will commence soon with casual jobs available for interested locals.

(BCDA),
UPS
to acquire Estafeta, providing powerful global logistics solutions and trade opportunities for customers in Mexico and beyond
UPS announced that it has agreed to acquire Estafeta, a leading Mexican express delivery company. This acquisition is a key part of UPS’s ‘Better and Bolder’ strategy, aimed at becoming the world’s premium international small package and logistics provider.
The acquisition is an evolution of a commercial agreement established between the two companies in 2020. When the two companies are combined, customers can rely on UPS’s integrated solutions that link small package, healthcare logistics and endto-end supply chain solutions, creating a differentiated ‘One UPS’ advantage.
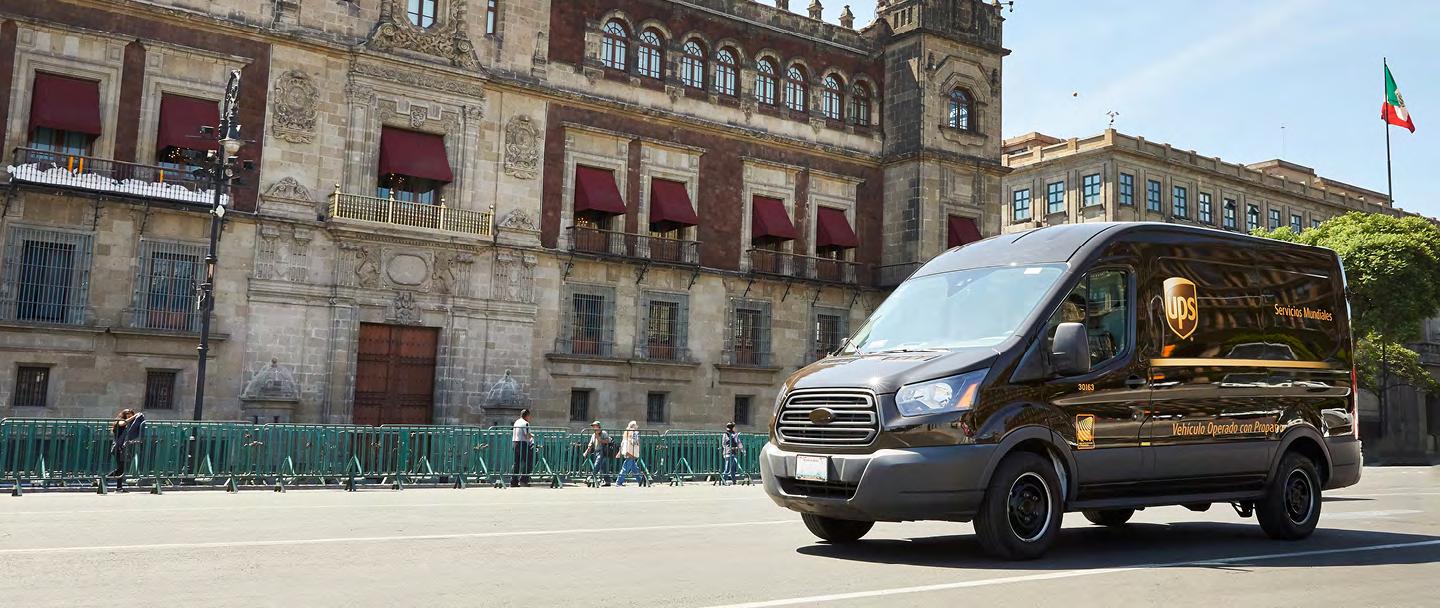
The acquisition is targeted to close by the end of this year, subject to customary closing conditions and regulatory
approvals. The value and terms of the transaction are not being disclosed at this time.
DHL extends partnership with Mitteldeutsche Flughafen AG until 2053

DHL Group has extended the framework agreement with Mitteldeutsche Flughafen AG (MFAG) ahead of schedule by a further 15 years until 2053. The company is making a significant contribution to the economic stability and future viability of Leipzig/Halle Airport and the region. In addition, the Group will continue to expand the aprons over the next few years and reaffirm its commitment to the Schkeuditz site.
Tobias Meyer, CEO DHL Group said, “The DHL Hub in Leipzig is an important engine for the economy of Central Germany. We welcome the extension of the framework agreement, which gives us planning security, enables further investment in
the site and provides long-term security for the jobs at the hub. Even though we are now paying significantly higher fees for the remaining term of the old agreement, the result is economically viable. We would like to expressly thank the Saxon state government for its continued strong commitment to the site. At the same time, we hope that MFAG will successfully overcome its structural problems and that business beyond DHL will also develop positively. DHL’s development at the Schkeuditz site is a success story and we hope for further fruitful cooperation with all partners involved.”
Opened in 2008, the DHL air freight hub at Leipzig/Halle Airport is the largest of

three global hubs in the DHL Express network with a unique significance for the Group’s worldwide logistics. The location has positive effects on the labor market and economic development in all neighboring districts. As a result, the region has developed into one of the world’s leading logistics locations. Every night, 2,000 tons of freight in the form of 350,000 shipments are handled and flown to more than 50 destinations worldwide by an average of 75 aircraft per working day. The Group has so far invested around 780 million euros at the Leipzig site and created more than 7,000 jobs.
Joost Meijs appointed CEO at Maastricht Aachen Airport
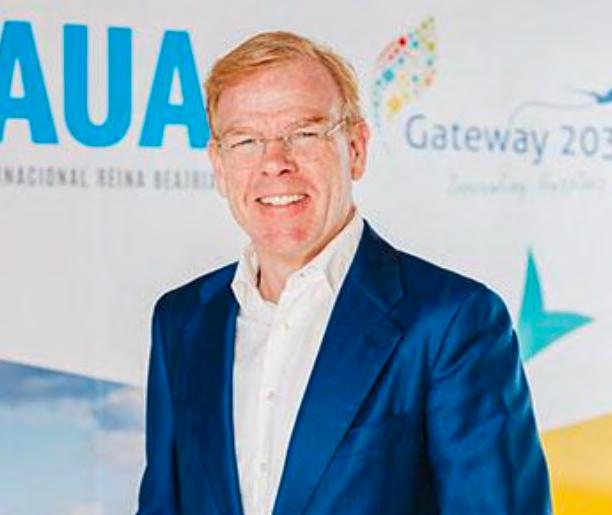
Joost Meijs has been appointed as CEO of Maastricht Aachen Airport (MST), starting 1st October 2024, with Meijs succeeding Jonas van Stekelenburg as director of NV HBLM.
NV HBLM includes the operating companies Maastricht Aachen Airport
DHL Global Forwarding announces new President Director for Indonesia

Kale Logistics
BV and Maastricht Aachen Airport Management & Infra. The Supervisory Board has appointed Joost Meijs due to his extensive leadership experience and track record in the aviation industry; currently, Joost Meijs is the CEO of Aruba Airport, and before that Eindhoven Airport. The shareholders and works council support his appointment.
Under Joost ́s leadership from 2008 until 2019, Eindhoven Airport developed into a mature airport in the Dutch market. Meijs created, in an open dialogue with the external stakeholders, the foundation for a sustainable development of the airport since then.
From 2019 until now, Meijs, as CEO of Aruba Airport, has navigated the airport through the pandemic and successfully implemented a new corporate strategy
DHL Global Forwarding has appointed Nicholas Bongsosartono as the new President Director of DHL Global Forwarding Indonesia. Based in Jakarta, Bongsosartono will report to Thomas Tieber, CEO of DHL Global Forwarding, Southeast Asia and South Pacific.
In this new position, Bongsosartono will drive growth, improve operational efficiency, and deliver service excellence to customers in the Indonesian market.
Bongsosartono joined DHL Global Forwarding Indonesia in May 2023 as Head of Airfreight. Before this, he was the Head of Product Management at AP Moller-Maersk for Indonesia and the Philippines, where he designed and managed a comprehensive portfolio of commercial products and services.
Bongsosartono also brings valuable
Solutions welcomes
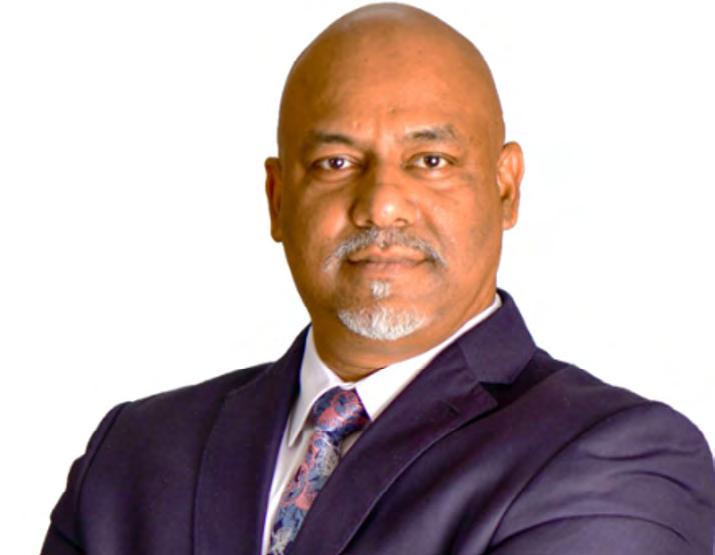
with his team. This strategy aims to make Aruba one of the safest, sustainable, and future-proofed airports in South America and the Caribbean; the first phase of Gateway 2030, an extensive USD300 million plus investment programme, was recently delivered.
Meijs played a key role in establishing the Dutch Caribbean Cooperation of Airports (DCCA), which aims to improve the safety, connectivity, and sustainability of the airports in the region. This initiative resulted in the launch of the first electric plane in the Caribbean airspace from Aruba Airport in 2022.
Meijs’ appointment comes after a successful start of the year for the airport, including new (cargo) airlines like Pegasus Airlines and ROM Cargo, Airport Carbon Accreditation level 3, and facilitating Europe’s first-ever international electric flight for members of the public.
expertise from his previous roles, where his responsibilities included health, safety, security, and environment, as well as procurement of goods and services such as warehousing, trucking, and customs clearance services. Additionally, he gained a wealth of experience in information technology as the IT manager of a logistics company in the early stages of his career.
DHL Global Forwarding Indonesia has expanded its presence and enhanced its service offerings to respond to customers’ evolving needs. In March 2024, the company launched its first EV logistics Hub in Batam, Indonesia to contribute to the country’s integrated EV supply chain development. It was also at the forefront of electric last-mile delivery in Jakarta, being the first freight forwarder to deploy an electric van in the city.
Sanjeev Madavi as new Chief Innovation Officer
Kale Logistics (Kale) has appointed a new Chief Innovation Officer Sanjeev Madavi, with nearly 30 years of experience in digital transformation and innovation in international supply chain and logistics industry.
In his new role, Sanjeev will lead Kale’s continued expansion into multi-modal community platforms, aiming to enhance and develop new services that complement the company’s flagship Cargo Community Systems (CCS). His
focus will be on addressing the evolving needs of the logistics community by introducing value-added services that further streamline and synchronize CCS platforms, transforming them into more adaptable and unified sources of data.
Sanjeev’s career is decorated with accolades, including the prestigious IDC CIO Award in 2022 and the AchieversX CDO Award in 2023, recognizing his outstanding contributions to enhancing digital capabilities in previous roles.

Safeguarding dangerous goods and pharmaceuticals in global logistics
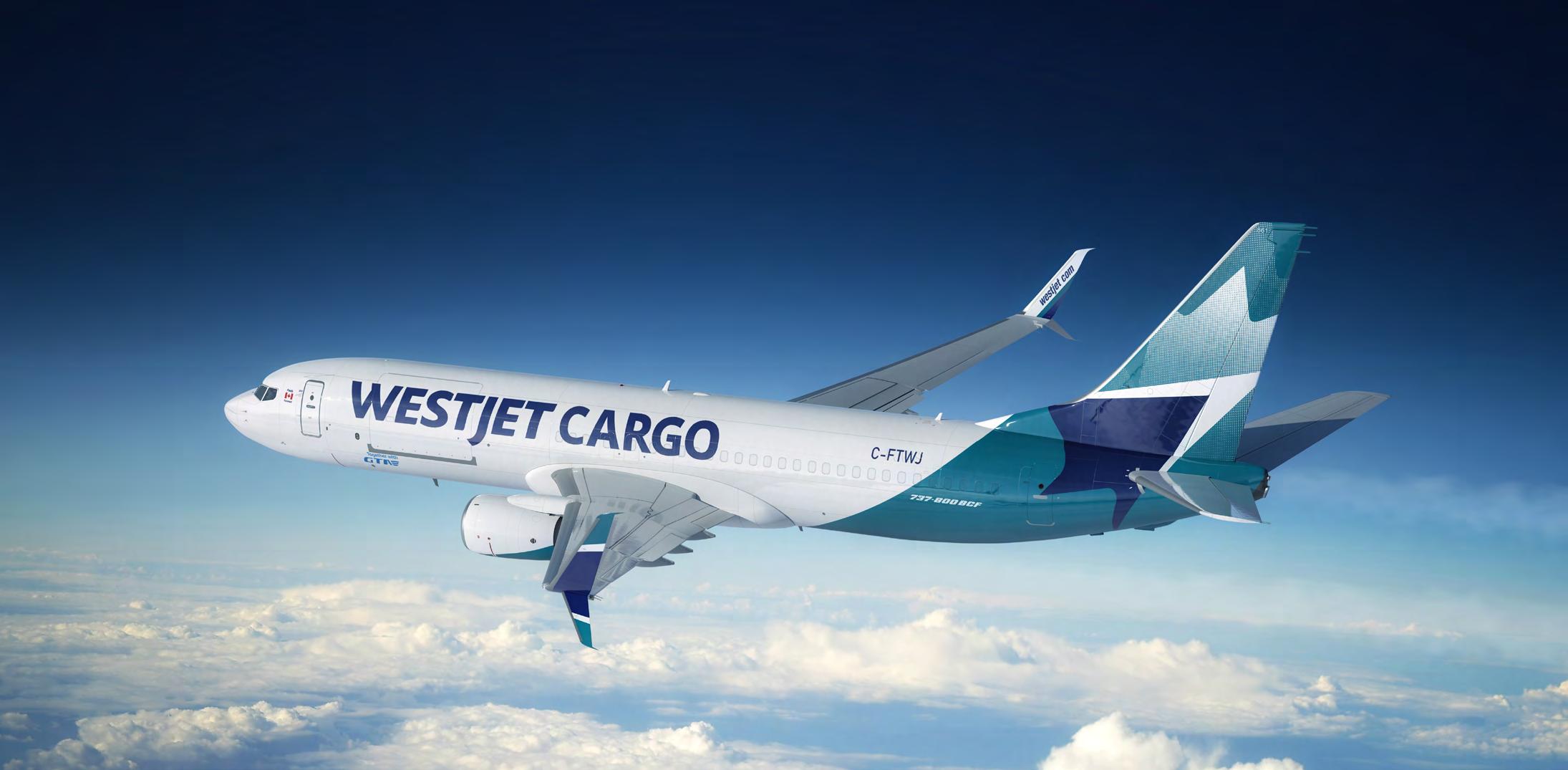
A specialised cargo plane touches down at midnight. Its cargo: a radiopharmaceutical with a six-hour halflife, racing against time to reach a patient across the globe. This is the high-stakes world of transporting dangerous goods and pharmaceuticals—where precision is paramount and the margin for error is zero.
In today’s complex cargo logistics landscape, ensuring safe and compliant transport of these sensitive materials isn’t just a priority—it’s an absolute necessity. Each shipment, be it volatile chemicals or temperature-sensitive medications, carries unique risks. A single oversight—a mislabeled package or slight temperature deviation—can trigger far-reaching consequences for public safety, the environment, and global supply chains.
As international trade expands, the logistics industry faces unprecedented challenges. Traditional methods are strained under growing demands while emerging technologies offer new solutions for safety and compliance. Meeting these challenges requires a coordinated effort from air cargo and logistics companies, regulatory bodies, and industry stakeholders, blending cutting-edge tech, rigorous safety protocols, and specialised training to navigate the intricacies of this critical field.
The stakes of safe transport
At the heart of the logistics industry’s
safety efforts are the inherent risks posed by dangerous goods and pharmaceuticals. According to the International Air Transport Association (IATA), time and temperature are critical when transporting pharmaceuticals, with radiological medicines posing particular challenges due to their extremely short half-life. “When goods are being transported across the globe, there are wide temperature variations, far more than that permitted by health authorities for medical products,” says Brendan Sullivan, IATA’s Global Head of Cargo. This highlights the need for stringent temperature control and tracking solutions
WestJet Cargo, for example, emphasises the importance of adhering to IATA’s Dangerous Goods Regulations (DGR). “We strictly follow IATA’s DGR to ensure the proper classification, packaging, labelling, and documentation of dangerous goods,” says Kirsten de Bruijn, Executive Vice President, WestJet Cargo, citing their comprehensive training programs and collaboration with regulatory bodies like Transport Canada Civil Aviation (TCCA) Regulatory landscape
The regulatory framework governing the transport of dangerous goods and pharmaceuticals is a complex web of international, national, and industryspecific guidelines. IATA plays a key role in setting these standards. “We work closely with our members, governments,

regulatory agencies, and specialised United Nations agencies, such as ICAO, to develop and improve upon these standards,” explains Brendan.
The annual updates to IATA’s Dangerous Goods Regulations reflect the evolving challenges in the industry. For instance, new regulations have been introduced for sodium-ion batteries and lithium battery-powered vehicles. These updates are part of a broader effort to address the increasing safety risks associated with the transport of new and emerging products

BRENDAN SULLIVAN
Global Head of Cargo, IATA

Emerging technologies and innovation
Innovative solutions are revolutionising the transport of hazardous goods and pharmaceuticals. While advanced tracking systems and temperaturecontrolled logistics remain crucial, emerging technologies are taking centre stage.
IATA’s ONE Record data exchange standard is leading this evolution. “The vision for ONE Record is to establish an end-to-end digital logistics and transport supply chain where data is easily and transparently exchanged in a digital ecosystem of air cargo stakeholders, communities, and data platforms,” explains Brendan.
Blockchain technology is enhancing supply chain transparency, while Artificial Intelligence (AI) is being leveraged for predictive analytics in risk management. “Screening technologies, their underlying assessment algorithms, and AI-assisted tools will continue to improve, enabling the detection and removal of noncomplying dangerous goods,” Brendan notes.
The Internet of Things (IoT) also plays a crucial role. IATA’s Recommended Practice 1692 for IoT data sharing standardises how data from tracking devices and sensors is shared, facilitating real-time monitoring of shipment conditions.
As the industry moves towards paperless operations, digital communication systems are reducing reliance on traditional documentation. Brendan predicts, “We will be seeing the data sitting in one source; shared and accessed as needed by the various stakeholders, significantly reducing the dwell time between the goods leaving the consignor
and arriving at the consignee.”
These technological advancements are not just improving safety and compliance; they’re transforming the entire landscape of dangerous goods and pharmaceutical transportation, paving the way for a more efficient, transparent, and secure future in global logistics.
The economics of safety
Meanwhile, the economic implications of safety measures in transporting dangerous goods and pharmaceuticals are significant, though often overlooked. Before the COVID-19 pandemic, over $15 billion worth of pharmaceutical products were lost annually due to temperature excursions. When factoring in costs such as damage analysis and replacement products, these losses total approximately $35 billion each year, according to a Coretex report.
Brendan hints at this when discussing the shift towards air cargo: “Manufacturers and wholesalers are turning more towards aviation due to the value of unproductive inventory that is in transit. Pharmaceuticals and healthcare industryrelated products that have a short shelf-life are especially susceptible to a relative loss in value when on water.” This suggests that the higher costs of air transport are offset by the reduced risk of product degradation or loss. Furthermore, IATA’s focus on minimising


KIRSTEN DE BRUIJN
Executive Vice President, WestJet Cargo
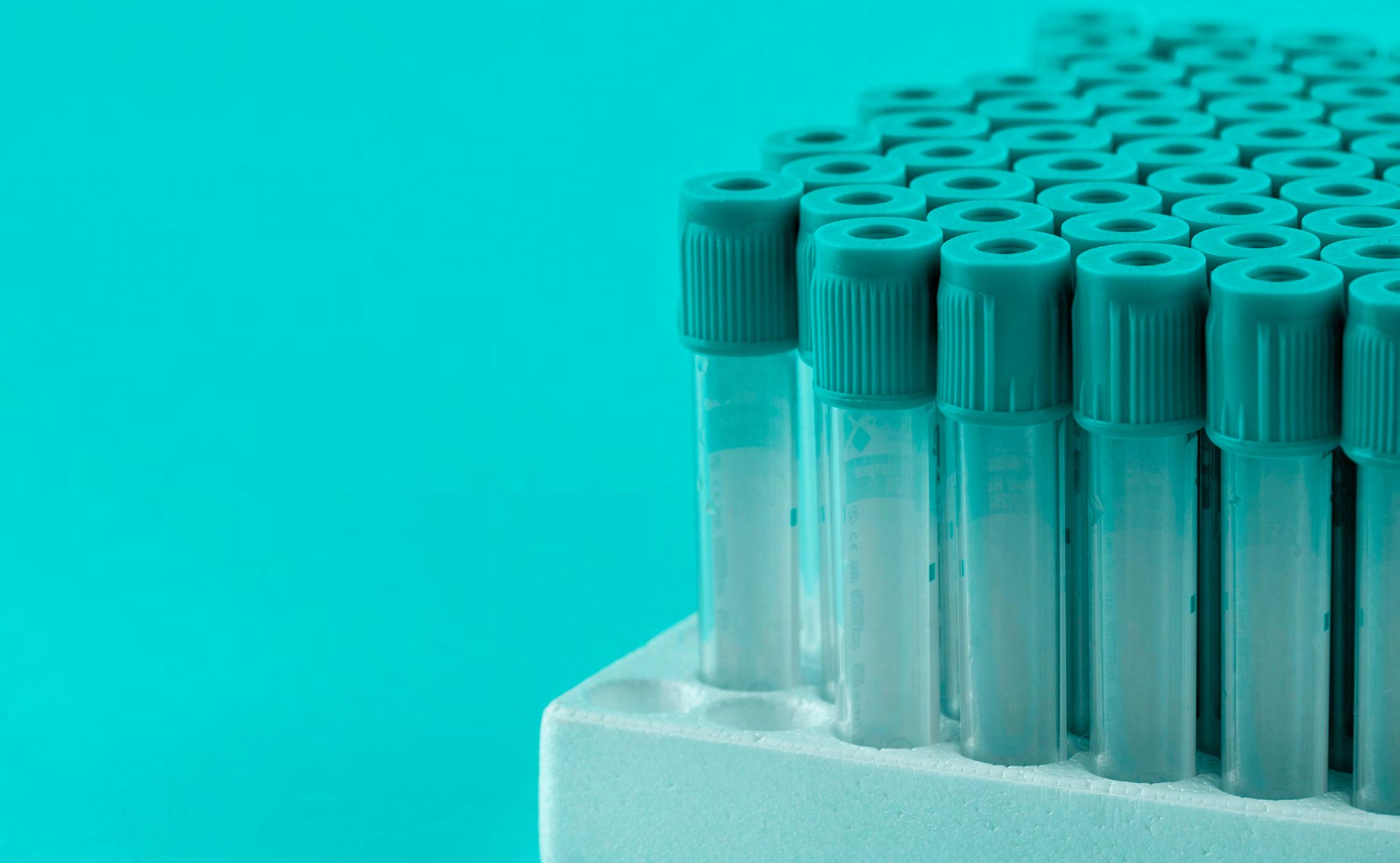
“the loss of goods during transportation due to temperature excursions, mishandling, improper packaging, and other factors” underscores the financial incentives for implementing robust safety measures. While the initial investment in advanced technologies and training may be substantial, the potential costs of noncompliance—including regulatory fines, reputational damage, and loss of highvalue cargo—make a compelling case for prioritising safety and compliance in the long term.
Training and expertise
Specialised training is another crucial component of ensuring safety and compliance. IATA offers a range of certification programs, such as CEIV Pharma and CEIV Lithium Batteries, to help companies enhance their handling of sensitive cargo. “We also provide courses on temperature-controlled cargo operations and risk management for time-sensitive goods,” says Brendan.
WestJet Cargo echoes the importance of training, noting that they offer comprehensive certification programs for employees handling dangerous goods. “We conduct regular drills and simulations to prepare staff for emergency situations and ensure swift, effective responses,”
adds Kirsten.
Case studies and success stories
Real-world scenarios provide a glimpse into how logistics companies are navigating these challenges. WestJet Cargo shares an example where they successfully transported aircraft engines across the Canada-U.S. border. “One of the critical safety requirements was having a certified Ground Handling Agent (GHA) available for each flight. By preparing a contingency plan, we maintained the highest safety standards and transported the engines without any disruptions,” explains Kirsten.
IATA also highlights the success of LATAM Cargo, which has benefited from the CEIV Pharma certification process. “The critical internal review of processes and procedures through CEIV has enabled LATAM Cargo to improve safety, and efficiency, and reduce wastage and errors,” says Brendan.
A vision for the future of logistics
As the air cargo and logistics industry looks to the future, sustainability, safety, and technological innovation are converging to redefine the transport of dangerous goods and pharmaceuticals. Companies

like WestJet Cargo are adopting ecofriendly packaging and modernising fleets to reduce carbon emissions, while IATA focuses on minimising single-use plastics and promoting sustainable infrastructure at cargo facilities.
The industry is at a pivotal moment, where advanced tracking systems, smart packaging, and automated handling solutions are becoming standard practices. Brendan emphasises the importance of digital transformation: “Future advancements will focus on improving digital communication and reducing reliance on paper-based systems. By integrating real-time data access across supply chains, we can significantly reduce errors and ensure the safety of dangerous goods transport.”
Kirsten De Bruijn from WestJet Cargo adds, “We are witnessing the rise of a more responsible logistics ecosystem— one that prioritises the timely delivery of life-saving pharmaceuticals while safeguarding the health of our planet.”
By investing in these technologies and adhering to evolving safety regulations, industry leaders are not only addressing today’s challenges but also shaping a safer, more sustainable future for logistics.
FEATURE - CATHAY CARGO
Cathay Cargo takes safety to new heights with its commitment to dangerous goods handling
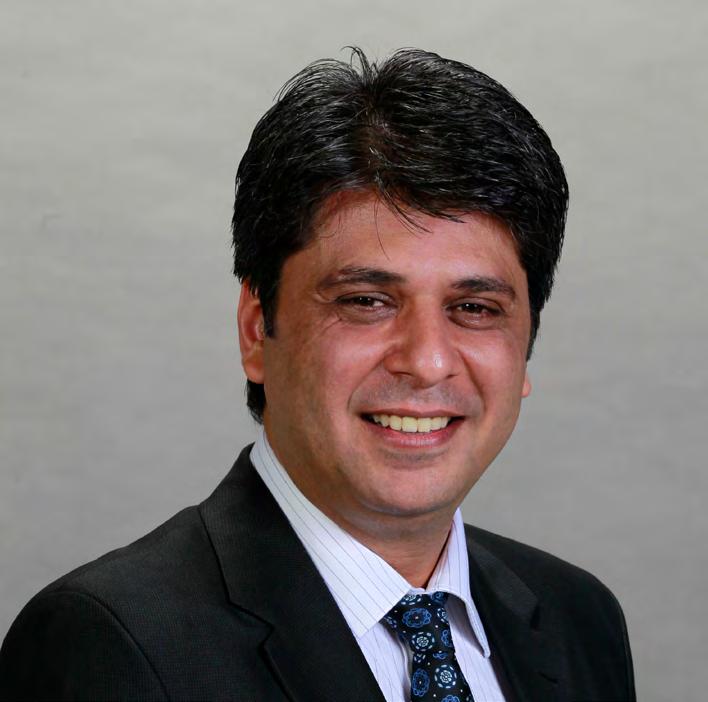
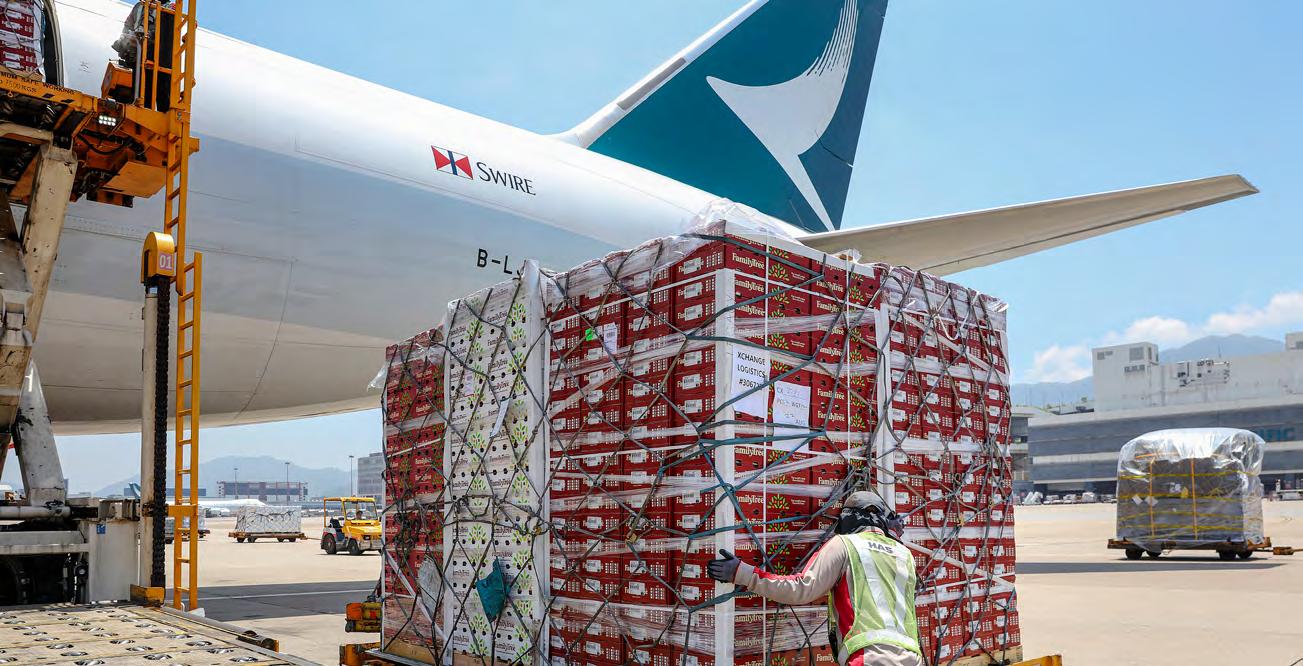
Payload Asia (PA): Given Cathay Cargo’s comprehensive risk assessment protocols, could you elaborate on how these processes have evolved to manage the complexities of shipping dangerous goods?
manages all the data, documents, and operations through digitisation. By doing so, we aim to optimise our end-to-end process and ensure efficiency and safety at all times.
Safety is paramount in the transportation of dangerous goods and pharmaceuticals. Every shipment carries not just valuable cargo but also the potential for catastrophic consequences if mishandled. The stakes are immense–from lithium batteries that can ignite without warning to temperature-sensitive pharmaceuticals critical to public health.
Recognising these challenges, industry leaders like Cathay Cargo have made safety excellence the cornerstone of their operations. By implementing rigorous risk assessment protocols, embracing continuous innovation, and prioritising comprehensive training programs, Cathay Cargo ensures that every shipment is handled with the utmost care—safeguarding both the cargo and the people who depend on it. In an exclusive interview, Ashish Kapur, Cathay Cargo’s Regional Head of Cargo, Southeast Asia, shares valuable insights into how the company upholds these high standards in the face of ever-evolving industry demands.
Ashish Kapur (AK): At Cathay, safety excellence is the cornerstone of our success. We are IOSA and CEIV Lithium Battery accredited. We implemented a Safety Management System (SMS) as a systematic, detailed, and proactive process for safety management. All cargo employees undergo comprehensive training and are certified to provide regulated handling at all stations, including collaborating closely with IATA, government regulators, cargo terminal operators and customers to ensure service and safety standards are above par.
With our unwavering focus on safety, we will continue to innovate and optimise our processes around the safe carriage of dangerous goods through the digitisation transformation journey. Notable initiatives include the implementation of electronic Dangerous Goods Declaration, NOTOC (Notification to Captain) and checklists.
PA: Cathay Cargo is at the forefront of employing innovative technologies for safety and efficiency. What are some recent technological advancements that have significantly enhanced your handling of dangerous goods?
AK: The Dangerous Goods Digitisation Project is currently in the BCD (Business Case Development) stage, which is a significant milestone in our commitment to enhancing our dangerous goods handling process. We aim to develop a common platform that seamlessly
PA: As Cathay Cargo prioritises rigorous training, what are some insights into these programmes that are continually updates and what skills are emphasised as regulations change?
AK: Our approach to DG handling involves a comprehensive review and refinement of our processes, incorporating firsthand experience and feedback from all levels of DG handling. This presents us with an opportunity to innovate our learning methods, ensuring that the latest information on DG handling is shared across all levels.
We recognise the importance of continuous learning and ensuring everyone receives the most up-todate information. To achieve this, we adopted the Competency-based training assessment (CBTA) module following the functions stated in IATA’s Dangerous Goods Training Guidance. Group discussions for real-world case studies and interactive exercises are conducted in our DG classroom training. We are also moving beyond traditional classroom learning and exploring new DG CBT training modules that engage our people through educational games and virtual reality learning. We believe this will stimulate their interest and enhance their learning experience.
PA: With Cathay Cargo’s integration of cutting-edge technology for shipment tracking, how has this technology particularly improved your management of dangerous goods?

ASHISH KAPUR
Regional Head of Cargo, Southeast Asia Cathay Cargo
AK: We take pride in our end-to-end shipment tracking capabilities. From the moment a shipment is accepted, we can track and have full visibility of the shipment until it reaches its destination. Our customers, too, receive the same level of insight.
Cathay Cargo’s multi-dimensional track-and-trace service, known as Ultra Track, gives customers near-real-time information on the airport-to-airport leg of the shipment journey using lowenergy Bluetooth data loggers. With this, we can monitor the shipment regularly and provide 24/7 proactive support and intervention on shipment irregularities. For example, we can check the shipment’s temperature status throughout the journey, ensuring the cargo’s integrity.
Cathay Cargo also implemented the Cargo IQ Master Operating Plan (MOP), which has been endorsed by IATA as a recommended industry practice. This includes various milestones that enable us to monitor the entire process of transporting air cargo from shipper to consignee.
PA: As Cathay Cargo navigates the complex landscape of international regulations, what are the most significant compliance challenges you face with dangerous goods, and what strategies have proven effective in addressing these?
AK: The carriage of mis-declared and un-declared dangerous goods poses significant threats to aviation safety. At Cathay Cargo, we take a proactive stance in cargo screening, having implemented the Cargo Agent Operation Program (CAOP) to assess cargo agent’s performance when handling DG shipments. Control measures have also been strengthened to prevent incidents involving dangerous goods.
PA: What are some insights into Cathay Cargo’s approach to incident management involving dangerous goods? What critical lessons have been learned from past incidents that have shaped your current practices?
AK: We have implemented a Safety Management System that manages safety as an integral part of our overall business. For every irregularity in a shipment, a comprehensive investigation will be conducted and proper reporting
FEATURE - CATHAY CARGO
to the authorities carried out. Rather than seeking to assign blame, our priority lies in understanding the root cause and why it occurred. This approach allows us to formulate corrective and preventive actions based on lessons learned, which is crucial in preventing similar incidents from recurring.
Furthermore, we promote a culture of knowledge-sharing across our network. Best practice are shared network-wide because safety insights benefit everyone, and we maintain an internal database dedicated to continuous improvement.
PA: How does Cathay Cargo ensure transparent communication with clients regarding the intricate requirements and restrictions of shipping dangerous goods?
AK: At Cathay Cargo, safety remains our top priority. We continuously review the latest industry and regulatory requirements to ensure we uphold the most stringent safety standards. Our commitment extends beyond compliance – we believe that open communication and regular knowledge-sharing sessions with our customers on the latest safety requirements and best industry practices will further enhance the overall safety of the industry.
PA: In what ways does Cathay Cargo collaborate with international aviation and safety authorities to influence and shape policies concerning dangerous goods?
AK: We actively participate in the IATA DG Board meeting regularly, engaging with different stakeholders from CTO, airlines, and relevant authorities. These meetings serve as a platform for in-depth discussions on the DGR amendments and DG handling processes. Additionally, we participate in regular meetings conducted in Hong Kong with members of the CLG (Carrier Liaison Group)DGWG (Dangerous Goods Working Group), where we exchange best practices and address safety-related issues to ensure the highest standards in DG transportation.
PA: What specific emergency scenarios has Cathay Cargo prepared for regarding dangerous goods, and how have these preparations influenced your broader operational strategies?
A.K.: The carriage of mis-declared and un-declared lithium batteries post significant safety threats to aviation safety. The agent needs to declare the battery models correctly so they can be identified and safely carried on our aircraft. We offer a complete suite of lithium battery carriage solutions to cater to the differing needs of our customers. This includes the fire containment bag (FCB), fire resistant container (FRC) and fire containment cover (FCC) to mitigate the fire risk. The FRC can take loads of up to 1,500kg and can passively contain a fire. It is also suitable, where permitted, for consolidation of loose or skid-size RBI cargo and general cargo in order to optimise flexibility and more efficient use of space.
PA: How does the handling of dangerous goods align with Cathay Cargo’s sustainability goals, especially regarding environmental impact reduction?
A.K.: Cathay’s commitment to sustainability leadership extends to our air cargo services, and is part of our commitment to tackling climate change by achieving net-zero carbon emissions by 2050. Fly Greener, our carbon-offset programme powered by an integrated carbon emissions calculator, was extended to air freight in 2022. Amongst other initiatives to reduce our environmental impact, our end-to-end digitisation project will help to significantly reduce paper waste.
Specific to dangerous goods, our handling process prioritises containment and spill prevention measures to protect the environment from potential releases or leaks.
P.A.: Are there any forthcoming changes or innovations within Cathay Cargo that aim to further enhance the safety and efficiency of dangerous goods transportation?
A.K.: The Dangerous Goods Digitisation Project has been launched with the goal of implementing the digitisation transformation of the Dangerous Goods end-to-end handling process. The initiative aims to establish a centralised platform for managing all data, digitised documents to improve data quality and traceability, and enhance operation efficiency.

FEATURE - JAPAN AIRLINES
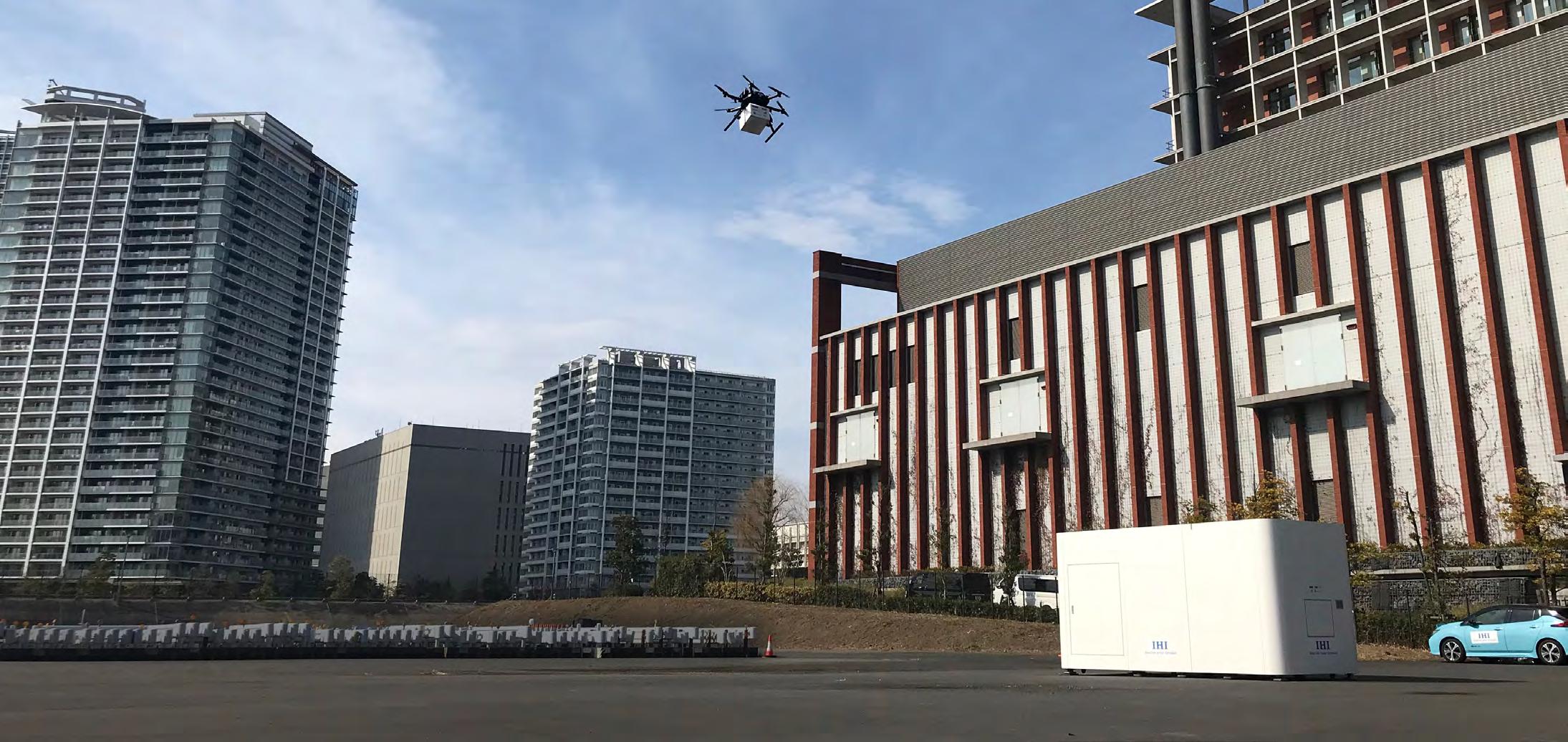
Japan Airlines’ vision for the future of pharmaceutical logistics
Japan Airlines (JAL) is taking a significant leap forward in the logistics and healthcare sectors by incorporating drone technology into its broader business strategy. This initiative is part of JAL’s Digital Transformation (DX) strategy, which focuses on integrating advanced technology with the airline’s expertise in safe operations. By collaborating with other companies and aligning with government policies, JAL aims to revolutionise air mobility through drones and electric Vertical Take-Off and Landing (eVTOL) vehicles.
At the core of this transformation is the Air Mobility Operation Platform (AMOP), a social infrastructure designed to manage
the safe operation of next-generation air mobility services. AMOP offers more than just operational management systems providing consulting, communication support, insurance, aircraft provision, and pilot training services. While the platform’s applications are vast, JAL sees particular potential in using drones to deliver lightweight, high-value, and timesensitive medical supplies.
“Combining our expertise in safe operations with advanced technology, we are collaborating with other companies to promote the next-generation air mobility business,” explains Eriko Yano, Manager, Drone Business Group, Air Mobility Business Creation Department,
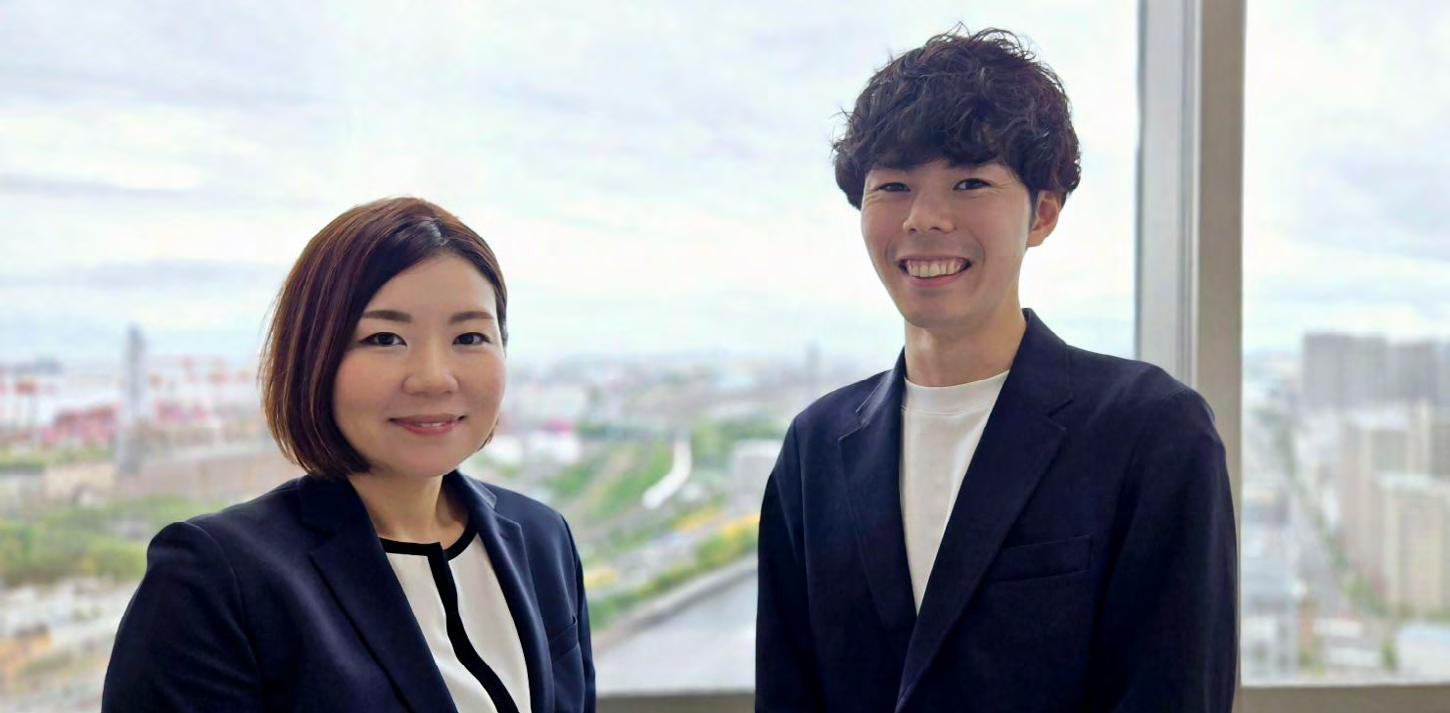
Innovation Division, at Japan Airlines. The airline envisions a future where drones and eVTOLs are a common feature of healthcare logistics, transforming how medical supplies are delivered.
Pioneering drone-based pharmaceutical delivery
One of JAL’s most promising ventures is its drone-based pharmaceutical delivery system, which aims to streamline the transportation of essential medications. In a demonstration in Tokyo, JAL partnered with consortium companies to deliver lowfrequency, high-value pharmaceutical products from warehouses to hospitals. This initiative aims to reduce wastage caused by expired pharmaceuticals, while also addressing the unique logistical challenges faced by hospitals in densely populated areas like Tokyo.
JAL has also expanded its efforts to more remote locations. On Amami Oshima Island, in collaboration with the Setouchi Town Office, JAL established “Amami Island Drone Co., Ltd.” to deliver pharmaceuticals to residents of remote islands. These efforts demonstrate how drone technology can bridge logistical gaps, ensuring that vital medical supplies reach even the most isolated communities.
Enhancing healthcare logistics with drone ports
A key takeaway from JAL’s recent demonstration in Koto-ku, Tokyo, was

(L-R) ERIKO YANO, Manager and KANTA ITO, Supervisor
Drone Business Group, Air Mobility Business Creation Department, Innovation Division, Japan Airlines Co.,Ltd.
the potential of drone ports in hospital settings. These ports could allow hospitals to receive pharmaceutical deliveries at their convenience, reducing reliance on traditional logistics systems. As the airline continues to explore the capabilities of drone technology, it also recognises the importance of addressing the shortage of manpower in the pharmaceutical industry.
In terms of operational efficiency, JAL is focusing on safety and reliability. The airline sees drone ports as an essential component in achieving this, allowing for automated takeoff and landing procedures that minimise human involvement while ensuring temperature control and delivery management. Hospital personnel involved in the demonstration expressed enthusiasm for the potential of drone ports, particularly in emergencies when road closures or disasters isolate healthcare facilities.
Overcoming challenges and advancing technology
JAL has faced challenges in its pursuit of drone-based logistics, particularly regarding Level 4 flights—drones flying beyond visual line of sight (BVLOS) in populated areas. Currently, only one drone model, the PF2-CAT3 by ACSL, is certified for these flights. To overcome this limitation, JAL works with partners to diversify drone options and expand operations into urban areas. “We need drones with advanced control capabilities and high-precision landing, especially for operations in limited spaces like urban areas,” Eriko noted.
In addition to enhancing drone technology, JAL is also developing a flight management system that allows a single operator to control multiple drones. This would significantly reduce operational costs and improve efficiency, paving the way for widespread drone adoption.
Building strategic partnerships
Collaboration is key to JAL’s success in the drone industry. The airline has partnered with several organisations, including KDDI Corporation, East Japan Railway Company, and local hospitals, to bring its vision to life. Each partner plays a unique role: KDDI provides essential LTE communication, East Japan Railway Company offers implementation support, and local hospitals serve as demonstration sites, providing
FEATURE - JAPAN AIRLINES

valuable feedback on the practicality of drone deliveries.
These partnerships are vital not only for the technical success of the project but also for gaining public acceptance of drones in everyday life. JAL has been proactively educating the public and healthcare professionals about the benefits and safety of drone technology through workshops and demonstrations. The airline is also working on initiatives to help hospital staff acquire the necessary skills to handle drone operations.
Navigating regulations and ensuring safety
Navigating Japan’s regulatory landscape for drone operations has been a complex process for JAL. The airline is working closely with Prodrone Co., Ltd. to meet the stringent requirements for Type 1 Certification, which allows for Level 4 flights in densely populated areas. In addition, JAL has introduced training programs based on Crew Resource Management (CRM), a concept used in aviation to improve safety and coordination among pilots.
JAL is also taking steps to ensure the sustainability of drone operations. One of its long-term goals is to reduce manpower and increase aircraft utilisation by allowing a single pilot to control multiple drones. Supported by the New Energy and Industrial Technology Development Organization (NEDO), JAL is conducting technological verification to achieve this.
The future of drone-based healthcare logistics
JAL’s drone initiatives can potentially transform healthcare logistics in Tokyo and beyond. Drones could be crucial in maintaining healthcare systems in depopulated areas, ensuring patients receive necessary medications and blood supplies even in remote regions. During

emergencies, drones could provide uninterrupted delivery services, ensuring the continuous flow of critical supplies.
“We believe that drones can contribute significantly to maintaining medical systems in areas where healthcare infrastructure is difficult to maintain,” Eriko states. The airline also sees potential for expanding drone deliveries to sectors beyond pharmaceuticals, such as food supplies and newspapers, as demonstrated by its operations on Amami Oshima Island.
Ultimately, JAL’s vision is to create a sustainable, efficient, and reliable drone logistics service that benefits healthcare providers and patients. By reducing medication waste, improving delivery times, and enhancing operational safety, drones have the potential to revolutionise the healthcare industry—not just in Tokyo, but across the globe.
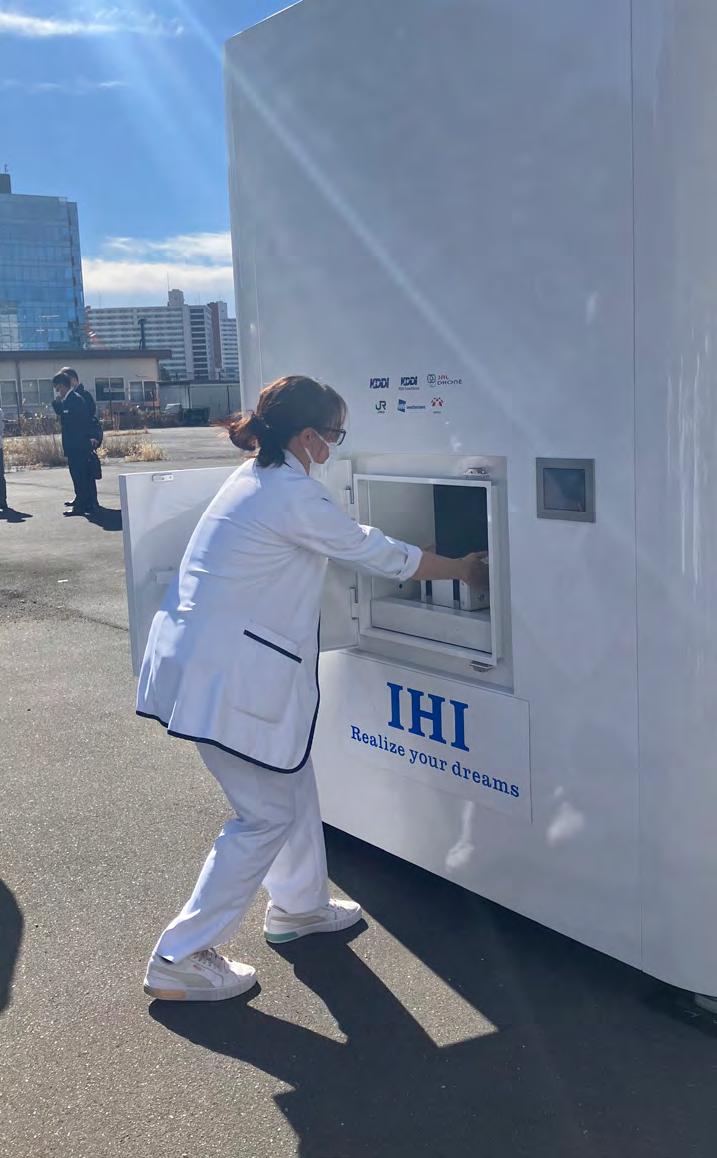
Temperature integrity in pharmaceutical transportation through automation
BY STEVE HEALY
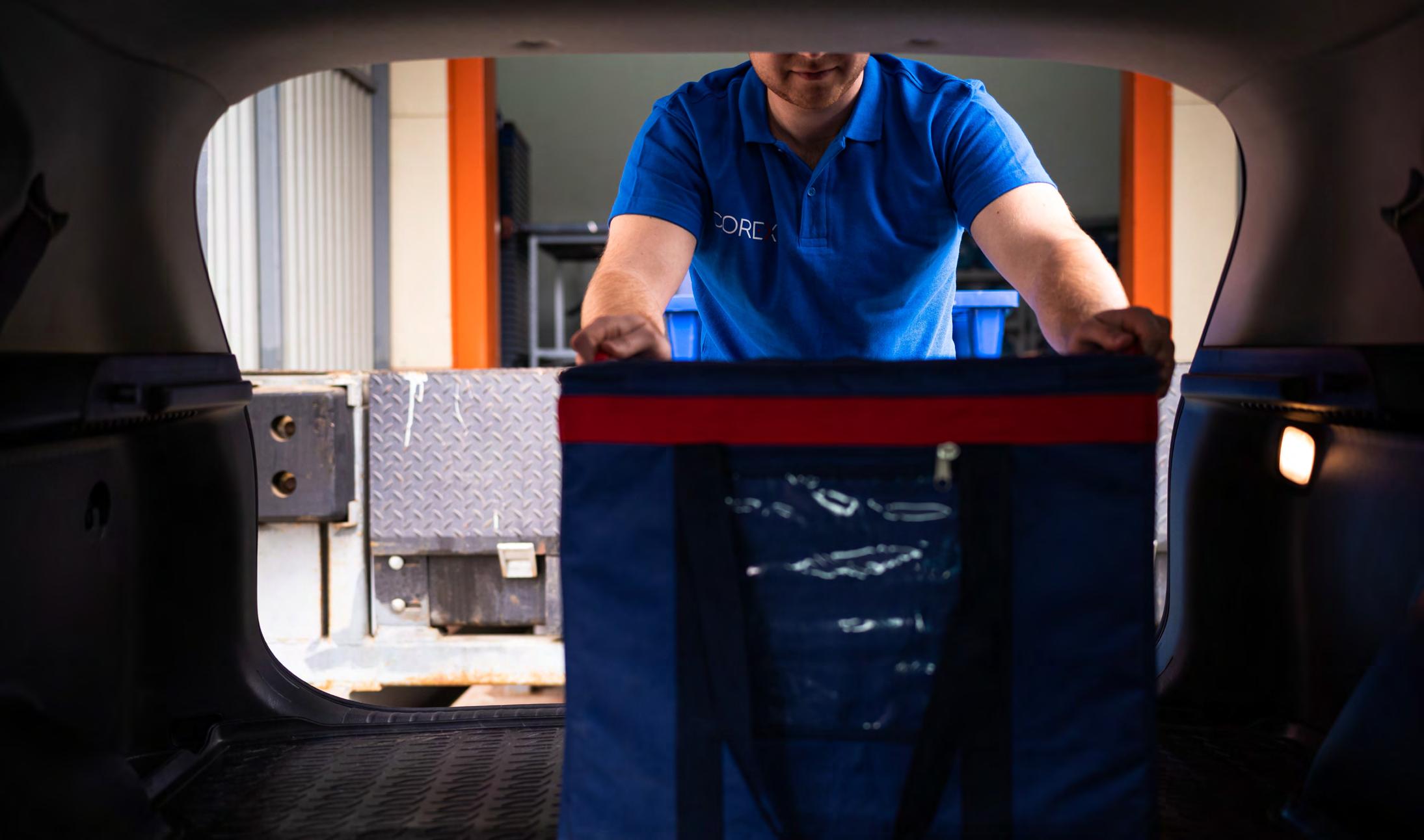
Automation is increasingly being utilised across all sectors, and pharmaceutical logistics is no exception, where it plays a pivotal part in ensuring temperature integrity for pharma shipments being transported worldwide.
Technological innovations are enabling new opportunities for supply chain visibility and reactivity, helping to protect the cold chain and ensuring temperaturesensitive, high-value pharmaceutical payloads reach their destinations in the correct condition.
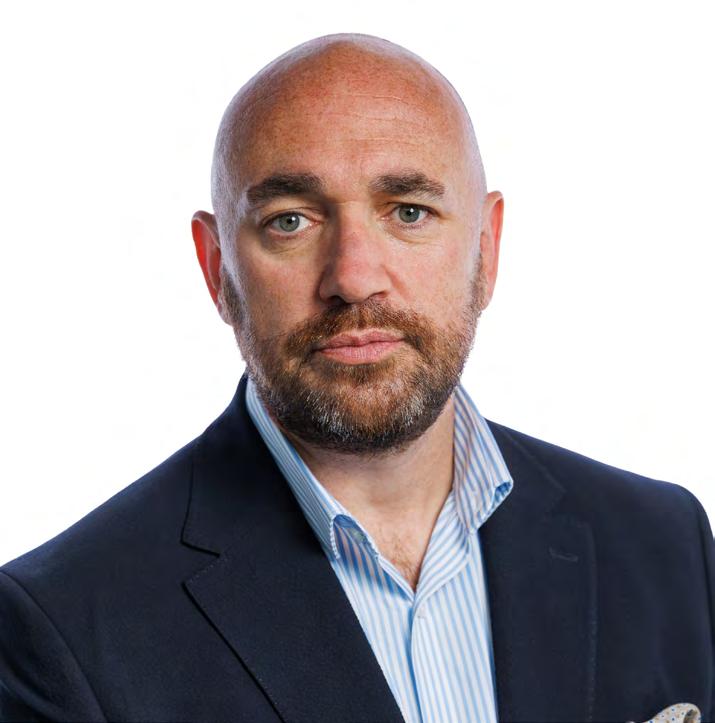
These innovations offer an exciting opportunity for logistics companies and their clinical research clients. The ability to react more effectively to temperature deviations, mitigate risks to better protect payloads, as well as use analytics to more effectively plan routes for shipments, means better service for the client and operational ease for the company and critically ensures the safe delivery of lifegiving, lifesaving pharmaceuticals for patients.
Defining the cold chain
Refrigerating shipments with ice has been common for centuries, but far more effective methods developed throughout the 20th century with the advent of more mobile and effective refrigeration technology. While originally primarily used for food, innovations in medicine have increasingly required more stringent refrigeration. Demand for cold chain systems has significantly grown, with a further spike following the COVID-19 pandemic due to the associated vaccinations requiring cold chains to travel to their destinations around the world.
Modern pharmaceutical cold chains are defined by precise temperature management at all stages of the logistics
process. Some medicines are incredibly sensitive to even the smallest variations in temperature or other environmental factors, so it is imperative that specific conditions are maintained throughout a payload’s journey. This ‘unbroken’ cold chain is the ideal form of cold chain logistics, with new technologies facilitating the possibility of this uninterrupted cold chain and the possibility of verifying that cold chain while the payload is in transit.
New technologies
Innovations in supply chain technology have broadly focussed on expanding the ‘visibility’ of the supply chain. Increasing visibility means making more information available to stakeholders throughout a product’s journey from point A to point B, such as location data, live inventory information and other status updates. This real-time monitoring provides the opportunity to see what is happening to a pharmaceutical shipment before it arrives at its end destination and allows those operating within the supply chain to react accordingly to any issues.
This can help limit disruption and allow for more responsive planning and risk mitigation management. This practice is especially helpful when data is shared between different involved

STEVE HEALY CEO, COREX Logistics
parties, including the logistics company transporting the payload, any ports along the journey, and the sender and the receiver, creating the possibility for more proactive and agile responses to new information.
For cold chain payloads, there are additional concerns that require more detailed information. Innovations such as real-time temperature tracking allow for more stringent and specific temperature management practices to be enacted in real-time. Any deviations can be spotted early and appropriately dealt with much faster than they would otherwise. This monitoring also creates data that can be used to derive insights about risk factors that cause temperatures to rise out of acceptable levels, enabling more detailed planning to mitigate these risks in the future, and in turn more effective reactive measures.
Even situations where the payload is damaged or going to arrive late can be dealt with more effectively. An irreparable temperature excursion that requires reshipping of the product can be immediately reacted to, minimising the delay to the receiving party and minimising any potential impact on patients.
Automation and connected software systems
These insights are enabled by connected software systems, allowing all stakeholders to stay informed about the status of a shipment. The more information available to the various stakeholders, the better. This allows all parties to stay abreast of important developments and react accordingly. However, software can also enable technologies to work together directly without the need for stakeholder intervention.
Advances in automation and Internet of Things (IoT) technologies mean that software and hardware can be calibrated to automatically mitigate risks, with IoT-enabled hardware reading the temperatures of payloads and adjusting environmental temperature controls to keep them in range.
Issues with equipment can also be identified earlier. For example, a temperature-controlled shipper may be experiencing larger temperature fluctuations than others, so a maintenance team can perform checks
FEATURE - COREX LOGISTICS
on it to resolve any issues, mitigating risks before they even arise. This maintenance may be urgent, so stakeholders can ensure a maintenance team is available on an existing route or divert the package if necessary.
The ground team at an airport can be made aware a pharma payload cannot be left on the tarmac for too long as it may deviate in temperature and take measures to ensure it is properly stored quickly and effectively. Even if a package is handled improperly, another stop along the route can be made aware of and increase temperature control methods to bring a product back into range quickly, minimising damage. These kinds of interconnected actions are enabled by automation and connected software systems.
Other applications include security updates, with reports on if or when a package is opened; and reports on other environmental factors, such as humidity. The more risk factors that are measured and controlled for, the more they can be mitigated, and the more medicine can reach its destination in good condition ready to be supplied to patients. Warehouses, ports and other touchpoints in a supply chain should be encouraged to add their own data points and monitoring technologies, adding more information to the process and procedures allowing for even more informed decision-making.
Post-journey optimisations and lane mapping
Post analysis also enables logistics businesses to use their analytics for ‘lane mapping’, which is the practice of creating simulations of temperature behaviour across potential shipping lanes

for an outbound pharma payload from its country of origin to its destination region. There may be direct or indirect options, but the key considerations will be the levels of temperature control capabilities that are available within the selected lane and route, the supply chain’s design, and completing a route analysis. Considerations must also be made regarding the suppliers, airline, courier and all other parties involved, ensuring they have the necessary expertise to handle cold chain payloads and can be relied upon to do so. Even their ability to react to issues should be measured as part of qualifying a stakeholder.
Automation provides an opportunity to inform these decisions and, should a less reliable route need to be utilised, a more comprehensive mitigation strategy can be prepared in advance.
It is important that customers involved in the supply chain have access to all the relevant information that is available
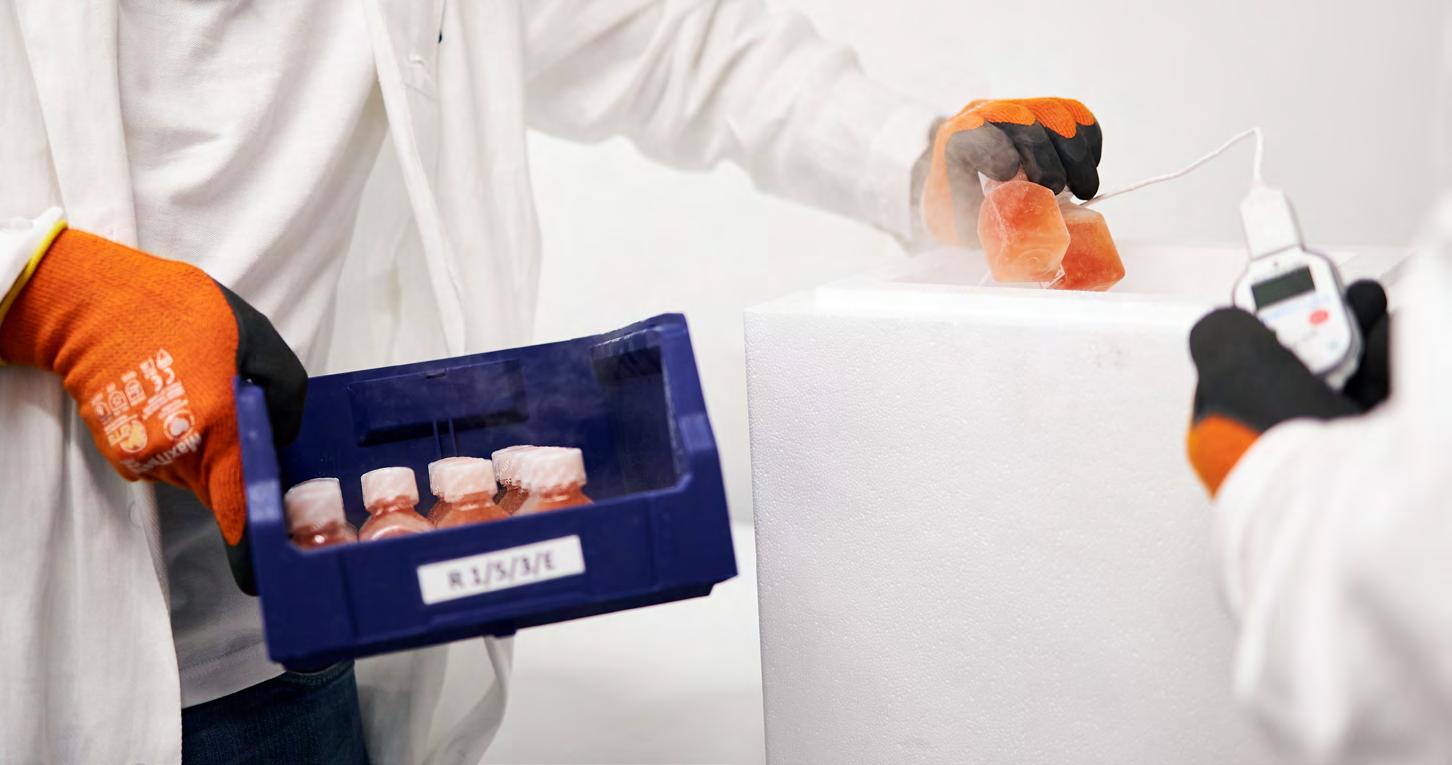

FEATURE - COREX LOGISTICS

during the shipping process. Various organisations operating within the pharma logistics sector can provide that visibility via various automated options. For example, clients can stay up to date on the transportation progress of their pharma payloads via COREX’s customer portal, which also provides information on any issues and risk factors.
This enables everyone within the supply chain to have constructive conversations
about how to react and be more informed when planning future shipping lanes. These platforms are often interoperable allowing seamless integration with all loggers, providing more information to be used in operational reviews with customers and collaborators within the pharma logistics space and to make suggestions on factors, such as packaging and level of service, helping to mitigate future issues.
Having data is all well and good, however, it is important to have experts on hand who can extract meaning from that data and analyse it effectively. Logistics companies should encourage proactive engagement with their pharmaceutical customers to offer solutions and suggestions to make their supply chains more efficient and to ensure integrity is maintained.
The future
The future for pharmaceutical logistics promises ever-increasing amounts of data to work with. IoT technologies produce huge amounts of data, and this is where artificial intelligence (AI) comes in. The large amount of data produced can be overwhelming to people managing supply chains, who may struggle to extract the necessary insights due to the sheer volume of data at their disposal.
AI can be implemented to more effectively

manage and interpret this data. AI can use data from previous trips and combine it with weather predictions and other data points to make recommendations for supply chain planning. This allows logistics companies to suggest more efficient methods to their clients in terms of cost, sustainability and maintaining temperature integrity. Use of AI in this context is still new, and humans should remain the ultimate decision makers on any supply chain planning decisions.
Another much-touted technology is blockchain. Blockchain is a decentralised ledger that can record transactions and can trigger them automatically. These transactions are encrypted in such a way that they are effectively un-hackable, meaning that no malign actors can alter the record for personal gain. While this is an enticing prospect, implementing blockchain technologies is very energyintensive. While certain schemes have been piloted, the sector is a long way from wide adoption, and the technology has more broadly fallen out of favour outside of cryptocurrency applications.
Many logistics and pharmaceutical businesses are increasingly concerned with sustainability, whether that be due to consumer preference, investor pressure or regulation. Existing technologies are contributing to increased sustainability, such as IoT technology increasing efficiency and therefore reducing emissions. Other concepts like the circular supply chain, meaning that containers and other materials should be reusable and used to send multiple payloads over time, should also be made easier to implement by IoT technologies. Sustainable containers that have the required temperature integrity are still in their infancy, but this is a promising avenue for sustainable development.
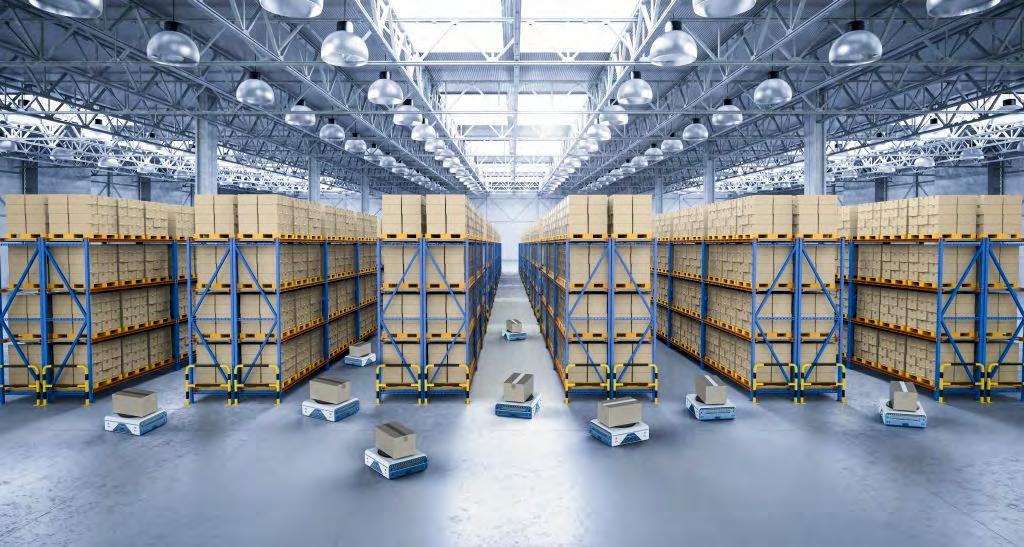
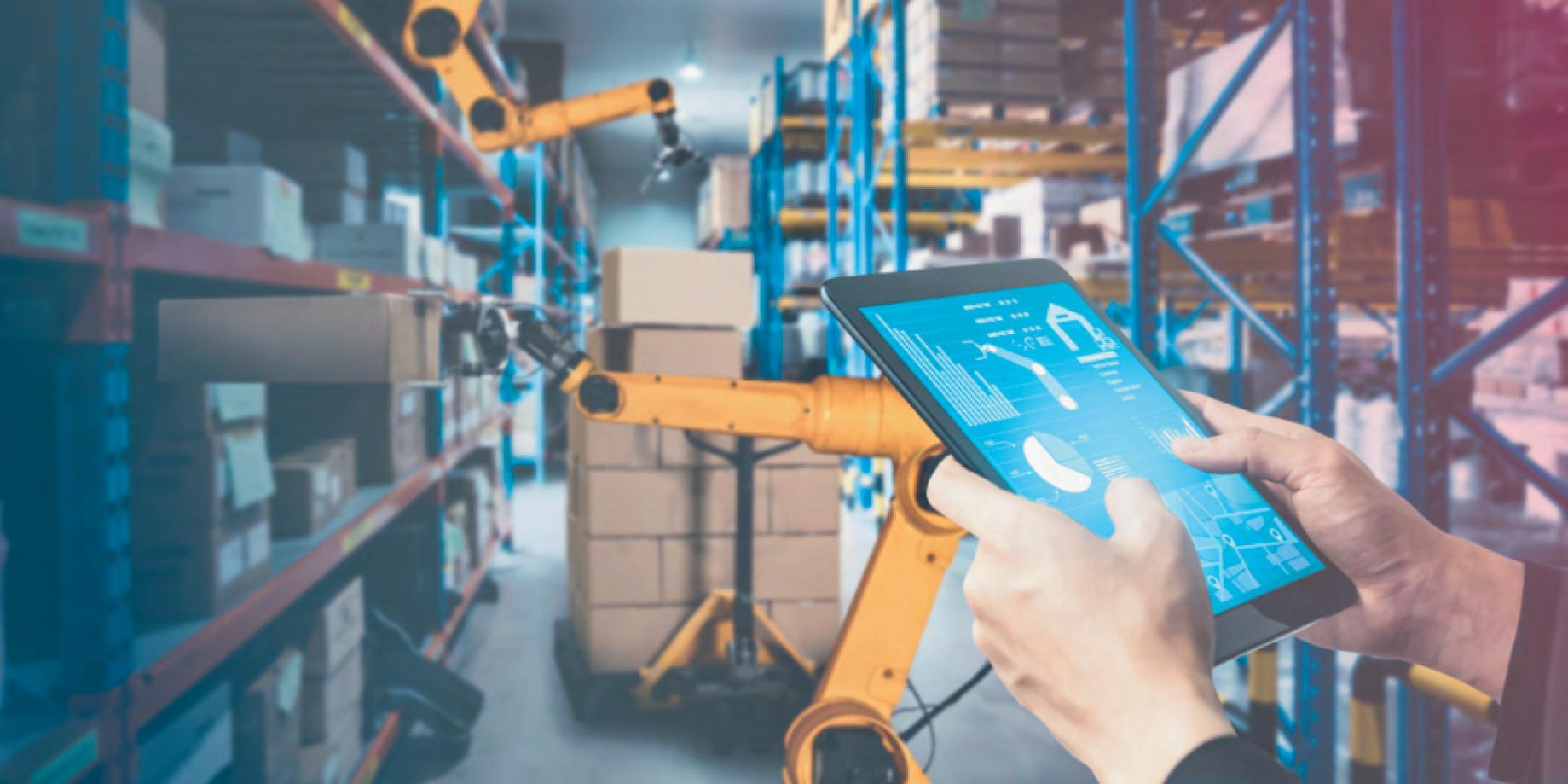
However, innovations like AI require a lot of energy to work, so certain advances could be offset by the implementation of energy-intensive technologies. There is a balance to be found between increased efficiency, sustainable supply chain concerns and cost-effectiveness.
Cold chain logistics and concerns about temperature integrity are a growing segment of the pharma logistics market. Some of the most exciting medical innovations of recent times require a cold chain to travel, which will only encourage more innovations in the sector.



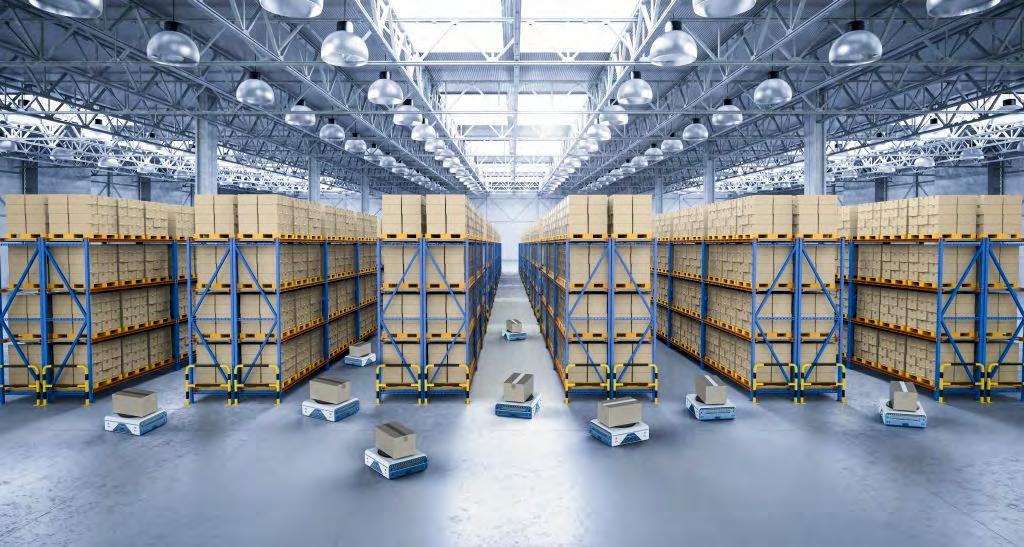
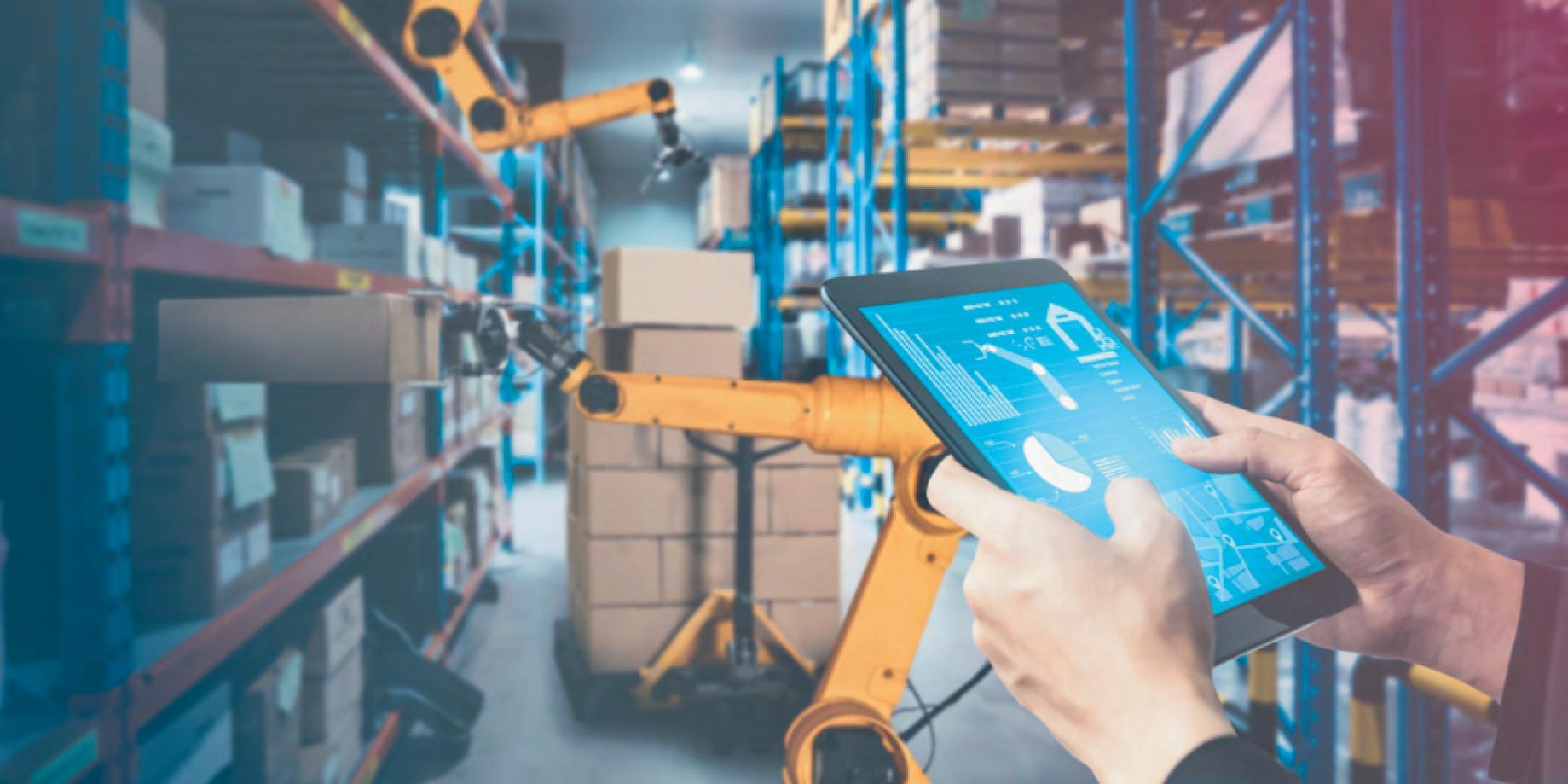
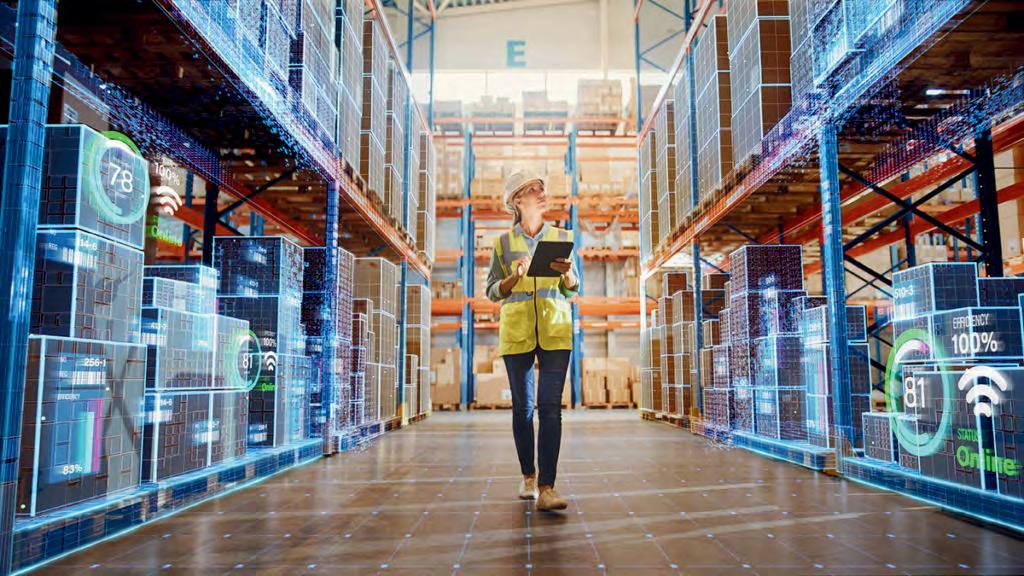

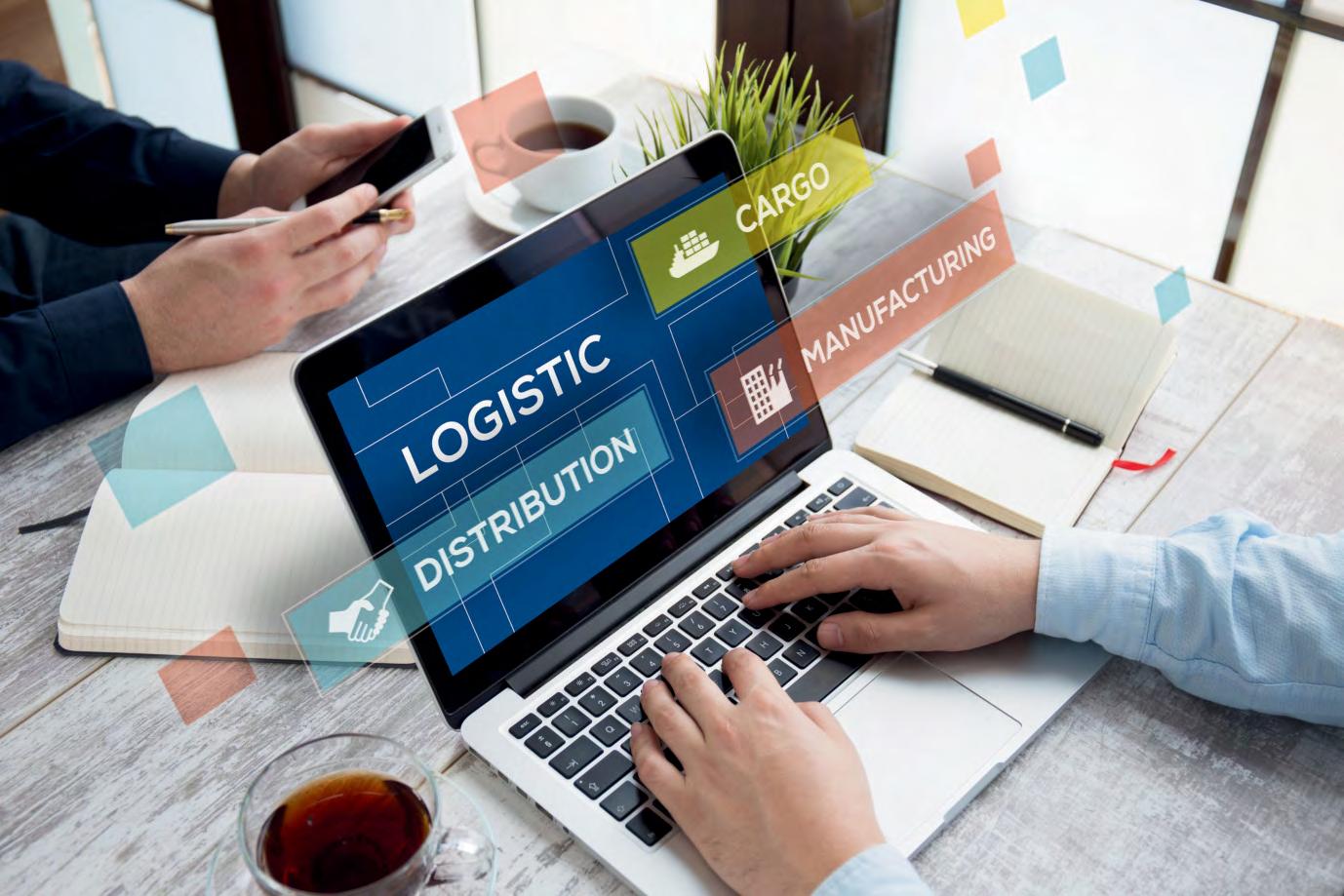

Harnessing collaboration and digitalisation to hone and grow the world’s busiest cargo airport
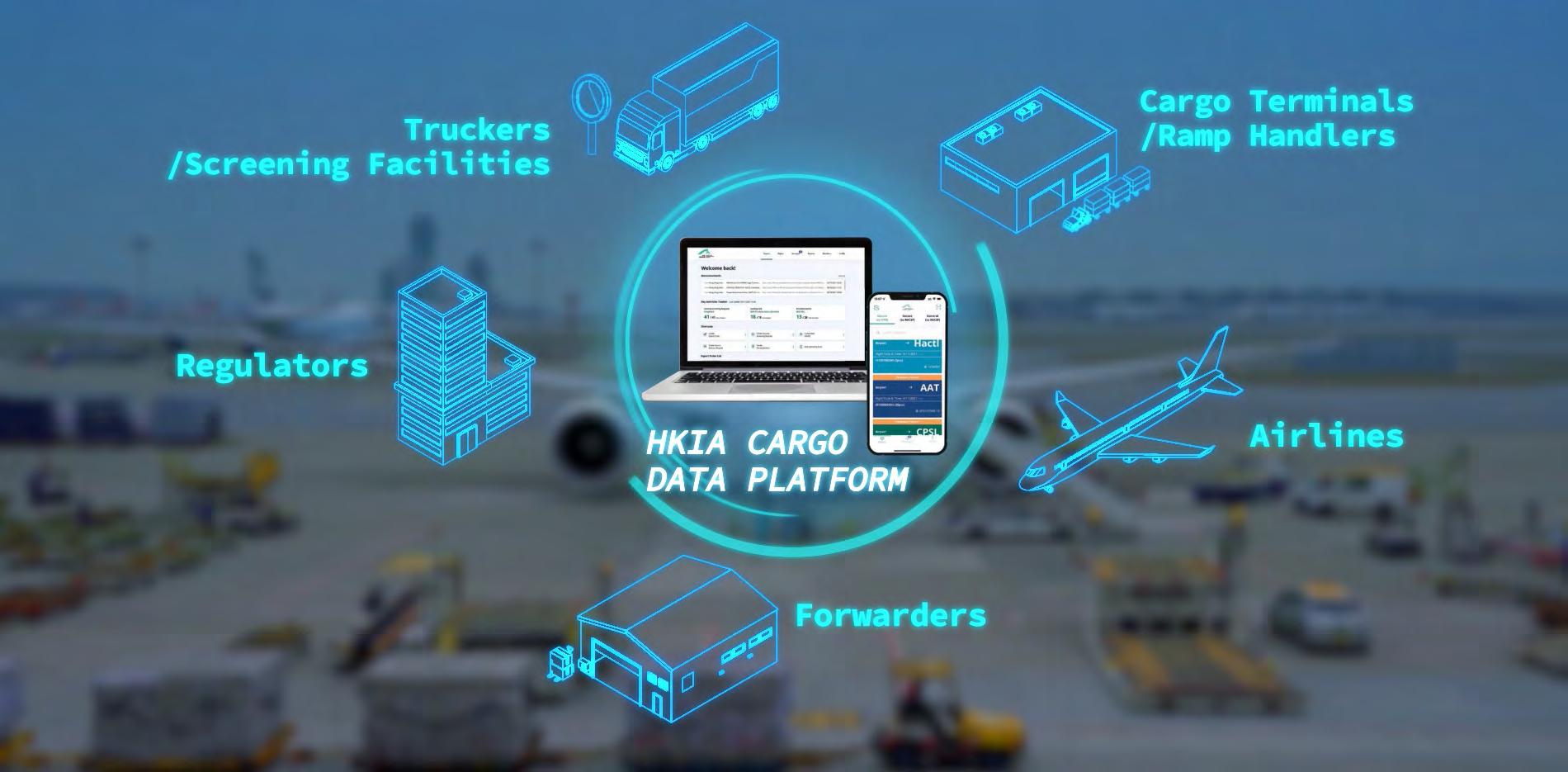
Hong Kong International Airport (HKIA) has been named once again the World’s Busiest Cargo Airport in 2023 with a throughput of 4.3 million tonnes. With state-of-the-art cargo facilities, an extensive air network and excellent operations efficiency, it is the 13th time since 2010 that the airport has received the title. Apart from the airport’s excellent capabilities to handle e-commerce and temperature-controlled shipment, continual investments in cutting-edge technologies and partnerships with major stakeholders demonstrate the airport’s commitment to leading the way in efficient global cargo operations. As a smart airport, HKIA is dedicated to staying ahead of the digitalisation trend in air cargo. In a recent interview with Irene Lau, General Manager, Aviation Logistics (Hong Kong), Airport Authority Hong Kong (AAHK), the airport representative detailed their strategy to reinforce their position at the forefront of the world’s busiest cargo hub.
Hong Kong’s digital leap with the HKIA Cargo Data Platform
The digital transformation era is ushering in significant changes across various
sectors, and the air cargo industry is no exception. In a strategic move to strengthen its leadership and thrive to the rapidly evolving e-commerce landscape, AAHK has taken the lead in developing the HKIA Cargo Data Platform, a community-based digital platform to connect key supply chain stakeholders and enhance the efficiency and transparency of the air cargo and logistics industry in Hong Kong.
Developed from the ground up by AAHK, the HKIA Cargo Data Platform is a testament to the power of innovation in overcoming industry challenges. The
Platform ensures a synchronised network by integrating technologies including blockchain, smart contracts, and mobility solutions and complying with the IATA One Record standards.
Irene reveals, “Leveraging such a synchronised and trusted network connecting our key air cargo stakeholders, including cargo terminal operators, freight forwarders, truckers, warehouse operators, regulators, and airlines, operation processes are streamlined and more efficient with seamless communication and better cargo journey visibility. Better user experience is enabled.”
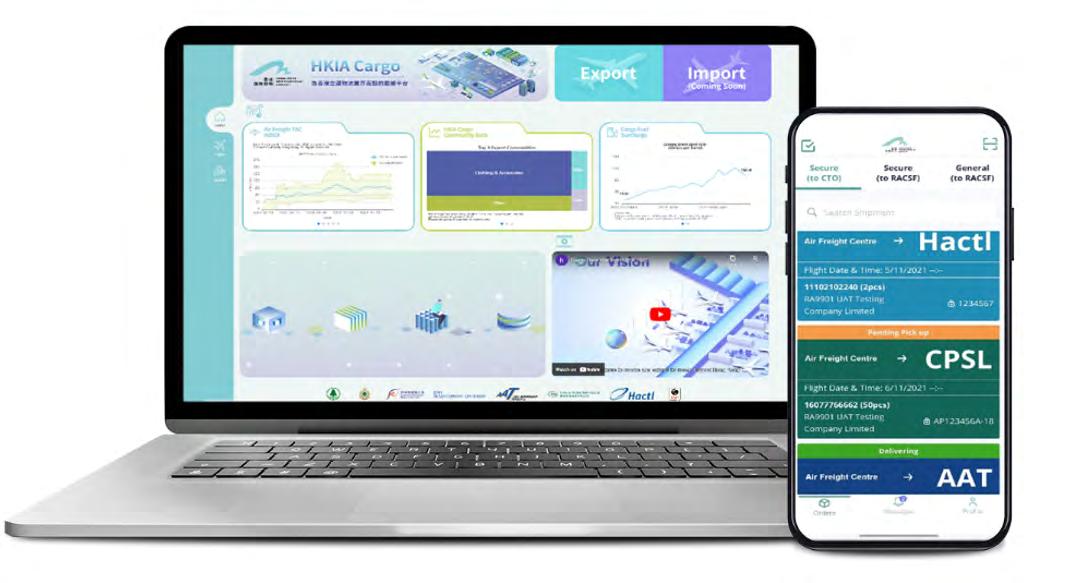
The HKIA Cargo Data Platform is an open and neutral community-based digital platform to connect air cargo stakeholders to enable global supply chain digitalisation and innovation as well as global trade facilitation.

Hong Kong International Airport, the world’s busiest cargo airport, has taken the lead in driving air cargo digitalisation for the Hong Kong air cargo industry.
SPECIAL FEATURE - HKIA

Pioneering digital solutions for efficient import cargo handling
The recent pilot launch of the Hong Kong Air Import Cargo Collection End-to-End Process Digitalisation Application, the latest application of HKIA Cargo Data Platform, is another industry breakthrough that brings the Hong Kong air cargo industry to a new frontier. Besides the supply chain stakeholders, it also connects with three Hong Kong Government regulators, namely the Agriculture, Fisheries and Conservation Department (AFCD), Customs and Excise Department (C&ED) and the Food and Environmental Hygiene Department (FEHD).
Through a single login, Hong Kong freight forwarders can access a wealth of import cargo information, such as flight arrival status, cargo collection order readiness, and activity milestones. Authorised personnel can retrieve their electronic Shipment Release Form (eSRF) off-site upon e-payment settlement and authentication. Cargo collection order assignment and advanced truck registration at the cargo terminal can be done online. The Application is also equipped with the regulator portal with ‘e-stamp’ and ‘e-queue’ functions to facilitate the cargo inspection process before shipment release. Truckers benefit from reduced physical dwell time at terminals, and cargo terminals can better deploy resources, leading to improved overall operational efficiency.
The groundbreaking application not only enables the issuance of eSRF, but import documents can also be shared with related stakeholders via Global Logistics System (HK) Co. Ltd.’s ePouch,
the world’s first digital pouch supporting IATA’s ONE Record standards. This digital feature allows the paperless, touchless, and seamless electronic transfer of cargo documents from global supply chain players to local entities, truly connecting the Hong Kong air cargo community ecosystem to the world.
The power of data in modern logistics
Apart from efficiency gain, the HKIA Cargo Data Platform facilitates realtime data sharing among supply chain stakeholders and enables them to access comprehensive dashboards and reports. This wealth of data, as newly accessible through the Platform supports robust, fact-based decision-making and strategic business planning.
“Data will be further aggregated into industry statistics to be shared with the community users as benchmarks. Through applications of data analytics functions, predictive insights and forecasting trends can be derived, which can further benefit the community in their resource planning and process optimisation,” Irene elaborates.
“Ultimately, a more resilient and sustainable cargo supply chain can be formulated, and the world’s leading smart aviation hub of Hong Kong can be reinforced.”
Engaging stakeholders in technological advancements
AAHK’s approach to digital transformation highlights the importance of community involvement. From the onset, the authority engaged with industry stakeholders to gather insights into their specific challenges and needs.
“Driving digitalisation requires a concerted effort from the entire supply chain stakeholders. Securing community support and change management are key success factors. This project started with an early engagement of the community in seeking their views and inputs on their industry challenges and pain points,” Irene explains.
“In particular, we appreciate the collaborative support of our business partners, like Cathay Cargo Terminal as our pioneer cargo terminal to work with us on the newly launched Hong Kong Air Import Cargo Collection End-toEnd Process Digitalization Application, making it a smooth implementation and successful adoption on this new technologies and streamlined operations”
Despite the challenges and complexities involved, the HKIA Cargo Data Platform has been met with positive feedback from the community, signalling a successful initial rollout. Looking ahead, AAHK aims to expand its digital connectivity beyond local boundaries to international markets.
“Way forward is to extend our digital connectivity beyond Hong Kong.”
“We are also cultivating collaboration with overseas partners, including aviation hubs, e-commerce platforms, and global trade-related stakeholders, to synergise more business values and facilitate global trade opportunities,” Irene shares.
Irene further highlights, “It is our objective to transform the platform into a global digital trade ecosystem network to facilitate not only physical air cargo flow but also information flow and capital flow to generate more innovative business solutions and new business opportunities to the industry and Hong Kong.”
As global supply chains recalibrate from traditional geographies, the Hong Kong air cargo community is not merely responding but strategically advancing. Through ongoing innovations in digital front and service offerings, HKIA stands ready to better serve worldwide air cargo customers and remain at the forefront of the global logistics and air cargo industry.

The Hong Kong Air Import Cargo Collection End-to-End Process Digitalization Application enables authorised personnel to enjoy a seamless user experience by retrieving their eSRF offsite upon e-payment settlement and authentication.
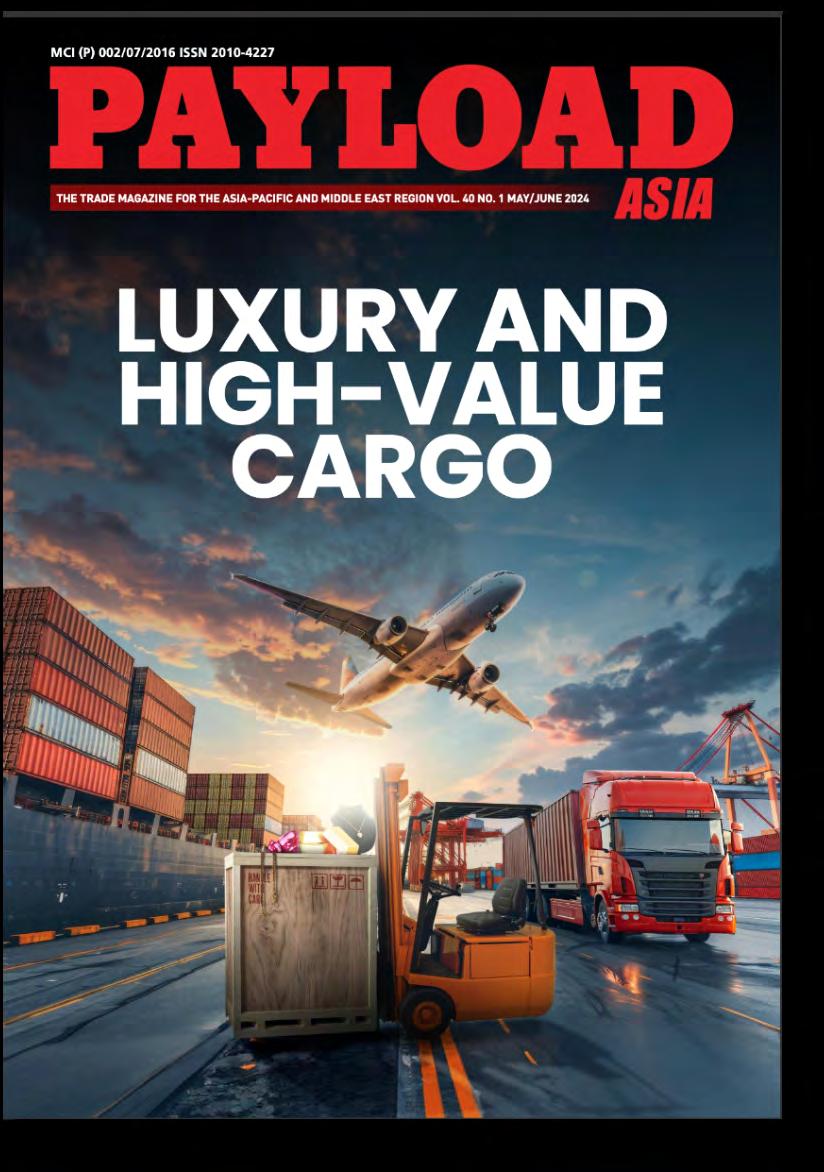
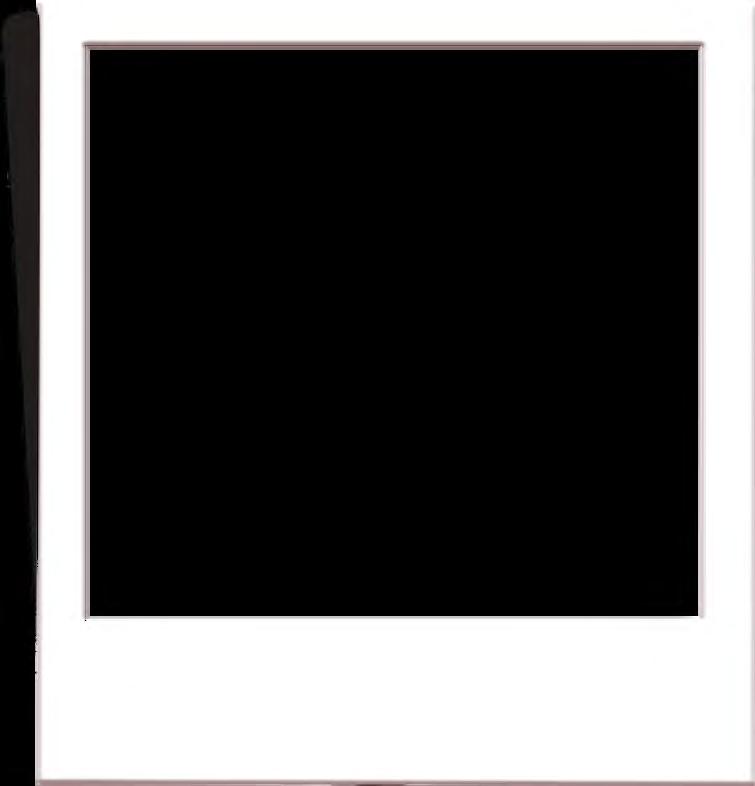
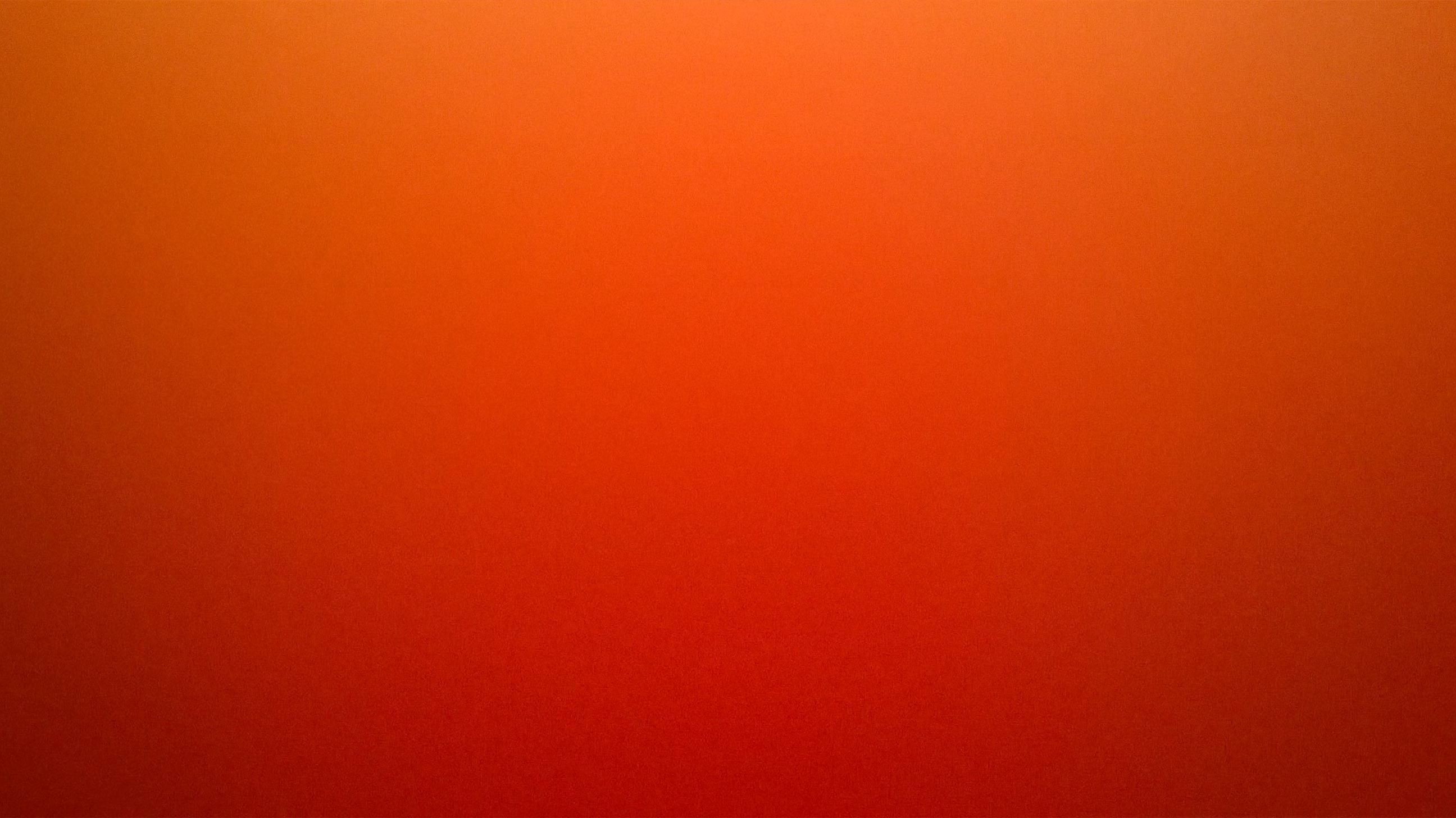
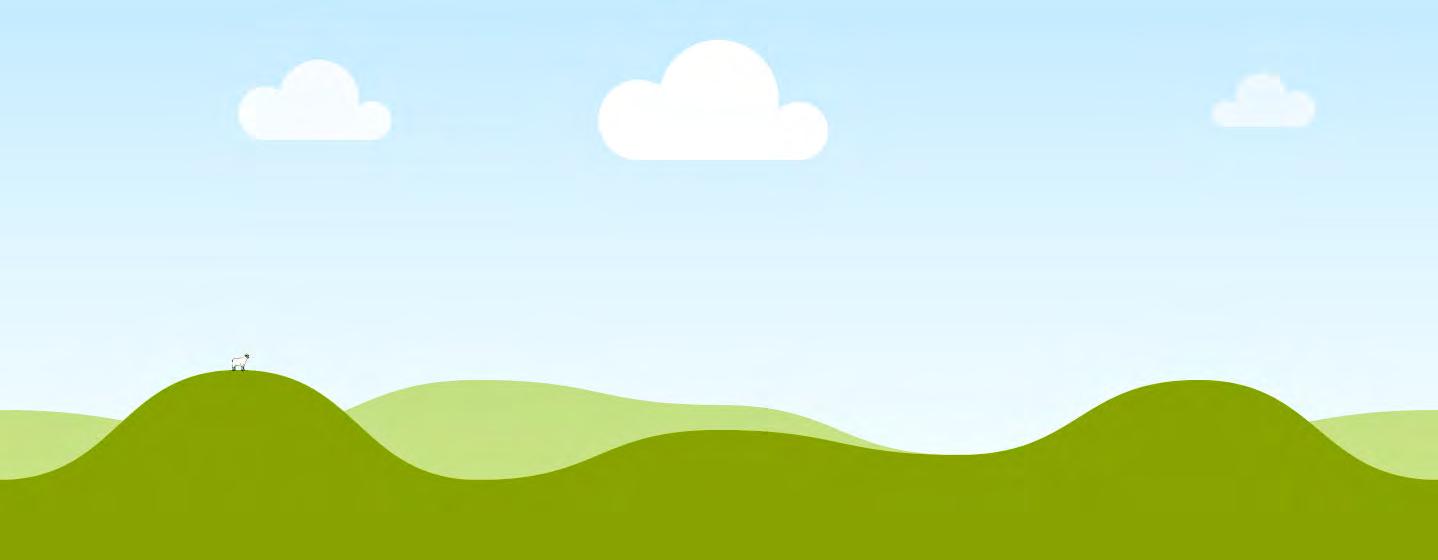