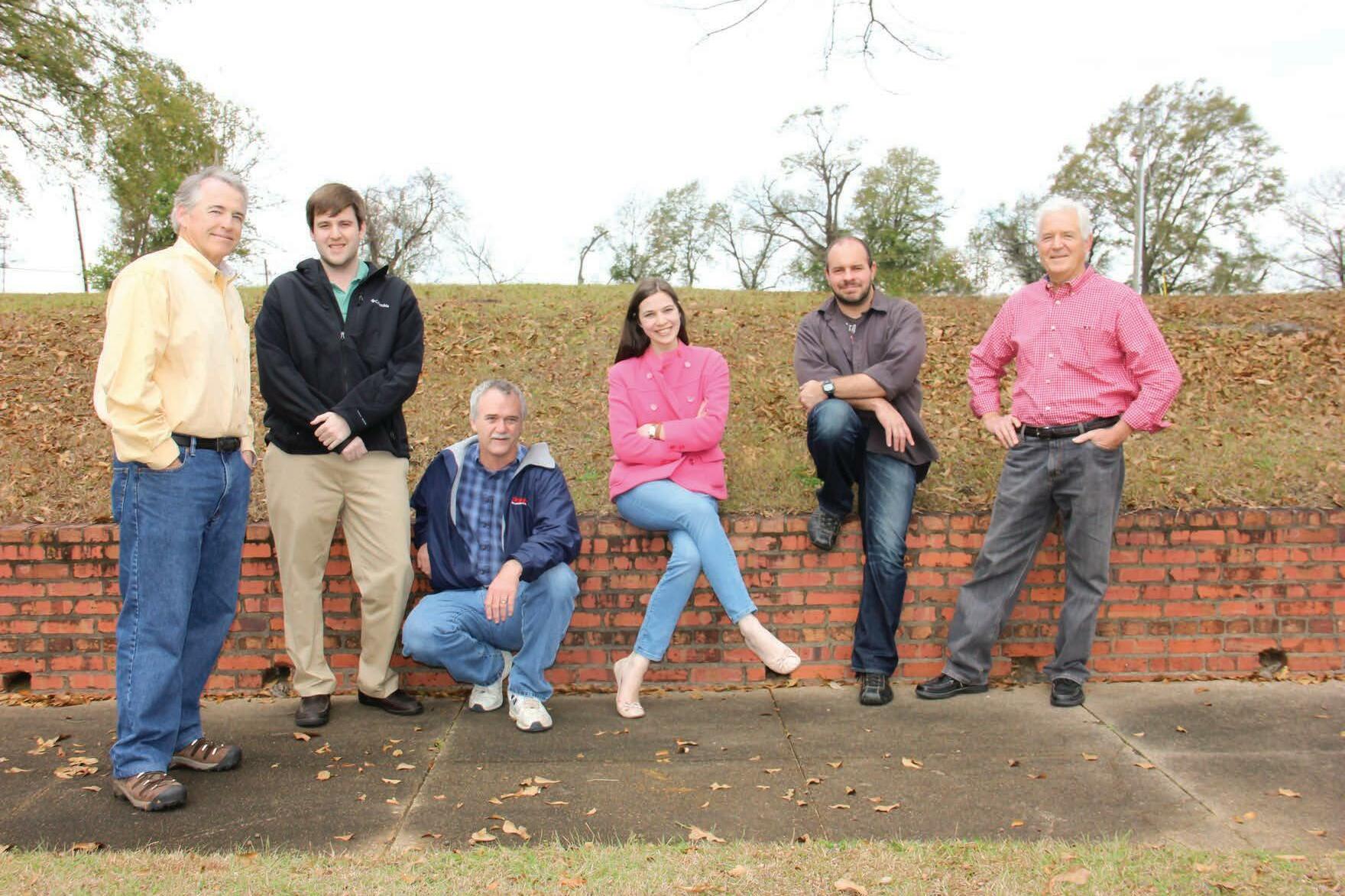
27 minute read
Southern Stumpin’
By David Abbott • Managing Editor • Ph. 334-834-1170 • Fax: 334-834-4525 • E-mail: david@hattonbrown.com
Pumpin’ Pain
The sky seems to be the limit...for fuel prices. And that's just the icing on the crap cake for loggers. Crad Jaynes, head of South Carolina Timber Producers Assn., is blunt: “In my 45 years it is the worst I have seen.”
With nearly as long in the industry, South Carolina logger Bob Lussier and Alabama Loggers Coun cil Director Joel Moon echo Crad’s assessment. “I’ve never seen anything quite like this,” Moon says. Lussier has seen five economic downturns, but never before such a rapid escalation of costs. “Inflation rate for logging here is anywhere from 38-42%," Crad continues. "Quite a few contract haulers have said to hell with it.”
Carolina Loggers Assn. Executive Director Jonzi Guill says she has not talked to a logger recently who isn’t considering downsizing crews or selling equipment: “Our loggers are hurting bad.”
One Mississippi logger anonymously summed it all up succinctly: “The margins were already tight but you factor in diesel prices along with inflation of every other thing we use, it’s a nightmare. I’m afraid the cost of fuel is gonna put a lot of loggers out of business. We have seen a little help from mills but when you’re getting a 3% bump and 40% inflation…even us ol’ dumb loggers can figure that math out!”
Bill Jones, Assistant Director, Southern Loggers Co-op, says it will remain tight until there is more production in refineries. “I don’t see it getting any better until maybe the fall.”
Moon thinks not even then. “The fall is gonna be worse, in my opinion.” His reasoning: fuel prices stay high, but demand for wood products declines (consider the Fed’s recent interest rate increase and the effect on housing starts). Right now maybe mills could pay more; then, maybe they can’t. “Lum ber has rolled back a little already and paper usually follows about six months later. I think there is a crisis coming.”
Supply, Demand
“We are in a challenging situation, with inventories running low at all the terminals across the whole United States,” Jones warns. “We have less than 12 days of inventory in the whole system.”
SLC President/CEO Todd Martin adds, “We have never witnessed the markets move in the way they have moved over the past year, especially since the beginning of this year. It makes it difficult for us to manage and even more difficult for our members to survive. From all indications we are hearing crude will reach $140 per barrel by fall.”
Jones explains, “What has happened on the world market is that the European Union has finally agreed not to buy any more fuel from Russia. It is putting more pressure on what inventory we have.” He doesn’t expect Saudi Arabia, Venezuela or Iran to help. “If we don’t start producing we will continue to tighten our grip on our inventory and there will be a bidding war for whatever is in those tank farms across the country,” Jones continues. “We might even see some rationing by the middle of the summer. Loggers hate the high price but they really don’t like it when they run out.”
Martin reports that SLC has already experienced supply difficulties, especially on the East Coast, and recently in Alabama too.
Despite the high prices, the volume of fuel purchased has not diminished yet. Some SLC stations are posting record days. That’s an upside for members: big dividends. “The SLC saves our members dollars at the pump, and we also give back,” Martin says. “Each year 100% of the SLC’s net profit is paid back to our members in the form of patronage dividends.”
Going Or Gone
“(We) can’t do what we are doing much longer,” another anonymous logger says. “I just got through running my P&L for the last five months and am losing $3,500 per week. Not only fuel but everything. Can’t and will not continue to lose money like this.”
Toni McAllister of Louisiana Loggers Assn. be lieves exorbitant fuel prices were just the stick that broke the mule’s back; now, she says, loggers are dropping like flies. One timber dealer, she re ports, recently lost four of his nine crews in a week.
“Inflation will kill us slowly; fuel will kill us this month,” North Carolina logger Brent Roberson warns.
Tim Rodrigues in Texas says he has parked or sold most of his equipment rather than continue producing at a loss. Same at Mark Pipkin Logging in Arkansas. “We can’t continue to lose money. We are no longer logging due to everything going up but our pay,” Rebecca Pipkin says.
“We are losing a few now but in the next 60-90 days we are going to lose a lot,” Lussier fears. He admits he is among those taking a hard look at his options if things don’t change. “I’m not going to keep losing money. When I was younger I had to take money from my savings to keep my business afloat, but I am to the point now I am not going to do that anymore.”
That’s no surprise to Richard Schwab at Florida’s M.A. Rigoni. “I think with Bobby (Goodson) going out, he and Lori have inspired a lot of people to strongly consider whether they want to re-up in this business climate.”
Years of equity help a generational company like Louisiana’s McManus Timber survive a while, but there’s a limit, Josh McAllister says. “We are starting to not break even, so we have to find the stopping point when we quit using up all our equity, because that is not a sustainable business model.”
Sometimes, loggers have to know when to say no. Buck Vandersteen, Director of Louisiana Forestry Assn., suggests, “In order to survive we have to ask, do I take a tract that is 80 miles away or decline it for one that is worse timber but closer?” Moon agrees. “I am seeing in some instances loggers walking away from jobs that would not be profitable to them.”
Too Little, Too Late
Lussier recently took a close look at his numbers using a cost calculator. He found that his fuel ex pense for the first half of the year is up 57% over the same period last year, while production is down 30% due to quotas. He tried to show the data to mills, hoping for better rates. To his dismay, some refused to even meet with him.
“As an association we want to do all we can to help our loggers succeed, but…until we get some help back from the mills I honestly do not know how long our loggers can maintain,” Guill says.
“It’s sad that they can all show record profits, but they can’t pass it down to their supply chain that is struggling,” Lussier states.
It is hard for loggers to see CEOs of large companies they work for paying billions in dividends to investors, while their suppliers are contemplating going out of business. “That is a hard pill for loggers to swallow,” Josh acknowledges. Toni adds, “We know we are the bottom of their supply chain but they still can’t have that product without us.”
Sources report that many mills (not all) are in fact paying fuel adjustments, but it is often too little, too late. And in some cases, the adjustment came with a cut in delivery price. “As long as trucks are going across the scales, they think everything must be lovely…but every load is losing $100 or more,” Crad says. “It is just so discouraging. I want them to make a profit, but they have been making record profits on the backs of the suppliers and forestland owners.”
“If you are relying on a mill to give you what you need without asking for it, you’re not gonna get it,” Schwab believes. “They’re not volunteering anything. Loggers have to demand it. The days of trying to push people to do it for less are over.”
Loggers can’t make up the difference with production anymore because of quotas. “Inventories are high at mills, so many loggers are not getting a full week of work,” Vandersteen acknowledges. “Loggers are frustrated with mills; mills are in an awkward position. They have made money, but a lot of it has been reinvested in plant improvements and new plants and that is critical. But a lot of people wonder, could they have done more to help the logging side of the industry?”
Moon cautions against loggers and mills fighting each other because it will be counterproductive for all in the long run. “Loggers and mills are partners. We’re all in this together.” SLT

Both Sides
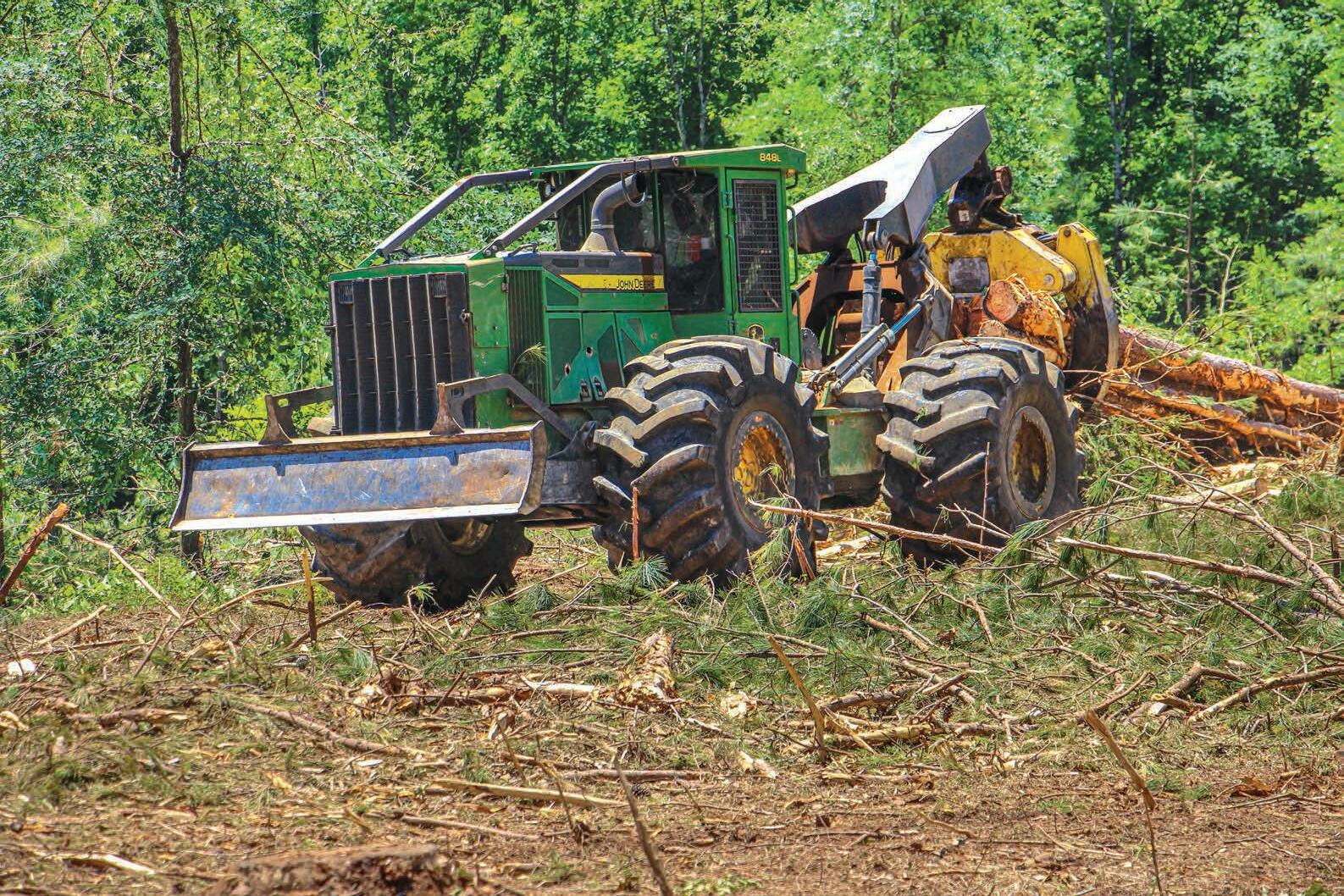
■ Stephen Singleton cuts trees under Southern Pine Harvesting and replants under Singleton Forestry Service.
By David Abbott
BUENA VISTA, Ga.
Stephen Singleton, 53, has worked in the woods for 35 years, but he’s only identified himself as a logger since 2014. His career has been focused primarily on reforestation. The company he started right out of high school, Singleton Forestry Service LLC, works all over the Southeast, spraying and prepping harvested sites from June to November and re planting from November to March.
Logging, he says, sort of grew out of that. It was something he had always wanted to do. “My dad was in timber management and procurement for years,” he says. “That is where the idea came from.” The elder Singleton started his career at Georgia Kraft and retired from MeadWestvaco, as the company changed ownership and names over the years. The family also farmed. Stephen skipped college, starting Singleton Forestry Service at age 18 in the winter of 1986. He also kept farming till age 25, when he decided to commit himself to forestry full time.
Eight years ago, an opening to deliver fiber to a local mill afforded Singleton the opportunity to expand his operations into logging. With help from Deere dealer Flint Equipment Co. and timber dealer Piedmont Forestry of Macon, Singleton started a second company, Southern Pine Harvesting, LLC.
Two years later, Singleton secured a position logging on land owned by REIT CatchMark Timber Trust (which recently announced a merger with PotlatchDeltic) and managed by FRC (Forest Resource Consultants, Inc.) of Macon. The crew continues to work FRC tracts exclusively. “We do no outside wood,” Singleton says. “We don’t even cut our wood that we own.” He owns about 1,000 acres spread out among several different locations, but contracts others to harvest it when it’s ready.
Singleton goes back and forth between the two companies, wherever he’s needed, and has foremen to help supervise the crews. “I am out of town a lot when we are planting pine; I live in hotels pretty much the whole winter. We cover 10,000 acres a year from here to Florida, east Alabama and northeast Georgia, about 150-200 mile radius.” He is a member of the Georgia Forestry Assn. as well as the Florida Forestry Assn. He does a lot of tree planting and spraying in Florida, but no logging.
★
Stephen Singleton and his daughter Calli
Crew
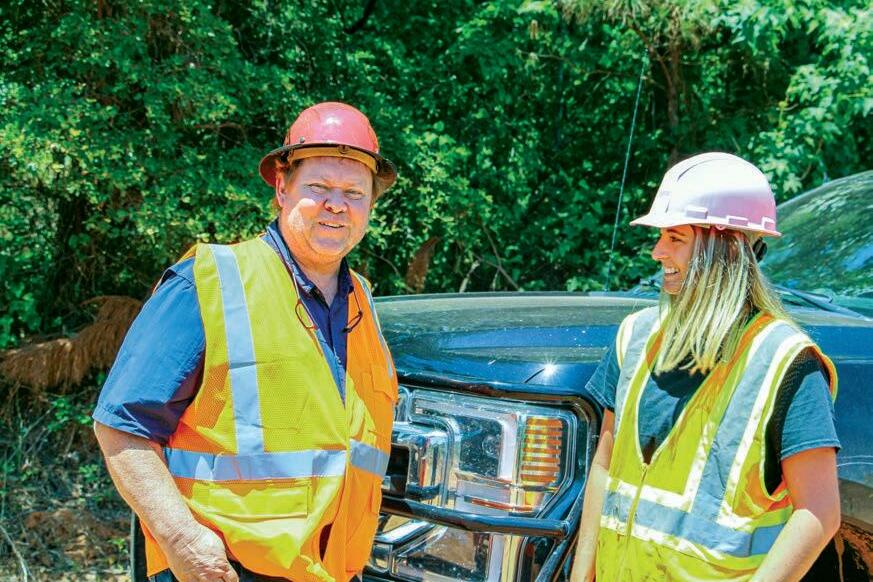
On the logging job, David “Peewee” Kelly runs the processor and the crew, serving as foreman. Kelly has family in the woods with him: his son, David Kelly, Jr., call ed D.J., operates the loader, while his brother Shane Kelly is a truck driver. So are David Dodson, Kelvin Jordan and Eric Tymes. Nick Dennard trims trucks, sets out trailers and prints load tickets on-site using an iPad. Trey Majors drives the skidder and Dexter Jones mans the feller-buncher. In the office, Melanie Harrelson serves as secretary/bookkeeper.
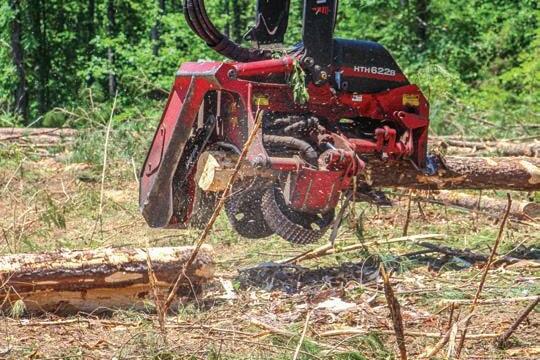
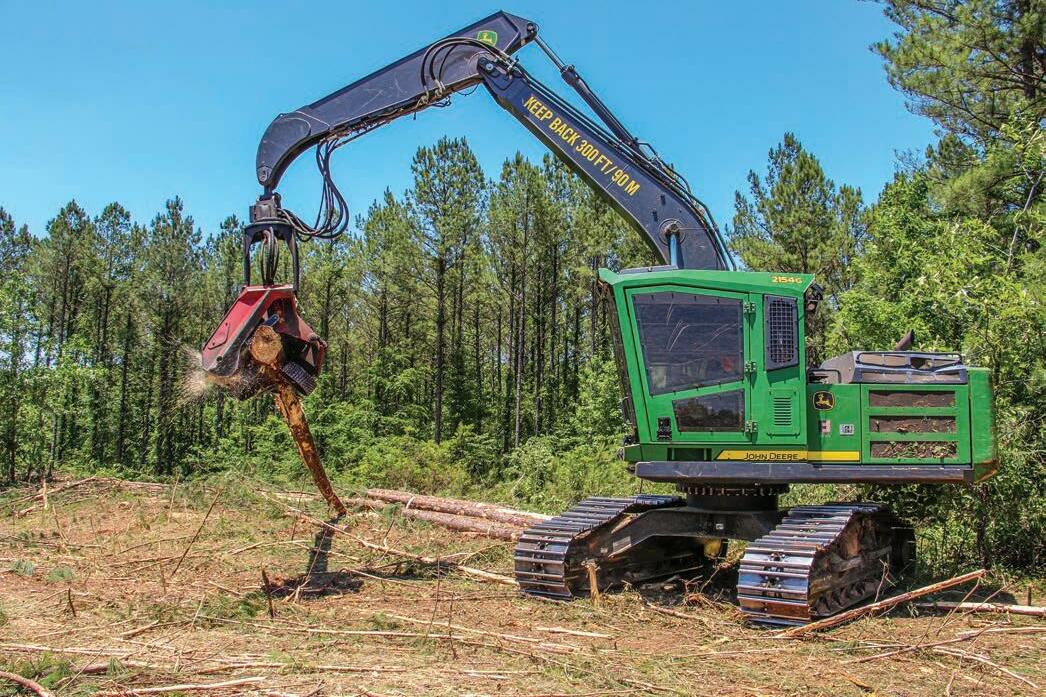
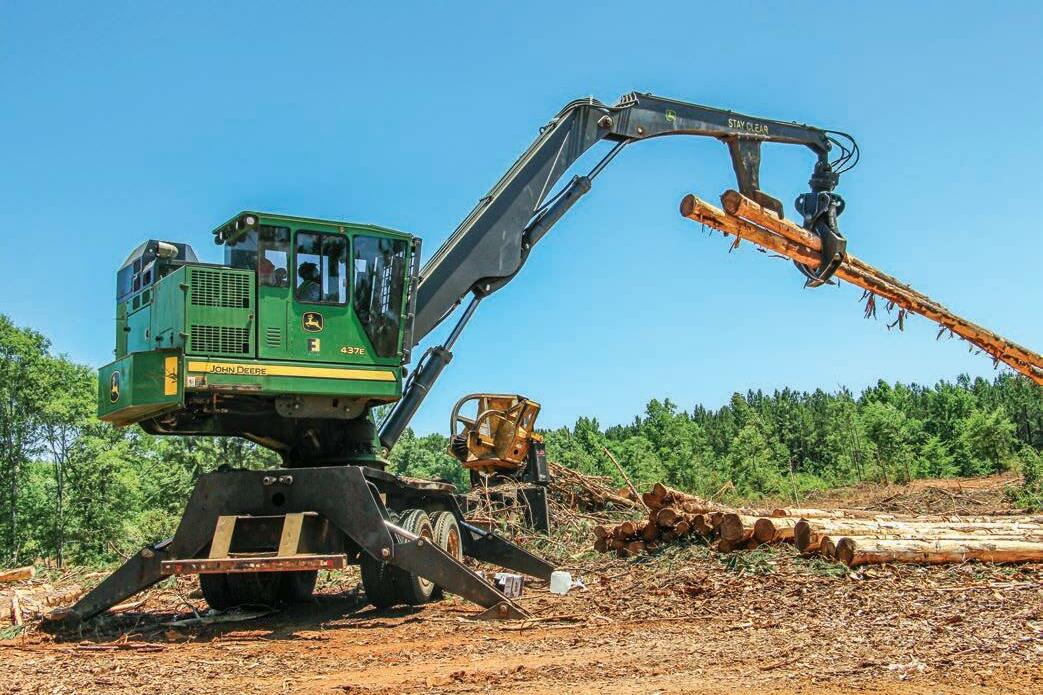


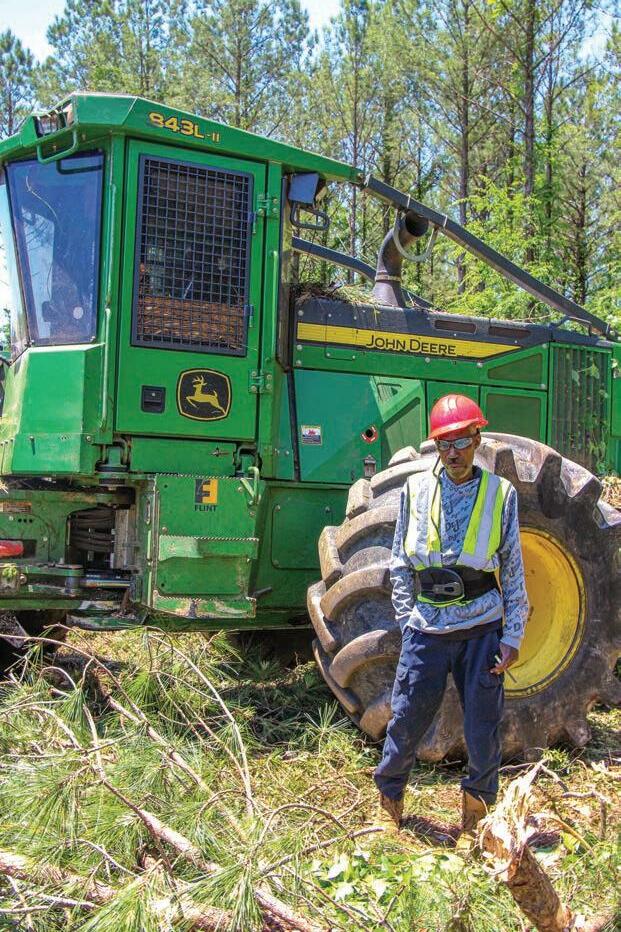
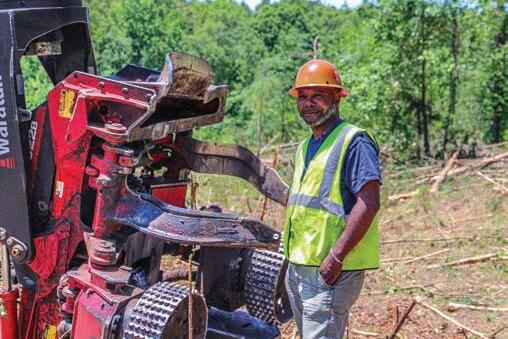
Most of this crew has been with Southern Pine Harvesting a long time. Except for young guns Majors and D.J., most of these guys are in that 50-60 age range, their employer points out. It’s a trend in the industry that Singleton finds distressing. “The older loggers are getting into their 70s and the younger ones aren’t coming up to replace them.” He worries what will happen to the industry in a few more years when all that collective experience evaporates as those veterans retire.
“Looks like the mills would not try to put out of business the ones who know what they’re doing,” he opines, considering how many seasoned and established pros, like North Carolina’s Bobby Goodson, are opting to walk away against a backdrop of record high demand and profits for the mills they supply. “Looks like it would be an opportune time to make some money if they would allow it, but they’re not. Logging is sick right now. It is an unhealthy industry.”
Singleton contracts consultant Darlene McDonald’s Safety On Site to conduct documented safety meetings with the crew once a month.
Singleton says the processor helps keep production steady.
Operations
“To me John Deere is second to none,” Singleton says. On the re planting crew, for 12 years he used to lease a dozen 650 dozers every year. With that kind of history, he says, it was no problem for him to get logging equipment financed. “They put us in business overnight, no money down, nothing.”
Other than one Tigercat loader in reserve, the logging side runs mostly Deere machines: an ’18 848L skidder (a ’16 model 948L is a spare that gets used quite a bit); ’19 model 437E loader; a 2020 model 843L-II feller-buncher; a 2154 carrier with Waratah 622B processor head; and a 650K dozer for road work.
The processor merchandises stems at the stump, then the skidder drags the processed wood to the loader. “Interfor, one of the companies we haul to, started wanting prime, cut-tolength wood. We were measuring it out with the loader and that just seemed to be really beating us up doing it that way, so I took a plunge and bought this thing,” Singleton says of the processor. He adds that the purchase was also motivated by a series of wet tracts. “You could reach down into the wet area, shoot the wood 60 ft. up the hill with less rutting, less drag on the skidder, and that thing doesn’t have to move much, about every 30 minutes. It works pretty well for us. It helps keep a steady pace with production. Only time it doesn’t pan out is when we get on a tract that is more pulpwood than logs. It is really made for logs.”
On the reforestation crew, Singleton attaches spray tanks to two John Deere 648 skidders to apply herbicide. “We spray to kill sweet gum and briers and all the competition for pine, anything you don’t want to grow,” he says. The crew also uses six D3 Cats pulling C&G tree planters.
Cat machines come from Yancey Bros. in Columbus, while Flint Equipment Co. branches in Colum-
From reforestation to harvesting, Singleton has a long history with John Deere machines.
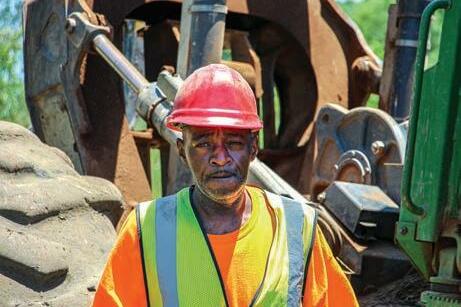
Foreman David Kelley Cutter operator Dexter Jones Skidder driver Trey Majors Loader man David “D.J.” Kelley, Jr. Nick Dennard mans the pole saw.

bus and Albany provide sales and service for all the Deere iron. Operators tackle routine maintenance and minor fixes in the woods, but Flint handles major repairs; in fact, one of their techs was on site the day Southern Loggin’ Times visited in late May, working on the 948. “That one is not under warranty,” Singleton laments, estimating the repair bill may run $5-6,000. A pin fell out on the steering cylinder, bent and broke the driveshaft. “That is the first major mechanical failure we have experienced,” he says.
Singleton fears that, for all the convenience of today’s technology, we lose something in exchange. “PR has lost some of the personal touch,” he fears. “You can look up anything online, but there is still a value in getting together in person, look in the eye, shake hands, ask questions. There are still a lot of us out here who like to fellowship.”
Southern Pine Harvesting hauls with four Mack trucks pulling eight Pitts trailers. He buys trucks from Nextran Truck Centers in Macon, and of course he buys his trailers directly from Pitts, whose headquarters is just across the Chattahoochee River in Pittsview, Ala.
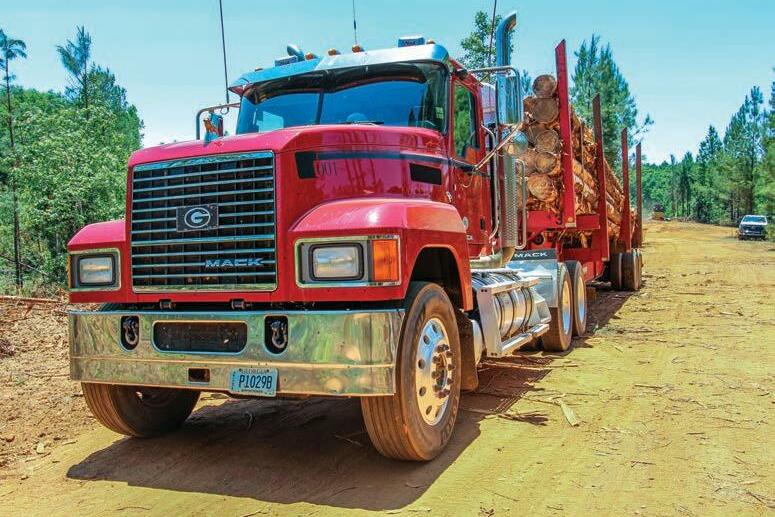
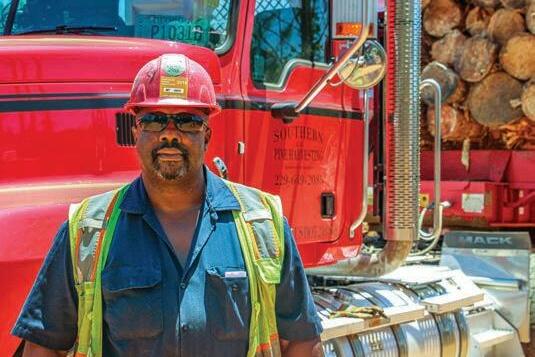
Truck driver Shane Kelley
Truck driver Eric Tymes
Timber
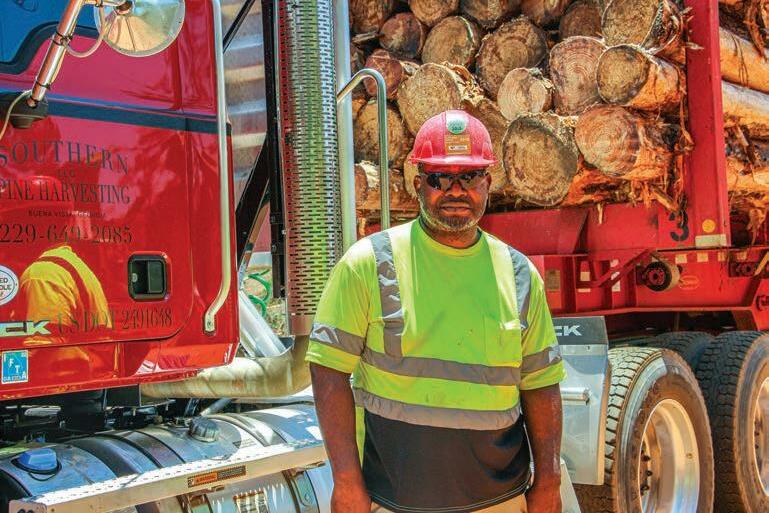
The crew typically clear-cuts mature, pine-heavy stands. “I have never thinned a tract,” Singleton says. “This stuff will be replanted, not this season but next season, because of the timing. It is on a rotation.” Singleton won’t be doing
A quartet of Mack/Pitts combos hauls 70s weekly for Singleton.
The logging crew does only clear-cuts, no thinning jobs.
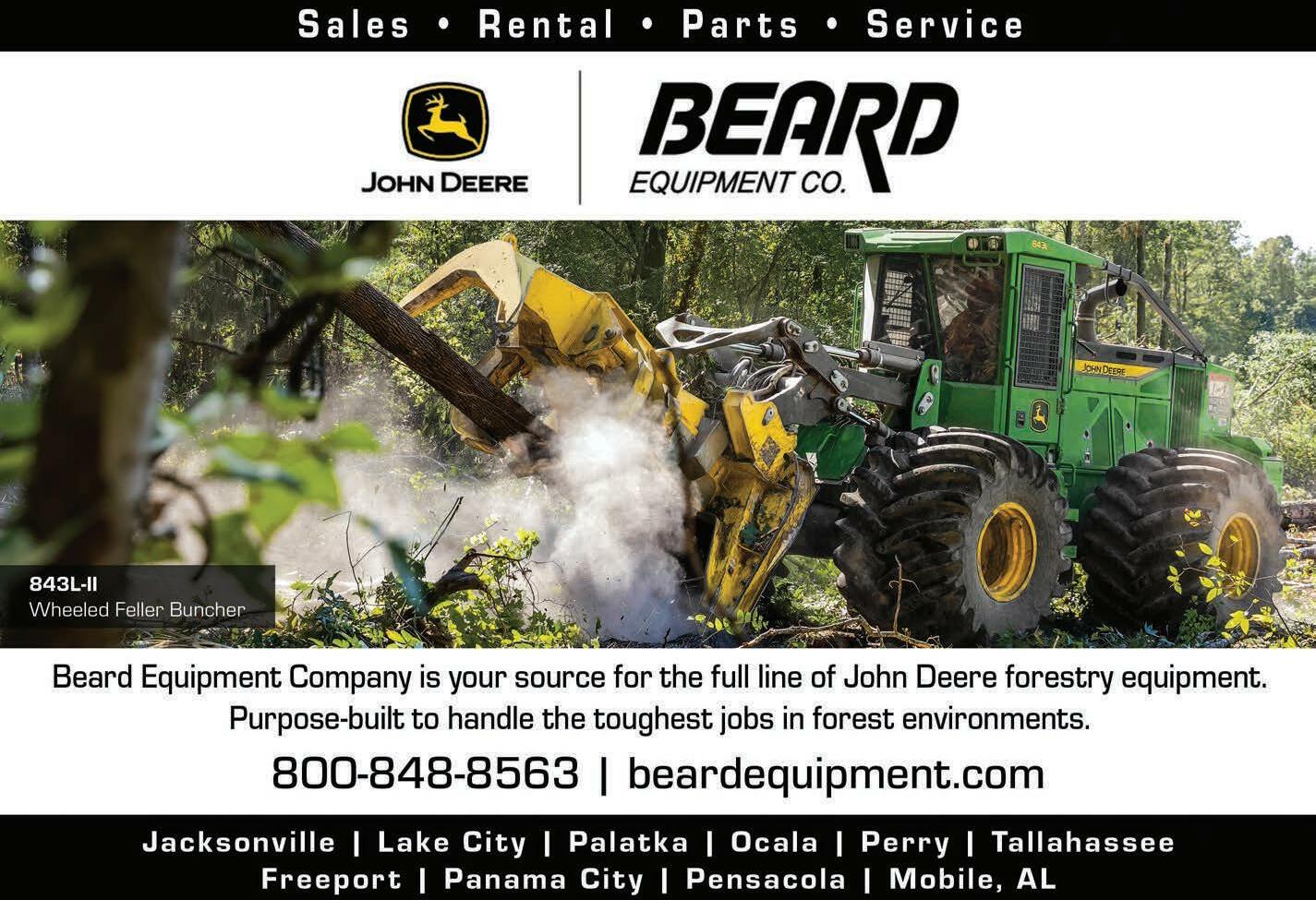
the replanting though; Singleton Forest Service seldom follows Southern Pine Harvesting, working other contracts.
Production lately goes to the WestRock mill in Cottonton, Ala. The crew looks to haul 70 loads a week, but Singleton admits the weekly total falls below that mark more often than he’d like due to weather and breakdowns.
“Fuel is really unbelievable right now,” Singleton echoes the thought on everyone’s mind. The mill has given a fuel surcharge, he acknow ledges gratefully. “We got some help back in March. We have some good people looking after us here and they have given us some extra here and there to help with some of the cost. The trucking doesn’t get a whole lot because I am hauling under 40 miles; the guys who haul more than 40 get a pretty good one. The fuel in the field is the worst part; we don’t get a whole lot for that. Right now we are kind of breaking even on the extra fuel cost, but it is about to catch us. It is going up like crazy.”
Southern Pine Harvesting runs Verizon GPS/dash cam systems in all its log trucks and pickups. “It works pretty good,” Singleton says. “You can tell where everybody is at. If anything happens it sends a video to my email, and tells when there is hard braking or taking off, or any close calls. It is a good safety practice.” He added the system at the suggestion of Commercial Insurance of Augusta, which covers all his insurance needs with carrier Bituminous.
Singleton’s wife Tammy is a nurse practitioner at CareConnect Family Practice in Buena Vista. They have two children: son Son ny, 25, and daughter Calli, 19. Son ny is studying sports management and Calli is a pre-nursing student at Georgia Southwestern State University in Americus. SLT

Singleton and Tymes discuss the next load. Flint Equipment handles repairs on-site; field tech Cason Taunton works on 948L skidder.
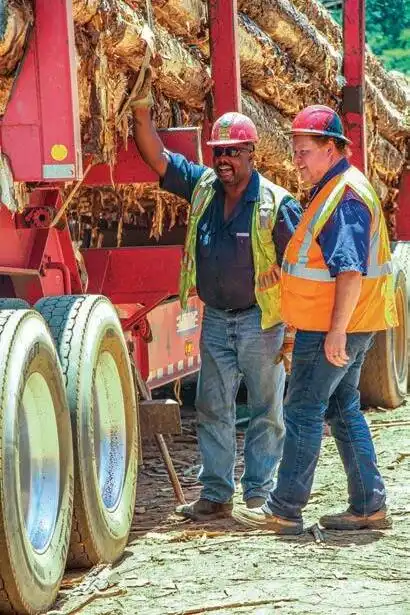
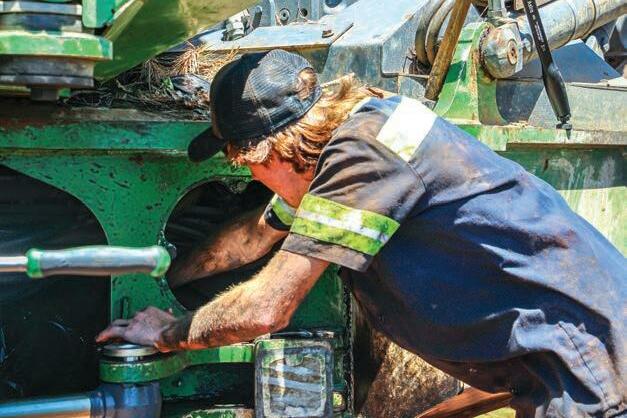

Back To Back
■ Expo Richmond returns to Virginia second consecutive year, making up for missing 2020.
In the context of equipment shortages, problems with labor and transportation, and high fuel prices, show organizers were pleased with turnout.
Despite extreme heat, attendance was strong, with 4,000+ registered guests.

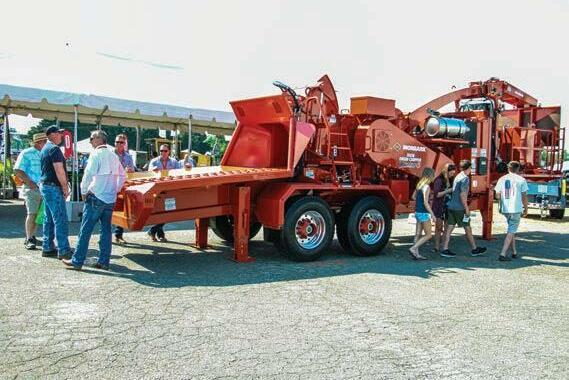
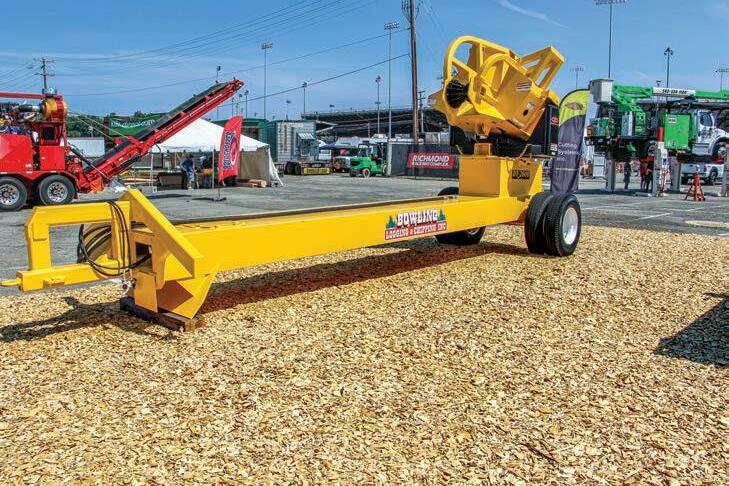
Schwab Brothers Hydraulics showed off their CHAD (compact hose assembly device). Equipment order backlogs continue. CSI could only bring one item available to sell: a delimber trailer; before the show even started, Forest Pro customer Tim Bowling bought it.
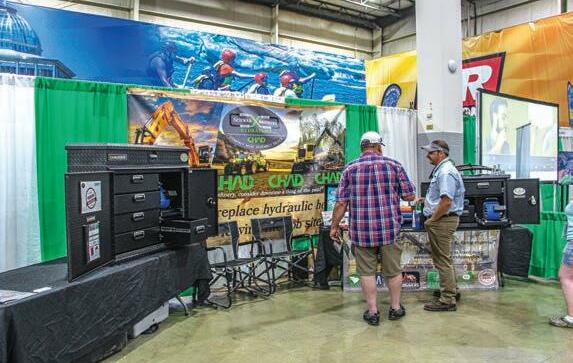
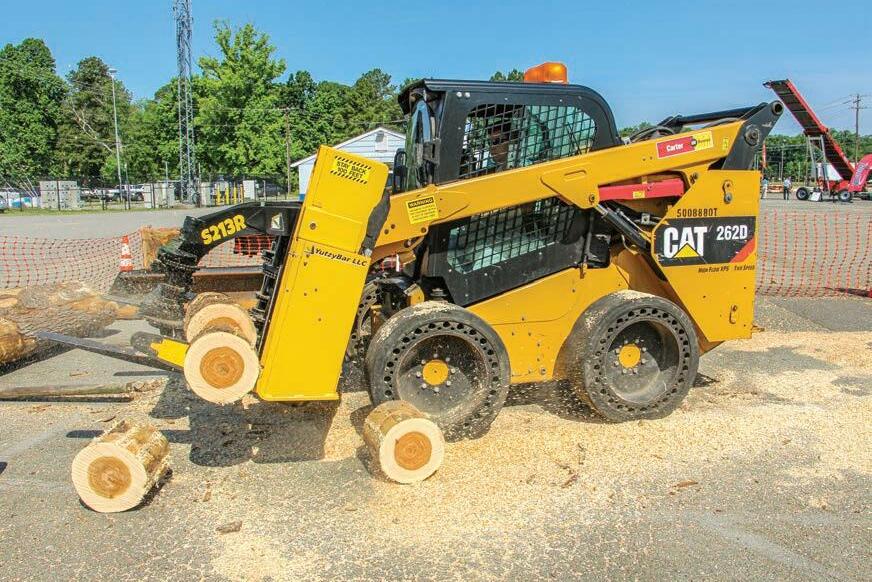
Exhibitors reported being pleased with the quality of attendees. Expo will return to Richmond Raceway on May 17-18, 2024.
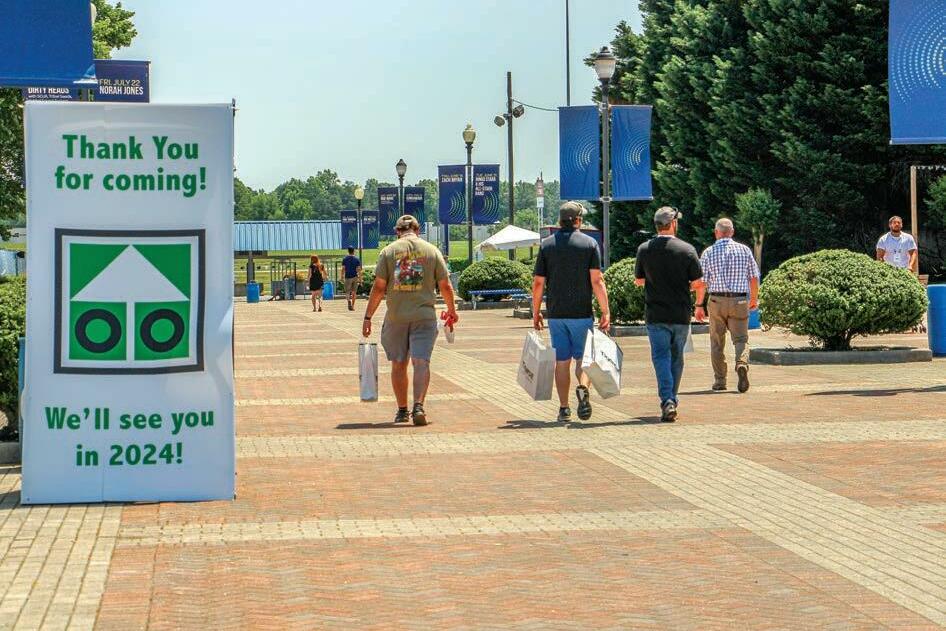
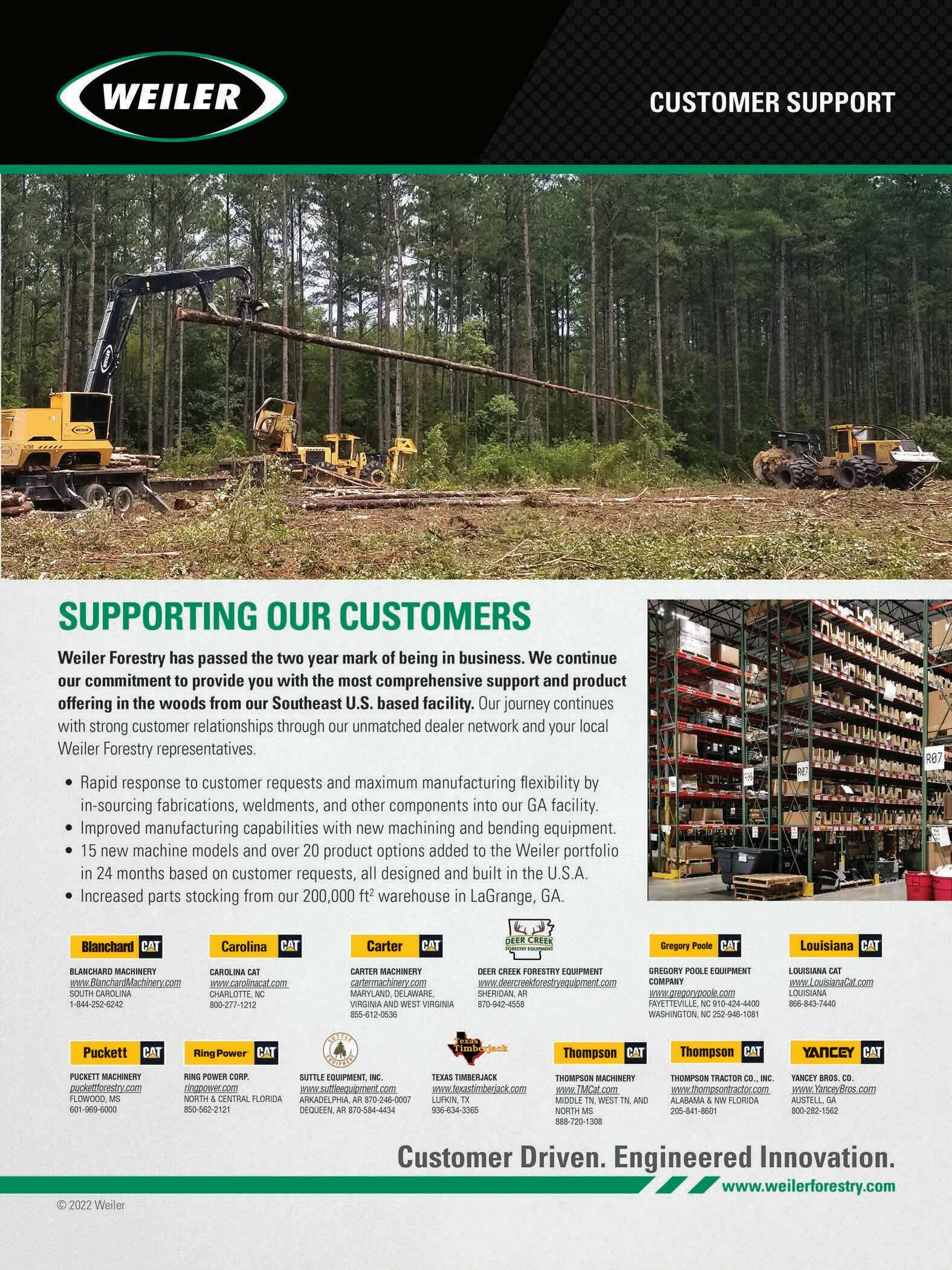
Spotlight On: Felling, Processing, Etc.
EDITORS NOTE: SLT invited manufacturers of feller-buncher and harvester saw heads, processors and related components to submit material on their offerings, presented here edited only for style consistency and space constraints.
John Deere
The John Deere FR50 felling head builds upon the successful qualities of previous models for increased productivity, range and visibility. The FR50 model is compatible with the 800M- and 900M-Series tracked feller bunchers, including the 803M, 853M, 859M, 903M, 953M and 959M models.
Designed to offer the quality and reliability customers expect from John Deere equipment, the FR50 model offers increased accumulating capacities, improved range of motion and excellent visibility. Additionally, the FR50 model features 30° and 310° wrist configurations respectively. This felling head helps to make the hardest tasks easier and more efficient for customers. The FR50 model has a cutting capacity of 20 in., and an accumulation capacity of 6.9 sq. ft.
The FR50 felling head features superior alignment of bunched timber to allow for optimal logging and harvesting. The felling heads provide a taller horn that works together with the pocket and arms to collect larger, tighter bunches. The horn delivers excellent handling of tall trees, which improves skidder productivity during tree removal. The FR50 model also includes arm cylinders mounted high for impressive wear protection of the saw housing, and can easily hold up to 15 six-in. trees.
The FR50 configuration maximizes versatility when positioning bunches in both plantation and thinning conditions due to the increased rotation. Additionally, the FR50 felling head provides excellent visibility to the cutting area and superior wear protection of saw housing. A full coverage option is available for both models, and for the FR50 model, sealed bushings in all clamp arm pivot joints are available. Visit deere.com for more.
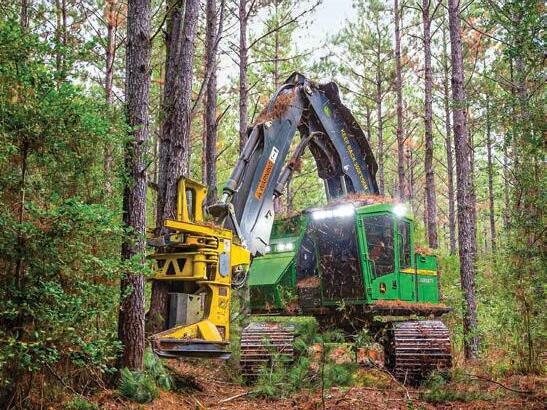
Ponsse
The completely upgraded Ponsse H8 harvester head features a powerful feed, firm grip and solid yet agile frame. Active Speed is available for the harvester head as a new feature, giving it a superior performance. With Active Speed, the harvester head’s operating speed can be adjusted based on the tree species and stem diameter. Equipped with this new function, working with the H8 harvester head is smooth and productive, no matter what the tree diameter is.
“We have developed our product range of harvester heads actively with our customers. Many of our customers work in challenging conditions, which is why their development ideas give us the best possible feedback for product development. With its completely new structure, the new H8 harvester head is ideal for processing large trees,” says Janne Loponen, product manager for harvester heads.
The new harvester head can be mounted on Ponsse Ergo, Scorpion Giant and Bear, the strongest harvesters in our product range. The saw box area is even wider, making the harvester head an excellent choice for trees with a high butt diameter. The harvester head’s structure has been designed for easy maintenance, and the frame has been built to be even more durable. A powerful feed, combined with a geometry that firmly supports larger stems on feed rollers, guarantees high productivity and fuel economy. The automatic features of the Opti control system, developed and built by Ponsse, control the feed speed and saw movement, according to the tree diameter, and ensure fast and precise sawing.
All Ponsse harvester heads have been designed to withstand the toughest conditions. They are characterised by a simple and solid structure, which is why they can be used in various harvesting applications. All Ponsse harvester heads are manufactured and designed at the Ponsse factory in Vieremä, Finland. Comprehensive design applies to both mechanical components and the electronic control system, controls and software. The manufacturing process is highly automated, guaranteeing a high level of quality and measuring accuracy.
For more information, contact Janne Loponen, product manager, harvester heads, janne.loponen@ponsse.com.
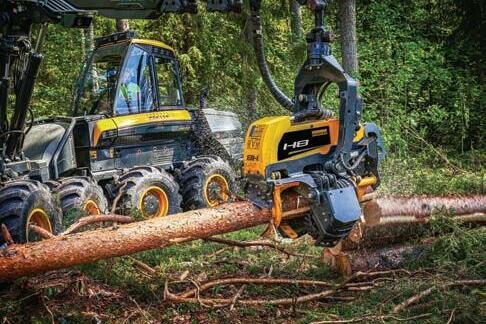
Quadco
The Quadco Group is three well-known industry leaders that joined forces to better serve you; Quadco, Southstar and Logmax. With over 165 team members worldwide, we offer you the largest selection of forestry attachments in both cut-tolength and full-tree systems, spanning the full spectrum of wood sizes and forest types.
Our high speed disc saws cover a wide range, available up to 27 in. capacity and in many styles: the “Arms-Down” BSeries, the “Arms-Up” C-Series, the “Super Capacity” SC-Series, and the Bunching-Series, which is our high accumulation model, made for young plantation stands.
Intermittent disc saws, up to 29 in., are true ‘big-wood’ and ‘steep-country’ tools that offer endless possibilities like the ability to shovel timber, trim oversize limbs and forked tops, common to many hardwoods, without running the risk of bending a bar or throwing chain.
Five models of bar saws, up to 43-in., in fixed-mount and dangle-style, followed by two shear models complete our felling head offering.
On harvesting heads, you are offered a choice between two strong brands, Southstar and Logmax, each with its own unique design characteristics, number of feed rollers, number of delimbing arms, top saw, with the same final objective of always delivering high feed speeds and delimbing forces, measuring precision, serviceability and durability. Our experienced sales specialists can help you choose the right product for your needs.
Our attachments and cutting tools are built for shift after shift production. You can find more about them at quadco.com, or reach us at info@quadco.com. You may also contact us through your favourite local equipment dealer. We look forward to being of service to you.


Tigercat harvesting heads are built to match the high-performance capabilities of Tigercat track and wheel carriers and are well suited to a variety of jobs including at-the-stump harvesting, roadside processing and debarking. The 570 is most productive working with trees 6-20 in. in diameter in softwood and hardwood stands. Although best suited to the Tigercat H845 series, the 570 is designed to work with the H822, H855 and 1185 carriers, or a 20-25 tonne forestry excavator. With optional hydraulically timed processor knives, the 570 can also be used for roadside processing. The 570 is also available with a fixed wrist for applications where positive control of felling and trimming of large limbs is required.
The 575 is a heavy-duty three-wheel drive harvesting head also best suited to in-stand harvesting in the 175-560 mm diameter range. It is very effective in tough applications like large limbed hardwood and crooked trees. With optional mechanically timed processor knives for easier picking, the 575 is also an excellent roadside processing head. The 575 features Tigercat’s unique three-two drive system. When processing a tree, the head starts in three-wheel drive, maximizing feed force for faster acceleration and quickly powering through bigger trees. As the load drops, it automatically shifts to two-wheel drive, improving efficiency and increasing feed speed up to 30%. Both the 570 and 575 use larger diameter hoses and larger capacity valves than similar class heads to match the greater hydraulic flovester carriers.
The 568 harvesting head is a robust, high performance head designed for tracked carriers. It is best suited for roadside processing applications, with trees in the 6-22 in. range. With timed knife arms and triangulated wheel arms, the 568 can quickly pick and maintain positive tree contact and control. The patented 4WD - 2WD auto-shift drive system provides extra power and positive grip when feeding large trees, fast speed in smaller trees and full manual control when needed. Knife arms feature double-edged, replaceable blades with optimal contour for clean delimbing. The front floating knife with spring preload follows the contour of the tree further enhancing delimbing performance. Other fea-


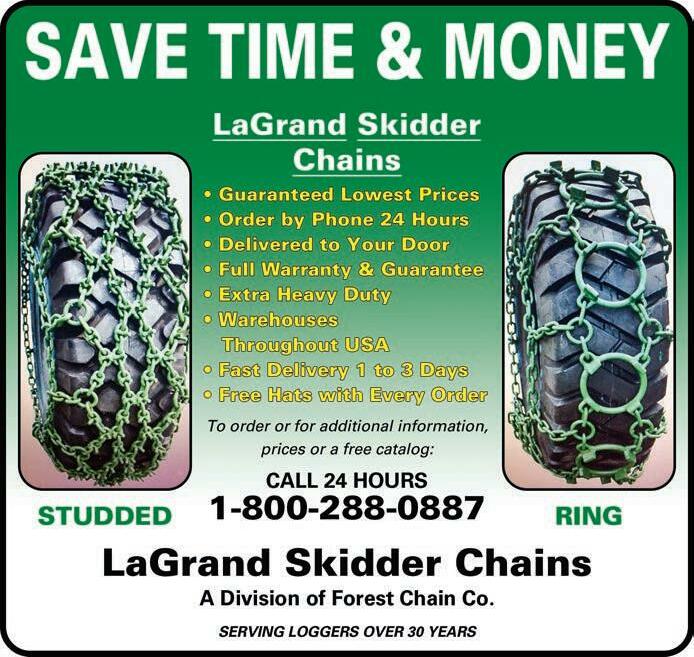
tures of the 568 include optional conventional boom or through-tip boom continuous rotation, laser diffuse or through-beam find end sensors, color marking and various feed wheels. Visit tigercat.com for more.
Gator Teeth save fuel and money since they cut more efficiently and maintain their cutting efficiency longer than any other saw teeth.
The patented design of the X Series of Gator Teeth are the world’s only self-sharpening saw teeth. The X Series have extra carbide (and steel) built out at the corners that direct the flow of sand and chips to
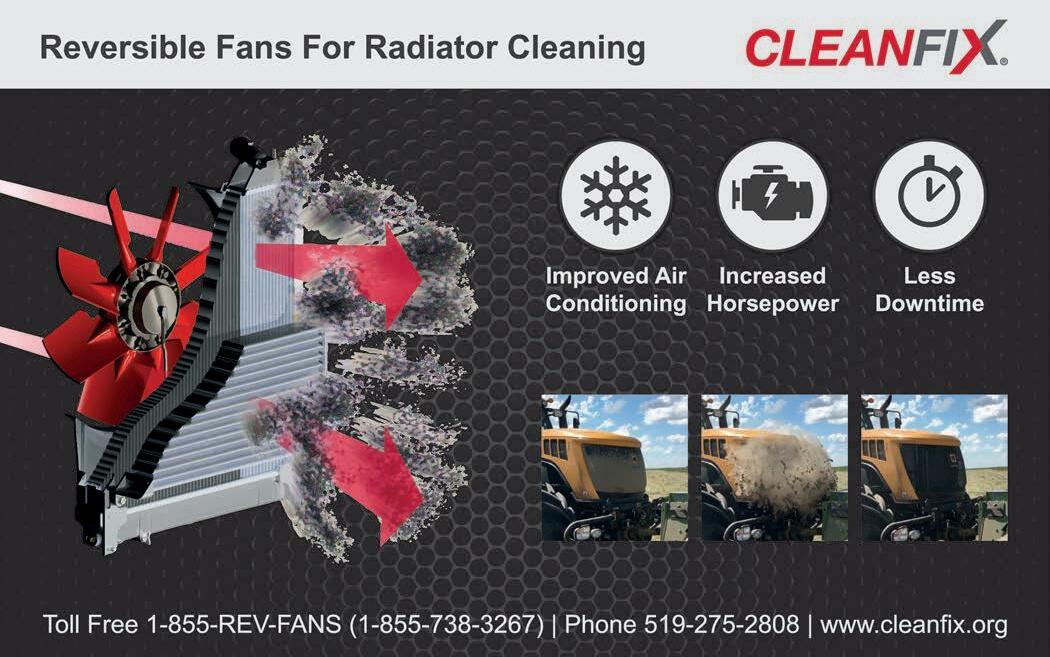
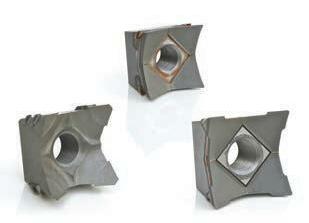
sharpen the Gator Teeth as they cut.
The original Gator Teeth with extra cutting tips at the corners result in the world’s most efficient cutting saw teeth giving long life, increased productivity and fuel savings.
For over 14 years Gator Teeth have been recognized for their superior performance due to their high quality, patented self-sharpening and extra cutting tip designs. Gator Teeth give you extra carbide at the corners where you need it. Long lasting, fast cutting Gator Teeth save fuel and money. Visit timberblade.com for more information or to locate a dealer near you.
Wallingford’s
Since 1959, GB has built a solid reputation by manufacturing products that set new industry standards, playing an active role in the development in the forestry equipment industry. A unique blend of titani-
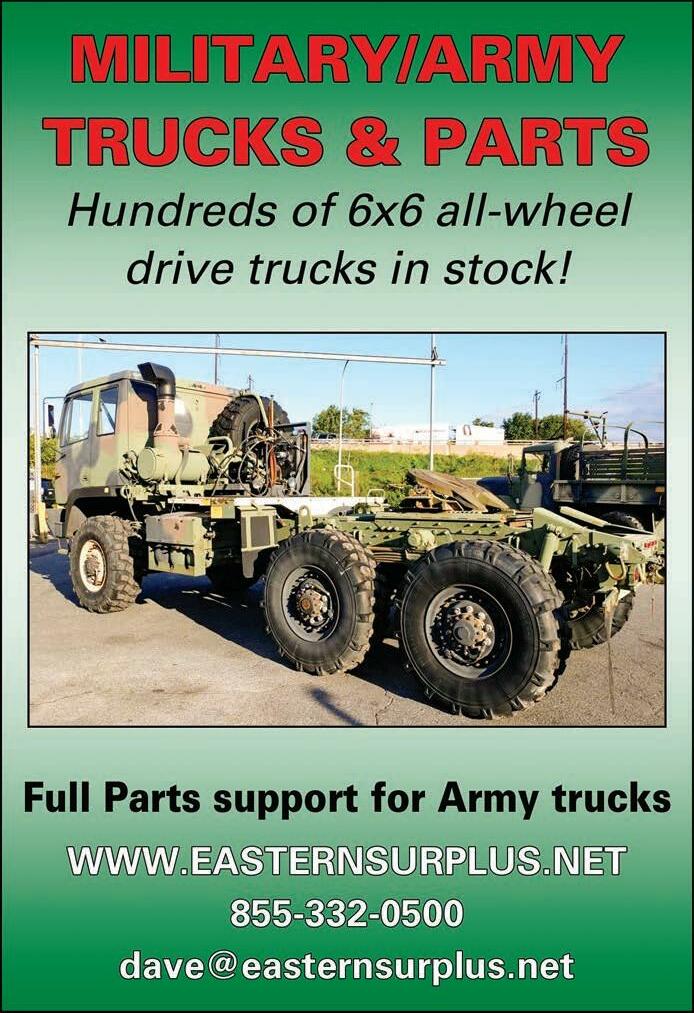
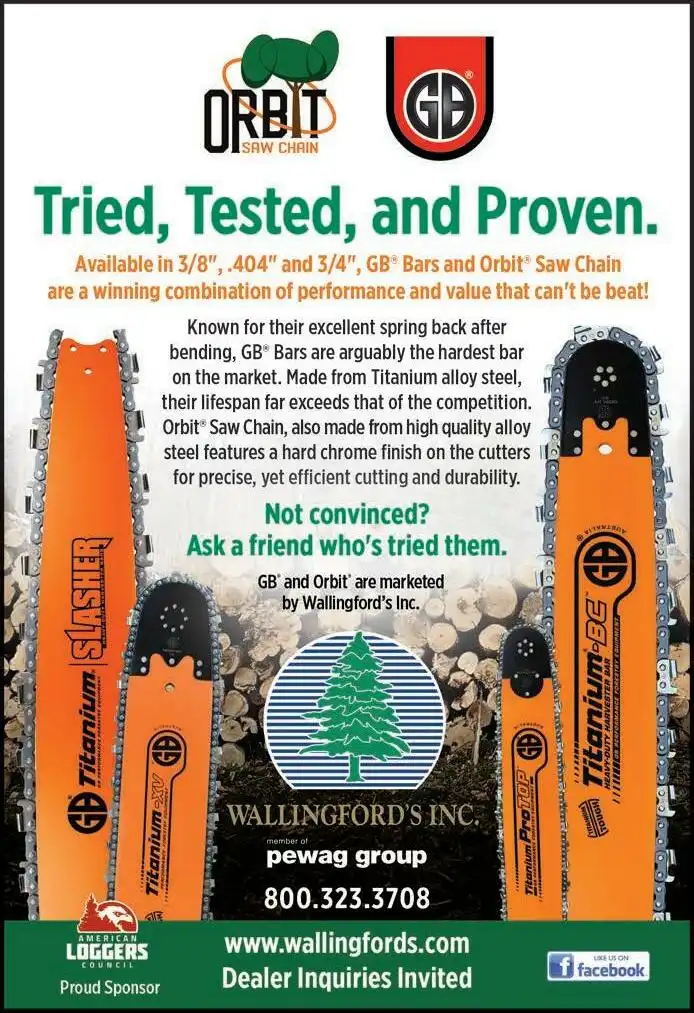
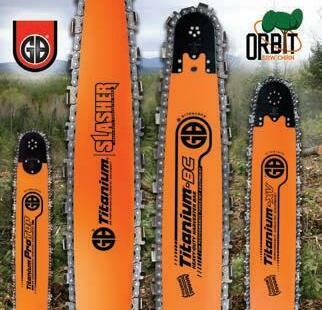
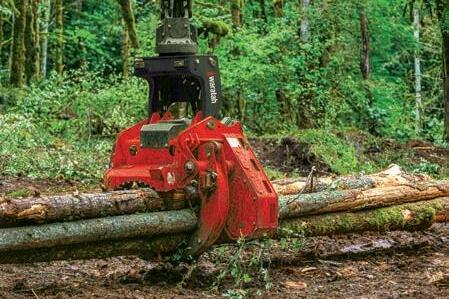
um and alloy steel yields the ultrahigh strength material with uniform metal hardness throughout the bar and because the rail is non-tempered this reduces rail flexing and cracking. This alloy steel is extremely durable, resulting in fewer bends and better “memory” allowing it to return to original shape, which increases run time for operators.GB professional harvester bars are available in both .404 in. and 3/4 in. pitch and are designed with mounting configurations to fit most mechanical harvesting processor heads. The .404 in. XVline has a patented 15-tooth sprocket, which reduces RPM, resulting in less friction and wear. This, combined with the patented “Lube Direct” channels to directly feed the bearings lubrication, improves overall performance and life. The 3/4 in. BC tip has the “Lube Direct” system and a machined edge to control chipping.
Orbit harvester saw chain is manufactured with high quality alloy steel and offers professionals the best balance of quality and value in the industry. Both Orbit 3/4 in. and .404 pitch saw chain havemicro radius semi-chisel cuttersand increased kerf width. Both Orbit lines of harvester chain are engineered for maximum performance and fast cutting speed. All Orbit saw chain is manufactured with enhanced multi-layered chrome plating providing excellent durability and wear resistance.
Please visit wallingfords.com for more information on Orbit and GB products, or call 1-800-323-3708.
Waratah
When it comes to unmatched strength and versatility, Waratah Forestry Equipment’s FL100 delivers. Designed for 30+ metric ton carriers, this large directional felling head is a multi-function workhorse, handling steep slope, shoveling, topping, bunching and traditional felling applications.
The FL100’s continuous rotation and dual rotate motors enable high rotation power requirements, helping increase productivity. This head features high-capacity grapple arms engineered for improving operational picking and holding force of logs. The extra-long, continuously curved opposing arms provide a 57.8 in. opening and 8.4 sq. ft. payload capacity. Additionally, its grapple force remains high even with its arms at capacity.
The FL100’s forward placed saw unit allows for easier cutting of larger timber. For power in small or large capacity loads, the FL100 has one cylinder per arm plus a synchronizing link for maximum grapple holding force and control.
The tough FL100 has a robust and sturdy design for increased durability. It handles various sizes of timber thanks to a one-piece, welded, high-strength steel frame coupled with large pin diameters and its grapple arm geometry. Its fixed saw box design also helps contribute to increased durability in a variety of applications.
The FL100 can adapt to any carrier and includes a valve-in-head design for simple integration. This head also utilizes Waratah’s TimberRite X-20 measuring and control system. The TimberRite X-20 controller provides configurable operational settings for improved head performance and productivity in varying applications. The adjustable settings help improve overall productivity by allowing operators more capabilities to properly fell timber.
Visit waratah.com for more information.
