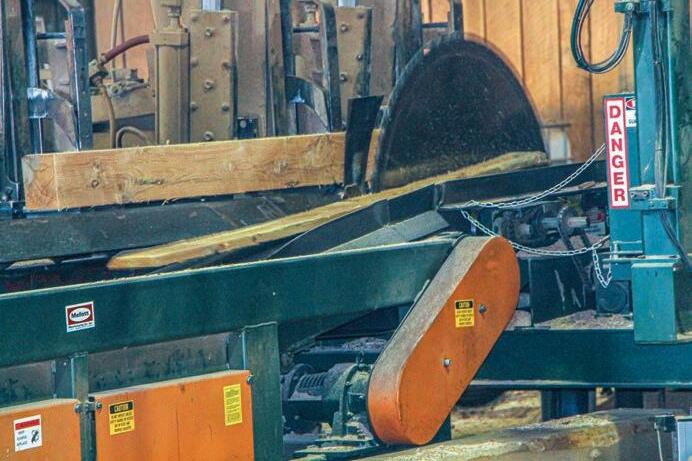
5 minute read
TO MILL WOODS
By
FREEBURG, Mo.
Skidmore Lumber Co., which includes sawmill and logging operations, is a family business. Current owners Howard, 62, and Doug Skidmore, 60, bought out the shares of their oldest brother, Odis, in 1992 and their dad, Oreal Skidmore, in ’94.
Doug and Howard each play an active role at Skidmore Lumber. Doug is the business manager, handling paperwork, finances, sales orders and so on at the mill; on top of that, when they added logging back into the mix a few years ago, he took on managing that side as well.
Howard focuses more on day-to-day production operations at the mill, and performs an engineering role applying industry knowledge into mechanical solutions.
Sibling rivalry can sometimes sabotage family businesses, but the Skidmore brothers attest that isn’t a problem for them. “I couldn’t ask for a better partner,” Doug says. Howard concurs: “We get along great.” It’s a rare enough thing; not every family can make it work when they work together, often butting heads and sometimes falling out with one another. The Skidmores are grateful to have no such drama in their working relationship. “That’s what our banker and our CPA tell us, to be thankful,” Howard acknowledges. “We are blessed,” Doug agrees.
All three Skidmore boys started out cutting cord wood as kids with their dad when Oreal went into logging. The family got into sawmilling almost by accident; someone owed Oreal a lot of money he didn’t have, so he signed over a sawmill he owned as payment for the debt. That was in the late ’70s when they acquired the original Skidmore mill.
It was a few years after that before they moved mill operations to the current location. In 1981, Oreal lost his right leg at the knee in a sawmill accident. “He was working on the guide on a friction feed slip belt with the carriage behind him,”
Doug recalls. “The carriage crept forward and threw him into the saw. So because of that we bought the sawmill here in Freeburg because it was an automatic, so our father could continue working.”
Even after Howard and Doug bought him out in 1994, Oreal continued working at the mill until his retirement in 2000. He lived until 2021, just shy of his 100th birthday.
Operations
In its current building and setup, the sawmill is about 15 years old. It is in an enclosed building, with everything closed off during the winter. “It’s proba- bly one of the cleanest sawmills in the state,” Doug figures.
Skidmore Lumber used to have a top saw but removed it and replaced it with a L-M Equipment LS-2000 log splitting system. “It’s a far better way to go than a top saw,” Howard believes, citing safer sharpening. Outside the mill, a Mellott LMR 48 in. debarker preps logs for transport by Deere wheel loader to the infeed deck.
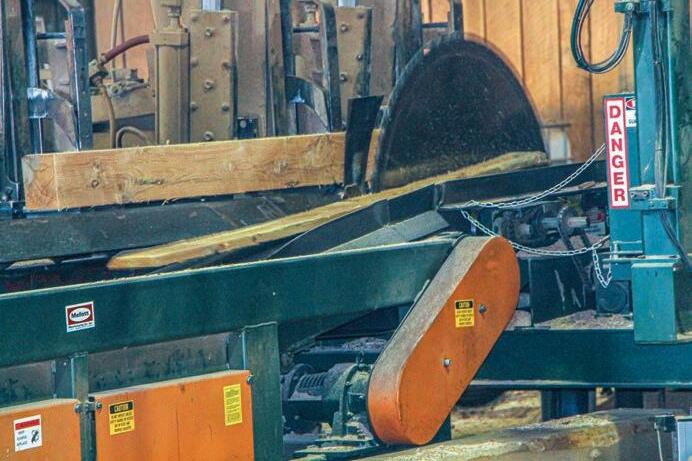
Inside, the mill’s Cleereman 38 linear positioning carriage processes each log with a circle saw. Pieces flow downstream to an edger from American Built Machinery out of West Plains, Mo. “This is edger number one,” Howard says, meaning serial number 1, the first one built by American Built. The Skidmores had a hand in helping design it to their specifications, just as they make adjustments to any machine in their mill. “We tweak everything, change this and that, to get it the way we want it,” Doug says. That applies to the carriage, the edger and log turners, which were also by American Built.
The Skidmore company logging crew sends most of its logs here, besides stave wood. The mill also takes in logs from other area loggers to complete its supply needs.
“We run about three truck loads of lumber a day on four 10-hour days,” Doug says. “We cut about 12 loads of lumber a week, and we save Fridays for maintenance.”
Markets
Skidmore Lumber processes rough green material for grade hardwood flooring, railroad ties and blocking, the latter of which goes to customers in Chicago and Texas. Despite having customers so far away, Skidmore avoids long distance freight; once upon a time, they did haul through contractors, but that changed after 9-11. “When the towers fell, trucking went crazy,” Doug recalls of the aftermath of that dark September day more than 21 years ago. “We lost a ton of money because we had contracts on lumber in Chicago and freight went from $424 to $1,250 a load to get it up there. So after that, when things leveled out, we decided no more.” Since then, they leave it to out-of-state customers to pay freight and handle delivery.
White and red oak are the major species, though the Skidmore Lumber logging crew goes into river bottoms to cut sycamore, soft maple and cottonwood for the company mill. The brothers sell walnut and some veneer logs elsewhere, and a lot of the white oak to
McGinnis Wood Products, a stave mill in Cuba, Mo.
The hardwood market right now could be better, the brothers agree—a LOT better. But there are bright spots. “The red oak market is dropping like a rock,” Doug laments. “The white oak market is dropping in the lumber but not near as much as the red oak. The stave market is fabulous and white oak veneer market is good.”
Logging
The Skidmore family started out in logging before they went into sawmilling, but they stepped away from logging for a while and focused exclusively on sawmills for a number of years. “We got plum out of logging,” Doug says.
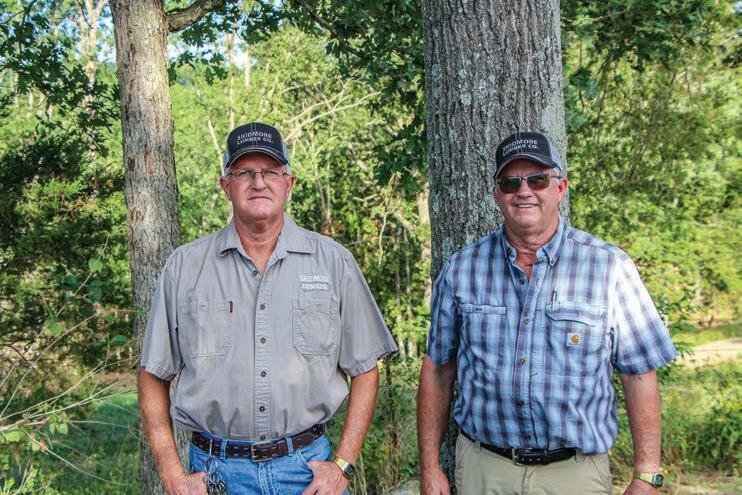
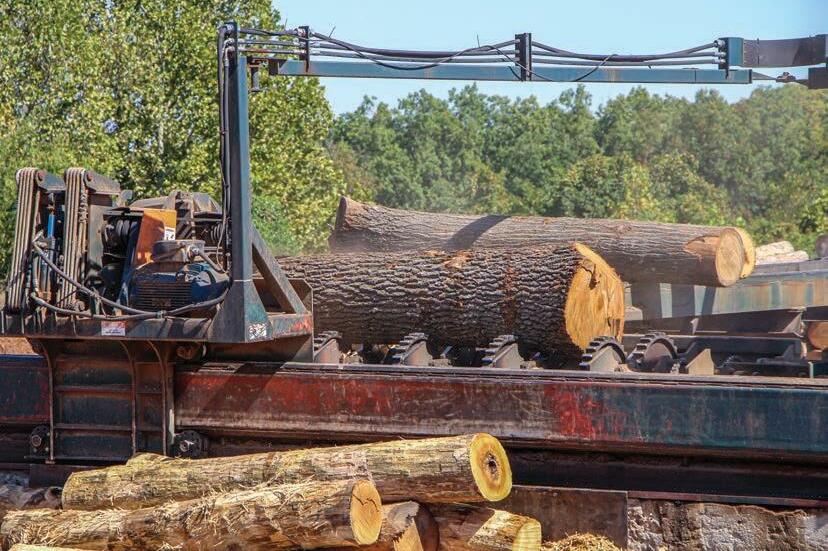
“We wanted to know how to expand our sawmill business without needing to buy more logs,” the younger Skidmore explains. “The answer to that question was to get back into logging.”
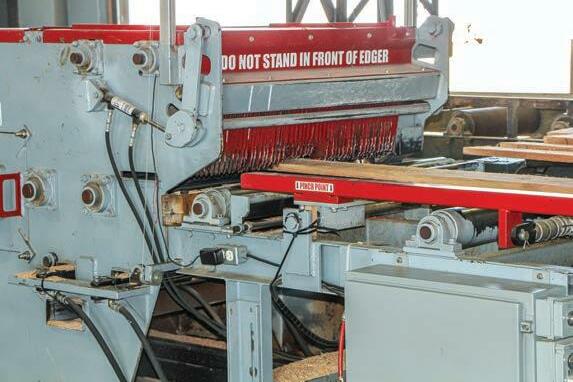
If they were going to log again, they determined they were going to do it as safely as possible, and that meant modern mechanization, something that still isn’t all that common in the woods in their area of Missouri. “We are not against the idea of cutting trees the old fashioned way,” Howard stresses. “That just isn’t what we wanted to do. Around here it is still mostly a man on the ground felling with a chain saw; that is still very common here, the most common by far. There are getting to be more machines in the woods though; 10 years ago there weren’t very many.”
In lieu of chain saws, the Skidmore crew fells with a Timber Pro TL745D tracked feller-buncher with a Quadco 2900 intermittent sawhead. A pair of John Deere 748L-II rubber tired skidders pull logs to the landing, where a Barko 595B knuckleboom loader paired with CSI pull-through delimber and ground saw sorts and merchandizes. Company log trucks, Western Stars and Internationals, also have Rotobec and Barko self-loaders mounted on the back and pull pup trailers.
Notably, a third skidder, this one a Tigercat 610E, is mounted on a set of tracks from G&R Manufactured Solutions, instead of riding on rubber tires. The brothers saw a video of these tracks online and got in touch with G&R sales manager Robert Reeves. The tracks have enabled the logging crew to pull wood out in both wet and steep terrain where tires would bog down or lose traction.
“They have so much flotation,” Doug says. “You don’t realize how low the ground pressure is because you have eight feet tracks that are two feet wide to spread all that weight out.” The G7R tracks have kept the crew working when conditions would likely have otherwise halted production, especially since many of the hardwood tracts this crew tackles for the mill are in difficult to access areas. In fact, Doug estimates that those tracks on that skidder have probably pulled about 75% of the wood for the sawmill for the last two years.
Skidmore’s operations aim to do more than just profit from the woods; they strive to act as responsible stewards of timberland. For instance, Doug points out, they take pains with skid steer and dozer to build logging roads that are clean and passable. “We focus on land management as well as logging,” he says.
The family is also active in the industry. Doug is a former board member of Missouri Forest Products Assn. and a current board member of the Missouri Wood Industry Trust, through which Skidmore Lumber obtains workers’ comp insurance.