
5 minute read
ADVANCED PNEUMATIC CONTROL
By Francois Tremblay and Alexandre Girard
In the early days of timber harvesting, log jams were a common site as felled trees floated downriver on the way to the sawmill. In today’s modern sawmills, however, log jams equate to equipment downtime, lost productivity, reduced profits and even potential safety risks. For one Canadian lumber company, upgrading the pneumatics on its
Primary Line
In the typical primary cutting process, debarked logs ranging from 10 to 16 ft. long are fed continuously on a narrow chain conveyor past two cutting heads to square off the sides. As each log goes down the line, a total of nine overhead press roll arms with guidewheels pivot down automatically in sequence on top of the log, keeping it positioned on the chain as it passes through the machine. As the toba winters are notoriously cold, so the mill must work with hard-to-handle frozen and slippery logs. In addition, log shapes can be curved or crooked, so the movement follows a non-linear path, making it harder to control. Finally, the force of the press rolls dropping on the logs as they pass underneath must be firm but not too strong, as too much pressure will kick the logs off the chain. log moves through, the press roll arms automatically retract in sequence to get ready for the next log.
Hydraulic press roll actuation is fast and powerful but can be very stiff and unforgiving, as hydraulic oil is not compressible. Hydraulic press rolls can also apply too much force, kicking the log off the conveyor chain. Consequently, the inelastic qualities of a hydraulic actuator combined with variations in the log’s diameter or shape could cause a jam, requiring a shutdown to remove the log manually and get the system back online.
Sawquip sawline vertical press roll actuators helped make log jams a thing of the past while increasing performance, lowering maintenance and saving on air consumption.
Headquartered in Manitoba, Spruce Products Ltd. makes premium lumber and wood products for the construction and integrated wood products industries. The company has supplied products for Canadian and international markets since 1942.
As part of its success, Spruce Products believes in using the latest technology available to use every aspect of a log in its product lines. That’s why the company decided to upgrade its pneumatic motion control with advanced components and technology from Emerson.
In many sawmills, these press arms are typically actuated using hydraulic cylinders, pneumatic cylinders or a combination of both mounted back-to-back, where the hydraulic cylinder provides the positioning, and the pneumatic cylinder provides cushioning (a very cost-prohibitive and maintenance-heavy setup).
Press Roll Control
The pivoting press arms are meant to keep logs from shifting on the chain during the cutting process. However, several issues can affect productivity. First, Mani-
Pneumatic actuation is a simple, inexpensive and very efficient solution for press roll control. However, traditional pneumatic actuators typically could only fully extend or fully retract, with stroke positioning dependent on the air pressure on either side of the piston. A full stroke extension and retraction requires higher air flow. The accuracy of the pneumatic positioning can also be affected by several factors, such as air temperature, amount of air pressure and the load on the actuator, which will change depending on the position of the press roll.
Advanced System
In this case, Spruce Products was using an existing pneumatic system on a Sawquip unit, which handles logs with diameters under 14 in. About 80% of Spruce Products’ lumber manufacturing takes place on the Sawquip line.
Seeking to improve efficiency and reduce downtime, Spruce Products brought in Francois Tremblay, an expert in sawmill automation, who partnered with Emerson to upgrade the pneumatics by adding highperformance proportional valves, pneumatic-specific control algorithms and a fieldbus-compatible manifold.
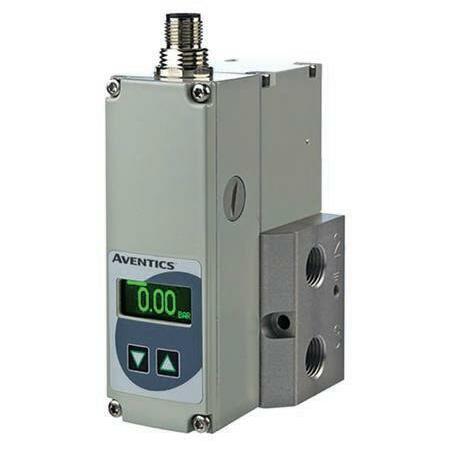
Working with the machine’s existing NFPA pneumatic cylinders, PLC and scanning laser, Tremblay recommended Emerson’s AVENTICS Sentronic proportional pneumatic control valve, combined with an AVENTICS G3 electronic fieldbus manifold system.
The AVENTICS Sentronic proportional valve is a 3-way, direct-operated digital control valve. With fast response times and high sensitivity, it was an ideal solution for this application, which required exact and responsive pressure control based on feedback for position and force. Using motion control algorithms specific to pneumatic positioning, valve control loop parameters are easily configured and optimized for specific customer requirements through AVENTICS Data Acquisition Software (DaS) and a PC connection.
For connectivity and control, the AVENTICS G3 electronic fieldbus valve system replaces conventional hardwired solutions. The platform integrates communication interfaces to the pneumatic valve system with input/output (I/O) capabilities. It provides easy access for connections and is simple to assemble, install, commission and maintain. Its functionality allows PLCs to turn valves on and off more efficiently and channel I/O data from sensors such as the scanning laser, other relays, individual valves and other I/O devices via various industrial networks. In addition, the G3 valve manifold contains a graphical display used for configuration, commissioning and diagnostics.

Although the pneumatics upgrade added many sophisticated capabilities, switching from traditional control to the new system was straightforward and quick. The changeover was accomplished during coffee breaks and at lunchtime, and the “plumbing” setup only took a few minutes per cylinder.
Improvements
By updating the press rolls with advanced pneumatic motion control, the process softened the high-velocity impact of the pivoting arms by using only the amount of pressure needed to hold the logs in place on the chain vs. the constant 100 psi required with the old system. This translated to a significant reduction in air consumption.
As a log approaches the cutting area, the scanning laser sends an input signal to the G3. Based on that input, the system calculates the distance between the press roll arm and the stroke of the actuator. Next, the G3 sends a signal to the valve, which converts the electric signal to the pneumatic pressure required to move the actuator piston as the press roll holds the log in place on the chain.
Regardless of the log shape or velocity, the saw line can now use feedback to preposition the press rolls at the right height and subsequently apply the right downward force. As a result, the pressure exerted on the logs is more accurate, eliminating the frequent jams due to the press rolls dropping too soon or too late. If a press roll drops too low, it will gently bounce to its correct position once the log hits it, thanks to the system’s feedback and proportional pressure on the actuator.
In addition, consider the weather extremes at the Spruce Products facility, from frigid winters to hot and humid summers. Feedback to the PLC enables the variables that can influence air compressibility in the pneumatic system. Responding to signals from the PLC, combined with pneumatic-specific algorithms developed by Emerson, the Sentronic valve can automatically provide the correct pressure for each press roll and log.
Benefits
Within the cylinder, the variable positioning capability alleviates the piston from being fully extended/fully retracted. As a result, the pneumatic system uses significantly less compressed air, reducing compressor operating time. In addition, reducing the stroke length minimizes the number of times the piston makes fullpressure contact with the head of the cylinder. This prolongs the life of the cushion and the U-Cup seal on the cylinder and lowers the maintenance and replacement requirements.
As an additional benefit, lights on the G3 indicate if the device is working correctly during operation. It can also provide historical data that Spruce Products technicians can use to refine system efficiency and further reduce compressed air usage.
Thanks to the recent development of high-performance pneumatic proportional control valves and manifolds supported by motion control algorithms specific to pneumatic positioning, PCI and Emerson overcame the challenges of controlling Spruce Products’ pneumatic actuators. Their approach to the saw line makes press roll operation more intelligent and more responsive for handling logs, saving on air consumption and maintenance while improving uptime. T P
Francois Tremblay is a technical expert in the sawmill industry and Alexandre Girard is a technical specialist for pneumatics and motion control at Emerson (www.emerson.com).