
10 minute read
TEAL-JONES
UPWARD TRENDING
By Jessica Johnson

Antlers, Oklahoma wasn’t known for large-scale sawmilling—until Teal-Jones came to town.
ANTLERS, Okla. T hroughout the years the farthest west southern yellow pine mill in the country has had three owners, and Mill Manager Dan Anderson has been there through it all. So, when The Teal-Jones Group came down in 2014 and purchased the relatively unknown entity in Oklahoma, folks were skeptical; but the Jones family quickly proved they were there for the right reasons. More recently Teal-Jones has expanded its SYP footprint with the acquisition of two mills in Virginia, but Antlers was their first.
“It has been nothing but positive for this place,” Anderson says. “They want to employ people and it’s been a good company to work for. Owners Tom and Dick Jones care about each individual they employ. I think as a whole everybody feels that way when they work for Teal-Jones.”
Having a caring ownership meant Anderson saw his staff step up a little bit more, saying his management group in Oklahoma is a very tight family-like group, and it matched culturally with the corporate operations. It greatly helped morale when the Jones family began investing in Antlers and really putting faith in the mill. “There’s more to come,” Anderson adds of the already lengthy completed project list. “It’s the
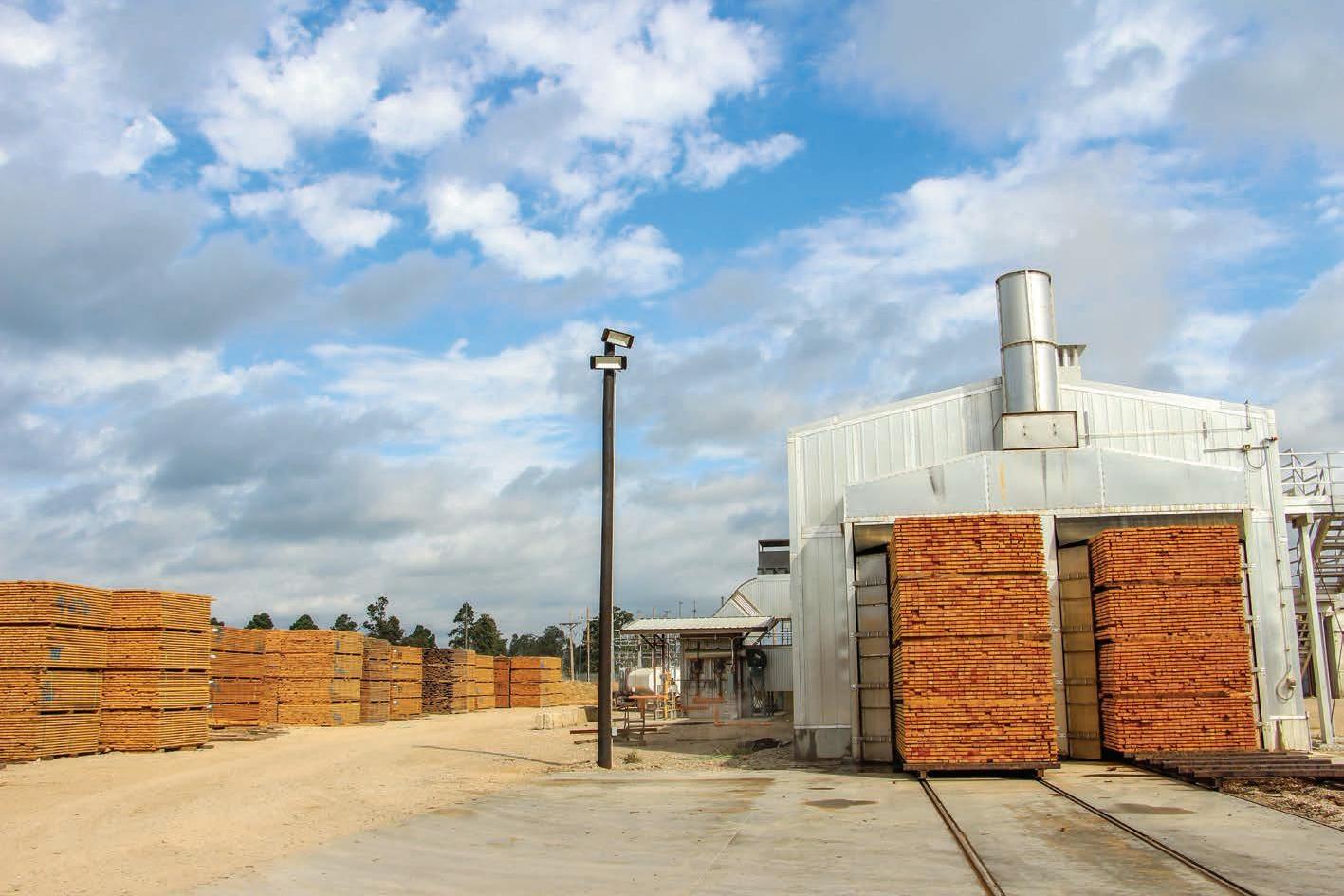
O ne of the latest projects in Antlers, a new American W ood Dryers continuous dry k iln, featuring a single-pass design that uses internal dampers and baffl es to control heat fl ow as lumber passes from one section to another
tip of the iceberg with us and them. They have really big dreams and everyone here does as well.” PROJECTS
Prior to being acquired by Teal-Jones, the Antlers sawmill operated modestly on a single shift basis, and scaling the operations to the next level proved challenging given the site’s mismatched and aged equipment. After getting the lay of the land, Teal-Jones identified some key areas to target with capital investment and began laying out a road map to get to that next level. Anderson calls 2019 the big project year. First, the vintage planer machine was upgraded to a refurbished Stetson-Ross. Anderson calls 2019 the big project year. First, the vintage planer machine was upgraded to a new used Stetson-Ross.
Next came the addition of an automated lumber grader from VAB—a much needed improvement, according to Anderson, saying, “It’s hard to train and keep lumber graders. Dick got everything lined up and made it happen with VAB for all the U.S. mills. Our mill was at a stage where we needed it.”
Anderson notes that the lumber grader project really demonstrated Dick and Tom’s commitment to Antlers. VAB, now owned by Timber Automation, was great to work with and the equipment is top notch— though it did come with a bit of a learning curve because of the type of SYP Antlers deals with in the extreme west end of the timber belt. The knot structure is a little bit different than pine in other parts of the South, and while some work had to be done, Anderson says the issues were resolved quickly and the mill is happier than ever to have it.
While the lumber grader was a game changer, the installation of a new continuous dry kiln, in addition to the two conventional kilns a year earlier, from American Wood Dryers (AWD) took Antlers to another level. The new kiln is gas fired, and Anderson says that was the single greatest point of pain in the project—bringing a gas line to the 200-acre mill site.
The single-pass system
A sling sorter handles Teal-Jones Antlers’ dimensional lumber just fine. Mill Manager Dan Anderson, right, is a young gun, but his love for the facility is palpable.

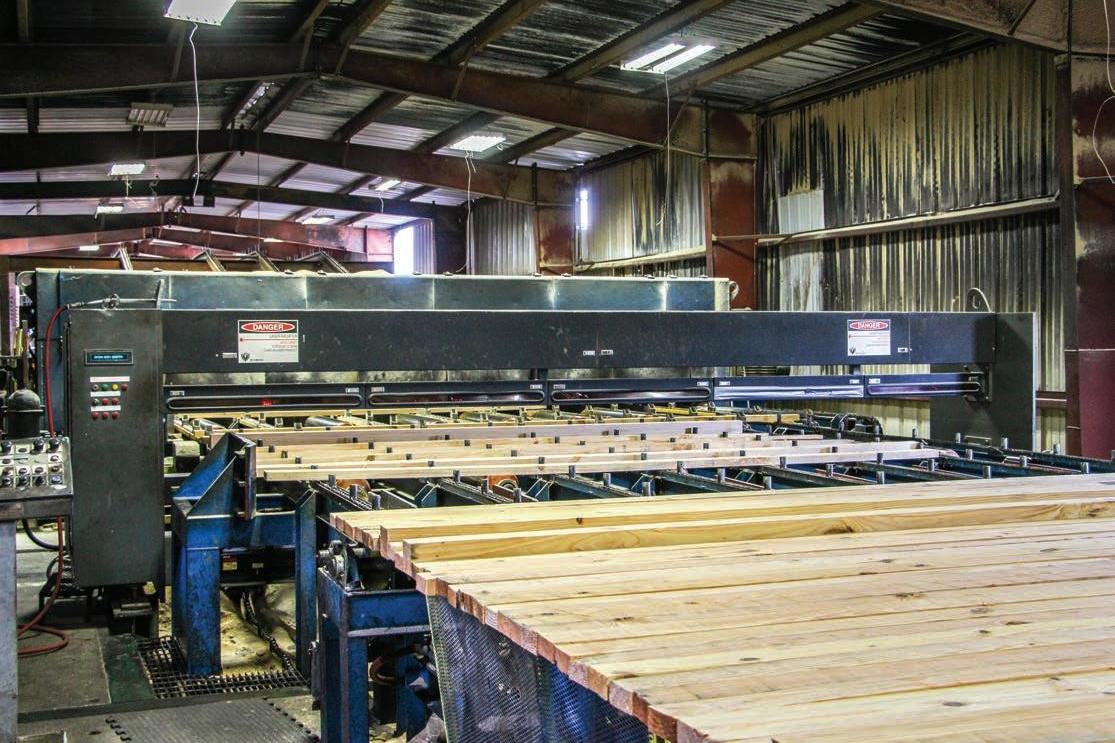




Maintenance staff works between shifts and on Saturdays and Sundays for preventive items.

that the AWD design uses takes hot gas from the main heating section and feeds it into the preheat section, so it’s already heating continuously as the lumber pack comes into the main heating section, then cooling and equalizing as it moves into the cooling section.
The preheating process also reduces dripping because there’s not as much on a condensation effect on the preheated wood entering the main heating chamber. The single-pass design uses internal dampers and baffles to control heat flow as lumber passes from one section to another. Hydraulic pushers below the kiln cart move lumber from the preheat section to main heat to the cooling-equalizing section determined by the AWD control system.
Drying capacity was the single greatest production bottleneck for Antlers, so by expanding 110MMBF through that kiln was huge, bringing overall capacity to 200MMBF of dimensional lumber annually. Apart from 2x4s and 2x6s the mill cuts a variety of products, including timbers, decking and 1 in. Though Anderson admits their product mix keeps capacity at a level that isn’t as high as it would be if the mill was only concentrating on dimensional lumber, the company takes pride in the specialty mix it produces at the current scale.
In addition to the new kiln, the mill installed a new RTS stacker with Automated Controls Solutions controls in late

A Samuel strapper produces packs of dimensional SYP destined primarily for treaters.


Thanks to small changes and big investments, capacity has soared to 200MMBF.
2019 to effectively kill any lingering delays in the dry end. “Now we have to go back to the sawmill and take the next step to move forward there,” he says with purpose.
MILL FLOW
With all the recent investment, Fiber Manager, Wesley Peters, has seen the demands of the mill skyrocket over the last year. The current log diet is a mix of gatewood and purchased stumpage in a radius of about 70 miles into Arkansas and Texas. “I’ve heard this place categorized as a coastal mill. If you go one way there’s no timber,” Anderson explains of the procurement radius, which isn’t as circular as SYP counterparts.
Roughly 60-80 log trucks a day pass through the scales, and are unloaded using John Deere machines, one knuckleboom and two wheel loaders including two brand new 824Ks purchased in October 2019. The mill keeps about seven to 10 days worth of storage outside, with no wet deck. Right now, the setup suits production just fine, though Anderson knows if volumes increase much more a wet deck will be next on the list.
The merchandizer is a three saw system, leading into a Nicholson A5 debarker, MDI metal detector ahead of the primary breakdown. Anderson says the CanCar twin bandmill with canter heads is fairly typical, but works well enough despite its age. A
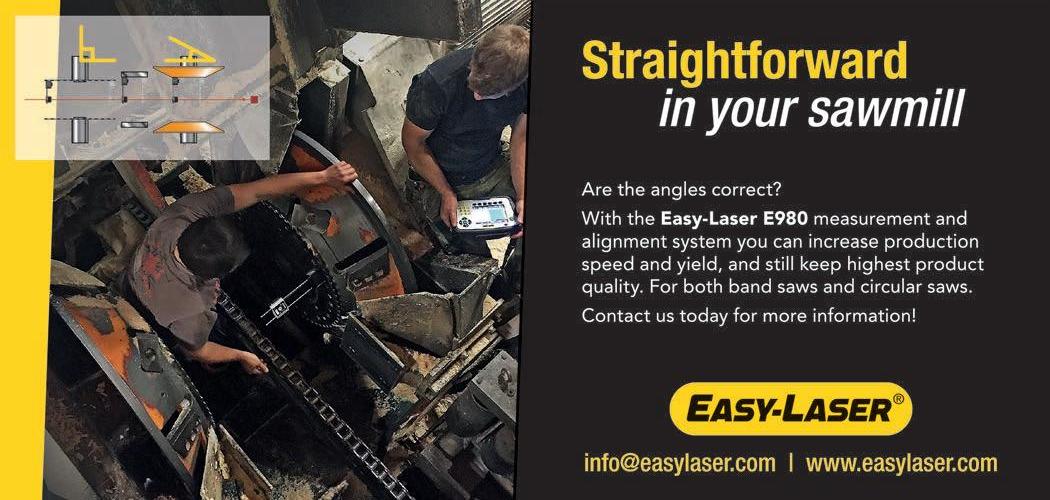
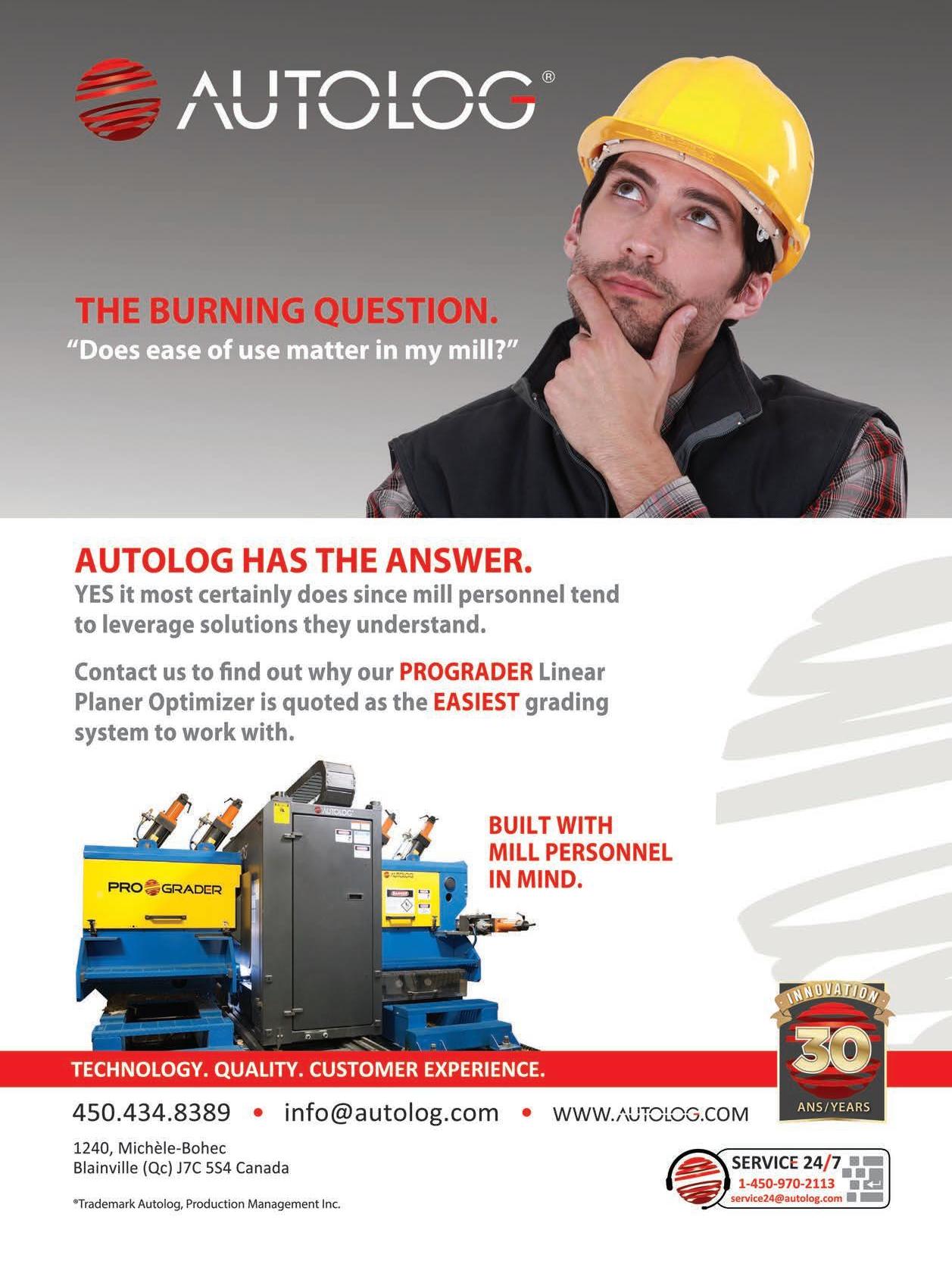

modified fixed saw Valley Machine edger follows as the gang.
Anderson says the mill is somewhat limited by the primary breakdown, and additionally he would like to see a Chip-N-Saw line at Antlers because of the timber basket. Right now the mill’s maximum log diameter is 24 in. with a 6 in. top, but the sweet spot is between 12 and 14 in. “We are limited by our gang,” he details. “It can only handle a 6 in. center cant from the primary breakdown.” Several upgrades are currently being planned out for the balance of 2020.
From the gang, boards travel to a Valley Machine board edger with four lineal positioning saws, and then an Advanced Sawmill Machinery (ASM) trimmer. The sorter line is pieced together with some older equipment. Before the kilns, lumber is stacked using a MoCo stacker.
Throughout the mill USNR Perceptron handles most optimization, with the exception of Baxley optimization on the ASM trimmer.
Antlers operates two Hurst 600 HP hybrid boilers, exclusively burning green sawdust to help them stay cleaner longer. The boilers have been the primary power source for drying for the life of the facility— until the new continuous dry kiln was installed. With the new kiln, Antlers has five kilns in all: three from AWD, including two 68 ft. steam batch kilns, and two Wellons kilns.
From drying, lumber hits an ASM tilt hoist ahead


of the Stetson-Ross planer machine. Once planed, lumber is graded using the VAB autograder, passes another ASM trimmer, USNR sorter and the RTS stacker before being stored both under roof and in the yard for shipment. A Taylor lift fleet handles lumber, with some Hyundai and Hyster machines.
MAINTENANCE
Antlers’ maintenance staff is homegrown with limited outside sawmill experience. “Being the farthest west mill, there’s not a lot of sawmillers that live in Antlers. We try to pull people in when we can but for the most part these are local people and this is the only mill they’ve worked at. We really have a good group of people here that care about the mill,” Anderson says of the dedicated team.
Led by Maintenance Manager Thomas Rosenthal and maintenance planner Tyson Thurman, preventative maintenance is handled on Saturdays and Sundays, with the hour and half window between shifts during the week

used to take care of smaller items. Weekends take maintenance priority, Anderson says, and if for some reason a part isn’t on the shelf there’s no telling who might be chasing it. “Everyone pitches in their own time to make sure the mill has what it needs to keep running. There’s always someone working on something.”
Head saw filer Mike McKinney got his start at the mill running the merchandizer before moving to the filing room. Four years ago the opportunity came up, and since he was always interested in filing, he made the switch. Now, Anderson says he’s the go-to guy, aided by a handful of assistants using an Armstrong leveler and grinder.
Like many, Anderson says labor can be a challenge, but Antlers has so far kept its head above water. He cites the investment not only that The Teal-Jones Group has made in the mill, but the investment of the people on the floor and the pride they have in seeing the mill succeed—safely. “Safety is always an improvement. You can always get better with safety,” Anderson believes.
PEOPLE POWER
The workforce in total is roughly 140 over two shifts, five days per week. The workforce’s economic impact on the small community is proportionately equal to a 12,000 employee company in Oklahoma City.
“Where we are located, there are not a lot of opportunities here. It’s the talk of the town—Go work at Teal and that’s where we want to be. These people have an opportunity to make a career at this and raise a family and stay right here at home,” the born and raised Antlers man says.
Anderson says the Antlers management team is a diverse group of people that all have the goal of making TealJones Antlers the best place to work.
“That’s what makes this place do good things, because of the people around the table.” He adds, “Everyone cares tremendously about the company, their job and the business.”
Anderson makes it clear, the mill once forgotten, or perhaps more aptly put discounted, by many is positioning itself to come roaring onto the scene thanks to the support of Teal-Jones. Volume-wise the mill is on track to increase production six fold.. That’s what Anderson says he’s most proud of: The direction the facility is going in since the transition to Teal-Jones ownership. TP
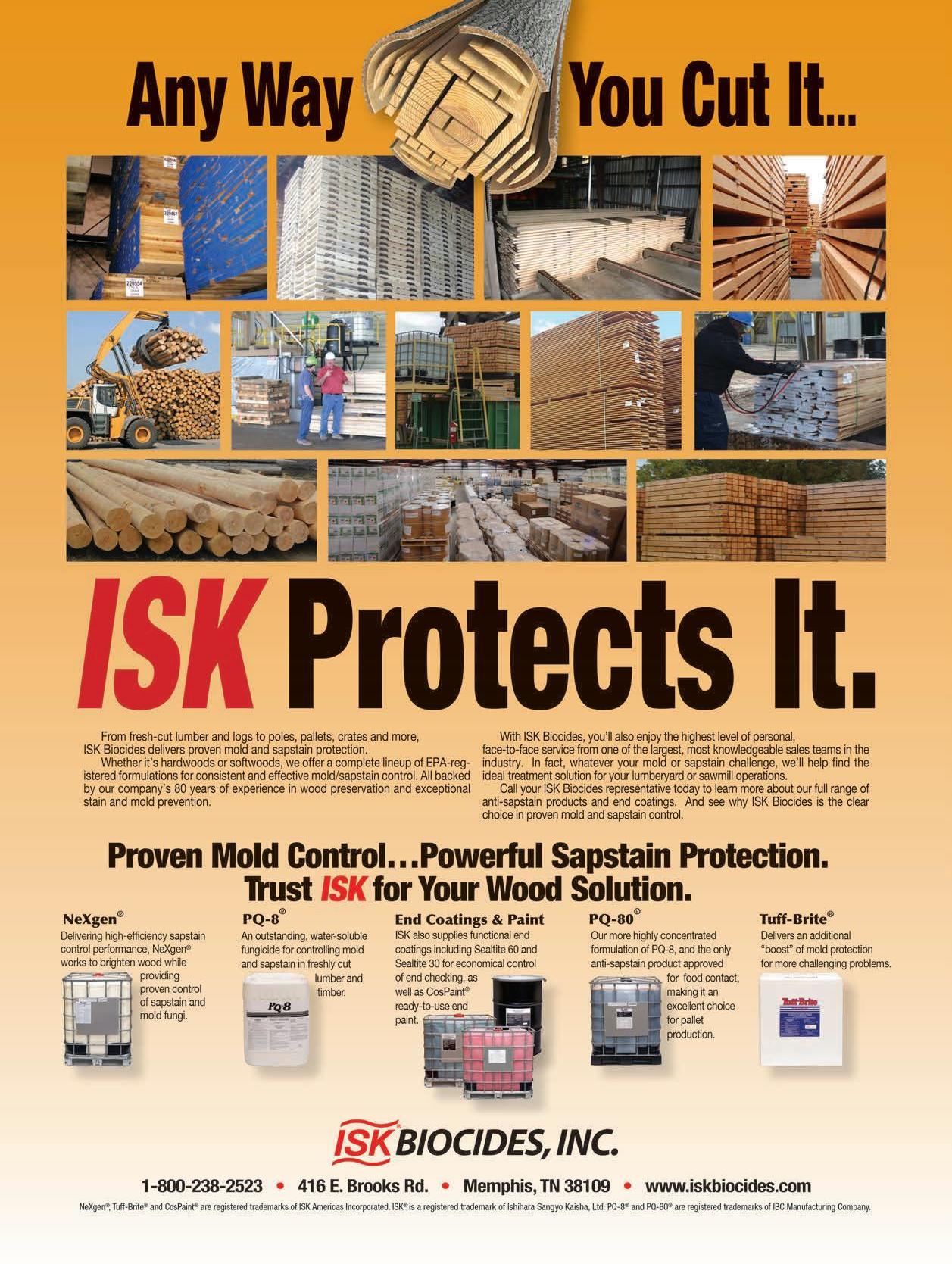

