
15 minute read
PLANER MILL BONANZA
EDITOR’S NOTE: The following companies supplied these editorial profiles and photos on their technologies in the planer mill, to complement their advertisements that can be found throughout this issue. AUTOLOG PLANERMILLS
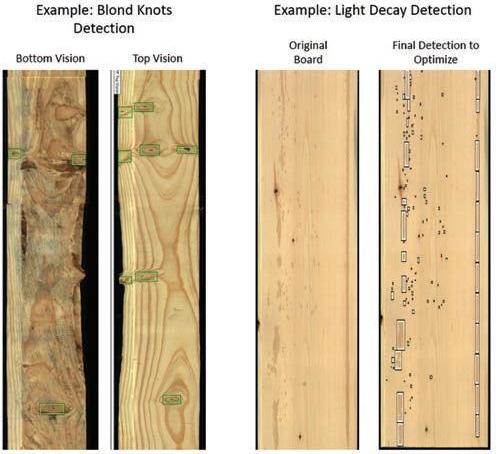
Autolog’s ProGrader is built with mill personnel in mind. Comact GradExpert: optimization and Artificial Intelligence
With more than 20 new optimizers recently installed in the U.S., Autolog’s ProGrader linear planer optimizer has been quoted by mill personnel as one of the easiest grading systems to work with.
What does easy to use mean exactly? It means you can quickly leverage the knowledge and the experience of your key graders. At many locations, graders with limited computer knowledge can learn and delve into the system in order to extract the most value out of every piece. Easy to use means that your resources will be autonomous.
Autolog’s ProGrader is a linear optimizer designed to fully automate the grading process of dressed lumber at the planer. Being positioned just after the planer, its group of sensors (geometric, vision and tracheid), which face each side of the board at 90 degrees, provides an unobstructed reading as well as stops any major planer mechanical production issue.
It is a reliable and fast system that can be installed closed coupled or not, processing all dimensions between 1x3 in. to 6x12 in., 6 ft. and up.
The 3D geometric sensors measure dimensions, skip, wane, holes and warp; the 2D vision sensors measure knots, rot, splits and shakes, bark, etc.; and the tracheid sensors measure slope of grain and detect knots and unsound wood.
The ProGrader LTS (Linear Tracking System) control module provides information on all data that is collected and how it is trending. It integrates the analysis of detailed and precise data on the tracking and synchronization of boards, keeps track of the board gap and synchronizes its speed with your electrical planer. It monitors and leverages information from all sensors, moisture reader and MSR to maximize the board value.
The ProGrader linear planer optimizer offers the best priceperformance ratio with less than one-year payback. Autolog’s automation solution can seamlessly integrate your selection of equipment from the tilt hoist to the stacker.
With Comact in its brand portfolio, BID Group is a North American leader of optimization products with vision. Over the last years, several members of our team have specialized in Artificial Intelligence (AI) after a R&D phase that allowed us to conclude that this was the future of wood grading.
AI is a computer science branch that enables the simulation of human intelligence based on specific instructions. Why will AI revolutionize wood grading? Because it allows the detection and interpretation of wood defects almost like the human eye.
However, this almost human detection has no value if it is not combined with a high-performance optimization software like the GradExpert original software platform. In fact, all defects identified by the AI must be processed by the optimization software that merges geometrical and visual data, applies defect analysis algorithms, and considers grading criteria as well as the client’s product priorities, to finally issue the best decision for grading and trimming.
The AI models used by the GradExpert were created in-house to ensure extremely high efficiency. Our AI internal experts with a team of wood processing specialists educated the basic model and each system installed. In other words, the Comact defect detection with AI models combined with the ultrapowerful optimization software is the equivalent of 25 Comact wood specialists in your machine 24/7.
The GradExpert with AI allows defect identification with pixel precision. Since the AI system is well educated, it can recognize the different shades of visual defects like rot and knots that may vary considerably according to the origin of the wood, the species and the severity of the defect. For instance, AI excels at identifying and dimensioning various shades of knots: blond, sound, scattered, black ring, decayed, star checked, hollow, etc. These few examples demonstrate how Comact’s AI platform will revolutionize the industry and establish new standards.
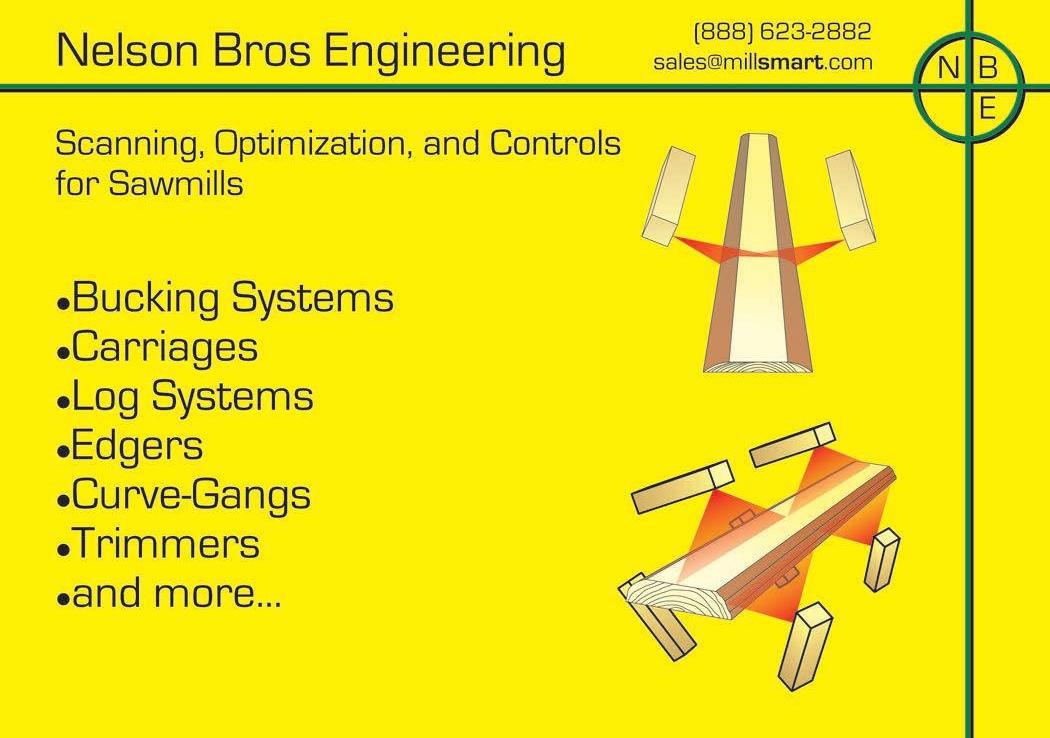
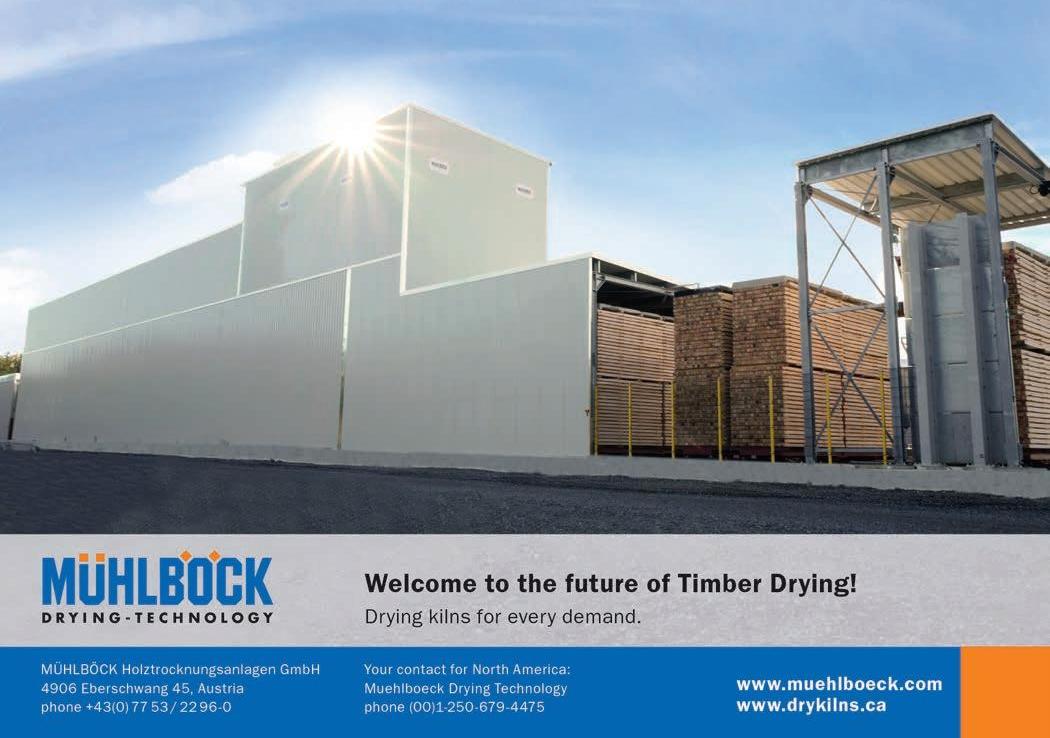
Con-Vey high speed continuous breakdown hoist
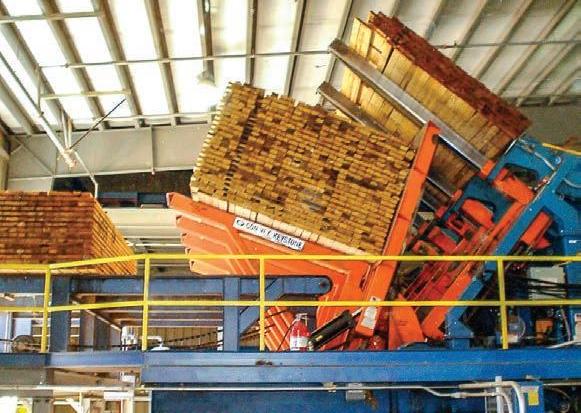
For more than 70 years Con-Vey has been producing high quality, high speed lumber handling equipment to increase capacity. Our innovative and cutting-edge company holds the original patent for the Continuous Breakdown Hoist for high speed feeding of lumber, and we’d love to provide you with the same innovative solutions and service.
We design each continuous breakdown hoist to fit the customer’s unique needs based on the unit specifications, speed requirements, and space available. Single or double units—with or without kiln sticks—can be provided based on needs and use. The continuous function of this equipment allows for feeding layers of lumber while the main hoist reloads with the next unit. The accumulator arms have load leveling capabilities. Options are also available for all package sizes, including 8 ft. wide crib loads.
Con-Vey offers a wide range of timber processing machinery—from tilt hoists to sawing and stacking. Come to Con-Vey for quality and dependable equipment and designs. LUCIDYNE TECHNOLOGIES
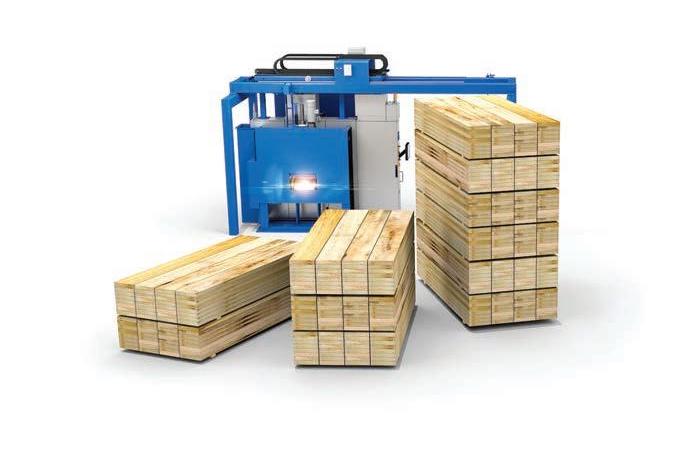
While the world carries the weight of this pandemic, Lucidyne is among those preparing for the inevitable bounce-back. During this difficult time, Lucidyne has not made any changes to its staffing, and remains prepared to support its customers throughout the crisis and beyond.
In February 2020, Lucidyne was granted the first and only patent in the world to use deep learning techniques to grade lumber. This technology, Perceptive Sight, is only available from Lucidyne, and is the software platform on all Lucidyne scanners.
Lucidyne continues to be the industry leader with the staff and the technology to deliver the results our customers have come to expect. Serving our customers since 1985, Lucidyne stands ready to continue the tradition as we move past this crisis and into the future together.
And the latest news from Lucidyne strengthens that position. This development expands our capabilities to use our AI technology in other areas of your mill, delivering unprecedented opportunities to maximize fiber and value recovery. MICROTEC
Microtec Goldeneye 900 multi-sensor transverse scanner
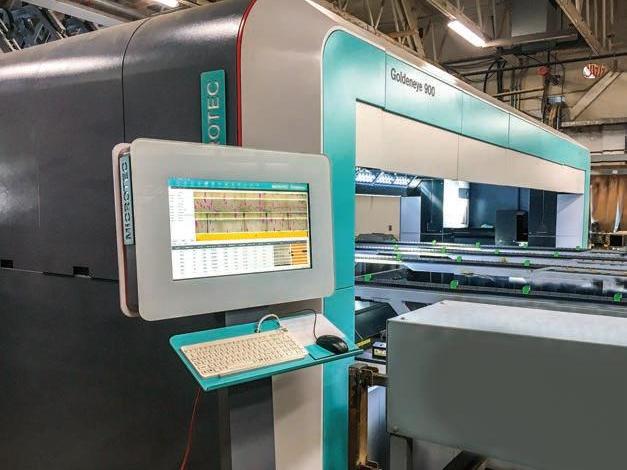
The Goldeneye 900 Multi-Sensor Quality Scanner in transverse transport is the ultimate showcase of Microtec’s technological innovation and leadership in scanning technologies. Using Microtec’s proprietary Crometic cameras, with the fastest and highest resolution available, the scanner is capable of seeing different wood defects that are important for your grade. Coupled with its integrated Deep Learning AI (Artificial Intelligence) module, advanced algorithms detect and localize all types of defects, including knots, cracks, discoloration, pitch pockets, wane, curvature and other dimensional defects.
Capable of imaging both rough green and planed dry surfaces, the scanner can be installed in both sawmills and planer mills, and be used for trimming, grading and sorting, as well as edging optimization. In addition to structural and visual fixed length product evaluation, re-edging/re-sawing, cut-in-two, and even finger jointing products can be simultaneously optimized to ensure maximum value for each board.
The Goldeneye 900 is a true four-sided scanner with a full

multi-channel view of each surface of the board. When fitted with the special occlusionless transport chain, no portion of the board is hidden, even on the bottom surface. Installation and startup is straightforward as the scanner fits in at standard chain height, with no elevation changes or height modifications.
Microtec, always at the forefront of innovation, includes in all recent quality scanners, whether lineal or transverse, the option of improved defect detection through Artificial Intelligence. The advanced AI module is currently providing real benefits to many clients all over the world, with six successfully installed transverse scanners in the last year and eight new orders placed since the Ligna show in May 2019. In fact, the new generation of Goldeneye 900 transverse quality scanners are running and creating value for customers in North and South America, Europe, Australia, as well as Russia. PICHÉ PLANERMILLS
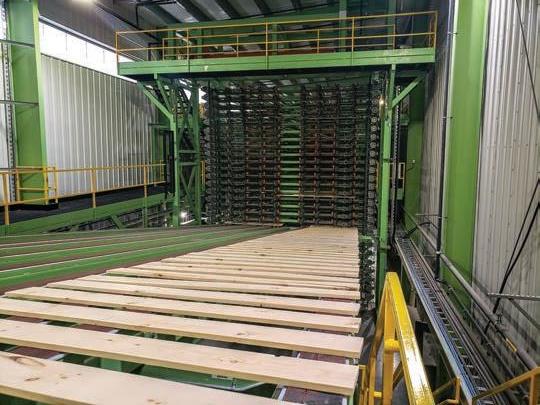
Samuel printing technologies for product identification
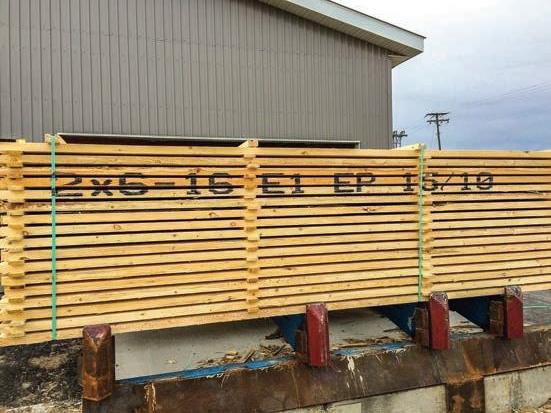
dreds of installations across North America we offer unparalleled industry experience.
Samuel Coding & Labeling Systems for wood products include ink jet grade mark systems, ink jet printers for marketing information, ink jet stencil machines for sawmills and planer mills, automatic board bar coding for retail sales, automatic package tag systems to print labels and staple them to finished packages, and product tracking by integrating printers and scanners for 2D bar codes. SIGNODE
Piché offers a range of technologies and solutions for the planer mill and lumber dry end.
When it comes to your planer mill operation, Piché can offer a multitude of innovative solutions to fit your needs— from the continuous tilt hoist and automated high speed planer infeeds, to automatic adjusting slow down belts, while paying attention to small details like a lug loader with urethane pinchers to prevent marking of your high grade lumber; from infinite adjusting fences and high speed, low maintenance lineshaft trimmers to bin sorters fully lined with UHMW on bins and bin floors, to tray sorters with integrated cut-in-two systems.
Piché also furnishes high speed package makers with automatic edge and layer even ending as well as dual inline strapping machines to enhance strapping time and generate perfect finished packs for your mill. We offer full mechanical and electrical installation packages and user friendly controls as well. SAMUEL
Samuel Coding and Labeling Div. is an industry leader in custom and off the shelf solutions for the wood products industry. With years of experience in the wood products industry, we are uniquely suited to provide you with solutions that are tailor made to suit your facilities. We provide a full system solution with design, fabrication, installation and ongoing support. With hun
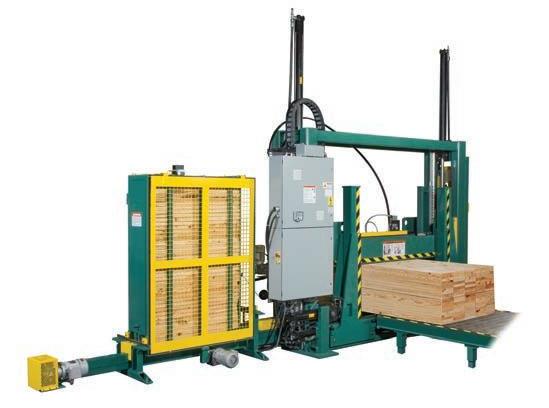
Signode BPX strapper delivers higher throughput and flexibility.
Signode’s BPX compression strapping system provides load stability and integrity throughout the transportation cycle. It incorporates independent side compression along with advanced consumable systems that work together to provide consistent load alignment and tension levels for unparalleled package performance. The BPX’s streamlined design with innovative, builtin features enables faster cycle times for higher throughput rates to maximize efficiency.
The BPX simplifies operation and maintenance to maximize uptime. It includes a highly intuitive, user-friendly HMI to
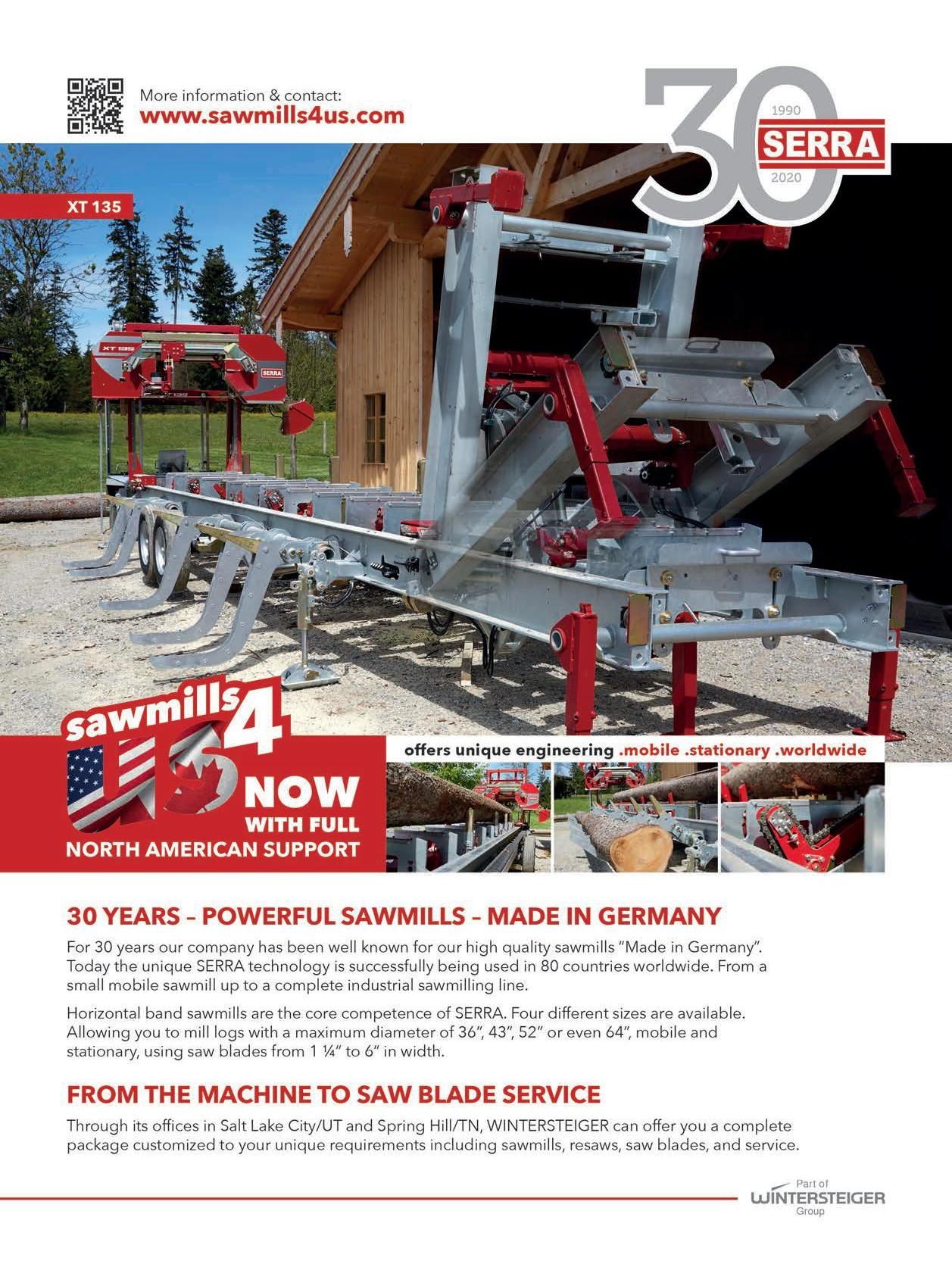
streamline operation. Machine pre-programming allows for a wide range of flexibility, including quarter-packs, half-packs and long loads, while limiting downtime due to production changes. Plus, the HMI provides quick and easy diagnosis of service-related issues.
When maintenance is required, the BPX features a unique modular design to simplify maintenance. Separate, lightweight strapping heads are easy to access and remove for maintenance. These low-maintenance, adjustment-free modules incorporate a simple design with few moving parts for minimal upkeep. When spare modules are kept on hand, maintenance downtime can be limited to a matter of minutes. Plus, the feed module is located off the platen, enabling it to be removed and serviced quickly.
Other productivity enhancing features include remote strap feeding and large capacity consumables to limit production interruptions. The BPX comes standard with a number of features, including an automated platen latch, multiple e-stops and more, that enhance operator safety and improve OSHA compliance.
The BPX compression strapping system delivers package performance and reliability in a simple to operate and easy to use machine. Its innovative features, overlapping functions and highefficiency design results in maximum load stability, while ensuring a lower total cost of ownership. STENNER
UK based Stenner Ltd. has a strong tradition in manufacturing heavy duty 36 in. radial arm resaws. The original model was the VHM36 and more than 7,000 have been sold worldwide with PLANERMILLS
STENNER ST100 resaw range
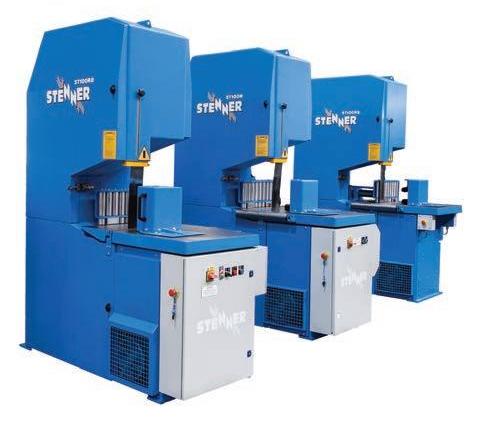
many of them still in operation today. The ST range is the latest generation and includes three different models.
The entry level ST100RB maintains the tradition of a heavy duty machine with cast iron pulleys driven by a 15kw main motor. The machine controls are relatively simple to use. Cast iron feed rollers and a robust multi roller fence ensure accurate, high quality cutting performance that is to be expected from a resaw in the Stenner stable.
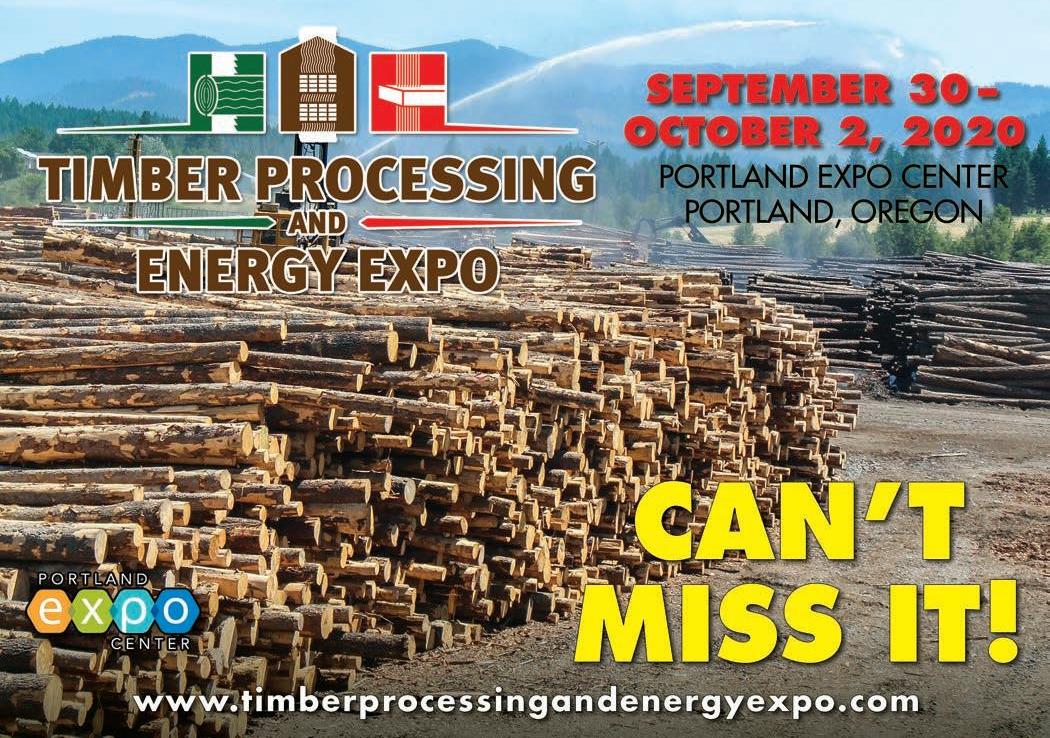

The ST100R is the main seller in the range with all of the features of the RB plus pneumatically operated in and out movement of the radial arm, PLC control of the main functions and a wide range of options to choose from.
Finally the ST100RS is the “top of the range” resaw with touch screen control of the main functions including the setting of the fence via electric motor activated by the pressing of a single pre-programmed button. An 18.5kw main motor is controlled via a frequency inverter giving the operator the option of controlling the pulley rotational speed so as to provide optimal performance on a wide range of timber species and a surface finish to match customer requirements.
Stenner resaws are marketed in North America by Akhurst Machinery. Director Graham Akhurst comments, “We have sold a number of the ST resaws all with excellent results. They are robust and are well equipped to satisfy the demands of the North American lumber producer.” TIMBER AUTOMATION (VAB)
Timber Automation’s VAB auto grader is an industry leader in ease of use, simplicity and rapid return on investment. Leveraging Artificial Intelligence and Machine Learning, our grading system gives you higher grades, more consistently, at a faster pace. Increasing premium grades, #2 and better and decreasing the amount of #3 and economy grades while also reducing trim loss leads to payback for most of our customers within six to 12 months. Plus, our grader doesn’t have a bad day, get tired or distracted. It consistently provides the maximum grade, every time. PLANERMILLS
Timber Automation VAB auto grader at Teal-Jones sawmill
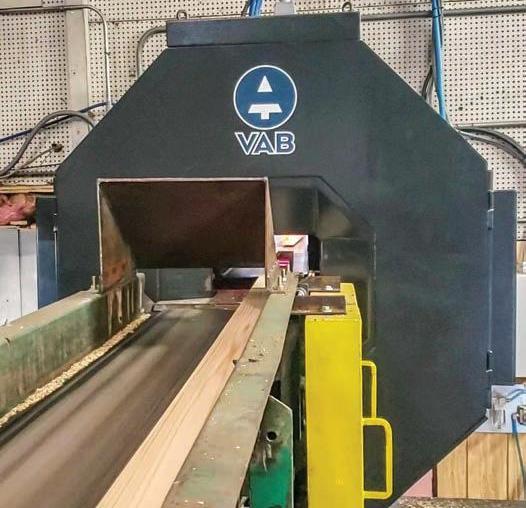
Simplified dashboards displayed prominently on the production floor and in the control room allow operators to quickly identify and correct quality concerns. An intuitive user interface enables user to quickly and easily change recipe parameters to ensure maximum value recovery. Run real-time simulations side-by-side with your current recipe to understand how
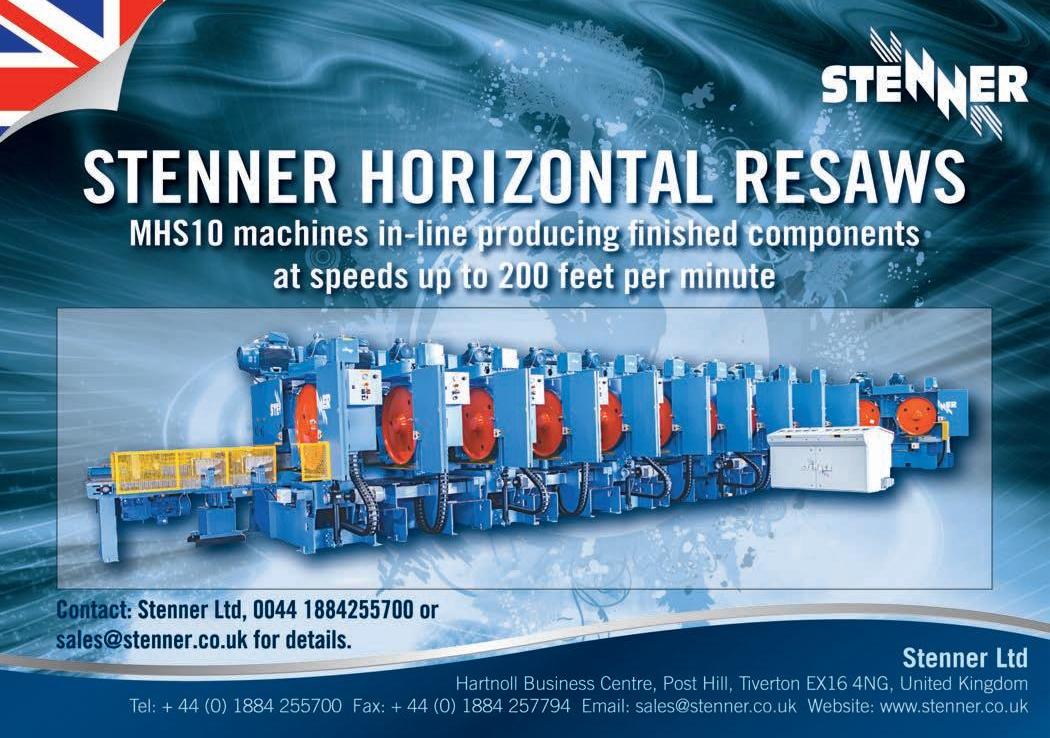
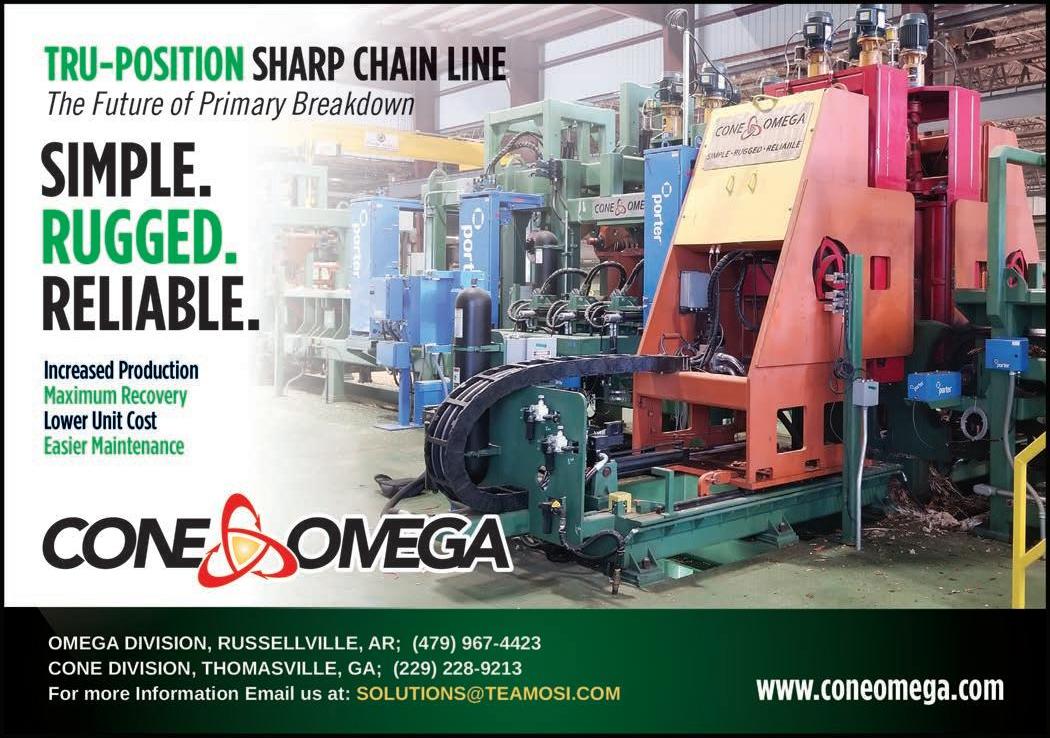
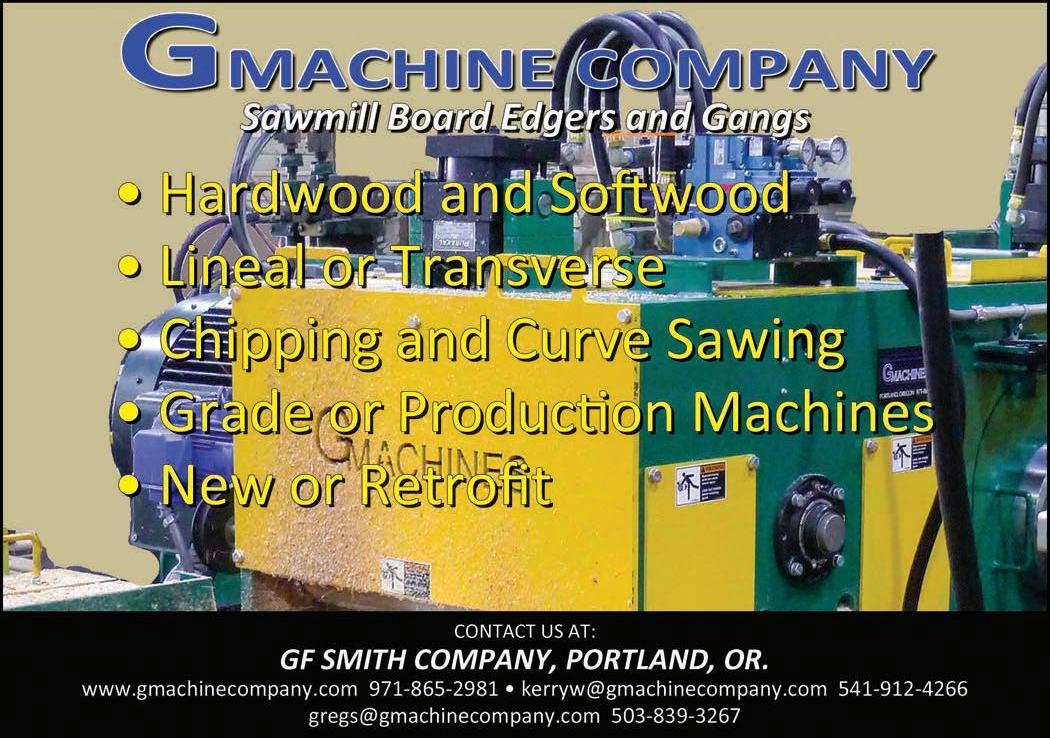
recipe changes could improve value. Our Air Board Tracker allows for contactless tracking and virtual numbering of lumber in the lugless section between the planer and the lug loader. No need for contact, speed limits, maintenance or ongoing, recurring consumable costs. Learn how one of our customers achieved an estimated $1.8 m per year return on investment through a 4% increase in premium grades, 12% increase in #2 or better, 4% increase in volume, 14% increase in production speed and decreases in labor costs. USNR PLANERMILLS
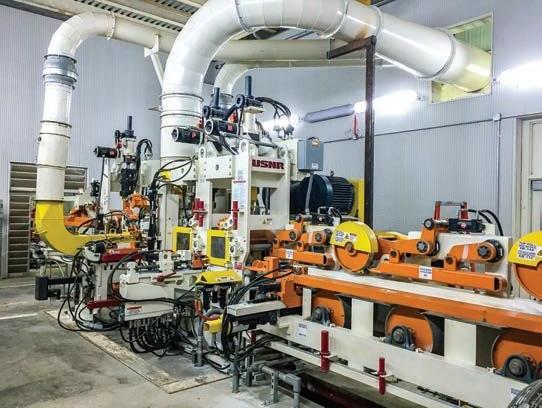
from the operator side, dramatically cutting maintenance downtime. The planer bedplates feature shim-less adjusters for independent multi-axis leveling alignment.
All-electric VFD drives with electronic speed-balancing make it easy to fine-tune your system for consistent results. It is equipped with positive locking head carriers for top, bottom and side heads to maintain accurate lumber dimensions, while the hydraulic-locking cutterheads facilitate rapid head changeout, preserving valuable production uptime. The removable cutterheads hold up to 42 knives for enhanced surface quality, providing a superior lumber finish.
Fast, solid and reliable, the 4200E planer features an all-electric design that’s built to last—and with all the latest features and functionality that any modern planer operation needs to carry it into the future. WEST COAST INDUSTRIAL SYSTEMS
USNR 4200E planer: larger cutterheads, more knives, higher production
USNR’s 4200E planer produces consistent results and accurately sized lumber with a smooth finish. The system has larger cutting heads, more knives, and operates at higher speeds than most planers in production today.
It offers all-electric, high-speed performance operating at speeds up to 4200 FPM (1300 m/min) designed for lumber 3 to 12 in. (76.2 to 304.8 mm) width, and 3 ⁄4 to 6 in. (19.1 to 152.4 mm) thickness, and down to 6 ft. (1.83 m) short lengths.
It’s available in right- and left-hand configurations with the ability to gap feed or ribbon feed. Ribbon-feeding allows the 4200E planer to achieve the same high-production rates as pull-through style planers but at more controlled speeds. This results in more accurately sized lumber with a smoother, snipefree finish.
Advanced PLC controls tightly coordinate the variable feed speeds between the infeed table, bridge and planer. This delivers a consistent ribbon-feed of lumber to the planer that enables the system to achieve high rates of production at more controlled feed speeds.
The 4200E series planer is built to last. The modular frame accommodates 6-, 8-, and 10-roll configurations and is constructed with 1.50 in. (38.1 mm) thick side plates mounted on a flange base for increased stability and additional strength.
It’s designed to make routine maintenance fast and efficient, minimizing downtime and maximizing production. For example: quick-change feed rolls, press rolls, and bedrolls are accessible
West Coast lumber material handling
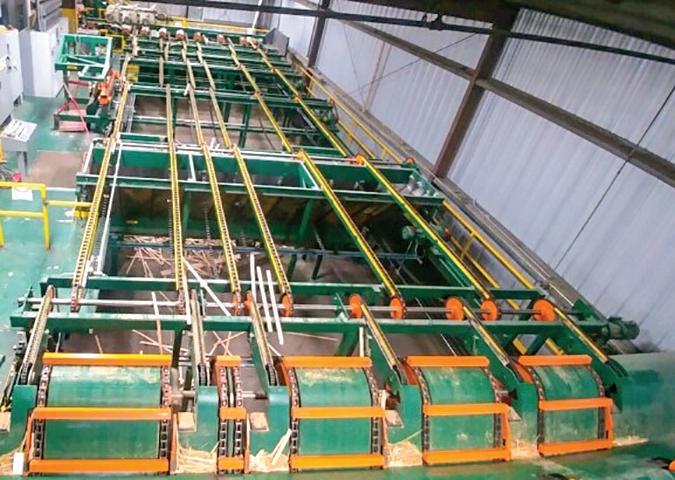
West Coast Industrial Systems is proud of the nationwide reputation we have built for quality systems and service since 1987. From infeed tilt hoists to finished packaging lines and the material handling between, our team custom-designs, manufactures and installs equipment for all planer mill lumber handling needs. We work closely with customers to identify everyday challenges and provide solutions quickly and efficiently.
WCIS products offered include but are not limited to tilt hoists, transfers, grading stations, unscramblers, feed tables, conveyors, sorter conversions, tray sorters, package handling equipment and paper wrap stations.
Our in house manufacturing facility can handle projects large and small—with a machine shop that boasts equipment from high speed CNC mills to a high capacity precision planer mill for providing high quality precision parts to our fabrication shop.
Our on-site, highly experienced teams oversee projects from start to finish, making sure your project flows smoothly, are on time and under budget. Our home support staff will also provide professional assistance to our field teams. Our goal is to provide what you need, when you need it.
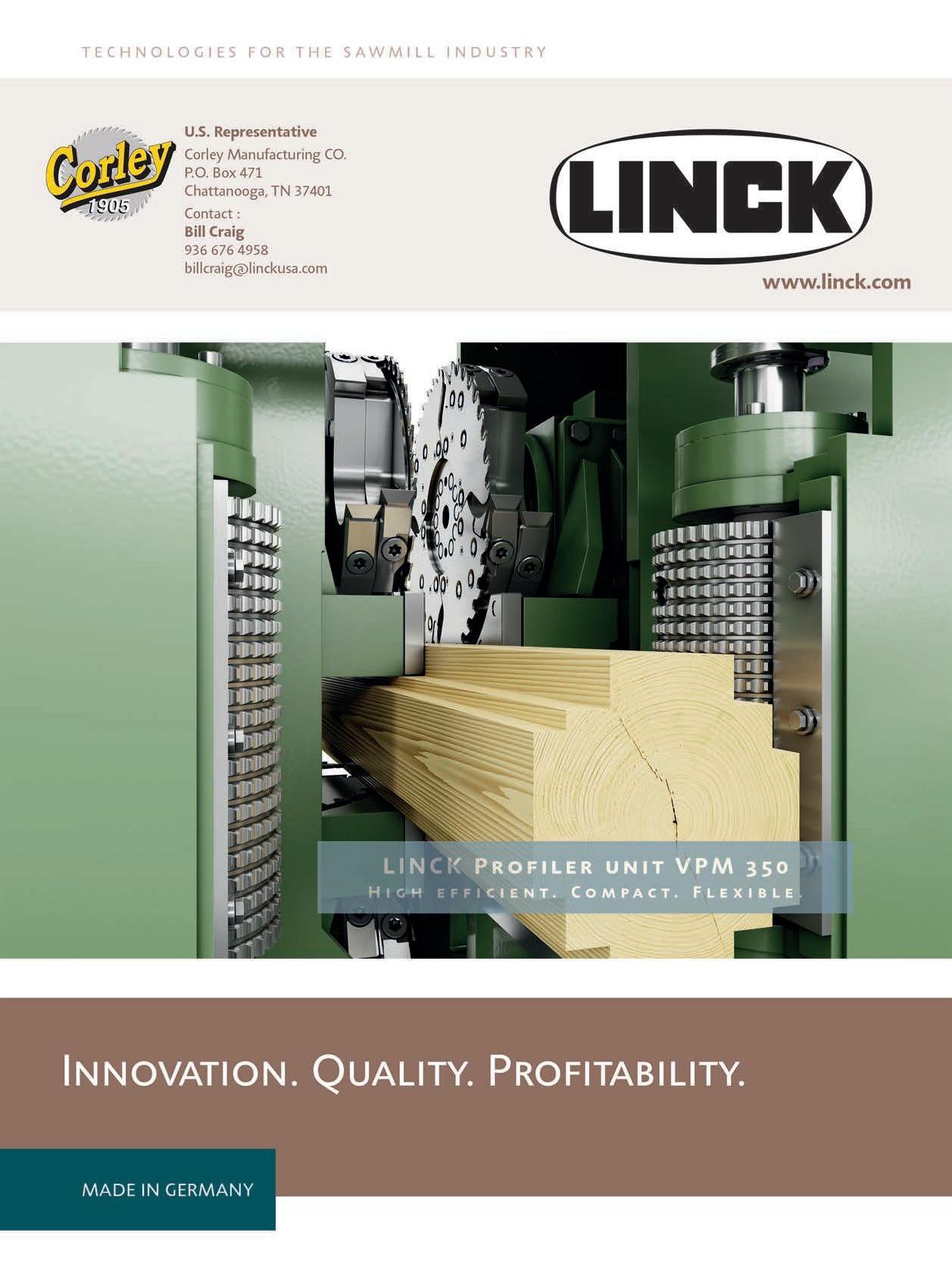