
32 minute read
DRY KILNS & ACCESSORIES
EDITOR’S NOTE: The following companies supplied these editorial profiles and images to complement their advertisements elsewhere in this issue. All statements and claims are attributable to the companies.
American Wood Dryers
ThermoVent by American Wood Dryers— manufacturer of single pass continuous track and package kilns—is a powered flat-plate air-to-air heat exchanger that harvests the heat energy in the hot, wet venting air (usually wasted energy) to preheat the entering cold, dry ambient air (by up to 70°F) to keep the air temperature inside the dry kiln very nearly constant.
The simple modular design enables easy installation that can be used on all types of kiln roofs such as peaked, sloped or flat. The ThermoVent is controlled by the wet bulb temperature (or EMC) just as your vents are now. Duct mounted powered intake and exhaust fans are re- American Wood Dryers ThermoVent heat exchanger versible and controlled by the kiln schedule.
Vent fan speed is controlled to accommodate different air densities (hot moist air is lighter than cold dry air, so the fans run at variable speeds).
Benefits include: l Air-to-air heat exchangers are more efficient than thermal fluid types and are simpler systems to operate without pumps and plumbing. l Shorter drying time; up to 15% less than without ThermoVents. l Much shorter heat-up time; half or less than without ThermoVents l Improved product uniformity. l Energy savings of up to 20%.
Recent installations have been showing a ROI even when there is the option of selling energy back to a utility as the lumber quality and energy savings are significant.
A.W. Stiles Contractors

At A. W. Stiles Contractors, we have done everything imaginable when it comes to hardwood and softwood dry kilns. From new greenfield construction to minor repairs, control upgrades and steam piping, we cover all the bases. With new custom kiln builds we keep our customers involved in the process to make sure they are getting exactly what they need and want out of their new kiln.
On the repair side we offer kiln reskins, roof replacements, steam piping, new custom heating coils, controls, competitive kiln part pricing, protective kiln coatings and scheduled kiln maintenance. A couple of the most requested kiln repairs are kiln reskins and roof replacements.
A kiln reskin consists of removing the existing wall sheeting and insulation, repairing any structural damage, then replacing with new wall sheeting and insulation. With older kilns there may be some damaged areas in existing wall sheeting from everyday use. These damaged areas can cause the insulation to basically act like a sponge with A.W. Stiles Contractors specializes in kiln modifications, including the moisture in the kiln. Once the insulation becomes water logged reskin and roof replacement. over time it will start to sink in the panels. This will cause your kiln efficiency to decrease. Over time it can add hours to drying a kiln charge.
We all know how important it is to be as efficient as possible in the business. Kiln roofs are not only a big part of kiln efficiency but also a huge safety concern. If a kiln roof has been leaking for a while there could be extensive damage to the kiln structure. This damage is not always visible from inside the kiln. This can be extremely dangerous if any employee has to access the roof of the kiln. If you have a few minor leaks or major roof issues, let us help. If not attended to properly a minor leak can turn in to a major one over a short period of time.
Our customers are like family and they do the most advertising for us because, let’s face it, we all know one another in the industry. Let us help you and your company with all your kiln drying process needs.
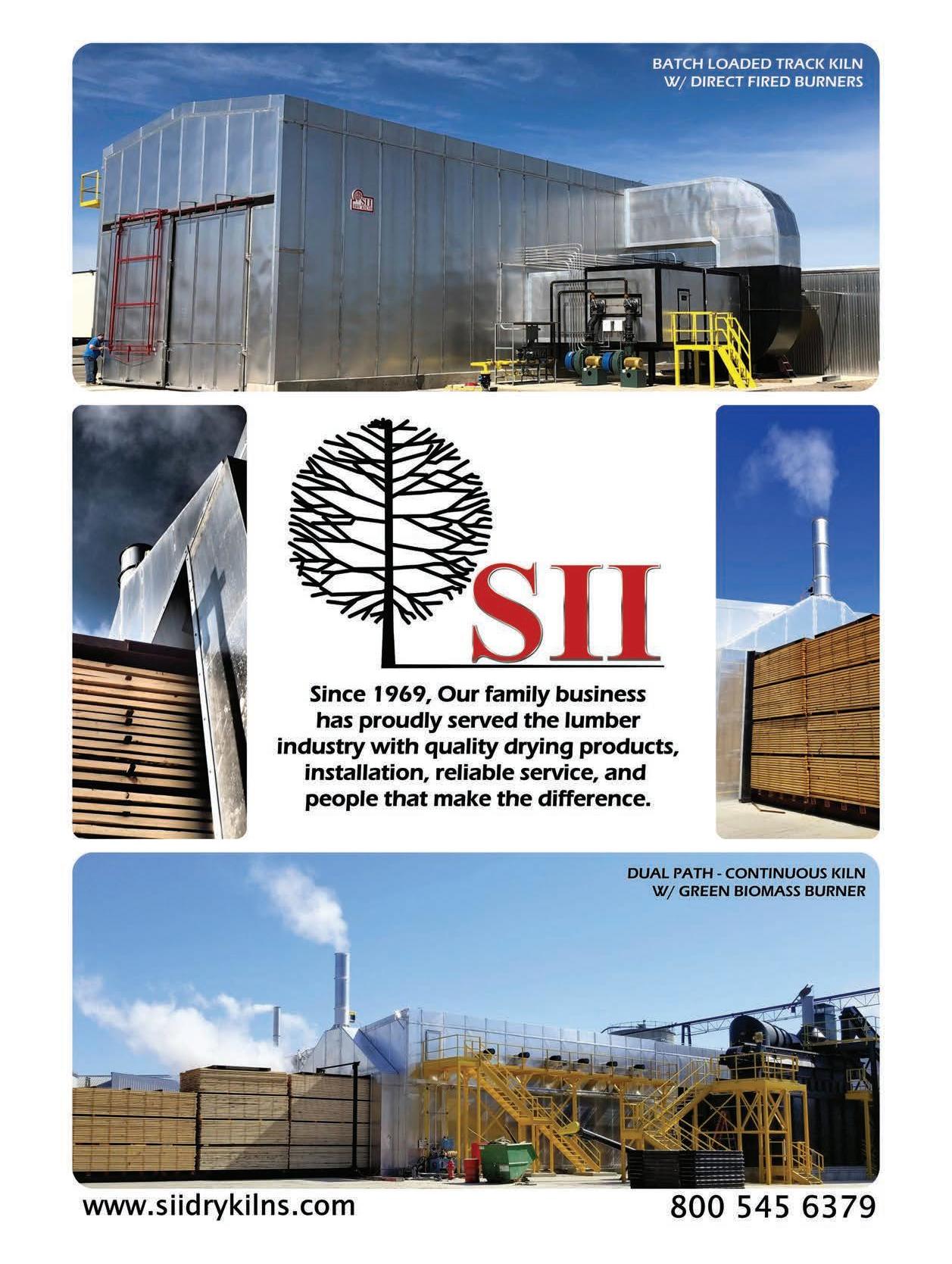
DRYKILNS BID Group
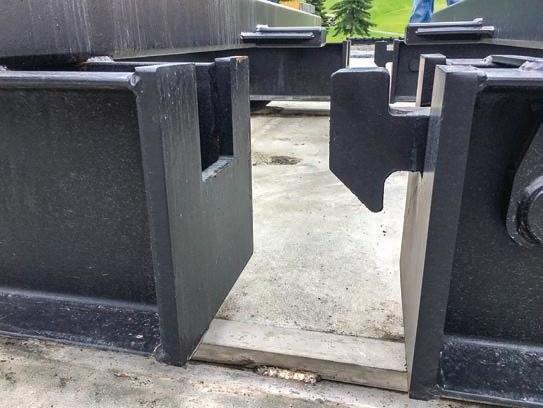
In a continuous dry kiln, the operator must ensure steady wood flow. To do so, the carts on the dry end must be brought back to the green end. To complete this task, the operator must get out of his vehicle and connect the cart to the chain. This operation is risky, so BID Group designed an innovative and automatic cart attachment system. Now, the operator can stay in his vehicle and connect carts easily and safely.
Unlike the chain and pin-based systems, the quick connect cart attachment system doesn’t require any manual labor, since the connection is done automatically. It reduces significantly the total time required to connect carts, so the operator can focus on other tasks. But most importantly, the operation is done safely without any compromise.
The quick connect cart attachment system has been used and tested for over a year and has proven its efficiency. This simple and clever mechanism is powered by gravity. It uses a hook that pivots on an axle which grabs the end plate of the next cart. A BID Group quick connect cart attachment stopper limits the stroke to naturally position the head horizontally while preventing it from over flipping. The head of the hook will line up perfectly with the frame to give a visual confirmation that it is locked in place. To release it, simply lift the cart.
This attachment system is designed to easily connect with a cart from several angles. So, the operator can connect, by approaching his vehicle, from whatever side is most convenient.
The quick connect cart attachment system is made of superior steel alloy and can pull up to 60 ft. of carts fully loaded. It is also compatible with all types of loaders and pushing systems, so it is possible to install and use this attachment system in any existing installation.
As for maintenance, you only need to grease the axle to protect it from contaminants and extend the reliability and durability of the equipment. Spare parts are inexpensive and can be replaced in minutes without causing any downtime to the kiln.
Brunner Hildebrand
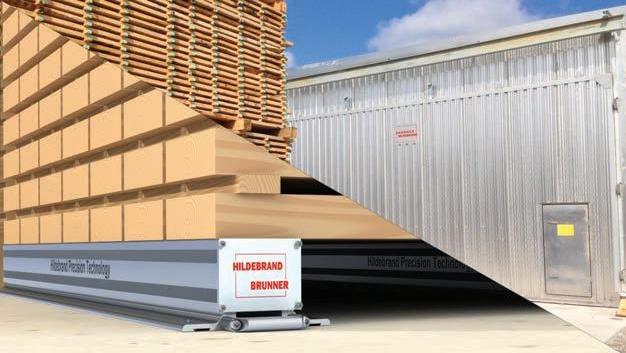
Brunner Hildebrand Lumber Dry Kiln Co. specializes in kilns for softwood and hardwood. The company’s expertise ensures that customers receive individual dry kiln solutions tailored to their needs. Each solution is chosen based on the requirements of the customer in terms of capacity and lumber grade. The priority is in providing the best-engineered, installed and serviced product in the market today. The company’s service network is on standby to provide full after-sales support, either on location or by remote access.
Recently, the company introduced Hildebrand Weight Precision Technology (HWPT), which is capable of weighing entire lumber stacks in wireless mode. In contrast to the former Brunner Hildebrand Brunner Hildebrand wireless weight precision technology in-kiln-probe system, this is a massive improvement because it produces more accurate results and it may easily be integrated into the daily work routine by using weighing devices looking just like regular 4x4s.
In combination with the new Vector EW control system, which shows kilns in appealing 2D and 3D mode, customers benefit from a superb level of accuracy and practical implementation.
The latest kiln development is the single-direction Hildebrand continuous kiln (HCK), which is the right solution for mills that produce large volumes of lumber, e.g. dimension SPF. While developing the HCK, Brunner Hildebrand put great emphasis on creating exactly the right drying conditions for the respective lumber moisture content. Integrated into the kiln carts, the HWPT devices ensure full control. To provide best results, the technical features of each individual drying zone are customized to the drying state and moisture of the lumber passing through.
Special emphasis has also been placed on energy-saving measures in the Hildebrand continuous kilns, such as the company’s special GreenKilns system with large cross-flow heat exchangers and the application of frequency-controlled fan motors throughout the kilns. Automatic indexing of kiln carts is performed hydraulically by powerful pusher units integrated in the feeding section of the kilns. Systems can be single-track or multi-track with lengths according to the desired production volume. It’s also applicable for drying different lumber dimensions simultaneously in one continuous kiln.
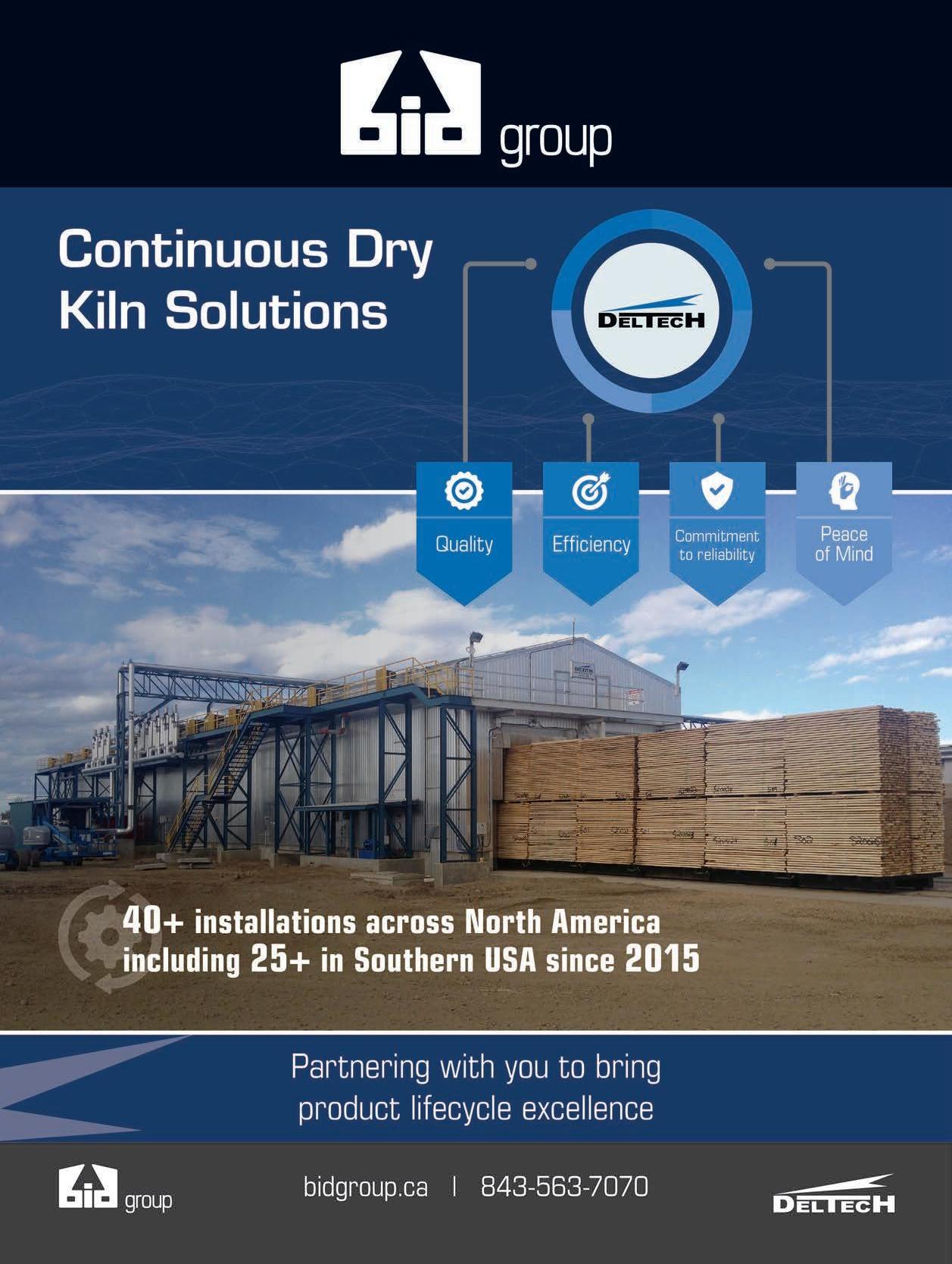
DRYKILNS Lignomat
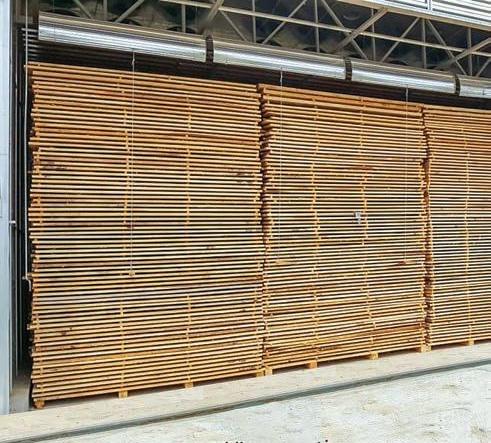
Lignomat offers a wide variety of products and technologies to control lumber drying, steaming, heat treatment and condition rooms. We also offer stand-alone monitors for wood moisture, wetbulb dry-bulb temperature, EMC, wood core temperature and integrated sample scales. Our control systems are in operation worldwide and have been fine-tuned for more than 40 years.
Lignomat’s newest kiln and predryer control systems have proven to be a great tool to dry lumber better, safer and more efficiently. The new systems are the culmination of 40 years of experience in engineering kiln control systems for the lumber drying industry in the U.S. We offer control systems for softwood and hardwood kilns, high temperature kilns, dehumidification kilns or vacuum kilns, for new installations or as retrofit for existing systems. We also have developed with great success a control system for the specific needs of predryers.
Latest software development allows Lignomat’s systems to be integrated in an existing network with many new and additional safety features. The control systems can be remotely operated, monitored and controlled with any mobile device via nearly any operating system with or without Internet. Lignomat’s text alert feature automati- Lignomat offers a great variety of control systems. cally sends specified alerts to a cell phone with no third party service or costs. Alerts include “kiln halted,” “over temp,” and “schedule complete,” to name a few.
The versatile systems can be easily tailored to a customer’s needs—starting with diverse drying schedule selections, which include time-based, moisture content-based, weight samples or loss/day schedules. The kiln operator can choose from a library of customer designed drying schedules to start the drying process. However, the system is so flexible that this schedule can be changed within the drying cycle.
Unique scheduling, AHDC, peak energy management, and steam optimization are a few more tools at the kiln operator’s disposal for efficiently drying with Lignomat control systems.
McConnell Industries
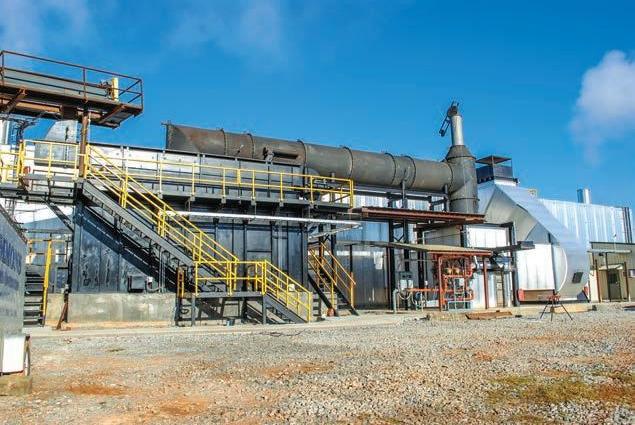
On November 1, 1970 Cliff McConnell left a family business and formed McConnell Industries to design and manufacture lumber dry kilns specializing in direct fired southern pine kilns. At the family business he was responsible for the design and manufacture of fossil fuel air heaters used in drying cotton, paint bake ovens, and other manufacturers’ lumber kilns. During this period an oil fired heater was developed that could fire direct into a cotton dryer without discoloring the cotton.
During the oil embargo in 1973 fossil fuels such as natural gas and #2 fuel oil became scarce and expensive. A direct oil fired kiln had been built for Joe N. Miles Lumber Co. in Bogalusa, La. in 1971 and the company in 1973 needed a second kiln. Oil was rationed to the amount purchased the prior year and McConnell Industries is celebrating its 50th anniversary. the company did not have access to natural gas.
In a meeting, a reference was made by a major lumber company about a company in San Diego, Calif. that they understood had developed a burner that would burn fine wood type material that may have an application in the forest products industry. From a phone call and visit to San Diego to the Energex company, we learned the company at that time had built three suspension burners. One was on a classified paper burner for the Navy; one was burning sander dust in a tee-pee burner; and one was on a plywood dryer. Energex was not familiar with softwood lumber kilns.
In reporting back to Miles in Bogalusa we felt the Energex burner could be used for heating a lumber dry kiln using hammermilled dry planer shavings as a fuel source. A 68 ft. double track kiln holding 120MBF was designed and built with a 36 in. ID model 27 Energex burner as heat source. Burner reportedly had capacity of 27 million BTU/hr, later re-rated to 24 MM BTU/hr. Only fossil fuel required was a one million BTU/hr propane burner to light the wood fire and run for 45 minutes.
The kiln was started up the first week in January 1974. LUA Insurance Company wanted to be on site during startup. Energex also had a startup man on site. First charge was run with only a few glitches, but when the kiln was opened, lumber was very black. Energex said they had a man with more experience whom they sent in two days later, but results were the same. Energex

had told us of the combustion that would take place inside the refractory lined combustion chamber. The lumber condition was like we had seen on oil fired installations with a mis-firing oil burner. Our success in firing oil into lumber or cotton was to have refractory combustion chamber after the burner so that there were no unburned hydrocarbons leaving the burner that could be quenched by the recirculating atmosphere.
The Energex burner was backed up 8 ft. and a refractory lined chamber was installed. The following kiln charges had no indication of the carbon black residue. The Miles people were very happy. LUA was concerned that we were putting products of combustion direct into the lumber drying chamber. LUA did admit that the fuel cost saving with our system along with savings by direct heating rather than converting to steam was how the industry was going to have to go. We worked with LUA to develop a set of standards for wood direct fired kilns that are still being used today.
In 1976 the control of the Energex company was acquired by a competitor and McConnell, who had been making major modifications to the Energex burner, began designing and manufacturing their own dry fuel suspension burners. McConnell had installed nine Energex burners. Since that time more than 300 McConnell dry fuel suspension burners have been installed, some as far as Scotland, China, Philippines, and many in Canada. Numerous improvements have been made on the suspension burner including a patent in 1990 on a chamber to reduce the grey ash carryover from a suspension burner. Dry fuel burners are offered from 15 to 50 million BU/hr.
In 1985 Alan Kasper was building a fairly crude green sawdust burner to heat small dry kilns. However it was working well enough so that McConnell felt it had possibilities in larger kilns. A meeting with Kasper found he was interested in a hardwood mill he owned in Missouri and wanted to phase out of the burner business. McConnell purchased the rights including drawings to sell and manufacture the Kasper burner, which was a sloping grate with ash dump grates.
McConnell built eight of the Kasper type burners including an early burner used to heat the Pollard dual pass kiln; the first 8 grate burner in 1989; and the first burner to have continuous fuel feed in 1991.
With Canadian companies investing in U.S. lumber companies and making major additions, including dual pass kilns that required larger sawdust burners with more sophisticated controls, McConnell was the first to develop a sloped grate burner with automatic control of temperature in gasification chamber as well as primary and secondary chambers, which resulted in an extremely clean, easily controlled burner with continuous fuel feed. For batch type kilns requiring more burner turn down, McConnell developed a control system that can provide a 10/1 or greater turn down without introducing fresh air or dumping heat to atmosphere.
McConnell burners are used extensively for heating rotary dryers and hot oil systems in the board industry as well as direct fired lumber kilns. The decision was made several years ago that the burner market is less crowded than the dry kiln market and the company is concentrating on only offering heating systems for other companies’ dryers.
In 2015, son-in law Warren Poe, with an engineering degree from Texas A&M and 25 years experience in designing and erecting cellular towers, joined the company as Chief Project Manager. Other key employees include Don Hicks, who has been with company since startup of first wood burner; Jimmy McDonald, auto CAD designer; and Teresa Shell, who handles all office functions.
McConnell is interested in working direct with mills or dryer suppliers in supplying wood fueled heating systems either with dry fuel suspension burners or sloped grate green sawdust burners.
MEC Dry Kiln

Séchoir MEC Dry Kiln is celebrating its 30th year of business in the industry in 2020. With more than 300 dry kilns sold in Canada MEC Dry Kiln has built a solid reputation in the industry. This solid standing has been based on many distinguished advantages that positions MEC as one of the most important dry kiln partner/suppliers. How? Through its important investments in Research and Development and its unsurpassed customer service.
Today MEC offers a wide variety of kilns at the best quality ratio: l Single or double pass l Rails or packages l Continuous (dpk) l Hybrid or 100% electric MEC also offers the services of kiln upgrades and rebuilds. With more than 100 modernization kilns projects done in its existence, MEC provides to its business partners the ultimate performance of their kiln. MEC Dry Kiln: 30 years and counting
MEC programmers have developed a unique kiln control program called the VIP II. This kiln control program can be installed in all brands of kilns in the industry. Many customers with competitive kilns have opted for MEC VIP II control program for numerous reasons: l Because of its best quality ratio l Many VIP II have demonstrated an average pay back of four to six months l Its unique intuitive interface ➤ 34
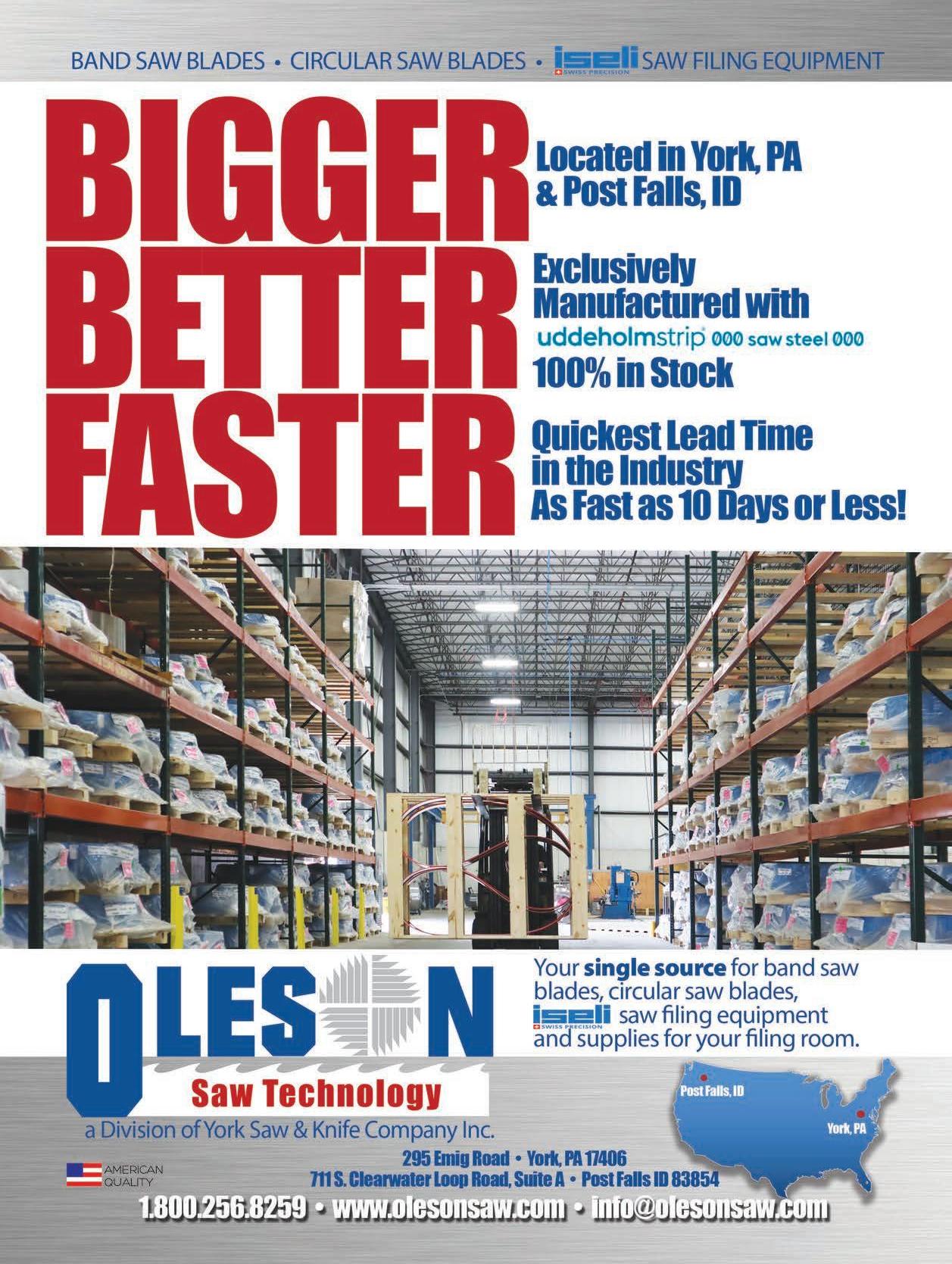
l Its complete alarms program that is displayed on the interface and sent by e-mail, SMS in real-time
MEC dry kilns encompass a unique moisture meter plate called KilnScout. This unique wireless system demonstrated an average ROI of four months and provides numerous advantages such as: —Accuracy: Shut down with confidence directly from moisture content —Increased production: Reduce drying time and improve kiln efficiency —Improved grade recovery: Reduce aggregate moisture content standard deviation —Safety: Eliminate the need for hot checks —Reduced energy costs: Through fan speed, temperature, and shutdown control by moisture content —Low acquisition costs: No wires, wireless system
MEC Dry Kiln invites all mills with future kiln projects to call them. They will experience rapidly the level of know-how, service, and unique solutions that MEC has offered for 30 years. MEC solutions are developed to be positioned as the most reliable and affordable in the industry. Our engineers, programmers and technicians who create our innovative solutions are highly qualified and experienced.
Mühlböck
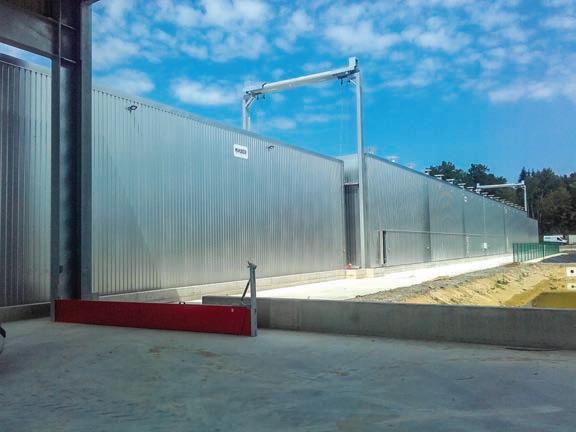
One of the latest innovations from the Austrian drying specialist is the Progressive kiln FLOW. Although Mühl böck has been scoring globally for several years with their Progressive kilns and various heat recovery systems, they still saw further potential in making the Progressive kiln even more flexible than before.
Mühlböck explains the origin of this idea: “Many of our customers have noted that with the forklift transport in the yard and time consuming loading/unloading of the conventional kilns, the logistics of their modern sawmill and planer mill process is interrupted. The Mühlböck unidirectional Progressive kilns ensure simple and fast loading and unloading, while the automatic transport system with buffer zones can eliminate the need for night shift forklift operation. And by combining these features with the drying qual- Mühlböck new Progressive kiln FLOW combines the advantages of a conity of conventional batch kilns, due to the 4.0 industry- tinuous and a batch kiln. ready Mühlböck K5 drying control system, the Mühlböck Progressive FLOW fills in the logistic gap and increases productivity.”
With their first of its kind green energy biomass project in Meadow Lake, Saskatchewan, Can. well under way, it is no wonder that the Meadow Lake Tribal Council has also decided on the most modern kiln drying technology for their NorSask sawmill. The handson expertise that Mühlböck brought to the table for this ambitious project appears to be the convincing factor. And Müh lböck’s engineers are working closely together with their Canadian counterparts for MLTC, in order to ensure that their Mülhböck Progressive FLOW continuous kiln with 1306 Heat Recovery will work seamlessly with the sawmill’s cogeneration and logistics systems. This continuous kiln that will handle over 81MMBF of NorSask’s lumber per year is scheduled to be installed next summer.
Nyle Dry Kilns
Kiln drying is a process in our industry that is sometimes considered the necessary evil, occasionally resulting in financial and even emotional pain! However, when this process becomes a well oiled machine it can transform into a highly profitable, gratifying operation that produces true works of art.
Nyle Dry Kilns has spent decades providing high quality kilns and services to the lumber industry. “At Nyle we believe that every company wants to improve their kiln drying performance, efficiency and results but sometimes they don’t always have a clear path to make that happen,” says Jeremy Howard, President of Sales and Marketing. “We believe we can help draw that map.” With that belief, Nyle recently unveiled their new industry leading Dry Kiln Optimization program.
Nyle’s Dry Kiln Optimization program is designed to give sawmills every tool needed to become more efficient and
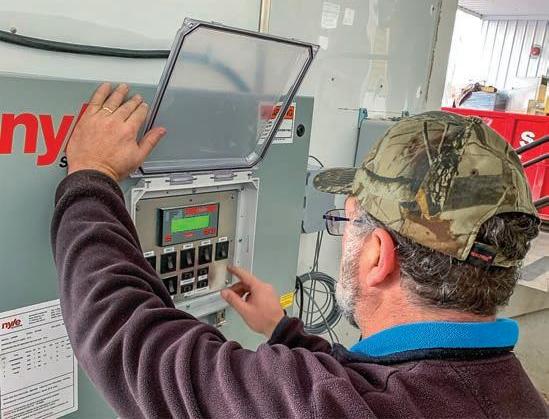
Nyle kiln specialist, Henco Viljoen, checks the kiln controls.
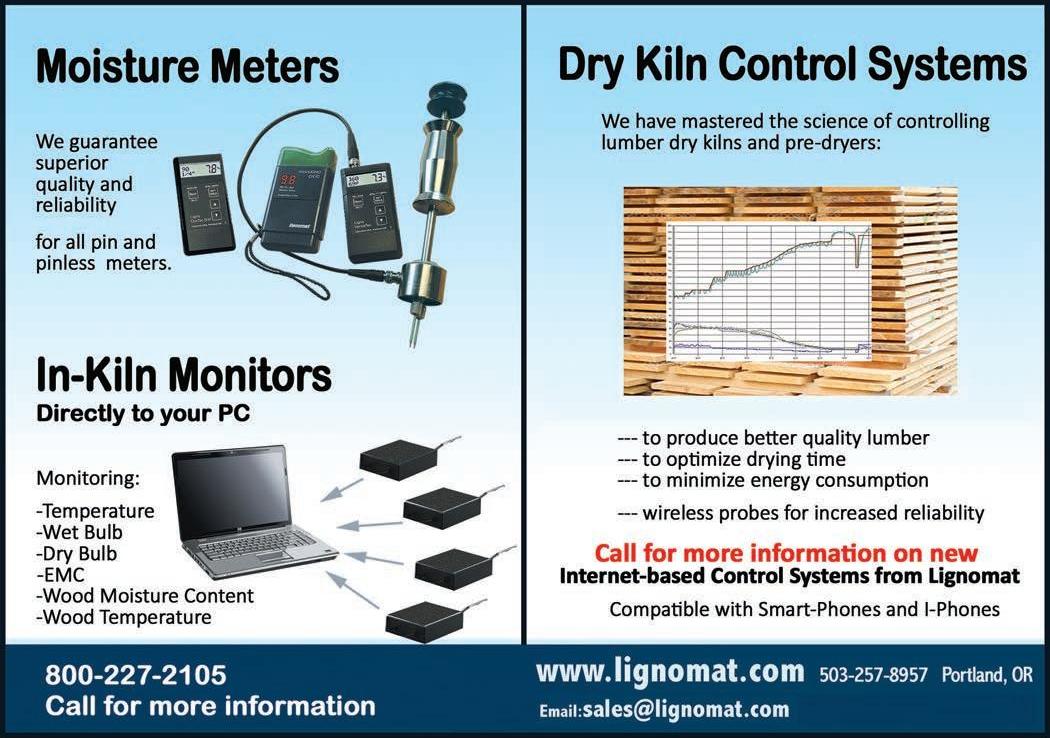

profitable. The program starts with a complete review of each facility, their current standard operating procedures in regards to the kilns as well as a comprehensive analysis including thermal imagery, kiln equipment grading and more.
Once the review portion of the program is complete they then create a training course and provide on site training completely tailored to the individual sawmill, management style and operator. In addition to the training, the sawmill will receive a detailed report on their kilns, processes and recommendations on how to further improve the efficiencies of each kiln.
Nyle wanted to clarify that this program is designed for all sawmills, not just those equipped with Nyle kilns. “We hope that by sharing our knowledge, helping to improve results, increase kiln efficiencies and reduce the lack of understanding that can sometimes exist we can in turn help the industry to produce a higher quality product,” Howard adds. “Please reach out to us with any questions or comments and let us show you that Nyle is here to help!”
Smithco
Smithco’s 2000 m to 84 in., 12-blade propellers are primarily used in track-loaded lumber kilns drying softwoods. Designed for high-volume airflow at increased static pressures in the 2.0 to 2.5 in. (500 to 620 Pa) range with a maximum rotational speed of 840 RPM, these propellers have adjustable pitch blades and tested reversibility with full-flow in both directions.
All Smithco propellers feature keyed taper lock bushings and stainless steel hardware, and the Smithco Degree Gauge allows you to easily set the blade pitch.
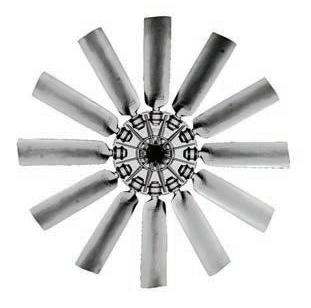
Smithco 12-blade propeller for dry kilns
Ultra Air Systems
A key component in modern continuous dry kiln (CDK) operations is the green sawdust fuel delivery system. This “free” source of fuel drives the economics of the process, and with storage silos allows the kilns to run 24/7 while most of the mills themselves run four or five days per week.
The flexible and efficient system for green fuel transport is pneumatic conveying. But these systems have had an Achilles Heel—that being the fabricated “wear back” style elbows that have been used to change direction as the routing through the plant requires. These elbows and bends see severe duty and are a frequent source of leaks, and critical kiln downtime for repairs.
Ultra AiR Systems, LLC of Franklin, Tenn. has introduced the Ultra 600 Induction Hardened Elbow, eliminating that problem, providing up to 10,000 hours of maintenance free service at a comparable initial cost to traditional wear backs. By using actual hardened steel pipe bends, the transitions on the inlets and outlets are eliminated. And through the patented bending and heat treating process, the interior surface of these elbows is 600 Brinnell. Test units on green sawdust systems are shown to last two to four times longer than traditional wear back elbows on identical applications.
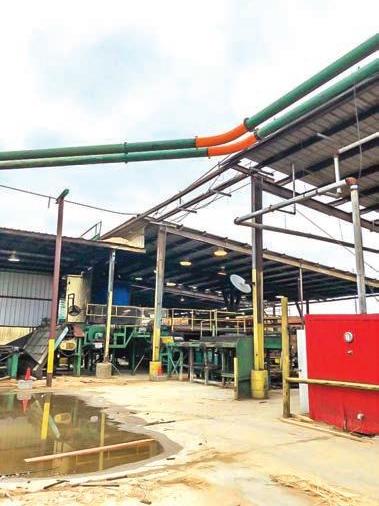
Ultra Air Systems induction hardened “orange” elbows
USNR
USNR’s ongoing technology advancements continue to produce excellent lumber quality while minimizing kiln operating costs. The Atlas Density Grader revolutionizes the way we sort lumber for drying. This new system is proven to reduce energy consumption and drying time, while increasing grade yield, length yield, and planer throughput.
Atlas Density Grader allows you to sort out lumber variations in moisture content (MC) so you can create intelligent recipes for drying, optimize kiln time and energy, and maximize the quality of your dried lumber. This reliable and affordable system uses a smart sensor that integrates with the mill PLC and sorter systems to deliver more than 250,000 accurate and repeatable weight and density measurements per second.
Atlas weighs the whole board up to 50,000 times per second at each weigh bridge, so the reported density is the average for the whole board and not just a localized density like other systems. By adding extra weigh bridges, the system can accommodate applications from 6 ft. studs to 28 ft. lumber lengths.
Atlas works on high-speed systems operating at 240+ LPM. Weight results are paired with scanned volume measurements resulting in reliable density values for the whole board. Atlas systems have no temperature or surface moisture limitations. Infrared, microwave, and X-ray density systems must be adjusted for temperature changes and will not work with frozen surfaces or cores.
Considerations: l Sorting dry boards with dry boards (<50-60% MC) allows drying two adjacent lengths in the same package. Dry kiln time is typically fairly short. l Drying wet boards (<130% MC) allows for higher BTU input for a longer duration. l Assign dual or triple bins only for the highest value or production volume dimensions. This results in a larger payback. l Different species tend to have different MC. Going from non-segregated Douglas fir and hemlock/fir kiln loads to two density/moisture segregated sorts, the kiln time reduction can be in the range of 20-25%. l Separating the production into three density/moisture sorts may reduce the standard deviation to approximately 2% or better for each sort. l Better knowledge of green moisture distribution allows you to tune the kiln schedules by season, by dimension, by species, and by harvesting region.

USNR technology improves dry kiln efficiency, lumber quality.
Valutec
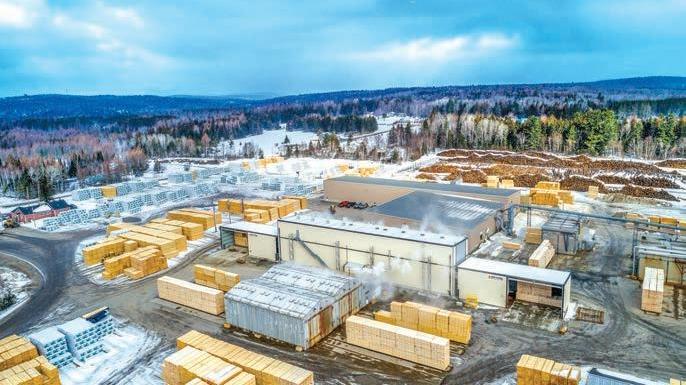
As the leading developer and world leader in continuous kilns, Valutec has delivered more than 1,500 continuous kilns to sawmills around the world. In October 2019, the company commissioned North America’s first TC continuous kiln at Pleasant River’s Moose River site in Jackman, Me. and now the feedback is in:
“It does a great job, in a lot less time than we’re used to and puts out a much better product,” says Fred Haigis, Lumber Yard Supervisor at Moose River.
“The installation process was smooth without any major issues. And when we saw one of the kilns in our mill for the first time we knew we made the right decision,” states Jason Brochu, owner of Pleasant River Lumber. North America’s first Valutec TC continuous kiln operates at Pleasant River’s operation, Moose River, in Maine.
A TC-kiln comes with distinguishing features such as high flexibility and superior capacity. It gives the operator the possibility to create the ultimate drying process with unlimited freedom to mix dimensions, minimal moisture content variation and reduced risk of checking. Annual capacity can reach 125MMBF with target moisture contents down to around 12–18%. The principle is based on the timber package being fed length-wise through zones in which the air circulates laterally across the drying channel. This enables the separate regulation of the climate in different zones according to a schedule that comes very close to the ideal schedule of a batch kiln.
“The leap in technology has fundamentally changed the way of working at many sawmills. Higher flexibility creates significant advantages, particularly when it comes to planning. Competition is extremely tough in the sawmill business, where margins are tight. So, customers in this sector rely on high efficiency and quality,” explains Ingo Wallocha, Managing Director, Valutec Wood Dryers Inc.
In April Valutec commissioned its second North American TC kiln at Pleasant River’s site in Dover, Me. Due to COVID 19 regulations the commissioning had to be done remotely.
“Corona has forced us to challenge ourselves and find new ways of working. Since the outbreak of the virus we’ve successfully commissioned kilns remotely in North America, Russia and Europe. This has been possible because we have proven solutions with well functioning components,” Wallocha adds.
The startup of the TC-kiln at Moose River has not gone unnoticed. Before the Corona outbreak several sawmills visited the sawmill to take a closer look at the Valutec TC-kiln and the response has been overwhelming as Valutec has already sold two more kilns to North America, including Canada’s first TC to a sawmill in New Brunswick.
“I can honestly say that whoever sees the Valutec TC-kiln at Moose River probably won’t buy another kiln again. Whenever I talk to the guys as Moose River or Dover I’m really proud to hear that they’ve had the best experience with our kilns,” Wallocha says.
DRYKILNS Wood-Mizer
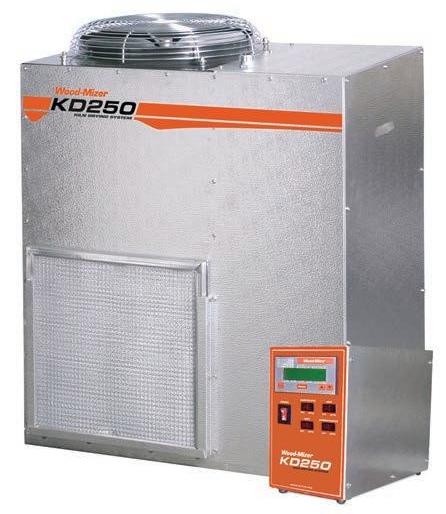
Kiln drying lumber is a simple, cost effective method recommended for anyone who wants to increase profits by selling dried lumber. Kiln dried wood typically sells for a third more than green lumber and eliminates the need for customers to incur costs associated with drying lumber before use. In addition, dry lumber kills infestations, hardens pitch, preserves color, and controls shrinkage while also reducing risk of developing fungal stain, decay, rot or mold. Dry lumber also machines, glues, and finishes better, resulting in nails and screws having higher holding power. Finally, dry lumber weighs more than 50% less and is over Wood-Mizer dehumidification kiln twice as strong and stiff as green lumber. Lumber that is not dried under controlled conditions with a kiln is prone to warping and other degrade that diminishes its selling price and workability. With a Wood-Mizer kiln, successful drying for better profitability is easy and affordable for virtually any size operation.
Wood-Mizer offers dehumidification and solar kilns with capacities ranging from 300 to 35,000 board feet for drying lumber. The Wood-Mizer KD series of kilns feature 100% corrosion resistant aluminum cabinets and specially coated dehumidification coils to ensure quality performance and an extra-long life. The KS solar kiln is a simple and economical system for starting to kiln dry lumber. Visit www.woodmizer.com to download a free Introduction to Kiln Drying Guide.
Wood-Mizer kiln offerings include: —KD150 Dehumidification Kiln Kit - Compact, entry-level dehumidification kiln for drying lumber between 300 and 1,000 board feet. —KD250 Dehumidification Kiln Kit - High-quality dehumidification kiln for controlled lumber drying of 1,500 to 4,000 board feet. —KD450 Dehumidification Kiln Kit - High-performance dehumidification kiln for producing up to 15MBF of kiln dried wood. —KD550 Dehumidification Kiln Kit - Commercial dehumidification kiln for precise controlled lumber drying up to 35MBF. —KS50 Solar Kiln - Cost-effective solar kiln for drying lumber up to 3MBF.
COMING IN DECEMBER Cutting Tools Technologies

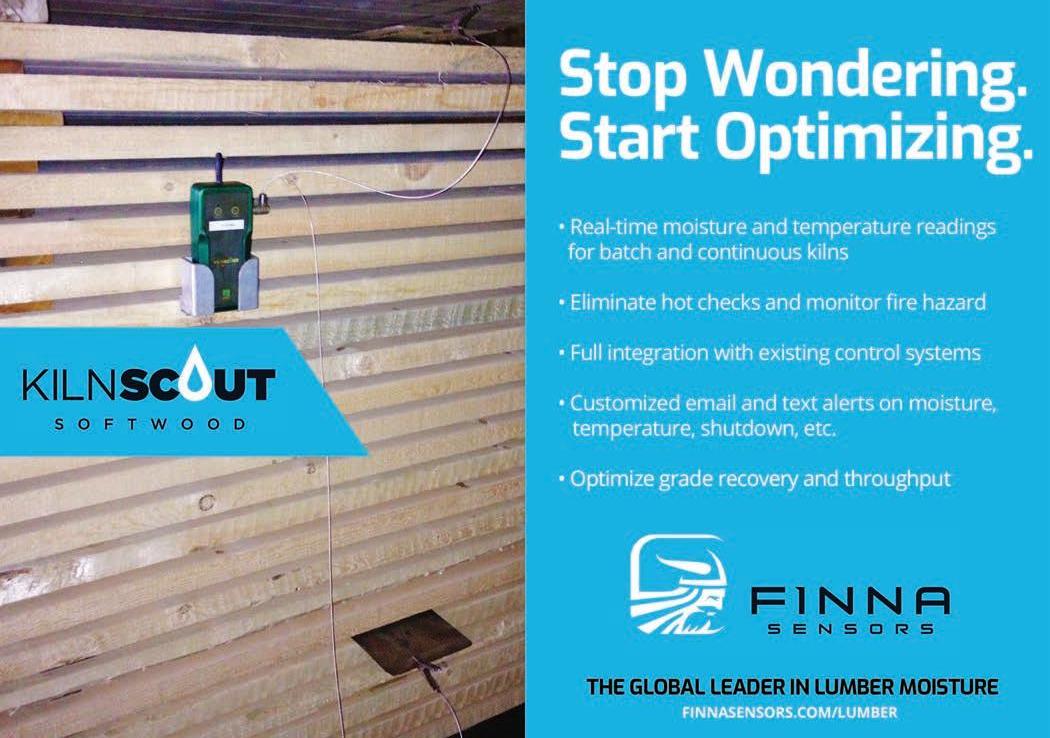
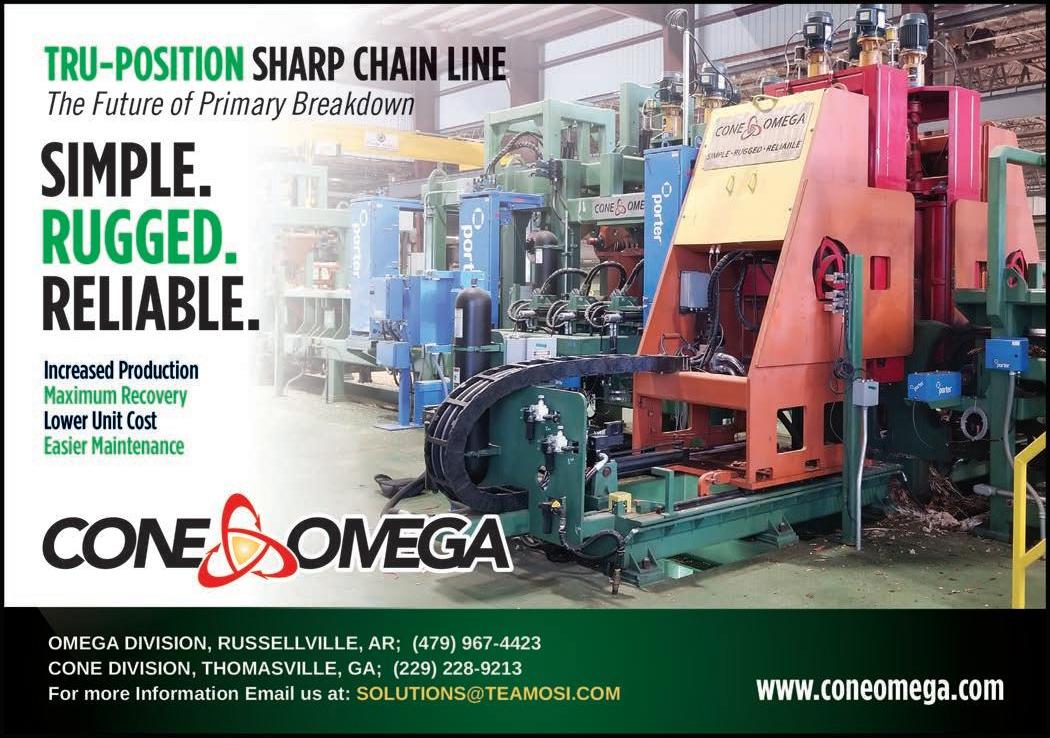
ULTIMATE GUIDE TO MOISTURE CONTROL Part 2: Kiln Drying
By Steve Maurer
Controlling moisture is key to producing a quality end product. Ironically, despite being where moisture is altered the most, kilns are also often the most overlooked.
West Fraser’s Thermal Energy Supervisor Martin Andres has been with the company for more than 42 years, and knows the importance of kilns as well as anyone. “With wets, you will obviously get claims,” Andres says. “Even though we don’t get a claim for over-dries, it degrades the wood and you’ll end up with more end and surface checking. The lumber shrinks just that much more so you end up with skip on your wood.”
Understanding how wood dries is crucial to developing effective drying schedules. Finding the right mix of temperature control, air flow and relative humidity improves the quality of the boards sent to the finishing stage. By finding the correct mix, mills can lessen problems such as wet claims, checks, warping, and unnecessary transportation costs due to excess water weight. l Previous Methods
Previous methods of measuring included weight sensors that were used to chart the drying process of sample boards. Using that data, it was possible to develop calculations for estimating moisture content. However, this provided more of an educated guess than reliable, repeatable results.
As more advanced technology produced more reliable methods, the process improved. Two types of metering sensors took readings directly from the lumber charges. The first in-kiln sensors developed detected the resistance between two probes inserted into the edge of boards. The data was collected by a handheld meter. Resistance values were extrapolated to indicate moisture content.
While this was a vast improvement, giving more accurate data from inside the kiln, there were limitations. First, the data came from a single representative board. While several probe sets could be used, the number of data collection points was limited. The second limitation was probe placement. Driven into the edge of the board, not the face, the probes could not measure at the optimal point for moisture release.
Used primarily in batch kilns, the probes were inserted before charge placement. Hot checks at various stages of the drying schedule were used to gather data for calculation. Real-time measurement could not be gathered, particularly during the early development of this type of sensor. Additionally, hot checks required shutting down the kiln and bringing it to human-friendly temperature levels. In a direct-fired kiln, this also meant venting noxious fumes. After measurement was complete, the kiln was restarted, resulting in lost time and wasted energy. l Drying Innovations
Other problems occurred with hot checks, primarily that there were less people to do them. As mills looked to reduce costs, many experienced kiln operators were transferred to other parts of the mill, or given added responsibilities that diverted their attention. With this loss of knowledge, technology was needed to pick up the slack.
Initially, wired radio frequency (RF) sensors were developed for batch kilns. These sensors use RF to determine capacitance, another method of determining moisture. Plates are non-invasively inserted between the stickers. With a plate near the top of the stack and the other near the bottom, a more representative value of the entire charge package is possible. Instead of a limited number of data collection points, moisture content value of up to 17 cubic feet, per sensing unit, are tracked. Cables connected the sensor plates to computer-based monitoring hardware, and software, outside the kiln. The data can be displayed, allowing the operator to manually make changes, or integrating with the kiln controls for automation. Especially with southern yellow pine, the variability of guessing when to shut down was removed.
With the development of continuous dry kilns (CDKs), static sensors were no longer feasible, leading to the development of wireless RF sensors. With no cables to tie them down, the sensors travel with the charge. These sensors also integrate with the kiln controls for either manual or automated operation. Up to 100 sensors monitoring moisture and temperature sets can be used per kiln, meaning the operator gets a more complete view of what’s going on inside the kiln, and can adjust the schedule accordingly.
“At a particular division, we were in need of replacing aged control equipment so we evaluated the [RF sensors] to ensure they would provide the right moisture content,” Andres says. “So far we have experienced time savings and consistent results using the moisture sensing system. We have not had wet lumber since it was installed.”
Using kiln systems connected to each other via network or internet, multiple kilns can be monitored and controlled from one location, also helping to offset the lack of operators.
According to Tony Nadeau, Sechoir MEC’s Dry Kiln Automation and Control Director, “We worked with a customer that bought kilns for two different sites. We installed KilnScout systems for each kiln with eight sensors per system. MEC’s sensor system was modified so the customer was able to monitor both sites from one location. The RF sensors and data collection units allowed the mill to monitor and modify the drying schedule for each kiln.” l What’s Next?
Despite providing several benefits including additional throughput, grade recovery and remote monitoring, in-kiln sensors are continuously being improved to keep up with the needs of modern lumber mills. The most pressing need for these mills is uptime. The sensors are now being built with Internet of Things (IoT) predictive maintenance features that actively notify the operator when there are upcoming issues, such as low battery strength. This allows action to be taken, before issues, and loss of data is prevented. Additionally, software has been built so that the kiln no longer needs to be relied upon as the sole manager of moisture—it can be monitored from the beginning of the process, from sawmill to the kiln. TP
Article supplied by Finna Sensors and written by Steve Maurer, an industrial copywriter. Next issue: Part 3: Planermill.