
12 minute read
VAAGEN BROS. LUMBER
LEANING IN TOLEAN
By Jessica Johnson
Vaagen Bros. Lumber has always done things a little bit differently.
COLVILLE, Wash.
Duane Vaagen says that over his decades in the lumber business, he’s heard the same thing over and over. It’s a chorus really, when he tours people through his mill: “That won’t work.” He says over the years as his family business has tried different things and pushed things past their specs and really their life expectancy, it’s always the same. “That’s not going to work like that.”
And yet Vaagen always finds a way to not only make it work, but make it great. For over four generations, Vaagen Bros. Lumber has produced dimensional lumber to the tune today of 175MMBF in the town of Colville, Wash., the last “big” small town in the U.S. before the Canadian border in eastern Washington.
Vaagen says first it was in the 1970s when they installed a green chain from a Southern engineering and manufacturing firm that he heard the speculation that he wasn’t going to get his chosen technology to work. In late 2020, that green chain
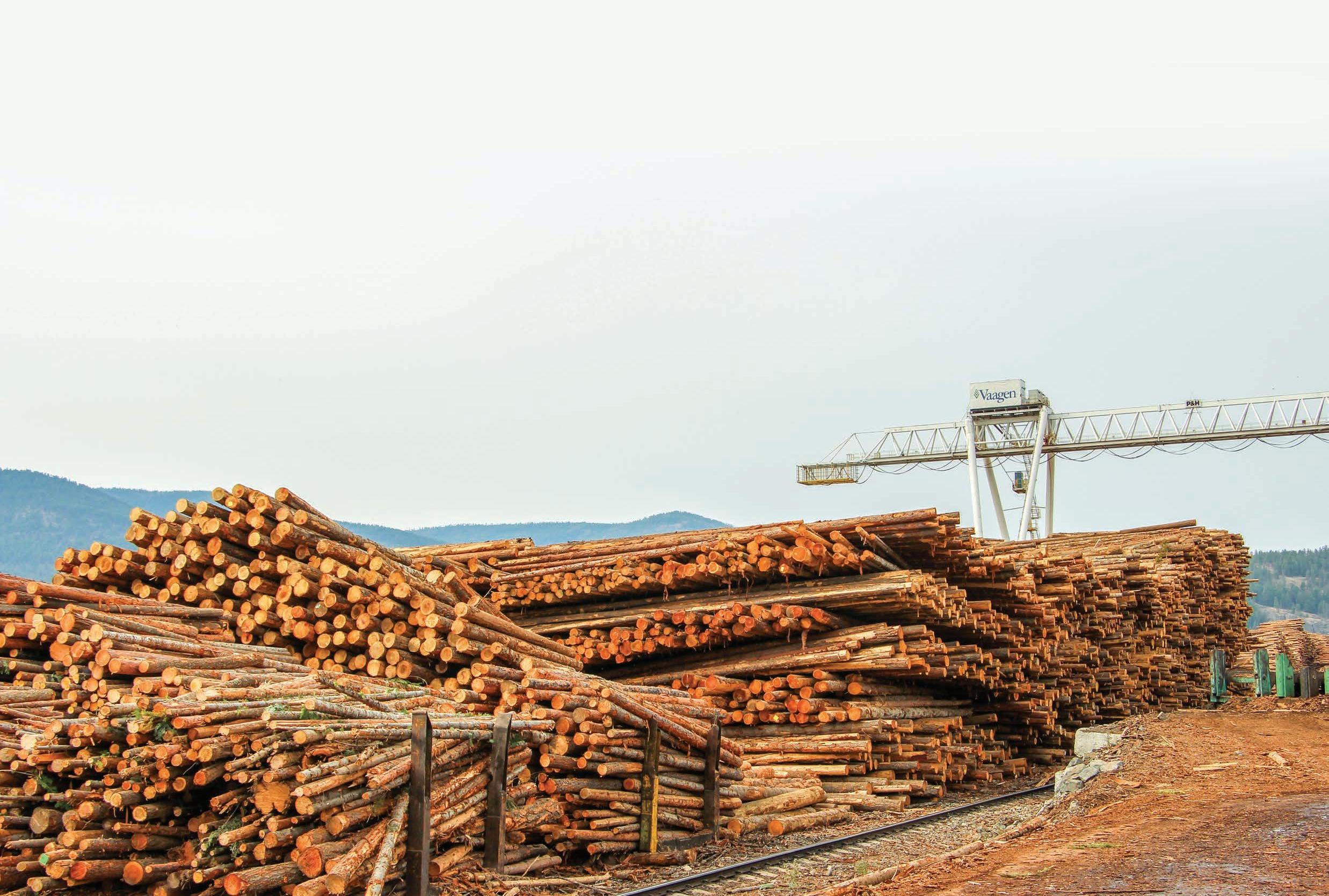
is still going. “I learned to just agree, because they are probably right. I just don’t know if it’s not going to work in 30 years or 80 years,” Vaagen laughs.
As Vaagen’s daughter, Emily Baker, serving the family business as Lean Team Leader, is quick to point out, “We might get frustrated with some of our vintage machinery, but its fed families. Its worked, and worked hard. We appreciate that.”
The Vaagen family looks at their machinery as an asset, absolutely, but as Duane’s son, Kurtis, who now serves the family business as Vice President of Operations, explains: Everything is vintage but everything has been modified in some way. Nothing is operating on manufacturer spec—including that green chain from 1976. In recent years there has been pres-
sure to just get a new sawmill, Duane says. “What we realized is we weren’t ready to do it.” So, instead of retooling the mill, or building a new one, the Vaagens decided to first invest in their people, the team members running the machine centers. They did this by jumping headfirst into Lean manufacturing—the popular way of doing things across healthcare and other manufacturing industries but not particularly popular with sawmilling because of the large number of raw material variables.
GETTING THERE
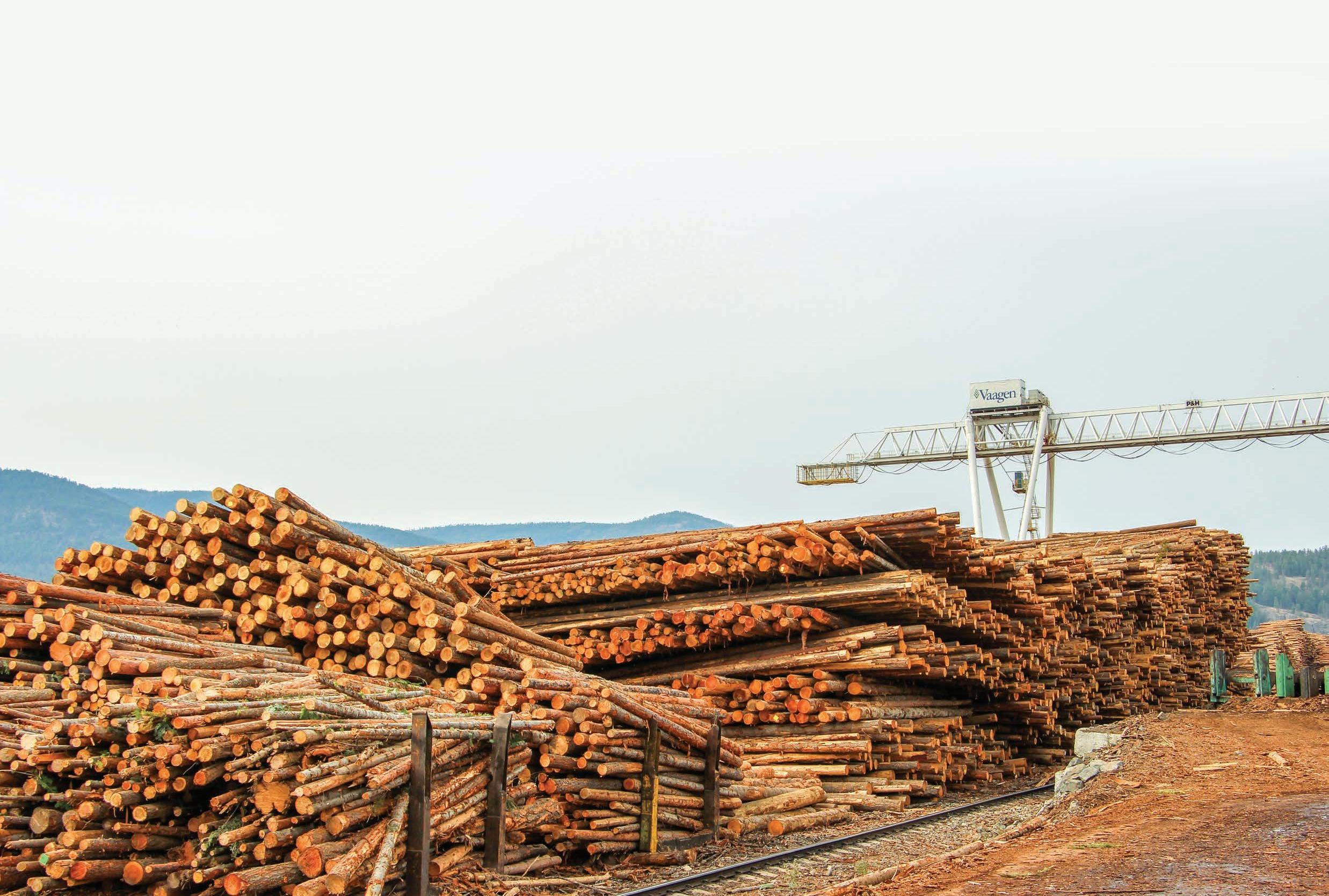
Once again, Vaagen found himself calling around, talking to people and hearing the chorus: “It won’t work.” But, after getting the Vaagen Executive Steering Team together, which included Duane; Baker; Kurtis; David Bruce, Vaagen Bros. CFO; Josh Anderson, Vaagen Bros. Vice President of Procurement; Daryl Evans, Colville Plant Manager; and Peter Deibel, Colville Controller, and really digging into the idea, it started to come together. Kurtis says the mill has always pushed the people to create the value in the lumber, so Lean did make sense. It especially made sense, he says, when looking at another facility in the area that had unfortunately closed down, but should have closed many years prior. “The employees, during the guidance of Lean, kept it going for probably five extra years,” he notes. That sort of employee ownership is second to none, and the kind of culture Vaagen Bros. wanted to have.
Partnering with Simpler Consultants, an IBM company that specializes in Lean manufacturing, the Vaagen Lean journey started in 2018. Bruce comments that the biggest thing that sold the leaders on Lean was it got rid of the excuses: “It’s a very complex business in general, but when you look at how this process and the amount of paperwork and studying and just time that it takes to do the Lean process and put it with the complexity of a sawmill, it takes commitment. But it is absolutely worth it.”
Officially, the Lean process at Vaagen is called the Vaagen Improvement Path (VIP), and is a continual improvement program that identifies specific places where the mill can eliminate waste, increase productivity and better ensure that customers get the quality expected from Vaagen.
Baker says it is not a one-time event; it’s an ongoing process. As part of VIP, she holds many “events” where areas of the facility, process and company are targeted for improvements. These events take months to prepare, and take five days to complete once the event actually begins. After that, there are weeks worth of sustainment follow up visits; it truly is a continual journey.
She laughs, saying that at first the Executive Team thought having one person dedicated to Lean, someone from the outside familiar with Lean, would be enough. It quickly became evident that not only would the company need that person, but also need multiple people in Colville dedicated to Lean, including Baker as the leader, and one person dedicated to Lean in the other two sawmills Vaagen owns and operates in Usk, Wash. and Midway, BC.
“We wanted to make


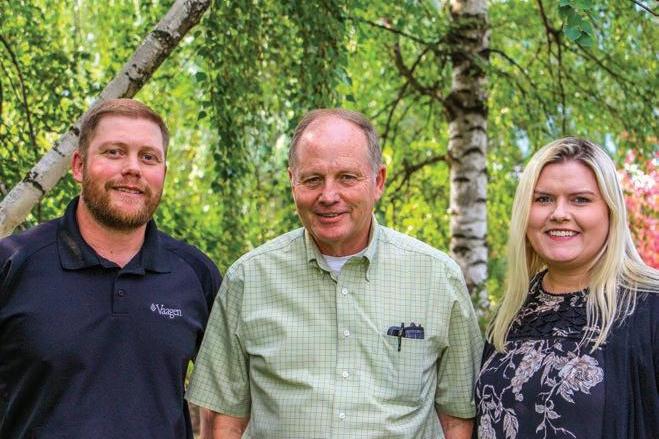
Left to right, Kurtis Vaagen, Duane Vaagen, Emily Baker
Vaagen implemented pre-sorting line years ago.
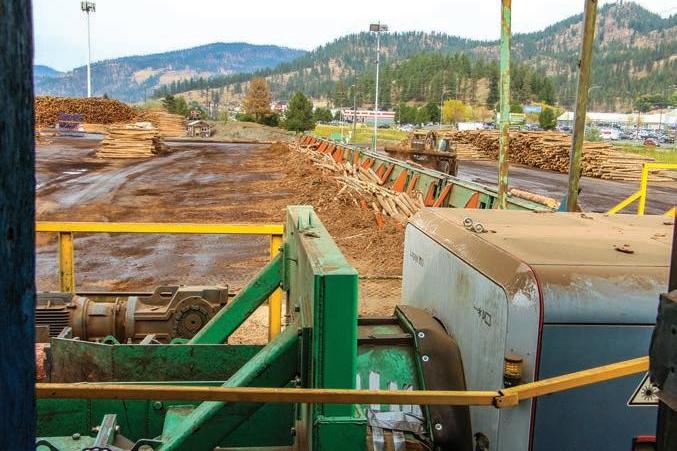


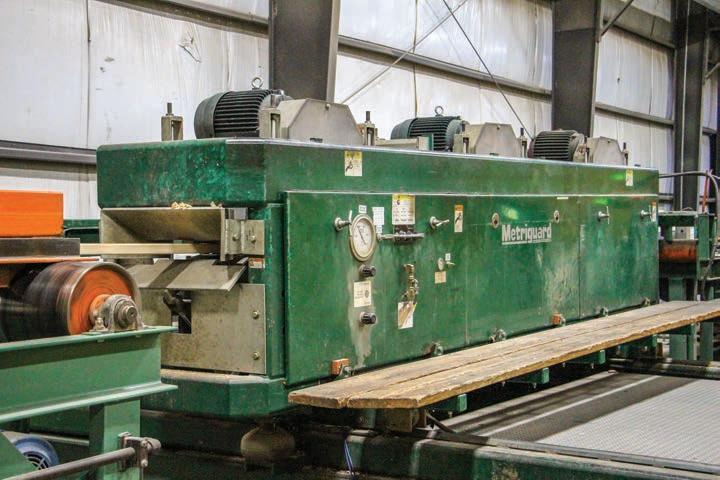
MSR has long been a Vaagen specialty.

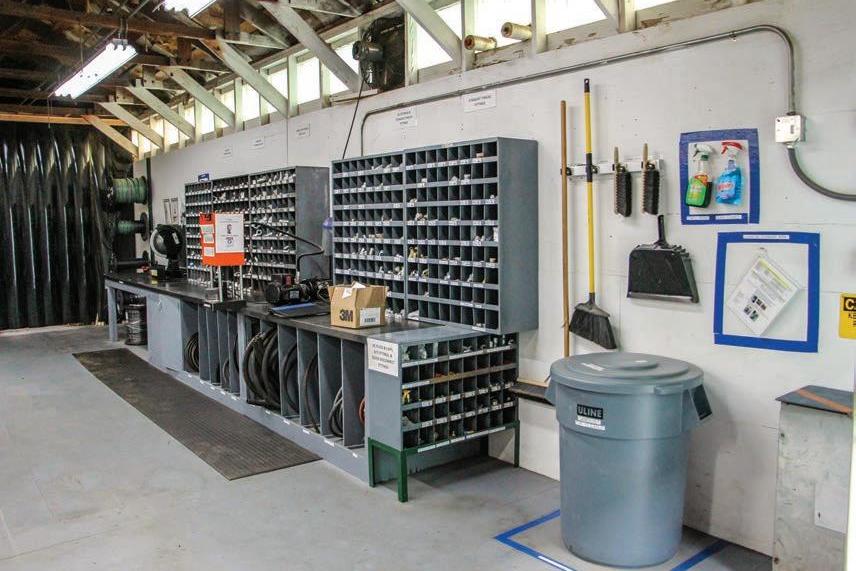
sure this is the safest place out ble without their father, who there,” she adds as to why they was the first recipient of the decided to go full throttle on Timber Processing Person of Lean, “and you have to do that the Year award in 1989. by making continuous im- “We’re blessed with a leader in provements.” our father who reads more and
Bruce says that in addition researches more about this into the safety benefit, Lean has dustry than anyone I’ve ever helped control costs. “In 2016, met. He kind of brought this ’17 and ’18, even though lum- idea to us and said; ‘I think this ber markets were pretty good, is the way forward.’ He was we noticed our costs were ris- right.” ing. We had a lot of money invested in training people, and HOW IT WORKS we were hiring more people. This process was designed to Before an event, and after solve some problems without the Executive Steering Team having management do it. We Lean program pushes setting and realizing objectives; not to men- has gone on a Gemba Walk, want the people that are doing tion putting parts and shop spaces in order. the employees of an area, the work to be part of the so- along with employees that lution.” Again, helping to might work in other areas or make Vaagen a place to be departments but used to work proud of, Duane says: “It’s a in the target area evaluate the place we all call home.” current state of a specific as-
For Bruce, while he saw pect of their work area. One the many benefits in Lean, as example of determining the the CFO it would be difficult current state is evaluating the sometimes to reconcile the cleanliness of a worksite; or overall, long-term benefit lack of standards and processes with the short-term cost in- for a specific task. Then, the vestment. “There’s so much group will evaluate the refocus on culture and not so source constraints, where much focus on the bottom someone might notice there are line immediately. The pay- simply not enough people back is going to come. needed for a given task. There’s always that flavor of the month realize what each really is. “Even if you After evaluating the current state, the book; this is a journey that never ends can do a little bit each day, it’s amazing next step is for employees to meet toand always trying to eliminate waste. We what the end of the year improvements gether and determine the target state. In all go on ‘Gemba Walks,’ which means will be,” Baker adds. other words, what should the current going to where the work is being done. For Kurtis, who is dealing with pro- state be like? In the case of leaving tools It’s a hands-on way of really seeing what duction on a daily basis, the Lean way of or materials out, it would simply be is going on and getting at the root of an doing things articulated what he always putting things back in their place after a issue. We use an acronym on these wanted from the employees. “We always job is done. Or with the lack of standards walks, DOWNTIME.” DOWNTIME wanted our people to come up with the or processes, it would be a matter of stands for: Defects—Overproduction— solutions. Before it was being pushed on making sure all employees know what to Waiting—Not utilizing human poten- them, coming from the top. Now they are do when a particular player is gone. tial—Transportation—Inventory—Mo- bringing the solutions to us,” he empha- Following the initial steps of evaluation—Extra processing/over processing. sizes. “It was a format of something tion, employees move forward with de-
Baker and Bruce say once you train we’ve always tried to do, we just didn’t termining how they can reach their new yourself to look at things in the DOWN- have it lined up correctly.” target state. This is done by utilizing a TIME way, those things will jump out in But Kurtis is quick to say that none of series of three tools: gap analysis, soluan almost overwhelming way once you the Lean journey would have been possi- tion approach and rapid experiments.
Beginning with gap analysis, employees work together to determine direct causes that keep them from reaching their target state. Employees then can brainstorm solutions. Once a solution is agreed upon they are now ready to test the solution through a series of rapid experiments. Did it get the result they were expecting? Or are there other solutions? After conducting rapid experiments and determining what didn’t work, the team now has a tested and tried and true solution that does work. It will now become part of their operating procedure and may be applied to other areas of Vaagen.
Creating a completion plan is the first step in applying the new solution. The completion plan is a document that states what will be done by whom and by when.
This step ensures follow through. Now that the completion plan has been put in place the target state becomes a confirmed state and as time continues employees will experience the new positive outcome. All that’s left is to document any insights from applying the VIP process.
Baker says that a lot of times the sawmill would have a mess and clean it up only to have it return to the messy condition it was before it was ever cleaned a year later. This would be extremely frustrating. So the completion plans make sure the mill is not backsliding. As an added benefit, it really helps with morale. “When someone puts a lot of effort into something and then it just goes back to the way it was, then they are much less likely to try again,” she says. Instead of just being gung-ho about cleaning up specific areas of the mill, Lean gives them a formula to get things done.
THE BENEFITS
When Baker and her Lean team go through an area before an event needs to be done, they utilize “6S” which stands for: 1. Safety 2. Sort 3. Set to flow 4. Shine 5. Standardize 6. Sustain “When we go through an area, this is the model we follow to make sure we are getting to a spot where it will stay that way.”
After an event, and the 6S are reached, the Lean team spends four to five weeks doing nightly audits of their level of sustainment, giving a score. “It almost becomes a competition between departments to reach sustainment level the fastest,” she says, bringing levity to something that can sometimes seem overwhelming. ➤ 18

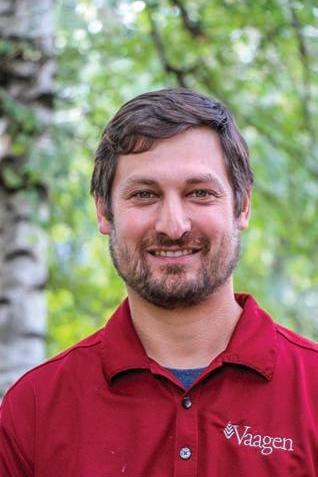
David Bruce, CFO Colville production is around 175MMBF annually.
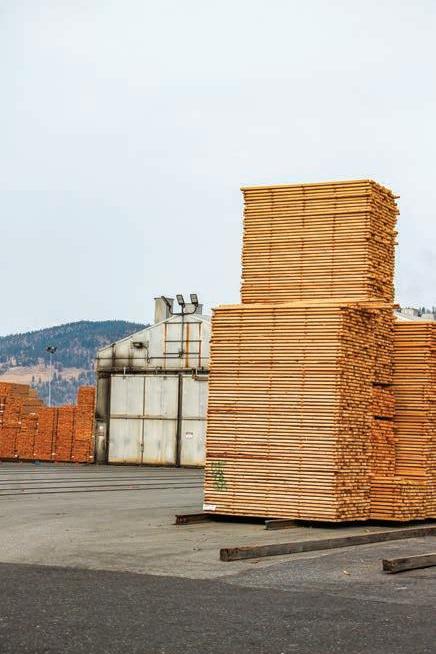


New improvement program enhances customer relations.


Vaagen lumber has been a mainstay in the Northwest.
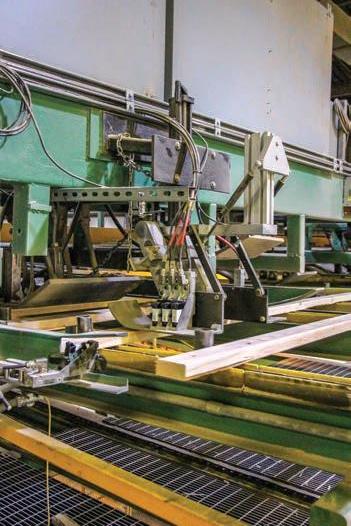

17 ➤ Back when the idea of Lean was first brought up, Baker says an employee survey showed that employees felt like communication was one of the biggest issues among the employees and management. An event that brought about daily huddles solved that. It was Vaagen’s first event and led by team member, Krystle Valli, the Lean team coordinator. During the daily huddle, every department discusses what the goal is, safety, production targets. “We cover a lot of ground with those huddles,” Baker comments. “The huddle doesn’t seem like a value-added activity because it’s 15-20 minutes where we could be producing just to talk. But it is.”
More than 75% of the Vaagen workforce has been through the Lean 101 training and every major area of the company has had an event to implement some sort of improvement.
For example, Bruce adds that with an event in the hydraulic hose room, where spare parts were stored for the truck shop, Vaagen has been able to drop spare parts inventory significantly and has recognized about $500,000 in savings in better managing what is needed.
“We’re turning our lumber inventory pretty much two times a month; it used to be one time a month. We’re trying more of a pull from our customer rather than push our inventory,” Kurtis adds.
In the last year and a half, after about six months of Lean, he says the mill started pulling material out to the planer, rather than pushing it out to the dry kilns from the sawmill. The mill used to have stockpiles of inventory in all locations because Kurtis thought these batches were the way to increase productivity. So, the rough dry, rough green and log inventory have all come down to a level that is a lot more manageable.
He adds succinctly: “Lean really did save us coming into the COVID scare. If this would have happened a year prior, with the log inventory that we had, we would have been in big trouble.” TP
