
7 minute read
FRAM FUELS
Fram Fuels Keeps On Keeping On
By Jessica Johnson
HAZLEHURST, Ga.
TThere are benefits to going with a prototype— being on the cutting edge means helping to shape the technology as it is being developed. It also means having to know when the prototype just is not working, and it is time to abort.
Fram Renewable Fuels wanted a way to construct a new pellet mill in a modular fashion. Fram also wanted to find a way to utilize the heat value of the VOCs produced by wood fiber drying that were typically controlled by incineration in the available drying systems. So, Fram contracted with a reputable, highly capable equipment manufacturer to produce such a system. After several years of intense and dedicated work on the project, the facility decided the expected results could not be economically achieved.
It was the right move, Harold E. Arnold, who handles sales and marketing for Fram, says. “Not being able to be consistent and hit the goals we wanted to was the reason why we ultimately pulled back.”
After delving into the experi- Harold E. Arnold

14 Wood Bioenergy / April 2021
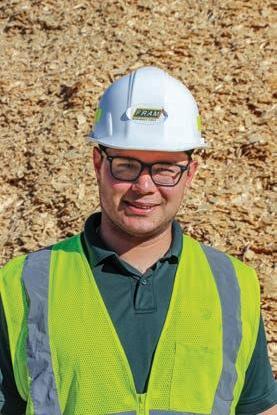
At left, looking at the TSI drum dryer from the outfeed end with flat back elbow on the discharge duct. To the left in background is the reciprocating grate furnace (wet bark burner) that provides heat energy for the dryer, and to the left of that (in foreground) is the main ID (induced draft) fan at ground level with big vertical duct from the dryer cyclones coming down into it. The silo on top of the dryer is the wet feed bin for the dryer. Below are the metering bins for dry hammermills. Fram prefers to run with sawmill residue, but does take in a significant amount of roundwood.

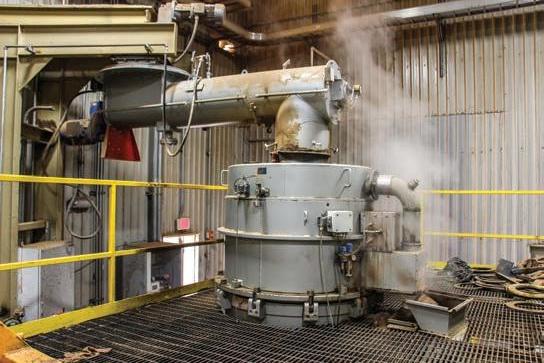

mental process and trying to make it right, Fram was ready for a change that would bring the mill the consistency it craved. After gathering information, including visiting other industry sites around the U.S. South, Fram signed the order with TSI for a complete redo of the dryer island, including the furnace, dryer, WESP and RTO.
These numerous trips with TSI were extremely helpful for Fram’s staff. “There’s competition, but it’s all mainly friendly competition because everybody knows everybody, there’s only a handful of producers,” Arnold says of these visits. “Everyone was open to telling us what they liked and what they didn’t like about the system; the engineers got to really discuss things.”
He says the driving force behind needing to replace the prototype system was the reliability of the system overall, and specifically with the pre-dryer/main dryer system installed in each of the three lines feeding the pelletizers. Fram had problems with how the system was capturing VOCs and running them back into the burner in the pre-dryer. Emissions control was a chief selling point going in, along with the modular approach to pellet production. “There comes a point where you have to kind of wrap it up,” Arnold says.
“The main thing we wanted to do was have the mill be reliable like our other operations,” Arnold adds. “We
Hazlehurst runs with Kahl flat die presses, 15 in total.
April 2021 / Wood Bioenergy 15
The wood yard can hold up to 80,000 tons of residue.

like to be very consistent in everything. That’s the only way to be in the wood industry. If you’re not consistent there are always a lot more problems down the road— starting with your truckers. If you can’t unload everything consistently they will find a new home. TSI had that track record that was hard to beat.”
The mill tried to keep as much of the original machinery as possible, including the radial “Superstacker,” bag houses, conveyors and long term conditioners. Citing similar industry experience and reliability as TSI, Bliss was selected in the replacement of the dry hammermill island.
The plant shut down in January 2019 to complete the install of the new dryer island, as well as the addition of three more Kahl flat die presses and the new Bliss dry hammermill island. In December 2020, Hazlehurst was once again pressing pellets.
The pandemic made startup a little tricker for Fram, as any construction project of this scale depends on numerous subcontractors. The site leaned on an outside cleaning and sanitation crew to keep the grounds safe for all involved. Overall Fram had little interruption to the installation schedule—though there were a number of pieces of equipment that were delayed due to other manufacturing plants being temporarily closed or logistical problems where trucks were just not available to deliver the materials needed.
Fram decided in part to continue to use the modular design. The facility has three pellet pressing lines fed by the single dryer island and dry hammermill. Each line originally had four Kahl flat die presses, but now uses five. A dry material storage silo feeds three long term conditioners before pelletizing. This means Fram is able to have the modular design they liked, giving flexibility to operate lines two or three if line one goes down for maintenance for example, while still have the reliability of TSI’s technologies.
Arnold explains, “It’s very little downtime with not having everything in one row. We’ve always liked that, from previous experience with other mills we’ve built. If you have all the material running in a straight through process, if something small goes down it can take more down than you really need to.”
As to adding the additional Kahl presses, Arnold says the flat die 600 HP machines get excellent throughput (around 6 tons per hour) and quality is spot on.
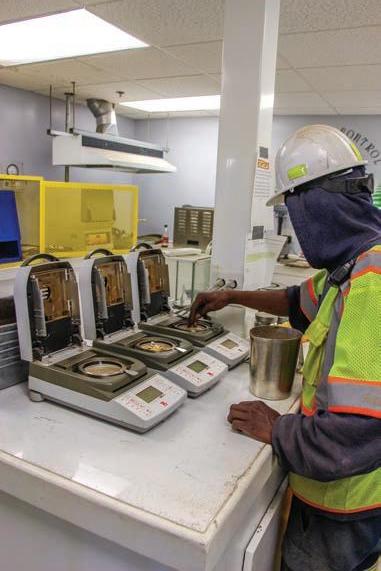
16 Wood Bioenergy / April 2021
Hazlehurst targets 5.5% moisture.
Mill Flow
The facility tries to purchase as much sawmill residue as possible, though the wood yard does have chipping capabilities to allow for roundwood deliveries—capacity peaks at 60,000 tons of roundwood and 80,000 tons of residuals. The radial stacker and green end chipping and hogging stations lead to the TSI dryer.
The facility uses a fully automated reclaim system, which stays consistent on the pile’s moisture. Arnold says this helps a lot with pellet quality: “It’s a recipe that’s easy to follow but never turns out the same. So many factors, it’s a little bit of magic.” From the dryer to the dry hammermill, material is conveyed to the press houses.
TSI’s heat energy system is an 80 m2 grate style, handling fuel moisture of a minimum of 35%. It includes primary and secondary combustion chambers, two wet ash conveyors, and a 15 minute metering bin capacity.
The drum dryer is 22 ft. by 110 ft. supported by a chips-fed metering bin capacity of 30 minutes. The system includes two cyclones and a 1200 RPM induced fan.
The dryer island also includes a single TSI wet ESP with four fields, and a TSI RTO with four combustion chambers and an exhaust stack height of 50 ft.
The facility has 2,000 tons of storage capacity in the dry storage silo if needed, another measure designed to keep pellet presses running if there’s a hiccup at the dryer.
The lion’s share of Fram’s Hazlehurst production, of which the facility tops 500,000 tons, is for indus-
trial use and therefore pressed in either 6 mm up to 8 mm sizes. This production is moved to the port of Brunswick and shipped to electricity generation markets overseas. The rest of production, about 100,000 tons per year, is for the home heating market and is pressed to 6 mm.
Pellet moisture content is under 6%, usually hovering around 5.5%. With the old dryer system, Arnold reports there was some inconsistencies in moisture content, which meant running material back through the drying system again. But, with TSI, those issues have dissipated.
Arnold says, “At the moment, everyone is happy and really liking the heat value. Durability has been as high as you can get. Fines are extremely low and moisture has been low as well.”
The increased output at Hazlehurst complements Fram’s pellet production at its Appling County Pellet, Archer Forest Products and Telfair Forest Products mills, giving the four sites a combined capacity of approximately 1 million metric tons.
Jason Yearty is the Plant Manager at Hazlehurst and Harold L. Arnold remains the President of Fram Renewable Fuels. Rusty Dubberly serves as Fram’s Operations Manager, in charge of all the plants.

Trucks are loaded in two minutes and a rail car 10.

April 2021 / Wood Bioenergy 17