
15 minute read
THE DRYER ISLAND
EDITOR’S NOTE: The following companies submitted these editorial profiles and images to complement their advertisements placed elsewhere in this issue. All statements and claims are attributable to the companies.
AIR BURNERS
The PGFireBox from Air Burners
As unwanted biomass is a sustainable energy source and its conversion carbon neutral, Air Burners has perfected affordable waste-to-energy technologies based on its standard products and air emissions control features. Energy released by wood waste combustion is harnessed and converted into green electricity, which is used onsite or sold to the utility. It can also be stored in readily available portable energy storage banks. Optionally, the same machine provides heat energy for product drying and heating of buildings. This is Air Burners well-established PGFireBox line with models from 100KW to 1MW+.
The PGFireBox is very simple to operate and is portable. It can “follow the waste” as the travel zone becomes unsustainable or the waste source is temporary. PGFireBox is a whole-log burner, simply meaning that no pre-processing of feedstock is needed. The chipping, grinding or pelletizing and related trucking of wood waste to make it suitable for most competing biomass plants is expensive and causes considerable pollution from the burning of hydrocarbon fuels by large diesels. None of that is required with the Air Burners machines.
Air Burners is pursuing several target industries for its PGFireBox, such as municipalities struggling with landfill diversion of woody biomass, sawmills that require power and heat for lumber drying, forest management operations tasked with wildfire mitigation and forest restoration, rural power companies looking for simple sustainable distributed power options, and military installations looking for reliable power backup options independent of petroleum-based fuel.
BAKER-RULLMAN
Baker-Rullman’s innovative triple-pass drum dryer design offers leading performance and efficiency in the smallest possible package size. A properly sized and tuned drum dryer system suited to your input volume is the key to planning an efficient system.
Three full length cylinders provide the maximum effective length and residence time in a very compact package. The drum drive uses specifically designed engineering class bushed roller chains and sprockets. Trunnion rollers are machined from a forged billet of 1060 steel with a minimum roller face hardness of 165 BHN. The internal tapered roller bearings, which have a “B-1” life of 15 years, allow the roller to rotate around our stationary roller shaft supported by our hold-down pillow blocks. This design has proven to be more reliable than the commonly used small diameter roller with an integral cast shaft.
The drum tire is hot forged from a single billet of AISI 1030 steel, then finish machined. There is no weld seam on it, and the steel grain structure is oriented for greater wear resistance and strength. To achieve efficiencies better than 1,500 BTUs per pound of water evaporated, the design incorporates longer residence times, robust temperature control and superior drum insulation. Precise electronic controls eliminate heat surges and fuel waste.
Consistent evaporation in Baker-Rullman’s triple pass dryer design protects wood biomass from under or over drying. Heavier, wetter product moves slower than fine particles, giving uniform drying to all particles. That’s why these rotary dryers have long been known for protecting the integrity of all types of material.
20 Wood Bioenergy / April 2021

High efficiency wood biomass drying
BRUKS SIWERTELL
Bruks Siwertell offers one of the most comprehensive ranges of conveyors on the market—from traditional belt and idler configurations and unique horizontal and vertical screw conveyors, to state-of-the-art, extremely efficient air-supported systems, including the Tubulator and the Belt Conveyor.
The Belt Conveyor is the future in belt conveying, combining the use of air-cushion technology with Bruks’ standard belt conveyors. Customers can benefit from a high-capacity conveying system that offers minimal equipment wear and very low operating costs because of reduced friction in the conveying line. The totally enclosed design protects the environment from dust emissions and reduces material losses.
With roughly 620 installations worldwide, the Tubulator is also an air-supported belt conveyor, built as a
closed system of steel tubes. Inside the tube, a rubber belt runs at high speed on top of an air cushion created by a series of in-line fans.
Both air-supported systems capitalize on the benefits of lowfriction conveying, delivering reduced operating and maintenance costs, with zero dust emissions and Bruks Siwertell conveyors for effiminimal material cient material flows losses.
In addition, Bruks Siwertell’s range of drag-chain conveyors offer a robust, effective method of conveying some of the industry’s hardest-to-handle products, such as stringy materials like unsorted bark. They are an optimum solution for the totally-enclosed transport of materials in applications with limited space.
Industry-leading innovations ensure that Bruks Siwertell’s range of conveyors consistently deliver smooth, safe, continuous material flows for minimal operating and maintenance costs. Systems can be configured to meet every requirement and can carry virtually any dry bulk material from low to very high capacities.
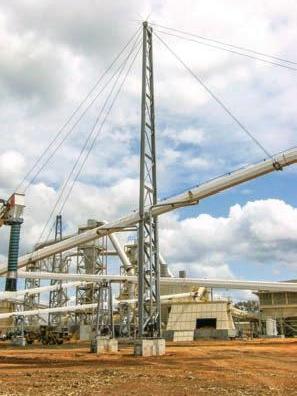
CAPTIS AIRE

Captis Aire delivers FBC technology.
Captis Aire has launched a new venture to transfer the Fluidized Bed Concentrator (FBC) technology to the wood processing industry. Since 2015, we have partnered with Environmental C&C to demonstrate the FBC’s ability to provide a capital and energy efficient industrial emissions control solution that reduces greenhouse gas emissions and optionally recovers valuable byproducts, such as terpenes, from wood drying. This effort included two successful pilot unit demonstrations at a commercial oriented strandboard (OSB) facility. Proprietary FBC technology is provided under license agreement to Captis Aire from the technology owner.
FBC carbon concentrator systems have been installed to treat exhaust volumes from 200 cfm to >100,000 cfm. Modular FBC systems can treat larger air volumes using a combination of multiple adsorber units. FBC units are most advantageous for treating dilute gas streams with concentrations in the 50-200 ppm range.
A case study at a commercial OSB mill successfully demonstrated >90% reduction efficiency of VOCs in two separate tests by two independent certified air emissions stack testing companies.
The attrition resistant sorbent, synthetic Bead Activated Carbon (BAC) is used worldwide. It can be regenerated continuously in unit. Or, BAC can be reactivated by California Carbon with a guarantee that it will be reactivated to 95% of virgin activity per ASTM D3467.
Compared to fixed bed adsorbent systems, the FBC provides superior mass transfer of emissions to sorbent through counter-flow fluidized adsorbent. Compared to an RTO or rotor, the FBC system reduces the number of moving parts.
The FBC can be either used with a condenser to recover organics or an oxidizer to efficiently oxidize the concentrated gas stream. The FBC is considerably lighter and smaller than competing RTOs providing roof mounting options. Compared to an RTO, the FBC reduces energy usage by up to 80% and greenhouse gas emissions by up to 60%.
Captis Aire has leveraged the benefits of partnering closely with Environmental C&C’s team who bring with them nearly 100 years combined experience.
EVERGREEN ENGINEERING

EE provides total engineering and design packages.
Evergreen Engineering is a full-service consulting engineering company, experienced in coordination of structural, electrical and mechanical engineering for
April 2021 / Wood Bioenergy 21
tube dryers, single-pass rotary dryers, triple-pass rotary dryers and belt dryers. Projects include RCO/RTOs, WESPs, and multi-clones for VOC and particulate emission control. We have provided designs for dryer islands that are compliant with NFPA standards regarding explosion prevention and explosion venting.
At a wood pellet plant in Brownsville, Ore., Evergreen provided civil, structural, mechanical, piping and electrical design, and control programming for a project that doubled the production capacity to 175,000 tons/year of the existing pellet plant. In addition to providing all the engineering for the project, Evergreen provided overall project management and startup assistance. The project included new material handling, sizing and screening, three new pellet mills, pellet cooling and a packaging line. A second dryer with a WESP and dust burner was also added.
Evergreen’s design covered equipment and WESP foundation; equipment supports and platforms; facility general arrangements; P&IDs and PFDs; design of fabricated equipment; and equipment selection including dust burner, material handling and sizing equipment, drying equipment, pellet production equipment, dust collection and conveying equipment, as well as design of natural gas piping system; new service transformer and switchgear; design of MCCs, VFDs and Softstarts; design of power, grounding, lighting and controls; PLC and HMI programming; and project management, including project budgeting and scheduling and contractor coordination.
HURST BOILER

Hurst offers modular package designs.
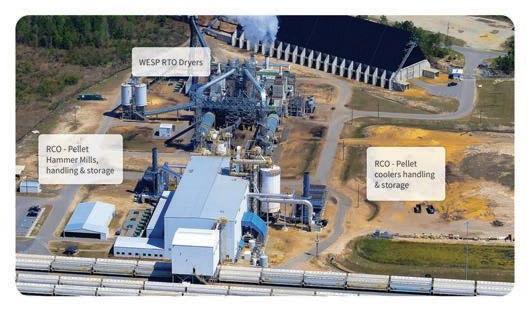
Hurst offers industrial grade wood fired burners with “clean-burn” stoker design, and modular packages available from 5 MMBTU/HR to 250 MMBTU/HR with operating temperatures from 200°F to 2000°F. These proven solid fuel burner systems are a leading choice in lumber dry kilns, boiler applications, oil heaters, rotary dryers, brick kilns and more. Hurst manufactures seven different types of biomass stoker/gasifiers, which have used 2,000+ different types of biomass fuels. Hurst is recognized for the highest code standards, innovative engineering and design, Energy Star rating, and renewable, sustainable solutions for green building design and operational efficiency.
Hurst STAG systems are a culmination of experience and knowledge of material handling, solid fuel combustion, and controls integration that offers a quality solution for most air heating applications. We are providing our customers the ability to economically and efficiently satisfy their air heating requirements by utilizing readily available waste as a fuel source in lieu of the expensive conventional sources.
The Hurst STAG unit can be utilized from 5 MMBTU/HR to 250 MMBTU/HR with operating temperature ranges from 200°F to 2000°F.
The Biomasster STAG control system developed for the direct fired burner is a computer based, data driven “SMART” monitoring and control system designed for the optimal clean combustion and operation of the direct fired burner system. It offers real-time modulation and reduces dirty flue-gas residue and hot ash carry-over issues.
Hurst equipment features a totally automated system; superior refractory material; automatic ash removal system (in wet and dry systems); ash sifting hoppers; a unique wall/grate interlocking discourages internal fuel leakage; reciprocating grate design— complete burn with automatic dust-free wet ash removal system. The modular packaged design means low cost project installation.
22 Wood Bioenergy / April 2021 NESTEC
Air emission control for industrial wood pellet plants
As modern economies transition from non-renewable energy sources and raw materials to those that can be naturally replenished, one of the most promising developments in this new paradigm has been the discovery of advanced new uses for wood and wood-based products. In the biomass sector, wood pellets have become especially well regarded in power plant electrical generation for their high durability and energy density.
Managing air emission control obligations for wood pellet facilities in the U.S. and other stringent regulatory environments requires understanding the complete plant operation, including not just the dryer island, but location of all emission VOC-HAP sources; wood source composition (ratio of softwood to hardwood) and associated potential emissions; proven air emission control features that have been effective at wood pellet facilities; and capital and operating cost analysis that identifies the best and most economical smart solution for the application.
A properly designed air emission control system can prevent lost production time, lower energy consumption, and reduce overall wood pellet production cost.
Specialized RTOs and RCOs have been developed specifically for wood pellet applications by NESTEC. Particulate matter (PM), alpha and beta pinene condensable and RTO-RCO non-uniform airflow can plug the regenerative heat exchange media, substantially reducing air emission control, increase operating costs, and limit the dryer pellet production capacity.
The first complete wood pellet air emission control system, in addition to the dryer exhaust, was installed in 2013 by NESTEC. It included RCO units that are still meeting air emission requirements today, with virtually no auxiliary fuel consumption.
NESTEC offers several proprietary, innovative, energy-saving features that can be incorporated initially or in the future.
POLYTECHNIK

Polytechnik installation in Croatia

Thermal modification of wood improves wood characteristics, increases durability and is often esthetical. Therefore those materials have a higher market value. Thermal modification is a large energy consumer. Depending on the setup, thermal consumtion goes up to 75% of the energy demand. Consequently, the energy center is becoming a focal point of the industry.
Process heat quality and reliable delivery directly impact the quality of the drying. This means that the boiler is a key component of the dryer island. We believe such heat production has to be based on low cost residues found within the production site; for several reasons: autonomy (fuel cost control), avoidance of waste removal costs, and circular economy principles to ensure maximum wood usage and zero waste. Such residues include mostly raw bark, chips with bark, and to a lesser degree sawdust and shavings because they tend to have a higher value. So combustion is key but that knowhow comes at a price.
The market is saturated with vendors that supply combustion solutions for dry and clean biomass; however, these are complete opposites to what a true raw residue stream with bark and hog fuel is. Polytechnik special combustion furnaces are tailor made for the worst kind of residues (M60, A10, P100) and operating conditions up to -60 °C, garanteeing output at all hours. Polytechnik has a few more improvements to offer: A new furnace that increases residence times for high efficiency and low emissions; poly held compact staged combustion furnace, which does not need any filter system downstream while having dust emission below 30 mg/Nm3 and efficiencies of 92%. Gasification reactor for wet fuels, which can be combined with gas engines to produce electricity.
When choosing boiler technology answer the following questions: 1. What are my fuel costs? 2. Is it more feasible to burn dry residues or sell them on the market? 3. Which is more feasible, wet or dry fuel? 4. Will I get the energy and quality of energy I require? 5. What are the guarantees and warranty? It pays to be flexible.
STELA
Stela low-temperature belt dryer, RecuDry
As a market leader in low-temperature belt dryers, Stela Laxhuber from Lower Bavaria continues to set new technology standards in the industry. Stela Laxhuber has improved its tried-and-tested technology and brought them to the market.
The pellet industry has been waiting a long time for more energy-efficient production facilities, not just in the field of drying. The technicians at Stela Laxhuber took up the topic at an early stage and found a solution
24 Wood Bioenergy / April 2021


that enables energy savings of up to 55%.
The Stela RecuDry system divides conventional technology into two drying areas. The Recu module saturates the drying air optimally by circulation and reheating. A partial stream of the saturated air is fed to the condensation module. The contained—mostly latent—energy warms the fresh air in the condensation module. By using an air-to-air heat exchanger, a large part of the energy used is thus recovered and guarantees a highly efficient drying.
The Stela Recu-Dry system makes it possible to retrofit existing plants quickly, is space-saving and costeffective, while also making a significant contribution to the reduction of emissions in the drying plant.
The steadily increasing number of realized projects in Europe shows the potential of the new technology and continues to make the industry take notice.

TRIPLE GREEN PRODUCTS
With the rising costs associated with using fossil fuels as a source of energy and the efforts being made to reduce carbon emissions, Triple Green Products wants the world to know that there is a better way. Triple Green Products’ BioDryAir system has been quietly supplying drying solutions to various industries for more than 10 years.

26 Wood Bioenergy / April 2021
Triple Green Products’ BioDryAir drying
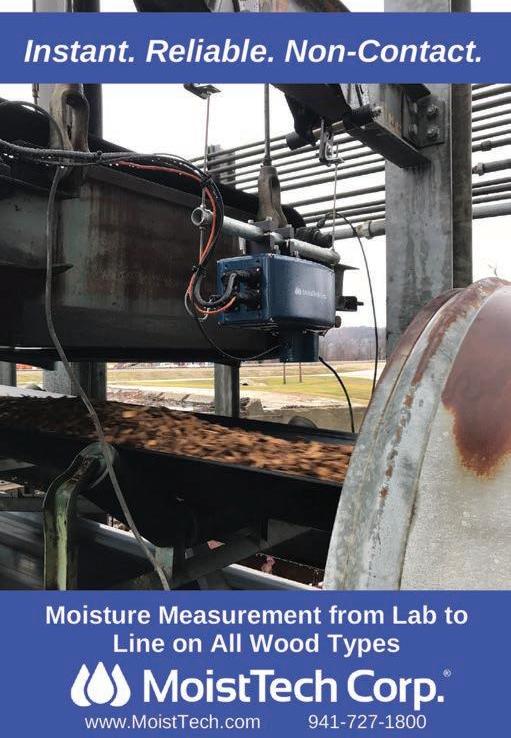
The BioDryAir system not only reduces operational drying costs by up to 80% over fossil fuels, it is also carbon neutral.
TGP offers systems up to 33,000,000 BTU on a single unit or can be supplied in multiples to achieve a much greater capacity. The BioDryAir supplies a very hot and much drier heat than either propane or natural gas making our system a much more effective solution.
BioDryAir operates seamlessly within current infrastructures— ease of adoption involves hooking it up to a rotary drum or a ducting system in place of the typical natural gas or propane burner.
TSI

Large format TSI dryers in a wood pellet plant
The TSI dryer island consists of single pass rotary drum recycle dryers combined with a heat energy system and pollution control equipment. TSI is a world leader in dryer technology being one of the originators of single pass dryer technology for industrial pellet production.
The pollution control systems for the dryers are designed by TSI engineers to meet regulatory requirements and can vary from high efficiency cyclones on smaller systems up to a combination of wet ESPs for particulate control and RTOs for destruction of volatile organics. Front-end heat energy systems can be either reciprocating grate furnaces (built in conjunction with Sigma Thermal) for wet bark fuel or fines burners for fuel derived from fine wood dust.
These three technologies form a process island with each technology entirely dependent on the correct functioning of the other two for a successful overall operation. TSI is the only North American company with a successful track record of large format dryers (up to 24 ft. diameter), and perhaps the only company worldwide that carries all three technologies as an in-house product. Not only does TSI offer a fully integrated package, they can also offer an installation, startup and training package—meaning the client has single point responsibility for the success of the entire island.
TSI experts are ready to assess any project and guide clients through the specification and design stages all the way through to ramp-up to full production.