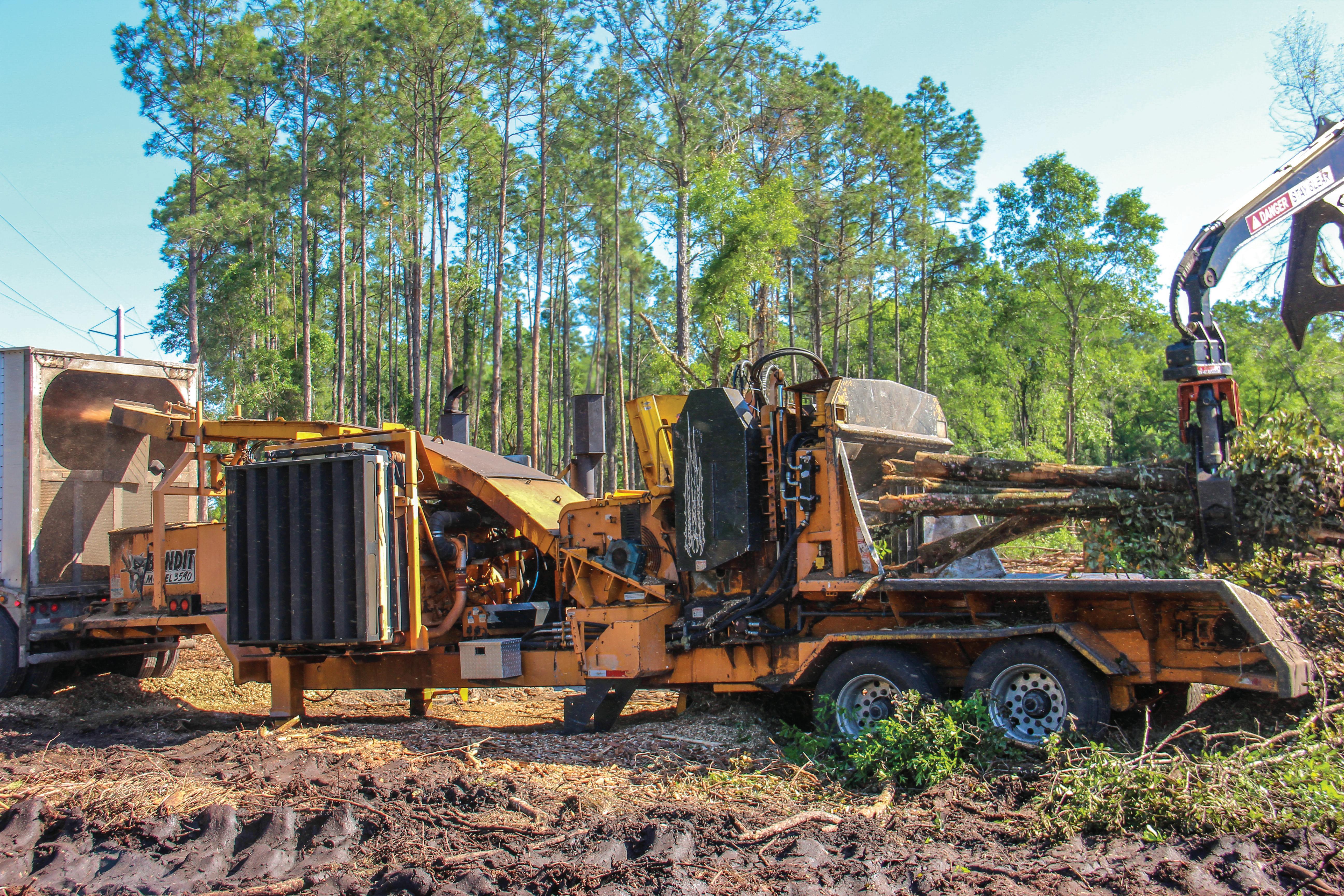
7 minute read
CHIPPER OPERATOR
Florida Logger Finds Success Supplying Power Plant
By Patrick Dunning
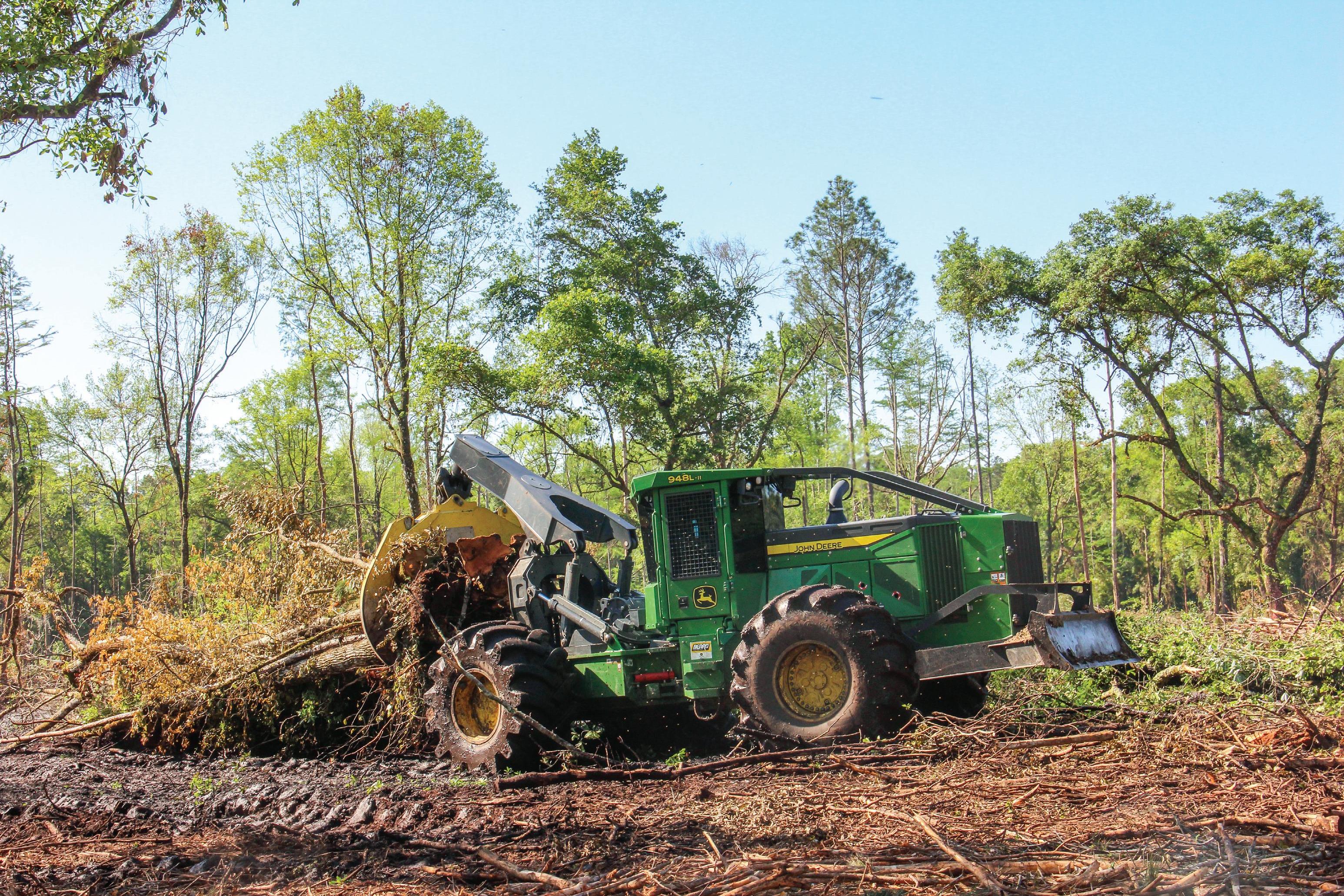
WILLISTON, Fla.
What began as a swamp and hill operation in 1971 hand-felling pulpwood in Williston, Fla., has diversified into a substantial chipping-for-biomass operation in recent years for William “Bill” Harrison, 69, and his company Harrison Logging Co. What brought the change? A variety of factors, but the biggest being the opening of a new market near Harrison’s home in Florida, a municipal electric utility burning wood chips for power, now operating under the name Deerhaven Renewable Generating Station. First brought online in late 2013 as Gainesville Renewable Energy Center (GREC), the 102.5 MW facility burns biomass chips sourced from the region Harrison cuts, so it was a natural fit.
Harrison has crews that contract cut for Columbia Timber Co., and have since the 1980s. Columbia had the first contract to provide wood for the Gainesville plant, and through that contract, Harrison was introduced to chipping-for-biomass. The logging company operated a Bandit chipper that Columbia purchased for a while, before stepping out on their own and purchasing a Bandit chipper.
In the beginning, the logging crew used the Columbia purchased Bandit 2590, but it quickly became evident that the market demanded a heavier-duty machine, and an increase in production. Now, Harrison operates three Bandit chippers, one 3590XL for M. A. Rigoni and two 3590s for Columbia Timber Co. producing a total of 250 loads of chips a week.
“The 3590 Bandit chipper helps us diversify our market and the landowners love it. Their land is clean when we leave,” Harrison explains of the machine and its re-
22 Wood Bioenergy / June 2021
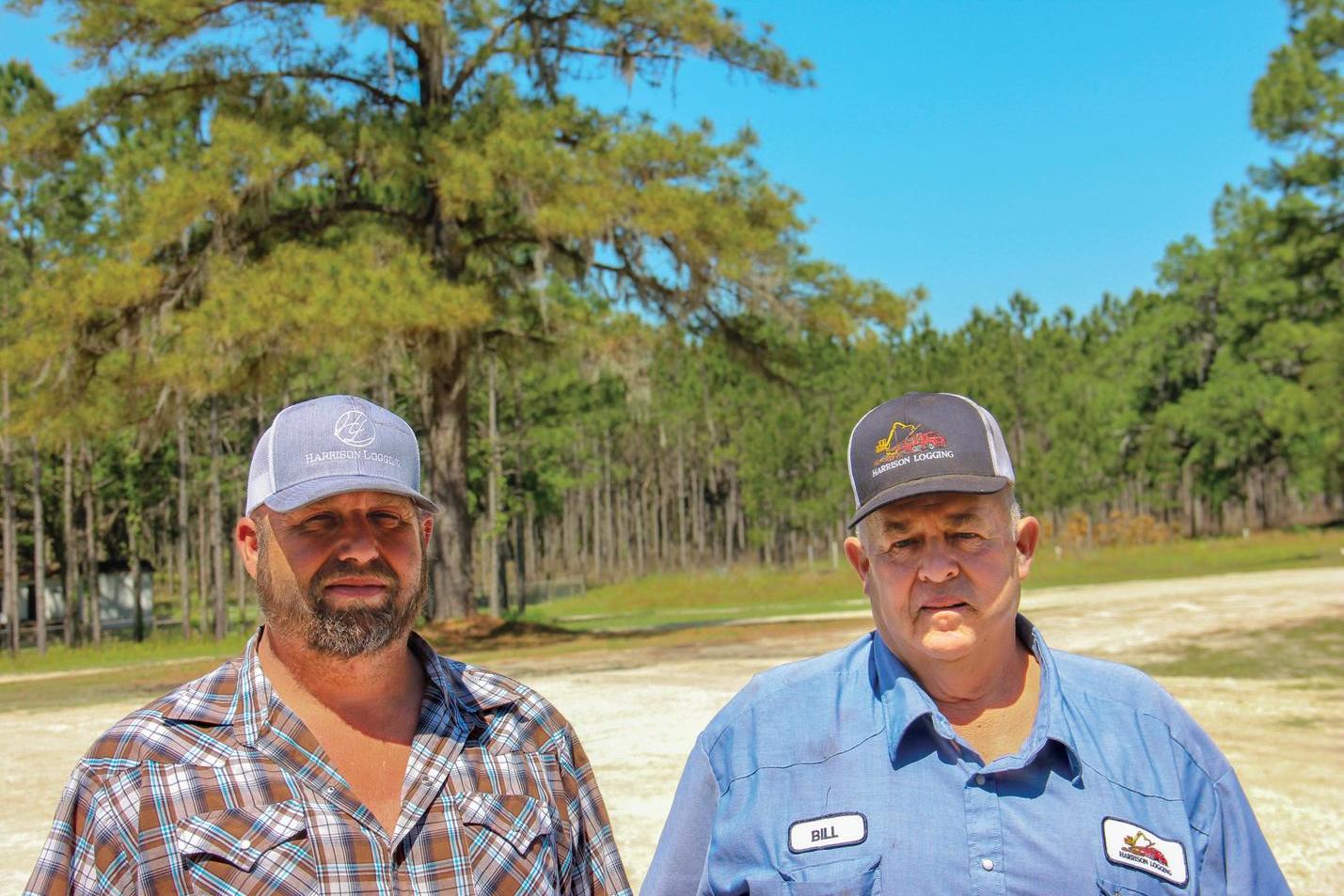
ception since being added to the equipment list as the biomass power plant’s demand rose. What might have taken months to cut, now takes Harrison a matter of weeks, and leaves the land cleaner.
For example, when Wood Bioenergy visited, the crew was chipping a 160-acre tract and was slated to finish the clear-cut in just under five weeks. “There is just not a lot of debris left when we leave,” he adds. “I wish there were chip mills everywhere. It would change the way people look at loggers. Sometimes we go behind pine crews and chip their block and it looks terrible. Not that they aren’t doing anything wrong, they just don’t have a chipper.”
On The Job
Harrison has always known what he wanted to do: “My mommy told me the first toy I asked for when I was a baby was a log truck.” At 18, he stepped out on his own and founded Harrison Logging. In ’87, he added a second crew—a few years after son Tripp, 45, joined the company.
In total, the company operates five crews (three chipping and two conventional logging). The chipping crews are set-up similarly, but not identically. One crew runs a 595 Barko loader, two 643L John Deere feller-bunchers, 948L John Deere skidder and 3590 Bandit chipper. One crew runs a Caterpillar 595B loader, DelFab threewheel feller-buncher, Cat 555D skidder and 3590 Bandit chipper. The other chipping crew runs a Cat 595B loader, John Deere 843L and 643L feller-bunchers, two 525C Cat skidders and a 3590XL Bandit.
Harrison prefers running two crews (one chipping and one conventional) on the jobsite simultaneously when a clear-cut block is available. “I like to have two crews on the same job that way the feller-buncher operator can cut everything as they go, put chips in one pile and pine in another, then carry it to whichever loader it needs to go,” he explains. “Pine is too thick to actually go through there and get the chipping wood out first. If you cut the pine first you’ll tear all the chip material down which makes it a nightmare to pick up. We prefer to run them together.”
Harrison Logging utilizes 22 Peerless and ITI chip vans, which under good conditions can be filled in 1315 minutes. Eight company trucks (a mix of Mack,
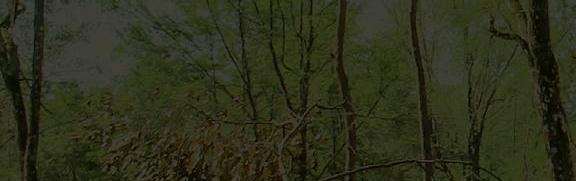
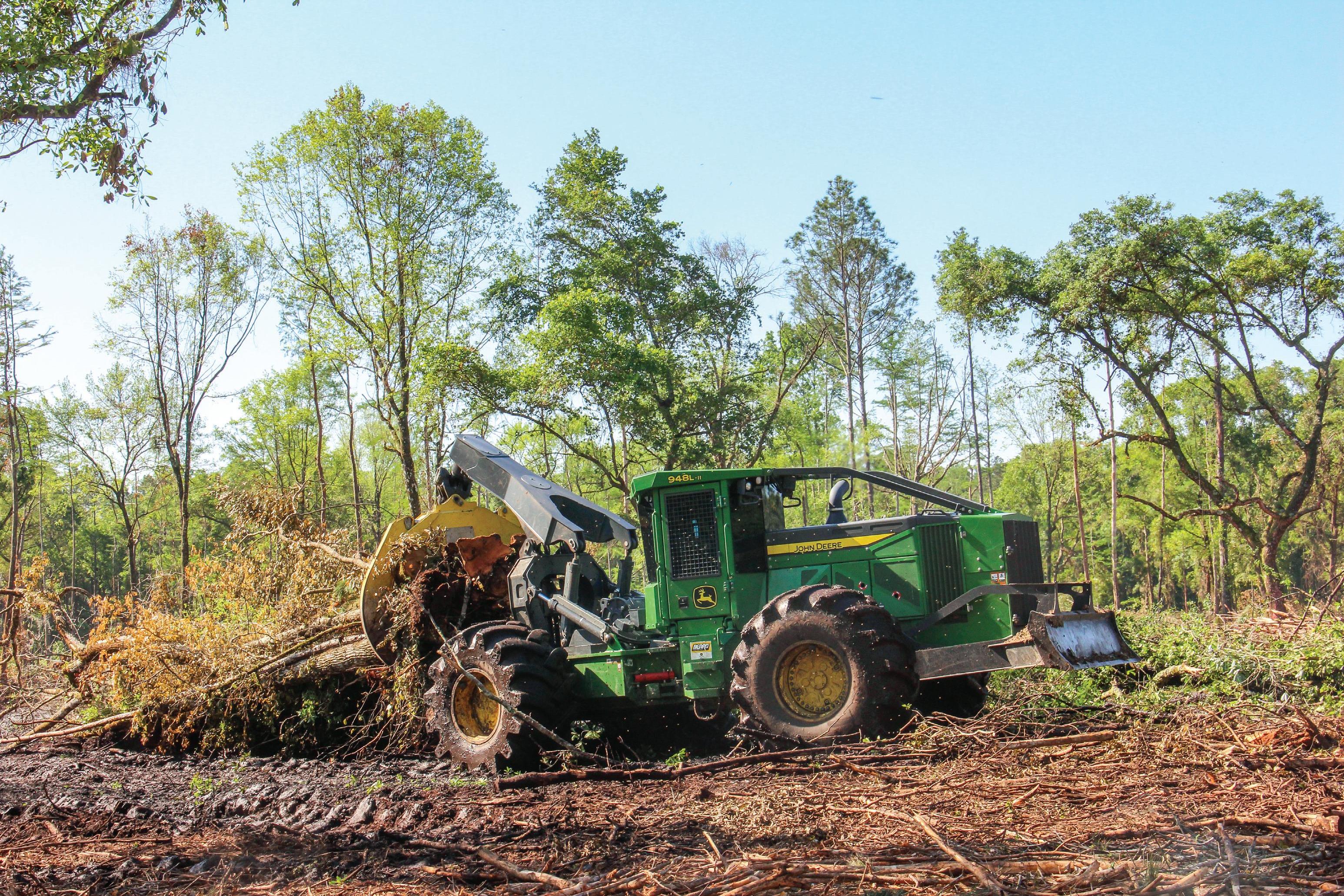
A mix of logging iron keeps Harrison’s three chippers steadily supplied with material. Tripp and Bill Harrison
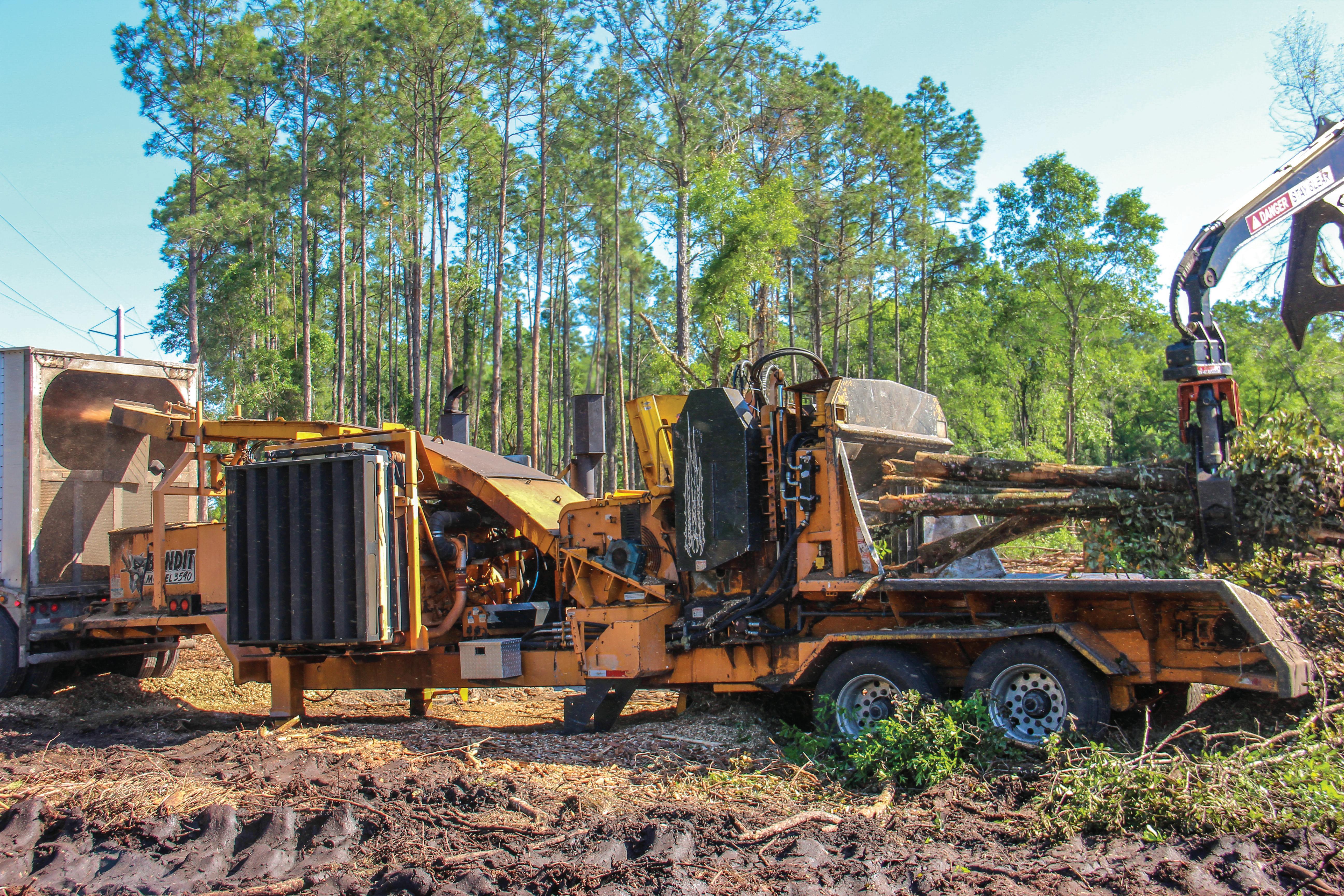
Western Star, Peterbilt and Kenworth) and 20 contract trucks get the production hauled.
In addition to Deerhaven, Harrison hauls pulpwood to GP, Palatka; WestRock, Maxville; a shavings mill in Cysero, and occasionally Rayonier, Fernandina Beach. Sawlog markets include Resolute Forest Products (Suwanee Lumber), Cross City; West Fraser, Lake Butler; West Fraser, Maxville; and Cross City Lumber, Cross City. Cypress logs are hauled to Cracker Style Log Homes, Williston; South Eastern Timber Corp., Lady Lake, takes mat logs.
While the crew hauls to many area mills, it’s clear both Bill and Tripp enjoy producing biomass chips. Tripp explains, “Future-wise were trying to produce more chips as long as the mills are wide open. I was out of town looking for a new chipper just a few weeks ago.”
Gainesville Still Likes Biomass
Construction on the Gainesville Renewable Energy Center (GREC) started in June 2011 and, when completed in October 2013, the $500 million, 102.5 MW biomass power facility began a nearly 10-year roller coaster ride of shutdowns, full-speed operation and acquisition. When the facility began commercial operation, with the intent to use 1 million tons of woody biomass annually, it faced significant scrutiny locally because of the costly and lengthy power purchase agreement between the city and the developers.
It then was plagued with other issues ranging from noise complaints to a lawsuit from one of its primary biomass suppliers over feedstock requirements. In late 2017, GREC was sold to Gainesville Regional Utilities (GRU), a municipal electric utility, owned by the city of Gainesville. This acquisition brought desperately needed diversity to GRU’s power generation portfolio—which has an aggressive longterm renewable energy goal.
Renamed Deerhaven Renewable Generating Station (DHR) following GRU’s acquisition, the plant provides reliable markets for fuel providers like Bill Harrison and is helping GRU towards its goal of becoming 100% renewable by 2045 across all generating sites.
“The DHR biomass plant is very important to the resolution. When you look at renewable energy in the state of Florida, your two options with current technology are solar and biomass,” Dino De Leo, GRU’s energy supply officer says. “Biomass is clearly a large portion of the renewable portfolio and will become even larger as we move towards our resolution.”
An independent energy services company operated and maintained the plant for two years from 2017-2019, until it transitioned to full GRU staffing in late 2019.
Reaching 100% renewable is currently impacted by natural gas pricing. GRU was 42% renewable in 2019 and 32% in 2020, due to the price point of natural gas.
“We have a responsibility to our customers to operate as efficiently and economically as we can, so when natural gas prices fell it did not make sense to run the biomass plant at higher loads,” De Leo says. “We still run it every day just not at higher loads because we can economically generate those megawatts at a lower cost with natural gas. Our obligation to our customers is to have renewable aspects of our generation but not to the point where it burdens them with higher rates.” De Leo says they tuned down the plant in 2017 from its previous minimum 70 MW load to 30 MW over the span of two months to preserve energy and associated costs. “The plant used to operate anywhere between 70-102.5 MW and did not fit our system very well,” he adds. “When everyone went to bed and load decreased we were dumping power into the grid below the cost of making it.” The plant now uses 30-35 MW on average in the mornings during lower loads and occasionally tops 100 MW in the afternoons based on customer demand and weather patterns.
At any one time there’s typically 30,000-40,000 tons of wood on-site that averages 19-30 days of operation— 2,400 tons a day full load average.
“We can’t keep wood in large quantities because of the decomposition of wood and we have to control the inventory based on needs,” De Leo says.
GRU’s integrated resource plan executes different goals and projections for higher renewable percentages with the understanding that technology evolves every seven years or so.
He explains, “When you think about the Deerhaven plant, it was put in service in 2013 as a 30-year plant and is scheduled to retire in 2043, so you could be looking at possibly two more biomass plants, based on the retirement of Deerhaven. Right now, our integrated resource plan does not call for another biomass plant; we won’t project that until we get there because we want to take advantage of the technology we have.”

24 Wood Bioenergy / June 2021