
13 minute read
IN-WOODS CHIPPING
EDITOR’S NOTE: The following companies submitted these editorial profiles and images to complement their advertisements placed elsewhere in this issue. All statements and claims are attributable to the companies.
Bandit
Bruks Siwertell

Since 1983, Bandit has manufactured equipment for a multitude of wood waste processing markets. The vision since the beginning is to build quality, highly productive, easy to maintain equipment providing years of dependable service. The commitment for quality, innovation and dedication is instilled in every employee and is one of the main reasons why Bandit became an employee-owned company (ESOP) in 2018.
Bandit’s line of whole tree chippers and horizontal grinders are either supported by a highly trained dealer network or the Bandit factory. For those supported by a dealer, each dealer has qualified sales, parts and service personnel that receive ongoing training from Bandit. These dealers carry a wide variety of parts and machines to meet your needs and are supported by Bandit regional sales and parts representatives. If there is not an authorized dealer in your area, then the Bandit factory would handle all your parts, sales and service needs. Bandit employs experienced and knowledgeable parts, sales and service personnel and has multiple service trucks on the road to service customers accordingly.
Bandit’s line of horizontal grinders known as “The Beast” are the most versatile units available on the market today. These units are the most efficient way to process wood waste. The heart of each Beast Recycler is a patented cuttermill that will cut material apart opposed to the beating action of competitive grinders. This process is best described by comparing an axe to a sledgehammer, which would you prefer to use to cut down a tree? A wide variety of towable and track units are available ranging from 18 in. to 45 in. diameter capacity and engine options up to 1,200 HP.
A line of durable and productive whole tree chippers is also available in capacities ranging from 18 in. to 36 in. diameter capacity and engine options up to 1,200 HP. Tracks can be equipped on most units and a cab and loader is available on select models. The patented slide box feed system provides unmatched pulling and compressing power reducing the need to trim or reposition material.
Bruks Siwertell is a market-leading supplier of dry bulk handling and wood processing systems. With thousands of installations worldwide, our machines handle your raw materials from the forests.
We design, produce and deliver systems for loading, unloading, conveying, storing as well as stacking and reclaiming dry bulk materials, alongside equipment for chipping, screening, milling and processing wood for the biofuel, board, sawmill, pulp and paper industries.
We are global and local. You will find main offices in Sweden, Germany, the U.S., China, Philippines, Russia and Taiwan, supported by a dedicated network of hundreds of representatives and dealers worldwide.
We deliver stationary and mobile chippers to match all needs. Wood chippers have been used for centuries making the most out of waste wood materials. Today’s machines have high-performance capabilities vital to supporting the booming renewable energy market, pulp industry and numerous other key applications.
Bruks Siwertell heavy-duty chipping machines, including both stationary and mobile chippers, are at the forefront of the industry, supplying facilities worldwide with high-capacities and quality wood chips. The size and variety of the wood to be processed are usually the deciding factors for which technology to select, but some industries require much greater control over chip size, while others need very low running costs.
Off-road chippers operate directly in the forest or nearby, handling residual production. The wood chipper is mounted most commonly on a forest machine type forwarder, but it can also be on dumpers, tractors or other purpose-built off-road vehicles.
On-road chippers operate directly in the forest by the
June 2021 / Wood Bioenergy 25
edges of roads, and transport the material, primarily residual products and tree parts, directly to the user. This system applies when using a truck as a chipper, on a trailer, or alternatively on a trailer pulled by a fastmoving farm tractor.
Bruks Siwertell has combined the best of our technologies to deliver machines that match all needs.
CW Mill
Do you need to go into the woods to grind? Look no further than a HogZilla track mounted tub grinder from CW Mill. HogZilla track mounted tub grinders come standard with a Caterpillar engine, torque converter drive and are available in model numbers HTC-1464T and HTC-1462T.
CW Mill Equipment Co., Inc. has been manufacturing track mounted tub grinders for 20 years. A HogZilla tub grinder on tracks is one of the most rugged heavyduty track mounted machines on the market, and our customers will attest to that. Jason Anderson with Missouri Organic, located in Kansas City, Missouri, says, “Their service is amazing. But then on top of that, these grinders are built stronger than anything else on the market.” Missouri Organic took delivery of a HogZilla HTC-1462T in early 2021.
A HogZilla on tracks is unparalleled in production and mobility; allowing for grinding in wet weather or on soft terrain; eliminating the need to build roads to get HogZilla moved and eliminating towing a truck and grinder on the job site; therefore saving hours a day moving from pile to pile; resulting in increased production. Clean up around and under the grinder is easier, which in turn reduces maintenance. Because the HogZilla on tracks is operated using a remote control, it allows for a one-man operation. The loader/excavator operator can stay in the cab while moving the track mounted HogZilla to different locations using a remote control. Hydrostat Pumps driven off the front of the engine allow grinding to continue while moving the HogZilla. Most other grinders require the operator to stop grinding before moving the grinder.
CW Mill is always looking ahead to see what can be improved for our customers, and each HogZilla is custom-built, how the customer wants.
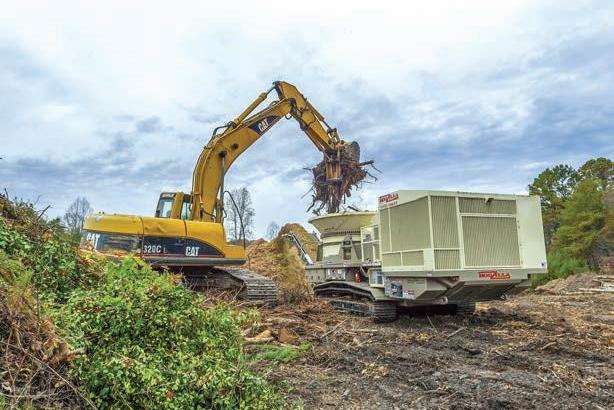
26 Wood Bioenergy / June 2021 Europe Forestry BV
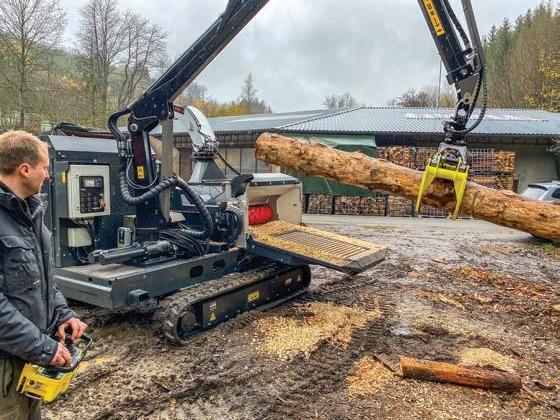
Europe Forestry BV from the Netherlands last year designed a brand new EC 640 wood chipper with an infeed opening of 600x400 mm, galvanized tandem trailer chassis, 175 HP engine, EFC crane 2050 that can lift 2 tonnes and have a reach of 5 m with the maximum weight of 3500 kg, to be road legal with a standard drivers license. Additionally, they just came out with a tracked version of the EC 640 on the same base as the trailer machine. Europe Chippers are built modularly, therefore using all the same components. The tracks can carry 6 dynamic tonnes and have a travel speed of 5 kilometers per hour in the high speed and 2 kilometers per hour in the low speed with double torque. The machines can climb steep hills up to 45°. The rubber tracks have seven support rollers with vibration dampeners. Dimensions of the tracks are 2500x300 mm wide. The total length of the EC 640 chipper is 3.5 m, therefore the overhang at the front and in the rear is only 50 cm.
On this new EC 640 clients can choose between two engine arrangements: Standard Europe Forestry supplied 175 HP engine or a C4.4 engine from Caterpillar/Perkins. For heavy duty activities, Caterpillar gives special arrangement with 140 kw between 1800 and 2000 rpm with high torque up to 750 Nm! It is this 10% higher torque that prevents the drum from blocking.
Another advantage of modular design is that clients can choose regular steel infeed plate or hydraulic foldable infeed table with hydraulic infeed chain. Clients also can choose the extra hydraulic operated bottom.
The standard Europe Forestry supplied hydraulic crane (EFC 2050) can lift 2000 kg at the boom cylinder and has a reach of 5 m; or clients can choose the
EFC4070 crane that can lift 4000 kg and has a reach of 7 m. All cranes will be supplied with proportional valves with radio remote control for the chipper and crane and with the grapple and rotator.
Europe Forestry sees a bright future for all EC 640 Europe Chippers, mainly because of their minimum dimensions that give maximum maneuverability, combined with maximum output. Plus, the big engine with 140 kw is the low fuel consumption of less than 7 L per hour average.
Tree Mech Ltd. represents Europe Forestry in the U.K.
Morbark

Morbark recently introduced a new, patent-pending Vtection system option for their 3000, 3400 and 6400 series Wood Hog horizontal grinders. The Vtection system monitors rotor vibration to reduce damage from contact with non-grindable objects or other causes of damaging vibration like an out-of-balance rotor, broken insert or defective bearing. When coupled with Morbark’s breakaway torque limiter, dual hammermill protection—both mechanical and electrical—is achieved.
To use the Vtection system, the operator sets an operating vibration level through the electronic controller. Since different feedstocks produce different vibration levels, the operator can quickly fine-tune the trip point to match the grinding application. Adjusting the trip point based on the feedstock can help avoid unnecessary stopping of the infeed from normal operating vibration.
If a non-grindable object enters the grinding chamber while in grinding protection mode, the Vtection system will sense the spike in vibration or trip point and instantly stop and reverse the infeed conveyor. By reversing the infeed conveyor, the vtection system lowers the rotor’s chance of repeatedly striking the foreign object.
Once the Vtection system is triggered, Morbark’s Integrated
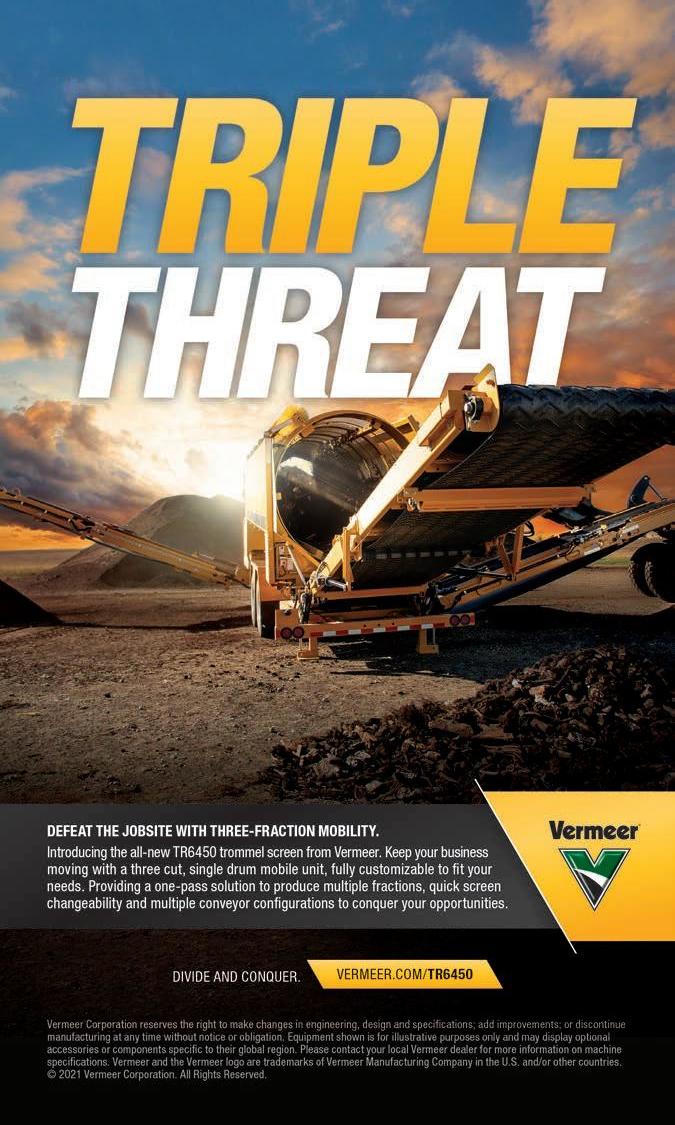
June 2021 / Wood Bioenergy 27
Control System (MICS) initiates several actions to remove the material out of the rotor area. The sequence of these actions includes reversing and stopping the infeed; bringing the engine speed to idle; disengaging the clutch, and displaying a warning message on the MICS screen. At this time, the operator can inspect the grinder and remove the object that caused the trip point before resuming operation.
The system cannot guarantee a machine is without a defect. Please use caution after the system trips and service work begins, as other components may have experienced damage.
Ship-out kits are available for in-woods installations on pre-existing 3000X, 3400X and 6400X horizontal grinders.
Precision-Husky
Since 1964 Precision Husky Corp. has led the industry in producing the highest quality, most rugged equipment available. That fact is evident in the Precision Husky whole tree chippers.
Built more rugged than the competition, the Precision Husky whole tree chippers are equipped with heavier trailer frames, oversized hydraulic stabilizers and the field-proven, industry-leading Precision chipper. Available in four sizes, from 58 in. to 86 in. models, roundwood capacities range from 18-30 in. in diameter. Each model comes with different number of knife options for many different applications and production rates and may be fitted with conventional or disposable knives. Depending on application and production, power options range from a Caterpillar or Cummins 500 HP (373 kW) diesel engine to a larger 1050 HP (783 kW) engine.
The engine is fitted with a totally enclosed, wet hydraulic PT Tech HPTO hydraulic power take-off, which acts as a torque-limiter by slipping to absorb the shock load. A microprocessor controller provides push-button engagement of the HPTO. The controller is capable of monitoring clutch pressure, temperature, filter condition, engine speed and clutch output speed.
The Precision whole tree chipper can be built with or without heavy-duty Husky loaders, may be trailer or track mounted, end or top loading. The Husky XL175 loader comes standard on chipper models 1858 and 2366, while the heavier XL-245 models are mounted on the larger 2675 and 3086 units. Models 2675 and 3086 come standard with a 15 ft. long chain infeed conveyor to allow the larger diameter stems to be consistently fed into the chipper.
Whether making micro-chips for the pellet industry or chipping 3 in. metallurgical chips for electric smelting the Precision chipper is a cut above the competition.
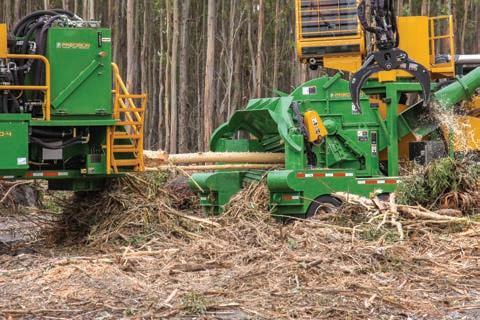
28 Wood Bioenergy / June 2021 US Blades
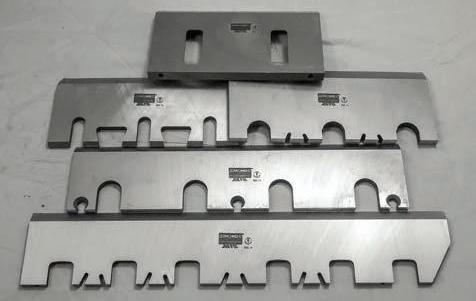
US Blades and the Wood Fiber Group provide the highest quality chipper and counter knives, anvils, knife holders, clamps and chipper parts for portable and stationary chippers. Our products are American made and shipped from various stocking locations around North America. The quality of our products are second to none and manufactured to the tightest tolerances in the industry. Inventory is shipped from stock typically.
US Blades not only provides premium knives and parts, we also service the products we sell. Our service area covers from Maine to Texas with US Blades trucks providing weekly pick-up and delivery from four strategically located service centers. Knives are sharpened, honed, babbitted and returned ready to run. Whether you are chipping for fuel, paper or micro-chipping for pellets, we have a service program that is tailored for your operation. We’ll help you minimize your cost with longer running knives that are professionally sharpened.
With 14 trucks running and 5,000+ inches of grinding capacity, you will never need to worry about running out of knives. Our knowledgeable staff can help with technical assistance if needed.
Vermeer
Vermeer offers two electric-powered trommel screen models for biomass producers looking for ways to help reduce exhaust emissions, noise levels and maintenance. The newest addition to Vermeer electric-powered recycling product line, the TR5300EM trommel screen, can produce up to 100 cubic yards (76.5 m3) per hour with .50 in. (12.7 mm)
screens when material moisture is at less than 40%. For larger production needs, choose the Vermeer TR626EM trommel screen with the capability of running up to 200 cubic yards (152.9 m3) per hour in with similar material.
The Vermeer TR5300EM is powered by an industrial-duty, fancooled 60 HP (44.7 kW) electric motor and delivers a drum speed of 0-24 revolutions per minute to handle multiple material types, including biomass. The quiet-operating TR5300EM also features a low hopper infeed with a capacity of 5.5 cubic yards (4.2 m3) and includes new service and operating enhancements.
The hydraulically driven drum on the TR5300EM is 15 ft. (4.6 m) long and 5 ft. (1.6 m) in diameter to optimize material processing and deliver a high-quality end product. Quick-change screens and a quickchange drum help make it convenient to perform sizing adjustments. The TR5300EM also features several access doors to help with servicing and a set of dual-hinged doors on both sides of the machine for full access to the drum at ground level.
The Vermeer TR626EM features a 6 ft. (1.83-m) drum and a hopper that holds 6 cubic yards (4.6 m3) of material, and is powered by two industrial-duty, fully enclosed and fan-cooled electric motors. A single 150 HP (112-kW) motor powers the hydraulic pump stack while a .75 HP (.6-kW) motor powers the cooling fan for the hydraulic system. It can be outfitted with a 180° arc radial stacking conveyor to increase the amount of material being stacked on the ground. The adjustable stacking height aids with dust control and helps to prevent material from blowing away.
Both Vermeer electric-powered trommel screens provide access to service areas and can be operated through either the Vermeer DP10 display mounted on the control panel or through a handheld transceiver remote. From either control, the operator can choose from four programmable presets or adjust on the fly based on the incoming material.
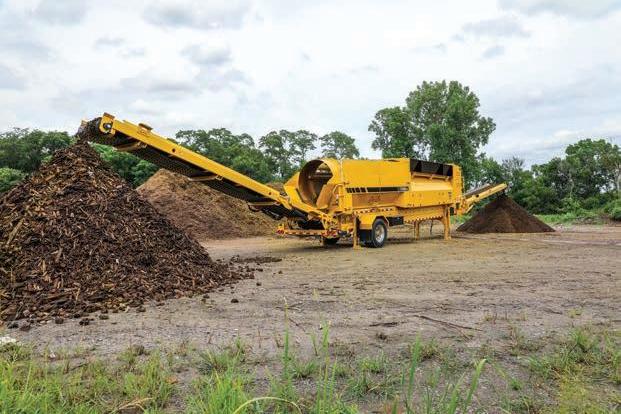
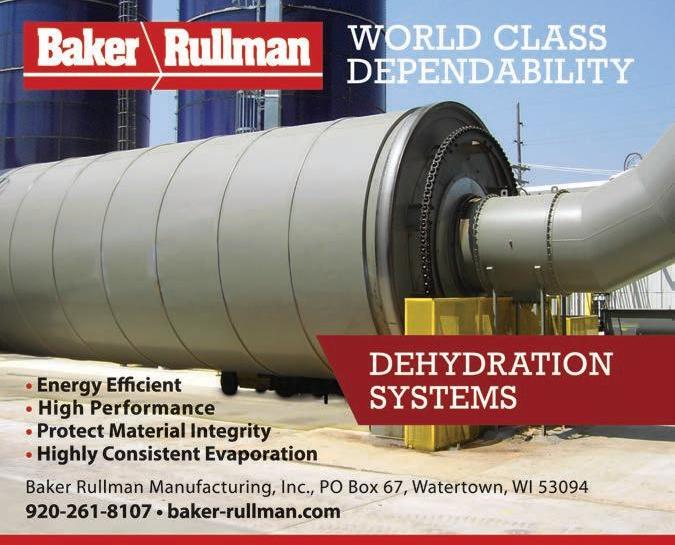

June 2021 / Wood Bioenergy 29