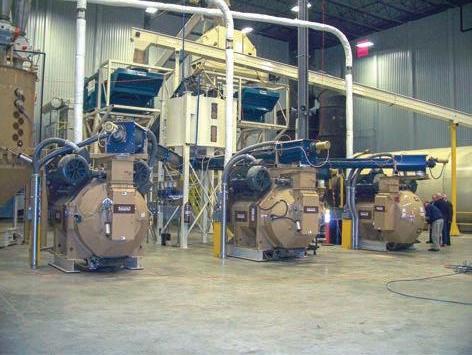
16 minute read
DRY END PELLETING
EDITOR’S NOTE: The following companies submitted these editorial profiles and images to complement their advertisements placed elsewhere in this issue. All statements and claims are attributable to the companies.
BIOMASS ENGINEERING & EQUIPMENT
BLISS INDUSTRIES
As the pellet industry has grown, so have the demands on material handling systems. Old technologies no longer suffice in a market where efficiency reigns and even short disruptions can cost hundreds of thousands of dollars. Yet options available to manufacturers are by and large little different than a century ago. It is this deficiency that Biomass Engineering & Equipment (BE&E) sought to address when it launched in 2011. A decade later, BE&E is fast becoming the premier supplier of bulk-handling equipment for the biomass industry with installations around the globe.
Discontent with the status quo, BE&E has engineered machines designed to address challenges associated with handling biomass. Chief among its solutions are SMART Conveyors. The conveyors’ unique design reduces wear and friction to effectively lower the costs of ownership by decreasing maintenance and unscheduled downtime. The machines’ modular construction further reduces costs by speeding build time. SMART Conveyors come in three standard heights and in widths ranging from 18 to 72 in.
Also popular in the company’s lineup is its SMART Floor, a push-pull system for reclaiming bulk materials. The floor provides first-in, first-out performance and delivers superior material control compared to chain floor and moving floor reclaim devices. Other equipment BE&E offers includes metering bins, surge bins, screw feeders, trailer load-out stations, and SMART Containers—stackable, modular storage units that feature the company’s push-pull floor system. All BE&E equipment is available with NFPA-compliant safety features.
BE&E’s innovative designs have won attention from manufacturers across the globe. Pellet customers include LJR Forest Products, Drax Biomass and Pacific Bioenergy, whom have either repeated orders or have ordered BE&E’s equipment for multiple sites. Outside the pellet industry, BE&E has supplied companies like Telfair Forest Products and Arauco, which have ordered SMART Conveyors time and again.
BE&E’s success is due not only to its equipment but the team behind it. Every member of the sales and support team has years of experience in wood industries and understands the challenges their customers face. It’s this knowledge that allows BE&E to provide solutions that work well and that serve its customers well in the long run.
18 Wood Bioenergy / August 2021
Bliss Industries, founded in 1981, is a U.S. manufacturer of robust wood reduction and pelleting equipment. We have always worked closely with our customers from testing their products in our lab and sizing equipment to providing quality manufacturing and service. l Hammermills: Bliss Industries manufactures a comprehensive line of hammermills for grinding everything from bark to wood flours. Our hammermill line consists of nine different diameters, 12 different widths and five individually distinct designs. Horsepower range is from 500 to 600, which makes it easy to find the correct mill for your application. l Pellet Mills: We offer a variety of models ranging from 21 in. diameter dies to 34 in. diameter dies. Our 3roll design along with the feed cone system delivers even striations throughout the body of the pellet. Resulting in uniform wear within the pelleting chamber and a high quality finished product. Our two-stage twin drive offers greater flexibility and allows for lower electrical demand at start-up. This along with a host of other user friendly features makes Bliss the obvious choice. l Coolers: Visit with us about the circular solution to counterflow cooling. The Bliss OP><FLO Cooler incorporates a well-engineered design for a high degree of quality production, low maintenance and minimal down time. l Testing Facility: Our new state-of-the-art testing center is ready for all of your testing needs. We offer material testing and analysis for all pelleting and size reduction projects. With years of testing experience, our engineers can help analyze the results and offer suggestions as to the proper equipment required for your application. l OEM Parts: Contact our office for original manufactured parts for your Bliss equipment, for a quick turnaround.
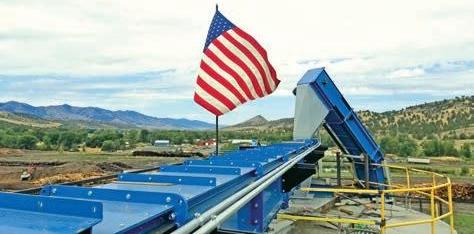
HURST BOILER
Hurst direct-fire burner systems are industrial grade wood fired burners with the Hurst “clean burn” stoker design. Modular packages available from 5 MMBTU/HR to 250 MMBTU/HR, with operating temperature ranges from 200°F to 2000°F, these proven solid fuel burner systems are a leading choice in lumber dry kilns, boiler applications, oil heaters, rotary dryers, brick kilns and more. Hurst manufactures seven different types of biomass stoker/gasifiers, which have used 2,000+ different types of biomass fuels. With installations across all industries worldwide, Hurst is recognized for the highest code standards, innovative engineering and design, Energy Star rating, and renewable, sustainable solutions for green building design and operational efficiency.
The Hurst Stag systems are a culmination of experience and knowledge of material handling, solid fuel combustion, and controls integration that offers a quality solution for most air heating applications. We are providing our customers the ability to economically and efficiently satisfy their air heating requirements by utilizing readily available waste as a fuel source in lieu of the expensive conventional sources. Hurst delivers the quality and performance that customers expect in a custom engineered solution to reduce operating expenses and maximize productivity. l Biomasster Stag control system developed for the direct fired burner: This computer based, data driven smart monitoring and control system is designed for the optimal clean combustion and operation of the direct fired burner system; and offers real-time modulation while also reducing dirty flue-gas residue and hot ash carry-over issues.
Hurst offers a selection of equipment to meet various needs inside a facility, including rotary dryers, sand dryers, grain dryers, lumber kilns, cement kilns and brick kilns.
Hurst equipment features a totally automated system; superior refractory material; automatic ash removal system (both wet and dry systems); ash sifting hoppers, and unique wall/grate interlocking discourages internal fuel leakage. The reciprocating grate design offers a complete burn with automatic dust-free wet ash removal system, while the modular packaged design means low cost project installation.
Hurst Boiler is a leader in the development of boiler technology as well as sustainable solutions for renewable energy. KESCO
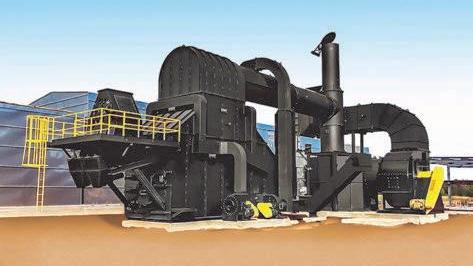
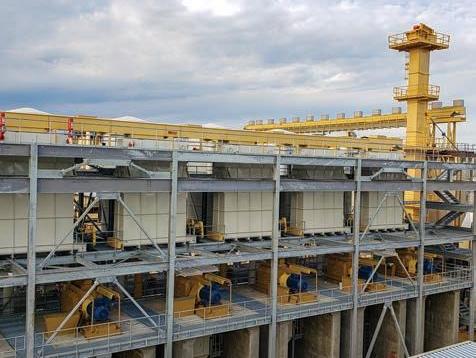
KESCO specializes in system design, equipment supply, project and construction management, commissioning, and after-sale service to the biomass and wood pellet industries. We have worked with our team of strategic partners for 20 years—each of our strategic partners are leaders in their respective fields. KESCO provides direct access to these manufacturers without having to deal with a third-party engineering firm. We utilize the engineering resources of each manufacturer, communicating directly with one another, to develop the most efficient system. KESCO Engineering operates as the system integrator, making these direct connections seamless. We bring in outside engineering firms for structural, civil and environmental work. KESCO handles the process design. This direct access to real-life solutions saves the customer months of delay and hundreds of thousands of dollars in boiler-plate nonsense.
KESCO’s strategic partners include: l Bliss Industries LLC: Hammermills, pellet mills, pellet coolers, shredders, rotary feeders, roller mills, and impact mills l Rapat Corp.: Belt conveyors, drag conveyors, bucket elevators, structural steel towers, support bents, truss, walkway, and chute work l WAM, Inc.: Screw conveyors, multi-screw feed bins, shaftless screws, super sack loading and unloading systems, retractable loading spouts, and vibratory bin bottoms l Tarsco Bolted Tank: Epoxy-coated bolted tanks, stainless steel bolted tanks, firewater tanks, structural steel supports, and installation crews with outstanding safety records l Puritan Magnetics, Inc.: Rotary drum magnets, drawer magnets, grate magnets, plate magnets, spout magnets, hump magnets, air-vey magnets, suspended belt magnets, head pulley magnets, liquid trap magnets, and customized magnetic systems l CV Technology, Inc.: Explosion vents, flameless vents, pressure detection, chemical suppression and isolation, pinch isolation valves, flap isolation valve, slide gate isolation valve, infrared detection, water mist sup-
August 2021 / Wood Bioenergy 19
pression, and gas detection l Kice Industries, Inc.: Dust collectors, cyclone collectors, airlock valves, centrifugal fans, PD blowers, multi-aspirators, diverter valves, slide gates, plus Rockwell Automation as a strategic partner
KESCO has partnered with these companies to provide complete wood pelleting plants while supplying portions of the process throughout North America. KESCO and our strategic partners have developed the expertise necessary to deliver a reliable, robust, and efficient turnkey solution.
Put a KESCO solution to work for you. Experience matters!
PAL
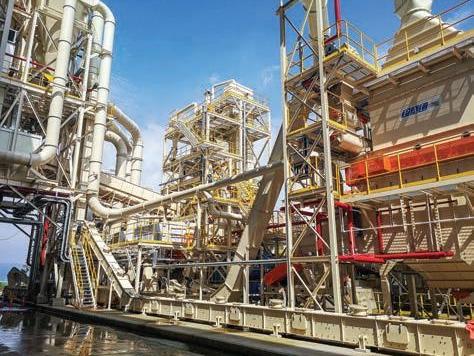
Founded in 1978, the Italian company PAL has been market leader for almost 40 years in wood preparation and cleaning for the production of wood based products. Relying on its experience, on a highly-skilled, inhouse technical team and a staff of more than 140 employees, PAL is able to supply engineering and machinery for the construction of complete plants tailored to suit a client’s requirements.
Combining experience and most importantly feedback from our customers, we had understood that pelleting was searching for significant improvements and innovations in the design: With this in mind our engineers set out to develop a family of pellet presses, specifically designed for processing wood fibers, that would raise the bar and meet the expectations of the pellet manufacturing industry. This was achieved some time ago and given the product name of Dyna Pellet Press.
Following the introduction of the Dyna Pellet Press into the manufacturing environment, the achieved performances are exactly accordance with our technical expectations some of which were to eliminate, as much as possible, any elastic instability or flexibility in the cinematic chain composed by shaft-supports for the rolls was the right approach for introducing something new in the market; and make the biggest pellet press (for now!) with a 1.2 m die diameter, that is performing more than 12 t/h with softwood and 10 t/h with hardwood, driven by a frequency converter at lower Hz value than the nominal one.
Where others have failed we have succeeded in producing quality pellets in the most difficult circumstances, given the robust design and strength of all the critical components, regardless of the input fiber—for example the pelletization of torrified bagasse. l Pallet blocks and pelleting, new project for BSC: The project is a combined plant where two lines, one for the production of pellets and one for the production of pallet blocks, utilize the same material preparation machinery. To have satisfied customers fills us with pride and it is great to feel part of their growth. l Hanwha, Korea’s largest pellet plant: At the end of 2020, a new 320,000 tonnes per year wood pellet plant entered into operations in Goseong-gun, Gyeongnam, South Korea. Not only is the SY Porto facility the largest to date in the country, it is the largest pellet plant project manufactured and supplied by the IMAL-PAL Group. The new pellet plant has been commissioned by plant manufacturer Hanwha Corp. Machinery, a member of the Hanwha Group, which carried out the entire process from planning to handover of the project to the final customer, SY Porto Co. Ltd, a Shinyoung E&P Co. Ltd company. South Korea’s largest, and one of southeast Asia’s larger wood pellet plants, it is the third plant for Shinyoung and represents a doubling of production capacity for the company. l Desmet: At present, the line in France is 20 t/hour of torreified pellets; we supplied a reception, preparation and cleaning area, including a turnkey electrical system. l Arbaflame: In Norway, you find our wood chip refining area, plus the entire pelleting area that includes storage silos, conveyor belts, press, cooler, pellet storage and truck unloading.
20 Wood Bioenergy / August 2021 POLYTECHNIK
Polytechnik sets a new milestone in New Zealand—among the best providers in technology and price, Polytechnik has new biomass boilers with an output of 15.6 MWth, which are earthquake-proofed for the affected area in Christchurch, NZ. The Minister for Climate Change, James Shaw, came to look at the new energy center, and said: “These new woody biomass boilers are really going to help us in terms of reducing our emissions. It will be great when we can decommission the current coal-fired boilers.” The biomass plant will be finished in Autumn 2021.
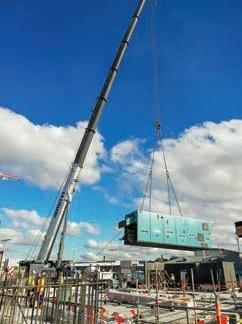

Drax Purchases Westervelt’s Share
Drax is acquiring Westervelt’s 20% minority interest in Alabama Pellets, LLC—the joint venture that owns the pellet plants in Demopolis and Aliceville, Ala.—for $29.7 million. The acquisition increases Drax’s interest in Alabama Pellets to 90% and provides Drax with economic control over a further 130,000 tonnes of pellet production capacity per year.
Drax gained majority control of the two pellet plants when it purchased Pinnacle Renewable Energy earlier this year. Westervelt, which had originally built the Aliceville plant, and subsequently sold the majority control of it to Pinnacle, ultimately maintained a 20% arrangement with Pinnacle in both the Aliceville and Demopolis plants, which carried over when Drax purchased Pinnacle.
Drax has been in discussions with Alabama Pellets joint venture partners regarding future working relationships, including their minority interests. The remaining joint venture partner, Two Rivers Lumber Co., LLC, still holds a 10% economic interest.
Demopolis and Aliceville have a combined nameplate production capacity of 660,000 tonnes per year. Aliceville was commissioned in 2018 and Demopolis (which was constructed by Pinnalce), is expected to be commissioned in 2021.
Drax Group has 13 operational pellet plants (including Aliceville) plus satellite plant developments and the Demopolis startup, which will ultimately give Drax a nameplate production capacity of 4.9 million tonnes per year.
Arbaflame Says It’s Ready To Roll
Arbaflame reports it is ready to start up the company’s first commercial full-scale factory in Kongs vinger, Norway. Arbaflame has developed patented wood pellets which it says will replace coal and cut CO2 emissions by 90%. In addition, it will produce valuable biochemicals.
“We have global growth ambitions that represent a major industrial investment in a Norwegian perspective. Our goal is to build a large Norwegian industrial company—step by step—that will replace parts of today’s coal power production,” says Bjørn Halvard Knappskog, CEO of Arbaflame.
The Norwegian company was founded in 2005 and has developed technology that recycles biowaste from sustainable forestry to renewable energy. By replacing coal with wood pellets, CO2 emissions can be cut by 90% in addition to supplying biochemicals as a byproduct such as bioplastics, proteins and dyes. The first factory has a production capacity of 1,500 tonnes of biochemicals in addition to 70,000 tonnes of pellets. With a possible global market of more than 7 billion tonnes of coal per year, Arbaflame plans to build a number of new factories, either alone or with partners.
“The completion of our first full-scale factory, which is based on more than 10 years of research, development and testing, is a ma jor milestone for us at Arba flame,” Knapp skog adds. “We are looking forward to getting started with com mercial production in Kongs vinger and to distributing the first deliveries of environmentally friendly wood pellets to Power Plant Rotterdam. It is a victory for the Norwegian forest industry and its renewable goals that, with Norwegian feedstock produced at our new factory, the coal plant in Rotterdam can reduce its emissions by approximately 140,000 tonnes a year.”
Arbaflame’s pellets are called ArbaCore and have been tested and verified at 15 energy plants operated by nine different companies in Europe, Japan, the USA and Canada. ArbaCore will be a full-fledged green coal substitute.
The pellets have virtually the same properties as coal, are waterresistant and have high energy density. The special properties mean that the cost of converting the coal power plant is significantly reduced.
22 Wood Bioenergy / August 2021
SFI Grants Focus On Partnerships
Sustainable Forestry Initiative (SFI) announced 13 SFI Community Grants featuring collaboration between 63 partner organizations. SFI Community Grants make a mean ingful impact in the communities that live and work near forests. This year’s grants support SFI’s mission of advancing sustainability through forest-focused collaboration by addressing relevant challenges facing communities.
The grants address key themes across SFI’s work including urban and community forestry, forest literacy and education, building a diverse and resilient workforce, promoting Indigenous forest stewardship, and connecting communities to conservation.
Some of the grant highlights include: l Michigan State University Dept. of Forestry will expand course content on forest carbon to create case-study-based materials for for esters, planners, builders, and decision-makers in cities and municipalities. l Waukesha County, Wisconsin, is completing its urban forest management plans for wood that must be removed due to disease, pests, or other circumstances. l The New Hampshire SFI Implementation Committee is bringing teachers together for a four-day work shop featuring forest and mill tours in July. l Students at the University of Miami School of Architecture will experience timber harvesting in a sustainably managed forest. l Ducks Unlimited Canada will provide training and resources to for estry students and Indigenous communities across Alberta to ensure better understanding of the role
of sustainable forest management in effective wetland conservation. l Clemson University is helping to address the future that women landowners will play in sustainable forest management through the Women Owning Woodlands (WOW) network, which will facilitate specific skills development for women landowners including chain saw and pesticide safety.
GreenWood Names Head Of Timberland
GreenWood Resources has appointed Chris Lipton as Head of Timberland Investment. Based in Portland, Ore., Lipton will oversee a team of 200 employees in 10 countries and will be responsible for GreenWood’s investment platform and operations. He will also develop the company’s future strategy for timberland development.
GreenWood is one of the top 10 managers of timberland globally with more than 741,000 acres across all assets and $1.7 billion of assets under management.
Lipton joins GreenWood from Hancock Natural Resource Group, where he was managing director for Timberland Mergers & Acquisitions. Previously, Lipton held senior positions at BTG Pactual Timberland Investment Group and Longview Timber Corp., where he developed extensive experience lead ing all phases of timberland transactions and operations throughout North America, South America and Australasia.
ALC Names Dane As Executive Director
Scott Dane is the new Executive Director for the American Loggers Council (ALC), replacing retiring Danny Dructor, who has been with ALC since July 2001.
Dane brings with him a vast amount of experience working with timber harvesting and timber hauling associations, having been the executive director for the Associated Contract Loggers and Truckers of Minnesota for the past 17 years. Dane, who spoke at the Republican National Convention last summer, has experience in both the state and national levels in issues impacting timber harvesting and timber hauling.
Dane has been a critical component of the ALC’s work to gain financial assistance for those businesses impacted by the COVID-19 pandemic. He has also been involved in legislation allowing state legal weight tolerances on the Federal Interstate Highway System and other ALC initiatives like the Future Careers in Logging Act.
The ALC office is relocating from Texas to Minnesota.

August 2021 / Wood Bioenergy 23