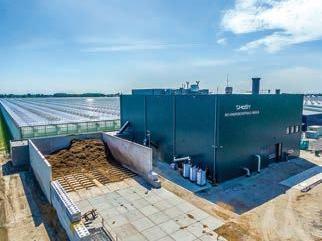
11 minute read
PRODUCT NEWS
HoSt Reveals New Bioenergy Plant
HoSt reports it has succeeded, after a decade of research, development and innovation, in developing a high-tech bioenergy plant with highly innovative NO-NOx thermal energy conversion of residual wood and residual waste streams. HoSt innovates with thermal conversion technology and deHighlights include: velops clean bioenergy plant l The technology achieves NOx (nitrogen oxides) emissions at less than 95% of the emission of natural gas: <2.2 mg/Nm3 well below the national emission limits of 145 mg/Nm3 l kNH3 slip (ammonia) of <0.06 well below national emission limits of 30 mg/Nm3 l Particulate emissions of 0.5 mg/Nm3 well below national emission limits of 5 mg/Nm3 l Distinctive innovative NO-NOx thermal conversion technology l CO2 capture for utilization, sales or storage possible (liquid and gaseous) l Fuel: regionally available residual and pruning wood and other residual streams from for example sawmills, RDF, and agricultural waste
HoSt’s mission is to remain at the forefront of hightech energy conversion from low-value unused residual streams that are available in abundance worldwide and for which no alternatives are available. The 15 MW bioenergy plant in Andijk, Netherlands with NO-NOx thermal conversion technology is the product resulting from years of research and innovation.
Independent measurements show that the plant produces energy from prunings and residual waste wood with a NOx emission reduction of >99%. This is achieved by HoSt NO-NOx technology in combination with ultra low-NOx innovative combustion technology, precise combustion temperature control and highly automated control. In addition to clean conversion and very high availability, the HoSt design ensures streamlined fast construction on site due to its modular and innovative construction, resulting in lower costs.
Wouter Kok from HoSt, an expert in the field of thermal conversion technology and responsible for the sales of the innovative bioenergy plant, explains, “It is not the application of only a baghouse filter that makes the plant exceptional. We achieve these lowest emissions through innovation in combustion technology and our innovative furnace, which creates a perfect mixing of flue gases with combustion air and a very high efficiency. Thanks to the clever configuration of the combustion zones on the grate, the three-stage combustion in the furnace in combination with flue gas recirculation, high peak temperatures are avoided, and the for-
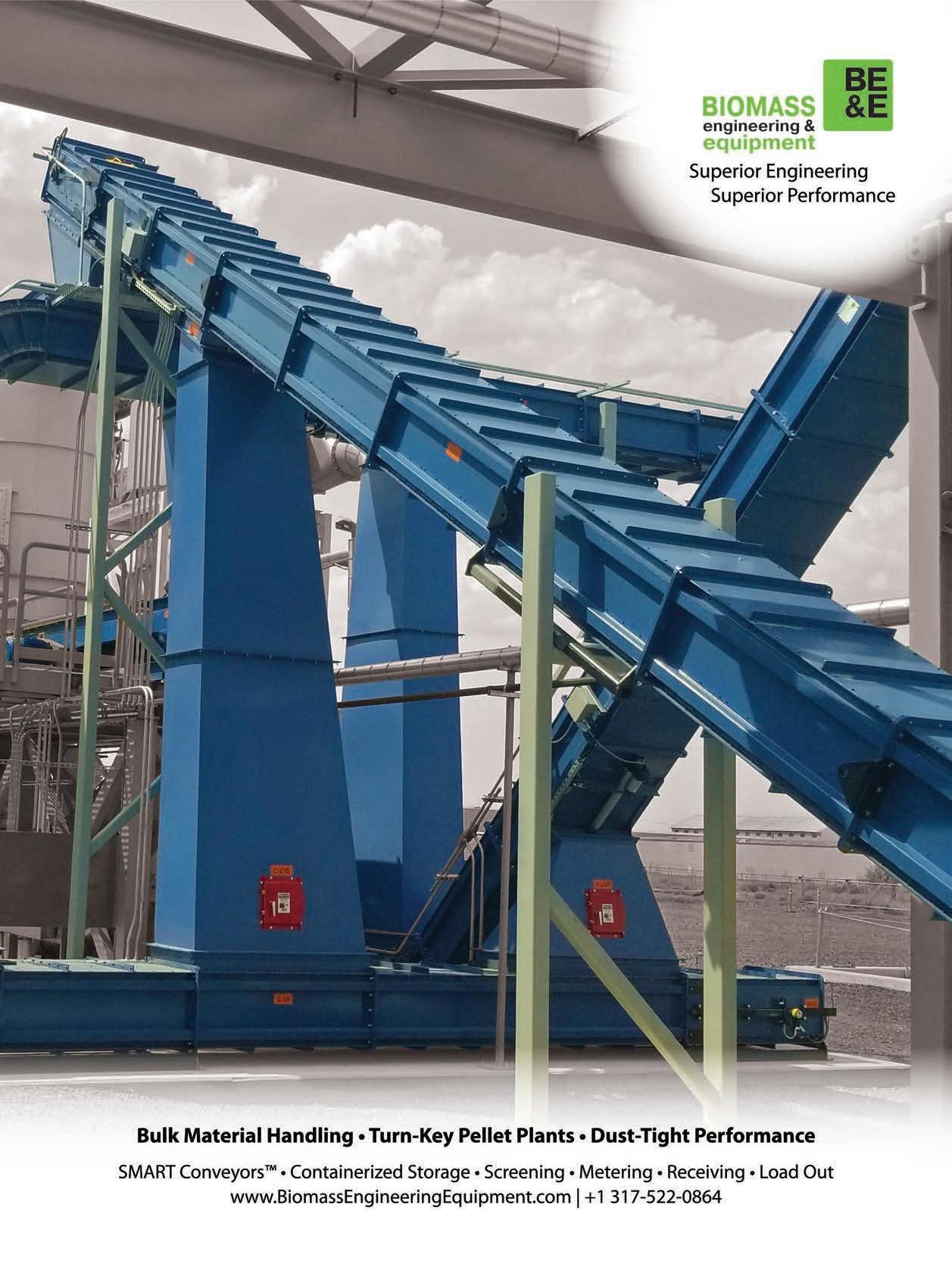
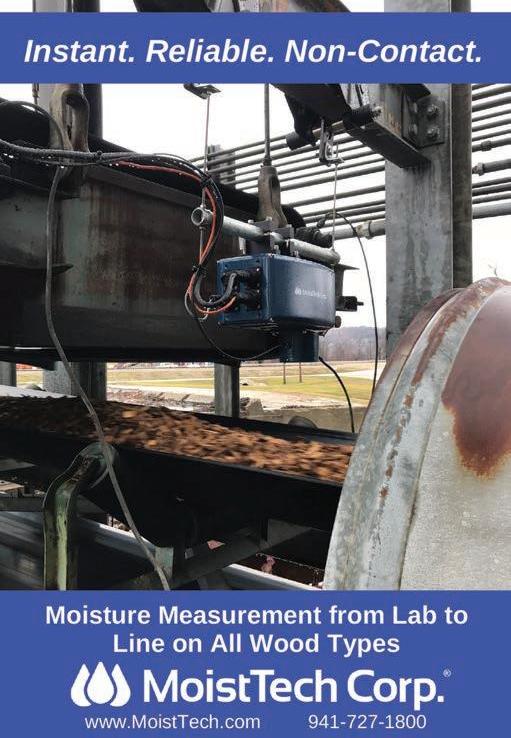
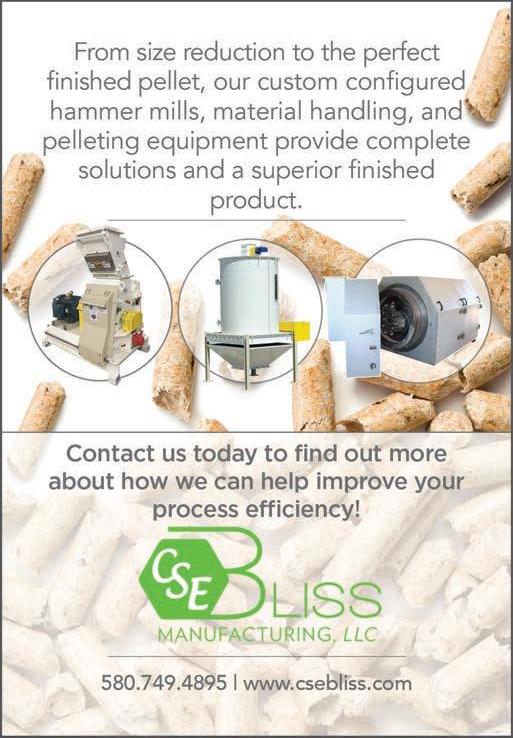
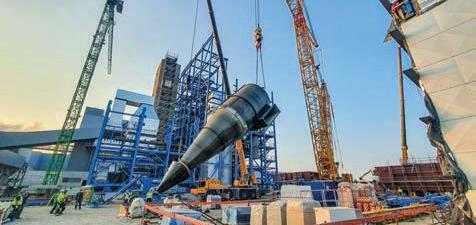
mation of the amount of NOx is strongly reduced compared to conventional combustion furnace designs.”
HoSt’s bioenergy plants fuel regionally available residual and pruning wood that is released in maintenance of nature and landscape and are also suitable for other low-value waste and residual flows, such as RDF and agricultural waste. The techniques are developed for the thermal conversion of residual streams that are not suitable for other applications. The waste streams are shredded and delivered to the bioenergy plants in the prescribed size. These can be pieces of up to 35 cm.
Eco-Friendly Paper Production
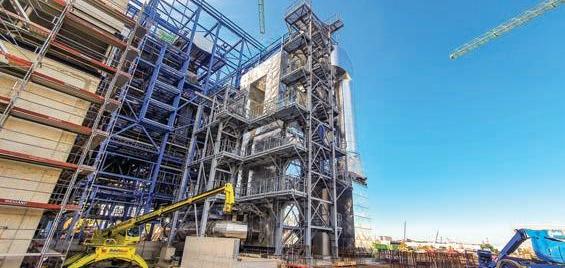
Plant for flue gas cleaning
At its site in Wörth am Rhein, Germany, paper manufacturing company Papierfabrik Palm GmbH & Co. KG (Palm Group) started using a Scheuch fabric filter with additive metering to clean the flue gas from a power station back in 2008. As part of a project to modernize and extend the site, the decision was made to construct another combined heat and power station with the goal to utilize the energy within the waste material left over from production. To assist with this endeavor, Scheuch was once again brought in. The Austrian air pollution control specialist was tasked with installing a fabric filter featuring high-efficiency sorption and a downstream SCR system to ensure compliance with the strictest of emissions regulations.
All five of the paper manufacturing sites operated by Palm Group in Europe are equipped with flexible, stateof-the-art power stations boasting energy efficiency levels of more than 90%. Keeping its paper manufacturing sustainable is clearly high on the company’s agenda, and it
Installation of a cyclone
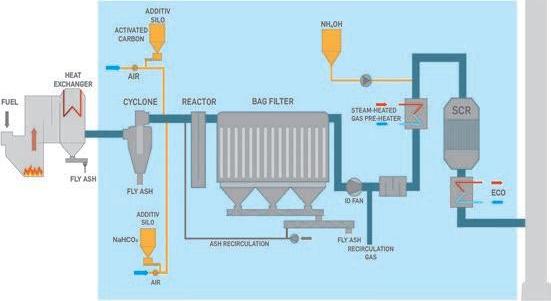
Functional schematic of Scheuch system at Papierfabrik Palm GmbH & Co.
was this that led it to invest around 200 million euros in modernizing the power stations at its three German sites.
Unlike fossil fuels, wood and recycled materials such as paper and biomass are CO2 neutral, which means that the combustion process only releases as much carbon dioxide as the plant absorbed as it grew. This quantity of CO2 would also be produced as a result of biogenic material rotting, and this makes biogenic material an appealing and useful choice of fuel. Nitrogen oxides are classified as reactive nitrogen compounds and have a negative impact on health and the environment. Nitrogen oxide (NOx) in flue gas is produced when biomass is burned, primarily as a result of nitrogen that is present in fuel, and this effect differs significantly according to the type of material being burned. Reflecting the customer’s dedication to sustainability and in the face of increasingly strict emissions requirements, the new product is now providing an effective way of separating not only the usual pollutants, but also NOx.
Given the positive experience from the first collaborative project—a Scheuch flue gas cleaning system with a capacity of 50 MW that has been running flawlessly since its completion in 2008—Palm Group chose Scheuch for the contract to build a second flue gas cleaning system, this time with a capacity of 44 MW, at the same site.
SNCR (selective non-catalytic reduction) technologies for separating dust, acidic flue gas components and nitrogen oxides (NOx) have been used in power stations for quite some time and constitute state-of-the-art technologies. However, ever stricter requirements concerning the NOx limit value and NH3 slip are making it necessary to implement additional emission reduction measures. For this reason, the flue gas cleaning system on modern power stations is being supplemented by tail-end SCR (selective catalytic reduction) to ensure that the lower limit values are met. This involves using a catalyst and adding ammonia (NH3) to convert the nitrogen oxides generated by the combustion process into harmless nitrogen (N2) and water (H2O). The SCR technology makes it possible to comply easily with even the lowest NOx val-
ues of ≤ 100 mg/Nm³ while also keeping the NH3 slip low.
While tail-end SCR brings advantages in terms of the clean gas values that can be achieved, it also makes more demands on the technology that is used. For example, the amount of SOx in the flue gas must be reduced significantly before the point of entry into the SCR system to prevent ammonium salts forming on the honeycomb catalysts. To this end, a pneumatic delivery method is used to add sodium hydrogen carbonate to the flue gas flow upstream of the SCR system and the products of the reaction are then separated at a fabric filter.
Adding activated carbon at this point as a means of reducing heavy metals and PCDD/F (dioxins/furans) also limits the flue gas temperature. The installation of a heat exchanger in the form of a steam-heated gas preheater directly upstream of the denitrification system raises the flue gas temperature again. This makes for long service life and eliminates the need for the catalyst elements to undergo regular burn-off. To make the system more efficient, the flue gas temperature is once again reduced by an economizer before the flue gas enters the chimney. This combined use of a variety of processes from Scheuch now ensures the lowest emissions and an energy-efficient increase in efficiency.
The lack of space proved particularly challenging in the case of this project, but Scheuch managed to install the second flue gas cleaning system directly next to the existing one in an area measuring just 19 x 15 m. The entire flue gas cleaning system was integrated into the external facade and clad in special noise insulation panels to keep both the gaseous emissions and the sound emissions to an absolute minimum. In addition, special attention was paid to making the entire flue gas cleaning system easy to maintain. To this end, the entire system can be accessed by a shared crane system.
“Compliance with the limit values has always been the top priority within the Palm Group and for this reason flue gas cleaning operations must be absolutely problem-free and reliable. We are pleased to see that the actual emission values being generated at full operation are well below the legal limit values,” comments Dr. Andreas Haas, Chief of Engineering Management, Papierfabrik Palm GmbH & Co.
(Article and images submitted by Scheuch. Visit Scheuch.com.)
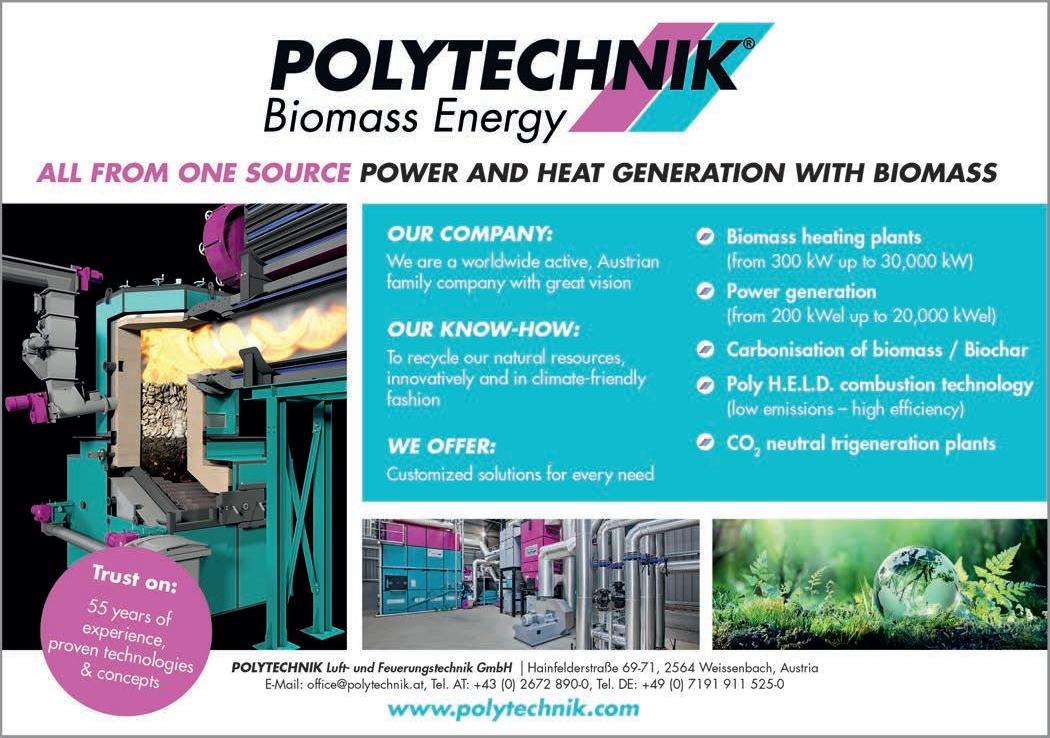
28 Wood Bioenergy / August 2021
BE&E Announces Major Developments
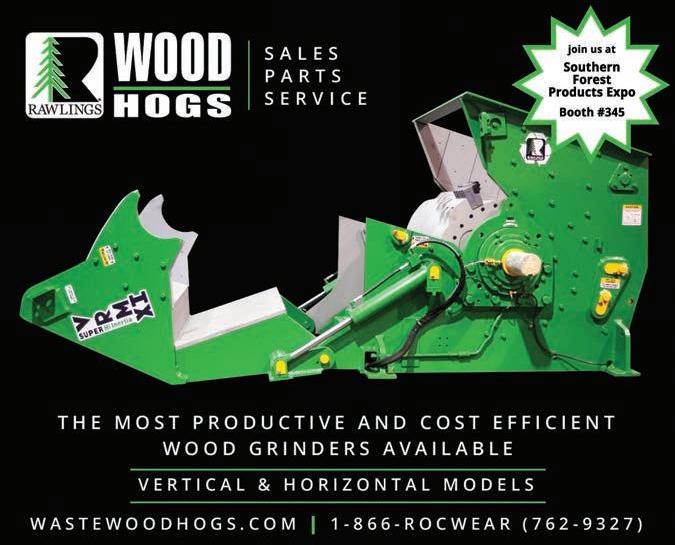
Biomass Engineering & Equipment has added two fulltime design engineers and a chief production manager at its Indiana headquarters to accommodate the demand for its products. The hires follow the addition of a full-time materials control supervisor in 2020 and the creation of a manufacturing engineer role in Q2 2021.
New team members include Carl Rosskopf and Michael Selenke, engineers; Scott Lawson, chief production manager; and Richard Weber, materials control supervisor. Jeff Niewedde serves as interim CFO and Jeremiah Richards as manufacturing engineer. The company plans to hire additional engineers, salespersons and support staff. l BE&E also announced the addition of Cory Frashefski, who will represent the company as Sales Engineer and Project Manager in the Northwest U.S., based in Spokane, Wash.
Before joining BE&E, Frashefski served as the factory engineer at Katerra’s CLT plant in Spokane Valley, Wash. There he played an integral role in procuring equipment and designing the facility. Frashefski’s other experiences include time as an advanced applications engineer at Flow International and a mechanical engineer with MTW Design Services.
“I realized it was a good opportunity,” Frashefski says about his position with BE&E. “It’s a growing company and a good fit.” l In another step of growth and to better serve its customers, BE&E is installing a Messer MetalMaster 2.0 plasma table and a 175-ton AccurPress brake. The investment will increase the company’s metal-forming and cutting capabilities, which will allow it to meet an increasing demand for its products and services.
“We’ve experienced incredible growth and are positioning for even more,” comments Dane Floyd, President and CEO. “Our goal is always to provide the best service and equipment to our customers. These investments in people and machinery allow us to serve even more companies with our expertise so they can benefit from our innovations. The team we’ve put together for this is exceptional— they’re smart guys with a lot of hands-on experience. With them and our SMART line of bulk handling equipment, I’m confident we’ll continue to experience significant growth in the coming years.”
woodbioenergymagazine.com
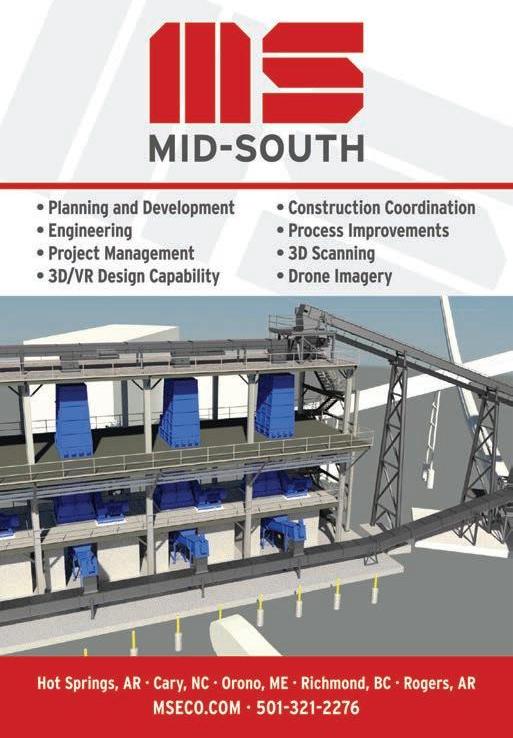
August 2021 / Wood Bioenergy 29
Morbark Gains Sourcewell Contract
Morbark, LLC and its affiliated brands Rayco Manufacturing, Denis Cimaf, and Boxer Equipment have been awarded a cooperative purchasing contract with Sourcewell in the Tree Maintenance Equipment, Attachments, and Accessories category.
Sourcewell is a self-sustaining government organization offering a cooperative purchasing program with more than 400 competitively solicited contracts to government, education and nonprofit entities throughout North America. By utilizing Sourcewell contracts, participating agencies save time and money by capturing the buying power of more than 50,000 organizations.
Morbark was awarded this Sourcewell contract following a rigorous request for proposal process resulting in contracts that meet, or exceed, local procurement requirements.
Morbark's contract with Sourcewell includes the complete lines of Eeger Beever brush chippers, Rayco stump cutters, horizontal and tub grinders, forestry mulchers, mulching attachments, as well as Boxer mini-skid steers, Rayco articulated wheel loaders, and attachments. Morbark's network of approximately 300 North American dealer and distributor locations, as well as nearly 700 combined Morbark employees, work diligently to provide exceptional customer service and after-the-sale support.
Learn more about Sourcewell and its contract with Morbark at sourcewell-mn.gov.
■ CLASSIFIED ADVERTISEMENTS ■
■ employment opportunities
1615 Top Wood Jobs
Recruiting and Staffing George Meek
geo@TopWoodJobs.com www.TopWoodJobs.com (360) 263-3371
3779
VISIT US ONLINE: woodbioenergymag.com
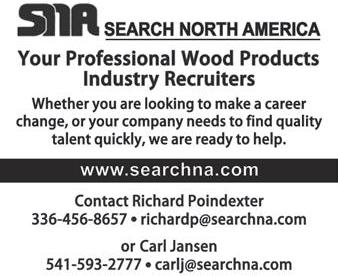
Kice Industries Names Regional Sales Mgr.
Kice has appointed Jeff Kinnunen as Regional Sales Manager, based out of Minneapolis, Minn. Kinnunen will be responsible for the oversight of sales throughout Minnesota, North and South Dakota, west Iowa, and northwestern Wisconsin territories.
Zak Leads Durr’s Clean Tech Systems
Ken Zak is the new head of the Dürr Group’s Clean Technology Systems division, succeeding Dr. Daniel Schmitt, who join the Board of Management of Homag Group AG. Clean Technology Systems is responsible for the Dürr Group’s environmental technology business.
Zak has been part of the Clean Technology Systems management team since October 2018. He joined Dürr through the acquisition of U.S. environmental technology company Megtec/Universal.

30 Wood Bioenergy / August 2021
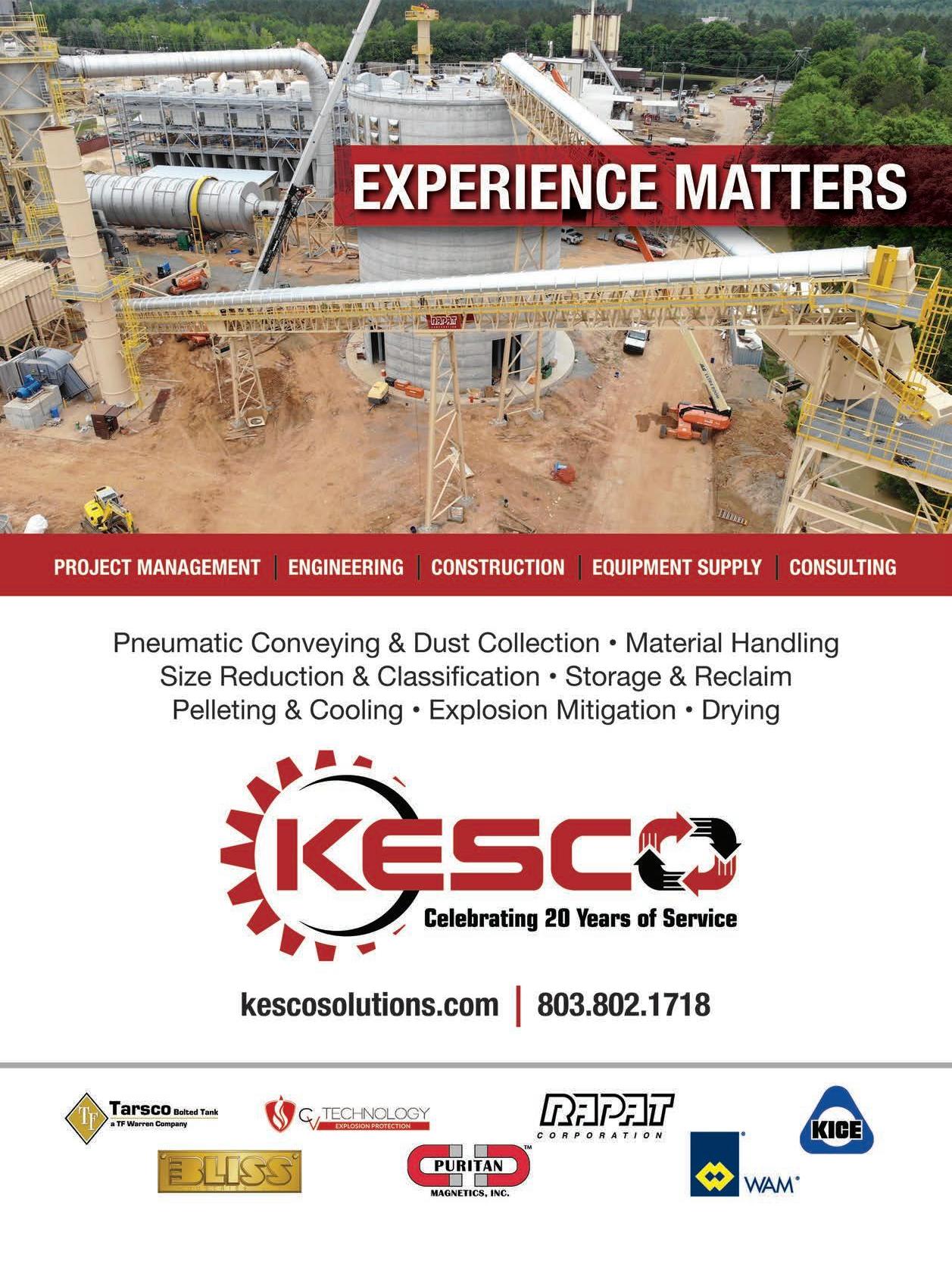
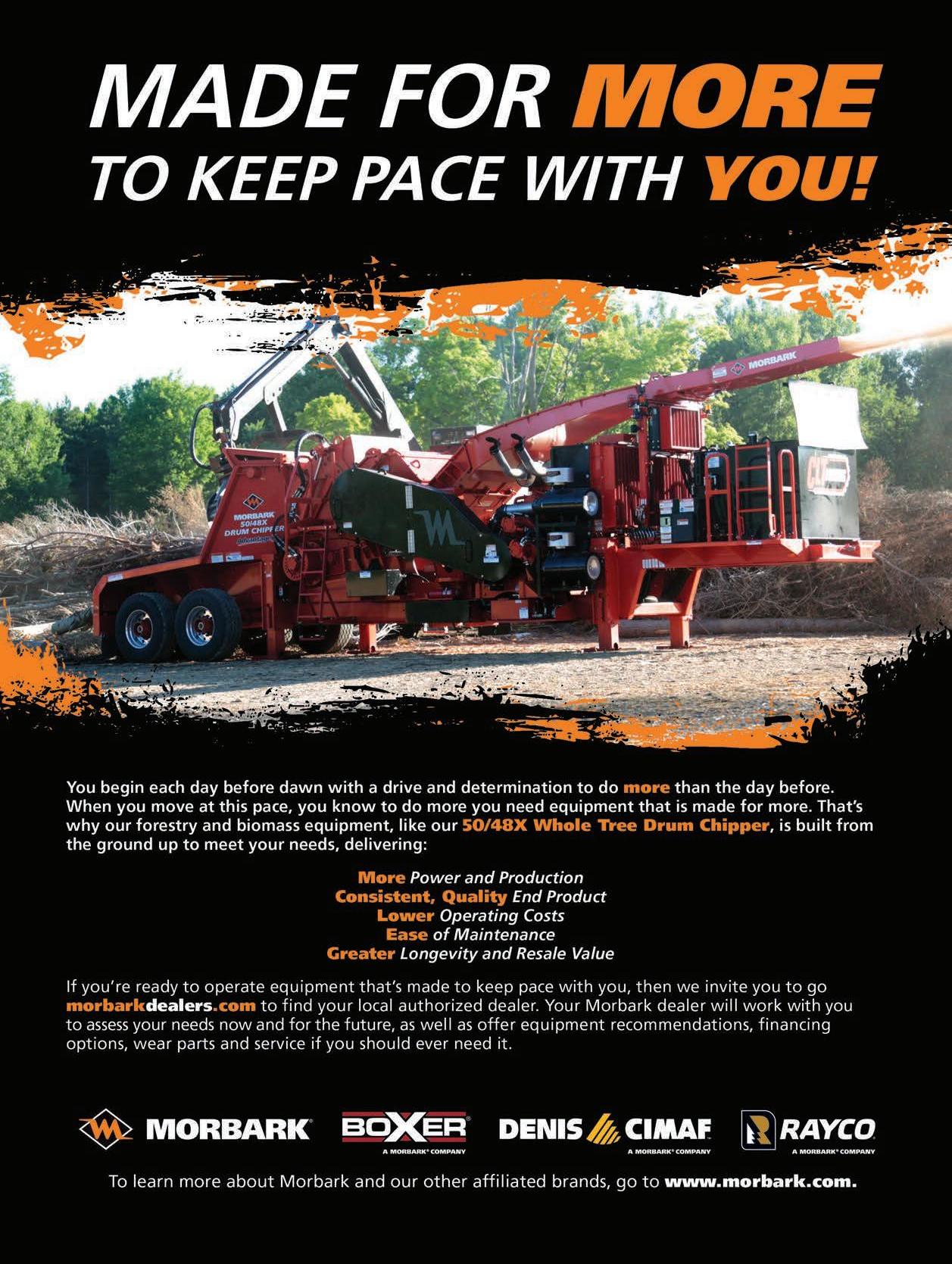