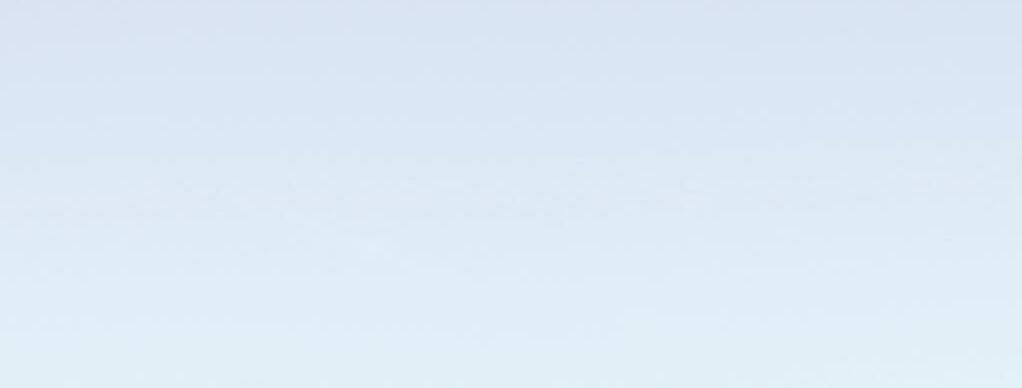
7 minute read
RESTORATION FUELS
Restoration Offers Torrefied High Carbon Opportunities

By Dan Shell
JOHN DAY, Ore.
Restoration Fuels is proving that torrefaction technology is a viable option for converting lower value biomass and mill residuals into higher value carbon products for fuel and other applications. The concept is especially important here in John Day, where the Malheur National Forest surrounding town has almost completed a first major 10-year forest health stewardship project and will soon embark on another.
Such projects generate sawlogs as well as lots of small diameter volume that includes post, pole and firewood material, and biomass. According to project task orders, all material needs to be removed to thin landscapes into more historically open and pine-dominant timber stands with reduced fuel loads that are more resistant to fire.
Finding markets and outlets for the low value material is key to the success of such projects, which are being implemented across the Western U.S. where public lands are increasingly hard hit by wildfire. Officials with Restoration Fuels believe their high carbon torrefied system can be transferred to other projects as well.
As a fully-owned subsidiary of the U.S. Endowment for Forestry and Communities, the plant was created in response to all of the above and to help fulfill the Endowment’s mission to support rural economies while boosting forest health and promoting wood utilization by creating leading edge high carbon fuels and materials.
The Restoration Fuels story originally began in 2014 with that objective in mind and worked with multiple groups and organizations including the USDA Consortium for Advanced Wood-to-Energy Solutions (CAWES) formed by the U.S. Forest Service (FS) and
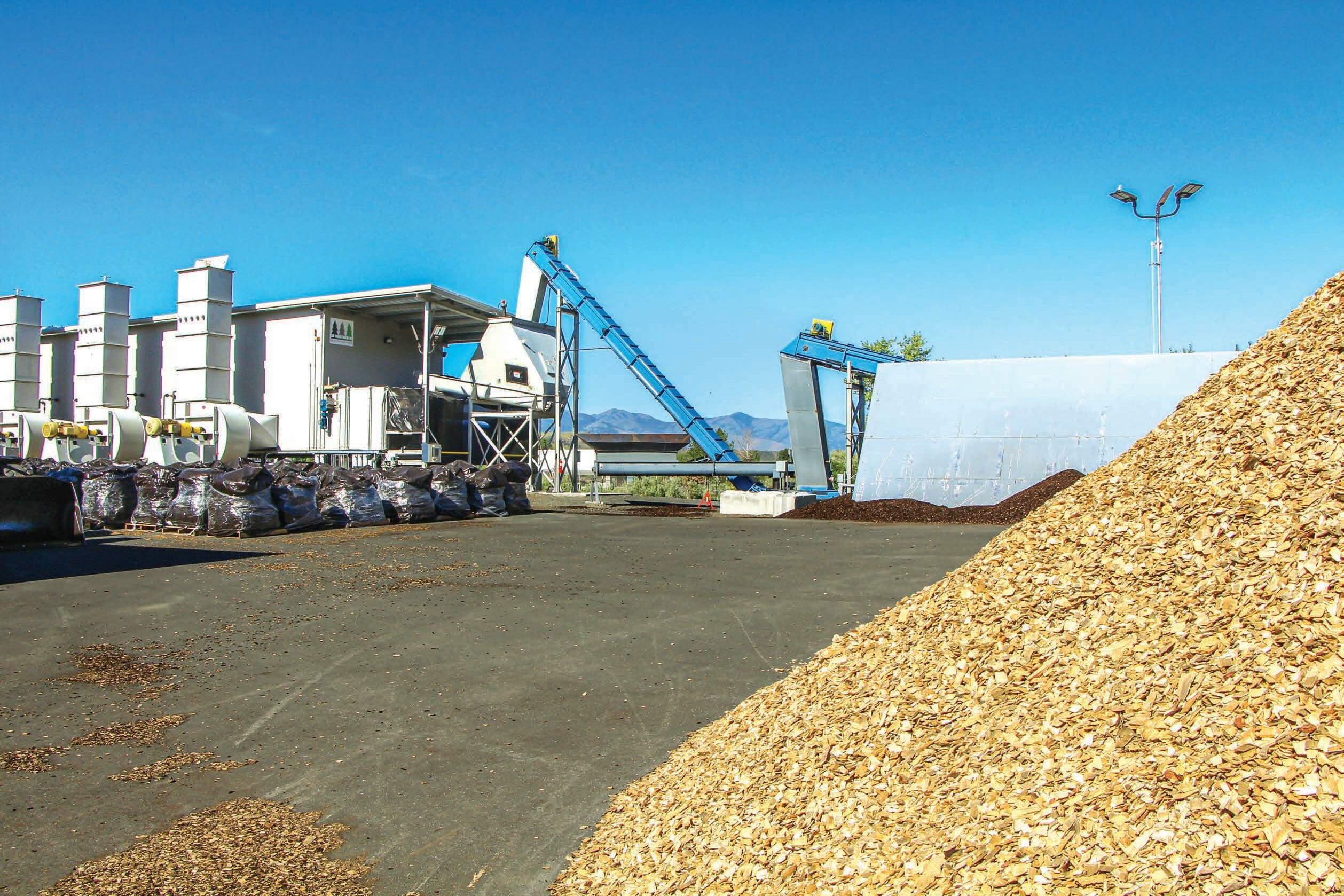
the Endowment. According to Restoration Fuels CEO Matt Krumenauer, the FS played a big role in bringing together a wide variety of stakeholders on the wood bioenergy issue, including seven higher education institutions, the USFS Forest Product Laboratory, plus large private timberland owners, forest products producers and technology vendors. The group focused on cooperative basic research and technologies and ways to accelerate commercialization.
Torrefaction and high carbon torrefied biomass material were identified as a technology and product that require less advanced research and also deliver an end product that can be used in a variety of applications, from high carbon sustainable fuel to soil treatments and much more.
Torrefaction is the roasting of wood in a high temperature, low-oxygen environment, resulting in a biomass product that has a higher carbon density. Restoration Fuels also re-burns the syngas from the torrefaction reaction, almost eliminating process heating fuel demand and further reducing the facility’s carbon footprint.
Construction on the plant began in 2019. It was sited at the back end of the Malheur Lumber Co. facility, near the sawmill’s chipping operations. Officials with Malheur Lumber, which has added small log processing equipment to handle material coming from local forest health projects, have been supportive of Restoration Fuels since the beginning. The plant began testing production capability in late 2021. Equipment has been a mix of mostly used and some new. Key pieces include Hurst Boiler, a low temperature belt dryer, Sensortech moisture meters, Biomass Engineering & Equipment
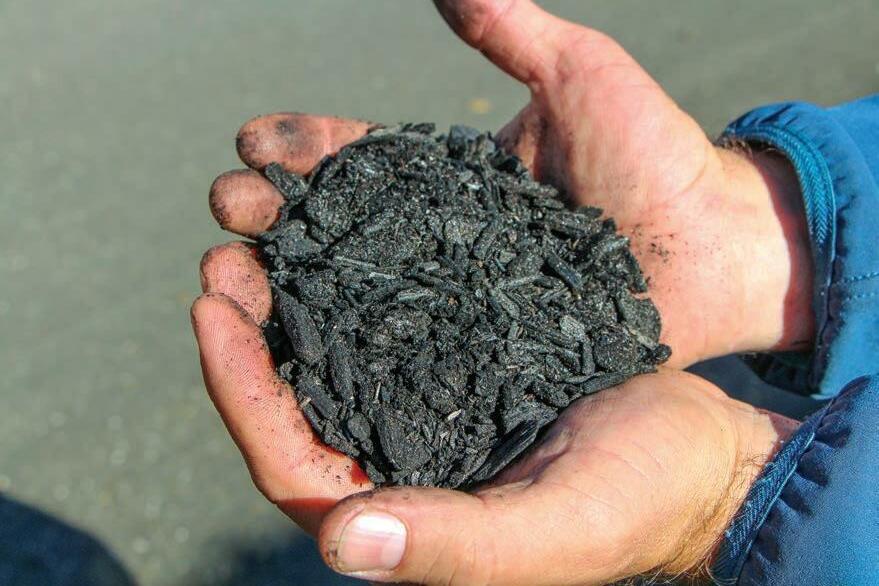
Advanced torrefied materials like this 80%+ carbon content product have the potential to open new markets and applications.
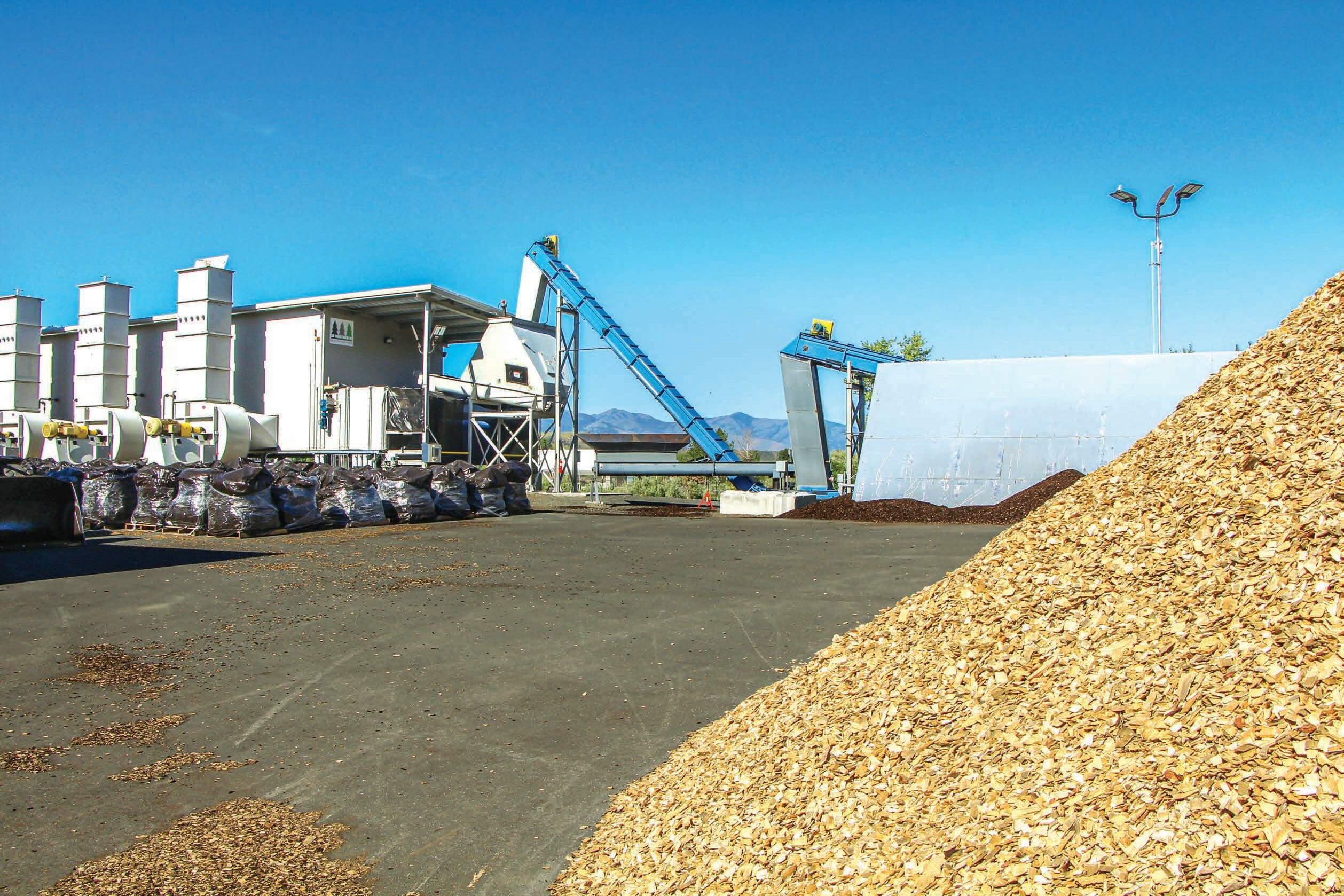
—Restoration Fuels CEO Matt Krumenauer

(BE&E) conveyors and material handling, Clarke’s spark detection system, Coen burners and C.F. Nielsen briquetting machines. New Allen-Bradley controls systems were integrated by Taurus Power & Controls.
Process
The continuous torrefaction process yields a 30% loss in mass: Every ton of raw material results in roughly 0.7 tons of end product. The other 30% is combusted in a thermal oxidizer to provide heat for both the torrefaction reactor and the chip dryer.
Currently all raw material is coming from the adjacent Malheur Lumber Co., which provides screened chips. Raw materials are deposited by wheel loader to the live floor reclaim infeed area, and are moved into a BE&E conveyor system that feeds the belt dryer. Plant operators shoot for a moisture content target of 8% for material coming out of the dryer.
Dried material is fed to the refurbished triple pass rotary drum dryer that’s been modified for the high-temp, low oxygen torrefaction application running at around
Krumenauer is a believer in the Restoration Fuels concept.
Heat exchanger burns syngas from torrefaction process. Two briquetting machines currently handle most output.
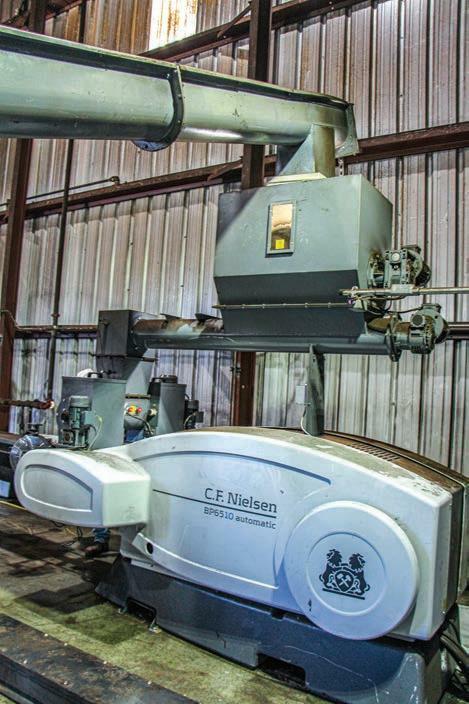
16 Wood Bioenergy / August 2022
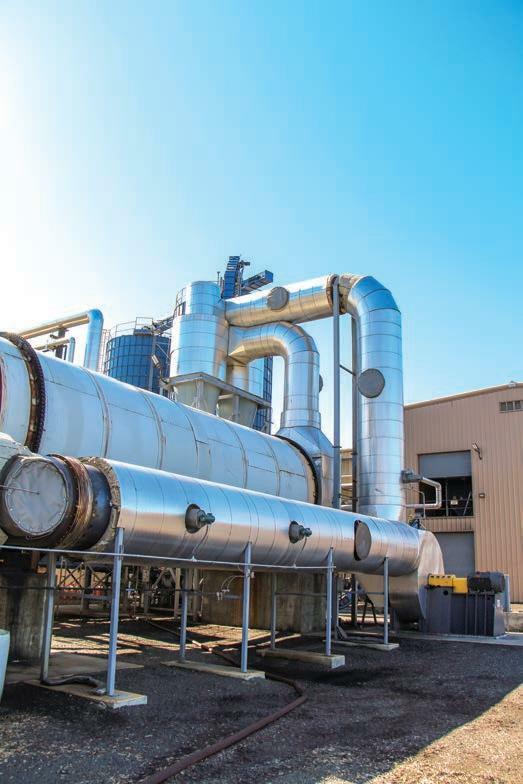
300° C. The process takes about 20-30 minutes, then torrefied material is fed via conveyor to a cooling system and into a set of silos preceding the densification area.
The torrefier features a dual fire system that begins with propane: “Once we get up to temp and start generating syngas, it drops to a pilot light so there’s minimal propane use once we’re up and running,” Krumenauer says. The system’s Coen thermal oxidizer burns the syngas and features two heat exchangers that provide heat for the torrefier and chip dryer.
The densification area currently features two Nielsen briquetting machines. Krumenauer notes that standard I2 pellet size wasn’t a viable option: Torrefied material is more abrasive on pellet machine dies and also requires a more tightly controlled temperature when briquetting since torrefaction reduces the material’s binding effect.
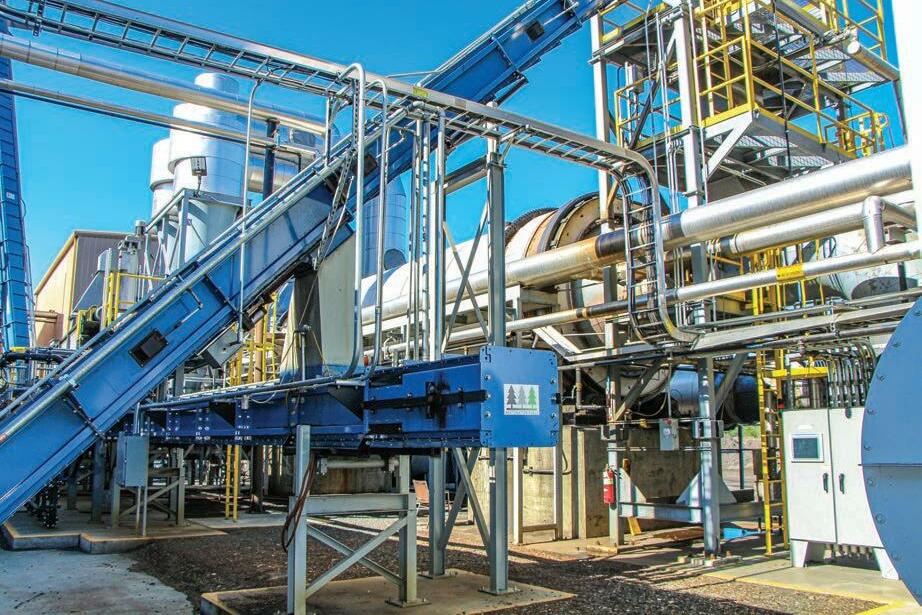
Officials believe the process can work in areas needing forest health work but lacking markets for biomass.
Opportunities Pressing Need
Currently, the densification area is a “planned bottleneck” that’s set to be solved as the plant develops its product line and customer base. “We wanted to get up and running, prove out our continuous operation and engage with more customers before we finalize a product mix,” Krumenauer says.
It was initially hoped the Portland General Electric (PGE) power plant at Boardman, Ore. was going to convert from coal to biomass and provide a key market for Restoration Fuels’ products, but PGE ultimately chose to decommission the plant altogether.
Krumenauer says that despite the challenges posed by PGE’s decision and pandemic labor and supply chain issues in remote John Day, he believes the Restoration Fuels project is still on track to meet its objectives. “We’re actually finding more opportunities as we discover there’s more than a single torrefied product and also other products with higher values,” he says.
Indeed, as operators become more familiar with the process, they’ve been able to produce extra-high 80%+ carbon content material and are able to fine tune carbon content for certain applications and higher value products such as metallurgical coke. “We’re finding a lot of different uses and opportunities, and it all comes back to the goal of providing new markets for low-value residuals from forest health treatments and long-term carbon sequestration,” Krumenauer says.
Helping drive the Restoration Fuels project has been the Malheur National Forest Ten-Year Integrated Resource Stewardship Contract, which was awarded in 2013 to local contractor Iron Triangle, LLC of John Day. As of 2020, task order activities under the contract have reduced wildfire risks on more than 55,000 acres, and led to the restoration of nearly 140,000 acres of wildlife habitat.
Iron Triangle significantly invested in its timber harvesting and handling capacity to execute the contract, and also started a post and pole manufacturing operation in Seneca south of John Day. Along with Malheur Lumber’s investment in a small log processing line to handle the smaller material coming off the stewardship, Restoration Fuels aims to provide a key piece of the puzzle when it comes to handling the biomass residuals from forest health improvement operations. The Forest Service is looking to award another, similar 10-year contract next year.
Restoration Fuels is currently running at about 30% of capacity, with hopes to have close to its 100,000+ annual ton capacity running next year. Meanwhile, Krumenauer says Restoration Fuels is proving its process on a commercial scale. “We’d ultimately like to be able to help create a ‘playbook’ where something like this can be replicated in multiple locations where we have forest health challenges and a lack of markets,” he says.
August 2022 / Wood Bioenergy 17