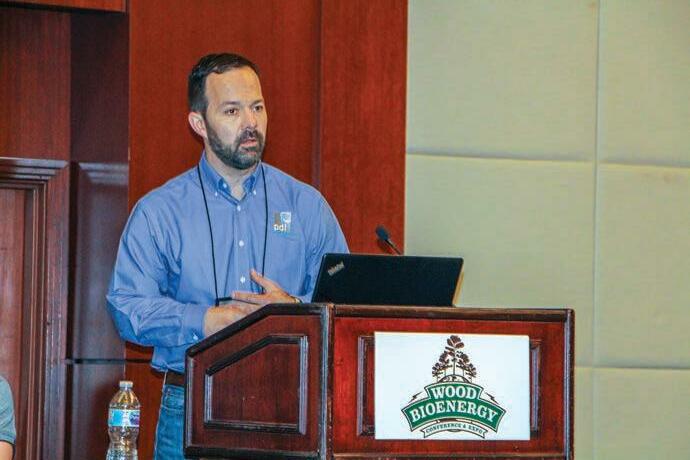
20 minute read
CONFERENCE REVIEW
Equipment Companies Reveal Latest Developments
EDITOR’S NOTE: This is the second of three parts in the coverage of the Wood Bioenergy Conference & Expo held March 29-30, 2022 at the Omni Hotel at CNN Center and hosted by Wood Bioenergy magazine. Part one in the June issue focused on the keynote talks from producer and consultant personnel. Part two highlights several presentations delivered by representatives of equipment and technologies companies. Look for part three in the October issue.
ATLANTA, Ga.
Tyler Player, president of Player Design Inc. (PDI), addressed the company’s development and technology involvement in collaboration with Active Energy Group (AEG) on the CoalSwitch steam-beneficiated pellet, now in pilot scale production in Ashland, Maine, and undergoing testing at sites in North America and Japan.
Player pointed to several advantages of the product over white pellets, including energy production, cost efficiency, co-firing with coal, and minimal expenditure to convert existing fossil fuel operations. He addressed impressive performance data of CoalSwitch, noting it has “proven to blend with coal at the conveyor or supplant coal entirely with retrofitting for existing coal fired power stations” and with carbon values comparable to coal.
As the venture expands marketing and sales efforts domestically and internationally, the product has
Tyler Player

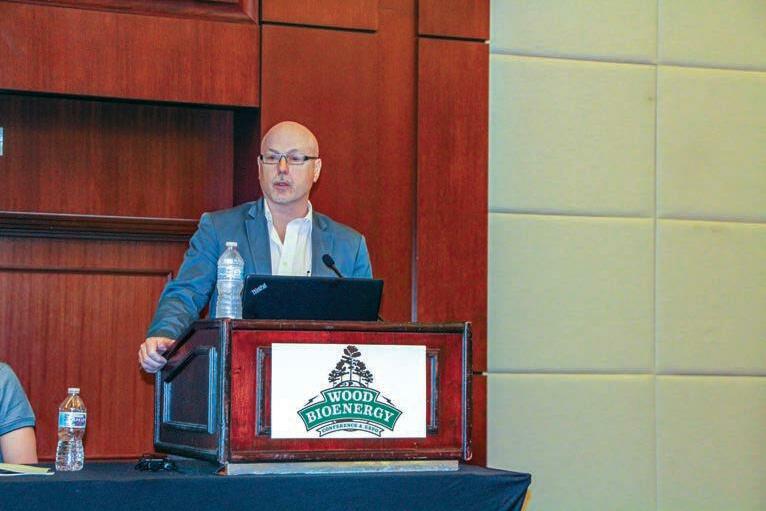
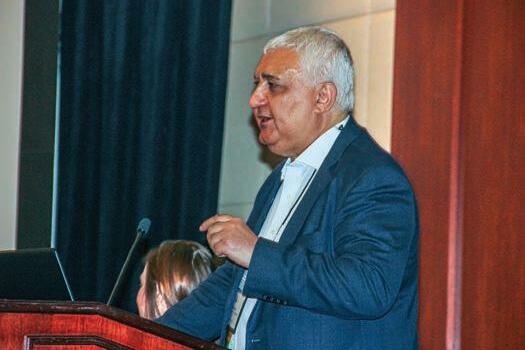
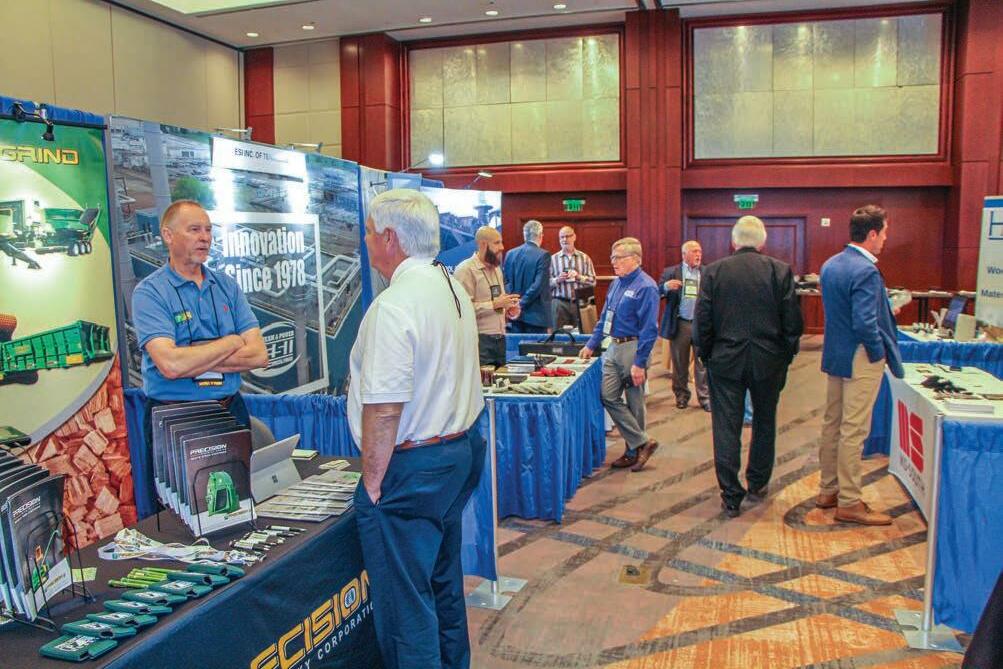
Conference exhibitors ranged from suppliers of air emissions control technologies to in-woods chipper manufacturers.
achieved Chain of Custody and Controlled Wood Certification compliance with the Forest Stewardship Council. Player said they are focusing not only on power utility partners but other industry coal users.
A 70,000 ton full-scale manufacturing plant is plan ned to be in operation by the first quarter of 2023, while identifying sites for other facilities and increasing production in 2023 and beyond.
Dane Floyd, principal at Biomass Engineering & Equipment, in his talk entitled, “The Time Bomb: Dust Safety in Wood Plants,” passionately touched on the recent deaths of three workers at a wood processing plant in Quebec. Floyd reviewed NFPA (National Fire Protection Assn.) codes and standards, and OSHA standards and proceeded to show photos of various plants which were obviously not in accordance.
Floyd addressed how to control dust, as with enclosed “dust tight” bins and conveyors; negative pressure on leaky machines; spark detection and deluge; explosion panels, flameless vents, anti-blowback devices; isolation of conveyors.
He specifically pointed to his company’s SMART conveyor material handling product, referring to reduced power requirements, enclosed dust tightness construction, and other characteristic in compliance with NFPA standards for dust hazard safety.
Bijan Shams, president of Cogent Industrial Technologies, addressed the complexity of delivering capital projects, noting that 70% of them fail, while the ones that succeed combine a stellar project execution team and project management team.
He addressed the steps of project execution, always with an eye on the outcome of delivering a safe, reliable and data-driven plant to drive the highest efficiency from assets, people and processes.
He also broke down project management into multiple phases and responsibilities, and kidded, “What could possibly go wrong?” He focused on the big picture phases of project management: initiation, planning, executing, monitoring/controlling the execution and closing. He cited the project filer server and project issue tracker as necessary tools throughout the project.
Circling back, Shams said the main causes of capital
Dane Floyd Bijan Shams
August 2022 / Wood Bioenergy 19
project failures are poor project execution and poor project management. Key reasons for execution failure include the wrong technology selection (which can cause headaches for years), neglecting safety and hiring the wrong team.
Key reasons for project management failure include poor contracts, lack of planning, poor monitoring and controls, and poor issue management and coordination, all of this leading to delays and overbudgeting. Jason Kovacik, sales manager with Finna Sensors, spoke on production enhancements and profitability by using IoT data-driven moisture control measurement sensors. He reviewed why IoT sensors are trending, including real-time process data, visibility of process trends and conditions, and more focused analysis. Compared to nonenabled sensors, IoT sensors enable cloud-based updates, remote diagnostics, and monitoring of sensor health and performance.
Kovacik spoke on the criteria for integrating IoT- enabled sensors into your process, including partnering with the right organization and having a strategy for adoption. More technology-specific, he focused on Finna’s OMNIR non-contact, non-destructive, real-time moisture control measurement, which features white
light, near-infrared energy filtering and resonance frequency of water molecules, and with advantages built into the associated and minimized system hardware. OMNIR can be implemented in numerous areas of a production facility, including pre- and post-dryer. Jaymie Deemer, president of Nestec, Inc., gave an in-depth look at dryer WESP and RTO systems, including the complexities of wood dryer emissions sometimes associated with the dryer technologies and with the particulate materials themselves. Some of these issues, as well as others, can contribute to common ESP and RTO issues and problems. He said, “Wet ESP performance and design of critical components are key to reliable operation,” and pointed to numerous such feaJason Kovacik tures in both WESP and RTO design, including, in the former, isolable electric fields, extended flushing, simple electrode alignment, irrigation, plug resistant spray nozzles, power supply, continuous loop blowdown, high temperature water flush, caustic grade; and in the latter, proper media, draft arrangements, multiple burners, and proper construction materials such as mastic coatings to protect the shell from condensation, and which materials to avoid such as low grade stainless steel. Rodney Schwartz, vice president Sales & Business
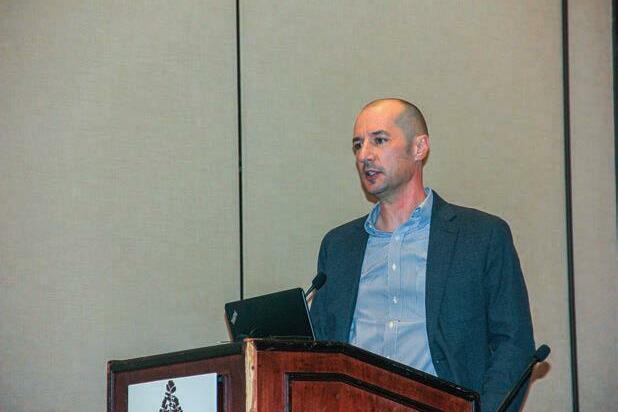
Jaymie Deemer The OMNI CNN Center’s Grand Ballroom North has hosted the conference since its beginning in 2010.
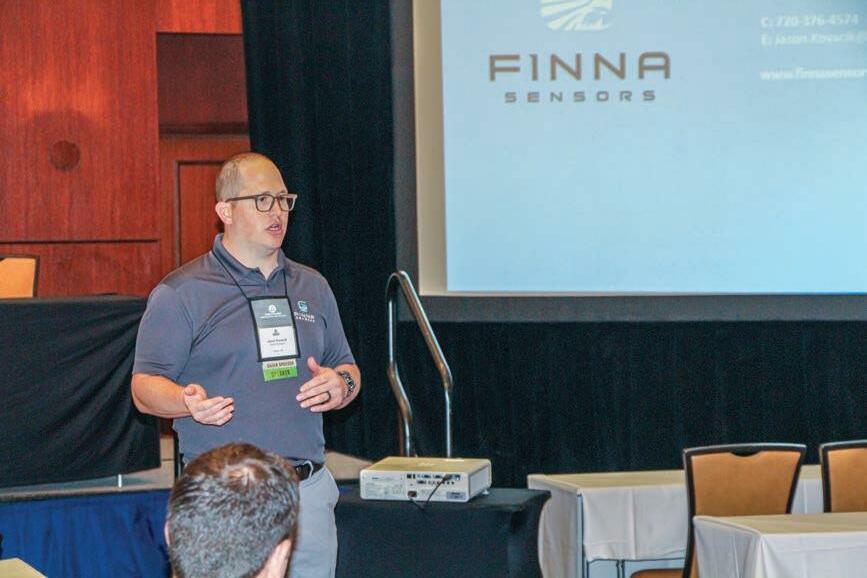
20 Wood Bioenergy / August 2022
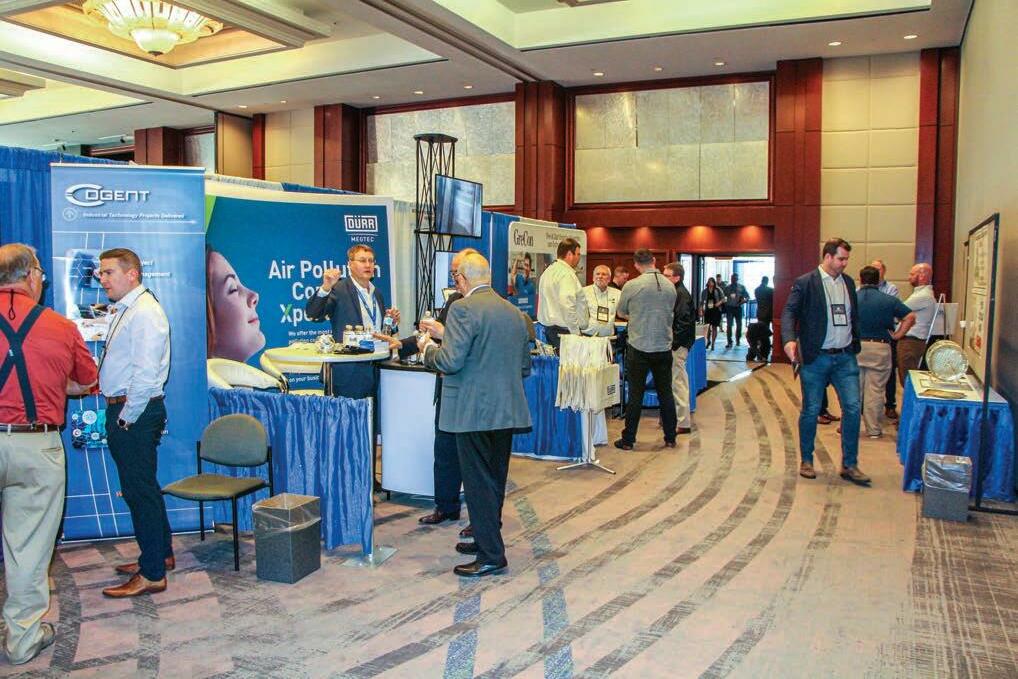
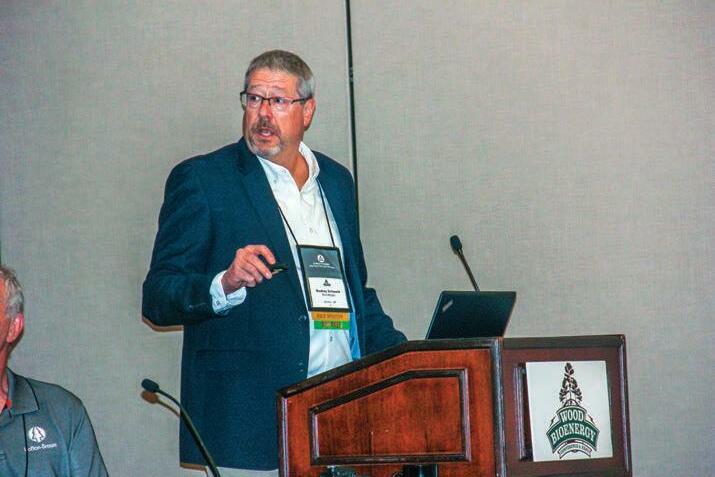
Development, Dürr Systems, spoke on the development and testing of new WESP design enhancements including an optimized electrode and tube design. After reviewing various factors that influence WESP performance, and issues and concerns with current designs, he said Dürr Rodney Schwartz approached producers and operators to get their input on current designs. The feedback included: tubes and electrodes get dirty and are difficult to clean, potentially impacting collection performance; capital cost is too high; installation time is too long; foaming problems; mist carryover into RTOs; performance drop when flushed.
Dürr promptly set goals for a new WESP based on the feedback, including modular shipping design, better fabrication, flexible sizing, new patentable ideas, online cleaning, offline flushing.
Dürr developed a 1/6th to-scale test model and performed testing over 16 weeks with 27 separate flow tests and 55 different particulate removal tests. Testing included various configurations of electrodes, including bottom mounted discharge electrodes that proved highly effective, and including the use of a High Area Trap (HAT) that showed numerous benefits.
They then built a to-scale 25,000 acfm pilot WESP that was installed at an OSB customer site in the Southern U.S. and was tested for 10 months downstream of rotary flake dryers. The new designs scored high compared to older designs on filterable particulate removal, organic condensable particulate removal, enhanced spray system cleaning and proved multiple other benefits.
The key features of the new product include maximum removal efficiencies, reliable operation, low operating costs, and significantly reduced maintenance. Jeff Nichols, managing partner at Industrial Fire Prevention, speaking on behalf of Fagus GreCon, noted wood and wood products still account for a significant share of dust-related industrial fires and explosions. He addressed GreCon’s range of spark extinguishing, fire Jeff Nichols protection and spark
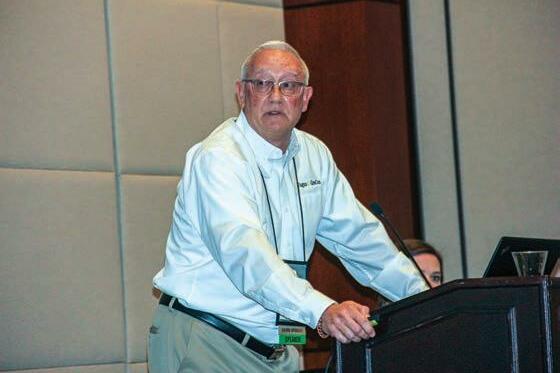
August 2022 / Wood Bioenergy 21
The next Wood Bioenergy Conference & Expo will be held March 12-13, 2024.
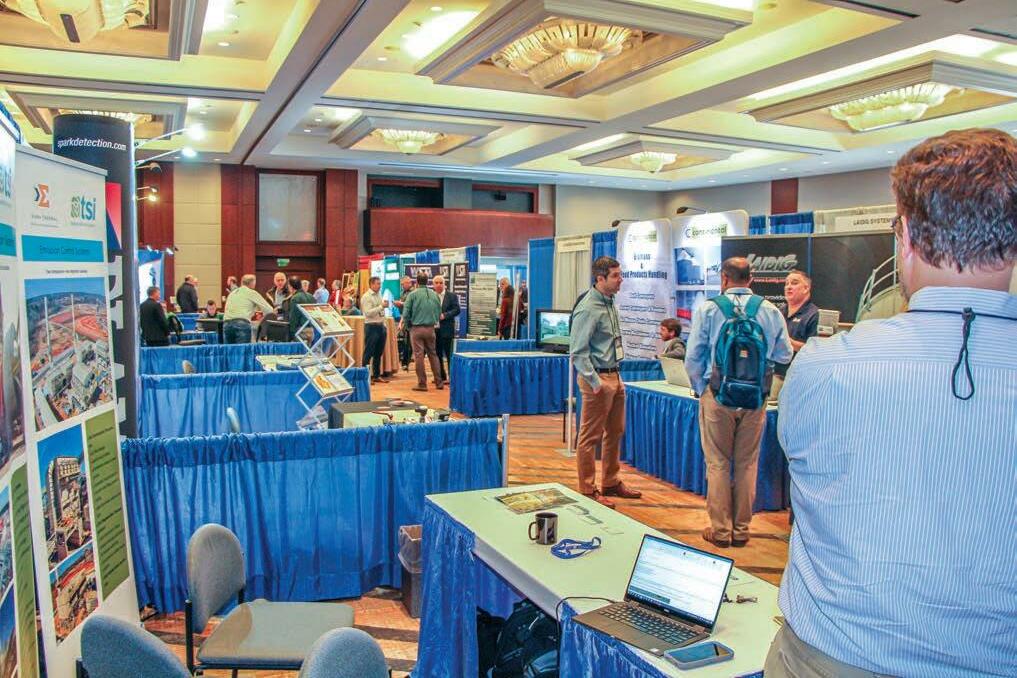
detection products, including the new DLD 1/9 spark detector.
He also spoke on the company’s extinguishment systems with atomized water droplet technology for larger spacing, better cooling and less usage.
Bernardo Sanson, sales engineer with CV Technology, addressed fire and explosion protection for biomass processes. He reviewed combustible dust basics, including dust ignition, and the multiple hazardous areas within the production facility.
He clarified the meaning of prevention and mitigation strategies and said a full solution often combines them in the name of optimal safety. Specifically for mitigation, he talked about explosion venting and flameless venting, the latter referred to as a passive mitigation technology using stainless steel mesh to extinguish the flame.
For fire prevention he spoke on spark detection and
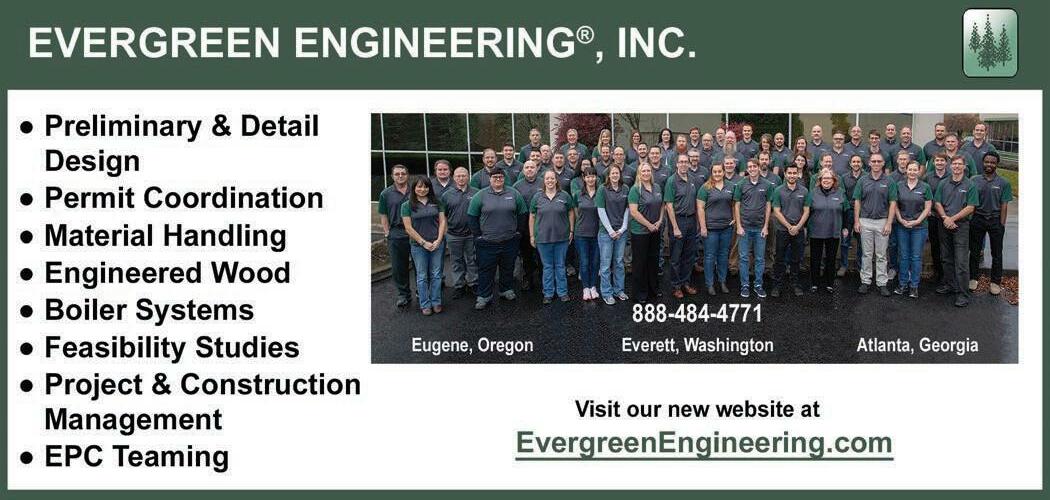
22 Wood Bioenergy / August 2022
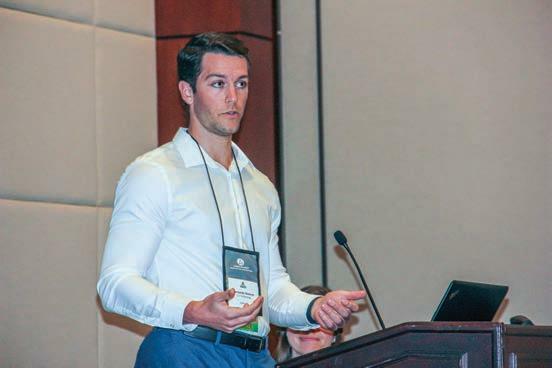
advances in the technology such as infrared detection— allowing detection of sparks at lower temperatures—intelligent detectors and remote monitoring. He addressed water mist quick suppression ideally suited for areas with hot bearings, motors, sparking equipment and heat generation. Bernardo Sanson “Biomass processes can have multiple areas with high risk of ignition sources,” Sanson said. “Understanding the risk scenario at each part of the process is crucial to managing these risks.” He added that a combination of explosion mitigation and fire prevention solutions allow for minimal loss in production, minimal downtime and enhanced safety performance. Andrew Johnson, vice president at TSI, spoke on the company’s rich history and development with torrefaction technology, and spoke on customized torrefaction through temperature and process controls. He said TSI built its pilot torrefactor in 2012, installed a scaled up torrefactor Andrew Johnson in 2013, developed a system to torrefy sugar cane leaves and bagasse in 2015 for a plant in Louisiana, installed a torrefactor in Thailand to torrefy pre-made pellets in 2019, installed one in Vietnam in 2021 and this year started construction on a 120K tpy system for the Japanese market.
Johnson said their technology has shown a positive experience in power station co-firing and in outright replacement of coal in power plants.
He reviewed the technology flow through the TSI system and concluded that “the technology is starting to go prime time,” pointing to applications not only as solid fuel for power production but in metallurgical coal applications, chemical compound recovery, concrete production, polymer extender, pre-treatment for gasification and bio-based hydrogen.
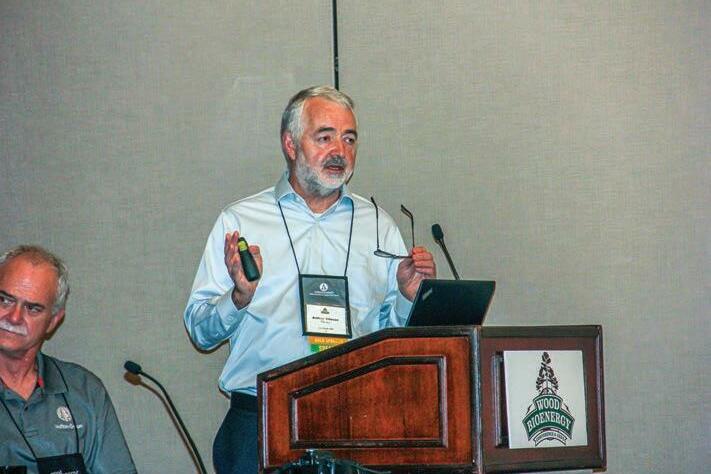
Wood Bioenergy editors Rich Donnell, Jessica Johnson, Dan Shell and David Abbott contributed to this story and the accompanying photography.
August 2022 / Wood Bioenergy 23
BAKER RULLMAN
Baker-Rullman’s innovative triple-pass drum dryer design offers industry leading performance and efficiency in the smallest possible package size. A properly sized and tuned drum dryer system suited to your input volume is the key to planning an efficient system. Baker-Rullman’s specialized engineers are dedicated to accomplishing these goals with each and every installation. Here are some key factors that have contributed to Baker-Rullman’s unequaled record of dependability: l Three full length cylinders that provide the maximum effective length and residence time in a very compact package. l The drum drive uses specifically designed engineering class bushed roller chains and sprockets. l Trunnion rollers are made from Class 50 cast iron with a minimum roller face hardness of 270 BHN. The inboard tapered roller bearings, which have a ‘B-1-’ life of 15 years, allow the roller to rotate around our stationary roller shaft supported by our hold-down pillow blocks. This design has proven to be more reliable than the commonly used small diameter roller with an integral cast shaft. l The drum tire in our systems is hot forged from a single billet of AISI 1025 steel, then finish machined. There is no weld seam on it, and the steel grain structure is oriented for greater wear resistance and strength. l To achieve efficiencies better than 1,500 BTUs per pound of water evaporated, our design incorporates longer residence times, robust temperature control, and superior drum insulation. l Precise electronic controls eliminate heat surges and fuel waste. l Consistent evaporation in Baker-Rullman’s triple pass dryer design protects woody biomass from under or over drying. Heavier, wetter product moves slower than fine particles, giving uniform drying to all particles. That’s why our rotary dryers have long been known for protecting the integrity of all types of material.
Baker-Rullman’s energy efficient, high-performance rotary dryers have developed a global reputation in ultimate reliability. It remains the most trusted dehydration technology for optimizing operating costs, efficiency, and product consistency.
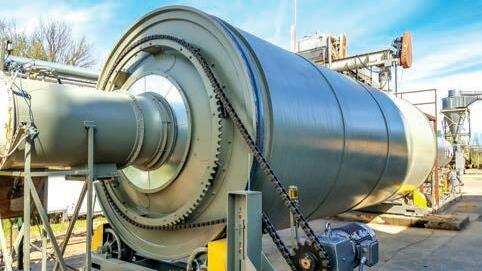
BIOMASS ENGINEERING & EQUIPMENT
Turn to Biomass Engineering & Equipment (BE&E) for reliable bulk handling. We supply turn-key systems for the pellet industry and offer drag conveyors, metering bins, trailer load-out stations, and containerized storage with live-floor reclaim, all of which we manufacture at our factories in Indianapolis, Indiana. We’re so confident in these products that we back them with a full, one-year warranty against defects. BE&E is best known for its SMART Conveyor, a premium drag conveyor designed around the challenges that come with handling biomass. SMART Conveyors excel at handling both green and dry materials, including pellets, which they won’t grind up like other chain conveyors are prone to do. They handle pellets gently because they run their chains in channels outside the material path. Because the chains are captured, they cannot ride atop the pellets and damage them. SMART Conveyors are uniquely suited to handle pellets at every stage, from the mill to the load-out station. They’re available in stainless steel to handle fresh pellets, and they can be angled up to 90° for loading silos and other machinery in constrained areas. SMART Conveyors can be modified to accurately distribute material in trailers, clam-shell bins, and warehouse floors.
Also popular from BE&E are SMART Containers, sea cans we convert into storage and feed devices by adding a push-pull reclaim system. Unlike slat-floor systems that shuffle the entire material pile toward the discharge area, SMART Containers employ strokers equipped with welded flights, which shear material off the bottom of the pile, thereby providing first-in, first-out material flow without uncontrolled surges. The hydraulics in SMART Containers also differentiates them from slat-floor systems. The hydraulics in BE&E’s containers are designed for simple maintenance, and technicians can access them easily through the container’s doors. And technicians needn’t empty the container to perform maintenance. Neither must they crawl under the floor to access moving components.
SMART Containers are available in 20 ft. and 40 ft. lengths and can be stacked up to three units high for additional capacity. Containers can also be placed side by side to increase redundancy and segregate products.
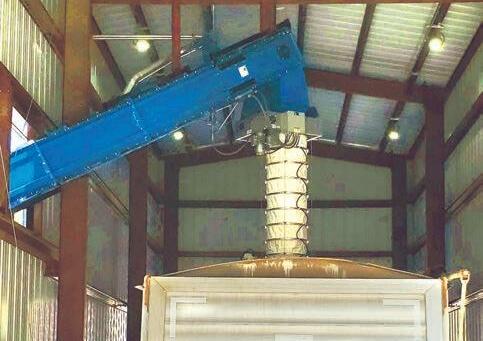
24 Wood Bioenergy / August 2022
BUETTNER ENERGY SYSTEMS
Founded 1874, Buettner is a manufacturer of energy systems, dryers and burners, headquartered in Krefeld, Germany. The U.S. branch office is located in Charlotte, North Carolina. Since 1995, Buettner has commissioned about 100 energy plants up to a total load of 340 MMBtu (100 MW), many of them combined with Buettner dryer systems (more than 2,000 dryers worldwide). The provided services concerning new plants include sales, planning, construction, assembly, commissioning and performance tests until the final handover to the customers.
Apart from new plants, Buettner offers inspections, retrofits, increased performance and upgrades for any own and foreign plants. Additionally, Buettner offers a fast and customer orientated service for spare parts.
Customized Energy Systems
The setup of the energy systems diversifies according to the demand of the production of pellets. The plants are individually designed for the customers’ demands, like flue gases of required quality, the supply with thermal
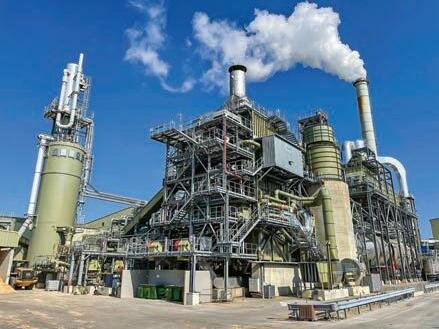
oil and the production of steam.
Regardless of any connected production lines, there are some core elements found in every energy system. The fuel handling (consisting of fuel bins, conveyors like screws, chain, vibrating or belt conveyors, hydraulic units and the fuel feeder unit) provides the fuel feed to the combustion. The necessary oxygen is supplied by the combustion air system with the primary and secondary air fan.
Buettner-Designed Main Components
The air-cooled reciprocating grate has a range of 129–1,184 sq. ft. (12–110 m²). Multi-fuel burners (gas, oil, granulates and dust) are available at load levels between 8.5–185 MMBtu (2.5–55 MW).
Recirculation gas systems lead to low concentrations of nitrogen oxides. Additionally, the concentration can still be lowered by the installation of a SNCR-system using urea. Cyclones, micro-cyclones or ESPs are also part of our expertise and scope of supply.
The boilers are designed as thermal oil heaters and evaporators including economizers. The steam production is either direct or indirect by heat exchangers.
By using an RTO, emission limits behind the dryer island can be fulfilled.
HURST BOILER
Industrial grade wood fired burners with Hurst “clean-burn” stoker design, as well as modular packages available from 5 MMBTU/HR-250 MMBTU/HR with operating temperature ranges from 200°F to 2000°F— These proven solid fuel burner systems are a leading choice in lumber dry kilns, boiler applications, oil heaters, rotary dryers, brick kilns and more. Hurst manufactures seven different types of biomass stoker/gasifiers, which have used 2,000+ different types of biomass fuels. With installations across all industries worldwide, Hurst is recognized for the highest code standards, innovative engineering and design, Energy Star rating, and renewable, sustainable solutions for green building design and operational efficiency.
Hurst STAG systems are a culmination of experience and knowledge of material handling, solid fuel combustion, and controls integration that offers a quality solution for most air heating applications. We are providing our customers the ability to economically and efficiently satisfy their air heating requirements by utilizing readily available waste as a fuel source in lieu of the expensive conventional sources. Hurst delivers the quality and performance that our customers expect in a custom engineered solution to reduce operating expenses and maximize productivity.
The Hurst STAG unit can be utilized from 5 MMBTU/HR- 250 MMBTU/HR with operating temperature ranges from 200°F to 2000°F. These systems are frequently utilized in lumber dry kilns, boiler applications, oil heaters, rotary dryers, brick kilns and much more.
The Biomasster STAG control system developed for the direct fired burner is a computer based, data driven “SMART” monitoring and control system designed for the optimal clean combustion and operation of the direct fired burner system. Offers real-time modulation and reduces dirty flue-gas residue and hot ash carry-over issues.
Hurst equipment features a totally automated system; superior refractory material; automatic ash removal system (in wet and dry systems); ash sifting hoppers; a unique wall/grate interlocking discourages internal fuel leakage; reciprocating grate design—complete burn with automatic dust-free wet ash removal system. The modular packaged design means low cost project installation.
Hurst Boiler is a leader in the development of boiler technology as well as sustainable solutions for renewable energy.
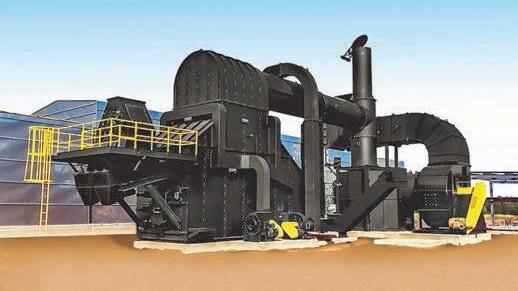
August 2022 / Wood Bioenergy 25
■ energy technology
MID-SOUTH ENGINEERING
Could an organic rankine cycle (ORC) turbine be a smart addition to your biomass or wood products facility? Mid-South Engineering has helped several clients evaluate this technology and we have the experience and expertise to help answer this question for your process.
Because of their unique ability to operate at lower temperatures, potentially even using waste or excess process heat, ORC systems can often make sense where a traditional steam turbine does not. In some cases, they provide a revenue stream for excess fuel or a “heat dump” that provides an offset to your facility’s electrical consumption. Additionally, ORC systems are relatively easier to operate than steam systems and can avoid many of the requirements for training and inspections that come with steam systems. Mid-South begins all evaluations with a heat and fuel balance to help determine the best option for your unique situation.
ORC systems are less efficient than steam systems for electrical generation, but they are often incentivized through renewable energy subsidies and credits, so the payback calculations must be given careful attention. Mid-South can help to ensure that all factors are being considered—capital investment, operational cost, system layout, and integration. Contact us today to learn more.
Mid-South is a leading consulting engineering firm that provides a broad range of professional engineering services. Our multi-disciplined staff has served state and local governments in addition to industrial and commercial clients with particular expertise within the biomass and building products industries. Combining innovative design tools and practical experience, we help our clients optimize opportunities, increase return on investment, and develop superior quality products.
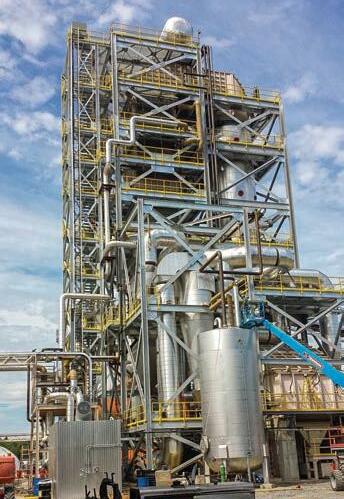
MOISTTECH
MoistTech’s near-infrared (NIR) moisture sensor allows manufacturers the ability to adjust moisture levels on real-time information lowering raw material and fuel costs, higher yields, and more uniform products. NIR moisture measurement is a non-contact measurement that offers clear advantages over the traditional methods, most important being ease-of-use, elimination of hazardous chemicals, and increased efficiency of product testing. With NIR analysis, all manual steps of collecting, drying and accurately weighing samples are eliminated. Continuous monitoring of moisture content provides proactive avoidance of potential issues caused by out of tolerance moisture levels. Evaluating and implementing lean manufacturing principles assists in eliminating waste and improving overall plant production. With the implementation of moisture control systems, manufacturing plants can save a large amount of money in a short amount of time. When considering the many challenges that plant operators are tasked with, moisture control plays a large role. Moisture content can affect product quality and equipment function, making it a crucial focus point in proactive avoidance of quality control issues. Dryer effectiveness is critical, as dryers consume a large amount of energy during operation. The implementation of moisture measurement before and after the dryer provides immediate control over the temperature and operational efficiency
Over-drying a product can result in a dusty environment that can lead to a fire or dust explosion. As such, greater plant safety is achieved with a proper moisture measurement system and cost savings are enhanced. The overuse of dryers results in overpaying on energy costs. By implementing a moisture detection process, producers can monitor 100% of their product quality instantly and consistently. Additionally, active adjustments can continuously be made to the process, optimizing the outcome.
Real-time process control with moisture detection provides true product data that can be used to improve operation efficiency. This reduces wasted effort and materials, and decreases the frequency of downtime, manual intervention and defective goods. Increased plant efficiency, lower energy costs, higher accuracy, instant return on investment (ROI) and low to zero maintenance are just a handful of benefits seen when implementing a moisture control system.
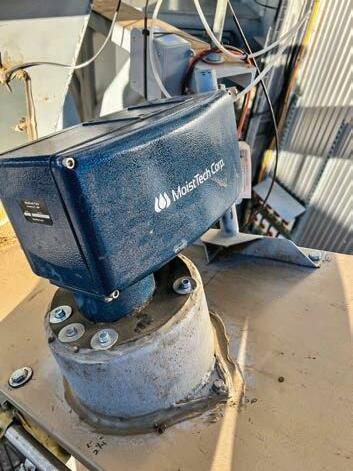
26 Wood Bioenergy / August 2022
PLAYER DESIGN
PDI developed its innovative energy system as a practical solution to industry needs; responding to demand for a system that would burn a wide range of fuels, allowing manufacturers to use available and inexpensive materials. PDI Energy Systems can be operated using either wet or dry fuel, or a combination of both.
Each PDI energy system is a custom design, utilizing precise calculations of retention time to prevent carry-over of ash, sparks, or other materials. Engineered combustion chambers and individualized burner management programming result in minimal emissions, regardless of the quality of incoming fuel sources. A PDI energy system offers a flexible and efficient approach to meet the energy demands of a modern manufacturing facility.
From robust fuel systems and machine bearing mounts, to our process design, every item matters to PDI. PDI’s experience in maintenance and operations is key to how we design our systems and ensure optimum performance for the durability and long life your facility demands.
Premium quality refractory installed and ready for production
Dampers machine coupled to actuators, with bearings on every shaft
Rotation of fuel system conveyors targeting 15RPM for low speed and long life
Shaft mounted gearboxes with c-face motors to avoid maintenance
Direct drive fans for maximum service life
Reinforced dual-pivoting doors for ease of access
Complete System Supply
PDI offers complete energy system plants. Our team of engineers and construction partners can design, build, and start up everything from a basic dryer furnace up to a fully-functional cogeneration plant. Our facilities can utilize solid fuel, natural gas, propane, or other fuels you may have available. Our engineering team custom designs fuel handling systems, thermal recovery plants, and fully integrates the facility for optimum energy recovery from your fuel. Our design and construction experience with various fuels ensures your system will perform as expected.
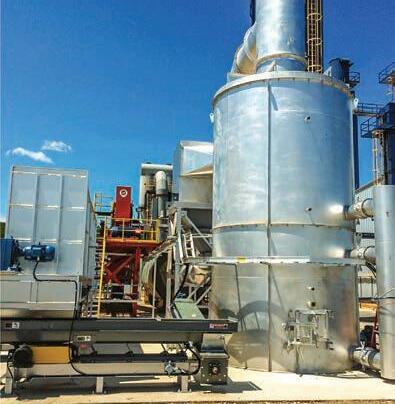
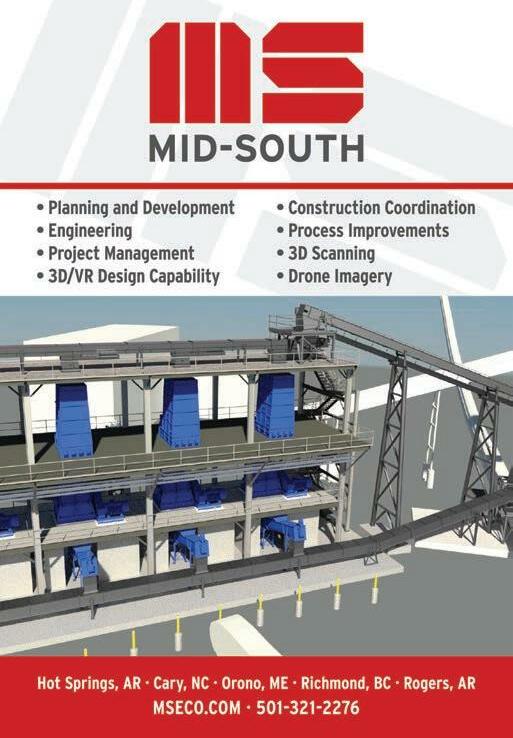
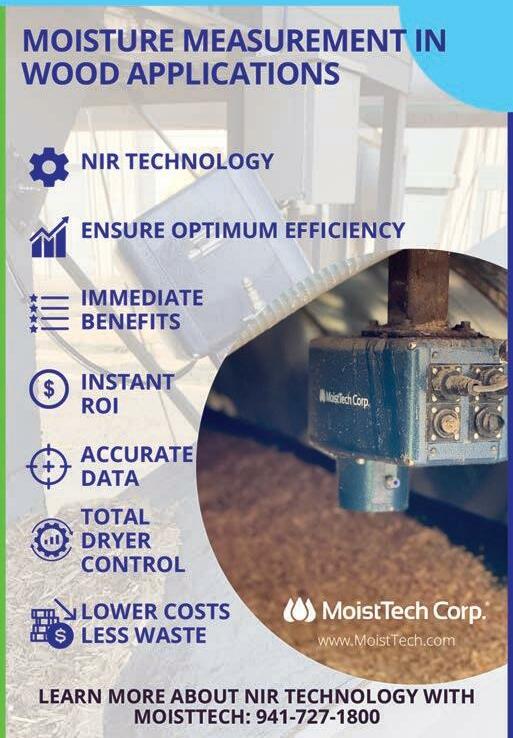