
7 minute read
CURRAN RENEWABLE ENERGY
Choosing To Pivot Loggers Make Pellets
By Jessica Johnson
MASSENA, New York
Sometimes being in business means finding problems to solve. Other times it means solving problems that are already there. Over 30 years ago when the Curran brothers, Pat, Lee and Tim, started their logging business—aptly named Curran Logging—they thought they knew what to expect. Hard workers from basically birth, this bunch from upstate New York has never met a challenge they won’t push through. Remembering an incident from just this past winter, when a machine got stuck and froze into the earth, Pat and Tim were trying to get it out. Tim remembers Pat asking if he thought

they were going to get it out. Without hesitation Tim said yes, he recalls, because there’s literally nothing the pair hasn’t been able to do when they work at it.
“Our father taught us to never quit,” Tim says. “Both our parents, really, taught us to never quit.” That never quit attitude has served them well and is evident in their business. Curran Logging, which started it all, has since morphed from just the family to more than 85 employees. In addition to the family’s logging and chipping crews, the Curran brothers operate a fully automated bagged pellet plant, called Curran Renewable Energy, producing 80,000 tons.

Curran Renewable Energy wasn’t part of the plan 30 years ago, but now it is an integral part of the operation. How does a logging company get into plant operation though? Easy—the brothers saw a problem and they fixed it. Pat explains, “We would have never done this if we had a solid paper industry in our area. That’s how we built the forestry side is supporting the paper industry. As of today, we’re not delivering a single load to the paper industry, but that is primarily due to the current situation with COVID.”
The brothers decided to build the plant to diversify their operation with the goal of being more independent. The push from the New England states to transition the
October 2021 / Wood Bioenergy 15
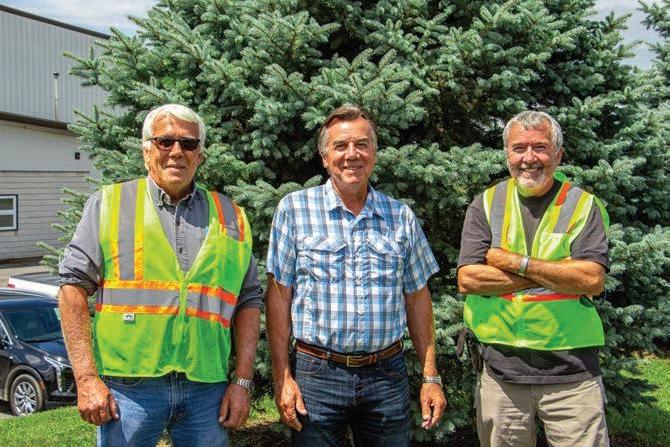
The Curran brothers, from left, Tim, Pat and Lee
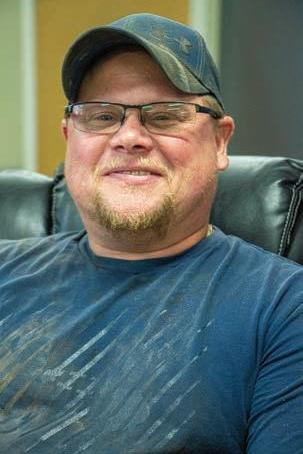
Four Sprout pelletizers handle the 80,000 produced tons.
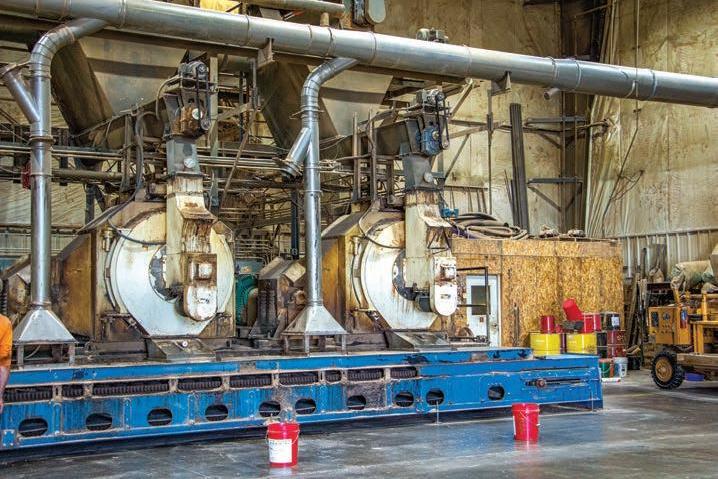
home heating market definitely helped drive the decision, Pat says. The opportunity was in front of their collective faces, so 13 years ago the plant was built. “None of it would have ever happened without the finances to pull it off,” he adds of the monster $15 million investment to get the project off the ground, up and running. Looking back? The Currans admit they were a little forward thinking, but in the space of a heartbeat they say they would do it all over again—even after COVID-19 dealt them a blow to markets further.
Pat believes that without the pellet plant, and the other diversification streams, because of what happened with COVID, there’s a chance the company might not have made it. Once again showing the brothers’ collective ability to think outside of the box and be flexible, they changed their business and kept it afloat.
“We’ve had to do other things forced and ourselves deeper into the aggregate business,” he admits. “But we will always remain in the timber business. Timber is going to be here until we leave the Earth, but as a company you have to do a lot of different things to survive, to keep your people working.” And keeping the people working has been a driving desire for the Currans.
16 Wood Bioenergy / October 2021 Building A Mill
The Currans leaned on John Lundell with Dan Measheaw Energy Unlimited, Inc. to engineer the plant. Pat explains that Lundell provided a turnkey solution for them, using Sprout machines. “I think we would have failed if he had a different engineering group,” he adds. “Right off the bat he asked me where do I want the fire, because all pellet mills will have a fire. He built this in such a way that when we’ve had fires, we’ve been back up in a week. That has saved us.”
Quickly, the brothers learned that in a pellet manufacturing operation, the equipment that got a lot of attention is the physical pellet mills. At the time of building,
Sprout had about 80% of the world market share. Since having been acquired by Andritz, Pat is happy with the machines. The plant’s rated capacity is 120,000 bagged tons for home heating, with an estimated less than 2% of production being sold as bulk production. Thanks to market demand, of the 120,000 capacity, Curran Renewable consistently produces 80,000 tons annually. In order to sell pellets to certain markets, Curran Renewable carries
FSC certification, but not every pellet produced is from the certified wood.
While the 16-acre site has a rail spur, most production is trucked. Pat says the company is open to move chips and pellets by rail, but for now trucks get it done just fine. The yard can store 10,000 tons, and thanks to a significant investment in concrete, Curran Renewable makes use of as much storage as it needs.
Pat sees tremendous value in investing in black top as it keeps not just the facility clean, but most importantly, keeps the pellets clean. Saying, “As far as I am concerned, in a pellet plant, every inch should be blacktop or concrete. If not, the dirt finds it way into the wood chips. The whole goal to meet the supply and needs of people is clean—clean on the wood chip side.
If it is not clean, it is going to fail you.”
Aside from more concrete, since the initial investment,
Curran has expanded to a second Hamer bag line. Used primarily for bagging pellets, but also mulch, the second line helps with bottlenecks on the first line. Though not a desperately needed purchase, Pat says the second line will be quite an advantage overall.
While Curran Renewable Energy has the ability to produce bulk pellets and does, the bread and butter are bagged options of hardwood/softwood blends. Kelli Curran Ramsey, Marketing Manager, says they’d like to see the bulk side get bigger, as it had recently stalled in New York as state incentive programs had lapsed. The cost stable prices of wood pellets against the volatile prices of fossil fuel, plus the BTU Acts new federal tax credit of 26% towards high-efficiency wood and wood pellet heating, should help create growth in the bulk pellet sector.
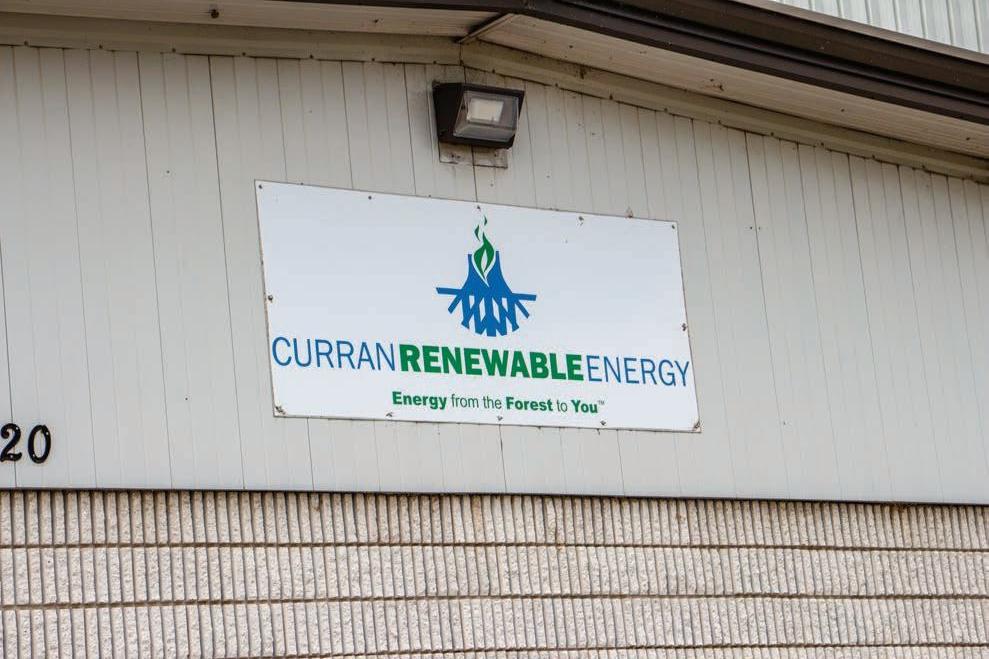
Pellet Flow
For Mill Manager Dan Measheaw, who started with the facility at the beginning working the bagging line, the mill flows well and doesn’t often need babysitting. Chips are trucked in from the Curran family logging operations at a steady clip, stored on the yard. Measheaw and his team have decided on what blends are being made on a given day, chips are dumped into a hopper and pass a Sprout 500 HP hammermill with 5/8th–sized screens.
From the wet hammermill, material enters a Baker 14 x 60 triple pass dryer, then flows to eight cyclones, made by Energy Unlimited, to separate any residual moisture and gases. A Sprout 3/8ths-sized screen dry hammermill preps material for pelleting. Curran Renewable Energy has four pellet mills from Sprout.
Finished pellets are cooled using a Millpro cooler, then pass a Sprout shaker to remove fines. Once clear, pellets are stored in multiple silos with a capacity of 750 tons each. A final Sprout shaker handles pellets before the Hamer bagging lines.
Measheaw runs the plant six days per week. Tim Curran, Jr. acts as night manager, keeping the process going 24 hours per day over the six-day period.
Started over 10 years ago, Curran Renewable Energy has kept the Curran brothers busy.

October 2021 / Wood Bioenergy 17