
10 minute read
FIRE PREVENTION
BIOMASS ENGINEERING & EQUIPMENT
Biomass Engineering & Equipment provides customized solutions for processing, conveying, storing, and receiving biomass and pellets. Our solutions range from individual machines to turn-key systems for bulk material handling and pellet plants with an output between 34,000 and 103,000 tons per year. With decades of experience among wood-product manufacturers, we understand what works and what doesn’t when it comes to wood and can design complete systems that perform better than the competition. Our SMART Conveyors are designed to lower operational costs and keep your facility compliant with NFPA standards to prevent fires and explosions. Environment, health, and safety professionals can confidently recommend our unique, twin-chain drag conveyors because we’re committed to manufacturing machinery that sets the bar for performance and safety. To this end, we offer our conveyors with bolt-on explosion panels, flameless vents, spark detection, deluge, and fast-acting diversion gates. Components standard on our conveyors include enclosed troughs, dust-tight bearings and bushings, dust-tight inspection doors, sealed shafts, low-friction chain assemblies and plug detection.
In our commitment to safety, we have physically tested and modeled our conveyors’ ability to withstand explosive pressures. We have also had our most common model analyzed by a third party for its ability to withstand a deflagration event.
We also offer explosion-mitigation technologies for other bulk-material handling equipment: Containerized silos, metering bins, and surge bins. And we offer belt-drive disc screens to remove metal and other foreign objects from the material stream as required by NFPA 664.
Other equipment we manufacture includes ash conveyors, push-pull reclaim floors, feeder bins, trailer-receiving stations, trailer-loading stations, drum chippers, high-volume roller debarkers, log decks, log troughs and rake-back systems for chain bin outfeed. We design all our equipment for long life and optimal efficiency to provide our customers the best value for their purchase.
CLARKE’S SHEET METAL
The PyroGuard System, manufactured by Clarke’s Sheet Metal, Inc., is designed to detect and extinguish sparks in pneumatic conveying and material transfer systems. The spark sensors detect infrared radiation, which in turn activates a solenoid valve to introduce an atomized water spray inside the duct to extinguish the sparks. During a normal activation, production can continue, as only a limited amount of water is introduced into the pneumatic system. The system is typically installed prior to a dust collector and provides protection for plant personnel as well as equipment and assets.
In addition, Clarke’s offers the PyroComm Windows software package, providing for interaction from the PyroGuard Control Console to a PC unit. This powerful software program enables monitoring of the spark detection and extinguishment system from a remote location.
To supplement the PyroGuard system, Clarke’s manufactures a complete line of safety devices such as HiSpeed abort gates, backdraft dampers and isolation dampers.
Other products which Clarke’s manufactures include flo-matic storage and metering bins, rotary screens and classifiers, pneu-aire filters, rotary airlocks, rotary feeders, fans and complete low pressure and high pressure pneumatic conveying systems.
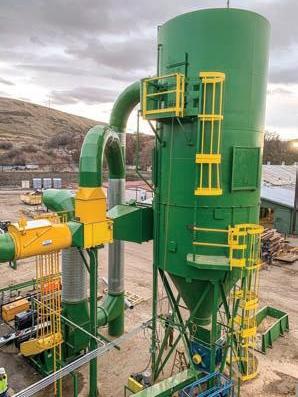
CV TECHNOLOGY

CV Technology has announced FM approval for its HRD suppression systems, after a long and very strict certification process. We want to share this extraordinary milestone, CV Technology’s products have had ATEX approval for over fifteen years, however, this additional level of FM certification further solidifies the company’s engineering reliability.
“We continue to push ourselves through innovation and certification,” says Marty Cvetas, President, CV Technology, “to be the best partner for you, for explosion isolation and protection.”
FM approval is a certification mark that companies get after successfully completing the five-step approval process. The certificate is issued by the independent testing division FM Approval, which belongs to the globally renowned insurance company FM Global Group. FM Approval focuses on researching and testing all products to ensure that they meet only
18 Wood Bioenergy / October 2021
the highest standards for property loss prevention and safety.
FM Global, based in Rhode Island, with offices worldwide, is one of the oldest and largest commercial insurance companies orientated on property loss and risk prevention, especially for large corporations. FM Global was established in 1835 and has been growing with its clients for nearly 180 years ever since. The FM Approved mark is recognized and respected worldwide, as a signifier that a product conforms to the highest standards of quality, technical integrity and performance.
EVERGREEN ENGINEERING
The 2020 COVID-19 crisis put a significant damper on wood processing facilities to perform the NFPA 652-required Dust Hazard Analysis (DHA). The need is still there to perform DHA and any subsequent mitigation of hazards for fire, flash fire, or explosions. Worldwide, incidents that can be contributed to issues with combustible dusts continue to happen weekly. Evergreen Engineering can help facility owners perform DHA through our knowledge of the NFPA standards, industry practice and the multiple DHA studies we have performed for wood processing facilities. We can lead companies step-by-step through a risk-based analysis on processes, equipment, and facility operations, creating a prioritized and well-documented plan for mitigation of dust hazards. Our team of engineers includes internal auditors formerly employed by Weyerhaeuser, SierraPine, Willamette Industries and other wood products-related companies. We will make recommendations for the collection and containment of combustible dust, along with recommendations for maintenance and operations best practices. Our employees have designed and overseen the installation of dust collection cleanup systems and internal audits in particleboard mills, machinery manufacturers, beverage companies (glass dust) and other industrial organizations, including the world’s largest producer of wood charcoal. What are the main points of an audit? Standards are retroactive: Each manufacturer of materials judged to be combustible is required to have a DHA performed. Assess your current requirements: Each state has different regulations that may exceed the NFPA standards. You must determine the hazardous characteristics of your combustible dusts. Based on NFPA 652 and your industry-specific related NFPA standards, you must evaluate your hazards and update documentation and your procedures on a regular basis. Develop a management of change procedure to manage change to the process materials, technology, equipment, procedures, and facilities.
How can Evergreen Engineering help you with compliance? First, with assessment: Evergreen will help you identify what is required for your plant based on the local, state, NFPA and OSHA standards. We will assess your current procedures, documentation, labeling, and processes to help you understand the requirements. Then, help you identify solutions by conducting a DHA to find solutions for being compliant. Finally, Evergreen will evaluate economic options and provide project management along with engineering to implement process changes.
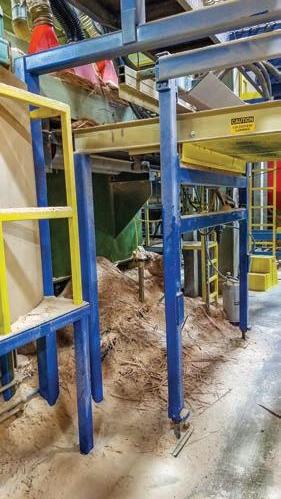
FAGUS GRECON
Fagus GreCon’s New Spark Detector offers preventive fire and explosion protection using new detection technology to identify dangerous ignition sources.
Common causes of fires are heat, sparks, embers and hot particles. One of the most efficient measures to prevent fire or dust explosion is the early identification of the ignition source.
Sparks and embers are often the source of larger fire and explosion events. Preventive fire and explosion protection is an important measure, not only to protect production, but also the company and the people working within the facility.
Fagus GreCon’s new DLD 1/9 Spark Detector offers additional protection to industries with new intelligent detection technology (IDT). IDT not only identifies hazardous moving ignition sources before a fire breaks out, but the DLD 1/9 detector is also able to differentiate between dangerous sparks or harmless incidence of extraneous light due to leaky/damaged pipes or an opening of an inspection flap.
The system provides excellent preventive protection, as it does not wait for an actual fire or explosion to erupt. The system prevents the development of a fire or explosion by the early detection and elimination of the ignition source. With a
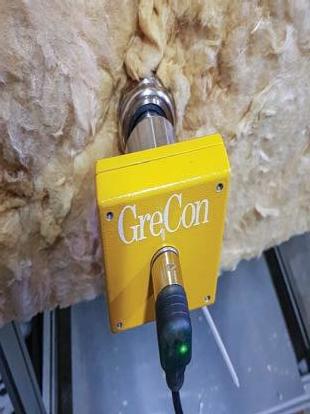
October 2021 / Wood Bioenergy 19
GreCon system it is possible to detect and eliminate ignition sources before a fire or a dust explosion occurs. IR detectors monitor the conveying paths and activate high-speed water extinguishing within milliseconds. The diversion or shut-off of product flow is also an option if extinguishing with water is not possible for the application.
FLAMEX
Flamex Inc. has been involved in protecting industrial facilities from the hazards of fire and explosion for over 40 years. We specialize in the prevention of ignition in facilities that handle combustible dusts. Our experience in the industrial wood pellet industry has given us a deep understanding of the risks inherent in the production process and how to address them in a manner that eliminates or minimizes production downtime.
The production of wood pellets involve operations that are often conducive to the generation of sparks and fire. Size reduction operations, such as the hammermilling of dry wood material, are often a source of sparks that are transported in the material flow through the pneumatic system. Fires and burning embers may also result from the drying process due to the presence of high temperatures and possible upset conditions with the dryer. Other processes such as pelletizing, pellet cooling, screening and product load out may also produce ignition from sparks, overheated pellets and mechanical friction sources.
If not addressed, fires and explosions resulting from normal production processes can have devastating consequences for a business large or small. This is an ever-present problem in this industry that requires continual management to ensure workplace safety, asset protection and business continuity. The design, installation, operation and maintenance of automatic fire protection systems play a critical part in the effort to mitigate these hazards.
Spark detection and extinguishing systems have long been recognized by the industry and the loss control community as an effective measure in the prevention of fire and explosions in dust collection and air filtration systems. Introduced to North America in the late 1970s, the Flamex Spark Detection and Extinguishing System became the first system of its type to gain a factory mutual approval. These systems have proven to be an invaluable part of an overall protection design in wood pellet facilities.
As part of a major global fire protection organization, Flamex Inc. has a wide range of detection and suppression components available to meet the specific protection requirements of varied applications that may be present within a single manufacturing facility. We continually strive to improve our product offerings in step with the latest technological advances.
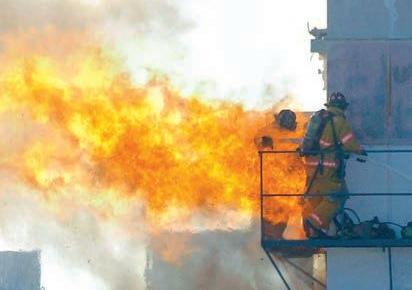
IEP TECHNOLOGY
Within a wood bioenergy processing facility, the use of explosion relief vents is a highly effective and economical option for a well-planned explosion protection strategy. Explosion vents are considered “passive” protec tion solutions meaning they operate solely from the pressure generated by an ex plosion. An explosion relief vent by design will open at a predetermined pressure and relieve any overpressure to a point outside the vessel. Of course, in the event of an explo sion, this pressure is also accompanied by flame that can cause additional damage outside of the protected vessel including providing an ignition source for secondary explosions. Two types of vents are available to provide protection for a protected vessel including “rupture style” and “flameless” vents. Both are economical protection option and are available in a va riety of sizes, configurations and materials to ensure fast reliable operation during an explosion event. The difference between these two vent types is that rupture style vents will relieve both pressure and flame while the flameless vent has an integrated flame arrestor, which will relieve pressure while preventing the release of flame outside of the protected vessel. Flameless explosion vents provide protection for a process that may be located indoors or other location where the explosion generated fireball cannot be released to a safe area.
IEP Technologies provides a complete range of cost-effective explosion protection solutions. The IEP range of vent rupture panels are available in a wide range of sizes and shapes including round, rectangular, flat and domed. IEP also provides flameless venting solutions with its the IV8 and EVN style flameless vents. These provide an explosion protection solution for process vessels that are located inside a building or other area where standard explosion venting cannot be safely employed. The IV8 utilizes a stainless-steel explosion relief vent and flame arresting mesh enclosed in a durable carbon steel coated frame. The integrated vent burst detection sensor allows plant personnel to respond accordingly in the event of an explosion within the protected application.

20 Wood Bioenergy / October 2021
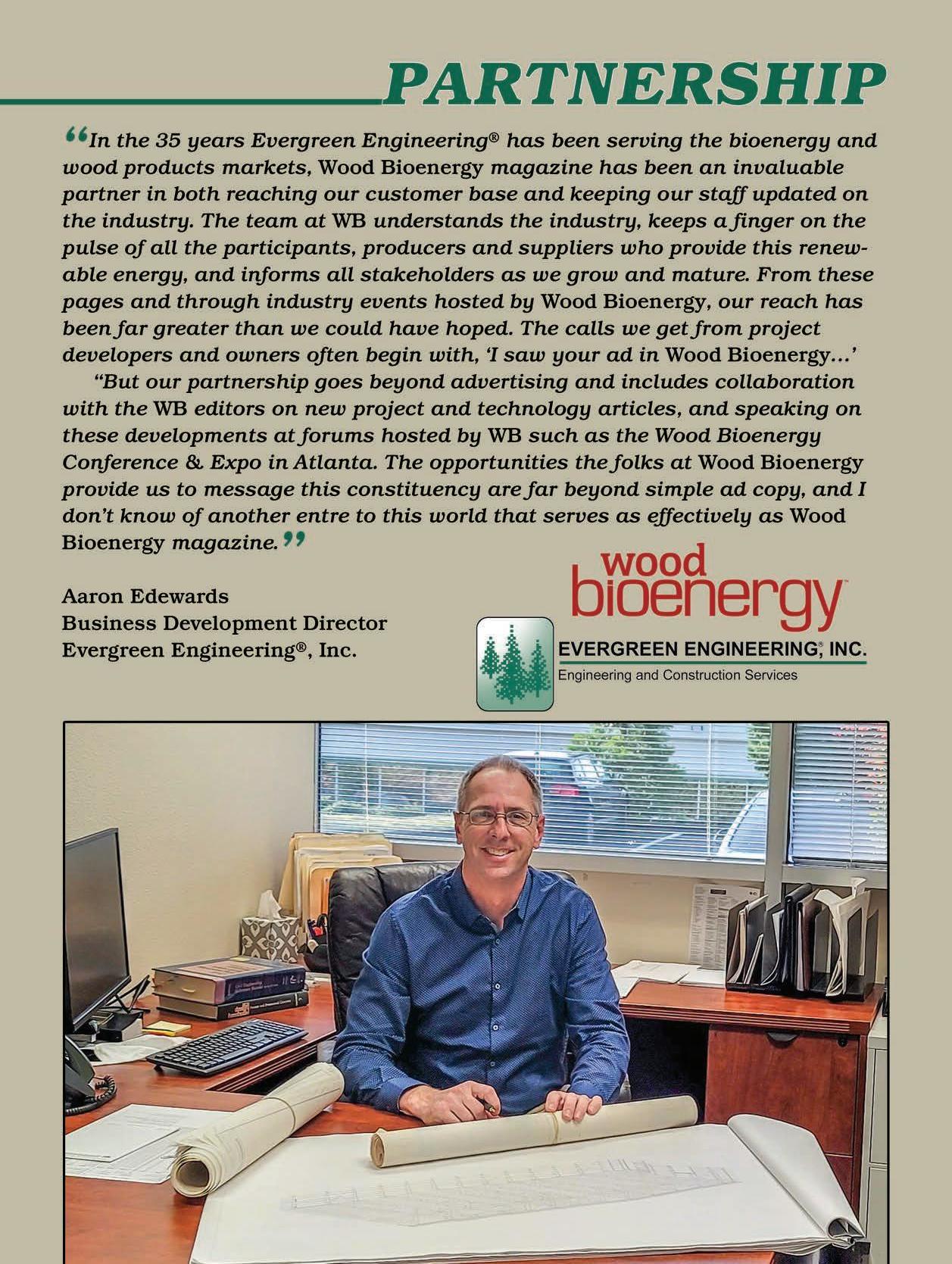