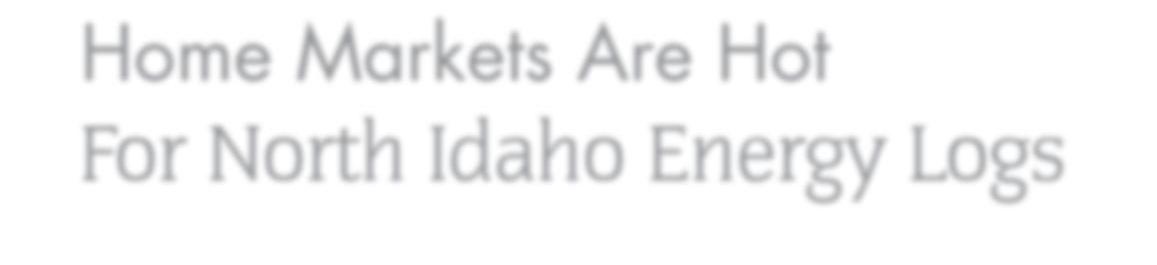
7 minute read
NORTH IDAHO ENERGY LOGS
Home Markets Are Hot For North Idaho Energy Logs
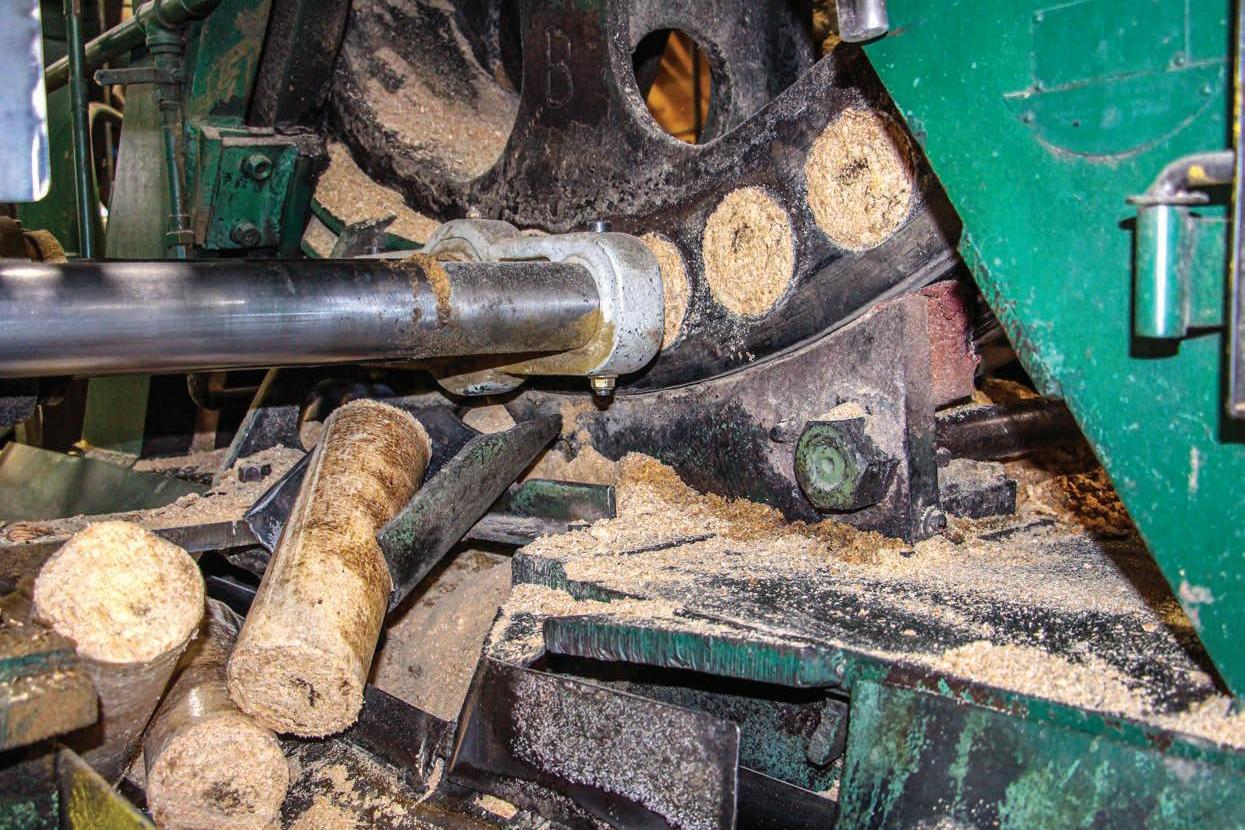
By David Abbott
MOYIE SPRINGS, Id.
Located in Boundary County, about 30 miles south of the Canadian border, the headquarters of North Idaho Energy Logs sports both the U.S. and Canadian flags. “That’s a common thing in the community,” says Clark Fairchild, co-owner of the company and general manger at this facility. “We do pull quite a bit of shavings and sawdust out of Canada.”
Fairchild has two partners, Rob Pluid and Tom Oxford, both of whom are also in other businesses. Pluid runs a logging operation while Oxford’s Oxford Inc. does municipal road work and dust control for several counties and some logging roads. Fairchild and plant manager Bob Warrell oversee the Moyie Springs plant day to day.
The company started in 1986; Fairchild’s and Pluid’s fathers were part of the original ownership team, along with two other partners. Their original focus was on energy logs, an 8 lbs. product made of sawmill residuals. In 1992 they added one pellet mill. Since the current generation bought the business in 2007, they have expanded both sides of the operation. Now they have nine log machines and three pellet mills.
Products
Home heating is the primary application for North Idaho’s products, sold primarily to feed and farm stores, lumber yards and hearth shops. Marketed as an alternative to traditional firewood, energy logs (or fire logs) have several benefits over cordwood, Fairchild says. Moisture content runs around 7%, compared to 18-20% in cordwood. The lower the moisture content, the higher the BTU.
Fire logs are also very dense. “Douglas fir (firewood logs) weigh roughly 34 lbs. a cubic foot,” Fairchild estimates. “Our logs…would weigh close to 80 lbs. a cubic foot.” As such, the size can be deceiving. The logs are relatively small: around 4 in. diameter and 13 in. long, but they pack a big punch in a
14 Wood Bioenergy / December 2021
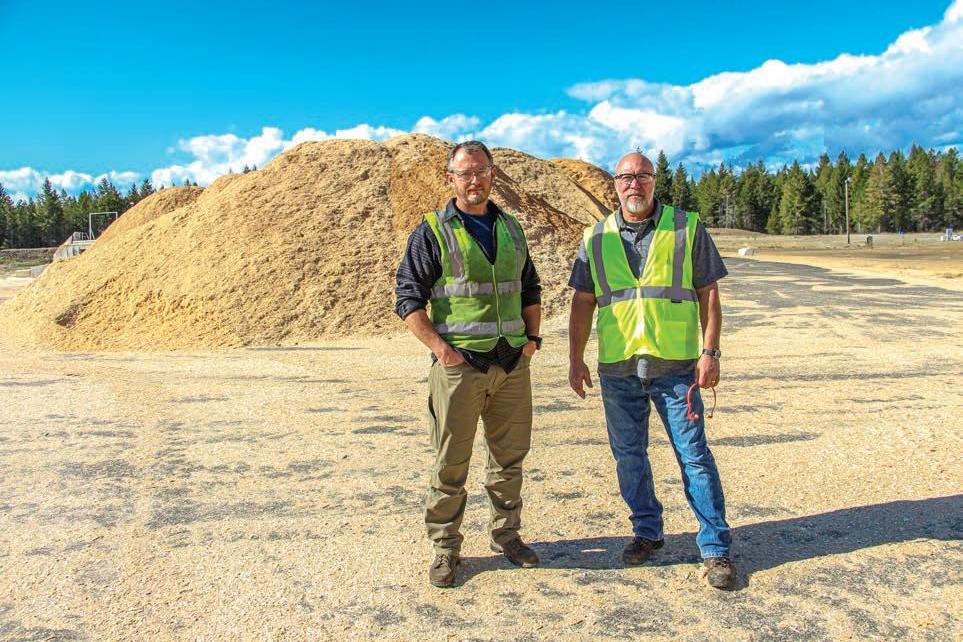

small package. “Most people, when using a wood stove to heat their home, will shove it as full as they can with cordwood, which they’re designed to do,” Fairchild says. “But with these we always tell customers no more than two at a time. When you put that load in it doesn’t look like your stove is full enough, but they achieve a very long burn time because of the density.” Each log generates about 68,000 BTU and can burn for up to 10 hours, he asserts, with variation based on draft location.
North Idaho’s market for pellets is similar to its log market: residential heating. Like the logs, the pellet blend is designed to make a very low ash, high BTU product. “The species we have available in this area lend themselves well to that,” Fairchild says.
The company has two different branded pellets: the North Idaho Energy Log brand, which is produced in Moyie Springs, and Purcell pellets, made at a sister plant 90 miles southwest in Hauser, Id., which the company acquired in 2013.
Process
The material for both pellets and logs is the same: sawdust and shavings, sourced from multiple sawmills around northern Idaho, British Columbia and eastern Washington. The plant does no whole log chipping whatsoever. “We are looking for clean fiber; we don’t want any bark whatsoever,” Fairchild explains. “Bark is where all the dirt ultimately ends up. It is abrasive to our machines and results in high ash content.”
Shavings, he goes on, work well, especially because it takes less to dry since it has already been through the kiln process. “Unfortunately there just aren’t enough shavings to supply the demand. Sawdust also works great; it just takes a little more energy to dry it.”
At the start of the process, sawdust can be as high as 50-55% moisture content; shavings can be 15-20% moisture. Before it is compacted into pellets or logs, everything, sawdust and shavings alike, runs through a large rotary dryer here to bring it down to roughly 8%. The material loses some additional moisture in the manufacturing process; logs end up around 6-7% moisture, pellets around 4-5%.
Incoming truckloads are dumped by tipper onto an asphalt pad and residuals are segregated into piles by species and by sawdust or shavings. “Once the material is separated, we build a blend that we have found over the years works really well to achieve a high BTU and low ash content,” Fairchild explains. “Ultimately that is what we are looking for.”
A wheel loader dumps mixed piles to a feed bin, from which the material flows to a collection screw that conveys it to the infeed of a Solagen rotary dryer drum, with heat supplied by a Coen 33 million BTU burner. After drying, a Williams hammer mill grinds the combined material into a consistent size—roughly 1/8 to 3/16 in. From that point it is blown over to a surge bin in the production facility. A distributor tank feeds nine log machines and three pellet mills. How much of the material feeds to the log side or the pellet side is determined by market Co-owner/GM Clark Fairchild, left and Moyie Springs plant manager Bob Warrell Each packaged fire log unit contains 240 logs.
December 2021 / Wood Bioenergy 15
demand. “We always run some of each but we might drop a log machine or a pellet machine out to maintain our production at the most efficient level,” Fairchild explains. If they ran all 12 machines wide open at the same time, the plant would exceed its permitted tons per hour with the DEQ (Department of Environmental Quality, a state agency) on the dryer system. “So we do have to watch that closely.”
The log machines were designed in 1929 and manufactured in the ‘30s-‘50s; they are the original Presto log machines. “That trade name is now owned by another company so that’s why we call them the North Idaho Energy Log even though it is made with the same equipment,” Fairchild says. “To my knowledge we are the only company still running the original Presto log machines.” In the log machines, a motor drives a tapered screw, which forces sawdust into the die on a wheel. A hydraulic ram holds resistance against each log as it is formed in the die, about 20,000 lbs. per square inch. The friction creates heat that warms the lignin and under pressure it binds that back together into log form. Cooling as it exits the die allows the log to solidify in its shape, as the lignin sets up and binds the sawdust back together; if it came out hot, it would accordion and break apart, Fairchild explains. As a new log is pushed out, it acts as a plug for the next log being formed behind it. The machines on average turn out four and a half or five units of logs per hour—at 240 logs per unit, that’s 1,080-1,200 logs an hour.
Meanwhile, on the pellet side, both the Moyie Springs plant and Hauser plant have three pellet mills: two Andritz and one CME (Colorado Mill Equipment).
Both plants have three pellet machines.
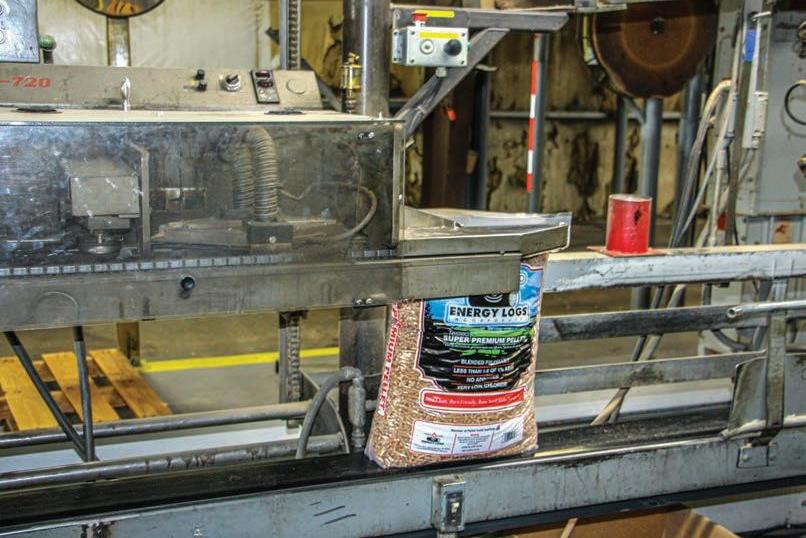
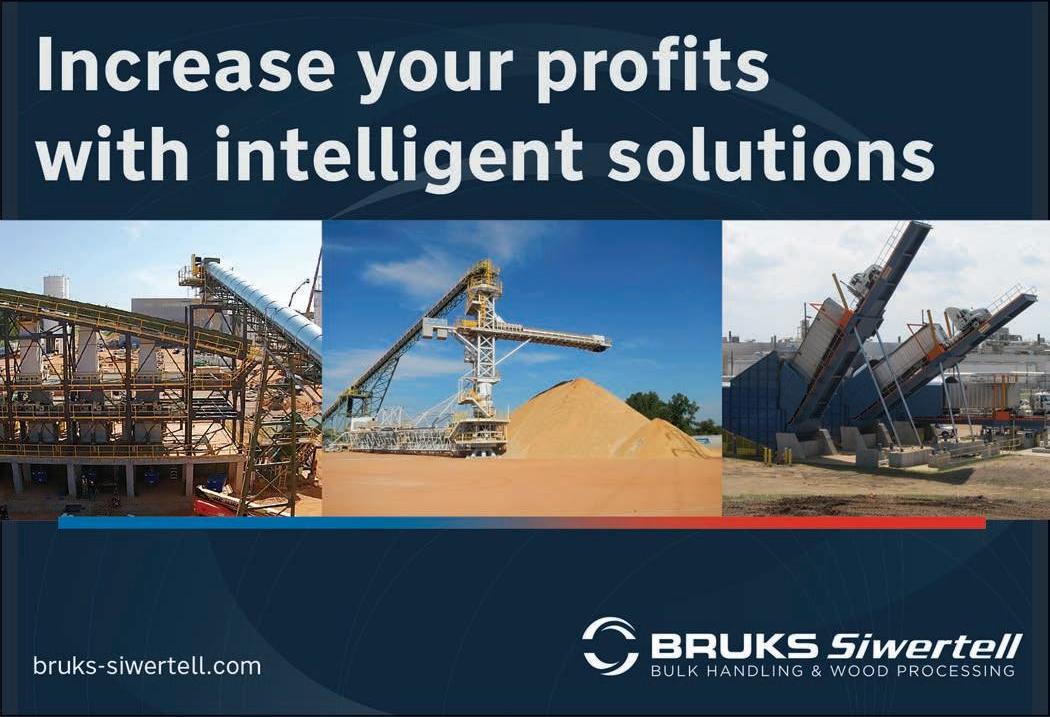
16 Wood Bioenergy / December 2021
Mill sawdust and shavings are dried and ground before processing into logs or pellets. When all three are running, the pellet mills together produce around 5.5 tons an hour. The Hauser plant, which only makes pellets, is much more automated; nobody there manually stacks or handles any bags. The Moyie Springs facility has a Columbia/Okura robot for stacking the bags, but an operator still slips empty bags on manually. The logs are also stacked manually. All logs are stored in one of four warehouses, while pallets of pellets are wrapped and can stay outside under double weather covers. Between the two plants, office staff and truck drivers, North Idaho employs 42. A lot of the manpower is dedicated to the tremendous amount of maintenance required throughout the plants. The company staffs a full machine shop to fabricate components for the log machines, which are no longer available off the shelf. “Unlike the components to make wood pellets; you can call up a number of companies and order those,” Fairchild notes. “But the parts for the log machines we have to build, and that is a constant job in itself. Sawdust is abrasive, especially under all that pressure and heat, and it wears out parts pretty quick.”
The pellet bag-stacking robot at Moyie Springs also requires a fair bit of maintenance, including the software side. “You don’t have computer programmers just standing around in Bonners Ferry, Id.,” Fairchild points out. “There are some in Coeur d’Alene and some locally who do an excellent job when it comes to PLC. They just don’t get into the robot side of things because that is so specialized. So we’ve had to bring people out of Texas and Chicago for the robotics.”

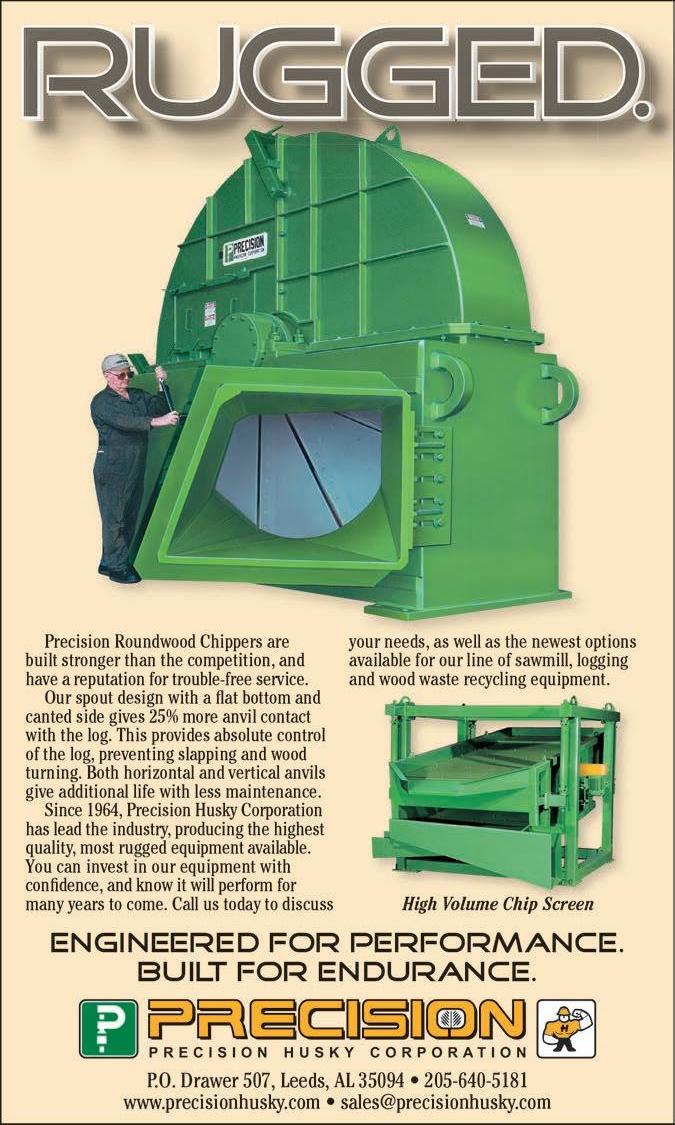
December 2021 / Wood Bioenergy 17