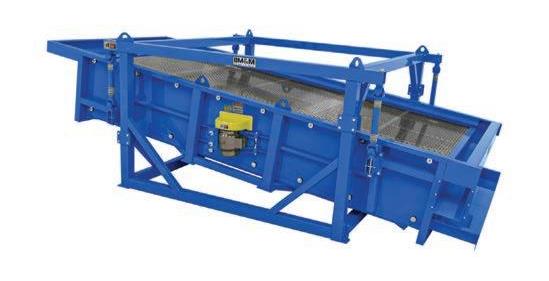
15 minute read
WOOD YARD TECH
EDITOR’S NOTE: The following companies submitted these editorial profiles and images to complement their advertisements placed elsewhere in this issue. Please refer to those advertisements for web site and contact information. All statements and claims are attributable to the companies.
BM&M
BM&M Screening Solutions manufactures a wide selection of custom high-speed gyratory screening machines for the bioenergy industry. We produce a variety of screening machine sizes to meet your capacity needs. The element area available ranges from 12 ft.² up to 600 ft.².
BM&M’s experienced engineering staff provides extensive before and after sales service that includes complimentary lifetime factory testing, building load calculations, sub-base engineering, courtesy start-up supervision, and stocked OEM aftermarket parts facilities in the United States and Canada. With our expertise built over more than 50 years of solving application issues, our team will provide you with the right soBM&M has a variety of screening machine sizes to fit a variety of capacity needs lution for the job. Reach out to BM&M Screening Solutions today for more information on how we can help your company.
Bruks Siwertell
Increased wood handling and dust requirements continue to fuel a strong demand for Bruks Siwertell’s expertise. The company’s extensive line of wood yard technologies enables dry bulk handling and processed wood industries to operate safely, maximizing their efficiency and minimizing the negative impact of dust. This improves both operational sustainability and environmental protection.
Optimized to reduce dust emissions, Bruks Siwertell’s low-profile end-pivot truck dumpers ensure that trucks unload their cargo at a low elevation (approximately 2.5 m above the ground) and directly into the back end of the hopper. This keeps the impact of free-flowing material from falling out of the back of the truck very low and results in minimal dust emissions, particularly when handling very dry materials such as wood shavings or pellets. Bruks Siwertell can help reduce dust emissions from stacker reclaimers.
The truck dumper can be covered with a fixed or rotating hood. Both versions mitigate dust emissions by bridging the gap between the truck dump end and the covered hopper. Where no dust emissions are permitted, a dust collector can also be specified. Dust collectors can be mounted directly over the covered hopper or ducted to a central baghouse so that the customer can make better use of it. Bruks Siwertell has provided several truck receiving systems with particulate emissions guarantees.
Bruks Siwertell also offers an extensive range of conveying systems, including air-supported conveyors, which eliminate the use of rollers beneath the belt, delivering the highest possible levels of dust control and operating efficiency, and bringing huge cost savings from reduced maintenance requirements.
The company has also developed upgrades specifically targeted at reducing dust emissions for facilities that use stacker reclaimers. These systems are always supplied with infeed hoppers on the stacker boom, which have undergone substantial design improvements. The latest generation of infeed hoppers incorporate several enhancements. Deflector plates located inside the hopper control the flow of material onto the conveyor, directing wood chips to the center of the stacker belt. This gives a greater level of material management to optimize the efficiency of the system, allowing for a smooth motion of the luffing boom and an important reduction in dust emissions.

Brunette Machinery
Brunette Machinery has been a premium supplier to the forest industry for over 75 years, specializing in wood processing and material handling systems. Our products are ideal for the lumber, pulp and paper, and renewable energy industries and include chippers, hogs, butt reducers, conveyors, debarkers, log singulators and other wood processing equipment.
But we don’t just sell chippers and hogs! Our sales team collaborates with our customers to provide complete wood
18 Wood Bioenergy / December 2021
processing systems that are designed to suit their needs. From a single machine to a complete plant system, our products meet the highest standards, are easy to implement and provide true benefits.
Our latest project involved such a plan. Our customer, a producer of industrial wood pellets, needed to expand their pellet mill facility due to increased global demand for sustainable wood bioenergy.
Our proposal was providing them with a complete Brunette chip supply system—including process planning, equipment, start-up and after-sales services. The main targets for this system are to increase uptime and capacity, minimize energy consumption, and maximize raw material yield.
Our custom-designed chip supply system will provide all the elements they need to convert whole logs into microchips as the first step of producing wood pellets for biomass fuel. From the scaffolding and maintenance platforms that house the log deck, to the conveyors and the chipper, they will have the benefit of dealing with one supplier for the entire project. Not only will this increase output, but it will also save on maintenance costs.
This Brunette chip supply system includes the design, engineering and project management of the entire system. The machinery includes a Brunette whole log micro chipper; chipper infeed chain conveyor; refuse conveyor and chuting; chipper and infeed system support structure complete with catwalks; custom flow control gate; chipper outfeed chuting; chipper outfeed chain conveyor; belt conveyor and chuting; outfeed conveyor supports complete with maintenance access platform; 20 ft. container complete with installation of HPU and hydraulic plumbing
After inspection and testing, the components of the chipper system were loaded onto 12 trucks and delivered to our customer in northern British Columbia.
Brunette Machinery supplies complete chipper systems to meet highest performance and reliability criteria.
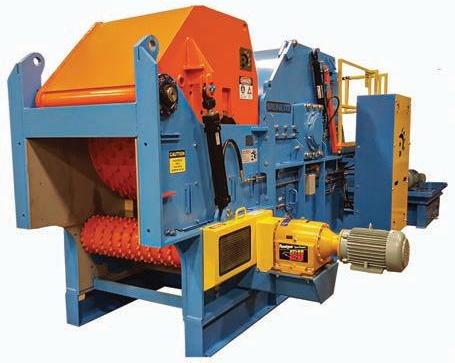
CEM Machine Inc.
CEM Machine is a 100% employee-owned manufacturer of large, heavy-duty disc chippers and microchip processors.
Pellet producers have to put energy in to get a product that provides their customers with even more energy out. Therefore, pellet producers achieving the greatest net energy difference can result in a higher operating margin. For efficient drying, you must reduce each feedstock to shreds.
The relative ease by which fragile 6 mm (1/4 in.) long micro chips can be reduced to shreds for drying is in stark contrast to the tremendous amount of work required to reduce the large conventional chips.
So while making micro chips from logs requires slightly more energy than making conventional chips from logs, micro chips are subsequently reduced to a drier feedstock with comparatively less energy. The result is that the total required chipping, plus milling energy for preparing a drier feedstock is substantially less with microchips.
Over a decade ago, CEM commissioned the first disc-type micro chip chipper in a pellet manufacturing facility powered by a drive less than half the size of all other major suppliers. This pellet producer and practically all of the others operating our microchip chippers have consistently preferred even smaller micro chips directly from the log to achieve their greatest efficiencies and production levels.
So whether your process needs high quality, efficiently produced micro chips or conventional wood chips, for superior design, long life, high reliability, and simple maintenance, choose CEM’s micro chip processors and chippers— your best choice.
An illustration comparing typical dryer feedstock (left), CEM micro chips sized to 1⁄4 in. and unscreened (middle), and conventional chips sized to 3⁄8 in. screened.
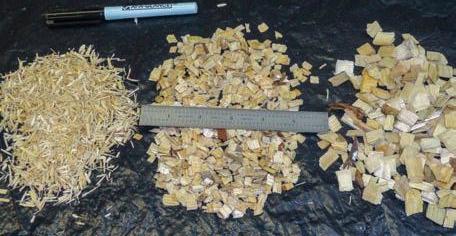
Evergreen Engineering
For more than three decades, Evergreen Engineering has offered the best possible range of knowledge and capabilities to address retrofit, expansion, and new construction for wood processing projects. We design new safety systems, develop new environmental controls, install power generation and distribution, and improve processes, helping mills
December 2021 / Wood Bioenergy 19
across North America remain competitive with greater safety, recovery and speed.
Evergreen is a full-service consulting engineering company, serving the wood products industry since 1985. Our staff comprises mechanical, civil/structural, electrical/controls, environmental, and chemical engineers, designers, and drafters. We can deploy all project phases from planning through construction, including scheduling, feasibility studies, preliminary engineering, capital estimates, detail engineering, process design, environmental permitting, purchasing, commissioning and start-up assistance, and project management.
We welcome your questions, and would be pleased to help with your new or existing facilities.

An example of Evergreen Engineering's material handling projects
Fulghum Industries
Fulghum Industries, a Georgia-based manufacturing company, has been serving the forest products industry for over 60 years, and continues to develop and improve the technology on which the industry relies. Recently, Fulghum developed a new knife clamp design to aid those utilizing disc chippers. These new, front-loading clamps will lead to a safer, more efficient chipper operation. Traditionally, knife clamps and their hard ware are located on opposite sides of the chipper disc, requiring two workers just to change knives. With Fulghum’s new design, the clamps and their mounting hardware are located on the same side as the knives, meaning that one worker can now change the knives in the same amount of time that it takes two workers with a traditional clamp. Also, with few er people having to physically interact with the clamps, there is a reduced chance of accidents due to misNew Fulghum front-loading clamps and their mounting hardware are located on the same side as the knives. communication or inexperience. In addition to greater efficiency and safety, Fulghum’s front-loading clamps are engineered to resist chip packing and unwanted stud releasing that can occur with traditional clamps. Contact us today to upgrade to a more dynamic chipping operation. Mid-South Engineering can assist with equipment center selections, as well as design and engineering of material handling systems.

Mid-South Engineering
Mid-South Engineering provides full-service engineering and consulting for building products, bioenergy and pulp and paper facilities many of which utilize wood yards for converting roundwood into chips or flakes for further processing downstream. The major equipment centers for these wood yards include log handling cranes, debarking drums, chippers and chip storage/reclaim systems. It goes without saying that selecting the right major equipment for the intended service is an important part of a successful wood yard operation.
Additionally, a properly designed material handling conveyor system for the products produced in the wood yard (bark, chips, flakes, etc.) is also critical in terms of production rates, operating and maintenance costs, ease of clean up and other factors as well. After all, the wood yard conveyor system has to efficiently handle the same quantity of material that is seen by the crane, drum and chipper.
While the major wood yard equipment center designs will vary from mill to mill, the equipment is somewhat standard for a given production rate, species to be processed and anticipated longevity or operating life, the material handling conveyor design is custom for each site. This is due to things like layout restraints, overall mill configuration and secondary processing equipment utilized such as bark hogs, chip screening systems, and secondary chip size reduction equipment.
Key design considerations for site specific conveyor systems include: belts vs. chains, operating speeds, transitions heights and arrangement from conveyor to conveyor or conveyor to process equipment, duplication of mechanical components where possible, chutework and transition plates angle of incline, conveyor clean-up means and methods,
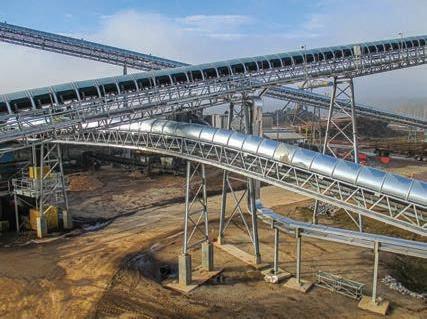
20 Wood Bioenergy / December 2021
maximum design capacities (flow rates) vs. average flow rates, use/application of control devices such as plug chute switches and “zero” speed switches, use of variable speed drives, and where the use of pneumatic aspiration systems make economic sense.
Mid-South can not only assist in the proper selection of the major wood yard equipment centers but also provide a well designed and engineered material handling system which is equally important for a properly functioning wood yard.
Precision Husky Corp.
Whether in a chip mill or pellet mill wood yard application, choosing the right chipper and the right chip screen can help maximize the efficiency of wood yard processing and production. Having the chipper sized according to the customer’s required production output and chip specifications makes the difference between a smooth-running wood yard and one that struggles to keep up. To assure that there is no bottleneck in the wood yard operation, the chipper and screen need to be sized to handle more than customer required production.
Precision Husky Corp. has been manufacturing chippers and screens for nearly six decades. During that time, we have developed the experience and expertise to supply the wood industry with over 5,000 chippers and nearly as many chip screens worldwide.
With nine different chipper sizes, ten different screen sizes and Precision Husky chippers are sized from 38 in. to dozens of configurations to meet the customer’s needs, Precision Husky can engineer and manufacture a chipper and screen to suit any 118 in.; screens offer as much of a variety from 13 tons per hour to 150 tons per hour. wood yard application. Whether making the conventional paper mill type chip or the special pellet mill micro chip, Precision chippers can be set up to accommodate a customer’s requirements.
From our smallest 38 in. sawmill chipper, to our largest 118 in. chipper with a 36 in. diameter roundwood capacity,

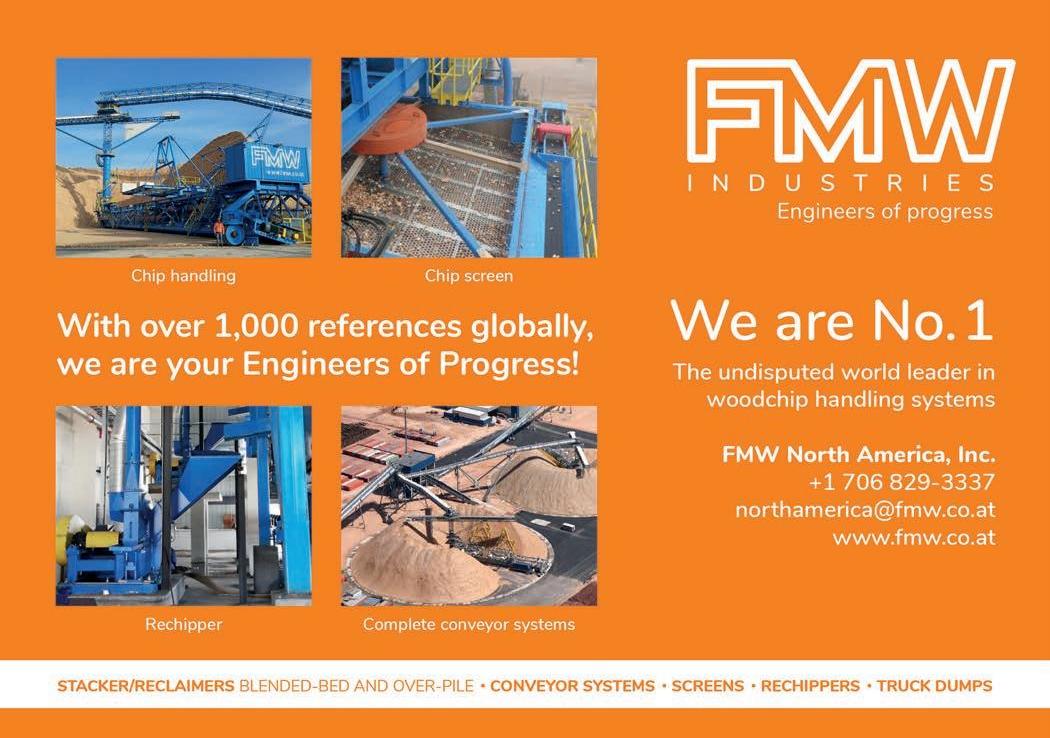
December 2021 / Wood Bioenergy 21
we can offer a chipper size to suit many wood processing applications.
The same can be said for Precision Husky chip screens. From our smallest PCS-55 sawmill screen, to our largest HV-1020 high-volume chip screen, we can handle production rates from 13 tons per hour to 150 tons per hour. If more production is required, then multiple screens can be arranged with a diverter valve setup, allowing constant production without any shut-downs due to maintenance requirements. In a configuration with a three screen setup, at least one or two screens, depending on required production, are always in operation, just in case one is down for maintenance.
It is imperative that the screen setup can adequately match the chipper output in wood yard applications. At Precision Husky Corp., our experienced engineers and sales team can ensure that these requirements are met in any application.
Rawlings Wood Hogs
With over 45 years of experience in the forest and sawmill related industries, Rawlings Wood Hogs has delivered a reputation for durability, high performance and reliability. As proven leader in wood grinding technology, Rawlings assists our customers with the design of custom wood recovery systems to meet our client’s specific processing needs and budget.
Rawlings Wood Hogs come in all shapes and sizes, we offer a complete line up of seven different sizes of both vertical and horizontal hogs to fit any application; from simple stand-alone vertical hogs, to complete multi-dimensional horizontal grinding systems. Add a wide variety of available options, and you’ve got the flexibility to customize the perfect wood recovery system. Each system can be designed with work platform decks, choice of belt, Rawlings has the flexibility to customize a wood recovery system thanks to its breadth of products. chain, vibrating infeed and outfeed conveyors, metal or magnet protection and product screening that allows the customer to protect their investment while producing a high-quality consistent end product.
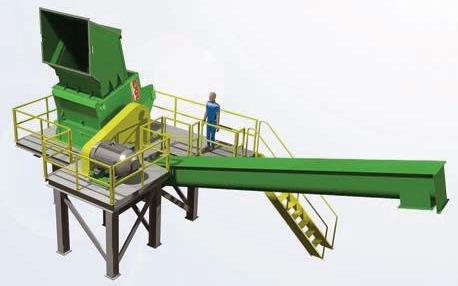
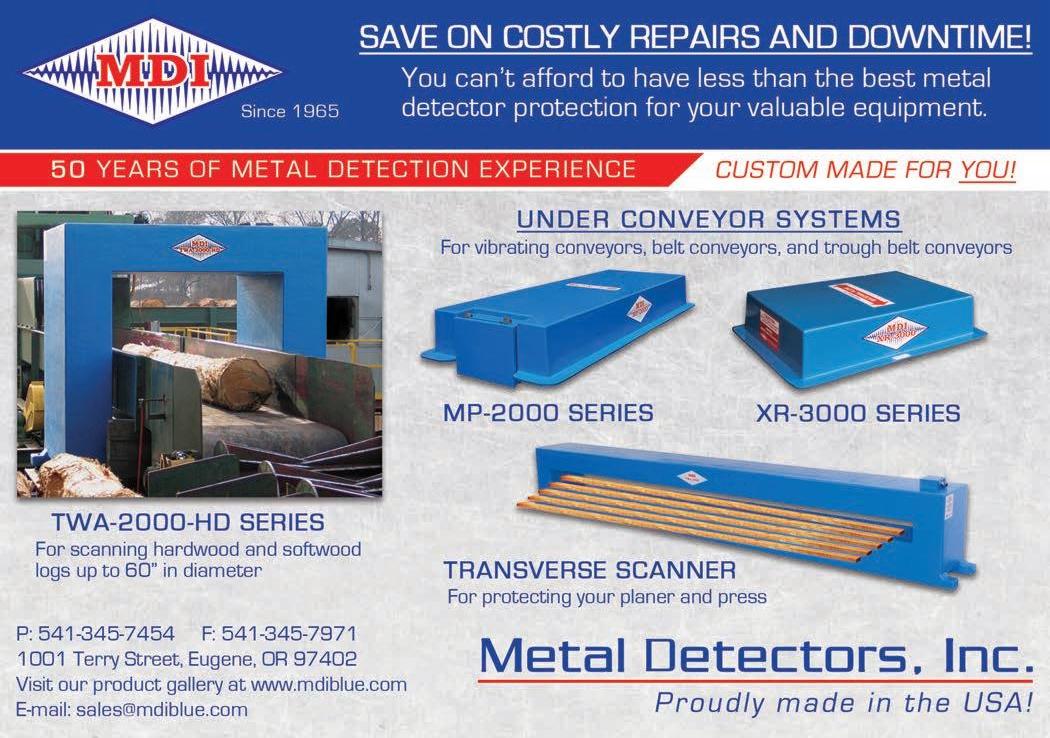
22 Wood Bioenergy / December 2021
The Rawlings Wood Hog is recognized in the industry as the “Green Monster Hog” and provides the crushing and shearing power needed to handle really tough jobs like green waste, cypress, redwood, cedar, black spruce, poplar and a wide range of other stringy and fibrous material. Each machine is equipped with the Rawlings Super Hi-Inertia solid steel rotor. With the increased inertia of the solid steel rotor our machine runs at lower RPMs than competitors resulting in overall savings of electricity and maintenance costs. The machines are tolerant of contaminants, rocks and metal without catastrophic maintenance costs if metal enters the grinding chamber.
We invite you to inquire about any of the projects that we have completed; we can provide you with full details.
Wolf Material Handling
Wolf Material Handling Systems is the premier designer and supplier of fuel yard systems for the biomass power and conversion, pulp and paper, power generation, gasification, resource recovery, mining, chemical, manufacturing and recycling, and other industries that require material handling. Wolf provides complete in-house design, engineering, manufacturing, assembly, and installation for systems using conveyance, stacking, reclaim, truck dumpers, receiving hoppers and ash/biochar receiving, handling, storage, and removal. Wolf understands the challenges required to handle biomass and its by-products, taking full responsibility for every aspect of the process from fuel receiving, sizing, storage, reclaim and boiler feed. With a long history Wolf has supplied material handling systems for several large U.S. biomass power projects. of delivering performance and innovation, Wolf is often considered not just a material handling systems provider, but a technology partner in the development of projects, by providing complete inter-disciplinary systems and support beginning with the conceptual phase through commissioning.
Wolf has successfully supplied the complete material handling systems for several of the largest biomass power projects in the U.S. For example, a 115 MW wood waste feedstock biomass power plant which was named the 2012 Biomass Project of the Year by Power Engineering. Also, a 102.5 MW wood waste feedstock biomass power plant, named a finalist for Power Engineering’s 2013 Bioenergy Project of the Year. In addition, several wood waste, agricultural residues, and other feedstocks for power generation ranging from 20 to 65 MW.
With over 40 years of experience, Wolf systems and equipment maximize process and production efficiency with consistent and reliable flow of materials. Each system is designed to reduce labor and maintenance costs and consume less power per mass unit than other alternatives. Wolf is committed to offer each client a custom material handling solution for their specific site and process requirements. Wolf’s in-house capabilities include consultation for scope definition, system design, equipment engineering, detail drawings, fabrication, assembly, inspection and start-up and commissioning. Wolf systems come with a performance guarantee and have never experienced major system failure.
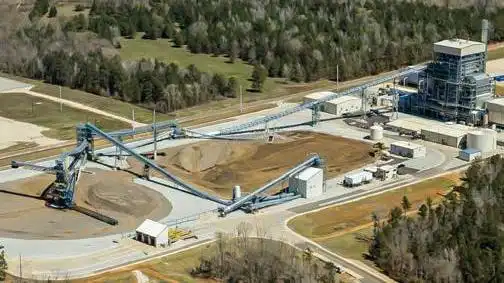
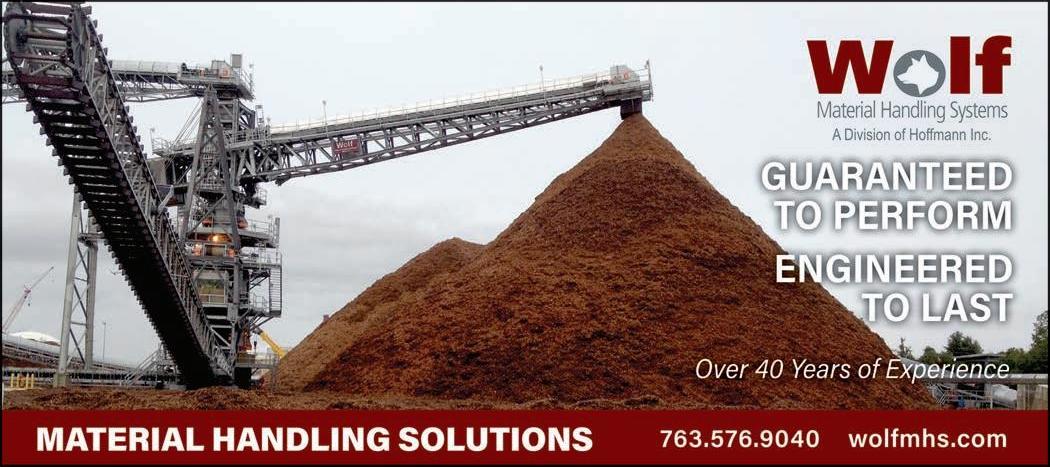
December 2021 / Wood Bioenergy 23