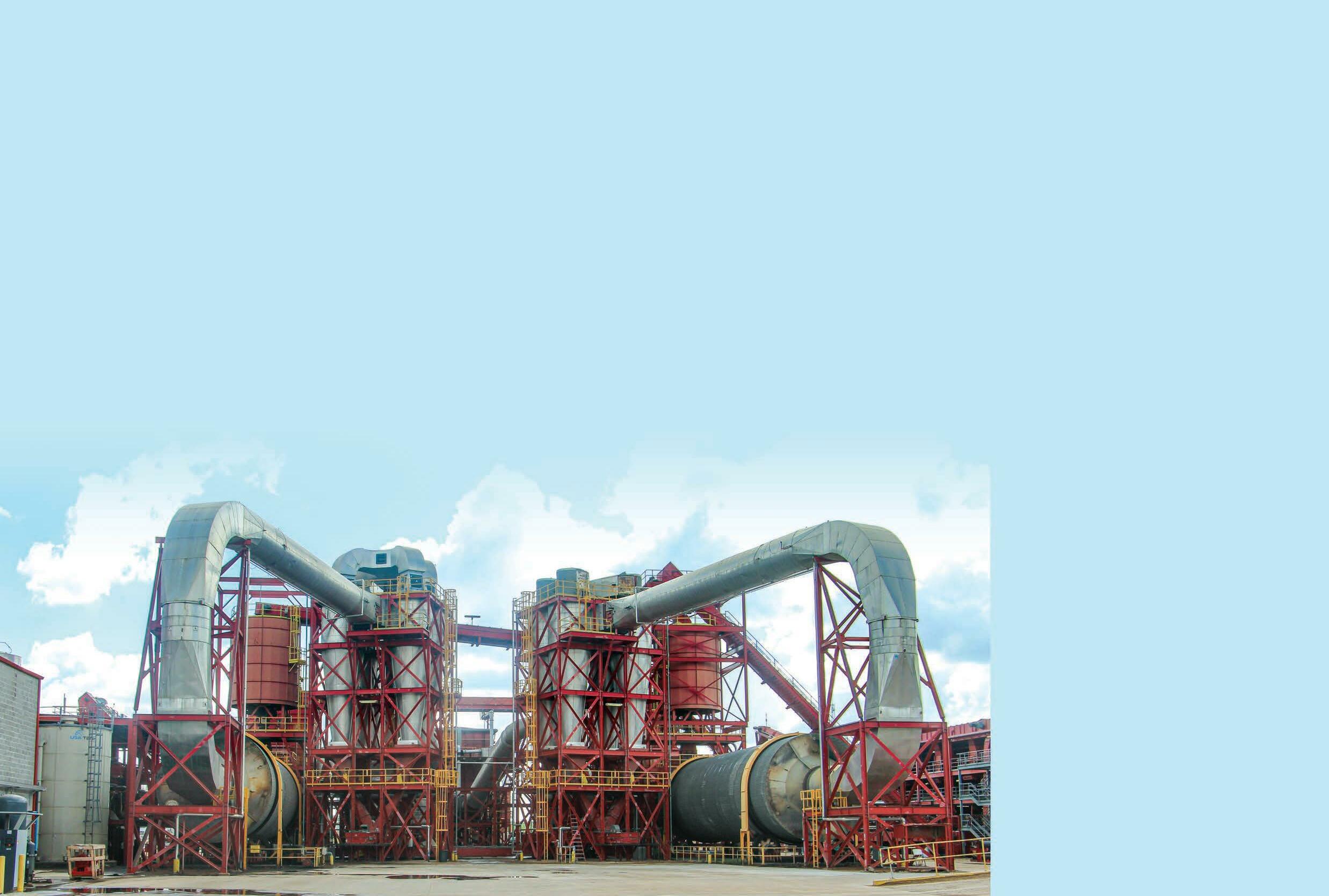
11 minute read
WELCOME TO THE U.S
Graanul Breathes Life Into Woodville
By Jessica Johnson
WOODVILLE, Tex.
Plagued by never-ending drama—from financing to fire—the former Texas Pellets facility here and its nearby port facility never saw the consistency that many other industrial wood pellet operations in the pine-rich U.S. South have experienced over the last decade. Instead, it battled engineering issues, machinery issues, staffing concerns and then finally a bankruptcy. When Baltics-based Graanul Invest, one of the world’s largest and most reliable wood pellet producers, purchased the mothballed six-year-old plant at auction in 2019, to be blunt, the facility was a mess. But it had an untapped potential. But first, some of the lingering legal messes had to be cleared by the administration. Then the familiar song of COVID-related delays killed some of the company’s timelines for re-start. But, as they say, the past is the past and the future, well, the future for Woodville Pellets, as the operation is now called, is bright.
12 Wood Bioenergy / December 2022
And it starts with recent industry veteran hires Jason Ansley as Vice President of U.S. Operations and Earl Herndon as General Manager of both the Port of Port Arthur facility (which was included in the purchase) and the Woodville site. The pair, having worked together for another manufacturer, have an easy comradery and clear vision of what they want the facility to achieve. Both see what the plant can be and want to get there—while also recognizing the process will take some time.
“The path we are on is going to be bumpy. There are things that will be up and down. We’re going to find something we didn’t expect,” Ansley says of the process to bring the facility to Graanul’s world-leading standards. But he’s quick to point out the team in place is going to help them get there together.
Herndon echoes him by saying that with all transitions there are pain points, and turnover happens, but the knowledge base with the 78 employees, some of whom have been with the facility since commissioning, is unmatched. And the team will stay focused and reach its aspirations as long as everyone, including the two at the top, don’t get overwhelmed.
Adding, “It’s always going to be about people; that triggers everything else. You focus on people and you get everything else done.” Herndon has only been on the job since late summer, but putting people first has already helped the plant actualize some of its goals.
Herndon is also incredibly invested in the team because this is his first facility to manage. He says he had gotten out of the industry when Ansley came calling to chat. Once his steel toes hit the ground and the sweat started coming, he knew he wanted in.
“I love the energy of the facility, but I also love the ability to be active here. You can affect real change here,” Herndon says. “You’re on the ground floor, but there’s also Jason’s leadership. He is really understanding if we want to change something or try something different. He will talk with us about it, get the details and let us go do it.” This perspective and open line of communication has brought the team success in data reporting and becoming much more aware of possible maintenance and processes that can help the plant run more efficiently, and strive to reach its nameplate capacity of 500,000 tons annually.
While Ansley and Herndon are leading the way in Texas, they are not on an island, and are definitely not without support from their head office in Estonia.
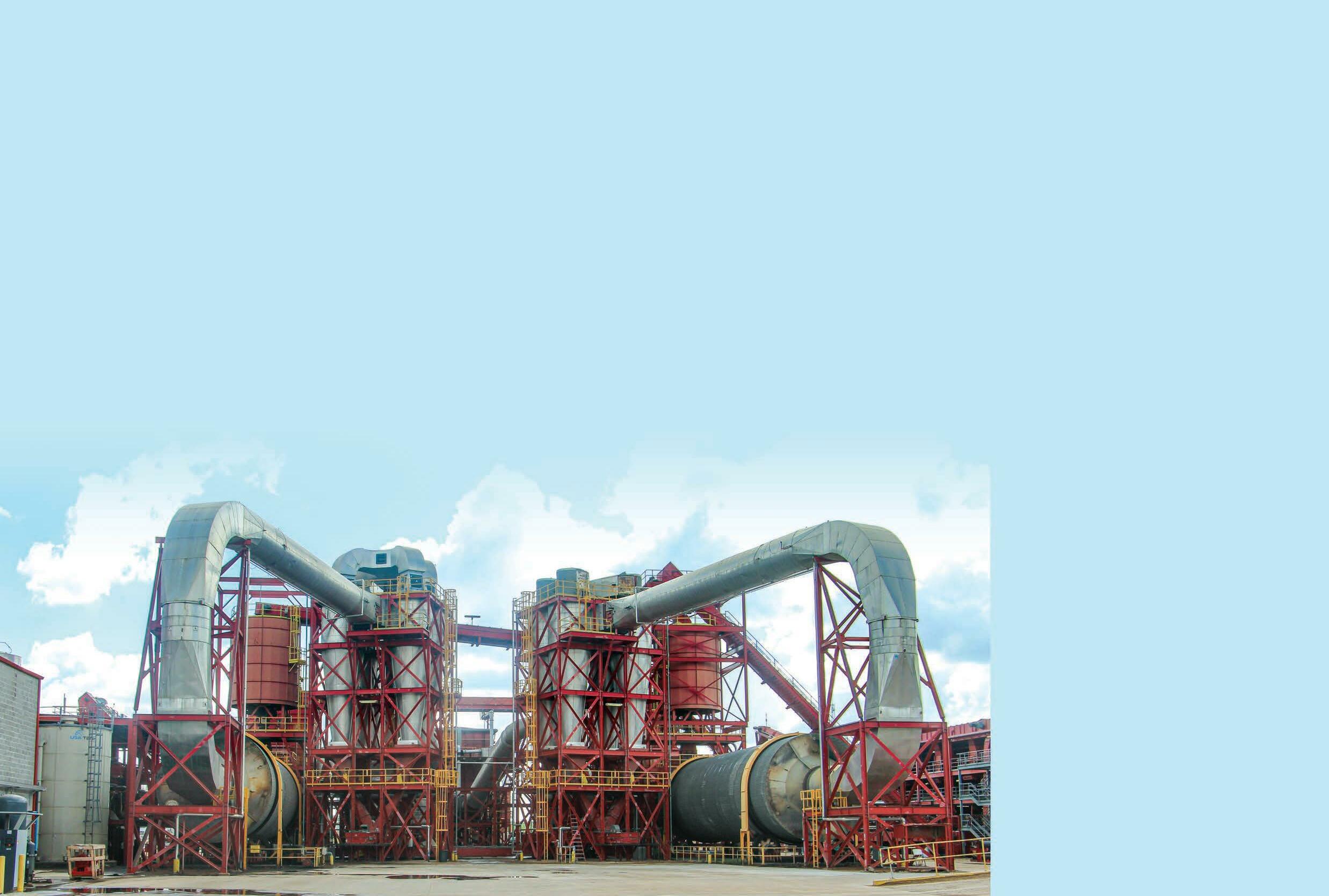
European Influence
Although Graanul Invest is a relative newcomer to the North American landscape, the company is well-established as the second largest pellet producer in Europe with 11 pellet plants and six combined heat and power plants operating in Estonia, Latvia and Lithuania. The U.S. facility brings Graanul’s pellet production capacity to 2.7 million metric tons. Ansley reports that Graanul has a good balance in that the team overseas is willing to help out, send people over, pick up the phone and support the U.S. team, but also is willing to allow the U.S. operation to take point and work through the process and get things done on their own. Herndon says the Graanul teams in Europe are very conservative in their thinking, and like to think things all the way through before making suggestions—an approach he respects deeply.
Ansley, who has spent time at the European plants, says the culture that Graanul has worked hard to build is evident. Employees are methodical in their approach to the care and upkeep of the plant’s machinery and structures and invested in the work the company is doing. Exactly the way he wants Woodville’s culture to become. He says, “You can tell it was not an overnight process, they invested time and money in getting it right and now culturally, they are invested in sustaining it.”
Herndon was not able to make the trip abroad, but from talking with other managers, watching videos Ansley and others have taken, he says he got a good feel for the operations, and loves the way they are organized. He echoes Ansley that it was clearly not an overnight process but something he certainly wants to reach in Texas—even if that means moving deliberately and recognizing the discipline needed to get to the point where everything doesn’t have to run full-speed all the time. Instead, Herndon is having the team focus on small pieces of the single points of failure that have been identified, or areas that need cleanliness attention, get them handled and reach sustainability. Then move on to the next portion of the process. For Herndon and Ansley, it’s all about the sustainability of the plant—a
December 2022 / Wood Bioenergy 13
The building stands tall, ready to hit its nameplate capacity of 500,000 tons annually.
plant they’ve only been working with for right around six months as a team, and a plant that Graanul has only had control over for three years.
“It’s an interesting spot to be in. This plant is nearly 10 years old. It obviously went through a bankruptcy. Graanul has only owned the facility for three years. In the grand scheme of things, that is not a whole lot of time,” Ansley says. “The facility has good bones with the layout and equipment.” Woodville has to get the right people in place, the right systems in place and then strategically invest in upgrades where it makes sense, he adds.
The European plants put more emphasis on stability, Ansley notes, than on just throwing around investments. “They do not run around and just tape something up and hope that it lasts for six months. They stop and fix it. They have redundancies built in. Earl and I are going through a list of where our single points of failures are and working through that. But it is too early to commit to next steps on projects. Because they are definitely out there and the company is very supportive of investing in the success of the plant.”
Ansley reiterates that this will not be an all at once process. There have been several projects that have been completed since the purchase, including air emissions control enhancement and upgrading the wet hammermills. The single most obvious project done by Graanul is pouring concrete and building a maintenance shop that wasn’t previously on site. Herndon and Ansley also added stairs to the Port of Port Arthur. Herndon says these projects aren’t, on face value, going to get the company more tons, or reduce costs. But it is about helping people do their jobs and making a better working environment. And that goes a long way culturally in the plant.
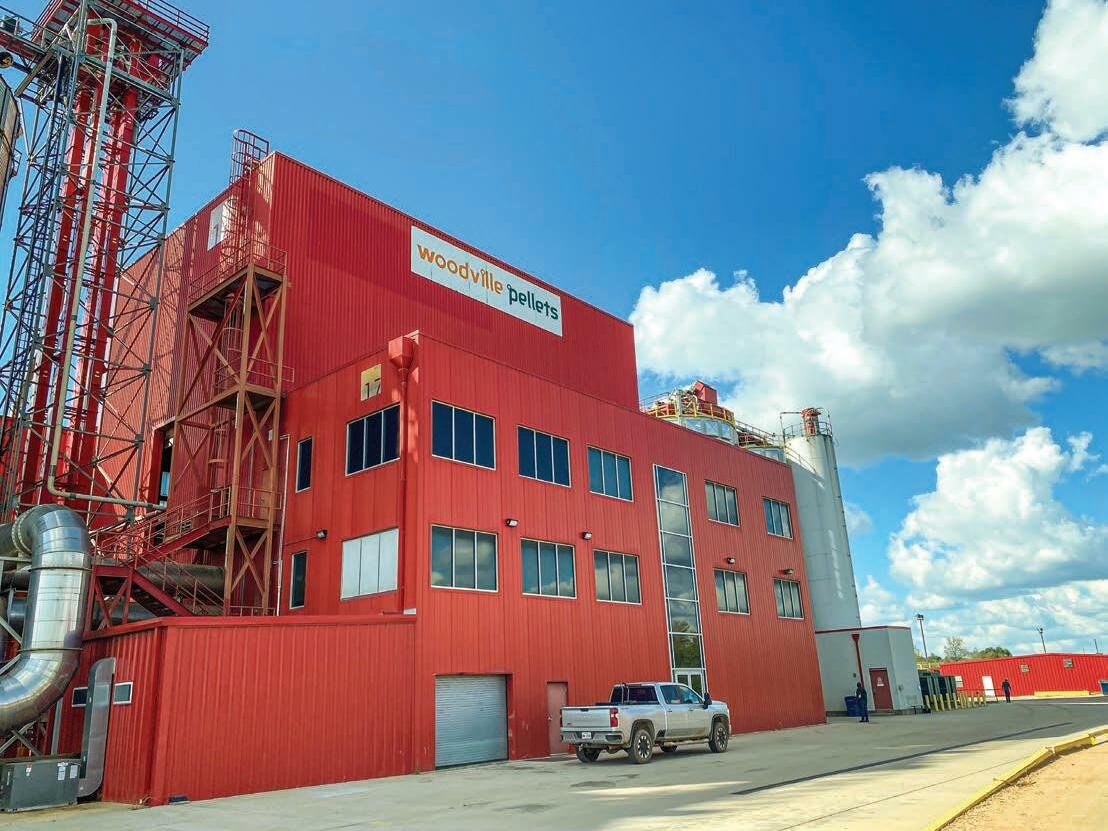
14 Wood Bioenergy / December 2022 Doing The Work
The facility operates four shifts, which gives staff plenty of time to transition from day to night. This includes giving staff every other weekend off, with two weeks on days and then back to nights. “This way you can get your internal clock in order instead of constantly switching shifts. And you always have time to run errands and get those kinds of things done, while still having your weekends back,” Herndon says of the shift change Ansley made.
The changes to the shifts is part of the bigger emphasis Herndon and Ansley put on employee experience. Herndon explains, “We made some key internal moves. A lot of people have been here for years, through the ups and downs. They are really dedicated. If I have a question about a part, Keith Mahaffey has the knowledge. We want to invest in them and make their jobs easier. We want to turn this plant around and we want to sustain it.”
Herndon is an electrical engineer by trade and selfproclaimed super nerdy dude, but he’s not afraid to get his hands dirty. He believes the best way to get buy-in is to show he’s willing to do the work. He admits, laughing, that sometimes the employees don’t want him in the thick of it, but he still shows up anyway: “The only way we get to where we want to be is by us all working together, not me and Jason sitting in the high tower yelling down direction about something. It is us on the ground floor, walking the plant, looking at things and making sure people are staying safe.”
Another culture-focused change Ansley and Herndon have implemented is War Room meetings, where each area manager is responsible for reporting their data, written on a white board, and reported on to other man-
agers during a fifteen-minute stand-up meeting. In these meetings, upcoming changes and ideas are discussed and managers are given equal say in what happens— with a twist.
Herndon says one of the area managers, Sonny Patrick, was always coming up with different ideas, so one day Herndon gave him the go ahead. But he told Patrick he only had this amount of time to complete the action, a little good-natured competition between the areas, as another area was also trying out an idea that day. Herndon gives cushion for the ideas he thinks are better than others. Explaining, “So, when we are in the War Room, and they say this is how long this action is going to take, if they’ve had a great idea, I will give them a little more buffer. They love that because it makes it a little more lighthearted instead of ‘gotta go do this or gotta go do that.’ Any of these ideas, I look at it from an engineering perspective. I am all about trying different things as long as it is not going to violate OEM constraints that will lead to other issues.”
Ansley loves Herndon’s approach to management, and says they are on the same page at (nearly) most turns. Implementing two-hour reporting, KPIs, and daily War Room meetings are things both were accustomed to at other facilities and helps give better visibility in the process and by using them in Woodville help take this plant to the next level.
Ansley points out that the Estonian head office did a really good job of giving Woodville a good foundation and providing good business systems that are automated. As Graanul has a very lean corporate staff, and each plant staff is relatively small, the company has put considerable time and effort into putting systems together that help operators do their job. Graanul has service programs for PM routes that are integrated onto tablets; items that help automate the scale house, tons tracking, fiber procurement, where typically if you were to come into a situation like this—taking a plant out of bankruptcy—there would be lack of organization. Fortunately, Graanul has already set the foundation for a digital factory, and now it is on the staff at Woodville to use those systems and leverage them.
Process Flow
Woodville operates on a 50/50 mix of lower value stemwood to pre-processed material, 100% southern yellow pine, of which 40% is residual chips from local sawmills, 10% is dust. Once trucks are received through the scale house, they are either dumped by a Phelps dumper to the chip pad or unloaded to the stemwood yard using a Caterpillar 990 wheel loader or LogPro crane. Fuel from the dumper goes onto a reversing belt from the chip pad. Lower quality stemwood is debarked using a LogPro drum debarker and chipped by a CEM chipper.
The chip pad is outfitted with an FMW stacker-reclaimer with screw to rake the pile. Chips are conveyed
to another belt, where the pulverized material goes to the Champion wet mill island, complete with Vecoplan pre-screeners that are currently being tweaked to reach operational level, then to the dryer island. Woodville’s dryer island is a dual line TSI system. This includes the heat energy system and dryers as well as the emission control system for the dryers, the wet ESP and RTO. The system was originally supplied over 10 years ago as the first of the new generation of TSI dryer islands that featured Sigma Thermal furnaces and TSI single pass recycle dryers along with newly intro-
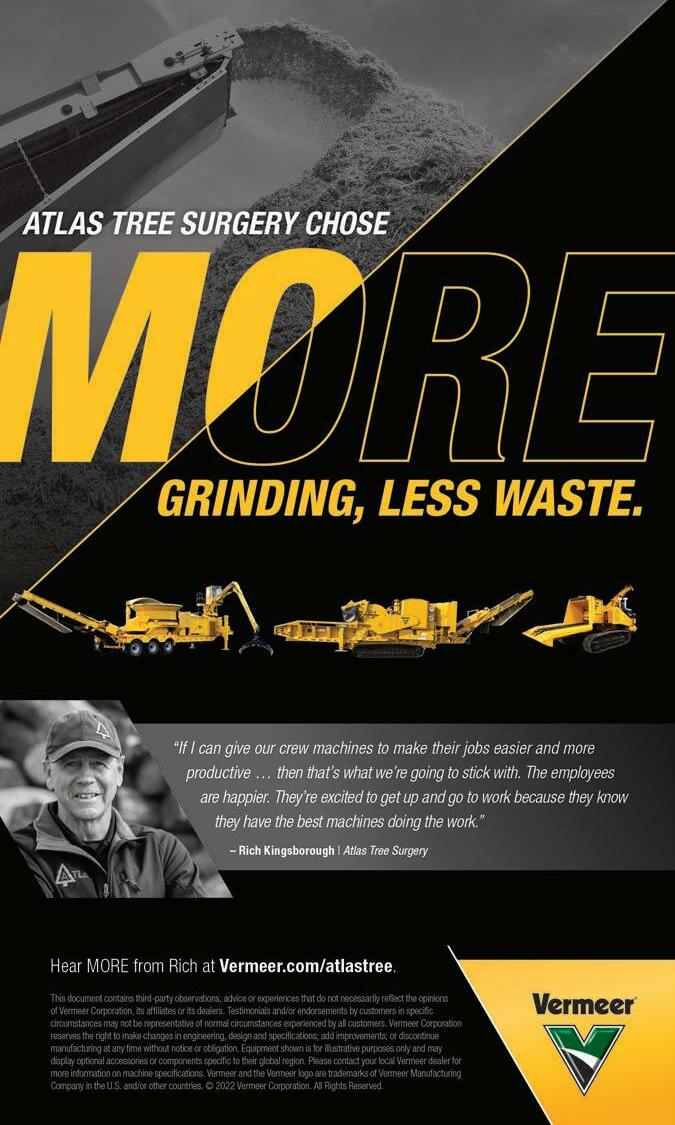
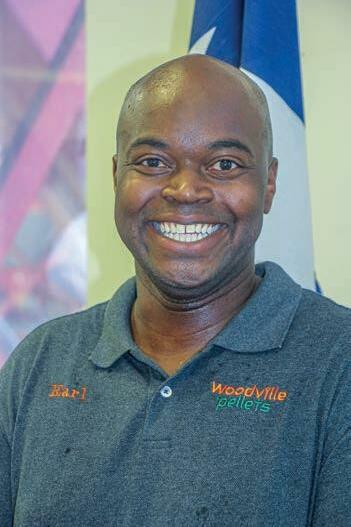
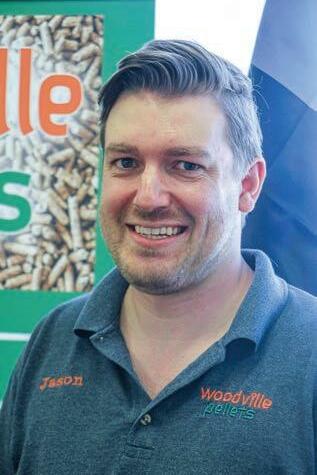
16 Wood Bioenergy / December 2022
Jason Ansley
Earl Herndon
duced TSI wet ESP and RTO providing a reliable integrated system from a single source.
Currently, dry material does pass additional processing, with four Vecoplan pre-screeners to help reach targeted chip size of between 88-92% 2 mm chips for producing smaller industrial pellets.
After the Champion dry mills, two Tank Connection dust silos act as more of a buffer between process islands. Part of the redundancy built in to help handle maintenance, these silos allow the facility to perform work without stopping the press hall. The silos are able to feed both lines of the press hall, which is broken up as line one with CPM presses ➤ 34
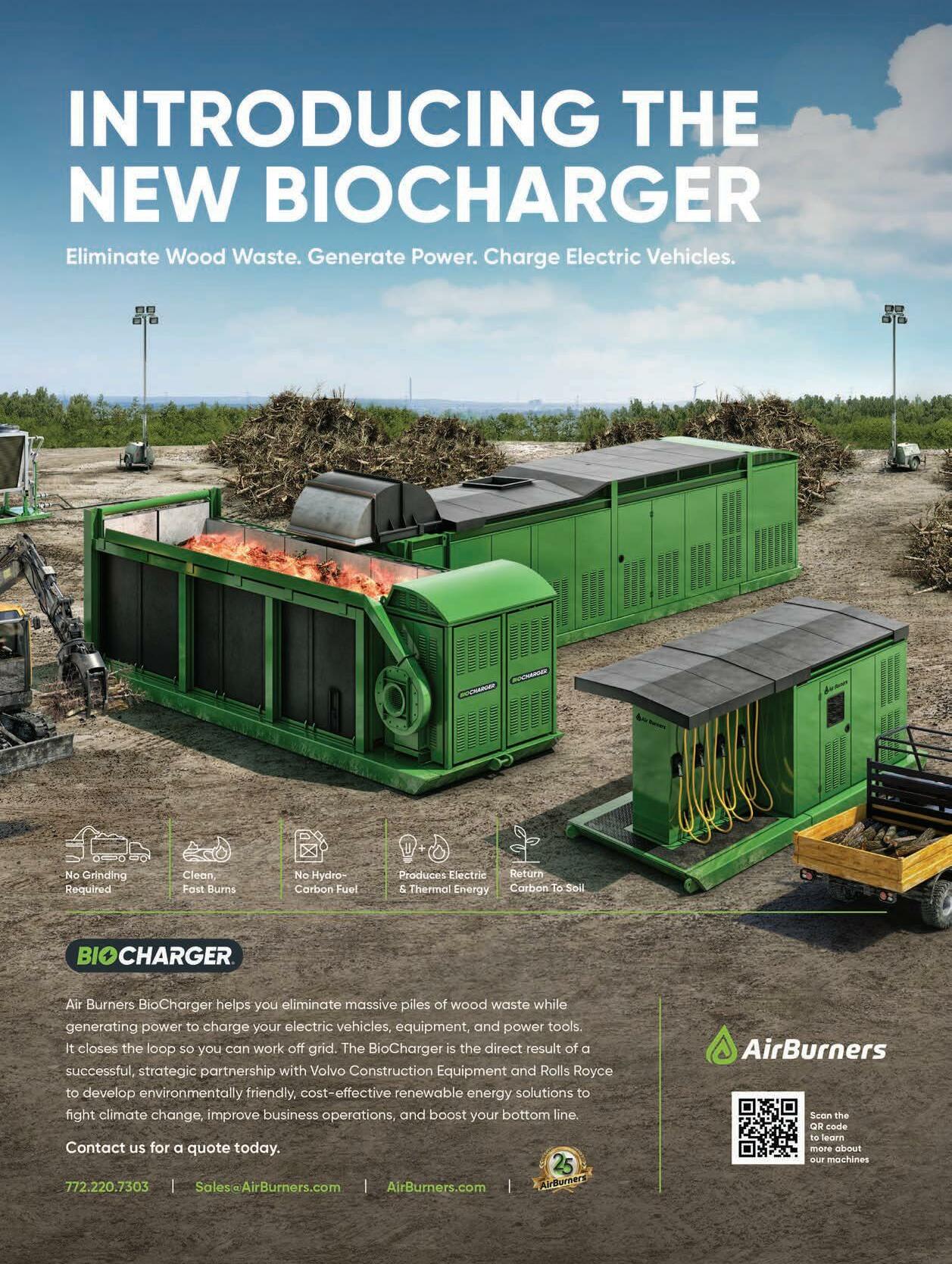