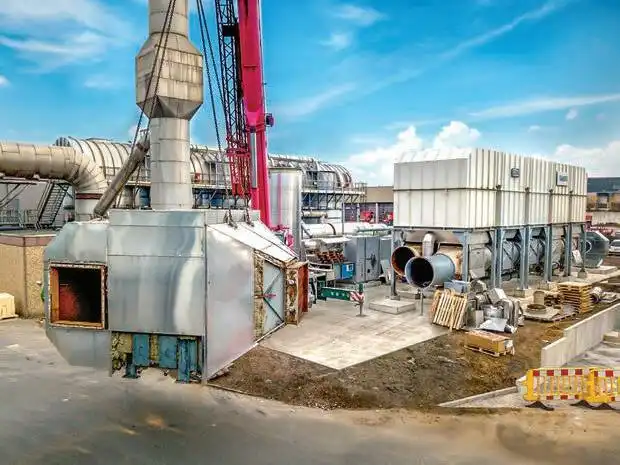
5 minute read
MAINTENANCE FOCUS
Determining The Best Path Forward For RTO Rebuilds Buys Back Uptime
By Greg Thompson
The wood pellet manufacturing process is not kind to regenerative thermal oxidizers (RTO). The process air flow downstream of the dryers contains a significant amount of moisture, particulates and other contributing factors that make life difficult for the owners and operators of these required emissions control systems. The question most deal with is not if, but when, an RTO requires a significant repair or rebuild. To complete this type of project, it requires two of the most feared words for any manufacturing facility: Money and downtime.
But, do not lose all hope. Each day presents an opportunity to recoup both. Everything done during the life cycle either reduces or buys back more time from the moment a repair or rebuild is required.
A well-developed preventive maintenance program? Buys back more time. Consistent bake-outs? There’s a few more weeks. Poor specification of materials of construction during the last rebuild project? Expedites your next major service to the next plant outage.
Choosing the right components for your process stream and a proper maintenance schedule will have long lasting, encouraging effects on overall system operation and uptime.
Making A Plan
Rebuilding an RTO is not a small investment. In addition to capital costs for material and onsite installation services, end users accrue hours of internal costs working with suppliers, subcontractors and others in development. The most efficient route is to work with a company that has significant experience rebuilding RTOs and can cover nearly all aspects of the design, fabrication, project management, installation and commissioning. Having one point of contact for all aspects of a rebuild will lead to a more complete and successful project.
Regardless of the company you choose, the best approach is to follow a series of strategic steps.
Repair Or Rejuvenate?
What is the end goal? If capital costs are limited or the longer-range plan is to completely replace the RTO system at some point, smaller repairs may be the best approach. If returning the existing RTO to a like-new condition with plans for another decade or more of operation is the goal, the plan should include a full rejuvenation of the RTO unit, using updated media arrangements, materials of construction and other new com ponents.
These discussions should happen internally and with an expert in RTO rebuilds. To better assess the situation, ask potential rebuild partners for potential highlevel budgetary costs.
RTO projects don’t have to mean lost time and money.
Gather Information
It’s important to evaluate existing information related to the design and operation of your RTO system. Providing data about the process is helpful when choosing ceramic heat exchange media, materials of construction, insulation, etc. The following items are normally requested:
Upstream process data: It’s imperative to have data about air constituents, moisture levels, temperature and other operating conditions. Knowledge of corrosioncausing agents guide materials of construction decisions and mitigate premature degradation of the newly rebuilt system.
Recent test reports: Destruction efficiency tests or particle loading assessments provide knowledge of what is in the process and how the RTO has been operating.
Maintenance reports: It is important to have your RTO inspected annually. Providing a baseline of the health of your equipment over the years helps reduce the chance of future operational failures.
RTO drawings: To expedite pre- and post-contract processes, provide existing drawings of the equipment and your site. General arrangements and component details provide valuable information.
18 Wood Bioenergy / December 2022
Assess The RTO
A great first step is to bring in a system expert to complete a full assessment or inspection of the RTO. This RTO unit review will confirm existing issues and may uncover additional items that require attention. In the long run, identifying a broad er scope initially will mitigate any unexpected future shutdowns and remobilizations. A detailed report should highlight the items required as part of the rebuild.
Develop A Scope Of Work
At this point, a decision about what to include in the rebuild project needs to be solidified. If destruction efficiency is of concern, now is the time to replace the worn valves. If the process fan is operating at max imum capacity, a change in ceramic media will reduce wear, while providing additional air flow capacity. Once a budget has been established, a complete scope of work can be developed to ensure the vendor can quote accurately and efficiently, and price effectively. Furthermore, let the vendor know the amount of downtime you have avail able. While the scope of work requested cannot always be completed in that time frame, using multiple crews, around-the-clock shifts, and onsite pull ahead work before the RTO shuts down can mitigate downtime.
Select Proper Materials
The goal of any major rebuild is to make the system last long term. As a result, the vendors should be cognizant of the proper materials of construction for the job. Improperly selecting components for the application could lead to a rebuild situation 12 to 18 months later. The following items generally make up the largest purchased equipment costs and are most affected by your air process stream: l Cold faces: These structures provide the structural support for the ceramic heat exchange media bed. High moisture or chlorides in your process stream can contribute to premature degradation of these structures and lead to a catastrophic failure. While 304 stainless steel and 304L have very similar structural similarities, 304L contains less carbon, which makes it more structurally capable in corrosive environments. Furthermore, the addition of more beams, bars and perforated plates will increase the likelihood of a long-term solution. Invest more initially or invest even more later as a result of component failure. l Air flow dampers: Improving or replacing these apparatuses is crucial to the overall destruction performance of the RTO unit. It‘s worth the investment to consider a more robust design or include air seals for better performance. l Ceramic heat exchange media: Switching from a random packing ceramic media to a more modern structured block could significantly increase process air flow capacity without major modifications to your fan or variable frequency drives. Also, using a mix of different styles of ceramic block can relieve the organic particulate plugging that is carried over from your dryers, without sacrificing thermal efficiency and experiencing higher utility bills.
Conclusion
Rebuilding RTOs is never convenient. Even if planned well in advance, the size and scope of the project still takes away from what these companies do best—producing wood pellets. But, by following the above steps and considering all of the factors discussed, operators can reduce downtime and achieve long-term RTO sustainability.
Greg Thompson is key account manager in the Clean Technology Systems division of Dürr Systems, Inc., located in Southfield, Mich. He earned a B.S. from Eastern Michigan University in Ypsilanti, Mich. and has 19 years of experience in the emissions control industry. This article and photos were submitted by Dürr as part of their Wood Bioenergy Conference gold sponsorship package.
December 2022 / Wood Bioenergy 19