STRUCTURAL TECHNOLOGYMATERIAL&REPORT
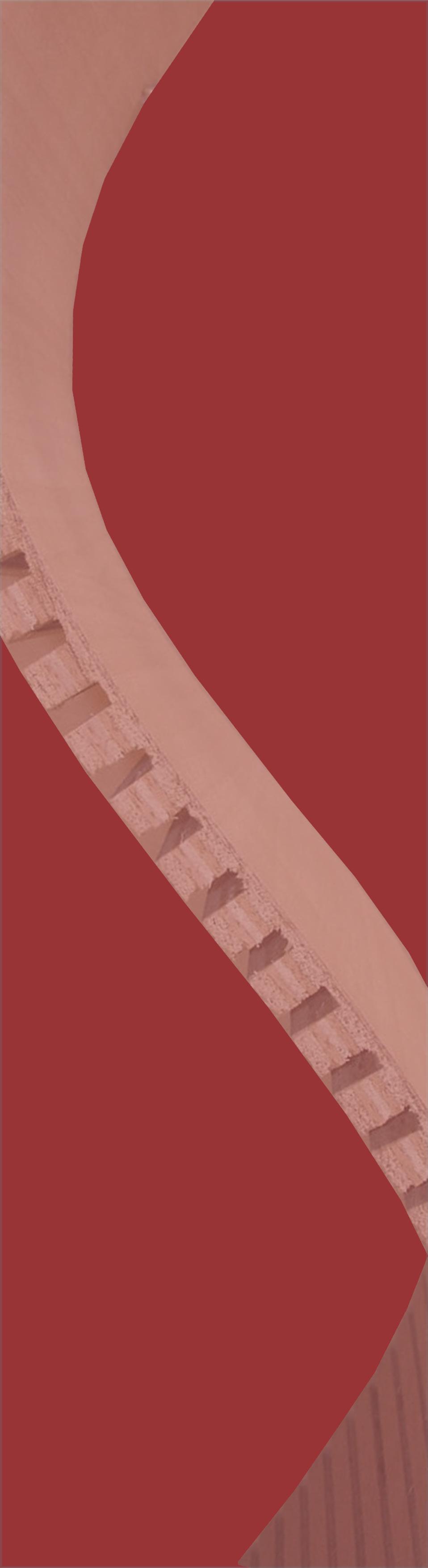
Arafa VeneziaOrmettiMinnielliHayaCarlottaChiaraMichela
Group 03
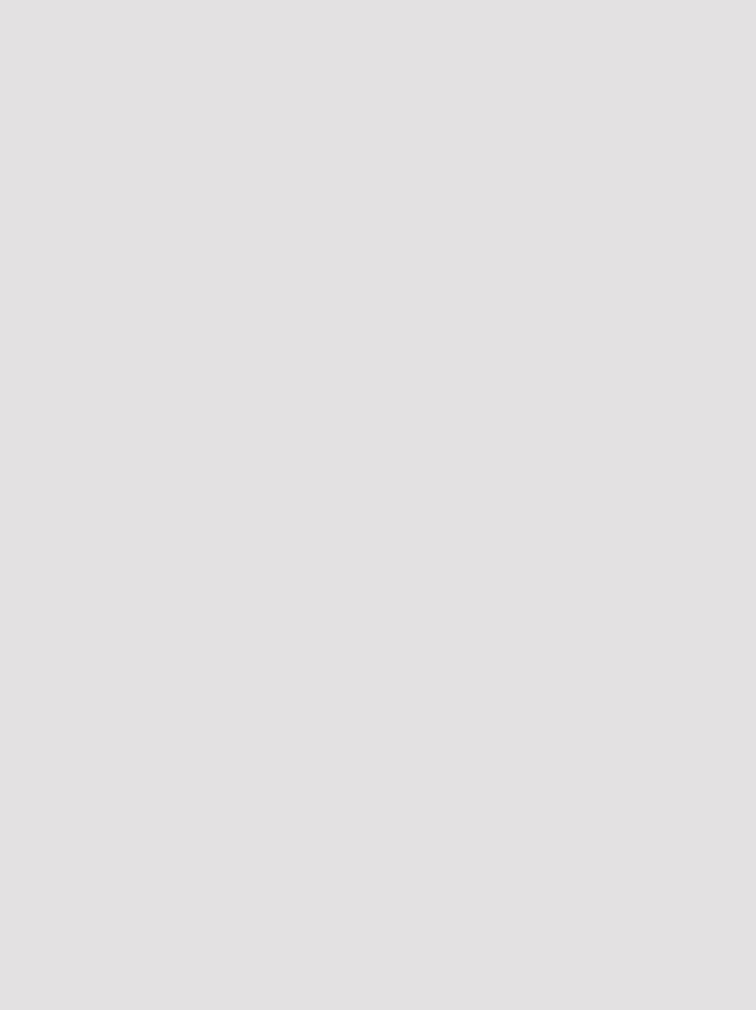
REFERENCES
INDEX MATERIAL,INTRODUCTIONSYSTEM & TECHNOLOGY STRUCTURALDETAILS
ANALYSIS 5 7 13 17 22
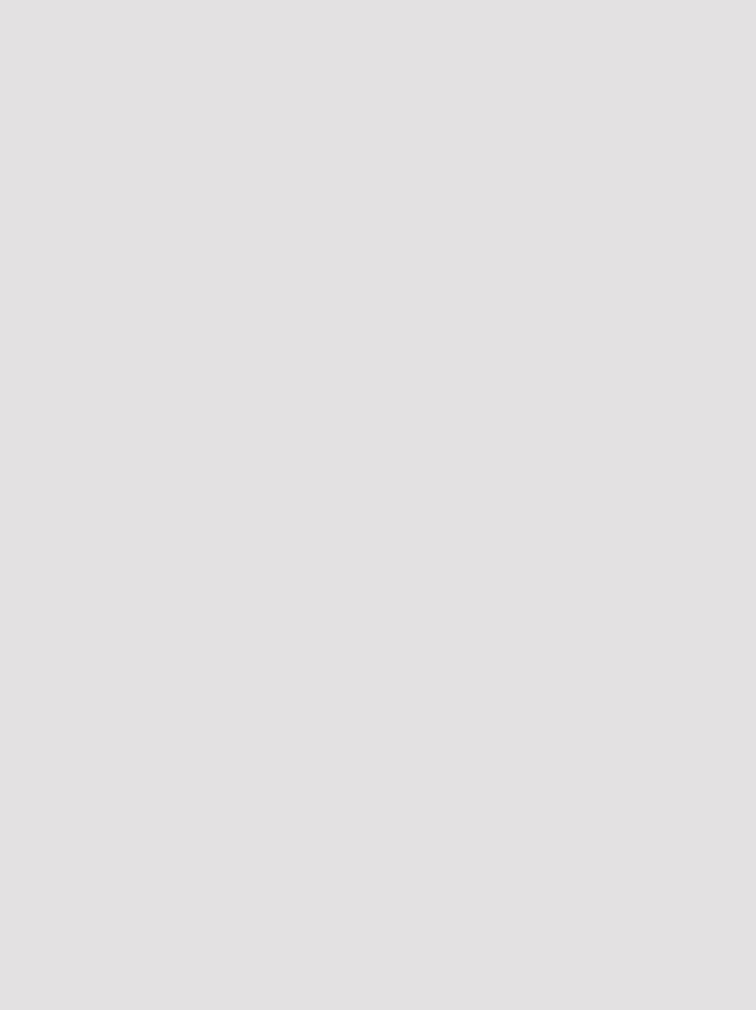
ABOUT PAVILIONTHE
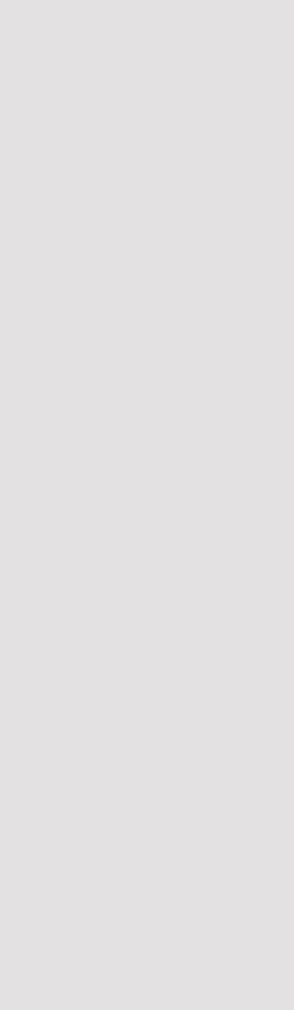
The pavilion consists of the main spiral slab and a par apet. The slab is made out of a zip shape wooden system ( an interlocking system inspired by the normal zipper) creating strong and flexible panels that can be bent easi ly and at the same time, when it interlocks, it is rigid. The parapet functions a double purpose: first, it acts as a sim ple handrail; second, on its lower part it becomes thicker and acts as a structural wall, supporting the zipshape slab. This multi-purpose system is entirely made out of x-lam wood.
Our temporary pavilion will be located in San Siro. The pavil ion is designed carefully to function as a sports pavilion and at the same time integrate with the landscape. Despite there are a lot of urban gardens in the area, they’re disconnected and small, so people are training in the streets without a specif ic place selected for this activity. We wanted to integrate the community that needed a place to train as well as make it a place for everyone to chill, have fun, relax, interact. A place where you can ”Find your Own Rhythm “ in the fast pace of life.
We eliminate the disadvantage of the zipshape technology, that is the fact that it produces wood waste, by re-using it as a paste with additives to 3d print, not only for the pieces of the furniture in the interior spaces, but also the bench we designed for the internal part of our spiral. This paste is com posed of a cellulose fiber filled plastic composite; this system is really great to generate bio based material medium and large sizes components for construction that is also recyclable.
Beneath the spiral, there are spaces dedicat ed to sports activities; these spaces are enclosed between xlam wood panels that rise beyond the zip shape slab, becoming the parapet for the running track.
The project is not only notable for it’s sculptural shape but also advances the use of wood technology as a flu id structure. Bringing together modern technology, dig ital fabrication methods and sustainable materials.
This report demonstrates the structure analysis providing technical data, construction details, load analysis, and mate rial technology overview that was prepared in order to make sure our spiral with the selected materials bear the load.
INTRODUCTION
Zip shape slab
5 X lam wood parapet
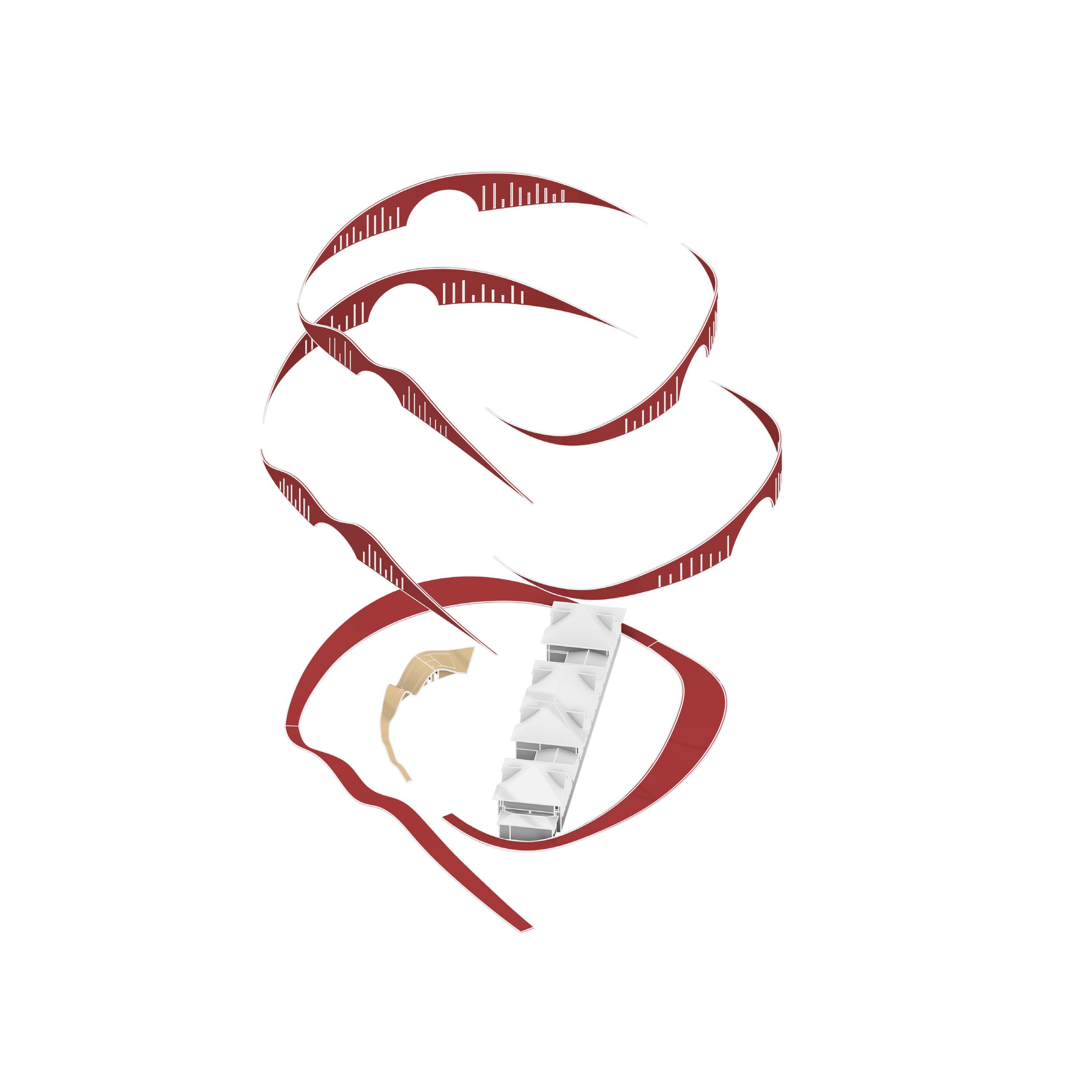
TECHNOLOGYSYSTEMMATERIAL&
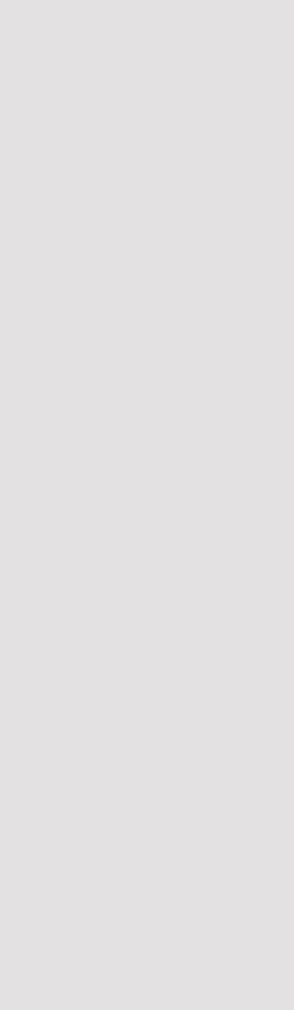
7 XLAM WOOD ZIP SHAPE LAMINATEDSYSTEMWOOD3DPRINTEDWITHCELLULOSE3 2 1 4
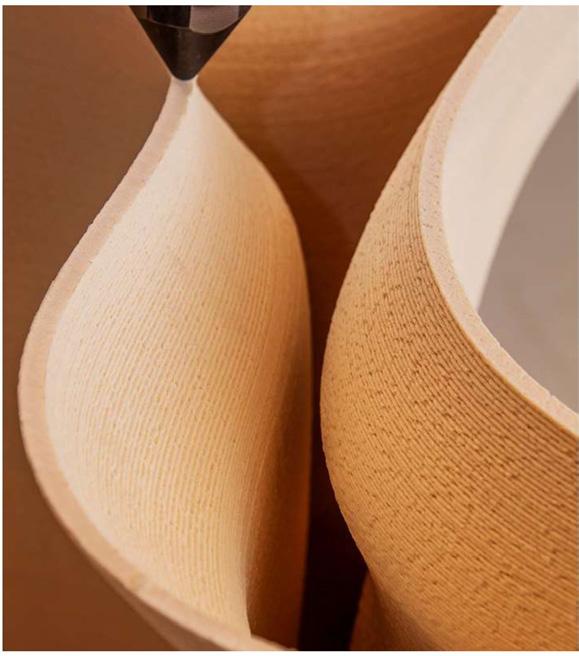
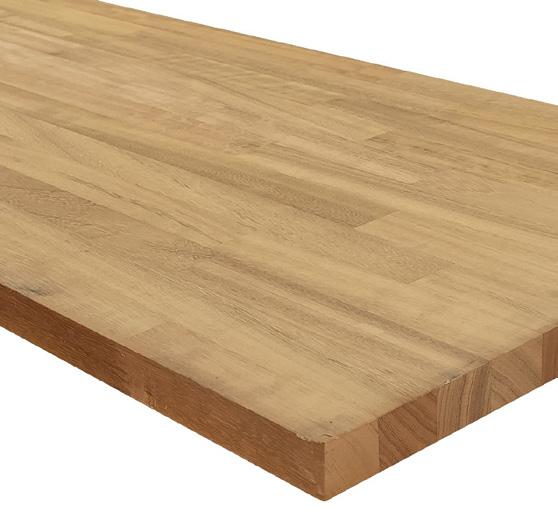
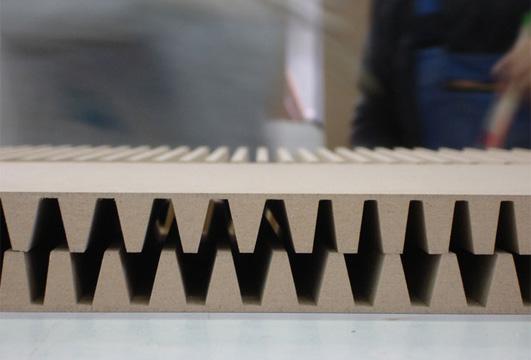
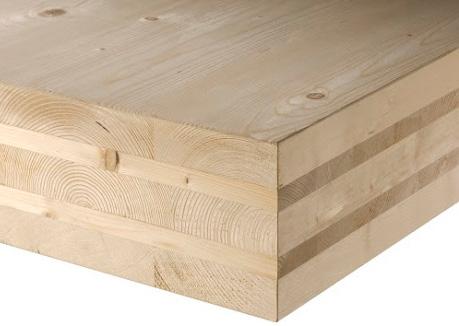
Beam length: up to 40 m
Density: For spruce, and depending on the strength class, approximately 400 kg/m³ to 500 kg/m³
Block bonding: >280 possiblemmon request
FISH BEAMS
Glued laminated timber
Span lengths: >40 m
Glued solid timber Duo/Trio
FISH BEAMS
SINGLE TAPERED BEAMS
Heights: up to 4,000 mm
Heights: up to 4,000 mm
LAMINATED TIMBER | HASSLACHER NORICA TIMBER 9
Cross laminated timber
possibleGLUED
Structural finger jointed solid timber & GLT ®
Block bonding: >280 possiblemmon request
up to 40 m 80 to 280 mm >280 possiblemmon request
Heights: up to 4,000 mm
Block bonding: >280 possiblemmon request
MECHANICAL DATA
-Positive impacts on climate protection through storage of CO2.
TRUSSED GIRDERS
Structural Fire Resistance:0.70 mm/min in accordance to EN 1995-1-2
Block bonding: >280 possiblemmon request
Glued ceiling systems
Glued laminated timber Special Components
FREE Lengths:FORMS
possible on request
Innovative: direct, pre-cambered and with
Thickness: Maximum lamella thicknesses: 45 mmMaximum service class 3 lamella thick nesses: 35 mm (also, 40 mm to 60,000 mm² of cross sectional area)For curved/arched special components: Lamella thickness from 6 to 45 mmRod bonding for three-dimensionalcomponents.shaped
Fire Behaviour: Dfl-s2, Dfl-s1 when used as floor covering
SPECIAL COMPONENTS
Width: 80 to 280 mm
Heights: up to 4,000 mm
up to 40 m
Glued ceiling systems
Special products
possibleGLUED
-High thermal insulation properties.
LAMINATED WOOD HASSLACHER NORICA TIMBER supplier
Heights: >4,000 mm are
Glued laminated timber
GLUED LAMINATED TIMBER | HASSLACHER NORICA TIMBER 15
Glued laminated timber –special components
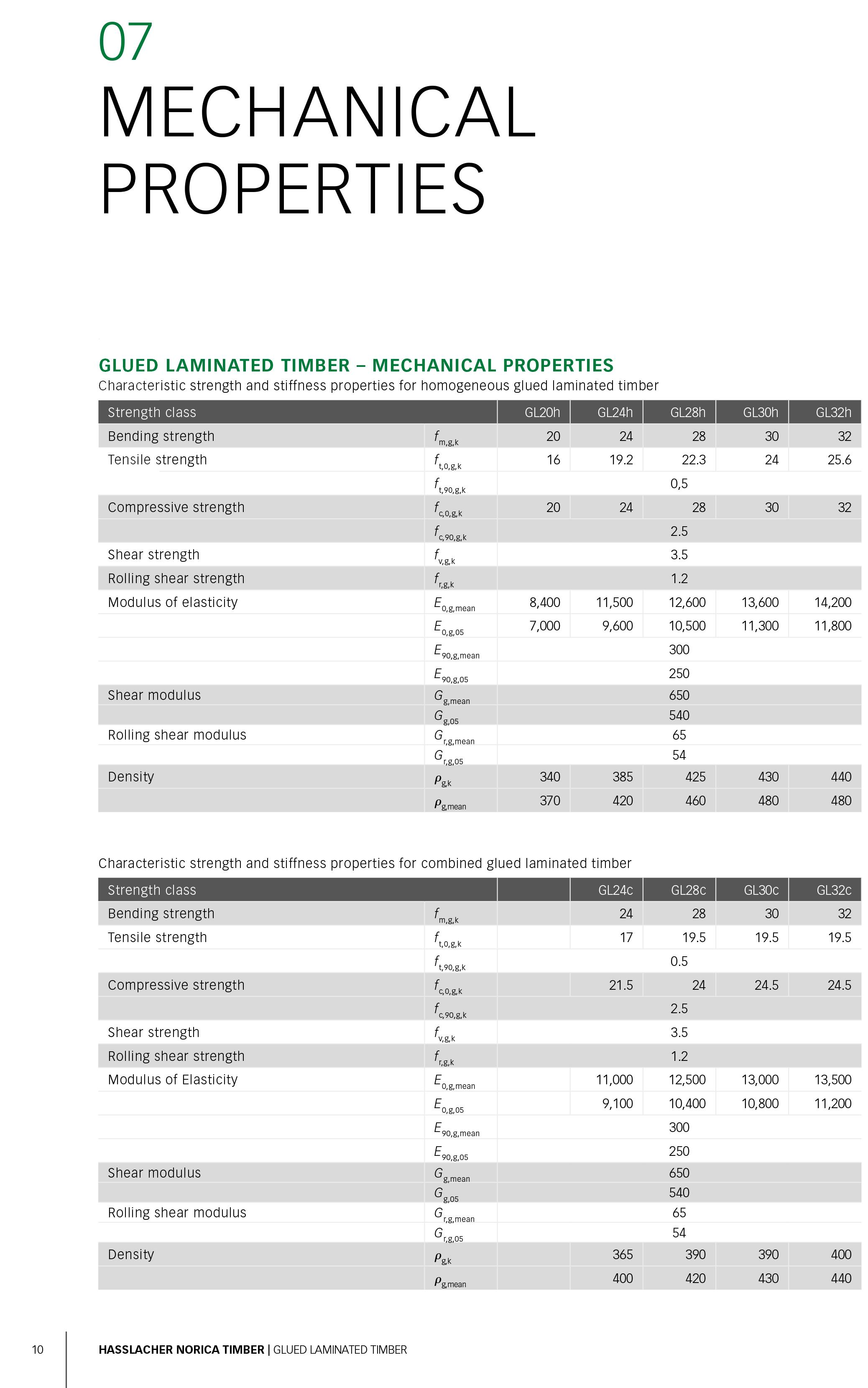

Span lengths: >40 m
Block bonding: >280 possiblemmon request
Heights: up to 4,000 mm
TRUSSED GIRDERS
Width: 80 to 280 mm
Duo/Trio
possible on request
Beam length: up to 40 m
CURVED BEAMS OR BeamPARALLELPRE-CAMBEREDBEAMSlength:
up to 4,000 mm
Free forms Curved Beams
Block bonding: >280 possiblemmon request
Heights: up to 4,000 mm
PRODUCT PORTFOLIO
Thermal Conductivity λ= 0.13 W/mK
up to 40 m
Width: 80 to 280 mm
Heights: >4,000 mm are
Diffusion Resistance: m = 50 (dry) to (wet)20
Pallets & packaging solutions
Heights: up to 4,000 mm
Widths: up to 280 mm
Advantages
Surfaced timber

-High fire and chemical resistance.
Width: 80 to 280 mm
possible on request
Width: 80 to 280 mm
-Natural, renewable and 100% recyclable building material.
Glued laminated timber
Concept of automated curve definition with software routines
2 Grooving the second flank.
Geometry definition
Before and after assembly: the curvature is defined by the difference between the angles a and a’.
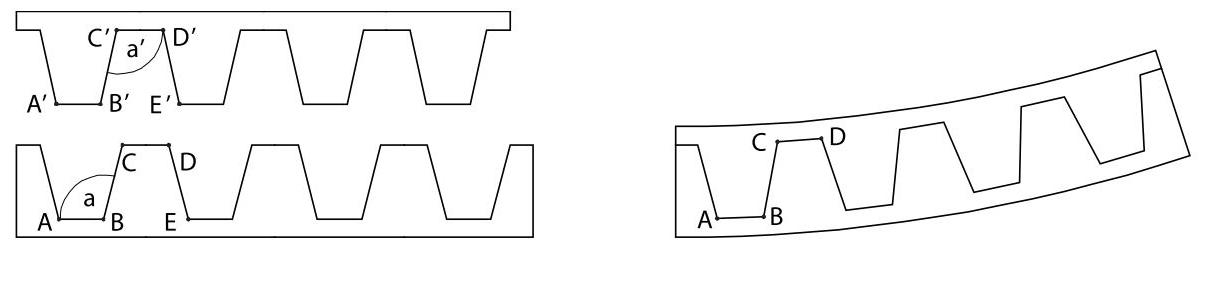
3 Assembly of Panels.
Process Detailing Development Machine code
ZipShape is a universal method that makes it easy to curve flat panels; it is a Computer Aided Fabrication method without molding A shaped piece consists of two plates that are jointed in such a way that they only fit together in the desired curvature. This means that the use of form gauges can be dispensed with when gluing the panels; two boards are pinned so that they only fit together in the desired form ZipShape is based on the elastic cold deforma tion of wood but prevents spring back due to mutual entanglement of the components. With the current state of research, radii up to a minimum of about five times the material thickness can be implemented. The planning steps be tween the definition of the curvature and the development of the two plates are automated with parametric software.

4 Hardening of the glue with uniform pressure in a vacuum bag; with a vacuum bag produced for our purposes, we could apply uniform pressure to our interlocked element while the bag’s shape could be adjusted to any desired curve.

9
SCHINDLERSALMERON & DESIGN production
ZIP SHAPE SYSTEM
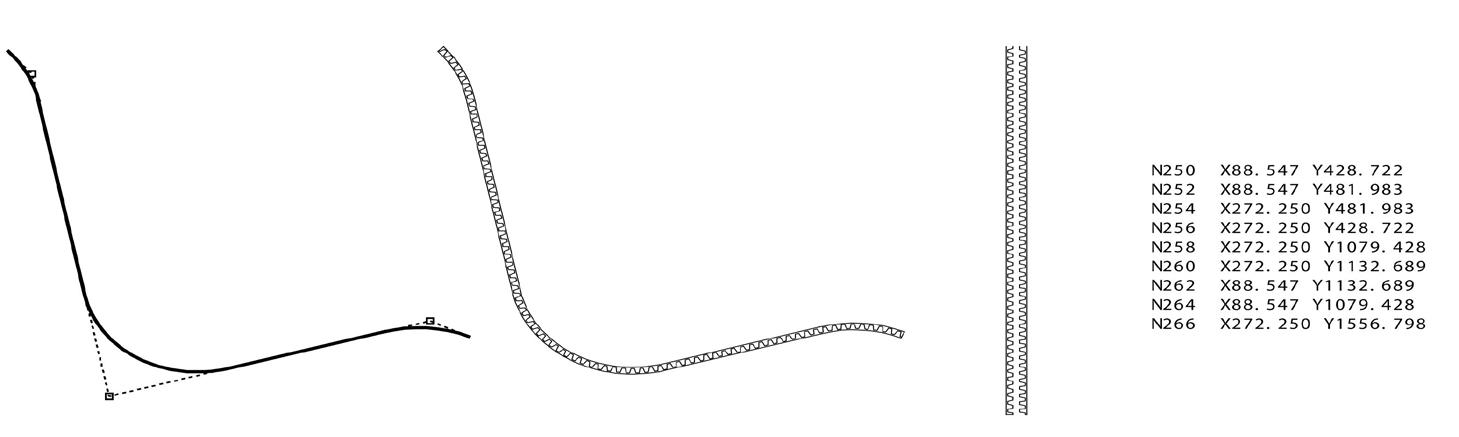
1 Grooving the teeth’s first flank with a 5-axis-controlled saw blade.
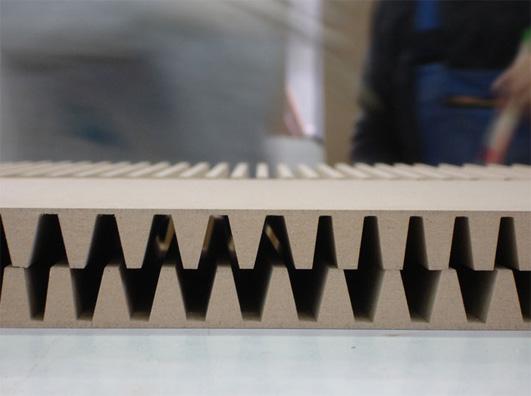
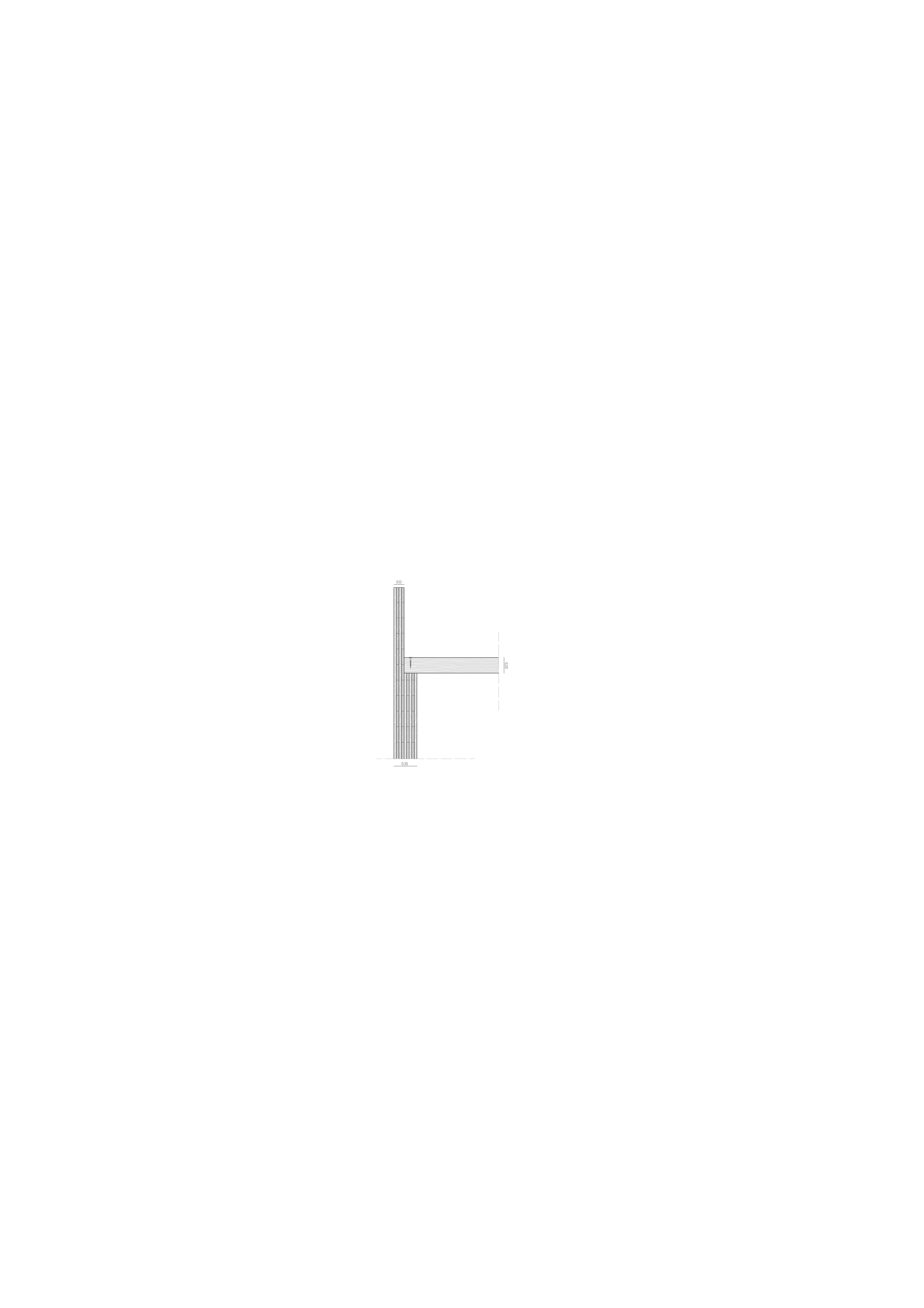
-Cellulose fibers prevent the creation of internal stresses -Extremely low shrinkage -Can be directly printed, quick production time.
Wouldwood addresses the challenge to modernize wood-based manufacturing and adapt it for large scale additive manufacturing. Wouldwood is an integrated design, material and production platform for advanced additive produc tion of biobased medium and large sizes components for construction and transportation. It includes digital design and production tools, communication systems, a biobased material system and a recycling strategy.
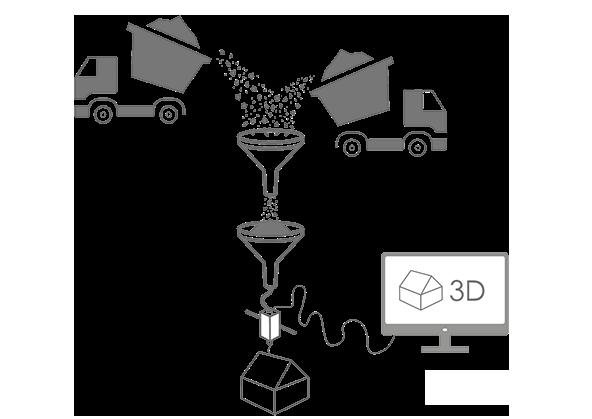
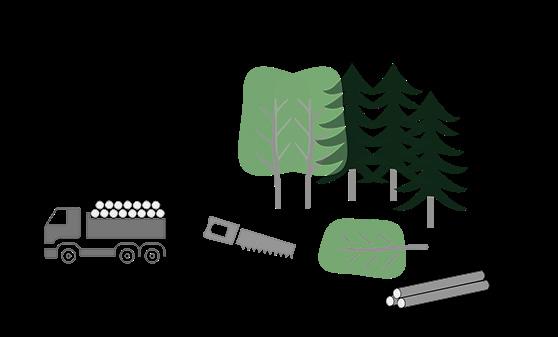
Advantages
Process
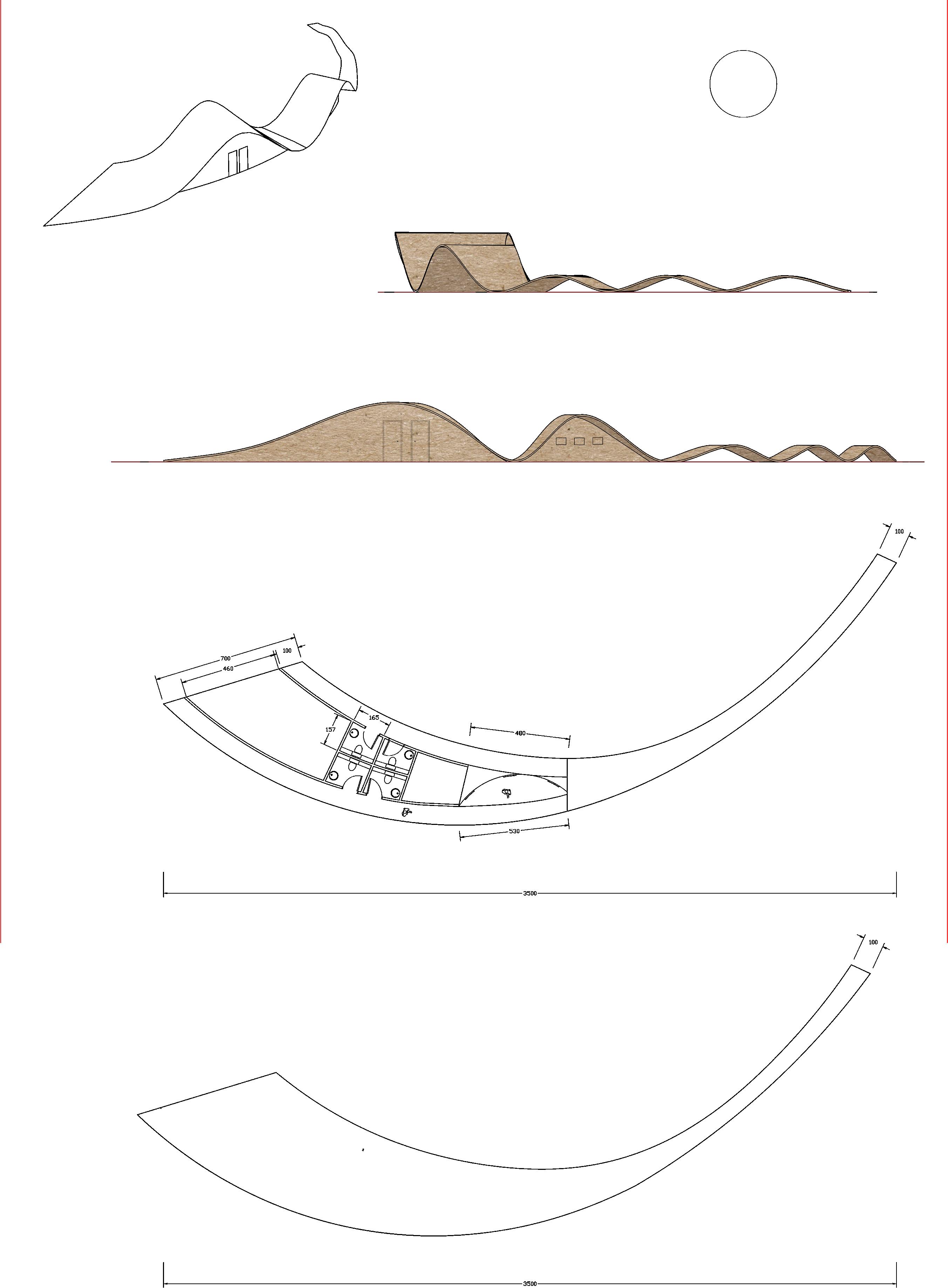
Cellulose is the most abundant natural polymer, whose repeat unit is derived from glucose. It is such a crucial component of the cell wall of different plants. Along with plants, cellulose is also present in a large variety of living species, like algae, fungi, bacteria, and even in sea animal such as tunicates. Although widely found in nature, at industrial scale cellulose is derived almost entirely from cotton and wood.
3D PRINTED WITH CELLULOSE
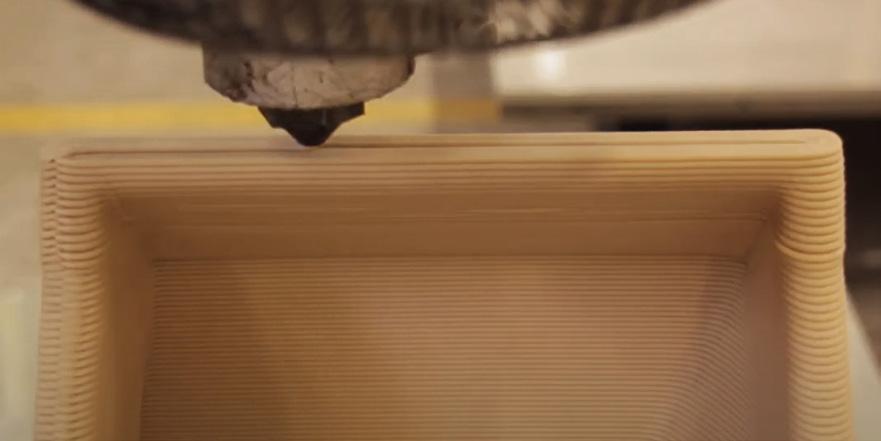
-Easy to print large constructions, no design limitations. -Superior strength and stability and minimum weight -Natural wood-like touch and feel -100% recyclable. No waste generated -Non-toxic and -Manufacturingodorlesswithout molds
WOULD WOOD Company
DETAILS
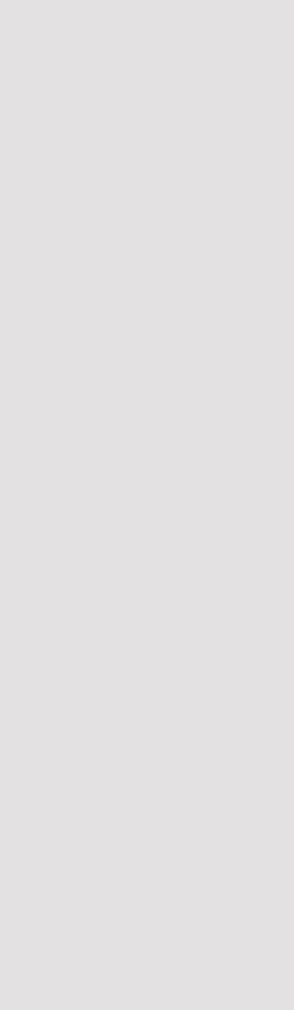
13

CONNECTION TO THE GROUND: VENTILATED CURB
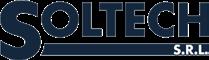
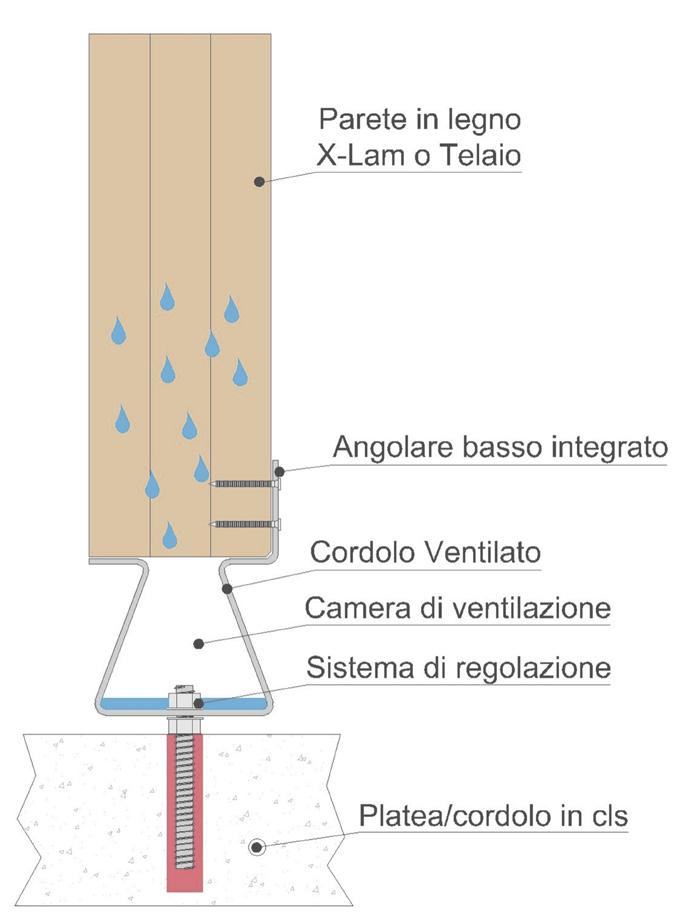



CONNECTION BETWEEN THE ZIP SHAPE SYSTEM
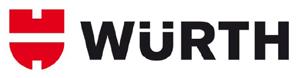
15
CONNECTION BETWEEN THE ZIP SHAPE AND THE PARAPET
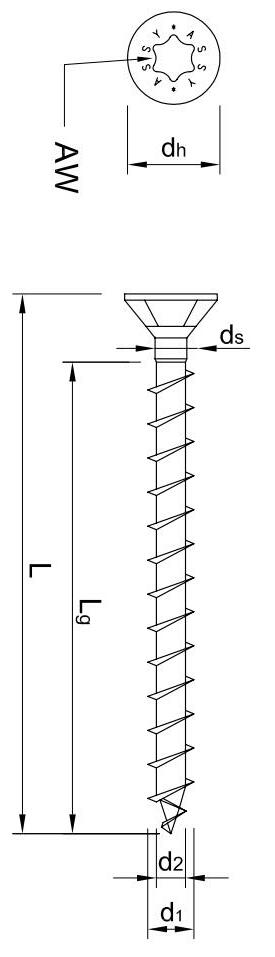
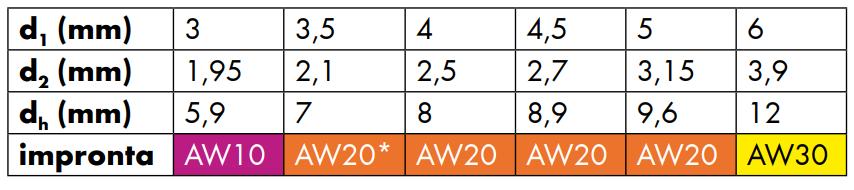
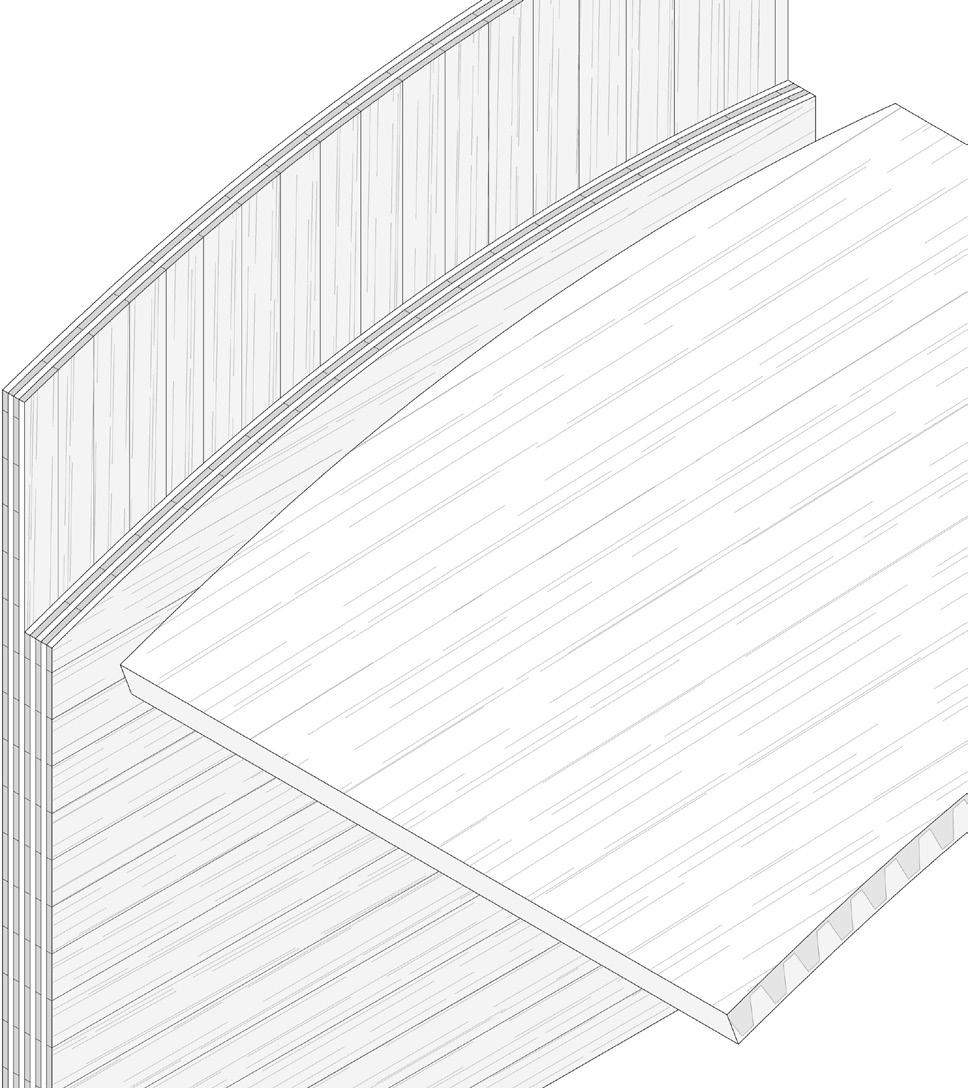
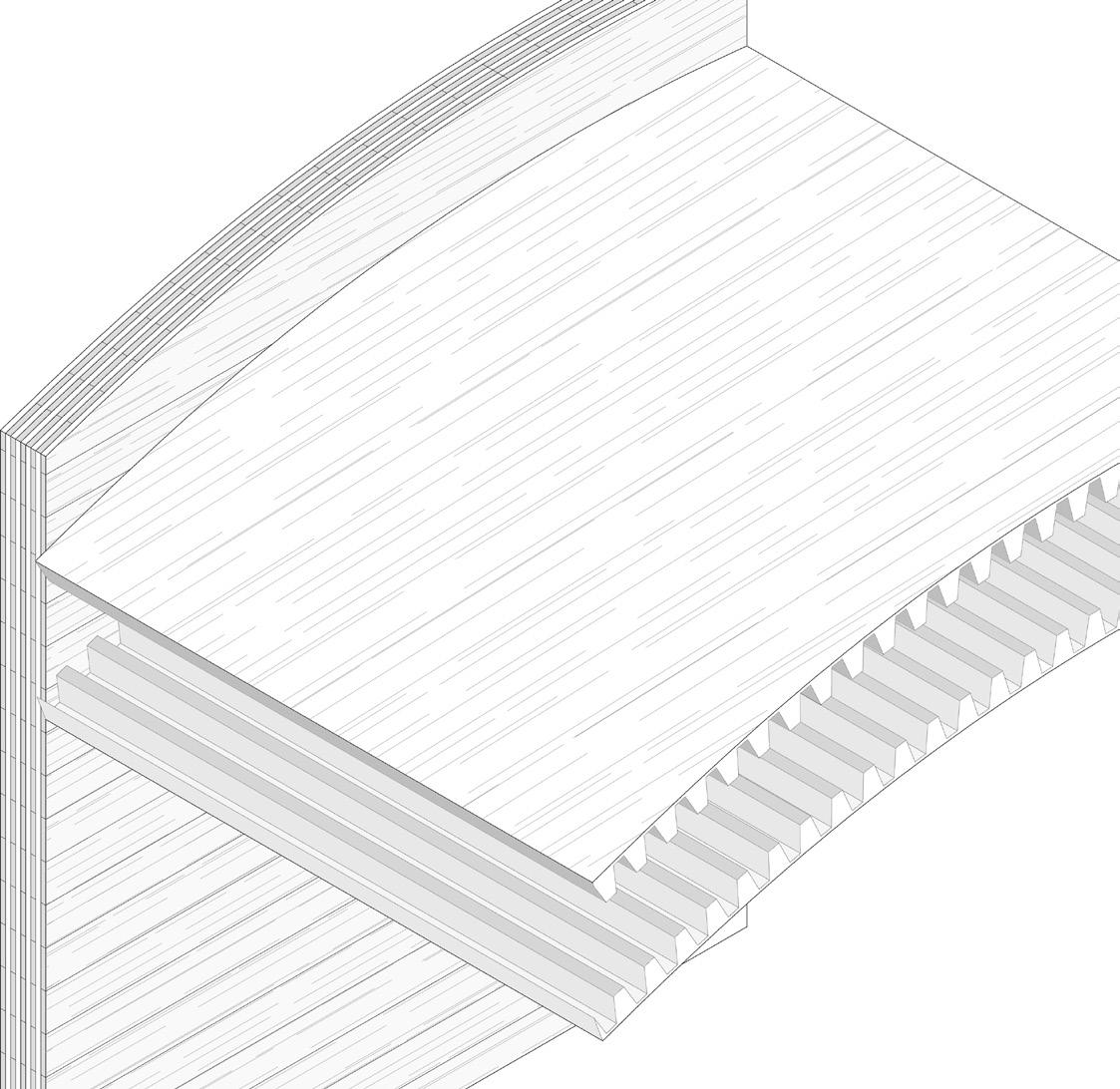
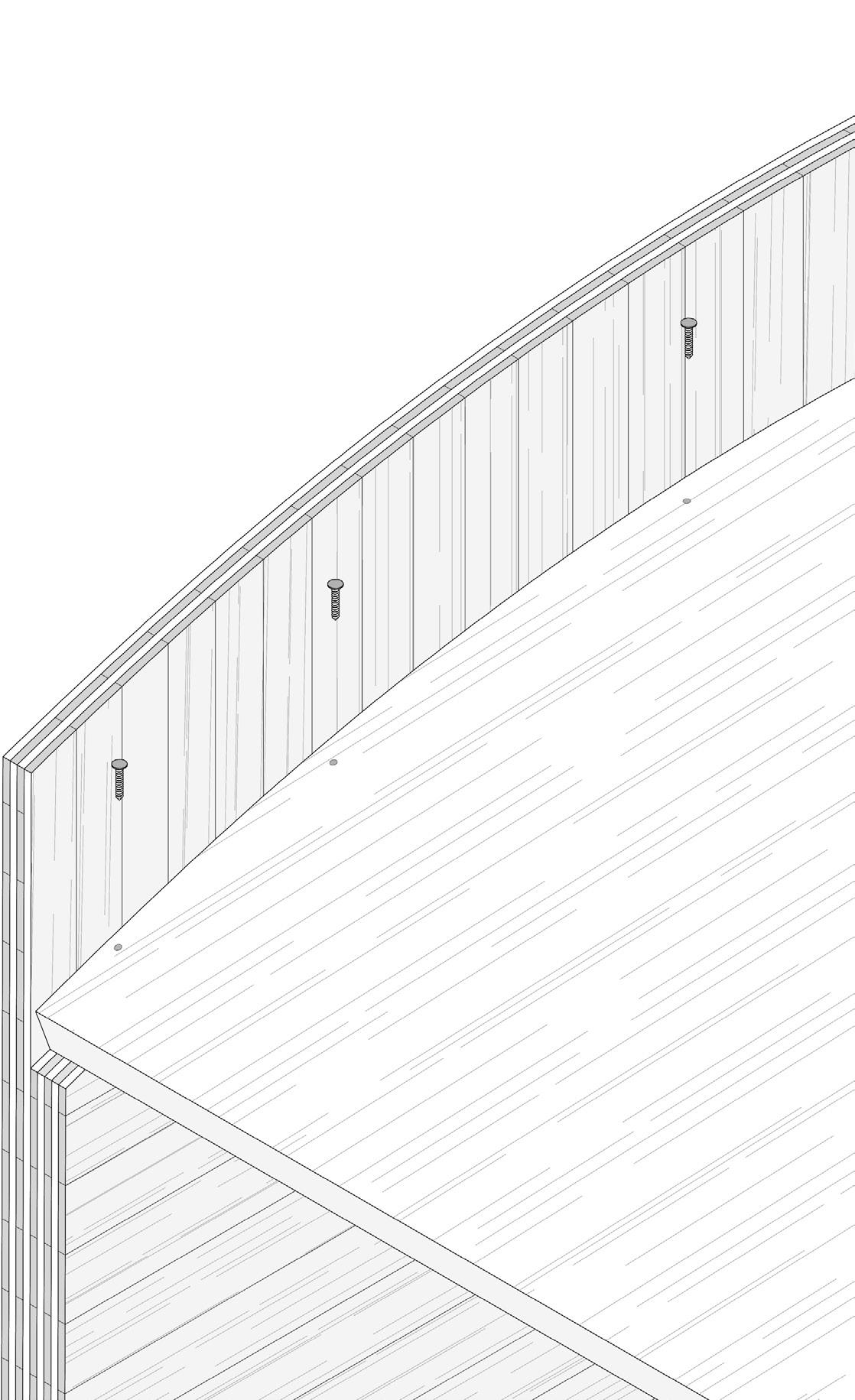
Classe of service 2, GL24C-->
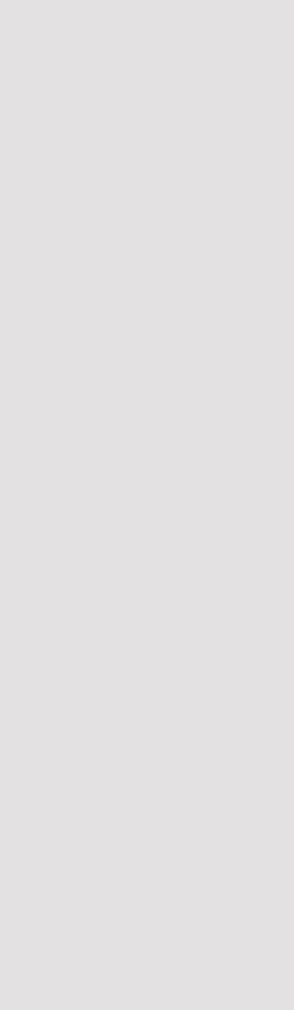
Fmk (flexural strength): 24 N/mm (safety coefficient): 1.45 6.70
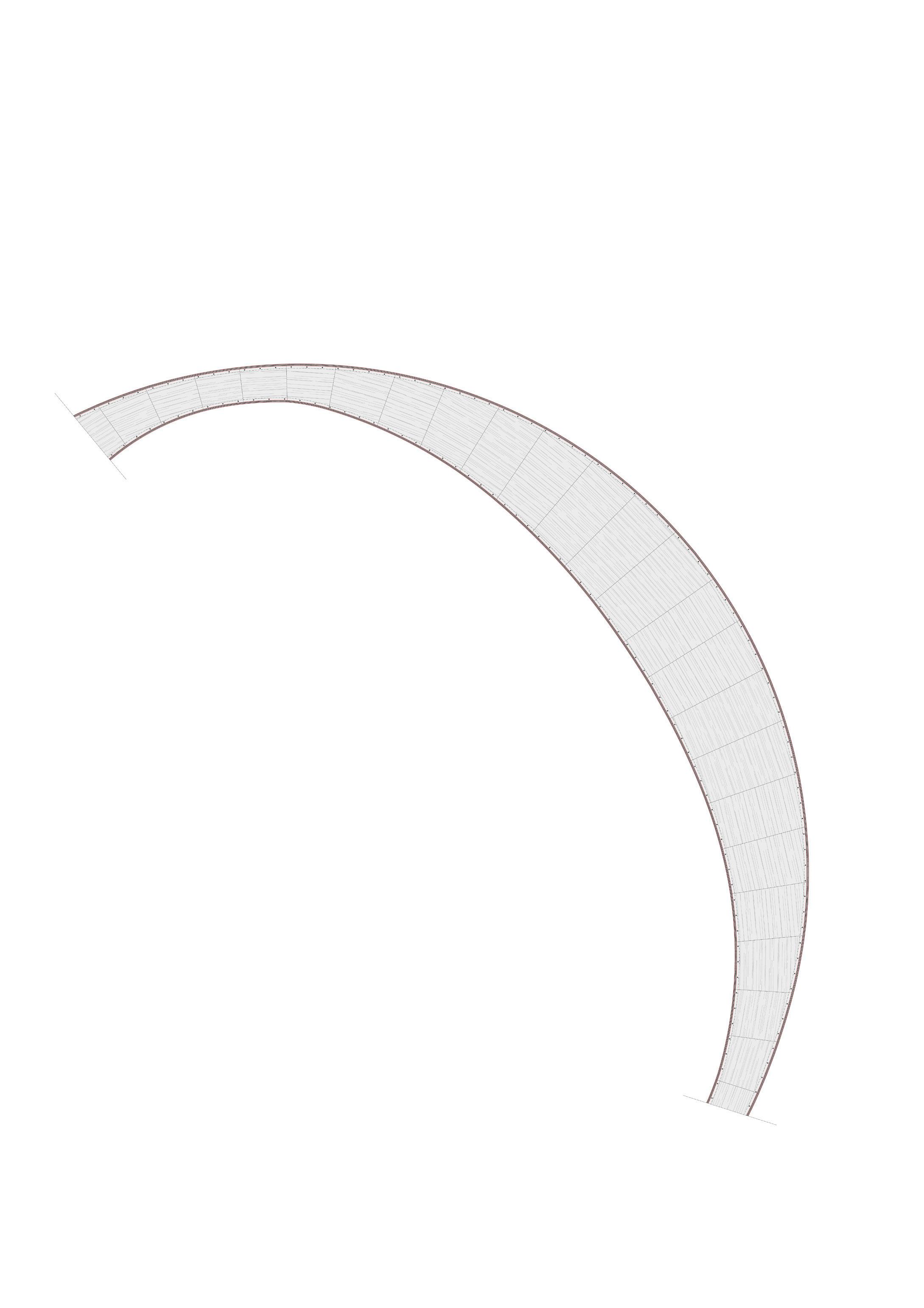
Dead weight: 5KN/mc
Specific weight: 3.9 KN/mc Kmod: 0.60
LAMELLAR WOOD
STRUCTURALANALYSIS
² /8
Q=q*l= 5kN/m²* 1m= 5kN/m
ADMISSIBLE STRESS: σfamm= (Fmk/γm)*Kmod= (24/1.45)*60=9.93 N/mm²
17 1m 6.70m
NAVIER FORMULA
BENDING MOMENT: Mmax= (q*l²)/8=[6.70²]/8= 28.05 kN*m
CALCULATION OF THE BENDING DEFORMATION OF THE ZIPSHAPE
W=b*h²/6=(100*20²)/6= 6666 cmq σmax= Mmax/W= 28.05/0.66= [28.05*(1000m)*(1000m)]/6666= 4.20 kN/mm² σfamm > σMax --> VERIFIED ql/2 ql/2 ql
Light
color: minor displacement
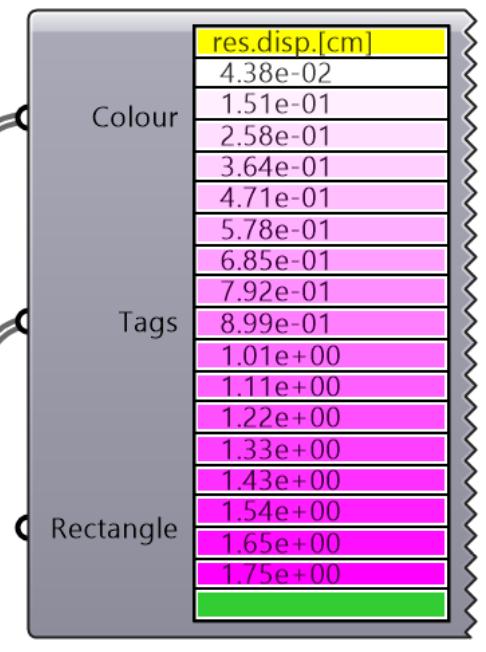
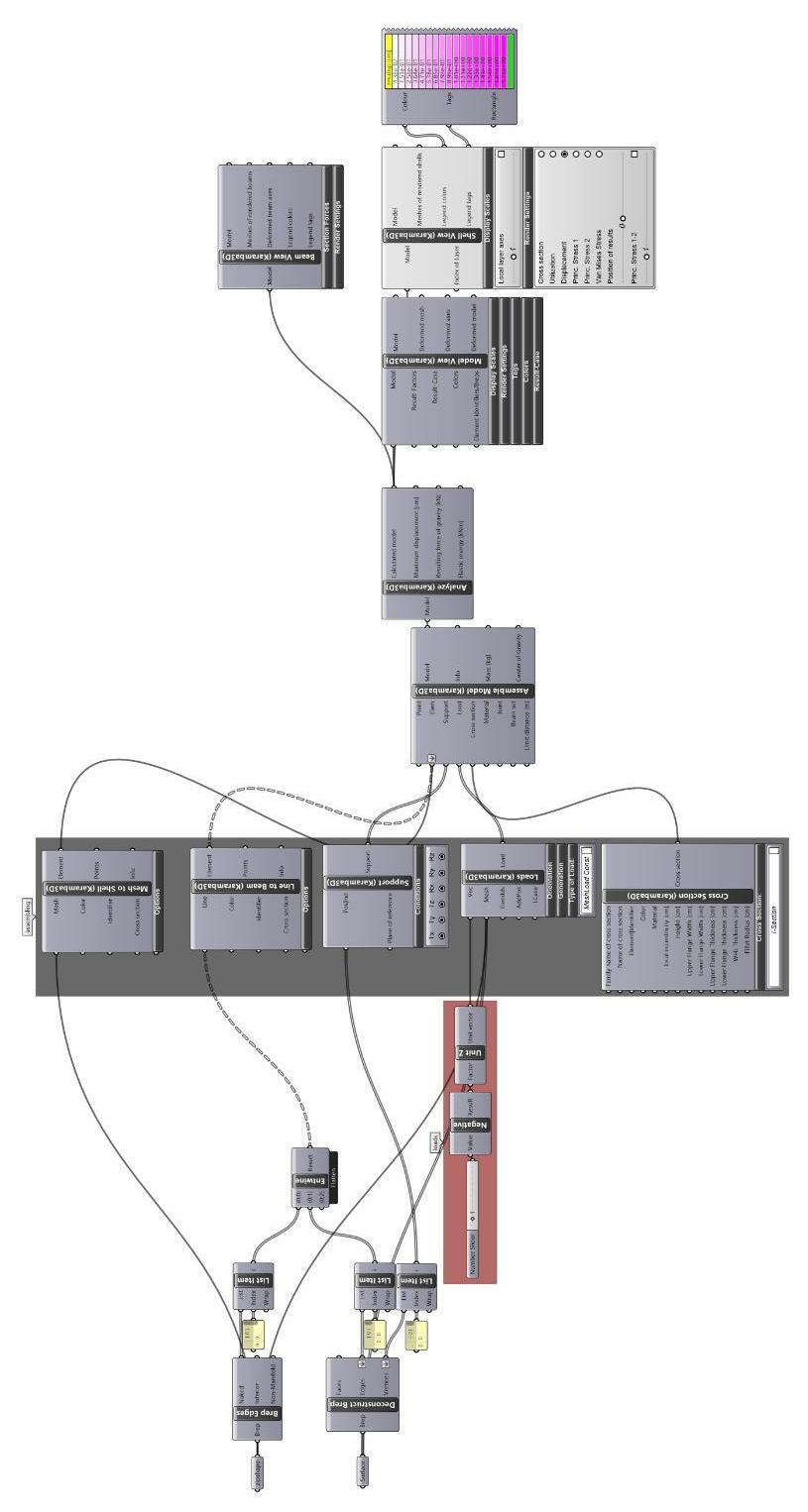
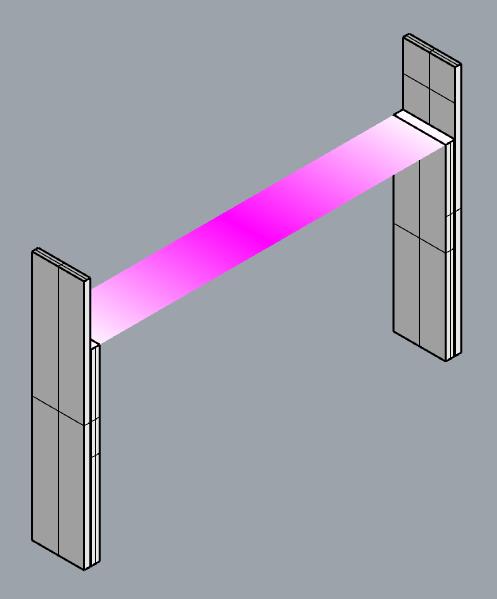
KARAMBA MODEL GRAVITY ONLY DISPLACEMENT* Maximum displacement: 1,75 cm
*Dark
color: strong displacement
19 KARAMBATOTALMODELLOADS DISPLACEMENT* Maximum displacement: 1,40 cm *Dark color: strong displacement Light color: minor displacement


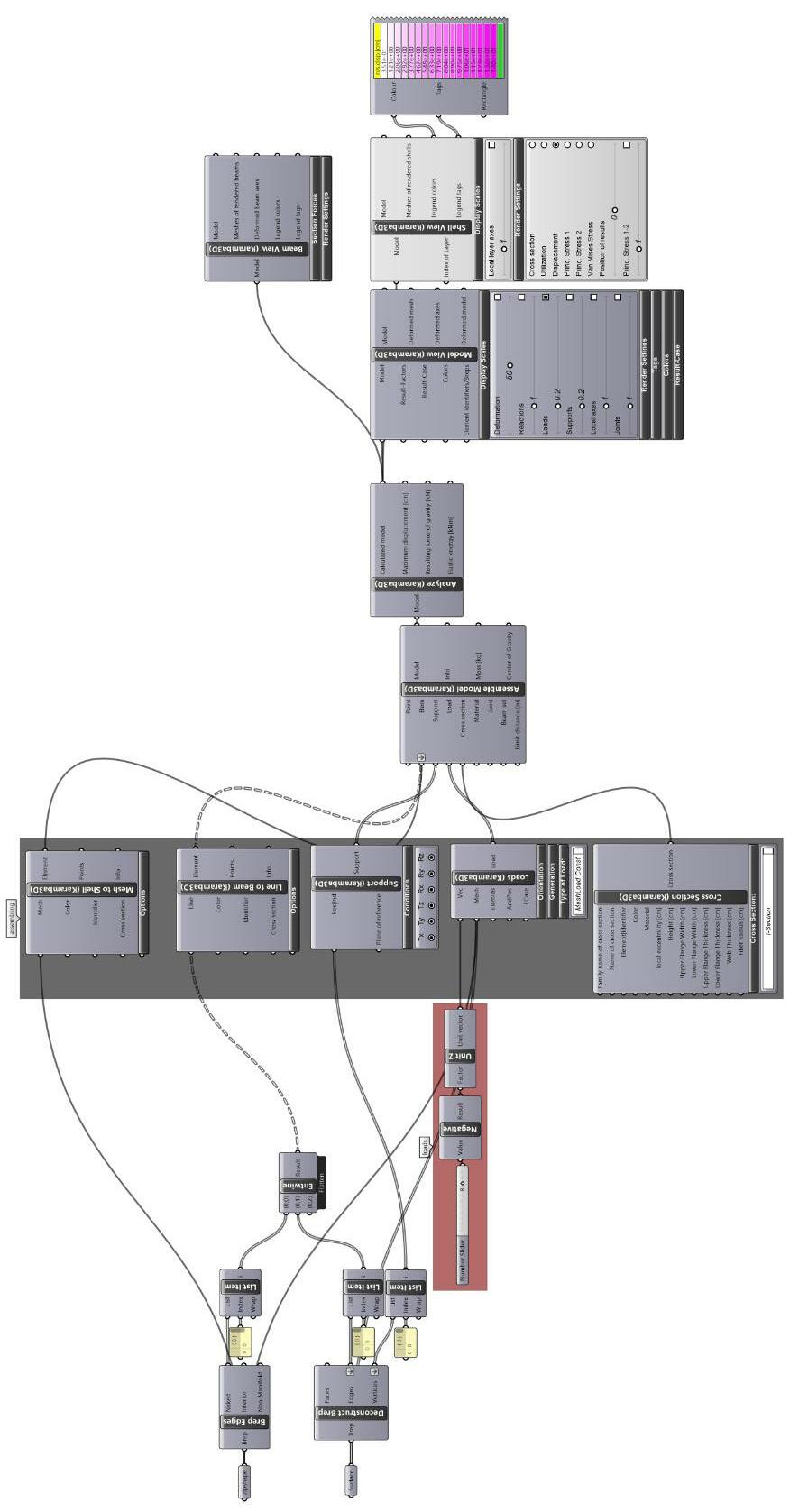
UTILIZATION*
KARAMBA MODEL
Using the Karamba plug-in we can observe the areas of the structure that appear to be thesolicited.most
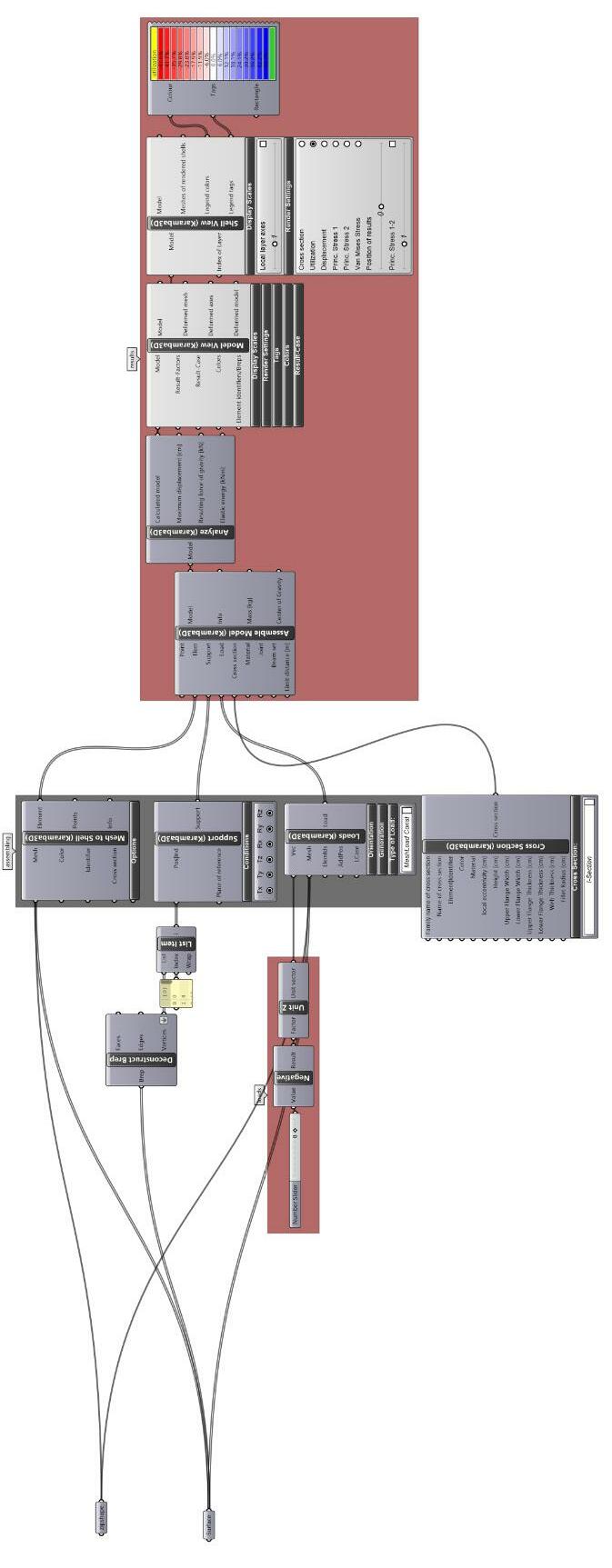
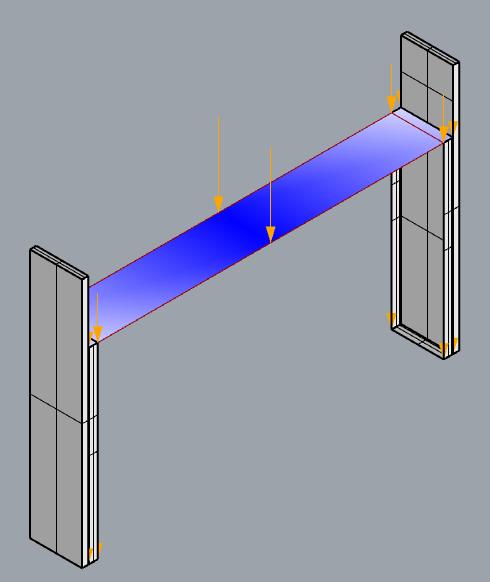
Blue shade: minor stress
TOTAL LOADS
Red shade: higher stress
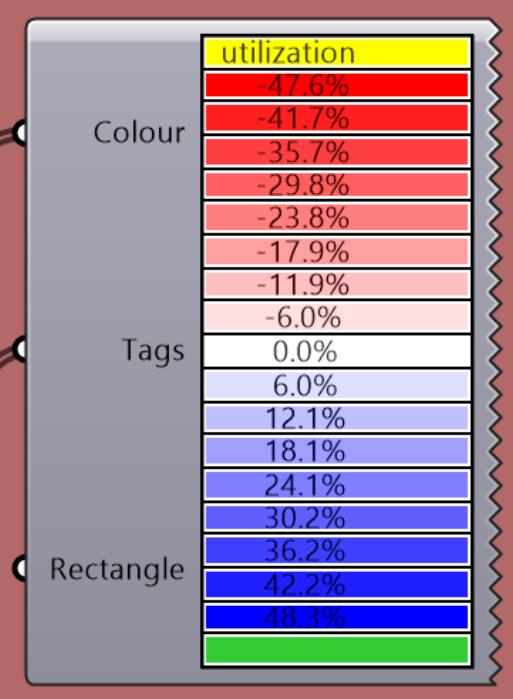
21 RESULTANTDIAGRAMSFORCES N AXIAL FORCESV SHEAR FORCESM BENDING MOMENTS QTOT = 5.15 KN/MQ Permanent loads: 0.15 kN/mq Accidental loads: 5 kN/mq
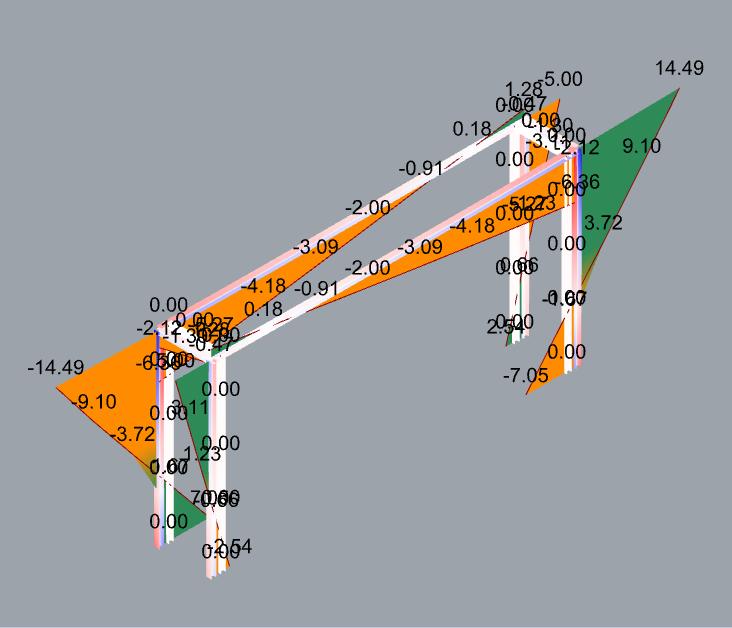
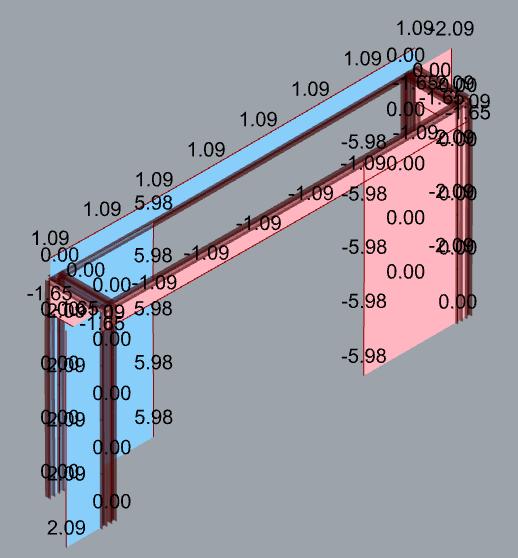
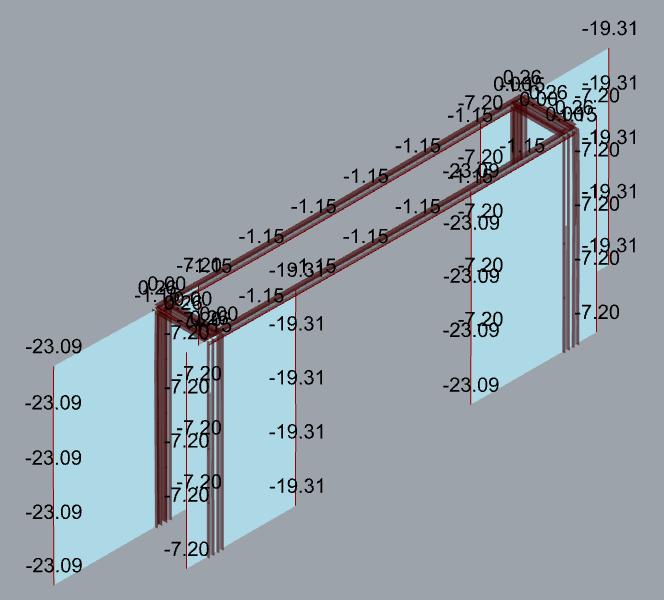
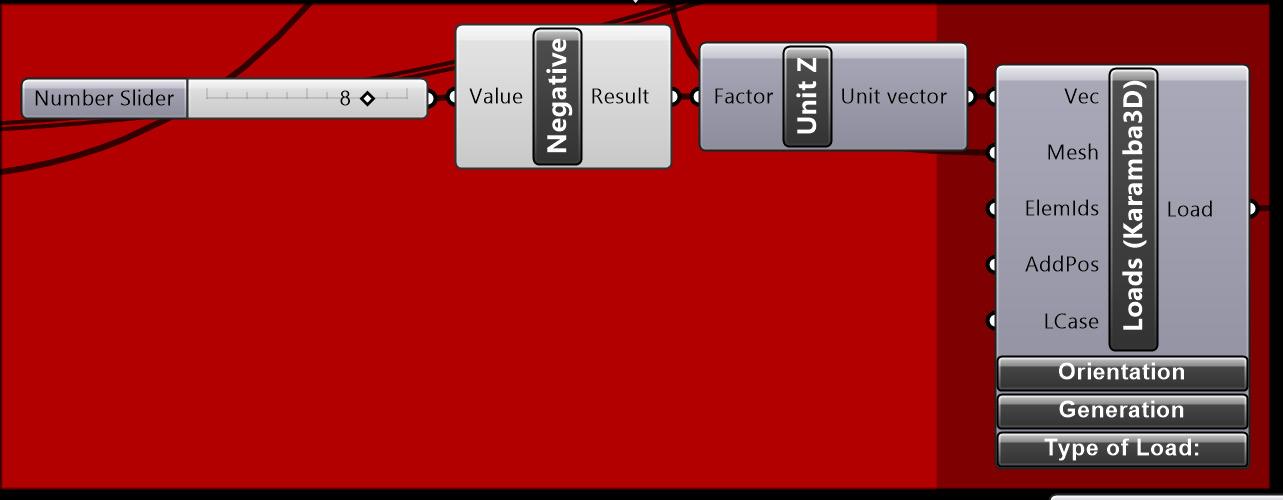
About 3D Printing with https://www.xlamdolomiti.it/Abouthttps://www.upmformi.com/biocomposite-products/3d-printing/large-scale-additive-manufac-turing/https://www.wouldwood.se/celluloseX-lamsystem
REFERENCES
· From control to design: Parametric/Algorithmic Architecture, Ferrè Albert (2008)
About zip shape system
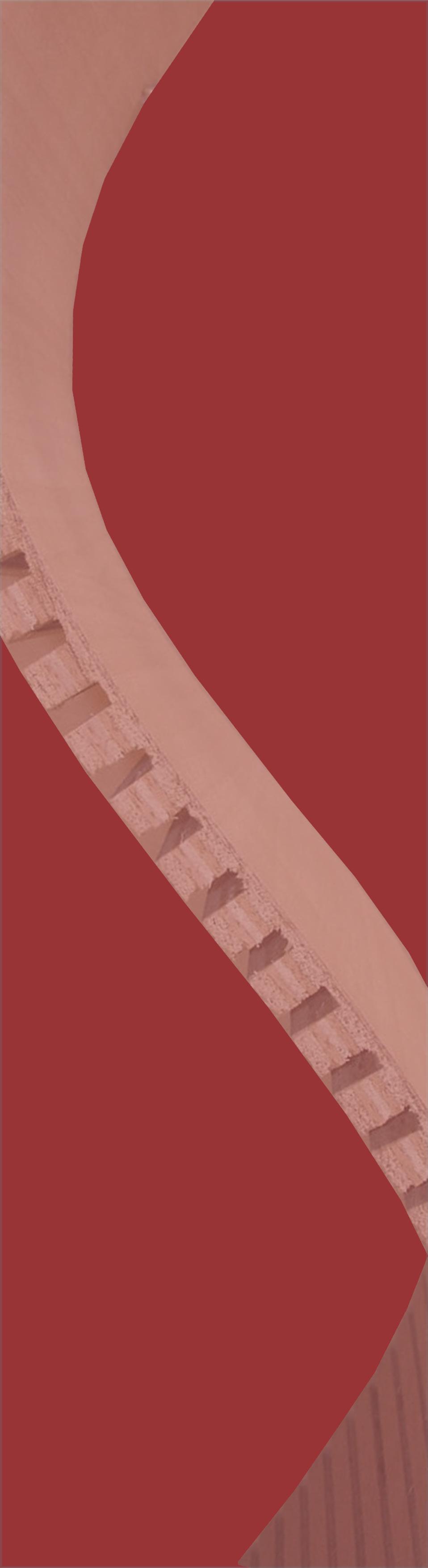