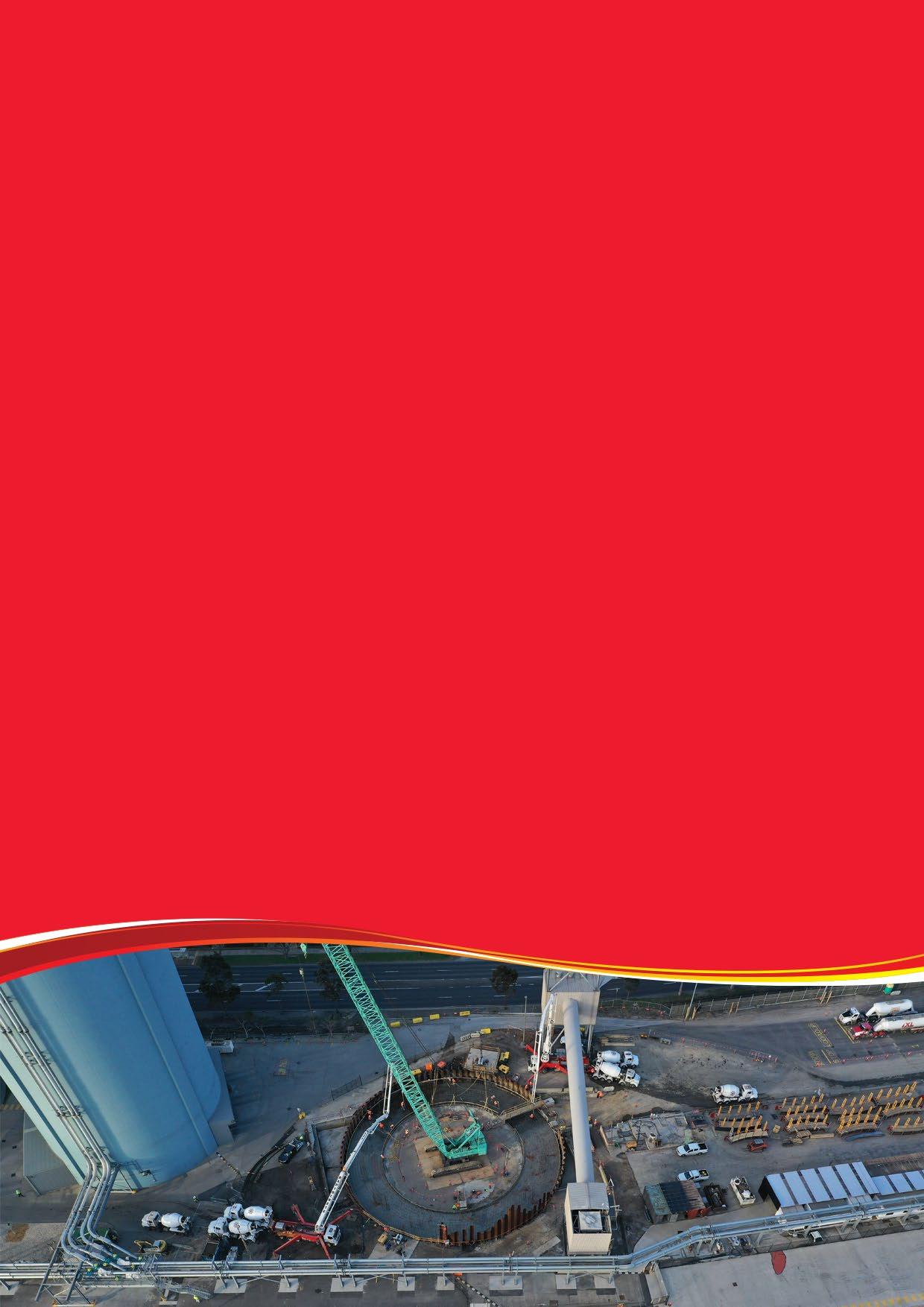
3 minute read
Melbourne Cement Facilities New Multi-Cell Concrete Silo
In efforts to meet Victoria’s demand for cementitious materials, the Melbourne Cement Facility (MCF) has embarked on the construction of an additional 45,000-tonne Multi-Cell Silo (MCS). The MCS is believed to be the largest of its kind in the world is under construction at South Wharf in Port Melbourne.
Designed to store multiple cementitious products such as Portland cement, ground granulated blast furnace slag (GGBFS) and fly ash the MCS is configured to receive a wide variety of pneumatic self-discharge vessels, accordingly the facility has been a design challenge for the team at MCF. This $90 million investment is a key piece of infrastructure that will supply Victoria’s “Big Build projects” into the future, with expectations for total completion in late 2022.
Design challenges the project needs to overcome
Located on some of the most difficult soil conditions, the foundation design has gone through significant rigour to ensure all conditions of silo loading can be safely accommodated, including earthquake loads. A significant number of 1m diameter Continuous Flight Auger concrete piles have been constructed 40m through the Coode Island Silts into the Moray Street Gravels.
The concrete mix designs contain various SCM’s to obtain various desired durability properties, (such as CI resistance, ASR conditions and durability whilst reducing the heat of hydration) demanded of the piles. Once these piles had been installed, a pile cap was required to connect all the piles, resulting in a sharing of the silo loads across all piles. The pile cap used was 1100 cubic metres, 1.3 metres deep that used cement and slag mix. 35% Cement/65% Slag mix was incorporated in the mix design to achieve both these specifications. This was of significant mass and thickness, demanding not only durability for its location but reduced heat of hydration to meet the design specification. Temperature monitoring was undertaken to ensure maximum differentials could be measured. Slag [Eco blend] was supplied from the nearby Steel Cement grinding facility. Steel Cement has been supplying the Victorian market for over 30 years, so it was great to share this local and relevant application with operators at the Yarraville plant, “all too often operators at the facility see tankers come and go without regard to the project destination,” said Alan Dow (Independents Cements Group Operations Manager) “observing the silo construction to its 80m finished height will now have some relevance for the operators,” Mr Dow continued.
The continuous slip walls will also contain supplementary cementitious products in the mix design to meet the demands of the continuous slip process, requiring 100 operators around the clock to feed reinforcement and concrete as the form continually moves upwards. Elements of the inverted cone are formed as precast elements and lifted into place and stitched jointed into place. Specialist supervisors have joined the project team to ensure the elements that will make up the final structure, are constructed per the designer’s intent. As part of the project team, Alan Dow has described the project as demanding and unique in both its design and construction, a showcase of concrete applications and construction techniques, combining continuous slip, traditional in-situ form, precast elements, and concrete piles to build a silo superstructure entirely of reinforced concrete, including the roof.
Steel Cement is a founding member of the Australasian (iron & steel) Slag Association (ASA), instrumental in the original formation of the Industry Association in 1990. Alan Dow was a member of the inaugural Executive Committee for the Association and has seen significant changes in those 30 plus years, with its acceptance as an important supplementary cementitious material. Steel Cement congratulates the work undertaken by various ASA working committees to promote the application of iron and steel slags into such significant projects.