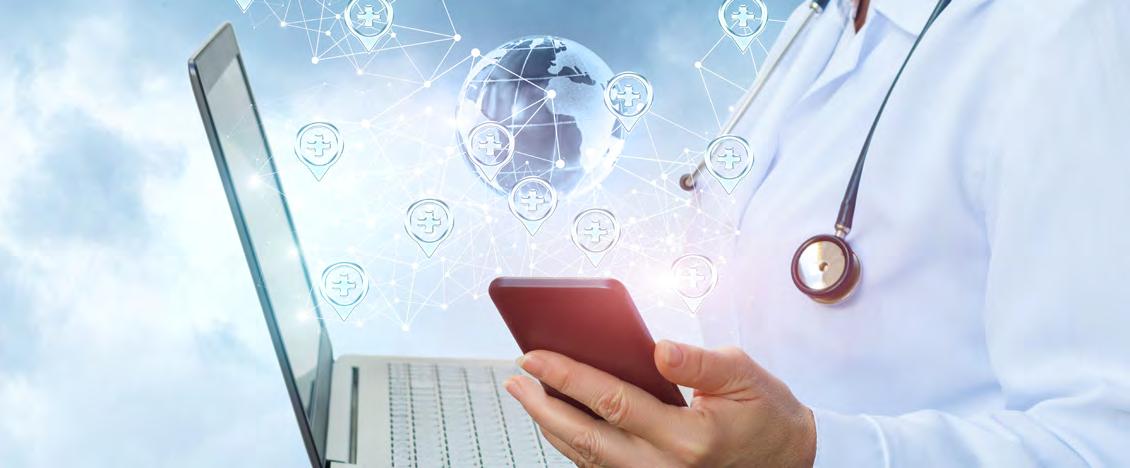
11 minute read
Integra LifeSciences on New Requirements for Medical Devices
Integra LifeSciences and Veeva Systems on New Requirements for Medical Devices How global compliance requirements will impact the device sector
Advertisement
A decade ago, the pharmaceutical industry experienced a shift in its operating model as a result of paradigm-shattering market dynamics and new regulations. The shockwaves continue to impact many large organizations, as specialty biotech companies enter the market, driving rapid innovation, globalization, and increased competition. Now, the medical devices and diagnostics industry (MDDI) is the next in line for dramatic change.
Just as the pharmaceutical industry enjoyed steady growth in the 1990s, the medical device and diagnostics industry has maintained attractive operating margins between 23% and 25% in recent years and 5% annual growth. 1 Established players compete successfully in the global market by applying common business models without much need for differentiation. Now, however, disruptive change is knocking on the industry’s front door largely due to increased regulatory scrutiny worldwide. New compliance requirements are expected to significantly impact medical device and diagnostics opera
tions very soon. Beginning March 2019, the 2016 revision to ISO 13485 will require the incorporation of risk management into every aspect of the quality management system. Additionally, the European Commission ratified new medical device regulations for all European member states, while the U.S. Food and Drug Administration (FDA) released more than a dozen new medical device guidance documents in 2016 and 2017 that set new expectations for risk assessment. Significantly, the new FDA 510(k) requirements for device clearance make the submission process more rigid and complicated. Also known as Premarket Notifications, the FDA 510(k) submission specifies unique content and format provisions for a range of medical device types and classifications to demonstrate that the product is safe and effective. In Europe, the stricter Medical Device Regulation (MDR) will replace the EU’s current Medical Device Directive and came into effect in May 2017 with a three-year transition period. MDR addresses concerns over the assessment of product safety and performance by placing stricter requirements on clinical evaluation and post-market clinical follow-up, and requiring better traceability of devices through the supply chain. “An increased concern for public safety is prompting big changes,” explains Andrew Tummon, director of global clinical affairs at Integra LifeSciences Corporation, a world leader in medical technology, including orthopedic products, surgical instruments, and neurosurgical devices, implants, instruments and systems. “By 2020, the devices industry must show clinical evidence for the effectiveness and safety of both new and existing products. The EU previously required a clinical evaluation report and literature review for many products. These reports involve the assessment and analysis of clinical data pertaining to the medical device to verify its clinical safety and performance.” Tummon remarks that companies will need to make hard decisions on determining which existing products are worth investing money to conduct clinical studies that meet new EU requirements. To get a CE Mark—an indicator that the product has met specifications—is going to be more difficult in the future. The new regulations will force a jump in the number of clinical studies conducted, impacting costs, processes, outsourcing strategy, and even organizational design. “Overall, new medical device regulations will require a significant change in operating processes for global medical device companies or anyone that sells into Europe,” notes Tummon.
INTEGRA’S GROWTH STORY Integra LifeSciences has grown immensely in recent years, especially through its $1 billion acquisition of Codman from J&J. Integra’s orthopedic products include devices and implants for foot and ankle, hand and wrist, shoulder and elbow, tendon and peripheral nerve protection and repair, and wound repair. The company offers a broad portfolio of implants, devices, instruments and systems used in neurosurgery, neuromonitoring, neurotrauma, and related critical care. In the United States, Integra is a leading provider of surgical instruments to hospitals, surgery centers and alternate care sites, including physician and dental offices. As a leader in med tech, it has to keep up with the latest technological advances if it is to meet its goals. Like too many in the med tech sector, Integra used to be largely paper-based, but is now upgrading most of its enterprise technology and moving to the cloud to leverage cost-efficiency and flexibility. Additionally, Integra and others in med tech may have to “weed out” some of their existing products to meet the new regulations, put ting more pressure on such tasks as their need to conduct more multi-center pre-clinical trials and post-approval studies done with optimal efficiency. Most important, Integra is dedicated to reducing uncertainty for surgeons, who make thousands of decisions every day and have no time to waste. This, too, depends on a rapid upgrade in technology, efficiency and collection of data.
PAPER VS. VAPOR— TECHNOLOGY REMAINS STUCK IN THE 90S Even as MD&D companies bring remarkable innovations to market, they have largely relied on dated technology—maintaining manual, paper-based processes and homegrown, on-premise legacy systems. For example, many continue to use email to share documents and information. Traditionally, these organizations have been less motivated to invest in new enterprise
systems because their businesses have enjoyed attractive operating margins between 23% and 25% with 5% annual growth. Plus, more companies in this space tend to be smaller and have had less of a need for solutions designed to improve speed and agility. In Europe, for example, 95% of MDDI companies are considered smallto medium-sized—less than 250 employees—and the majority of these employ 50 people or fewer. 2
However, a sharp rise in adverse events has prompted more increased regulations and strictly enforced modus operandi. In 2015, the FDA issued a total of 3,525 Form 483 Inspectional Observations to 924 medical device companies relating to 21 CFR Part 820 and issued 121 warning letters—a significant rise from a decade ago. While forecasts indicate global MDDI growth at a CAGR of 5.3% through 2020, operating margins are predicted to decline by eight points if companies don’t pivot direction in response to this more highly-regulated market environment. 1 There’s a high-growth, $475+ billion industry at stake, and Europe, where there are nearly 25,000 medical technology companies, is growing even faster than the U.S. 2,3
GETTING AHEAD OF THE CURVE Modern technology will be the game changer in ensuring compliance with new global regulations while gaining greater efficiencies throughout the device development process. Aging infrastructures and paperbased solutions or outdated software will not take these companies into the future. While innovative in medical product development, many medical device companies are conservative about technology and continue to use email to share documents and information. These systems don’t support efficient file sharing, collaboration, or broad visibility. They also are risk-averse and inefficient as clinical and other team members waste valuable time going in and out of static documents to make changes and inputs that reduce productivity and overall program progress. Additionally, many device company’s quality management systems do not meet the new ISO requirements, forcing upgrades. Most important, these legacy systems are inherently inflexible and cannot adapt to changing regulations or market conditions. Data is often trapped in multiple systems, or on paper only, so companies cannot get a comprehensive view of status. Most do not provide a detailed audit trail to support growing requirements throughout the different stages of device studies.
“With automated processes and capabilities to complete tasks in real time, from anywhere, we can optimize staff time and clinical research associates can more easily execute their jobs.”— Andrew Tummon, Director of Global Clinical Affairs, Integra Life Sciences
“As medical device companies are forced to conduct more clinical studies, advanced technology becomes critical,” Tummon points out. “It’s not sustainable to hire more and more people to manage increased numbers of studies. At Integra, we want to completely eliminate paper and paper-based processes, automate, and generate reports at the press of a button. With streamlined processes and capabilities to complete tasks in real time, from anywhere, we can optimize staff time and clinical research associates can more easily execute their jobs.”
NEXT-GEN TECHNOLOGY OPENS NEW DOORS Modern systems provide the framework for more collaborative and transparent document and data management across all functions. As companies outsource more specialized work to third-parties and communicate more regularly with regulatory authorities, nextgeneration cloud solutions offer an easily accessible platform that allows various stakeholders to edit, review, and approve documents without pulling from multiple sources. Most importantly, tasks are documented through the entire product life cycle, establishing an audit trail from the moment a record enters a system until archival. Status updates are automatic and easily referenced through a dashboard. With built-in metrics, companies can generate reports for both internal and external use and capture valuable insights on performance. Advanced technologies knock
down the silos to provide transparency into workflows and document lifecycles across therapeutic groups and, externally, with outsourcing partners who formerly stood outside the corporate firewall. This is particularly important now as medical device companies will need to engage with more external partners to handle increased regulatory requirements. Transparency is essential to control quality and bring together regulatory information. “Increased number of trials will trigger more companies to outsource work to contract research organizations (CROs) rather than build large internal staffs to manage studies, notes Tummon. “As such, we will require CROs to use our cloud-based eTMF and clinical trial management systems. By owning the data and trial master file, we can better assess vendor performance and track progress. The ultimate responsibility for regulatory compliance always lies with the medical device company.”
TAKING IT TO THE (MULTITENANT) CLOUD In an effort to leverage new technologies, many device companies have stacked disparate applications onto legacy systems. As a result, no one is working the same way, resulting in inconsistent data definition, data capture, and processes. Moving forward, many medical device companies are enforcing a “cloud first” policy that eliminates the need for infrastructure and software investments to control costs and simplify management of the IT solution. With cloud providers responsible for upgrades and maintenance, IT staff can concentrate on core business activities. Piloting new technology becomes cheaper, easier, and faster. “Just as the pharmaceutical industry realized, the devices industry can benefit from cloud platforms that allow companies to manage more with less,” says Tummon. “Plus cloud applications allow us to work smarter and from convenient locations. Remote workers and frequent travelers can upload reports in real time from investigative sites, hotels, anywhere…saving time and improving accuracy.” The key is to adopt a multitenant cloud solution rather than a hosted or single-tenant cloud system. Multitenancy is cloud’s hallmark and the defining factor that enables dramatic economies of scale, explained at right. While one software application serves different “tenants” or companies, authorized users can only access their data and their unique instance of the application. Traceable and constantly current, data is always ready for an audit. Companies can integrate a suite of applications onto a single cloud platform to enable transformation across clinical, quality, medical, and commercial business processes.
Multitenant Cloud Defined To explain a multitenant cloud, think of a neighborhood community versus an apartment complex. In the neighborhood, homeowners maintain their own property within a community much the same way that a customer in a singletenant cloud structure manages a dedicated server to run their own version of an application. In the apartment or multitenant model, maintenance and upgrades are handled by a third party. However, owners can customize their apartments any way they want. Much the same way, the provider of a multitenant cloud solution handles all system upgrades, which are transparent and automatic to the user but customers can customize their version or “instance” of the software to meet their needs. Applications are scalable to meet users changing requirements. It’s this multitenancy that delivers all of the highly touted benefits of cloud technology, like cost efficiency and flexibility.
A multitenant cloud solution like Veeva CRM saves companies from having to purchase expensive hardware, troubleshoot problems, or maintain the infrastructure. The provider handles all system upgrades, which are transparent and automatic to users who benefit from always working on the latest application release. Because the model is scalable, companies can quickly make changes and deploy new features and functionality in response to regulatory changes, market fluctuations, and technology innovation. In a client/server environment, a simple field change may require weeks to months of reconfigurations and data migrations. Changes in a multitenant cloud system take just minutes. “As new regulations force medical device companies to conduct more clinical studies to remain in compliance, new technology platforms will help them to work more efficiently,” Tummon concludes. “While medical devices remain a high-growth area in terms of innovation, next-generation technology is the key to working smarter, faster and maintaining the competitive edge.” • SOURCES: 1. AT Kearney “Medical Devices: Equipped for the Future?” https://www.atkearney.com/docu
ments/10192/5227116/Medical+Devices+- +Equipped+for+the+Future.pdf
2. Medtech Europe, “The European Medical Technology Industry, in figures,” pg. 21. http://www.medtecheu
rope.org/sites/default/files/resource_items/files/ MEDTECH_FactFigures_ONLINE3.pdf
3. Deloitte & Company, “2017 Global Life Sciences Outlook: Thriving in today’s uncertain market,” pg. 9. https://
www2.deloitte.com/content/dam/Deloitte/global/ Documents/Life-Sciences-Health-Care/gx-lshc2017-life-sciences-outlook.pdf
Melonie Warfel VP of Medical Devices & Diagnostics Veeva Systems Melonie has more than 25 years of technology experience, with expertise across multiple verticals— including life sciences, healthcare, manufacturing, and government. As vice president of medical device & diagnostics at Veeva Systems, she is responsible for MD&D strategy, customer engagement, business development, strategic alliances, and market adoption. Before her role in MD&D, Warfel was vice president of Vault platform, where she was responsible for new market development, solution identification, customer engagements, and go-to-market activities. Prior to joining Veeva, Warfel spent six years building and growing the life sciences practice at l Pegasystems, and 19 years at Adobe Systems, where she drove the development of the company’s vertical business strategy.
melonie.warfel@veeva.com
Veeva Systems Inc. is a leader in cloud-based software for the global life sciences industry. Committed to innovation, product excellence, and customer success, Veeva has more than 550 customers, ranging from the world’s largest pharmaceutical companies to emerging biotechs. Veeva is headquartered in the San Francisco Bay Area, with offices in Europe, Asia, and Latin America. For more information, visit veeva.com.