
1 minute read
Perfect paint preparation of agricultural equipment components
Agricultural equipment is constantly exposed to tough climate and weather. For this reason optimal paint preparation is essential for the equipment to hold up under such tough conditions. A custom-engineered continuous feed spinner hanger blast machine
RHBD-K 22/27-HD, installed in a new factory of a globally active manufacturer, is making a significant contribution towards this goal. The shot blast machine is integrated into a fully automated manufacturing line. It allows the blastcleaning of a variety of complex weldments, weighing up to two tons, prior to painting.
This Brazilian manufacturer supplies innovative agricultural machinery for a wide range of applications. For example, it is used for harvesting coffee beans and sugar cane as well as for seeding and cultivating all kinds of agricultural crops. The company is active in more than 100 countries. Reasons for this success are the excellent productivity and quality of the equipment as well as the continuous improvement of the manufacturing operation. It is not surprising that the new factory in Brazil is equipped with a fully automated, digitized manufacturing line. There, steel plates and profiles are cut, welded into complex constructions, shot blasted and painted in continuous flow operation. Based on the tailormade equipment concept, the technical implementation and the high equipment quality, the company had decided to purchase the continuous feed spinner hanger blast machine RHBD-K 22/27-HD made by Rösler.
The work pieces are transported through the shot blast machine by the power & free conveyor system of the manufacturing line. This required optimal coordination of the various interfaces in the manufacturing line. But thanks to the help by the colleagues at Rösler Brazil the whole project went very smoothly.
Energy-saving shot blast operation integrated into the overall manufacturing process
After the welding operation the components are transported through an inlet chamber into the actual blast chamber equipped with 12 Gamma 400G turbines, each with a drive power of 11 kW. These innovative Rösler high-performance turbines contain curved throwing blades in “Y” design. Compared to conventional turbines the special blade design with optimal curvature increases the throwing speed significantly.
The shot blast machine for the continuous blast-cleaning of welding assemblies is integrated into the overall manufacturing line. Manual touchup blasting of particularly complex surface areas can be done in a blast room located behind the outlet chamber of the shot blast machine. The thrown blast media from the blast room is transferred to the media cleaning system of the shot blast machine.
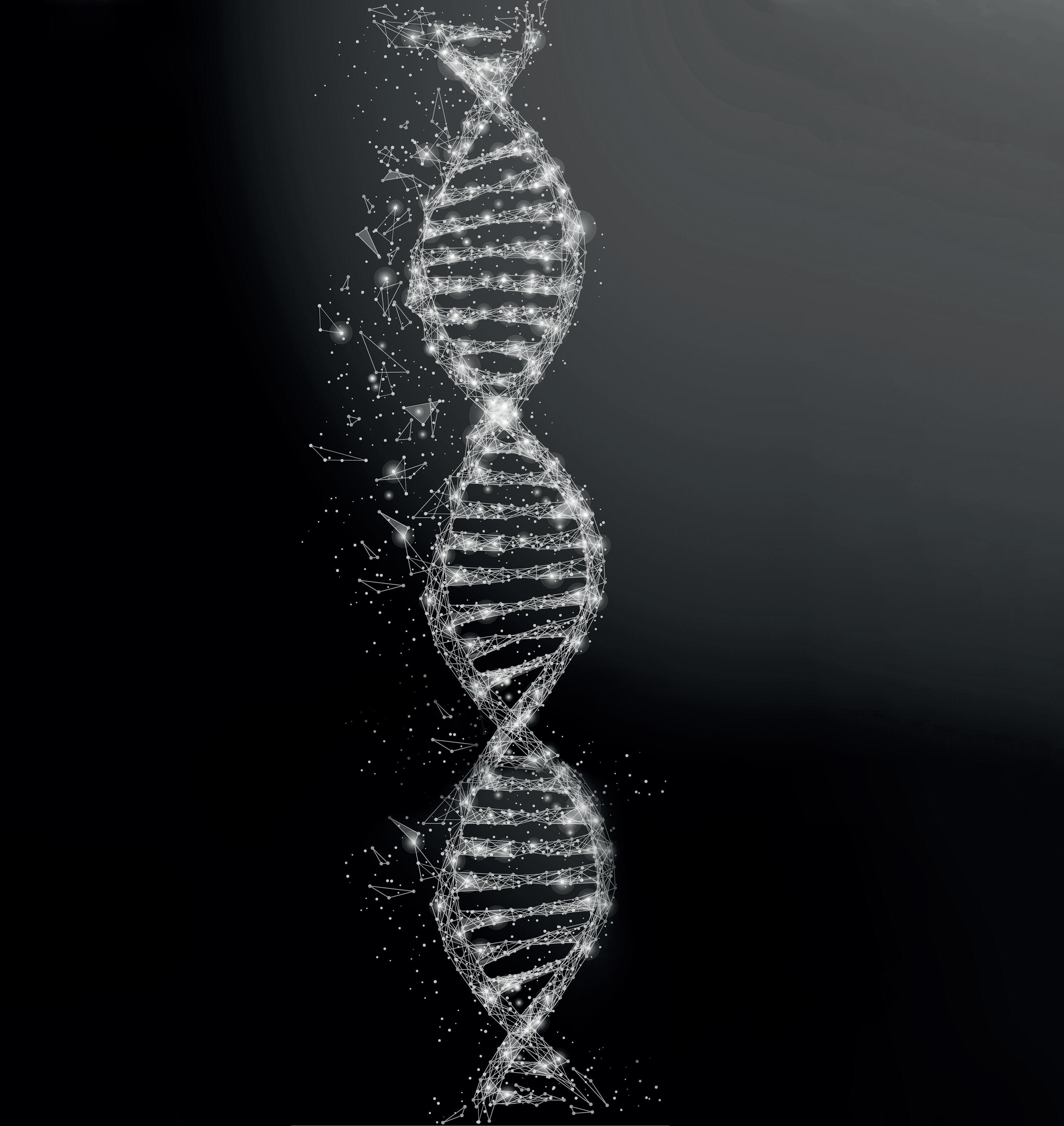