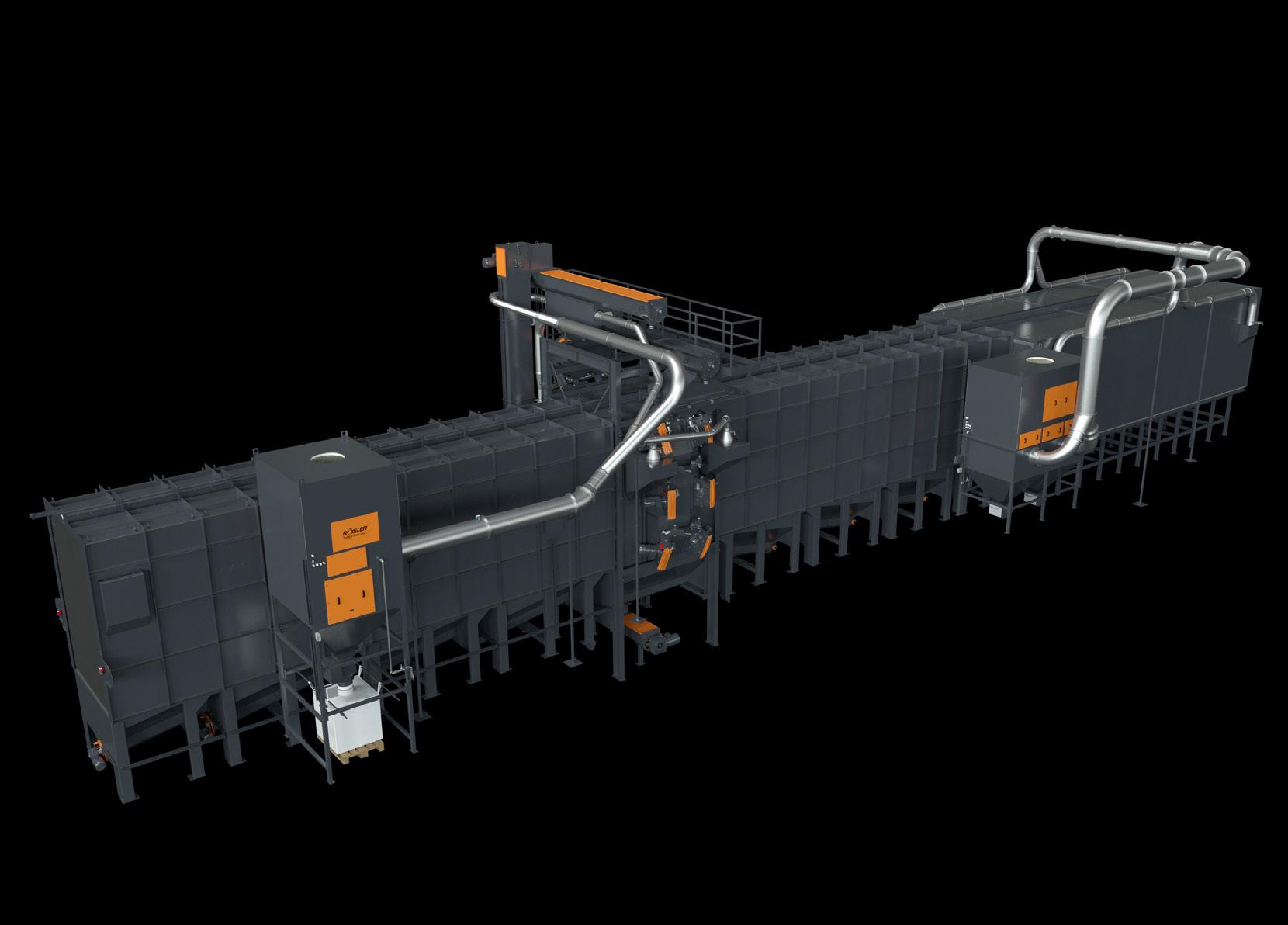
1 minute read
PRE-TREATMENT, SURFACE PREPARATION, DEGREASING & CLEANING
This results not only in an up to 20 % higher blasting performance but also in significantly shorter cycle times.
Sophisticated equipment design allows more flexible shot blasting operation
Because of the enormous work piece diversity the shot blast machine was designed to handle welding assemblies with dimensions of up 10,000 x 2,000 x 2,500 mm (L x W x H) and weights of maximum 2,000 kg. Some of the weldments have thick walls and are very sturdy, whereas others have thin walls and are delicate. To account for these differences and to consistently achieve the required preparation grade of Sa 2,5 as well as the specified surface roughness values, the turbine RPM is controlled by frequency inverters. This ensures optimal paint adhesion and prevents warping of the thin-walled components. The variable turbine speed and the automatic control of the media flow allows precise adaptation of the blast-cleaning process to the different welding assemblies. Selection of the workpiece-specific shot blast programs is done at the master computer of the manufacturing line. Behind the outlet chamber of the shot blast machine is a blast room that allows the manual touchup blasting of geometrically complex assemblies with undercuts and internal passages. Augers below the blast room floor transport the thrown blast media to the central media cleaning system. This eliminates the need for a separate media transport and cleaning system for the blast room.
Wear-resistant design ensures high equipment availability
The customer was also impressed by the wear-resistant design of the Rösler equipment. For example, the blast chamber is made from manganese steel and is protected by easily replaceable 10 mm thick wear liners, also made from manganese steel. Another plus is the fact that both sides of the throwing blades can be used, which practically doubles their usable life. The throwing blades can be replaced with a quick-change system without having to take the turbine apart.
Visit: www.rosler.com
The 12 Gamma 400G turbines are arranged in a circle around the blast chamber. Because of the curved design of the throwing blades, the shot blast process is particularly productive and energy efficient. The turbine RPM is controlled by frequency inverters. The variable turbine speed and the automatic control of the media flow allows the precise adaptation of the blast-cleaning process to the different welding assemblies. This ensures optimal paint adhesion and prevents warping of thin-walled components.