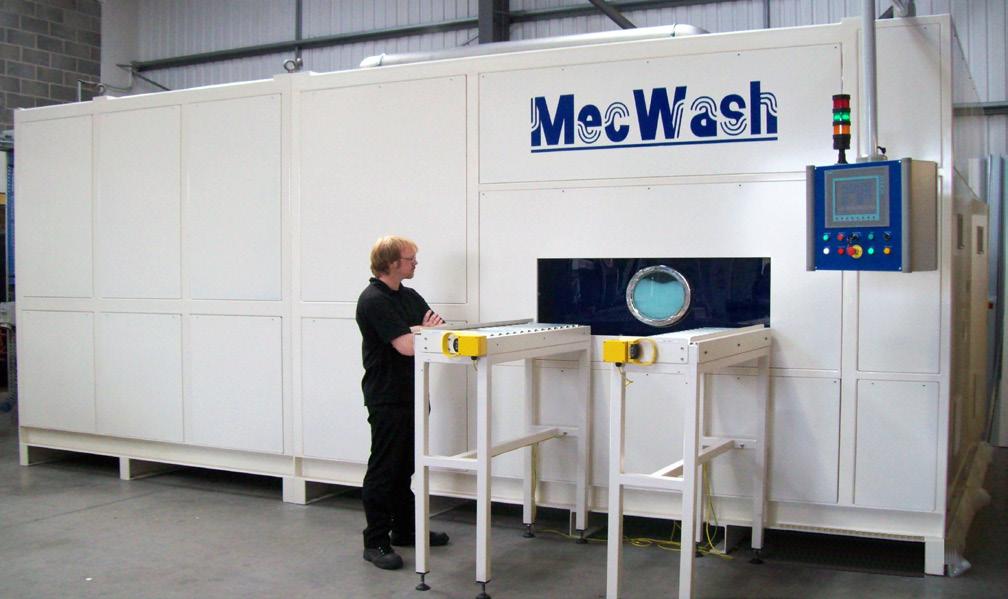
1 minute read
SURFACE PREPARATION, PRE-TREATMENT & DEGREASING
“We know that substandard cleaning will breach stringent requirements, so the need to achieve a first-class finish in aerospace is paramount. We work with customers to fully understand their situation and build their parts washing system to surpass expectations, no matter the application.” said Pattison.
MecWash appreciates that some applications require a long development process working in partnership with a manufacturer. For example, MecWash spent about two years working on one blade cleaning application from concept design, through prototyping, then numerous trials and supporting the internal approval process for the required process change, before building the final system. MecWash are comfortable making the investment to develop relationships with key customers.
Different aerospace applications can require a variety of different wash solutions.
Engine Components
MecWash has designed and built systems to wash a wide range of the most challenging components with complex geometries or with tenacious contamination including high and medium pressure blades at various stages of manufacture, bearing housings, NGVs, heat exchangers and heat shields. In addition to our more standard systems, two were developed specifically for engine components.
The SuperMaxi is the largest parts washing machine made by MecWash and can clean components such as bearing housings, blisks and intercases. The system includes our unique direct jetting technique, where the component is held in a rotating fixture with nozzles built into it, that continuously flush out critical features, blind holes or oil ways as the component rotates. Along with the flood and spray wash and rinse stages, this dedicated jetting provides powerful cleaning and highly focussed contaminant removal for engine components.
A second tailor made system is the BladeWash, created to address the tough challenge of flushing the internal cooling channels of highpressure turbine blades. This unique system was developed by working closely with a leading blade manufacturer. The system holds the blades firmly while high speed / volume flushing over and through the blades takes place.
BENEFIT FROM GLOBAL SOLUTIONS DELIVERED WITH THE CONFIDENCE OF LOCAL SUPPORT
When it comes to heavy equipment, there’s no room for error.
From demanding durability requirements to exacting color and finish criteria, the toughest of applications require the most formidable of solutions.
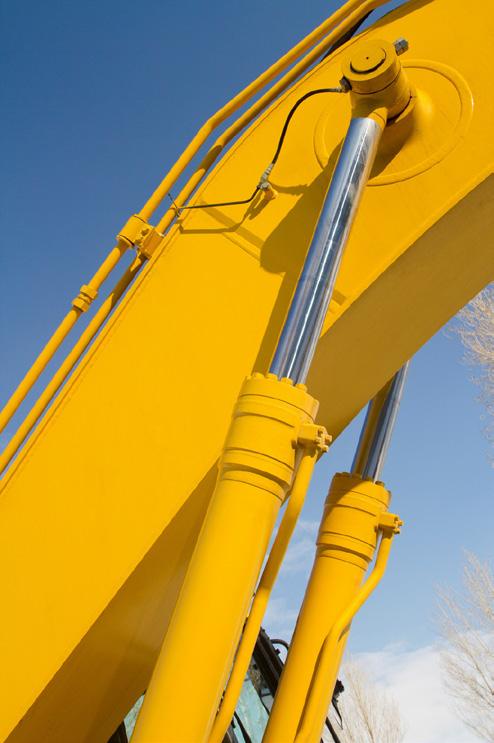

Contact: gi.emeai.marketing@sherwin.com
Visit: www.sherwin-williams.eu