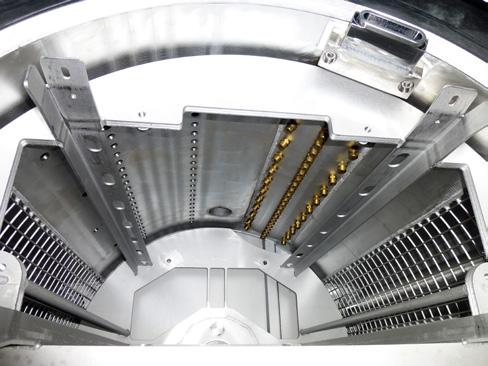
1 minute read
SURFACE PREPARATION, PRE-TREATMENT & DEGREASING
Actuators and Controls
MecWash clean a very broad range of actuation systems for aerospace customers, from hydraulic manifolds to gears. Applications range from control surfaces to undercarriage and brakes with customers including Goodrich and Meggitt.
The precise nature of these actuation systems demands very high cleanliness standards and MecWash’s MWX400 system with flood washing, ultrasonics at 20 watts / litre and vacuum drying is typically used to remove the coolant, oil, and other contamination to hit tight cleanliness standards.
Sensors
Sensors require very high specification cleaning, but often need a delicate touch to avoid potential harm. The MWX300 is a small footprint high specification system, that often fits well in the smaller production facilities for these high value components, while delivering the highest cleanliness standards.
Fasteners
MecWash has decades of experience of working with aerospace fastener manufacturers, including SPS Technologies, to build systems for the cleaning of high volumes of titanium, brass, and steel fasteners. A high volume, good quality and good value system is typically required for these components.
The MecWash Duo is the most used machine by customers manufacturing fasteners. Suitable for both large components and dense baskets of small parts, the flood wash, spray rinse and hot air dry gives a simple but consistent wash process for such parts.
As well as delivering the highest cleanliness standards, aerospace companies require precise process control. MecWash systems support this with their fully integrated communications architecture. Each system comes with a built in eWon router that enables an external connection via a guest network (outside the firewall protected system) to the PLC.
Once connected, the system’s Profibus connectivity allows you to inspect not only the PLC & HMI but the pneumatic valve island, inverters, and individual sensors. This approach is ideal for both maintenance and remote support.
John Pattison continued: “The majority of manufacturers in aerospace are focused on reducing their environmental impact wherever possible. Using a MecWash machine can contribute to this in a couple of ways. First, selecting an aqueous wash solution is far preferable for both the workforce and the environment than toxic solvents. Secondly, a MecWash machine is very efficient in its use of water. We have developed the Aqua-Save system, that allows the wash and rinse solutions to be continuously recycled, greatly reducing the frequency of replacing the wash and rinse solutions.”
MecWash’s rigorous approach to aerospace components always starts with the in-house laboratory. Components are tested for cleanliness. Contaminants and substrates are assessed with different processes and chemistries and numerous options can be examined before machine trials begin. “With the experience of the team at MecWash, we are confident in our ability to build the optimum machine for any application within aerospace.” said John.
Telephone: +44 (0) 1684 271600
Email: enquire@mecwash.co.uk
Visit: www.mecwash.co.uk