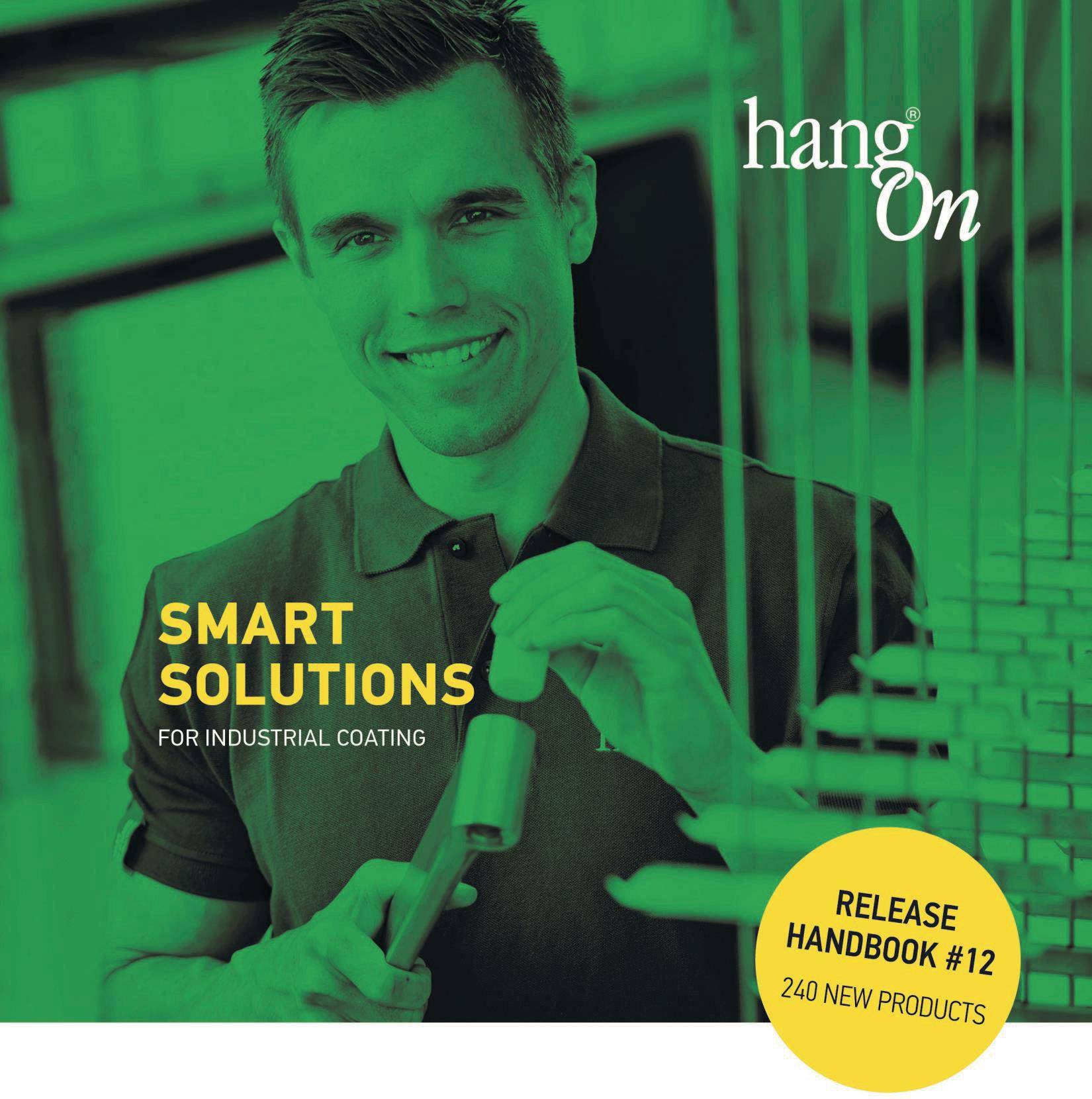
1 minute read
THIS IS HANGON
HangOn is a partner who helps customers to nd smart solutions to increase the e ciency in their coating process and improve their pro tability. We develop and produce in own factories. Our products are distributed from our warehouses into more than 40 countries.
Accuracy of data can be maximized through auto application of both data logger and thermocouple correction factors. All analysis and reporting requirements of the CQI-12 are provided by the software to verify full compliance.
For continuous processes the data logger can travel safely, protected by a suitable thermal barrier, with the TUS frame through the process. Live data can be transferred if RF telemetry is used, otherwise, the TUS run can be simply downloaded post run for full TUS analysis and reporting.
For batch oven processes the data logger can be used externally to the oven trailing TUS thermocouples without need for thermal protection. Each thermocouple is fixed to the designated location on the TUS frame positioned in the oven cavity. Live data generated during the run can be viewed in real time in the survey software during the TUS run. Data transfer from data logger to PC can be performed by either a hardwired comms cable, Bluetooth or optional RF telemetry feature.
Oven Optical Profiling
Thru-process temperature profiling provides a great understanding of what temperatures the product sees travelling through the cure oven. In terms of paint quality though, in particular cosmetic finish and paint defects, this is not the complete story. During the journey through the oven the painted part can experience many problems that are not temperature related that can affect the quality of the cured paint. Problems such as paint runs, drips, or paint inclusions from dust or particulates can only be detected post process without any specific knowledge of the root cause / location in the oven of the problem. The Optic system developed by PhoenixTM travels through the paint cure oven with the product capturing a live video of exactly what the product sees on its journey. The optic system shown above can combine temperature and optical profiling in a single run. The technology is perfect to detect the source / root cause of paint inclusions. Dust contamination in the oven can be detected as streaks of light passing across the torch illuminated video image, just like a shooting star across the night sky. The same system can detect damage to the inner oven walls / insulation which may be the cause of heat losses resulting in inefficient operation and wasted energy.
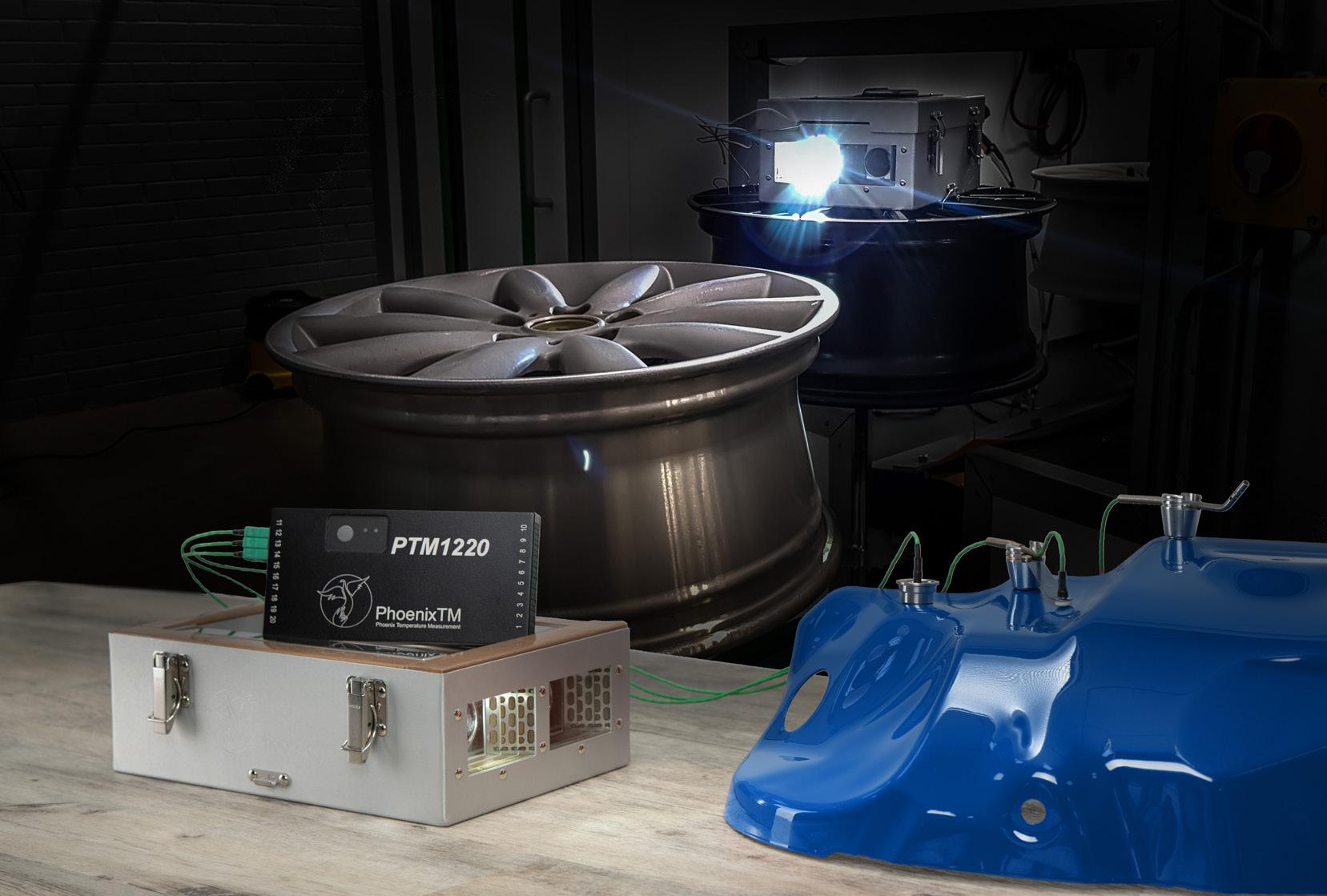
To understand, control and optimise your coating operation why not PhoenixTM your finishing oven today!
Email: sales@phoenixtm.com
Visit: www.phoenixtm.com