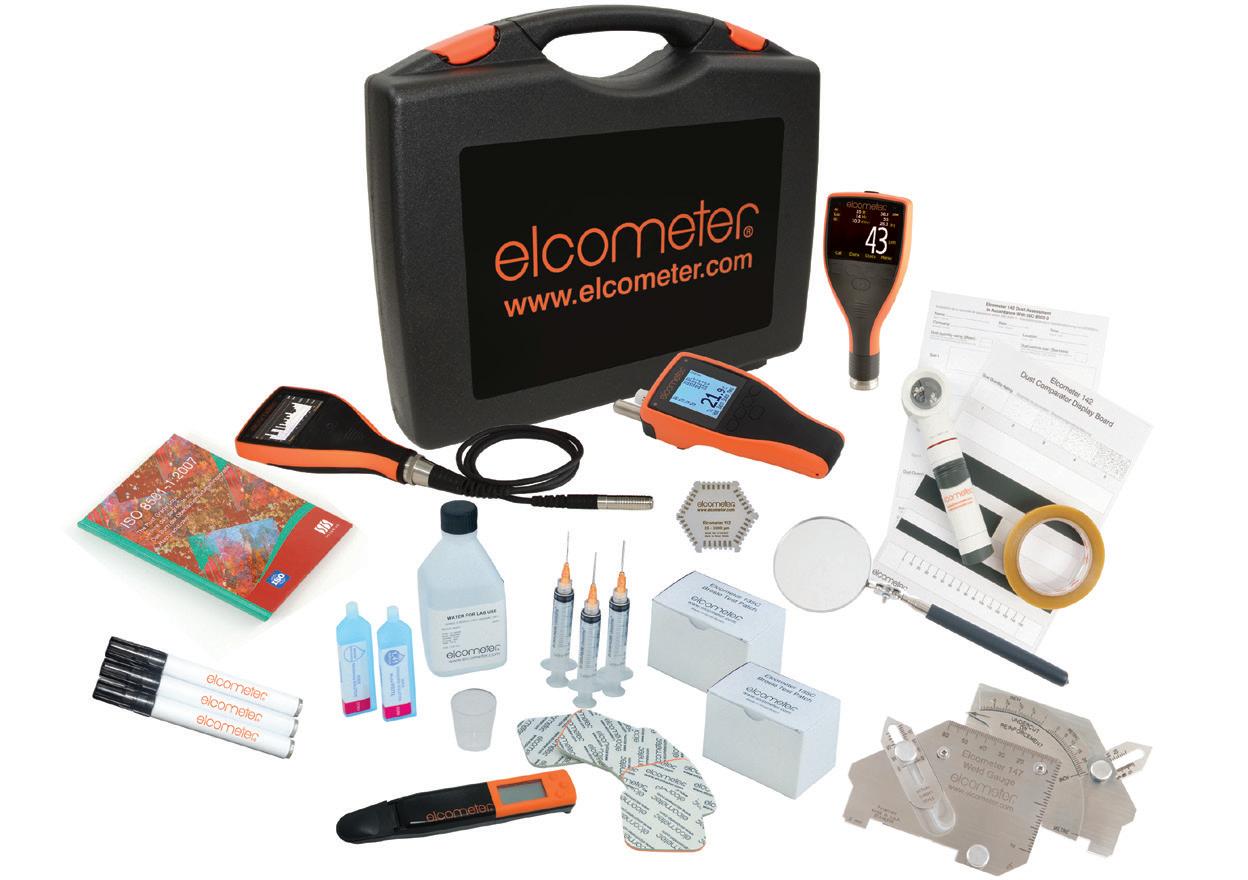
2 minute read
Gas Process Burners
Lanemark gas burner systems offer users reliable, high efficiency, process heating solutions.
FD Series Packaged Oven/Dryer Burners
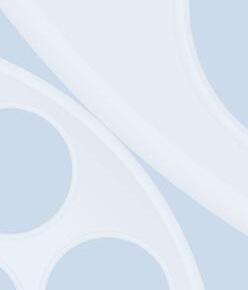
•Speci cally designed for process air heating applications in convection ovens and dryers
•High turndown/short ame lengths providing accurate process temperature control
•High ef ciency gas + air modulation, gas only modulation and simple high/low control options
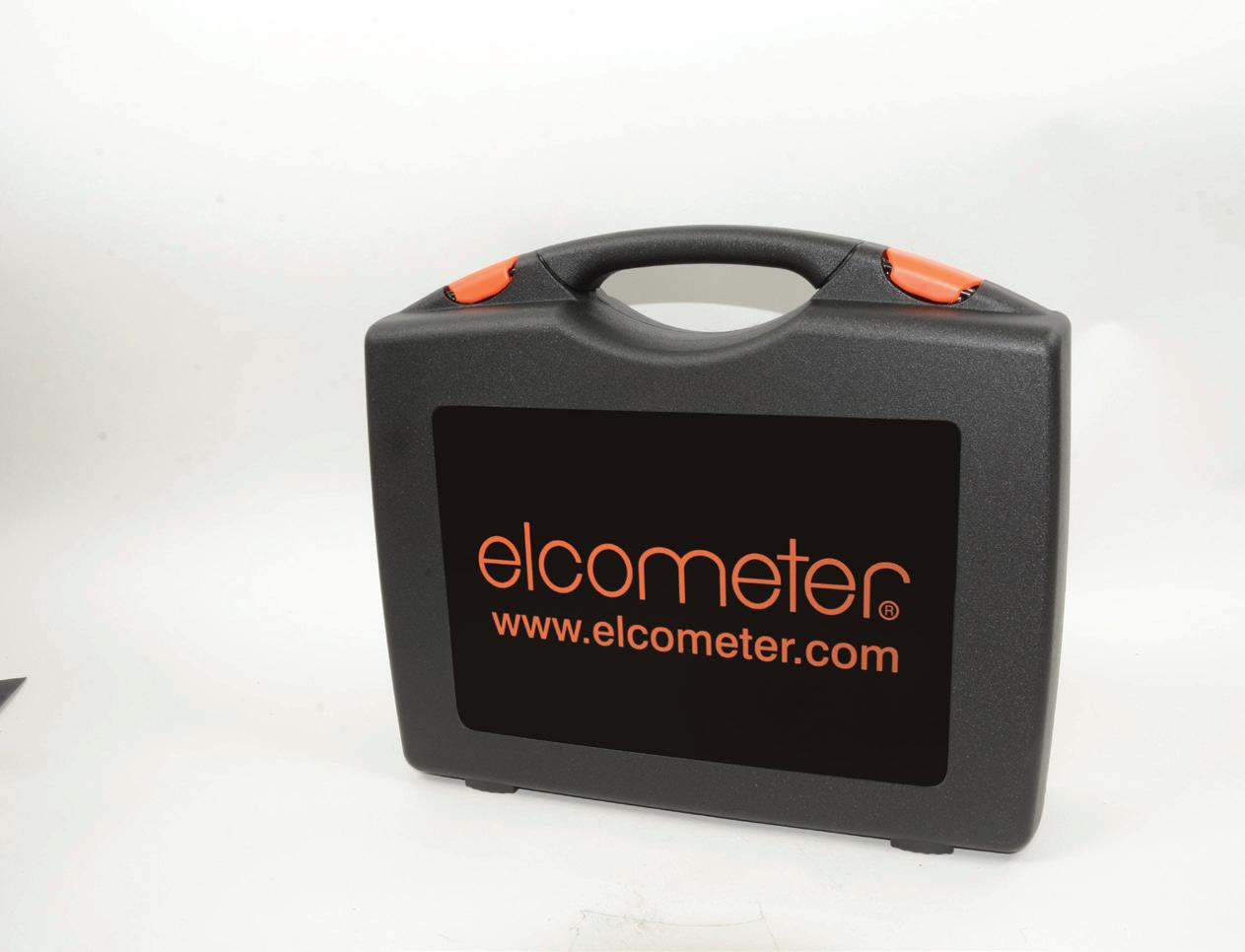
•Heat Input Range: 9 kW – 1550 kW
TX Series Gas Fired Process Tank Heating Systems
•High ef ciency (80%+) heating of all types of spray and dip process tanks
•Compact high ef ciency small diameter immersion tube heat exchangers occupying minimum tank space
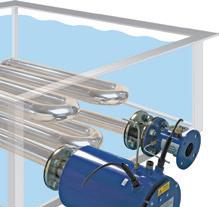
•Accurate performance modelling using Lanemark TxCalc design software
•Heat Input Range: 15 kW (1½") – 1150 kW (8")

Midco HMA Series Air Replacement or “Make-Up” Air Heating Burners
•Direct red, high ef ciency burner systems, for high volume air heating applications such as paint spray booths, ovens and dryers.
•Supplied either as Midco burner heads for OEM system integration or as Lanemark DB or FDB complete packaged systems including modulating gas valve trains and controls
•Wide range of ring rates to suit alternative temperature rise and air velocity system requirements
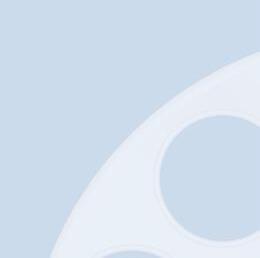


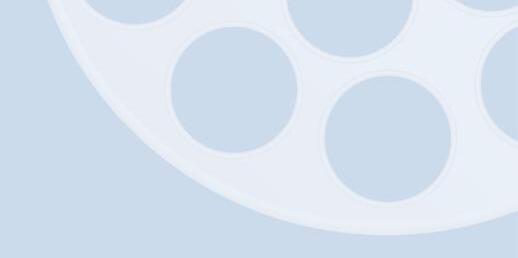
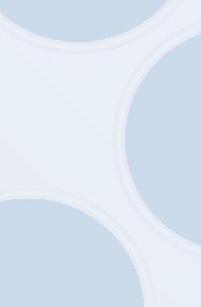
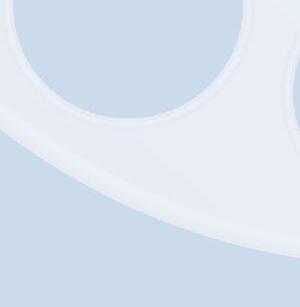
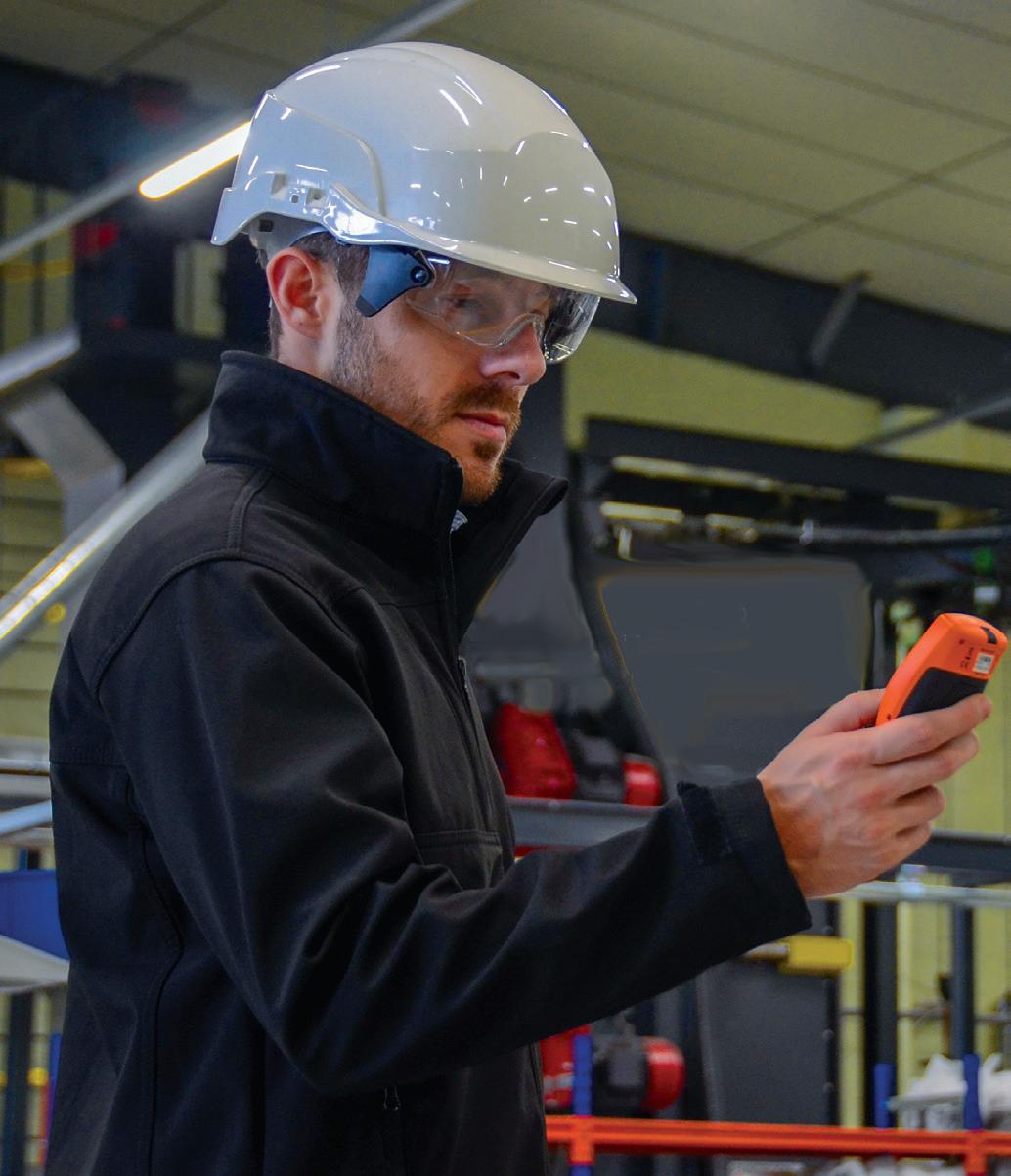
•DbCalc system design software

It became obvious during research that the aluminium alloy itself was the contributing factor, so the Working Group began to develop a specification for the alloys used in fenestration, namely alloy 6060 and 6063. The resulting alloy specification, which now forms Appendix A13 of the QUALICOAT Specifications 2023, requires the alloys to fall within the EN573-3:2019 Standard, which can be met using primary or secondary (recycled) aluminium and requires the following three tests to be carried out, Optical Emission Spectroscopy (OES), Anodic Cyclic Polarisation (ACP) and Metallographic Study for Aluminium.
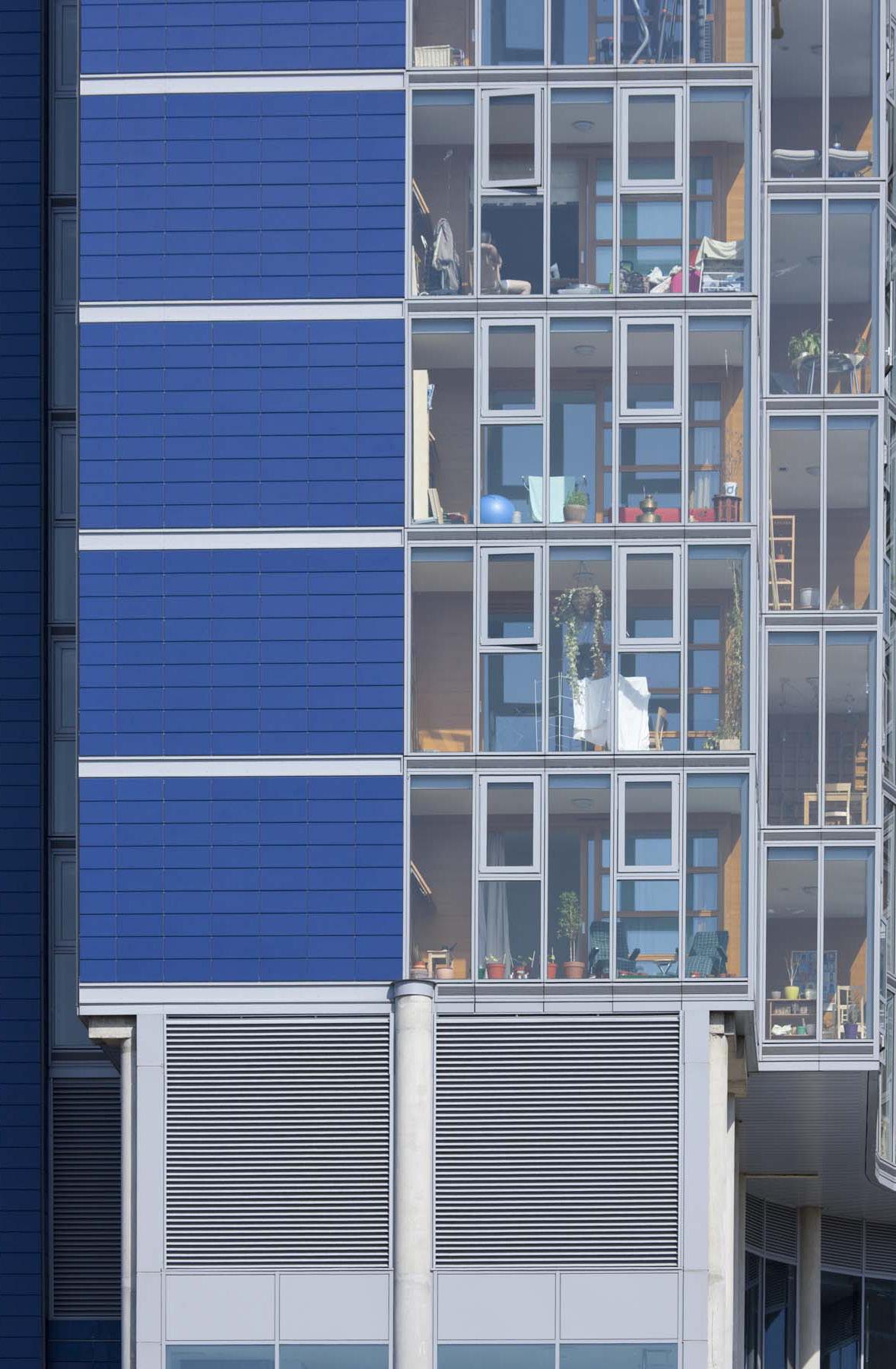
All requirements of these tests need to be undertaken and passed by an independent test house before an approval is awarded. By ensuring that the alloy is of the correct standard, with reduced inclusions and improved grain consistency, it has been demonstrated by QUALICOAT that architectural powder coat finishes can be further enhanced for sustainability, especially when used with Class 2 powders (super-durable) and Class 3 powders (hyper-durable)
Appendix A13 of the QUALICOAT Specifications is now aimed at specifiers who have large facade projects and wish to take advantage of the additional protection that comes from a ‘QUALICOAT 3.0’ Specification. Whilst the current QUALICOAT supply chain includes powder manufacturers, pretreatment systems providers and architectural powder coaters, QUALICOAT 3.0 introduces for the first time the aluminium extruders into the QUALICOAT powder coating supply chain.
Specifiers who wish to take advantage of QUALICOAT 3.0 should in the first instance contact QUALICOAT UK & Ireland for guidance on specification and help in choosing the correct supply chain.
The current QUALICOAT Specification is freely available for download via the Association’s website, qualicoatuki.org and offers an up-to-date list of licensed UK and Ireland Powder Suppliers, Pretreatment Suppliers and Applicators. Telephone support is available from QUALICOAT UK & Ireland Head Office in Birmingham on 0330 236 2800, the Association can also be followed on Twitter @Qualicoatuki.
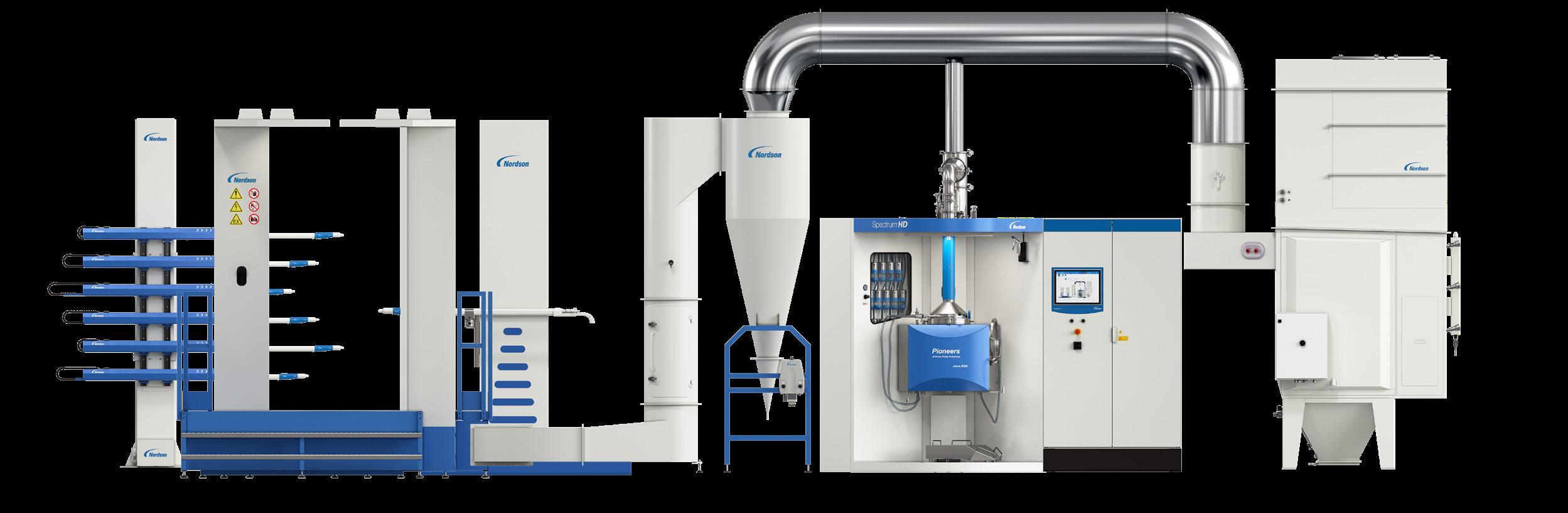
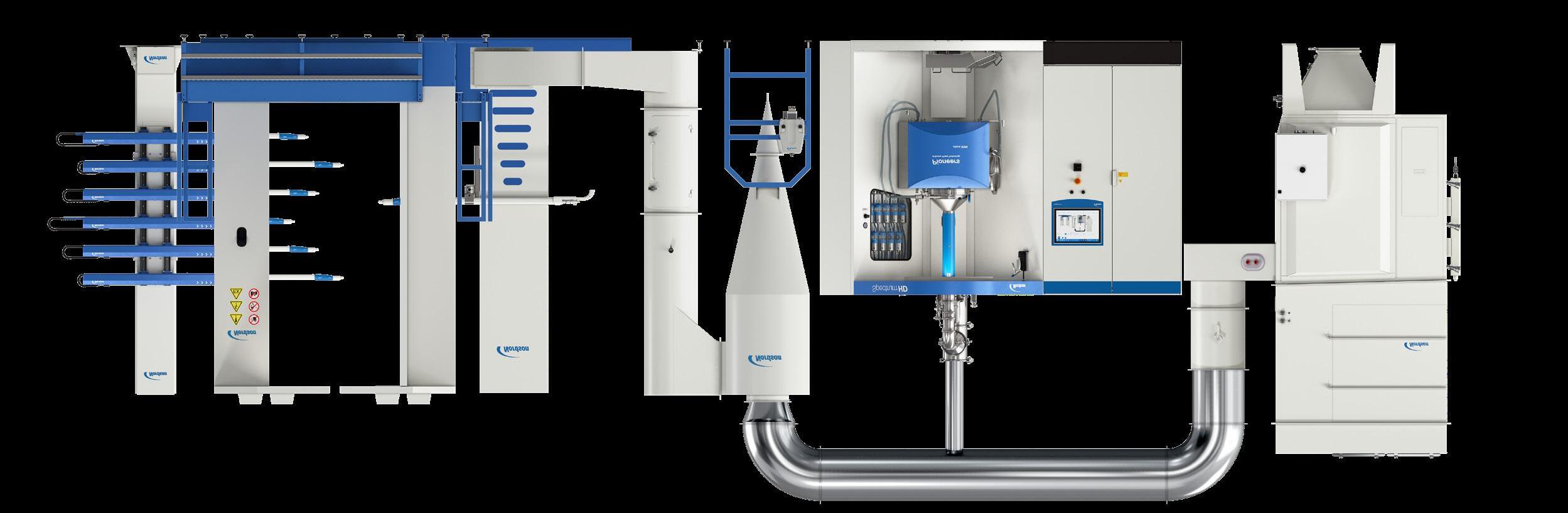