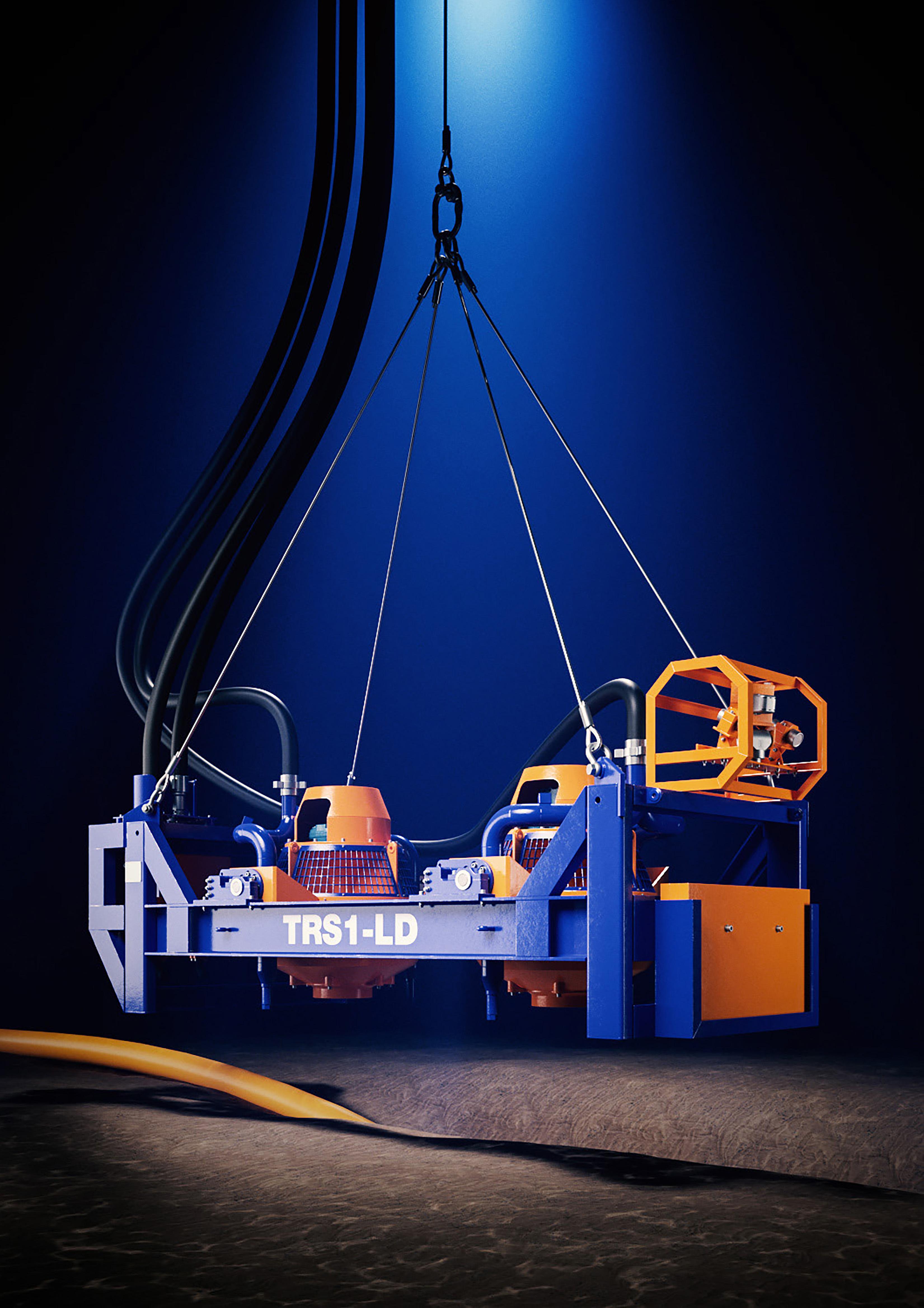
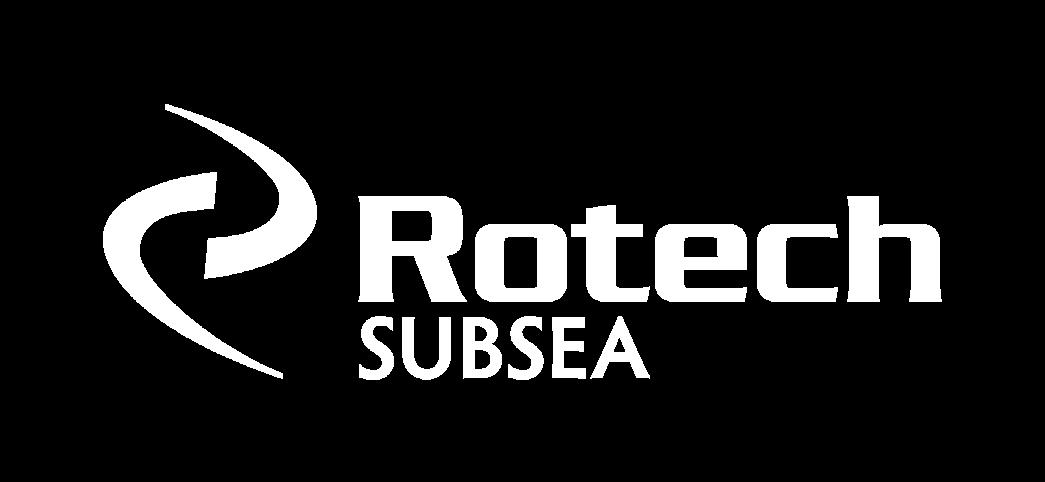
Trenching and excavation specialists since 1994
Trenching and excavation specialists since 1994
Rotech Subsea is the global leader in Controlled Flow Excavation (CFE) technology, delivering trenching, de-burial & backfilling solutions worldwide to the Oil & Gas and Energy sectors, using the latest range of patented RS equipment. For over two decades we have pioneered the development of cutting-edge subsea excavation technology. Dedication to innovation has seen Rotech continually evolve and enhance our specialised equipment to meet demand and deliver for the needs of many major clients in the subsea industry.
As a result, Rotech’s engineering teams have designed the latest range of RS tools with more power, enhanced jet profile, improved performance and safety, higher velocities, greater control and precision, improved stability and higher cutting capabilities.
The Rotech group are unique in that we are the only Subsea Excavation & Trenching company that Design, Manufacture and Operate our own equipment. we do not build equipment for anyone else. Innovate, Fabricate & Operate.
pending
Cable / Pipeline / Umbilical Trenching
Cable / Pipeline / Umbilical Deburial
Freespan & Sandwave Clearance
Backfilling and Burial
Jack Up Spud Can Clearing & Cleaning
UXO & Salvage Deburial
Rock Dump & Drill Cutting Removal
Harbour Clearance
Subsea Structure Foundation Access
Max Jet Flow 1,700L/s Max Jet Pressure 80kPa Max Jet Power 85kW Minimum Operating Depth 2.5m
Safer
Highly qualified
Real time sonar
Rotech Engineering &
of
Rotech
for 24hr
Rotech operators are supplied to operate the jetting system for soils in excess of 80kPa
Max RS1LD
RS3
RS1LD
Maximum flow
pressure
(Vertical)
(Horizontal)
grip force
grab diameter
grab diameter
depth
Rotech Subsea were contracted by Jan De Nul to provide the TRS1LD Jet Trenching tool to carry out Post-Lay Trenching works on OWF in Taiwan. The scope of work consisited of burying a total of 21 cables (4 Export, 17 Array) to client specification of 2.0m DoL. The project will be completed in 2 phases.
The TRS1LD was selected by Jan De Nul due to its unparallelled technical and performance capabilities resulting in increased productivity and a reduction on the projects total costs. The subsea spread of equipment was mobilised on the Willem De Vlamingh as well as being mobilised on the Grand Canyon II and deployed using the ships crane. Water Depths ranged from 8.0m - 29.0m LAT.
Phase 1 of the project was a success with 4 Export Cables and 7 Array cables being buried to client specification with ease. Soil conditions were described as soft sands however, we experienced large sections of stiff clay with shear strengths up to 80kPa. Despite this, the TRS1LD excelled and still achieved Jan De Nuls burial specifications. The TRS1LD lowered the cable with 2 passes at an average rate of 4m/min and reaching speeds of up to 10m/min in some sections.
Rotech Subsea were contracted by Subsea 7 to provide the TRS1 Jet Trenching tool to carry out Post-Lay Trenching works in Offshore Australia. The scope of work consisited of burying 6000m of 118mm diameter umbilical, to client specification of 0.6m Top of Cable.
The subsea spread of equipment was mobilised in January 2021 on the Seven Eagle and was deployed using the vessel crane. The TRS1 was operated in water depths up to 50m LAT, experiencing soil conditions of medium to coarse grained sand as well as harder, more cohesive soils.
The project was a great sucess with Subsea 7 delighted in the TRS1’s technical and performance capabilities. The umbilical was easily trenched to client specification with the Rotech Equipment being operational for only 22 hours for the entire proejct. In the soft soil areas, a trench depth between 1.3m - 1.6m BOT was achieved at a progress rate of 4m/ min. In the harder areas, depths betwen 1.0m - 1.3m BOT were observed at a progress rate of 3m/min. These depths were all achieved with only 1 Pass.
The TRS1’s unparalled capabilities allows for excellent productivity thus leading to a reduction on the projects total costs. A successful project for all parties, and Rotech Subsea look forward to future collaborations with Subsea 7.
Rotech Subsea Ltd were contracted by SAIPEM as part of a Power-Fibre Optic Cable (PFOC) and Flexible and umbilical Post Lay Jet Trenching Project. The Rotech Subsea TRS1LD tool c/w HP Jets was selected by Saipem for this workscope due to advanced Technical capabilities and cutting ability in stiff soils.
The spread of equipment was mobilised on the Mubarak Multicat Vessel to complete the post lay trenching of various FPOC, flexible pipelines and umbilicals.
TRS1LD performance was as expected and Rotech Subsea delivered as promised in soils in excess of 200kPa undrained shear strength
Each Product was lowered to 1m Top of Pipe/Top of Cable below the adjacent seabed level. The post lay trenching operations were completed whilst progressing at a rate averaging 3m/minute.
Rotech Subsea are contracted by Seaway 7 to provide the TRS2 CFE tool for Sandwave Clearance operations at OWF located in Taiwan. The scope of work is to be completed in 2 phases with phase 1 having being completed in the third quarter of 2020. Phase 2 is to commence in the early stages of 2021.
The TRS2 was selected by Seaway 7 due to its high volume output performance making it the ideal tool for sandwave clearance due to its ability to displace large amounts of subsea material. The Rotech Equipment was mobilised on the Topaz Installer and operated in water depths of between 5m-10m.
Phase 1 of the project was a success. The TRS2 was utilised for seabed lowering excavations. The TRS2 tool was used to carry out 25 grid Line excavations, lowering the seabed to allow vessel access to the worskite during spring tides. The sections to be levelled varied in height ranging between 0.4m - 1.8m. Rotech carried out excavations at speeds between 4m/min - 10m/min. Rotech look forward to returning to Yunlin Offshore Wind Farm to complete Phase 2 of the project in 2021.
Rotech Subsea were contracted by Orsted to provide the TRS1LD Jet Trenching tool - equipped with HP jets - to carry out cable burial at OWF located in the Irish Sea. Rotech Subsea took control of all operations for this project from chartering the vessel to contracting all relevant parties required to carry out a successful excavation project. The TRS1LD was selected by Orsted due to its unparallelled technical and performance capabilities resulting in increased productivity and a reduction on the projects total costs.
The subsea spread of equipment was mobilised on the OSV Relume and deployed using the ships crane. Two separate cables (WOW03 & WOW04) - totalling approximately 3.5km in length - were to be trenched to Orsted specification of 2.0m TOC in the soft sand areas and to 1.0m TOC in the Stiff Clay areas. Water depth ranged from -2.0m to +14.0m LAT.
The project was a success,with the cables trenched to Orsted Specification at an average rate of 4m/min in the soft sand areas and 2m/min in the stiff clay.
Rotech Subsea were contracted by Maersk Supply Services to provide the TRS2 CFE tool for Jacket Template & Well-head De-burial in the Tyne Field. The Rotech RSG grab system was also used to assist in the recovery of a PLET Structure in the Southern North Sea.
The TRS2 was selected by Maersk Supply Services due to its high volume output performance making it the ideal tool for De-burial due to its ability to fluidise and displace large amounts of sediment. The Rotech Equipment was mobilised on the Maersk Inventor and operated in water depths of approximately 17m.
The project was a success. The TRS2 de-buried the Jacket Template and Wellhead with ease reaching up to 5.5m deburial depth. This was achieved in Dense Sand soils. The TRS2 was also additionally used for backfilling operations, minimising the effect on the seabed by filling the excavated area with the removed sediment allowing for NSBL to be achieved. The Rotech Grab operations were also a sucess with the grab being utilised to lift the cuts of the PLET into a subsea Basket.
TRS2 & RSG- Structure De-Burial & Recovery Q3, 2020 - Rotech Equipment & the Structure to De-bury
Rotech Subsea were contracted to assist with remedial cable burial operations on x3 offshore wind farms offshore Germany. Rotech provided the RS1-2 Hybrid Controlled Flow Excavator (CFE) equipment spread to carry out this scope.
Rotech were to carry out:
• Remedial Cable burial in various locations along multiple cables
• x1 cable to be buried to 1.5m Depth of Lowering
• All other cables to be buried to 3m Depth of Lowering – Reasonable endeavours.
Water Depth - 3m– 13m
Scope - Cable Burial
Soils - Silty Sands with intermittent hard layers
Currents - Up to 2.4 Kts max
General Sea State - 0.25 – 1m Hs
Rotech’s Scope of Work was to lower existing export cables on each worksite to client specific depths. Wind farm 1 - 1.5mtrs DOL, Wind Farm 2 & 3 the spec was maximum 3m DOL or best endeavours should the material being excavated be too hard. Prior to the project it was known possible hard and cemented areas could be encountered along the route.
The RS1-2 was deployed from the vessel crane of single fall wire, the equipment was deployed over the starboard side of the vessel.
Vessel forward & aft deck winches were used for our orientation tuggers. These were routed through snatch blocks fixed to pad eyes on the extended outriggers.
The RS1-2 remained suspended above the seabed / cable and in line with the cable to complete all trenching operations. The vessel’s DP positioning system was used to move the CFE tool along the cable RPL routes/areas that required trenching works. The RS1 tool was the lead excavator. USBL transponders fitted to the tool provided accurate data on the location of the RS1-2 to ensure operations were completed in the correct locations.
Trench depth was monitored real time using a sonar imager mounted to the CFE tool to confirm the trench depth and when the cable had been buried to the correct specification for the remedial burial works.
Once Rotech completed their scope, the client surveyed the area using separate survey equipment to confirm that the completed trenching ops met the required specifications.
On Windfarm 1 - 1.5m Depth of Lowering was achieved with two passes.
On Windfarms 2 & 3 the average DOL was 2 – 2.5mtrs. The mobility of the seabed was very active on these sites as confirmed by the client reps data with some areas gaining/losing up to 6mtrs over a season. This was completed in 2 passes and was passed off by client.
Rotech Crew and the vessel deck crew worked very well together with good communication which lead to safe & efficient tool launch and recovery operations, and overall project success.The RS1-2 hybrid tool worked very well and performed as expected and achieved the excavation specifications required by the client