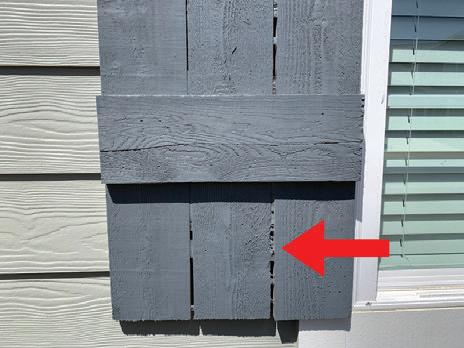
15 minute read
SUPER CEDAR SHUTTERS
SUPER CEDAR
SHUTTERS
Advertisement
By Matt Weber
Anyone can make shabby board-and-batten shutters. Go grab three long boards off a shelf, nail a couple short boards across
them, and voilà! You’ve got rustic shutters … right? Maybe even squirt some caulk between the boards, because, why not?!
You shouldn’t do that because wood swells and contracts with changes in temperature, causing separation between the joints and resulting in that melted cheese look from the caulk failing between your shutter boards. It ain’t pretty. And now it’s on the front of your house.
The truth is that you get what you pay for, and the guys at Rustic Shelves & Shutters of Gardendale, Alabama, build theirs to look great and last long. Their decorative shutters are made from genuine cedar, and the vertical boards are all edge-joined with wood biscuits and strengthened with Titebond III wood glue, then clamped into a solid unit. They offer router detailing, sanding and/or planing for the texture of your preference, plus a wide array of finish options. Once stained and fully assembled, a UV protective clear-coat is applied and a water-seal coating is added to the backs.
WHY CEDAR?
The shutters from Rustic Shelves & Shutters are all made of genuine cedar lumber. Cedar is versatile, sustainable and beautiful with rich color tones in the grain, which is also free of pitch and resin, making it ideal for accepting a wide range of finishes. Compared to other coniferous woods, cedar is dimensionally stable with a very low shrinkage factor, so
it resists warping, twisting and checking—critical to the look and performance of your shutters.
Cedar is also an excellent choice for outdoor applications thanks to its natural durability. The wood contains natural oils that make it resistant to rot, decay and insect attacks. Properly finished and maintained, cedar will deliver decades of trouble-free service.
MEASURING
Most homeowners prefer shutters to match the height of the window glass. Some customers
Board-and-batten shutters look deceptively simple to construct, but poorly-built shutters will soon show signs of deterioration.

Carpenters who make shutters on a regular basis will use a thickness planer to process the boards before assembly. The crew at Rustic Shelves & Shutters relies on the DeWalt DW735 13” two-speed planer. The wood texture will affect the final finish. Smooth-sanded surfaces tend to show more grain detail while roughsawn textures absorb more stain for a darker, more uniform look.
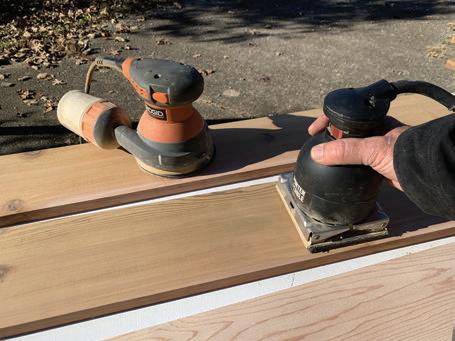
When cutting several boards to the same length on a miter saw, measure one board and set a stop to cut the rest. Some miter-saw stands come equipped with a stop, or you can make your own by attaching a fence to a workbench square to your miter saw’s fence.

request shutters slightly taller than the window, but you should avoid making shutters that will be too short for the window. The width of the shutters will be determined by the style and taste of the homeowner, but a good rule of thumb is to limit each shutter’s width to half the width of the window.
The most commonly available board sizes for rustic cedar shutters are 1x4 and 1x6, which can be configured in a variety of patterns for decorative appeal. The basics of construction rely on vertical boards edge-joined into a panel with horizontal or diagonal battens attached on top, which adds strength to the construction.
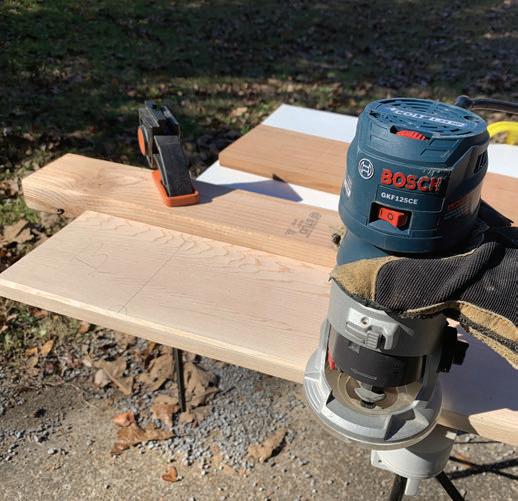
Add any sort of edge-routing detail prior to cutting the biscuit slots in the boards.
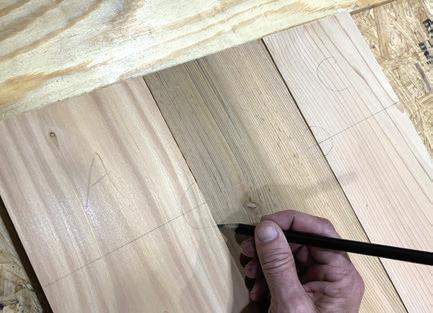
To mark the biscuit slots, arrange the boards edge to edge with all ends flush. Label the boards in sequence, draw square lines across the panel at each biscuit-slot location, then draw circles where each line intersects the joints between boards.
PLANING/SANDING
Depending on the condition of the lumber, planing the cedar boards to a common thickness prior to assembly might not be required. A DIY homeowner can take the time to carefully hand-select boards that won’t require planning, but a professional will find a power planer incredibly useful if making shutters on a regular basis.
When it is necessary, the RS&S crew uses a DeWalt DW735 thickness planer to level all the boards to the same size. The best practice is to give the boards shallow passes through the planer to remove the least amount of material necessary. A planer is also a good time- and labor-saving tool to smooth the wood surface instead of sanding the boards.
The wood texture ultimately impacts the look of the shutter. Once a stain is applied, smooth board textures tend to show more grain differentiation than rough-sawn wood, which will have a more uniform appearance. If you don’t have a planer at your disposal and you want the smooth grain to shine though, then power sanders can be used to prep the wood for a new coating.
CUT BOARDS TO LENGTH
Next step in shutter construction is to cut the vertical boards to length. Pro tip: The guys at RS&S cut their vertical boards 1 inch longer than the final shutter measurement. Once the shutters are completely assembled, the carpenters use a saw guide on that extra inch to make
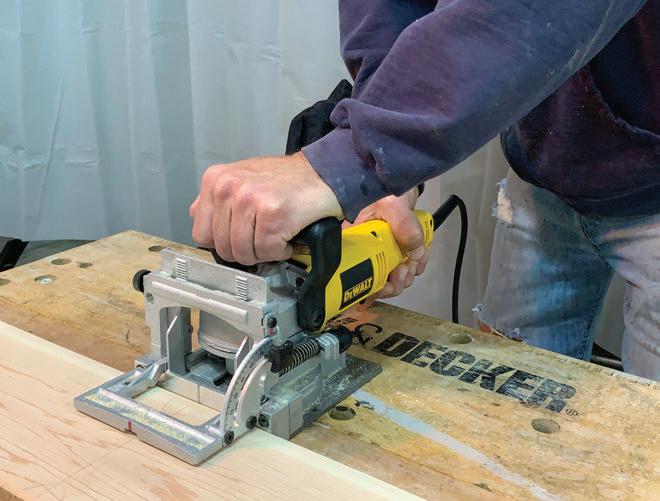
The RS&S crew uses a DeWalt DW682 plate joiner to cut slots at each half-circle mark along the board edges.
a final cut along the top and bottom edge, ensuring the board ends are in perfect alignment.
ROUTING
A popular option for cedar shutters is to apply detail to the board edges using a router. The most common request is to cut a bevel along the inner edge of the vertical boards. When the beveled edges are assembled, they form V-grooves between the boards for more visible differentiation. Customers may also want a similar detail applied to the batten edges. A variety of router bits can produce differently shaped profiles along the board edges. The most popular edge profiles for shutters are bevel and cove shapes.
Note that if you decide to rout the boards, do so prior to cutting slots in the the board edges with a plate joiner. Otherwise, the slots made by the plate joiner (a.k.a. biscuit joiner) can interfere with the guide wheel of the router bit, causing the bit to misalign and disrupting the cut.
MARK THE PANELS
For each shutter, the long, vertical boards are first assembled into a panel by joining the long edges using glue and biscuits. The first step is to mark the biscuit locations.
You’ll need a flat, sturdy work surface that won’t be ruined by exposure to wood glue. It might be helpful to screw two scrap boards onto your workbench in L-formation to serve as fences along one side and one end of the shutters while you group the shutter boards together.
Align the long edges of the panel boards (typically 3 to 5 boards) so their ends are flush. Write numbers or letters on the boards to keep them in sequence. Use a framing square and pencil to draw 90-degree lines square across the panel at each biscuit location. The shutters usually get three to five plate-joining biscuits between each board, depending on the length of the shutter. Mark biscuit lines 3-4 inches from the ends of the shutter panel and space the other biscuit lines evenly between them.
Draw circles at each intersection where the lines cross the joint between two shutters. The circles indicate where to make the biscuit cuts using the plate joiner. (Note: Instead of assembling the shutters with plate-joining biscuits, you can use pocket screws as an alternative).
CUT THE BISCUIT SLOTS
A plate joiner is a power tool that enables you to make extremely strong and accurate joints in wood. The tool works by a plunging a blade to
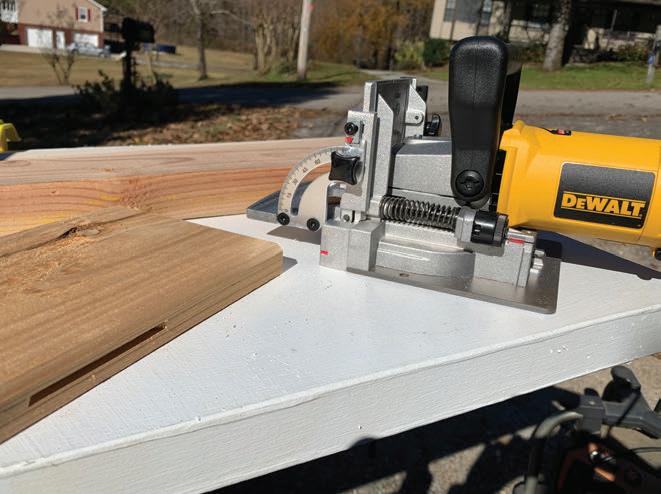
Clean the slots of any wood chips or debris. Insert the plate-joining biscuits to check board alignment.
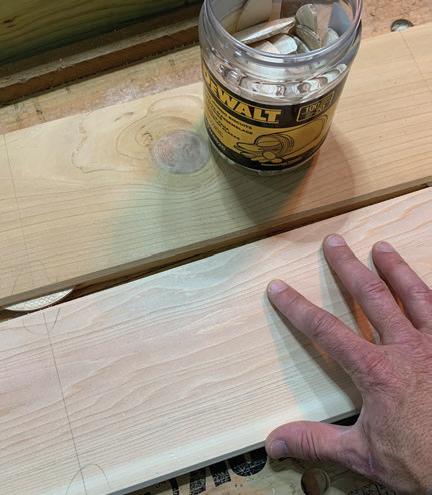
precisely cut crescent-shaped slots for the placement of flat wooden dowels or “biscuits” that will bridge between the mating boards. To make shutters, the biscuits are all located along the edges where the boards meet.
The RS&S crew uses a DeWalt DW682 biscuit joiner for this operation. Make sure you’ve selected the proper depth setting for your biscuits. (Use 1/2-in. cutting depth for the recommended #20 biscuits). Clamp each board firmly and align the plate joiner’s center registration mark with your layout mark inside the half circle. Bring the blade up to full speed, position the fence squarely against the board edge, and plunge the blade until it bottoms against the stop. Repeat the procedure to cut slots at each biscuit location in all the boards.
Pro tip: Use compressed air to clear the slots of any sawdust or wood chips that can interfere with insertion of the biscuits.
Return the boards to your workbench for assembly, arranging them according to their numbered or lettered sequence. Insert biscuits into the slots and check the alignment between boards. Make adjustments as necessary.
GLUE AND CLAMP
Remove the biscuits from the slots and apply quality wood glue to the edges of the adjoining shutter boards. RS&S recommends using Titebond III adhesive. Use a rubber brush to spread the glue completely over the mating edges, making sure to work glue into the biscuit slots. Replace the biscuits in the slots, assemble
Apply a quality glue such as Titebond III to the board edges. Fun fact: A joint made with proper application of wood glue is actually stronger than wood. Make sure to apply glue to the slots, because the biscuits will absorb moisture in the glue and expand to form a tight joint.
The shutters each require two to three bar clamps to hold the edges together, and a variety of smaller clamps to hold them flat to the work surface while drying.
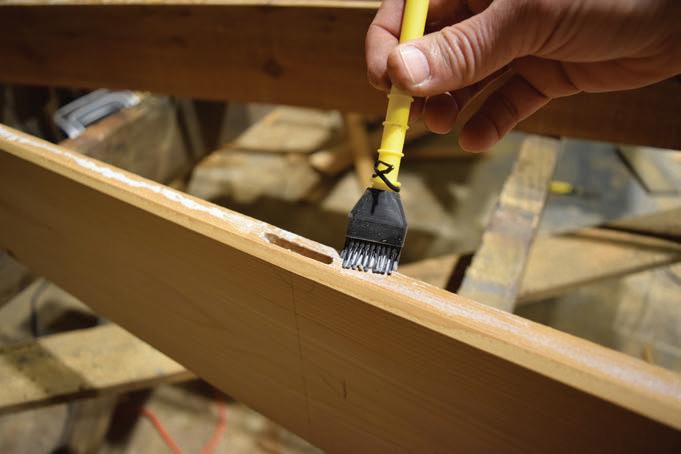

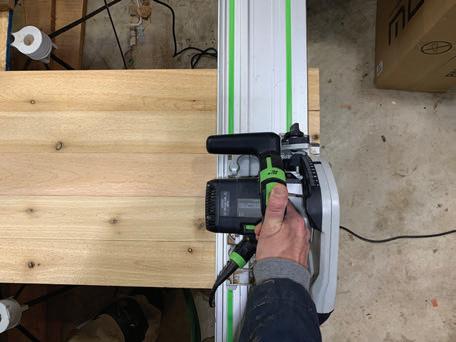
Once the panels are dry, carefully cut them to their final length. Apply your stain/finish of choice, coating the panels and battens separately.

the joint, and clamp until dry. For a biscuit joint to be most effective, it is important that the biscuits themselves be in contact with the glue. This is because the biscuits absorb moisture in the glue and expand to form a tight joint.
You will need several clamps to hold the board edges together across the body of the shutter while the glue dries. Make sure the shutter panel remains in a flat plane. This may require clamping the boards down onto the workbench. Use a plastic scraper to remove excess glue that squeezes out between the joints. Clamp the shutter panels for 24 hours.
FINAL CUTS
The width of the shutter panels will determine the length of the battens. Enhance your cutting accuracy by skipping the tape measure and instead place the batten boards directly over the panels and mark the cutlines in place. Cut the boards to length on the miter saw. In case of slight discrepancies in shutter size, keep the battens and their corresponding panels together.
Don’t forget to cut any excess length off the shutter panels prior to applying the finish.
PREFINISH THE SHUTTERS
Stain the panels and battens separately before attaching the battens. Finish options abound, but the guys at RS&S prefer to sprayapply General Finishes brand water-based wood stains to their shutters.
ATTACH THE BATTENS
Once the stain has dried, the battens can be attached to the panel. A simple shop-made spacing jig can help keep the batten placement consistent. Otherwise measure and mark each shutter carefully, apply glue to the backs of the

STRUT YOUR STUFF
We’ve covered the basics of construction, and the rest is up to you. Research shutter photos online to get an idea of all the available batten patterns to give your project a style of its own. You’ll also find lots of decorative hardware styles to accentuate the look, including S-shaped hold-back hooks, corner brackets, “hand-forged” nail heads, and hinges of all shapes and sizes. Experiment with detailed cut-outs or arch-shaped tops. Sketch a few designs on paper and play with the look until you get exactly what you want. Whether you make your own shutters or hire a carpenter for the construction, creating a custom design is a great way to put a personal stamp on your home.
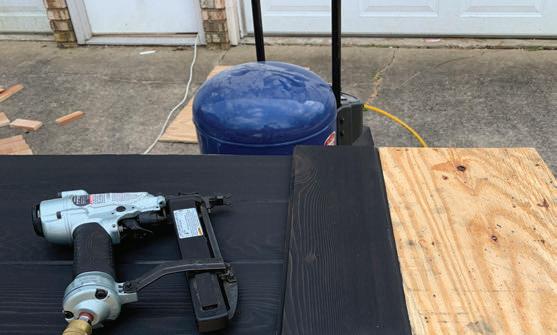
To space the battens consistently on the shutters, make a simple rectangular jig with a stop attached along one end that aligns with the panel ends. Glue is then attached to the rear of the battens, and they’re fastened through the back of the shutters using crown staples. Clamps are often necessary to hold the battens flush with the surface while the glue dries.

Six beautiful sets of matching shutters.
battens, and fasten them in place through the back of the shutter with crown staples or wood screws. Clamps are often necessary to hold the battens flat to the shutter.
Note: Once the battens are attached, the glue tends to run down the face of the shutters if they are stored upright before the adhesive dries. For this reason, it’s best to keep the shutters flat overnight.
FINAL TOUCHES
Once the batten glue has dried, RS&S coats the backs of the shutters with Thompson’s Water Seal. The fronts of the
The completed project after installation.
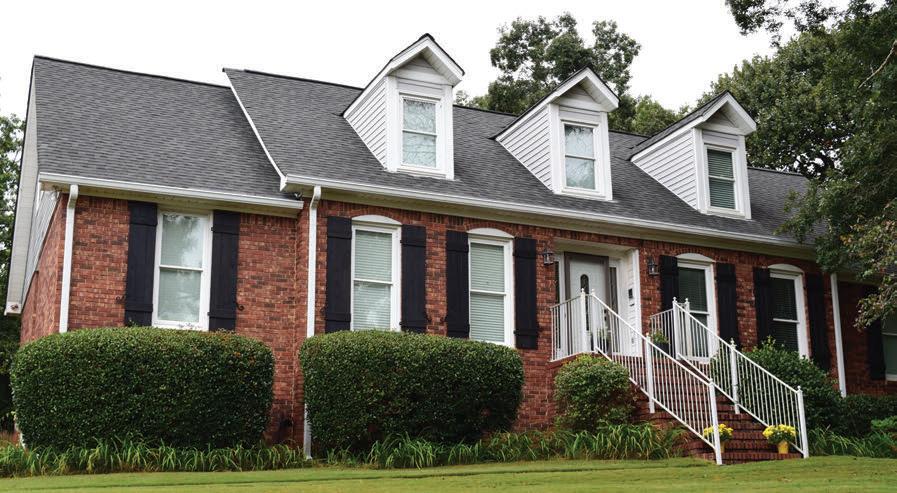
shutters get sprayed with General Finishes Exterior 450 water-based topcoat, which has UV absorbers and built-in mildewcides.
You might even consider additional accessories such as decorative hardware, or even black vinyl hinges and shutter dogs, which provide a classical look at a fraction of the price of metal hardware.
Say no to shabby shutters and humdrum curb appeal. Follow these tips to make super shutters that are built to look great for years to come. You can follow Rustic Shelves & Shutters online at facebook.com/supershutters.
H
Editor’s Note: Thanks to Cary Lott of Birmingham, Al., for help with this article.
HOW’S IT HANGING?
You have a number of options when it comes to installing shutters, and methods vary based on home construction. Do you mind visible fasteners, or would you prefer to hide them? Are you nailing into wood, Hardiboard, or brick?
Fastener type should match the substrate. If you’re nailing through cement-board, metal or wood siding, pre-drill the holes and use wood screws long enough to penetrate solidly through the house sheathing.
Shutters on brick, block or concrete walls can be installed with concrete screws long enough to embed at least 1 in. deep into the substrate. You’ll need a hammer-drill and masonry bit to To hang the shutters, Randy Stephenson of Cropwell, Al., uses a simple layout jig to make sure the fastener placement is consistent among the shutters and that his concrete screws will embed into brick rather than mortar joints.
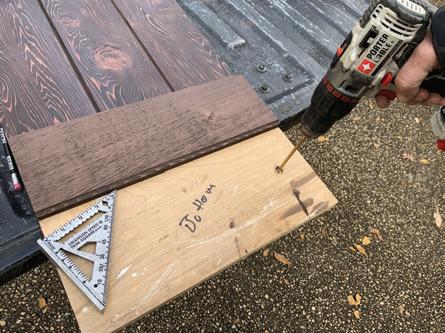
When drilling 1/2” holes for wood plugs, be sure to use a Forstner bit, which will cut clean holes in the finished shutter surface to provide a tidy fit for the stain-matched plugs.
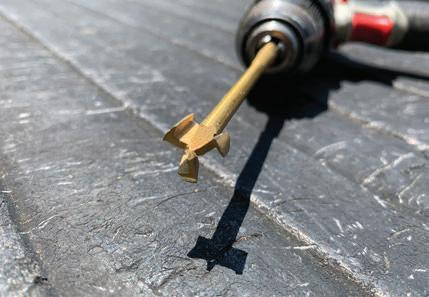
pre-drill the fastener holes. Drive concrete screws into brick or block rather than into the mortar joints. Masonry walls will require masonry anchors.
Rustic Shelves & Shutters recommends using 4 to 6 fasteners per shutter, depending on size, with the first four placed near the corners of each shutter to prevent vibration in the wind.
One option is to use color-matched fasteners driven flush with the shutter surface. This method permits easy removal for maintenance. Another option is to slightly countersink the fasteners and cover the heads with color-matched wood putty.
Decorative hinges provide a prime location to drive screws (painted to match the hardware) right through the shutter, leaving the heads exposed. You can then pin down the opposite
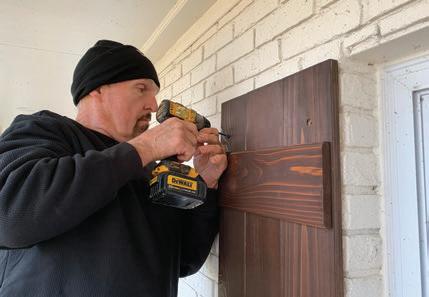
With the fastener locations established, the plug holes serve as a guide to drill pilot holes into the brick with a hammer-drill.

The shutters are anchored with Tapcon concrete screws, and Stephenson prefers the 1/4” versions. Make sure the shutters are plumb, level, and aligned with the window. The concrete screws should embed into the brick by at least 1”.
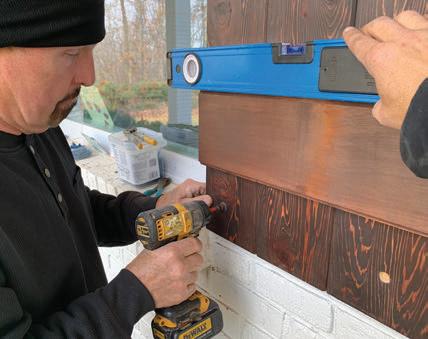
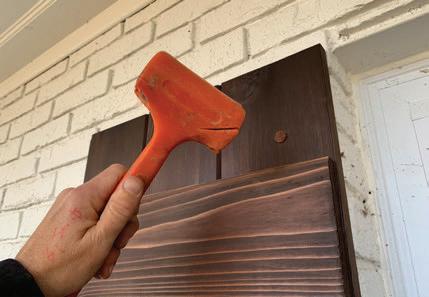
The color-matched wood plugs will tap snugly into the holes to conceal the fasteners and complete the project.
corners using Fine Screws, which have a small trim-head that is easy to conceal.
Another option for discerning homeowners is to hang the shutters with countersunk fasteners that are covered with stain-matched wood plugs.
Pro tip: If drilling holes in the shutters for wood plugs, it’s important to use a Forstner bit, which cuts a very clean hole for the plug. Spade bits and even spiral bits tend to splinter or chip the wood around the holes, causing noticeable damage to the finished surface. The clean hole of a Forstner bit will provide a snug, tidy fit for the plug, achieving an attractive finished look.